4.8. Introducción al Mantenimiento Predictivo
Libros31 de agosto de 2020
Los estudios relativos a la confiabilidad vienen recibiendo, en los últimos años, la atención de especialistas en diversos ramos de empresas, particularmente ligados al área de mantenimiento. Muchos son los trabajos desarrollados y en actual desarrollo, buscando la aplicación del llamado "Mantenimiento Predictivo" o "Mantenimiento Previsivo", o "Control Predictivo del Mantenimiento", que tiene como objetivo, ejecutar el mantenimiento preventivo en equipos en el momento exacto, en que estos interfieren en la confiabilidad del sistema.
Se entiende por Control Predictivo de Mantenimiento, la determinación del punto óptimo para la ejecución del mantenimiento preventivo en un equipo, o sea, el punto a partir del cual la probabilidad que el equipo falle, asume valores indeseables.
La determinación de ese punto trae como resultado, índices ideales de prevención de fallas, tanto en el aspecto técnico como en el económico, ya que, la intervención en el equipo, no es efectuada durante el periodo en que aún está en condiciones de prestar servicio, ni en el periodo en que sus características operativas están comprometidas.
Los estudios de determinación de ese punto, que es llamado “Punto Predictivo”, pueden ser realizados bajo dos formas, en función de las características de los equipos: Análisis Estadístico y Análisis de Síntomas.
El análisis estadístico, es aplicado cuando existe en la instalación, una cantidad apreciable de equipos o componentes con las mismas características, que puedan ser considerados como un "universo", para el desarrollo de los cálculos de probabilidades y que tienen características randómicas (aleatorias) de fallo, o sea, a los cuales no es posible hacer acompañamiento de sus variables.
El análisis de síntomas, es aplicado cuando es necesario el desarrollo de estudios para la determinación del punto predictivo, en equipos con características impares, con relación a los demás equipos instalados y en los cuales es posible hacer mediciones de sus variables.
En ambos casos, es recomendable que este trabajo sea desarrollado para equipos prioritarios de las instalaciones, ya que abarcan costos adicionales de inversión de material (instrumentos de medición) y mano de obra.
El análisis estadístico se basa en la determinación del término de vida útil, objeto del estudio en la curva de tasa de fallas con relación al tiempo, entendiéndose por tasa de fallas "la relación entre un incremento del número de fallas y el incremento correspondiente de tiempo, en cualquier instante de la vida de un equipo" y por vida útil "el periodo de tiempo, durante el cual el equipo desempeña su función con una tasa de fallas aceptable"(23).
Por simplicidad, se tratará el asunto a partir de este punto, relacionado a los equipos, sin embargo, el estudio del mantenimiento predictivo puede ser aplicado en las partes de un equipo (componentes), o en nivel más detallado, (piezas) o para un conjunto de equipos (subsistema o sistema operacional).
Tradicionalmente, la tasa de fallas representa la medida de probabilidad que un equipo que está operando presente fallas, o sea, deje de operar, cuando se incrementa un intervalo de tiempo. Para su determinación, es necesario agrupar los datos de muestreo de las ocurrencias por periodos de tiempo, determinar la "Función de Distribución Cumulativa" F(t) definida como: el número de ítems del universo que fallan en un determinado intervalo de tiempo.
La "Función Densidad de Probabilidad" F(t), definida como: la relación entre el número de equipos, que fallarán cuando se incrementa un lapso infinitesimal de tiempo, obtenida como la derivada de la función Distribución Cumulativa para un incremento de tiempo.
La relación de la primera con el simétrico de la segunda (1 - Función Densidad de Probabilidad), genera una función llamada "Probabilidad de Supervivencia", que representa la cantidad de equipos del muestreo que sobreviven, con relación al universo inicial cuando se incrementa un infinitesimal de tiempo.
Funciones según Weibull(29)
Wallodi Weibull, en sus estudios sobre la resistencia de aceros, estableció una expresión semi-empírica, con el objetivo de permitir:
- a) representar fallas típicas de partida (mortalidad infantil), fallas aleatorias y fallas debidas a desgaste;
- b) obtener parámetros significativos de la configuración de la falla a ejemplo del tiempo mínimo probable hasta la falla;
- c) la representación gráfica y simple para su aplicación.
En función de la situación en que el equipo se encuentre, con el pasar del tiempo presentará uno de los tres estándares de falla. La composición de las tres condiciones que normalmente representan las fases de vida de una instalación, equipo o pieza es conocida como "Curva del Ciclo de Vida" - Figura 56.

La elección apropiada de ß en la distribución de Weibull, permite su uso para representar una larga banda de aplicaciones, incluyendo tanto las fortuitas, que se comportan según un Exponente Negativo, como las que se comportan aproximadamente según una Distribución Normal. No obstante la experiencia, haya mostrado que la función de Weibull, puede ser usada para una gran mayoría de modelos de falla, es esencial notar que se trata de una función promedio empírica y puede no ser capaz de representar, algunas distribuciones particulares encontradas en la práctica.
El valor ß = 1 (tasa de fallas constante) puede ser indicativo, que modos múltiplos de falla existente o, que los datos de los tiempos para fallas son sospechosos. Este es frecuentemente el caso de sistemas, en los cuales diferentes componentes tienen diferentes edades y el tiempo individual de operación de los componentes no está disponible. Una tasa de fallas constante, puede también indicar que las fallas son debidas a eventos externos, tales como el uso indebido del equipo o deficiencia de las intervenciones para mantenimiento.
NOTA: En la presentación de este tópico transcribimos el trabajo "Mantenimiento - Conceptos Básicos" del Ingeniero Haroldo Rittmeister(30).
En los conceptos presentados a continuación, está siendo utilizada por conveniencia, como referencia una pieza del equipo, sin embargo, esos conceptos son válidos igualmente si son aplicados: al Sistema Operacional, Equipo o Componente.
Especificación de origen y degeneración
Toda pieza es caracterizada, por valores de grandezas mensurables y por procesos específicos, establecidos en su proyecto, fabricación o instalación. Al conjunto de valores que definen la condición inicial de la pieza, se llama Especificación de Origen identificada por {E0}.
La utilización y/o exposición de la pieza a agentes externos, hace que {E0} se transforme en {E}, o sea:

La ocurrencia de ∆ diferente de cero, significa la degeneración de la pieza y su valor podrá determinar, una condición inaceptable de utilización.
Vida útil
Por simplicidad se considerará apenas uno de los elementos "E" del conjunto "{E}" y la variación de "E" en función del tiempo, representa la curva de degeneración "E(t)". Por conveniencia está siendo utilizado como variable independiente el tiempo (t), sin embargo, podrían ser utilizadas, según el caso a estudiar, otras variables como Toneladas, Litros, Kw-hora, Ciclos etc.
Sea "Eu" un valor fijado por un criterio técnico económico tal que:
- Mientras "E" sea mayor que "Eu", tenemos la condición técnico económica aceptable de utilización;
- Cuando "E" sea menor o igual a "Eu", tenemos la condición técnico - económica inaceptable de utilización.
La intersección de la curva de degeneración con el valor de "Eu" , determina la vida útil de la pieza y todo el concepto, está basado en curvas de degeneración, donde "E(t)" es menor o igual a "E0 ". Para casos en que "E(t)" es mayor o igual a "E0 ", el tratamiento sería semejante y no alteraría los conceptos emitidos. Figura 57.

En el mantenimiento preventivo convencional se ejecutan acciones correspondientes a los pasajes de las condiciones:

La ocurrencia de valores de "E" menor o igual a "Eu", caracteriza al Mantenimiento Correctivo y esto puede ser debido a una de las dos situaciones siguientes.
- a) inexistencia de anomalía brusca en la curva de degeneración, sin embargo, el valor de "E" alcanza o queda menor que el valor de "Eu" y consecuentemente el valor de "te" queda igual o mayor que el valor de "tu".
- b) existencia de anomalía brusca en la curva de degeneración que causa que el valor "E" caiga a valores inferiores a "Eu" en un tiempo "te" menor que el valor de "tu".
Inspección predictiva / Mantenimiento predictivo
La inspección convencional determina apenas los valores "E(t)" y si fueran hechas de forma sucesiva, permiten la extrapolación para la determinación de "tu". Muchas veces la pieza no es accesible y hay necesidad de desmontaje, con la interrupción de la producción.
En la Inspección Predictiva, los valores de "E(t)" son medidos a través de sensores adecuados sin interrupción de la producción (monitoreo). Esos valores reciben tratamiento matemático, con la determinación del mecanismo de degeneración, con el objetivo de prever la ocurrencia de una anomalía en la curva de degeneración y la optimización de los tiempos "tpi".
La determinación de las curvas de degeneración de las diversas variables, permitirá determinar los tiempos "tu" que indicarán las mejores épocas para la intervención en el equipo. Las intervenciones, según esta técnica de análisis, caracterizan el Mantenimiento Predictivo que tiene por objetivo:
- 1 - Aumentar los valores "E0 ", " E' '', " E" " etc.
- 2 - Aumentar los valores "t0i" por alteración en el desarrollo de la curva "E(t)”.
Ese tipo de mantenimiento empieza en las fases de especificación, proyecto, fabricación e instalación logrando:
- - La minimización de los costos de mantenimiento preventivo y correctivo;
- - La maximización de la eficiencia del mantenimiento.
Cursos recomendados




%252FImagen%252FRAMPREDYC-1730060420837.webp%3Falt%3Dmedia%26token%3D2634a7f0-988e-4022-b91f-382503e6e9db&w=3840&q=75)



Referencias
- (23) ABNT – TB-116. Confiabilidade de Equipamentos e Componentes Eletrônicos. Termos Básicos e Definições – 1975
- (29) Generating Station Maintenance. Commonwealth Edison Company – Chicago. Frank Blake, Richard E. Vanderway, Haward Glefke. January – 1974
- (30) I Seminário de Manutenção Metro-Ferroviária. Manutenção Preventiva “Versus” Manutenção Corretiva. Eduardo de Santana Seixas. Rio de Janeiro – 1986
Autor: Lourival Augusto Tavares
Brasil
Consultor en Ingeniería de Mantenimiento
Empresa: Director nacional de ABRAMAN (Asociación Brasileña de Mantenimiento) en dos mandatos.
Correo: l.tavares@mandic.com.br
Ingeniero Electricista, formado por la Escuela Federal de Ingeniería de Rio de Janeiro, en el año de 1967. Past-Presidente del Comité Panamericano de Ingeniería de Mantenimiento. Supervisor de Mantenimiento en FURNAS – Centrales Eléctricas S.A. durante 23 años. Fue el jefe de la Asesoría Técnica de Apoyo en ITAIPU Binacional. Reconocido como “notorio saber” en mantenimiento por la Universidad Federal de Rio de Janeiro y por la Universidad Federal de Paraíba.
Dinos qué te ha parecido el artículo
Artículos recomendados
2.3. Selección del Software de Mantenimiento

Métodos Estadísticos para datos confiables

1.2.- ¿Qué son las Bombas Centrífugas?

6.1.- Como se Determina el NPSHA

Publica tu artículo en la revista #1 de Mantenimiento Industrial
Publicar un artículo en la revista es gratis, no tiene costo.
Solo debes asegurarte que no sea un artículo comercial.
¿Qué esperas?
O envía tu artículo directo: articulos@predictiva21.com
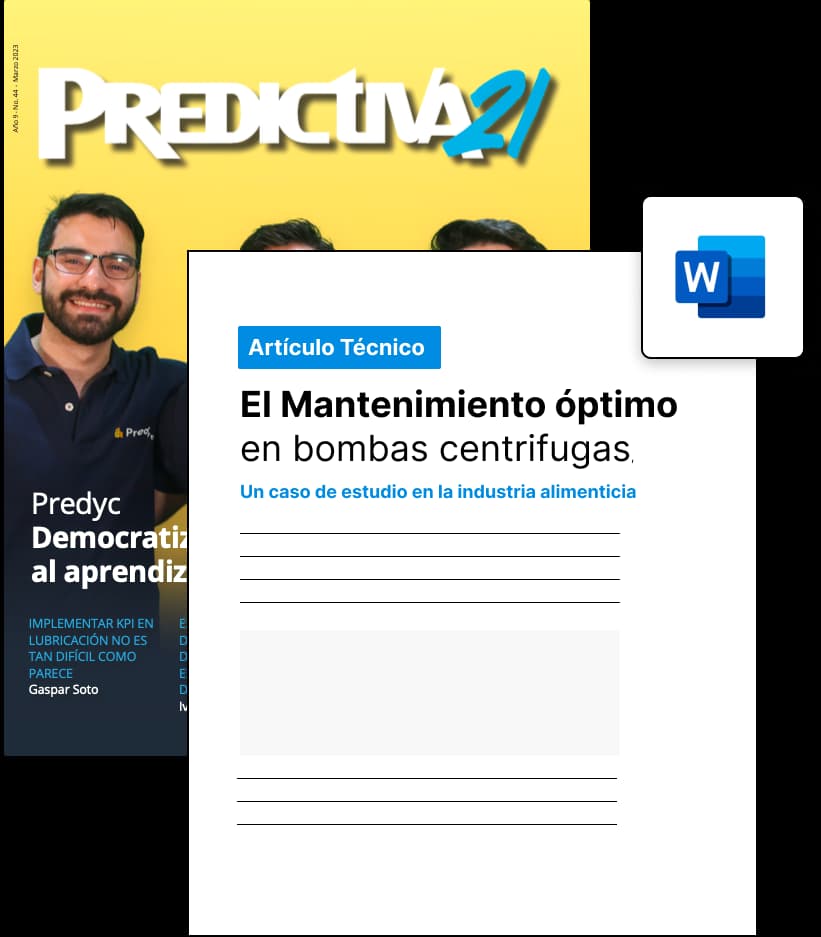
4.8. Introducción al Mantenimiento Predictivo
Libros 31 de agosto de 2020Los estudios relativos a la confiabilidad vienen recibiendo, en los últimos años, la atención de especialistas en diversos ramos de empresas, particularmente ligados al área de mantenimiento. Muchos son los trabajos desarrollados y en actual desarrollo, buscando la aplicación del llamado "Mantenimiento Predictivo" o "Mantenimiento Previsivo", o "Control Predictivo del Mantenimiento", que tiene como objetivo, ejecutar el mantenimiento preventivo en equipos en el momento exacto, en que estos interfieren en la confiabilidad del sistema.
Se entiende por Control Predictivo de Mantenimiento, la determinación del punto óptimo para la ejecución del mantenimiento preventivo en un equipo, o sea, el punto a partir del cual la probabilidad que el equipo falle, asume valores indeseables.
La determinación de ese punto trae como resultado, índices ideales de prevención de fallas, tanto en el aspecto técnico como en el económico, ya que, la intervención en el equipo, no es efectuada durante el periodo en que aún está en condiciones de prestar servicio, ni en el periodo en que sus características operativas están comprometidas.
Los estudios de determinación de ese punto, que es llamado “Punto Predictivo”, pueden ser realizados bajo dos formas, en función de las características de los equipos: Análisis Estadístico y Análisis de Síntomas.
El análisis estadístico, es aplicado cuando existe en la instalación, una cantidad apreciable de equipos o componentes con las mismas características, que puedan ser considerados como un "universo", para el desarrollo de los cálculos de probabilidades y que tienen características randómicas (aleatorias) de fallo, o sea, a los cuales no es posible hacer acompañamiento de sus variables.
El análisis de síntomas, es aplicado cuando es necesario el desarrollo de estudios para la determinación del punto predictivo, en equipos con características impares, con relación a los demás equipos instalados y en los cuales es posible hacer mediciones de sus variables.
En ambos casos, es recomendable que este trabajo sea desarrollado para equipos prioritarios de las instalaciones, ya que abarcan costos adicionales de inversión de material (instrumentos de medición) y mano de obra.
El análisis estadístico se basa en la determinación del término de vida útil, objeto del estudio en la curva de tasa de fallas con relación al tiempo, entendiéndose por tasa de fallas "la relación entre un incremento del número de fallas y el incremento correspondiente de tiempo, en cualquier instante de la vida de un equipo" y por vida útil "el periodo de tiempo, durante el cual el equipo desempeña su función con una tasa de fallas aceptable"(23).
Por simplicidad, se tratará el asunto a partir de este punto, relacionado a los equipos, sin embargo, el estudio del mantenimiento predictivo puede ser aplicado en las partes de un equipo (componentes), o en nivel más detallado, (piezas) o para un conjunto de equipos (subsistema o sistema operacional).
Tradicionalmente, la tasa de fallas representa la medida de probabilidad que un equipo que está operando presente fallas, o sea, deje de operar, cuando se incrementa un intervalo de tiempo. Para su determinación, es necesario agrupar los datos de muestreo de las ocurrencias por periodos de tiempo, determinar la "Función de Distribución Cumulativa" F(t) definida como: el número de ítems del universo que fallan en un determinado intervalo de tiempo.
La "Función Densidad de Probabilidad" F(t), definida como: la relación entre el número de equipos, que fallarán cuando se incrementa un lapso infinitesimal de tiempo, obtenida como la derivada de la función Distribución Cumulativa para un incremento de tiempo.
La relación de la primera con el simétrico de la segunda (1 - Función Densidad de Probabilidad), genera una función llamada "Probabilidad de Supervivencia", que representa la cantidad de equipos del muestreo que sobreviven, con relación al universo inicial cuando se incrementa un infinitesimal de tiempo.
Funciones según Weibull(29)
Wallodi Weibull, en sus estudios sobre la resistencia de aceros, estableció una expresión semi-empírica, con el objetivo de permitir:
- a) representar fallas típicas de partida (mortalidad infantil), fallas aleatorias y fallas debidas a desgaste;
- b) obtener parámetros significativos de la configuración de la falla a ejemplo del tiempo mínimo probable hasta la falla;
- c) la representación gráfica y simple para su aplicación.
En función de la situación en que el equipo se encuentre, con el pasar del tiempo presentará uno de los tres estándares de falla. La composición de las tres condiciones que normalmente representan las fases de vida de una instalación, equipo o pieza es conocida como "Curva del Ciclo de Vida" - Figura 56.

La elección apropiada de ß en la distribución de Weibull, permite su uso para representar una larga banda de aplicaciones, incluyendo tanto las fortuitas, que se comportan según un Exponente Negativo, como las que se comportan aproximadamente según una Distribución Normal. No obstante la experiencia, haya mostrado que la función de Weibull, puede ser usada para una gran mayoría de modelos de falla, es esencial notar que se trata de una función promedio empírica y puede no ser capaz de representar, algunas distribuciones particulares encontradas en la práctica.
El valor ß = 1 (tasa de fallas constante) puede ser indicativo, que modos múltiplos de falla existente o, que los datos de los tiempos para fallas son sospechosos. Este es frecuentemente el caso de sistemas, en los cuales diferentes componentes tienen diferentes edades y el tiempo individual de operación de los componentes no está disponible. Una tasa de fallas constante, puede también indicar que las fallas son debidas a eventos externos, tales como el uso indebido del equipo o deficiencia de las intervenciones para mantenimiento.
NOTA: En la presentación de este tópico transcribimos el trabajo "Mantenimiento - Conceptos Básicos" del Ingeniero Haroldo Rittmeister(30).
En los conceptos presentados a continuación, está siendo utilizada por conveniencia, como referencia una pieza del equipo, sin embargo, esos conceptos son válidos igualmente si son aplicados: al Sistema Operacional, Equipo o Componente.
Especificación de origen y degeneración
Toda pieza es caracterizada, por valores de grandezas mensurables y por procesos específicos, establecidos en su proyecto, fabricación o instalación. Al conjunto de valores que definen la condición inicial de la pieza, se llama Especificación de Origen identificada por {E0}.
La utilización y/o exposición de la pieza a agentes externos, hace que {E0} se transforme en {E}, o sea:

La ocurrencia de ∆ diferente de cero, significa la degeneración de la pieza y su valor podrá determinar, una condición inaceptable de utilización.
Vida útil
Por simplicidad se considerará apenas uno de los elementos "E" del conjunto "{E}" y la variación de "E" en función del tiempo, representa la curva de degeneración "E(t)". Por conveniencia está siendo utilizado como variable independiente el tiempo (t), sin embargo, podrían ser utilizadas, según el caso a estudiar, otras variables como Toneladas, Litros, Kw-hora, Ciclos etc.
Sea "Eu" un valor fijado por un criterio técnico económico tal que:
- Mientras "E" sea mayor que "Eu", tenemos la condición técnico económica aceptable de utilización;
- Cuando "E" sea menor o igual a "Eu", tenemos la condición técnico - económica inaceptable de utilización.
La intersección de la curva de degeneración con el valor de "Eu" , determina la vida útil de la pieza y todo el concepto, está basado en curvas de degeneración, donde "E(t)" es menor o igual a "E0 ". Para casos en que "E(t)" es mayor o igual a "E0 ", el tratamiento sería semejante y no alteraría los conceptos emitidos. Figura 57.

En el mantenimiento preventivo convencional se ejecutan acciones correspondientes a los pasajes de las condiciones:

La ocurrencia de valores de "E" menor o igual a "Eu", caracteriza al Mantenimiento Correctivo y esto puede ser debido a una de las dos situaciones siguientes.
- a) inexistencia de anomalía brusca en la curva de degeneración, sin embargo, el valor de "E" alcanza o queda menor que el valor de "Eu" y consecuentemente el valor de "te" queda igual o mayor que el valor de "tu".
- b) existencia de anomalía brusca en la curva de degeneración que causa que el valor "E" caiga a valores inferiores a "Eu" en un tiempo "te" menor que el valor de "tu".
Inspección predictiva / Mantenimiento predictivo
La inspección convencional determina apenas los valores "E(t)" y si fueran hechas de forma sucesiva, permiten la extrapolación para la determinación de "tu". Muchas veces la pieza no es accesible y hay necesidad de desmontaje, con la interrupción de la producción.
En la Inspección Predictiva, los valores de "E(t)" son medidos a través de sensores adecuados sin interrupción de la producción (monitoreo). Esos valores reciben tratamiento matemático, con la determinación del mecanismo de degeneración, con el objetivo de prever la ocurrencia de una anomalía en la curva de degeneración y la optimización de los tiempos "tpi".
La determinación de las curvas de degeneración de las diversas variables, permitirá determinar los tiempos "tu" que indicarán las mejores épocas para la intervención en el equipo. Las intervenciones, según esta técnica de análisis, caracterizan el Mantenimiento Predictivo que tiene por objetivo:
- 1 - Aumentar los valores "E0 ", " E' '', " E" " etc.
- 2 - Aumentar los valores "t0i" por alteración en el desarrollo de la curva "E(t)”.
Ese tipo de mantenimiento empieza en las fases de especificación, proyecto, fabricación e instalación logrando:
- - La minimización de los costos de mantenimiento preventivo y correctivo;
- - La maximización de la eficiencia del mantenimiento.
Cursos recomendados




%252FImagen%252FRAMPREDYC-1730060420837.webp%3Falt%3Dmedia%26token%3D2634a7f0-988e-4022-b91f-382503e6e9db&w=3840&q=75)



Referencias
- (23) ABNT – TB-116. Confiabilidade de Equipamentos e Componentes Eletrônicos. Termos Básicos e Definições – 1975
- (29) Generating Station Maintenance. Commonwealth Edison Company – Chicago. Frank Blake, Richard E. Vanderway, Haward Glefke. January – 1974
- (30) I Seminário de Manutenção Metro-Ferroviária. Manutenção Preventiva “Versus” Manutenção Corretiva. Eduardo de Santana Seixas. Rio de Janeiro – 1986
Autor: Lourival Augusto Tavares
Brasil
Consultor en Ingeniería de Mantenimiento
Empresa: Director nacional de ABRAMAN (Asociación Brasileña de Mantenimiento) en dos mandatos.
Correo: l.tavares@mandic.com.br
Ingeniero Electricista, formado por la Escuela Federal de Ingeniería de Rio de Janeiro, en el año de 1967. Past-Presidente del Comité Panamericano de Ingeniería de Mantenimiento. Supervisor de Mantenimiento en FURNAS – Centrales Eléctricas S.A. durante 23 años. Fue el jefe de la Asesoría Técnica de Apoyo en ITAIPU Binacional. Reconocido como “notorio saber” en mantenimiento por la Universidad Federal de Rio de Janeiro y por la Universidad Federal de Paraíba.
Dinos qué te ha parecido el artículo
Artículos recomendados
Confiabilidad de los Sistemas y Prevención de Fallas

5.4.- Cebado con Eyectores

Hornos de Fuego Directo

1.1.- ¿Qué es una bomba?

Publica tu artículo en la revista #1 de Mantenimiento Industrial
Publicar un artículo en la revista es gratis, no tiene costo.
Solo debes asegurarte que no sea un artículo comercial.
¿Qué esperas?
O envía tu artículo directo: articulos@predictiva21.com
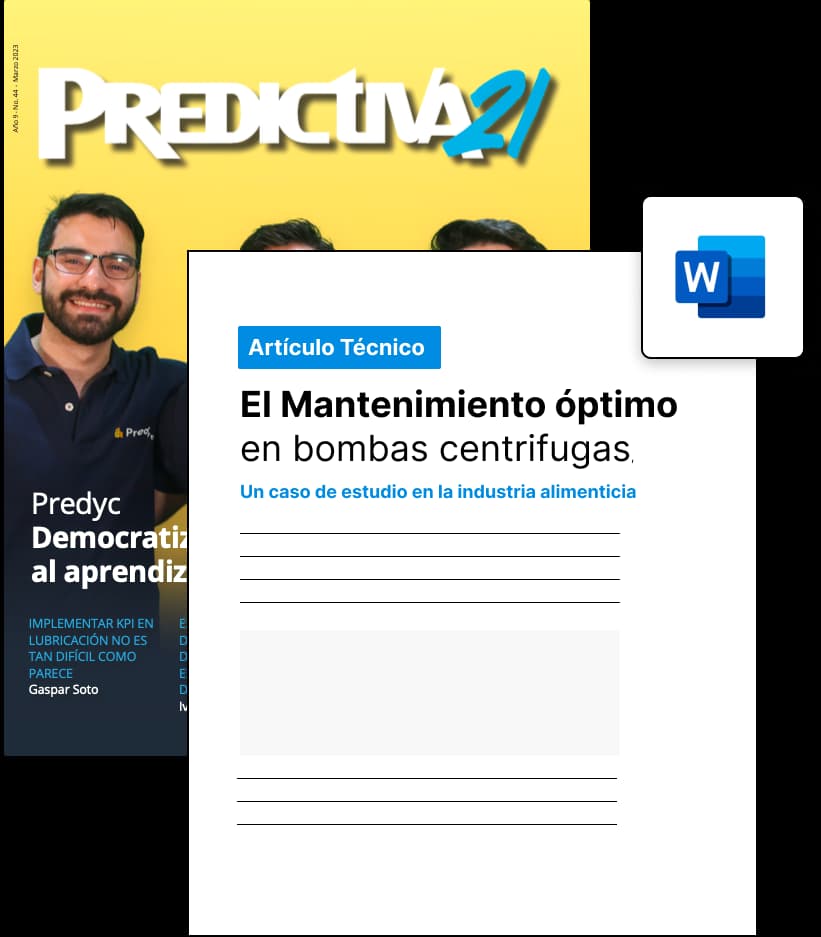