RCM II: Reliability Centered Maintenance - John Moubray
Libros>Reseña - Tienda15 de marzo de 2020
Introducción al tema

El Mantenimiento Centrado en la Confiabilidad, conocido por sus siglas en inglés como RCM (Reliability Centered Maintenance), comenzó a desarrollarse dentro de la industria de la aviación, convirtiéndose exponencialmente en un pilar fundamental en la práctica de la gestión de mantenimiento. Actualmente es aplicado en todo el mundo por muchas organizaciones industriales y prestadoras de servicios. En el clásico libro de John Moubray titulado "RCM 2: Reliability Centered Maintenance Second Edition 2 Revised edition by Moubray, John (1997) Hardcover" se expone información práctica, autorizada y sobre la aplicación correspondiente del RCM. Representa un aspecto fundamental para los ingenieros centrados en su productividad, calidad, seguridad e integridad ambiental. Moubray se caracteriza por ser experto en el área y ha prestado ayuda a profesionales de muchos países en la aplicación del RCM y de su sucesor, el RCM2.
[su_button url="https://amzn.to/2lpWeo5" target="blank" style="flat" size="6" center="yes" rel="nofollow"]Comprar en Amazon[/su_button]¿Qué es el RCM2?
El término de RCM2 se refiere a una versión mejorada del RCM, realizada por el autor John Moubray, la cual consiste en la aplicación de la metodología del Mantenimiento Centrado en la Confiabilidad en el ámbito industrial.
Documentación del RCM2 de John Moubray
Consiste en un libro de texto muy utilizado cuyo primer número se publicó en el Reino Unido en 1991 y en los Estados Unidos en 1992. Como resultado, se realizaron varias actualizaciones y versiones, producidas por la compañía británica “The Aladon Network” (conocida inicialmente como Aladon Ltd en 1986 y luego como Aladon LLC en 1998), fundada por Moubray y dirigida por el mismo como director ejecutivo hasta su fallecimiento en 2004. Actualmente la compañía se dedica a difundir e implementar la metodología de RCM alrededor del mundo.
El contenido de la segunda edición del libro de Moubray abarca temas tales como las funciones de los activos físicos, fallos funcionales, análisis de modos de fallo y sus efectos, consecuencias de los fallos, diagramas de decisión RCM, implementación de recomendaciones de RCM, datos de los fallos, aplicación del proceso RCM, beneficios el RCM, historia del RCM, un glosario de términos, y algunos detalles adicionales.
A continuación se presenta un resumen en español de los capítulos del libro.
Historia del RCM
En la década de 1960 se presentó una cantidad inaceptable de accidentes de aviación, lo cual motivó a un equipo de ejecutivos e ingenieros de alto nivel de United Airlines a desarrollar un proceso para determinar los requerimientos de mantenimiento óptimos de las aeronaves, lo cual dio origen a documentos públicos donde se utilizó por primera vez el termino de Mantenimiento centrado en la confiabilidad o RCM (Reliability Centered Maintenance). Los estudios demostraron que el supuesto fundamental de los ingenieros de diseño y de los planificadores de mantenimiento era que cada avión y cada componente principal del mismo tenían una "vida útil" específica de servicio confiable, después de ello tenía que ser reemplazado o revisado para así prevenir fallas.
Años más tarde, United Airlines fue patrocinada por el Departamento de Defensa de los Estados Unidos para la creación de un libro sobre el RCM, el cual fue publicado en el año 1978 en conjunto con un informe de evaluación de Rand Corporation, ambos textos dieron a conocer al RCM al público en general. Este fue uno de los muchos descubrimientos sorprendentes que han revolucionado la disciplina administrativa de la gestión de los activos físicos. Entre algunos de los cambios de paradigma inspirados en RCM fueron que el entendimiento de que la gran mayoría de las fallas no están necesariamente vinculadas a la edad del activo, la comprensión de la diferencia entre los requisitos de los activos desde la perspectiva del usuario y la confiabilidad del diseño del activo, la comprensión de la importancia de administrar los activos bajo condición y la vinculación de niveles de riesgo tolerable al desarrollo de la estrategia de mantenimiento.
A partir del año 1980 se extiende el uso de la metodología para la industria naval y en la armada, algunos años después se aplicó para la industria nuclear de Estados Unidos. Para el año 1993 se comenzó a aplicar en Francia. Moubray obtuvo el mayor éxito en su aproximación a la industria con el RCM mediante la creación de la metodología de RCM2, la cual incorporó cuestiones ambientales, precisión de tareas de mantenimiento y la definición de criterios de riesgo cuantitativos. Fue en el año 1999 donde se normalizó el proceso de RCM2 mediante la normativa SAE JA1011, con el documento “Criterios de Evaluación para Procesos de Mantenimiento Centrado en la Confiabilidad”, el cual establece los criterios mínimos para lo que es, y para lo que no se puede definir como RCM.
El estándar es algo decisivo en la evolución continua de la disciplina de la gestión de activos físicos. Antes del desarrollo del estándar, muchos procesos se etiquetaban como RCM, aunque no eran fieles a las intenciones y los principios del informe original que definían el término públicamente.
Hoy en día, las compañías pueden usar este estándar para garantizar que los procesos, servicios y software que compran e implementen se ajusten a lo que se define como RCM, lo que garantiza la mejor posibilidad de lograr los muchos beneficios atribuibles a la aplicación rigurosa de RCM.
Funciones de los activos físicos en RCM
Los usuarios de los activos tienen la expectativa de que el activo además de cumplir con una función, lo haga con un nivel de funcionamiento aceptable, por lo tanto la definición de una función en conjunto con la definición de los objetivos de mantenimiento para ese activo físico no estarían completas a menos que el usuario detalle de la manera más precisa posible el nivel de funcionamiento esperado. Por lo tanto:
“La definición de una función consiste de un verbo, un objeto y el estándar de funcionamiento deseado por el usuario.”
Reliability Centered Maintenance Second Edition 2 Revised edition by Moubray, John (1997)
La finalidad del mantenimiento es asegurar que los activos físicos se mantengan realizando la labor que sus usuarios desean, cuya magnitud debería definirse mediante un estándar mínimo de funcionamiento. Lo ideal sería que los activos puedan mantenerse en el rendimiento de su funcionamiento mínimo de manera indefinida, es decir, sin deteriorarse en ningún momento, por lo tanto las máquinas nunca tendrían la necesidad de mantenimiento, pero a causa de las leyes de la física esto no es posible, puesto que cualquier sistema organizado expuesto al mundo real se deteriorará, teniendo como consecuencia situaciones impredecibles que conllevan al caos o a la entropía. En este sentido el mantenimiento centrado en la confiabilidad se aplica para detener los procesas que causan el deterioro de los sistemas.
Fallas Funcionales en RCM
Un activo físico presenta fallas cuando este no cumple con la función esperada por el usuario. Todo lo que se requiere que haga el activo es definido como una función y cada una de ellos tiene más de una función y frecuentemente muchas diferentes. Ya que es posible que cada una de estas funciones presente una falla, se deduce que cualquier activo puede sufrir una variedad de estados de falla distintos. Esto demuestra por qué es más preciso definir fallas en términos de pérdida de funciones específicas, en lugar de la falla de un activo en su conjunto. El proceso de RCM utiliza el término "falla funcional" para describir estados de falla y no a una “falla” por sí sola, por lo tanto para completar la definición de falla, se debe analizar más de cerca la cuestión de los estándares de rendimiento. Entonces:
“Una falla funcional se define como la incapacidad de cualquier activo físico de cumplir una función según un parámetro de funcionamiento aceptable para el usuario.”
Reliability Centered Maintenance Second Edition 2 Revised edition by Moubray, John (1997)
Cursos recomendados






%252FImagen%252FRAMPREDYC-1730060420837.webp%3Falt%3Dmedia%26token%3D2634a7f0-988e-4022-b91f-382503e6e9db&w=3840&q=75)

Análisis de Modos de Falla y sus Efectos en RCM
Un modo de falla puede ser descrita como una situación que probablemente haga que un activo, sistema o proceso falle. Es necesario diferenciar una "falla funcional" y un "modo de falla" por consiguiente se pude definir de manera más precisa lo que es un “modo de falla”, siendo así:
“Un modo de falla es cualquier evento que cause una falla funcional”
Reliability Centered Maintenance Second Edition 2 Revised edition by Moubray, John (1997)
El mejor modo de indicar la relación y la divergencia entre estados fallidos (falla funcional) y los eventos que podrían causarlos (modo de falla), es enumerar las fallas funcionales, para posteriormente señalar los modos de falla que pueden ocasionar cada falla funcional. Una sola máquina puede fallar por muchas razones. Un grupo de máquinas o sistemas, como una línea de producción, pueden fallar por cientos de razones. Respecto a una planta completa, esta puede fallar por miles o incluso decenas de miles de razones.
Muchos gerentes se estremecen al pensar en el tiempo y el esfuerzo que probablemente se involucren en la identificación de todos estos modos de falla, entonces deciden que este tipo de análisis representa exceso de trabajo y finalmente desisten totalmente de la idea. Al hacerlo, estos gerentes pasan por alto el hecho de que todo el tiempo el mantenimiento se basa en los modos de falla, esto es debido a que las órdenes de trabajo surgen para cubrir modos de falla específicos, la planificación del mantenimiento diario se ejecuta para tratar determinados modos de falla. Cabe destacar que también el personal de mantenimiento y operaciones de la mayoría de las empresas industriales tienen reuniones todos los días, las cuales consisten más que todo en discusiones sobre lo que ha fallado, qué lo causó y quién tiene la culpa, qué se está haciendo para arreglar la falla y, a veces, qué se puede hacer para evitar que vuelva a suceder, así pues una gran parte de la reunión se dedica a la discusión de los modos de falla.
Luego de haber identificado los modos de falla, se procede a sopesar lo que acontece, en qué momento se produce, tantear las consecuencias y determinar si se requieren acciones pertinentes para anticipar, prever, detectar, corregir e incluso rediseñar. Y así se llevan a cabo a nivel del modo de falla, el proceso de selección de tareas de mantenimiento y gran parte de la administración de dichas tareas.
Consecuencias de las fallas en RCM
Siempre que se manifiesta una falla, la organización que es usuaria del activo se ve afectada de una que otra manera. Ciertas fallas afectan la salida, la calidad del producto o el servicio al cliente; otras amenazan la seguridad o el medio ambiente; algunas pueden aumentar los costos operativos, por ejemplo, al aumentar el consumo de energía, mientras que algunos tienen un impacto en cuatro, cinco o incluso en las seis áreas; en algunos casos podría parecer que algunas fallas no tienen ningún efecto si ocurren por sí mismas, pero pueden exponer a la organización al riesgo de otras mucho más graves.
Si cualquiera de estos tipos de fallas no se evita, el tiempo y el esfuerzo que deben dedicarse a corregirlas también afectan a la organización, porque la reparación de daños ocasionados por las fallas consume recursos que podrían utilizarse mejor para otros aspectos.
Mantenimiento proactivo para prevenir en RCM
Es gratificante realizar tareas proactivas, tomando en cuenta los costos que conllevan, estas son factibles si físicamente pueden realizar acciones para disminuir las consecuencias del modo de falla asociado, a un nivel admisible para el propietario o usuario de los activos. Desde el punto de vista técnico se debe tener en cuenta la relación entre la edad del componente que se está considerando y la probabilidad de que falle, y que sucede una vez que ha comenzado a ocurrir la falla.
Mantenimiento proactivo para predecir en RCM
Existen muchas formas para determinar si las fallas están próximas a producirse. Las tareas denominadas para detectar fallas potencias se conocen como tareas a condición, las cuales consisten en chequear si hay fallas potenciales, para que se pueda actuar para prevenir la falla funcional o evitar las consecuencias de la falla funcional. Esto se conoce también como mantenimiento predictivo ya que basándose en el comportamiento del elemento, se está trata de predecir si va a fallar.
Aplicación del Proceso RCM
El RCM se fundamenta en el supuesto de que cada activo físico se obtiene para que cumpla una o varias funciones específicas, y el mantenimiento se lleva a cabo para hacer todo lo posible para garantizar que el activo siga cumpliendo las funciones esperadas por sus usuarios, siendo los más importantes la mayoría de las veces, los gerentes de operaciones y de producción, es necesario que estos participen activamente durante todo el proceso para garantizar un programa de mantenimiento óptimo de RCM. También son elementos clave en este asunto el personal de mantenimiento y de diseño, mayormente en los niveles de supervisión, pues son los custodios de la información, y si esta es compartida en un grupo determinado, el personal de mantenimiento recibe de manera más precisa lo que quieren obtener los operadores, además de que los usuarios logran comprender más claramente lo que el mantenimiento puede y no puede conceder.
Beneficios de la aplicación del RCM
La aplicación adecuada de la metodología de RCM genera:
- Mayor Seguridad e Integridad Ambiental
- Mayor Disponibilidad y Confiabilidad de Planta
- Mejor Calidad del Producto
- Mayor Eficiencia del Mantenimiento (Costo-efectividad)
- Vida Útil más Larga de Ítems Caros
- Mayor motivación de los individuos
- Mejor Trabajo en Equipo
- Una Base de Datos de Mantenimiento
- Un Marco de Referencia Integrador
Nota de la editorial: En todas las cuestiones relativas al sentido, los textos originales en inglés citados en esta entrada tienen validez última.
Más libros
Dinos qué te ha parecido el artículo
Artículos recomendados
El Manual del Ingeniero de Confiabilidad Certificado (Mark Allen Durivage)

Ingeniería de Confiabilidad: Teoría y Práctica

Ingeniería de Confiabilidad y Análisis de Riesgos: una Guía Práctica

Evaluación Comparativa de Mejores Prácticas - Terry Wireman

Publica tu artículo en la revista #1 de Mantenimiento Industrial
Publicar un artículo en la revista es gratis, no tiene costo.
Solo debes asegurarte que no sea un artículo comercial.
¿Qué esperas?
O envía tu artículo directo: articulos@predictiva21.com
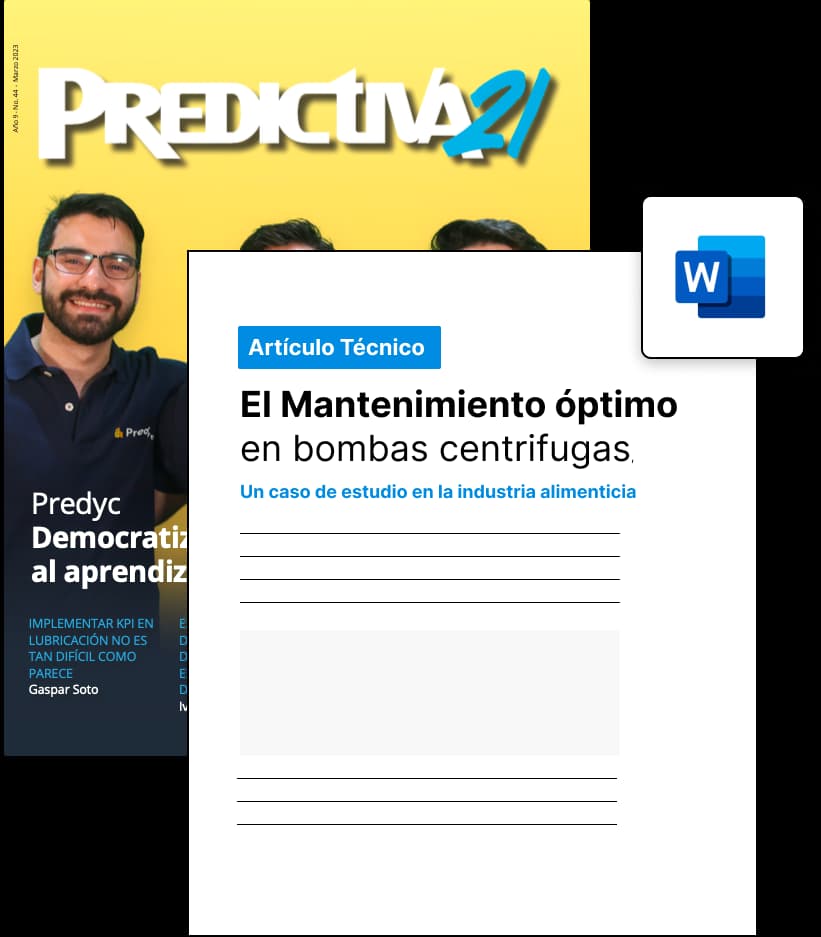
RCM II: Reliability Centered Maintenance - John Moubray
Libros>Reseña - Tienda 15 de marzo de 2020Introducción al tema

El Mantenimiento Centrado en la Confiabilidad, conocido por sus siglas en inglés como RCM (Reliability Centered Maintenance), comenzó a desarrollarse dentro de la industria de la aviación, convirtiéndose exponencialmente en un pilar fundamental en la práctica de la gestión de mantenimiento. Actualmente es aplicado en todo el mundo por muchas organizaciones industriales y prestadoras de servicios. En el clásico libro de John Moubray titulado "RCM 2: Reliability Centered Maintenance Second Edition 2 Revised edition by Moubray, John (1997) Hardcover" se expone información práctica, autorizada y sobre la aplicación correspondiente del RCM. Representa un aspecto fundamental para los ingenieros centrados en su productividad, calidad, seguridad e integridad ambiental. Moubray se caracteriza por ser experto en el área y ha prestado ayuda a profesionales de muchos países en la aplicación del RCM y de su sucesor, el RCM2.
[su_button url="https://amzn.to/2lpWeo5" target="blank" style="flat" size="6" center="yes" rel="nofollow"]Comprar en Amazon[/su_button]¿Qué es el RCM2?
El término de RCM2 se refiere a una versión mejorada del RCM, realizada por el autor John Moubray, la cual consiste en la aplicación de la metodología del Mantenimiento Centrado en la Confiabilidad en el ámbito industrial.
Documentación del RCM2 de John Moubray
Consiste en un libro de texto muy utilizado cuyo primer número se publicó en el Reino Unido en 1991 y en los Estados Unidos en 1992. Como resultado, se realizaron varias actualizaciones y versiones, producidas por la compañía británica “The Aladon Network” (conocida inicialmente como Aladon Ltd en 1986 y luego como Aladon LLC en 1998), fundada por Moubray y dirigida por el mismo como director ejecutivo hasta su fallecimiento en 2004. Actualmente la compañía se dedica a difundir e implementar la metodología de RCM alrededor del mundo.
El contenido de la segunda edición del libro de Moubray abarca temas tales como las funciones de los activos físicos, fallos funcionales, análisis de modos de fallo y sus efectos, consecuencias de los fallos, diagramas de decisión RCM, implementación de recomendaciones de RCM, datos de los fallos, aplicación del proceso RCM, beneficios el RCM, historia del RCM, un glosario de términos, y algunos detalles adicionales.
A continuación se presenta un resumen en español de los capítulos del libro.
Historia del RCM
En la década de 1960 se presentó una cantidad inaceptable de accidentes de aviación, lo cual motivó a un equipo de ejecutivos e ingenieros de alto nivel de United Airlines a desarrollar un proceso para determinar los requerimientos de mantenimiento óptimos de las aeronaves, lo cual dio origen a documentos públicos donde se utilizó por primera vez el termino de Mantenimiento centrado en la confiabilidad o RCM (Reliability Centered Maintenance). Los estudios demostraron que el supuesto fundamental de los ingenieros de diseño y de los planificadores de mantenimiento era que cada avión y cada componente principal del mismo tenían una "vida útil" específica de servicio confiable, después de ello tenía que ser reemplazado o revisado para así prevenir fallas.
Años más tarde, United Airlines fue patrocinada por el Departamento de Defensa de los Estados Unidos para la creación de un libro sobre el RCM, el cual fue publicado en el año 1978 en conjunto con un informe de evaluación de Rand Corporation, ambos textos dieron a conocer al RCM al público en general. Este fue uno de los muchos descubrimientos sorprendentes que han revolucionado la disciplina administrativa de la gestión de los activos físicos. Entre algunos de los cambios de paradigma inspirados en RCM fueron que el entendimiento de que la gran mayoría de las fallas no están necesariamente vinculadas a la edad del activo, la comprensión de la diferencia entre los requisitos de los activos desde la perspectiva del usuario y la confiabilidad del diseño del activo, la comprensión de la importancia de administrar los activos bajo condición y la vinculación de niveles de riesgo tolerable al desarrollo de la estrategia de mantenimiento.
A partir del año 1980 se extiende el uso de la metodología para la industria naval y en la armada, algunos años después se aplicó para la industria nuclear de Estados Unidos. Para el año 1993 se comenzó a aplicar en Francia. Moubray obtuvo el mayor éxito en su aproximación a la industria con el RCM mediante la creación de la metodología de RCM2, la cual incorporó cuestiones ambientales, precisión de tareas de mantenimiento y la definición de criterios de riesgo cuantitativos. Fue en el año 1999 donde se normalizó el proceso de RCM2 mediante la normativa SAE JA1011, con el documento “Criterios de Evaluación para Procesos de Mantenimiento Centrado en la Confiabilidad”, el cual establece los criterios mínimos para lo que es, y para lo que no se puede definir como RCM.
El estándar es algo decisivo en la evolución continua de la disciplina de la gestión de activos físicos. Antes del desarrollo del estándar, muchos procesos se etiquetaban como RCM, aunque no eran fieles a las intenciones y los principios del informe original que definían el término públicamente.
Hoy en día, las compañías pueden usar este estándar para garantizar que los procesos, servicios y software que compran e implementen se ajusten a lo que se define como RCM, lo que garantiza la mejor posibilidad de lograr los muchos beneficios atribuibles a la aplicación rigurosa de RCM.
Funciones de los activos físicos en RCM
Los usuarios de los activos tienen la expectativa de que el activo además de cumplir con una función, lo haga con un nivel de funcionamiento aceptable, por lo tanto la definición de una función en conjunto con la definición de los objetivos de mantenimiento para ese activo físico no estarían completas a menos que el usuario detalle de la manera más precisa posible el nivel de funcionamiento esperado. Por lo tanto:
“La definición de una función consiste de un verbo, un objeto y el estándar de funcionamiento deseado por el usuario.”
Reliability Centered Maintenance Second Edition 2 Revised edition by Moubray, John (1997)
La finalidad del mantenimiento es asegurar que los activos físicos se mantengan realizando la labor que sus usuarios desean, cuya magnitud debería definirse mediante un estándar mínimo de funcionamiento. Lo ideal sería que los activos puedan mantenerse en el rendimiento de su funcionamiento mínimo de manera indefinida, es decir, sin deteriorarse en ningún momento, por lo tanto las máquinas nunca tendrían la necesidad de mantenimiento, pero a causa de las leyes de la física esto no es posible, puesto que cualquier sistema organizado expuesto al mundo real se deteriorará, teniendo como consecuencia situaciones impredecibles que conllevan al caos o a la entropía. En este sentido el mantenimiento centrado en la confiabilidad se aplica para detener los procesas que causan el deterioro de los sistemas.
Fallas Funcionales en RCM
Un activo físico presenta fallas cuando este no cumple con la función esperada por el usuario. Todo lo que se requiere que haga el activo es definido como una función y cada una de ellos tiene más de una función y frecuentemente muchas diferentes. Ya que es posible que cada una de estas funciones presente una falla, se deduce que cualquier activo puede sufrir una variedad de estados de falla distintos. Esto demuestra por qué es más preciso definir fallas en términos de pérdida de funciones específicas, en lugar de la falla de un activo en su conjunto. El proceso de RCM utiliza el término "falla funcional" para describir estados de falla y no a una “falla” por sí sola, por lo tanto para completar la definición de falla, se debe analizar más de cerca la cuestión de los estándares de rendimiento. Entonces:
“Una falla funcional se define como la incapacidad de cualquier activo físico de cumplir una función según un parámetro de funcionamiento aceptable para el usuario.”
Reliability Centered Maintenance Second Edition 2 Revised edition by Moubray, John (1997)
Cursos recomendados






%252FImagen%252FRAMPREDYC-1730060420837.webp%3Falt%3Dmedia%26token%3D2634a7f0-988e-4022-b91f-382503e6e9db&w=3840&q=75)

Análisis de Modos de Falla y sus Efectos en RCM
Un modo de falla puede ser descrita como una situación que probablemente haga que un activo, sistema o proceso falle. Es necesario diferenciar una "falla funcional" y un "modo de falla" por consiguiente se pude definir de manera más precisa lo que es un “modo de falla”, siendo así:
“Un modo de falla es cualquier evento que cause una falla funcional”
Reliability Centered Maintenance Second Edition 2 Revised edition by Moubray, John (1997)
El mejor modo de indicar la relación y la divergencia entre estados fallidos (falla funcional) y los eventos que podrían causarlos (modo de falla), es enumerar las fallas funcionales, para posteriormente señalar los modos de falla que pueden ocasionar cada falla funcional. Una sola máquina puede fallar por muchas razones. Un grupo de máquinas o sistemas, como una línea de producción, pueden fallar por cientos de razones. Respecto a una planta completa, esta puede fallar por miles o incluso decenas de miles de razones.
Muchos gerentes se estremecen al pensar en el tiempo y el esfuerzo que probablemente se involucren en la identificación de todos estos modos de falla, entonces deciden que este tipo de análisis representa exceso de trabajo y finalmente desisten totalmente de la idea. Al hacerlo, estos gerentes pasan por alto el hecho de que todo el tiempo el mantenimiento se basa en los modos de falla, esto es debido a que las órdenes de trabajo surgen para cubrir modos de falla específicos, la planificación del mantenimiento diario se ejecuta para tratar determinados modos de falla. Cabe destacar que también el personal de mantenimiento y operaciones de la mayoría de las empresas industriales tienen reuniones todos los días, las cuales consisten más que todo en discusiones sobre lo que ha fallado, qué lo causó y quién tiene la culpa, qué se está haciendo para arreglar la falla y, a veces, qué se puede hacer para evitar que vuelva a suceder, así pues una gran parte de la reunión se dedica a la discusión de los modos de falla.
Luego de haber identificado los modos de falla, se procede a sopesar lo que acontece, en qué momento se produce, tantear las consecuencias y determinar si se requieren acciones pertinentes para anticipar, prever, detectar, corregir e incluso rediseñar. Y así se llevan a cabo a nivel del modo de falla, el proceso de selección de tareas de mantenimiento y gran parte de la administración de dichas tareas.
Consecuencias de las fallas en RCM
Siempre que se manifiesta una falla, la organización que es usuaria del activo se ve afectada de una que otra manera. Ciertas fallas afectan la salida, la calidad del producto o el servicio al cliente; otras amenazan la seguridad o el medio ambiente; algunas pueden aumentar los costos operativos, por ejemplo, al aumentar el consumo de energía, mientras que algunos tienen un impacto en cuatro, cinco o incluso en las seis áreas; en algunos casos podría parecer que algunas fallas no tienen ningún efecto si ocurren por sí mismas, pero pueden exponer a la organización al riesgo de otras mucho más graves.
Si cualquiera de estos tipos de fallas no se evita, el tiempo y el esfuerzo que deben dedicarse a corregirlas también afectan a la organización, porque la reparación de daños ocasionados por las fallas consume recursos que podrían utilizarse mejor para otros aspectos.
Mantenimiento proactivo para prevenir en RCM
Es gratificante realizar tareas proactivas, tomando en cuenta los costos que conllevan, estas son factibles si físicamente pueden realizar acciones para disminuir las consecuencias del modo de falla asociado, a un nivel admisible para el propietario o usuario de los activos. Desde el punto de vista técnico se debe tener en cuenta la relación entre la edad del componente que se está considerando y la probabilidad de que falle, y que sucede una vez que ha comenzado a ocurrir la falla.
Mantenimiento proactivo para predecir en RCM
Existen muchas formas para determinar si las fallas están próximas a producirse. Las tareas denominadas para detectar fallas potencias se conocen como tareas a condición, las cuales consisten en chequear si hay fallas potenciales, para que se pueda actuar para prevenir la falla funcional o evitar las consecuencias de la falla funcional. Esto se conoce también como mantenimiento predictivo ya que basándose en el comportamiento del elemento, se está trata de predecir si va a fallar.
Aplicación del Proceso RCM
El RCM se fundamenta en el supuesto de que cada activo físico se obtiene para que cumpla una o varias funciones específicas, y el mantenimiento se lleva a cabo para hacer todo lo posible para garantizar que el activo siga cumpliendo las funciones esperadas por sus usuarios, siendo los más importantes la mayoría de las veces, los gerentes de operaciones y de producción, es necesario que estos participen activamente durante todo el proceso para garantizar un programa de mantenimiento óptimo de RCM. También son elementos clave en este asunto el personal de mantenimiento y de diseño, mayormente en los niveles de supervisión, pues son los custodios de la información, y si esta es compartida en un grupo determinado, el personal de mantenimiento recibe de manera más precisa lo que quieren obtener los operadores, además de que los usuarios logran comprender más claramente lo que el mantenimiento puede y no puede conceder.
Beneficios de la aplicación del RCM
La aplicación adecuada de la metodología de RCM genera:
- Mayor Seguridad e Integridad Ambiental
- Mayor Disponibilidad y Confiabilidad de Planta
- Mejor Calidad del Producto
- Mayor Eficiencia del Mantenimiento (Costo-efectividad)
- Vida Útil más Larga de Ítems Caros
- Mayor motivación de los individuos
- Mejor Trabajo en Equipo
- Una Base de Datos de Mantenimiento
- Un Marco de Referencia Integrador
Nota de la editorial: En todas las cuestiones relativas al sentido, los textos originales en inglés citados en esta entrada tienen validez última.
Más libros
Dinos qué te ha parecido el artículo
Artículos recomendados
El Manual del Ingeniero de Confiabilidad Certificado (Mark Allen Durivage)

Ingeniería de Confiabilidad Práctica

Confiabilidad, Mantenibilidad y Riesgo: Métodos prácticos para ingenieros

Modelos para la Excelencia Operativa

Publica tu artículo en la revista #1 de Mantenimiento Industrial
Publicar un artículo en la revista es gratis, no tiene costo.
Solo debes asegurarte que no sea un artículo comercial.
¿Qué esperas?
O envía tu artículo directo: articulos@predictiva21.com
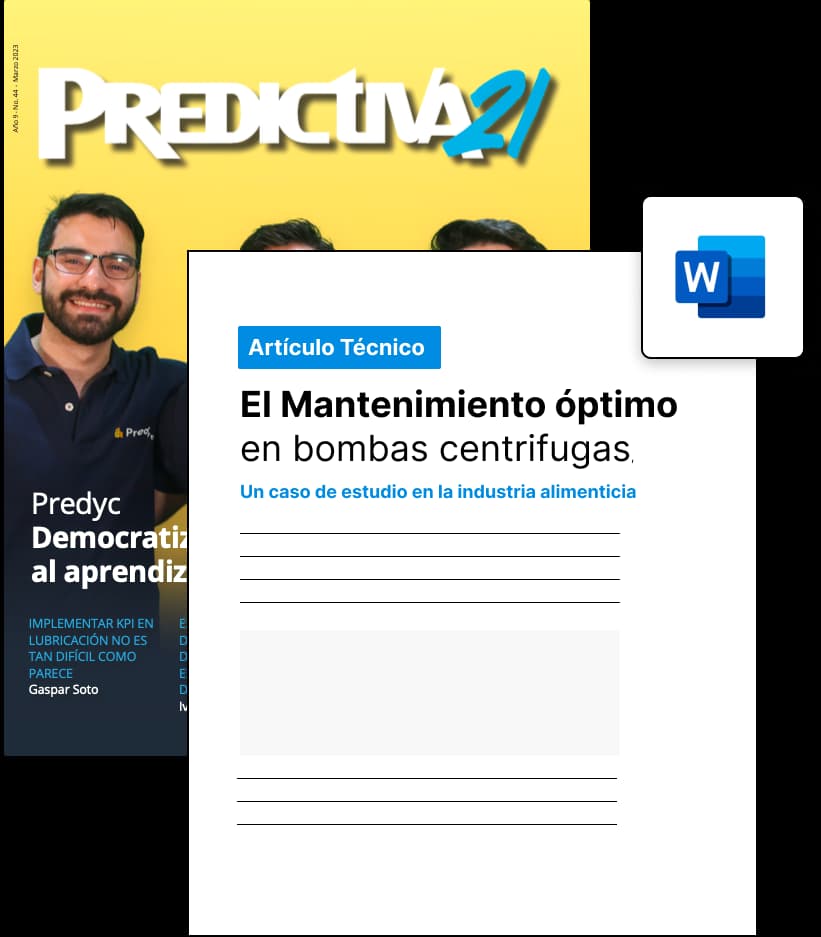