Metodología de Inspección Basada en Riesgo API 581 Aplicada a Haces Tubulares de Intercambiadores de Calor: Activo Físico Instalado en la Industria Petroquímica
Articulo22 de junio de 2020
Resumen
Los intercambiadores de calor son un elemento fundamental en todo tipo de industria ya que los mismos juegan un papel fundamental en la optimización de la energía producida para ser transferida a lo largo de la cadena de producción o procesos.
Tras el paso de la primera década del nuevo siglo, se ha visto como objetivo primordial el consumo mínimo de energía por parte del sector industrial y más específicamente la industria petroquímica. Los intercambiadores de calor son los equipos más utilizados para ese fin. Esto se logra haciendo pasar fluidos de distinta temperatura por las caras opuestas de un material y, mediante la conductividad térmica de este, el fluido caliente transfiere el calor al fluido de menor temperatura.
El objetivo de este artículo es la de mostrar cómo puede ser evaluado un haz tubular de un intercambiador de calor del tipo carcasa y tubo que fue diseñado para operar con soda cáustica e instalado en una planta química. Es de hacer notar que en la industria petroquímica, la instalación de intercambiadores de calor tipo carcasa y tubo ha sido predominante durante muchas décadas.
Palabras claves: Inspección basada en riesgo, intercambiador de calor, mecanismos de deterioro, riesgo, probabilidad de falla, consecuencia de falla, análisis Weibull , método Weibayes.
1 Introducción
Se suele establecer como origen de los intercambiadores de calor la segunda mitad del siglo XIX. Se conoce con el nombre de intercambiador de calor a cualquier dispositivo en el que se experimenta un intercambio de calor entre dos fluidos separados por una pared metálica, esta pared representa la superficie de transferencia de calor y puede tener cualquier geometría. En las industrias, se utilizan intercambiadores de calor de diferentes tipos, por lo tanto elegir el equipo de transferencia de calor más adecuado es una gran labor.
En los inicios de la segunda revolución industrial (1852) fue inventado el intercambiador de carcasa-tubo, utilizándolo para el condensado del vapor en navíos fluviales con el fin de transportar mercancías y personas. Estos equipos fueron tomando formas y configuraciones diferentes e introduciéndose de manera gradual en todo tipo de sectores industriales.
Tal como sucede en las plantas químicas, como por ejemplo, las de Cloro Soda que se caracterizan por producir o procesar sus productos principales y esenciales a través de la electrólisis (método de membrana) ver figura 1, éste consiste en dividir una celda electrolítica en el lado anódico y el lado catódico con una membrana de intercambio iónico que es una resina especial. Esta membrana de intercambio iónico tiene una característica especial de interceptar aniones (iones negativos) y dejar pasar solamente cationes (iones positivos) de una solución de soda clorada.
La aplicación de ambos químicos se encuentra alrededor del mundo en las industrias químicas y de procesos. Aproximadamente la mitad de toda la soda cáustica producida es usada en la producción de otros productos. Así como otros importantes usos en la producción de celulosa, textiles, productos del petróleo, jabón y la refinación del mineral bauxita en la producción de aluminio.

Fuente: www.sapiensman.com.
2 Marco conceptual
2.1 Intercambiador de calor tipo carcasa y tubo
Los intercambiadores de calor son equipos de proceso construidos y diseñados para la máxima eficiencia de transferencia de calor entre dos medios diferentes, ver figura 2. En la mayoría de los procesos industriales, la pérdida de calor es muy derrochadora e ineficiente. Debido a esto, los intercambiadores de calor se crearon para capturar y reutilizar el calor que de otro modo se perdería en el medio ambiente.
En general, un intercambiador de calor funciona permitiendo que un fluido caliente fluya a través del intercambiador más allá de un fluido frío sin mezclar los dos. El calor fluye del fluido caliente al fluido frío, calentando el fluido frío y enfriando el fluido caliente. Esto permite que el calor se transporte y se reutilice en lugar de simplemente descartarse. Los dos fluidos pasarán uno al lado del otro, uno generalmente en una tubería estrecha mientras que el otro fluye fuera de la tubería en una carcasa circundante.
Hay muchos tipos diferentes de intercambiadores de calor ver tabla 1; algunos más apropiados para ciertos entornos que otros. Algunos tienen divisores incorporados para separar el almacenamiento de calor, mientras que otros permiten la mezcla de calor. De estos diferentes tipos, cada uno se ajusta a una de las tres clasificaciones más grandes según su tipo de flujo. (Fuente: https://inspectioneering.com).

Fuente: TEMA Standards of Tubular Exchanger Manufacture Association. Eight Edition.
Los componentes básicos de un intercambiador de calor son:
- Haz tubular: Los tubos proporcionan la superficie de trasferencia de calor entre el fluido que circula por su interior y el fluido que circula por la carcasa. Alojan el fluido secundario, es decir, el producto a calentar.
- Falla de un Haz Tubular: Es definida como una fuga del tubo para propósitos de la Inspección Basada en Riesgo.
- Placa tubular: Es una placa de metal perforada para albergar los tubos, los cuales se fijan mediante expansión o soldadura.
- Deflectores: Son placas segmentadas dispuestas a lo largo del intercambiador. Sirven para mantener los tubos en la posición adecuada y obligar al fluido primario a que circule perpendicularmente al haz tubular.
- Carcasa y conexiones: La carcasa es la envolvente del fluido primario y consiste en un cilindro soldado a las placas tubulares. Dispone de conexiones para la entrada y salida del fluido secundario.
- Cabezales desmontables: Elementos conectados a las placas tubulares por ambos extremos, para facilitar la circulación del producto por el haz tubular. Pueden disponer de placas para partición del haz tubular, con el fin de conseguir que el fluido circule por varios pasos.
2.2 Materiales para la construcción de Haces Tubulares que operan con hidróxido de sodio
Un número de materiales de construcción pueden ser usados para producir y manejar soluciones de soda. La capacidad para específicas aplicaciones dependerá sobre los factores asociados con la concentración y use del cáustico y las variables de proceso envueltas.
En general, los factores a ser considerados en la selección de materiales incluyen prácticamente, disponibilidad, propiedades mecánicas, corrosión, resistencia, consideraciones riesgo-beneficio y económicos.
Los factores críticos incluidos en servicios de soda cáustica, son:
- La concentración de la solución.
- Las temperaturas a ser encontradas.
- La presencia de otros químicos, los cuales pueden estar presentes en la soda cáustica, como contaminantes o aditivos.
- Los límites de tolerancia por contaminación del ion metálico en la soda cáustica.
- Esfuerzo de tensión residual o aplicada, el cual puede afectar la resistencia a la corrosión.
- Consideraciones económicas del costo de vida.
Los metales y aleaciones más frecuentemente consideradas para el uso de soda cáustica, son: Acero al carbón, Acero inoxidable, níquel y aleaciones de alto níquel.
2.3 ¿Por qué utilizar Níquel para servicios de soda cáustica?
El níquel es uno de los metales más resistentes a la soda cáustica, con concentraciones superiores a los 50 % y elevadas temperaturas en el cual generalmente predominan. En concentraciones de soda cáustica por encima de 73 %, la velocidad de corrosión incrementa significativamente y generalmente es menos de 1 mpy (0,0254 mm/yr).

Fuente: Selección de aleaciones para servicios de Soda Cáustica NIDI 10019.
2.4 Inspección Basada en Riesgo (IBR)
La inspección basada en el riesgo (RBI) es una metodología y proceso de análisis que, a diferencia de la inspección basada en la condición, requiere una evaluación cualitativa o cuantitativa de la probabilidad de falla (PoF) y la consecuencia de la falla (CoF) asociada con cada elemento del equipo, circuitos de tuberías incluidos, en una unidad de proceso particular. Un programa RBI implementado adecuadamente clasifica las piezas individuales de los equipos según sus riesgos y prioriza los esfuerzos de inspección basados en esta categorización. (Fuente: https://inspectioneering.com).
2.5 Integridad Mecánica
La Integridad Mecánica (IM) se puede definir como la gestión del equipo para garantizar que esté diseñado e instalado correctamente, y que funcione y se mantenga adecuadamente (es decir, sin fugas y todos los elementos son aptos para el servicio). Un programa de integridad mecánica debe tener en cuenta la inspección y las pruebas del equipo utilizando procedimientos reconocidos y generalmente aceptados como buenas prácticas de ingeniería y también debe considerar la idoneidad de los equipos recién fabricados para su uso. (Fuente: https://inspectioneering.com).
2.6 Confiabilidad
Probabilidad de que un equipo o sistema cumpla adecuadamente con la función requerida ante condiciones específicas, durante un periodo de tiempo dado (Fuente: ISO 14224).
2.7 Fases de la implantación

Fuente: El autor.
2.8 Equipo multidisciplinario
Un equipo multidisciplinario es un grupo de profesionales con experiencia, calificaciones y habilidades que colaboran en proyectos específicos o de manera continua. Este tipo de equipo de trabajo es común en un entorno industrial debido a su valor para discutir problemas o desafíos con perspectivas variadas.
Los equipos multidisciplinarios transmiten muchos beneficios. Estos incluyen mejores resultados organizacionales y una mayor optimización y un uso más eficiente de los recursos y una mayor satisfacción laboral para los miembros del equipo.
Las ventajas de formar un equipo multidisciplinario son las siguientes:
- Ampliar de perspectiva del trabajo y de análisis.
- Fragmentar la resistencia y criterios preconcebidos. Ahorro de tiempo y energía.
- Mejorar el rendimiento de las competencias individuales.
- Personal calificado para una situación determinada.
- Garantizar el seguimiento de los proyectos.
- No depender de una persona o de una sola profesión.
- Permitir un cierto distanciamiento intelectual respecto a lo cotidiano.
Responsabilidades de los miembros de un equipo multidisciplinario para la aplicación de la metodología de Inspección Basada en Riesgo:

Fuente: Práctica recomendada API 580, Tercera Edición, Febrero 2016.
2.9 Mecanismos de Deterioro
Mecanismos de daños (también conocidos como mecanismos de degradación) es un término general que se refiere a cualquier causa de problemas o fallas dentro del equipo de proceso. Estos pueden variar desde corrosión hasta grietas, daños por calor y todo lo demás.
Al evaluar los mecanismos de daño, se debe tener en cuenta el estado actual del equipo, así como cualquier daño potencial que el mecanismo pueda causar más adelante. La susceptibilidad del equipo a un mecanismo de daño particular se ve afectada por una serie de variables, incluidos los materiales de construcción, los fluidos de proceso, las condiciones de operación, el entorno externo, etc.
Una revisión exhaustiva de los mecanismos de daños es esencial para crear una estrategia de inspección efectiva. Una vez que se entienden los mecanismos y la morfología del daño, los estrategas de inspección pueden usar esta información para seleccionar métodos de inspección con la mayor probabilidad de detectar, caracterizar y medir el daño potencial. Además, los intervalos de inspección se pueden establecer utilizando códigos y estándares de la industria como API 510, 570, 653, API RP 579 para la aptitud para el servicio, y API 580 y 581 para la inspección basada en el riesgo. (Fuente: https://inspectioneering.com).
3 Caso de Estudio Basado en Métodos y Normas Vigentes
El objetivo de este articulo técnico es la de dar a conocer la aplicabilidad de la metodología de inspección basada en riesgo API 581 a intercambiadores de calor en la industria petroquímica. A continuación se mostrará un caso específico de estudio aplicado a un activo físico instalado en una planta de procesamiento de Cloro-Soda.
El método industrial de producción que cubre los requerimientos de estas plantas de Cloro Soda es el de electrólisis (membrana de intercambio iónico) del cloruro sodio e hidróxido de sodio. Para procesar en cantidad, calidad y costos estos valiosos productos químicos, donde la variable temperatura juega un rol importante debido a que se debe mantener un rango óptimo de ella, tanto para la salmuera que alimenta las celdas, como la soda cáustica que se recircula y entra a los electrolizadores. Según lo anteriormente expuesto se recomienda que los electrolizadores de membrana sean operados con lazos de recirculación para la soda cáustica y la salmuera con un intercambiador de calor. Esto permitirá optimizar la temperatura de las celdas y enfriar los electrolizadores en el caso que se detenga la planta y así evitar la producción de soda fuera de especificación. Operando con grandes volúmenes de soda, la planta se hace menos sensible a pequeñas perturbaciones, como por ejemplo: variaciones en la alimentación de agua desmineralizada.
Los tipos de Intercambiadores de calor utilizados para este proceso químico son los de tipo carcasa y tubo, (ver figura 4). Estos intercambiadores tienen ambos extremos del cabezal de tubos sujetos a la carcasa. Así como también la utilización de una junta de expansión debido al diferencial de la carcasa y de los tubos. Esta expansión se debe a la operación del equipo a diferentes temperaturas y a la utilización de diferentes materiales.

Fuente: El autor.
Durante más de 20 años de servicio, el intercambiador de calor HE-E101A ha sido sometido a un ambiente de trabajo externo considerablemente agresivo debido a que este equipo se encuentra cercano a diferentes sistemas de procesos que por su contexto operacional, emanan vapores, como por ejemplo: salmuera, ácido clorhídrico y soda cáustica. Así como también la planta de cloro soda se encuentra cercana a un lago donde esto puede ocasionar un incremento de cloruros en el ambiente.
De lo anteriormente expuesto se puede inferir que la combinación de las condiciones de procesos y materiales existentes de construcción para cada componente del equipo debe ser evaluado para identificar los activos y creíbles mecanismos de daños. A continuación, se mostrará evidencia fotográfica de la condición externa del intercambiador de calor bajo evaluación.

Fuente: El autor.

Fuente: El autor.

Fuente: El autor.
Para los mecanismos de daños mencionados anteriormente, la velocidad de progresión del deterioro pudo ser estimada para este tipo de equipo de proceso de planta. Esto quiere decir que para nuestro caso de estudio, la velocidad de deterioro fue expresada en términos de velocidad de corrosión por adelgazamiento. Asimismo existe la creíble posibilidad de la susceptibilidad de la corrosión bajo tensión donde la velocidad de deterioro es desconocida o inmedible. La susceptibilidad es a menudo designada como alta, media o baja basada sobre las condiciones ambientales y la combinación de los materiales de construcción.
El historial de inspección es la mejor información debido a que pudimos conocer la experiencia operacional del equipo y las condiciones que conllevaron a la velocidad de deterioro observada a ser realísticamente esperada a ocurrir en el equipo bajo consideración. Otra fuente de información incluyó la base de datos de la experiencia con similares equipos de planta y la opinión de expertos.
Para nuestro caso de estudio existe un historial de inspecciones mediante el ensayo no destructivo NDE llamado ultrasonido. A continuación, se muestran las gráficas del análisis de la corrosión monitoreada a través del software Ultrapipe. Es importante mencionar que la base de datos del software fue alimentada con las inspecciones realizadas al intercambiador en paradas programadas de planta.

Fuente: Ultra pipe for corrosion monitoring.

Fuente: Ultra pipe for corrosion monitoring.

Fuente: Ultra pipe for corrosion monitoring.
Las gráficas anteriores muestran el resultado del proceso de deterioro al cual ha sido sometida la pared externa y conexiones principales del intercambiador de calor HE-E101A debido a los mecanismos de daño que suelen ser incrementales, acumulativos y, en algunos casos, irrecuperables. Contrario a la condición mostrada de la parte externa del intercambiador, el haz tubular ha tenido un comportamiento al servicio con una muy baja cantidad de fallas por tubos como se mostrara a continuación.

Fuente: El autor.

Fuente: El autor.
Los estadísticos siempre prefieren grandes muestras de datos, pero los ingenieros se ven obligados a hacer análisis con muestras muy pequeñas, incluso de una a tres fallas. Cuando el resultado de una falla involucra seguridad, daños ambientales, interrupción del negocio, optimización de los recursos de la compañía o costos extremos, es inapropiado solicitar más fallas. La principal ventaja del análisis de la evaluación que se mostrará a continuación, revelará que los objetivos de ingeniería a menudo se pueden cumplir incluso con muestras extremadamente pequeñas. Por supuesto, las muestras pequeñas siempre implican grandes incertidumbres. Para evaluar estas pequeñas incertidumbres muéstrales, los límites de confianza jugaron un rol importante.
Para estimar el riesgo relacionado a la falla de haces tubulares es recomendable evaluarlos mediante la metodología Inspección Basada en Riesgo API 581.
El riesgo es un término de naturaleza probabilística, que se define como la “probable ocurrencia de una falla o evento no deseado”. En este simple pero poderoso concepto coexiste la posibilidad de que un evento o aseveración se haga realidad o se satisfaga, con las consecuencias de que ello ocurra.

El análisis de esta ecuación permite entender el estudio y la toma de decisiones. A través de este indicador, pueden compararse situaciones y escenarios que bajo una perspectiva cotidiana resultarían disímiles, pero bajo ciertas circunstancias deben evaluarse y considerarlas en un proceso de toma de decisiones. Por ejemplo, podría utilizarse para comprender entre diferentes acciones de mantenimiento a equipos estáticos, caracterizados por presentar una frecuencias de fallas bajas pero con consecuencias tradicionalmente muy altas.
Cálculo de la probabilidad de falla.
Ecuación para el cálculo de la probabilidad de falla en haces tubulares.

En API 581 2016 tercera edición, sección 8.3.3. Indica que para realizar una evaluación se debería contar con información proveniente de una biblioteca de confiabilidad de haces de intercambiadores de calor o base de datos instaurada por el propietario o usuario de la instalación. A continuación se describen los aspectos a lograr para realizar una adecuada evaluación.
a) General: Una base de datos o biblioteca de Weibull es extremadamente importante para la evaluación de los riesgos asociados con la falla de haces tubulares. Ciertos detalles del intercambiador son requeridos para ser reunidos por cada haz que ingresa a la base de datos de confiabilidad creada.
b) Análisis de Weibayes: Si la suposición es hecha de que haces similarmente diseñados y en similares servicios tendrán el mismo mecanismo de falla, un enfoque Weibayes puede ser utilizado. Este enfoque asume que los parámetros beta (β) y eta (η) de la curva de Weibull para el conjunto de eventos de similares haces será idéntico al haz que está siendo evaluado. El enfoque Weibayes también permite un análisis estadístico preciso de fallas sin tener una larga cantidad de data para el haz específico que está siendo evaluado.
c) Desarrollar criterios de coincidencia o conjunto de eventos “Cut-Set”: Antes de indicar el significado de cut-set es importante mencionar y conceptualizar lo siguiente:
- Árbol de fallas: Es un diagrama lógico que exhibe la interrelación entre un evento de un sistema crítico y sus causas.
- Análisis del árbol de fallas: Es el análisis cualitativo y cuantitativo que puede ser llevado a cabo sobre las bases de un árbol de fallas.
- Cut-Set: En un árbol de fallas se establece a un cut-set como un conjunto de eventos básicos quienes simultáneamente ocurren asegurando que el evento TOP ocurra. Es importante notar que hay diferentes tipos de mecanismos de falla que un haz de intercambiador de calor puede experimentar.

Fuente: El autor.
d) Prueba de bondad de ajuste: Si un diagrama de Weibull es creado a partir de un conjunto de eventos demasiado extenso y sobre la base de datos de una biblioteca de confiabilidad y si los datos no están correctamente diagramados. Entonces la probable razón de esto, es que múltiples mecanismos de fallas están siendo diagramados y una lista más específica de criterios coincidentes es requerida para aislar las fallas para un mecanismo. Una prueba de bondad de ajuste debería ser usado para determinar si o no el subconjunto de datos es incorrecto. Una vez esto es logrado, hay confianza agregada en la distribución Weibull y el conjunto de eventos es aplicable a él específico haz tubular del intercambiador de calor que está siendo evaluado.
e) Determinación de los parámetros de la curva de Weibull desde datos coincidentes: Después que haces similares han sido combinados desde la base de datos y diagramados sobre Weibull así como también una prueba de ajuste de bondad ha sido aplicada, entonces los parámetros beta (β) y eta (η) serán obtenidos en conformidad con el Weibull Handbook.
Caso real aplicado a un activo físico instalado en la industria petroquímica. Cálculo de la probabilidad de falla utilizando Weibayes’ con base de datos de fallas.
Para calcular la probabilidad de falla como una función del tiempo en servicio para un haz de intercambiador de calor, una base de datos de confiabilidad y/o inspección fue investigada y donde se encontró una combinación de haces tubulares de igual característica y servicio:

Fuente: El autor.
Para estimar o calcular la probabilidad de falla de un haz tubular, éste puede ser realizado utilizando el método que mejor se ajuste a la base de datos disponible para el momento de ejecutar la evaluación. Es importante indicar que la práctica recomendada, API 581 Inspección Basada en Riesgo, 3 tercera edición. Parte 1. Metodología de la planificación de la inspección, más específicamente en la sección 8: Haz de tubos del intercambiador de calor, muestra que hay cuatro (4) métodos para calcular la probabilidad de falla de un haz tubular.
Metodología de inspección basada en riesgo (Referencia API 581 2016 Parte 1. Metodología de planificación de inspección)
La aplicación de los principios de riesgo a la inspección de haces tubulares del intercambiador permite tomar decisiones basadas en las consecuencias de la falla del haz, incluidos los costos asociados con la pérdida de producción y los costos de impacto ambiental, los costos de reemplazo y mantenimiento asociados con el reemplazo del haz.
Para facilitar una predicción más precisa del rendimiento futuro del haz, la experiencia combinada de otros haces tubulares de intercambiadores de calor de diseño y servicio similar pueden combinarse y analizarse estadísticamente. Con este método, es crítico que el usuario (departamento de confiabilidad, integridad mecánica, inspección de equipos estáticos, corrosión y materiales, custodio de la instalación) o llámese como se llame dentro de una organización quien es responsable por llevar la estadística de falla de los equipos, mantenga una base de datos de fallas real de los haces de intercambiador de calor.
De lo anteriormente descrito podríamos agregar que no solo es importante llevar una base de datos de fallas de los haces tubulares de intercambiador de calor. Es más importante determinar la efectividad de inspecciones pasadas que hayan ejecutado el departamento de inspección mediante la combinación de métodos de examen no destructivo (NDE) como visual, ultrasónico (UT), radiográfico, etc. Registrar la falla de uno o más tubos de un haz tubular son necesarios, ya que indicar la frecuencia, cobertura, ubicación y efectividad para localizar, caracterizar y determinar el tamaño y velocidad del deterioro, es sumamente importante para después identificar los mecanismos de daños creíbles y probables y posteriormente determinar la efectividad en la búsqueda de los mismos. La reducción de la incertidumbre sobre el estado del daño de un componente es una función de la efectividad de la inspección para detectar, caracterizar y cuantificar el tipo y la extensión del daño.
Análisis para evaluar la probabilidad de falla en haces tubulares con o sin fallas. Para este caso de estudio en particular hemos seleccionado el método 4 “API 581 Sección 8”. Haces tubulares de intercambiadores de calor” debido a que el mismo se ajusta a la base de datos disponible para realizar la evaluación de un Haz Tubular.
Es conocido que los equipos estáticos tienden a una frecuencia de falla baja pero con consecuencias tradicionalmente muy altas. Qué hacer cuando existe una frecuencia de falla muy baja? Por ejemplo; para pequeñas muestras (entre 1 y 3) o cero fallas. Existe un método de análisis que puede ser útil para realizar evaluaciones bajo las características mencionadas con anterioridad. Ese método es llamado Weibull ya que tiene un gran beneficio y puede ser útil para evaluaciones con extremadamente muestras pequeñas de fallas y conjunto de datos que tienen mayores deficiencias, el cual puede ser llamado “dirty data” Cada industria tiene este tipo de información, aunque esta situación puede mejorar donde las gerencias se han dado cuenta de la efectividad en los resultados al adquirir alta calidad de datos de información.
Un análisis Weibayes es un método para construir una distribución de Weibull basada sobre un conocido o asumido valor del parámetro de forma (β), el parámetro (β) de Weibull es usado cuando hay ciertas deficiencias en la información (data) por ejemplo, en el histórico de fallas, experiencia previa o conocimiento ingenieril de la física de la falla.; cuando no hay fallas o pocas fallas, un análisis Weibayes es significativamente más preciso que Weibull, ya que puede ser derivada usando el Método de Máxima Probabilidad (MLE) para determinar la característica de vida (η). Esto es útil para tratar conjunto de datos que pueden tener interrupciones.
Una interrupción puede ser definida como una unidad que no ha fallado por un modo de falla o no fallar del todo. Para citar un ejemplo: Un perno que falla en la cabeza en una prueba de esfuerzo es una interrupción.
La ventaja de utilizar el análisis de Weibayes es que se pueden tomar decisiones acertadas de ingeniería con significativamente menos puntos de datos de falla como se necesitaría con otras distribuciones estadísticas. El enfoque de Weibayes se utiliza ya que este método incorpora la experiencia pasada de otros haces similares (biblioteca de Weibull o base de datos) con los datos específicos disponibles para el haz tubular que se está evaluando.
Situación típica con falla:
- Con pequeñas muestras Weibayes es más preciso que Weibull si hay conocimiento previo de beta (β).
- Pruebas de sustentación pueden ser diseñadas con los más pequeños tamaños de muestras posibles si Weibayes es empleado.
- Las pruebas de muerte súbita son también buenos candidatos de Weibayes.
- Los tiempos de operación de las unidades y los números de fallas son conocidos, pero las fallas no son identificadas. Reparaciones generales puede generar este tipo de información.
Para el caso de estudio hemos obtenido un valor del parámetro Beta (β) mediante una prueba de ajuste de bondad RARE. Los datos de tiempos entre fallas (TPF) para realizar la evaluación fueron tomados del comportamiento en servicio de los haces tubulares compatibles al intercambiador HE-E101-B/C mostrados en la Tabla 4. Por motivos de confidencialidad se mostrarán las siguientes gráficas realizadas sin mostrar los datos de TPF.

Fuente: El autor.
Finalizada la caracterización de la variable a través del RARE (Distribution Estimation), los resultados indican que la distribución Weibull es la distribución que mejor representa a los datos.

Fuente: Reliability engineering & risk analysis 1999 by Modarres, Kaminskiy & Krivtsov RARE.
Una vez obtenido el valor del parámetro y los datos suministrados en la Tabla 4 para los haces tubulares compatibles o coincidentes se procedió a estimar la Probabilidad de Falla (POF) para el haz tubular HE-E101-B que ha presentado historial de fallas.
Cálculo de la probabilidad de falla POF a través de la “Sección 8. Haces tubulares de intercambiadores de calor” (Referencia API 581 2016 Parte 1. Metodología de planificación de inspección)
Utilización del Método 4.El cual especifica que una vez acumulado suficiente historial de inspección, la estadística para el haz podría ser determinado. El parámetro Eta (η) o también conocido como característica de vida puede ser recalculado utilizando la ecuación 3.

Para simular los datos de la Tabla 4 con el propósito de conocer un valor inicial del parámetro Eta (η). Fue necesario utilizar el software SuperSMITH ya que el mismo se considera como el avance técnico más significativo. Este software se considera amigable y fácil de usar. El software ha hecho la aplicación mucho más fácil, eficiente y divertida.
Simulación de los datos de la Tabla 3. Utilizando el software SuperSMITH de Weibull.
Esta referencia puede parecer inapropiada, pero la dependencia del software se requiere. Ya que si el evaluador lo desea, puede evitar casi todos los cálculos y trazados manuales utilizando SuperSMITH, pero en la humilde opinión de los autores de este artículo, recomiendmos realizar los primeros cálculos de forma manual ya que esto le proporcionará al evaluador un mayor entendimiento de las suposiciones necesarias para estimar los parámetros Beta (β) y Eta (η) de Weibull.
Simulación del parámetro Eta (η) con un intervalo de confianza de límite inferior (LBC) del 90%.
Esta simulación indica un valor inicial del parámetro Eta (η) así como un valor pronosticado de una inspección recomendada en años. Es importante mencionar que la mayoría de los estadísticos utilizarán límites de confianza en datos de esta naturaleza para dar cuenta de la distribución estadística en los datos. Se recomendó un intervalo de confianza de límite inferior (LBC) del 90%. Esto representa el conjunto de haces tubulares coincidentes en la base de datos de confiabilidad.

Fuente: DEMO Súper SMITH WEIBUL software by Fulton Findings.
Para citar un ejemplo sobre cómo se debe calcular el riesgo en cualquier punto del tiempo. La Grafica x proporciona la curva POF para el caso de estudio utilizando los haces de intercambiadores de calor correspondientes de la base de datos. Con los parámetros de Weibull definidos, el POF en función del tiempo se determina para el caso de estudio usando la ecuación 2.

Una vez que el haz tubular ha acumulado al menos dos ciclos de vida con datos de inspección, se puede realizar un análisis de Weibayes manteniendo el parámetro Beta (β) igual al determinado a partir de los criterios de haces tubulares coincidentes. El parámetro Eta (η) de vida característica se puede volver a recalcular utilizando la ecuación 3.

Para obtener el valor de la probabilidad de falla del haz tubular mediante la ecuación 1, se utilizó el valor recalculado del parámetro Eta (η).

Estimación de la Confiabilidad del Haz Tubular para los próximos 20 años, partiendo del cálculo anteriormente realizado de la probabilidad de falla.

Fuente: El autor.

Fuente: El autor.
Reducción de la incertidumbre a través de la inspección. Podríamos hacernos una pregunta. ¿Cómo introducir incertidumbre?
Bueno, si no hay un gran muestreo de datos de inspección para el haz, entonces existe un grado de incertidumbre asociado con respecto a si el conjunto coincidente de haces tubulares de la base de datos de fallas representa con precisión el haz que se está evaluando. Para tener en cuenta las imprecisiones y los sesgos inherentes a la base de datos de fallas, se introduce incertidumbre adicional en las estadísticas. Se utiliza un valor predeterminado para una incertidumbre adicional del 50%.
Gestión del riesgo mediante la reducción de la incertidumbre a través de la inspección.
El riesgo puede gestionarse mediante inspección. Obviamente, la inspección en sí no detiene ni mitiga los mecanismos de daño ni reduce el riesgo, pero la información obtenida a través de una inspección efectiva puede cuantificar mejor el riesgo real. Las actividades de inspección no evitan la falla inminente del equipo a menos que la inspección precipite las actividades de mitigación de riesgos que cambian la probabilidad de falla POF.
La inspección sirve para identificar, monitorear y medir los mecanismos de daño. Es una aportación invaluable en la predicción de cuándo el daño alcanzará un punto crítico. La correcta aplicación de las inspecciones mejorará la capacidad del usuario para predecir los mecanismos de daño y las tasas de deterioro. Cuanto mejor sea la previsibilidad, menos incertidumbre habrá sobre cuándo puede ocurrir una falla. La mitigación (reparación, reemplazo, cambios, etc.) se puede planificar e implementar antes de la fecha de falla prevista. La reducción de la incertidumbre y el aumento de la previsibilidad a través de la inspección se traduce directamente en una mejor estimación de la probabilidad de falla y, por lo tanto, en una reducción del riesgo calculado. Sin embargo, los usuarios deben ser diligentes para garantizar que las alternativas de inspección temporal, en lugar de reducciones de riesgo más permanentes, sean realmente efectivas.
La mitigación de riesgos (por la reducción de la incertidumbre) lograda mediante la inspección supone que las organizaciones actuarán de manera oportuna sobre los resultados de la inspección. La mitigación del riesgo no se logra si los datos de inspección que se recopilan no se analizan y actúan adecuadamente cuando es necesario. La calidad de los datos de inspección y el análisis o interpretación afectarán en gran medida el nivel de mitigación de riesgos. Por lo tanto, los métodos de inspección adecuados y las herramientas de análisis de datos son fundamentales.
Simulación donde se introduce una adición de la incertidumbre del 50%.

Fuente: DEMO SuperSMITH WEIBUL software by Fulton Findings.
Si el haz tubular no tiene registro de inspección y no existe conocimiento de la condición del mismo, la curva de incertidumbre del 50% se usa para predecir el POF como una función del tiempo. El riesgo calculado para un haz tubular sin ningún conocimiento de inspección será mayor que para un haz tubular que tiene registros de inspección. Aunque la acción de inspección no reduce el riesgo en sí misma, esto está de acuerdo con los principios de RBI que establecen que cuanto más conocimiento se obtenga para un componente de equipo, menos incertidumbre existe, lo que resulta en una reducción del riesgo calculado.
En la Gráfica 7, se visualiza que la inspección recomendada sería 13.7 años. Esto se compara con un valor pronosticado de 19.8 años mostrado en la Gráfica 5, donde se usaron los datos sin procesar (90% LBC) que representan el conjunto de haces tubulares coincidentes en la base de datos de confiabilidad. Esto muestra el efecto directo que la incertidumbre de la inspección tiene sobre el riesgo calculado y el plan de inspección posterior.
Cálculo de las consecuencias de la Falla.
Método de cálculo: La falla del haz tubular es definida como una fuga del tubo. Las consecuencias financieras son determinadas basadas en la criticidad del haz, el cual incluye costos asociados con pérdida de oportunidad debido a tiempos debajo de producción, costos por impacto ambiental, costos asociados con mantenimiento y reemplazo del haz tubular. Las consecuencias de un paro no planificado debido a fuga del tubo del haz tubular es determinada usando la ecuación 4.

La producción de la unidad o costos de la pérdida de producción, es determinada usando la ecuación 5.

El costo al impacto ambiental se estimó considerando daños a las áreas ambientales cercanas al intercambiador o que el producto liberado, debido a la pérdida de contención interna, conlleve a la contaminación con el medio calentador (vapor) o enfriador (agua de enfriamiento) y este a su vez fuera enviado a la zona de desecho de productos químicos de la planta y que no pudiese ser neutralizado correctamente.

La siguiente ecuación puede ser usada para estimar los costos de reemplazo del haz tubular.

Es importante destacar que para este caso de estudio en particular se realizó el cálculo de , considerando la falla funcional o falla del tubo en el intercambiador de calor que pudiera conllevar a una pérdida de contención del mismo o equipo auxiliar. Estos típicamente supondrían una fuga desde un lugar de alta presión a uno de baja presión del intercambiador y abrir una posterior contaminación al sitio de baja presión. Fallas en tubos de intercambiadores de calor pueden resultar en una contaminación del sistema de agua enfriamiento o vapor con materiales tóxicos y consecuentemente obtener pérdida de contención con consecuencias a la seguridad, salud e impacto ambiental. Ahora bien, para establecer el cálculo total del haz tubular se tiene que considerar la totalidad de los tubos así como las placas tubulares.

Se calculó los Costos de mantenimiento considerando la mano de obra que intervendría al momento de fallar alguno de los tubos del haz tubular; este recurso pudiera estar distribuido de la siguiente forma: técnicos mecánicos, grupo de soldadura, montacargas, máquinas de soldadura, operadores, entre otros.

Costo total de las consecuencias de fallas

Administración del Riesgo mediante la limitación de cualquier consecuencia negativa o reducción en probabilidad de un particular evento.
Las evaluaciones previas realizadas al haz tubular del intercambiador de calor HE-E101-A indican que sería posible realizar alguna actividad de mitigación del riesgo al equipo, como por ejemplo: modificar a través de un rediseño, reemplazo general o revaloración de toda la sección externa del equipo, con el propósito de mantener el haz tubular en continuo servicio.
Hay metodologías que apoyan los procesos de toma de decisiones para evitar tomar decisiones arbitrarias o inconsistentes, sin base en la información disponible y que no cumplan con los objetivos medulares del negocio. Resultan particularmente útiles para decidir en escenarios con intereses en conflicto, como el escenario “operación – mantenimiento”, en el cual el operador requiere que el equipo o proceso opere en forma continua para garantizar máxima producción, y simultáneamente, el mantenedor requiere que el proceso se detenga con cierta frecuencia para poder mantener y ganar confiabilidad en el mismo.
Recordemos que cuando el deterioro de un equipo ha alcanzado un punto en el que el riesgo de falla no se puede manejar a un nivel aceptable, el reemplazo / reparación es a menudo la única forma de mitigar el riesgo.
En opinión de los autores de este artículo, la toma de decisiones en la alta dirección de una organización se fundamenta no solo en que la alternativa propuesta sea técnicamente factible, sino también debe ser económicamente rentable y presupuestariamente viable para garantizar que las inversiones sean oportunas para maximizar la rentabilidad del negocio. Por lo anteriormente expuesto fue necesario agregar una evaluación económica para soportar la decisión eficaz para mitigar el riesgo relativo relacionado a los componentes externos del intercambiador de calor HE-E101-A.
Como gestionar el riesgo: En función de la clasificación de los elementos, se podría iniciar un proceso de gestión de los riesgos. Por ejemplo; Para aquellos riesgos que se juzgan aceptables, no se requiere mitigación y no se requieren acciones adicionales pero para los riesgos considerados inaceptables y, por lo tanto, que requieren mitigación de riesgos, existen varias categorías de mitigación que deberían ser considerados, como por ejemplo:
- Mitigación de probabilidad: ¿se pueden tomar medidas para disminuir la POF, como los cambios en el material de construcción, cambios operativos o rediseño de equipos? Ahora se pueden tomar decisiones de gestión de riesgos sobre qué medidas de mitigación tomar.
Modificación, rediseño y revaloración de equipos.
La modificación y el rediseño de los equipos, utilizando un proceso riguroso de MOC, pueden proporcionar mitigación de POF. Ejemplos Incluya lo siguiente:
- Cambio de metalurgia.
- Adición de revestimientos.
- Eliminación de las piernas muertas.
- Mayor tolerancia a la corrosión.
- Cambios físicos que ayudarán a controlar / minimizar el deterioro.
- Mejoras de aislamiento.
- Cambios en el diseño del punto de inyección.
- Cambio de tamaño del dispositivo de alivio.
4 Evaluación económica del haz tubular del intercambiador de calor HE-E101-A
La decisión de reemplazar o continuar manteniendo un determinado equipo representa uno de los elementos fundamentales de la estrategia de desarrollo de una industria o empresa. Un reemplazo postergado más tiempo del razonable puede elevar los costos de producción debido a una serie de problemas fáciles de identificar. Un reemplazo prematuro puede ocasionar el desvío de recursos que pudieran tener otras prioridades para la empresa, además de los costos de oportunidad que implican no trabajar con adecuadas estructuras y óptimos costos y riesgos. El estudio de las inversiones de modernización por la vía del reemplazo es el más simple de realizar, la metodología a aplicar en este artículo, es el análisis económico del costo de ciclo de vida, la cual se basa en estimar o pronosticar todos los posibles “flujos de caja” durante toda la vida útil de un activo, sistema o proceso; incluyendo todas las fases desde el diseño, procura, construcción, operación, mantenimiento hasta su desincorporación y en la conversión de estos flujos de caja proyectados o futuros, a un valor económicamente comparable considerando el valor del dinero en el tiempo para equipo con vida diferente.
Suposiciones para la aplicación del modelo:
- La inflación se considera a través de la tasa real de interés (Tasa de descuento) de la empresa.
- Los costos de operación y mantenimiento del equipo por unidad de tiempo se incrementan con el tiempo y son considerados al final de cada año.
- El reemplazo es por un equipo idéntico al instalado.
- El valor de salvamento o reventa decrece con el tiempo.
- El análisis se realizará para un modo de falla predominante en función de las penalizaciones al momento de ocurrir la pérdida de la función.
Como puede observarse, los costos de operación y mantenimiento del equipo actual van aumentando a medida que aumenta el número de periodos “n” para reemplazar el equipo, mientras que los costos de operación y mantenimiento del equipo nuevo van disminuyendo puesto que opera menos tiempo.
Como puede observarse en la siguiente tabla, la vida útil económica del equipo nuevo obtenida con la aplicación del modelo matemático para un periodo indefinido arrojó un resultado igual a 6 años, mientras que la vida remanente para el equipo actual es 20 años, es decir, el tiempo óptimo para reemplazar el activo actual está en el futuro. La recomendación es mantener el equipo instalado más tiempo en operación de tal manera de maximizar la rentabilidad del negocio. Realizar el reemplazo del activo antes de este tiempo estaríamos incurriendo en un desembolso de dinero el cual podría ser aplicado o direccionado a otras oportunidad de inversión de capital en la organización. Este cálculo matemático considerando las evaluaciones financieras soportan los resultados obtenidos en los cálculos mostrados en las primeras líneas de este artículo.

Fuente: El autor.
A continuación se mostrará evidencia fotográfica de los resultados obtenidos al aplicar la acción de mitigación: REEMPLAZO DE TODOS LOS COMPONENTES EXTERNOS DEL INTERCAMBIADOR DE CALOR HE-E101-A.

Fuente: El autor.

Fuente: El autor.

Fuente: El autor.
Actualización del intervalo de inspección del intercambiador de calor una vez sometido a REEMPLAZO DE TODOS LOS COMPONENTES EXTERNOS.
Una inspección no solo reduce la incertidumbre en los datos, sino que también proporciona conocimiento de la actual condición del haz tubular. Se puede determinar que el haz está en óptimas condiciones y que la probabilidad de falla POF es demasiado conservador. Por el contrario, también se puede determinar que el haz está en peor condición de lo que se ha predicho usando la información de un haz tubular en un servicio similar.
Donde la corrosión general es el mecanismo de control de daños en el haz, el promedio medido de los datos de espesor del tubo pueden usarse para predecir la fecha futura de inspección del haz tubular. Por otro mecanismo de daño como vibración, adelgazamiento del extremo del tubo, etc. o donde no existen datos medidos de espesor.
Cualquiera que sea el método utilizado para calcular una fecha futura basada en un registro de inspección, el pronóstico de los datos puede ser usado para modificar la curva POF base.
Fecha de inspección basada en datos medidos de espesor
La tasa de adelgazamiento del haz de tubos se puede determinar utilizando el espesor de pared promedio suministrada y el espesor de pared medido en la última inspección.
La tasa de adelgazamiento del haz de tubos se calcula utilizando la siguiente ecuación

La vida útil prevista del haz tubular ajustado para inspección, se calcula utilizando la siguiente ecuación:

A este ritmo, el espesor promedio de la pared alcanzaría el 50% del espesor original o el resto espesor de pared RWTƒ en 10 años.
Ajuste a la curva de tasa de falla basada en la condición real del haz tubular

El intervalo de inspección recomendado en el POF máximo aceptable del 50%

Conclusiones
- Para efectos de evaluaciones como la realizada en este artículo es estrictamente importante contar con un sistema de gerencia del dato, ya que resulta muy complicado reducir la incertidumbre con muy o poca información (conjunto de datos o base de datos) disponible por las organizaciones.
- La información obtenida de la inspecciones del haz tubular, fue utilizada no solo para cuantificar la actual o real condición del equipo (espesor de pared restante, velocidad de corrosión o estimado de la vida remanente) sino que también pudo ser usada en la toma de decisiones acertadas respecto a mitigar el riesgo relativo relacionado a la posible pérdida de contención de tubos o carcasa externa y hacer ajustes a las curvas de tasa de POF.
- Se redujo la incertidumbre respecto a la actual o real condición del equipo esto quiere decir que la curva graficada de POF mediante SSW (Datos confidenciales) se movió hacia la derecha y el POF disminuye. De esta manera, el conocimiento de inspección adquirido durante la intervención (Parada Mayor) del intercambiador de calor reduce el POF y el cálculo del riesgo.
- La vida remanente económica del intercambiador actual se pudo calcular por conocer un reemplazo posible.
- La vida útil económica del intercambiador depende de la diferencia de desempeños entre el activo actual y el posible reemplazo y del costo del reemplazo y de su deterioro en el tiempo.
- El desempeño del activo actual y el posible reemplazo se evalúo en términos de costos y riesgos.
- Como la opción ganadora es mantener el equipo actual se debe realizar nuevamente el análisis en el próximo mantenimiento mayor para verificar si sigue siendo la mejor alternativa, o existe otra alternativa en el mercado con un CAE menor que la opción actual.
- Si la inflación es constante por unidad de tiempo no debemos preocuparnos por su efecto.
Recomendaciones
- Mantener el intercambiador de calor HE-E101-A por más tiempo en operación para maximizar la rentabilidad del negocio.
- Reducir la incertidumbre sobre el actual o real estado del daño del haz tubular HE-E101-A o componente asociados mediante la selección de inspecciones efectivas para detectar, caracterizar y cuantificar el tipo y la extensión de posibles nuevos mecanismos de deterioro.
- Ejecutar actividades de inspección del haz tubular HE-E101-A para actualizar la base de datos recolectados con el propósito de cuantificar la actual o real condición del equipo (espesor de pared restante, velocidad de corrosión o estimado de la vida remanente).
- Adiestrar al personal de inspección y confiabilidad de equipos estáticos de la organización en la implementación de la metodología de Inspección Basada en Riesgo API 580 / 581 para planificar un adecuado plan de inspección con el propósito de conocer; Qué inspeccionar, Cómo inspeccionar (técnica), Dónde inspeccionar (ubicación), Cuánto inspeccionar (cobertura) y Cuándo inspeccionar.
- Seleccionar las mejores alternativas en base a conocimiento previo a través de evaluaciones y resultados técnicos, con el propósito de optimizar los recursos asignados a la intervención de equipos estáticos de la organización y no tomarlas en base a solo conocimiento empírico y / o reactivo.
Referencias y Lecturas Complementarias
- Risk Based Inspection API Recommended Practice 580 Third Edition, February 2016.
- Risk Based Inspection Methodology API Recommended Practice 581 Third Edition, April 2016.
- The New Weibull Handbook, Fifth Edition by Dr. Robert B. Abernethy 2004.
- Alloy Selection for Caustic Soda Service by C.M. Schillmoller. NIDI Technical Series N° 10019.
- TEMA Standards of Tubular Exchanger Manufacture Association. Eight Edition.
- Ultrapipe of Siemens for corrosion monitoring and remaining life.
- ISO – 55000 Asset Management — Overview, Principles and Terminology, 2014.
- John Woodhouse.: ‘Asset Management Decision-Making: The SALVO Process’, Strategic Assets: Life Cycle Value Optimization, United Kingdom, TWPL. 2014.
- Edgar Fuenmayor. Análisis de Reemplazo de un Activo Basado en Costos de Ciclo de Vida. Revista Confiabilidad Industrial Nº 11. Venezuela. 2011. www.confiabilidad.com.ve
- UNE – EN 60300 – 3 – 3 Cálculo del Costo del Ciclo de Vida. 2009.
- ISO – 15663 (E) Petroleum and natural gas industries – Life Cycle Costing, 2001.
- John Woodhouse.: ‘Managing Industrial Risk’, Getting value for money in your business, London, Chapman & Hall. 1993.
Autores:
Evelio Chirinos
Venezuela
Supervisor de mantenimiento mecánico
Empresa: Petroquímica de Venezuela
Correo: evelioch30@hotmail.com
Ingeniero Mecánico con más de 11 años en la industria petroquímica venezolana con experiencia en las áreas de mantenimiento mecánico, inspección y confiabilidad de equipos estáticos, administración del riesgo e integridad mecánica.
Rosangel Leal
Venezuela
Ingeniera de confiabilidad
Empresa: Petroquímica de Venezuela
Correo: rosangelcristal@gmail.com
Ingeniera química con experiencia en la industria petroquímica en el área de confiabilidad mecánica empleando metodologías centradas en mantenimiento, gestión del riesgo y análisis de criticidad.
Edgar Fuenmayor
Venezuela
Consultor
Empresa: Machinery & Reliability Institute – MRI
Correo: edgarfuenmayor1@gmail.com
Es Ingeniero Mecánico con Maestría en Gerencia de Mantenimiento de la Universidad del Zulia en Venezuela. Es un Profesional Certificado en Mantenimiento y Confiabilidad (CMRP) por la Sociedad de Profesionales de Mantenimiento y Confiabilidad (SMRP) en USA. Es Profesor Universitario, Articulista y Conferencista de Trabajos de Ingeniería de Confiabilidad, Mantenimiento y Gestión de Activos. Actualmente es Consultor para la firma Machinery & Reliability Institute – MRI.
Dinos qué te ha parecido el artículo
Artículos recomendados
Vibraciones Mecánicas

Educación Formal para el Mantenimiento

¿Qué es la transformación digital para el mantenimiento predictivo?

Gestión del Mantenimiento

Publica tu artículo en la revista #1 de Mantenimiento Industrial
Publicar un artículo en la revista es gratis, no tiene costo.
Solo debes asegurarte que no sea un artículo comercial.
¿Qué esperas?
O envía tu artículo directo: articulos@predictiva21.com
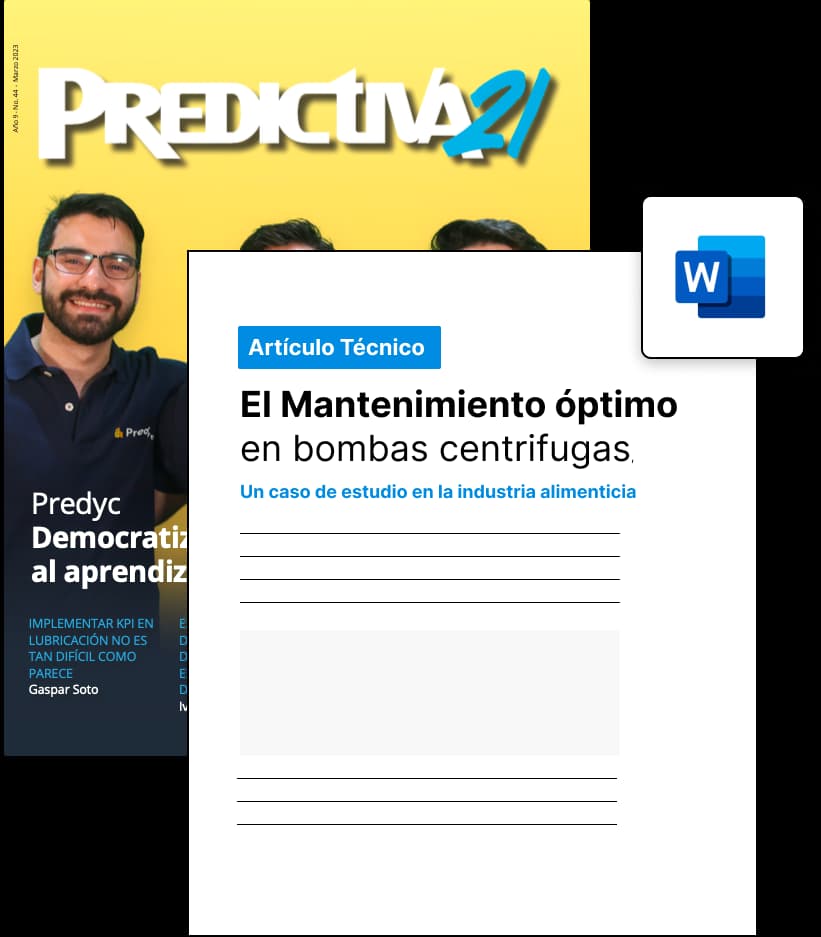
Metodología de Inspección Basada en Riesgo API 581 Aplicada a Haces Tubulares de Intercambiadores de Calor: Activo Físico Instalado en la Industria Petroquímica
Articulo 22 de junio de 2020Resumen
Los intercambiadores de calor son un elemento fundamental en todo tipo de industria ya que los mismos juegan un papel fundamental en la optimización de la energía producida para ser transferida a lo largo de la cadena de producción o procesos.
Tras el paso de la primera década del nuevo siglo, se ha visto como objetivo primordial el consumo mínimo de energía por parte del sector industrial y más específicamente la industria petroquímica. Los intercambiadores de calor son los equipos más utilizados para ese fin. Esto se logra haciendo pasar fluidos de distinta temperatura por las caras opuestas de un material y, mediante la conductividad térmica de este, el fluido caliente transfiere el calor al fluido de menor temperatura.
El objetivo de este artículo es la de mostrar cómo puede ser evaluado un haz tubular de un intercambiador de calor del tipo carcasa y tubo que fue diseñado para operar con soda cáustica e instalado en una planta química. Es de hacer notar que en la industria petroquímica, la instalación de intercambiadores de calor tipo carcasa y tubo ha sido predominante durante muchas décadas.
Palabras claves: Inspección basada en riesgo, intercambiador de calor, mecanismos de deterioro, riesgo, probabilidad de falla, consecuencia de falla, análisis Weibull , método Weibayes.
1 Introducción
Se suele establecer como origen de los intercambiadores de calor la segunda mitad del siglo XIX. Se conoce con el nombre de intercambiador de calor a cualquier dispositivo en el que se experimenta un intercambio de calor entre dos fluidos separados por una pared metálica, esta pared representa la superficie de transferencia de calor y puede tener cualquier geometría. En las industrias, se utilizan intercambiadores de calor de diferentes tipos, por lo tanto elegir el equipo de transferencia de calor más adecuado es una gran labor.
En los inicios de la segunda revolución industrial (1852) fue inventado el intercambiador de carcasa-tubo, utilizándolo para el condensado del vapor en navíos fluviales con el fin de transportar mercancías y personas. Estos equipos fueron tomando formas y configuraciones diferentes e introduciéndose de manera gradual en todo tipo de sectores industriales.
Tal como sucede en las plantas químicas, como por ejemplo, las de Cloro Soda que se caracterizan por producir o procesar sus productos principales y esenciales a través de la electrólisis (método de membrana) ver figura 1, éste consiste en dividir una celda electrolítica en el lado anódico y el lado catódico con una membrana de intercambio iónico que es una resina especial. Esta membrana de intercambio iónico tiene una característica especial de interceptar aniones (iones negativos) y dejar pasar solamente cationes (iones positivos) de una solución de soda clorada.
La aplicación de ambos químicos se encuentra alrededor del mundo en las industrias químicas y de procesos. Aproximadamente la mitad de toda la soda cáustica producida es usada en la producción de otros productos. Así como otros importantes usos en la producción de celulosa, textiles, productos del petróleo, jabón y la refinación del mineral bauxita en la producción de aluminio.

Fuente: www.sapiensman.com.
2 Marco conceptual
2.1 Intercambiador de calor tipo carcasa y tubo
Los intercambiadores de calor son equipos de proceso construidos y diseñados para la máxima eficiencia de transferencia de calor entre dos medios diferentes, ver figura 2. En la mayoría de los procesos industriales, la pérdida de calor es muy derrochadora e ineficiente. Debido a esto, los intercambiadores de calor se crearon para capturar y reutilizar el calor que de otro modo se perdería en el medio ambiente.
En general, un intercambiador de calor funciona permitiendo que un fluido caliente fluya a través del intercambiador más allá de un fluido frío sin mezclar los dos. El calor fluye del fluido caliente al fluido frío, calentando el fluido frío y enfriando el fluido caliente. Esto permite que el calor se transporte y se reutilice en lugar de simplemente descartarse. Los dos fluidos pasarán uno al lado del otro, uno generalmente en una tubería estrecha mientras que el otro fluye fuera de la tubería en una carcasa circundante.
Hay muchos tipos diferentes de intercambiadores de calor ver tabla 1; algunos más apropiados para ciertos entornos que otros. Algunos tienen divisores incorporados para separar el almacenamiento de calor, mientras que otros permiten la mezcla de calor. De estos diferentes tipos, cada uno se ajusta a una de las tres clasificaciones más grandes según su tipo de flujo. (Fuente: https://inspectioneering.com).

Fuente: TEMA Standards of Tubular Exchanger Manufacture Association. Eight Edition.
Los componentes básicos de un intercambiador de calor son:
- Haz tubular: Los tubos proporcionan la superficie de trasferencia de calor entre el fluido que circula por su interior y el fluido que circula por la carcasa. Alojan el fluido secundario, es decir, el producto a calentar.
- Falla de un Haz Tubular: Es definida como una fuga del tubo para propósitos de la Inspección Basada en Riesgo.
- Placa tubular: Es una placa de metal perforada para albergar los tubos, los cuales se fijan mediante expansión o soldadura.
- Deflectores: Son placas segmentadas dispuestas a lo largo del intercambiador. Sirven para mantener los tubos en la posición adecuada y obligar al fluido primario a que circule perpendicularmente al haz tubular.
- Carcasa y conexiones: La carcasa es la envolvente del fluido primario y consiste en un cilindro soldado a las placas tubulares. Dispone de conexiones para la entrada y salida del fluido secundario.
- Cabezales desmontables: Elementos conectados a las placas tubulares por ambos extremos, para facilitar la circulación del producto por el haz tubular. Pueden disponer de placas para partición del haz tubular, con el fin de conseguir que el fluido circule por varios pasos.
2.2 Materiales para la construcción de Haces Tubulares que operan con hidróxido de sodio
Un número de materiales de construcción pueden ser usados para producir y manejar soluciones de soda. La capacidad para específicas aplicaciones dependerá sobre los factores asociados con la concentración y use del cáustico y las variables de proceso envueltas.
En general, los factores a ser considerados en la selección de materiales incluyen prácticamente, disponibilidad, propiedades mecánicas, corrosión, resistencia, consideraciones riesgo-beneficio y económicos.
Los factores críticos incluidos en servicios de soda cáustica, son:
- La concentración de la solución.
- Las temperaturas a ser encontradas.
- La presencia de otros químicos, los cuales pueden estar presentes en la soda cáustica, como contaminantes o aditivos.
- Los límites de tolerancia por contaminación del ion metálico en la soda cáustica.
- Esfuerzo de tensión residual o aplicada, el cual puede afectar la resistencia a la corrosión.
- Consideraciones económicas del costo de vida.
Los metales y aleaciones más frecuentemente consideradas para el uso de soda cáustica, son: Acero al carbón, Acero inoxidable, níquel y aleaciones de alto níquel.
2.3 ¿Por qué utilizar Níquel para servicios de soda cáustica?
El níquel es uno de los metales más resistentes a la soda cáustica, con concentraciones superiores a los 50 % y elevadas temperaturas en el cual generalmente predominan. En concentraciones de soda cáustica por encima de 73 %, la velocidad de corrosión incrementa significativamente y generalmente es menos de 1 mpy (0,0254 mm/yr).

Fuente: Selección de aleaciones para servicios de Soda Cáustica NIDI 10019.
2.4 Inspección Basada en Riesgo (IBR)
La inspección basada en el riesgo (RBI) es una metodología y proceso de análisis que, a diferencia de la inspección basada en la condición, requiere una evaluación cualitativa o cuantitativa de la probabilidad de falla (PoF) y la consecuencia de la falla (CoF) asociada con cada elemento del equipo, circuitos de tuberías incluidos, en una unidad de proceso particular. Un programa RBI implementado adecuadamente clasifica las piezas individuales de los equipos según sus riesgos y prioriza los esfuerzos de inspección basados en esta categorización. (Fuente: https://inspectioneering.com).
2.5 Integridad Mecánica
La Integridad Mecánica (IM) se puede definir como la gestión del equipo para garantizar que esté diseñado e instalado correctamente, y que funcione y se mantenga adecuadamente (es decir, sin fugas y todos los elementos son aptos para el servicio). Un programa de integridad mecánica debe tener en cuenta la inspección y las pruebas del equipo utilizando procedimientos reconocidos y generalmente aceptados como buenas prácticas de ingeniería y también debe considerar la idoneidad de los equipos recién fabricados para su uso. (Fuente: https://inspectioneering.com).
2.6 Confiabilidad
Probabilidad de que un equipo o sistema cumpla adecuadamente con la función requerida ante condiciones específicas, durante un periodo de tiempo dado (Fuente: ISO 14224).
2.7 Fases de la implantación

Fuente: El autor.
2.8 Equipo multidisciplinario
Un equipo multidisciplinario es un grupo de profesionales con experiencia, calificaciones y habilidades que colaboran en proyectos específicos o de manera continua. Este tipo de equipo de trabajo es común en un entorno industrial debido a su valor para discutir problemas o desafíos con perspectivas variadas.
Los equipos multidisciplinarios transmiten muchos beneficios. Estos incluyen mejores resultados organizacionales y una mayor optimización y un uso más eficiente de los recursos y una mayor satisfacción laboral para los miembros del equipo.
Las ventajas de formar un equipo multidisciplinario son las siguientes:
- Ampliar de perspectiva del trabajo y de análisis.
- Fragmentar la resistencia y criterios preconcebidos. Ahorro de tiempo y energía.
- Mejorar el rendimiento de las competencias individuales.
- Personal calificado para una situación determinada.
- Garantizar el seguimiento de los proyectos.
- No depender de una persona o de una sola profesión.
- Permitir un cierto distanciamiento intelectual respecto a lo cotidiano.
Responsabilidades de los miembros de un equipo multidisciplinario para la aplicación de la metodología de Inspección Basada en Riesgo:

Fuente: Práctica recomendada API 580, Tercera Edición, Febrero 2016.
2.9 Mecanismos de Deterioro
Mecanismos de daños (también conocidos como mecanismos de degradación) es un término general que se refiere a cualquier causa de problemas o fallas dentro del equipo de proceso. Estos pueden variar desde corrosión hasta grietas, daños por calor y todo lo demás.
Al evaluar los mecanismos de daño, se debe tener en cuenta el estado actual del equipo, así como cualquier daño potencial que el mecanismo pueda causar más adelante. La susceptibilidad del equipo a un mecanismo de daño particular se ve afectada por una serie de variables, incluidos los materiales de construcción, los fluidos de proceso, las condiciones de operación, el entorno externo, etc.
Una revisión exhaustiva de los mecanismos de daños es esencial para crear una estrategia de inspección efectiva. Una vez que se entienden los mecanismos y la morfología del daño, los estrategas de inspección pueden usar esta información para seleccionar métodos de inspección con la mayor probabilidad de detectar, caracterizar y medir el daño potencial. Además, los intervalos de inspección se pueden establecer utilizando códigos y estándares de la industria como API 510, 570, 653, API RP 579 para la aptitud para el servicio, y API 580 y 581 para la inspección basada en el riesgo. (Fuente: https://inspectioneering.com).
3 Caso de Estudio Basado en Métodos y Normas Vigentes
El objetivo de este articulo técnico es la de dar a conocer la aplicabilidad de la metodología de inspección basada en riesgo API 581 a intercambiadores de calor en la industria petroquímica. A continuación se mostrará un caso específico de estudio aplicado a un activo físico instalado en una planta de procesamiento de Cloro-Soda.
El método industrial de producción que cubre los requerimientos de estas plantas de Cloro Soda es el de electrólisis (membrana de intercambio iónico) del cloruro sodio e hidróxido de sodio. Para procesar en cantidad, calidad y costos estos valiosos productos químicos, donde la variable temperatura juega un rol importante debido a que se debe mantener un rango óptimo de ella, tanto para la salmuera que alimenta las celdas, como la soda cáustica que se recircula y entra a los electrolizadores. Según lo anteriormente expuesto se recomienda que los electrolizadores de membrana sean operados con lazos de recirculación para la soda cáustica y la salmuera con un intercambiador de calor. Esto permitirá optimizar la temperatura de las celdas y enfriar los electrolizadores en el caso que se detenga la planta y así evitar la producción de soda fuera de especificación. Operando con grandes volúmenes de soda, la planta se hace menos sensible a pequeñas perturbaciones, como por ejemplo: variaciones en la alimentación de agua desmineralizada.
Los tipos de Intercambiadores de calor utilizados para este proceso químico son los de tipo carcasa y tubo, (ver figura 4). Estos intercambiadores tienen ambos extremos del cabezal de tubos sujetos a la carcasa. Así como también la utilización de una junta de expansión debido al diferencial de la carcasa y de los tubos. Esta expansión se debe a la operación del equipo a diferentes temperaturas y a la utilización de diferentes materiales.

Fuente: El autor.
Durante más de 20 años de servicio, el intercambiador de calor HE-E101A ha sido sometido a un ambiente de trabajo externo considerablemente agresivo debido a que este equipo se encuentra cercano a diferentes sistemas de procesos que por su contexto operacional, emanan vapores, como por ejemplo: salmuera, ácido clorhídrico y soda cáustica. Así como también la planta de cloro soda se encuentra cercana a un lago donde esto puede ocasionar un incremento de cloruros en el ambiente.
De lo anteriormente expuesto se puede inferir que la combinación de las condiciones de procesos y materiales existentes de construcción para cada componente del equipo debe ser evaluado para identificar los activos y creíbles mecanismos de daños. A continuación, se mostrará evidencia fotográfica de la condición externa del intercambiador de calor bajo evaluación.

Fuente: El autor.

Fuente: El autor.

Fuente: El autor.
Para los mecanismos de daños mencionados anteriormente, la velocidad de progresión del deterioro pudo ser estimada para este tipo de equipo de proceso de planta. Esto quiere decir que para nuestro caso de estudio, la velocidad de deterioro fue expresada en términos de velocidad de corrosión por adelgazamiento. Asimismo existe la creíble posibilidad de la susceptibilidad de la corrosión bajo tensión donde la velocidad de deterioro es desconocida o inmedible. La susceptibilidad es a menudo designada como alta, media o baja basada sobre las condiciones ambientales y la combinación de los materiales de construcción.
El historial de inspección es la mejor información debido a que pudimos conocer la experiencia operacional del equipo y las condiciones que conllevaron a la velocidad de deterioro observada a ser realísticamente esperada a ocurrir en el equipo bajo consideración. Otra fuente de información incluyó la base de datos de la experiencia con similares equipos de planta y la opinión de expertos.
Para nuestro caso de estudio existe un historial de inspecciones mediante el ensayo no destructivo NDE llamado ultrasonido. A continuación, se muestran las gráficas del análisis de la corrosión monitoreada a través del software Ultrapipe. Es importante mencionar que la base de datos del software fue alimentada con las inspecciones realizadas al intercambiador en paradas programadas de planta.

Fuente: Ultra pipe for corrosion monitoring.

Fuente: Ultra pipe for corrosion monitoring.

Fuente: Ultra pipe for corrosion monitoring.
Las gráficas anteriores muestran el resultado del proceso de deterioro al cual ha sido sometida la pared externa y conexiones principales del intercambiador de calor HE-E101A debido a los mecanismos de daño que suelen ser incrementales, acumulativos y, en algunos casos, irrecuperables. Contrario a la condición mostrada de la parte externa del intercambiador, el haz tubular ha tenido un comportamiento al servicio con una muy baja cantidad de fallas por tubos como se mostrara a continuación.

Fuente: El autor.

Fuente: El autor.
Los estadísticos siempre prefieren grandes muestras de datos, pero los ingenieros se ven obligados a hacer análisis con muestras muy pequeñas, incluso de una a tres fallas. Cuando el resultado de una falla involucra seguridad, daños ambientales, interrupción del negocio, optimización de los recursos de la compañía o costos extremos, es inapropiado solicitar más fallas. La principal ventaja del análisis de la evaluación que se mostrará a continuación, revelará que los objetivos de ingeniería a menudo se pueden cumplir incluso con muestras extremadamente pequeñas. Por supuesto, las muestras pequeñas siempre implican grandes incertidumbres. Para evaluar estas pequeñas incertidumbres muéstrales, los límites de confianza jugaron un rol importante.
Para estimar el riesgo relacionado a la falla de haces tubulares es recomendable evaluarlos mediante la metodología Inspección Basada en Riesgo API 581.
El riesgo es un término de naturaleza probabilística, que se define como la “probable ocurrencia de una falla o evento no deseado”. En este simple pero poderoso concepto coexiste la posibilidad de que un evento o aseveración se haga realidad o se satisfaga, con las consecuencias de que ello ocurra.

El análisis de esta ecuación permite entender el estudio y la toma de decisiones. A través de este indicador, pueden compararse situaciones y escenarios que bajo una perspectiva cotidiana resultarían disímiles, pero bajo ciertas circunstancias deben evaluarse y considerarlas en un proceso de toma de decisiones. Por ejemplo, podría utilizarse para comprender entre diferentes acciones de mantenimiento a equipos estáticos, caracterizados por presentar una frecuencias de fallas bajas pero con consecuencias tradicionalmente muy altas.
Cálculo de la probabilidad de falla.
Ecuación para el cálculo de la probabilidad de falla en haces tubulares.

En API 581 2016 tercera edición, sección 8.3.3. Indica que para realizar una evaluación se debería contar con información proveniente de una biblioteca de confiabilidad de haces de intercambiadores de calor o base de datos instaurada por el propietario o usuario de la instalación. A continuación se describen los aspectos a lograr para realizar una adecuada evaluación.
a) General: Una base de datos o biblioteca de Weibull es extremadamente importante para la evaluación de los riesgos asociados con la falla de haces tubulares. Ciertos detalles del intercambiador son requeridos para ser reunidos por cada haz que ingresa a la base de datos de confiabilidad creada.
b) Análisis de Weibayes: Si la suposición es hecha de que haces similarmente diseñados y en similares servicios tendrán el mismo mecanismo de falla, un enfoque Weibayes puede ser utilizado. Este enfoque asume que los parámetros beta (β) y eta (η) de la curva de Weibull para el conjunto de eventos de similares haces será idéntico al haz que está siendo evaluado. El enfoque Weibayes también permite un análisis estadístico preciso de fallas sin tener una larga cantidad de data para el haz específico que está siendo evaluado.
c) Desarrollar criterios de coincidencia o conjunto de eventos “Cut-Set”: Antes de indicar el significado de cut-set es importante mencionar y conceptualizar lo siguiente:
- Árbol de fallas: Es un diagrama lógico que exhibe la interrelación entre un evento de un sistema crítico y sus causas.
- Análisis del árbol de fallas: Es el análisis cualitativo y cuantitativo que puede ser llevado a cabo sobre las bases de un árbol de fallas.
- Cut-Set: En un árbol de fallas se establece a un cut-set como un conjunto de eventos básicos quienes simultáneamente ocurren asegurando que el evento TOP ocurra. Es importante notar que hay diferentes tipos de mecanismos de falla que un haz de intercambiador de calor puede experimentar.

Fuente: El autor.
d) Prueba de bondad de ajuste: Si un diagrama de Weibull es creado a partir de un conjunto de eventos demasiado extenso y sobre la base de datos de una biblioteca de confiabilidad y si los datos no están correctamente diagramados. Entonces la probable razón de esto, es que múltiples mecanismos de fallas están siendo diagramados y una lista más específica de criterios coincidentes es requerida para aislar las fallas para un mecanismo. Una prueba de bondad de ajuste debería ser usado para determinar si o no el subconjunto de datos es incorrecto. Una vez esto es logrado, hay confianza agregada en la distribución Weibull y el conjunto de eventos es aplicable a él específico haz tubular del intercambiador de calor que está siendo evaluado.
e) Determinación de los parámetros de la curva de Weibull desde datos coincidentes: Después que haces similares han sido combinados desde la base de datos y diagramados sobre Weibull así como también una prueba de ajuste de bondad ha sido aplicada, entonces los parámetros beta (β) y eta (η) serán obtenidos en conformidad con el Weibull Handbook.
Caso real aplicado a un activo físico instalado en la industria petroquímica. Cálculo de la probabilidad de falla utilizando Weibayes’ con base de datos de fallas.
Para calcular la probabilidad de falla como una función del tiempo en servicio para un haz de intercambiador de calor, una base de datos de confiabilidad y/o inspección fue investigada y donde se encontró una combinación de haces tubulares de igual característica y servicio:

Fuente: El autor.
Para estimar o calcular la probabilidad de falla de un haz tubular, éste puede ser realizado utilizando el método que mejor se ajuste a la base de datos disponible para el momento de ejecutar la evaluación. Es importante indicar que la práctica recomendada, API 581 Inspección Basada en Riesgo, 3 tercera edición. Parte 1. Metodología de la planificación de la inspección, más específicamente en la sección 8: Haz de tubos del intercambiador de calor, muestra que hay cuatro (4) métodos para calcular la probabilidad de falla de un haz tubular.
Metodología de inspección basada en riesgo (Referencia API 581 2016 Parte 1. Metodología de planificación de inspección)
La aplicación de los principios de riesgo a la inspección de haces tubulares del intercambiador permite tomar decisiones basadas en las consecuencias de la falla del haz, incluidos los costos asociados con la pérdida de producción y los costos de impacto ambiental, los costos de reemplazo y mantenimiento asociados con el reemplazo del haz.
Para facilitar una predicción más precisa del rendimiento futuro del haz, la experiencia combinada de otros haces tubulares de intercambiadores de calor de diseño y servicio similar pueden combinarse y analizarse estadísticamente. Con este método, es crítico que el usuario (departamento de confiabilidad, integridad mecánica, inspección de equipos estáticos, corrosión y materiales, custodio de la instalación) o llámese como se llame dentro de una organización quien es responsable por llevar la estadística de falla de los equipos, mantenga una base de datos de fallas real de los haces de intercambiador de calor.
De lo anteriormente descrito podríamos agregar que no solo es importante llevar una base de datos de fallas de los haces tubulares de intercambiador de calor. Es más importante determinar la efectividad de inspecciones pasadas que hayan ejecutado el departamento de inspección mediante la combinación de métodos de examen no destructivo (NDE) como visual, ultrasónico (UT), radiográfico, etc. Registrar la falla de uno o más tubos de un haz tubular son necesarios, ya que indicar la frecuencia, cobertura, ubicación y efectividad para localizar, caracterizar y determinar el tamaño y velocidad del deterioro, es sumamente importante para después identificar los mecanismos de daños creíbles y probables y posteriormente determinar la efectividad en la búsqueda de los mismos. La reducción de la incertidumbre sobre el estado del daño de un componente es una función de la efectividad de la inspección para detectar, caracterizar y cuantificar el tipo y la extensión del daño.
Análisis para evaluar la probabilidad de falla en haces tubulares con o sin fallas. Para este caso de estudio en particular hemos seleccionado el método 4 “API 581 Sección 8”. Haces tubulares de intercambiadores de calor” debido a que el mismo se ajusta a la base de datos disponible para realizar la evaluación de un Haz Tubular.
Es conocido que los equipos estáticos tienden a una frecuencia de falla baja pero con consecuencias tradicionalmente muy altas. Qué hacer cuando existe una frecuencia de falla muy baja? Por ejemplo; para pequeñas muestras (entre 1 y 3) o cero fallas. Existe un método de análisis que puede ser útil para realizar evaluaciones bajo las características mencionadas con anterioridad. Ese método es llamado Weibull ya que tiene un gran beneficio y puede ser útil para evaluaciones con extremadamente muestras pequeñas de fallas y conjunto de datos que tienen mayores deficiencias, el cual puede ser llamado “dirty data” Cada industria tiene este tipo de información, aunque esta situación puede mejorar donde las gerencias se han dado cuenta de la efectividad en los resultados al adquirir alta calidad de datos de información.
Un análisis Weibayes es un método para construir una distribución de Weibull basada sobre un conocido o asumido valor del parámetro de forma (β), el parámetro (β) de Weibull es usado cuando hay ciertas deficiencias en la información (data) por ejemplo, en el histórico de fallas, experiencia previa o conocimiento ingenieril de la física de la falla.; cuando no hay fallas o pocas fallas, un análisis Weibayes es significativamente más preciso que Weibull, ya que puede ser derivada usando el Método de Máxima Probabilidad (MLE) para determinar la característica de vida (η). Esto es útil para tratar conjunto de datos que pueden tener interrupciones.
Una interrupción puede ser definida como una unidad que no ha fallado por un modo de falla o no fallar del todo. Para citar un ejemplo: Un perno que falla en la cabeza en una prueba de esfuerzo es una interrupción.
La ventaja de utilizar el análisis de Weibayes es que se pueden tomar decisiones acertadas de ingeniería con significativamente menos puntos de datos de falla como se necesitaría con otras distribuciones estadísticas. El enfoque de Weibayes se utiliza ya que este método incorpora la experiencia pasada de otros haces similares (biblioteca de Weibull o base de datos) con los datos específicos disponibles para el haz tubular que se está evaluando.
Situación típica con falla:
- Con pequeñas muestras Weibayes es más preciso que Weibull si hay conocimiento previo de beta (β).
- Pruebas de sustentación pueden ser diseñadas con los más pequeños tamaños de muestras posibles si Weibayes es empleado.
- Las pruebas de muerte súbita son también buenos candidatos de Weibayes.
- Los tiempos de operación de las unidades y los números de fallas son conocidos, pero las fallas no son identificadas. Reparaciones generales puede generar este tipo de información.
Para el caso de estudio hemos obtenido un valor del parámetro Beta (β) mediante una prueba de ajuste de bondad RARE. Los datos de tiempos entre fallas (TPF) para realizar la evaluación fueron tomados del comportamiento en servicio de los haces tubulares compatibles al intercambiador HE-E101-B/C mostrados en la Tabla 4. Por motivos de confidencialidad se mostrarán las siguientes gráficas realizadas sin mostrar los datos de TPF.

Fuente: El autor.
Finalizada la caracterización de la variable a través del RARE (Distribution Estimation), los resultados indican que la distribución Weibull es la distribución que mejor representa a los datos.

Fuente: Reliability engineering & risk analysis 1999 by Modarres, Kaminskiy & Krivtsov RARE.
Una vez obtenido el valor del parámetro y los datos suministrados en la Tabla 4 para los haces tubulares compatibles o coincidentes se procedió a estimar la Probabilidad de Falla (POF) para el haz tubular HE-E101-B que ha presentado historial de fallas.
Cálculo de la probabilidad de falla POF a través de la “Sección 8. Haces tubulares de intercambiadores de calor” (Referencia API 581 2016 Parte 1. Metodología de planificación de inspección)
Utilización del Método 4.El cual especifica que una vez acumulado suficiente historial de inspección, la estadística para el haz podría ser determinado. El parámetro Eta (η) o también conocido como característica de vida puede ser recalculado utilizando la ecuación 3.

Para simular los datos de la Tabla 4 con el propósito de conocer un valor inicial del parámetro Eta (η). Fue necesario utilizar el software SuperSMITH ya que el mismo se considera como el avance técnico más significativo. Este software se considera amigable y fácil de usar. El software ha hecho la aplicación mucho más fácil, eficiente y divertida.
Simulación de los datos de la Tabla 3. Utilizando el software SuperSMITH de Weibull.
Esta referencia puede parecer inapropiada, pero la dependencia del software se requiere. Ya que si el evaluador lo desea, puede evitar casi todos los cálculos y trazados manuales utilizando SuperSMITH, pero en la humilde opinión de los autores de este artículo, recomiendmos realizar los primeros cálculos de forma manual ya que esto le proporcionará al evaluador un mayor entendimiento de las suposiciones necesarias para estimar los parámetros Beta (β) y Eta (η) de Weibull.
Simulación del parámetro Eta (η) con un intervalo de confianza de límite inferior (LBC) del 90%.
Esta simulación indica un valor inicial del parámetro Eta (η) así como un valor pronosticado de una inspección recomendada en años. Es importante mencionar que la mayoría de los estadísticos utilizarán límites de confianza en datos de esta naturaleza para dar cuenta de la distribución estadística en los datos. Se recomendó un intervalo de confianza de límite inferior (LBC) del 90%. Esto representa el conjunto de haces tubulares coincidentes en la base de datos de confiabilidad.

Fuente: DEMO Súper SMITH WEIBUL software by Fulton Findings.
Para citar un ejemplo sobre cómo se debe calcular el riesgo en cualquier punto del tiempo. La Grafica x proporciona la curva POF para el caso de estudio utilizando los haces de intercambiadores de calor correspondientes de la base de datos. Con los parámetros de Weibull definidos, el POF en función del tiempo se determina para el caso de estudio usando la ecuación 2.

Una vez que el haz tubular ha acumulado al menos dos ciclos de vida con datos de inspección, se puede realizar un análisis de Weibayes manteniendo el parámetro Beta (β) igual al determinado a partir de los criterios de haces tubulares coincidentes. El parámetro Eta (η) de vida característica se puede volver a recalcular utilizando la ecuación 3.

Para obtener el valor de la probabilidad de falla del haz tubular mediante la ecuación 1, se utilizó el valor recalculado del parámetro Eta (η).

Estimación de la Confiabilidad del Haz Tubular para los próximos 20 años, partiendo del cálculo anteriormente realizado de la probabilidad de falla.

Fuente: El autor.

Fuente: El autor.
Reducción de la incertidumbre a través de la inspección. Podríamos hacernos una pregunta. ¿Cómo introducir incertidumbre?
Bueno, si no hay un gran muestreo de datos de inspección para el haz, entonces existe un grado de incertidumbre asociado con respecto a si el conjunto coincidente de haces tubulares de la base de datos de fallas representa con precisión el haz que se está evaluando. Para tener en cuenta las imprecisiones y los sesgos inherentes a la base de datos de fallas, se introduce incertidumbre adicional en las estadísticas. Se utiliza un valor predeterminado para una incertidumbre adicional del 50%.
Gestión del riesgo mediante la reducción de la incertidumbre a través de la inspección.
El riesgo puede gestionarse mediante inspección. Obviamente, la inspección en sí no detiene ni mitiga los mecanismos de daño ni reduce el riesgo, pero la información obtenida a través de una inspección efectiva puede cuantificar mejor el riesgo real. Las actividades de inspección no evitan la falla inminente del equipo a menos que la inspección precipite las actividades de mitigación de riesgos que cambian la probabilidad de falla POF.
La inspección sirve para identificar, monitorear y medir los mecanismos de daño. Es una aportación invaluable en la predicción de cuándo el daño alcanzará un punto crítico. La correcta aplicación de las inspecciones mejorará la capacidad del usuario para predecir los mecanismos de daño y las tasas de deterioro. Cuanto mejor sea la previsibilidad, menos incertidumbre habrá sobre cuándo puede ocurrir una falla. La mitigación (reparación, reemplazo, cambios, etc.) se puede planificar e implementar antes de la fecha de falla prevista. La reducción de la incertidumbre y el aumento de la previsibilidad a través de la inspección se traduce directamente en una mejor estimación de la probabilidad de falla y, por lo tanto, en una reducción del riesgo calculado. Sin embargo, los usuarios deben ser diligentes para garantizar que las alternativas de inspección temporal, en lugar de reducciones de riesgo más permanentes, sean realmente efectivas.
La mitigación de riesgos (por la reducción de la incertidumbre) lograda mediante la inspección supone que las organizaciones actuarán de manera oportuna sobre los resultados de la inspección. La mitigación del riesgo no se logra si los datos de inspección que se recopilan no se analizan y actúan adecuadamente cuando es necesario. La calidad de los datos de inspección y el análisis o interpretación afectarán en gran medida el nivel de mitigación de riesgos. Por lo tanto, los métodos de inspección adecuados y las herramientas de análisis de datos son fundamentales.
Simulación donde se introduce una adición de la incertidumbre del 50%.

Fuente: DEMO SuperSMITH WEIBUL software by Fulton Findings.
Si el haz tubular no tiene registro de inspección y no existe conocimiento de la condición del mismo, la curva de incertidumbre del 50% se usa para predecir el POF como una función del tiempo. El riesgo calculado para un haz tubular sin ningún conocimiento de inspección será mayor que para un haz tubular que tiene registros de inspección. Aunque la acción de inspección no reduce el riesgo en sí misma, esto está de acuerdo con los principios de RBI que establecen que cuanto más conocimiento se obtenga para un componente de equipo, menos incertidumbre existe, lo que resulta en una reducción del riesgo calculado.
En la Gráfica 7, se visualiza que la inspección recomendada sería 13.7 años. Esto se compara con un valor pronosticado de 19.8 años mostrado en la Gráfica 5, donde se usaron los datos sin procesar (90% LBC) que representan el conjunto de haces tubulares coincidentes en la base de datos de confiabilidad. Esto muestra el efecto directo que la incertidumbre de la inspección tiene sobre el riesgo calculado y el plan de inspección posterior.
Cálculo de las consecuencias de la Falla.
Método de cálculo: La falla del haz tubular es definida como una fuga del tubo. Las consecuencias financieras son determinadas basadas en la criticidad del haz, el cual incluye costos asociados con pérdida de oportunidad debido a tiempos debajo de producción, costos por impacto ambiental, costos asociados con mantenimiento y reemplazo del haz tubular. Las consecuencias de un paro no planificado debido a fuga del tubo del haz tubular es determinada usando la ecuación 4.

La producción de la unidad o costos de la pérdida de producción, es determinada usando la ecuación 5.

El costo al impacto ambiental se estimó considerando daños a las áreas ambientales cercanas al intercambiador o que el producto liberado, debido a la pérdida de contención interna, conlleve a la contaminación con el medio calentador (vapor) o enfriador (agua de enfriamiento) y este a su vez fuera enviado a la zona de desecho de productos químicos de la planta y que no pudiese ser neutralizado correctamente.

La siguiente ecuación puede ser usada para estimar los costos de reemplazo del haz tubular.

Es importante destacar que para este caso de estudio en particular se realizó el cálculo de , considerando la falla funcional o falla del tubo en el intercambiador de calor que pudiera conllevar a una pérdida de contención del mismo o equipo auxiliar. Estos típicamente supondrían una fuga desde un lugar de alta presión a uno de baja presión del intercambiador y abrir una posterior contaminación al sitio de baja presión. Fallas en tubos de intercambiadores de calor pueden resultar en una contaminación del sistema de agua enfriamiento o vapor con materiales tóxicos y consecuentemente obtener pérdida de contención con consecuencias a la seguridad, salud e impacto ambiental. Ahora bien, para establecer el cálculo total del haz tubular se tiene que considerar la totalidad de los tubos así como las placas tubulares.

Se calculó los Costos de mantenimiento considerando la mano de obra que intervendría al momento de fallar alguno de los tubos del haz tubular; este recurso pudiera estar distribuido de la siguiente forma: técnicos mecánicos, grupo de soldadura, montacargas, máquinas de soldadura, operadores, entre otros.

Costo total de las consecuencias de fallas

Administración del Riesgo mediante la limitación de cualquier consecuencia negativa o reducción en probabilidad de un particular evento.
Las evaluaciones previas realizadas al haz tubular del intercambiador de calor HE-E101-A indican que sería posible realizar alguna actividad de mitigación del riesgo al equipo, como por ejemplo: modificar a través de un rediseño, reemplazo general o revaloración de toda la sección externa del equipo, con el propósito de mantener el haz tubular en continuo servicio.
Hay metodologías que apoyan los procesos de toma de decisiones para evitar tomar decisiones arbitrarias o inconsistentes, sin base en la información disponible y que no cumplan con los objetivos medulares del negocio. Resultan particularmente útiles para decidir en escenarios con intereses en conflicto, como el escenario “operación – mantenimiento”, en el cual el operador requiere que el equipo o proceso opere en forma continua para garantizar máxima producción, y simultáneamente, el mantenedor requiere que el proceso se detenga con cierta frecuencia para poder mantener y ganar confiabilidad en el mismo.
Recordemos que cuando el deterioro de un equipo ha alcanzado un punto en el que el riesgo de falla no se puede manejar a un nivel aceptable, el reemplazo / reparación es a menudo la única forma de mitigar el riesgo.
En opinión de los autores de este artículo, la toma de decisiones en la alta dirección de una organización se fundamenta no solo en que la alternativa propuesta sea técnicamente factible, sino también debe ser económicamente rentable y presupuestariamente viable para garantizar que las inversiones sean oportunas para maximizar la rentabilidad del negocio. Por lo anteriormente expuesto fue necesario agregar una evaluación económica para soportar la decisión eficaz para mitigar el riesgo relativo relacionado a los componentes externos del intercambiador de calor HE-E101-A.
Como gestionar el riesgo: En función de la clasificación de los elementos, se podría iniciar un proceso de gestión de los riesgos. Por ejemplo; Para aquellos riesgos que se juzgan aceptables, no se requiere mitigación y no se requieren acciones adicionales pero para los riesgos considerados inaceptables y, por lo tanto, que requieren mitigación de riesgos, existen varias categorías de mitigación que deberían ser considerados, como por ejemplo:
- Mitigación de probabilidad: ¿se pueden tomar medidas para disminuir la POF, como los cambios en el material de construcción, cambios operativos o rediseño de equipos? Ahora se pueden tomar decisiones de gestión de riesgos sobre qué medidas de mitigación tomar.
Modificación, rediseño y revaloración de equipos.
La modificación y el rediseño de los equipos, utilizando un proceso riguroso de MOC, pueden proporcionar mitigación de POF. Ejemplos Incluya lo siguiente:
- Cambio de metalurgia.
- Adición de revestimientos.
- Eliminación de las piernas muertas.
- Mayor tolerancia a la corrosión.
- Cambios físicos que ayudarán a controlar / minimizar el deterioro.
- Mejoras de aislamiento.
- Cambios en el diseño del punto de inyección.
- Cambio de tamaño del dispositivo de alivio.
4 Evaluación económica del haz tubular del intercambiador de calor HE-E101-A
La decisión de reemplazar o continuar manteniendo un determinado equipo representa uno de los elementos fundamentales de la estrategia de desarrollo de una industria o empresa. Un reemplazo postergado más tiempo del razonable puede elevar los costos de producción debido a una serie de problemas fáciles de identificar. Un reemplazo prematuro puede ocasionar el desvío de recursos que pudieran tener otras prioridades para la empresa, además de los costos de oportunidad que implican no trabajar con adecuadas estructuras y óptimos costos y riesgos. El estudio de las inversiones de modernización por la vía del reemplazo es el más simple de realizar, la metodología a aplicar en este artículo, es el análisis económico del costo de ciclo de vida, la cual se basa en estimar o pronosticar todos los posibles “flujos de caja” durante toda la vida útil de un activo, sistema o proceso; incluyendo todas las fases desde el diseño, procura, construcción, operación, mantenimiento hasta su desincorporación y en la conversión de estos flujos de caja proyectados o futuros, a un valor económicamente comparable considerando el valor del dinero en el tiempo para equipo con vida diferente.
Suposiciones para la aplicación del modelo:
- La inflación se considera a través de la tasa real de interés (Tasa de descuento) de la empresa.
- Los costos de operación y mantenimiento del equipo por unidad de tiempo se incrementan con el tiempo y son considerados al final de cada año.
- El reemplazo es por un equipo idéntico al instalado.
- El valor de salvamento o reventa decrece con el tiempo.
- El análisis se realizará para un modo de falla predominante en función de las penalizaciones al momento de ocurrir la pérdida de la función.
Como puede observarse, los costos de operación y mantenimiento del equipo actual van aumentando a medida que aumenta el número de periodos “n” para reemplazar el equipo, mientras que los costos de operación y mantenimiento del equipo nuevo van disminuyendo puesto que opera menos tiempo.
Como puede observarse en la siguiente tabla, la vida útil económica del equipo nuevo obtenida con la aplicación del modelo matemático para un periodo indefinido arrojó un resultado igual a 6 años, mientras que la vida remanente para el equipo actual es 20 años, es decir, el tiempo óptimo para reemplazar el activo actual está en el futuro. La recomendación es mantener el equipo instalado más tiempo en operación de tal manera de maximizar la rentabilidad del negocio. Realizar el reemplazo del activo antes de este tiempo estaríamos incurriendo en un desembolso de dinero el cual podría ser aplicado o direccionado a otras oportunidad de inversión de capital en la organización. Este cálculo matemático considerando las evaluaciones financieras soportan los resultados obtenidos en los cálculos mostrados en las primeras líneas de este artículo.

Fuente: El autor.
A continuación se mostrará evidencia fotográfica de los resultados obtenidos al aplicar la acción de mitigación: REEMPLAZO DE TODOS LOS COMPONENTES EXTERNOS DEL INTERCAMBIADOR DE CALOR HE-E101-A.

Fuente: El autor.

Fuente: El autor.

Fuente: El autor.
Actualización del intervalo de inspección del intercambiador de calor una vez sometido a REEMPLAZO DE TODOS LOS COMPONENTES EXTERNOS.
Una inspección no solo reduce la incertidumbre en los datos, sino que también proporciona conocimiento de la actual condición del haz tubular. Se puede determinar que el haz está en óptimas condiciones y que la probabilidad de falla POF es demasiado conservador. Por el contrario, también se puede determinar que el haz está en peor condición de lo que se ha predicho usando la información de un haz tubular en un servicio similar.
Donde la corrosión general es el mecanismo de control de daños en el haz, el promedio medido de los datos de espesor del tubo pueden usarse para predecir la fecha futura de inspección del haz tubular. Por otro mecanismo de daño como vibración, adelgazamiento del extremo del tubo, etc. o donde no existen datos medidos de espesor.
Cualquiera que sea el método utilizado para calcular una fecha futura basada en un registro de inspección, el pronóstico de los datos puede ser usado para modificar la curva POF base.
Fecha de inspección basada en datos medidos de espesor
La tasa de adelgazamiento del haz de tubos se puede determinar utilizando el espesor de pared promedio suministrada y el espesor de pared medido en la última inspección.
La tasa de adelgazamiento del haz de tubos se calcula utilizando la siguiente ecuación

La vida útil prevista del haz tubular ajustado para inspección, se calcula utilizando la siguiente ecuación:

A este ritmo, el espesor promedio de la pared alcanzaría el 50% del espesor original o el resto espesor de pared RWTƒ en 10 años.
Ajuste a la curva de tasa de falla basada en la condición real del haz tubular

El intervalo de inspección recomendado en el POF máximo aceptable del 50%

Conclusiones
- Para efectos de evaluaciones como la realizada en este artículo es estrictamente importante contar con un sistema de gerencia del dato, ya que resulta muy complicado reducir la incertidumbre con muy o poca información (conjunto de datos o base de datos) disponible por las organizaciones.
- La información obtenida de la inspecciones del haz tubular, fue utilizada no solo para cuantificar la actual o real condición del equipo (espesor de pared restante, velocidad de corrosión o estimado de la vida remanente) sino que también pudo ser usada en la toma de decisiones acertadas respecto a mitigar el riesgo relativo relacionado a la posible pérdida de contención de tubos o carcasa externa y hacer ajustes a las curvas de tasa de POF.
- Se redujo la incertidumbre respecto a la actual o real condición del equipo esto quiere decir que la curva graficada de POF mediante SSW (Datos confidenciales) se movió hacia la derecha y el POF disminuye. De esta manera, el conocimiento de inspección adquirido durante la intervención (Parada Mayor) del intercambiador de calor reduce el POF y el cálculo del riesgo.
- La vida remanente económica del intercambiador actual se pudo calcular por conocer un reemplazo posible.
- La vida útil económica del intercambiador depende de la diferencia de desempeños entre el activo actual y el posible reemplazo y del costo del reemplazo y de su deterioro en el tiempo.
- El desempeño del activo actual y el posible reemplazo se evalúo en términos de costos y riesgos.
- Como la opción ganadora es mantener el equipo actual se debe realizar nuevamente el análisis en el próximo mantenimiento mayor para verificar si sigue siendo la mejor alternativa, o existe otra alternativa en el mercado con un CAE menor que la opción actual.
- Si la inflación es constante por unidad de tiempo no debemos preocuparnos por su efecto.
Recomendaciones
- Mantener el intercambiador de calor HE-E101-A por más tiempo en operación para maximizar la rentabilidad del negocio.
- Reducir la incertidumbre sobre el actual o real estado del daño del haz tubular HE-E101-A o componente asociados mediante la selección de inspecciones efectivas para detectar, caracterizar y cuantificar el tipo y la extensión de posibles nuevos mecanismos de deterioro.
- Ejecutar actividades de inspección del haz tubular HE-E101-A para actualizar la base de datos recolectados con el propósito de cuantificar la actual o real condición del equipo (espesor de pared restante, velocidad de corrosión o estimado de la vida remanente).
- Adiestrar al personal de inspección y confiabilidad de equipos estáticos de la organización en la implementación de la metodología de Inspección Basada en Riesgo API 580 / 581 para planificar un adecuado plan de inspección con el propósito de conocer; Qué inspeccionar, Cómo inspeccionar (técnica), Dónde inspeccionar (ubicación), Cuánto inspeccionar (cobertura) y Cuándo inspeccionar.
- Seleccionar las mejores alternativas en base a conocimiento previo a través de evaluaciones y resultados técnicos, con el propósito de optimizar los recursos asignados a la intervención de equipos estáticos de la organización y no tomarlas en base a solo conocimiento empírico y / o reactivo.
Referencias y Lecturas Complementarias
- Risk Based Inspection API Recommended Practice 580 Third Edition, February 2016.
- Risk Based Inspection Methodology API Recommended Practice 581 Third Edition, April 2016.
- The New Weibull Handbook, Fifth Edition by Dr. Robert B. Abernethy 2004.
- Alloy Selection for Caustic Soda Service by C.M. Schillmoller. NIDI Technical Series N° 10019.
- TEMA Standards of Tubular Exchanger Manufacture Association. Eight Edition.
- Ultrapipe of Siemens for corrosion monitoring and remaining life.
- ISO – 55000 Asset Management — Overview, Principles and Terminology, 2014.
- John Woodhouse.: ‘Asset Management Decision-Making: The SALVO Process’, Strategic Assets: Life Cycle Value Optimization, United Kingdom, TWPL. 2014.
- Edgar Fuenmayor. Análisis de Reemplazo de un Activo Basado en Costos de Ciclo de Vida. Revista Confiabilidad Industrial Nº 11. Venezuela. 2011. www.confiabilidad.com.ve
- UNE – EN 60300 – 3 – 3 Cálculo del Costo del Ciclo de Vida. 2009.
- ISO – 15663 (E) Petroleum and natural gas industries – Life Cycle Costing, 2001.
- John Woodhouse.: ‘Managing Industrial Risk’, Getting value for money in your business, London, Chapman & Hall. 1993.
Autores:
Evelio Chirinos
Venezuela
Supervisor de mantenimiento mecánico
Empresa: Petroquímica de Venezuela
Correo: evelioch30@hotmail.com
Ingeniero Mecánico con más de 11 años en la industria petroquímica venezolana con experiencia en las áreas de mantenimiento mecánico, inspección y confiabilidad de equipos estáticos, administración del riesgo e integridad mecánica.
Rosangel Leal
Venezuela
Ingeniera de confiabilidad
Empresa: Petroquímica de Venezuela
Correo: rosangelcristal@gmail.com
Ingeniera química con experiencia en la industria petroquímica en el área de confiabilidad mecánica empleando metodologías centradas en mantenimiento, gestión del riesgo y análisis de criticidad.
Edgar Fuenmayor
Venezuela
Consultor
Empresa: Machinery & Reliability Institute – MRI
Correo: edgarfuenmayor1@gmail.com
Es Ingeniero Mecánico con Maestría en Gerencia de Mantenimiento de la Universidad del Zulia en Venezuela. Es un Profesional Certificado en Mantenimiento y Confiabilidad (CMRP) por la Sociedad de Profesionales de Mantenimiento y Confiabilidad (SMRP) en USA. Es Profesor Universitario, Articulista y Conferencista de Trabajos de Ingeniería de Confiabilidad, Mantenimiento y Gestión de Activos. Actualmente es Consultor para la firma Machinery & Reliability Institute – MRI.
Dinos qué te ha parecido el artículo
Artículos recomendados
Predictiva21 llega a su edición número 40, por lo que hemos preparado una entrevista con dos versiones complementarias de la trayectoria de la revista, el origen y el futuro.

Aspectos claves en la gestión de inventarios

Monitoreo de condición a equipos dinámicos

Implementar KPIs en lubricación no es tan difícil como parece

Publica tu artículo en la revista #1 de Mantenimiento Industrial
Publicar un artículo en la revista es gratis, no tiene costo.
Solo debes asegurarte que no sea un artículo comercial.
¿Qué esperas?
O envía tu artículo directo: articulos@predictiva21.com
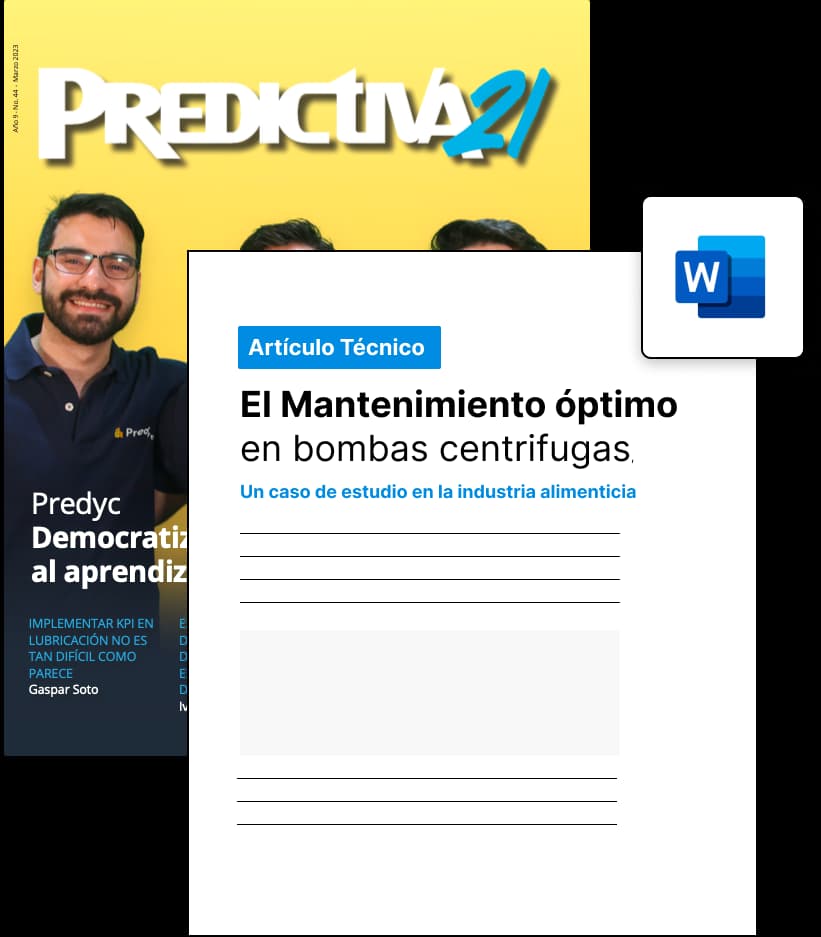