4.2. Indices Clase Mundial
Libros31 de agosto de 2020
Son llamados "índices clase mundial" aquellos que son utilizados según la misma expresión en todos los países. De los seis "índices clase mundial", cuatro son los que se refieren al Análisis de la Gestión de Equipos y dos a la Gestión de Costos, de acuerdo con las siguientes relaciones:
Tiempo Medio Entre Fallas - Relación entre el producto del número de ítems por sus tiempos de operación y el número total de fallas detectadas en esos ítems, en el periodo observado.

Este índice debe ser usado para ítems que son reparados después de la ocurrencia de una falla.
Tiempo Medio Para Reparación - Relación entre el tiempo total de intervención correctiva en un conjunto de ítems con falla y el número total de fallas detectadas en esos ítems, en el periodo observado.

Este índice debe ser usado, para ítems en los cuales el tiempo de reparación es significativo con relación al tiempo de operación.
Tiempo Medio Para la Falla - Relación entre el tiempo total de operación de un conjunto de ítems no reparables y el número total de fallas detectadas en esos ítems, en el periodo observado.

Este índice debe ser usado para ítems que son sustituidos después de la ocurrencia de una falla.
Es importante observar la diferencia conceptual existente entre los índices Tiempo medio Para la Falla y Tiempo medio Entre Fallas. El primer índice (TMPF) es calculado para ítems que NO SON reparados tras la ocurrencia de una falla, o sea, cuando fallan son sustituidos por nuevos y, en consecuencia, su tiempo de reparación es cero. El segundo índice (TMEF) es calculado para ítems que SON reparados tras la ocurrencia de la falla. Por lo tanto, los dos índices son mutuamente exclusivos, o sea, el cálculo de uno excluye el cálculo del otro, para ítems iguales.
El cálculo del Tiempo medio Entre Fallas debe estar asociado al cálculo del Tiempo medio para la Reparación. La interpretación gráfica entre estos índices, está representada en la Figura 34.
Debido a que dichos índices presentan un resultado promedio, su exactitud está asociada a la cantidad de ítems observados y al periodo de observación. Cuanto mayor sea la cantidad de datos, mayor será la precisión de la expectativa de sus valores.
En caso de no existir gran cantidad de ítems, o en el caso que se desee obtener los Tiempos Promedios Entre Fallas de cada uno, es recomendable trabajar con periodos bastante amplios de observación (cinco años o más), para garantizar la confiabilidad de los resultados.

Especial atención se debe tener en el desarrollo de programas informatizados para el cálculo de estos índices, pues puede ocurrir que, en el periodo considerado, el número de ocurrencias (fallas) sea cero, lo que llevaría a la computadora a realizar un cálculo, que daría como resultado un valor "infinito" (división entre cero), haciendo que el programa se trabe. Como sugerencia para este tipo de acontecimiento, debe ser hecha la consideración de la existencia de una falla con tiempo igual a cero, que daría un valor constante para cualquier condición de cálculo.
Disponibilidad de Equipos - Relación entre la diferencia del número de horas del periodo considerado (horas calendario) con el número de horas de intervención por el personal de mantenimiento (mantenimiento preventivo por tiempo o por estado, mantenimiento correctivo y otros servicios) para cada ítem observado y el número total de horas del periodo considerado.

La disponibilidad de un ítem representa el porcentaje del tiempo en que quedó a disponibilidad del órgano de operación para desempeñar su actividad.
El índice de Disponibilidad también es identificado como "Performance o Desempeño de Equipos" y, para ítems de operación eventual, puede ser calculado como la relación entre el tiempo total de operación de cada uno y la suma de este tiempo con el respectivo tiempo total de mantenimiento en el periodo considerado.

Este índice también puede ser calculado como la diferencia entre la unidad y la relación entre las horas de mantenimiento y la suma de esas horas con las de operación de los equipos.
Otra expresión muy común, utilizada para el cálculo de la Disponibilidad de equipos sometidos exclusivamente a la reparación de fallas es obtenida por la relación entre el Tiempo medio Entre Falla (TMEF) y su suma con el Tiempo medio para Reparación y los Tiempos Ineficaces del Mantenimiento (tiempos de preparación para desconexión y nueva conexión y tiempos de espera que pueden estar contenidos en los tiempos promedios entre fallos y de reparación).

Es posible observar que ésta es la expresión más simple ya que es obtenida a partir de la relación entre dos otros índices normalmente ya calculados.
El índice de Disponibilidad (o Performance) es de gran importancia para la gestión del mantenimiento, pues a través de éste, puede ser hecho un análisis selectivo de los equipos, cuyo comportamiento operacional está por debajo de estándares aceptables.
Para su análisis, se recomienda poner en tablas mensualmente, la disponibilidad (o performance) de los equipos seleccionados por el usuario y establecer un límite mínimo aceptable de sus valores, a partir del cual, serán hechas las selecciones para el análisis, conforme es ilustrado en la Figura 35.

En la misma tabla, pueden ser presentados los valores promedios de disponibilidad del "periodo anterior" (12 meses anteriores al actual o más) y del "periodo actual", para permitir el acompañamiento de los equipos en periodos más amplios.
Se observa que en el ejemplo presentado, fueron indicados varios equipos/mes que presentaron el índice de disponibilidad bajo, donde cuatro de ellos (los dos "after cooler", los dos compresores y el destilador #1) presentaron una disponibilidad anual inferior a los demás analizados, con pequeña variación de un periodo para otro.
En especial, el destilador #1 se destaca, por presentar una disponibilidad anual inferior a 90% en los dos periodos, aunque haya tenido un incremento de su valor en 5 puntos porcentuales.
Para los equipos que presenten resultados inferiores al mínimo aceptable, podrá ser trazado el gráfico - Figura 36, que es el punto de partida para la aplicación del llamado Modo de Análisis de Efecto de Fallas (FMEA).

Como variante de los cálculos de Disponibilidad absoluta, pueden ser obtenidas las relaciones entre los tiempos de cada tipo de intervención en el equipo (correctiva, preventiva por tiempo, preventiva por estado y otros servicios - montaje, mejora de mantenimiento, mejora de seguridad operacional etc.) y mantenimiento con relación a la suma de los tiempos gastados en esas actividades. A ese tipo de cálculo se le denomina "Disponibilidad Relativa", cuya suma de valores siempre totalizarán 100%.
El análisis de la "Disponibilidad Relativa" debe ser hecho en comparación con la "Disponibilidad Absoluta" a través del producto de una por la otra, para evitar errores de interpretación ya que eventuales valores elevados de Disponibilidad Relativa de Mantenimiento Correctivo pueden, en el cómputo general (al multiplicar por la Disponibilidad Absoluta), ser de bajo valor.
Ejemplificando:
Imaginemos que el "Horno #5" de la fábrica de San José, que opera 24 horas al día, presentó en el mes de agosto de 1 999 los siguientes tiempos totales en mantenimiento:
- Preventivo: 0,3 hr.
- Correctivo: 1,3 hr.
- Apoyo: 0,2 hr.
Se tiene que el tiempo total de mantenimiento fue de 0,3 + 1,3 +0,2 = 1,8 hr.
Por lo tanto, sus valores de disponibilidad relativa serían:
- Disponibilidad Relativa Preventiva = (0,3/1,8) x 100 = 16,67%
- Disponibilidad Relativa Correctiva = (1,3/1,8) x 100 = 72,22 %
- Disponibilidad Relativa de Apoyo = (0,2/1,8) x 100 = 11,11%
Dando la impresión, de que se tuvo una excesiva cantidad de mantenimientos correctivos.
En la realidad si son multiplicados los valores relativos por el valor de la indisponibilidad absoluta, se encontrará que las disponibilidades relativas son:
- Disponibilidad Absoluta = [1-(24 x 31 - 1,8) / 744] x 100
Disponibilidad Absoluta = [1 - (744 - 1,8) / 744] x 100 = 0,24% - Disponibilidad Relativa Preventiva = 16,67% x 0,24% = 0,04%
- Disponibilidad Relativa Correctiva = 72,22 % x 0,24% = 0,17%
- Disponibilidad Relativa de Apoyo = 11,11% x 0,24% = 0,03%
Que no causan un mayor impacto en el observador. Una característica, ya constatada por algunos gerentes del área de ejecución del mantenimiento que hacen el análisis de Disponibilidad Relativa, es que, después de la realización de una Gran Reparación (Reforma o Gran Parada), el índice de correctivos normalmente es elevado, debido al retorno del equipo a sus características normales de operación.
Una vez definidos los cuatro índices "clase mundial" para la gestión de equipos, presentamos los dos restantes, aplicados en la gestión de costos.
Costo de Mantenimiento por Facturación - Relación entre el costo total de mantenimiento y la facturación de la empresa en el periodo considerado.

Este índice es de fácil cálculo ya que los valores, tanto del numerador como los del denominador, son normalmente procesados por el órgano de contabilidad de la empresa.
Costo de Mantenimiento por el Valor de Reposición - Relación entre el costo total acumulado en el mantenimiento de un determinado equipo y el valor de compra de ese mismo equipo nuevo (valor de reposición)

Este índice debe ser calculado para los ítems más importantes de la empresa (que afectan la facturación, la calidad de los productos o servicios, la seguridad o al medio ambiente), ya que como fue indicado, es personalizado para el ítem y utiliza valores acumulados, lo que torna su procesamiento más demorado que los demás, no justificando de esta forma ser utilizado para ítems secundarios.
Su resultado debe ser acompañado por un gráfico lineal o de superficie, con la indicación de su variación, en por lo menos los doce últimos meses, conforme es ilustrado en la figura 37.

No obstante el costo total del mantenimiento, esta compuesto por cinco elementos (personal, material, terceros, depreciación y pérdida/reducción en la facturación), cada una de ellos con tres subdivisiones (costos directos, costos indirectos y costos administrativos); difícilmente es hecha esta composición, limitándose las empresas a considerar dos o tres elementos (personal, material y eventualmente terceros) y de igual manera, una o dos de sus subdivisiones (costos directos y eventualmente, costos indirectos).
Otro factor que torna los índices de costo imprecisos, es la utilización de valores contables pertenecientes al historial de los equipos, sin corrección monetaria lo que es más susceptible de originar errores en el caso de una inflación monetaria. De la misma manera, cuando la empresa utiliza un valor de referencia (dólar o mix de monedas), la imprecisión aparece, debido a la variedad de los índices de corrección, o a la no consideración de la devaluación del dólar o de otras unidades monetarias adoptadas.
Esta imprecisión no es sensible, cuando es realizado el seguimiento de los índices en la propia empresa, ya que estará cometiéndose el mismo error a lo largo del tiempo; pero puede llevar a grandes errores de interpretación, cuando estos índices son comparados con otras empresas, y mucho peor, cuando son comparados con empresas de otros países.
Autor: Lourival Augusto Tavares
Brasil
Consultor en Ingeniería de Mantenimiento
Empresa: Director nacional de ABRAMAN (Asociación Brasileña de Mantenimiento) en dos mandatos.
Correo: l.tavares@mandic.com.br
Ingeniero Electricista, formado por la Escuela Federal de Ingeniería de Rio de Janeiro, en el año de 1967. Past-Presidente del Comité Panamericano de Ingeniería de Mantenimiento. Supervisor de Mantenimiento en FURNAS – Centrales Eléctricas S.A. durante 23 años. Fue el jefe de la Asesoría Técnica de Apoyo en ITAIPU Binacional. Reconocido como “notorio saber” en mantenimiento por la Universidad Federal de Rio de Janeiro y por la Universidad Federal de Paraíba.
Dinos qué te ha parecido el artículo
Artículos recomendados
2.3. Selección del Software de Mantenimiento

Análisis de causa raíz: herramientas y técnicas simplificadas

12.1.- Cojinetes Radiales

Evaluación de riesgos: Teoría, métodos y aplicaciones

Publica tu artículo en la revista #1 de Mantenimiento Industrial
Publicar un artículo en la revista es gratis, no tiene costo.
Solo debes asegurarte que no sea un artículo comercial.
¿Qué esperas?
O envía tu artículo directo: articulos@predictiva21.com
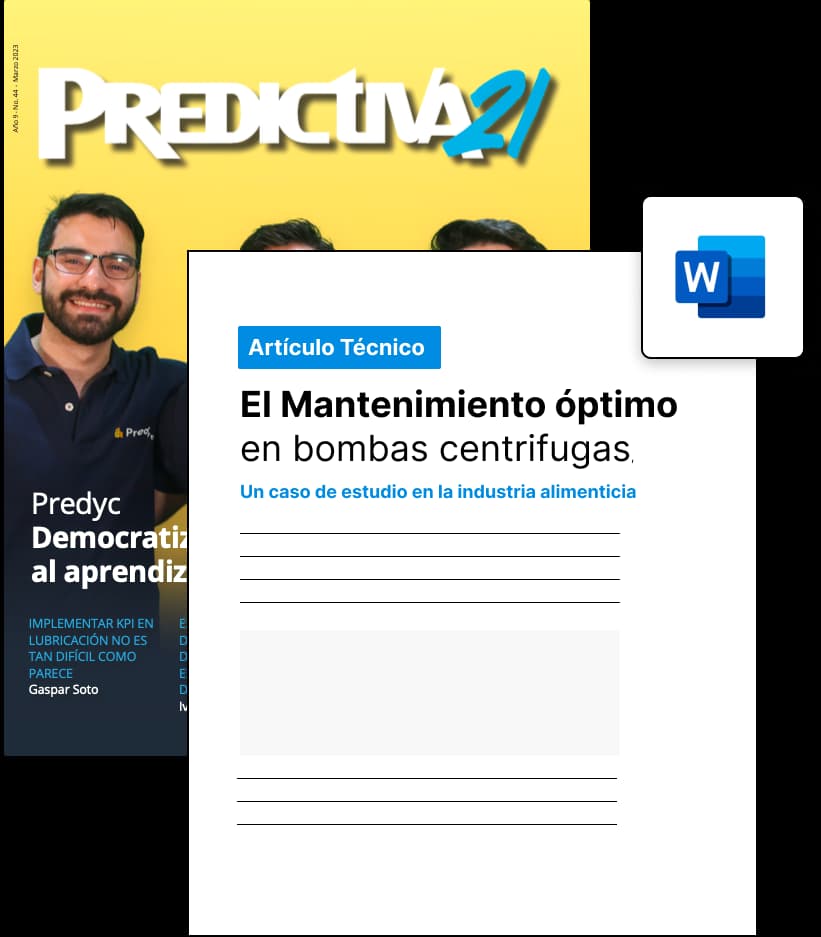
4.2. Indices Clase Mundial
Libros 31 de agosto de 2020Son llamados "índices clase mundial" aquellos que son utilizados según la misma expresión en todos los países. De los seis "índices clase mundial", cuatro son los que se refieren al Análisis de la Gestión de Equipos y dos a la Gestión de Costos, de acuerdo con las siguientes relaciones:
Tiempo Medio Entre Fallas - Relación entre el producto del número de ítems por sus tiempos de operación y el número total de fallas detectadas en esos ítems, en el periodo observado.

Este índice debe ser usado para ítems que son reparados después de la ocurrencia de una falla.
Tiempo Medio Para Reparación - Relación entre el tiempo total de intervención correctiva en un conjunto de ítems con falla y el número total de fallas detectadas en esos ítems, en el periodo observado.

Este índice debe ser usado, para ítems en los cuales el tiempo de reparación es significativo con relación al tiempo de operación.
Tiempo Medio Para la Falla - Relación entre el tiempo total de operación de un conjunto de ítems no reparables y el número total de fallas detectadas en esos ítems, en el periodo observado.

Este índice debe ser usado para ítems que son sustituidos después de la ocurrencia de una falla.
Es importante observar la diferencia conceptual existente entre los índices Tiempo medio Para la Falla y Tiempo medio Entre Fallas. El primer índice (TMPF) es calculado para ítems que NO SON reparados tras la ocurrencia de una falla, o sea, cuando fallan son sustituidos por nuevos y, en consecuencia, su tiempo de reparación es cero. El segundo índice (TMEF) es calculado para ítems que SON reparados tras la ocurrencia de la falla. Por lo tanto, los dos índices son mutuamente exclusivos, o sea, el cálculo de uno excluye el cálculo del otro, para ítems iguales.
El cálculo del Tiempo medio Entre Fallas debe estar asociado al cálculo del Tiempo medio para la Reparación. La interpretación gráfica entre estos índices, está representada en la Figura 34.
Debido a que dichos índices presentan un resultado promedio, su exactitud está asociada a la cantidad de ítems observados y al periodo de observación. Cuanto mayor sea la cantidad de datos, mayor será la precisión de la expectativa de sus valores.
En caso de no existir gran cantidad de ítems, o en el caso que se desee obtener los Tiempos Promedios Entre Fallas de cada uno, es recomendable trabajar con periodos bastante amplios de observación (cinco años o más), para garantizar la confiabilidad de los resultados.

Especial atención se debe tener en el desarrollo de programas informatizados para el cálculo de estos índices, pues puede ocurrir que, en el periodo considerado, el número de ocurrencias (fallas) sea cero, lo que llevaría a la computadora a realizar un cálculo, que daría como resultado un valor "infinito" (división entre cero), haciendo que el programa se trabe. Como sugerencia para este tipo de acontecimiento, debe ser hecha la consideración de la existencia de una falla con tiempo igual a cero, que daría un valor constante para cualquier condición de cálculo.
Disponibilidad de Equipos - Relación entre la diferencia del número de horas del periodo considerado (horas calendario) con el número de horas de intervención por el personal de mantenimiento (mantenimiento preventivo por tiempo o por estado, mantenimiento correctivo y otros servicios) para cada ítem observado y el número total de horas del periodo considerado.

La disponibilidad de un ítem representa el porcentaje del tiempo en que quedó a disponibilidad del órgano de operación para desempeñar su actividad.
El índice de Disponibilidad también es identificado como "Performance o Desempeño de Equipos" y, para ítems de operación eventual, puede ser calculado como la relación entre el tiempo total de operación de cada uno y la suma de este tiempo con el respectivo tiempo total de mantenimiento en el periodo considerado.

Este índice también puede ser calculado como la diferencia entre la unidad y la relación entre las horas de mantenimiento y la suma de esas horas con las de operación de los equipos.
Otra expresión muy común, utilizada para el cálculo de la Disponibilidad de equipos sometidos exclusivamente a la reparación de fallas es obtenida por la relación entre el Tiempo medio Entre Falla (TMEF) y su suma con el Tiempo medio para Reparación y los Tiempos Ineficaces del Mantenimiento (tiempos de preparación para desconexión y nueva conexión y tiempos de espera que pueden estar contenidos en los tiempos promedios entre fallos y de reparación).

Es posible observar que ésta es la expresión más simple ya que es obtenida a partir de la relación entre dos otros índices normalmente ya calculados.
El índice de Disponibilidad (o Performance) es de gran importancia para la gestión del mantenimiento, pues a través de éste, puede ser hecho un análisis selectivo de los equipos, cuyo comportamiento operacional está por debajo de estándares aceptables.
Para su análisis, se recomienda poner en tablas mensualmente, la disponibilidad (o performance) de los equipos seleccionados por el usuario y establecer un límite mínimo aceptable de sus valores, a partir del cual, serán hechas las selecciones para el análisis, conforme es ilustrado en la Figura 35.

En la misma tabla, pueden ser presentados los valores promedios de disponibilidad del "periodo anterior" (12 meses anteriores al actual o más) y del "periodo actual", para permitir el acompañamiento de los equipos en periodos más amplios.
Se observa que en el ejemplo presentado, fueron indicados varios equipos/mes que presentaron el índice de disponibilidad bajo, donde cuatro de ellos (los dos "after cooler", los dos compresores y el destilador #1) presentaron una disponibilidad anual inferior a los demás analizados, con pequeña variación de un periodo para otro.
En especial, el destilador #1 se destaca, por presentar una disponibilidad anual inferior a 90% en los dos periodos, aunque haya tenido un incremento de su valor en 5 puntos porcentuales.
Para los equipos que presenten resultados inferiores al mínimo aceptable, podrá ser trazado el gráfico - Figura 36, que es el punto de partida para la aplicación del llamado Modo de Análisis de Efecto de Fallas (FMEA).

Como variante de los cálculos de Disponibilidad absoluta, pueden ser obtenidas las relaciones entre los tiempos de cada tipo de intervención en el equipo (correctiva, preventiva por tiempo, preventiva por estado y otros servicios - montaje, mejora de mantenimiento, mejora de seguridad operacional etc.) y mantenimiento con relación a la suma de los tiempos gastados en esas actividades. A ese tipo de cálculo se le denomina "Disponibilidad Relativa", cuya suma de valores siempre totalizarán 100%.
El análisis de la "Disponibilidad Relativa" debe ser hecho en comparación con la "Disponibilidad Absoluta" a través del producto de una por la otra, para evitar errores de interpretación ya que eventuales valores elevados de Disponibilidad Relativa de Mantenimiento Correctivo pueden, en el cómputo general (al multiplicar por la Disponibilidad Absoluta), ser de bajo valor.
Ejemplificando:
Imaginemos que el "Horno #5" de la fábrica de San José, que opera 24 horas al día, presentó en el mes de agosto de 1 999 los siguientes tiempos totales en mantenimiento:
- Preventivo: 0,3 hr.
- Correctivo: 1,3 hr.
- Apoyo: 0,2 hr.
Se tiene que el tiempo total de mantenimiento fue de 0,3 + 1,3 +0,2 = 1,8 hr.
Por lo tanto, sus valores de disponibilidad relativa serían:
- Disponibilidad Relativa Preventiva = (0,3/1,8) x 100 = 16,67%
- Disponibilidad Relativa Correctiva = (1,3/1,8) x 100 = 72,22 %
- Disponibilidad Relativa de Apoyo = (0,2/1,8) x 100 = 11,11%
Dando la impresión, de que se tuvo una excesiva cantidad de mantenimientos correctivos.
En la realidad si son multiplicados los valores relativos por el valor de la indisponibilidad absoluta, se encontrará que las disponibilidades relativas son:
- Disponibilidad Absoluta = [1-(24 x 31 - 1,8) / 744] x 100
Disponibilidad Absoluta = [1 - (744 - 1,8) / 744] x 100 = 0,24% - Disponibilidad Relativa Preventiva = 16,67% x 0,24% = 0,04%
- Disponibilidad Relativa Correctiva = 72,22 % x 0,24% = 0,17%
- Disponibilidad Relativa de Apoyo = 11,11% x 0,24% = 0,03%
Que no causan un mayor impacto en el observador. Una característica, ya constatada por algunos gerentes del área de ejecución del mantenimiento que hacen el análisis de Disponibilidad Relativa, es que, después de la realización de una Gran Reparación (Reforma o Gran Parada), el índice de correctivos normalmente es elevado, debido al retorno del equipo a sus características normales de operación.
Una vez definidos los cuatro índices "clase mundial" para la gestión de equipos, presentamos los dos restantes, aplicados en la gestión de costos.
Costo de Mantenimiento por Facturación - Relación entre el costo total de mantenimiento y la facturación de la empresa en el periodo considerado.

Este índice es de fácil cálculo ya que los valores, tanto del numerador como los del denominador, son normalmente procesados por el órgano de contabilidad de la empresa.
Costo de Mantenimiento por el Valor de Reposición - Relación entre el costo total acumulado en el mantenimiento de un determinado equipo y el valor de compra de ese mismo equipo nuevo (valor de reposición)

Este índice debe ser calculado para los ítems más importantes de la empresa (que afectan la facturación, la calidad de los productos o servicios, la seguridad o al medio ambiente), ya que como fue indicado, es personalizado para el ítem y utiliza valores acumulados, lo que torna su procesamiento más demorado que los demás, no justificando de esta forma ser utilizado para ítems secundarios.
Su resultado debe ser acompañado por un gráfico lineal o de superficie, con la indicación de su variación, en por lo menos los doce últimos meses, conforme es ilustrado en la figura 37.

No obstante el costo total del mantenimiento, esta compuesto por cinco elementos (personal, material, terceros, depreciación y pérdida/reducción en la facturación), cada una de ellos con tres subdivisiones (costos directos, costos indirectos y costos administrativos); difícilmente es hecha esta composición, limitándose las empresas a considerar dos o tres elementos (personal, material y eventualmente terceros) y de igual manera, una o dos de sus subdivisiones (costos directos y eventualmente, costos indirectos).
Otro factor que torna los índices de costo imprecisos, es la utilización de valores contables pertenecientes al historial de los equipos, sin corrección monetaria lo que es más susceptible de originar errores en el caso de una inflación monetaria. De la misma manera, cuando la empresa utiliza un valor de referencia (dólar o mix de monedas), la imprecisión aparece, debido a la variedad de los índices de corrección, o a la no consideración de la devaluación del dólar o de otras unidades monetarias adoptadas.
Esta imprecisión no es sensible, cuando es realizado el seguimiento de los índices en la propia empresa, ya que estará cometiéndose el mismo error a lo largo del tiempo; pero puede llevar a grandes errores de interpretación, cuando estos índices son comparados con otras empresas, y mucho peor, cuando son comparados con empresas de otros países.
Autor: Lourival Augusto Tavares
Brasil
Consultor en Ingeniería de Mantenimiento
Empresa: Director nacional de ABRAMAN (Asociación Brasileña de Mantenimiento) en dos mandatos.
Correo: l.tavares@mandic.com.br
Ingeniero Electricista, formado por la Escuela Federal de Ingeniería de Rio de Janeiro, en el año de 1967. Past-Presidente del Comité Panamericano de Ingeniería de Mantenimiento. Supervisor de Mantenimiento en FURNAS – Centrales Eléctricas S.A. durante 23 años. Fue el jefe de la Asesoría Técnica de Apoyo en ITAIPU Binacional. Reconocido como “notorio saber” en mantenimiento por la Universidad Federal de Rio de Janeiro y por la Universidad Federal de Paraíba.
Dinos qué te ha parecido el artículo
Artículos recomendados
2.2.- Eje

Factores que rigen el crecimiento de los bigotes de estaño (Tesis de Springer)

12.2.- Cojinetes de Empuje

Análisis de datos mediante regresión y modelos jerárquicos / multinivel

Publica tu artículo en la revista #1 de Mantenimiento Industrial
Publicar un artículo en la revista es gratis, no tiene costo.
Solo debes asegurarte que no sea un artículo comercial.
¿Qué esperas?
O envía tu artículo directo: articulos@predictiva21.com
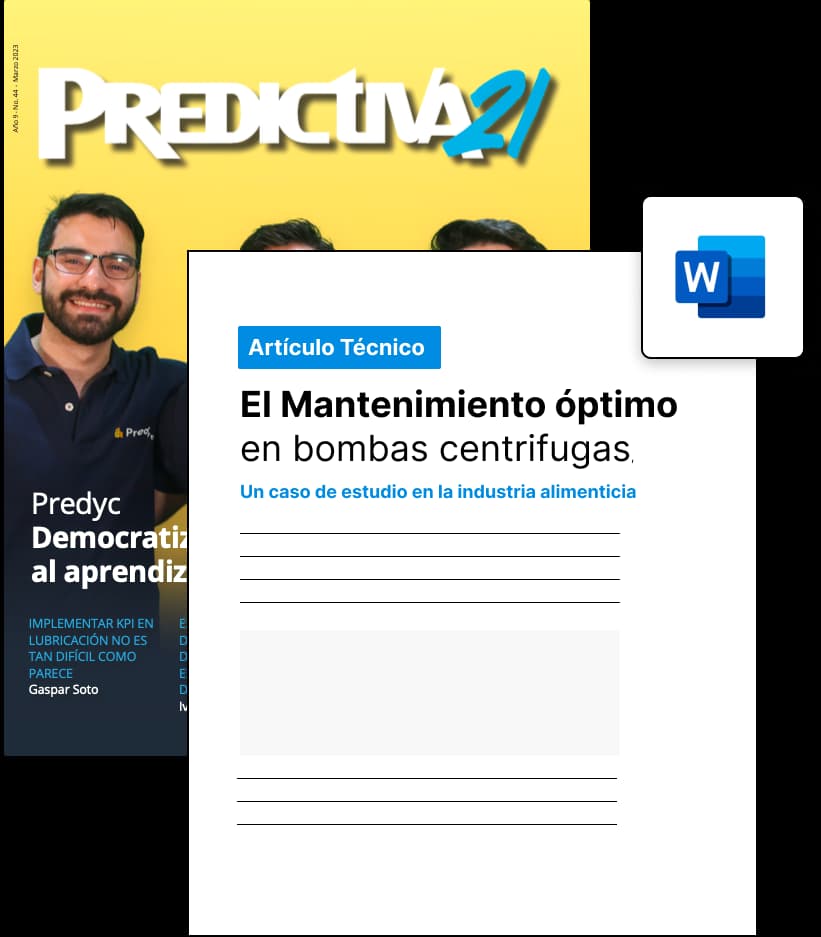