El Significado de Backlog en la Gestión de Mantenimiento
Articulo7 de septiembre de 2020
Unos de los tantos términos del BACKLOG significa “atraso”; pero en la Gestión de Mantenimiento podemos definirla como: Aquellas órdenes de trabajo que debieron salir al campo a ser ejecutadas y debido un determinado “atraso” no han salido, dificultado su ejecución. Estos atrasos pueden estar relacionados principalmente a: falta de mano de obra para ejecutar el trabajo, falta de materiales, partes y repuestos (M.P.R), alguna orden de compra de un M.P.R que es de stock o no, y que no ha llegado; ausencia de alguna herramienta especial, atraso por la espera de un contratista especial que se requiere para ejecutar algún trabajo; o sencillamente por el exceso de trabajo de un planificador, que impide que éste no concluya un trabajo de planificación, por falta de tiempo. En este último punto no juzgaremos la experticia o conocimiento de un planificador que ocasiona lentitud en el proceso, que con seguridad los hay.
Es importante recordar, que la que “Planificación” obedece a responder a las siguientes preguntas: qué hacer, cómo hacerlo, en cuánto tiempo hacerlo, para qué hacerlo, con quién hacerlo, dónde hacerlo. Fíjense que me refiero al significado planificar, no desde un punto de vista de un departamento de planificación que contempla a ambos (planificación y programación), me refiero estrictamente a la palabra planificar, debido a que el “cuándo hacerlo” y con quién hacerlo” corresponde a programación. En términos sencillos: Programación coloca nombre y apellido a la Planificación. Viéndolo de esta manera: tenemos que pintar un salón de clase de 300 metros cuadrados, planificación dice: necesitamos dos cuñetes de pintura, una escalera, dos brochas, máscaras, lentes, un rodillo con su extensión, tirro, dos pintores y eso tomará dos días. Qué dice programación: el trabajo lo vamos a realizar el día 15 y 16 de julio de 8 a 4 de la tarde (16 horas), con Pedro y Pablo; y una vez que se haya revisado que tenemos todas las herramientas y materiales disponibles realizar el trabajo.
Ahora bien, no quiero extenderme es estas definiciones y continuar con la interpretación del BACKLOG. Para esto, a continuación les dejo un esquema extraído de mi libro “Cómo Desarrollar e Implantar un Sistema de Mantenimiento”, segunda edición.

Si observamos el esquema, encontramos involucrados a: planificación, programación y ejecución. Fíjense que en el tanque de programación, hay una cantidad de órdenes de trabajo que se encuentra aún allí y que “debieron salir al campo y aún no salen por atrasos”, por cualquiera de las causas anteriormente descritas al inicio. Igual sucede con planificación; hay un atraso en algunas órdenes; quizás sea posiblemente, porque el planificador no ha tenido tiempo de sacarlas por falta de tiempo o por falta información. Dentro de ese esquema anterior encontramos como ejemplo una codificación numérica para las órdenes y éstas pueden ser de: correctivo normal, actividades predictivas y trabajos preventivos. Estos últimos porque forman parte de un programa; ya fueron planificadas, tan solo están para ajustes de ser necesarios; porque son trabajos que significan: hacer siempre lo mismo, con la misma gente, con el mismo tiempo, con los mismos materiales, con la misma frecuencia. Con relación al tiempo total, posiblemente exista una ligera desviación. Igualmente, también puede suceder que tan solo se está a la espera de que operaciones o producción entregue el equipo para proceder a su intervención.
El BACKLOG comprende por decirlo de alguna manera: el espacio de tiempo por atraso que hay por órdenes entre Planificación y Programación. Posiblemente, algunas personas entiendan que el Backlog corresponde tan sólo a la responsabilidad de programación. Para mi opinión, debemos ser más amplio y verlo como un conjunto (planificación-programación), porque todo recae sobre una gerencia o departamento de mantenimiento. Sin embargo “pendiente”, puede suceder también que un BACKLOG respectivo se refiera a que una(s) orden(es) que no ha salido al campo, porque no hay personal de ejecución disponible para hacer un trabajo. Si nuevamente vemos el esquema, el programador no puede abrir la llave para sacar más órdenes al campo si no hay disponibilidad de mano de obra y los demás recursos no están disponibles. Esto sería abarrotar el campo con órdenes de trabajo que ocasionaría una desorganización. Como consultor dejaría abierta esta posibilidad de incluir a “Ejecución” dentro del Backlog, porque posiblemente no haya más recursos para ingresar gente a la gerencia de mantenimiento. En consecuencia, para mi punto de vista lo dejaría fuera del BACKLOG. Es importante precisar que el tiempo por atraso de trabajos porque operaciones o Producción no ha autorizado intervenir algún activo, está fuera del BACKLOG.
Continuando, la planificación como parte del BACKLOG no puede detener su actividad y responsabilidad de planificar, así haya en el tanque del programador demasiadas órdenes. Un planificador debe continuar sin parar su actividad y echar al tanque del programador las órdenes de trabajo ya planificadas; y éstas, acompañarlas de su set de trabajo que contempla: orden de trabajo, sub-ordenes de trabajos, vales de almacén, guía de procedimientos técnicos, planos, esquemas, guías de detención de fallas, etc. como parte de una efectiva planificación.
Ahora bien, los trabajos de emergencia no forman parte de BACKLOG, debido a que cuando hay una situación de emergencia, todos los recursos: tanto planificación, programación y ejecución se colocan al frente para restablecer la condición operacional que ocasiona la paralización o degradación del equipo. Recordemos que un trabajo de emergencia está afectando y amenazando: la producción, la seguridad de las personas, activos y ambiente; por lo tanto, no debería haber margen de espera.
Es importante ver cada proceso del BACKLOG individualmente, porque se aplica a cada una de las órdenes que están en atraso. Aunque a través de los indicadores generales de planificación y programación los analicemos globalmente, por ejemplo cuando decimos: cantidad de trabajos planificados VS cantidad de trabajos solicitados en el tiempo (X), efectividad de los preventivos, relación de trabajos programados y paralizados por falta de: M.P.R, mano de obra, etc. del total de órdenes; y así sucesivamente. Quisiera dejar claro que “Programación” es la responsable por el balanceo efectivo de los recursos, revisar la disponibilidad de M.P.R en el almacén, disponibilidad de mano de obra, revisar la llegada de una orden de compra respectiva, seguimiento a los programas preventivos y correctivos. La programación trata de la asignación eficiente de recursos en el tiempo para realizar un trabajo, sea éste de preventivo o correctivo y del seguimiento respectivo.
Para concluir, analizando en detalle todo lo que he comentado: podemos sacar varias lecturas cuando no hay un control racional del BACKLOG: la primera, posiblemente sea que hay demasiados trabajos y el BAKLOG se está haciendo incontrolable y requerimos rápidamente de una política de mantenimiento. Una podría ser: desarrollar estrategias de acciones predictivas o mejorar las existentes para minimizar las fallas de los activos. Otra lectura es que debemos revisar la cantidad de personas que tenemos en la planta para realizar los trabajos. Posiblemente tengamos que revisar destrezas en cuanto a planificación y programación; revisar velocidad de respuestas del departamento de compra, optimiza el control de inventario. En general, realizar un proceso de “Reingeniería” del cual algún consultor haya escrito en esta prestigiosa revista; en caso contrario, con seguridad comentaremos en una próxima edición.
Autor: Brau Clemenza
www.sistemademantenimiento.com
YouTube: Brau Clemenza
Dinos qué te ha parecido el artículo
Artículos recomendados
El Tiempo no Perdona

Gestión de la Información de Activos Físicos Empleando Códigos Bidimensionales de Respuesta Rápida - QR

Proceso de evaporación de petróleo y sus derivados en tanques de almacenamiento

¿Qué es la Ingeniería Industrial?

Publica tu artículo en la revista #1 de Mantenimiento Industrial
Publicar un artículo en la revista es gratis, no tiene costo.
Solo debes asegurarte que no sea un artículo comercial.
¿Qué esperas?
O envía tu artículo directo: articulos@predictiva21.com
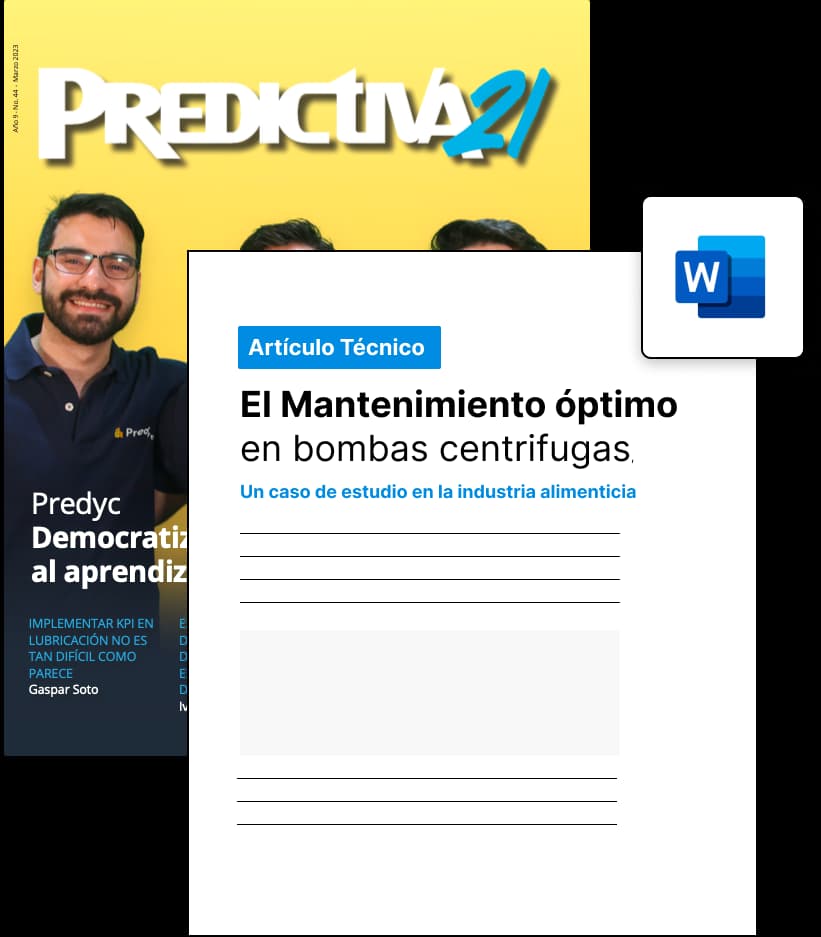
El Significado de Backlog en la Gestión de Mantenimiento
Articulo 7 de septiembre de 2020Unos de los tantos términos del BACKLOG significa “atraso”; pero en la Gestión de Mantenimiento podemos definirla como: Aquellas órdenes de trabajo que debieron salir al campo a ser ejecutadas y debido un determinado “atraso” no han salido, dificultado su ejecución. Estos atrasos pueden estar relacionados principalmente a: falta de mano de obra para ejecutar el trabajo, falta de materiales, partes y repuestos (M.P.R), alguna orden de compra de un M.P.R que es de stock o no, y que no ha llegado; ausencia de alguna herramienta especial, atraso por la espera de un contratista especial que se requiere para ejecutar algún trabajo; o sencillamente por el exceso de trabajo de un planificador, que impide que éste no concluya un trabajo de planificación, por falta de tiempo. En este último punto no juzgaremos la experticia o conocimiento de un planificador que ocasiona lentitud en el proceso, que con seguridad los hay.
Es importante recordar, que la que “Planificación” obedece a responder a las siguientes preguntas: qué hacer, cómo hacerlo, en cuánto tiempo hacerlo, para qué hacerlo, con quién hacerlo, dónde hacerlo. Fíjense que me refiero al significado planificar, no desde un punto de vista de un departamento de planificación que contempla a ambos (planificación y programación), me refiero estrictamente a la palabra planificar, debido a que el “cuándo hacerlo” y con quién hacerlo” corresponde a programación. En términos sencillos: Programación coloca nombre y apellido a la Planificación. Viéndolo de esta manera: tenemos que pintar un salón de clase de 300 metros cuadrados, planificación dice: necesitamos dos cuñetes de pintura, una escalera, dos brochas, máscaras, lentes, un rodillo con su extensión, tirro, dos pintores y eso tomará dos días. Qué dice programación: el trabajo lo vamos a realizar el día 15 y 16 de julio de 8 a 4 de la tarde (16 horas), con Pedro y Pablo; y una vez que se haya revisado que tenemos todas las herramientas y materiales disponibles realizar el trabajo.
Ahora bien, no quiero extenderme es estas definiciones y continuar con la interpretación del BACKLOG. Para esto, a continuación les dejo un esquema extraído de mi libro “Cómo Desarrollar e Implantar un Sistema de Mantenimiento”, segunda edición.

Si observamos el esquema, encontramos involucrados a: planificación, programación y ejecución. Fíjense que en el tanque de programación, hay una cantidad de órdenes de trabajo que se encuentra aún allí y que “debieron salir al campo y aún no salen por atrasos”, por cualquiera de las causas anteriormente descritas al inicio. Igual sucede con planificación; hay un atraso en algunas órdenes; quizás sea posiblemente, porque el planificador no ha tenido tiempo de sacarlas por falta de tiempo o por falta información. Dentro de ese esquema anterior encontramos como ejemplo una codificación numérica para las órdenes y éstas pueden ser de: correctivo normal, actividades predictivas y trabajos preventivos. Estos últimos porque forman parte de un programa; ya fueron planificadas, tan solo están para ajustes de ser necesarios; porque son trabajos que significan: hacer siempre lo mismo, con la misma gente, con el mismo tiempo, con los mismos materiales, con la misma frecuencia. Con relación al tiempo total, posiblemente exista una ligera desviación. Igualmente, también puede suceder que tan solo se está a la espera de que operaciones o producción entregue el equipo para proceder a su intervención.
El BACKLOG comprende por decirlo de alguna manera: el espacio de tiempo por atraso que hay por órdenes entre Planificación y Programación. Posiblemente, algunas personas entiendan que el Backlog corresponde tan sólo a la responsabilidad de programación. Para mi opinión, debemos ser más amplio y verlo como un conjunto (planificación-programación), porque todo recae sobre una gerencia o departamento de mantenimiento. Sin embargo “pendiente”, puede suceder también que un BACKLOG respectivo se refiera a que una(s) orden(es) que no ha salido al campo, porque no hay personal de ejecución disponible para hacer un trabajo. Si nuevamente vemos el esquema, el programador no puede abrir la llave para sacar más órdenes al campo si no hay disponibilidad de mano de obra y los demás recursos no están disponibles. Esto sería abarrotar el campo con órdenes de trabajo que ocasionaría una desorganización. Como consultor dejaría abierta esta posibilidad de incluir a “Ejecución” dentro del Backlog, porque posiblemente no haya más recursos para ingresar gente a la gerencia de mantenimiento. En consecuencia, para mi punto de vista lo dejaría fuera del BACKLOG. Es importante precisar que el tiempo por atraso de trabajos porque operaciones o Producción no ha autorizado intervenir algún activo, está fuera del BACKLOG.
Continuando, la planificación como parte del BACKLOG no puede detener su actividad y responsabilidad de planificar, así haya en el tanque del programador demasiadas órdenes. Un planificador debe continuar sin parar su actividad y echar al tanque del programador las órdenes de trabajo ya planificadas; y éstas, acompañarlas de su set de trabajo que contempla: orden de trabajo, sub-ordenes de trabajos, vales de almacén, guía de procedimientos técnicos, planos, esquemas, guías de detención de fallas, etc. como parte de una efectiva planificación.
Ahora bien, los trabajos de emergencia no forman parte de BACKLOG, debido a que cuando hay una situación de emergencia, todos los recursos: tanto planificación, programación y ejecución se colocan al frente para restablecer la condición operacional que ocasiona la paralización o degradación del equipo. Recordemos que un trabajo de emergencia está afectando y amenazando: la producción, la seguridad de las personas, activos y ambiente; por lo tanto, no debería haber margen de espera.
Es importante ver cada proceso del BACKLOG individualmente, porque se aplica a cada una de las órdenes que están en atraso. Aunque a través de los indicadores generales de planificación y programación los analicemos globalmente, por ejemplo cuando decimos: cantidad de trabajos planificados VS cantidad de trabajos solicitados en el tiempo (X), efectividad de los preventivos, relación de trabajos programados y paralizados por falta de: M.P.R, mano de obra, etc. del total de órdenes; y así sucesivamente. Quisiera dejar claro que “Programación” es la responsable por el balanceo efectivo de los recursos, revisar la disponibilidad de M.P.R en el almacén, disponibilidad de mano de obra, revisar la llegada de una orden de compra respectiva, seguimiento a los programas preventivos y correctivos. La programación trata de la asignación eficiente de recursos en el tiempo para realizar un trabajo, sea éste de preventivo o correctivo y del seguimiento respectivo.
Para concluir, analizando en detalle todo lo que he comentado: podemos sacar varias lecturas cuando no hay un control racional del BACKLOG: la primera, posiblemente sea que hay demasiados trabajos y el BAKLOG se está haciendo incontrolable y requerimos rápidamente de una política de mantenimiento. Una podría ser: desarrollar estrategias de acciones predictivas o mejorar las existentes para minimizar las fallas de los activos. Otra lectura es que debemos revisar la cantidad de personas que tenemos en la planta para realizar los trabajos. Posiblemente tengamos que revisar destrezas en cuanto a planificación y programación; revisar velocidad de respuestas del departamento de compra, optimiza el control de inventario. En general, realizar un proceso de “Reingeniería” del cual algún consultor haya escrito en esta prestigiosa revista; en caso contrario, con seguridad comentaremos en una próxima edición.
Autor: Brau Clemenza
www.sistemademantenimiento.com
YouTube: Brau Clemenza
Dinos qué te ha parecido el artículo
Artículos recomendados
Repercusión de la depresión en Confiabilidad Humana

ISO Commitee works on revision of ISO55002

Prontuario de Lubricación: Guía de lubricación de motores para no expertos

Diagramas de Pareto y de Dispersión, herramientas claves de evaluación seguimiento y control del mantenimiento

Publica tu artículo en la revista #1 de Mantenimiento Industrial
Publicar un artículo en la revista es gratis, no tiene costo.
Solo debes asegurarte que no sea un artículo comercial.
¿Qué esperas?
O envía tu artículo directo: articulos@predictiva21.com
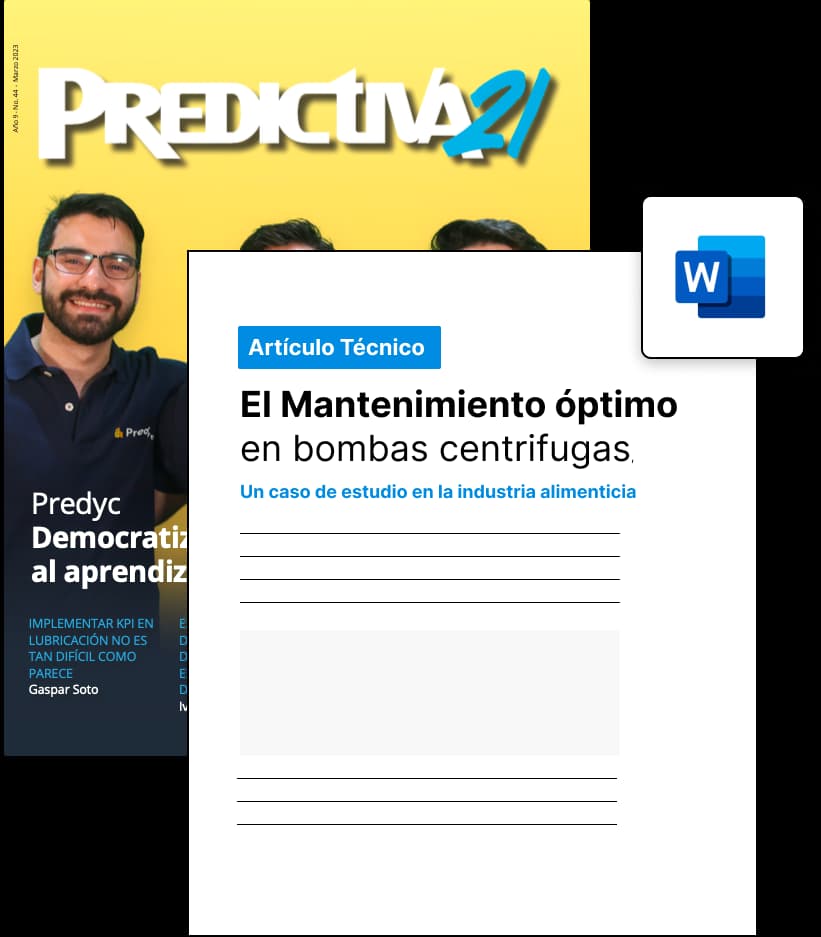