Políticas y Procedimientos
Articulo17 de abril de 2019
Plant Hexcellence™ - Políticas y Procedimientos
Este es el cuarto de una serie de artículos. La misma documenta la trayectoria continua en búsqueda de una guía para la Excelencia en la Manufactura. El marco que estamos usando para referencia en esta trayectoria es el modelo denominado Plant Hexcellence™. Como lo hemos discutido en la anterior entrega, la Celda de Procesos (Processes Cell) es utilizada para visualizar el flujo en un procedimiento o metodologia. También discutimos la interconexión entre la Celda de Procesos y la Celda de Políticas y Procedimientos (Policy and Procedures cell).
Al enfocarnos en la celda P&P, vamos a discutir en primer lugar lo que es una política, luego hablaremos sobre procedimientos y procesos y su conectividad en apoyo a la política.
Ciertos procesos son lo suficientemente importantes para requerir la adherencia estricta al proceso.
Tradicionalmente, las políticas se crean y establecen para ajustarse a las regulaciones, pero pueden ser expandidas fácilmente para acompañar cualquier proceso considerado crítico o que tenga muchas variables que necesitan ser controladas.

Definición
Una Política es un juego de reglas, principios y orientaciones escritas y publicada para crear gobernabilidad. Las políticas son diseñadas para crear una conducta o acción estandarizada documentada en circunstancias específicas. Las políticas son apoyadas por los procedimientos.
Los Procedimientos son los métodos específicos empleados para expresar políticas convertidas en acción operacional día a día en una organización. Juntas, las políticas y procedimientos aseguran que un punto de vista/orientación proveniente de un cuerpo gobernante se traduzca en pasos documentados que se identifiquen con un resultado compatible con ese punto de vista.
Vamos a discutir un ejemplo real muy relevante y que he visto como ausente dentro de las organizaciones. El mismo reforzará la conectividad de la cadena Política-Procedimiento-Proceso.
Análisis de Falla Causa Raíz (RCA/RCFA)
He visto cómo en la mayoría de las compañías y organizaciones existe una forma de RCFA en ejecución. Usualmente se encuentra alrededor de investigaciones de incidentes de seguridad/medio ambiente, pero puede ser bastante visible también fuera de esas disciplinas. Además, con mucha frecuencia, las entidades de Seguridad y Ambiente actúan independientemente con casi ningún método o herramienta compartida para llevar a cabo la investigación. Un RCFA puede ser un método muy efectivo como herramienta para identificar y eliminar una falla mientras se entiende los factores reales causantes alrededor del incidente. El punto es que esto es hecho de manera muy aleatoria y ad hoc en cuanto a tiempo y metodología. Esto es especialmente cierto en organizaciones con múltiples sitios y que se han desarrollado más por adquisición en vez de por crecimiento orgánico.
En recientes artículos, hemos discutido el equilibrio necesario dentro de una compañía para que sea saludable. Debe haber un balance entre Seguridad, Ambiente y Ganancias. Una simple política de RCA/RCFA debe escribirse para acompañar todos estos elementos.
- Dicha política incluye declarar que debe ejecutarse un RCA/RCFA en circunstancias especificas. (nota: "Debe" es una palabra que implica obligacion legal, no una ejecucion opcional)
- Deben definirse los de enfoque
- Un incidente de Seguridad o su probabilidad de ocurrencia.
- Un incidente de Ambiente o su probabilidad de ocurrencia.
- Un incidente de Pérdida de Ganancia.
- a) Pérdidas económicas por una cantidad mayor de X dólares como resultado de una falla (asegúrese de incluir multas potenciales o pérdida de contrato como parte del valor potencial total).
- b) Pérdida de tiempo de producción mayor a X como resultado de la falla (el uso de dicha medida se produce cuando el costo de falta de tiempo se desconoce o está en proceso de acumulación de WIP (Work in Progress o Trabajo en Proceso) y por lo tanto, hay una pérdida mínima o ninguna pérdida en la ganancia final.
- c) El costo de la reparación es mayor a X dólares como resultado de la falla (esto debe incluir toda la mano de obra y refacción).
- Debe haber dos niveles por cada punto de manera que pueda usarse un método menos riguroso de RCFA sin afectar grandemente las operaciones, p.ej. 5-Why.
- Una vez que el punto ha sido activado, un equipo funcional mixto debe reunirse dentro de un marco especifico del indicdente (preferiblemente 24 horas o menos).
- El equipo de RCFA tendrá una lista de funciones estándar a ser consideradas.
- Nombres individuales en una lista que determinara quien esta calificado para realizar dicha función en esa circunstancia especifica.
- El método de RCFA está incluido en la política.
- Todo el personal enlistado deberá haber tenido entrenamiento en la metodología.
- Se designará un marco de tiempo para los resultados iniciales.
- Se designará un marco de tiempo para los resultados finales.
- Debe establecerse un procedimiento y proceso sobre la manera cómo documentar e implementar cambios como resultado de los hallazgos.
Debe realizarse un mapa de proceso de flujo de trabajo documentado para crear una representación visual del método de: 1. Cuando ejecutar un RCFA? 2. Método y flujo para ejecutar el RCFA) 3. Métodos para implementar acciones como resultado del RCFA.
Ahora, la organización tiene una política y método estándar para entender:
- ¿Qué es un RCFA?
- ¿Por qué debe ejecutarse?
- ¿Cuándo debe ejecutarse?
- ¿Quién debe ejecutarlo?
- ¿Cómo debe ejecutarse?
- Expectativas resultantes de la ejecución.
Al observar el ejemplo anterior, es evidente la interconectividad entre la cadena Política-Procedimiento-Procesos y cómo esa conectividad puede ayudar a una organización a alcanzar sus metas.
Manténgase en contacto por el siguiente artículo de la serie en el cual discutiremos la Ejecución (medición) de una organización.
Autor: Scott Kelley, CMRP
Managing Director
C.I.: 713.962.1978
Correo: scottkelley@geometricreliability.com
Dinos qué te ha parecido el artículo
Artículos recomendados
Entrevista con Chris Struve

Curso de planificación en mantenimiento

Gestión de Mantenimiento: 7 KPIs imprescindibles

Vacas sagradas y abejas asesinas: el desafío de comportamientos destructivos en la empresa

Publica tu artículo en la revista #1 de Mantenimiento Industrial
Publicar un artículo en la revista es gratis, no tiene costo.
Solo debes asegurarte que no sea un artículo comercial.
¿Qué esperas?
O envía tu artículo directo: articulos@predictiva21.com
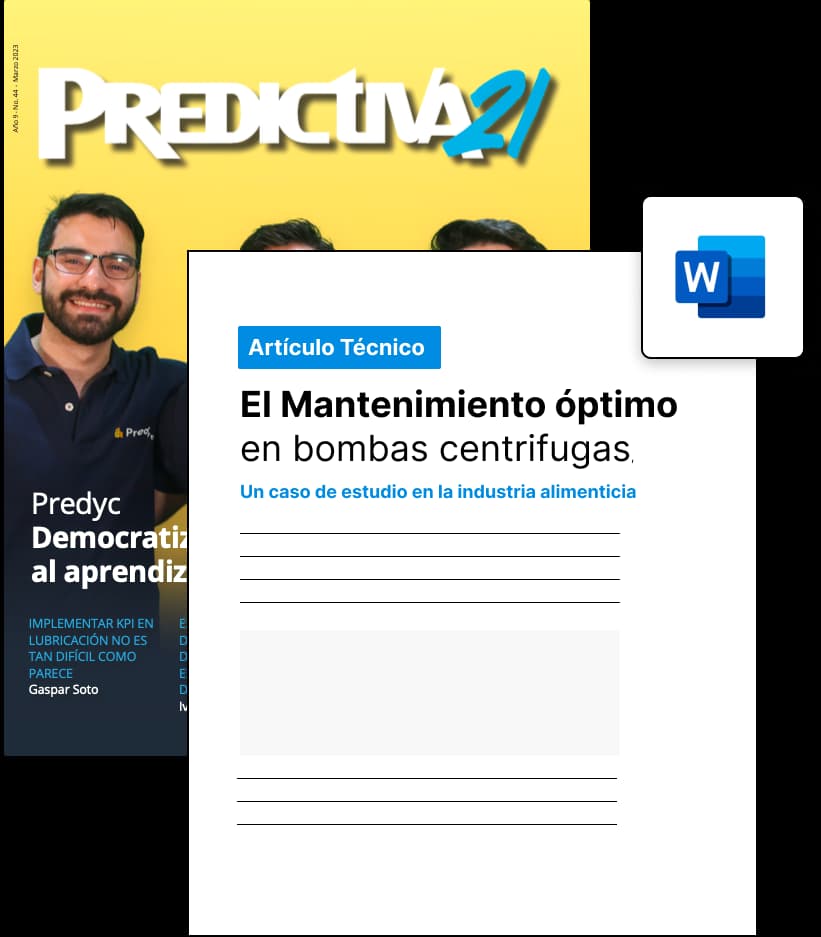
Políticas y Procedimientos
Articulo 17 de abril de 2019Plant Hexcellence™ - Políticas y Procedimientos
Este es el cuarto de una serie de artículos. La misma documenta la trayectoria continua en búsqueda de una guía para la Excelencia en la Manufactura. El marco que estamos usando para referencia en esta trayectoria es el modelo denominado Plant Hexcellence™. Como lo hemos discutido en la anterior entrega, la Celda de Procesos (Processes Cell) es utilizada para visualizar el flujo en un procedimiento o metodologia. También discutimos la interconexión entre la Celda de Procesos y la Celda de Políticas y Procedimientos (Policy and Procedures cell).
Al enfocarnos en la celda P&P, vamos a discutir en primer lugar lo que es una política, luego hablaremos sobre procedimientos y procesos y su conectividad en apoyo a la política.
Ciertos procesos son lo suficientemente importantes para requerir la adherencia estricta al proceso.
Tradicionalmente, las políticas se crean y establecen para ajustarse a las regulaciones, pero pueden ser expandidas fácilmente para acompañar cualquier proceso considerado crítico o que tenga muchas variables que necesitan ser controladas.

Definición
Una Política es un juego de reglas, principios y orientaciones escritas y publicada para crear gobernabilidad. Las políticas son diseñadas para crear una conducta o acción estandarizada documentada en circunstancias específicas. Las políticas son apoyadas por los procedimientos.
Los Procedimientos son los métodos específicos empleados para expresar políticas convertidas en acción operacional día a día en una organización. Juntas, las políticas y procedimientos aseguran que un punto de vista/orientación proveniente de un cuerpo gobernante se traduzca en pasos documentados que se identifiquen con un resultado compatible con ese punto de vista.
Vamos a discutir un ejemplo real muy relevante y que he visto como ausente dentro de las organizaciones. El mismo reforzará la conectividad de la cadena Política-Procedimiento-Proceso.
Análisis de Falla Causa Raíz (RCA/RCFA)
He visto cómo en la mayoría de las compañías y organizaciones existe una forma de RCFA en ejecución. Usualmente se encuentra alrededor de investigaciones de incidentes de seguridad/medio ambiente, pero puede ser bastante visible también fuera de esas disciplinas. Además, con mucha frecuencia, las entidades de Seguridad y Ambiente actúan independientemente con casi ningún método o herramienta compartida para llevar a cabo la investigación. Un RCFA puede ser un método muy efectivo como herramienta para identificar y eliminar una falla mientras se entiende los factores reales causantes alrededor del incidente. El punto es que esto es hecho de manera muy aleatoria y ad hoc en cuanto a tiempo y metodología. Esto es especialmente cierto en organizaciones con múltiples sitios y que se han desarrollado más por adquisición en vez de por crecimiento orgánico.
En recientes artículos, hemos discutido el equilibrio necesario dentro de una compañía para que sea saludable. Debe haber un balance entre Seguridad, Ambiente y Ganancias. Una simple política de RCA/RCFA debe escribirse para acompañar todos estos elementos.
- Dicha política incluye declarar que debe ejecutarse un RCA/RCFA en circunstancias especificas. (nota: "Debe" es una palabra que implica obligacion legal, no una ejecucion opcional)
- Deben definirse los de enfoque
- Un incidente de Seguridad o su probabilidad de ocurrencia.
- Un incidente de Ambiente o su probabilidad de ocurrencia.
- Un incidente de Pérdida de Ganancia.
- a) Pérdidas económicas por una cantidad mayor de X dólares como resultado de una falla (asegúrese de incluir multas potenciales o pérdida de contrato como parte del valor potencial total).
- b) Pérdida de tiempo de producción mayor a X como resultado de la falla (el uso de dicha medida se produce cuando el costo de falta de tiempo se desconoce o está en proceso de acumulación de WIP (Work in Progress o Trabajo en Proceso) y por lo tanto, hay una pérdida mínima o ninguna pérdida en la ganancia final.
- c) El costo de la reparación es mayor a X dólares como resultado de la falla (esto debe incluir toda la mano de obra y refacción).
- Debe haber dos niveles por cada punto de manera que pueda usarse un método menos riguroso de RCFA sin afectar grandemente las operaciones, p.ej. 5-Why.
- Una vez que el punto ha sido activado, un equipo funcional mixto debe reunirse dentro de un marco especifico del indicdente (preferiblemente 24 horas o menos).
- El equipo de RCFA tendrá una lista de funciones estándar a ser consideradas.
- Nombres individuales en una lista que determinara quien esta calificado para realizar dicha función en esa circunstancia especifica.
- El método de RCFA está incluido en la política.
- Todo el personal enlistado deberá haber tenido entrenamiento en la metodología.
- Se designará un marco de tiempo para los resultados iniciales.
- Se designará un marco de tiempo para los resultados finales.
- Debe establecerse un procedimiento y proceso sobre la manera cómo documentar e implementar cambios como resultado de los hallazgos.
Debe realizarse un mapa de proceso de flujo de trabajo documentado para crear una representación visual del método de: 1. Cuando ejecutar un RCFA? 2. Método y flujo para ejecutar el RCFA) 3. Métodos para implementar acciones como resultado del RCFA.
Ahora, la organización tiene una política y método estándar para entender:
- ¿Qué es un RCFA?
- ¿Por qué debe ejecutarse?
- ¿Cuándo debe ejecutarse?
- ¿Quién debe ejecutarlo?
- ¿Cómo debe ejecutarse?
- Expectativas resultantes de la ejecución.
Al observar el ejemplo anterior, es evidente la interconectividad entre la cadena Política-Procedimiento-Procesos y cómo esa conectividad puede ayudar a una organización a alcanzar sus metas.
Manténgase en contacto por el siguiente artículo de la serie en el cual discutiremos la Ejecución (medición) de una organización.
Autor: Scott Kelley, CMRP
Managing Director
C.I.: 713.962.1978
Correo: scottkelley@geometricreliability.com
Dinos qué te ha parecido el artículo
Artículos recomendados
¿Qué es la confiabilidad consciente?

Modelo de Confiabilidad con Metodología RAM para un sistema de bombeo de agua de inyección

La Serie de Normas ISO 55000, Herramienta para la Gestión de Activos

Predictiva21 llega a su edición número 40, por lo que hemos preparado una entrevista con dos versiones complementarias de la trayectoria de la revista, el origen y el futuro.

Publica tu artículo en la revista #1 de Mantenimiento Industrial
Publicar un artículo en la revista es gratis, no tiene costo.
Solo debes asegurarte que no sea un artículo comercial.
¿Qué esperas?
O envía tu artículo directo: articulos@predictiva21.com
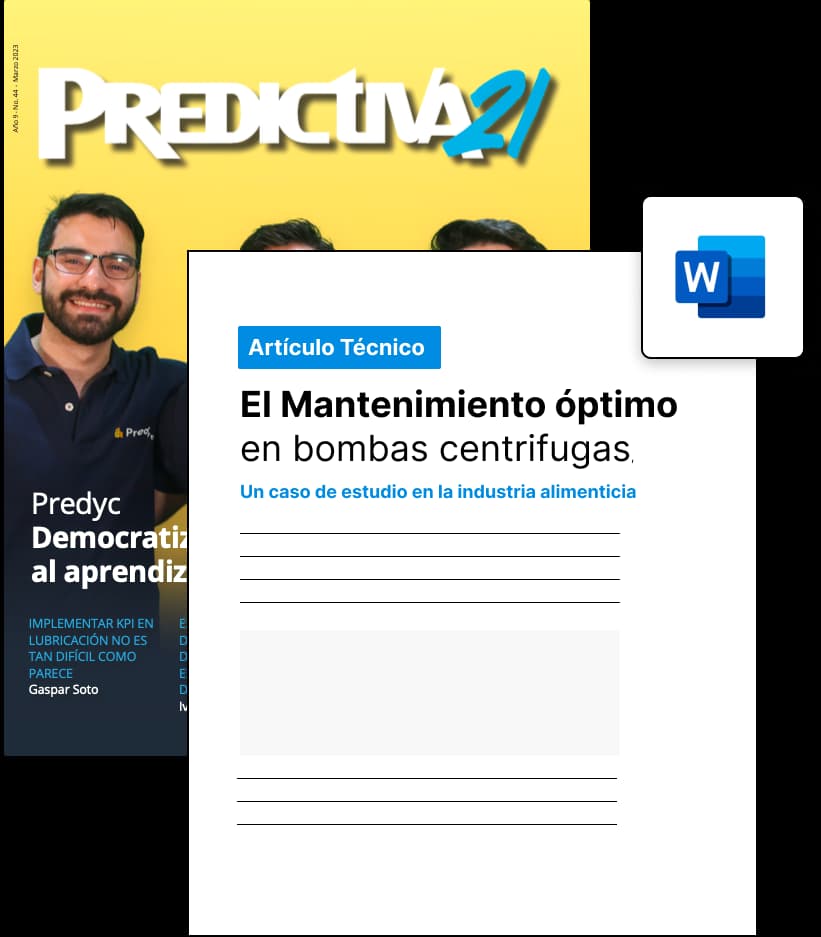