How does misalignment affect the reliability of an electrical engine?
Articulo9 de septiembre de 2019
Nowadays, a great deal of reliability or maintenance departments have concerns (or not) when the moment comes to identify the presence of a misalignment out of the allowed range of performance. Thus, the question to consider is the fact of WHY WE SHOULD PAY ATTENTION TO THE PRESENCE OF THAT FAILURE?.
A statistical analysis of occurrence on the different problems related to machinery indicates that approximately:
- 40% of the problems are due to misalignment.
- 30% of the failures is due to misalignment in coupled machines.
- 30% of the problems is due to problems in belts and pulleys of machines.
- 20% of inconveniences are due to bearings.
- 10% of the problems are related to resonances.
- 10% of the failures may be caused by: cavitation, oil swirl, allowance or mechanical play, turbulence in plumbing, etc.
When speaking of misalignments, we refer to a statistical 50% of all the premature failures that electrical machines may show. Nowadays, electrical engines rotate much faster andreceive more load, and at the same time modern manufacturing tends to use lighter elements, so electrical engines are more and more sensitive to misalignment mistakes.

Alignment is a condition in which two or more machines share their axial lines, that is, they are collinear.

A good alignment between the axes of a system formed by an electrical engine and a driven machine would have the following advantages:
- Increases the useful life of bearings.
- Reduces the risk of breaking in couplings.
- Reduces electrical waste.
- Diminishes vibration amplitude.
- Increases reliability of the engine.
- Decrease risk of overheating.
- Increases production levels of equipment.
- Minimizes sudden shutdown of machines.
Now, misalignment can be defined as the condition in which the axis of the conducting machine and the conducted one do not have the same center lines, that is, they do not comply with the collinear condition. It is also true there will be a small misalignment for which the perfect alignment is impossible. Thus, it is very important to choose a coupling that absorbs such defect in order to minimize the efforts generated by such allowed misalignment in the performance.
The most common causes for misalignment can be:
- Flaw associated to coupling of machines during mounting (Defficient mounting).
- Poor mechanizing of coupling.
- Thermal expansions during performance.
- Transmitted forces due to expansions in piping.
- Irregular or deffective foundry.
- Week support.
- Looseness of fixations.
- Deformities.

Actually, there is always a combined misalignment, that is, the existence of two types of misalignment: angular and parallel. Here, we will briefly explain the typical “diagnosis rules” to recognize each of the misalignment types in a system.
Angular misalignment:
•The typical vibration spectrum would be of high axial vibrations of 1X and 2X from the rotational frequency predominantly, with little input from the rotational frequency in 3X.
•For a phase analysis, it should have a mismatch of 180 degrees throughout the coupling in the axial direction.
•When the axial misalignment turns severe, it can generate high amplitude peaks to the harmonics of the rotational frequency much higher (4X-8X), of a complete series of high-frequency harmonics similar to the mechanical looseness.

Cursos recomendados




%252FImagen%252FRAMPREDYC-1730060420837.webp%3Falt%3Dmedia%26token%3D2634a7f0-988e-4022-b91f-382503e6e9db&w=3840&q=75)



Parallel misalignment:
•The typical vibration spectrum would be high radial vibrations of 1X and 2X of the predominant rotational frequency with a little input from 3X of rotational frequency. Also, the amplitude of 2X from the rotational frequency will often be higher than the amplitude of 1X rotational frequency.
•For a phase analysis, it should have a mismatch of 180 degrees throughout the coupling, in the radial direction.
•When parallel misalignment becomes severe, it can generate high amplitude peaks to higher rotational frequency harmonics (4X-8X), or even a complete series of high frequency harmonics similar to mechanical looseness.

We should mention that these typical “diagnosis rules” will not always appear in the same form for all the misaligned machines; that means these typical spectra will not always be reliable due to the different ways that the system being studied can move, which could generate vibration behaviors that are out of the range ofsuch diagnosis rules.
Another important detail points to the fact of how the presence of misalignment can affect the useful life of bearings, which has a direct proportional relation with the force acting on it, thus significantly affecting the useful life of bearings.



Real Case “Misalignment in the pump-engine system”
Motor: ACEC - Speed: 2960 RPM - Power: 132 kW
COUPLING SIDE OF ENGINE – SPEED SPECTRUM

COUPLING SIDE OF PUMP – SPEED SPECTRUM

As we observe each of the speed spectra, either the engine or the pump, we can see that the higher vibration amplitude is associated to 1X and 2X from the rotational frequency, so it can be said that the motor-pump set is misaligned.
Finally, we can conclude that when an electrical engine has an out-of-tolerance range misalignment, there has to be special consideration in minimizing efforts generated from the presence of such force, with the sole purpose of increasing the reliability of the system under study.
Author: Lic. Martín Lémoli
Vibrations Analyst Cathegory 3
Mail: mlemoli@hotmail.com / mlemoli@yahoo.com
Dinos qué te ha parecido el artículo
Artículos recomendados
Conoce el FMECA y cuáles son sus objetivos

Barreras y factores de éxito para implementar la Gestión de Activos

¿Quedaremos off line en el mantenimiento aplicado a rodamientos?

Cómo crear un plan de mantenimiento exitoso

Publica tu artículo en la revista #1 de Mantenimiento Industrial
Publicar un artículo en la revista es gratis, no tiene costo.
Solo debes asegurarte que no sea un artículo comercial.
¿Qué esperas?
O envía tu artículo directo: articulos@predictiva21.com
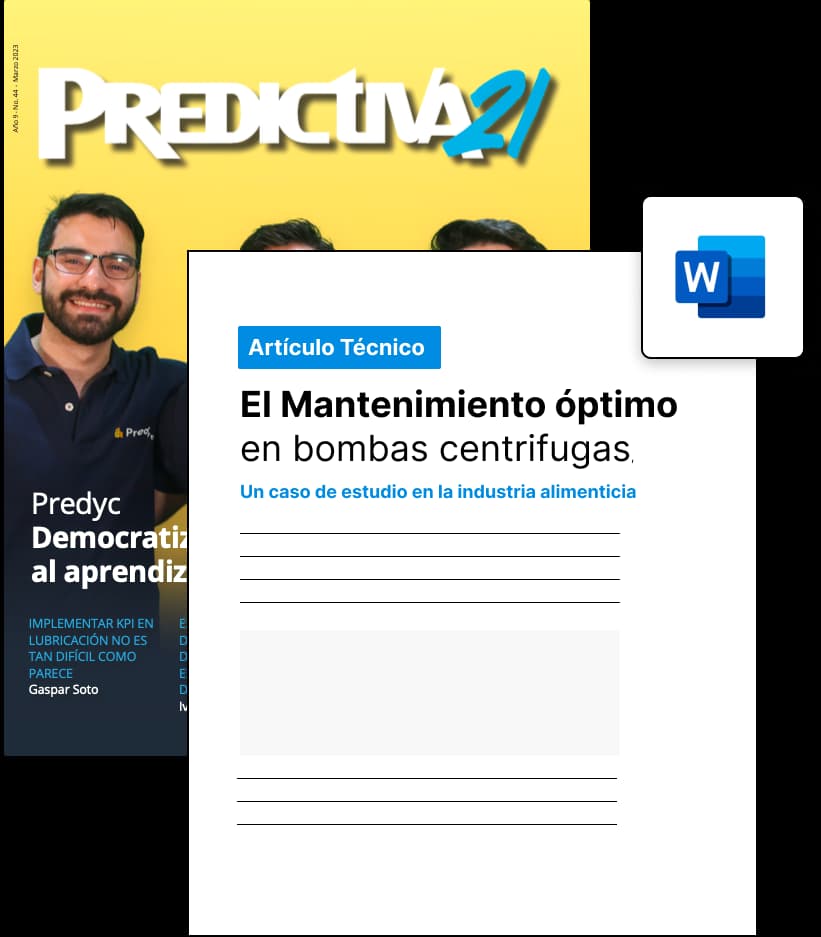
How does misalignment affect the reliability of an electrical engine?
Articulo 9 de septiembre de 2019Nowadays, a great deal of reliability or maintenance departments have concerns (or not) when the moment comes to identify the presence of a misalignment out of the allowed range of performance. Thus, the question to consider is the fact of WHY WE SHOULD PAY ATTENTION TO THE PRESENCE OF THAT FAILURE?.
A statistical analysis of occurrence on the different problems related to machinery indicates that approximately:
- 40% of the problems are due to misalignment.
- 30% of the failures is due to misalignment in coupled machines.
- 30% of the problems is due to problems in belts and pulleys of machines.
- 20% of inconveniences are due to bearings.
- 10% of the problems are related to resonances.
- 10% of the failures may be caused by: cavitation, oil swirl, allowance or mechanical play, turbulence in plumbing, etc.
When speaking of misalignments, we refer to a statistical 50% of all the premature failures that electrical machines may show. Nowadays, electrical engines rotate much faster andreceive more load, and at the same time modern manufacturing tends to use lighter elements, so electrical engines are more and more sensitive to misalignment mistakes.

Alignment is a condition in which two or more machines share their axial lines, that is, they are collinear.

A good alignment between the axes of a system formed by an electrical engine and a driven machine would have the following advantages:
- Increases the useful life of bearings.
- Reduces the risk of breaking in couplings.
- Reduces electrical waste.
- Diminishes vibration amplitude.
- Increases reliability of the engine.
- Decrease risk of overheating.
- Increases production levels of equipment.
- Minimizes sudden shutdown of machines.
Now, misalignment can be defined as the condition in which the axis of the conducting machine and the conducted one do not have the same center lines, that is, they do not comply with the collinear condition. It is also true there will be a small misalignment for which the perfect alignment is impossible. Thus, it is very important to choose a coupling that absorbs such defect in order to minimize the efforts generated by such allowed misalignment in the performance.
The most common causes for misalignment can be:
- Flaw associated to coupling of machines during mounting (Defficient mounting).
- Poor mechanizing of coupling.
- Thermal expansions during performance.
- Transmitted forces due to expansions in piping.
- Irregular or deffective foundry.
- Week support.
- Looseness of fixations.
- Deformities.

Actually, there is always a combined misalignment, that is, the existence of two types of misalignment: angular and parallel. Here, we will briefly explain the typical “diagnosis rules” to recognize each of the misalignment types in a system.
Angular misalignment:
•The typical vibration spectrum would be of high axial vibrations of 1X and 2X from the rotational frequency predominantly, with little input from the rotational frequency in 3X.
•For a phase analysis, it should have a mismatch of 180 degrees throughout the coupling in the axial direction.
•When the axial misalignment turns severe, it can generate high amplitude peaks to the harmonics of the rotational frequency much higher (4X-8X), of a complete series of high-frequency harmonics similar to the mechanical looseness.

Cursos recomendados




%252FImagen%252FRAMPREDYC-1730060420837.webp%3Falt%3Dmedia%26token%3D2634a7f0-988e-4022-b91f-382503e6e9db&w=3840&q=75)



Parallel misalignment:
•The typical vibration spectrum would be high radial vibrations of 1X and 2X of the predominant rotational frequency with a little input from 3X of rotational frequency. Also, the amplitude of 2X from the rotational frequency will often be higher than the amplitude of 1X rotational frequency.
•For a phase analysis, it should have a mismatch of 180 degrees throughout the coupling, in the radial direction.
•When parallel misalignment becomes severe, it can generate high amplitude peaks to higher rotational frequency harmonics (4X-8X), or even a complete series of high frequency harmonics similar to mechanical looseness.

We should mention that these typical “diagnosis rules” will not always appear in the same form for all the misaligned machines; that means these typical spectra will not always be reliable due to the different ways that the system being studied can move, which could generate vibration behaviors that are out of the range ofsuch diagnosis rules.
Another important detail points to the fact of how the presence of misalignment can affect the useful life of bearings, which has a direct proportional relation with the force acting on it, thus significantly affecting the useful life of bearings.



Real Case “Misalignment in the pump-engine system”
Motor: ACEC - Speed: 2960 RPM - Power: 132 kW
COUPLING SIDE OF ENGINE – SPEED SPECTRUM

COUPLING SIDE OF PUMP – SPEED SPECTRUM

As we observe each of the speed spectra, either the engine or the pump, we can see that the higher vibration amplitude is associated to 1X and 2X from the rotational frequency, so it can be said that the motor-pump set is misaligned.
Finally, we can conclude that when an electrical engine has an out-of-tolerance range misalignment, there has to be special consideration in minimizing efforts generated from the presence of such force, with the sole purpose of increasing the reliability of the system under study.
Author: Lic. Martín Lémoli
Vibrations Analyst Cathegory 3
Mail: mlemoli@hotmail.com / mlemoli@yahoo.com
Dinos qué te ha parecido el artículo
Artículos recomendados
Planificación de mantenimiento

Precursores de la ingeniería industrial

Descubre la utilidad de la KPI

Curso de especialización en digitalización del mantenimiento

Publica tu artículo en la revista #1 de Mantenimiento Industrial
Publicar un artículo en la revista es gratis, no tiene costo.
Solo debes asegurarte que no sea un artículo comercial.
¿Qué esperas?
O envía tu artículo directo: articulos@predictiva21.com
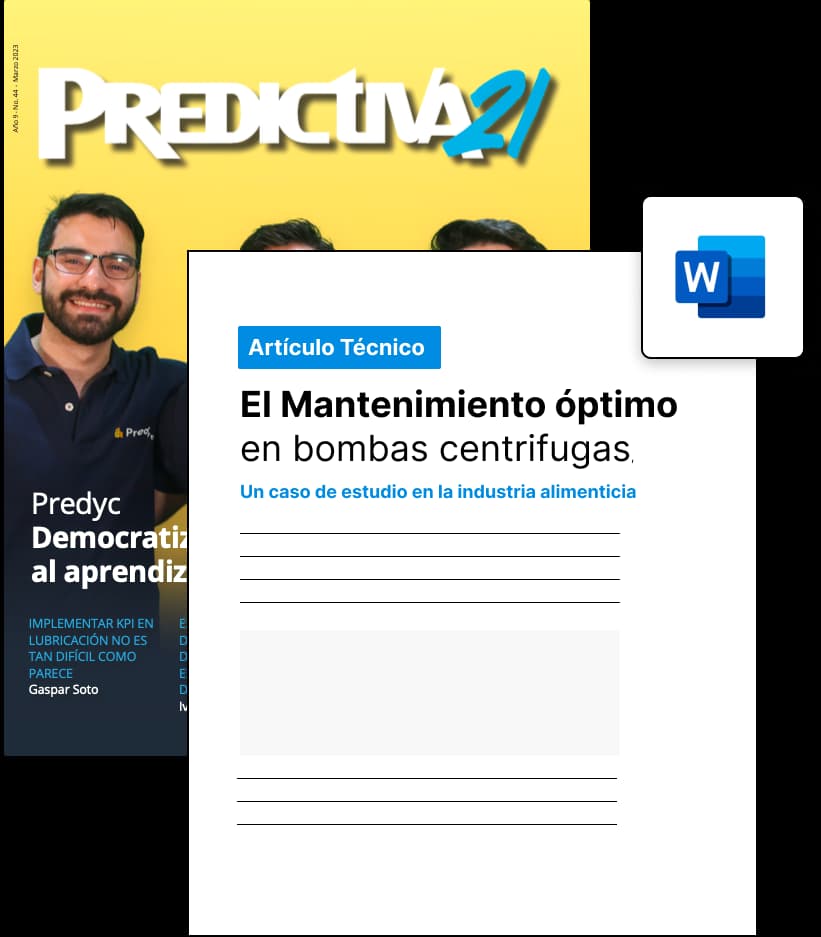