9.8 Técnicas que Monitorean la Performance
Articulo9 de noviembre de 2021
El monitoreo del comportamiento o performance de una máquina y/o de sus componentes es uno de los métodos más directos de monitorear su condición. La principal ventaja de estas técnicas es que es muy difícil una falsa interpretación de ellas, es decir, cualquier desviación de las performances debe revelar la existencia de un problema real. Sus principales desventajas, cuando se monitorea la performance de una máquina completa, es que tiende a ser un método más bien insensitivo de detectar fallas incipientes. Deberán ocurrir daños apreciables en algunos componentes individuales de la máquina antes que ello se traduzca en efectos medibles en su Performance.
Además del monitoreo de la Performance de la máquina total, se puede vigilar la condición mecánica de algunos de sus componentes monitoreando cómo realizan su función. Por ejemplo:
- Un filtro de aire sucio puede ser detectado controlando si se produce un aumento en la caída de presión a través del filtro.
- En un compresor la temperatura del flujo de aceite en los sellos puede ser un indicativo de su desgaste. El desgaste del sello debería producir un mayor flujo de aceite y bajar su temperatura.
- Una tobera doblada en una turbina de gas puede ser detectada con el aumento de la temperatura de salida del gas.
- Problemas asociados con las aletas en un sistema de enfriamiento pueden ser detectados por el aumento de la caída de presión en la línea.
Técnicas que Monitorean el Fluido Lubricante y sus Residuos
Estas técnicas podemos clasificarlas en dos grupos:
- Técnicas que analizan la condición del fluido lubricante / refrigerante.
- Técnicas que analizan las partículas o residuos en el fluido lubricante / refrigerante.
Para la implementación de las primeras técnicas, los índices más usados para determinar la condición del fluido lubricante son:
• Su aspecto. Un color oscuro en el lubricante es indicativo de deterioro y requiere hacer un análisis de él. Un olor fuerte en el fluido lubricante puede indicar una fuga excesiva. Por ejemplo, analizando el aumento de temperatura en un compresor centrífugo se observó que el aceite tenía fuerte olor. Un sello dañado permitía la formación de sulfuro de hierro, el cual restringía el flujo de aceite en el descanso y éste se calentaba. El olor dio la clave. Reparado el sello se solucionó el problema.
• Contenido de agua (ASTM D95). Para la mayoría de las máquinas no debería exceder 100 ppm. en el aceite lubricante.
• Número de acidez (mg KOH/gr aceite, ASTM D664). Para la mayoría de las aplicaciones no debería exceder 0.25. Si es mayor podría ser indicativo de fuga en los sellos.
• Viscosidad. Tal vez es la característica más importante del aceite lubricante. Siempre debe estar en los rangos especificados por el constructor de la máquina. Un aumento de la viscosidad puede indicar, por ejemplo, puntos calientes dentro de la máquina.
• Número base total, TBN, es una media ponderada de la alcalinidad, detergencia y dispersibilidad. Disminución del TBN en un motor a combustión puede indicar por ejemplo mala combustión, falla de las válvulas de salida o alta contaminación en agua.
• Oxidación.
• Punto de inflamación.
El monitoreo de las partículas o residuos en el lubricante permite obtener una indicación de la condición de los diferentes componentes de la máquina que están en contacto con el lubricante. Para muchos fallos de las superficies lubricadas que son de naturaleza progresiva más que repentina, con el uso de estas técnicas también se puede obtener un aviso de fallo con bastante anticipación.
Para el monitoreo de las partículas o residuos en el aceite, existen varios métodos, dependiendo del tamaño de las partículas que se desean analizar:
- La espectrometría metálica analiza tamaño de partículas de hasta 10 ó 15 um.
- La ferrografía o examinación microscópica analiza tamaño de partícula entre unos 2 y 200 um.
- Los detectores de astilla (chip) analizan tamaño de partículas entre unos 15 a 700 um.
- La evaluación de filtros y las pantallas visuales analizan tamaños de partículas entre unos 50 y 1500 um.
Aunque la selección de parámetros a monitorear depende del tipo de equipo involucrado se podría sugerir las siguientes guías generales:
• Llevar tendencia en lo posible de aquellas propiedades físicas del aceite que entregan crucial información respecto a la capacidad de lubricar del fluido: viscosidad, TBN, oxidación.
• Llevar tendencia de todos los desgastes de metales que se detectan en la zona lubricada.
• No es necesario llevar tendencias de los aditivos metálicos.
• Contaminantes. Dentro del grupo de contaminantes metálicos típicamente se tiene los que indican suciedad (silicio) o los que indican elementos refrigerantes (sodio y boro) en el sistema lubricante. Otros contaminantes comúnmente encontrados son combustibles, hollín e insolubles. En muchas situaciones no se permite ni una ligera cantidad de contaminante; sin embargo, si el sistema puede tolerar un cierto nivel de contaminación, es aconsejable llevar una tendencia.
• Partículas ferromagnéticas: En general los ferrógrafos de lectura directa entregan cantidad de partículas pequeñas (menores de 2 um.), de partículas grandes (sobre 3 um.) y de la concentración total de partículas. Puede ser beneficioso en algunos casos llevar la tendencia de estas cantidades.
• La concentración total de partículas es más una indicación de contaminación que de desgaste. En general es más conveniente llevar tendencia de ello, en sistemas tales como los hidráulicos, donde la limpieza del lubricante es crítica.
Principales Técnicas de Inspección Visual
Objetivos | Técnicas a usar |
Iluminar partes internas oscuras | Sonda de luz |
Mejorar accesos a zonas nominalmente inaccesibles | Boroscopio |
Obtener muestras en zonas normalmente inaccesibles | Endoscopio |
Realizar un agrandamiento | Lupas, boroscopios, televisión |
Congelar el movimiento de componentes rotativos | Estroboscopio |
Resaltar la existencia de pequeñas grietas superficiales | Tintas penetrantes |
Extender el rango visual más allá del rango humano | Termografía infrarroja, Examen por rayos X o gamma |
Visualizar Temperaturas superficiales | Pinturas termográficas |
Ejemplos de monitoreo de performance de equipos
Método de monitoreo de la performance | Ejemplo |
Medición de la cantidad de flujo salida | Cambios en el flujo medio de salida bajo condiciones estándar |
Medición de la cantidad del producto de salida de la máquina | Cambios en la tolerancia de fabricación en una máquina, herramienta |
Medición de la razón entre la entrada y la salida de la máquina | Razón entre el consumo de combustible y la salida eléctrica de un generador diesel |
Razón entre la medición simultánea de dos variables de salida | Razón entre el flujo y el aumento de presión en una bomba |
Naturaleza de los residuos de desgaste generados por diferentes elementos de las máquinas
Tipo de Elemento | Ejemplo típico | Naturaleza de los residuos de desgaste asociados con fallas de elemento |
Elementos móviles en los cuales la carga esta concentrada en el área de contacto deslizante | Rodamientos, dientes de engranaje, leva y seguidor | Partículas ferrosas de varias formas y tamaños, generalmente fornidas y de alrededor de 1 mm. De tamaño (Fatiga de la superficie) |
Elementos móviles con la carga concentrada en una pequeña área | Anillos de pistón, cilindros, guías, acoplamianto de engranajes | Escamas ferrosas menores de 0,15 mm y de partículas finas de óxido de hierro |
Elementos móviles con la carga repartida sobre una gran área | Descansos planos, pistones, cilindros | Escamas y partículas ferrosas y no ferrosas muy pequeñas |
Sellos que deben operar con juego | Laberintos | Astillas metálicas generalmente grande, sobre un 1 mm de longitud |
Elementos fijos unos a otros, pero que desarrollan un ligero movimiento relativo entre ellos | Juntas apernadas, ajuste por interferencia | Residuos de frotamiento de partículas finas de óxido de hierro |
Técnicas de Mantenimiento Predictivo Industrial Basadas en Sistemas Expertos
En el campo del mantenimiento predicativo los sistemas expertos se utilizan fundamentalmente como herramientas de diagnóstico. Se trata de que el programa pueda determinar en cada momento el estado de funcionamiento de sistemas complejos, anticipándose a los posibles incidentes que pudieran acontecer. Así, usando un modelo computacional del razonamiento de un experto humano, proporciona los mismos resultados que alcanzaría dicho experto.
Figura 1. Sistema experto de mantenimiento
Estrategia de Mantenimiento
Un aspecto básico en la selección del tipo de mantenimiento a utilizar, son las características de los fallos que se espera que puedan ocurrir. A este respecto podemos clasificar los fallos en tres categorías.
- Fallos repentinos: que ocurren en un tiempo extremadamente corto.
- Fallos de desarrollo progresivo: en un intervalo de tiempo uniforme.
- Fallos de desarrollo progresivo: en un intervalo de tiempo aleatorio.
Los principios tanto del mantenimiento preventivo, como del mantenimiento predictivo, asumen que el fallo se va a desarrollar progresivamente. El mantenimiento preventivo asume además, que el fallo se desarrolla razonablemente en forma uniforme para justificar los intervalos regulares de intervención. El mantenimiento predictivo asume a su vez un desarrollo progresivo del fallo para justificar el concepto de tendencia. Aunque lo anterior es lo que sucede generalmente, hay situaciones en que fallos repentinos tienden a ocurrir con mayor frecuencia que los fallos progresivos.
En los molinos de carbón que producen combustible pulverizado para centrales de energía, la ocasional ingestión de piezas de metal o rocas muy duras, puede causar repentinas roturas de los elementos internos del molino. Esto puede ocurrir más frecuentemente que los fallos progresivos que ocurren en la transmisión. Cuando sucede, la única solución es utilizar una estrategia de mantenimiento reactivo. Cualquier programa de mantenimiento basado en intervalos regulares de tiempo sería ilógico.
Otro ejemplo donde el mantenimiento correctivo es adecuado, son los sistemas digitales electrónicos, los cuáles operan fundamentalmente en un modo on/off y por consiguiente, debería esperarse que fallaran de una manera repentina o intermitente, más que de una manera progresiva.
Hay en cambio situaciones donde un mantenimiento preventivo regular es la mejor estrategia, tal como cuando el deterioro de elementos en la máquina tienen un desarrollo progresivo regularmente uniforme. Ejemplos típicos son los cambios de filtro o los cambios de elementos de sacrificio para el control de la corrosión.
A pesar de los casos de excepción citados precedentemente, la tendencia general actual en mantenimiento es hacia una estrategia basada en la condición de la máquina. Sin embargo, debe tenerse presente que la estrategia de mantenimiento más eficaz será un desarrollo combinado y ponderado de un programa correctivo / preventivo / predictivo.
Otro aspecto básico a considerar en la selección de una estrategia de mantenimiento es de tipo económico. Para establecer si es económicamente ventajosa utilizar una estrategia de mantenimiento predictivo para una o más máquinas o elementos de ellos, deberá efectuarse un balance de costes / ahorros.
Sin embargo, evaluar los posibles ahorros que se obtendrían en la implementación de una estrategia de mantenimiento predictivo es difícil. Por ejemplo, si no ha producido un fallo catastrófico en una máquina es difícil evaluar lo que se ahorraría si se puede evitar que ella se produzca.
Una forma en la que se podría intentar evaluar los ahorros que se obtendrían al implementar una estrategia de mantenimiento predictivo es confeccionando una lista de las detenciones producidos en los últimos años en conjunto con sus causas.
Con esto se podría determinar:
• Cuáles intervenciones podrían haber resultado más económicas si se hubiera detectado, el fallo en una etapa más incipiente, evitando que la máquina funcionara hasta la rotura.
• Qué averías podrían haber sido reparadas más rápidamente si se hubiese conocido bien, antes de abrir la máquina, cuál era el elemento defectuoso.
• Cuáles serían los ahorros si después de efectuado un mantenimiento se controla la calidad del mantenimiento realizado. Para esto se evalúa la condición mecánica en que quedó la máquina a través del análisis de las mediciones realizadas inmediatamente después de la reparación. Las técnicas actuales del mantenimiento predictivo permiten verificar si un elemento reemplazado quedó disminuido debido a un procedimiento de montaje inadecuado (por ejemplo, un rodamiento con sus pistas de rodadura sin dientes). Evalúe así las economías que se obtendrían por ese concepto si los elementos reemplazables de las máquinas de su planta duraran lo especificado en las normas bajo los cuales fueron compradas las máquinas. El coste del mantenimiento debe considerar: Costes directos (recambio, materiales, mano de obra, etc.), costes de movilización de recambio, costes de lucro cesante o pérdidas por no producción, costes por falta de calidad del producto.
Dinos qué te ha parecido el artículo
Artículos recomendados
Podcast de Gestión de Activos

Herramientas para la Auditoria y Certificación en Gestión de Activos. Pas 55 - Pam - Sam e ISO 55001

Evaluación de Calidad de Potencia como Estrategia de Mantenimiento Predictivo

¿De que hablamos cuando hablamos de "Estratégico"?

Publica tu artículo en la revista #1 de Mantenimiento Industrial
Publicar un artículo en la revista es gratis, no tiene costo.
Solo debes asegurarte que no sea un artículo comercial.
¿Qué esperas?
O envía tu artículo directo: articulos@predictiva21.com
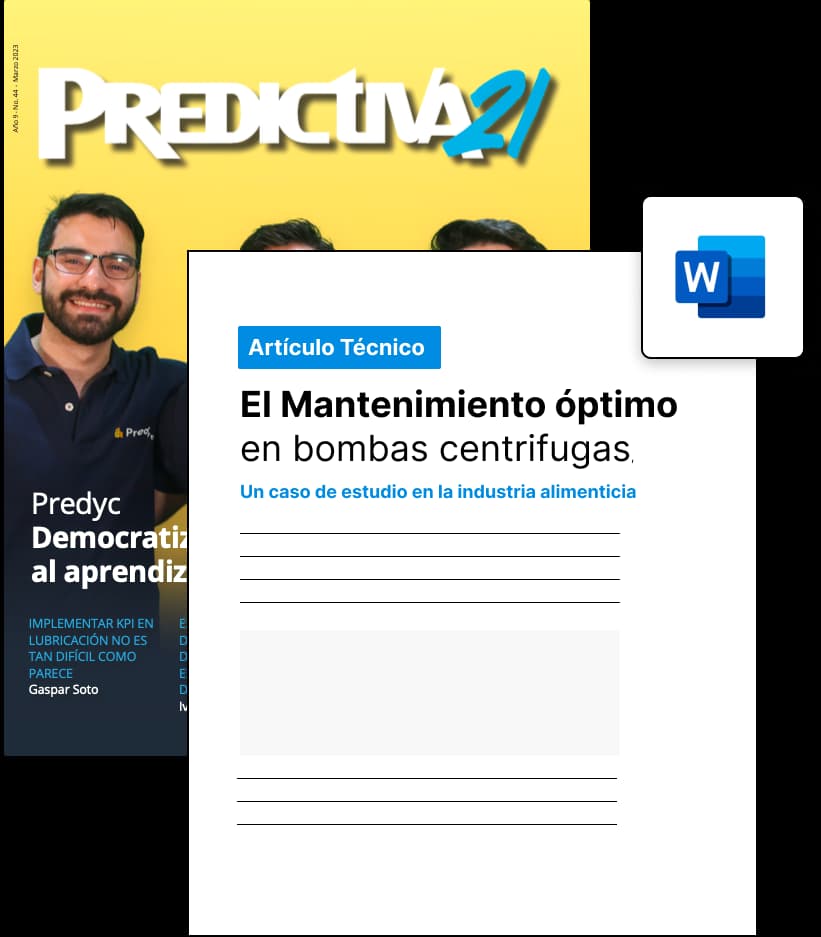
9.8 Técnicas que Monitorean la Performance
Articulo 9 de noviembre de 2021El monitoreo del comportamiento o performance de una máquina y/o de sus componentes es uno de los métodos más directos de monitorear su condición. La principal ventaja de estas técnicas es que es muy difícil una falsa interpretación de ellas, es decir, cualquier desviación de las performances debe revelar la existencia de un problema real. Sus principales desventajas, cuando se monitorea la performance de una máquina completa, es que tiende a ser un método más bien insensitivo de detectar fallas incipientes. Deberán ocurrir daños apreciables en algunos componentes individuales de la máquina antes que ello se traduzca en efectos medibles en su Performance.
Además del monitoreo de la Performance de la máquina total, se puede vigilar la condición mecánica de algunos de sus componentes monitoreando cómo realizan su función. Por ejemplo:
- Un filtro de aire sucio puede ser detectado controlando si se produce un aumento en la caída de presión a través del filtro.
- En un compresor la temperatura del flujo de aceite en los sellos puede ser un indicativo de su desgaste. El desgaste del sello debería producir un mayor flujo de aceite y bajar su temperatura.
- Una tobera doblada en una turbina de gas puede ser detectada con el aumento de la temperatura de salida del gas.
- Problemas asociados con las aletas en un sistema de enfriamiento pueden ser detectados por el aumento de la caída de presión en la línea.
Técnicas que Monitorean el Fluido Lubricante y sus Residuos
Estas técnicas podemos clasificarlas en dos grupos:
- Técnicas que analizan la condición del fluido lubricante / refrigerante.
- Técnicas que analizan las partículas o residuos en el fluido lubricante / refrigerante.
Para la implementación de las primeras técnicas, los índices más usados para determinar la condición del fluido lubricante son:
• Su aspecto. Un color oscuro en el lubricante es indicativo de deterioro y requiere hacer un análisis de él. Un olor fuerte en el fluido lubricante puede indicar una fuga excesiva. Por ejemplo, analizando el aumento de temperatura en un compresor centrífugo se observó que el aceite tenía fuerte olor. Un sello dañado permitía la formación de sulfuro de hierro, el cual restringía el flujo de aceite en el descanso y éste se calentaba. El olor dio la clave. Reparado el sello se solucionó el problema.
• Contenido de agua (ASTM D95). Para la mayoría de las máquinas no debería exceder 100 ppm. en el aceite lubricante.
• Número de acidez (mg KOH/gr aceite, ASTM D664). Para la mayoría de las aplicaciones no debería exceder 0.25. Si es mayor podría ser indicativo de fuga en los sellos.
• Viscosidad. Tal vez es la característica más importante del aceite lubricante. Siempre debe estar en los rangos especificados por el constructor de la máquina. Un aumento de la viscosidad puede indicar, por ejemplo, puntos calientes dentro de la máquina.
• Número base total, TBN, es una media ponderada de la alcalinidad, detergencia y dispersibilidad. Disminución del TBN en un motor a combustión puede indicar por ejemplo mala combustión, falla de las válvulas de salida o alta contaminación en agua.
• Oxidación.
• Punto de inflamación.
El monitoreo de las partículas o residuos en el lubricante permite obtener una indicación de la condición de los diferentes componentes de la máquina que están en contacto con el lubricante. Para muchos fallos de las superficies lubricadas que son de naturaleza progresiva más que repentina, con el uso de estas técnicas también se puede obtener un aviso de fallo con bastante anticipación.
Para el monitoreo de las partículas o residuos en el aceite, existen varios métodos, dependiendo del tamaño de las partículas que se desean analizar:
- La espectrometría metálica analiza tamaño de partículas de hasta 10 ó 15 um.
- La ferrografía o examinación microscópica analiza tamaño de partícula entre unos 2 y 200 um.
- Los detectores de astilla (chip) analizan tamaño de partículas entre unos 15 a 700 um.
- La evaluación de filtros y las pantallas visuales analizan tamaños de partículas entre unos 50 y 1500 um.
Aunque la selección de parámetros a monitorear depende del tipo de equipo involucrado se podría sugerir las siguientes guías generales:
• Llevar tendencia en lo posible de aquellas propiedades físicas del aceite que entregan crucial información respecto a la capacidad de lubricar del fluido: viscosidad, TBN, oxidación.
• Llevar tendencia de todos los desgastes de metales que se detectan en la zona lubricada.
• No es necesario llevar tendencias de los aditivos metálicos.
• Contaminantes. Dentro del grupo de contaminantes metálicos típicamente se tiene los que indican suciedad (silicio) o los que indican elementos refrigerantes (sodio y boro) en el sistema lubricante. Otros contaminantes comúnmente encontrados son combustibles, hollín e insolubles. En muchas situaciones no se permite ni una ligera cantidad de contaminante; sin embargo, si el sistema puede tolerar un cierto nivel de contaminación, es aconsejable llevar una tendencia.
• Partículas ferromagnéticas: En general los ferrógrafos de lectura directa entregan cantidad de partículas pequeñas (menores de 2 um.), de partículas grandes (sobre 3 um.) y de la concentración total de partículas. Puede ser beneficioso en algunos casos llevar la tendencia de estas cantidades.
• La concentración total de partículas es más una indicación de contaminación que de desgaste. En general es más conveniente llevar tendencia de ello, en sistemas tales como los hidráulicos, donde la limpieza del lubricante es crítica.
Principales Técnicas de Inspección Visual
Objetivos | Técnicas a usar |
Iluminar partes internas oscuras | Sonda de luz |
Mejorar accesos a zonas nominalmente inaccesibles | Boroscopio |
Obtener muestras en zonas normalmente inaccesibles | Endoscopio |
Realizar un agrandamiento | Lupas, boroscopios, televisión |
Congelar el movimiento de componentes rotativos | Estroboscopio |
Resaltar la existencia de pequeñas grietas superficiales | Tintas penetrantes |
Extender el rango visual más allá del rango humano | Termografía infrarroja, Examen por rayos X o gamma |
Visualizar Temperaturas superficiales | Pinturas termográficas |
Ejemplos de monitoreo de performance de equipos
Método de monitoreo de la performance | Ejemplo |
Medición de la cantidad de flujo salida | Cambios en el flujo medio de salida bajo condiciones estándar |
Medición de la cantidad del producto de salida de la máquina | Cambios en la tolerancia de fabricación en una máquina, herramienta |
Medición de la razón entre la entrada y la salida de la máquina | Razón entre el consumo de combustible y la salida eléctrica de un generador diesel |
Razón entre la medición simultánea de dos variables de salida | Razón entre el flujo y el aumento de presión en una bomba |
Naturaleza de los residuos de desgaste generados por diferentes elementos de las máquinas
Tipo de Elemento | Ejemplo típico | Naturaleza de los residuos de desgaste asociados con fallas de elemento |
Elementos móviles en los cuales la carga esta concentrada en el área de contacto deslizante | Rodamientos, dientes de engranaje, leva y seguidor | Partículas ferrosas de varias formas y tamaños, generalmente fornidas y de alrededor de 1 mm. De tamaño (Fatiga de la superficie) |
Elementos móviles con la carga concentrada en una pequeña área | Anillos de pistón, cilindros, guías, acoplamianto de engranajes | Escamas ferrosas menores de 0,15 mm y de partículas finas de óxido de hierro |
Elementos móviles con la carga repartida sobre una gran área | Descansos planos, pistones, cilindros | Escamas y partículas ferrosas y no ferrosas muy pequeñas |
Sellos que deben operar con juego | Laberintos | Astillas metálicas generalmente grande, sobre un 1 mm de longitud |
Elementos fijos unos a otros, pero que desarrollan un ligero movimiento relativo entre ellos | Juntas apernadas, ajuste por interferencia | Residuos de frotamiento de partículas finas de óxido de hierro |
Técnicas de Mantenimiento Predictivo Industrial Basadas en Sistemas Expertos
En el campo del mantenimiento predicativo los sistemas expertos se utilizan fundamentalmente como herramientas de diagnóstico. Se trata de que el programa pueda determinar en cada momento el estado de funcionamiento de sistemas complejos, anticipándose a los posibles incidentes que pudieran acontecer. Así, usando un modelo computacional del razonamiento de un experto humano, proporciona los mismos resultados que alcanzaría dicho experto.
Figura 1. Sistema experto de mantenimiento
Estrategia de Mantenimiento
Un aspecto básico en la selección del tipo de mantenimiento a utilizar, son las características de los fallos que se espera que puedan ocurrir. A este respecto podemos clasificar los fallos en tres categorías.
- Fallos repentinos: que ocurren en un tiempo extremadamente corto.
- Fallos de desarrollo progresivo: en un intervalo de tiempo uniforme.
- Fallos de desarrollo progresivo: en un intervalo de tiempo aleatorio.
Los principios tanto del mantenimiento preventivo, como del mantenimiento predictivo, asumen que el fallo se va a desarrollar progresivamente. El mantenimiento preventivo asume además, que el fallo se desarrolla razonablemente en forma uniforme para justificar los intervalos regulares de intervención. El mantenimiento predictivo asume a su vez un desarrollo progresivo del fallo para justificar el concepto de tendencia. Aunque lo anterior es lo que sucede generalmente, hay situaciones en que fallos repentinos tienden a ocurrir con mayor frecuencia que los fallos progresivos.
En los molinos de carbón que producen combustible pulverizado para centrales de energía, la ocasional ingestión de piezas de metal o rocas muy duras, puede causar repentinas roturas de los elementos internos del molino. Esto puede ocurrir más frecuentemente que los fallos progresivos que ocurren en la transmisión. Cuando sucede, la única solución es utilizar una estrategia de mantenimiento reactivo. Cualquier programa de mantenimiento basado en intervalos regulares de tiempo sería ilógico.
Otro ejemplo donde el mantenimiento correctivo es adecuado, son los sistemas digitales electrónicos, los cuáles operan fundamentalmente en un modo on/off y por consiguiente, debería esperarse que fallaran de una manera repentina o intermitente, más que de una manera progresiva.
Hay en cambio situaciones donde un mantenimiento preventivo regular es la mejor estrategia, tal como cuando el deterioro de elementos en la máquina tienen un desarrollo progresivo regularmente uniforme. Ejemplos típicos son los cambios de filtro o los cambios de elementos de sacrificio para el control de la corrosión.
A pesar de los casos de excepción citados precedentemente, la tendencia general actual en mantenimiento es hacia una estrategia basada en la condición de la máquina. Sin embargo, debe tenerse presente que la estrategia de mantenimiento más eficaz será un desarrollo combinado y ponderado de un programa correctivo / preventivo / predictivo.
Otro aspecto básico a considerar en la selección de una estrategia de mantenimiento es de tipo económico. Para establecer si es económicamente ventajosa utilizar una estrategia de mantenimiento predictivo para una o más máquinas o elementos de ellos, deberá efectuarse un balance de costes / ahorros.
Sin embargo, evaluar los posibles ahorros que se obtendrían en la implementación de una estrategia de mantenimiento predictivo es difícil. Por ejemplo, si no ha producido un fallo catastrófico en una máquina es difícil evaluar lo que se ahorraría si se puede evitar que ella se produzca.
Una forma en la que se podría intentar evaluar los ahorros que se obtendrían al implementar una estrategia de mantenimiento predictivo es confeccionando una lista de las detenciones producidos en los últimos años en conjunto con sus causas.
Con esto se podría determinar:
• Cuáles intervenciones podrían haber resultado más económicas si se hubiera detectado, el fallo en una etapa más incipiente, evitando que la máquina funcionara hasta la rotura.
• Qué averías podrían haber sido reparadas más rápidamente si se hubiese conocido bien, antes de abrir la máquina, cuál era el elemento defectuoso.
• Cuáles serían los ahorros si después de efectuado un mantenimiento se controla la calidad del mantenimiento realizado. Para esto se evalúa la condición mecánica en que quedó la máquina a través del análisis de las mediciones realizadas inmediatamente después de la reparación. Las técnicas actuales del mantenimiento predictivo permiten verificar si un elemento reemplazado quedó disminuido debido a un procedimiento de montaje inadecuado (por ejemplo, un rodamiento con sus pistas de rodadura sin dientes). Evalúe así las economías que se obtendrían por ese concepto si los elementos reemplazables de las máquinas de su planta duraran lo especificado en las normas bajo los cuales fueron compradas las máquinas. El coste del mantenimiento debe considerar: Costes directos (recambio, materiales, mano de obra, etc.), costes de movilización de recambio, costes de lucro cesante o pérdidas por no producción, costes por falta de calidad del producto.
Dinos qué te ha parecido el artículo
Artículos recomendados
Análisis RAM como Herramienta para la Gestión de Activos Físicos: Caso de Aplicación Industrial

Planificación de mantenimiento mecánico

Evaluación de Desempeño de Compresor Axial de Turbinas de Gas después de Lavado en línea en una planta de inyección de agua mediante pruebas en campo (Parte II)

14.3.- Acoplamientos Elastoméricos

Publica tu artículo en la revista #1 de Mantenimiento Industrial
Publicar un artículo en la revista es gratis, no tiene costo.
Solo debes asegurarte que no sea un artículo comercial.
¿Qué esperas?
O envía tu artículo directo: articulos@predictiva21.com
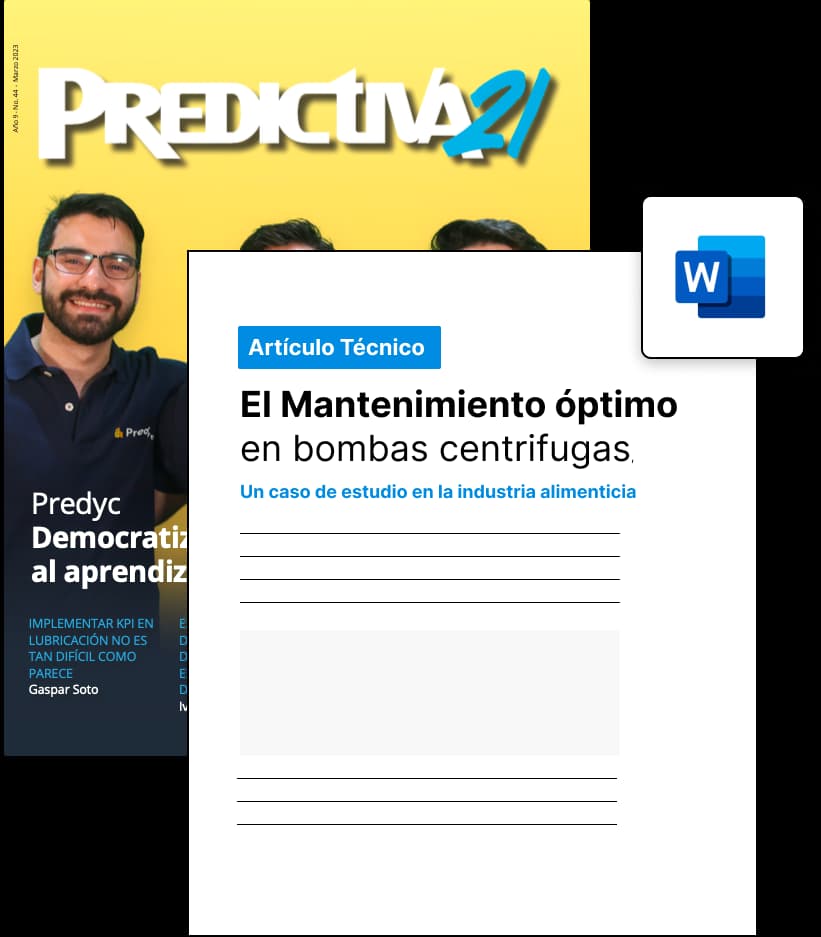