Detección de Fugas Internas en Válvulas Mediante la Técnica De Ultrasonido (II Parte)
Articulo8 de enero de 2020
Introducción
Las válvulas son dispositivos de control de flujo utilizados en todo tipo de industrias (petroquímica, energía, alimentación, papel, minería, etc.) Existen multitud de tipos, configuraciones y tamaños diseñados según las necesidades concretas de los procesos en que se integran.
Dependiendo del régimen de funcionamiento y las condiciones de operación e instalación, una válvula puede fallar de diversos modos: acumulación de suciedad o depósitos en obturador y asientos, ejes doblados o rotos, fugas en empaquetaduras, rotura de juntas, corrosión y erosión en cuerpo, fallos en dispositivos actuadores o de control, etc. Centrándonos en el caso de las fugas internas, la detección de este tipo de problemas puede suponer un ahorro significativo de costes asociados a paradas de emergencia, pérdidas de producción, disminución de la eficiencia energética e impacto ambiental.
Estudios de campo han demostrado que entre el 5 y el 10% de las válvulas de cualquier instalación industrial presentan alguna sintomatología relacionada con fugas internas. Por ejemplo, las válvulas que manejan vapor y presentan fugas pueden ocasionar considerables pérdidas de energía traducidas en costes elevados. Ni que decir tiene la importancia en el caso de instalaciones que procesan fluidos tóxicos, radiactivos, explosivos, combustibles o corrosivos y que supongan un riesgo para la integridad de las personas, las instalaciones o el medio ambiente. Por tanto, eliminar o minimizar estas fugas ha de ser considerado como un objetivo prioritario en empresas que basan su filosofía de mantenimiento en el seguimiento de la condición de sus activos.
Continuación
Ensayo indeterminado
En ocasiones, la presencia de ruido de fondo impide diagnosticar adecuadamente una válvula, bien porque enmascare el ultrasonido generado por la propia fuga o bien por la alta intensidad del mismo que impide llegar a conclusiones acertadas. En estos casos puede resultar útil modificar los filtros del equipo de ultrasonidos a fin de despreciar determinados rangos de frecuencias, pero por lo general es un problema insalvable que se convierte en una de las limitaciones propias de esta técnica.

Selección de los puntos de inspección
El método ABCD se puede complementar con medidas adicionales (E,F,…) en diferentes puntos de la válvula, en función del tipo y dimensiones. El disponer de lecturas complementarias permite realizar un diagnóstico más preciso.


Consideraciones adicionales
Selección de la frecuencia
En la mayoría de los casos, las señales ultrasónicas generadas por una fuga tienen un amplio rango de frecuencias que, sumadas, constituyen el típico ruido blanco característico de una fuga y, en ocasiones, de mayor intensidad que cualquier componente audible presente. Muy pocas veces una fuga particular suele tener una frecuencia característica tanto en el dominio audible como en el ultrasónico. Es muy difícil predecir la respuesta en frecuencia de una válvula en particular para una fuga en particular. Factores como la dimensión, forma de cuerpo y asientos, obturador, tipo de fluido, viscosidad, área de paso, caída de presión, etc. influyen en la respuesta final.
No obstante, los equipos de ultrasonidos modernos permiten seleccionar la frecuencia de corte, e incluso rangos de frecuencias, a fin de discriminar información de escaso interés.

Selección del sensor
Es muy útil utilizar en un principio el sensor magnético en aquellas válvulas donde sea posible debido a su alta sensibilidad, facilidad de uso y mejora de la repetitividad. Si los resultados obtenidos no son convincentes, utilizar el módulo de contacto para una inspección más amplia. No obstante, la presión ejercida en el punto de medida así como el ángulo de incidencia en el caso de los módulos de contacto de varilla pueden alterar la lectura final.

Circuitos de alta presión
Los sistemas que trabajan a altas presiones producen intensos niveles de ultrasonido que se propaga con facilidad por las estructuras (tuberías, soportes, válvulas, depósitos, etc.) En estos casos pudiera ser complejo determinar la presencia de una fuga interna en una válvula, ya que el nivel de fondo de ultrasonido es muy elevado en comparación con el generado por la fuga. La experiencia del operador y el método comparativo ABCD es el más recomendable en esta situación.
Consideraciones finales
- Es recomendable que los puntos ABCD tengan secciones similares (mismo o similar DN) En caso contrario, es la experiencia del inspector y el registro de datos históricos el mejor indicador del estado de la válvula.
- Tener en cuenta el sentido del flujo para aplicar adecuadamente el método ABCD.
- Verificar que la válvula está realmente cerrada y que no procede ruido audible de la misma. Si tal fuera el caso, no sería necesaria la inspección ultrasónica. De hecho, en grandes fugas pudiera haber una baja intensidad de ultrasonidos.
- Procurar inspeccionar con el módulo de contacto ejerciendo siempre la misma presión y ángulo sobre el punto a inspeccionar. La variación de los mismos provoca modificaciones en las lecturas y dificulta la repetitividad de las medidas. Si se dispone, utilizar un módulo magnético.
- Es muy importante por parte del inspector, familiarizarse con los sonidos procedentes de válvulas en buen y mal estado.
- En la medida de lo posible, las inspecciones las ha de realizar el mismo operador.
- Ajustar los valores de sensibilidad y frecuencia a fin de obtener un sonido “limpio” libre de ruidos procedentes de otras fuentes competidoras.
- Comparar válvulas similares adyacentes.
- Registrar la presión de trabajo y temperatura de proceso en el momento de la inspección, pues condicionará los resultados en caso de variaciones.
- Tener en cuenta que la viscosidad y densidad del fluido, dependientes de su temperatura, influyen en la turbulencia del fluido en las zonas de fuga.
- Conocer el proceso y las posibles fuentes de ultrasonido competidor.
- Anotar todos los resultados y observaciones adicionales en la hoja de campo.
- Realizar las inspecciones siempre en los mismos puntos.
- Prestar atención a todas las recomendaciones de seguridad (fluidos peligrosos, salpicaduras, contacto con temperaturas extremas, gases, etc).
- Identificar la válvula problemática en campo con una etiqueta.
- Realizar una inspección visual de la válvula una vez diagnosticada para corroborar los hallazgos.
Es especialmente necesario tomar las precauciones de seguridad necesarias a la hora de inspeccionar válvulas que operan a altas temperaturas o con fluidos peligrosos, no solo por los riesgos a que se ve expuesto el operador sino por el hecho de que pueden afectar o dañar la electrónica del equipo.
Por otro lado, hay multitud de mecanismos adicionales que condicionan la forma en que una válvula con fugas genera ruido ultrasónico: tipo de degradación de la zona de cierre, resonancias estructurales, ultrasonido de procesos próximos, etc. Como ya se ha indicado, la técnica se puede complicar cuando se trata de inspeccionar sistemas hidráulicos o redes de vapor debido al alto ruido de fondo.
Estimación del caudal de fuga y pérdidas económicas
Los equipos de detección de ultrasonidos no se fabrican siguiendo un estándar mundial, por lo que determinadas características de diseño de los mismos, como la sensibilidad, son propios de cada fabricante. Por este motivo, tampoco es posible establecer con facilidad una metodología de cálculo de los caudales de fuga en función del ruido ultrasónico de la válvula. Algunos fabricantes, basándose en su propia experiencia y en datos empíricos han creado algoritmos para la estimación de los flujos de fuga y las pérdidas económicas asociadas a los mismos. No obstante, sí se puede afirmar que cuanto mayor sea el diferencial de amplitud en dB en la zona de cierre de la válvula con respecto a otros puntos de la misma, tanto mas severa será la fuga.

Como cabe esperar, la detección y la cuantificación de las fugas puede conducir a ahorros significativos, maximización de la eficiencia de la planta y protección del medio ambiente así como una mejora sustancial de las actividades de operación y mantenimiento. En definitiva, un aumento de la fiabilidad de las instalaciones.
Un ejemplo de equipo de inspección: UESystems UP2000
En el mercado existen multitud de marcas y modelos de instrumentos de inspección de ultrasonidos. El equipo analógico del fabricante UE-Systems (modelo UP2000) capaz de detectar ultrasonido en el rango 20-100KHz. Para la inspección se emplea un módulo de contacto con el que se palpan determinados puntos de la válvula a fin de medir el valor en dB de ultrasonidos. También puede usarse el módulo magnético a fin de garantizar una mejor repetitividad de las lecturas, pero solo es posible utilizarlo sobre materiales ferromagnéticos.

Puesto que el equipo UP2000 es analógico y no muestra una lectura directa en dB sino en una escala de intensidad 0-100%, es necesario ajustar la sensibilidad a una lectura de, aproximadamente, el 50% de la escala con respuesta lineal y banda fija. Esto es lo que se conoce como ajuste de la línea base y se realiza en los dos primeros puntos A-B del método de inspección ABCD, anotando en ese instante el correspondiente valor de sensibilidad. La intensidad de sonido de la línea base se compara posteriormente con el punto de prueba C. Como ya hemos visto, el punto de prueba D se toma a fin de asegurar que no hay otra fuente de ultrasonidos ajenos a la fuga en sí misma y procedentes de otras fuentes. Si la lectura D es más alta que C, significa que dicho ultrasonido competidor existe y es de gran amplitud y, por tanto, el ensayo no es concluyente. Esto mismo es aplicable a cualquier otro equipo analógico del mercado cuyo principio de funcionamiento sea similar.

Puesto que el equipo UP2000 no da en dB su salida de intensidad, se ha de utilizar la curva de respuesta para el módulo empleado. Esta curva relaciona la sensibilidad al 50% de la escala con su valor en dB, que es el valor registrable.
Registro y documentación de inspecciones
El registro histórico de las inspecciones para su posterior estudio y documentación es una parte esencial en cualquier programa de mantenimiento predictivo.
Para obtener (y registrar) los valores en dB es necesaria la optimización del método en cada válvula. Esto significa realizar las inspecciones utilizando la configuración óptima del instrumento que a su vez vendrá dada la experiencia del inspector y las condiciones particulares de proceso. El registro de estos valores de configuración asegurará la repetitividad de las lecturas en sucesivas inspecciones.
Registro y documentación de inspecciones
El registro histórico de las inspecciones para su posterior estudio y documentación es una parte esencial en cualquier programa de mantenimiento predictivo.
Para obtener (y registrar) los valores en dB es necesaria la optimización del método en cada válvula. Esto significa realizar las inspecciones utilizando la configuración óptima del instrumento que a su vez vendrá dada la experiencia del inspector y las condiciones particulares de proceso. El registro de estos valores de configuración asegurará la repetitividad de las lecturas en sucesivas inspecciones.
Es recomendable que en el formulario de registro de cada válvula aparezca:
- La configuración del instrumento de medida.
- El tipo, la presión y temperatura del fluido de proceso.
- El tipo de válvula.
- Fecha de la inspección.
- La orden de trabajo.
- Identificación de la válvula.
- Las secciones en cada punto de inspección.
- Los valores en dB de cada punto.
- Otra información relevante.
El sistema de registro ha de permitir generar informes históricos, así como la planificación de las inspecciones. Por otro lado, se ha de reportar a la dirección de la empresa los potenciales beneficios en términos de fiabilidad y ahorro de costes conseguidos con los planes de inspección.
A continuación se muestran algunos informes de ejemplos reales:




Monitorización remota
Algunos procesos industriales pueden requerir la monitorización de fugas en tiempo real de determinadas válvulas críticas. Un ejemplo lo constituyen las válvulas de seguridad, las cuales, tras un disparo pudieran no cerrar adecuadamente debido al mal posicionamiento del obturador al retornar a su posición de reposo. Habitualmente, los métodos tradicionales para la determinación de la presencia de una fuga interna han sido la presencia de ruido en el rango audible o la combustión del gas en antorcha. Obviamente estos métodos resultan del todo ineficaces y suelen generar impactos negativos tanto para el medio ambiente como a nivel de costes operativos. Por otro lado, si el técnico de mantenimiento es incapaz de determinar si la válvula se ha posicionado adecuadamente en su posición de cierre tras un disparo, pudiera verse tentado a planificar una actividad correctiva innecesaria (mecanizado de tobera, lapeado de asientos, sustitución del muelle, etc.) Actuando así, deja indisponible el sistema y genera un gasto evitable. Es por los motivos expuestos que un sistema de detección online de fugas internas se convierte en una potentísima herramienta para minimizar los costes y aumentar la fiabilidad de las válvulas críticas de cualquier proceso industrial. Además, un sistema online de detección:
- Reduce las falsas alarmas o errores de diagnóstico del operador.
- Permite cumplir con determinados requisitos medioambientales que establece el marco legislativo.
- Reduce las emisiones.
- Aumenta la eficiencia energética.
- Minimiza los procesos de erosión y corrosión debidos a la presencia de fugas.
- Mejora la imagen corporativa.
Descripción del sistema
La posición adecuada para situar los sensores es la más próxima a la fuente de ultrasonido (zona de cierre de la válvula) y en una ubicación donde se minimice el trayecto que ha de recorrer la onda ultrasónica hasta el detector. Por otro lado, se ha de procurar un contacto íntimo entre la superficie del sensor y la válvula. Aunque no es necesaria una preparación especial de la superficie, sí es conveniente eliminar la película de pintura o depósitos de óxido. El método de fijación del sensor puede ser atornillado, mediante uso de flejes o abrazaderas o incluso con adhesivos especiales.
A la hora de parametrizar y optimizar el lazo de medida es necesario tener en cuenta otras posibles fuentes de ultrasonido competidor o ruido de fondo tales como:
- Flujos de vapor en tuberías de acompañamiento (traceado de vapor).
- Fugas atmosféricas próximas.
- Fugas o purgas adyacentes de aire de instrumentos.
- Válvulas de control cercanas.
- Accesorios próximos tales como codos, tes o reducciones, que originan turbulencia en el flujo.

El lazo de medida constará del elemento sensor, acondicionador de señal, transmisor, cableado de campo, barreras galvánicas o zéner en caso necesario y tarjeta de adquisición de datos dinámicos. También es posible, aparte de la señal de ultrasonido, incluir otros instrumentos de medida, como termopares, para complementar el diagnóstico. La adecuada configuración de estos lazos de medida ha de tener como objetivo final generar una alarma en la sala de control que alerte de la presencia de una fuga y minimizar los tiempos de respuesta para intervenir sobre la misma, así como un histórico lo suficientemente rico.

Por otro lado, la salida del sensor debería ser una señal digital, debido a las ventajas de las señales digitales frente a las analógicas. Los sensores han de disponer de una salida RS485, RS232, Modbus, así como la opción de relé y salida estándar 4-20mA. Mediante el uso de la opción digital, es posible una comunicación bidireccional con el sensor, permitiendo al operador cambiar los ajustes de forma remota. Además, en el caso de determinadas industrias como la petroquímica, se hace necesario la instalación de lazos intrínsecamente seguros mediante el uso de barreras zéner o de aislamiento galvánico.
El siguiente gráfico muestra los ciclos de apertura y cierre de una válvula de seguridad timbrada a 5.5 bar. Como puede observarse al final de la curva, llega un momento en que la válvula no retorna adecuadamente a su posición de cierre y provoca una fuga interna detectada por el sensor de ultrasonidos, que alerta al operador de sala de control.


Cursos recomendados




%252FImagen%252FRAMPREDYC-1730060420837.webp%3Falt%3Dmedia%26token%3D2634a7f0-988e-4022-b91f-382503e6e9db&w=3840&q=75)



Normativa
Como ensayo no destructivo, para la inspección de fugas con ultrasonidos existe actualmente una práctica recomendada designada como ASTM E1002 - 11 Standard Practice for Leaks Using Ultrasonics, cuyo contenido es el siguiente:
Practice A—This practice is useful for locating and estimating the size of pressurized gas leaks, either as a quality control test or as a field inspection procedure. It is also valuable as a pretest before other more time consuming and more sensitive leak tests are employed. It should not be used exclusively to locate highly toxic or explosive gas leaks.
Practice B—This practice is useful for locating leaks in systems that are not under pressure or vacuum as either a quality control or a field inspection procedure. It is not useful for estimating the size of a leak. It is also valuable as a pretest before leak tests using pressurized gas methods and more sensitive leak tests are employed.
Ventajas e inconvenientes
Algunas de las ventajas e inconvenientes de la inspección de ultrasonidos son las siguientes:
- Inspección no invasiva.
- Método simple y seguro.
- Utilización de instrumentación portátil.
- Medidas on-line, en tiempo real y determinación del estado de forma inmediata.
- Reducción de costes de mantenimiento.
- Discrimina sonidos no ultrasónicos.
- Perfecto para fugas de bajo caudal.
- Muy sensible.
- Aumento de la fiabilidad de válvulas.
- Monitorización medioambiental de las fugas.
- No válido para fugas de pequeño caudal inaudibles.
- Necesario contacto con el elemento a inspeccionar.
- No adecuado para muy altas temperaturas.
- No válido en fugas de régimen no turbulento.
Como conclusión podemos decir que las técnicas más utilizadas para la detección de fugas son la termografía infrarroja y el ultrasonido de contacto. Ambas, que son complementarias, presentan ventajas e inconvenientes y en ningún caso son infalibles, pues están muy condicionadas por diversos factores. No obstante, su aplicación conjunta constituye un método efectivo para la detección de un problema tan común en la industria como son las fugas internas en válvulas, lo que supone un aumento de la fiabilidad de las instalaciones y una minimización del coste de mantenimiento asociado a las mismas.
Referencias
- www.uesystems.com
- www.isa.org
- www.sdt.eu
- www.mistrasgroup.com
Autor: Antonio Abejaro Soto
Dinos qué te ha parecido el artículo
Artículos recomendados
Planificación de Mantenimiento en PM-SAP

CONOCIENDO LAS HOJAS TÉCNICAS DE PRODUCTOS Y LAS HOJAS DE SEGURIDAD DE PRODUCTOS

Gestión de mantenimiento preventivo

La Confiabilidad: La Lucha del Bien Contra el Mal

Publica tu artículo en la revista #1 de Mantenimiento Industrial
Publicar un artículo en la revista es gratis, no tiene costo.
Solo debes asegurarte que no sea un artículo comercial.
¿Qué esperas?
O envía tu artículo directo: articulos@predictiva21.com
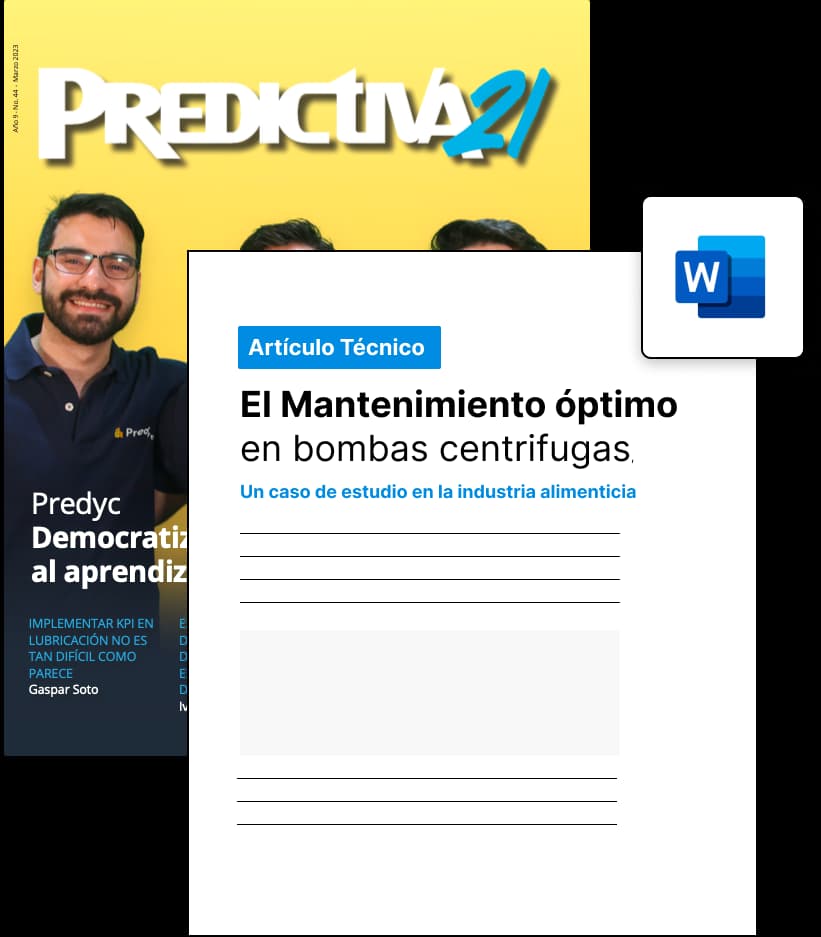
Detección de Fugas Internas en Válvulas Mediante la Técnica De Ultrasonido (II Parte)
Articulo 8 de enero de 2020Introducción
Las válvulas son dispositivos de control de flujo utilizados en todo tipo de industrias (petroquímica, energía, alimentación, papel, minería, etc.) Existen multitud de tipos, configuraciones y tamaños diseñados según las necesidades concretas de los procesos en que se integran.
Dependiendo del régimen de funcionamiento y las condiciones de operación e instalación, una válvula puede fallar de diversos modos: acumulación de suciedad o depósitos en obturador y asientos, ejes doblados o rotos, fugas en empaquetaduras, rotura de juntas, corrosión y erosión en cuerpo, fallos en dispositivos actuadores o de control, etc. Centrándonos en el caso de las fugas internas, la detección de este tipo de problemas puede suponer un ahorro significativo de costes asociados a paradas de emergencia, pérdidas de producción, disminución de la eficiencia energética e impacto ambiental.
Estudios de campo han demostrado que entre el 5 y el 10% de las válvulas de cualquier instalación industrial presentan alguna sintomatología relacionada con fugas internas. Por ejemplo, las válvulas que manejan vapor y presentan fugas pueden ocasionar considerables pérdidas de energía traducidas en costes elevados. Ni que decir tiene la importancia en el caso de instalaciones que procesan fluidos tóxicos, radiactivos, explosivos, combustibles o corrosivos y que supongan un riesgo para la integridad de las personas, las instalaciones o el medio ambiente. Por tanto, eliminar o minimizar estas fugas ha de ser considerado como un objetivo prioritario en empresas que basan su filosofía de mantenimiento en el seguimiento de la condición de sus activos.
Continuación
Ensayo indeterminado
En ocasiones, la presencia de ruido de fondo impide diagnosticar adecuadamente una válvula, bien porque enmascare el ultrasonido generado por la propia fuga o bien por la alta intensidad del mismo que impide llegar a conclusiones acertadas. En estos casos puede resultar útil modificar los filtros del equipo de ultrasonidos a fin de despreciar determinados rangos de frecuencias, pero por lo general es un problema insalvable que se convierte en una de las limitaciones propias de esta técnica.

Selección de los puntos de inspección
El método ABCD se puede complementar con medidas adicionales (E,F,…) en diferentes puntos de la válvula, en función del tipo y dimensiones. El disponer de lecturas complementarias permite realizar un diagnóstico más preciso.


Consideraciones adicionales
Selección de la frecuencia
En la mayoría de los casos, las señales ultrasónicas generadas por una fuga tienen un amplio rango de frecuencias que, sumadas, constituyen el típico ruido blanco característico de una fuga y, en ocasiones, de mayor intensidad que cualquier componente audible presente. Muy pocas veces una fuga particular suele tener una frecuencia característica tanto en el dominio audible como en el ultrasónico. Es muy difícil predecir la respuesta en frecuencia de una válvula en particular para una fuga en particular. Factores como la dimensión, forma de cuerpo y asientos, obturador, tipo de fluido, viscosidad, área de paso, caída de presión, etc. influyen en la respuesta final.
No obstante, los equipos de ultrasonidos modernos permiten seleccionar la frecuencia de corte, e incluso rangos de frecuencias, a fin de discriminar información de escaso interés.

Selección del sensor
Es muy útil utilizar en un principio el sensor magnético en aquellas válvulas donde sea posible debido a su alta sensibilidad, facilidad de uso y mejora de la repetitividad. Si los resultados obtenidos no son convincentes, utilizar el módulo de contacto para una inspección más amplia. No obstante, la presión ejercida en el punto de medida así como el ángulo de incidencia en el caso de los módulos de contacto de varilla pueden alterar la lectura final.

Circuitos de alta presión
Los sistemas que trabajan a altas presiones producen intensos niveles de ultrasonido que se propaga con facilidad por las estructuras (tuberías, soportes, válvulas, depósitos, etc.) En estos casos pudiera ser complejo determinar la presencia de una fuga interna en una válvula, ya que el nivel de fondo de ultrasonido es muy elevado en comparación con el generado por la fuga. La experiencia del operador y el método comparativo ABCD es el más recomendable en esta situación.
Consideraciones finales
- Es recomendable que los puntos ABCD tengan secciones similares (mismo o similar DN) En caso contrario, es la experiencia del inspector y el registro de datos históricos el mejor indicador del estado de la válvula.
- Tener en cuenta el sentido del flujo para aplicar adecuadamente el método ABCD.
- Verificar que la válvula está realmente cerrada y que no procede ruido audible de la misma. Si tal fuera el caso, no sería necesaria la inspección ultrasónica. De hecho, en grandes fugas pudiera haber una baja intensidad de ultrasonidos.
- Procurar inspeccionar con el módulo de contacto ejerciendo siempre la misma presión y ángulo sobre el punto a inspeccionar. La variación de los mismos provoca modificaciones en las lecturas y dificulta la repetitividad de las medidas. Si se dispone, utilizar un módulo magnético.
- Es muy importante por parte del inspector, familiarizarse con los sonidos procedentes de válvulas en buen y mal estado.
- En la medida de lo posible, las inspecciones las ha de realizar el mismo operador.
- Ajustar los valores de sensibilidad y frecuencia a fin de obtener un sonido “limpio” libre de ruidos procedentes de otras fuentes competidoras.
- Comparar válvulas similares adyacentes.
- Registrar la presión de trabajo y temperatura de proceso en el momento de la inspección, pues condicionará los resultados en caso de variaciones.
- Tener en cuenta que la viscosidad y densidad del fluido, dependientes de su temperatura, influyen en la turbulencia del fluido en las zonas de fuga.
- Conocer el proceso y las posibles fuentes de ultrasonido competidor.
- Anotar todos los resultados y observaciones adicionales en la hoja de campo.
- Realizar las inspecciones siempre en los mismos puntos.
- Prestar atención a todas las recomendaciones de seguridad (fluidos peligrosos, salpicaduras, contacto con temperaturas extremas, gases, etc).
- Identificar la válvula problemática en campo con una etiqueta.
- Realizar una inspección visual de la válvula una vez diagnosticada para corroborar los hallazgos.
Es especialmente necesario tomar las precauciones de seguridad necesarias a la hora de inspeccionar válvulas que operan a altas temperaturas o con fluidos peligrosos, no solo por los riesgos a que se ve expuesto el operador sino por el hecho de que pueden afectar o dañar la electrónica del equipo.
Por otro lado, hay multitud de mecanismos adicionales que condicionan la forma en que una válvula con fugas genera ruido ultrasónico: tipo de degradación de la zona de cierre, resonancias estructurales, ultrasonido de procesos próximos, etc. Como ya se ha indicado, la técnica se puede complicar cuando se trata de inspeccionar sistemas hidráulicos o redes de vapor debido al alto ruido de fondo.
Estimación del caudal de fuga y pérdidas económicas
Los equipos de detección de ultrasonidos no se fabrican siguiendo un estándar mundial, por lo que determinadas características de diseño de los mismos, como la sensibilidad, son propios de cada fabricante. Por este motivo, tampoco es posible establecer con facilidad una metodología de cálculo de los caudales de fuga en función del ruido ultrasónico de la válvula. Algunos fabricantes, basándose en su propia experiencia y en datos empíricos han creado algoritmos para la estimación de los flujos de fuga y las pérdidas económicas asociadas a los mismos. No obstante, sí se puede afirmar que cuanto mayor sea el diferencial de amplitud en dB en la zona de cierre de la válvula con respecto a otros puntos de la misma, tanto mas severa será la fuga.

Como cabe esperar, la detección y la cuantificación de las fugas puede conducir a ahorros significativos, maximización de la eficiencia de la planta y protección del medio ambiente así como una mejora sustancial de las actividades de operación y mantenimiento. En definitiva, un aumento de la fiabilidad de las instalaciones.
Un ejemplo de equipo de inspección: UESystems UP2000
En el mercado existen multitud de marcas y modelos de instrumentos de inspección de ultrasonidos. El equipo analógico del fabricante UE-Systems (modelo UP2000) capaz de detectar ultrasonido en el rango 20-100KHz. Para la inspección se emplea un módulo de contacto con el que se palpan determinados puntos de la válvula a fin de medir el valor en dB de ultrasonidos. También puede usarse el módulo magnético a fin de garantizar una mejor repetitividad de las lecturas, pero solo es posible utilizarlo sobre materiales ferromagnéticos.

Puesto que el equipo UP2000 es analógico y no muestra una lectura directa en dB sino en una escala de intensidad 0-100%, es necesario ajustar la sensibilidad a una lectura de, aproximadamente, el 50% de la escala con respuesta lineal y banda fija. Esto es lo que se conoce como ajuste de la línea base y se realiza en los dos primeros puntos A-B del método de inspección ABCD, anotando en ese instante el correspondiente valor de sensibilidad. La intensidad de sonido de la línea base se compara posteriormente con el punto de prueba C. Como ya hemos visto, el punto de prueba D se toma a fin de asegurar que no hay otra fuente de ultrasonidos ajenos a la fuga en sí misma y procedentes de otras fuentes. Si la lectura D es más alta que C, significa que dicho ultrasonido competidor existe y es de gran amplitud y, por tanto, el ensayo no es concluyente. Esto mismo es aplicable a cualquier otro equipo analógico del mercado cuyo principio de funcionamiento sea similar.

Puesto que el equipo UP2000 no da en dB su salida de intensidad, se ha de utilizar la curva de respuesta para el módulo empleado. Esta curva relaciona la sensibilidad al 50% de la escala con su valor en dB, que es el valor registrable.
Registro y documentación de inspecciones
El registro histórico de las inspecciones para su posterior estudio y documentación es una parte esencial en cualquier programa de mantenimiento predictivo.
Para obtener (y registrar) los valores en dB es necesaria la optimización del método en cada válvula. Esto significa realizar las inspecciones utilizando la configuración óptima del instrumento que a su vez vendrá dada la experiencia del inspector y las condiciones particulares de proceso. El registro de estos valores de configuración asegurará la repetitividad de las lecturas en sucesivas inspecciones.
Registro y documentación de inspecciones
El registro histórico de las inspecciones para su posterior estudio y documentación es una parte esencial en cualquier programa de mantenimiento predictivo.
Para obtener (y registrar) los valores en dB es necesaria la optimización del método en cada válvula. Esto significa realizar las inspecciones utilizando la configuración óptima del instrumento que a su vez vendrá dada la experiencia del inspector y las condiciones particulares de proceso. El registro de estos valores de configuración asegurará la repetitividad de las lecturas en sucesivas inspecciones.
Es recomendable que en el formulario de registro de cada válvula aparezca:
- La configuración del instrumento de medida.
- El tipo, la presión y temperatura del fluido de proceso.
- El tipo de válvula.
- Fecha de la inspección.
- La orden de trabajo.
- Identificación de la válvula.
- Las secciones en cada punto de inspección.
- Los valores en dB de cada punto.
- Otra información relevante.
El sistema de registro ha de permitir generar informes históricos, así como la planificación de las inspecciones. Por otro lado, se ha de reportar a la dirección de la empresa los potenciales beneficios en términos de fiabilidad y ahorro de costes conseguidos con los planes de inspección.
A continuación se muestran algunos informes de ejemplos reales:




Monitorización remota
Algunos procesos industriales pueden requerir la monitorización de fugas en tiempo real de determinadas válvulas críticas. Un ejemplo lo constituyen las válvulas de seguridad, las cuales, tras un disparo pudieran no cerrar adecuadamente debido al mal posicionamiento del obturador al retornar a su posición de reposo. Habitualmente, los métodos tradicionales para la determinación de la presencia de una fuga interna han sido la presencia de ruido en el rango audible o la combustión del gas en antorcha. Obviamente estos métodos resultan del todo ineficaces y suelen generar impactos negativos tanto para el medio ambiente como a nivel de costes operativos. Por otro lado, si el técnico de mantenimiento es incapaz de determinar si la válvula se ha posicionado adecuadamente en su posición de cierre tras un disparo, pudiera verse tentado a planificar una actividad correctiva innecesaria (mecanizado de tobera, lapeado de asientos, sustitución del muelle, etc.) Actuando así, deja indisponible el sistema y genera un gasto evitable. Es por los motivos expuestos que un sistema de detección online de fugas internas se convierte en una potentísima herramienta para minimizar los costes y aumentar la fiabilidad de las válvulas críticas de cualquier proceso industrial. Además, un sistema online de detección:
- Reduce las falsas alarmas o errores de diagnóstico del operador.
- Permite cumplir con determinados requisitos medioambientales que establece el marco legislativo.
- Reduce las emisiones.
- Aumenta la eficiencia energética.
- Minimiza los procesos de erosión y corrosión debidos a la presencia de fugas.
- Mejora la imagen corporativa.
Descripción del sistema
La posición adecuada para situar los sensores es la más próxima a la fuente de ultrasonido (zona de cierre de la válvula) y en una ubicación donde se minimice el trayecto que ha de recorrer la onda ultrasónica hasta el detector. Por otro lado, se ha de procurar un contacto íntimo entre la superficie del sensor y la válvula. Aunque no es necesaria una preparación especial de la superficie, sí es conveniente eliminar la película de pintura o depósitos de óxido. El método de fijación del sensor puede ser atornillado, mediante uso de flejes o abrazaderas o incluso con adhesivos especiales.
A la hora de parametrizar y optimizar el lazo de medida es necesario tener en cuenta otras posibles fuentes de ultrasonido competidor o ruido de fondo tales como:
- Flujos de vapor en tuberías de acompañamiento (traceado de vapor).
- Fugas atmosféricas próximas.
- Fugas o purgas adyacentes de aire de instrumentos.
- Válvulas de control cercanas.
- Accesorios próximos tales como codos, tes o reducciones, que originan turbulencia en el flujo.

El lazo de medida constará del elemento sensor, acondicionador de señal, transmisor, cableado de campo, barreras galvánicas o zéner en caso necesario y tarjeta de adquisición de datos dinámicos. También es posible, aparte de la señal de ultrasonido, incluir otros instrumentos de medida, como termopares, para complementar el diagnóstico. La adecuada configuración de estos lazos de medida ha de tener como objetivo final generar una alarma en la sala de control que alerte de la presencia de una fuga y minimizar los tiempos de respuesta para intervenir sobre la misma, así como un histórico lo suficientemente rico.

Por otro lado, la salida del sensor debería ser una señal digital, debido a las ventajas de las señales digitales frente a las analógicas. Los sensores han de disponer de una salida RS485, RS232, Modbus, así como la opción de relé y salida estándar 4-20mA. Mediante el uso de la opción digital, es posible una comunicación bidireccional con el sensor, permitiendo al operador cambiar los ajustes de forma remota. Además, en el caso de determinadas industrias como la petroquímica, se hace necesario la instalación de lazos intrínsecamente seguros mediante el uso de barreras zéner o de aislamiento galvánico.
El siguiente gráfico muestra los ciclos de apertura y cierre de una válvula de seguridad timbrada a 5.5 bar. Como puede observarse al final de la curva, llega un momento en que la válvula no retorna adecuadamente a su posición de cierre y provoca una fuga interna detectada por el sensor de ultrasonidos, que alerta al operador de sala de control.


Cursos recomendados




%252FImagen%252FRAMPREDYC-1730060420837.webp%3Falt%3Dmedia%26token%3D2634a7f0-988e-4022-b91f-382503e6e9db&w=3840&q=75)



Normativa
Como ensayo no destructivo, para la inspección de fugas con ultrasonidos existe actualmente una práctica recomendada designada como ASTM E1002 - 11 Standard Practice for Leaks Using Ultrasonics, cuyo contenido es el siguiente:
Practice A—This practice is useful for locating and estimating the size of pressurized gas leaks, either as a quality control test or as a field inspection procedure. It is also valuable as a pretest before other more time consuming and more sensitive leak tests are employed. It should not be used exclusively to locate highly toxic or explosive gas leaks.
Practice B—This practice is useful for locating leaks in systems that are not under pressure or vacuum as either a quality control or a field inspection procedure. It is not useful for estimating the size of a leak. It is also valuable as a pretest before leak tests using pressurized gas methods and more sensitive leak tests are employed.
Ventajas e inconvenientes
Algunas de las ventajas e inconvenientes de la inspección de ultrasonidos son las siguientes:
- Inspección no invasiva.
- Método simple y seguro.
- Utilización de instrumentación portátil.
- Medidas on-line, en tiempo real y determinación del estado de forma inmediata.
- Reducción de costes de mantenimiento.
- Discrimina sonidos no ultrasónicos.
- Perfecto para fugas de bajo caudal.
- Muy sensible.
- Aumento de la fiabilidad de válvulas.
- Monitorización medioambiental de las fugas.
- No válido para fugas de pequeño caudal inaudibles.
- Necesario contacto con el elemento a inspeccionar.
- No adecuado para muy altas temperaturas.
- No válido en fugas de régimen no turbulento.
Como conclusión podemos decir que las técnicas más utilizadas para la detección de fugas son la termografía infrarroja y el ultrasonido de contacto. Ambas, que son complementarias, presentan ventajas e inconvenientes y en ningún caso son infalibles, pues están muy condicionadas por diversos factores. No obstante, su aplicación conjunta constituye un método efectivo para la detección de un problema tan común en la industria como son las fugas internas en válvulas, lo que supone un aumento de la fiabilidad de las instalaciones y una minimización del coste de mantenimiento asociado a las mismas.
Referencias
- www.uesystems.com
- www.isa.org
- www.sdt.eu
- www.mistrasgroup.com
Autor: Antonio Abejaro Soto
Dinos qué te ha parecido el artículo
Artículos recomendados
17.- Instrumentación y Control

Evaluación de la Base de Datos de Mantenimiento

Selección de Potencia del Motor Eléctrico en Compresores Reciprocantes de Múltiples Etapas

Indicadores BS-EN 15341

Publica tu artículo en la revista #1 de Mantenimiento Industrial
Publicar un artículo en la revista es gratis, no tiene costo.
Solo debes asegurarte que no sea un artículo comercial.
¿Qué esperas?
O envía tu artículo directo: articulos@predictiva21.com
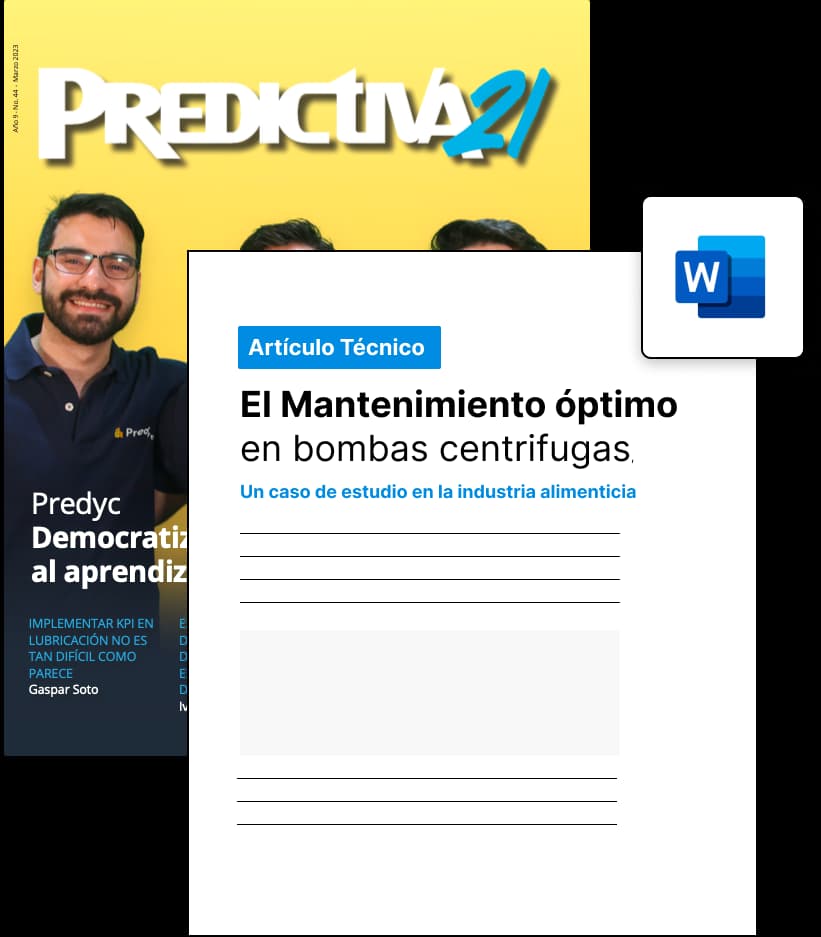