Oil Condition Monitoring: Analítica de Datos Aplicada al PQindex
Articulo25 de junio de 2021
El PQindex es uno de esos ensayos de laboratorio que están en el limbo, entre lo físico explicable, medible-cuantificable y lo etéreo. Aporta un valor, ¡pero con cuidado! es un valor adimensional y debe ser tratado como tal. La pregunta es ¿cómo deberíamos tratar a un valor que no tiene unidades? Mientras escribía este artículo y realizaba unos análisis con un lote de muestras de cerca de 10 mil muestras, consulté con un profesor de estadística aplicada, como se debe trabajar con un valor de estas características. Su respuesta respaldó las suposiciones iniciales sobre las que había basado el estudio. El verdadero aporte del PQ al análisis de aceite como herramienta de mantenimiento predictivo tiene un matiz interesante y esto dio lugar a que este test haya cobrado nuevamente una importancia relevante.
Veamos el caso de fallo de una reductora con un aceite EP220 y un volumen cercano a los 250 litros. Por una razón técnico económica se decidió no realizar el análisis de PQ en el laboratorio, hablamos de alrededor de $3 adicionales por muestra - una ruina para cualquier empresa. Una concentración elevada de hierro alertó al usuario final de un potencial desgaste anormal y sus posibles consecuencias en un plazo de tiempo medio, algo entre 6 a 9 meses según experiencias previas. El informe establecía claramente que debido al tipo de desgaste los análisis posteriores podrían presentar una caída drástica en la concentración de hierro y ¡así fue!
Esta caída se debía simplemente a que la rugosidad de las superficies en contacto había sido pulida debido al contacto metal con metal. El problema en este tipo de componentes radica en que muchas veces ese contacto no se detiene ahí, sino que continúa y los desgastes se siguen generando, pero van a más en cuanto a tamaño de la partícula.

Una explicación gráfica relativamente sencilla de cómo se producen las partículas de desgaste (por contacto) en sistemas lubricados ya sea por grasa o por aceite es la que tenemos a continuación. Es indiscutible que en muchos casos nos perdemos parte del escenario del desgaste cuando, por la razón que sea, no se determina si existen partículas ferromagnéticas superiores a las 7-10µ.
Volvamos a la reductora en cuestión. En casos de desgaste anormal como este, el fallo funcional puede ser detectado con anterioridad si se ponen las piezas en el orden adecuado, es decir la concentración de hierro y partículas ferromagnéticas en función tiempo-producción.
Veamos primero el gráfico en función de tiempo sin tomar en cuenta el valor maximizado de PQ (PQm), que es como llamaremos de aquí en adelante al dato tratado como un par de ecuaciones basadas en estadística aplicada y en datos operacionales. A menos que se haya realizado algún tipo de rectificado mecánico o reemplazo de la(s) pieza(s) que sufre(n) desgaste, un deterioro tan marcado no puede simplemente desaparecer, de 78ppm a 14ppm.

Descrito algunas líneas atrás, el gráfico anterior evidencia que la desaparición del hierro de la concentración de hierro se debe al proceso de pulido. Es aquí, en el punto de inflexión donde la pendiente desaparece por completo y muchos usuarios del análisis de aceite dan por hecho que con ella también desaparece el desgaste, aquel que meses antes había llamado su atención debido no únicamente al incremento en la concentración de hierro sino a la tasa normalizada de desgaste.
La pregunta que surge aquí es ¿cómo se llega al fallo funcional o en algunos casos a uno catastrófico si se está haciendo un seguimiento al desgaste con una frecuencia establecida?
Volvamos a ver el mismo gráfico pero esta vez añadiendo el PQm. Una de las maneras más comunes de utilizarlo es ponerlo en comparación en una serie temporal (no de unidades) con la concentración de Hierro (Fe) determinada por un equipo de espectroscopia de emisión atómica como puede ser el ICP.

Con solo ver el gráfico completo, hace falta poca explicación de porqué se produce un fallo funcional del componente. Es evidente que el desgaste no se detuvo en ningún momento sino que evolucionó hacia uno mucho más drástico en el que la generación de partículas de desgaste se vio incrementada en cuanto al tamaño de las partículas. En el punto del Fallo Funcional el tamaño de partículas ferromagnéticas superó las 200µ.
Los valores de seguimiento de ambos parámetros se detallan en la tabla siguiente:

Recuerde que la mayoría de los ensayos de laboratorio están, de una u otra manera, ligados entre si y que unos suelen medir el efecto de los cambios en los otros.
No menosprecie nunca el valor que puede tener un ensayo por muy sencillo que parezca y sobre todo valore los avances de la analítica de datos y el conocimiento aplicado que le brinda su laboratorio, al mismo tiempo evalúe la potencial aplicación de estos avances en sus máquinas.
Autor: Jorge Alarcón
Global Technical Manager, OCM
Correo: jorge.alarcon@bureauveritas.com
LinkedIn: https://www.linkedin.com/in/jorge-alarcon-70303412/
Dinos qué te ha parecido el artículo
Artículos recomendados
19.1.- Como se Miden las Vibraciones y Como son Interpretadas

Planificación de Mantenimiento en PM-SAP

Monitoreo de condición a equipos dinámicos

Costos operacionales: ¿Conoce usted el costo de conducción por kilometro de su vehículo?

Publica tu artículo en la revista #1 de Mantenimiento Industrial
Publicar un artículo en la revista es gratis, no tiene costo.
Solo debes asegurarte que no sea un artículo comercial.
¿Qué esperas?
O envía tu artículo directo: articulos@predictiva21.com
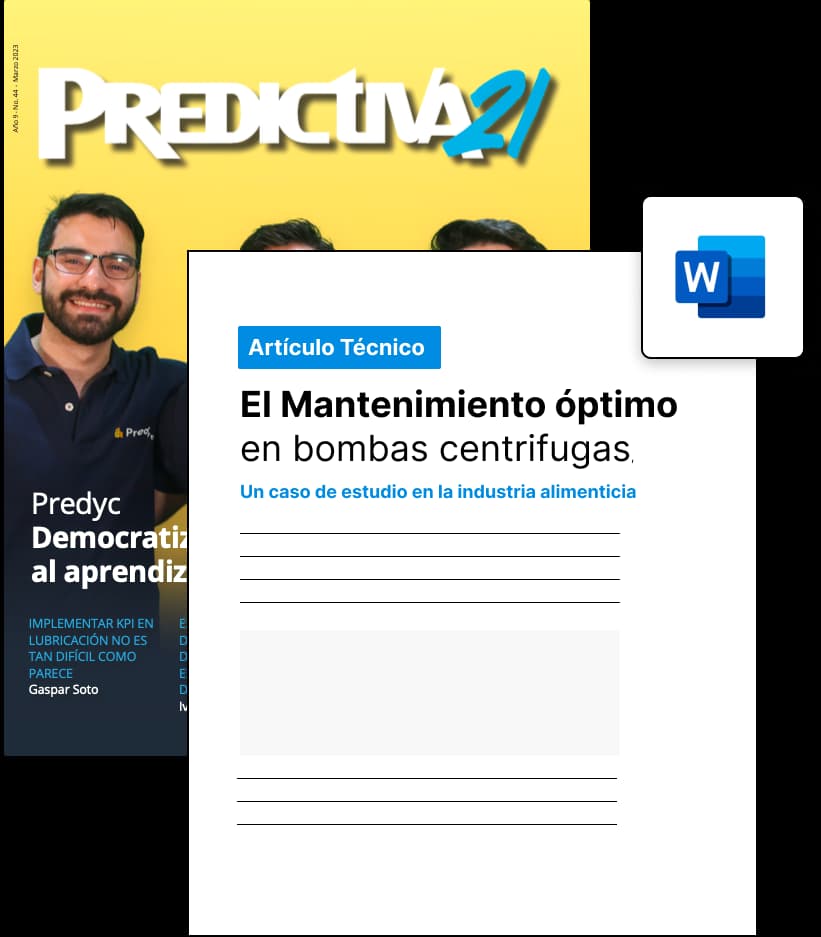
Oil Condition Monitoring: Analítica de Datos Aplicada al PQindex
Articulo 25 de junio de 2021El PQindex es uno de esos ensayos de laboratorio que están en el limbo, entre lo físico explicable, medible-cuantificable y lo etéreo. Aporta un valor, ¡pero con cuidado! es un valor adimensional y debe ser tratado como tal. La pregunta es ¿cómo deberíamos tratar a un valor que no tiene unidades? Mientras escribía este artículo y realizaba unos análisis con un lote de muestras de cerca de 10 mil muestras, consulté con un profesor de estadística aplicada, como se debe trabajar con un valor de estas características. Su respuesta respaldó las suposiciones iniciales sobre las que había basado el estudio. El verdadero aporte del PQ al análisis de aceite como herramienta de mantenimiento predictivo tiene un matiz interesante y esto dio lugar a que este test haya cobrado nuevamente una importancia relevante.
Veamos el caso de fallo de una reductora con un aceite EP220 y un volumen cercano a los 250 litros. Por una razón técnico económica se decidió no realizar el análisis de PQ en el laboratorio, hablamos de alrededor de $3 adicionales por muestra - una ruina para cualquier empresa. Una concentración elevada de hierro alertó al usuario final de un potencial desgaste anormal y sus posibles consecuencias en un plazo de tiempo medio, algo entre 6 a 9 meses según experiencias previas. El informe establecía claramente que debido al tipo de desgaste los análisis posteriores podrían presentar una caída drástica en la concentración de hierro y ¡así fue!
Esta caída se debía simplemente a que la rugosidad de las superficies en contacto había sido pulida debido al contacto metal con metal. El problema en este tipo de componentes radica en que muchas veces ese contacto no se detiene ahí, sino que continúa y los desgastes se siguen generando, pero van a más en cuanto a tamaño de la partícula.

Una explicación gráfica relativamente sencilla de cómo se producen las partículas de desgaste (por contacto) en sistemas lubricados ya sea por grasa o por aceite es la que tenemos a continuación. Es indiscutible que en muchos casos nos perdemos parte del escenario del desgaste cuando, por la razón que sea, no se determina si existen partículas ferromagnéticas superiores a las 7-10µ.
Volvamos a la reductora en cuestión. En casos de desgaste anormal como este, el fallo funcional puede ser detectado con anterioridad si se ponen las piezas en el orden adecuado, es decir la concentración de hierro y partículas ferromagnéticas en función tiempo-producción.
Veamos primero el gráfico en función de tiempo sin tomar en cuenta el valor maximizado de PQ (PQm), que es como llamaremos de aquí en adelante al dato tratado como un par de ecuaciones basadas en estadística aplicada y en datos operacionales. A menos que se haya realizado algún tipo de rectificado mecánico o reemplazo de la(s) pieza(s) que sufre(n) desgaste, un deterioro tan marcado no puede simplemente desaparecer, de 78ppm a 14ppm.

Descrito algunas líneas atrás, el gráfico anterior evidencia que la desaparición del hierro de la concentración de hierro se debe al proceso de pulido. Es aquí, en el punto de inflexión donde la pendiente desaparece por completo y muchos usuarios del análisis de aceite dan por hecho que con ella también desaparece el desgaste, aquel que meses antes había llamado su atención debido no únicamente al incremento en la concentración de hierro sino a la tasa normalizada de desgaste.
La pregunta que surge aquí es ¿cómo se llega al fallo funcional o en algunos casos a uno catastrófico si se está haciendo un seguimiento al desgaste con una frecuencia establecida?
Volvamos a ver el mismo gráfico pero esta vez añadiendo el PQm. Una de las maneras más comunes de utilizarlo es ponerlo en comparación en una serie temporal (no de unidades) con la concentración de Hierro (Fe) determinada por un equipo de espectroscopia de emisión atómica como puede ser el ICP.

Con solo ver el gráfico completo, hace falta poca explicación de porqué se produce un fallo funcional del componente. Es evidente que el desgaste no se detuvo en ningún momento sino que evolucionó hacia uno mucho más drástico en el que la generación de partículas de desgaste se vio incrementada en cuanto al tamaño de las partículas. En el punto del Fallo Funcional el tamaño de partículas ferromagnéticas superó las 200µ.
Los valores de seguimiento de ambos parámetros se detallan en la tabla siguiente:

Recuerde que la mayoría de los ensayos de laboratorio están, de una u otra manera, ligados entre si y que unos suelen medir el efecto de los cambios en los otros.
No menosprecie nunca el valor que puede tener un ensayo por muy sencillo que parezca y sobre todo valore los avances de la analítica de datos y el conocimiento aplicado que le brinda su laboratorio, al mismo tiempo evalúe la potencial aplicación de estos avances en sus máquinas.
Autor: Jorge Alarcón
Global Technical Manager, OCM
Correo: jorge.alarcon@bureauveritas.com
LinkedIn: https://www.linkedin.com/in/jorge-alarcon-70303412/
Dinos qué te ha parecido el artículo
Artículos recomendados
Confiabilidad de Bombas Centrífugas

Costos operacionales: ¿Conoce usted el costo de conducción por kilometro de su vehículo?

Monitoreo de condición a equipos estáticos

Do Invento da Roda a Fórmula 1

Publica tu artículo en la revista #1 de Mantenimiento Industrial
Publicar un artículo en la revista es gratis, no tiene costo.
Solo debes asegurarte que no sea un artículo comercial.
¿Qué esperas?
O envía tu artículo directo: articulos@predictiva21.com
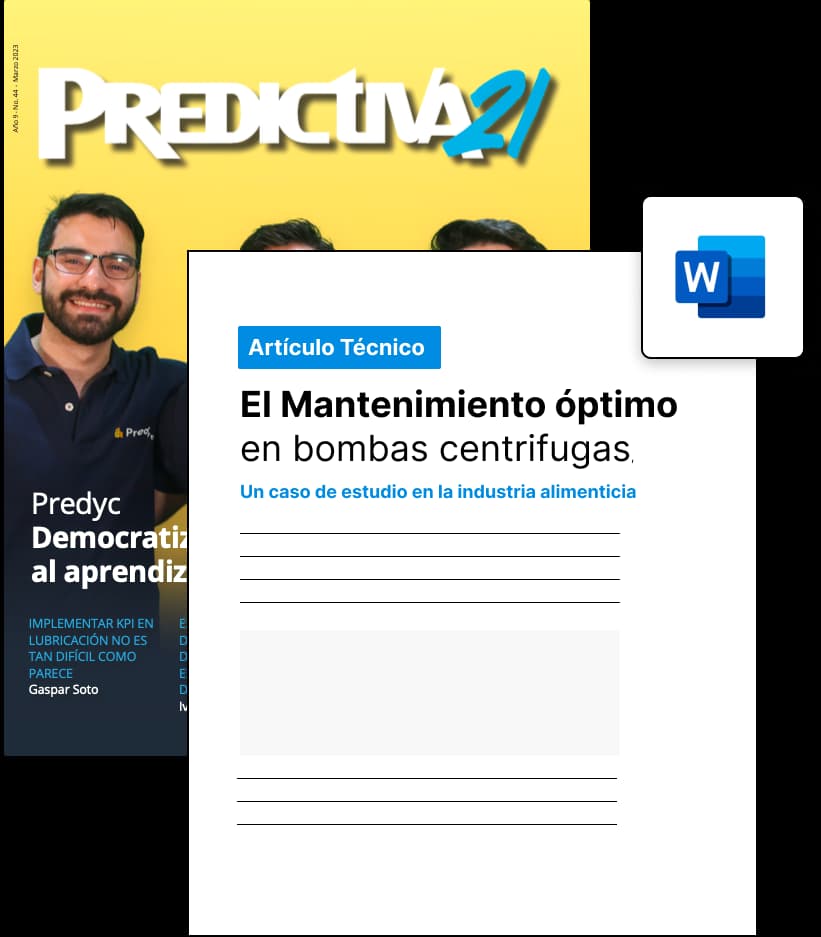