Modelos para la Excelencia Operativa
Libros>Reseña - Tienda12 de agosto de 2019
Sobre el libro

Haciendo del Sentido una Práctica Común: Modelos para la Excelencia Operativa (Making Common Sense Common Practice: Models for Operational Excellence) es un libro en inglés de 547 páginas, escrito por Ron Moore y publicado por la editorial Reliabilityweb.com en el año 2013 en su cuarta edición. También está disponible en Edición Kindle y pesa 6890 KB. El libro presenta modelos probados para lograr un rendimiento de clase mundial. Utilizando un estudio de caso de una compañía ficticia llamada Beta International, Moore ilustra cómo aumentar el tiempo de actividad, reducir los costos, aumentar la participación en el mercado, maximizar la utilización de activos, aplicar puntos de referencia y mejores prácticas, y mejorar muchos otros aspectos que finalmente elevan el desempeño de una compañía al nivel de clase mundial.
[su_button url="https://amzn.to/2MSSC9L" target="blank" style="soft" background="#e4c111" color="#000000" size="7" icon="icon: shopping-cart" icon_color="#000000" rel="nofollow"]Comprar en Amazon[/su_button]"Haciendo del Sentido una Práctica Común: Modelos para la Excelencia Operativa" analiza detenidamente el diseño de la planta, la adquisición, la gestión de piezas, la instalación y el mantenimiento, la capacitación y la implementación de un sistema de gestión de mantenimiento computarizado. Al analizar los éxitos y fracasos de los principales fabricantes del mundo, Moore describe un camino estable de crecimiento para casi cualquier empresa de fabricación. En los difíciles mercados competitivos de hoy en día, 'Hacer que el sentido común sea una práctica común' mejora en gran medida las posibilidades de éxito y ganancias de su empresa.
El libro cuenta con las siguientes características:
* Presenta actualizaciones más nuevas secciones sobre innovación, gestión de cambios y liderazgo.
* Presenta modelos probados para lograr un rendimiento de clase mundial basado en historias de casos reales.
* Altamente legible, el estilo concreto da vida a los puntos clave a través de un estudio de caso de una organización ficticia, Beta International, que se extiende a lo largo del libro, basado en historias de casos reales.
Sobre el autor
Ron Moore es socio gerente de The RM Group, Inc., y una autoridad reconocida internacionalmente sobre estrategias y prácticas para la fabricación y la excelencia operativa. Viaja por todo el mundo, generalmente trabajando con grandes empresas manufactureras e industriales en América del Norte y del Sur, Europa, Australia, África y Asia.
Antes de The RM Group, Ron se desempeñó durante cinco años como presidente de Computational Systems, Inc (CSI), un proveedor de tecnologías de monitoreo de condición de equipos industriales, principalmente instrumentos y software para monitoreo y análisis de vibraciones, aceite, infrarrojos y ultrasonidos de equipos industriales. condición. Durante su mandato, la compañía creció al 30% anual, mientras que al mismo tiempo mantenía ganancias saludables y una posición de efectivo, y un sólido balance. Antes de eso, trabajó para varias compañías que prestaron servicios a operaciones industriales y fabricantes, principalmente en centrales nucleares y fósiles, pero también diseñó submarinos nucleares. Tiene títulos de licenciatura y maestría en ingeniería mecánica de la Universidad de New Hampshire, un MBA de la Universidad de New Haven, y es un Profesional Certificado en Mantenimiento y Confiabilidad (Certified Maintenance and Reliability Professional).
Ron vive en Knoxville, Tennessee, con su esposa Kathy.
Contenido de "Haciendo del Sentido una Práctica Común: Modelos para la Excelencia Operativa"
- Contenido
- Expresiones de Gratitud
- Prefacio
- Fabricación y Excelencia Empresarial
- Puntos de Referencia, Cuellos de Botella y Mejores Prácticas
- Integrando las Estrategias de Marketing y Fabricación
- Diseño de Plantas y Prácticas de Proyectos de Capital
- Prácticas de AdquisiciónTiendas / Prácticas de Gestión de Piezas
- Prácticas de InstalaciónPrácticas Operacionales
- Prácticas de MantenimientoOptimizar el Proceso de Mantenimiento Preventivo
- Implementación de un Sistema de Gestión de Mantenimiento Computarizado
- Uso Efectivo de Contratistas en una Planta de FabricaciónMantenimiento Centrado Totalmente Productivo y de Confiabilidad
- Implementación de Procesos de Confiabilidad
- Liderazgo y Comportamiento Organizacional y Estructura
- Formación
- Medición del Desempeño
- Epílogo
- Apéndice A Clase-Mundial
- Fabricación - una Revisión de Varios Factores Clave de Éxito
- Índice
Fabricación y Excelencia Empresarial
A continuación se reproduce un extracto del primer capítulo del libro:
Sobre la Excelencia Empresarial
La excelencia empresarial en la mayoría de las empresas requiere que la empresa haga cada una de las tres cosas que se muestran en la Imagen 1 excepcionalmente bien: marketing, investigación y desarrollo (I + D) y fabricación. La excelencia en cada uno es esencial para el éxito a largo plazo, y cada uno debe estar completamente integrado con el otro. Cada uno debe reconocer ciertas áreas superpuestas donde se requiere el trabajo en equipo y la cooperación, y que todas las áreas deben estar completamente integradas con un sentido común de propósito: maximizar el rendimiento financiero de los accionistas.

Fuente: Making Common Sense Common Practice: Models for Operational Excellence by Ron Moore
Convertirse en un Productor de Bajo Costo
En la fabricación, casi siempre hay una mayor oferta que demanda, lo que requiere que una planta determinada se enfoque en convertirse en el productor de bajo costo de sus productos. Por supuesto, también hay otros diferenciadores del mercado, como la calidad del producto, el rendimiento de entrega, el servicio al cliente, la tecnología, etc., pero un indicador comercial clave es la capacidad de producir un producto de calidad al menor costo posible para un segmento de mercado específico. Esto ayuda a garantizar un mayor rendimiento de los activos para una mayor inversión en I + D, canales de comercialización y distribución, etc., para mejorar aún más el éxito comercial de una empresa.
Aplicación de Mayor Capacidad
La Imagen 2 proporciona una manera fácil de mapear el desempeño de fabricación con las condiciones del mercado y juzgar rápidamente su impacto en el desempeño financiero. Traza el rendimiento de los activos netos (o margen bruto / ganancias) en función del tiempo de actividad (y / o costos unitarios) para precios de mercado dados. Para este gráfico, la lógica es algo como esto. Para una planta determinada, puede determinar cuál es su tasa de utilización de activos actual o tiempo de actividad. Para ese tiempo de actividad, y cuando se combina con los costos operativos actuales, también puede determinar cuál es su costo unitario actual de producción para un conjunto de productos dado. Con una gran cantidad de productos, esto puede ser un poco más difícil, pero algunas empresas utilizan el concepto de unidades de producto equivalentes (UE) para este propósito.
Para un costo unitario dado, y en una determinada condición de mercado (precio), también podría determinar el beneficio bruto y, posteriormente, el rendimiento de los activos netos (RoNA). De hecho, para una familia de precios, puede determinar el tiempo de actividad requerido para lograr un determinado RoNA.

Fuente: Making Common Sense Common Practice: Models for Operational Excellence by Ron Moore
Un modelo para Convertirse en el Productor de Bajo Costo
Una estrategia de marketing es posicionarse estratégicamente con los clientes clave y ofrecer reducir modestamente los precios en los próximos años, a cambio de un nivel mínimo de negocios, reconociendo que el rendimiento de fabricación también debe mejorar para proporcionar un suministro confiable a esos clientes, y mejorar al mismo tiempo el RoNA .
Pasos hacia la excelencia de fabricación
Los pasos clave para que los gerentes operativos determinen lo que cada una de las plantas operativas deben hacer específicamente son los siguientes:
• El primer paso en el proceso de mejora es determinar dónde se encuentra en comparación con el mejor. ¿Cómo se compara con compañías de clase mundial, en tiempo de actividad, en costo unitario, en medidas puntuales / completas, por ejemplo? ¿Cómo se compara con las empresas típicas? Para hacer esto, debes hacer algunos benchmarking. Esto generalmente crea cierta disonancia cognitiva, o tensión positiva, porque crea una conciencia de cuán grandes son las brechas entre el rendimiento típico y el de clase mundial. Cuando se aplica correctamente, este conocimiento puede conducir a un mejor rendimiento.
• Luego, debes determinar dónde están tus pérdidas en comparación con las circunstancias ideales. Esto requiere un sistema que te permita realizar un seguimiento de cada hora en la que no estás operando a la velocidad ideal, y asignar una razón por la que no se realiza a la velocidad ideal. Esto puede usarse para el análisis de pérdidas clave y los pasos clave para eliminar esas pérdidas. Al implementar este sistema, si aún no tienes uno, puedes identificar las principales causas de pérdidas utilizando la técnica descrita en el Capítulo 2 del libro.
• Finalmente, debes comparar tus prácticas con las mejores prácticas. Ten en cuenta que esto difiere de los puntos de referencia o números. Las prácticas son lo que haces, no cómo mides. Las mejores empresas de fabricación se posicionan para diseñar, comprar, almacenar, instalar, operar y mantener sus activos para obtener el máximo tiempo de actividad y confiabilidad: confiabilidad del proceso de producción y confiabilidad de los equipos. Las mejores prácticas en cada una de estas áreas se describen en detalle en los capítulos del 4–13del libro. Además, las mejores plantas integran su estrategia de fabricación con su estrategia y plan de marketing, como se describe en el Capítulo 3 del libro. Considera la Imagen 3, que se refiere al proceso de confiabilidad para la excelencia de fabricación.

Fuente: Making Common Sense Common Practice: Models for Operational Excellence by Ron Moore
[su_button url="https://amzn.to/2MSSC9L" target="blank" style="soft" background="#e4c111" color="#000000" size="7" icon="icon: shopping-cart" icon_color="#000000" rel="nofollow"]Comprar en Amazon[/su_button]
Medición de Pérdidas del Ideal
La Imagen 4 ilustra una definición general del tiempo de actividad, la efectividad general del equipo (OEE) o la utilización de activos y las pérdidas relacionadas con el mismo.

Fuente: Making Common Sense Common Practice: Models for Operational Excellence by Ron Moore
Los términos en la Imagen 4 se definen de la siguiente manera:
• Tasa de Utilización de Activos: ese porcentaje de la tasa ideal a la que opera una planta en un período de tiempo determinado. El período de tiempo recomendado es de 8,760 horas por año, pero se puede definir como cualquier período, dependiendo de cómo se tratan las pérdidas del mercado.
• Tiempo de Actividad o Efectividad General del Equipo (OEE): ese porcentaje de la tasa ideal a la que opera una planta en un período de tiempo determinado, más el tiempo para pérdidas sin demanda del mercado.
• Utilización de Calidad: Es ese porcentaje de la tasa ideal a la que opera una planta en un período de tiempo determinado, más las pérdidas de demanda del mercado y las pérdidas por cambio y transición.
• Utilización de la Tasa Potencial: Es ese porcentaje de la tasa ideal a la que opera una planta en un período de tiempo determinado, más las pérdidas de demanda del mercado, las pérdidas de transición y transición, y las pérdidas de calidad.
• Disponibilidad: Es ese período de tiempo en que la planta está disponible para funcionar a cualquier ritmo.
Estos términos pueden ser confusos, dependiendo de la base de experiencia de cualquier individuo, de ahí el esfuerzo para definirlos. Por ejemplo, muchas personas se refieren al tiempo de actividad como cada vez que una línea o planta está en funcionamiento.
El objetivo con esta metodología es asegurar que "no hay lugar para ocultar" ninguna pérdida del ideal. Una vez que los tenemos en cuenta, podemos comenzar a administrarlos de manera integrada. De hecho, podemos encontrar que algunas de las llamadas "pérdidas" son completamente apropiadas y aseguran un rendimiento óptimo a largo plazo.
Además, la tasa máxima sostenible es, como su nombre lo indica, que la tasa máxima demostró ser sostenible durante un período prolongado.
Tiempo de Inactividad Programado y No Programado: Estos son normalmente, aunque incorrectamente como veremos, considerados la única responsabilidad del mantenimiento. El tiempo de inactividad no programado es típicamente para averías o mantenimiento reactivo. El tiempo de inactividad programado suele ser para mantenimiento preventivo o PM, así como para mantenimiento correctivo y / o planificado. Al respaldar las mediciones de excelencia empresarial, generalmente queremos eliminar, o al menos minimizar, el tiempo de inactividad no programado; y queremos optimizar (minimizar para un efecto u objetivo determinado) el tiempo de inactividad programado utilizando un proceso de optimización de PM (Capítulos 9 y 10 del libro) que combina métodos preventivos, predictivos y proactivos con el historial del equipo y el conocimiento de la condición actual para asegurar que se haga solo lo que es necesario, cuando es necesario. Restar estos tiempos produce disponibilidad real.
Pérdidas de Tasa de Proceso. En general, se trata de pérdidas que ocurren cuando el proceso no funciona de manera ideal, por ejemplo, tasas de proceso de producción inferiores al ideal, tiempos de ciclo superiores al tiempo ideal, rendimientos inferiores al ideal, etc.
Pérdidas de Calidad. Por lo general, se trata de pérdidas debido a que la calidad del producto no cumple con las especificaciones, lo que resulta en chatarra o reelaboración. También puede ser el resultado de un mal diseño, prácticas operativas o de mantenimiento, o alguna combinación.
Pérdidas de Transición / Transición. Estos incluyen pérdidas por tiempo de inactividad, pérdidas por disminución y / o pérdidas de calidad del producto que ocurren durante un cambio o transición a un nuevo producto, tanto las pérdidas por cierre del producto existente, como las pérdidas de inicio por el nuevo producto. Minimizar las pérdidas de transición y transición ayudará a minimizar los costos de fabricación.
Sin Demanda y Pérdidas del Mercado. Estos generalmente se refieren a las pérdidas asociadas con la falta de demanda del mercado. El personal de fabricación tiene poca influencia a corto plazo en la demanda del mercado. Sin embargo, es fundamental para el éxito a largo plazo de la empresa destacar este equipo y la disponibilidad de procesos para la toma de decisiones estratégicas con respecto a la obtención de una participación de mercado adicional, nuevos requisitos de capital y / o para la racionalización de la capacidad.
Cursos recomendados






%252FImagen%252FRAMPREDYC-1730060420837.webp%3Falt%3Dmedia%26token%3D2634a7f0-988e-4022-b91f-382503e6e9db&w=3840&q=75)

Lean Manufacturing, Six Sigma y Fábricas Enfocadas
En los últimos años, Lean Manufacturing, Focused and Agile Factories y Six Sigma Methods han llegado a la vanguardia como modelos para la excelencia en la fabricación. A continuación hay una discusión de estos principios o métodos.
Lean Manufacturing
Lean Manufacturing es más una filosofía o condición que un proceso. Por ejemplo, cuando eres lean o tienes una producción limpia, tú:
- Tienes un inventario mínimo, WIP y materia prima.
- Tienes un alto rendimiento en la entrega a tiempo.
- Por lo general, estás operando en un modo "pull": solo ganas lo suficiente para satisfacer la demanda a corto plazo.
- Haces lotes más pequeños y tienes menos carreras más largas (un poco contra-intuitivo).
Y usas técnicas tales como:
- Flujo de una pieza, cambio rápido, takt time10 y prueba de errores.
- Medir los tiempos de ciclo del sistema y los tiempos de retraso, y gestionarlos de manera más efectiva.
- Minimizar la variabilidad de sus procesos.
- Tener equipos muy confiables a través del mantenimiento proactivo.
Six Sigma
Six Sigma es un término estadístico que caracteriza su calidad con menos de 3.4 defectos por millón para un producto determinado o especificación de proceso. Sin embargo, Six Sigma se ha convertido en una metodología para reducir la variabilidad de los procesos de modo que el resultado sea una mayor calidad y consistencia. Destaca simultáneamente el logro de objetivos aparentemente contrarios:
- Ser estable e innovador.
- Ver el panorama general y los detalles.
- Ser creativo y racional.
Similar al "plan, hacer, verificar, actuar" de Deming, aplica el modelo DMAIC —definir, medir, analizar, mejorar, controlar— a los procesos centrales y clientes clave.
Los temas principales incluyen:
- Centrarse en la satisfacción / éxito del cliente.
- Gestión basada en datos / hechos.
- Gestión y mejora de procesos.
- Gestión proactiva.
- Colaboración sin límites.
- Impulsar la perfección, pero la tolerancia al fracaso.
Las principales herramientas / métodos incluyen:
- Mejora Continua.
- Gestión de Proceso.
- Diseño de Procesos / Rediseño.
- Comentarios de los Clientes.
- Pensamiento Creativo.
- Análisis de Variación.
- Cuadros de Mando Equilibrados.
- Diseño de Experimentos.
- Control del Proceso Estadístico.
- Proyectos de Mejora.
Fábricas Enfocadas (Focused and Agile Factories)
El concepto de fábricas enfocadas también se ha ofrecido como una estrategia para asegurar la excelencia en la fabricación. La opinión de algunos defensores de fábricas enfocadas en que contar con maquinaria y equipo de respaldo es una solución a los problemas de capacidad y producción, no parece estar bien fundada. Normalmente, el equipo adicional no es la solución para las malas prácticas de mantenimiento, ya que aumenta la necesidad de capital adicional, así como los gastos de operación y mantenimiento, etc. Llegar a la causa raíz de las fallas del equipo y mejorar las prácticas de mantenimiento es un enfoque mucho mejor.
Sumario
El desempeño comercial de clase mundial requiere excelencia e integración del marketing, la fabricación y la I + D, y sabemos qué es la excelencia al medirla; requiere que sepamos lo que significa ser el productor de bajo costo de nuestros productos, y cómo lograr y mantener esa posición; requiere que comprendamos cómo nuestro desempeño de fabricación se relaciona con nuestro retorno sobre los activos netos y el desempeño corporativo general; requiere que comprendamos nuestras pérdidas desde el ideal y las gestionemos; requiere que establezcamos un proceso de confiabilidad para la fabricación que asegure que diseñamos, compramos, almacenamos, instalamos, operamos y mantenemos nuestros activos de fabricación de una manera excelente. Finalmente, requiere que integremos nuestra estrategia de comercialización y fabricación de manera integral, centrada en un rendimiento de clase mundial.
Nota de la editorial: En todas las cuestiones relativas al sentido, los textos originales en inglés citados en esta entrada tienen validez última.
[su_button url="https://amzn.to/2MSSC9L" target="blank" style="soft" background="#e4c111" color="#000000" size="7" icon="icon: shopping-cart" icon_color="#000000" rel="nofollow"]Comprar en Amazon[/su_button]Más libros
Dinos qué te ha parecido el artículo
Artículos recomendados
Las Claves del Éxito de Toyota - Jeffrey K. Liker

El Manual del Ingeniero de Confiabilidad Certificado (Mark Allen Durivage)

Confiabilidad en la Ingeniería Automotriz y Mecánica: Determinación de los Componentes y de la Confiabilidad del sistema

Modelos para la Excelencia Operativa

Publica tu artículo en la revista #1 de Mantenimiento Industrial
Publicar un artículo en la revista es gratis, no tiene costo.
Solo debes asegurarte que no sea un artículo comercial.
¿Qué esperas?
O envía tu artículo directo: articulos@predictiva21.com
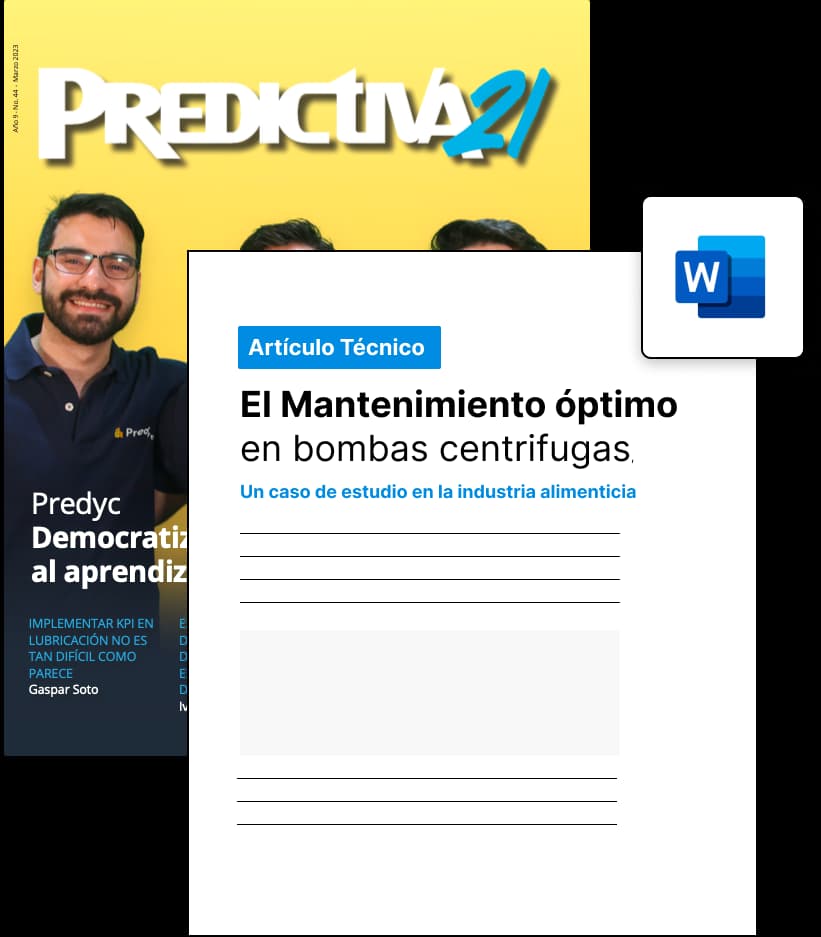
Modelos para la Excelencia Operativa
Libros>Reseña - Tienda 12 de agosto de 2019Sobre el libro

Haciendo del Sentido una Práctica Común: Modelos para la Excelencia Operativa (Making Common Sense Common Practice: Models for Operational Excellence) es un libro en inglés de 547 páginas, escrito por Ron Moore y publicado por la editorial Reliabilityweb.com en el año 2013 en su cuarta edición. También está disponible en Edición Kindle y pesa 6890 KB. El libro presenta modelos probados para lograr un rendimiento de clase mundial. Utilizando un estudio de caso de una compañía ficticia llamada Beta International, Moore ilustra cómo aumentar el tiempo de actividad, reducir los costos, aumentar la participación en el mercado, maximizar la utilización de activos, aplicar puntos de referencia y mejores prácticas, y mejorar muchos otros aspectos que finalmente elevan el desempeño de una compañía al nivel de clase mundial.
[su_button url="https://amzn.to/2MSSC9L" target="blank" style="soft" background="#e4c111" color="#000000" size="7" icon="icon: shopping-cart" icon_color="#000000" rel="nofollow"]Comprar en Amazon[/su_button]"Haciendo del Sentido una Práctica Común: Modelos para la Excelencia Operativa" analiza detenidamente el diseño de la planta, la adquisición, la gestión de piezas, la instalación y el mantenimiento, la capacitación y la implementación de un sistema de gestión de mantenimiento computarizado. Al analizar los éxitos y fracasos de los principales fabricantes del mundo, Moore describe un camino estable de crecimiento para casi cualquier empresa de fabricación. En los difíciles mercados competitivos de hoy en día, 'Hacer que el sentido común sea una práctica común' mejora en gran medida las posibilidades de éxito y ganancias de su empresa.
El libro cuenta con las siguientes características:
* Presenta actualizaciones más nuevas secciones sobre innovación, gestión de cambios y liderazgo.
* Presenta modelos probados para lograr un rendimiento de clase mundial basado en historias de casos reales.
* Altamente legible, el estilo concreto da vida a los puntos clave a través de un estudio de caso de una organización ficticia, Beta International, que se extiende a lo largo del libro, basado en historias de casos reales.
Sobre el autor
Ron Moore es socio gerente de The RM Group, Inc., y una autoridad reconocida internacionalmente sobre estrategias y prácticas para la fabricación y la excelencia operativa. Viaja por todo el mundo, generalmente trabajando con grandes empresas manufactureras e industriales en América del Norte y del Sur, Europa, Australia, África y Asia.
Antes de The RM Group, Ron se desempeñó durante cinco años como presidente de Computational Systems, Inc (CSI), un proveedor de tecnologías de monitoreo de condición de equipos industriales, principalmente instrumentos y software para monitoreo y análisis de vibraciones, aceite, infrarrojos y ultrasonidos de equipos industriales. condición. Durante su mandato, la compañía creció al 30% anual, mientras que al mismo tiempo mantenía ganancias saludables y una posición de efectivo, y un sólido balance. Antes de eso, trabajó para varias compañías que prestaron servicios a operaciones industriales y fabricantes, principalmente en centrales nucleares y fósiles, pero también diseñó submarinos nucleares. Tiene títulos de licenciatura y maestría en ingeniería mecánica de la Universidad de New Hampshire, un MBA de la Universidad de New Haven, y es un Profesional Certificado en Mantenimiento y Confiabilidad (Certified Maintenance and Reliability Professional).
Ron vive en Knoxville, Tennessee, con su esposa Kathy.
Contenido de "Haciendo del Sentido una Práctica Común: Modelos para la Excelencia Operativa"
- Contenido
- Expresiones de Gratitud
- Prefacio
- Fabricación y Excelencia Empresarial
- Puntos de Referencia, Cuellos de Botella y Mejores Prácticas
- Integrando las Estrategias de Marketing y Fabricación
- Diseño de Plantas y Prácticas de Proyectos de Capital
- Prácticas de AdquisiciónTiendas / Prácticas de Gestión de Piezas
- Prácticas de InstalaciónPrácticas Operacionales
- Prácticas de MantenimientoOptimizar el Proceso de Mantenimiento Preventivo
- Implementación de un Sistema de Gestión de Mantenimiento Computarizado
- Uso Efectivo de Contratistas en una Planta de FabricaciónMantenimiento Centrado Totalmente Productivo y de Confiabilidad
- Implementación de Procesos de Confiabilidad
- Liderazgo y Comportamiento Organizacional y Estructura
- Formación
- Medición del Desempeño
- Epílogo
- Apéndice A Clase-Mundial
- Fabricación - una Revisión de Varios Factores Clave de Éxito
- Índice
Fabricación y Excelencia Empresarial
A continuación se reproduce un extracto del primer capítulo del libro:
Sobre la Excelencia Empresarial
La excelencia empresarial en la mayoría de las empresas requiere que la empresa haga cada una de las tres cosas que se muestran en la Imagen 1 excepcionalmente bien: marketing, investigación y desarrollo (I + D) y fabricación. La excelencia en cada uno es esencial para el éxito a largo plazo, y cada uno debe estar completamente integrado con el otro. Cada uno debe reconocer ciertas áreas superpuestas donde se requiere el trabajo en equipo y la cooperación, y que todas las áreas deben estar completamente integradas con un sentido común de propósito: maximizar el rendimiento financiero de los accionistas.

Fuente: Making Common Sense Common Practice: Models for Operational Excellence by Ron Moore
Convertirse en un Productor de Bajo Costo
En la fabricación, casi siempre hay una mayor oferta que demanda, lo que requiere que una planta determinada se enfoque en convertirse en el productor de bajo costo de sus productos. Por supuesto, también hay otros diferenciadores del mercado, como la calidad del producto, el rendimiento de entrega, el servicio al cliente, la tecnología, etc., pero un indicador comercial clave es la capacidad de producir un producto de calidad al menor costo posible para un segmento de mercado específico. Esto ayuda a garantizar un mayor rendimiento de los activos para una mayor inversión en I + D, canales de comercialización y distribución, etc., para mejorar aún más el éxito comercial de una empresa.
Aplicación de Mayor Capacidad
La Imagen 2 proporciona una manera fácil de mapear el desempeño de fabricación con las condiciones del mercado y juzgar rápidamente su impacto en el desempeño financiero. Traza el rendimiento de los activos netos (o margen bruto / ganancias) en función del tiempo de actividad (y / o costos unitarios) para precios de mercado dados. Para este gráfico, la lógica es algo como esto. Para una planta determinada, puede determinar cuál es su tasa de utilización de activos actual o tiempo de actividad. Para ese tiempo de actividad, y cuando se combina con los costos operativos actuales, también puede determinar cuál es su costo unitario actual de producción para un conjunto de productos dado. Con una gran cantidad de productos, esto puede ser un poco más difícil, pero algunas empresas utilizan el concepto de unidades de producto equivalentes (UE) para este propósito.
Para un costo unitario dado, y en una determinada condición de mercado (precio), también podría determinar el beneficio bruto y, posteriormente, el rendimiento de los activos netos (RoNA). De hecho, para una familia de precios, puede determinar el tiempo de actividad requerido para lograr un determinado RoNA.

Fuente: Making Common Sense Common Practice: Models for Operational Excellence by Ron Moore
Un modelo para Convertirse en el Productor de Bajo Costo
Una estrategia de marketing es posicionarse estratégicamente con los clientes clave y ofrecer reducir modestamente los precios en los próximos años, a cambio de un nivel mínimo de negocios, reconociendo que el rendimiento de fabricación también debe mejorar para proporcionar un suministro confiable a esos clientes, y mejorar al mismo tiempo el RoNA .
Pasos hacia la excelencia de fabricación
Los pasos clave para que los gerentes operativos determinen lo que cada una de las plantas operativas deben hacer específicamente son los siguientes:
• El primer paso en el proceso de mejora es determinar dónde se encuentra en comparación con el mejor. ¿Cómo se compara con compañías de clase mundial, en tiempo de actividad, en costo unitario, en medidas puntuales / completas, por ejemplo? ¿Cómo se compara con las empresas típicas? Para hacer esto, debes hacer algunos benchmarking. Esto generalmente crea cierta disonancia cognitiva, o tensión positiva, porque crea una conciencia de cuán grandes son las brechas entre el rendimiento típico y el de clase mundial. Cuando se aplica correctamente, este conocimiento puede conducir a un mejor rendimiento.
• Luego, debes determinar dónde están tus pérdidas en comparación con las circunstancias ideales. Esto requiere un sistema que te permita realizar un seguimiento de cada hora en la que no estás operando a la velocidad ideal, y asignar una razón por la que no se realiza a la velocidad ideal. Esto puede usarse para el análisis de pérdidas clave y los pasos clave para eliminar esas pérdidas. Al implementar este sistema, si aún no tienes uno, puedes identificar las principales causas de pérdidas utilizando la técnica descrita en el Capítulo 2 del libro.
• Finalmente, debes comparar tus prácticas con las mejores prácticas. Ten en cuenta que esto difiere de los puntos de referencia o números. Las prácticas son lo que haces, no cómo mides. Las mejores empresas de fabricación se posicionan para diseñar, comprar, almacenar, instalar, operar y mantener sus activos para obtener el máximo tiempo de actividad y confiabilidad: confiabilidad del proceso de producción y confiabilidad de los equipos. Las mejores prácticas en cada una de estas áreas se describen en detalle en los capítulos del 4–13del libro. Además, las mejores plantas integran su estrategia de fabricación con su estrategia y plan de marketing, como se describe en el Capítulo 3 del libro. Considera la Imagen 3, que se refiere al proceso de confiabilidad para la excelencia de fabricación.

Fuente: Making Common Sense Common Practice: Models for Operational Excellence by Ron Moore
[su_button url="https://amzn.to/2MSSC9L" target="blank" style="soft" background="#e4c111" color="#000000" size="7" icon="icon: shopping-cart" icon_color="#000000" rel="nofollow"]Comprar en Amazon[/su_button]
Medición de Pérdidas del Ideal
La Imagen 4 ilustra una definición general del tiempo de actividad, la efectividad general del equipo (OEE) o la utilización de activos y las pérdidas relacionadas con el mismo.

Fuente: Making Common Sense Common Practice: Models for Operational Excellence by Ron Moore
Los términos en la Imagen 4 se definen de la siguiente manera:
• Tasa de Utilización de Activos: ese porcentaje de la tasa ideal a la que opera una planta en un período de tiempo determinado. El período de tiempo recomendado es de 8,760 horas por año, pero se puede definir como cualquier período, dependiendo de cómo se tratan las pérdidas del mercado.
• Tiempo de Actividad o Efectividad General del Equipo (OEE): ese porcentaje de la tasa ideal a la que opera una planta en un período de tiempo determinado, más el tiempo para pérdidas sin demanda del mercado.
• Utilización de Calidad: Es ese porcentaje de la tasa ideal a la que opera una planta en un período de tiempo determinado, más las pérdidas de demanda del mercado y las pérdidas por cambio y transición.
• Utilización de la Tasa Potencial: Es ese porcentaje de la tasa ideal a la que opera una planta en un período de tiempo determinado, más las pérdidas de demanda del mercado, las pérdidas de transición y transición, y las pérdidas de calidad.
• Disponibilidad: Es ese período de tiempo en que la planta está disponible para funcionar a cualquier ritmo.
Estos términos pueden ser confusos, dependiendo de la base de experiencia de cualquier individuo, de ahí el esfuerzo para definirlos. Por ejemplo, muchas personas se refieren al tiempo de actividad como cada vez que una línea o planta está en funcionamiento.
El objetivo con esta metodología es asegurar que "no hay lugar para ocultar" ninguna pérdida del ideal. Una vez que los tenemos en cuenta, podemos comenzar a administrarlos de manera integrada. De hecho, podemos encontrar que algunas de las llamadas "pérdidas" son completamente apropiadas y aseguran un rendimiento óptimo a largo plazo.
Además, la tasa máxima sostenible es, como su nombre lo indica, que la tasa máxima demostró ser sostenible durante un período prolongado.
Tiempo de Inactividad Programado y No Programado: Estos son normalmente, aunque incorrectamente como veremos, considerados la única responsabilidad del mantenimiento. El tiempo de inactividad no programado es típicamente para averías o mantenimiento reactivo. El tiempo de inactividad programado suele ser para mantenimiento preventivo o PM, así como para mantenimiento correctivo y / o planificado. Al respaldar las mediciones de excelencia empresarial, generalmente queremos eliminar, o al menos minimizar, el tiempo de inactividad no programado; y queremos optimizar (minimizar para un efecto u objetivo determinado) el tiempo de inactividad programado utilizando un proceso de optimización de PM (Capítulos 9 y 10 del libro) que combina métodos preventivos, predictivos y proactivos con el historial del equipo y el conocimiento de la condición actual para asegurar que se haga solo lo que es necesario, cuando es necesario. Restar estos tiempos produce disponibilidad real.
Pérdidas de Tasa de Proceso. En general, se trata de pérdidas que ocurren cuando el proceso no funciona de manera ideal, por ejemplo, tasas de proceso de producción inferiores al ideal, tiempos de ciclo superiores al tiempo ideal, rendimientos inferiores al ideal, etc.
Pérdidas de Calidad. Por lo general, se trata de pérdidas debido a que la calidad del producto no cumple con las especificaciones, lo que resulta en chatarra o reelaboración. También puede ser el resultado de un mal diseño, prácticas operativas o de mantenimiento, o alguna combinación.
Pérdidas de Transición / Transición. Estos incluyen pérdidas por tiempo de inactividad, pérdidas por disminución y / o pérdidas de calidad del producto que ocurren durante un cambio o transición a un nuevo producto, tanto las pérdidas por cierre del producto existente, como las pérdidas de inicio por el nuevo producto. Minimizar las pérdidas de transición y transición ayudará a minimizar los costos de fabricación.
Sin Demanda y Pérdidas del Mercado. Estos generalmente se refieren a las pérdidas asociadas con la falta de demanda del mercado. El personal de fabricación tiene poca influencia a corto plazo en la demanda del mercado. Sin embargo, es fundamental para el éxito a largo plazo de la empresa destacar este equipo y la disponibilidad de procesos para la toma de decisiones estratégicas con respecto a la obtención de una participación de mercado adicional, nuevos requisitos de capital y / o para la racionalización de la capacidad.
Cursos recomendados






%252FImagen%252FRAMPREDYC-1730060420837.webp%3Falt%3Dmedia%26token%3D2634a7f0-988e-4022-b91f-382503e6e9db&w=3840&q=75)

Lean Manufacturing, Six Sigma y Fábricas Enfocadas
En los últimos años, Lean Manufacturing, Focused and Agile Factories y Six Sigma Methods han llegado a la vanguardia como modelos para la excelencia en la fabricación. A continuación hay una discusión de estos principios o métodos.
Lean Manufacturing
Lean Manufacturing es más una filosofía o condición que un proceso. Por ejemplo, cuando eres lean o tienes una producción limpia, tú:
- Tienes un inventario mínimo, WIP y materia prima.
- Tienes un alto rendimiento en la entrega a tiempo.
- Por lo general, estás operando en un modo "pull": solo ganas lo suficiente para satisfacer la demanda a corto plazo.
- Haces lotes más pequeños y tienes menos carreras más largas (un poco contra-intuitivo).
Y usas técnicas tales como:
- Flujo de una pieza, cambio rápido, takt time10 y prueba de errores.
- Medir los tiempos de ciclo del sistema y los tiempos de retraso, y gestionarlos de manera más efectiva.
- Minimizar la variabilidad de sus procesos.
- Tener equipos muy confiables a través del mantenimiento proactivo.
Six Sigma
Six Sigma es un término estadístico que caracteriza su calidad con menos de 3.4 defectos por millón para un producto determinado o especificación de proceso. Sin embargo, Six Sigma se ha convertido en una metodología para reducir la variabilidad de los procesos de modo que el resultado sea una mayor calidad y consistencia. Destaca simultáneamente el logro de objetivos aparentemente contrarios:
- Ser estable e innovador.
- Ver el panorama general y los detalles.
- Ser creativo y racional.
Similar al "plan, hacer, verificar, actuar" de Deming, aplica el modelo DMAIC —definir, medir, analizar, mejorar, controlar— a los procesos centrales y clientes clave.
Los temas principales incluyen:
- Centrarse en la satisfacción / éxito del cliente.
- Gestión basada en datos / hechos.
- Gestión y mejora de procesos.
- Gestión proactiva.
- Colaboración sin límites.
- Impulsar la perfección, pero la tolerancia al fracaso.
Las principales herramientas / métodos incluyen:
- Mejora Continua.
- Gestión de Proceso.
- Diseño de Procesos / Rediseño.
- Comentarios de los Clientes.
- Pensamiento Creativo.
- Análisis de Variación.
- Cuadros de Mando Equilibrados.
- Diseño de Experimentos.
- Control del Proceso Estadístico.
- Proyectos de Mejora.
Fábricas Enfocadas (Focused and Agile Factories)
El concepto de fábricas enfocadas también se ha ofrecido como una estrategia para asegurar la excelencia en la fabricación. La opinión de algunos defensores de fábricas enfocadas en que contar con maquinaria y equipo de respaldo es una solución a los problemas de capacidad y producción, no parece estar bien fundada. Normalmente, el equipo adicional no es la solución para las malas prácticas de mantenimiento, ya que aumenta la necesidad de capital adicional, así como los gastos de operación y mantenimiento, etc. Llegar a la causa raíz de las fallas del equipo y mejorar las prácticas de mantenimiento es un enfoque mucho mejor.
Sumario
El desempeño comercial de clase mundial requiere excelencia e integración del marketing, la fabricación y la I + D, y sabemos qué es la excelencia al medirla; requiere que sepamos lo que significa ser el productor de bajo costo de nuestros productos, y cómo lograr y mantener esa posición; requiere que comprendamos cómo nuestro desempeño de fabricación se relaciona con nuestro retorno sobre los activos netos y el desempeño corporativo general; requiere que comprendamos nuestras pérdidas desde el ideal y las gestionemos; requiere que establezcamos un proceso de confiabilidad para la fabricación que asegure que diseñamos, compramos, almacenamos, instalamos, operamos y mantenemos nuestros activos de fabricación de una manera excelente. Finalmente, requiere que integremos nuestra estrategia de comercialización y fabricación de manera integral, centrada en un rendimiento de clase mundial.
Nota de la editorial: En todas las cuestiones relativas al sentido, los textos originales en inglés citados en esta entrada tienen validez última.
[su_button url="https://amzn.to/2MSSC9L" target="blank" style="soft" background="#e4c111" color="#000000" size="7" icon="icon: shopping-cart" icon_color="#000000" rel="nofollow"]Comprar en Amazon[/su_button]Más libros
Dinos qué te ha parecido el artículo
Artículos recomendados
Evaluación Comparativa de Mejores Prácticas - Terry Wireman

Confiabilidad Aplicada

Confiabilidad en la Ingeniería Automotriz y Mecánica: Determinación de los Componentes y de la Confiabilidad del sistema

Ingeniería de Confiabilidad y Análisis de Riesgos: una Guía Práctica

Publica tu artículo en la revista #1 de Mantenimiento Industrial
Publicar un artículo en la revista es gratis, no tiene costo.
Solo debes asegurarte que no sea un artículo comercial.
¿Qué esperas?
O envía tu artículo directo: articulos@predictiva21.com
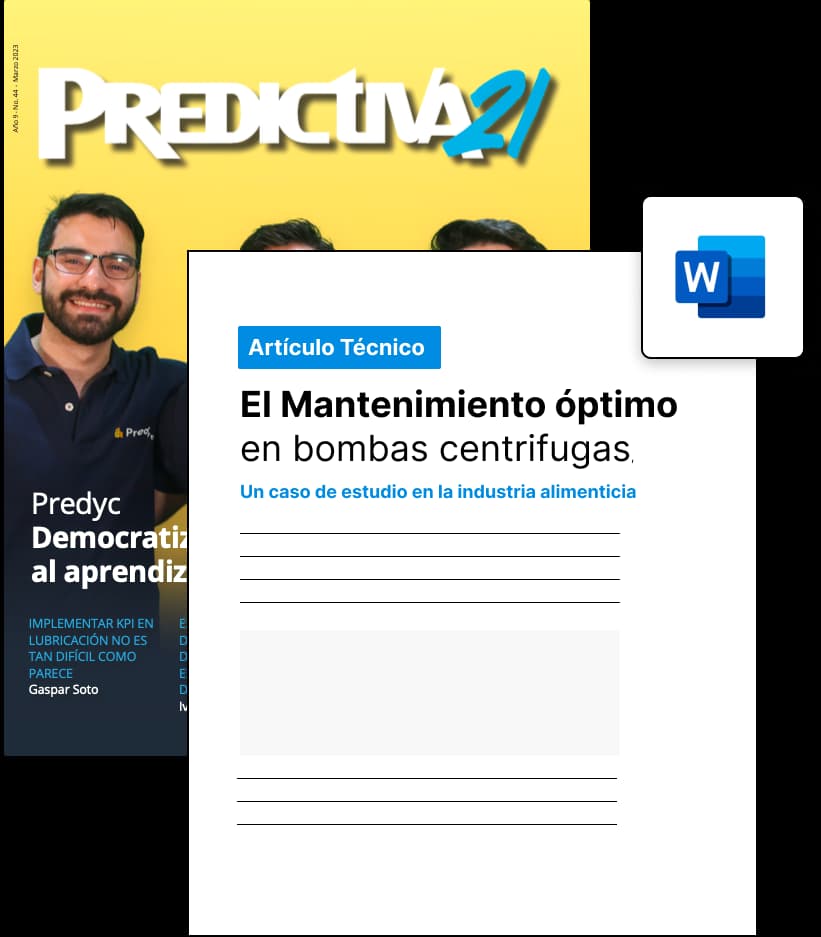