1.2. Costos y productividad
Libros30 de agosto de 2020
En el aspecto de costos, el mantenimiento correctivo a lo largo del tiempo, se presenta con la configuración de una curva ascendente, debido a la reducción de la vida útil de los equipos y la consecuente depreciación del activo, pérdida de producción o calidad de los servicios, aumento de adquisición de repuestos, aumento del "stock" de materia prima improductiva, pago de horas extras del personal de ejecución del mantenimiento, ociosidad de mano de obra operativa, pérdida de mercado y aumento de riesgos de accidentes - Figura 8.

La implantación de la planificación y control, buscando la prevención o predicción de la falla, presenta una configuración de costos invertida, con tasa negativa anual del orden de 20% y tendencia a valores estables, que pueden representar en el computo total, un ahorro de 300 a 500%(9 y 10), siendo más de la mitad de este ahorro debido a la facturación cesante, considerando el Costo Total de una parada de equipo, como la suma del Costo del Mantenimiento, que incluye los costos de mano de obra, repuestos, materiales, combustibles y lubricantes, y el Costo de Indisponibilidad que incluye el costo de Pérdida de Producción (horas no trabajadas), debido a: mala calidad del trabajo; falta de equipos; costo por emergencias; costos extras para reorganizar la producción; costo por repuestos de emergencia; penalidades comerciales e imagen de la empresa. Experiencias de evaluación del Costo de Indisponibilidad muestran que este representa más de la mitad del Costo Total de la parada.(11)
Un ejemplo evidente de los resultados obtenidos con la ejecución de la adecuada Planeación y Control de la función Mantenimiento fue divulgado por una empresa metalúrgica de los Estados Unidos de Norteamérica(12), que presentó los siguientes resultados:
- 1) Conservar el mantenimiento no planificado por debajo del 10%, de los cuales 8,3% es mantenimiento correctivo (la meta de la empresa era de 85% de mantenimiento planificado);
- 2) 0,5% de las horas de trabajo de mantenimiento fueron empleadas en arreglo de daños accidentales, 4,2% en fallas, 2,5% en lubricación, 25,6% en inspecciones, 4,1% en llamadas de emergencia, 6,1% en desmontajes, 40,2% en servicio de rutina programada, 0,2% en servicio de rutina no programada, 7,8% en fabricación y modificaciones y 8,8% en otras actividades como reuniones y capacitación;
- 3) Los costos de mantenimiento eran cerca de 40% por debajo de otras fábricas del mismo tamaño en el sector y se debe básicamente al uso eficiente de mano de obra y el mínimo de horas extras, que da, en promedio, menos de 0,5% por operario/año;
- 4) Los problemas de los equipos son detectados de manera precoz;
- 5) La inversión en mantenimiento incluye personas altamente calificadas, soporte sofisticado de computadora para mantenimiento planificado y una política de mantenimiento de la fábrica y equipos en "estado de nuevo";
- 6) El departamento de mantenimiento tiene total responsabilidad por el mantenimiento de los equipos e instalaciones de la fábrica. Cerca de 2.000 ítems por un valor superior a US$ 200 millones forman la mayor parte de esa responsabilidad.
La inversión inicial en mantenimiento planeado es mayor que el de mantenimiento no planeado y no elimina totalmente las fallas aleatorias, cuyo alto valor inicial es justificado por la inexperiencia del personal de mantenimiento que, al actuar en el equipo, altera su equilibrio operativo. Con el pasar del tiempo y al ganar experiencia, el mantenimiento aleatorio tiende a valores reducidos y estables. La suma general de los gastos del mantenimiento planeado y aleatorio, identificado como mantenimiento preventivo, a partir de un determinado tiempo, pasa a ser inferior al de mantenimiento por rotura(3).
Consecuentemente los beneficios de la prevención solamente ocurrirán a partir del momento en que las áreas comprendidas entre las curvas de mantenimiento por rotura y con prevención, antes y después de ese punto sean iguales. Si la vida útil de los equipos de la instalación es menor que el tiempo de obtención del beneficio, el mantenimiento preventivo pasa a ser económicamente inadecuado. La preparación previa del grupo de ejecución del mantenimiento preventivo reduce los costos iniciales del mantenimiento aleatorio restante, sin embargo, el aumento de la inversión para la formación de ese grupo poco altera el resultado económico del periodo de generación de ingresos o beneficios.
En el aspecto de disponibilidad y confiabilidad, la planeación y control disminuye las interrupciones imprevistas de producción(13) y mejora la distribución de la ocupación de la mano de obra, reduciendo las colas de espera de los equipos que aguardan mantenimiento. La planificación adecuada conduce a métodos de mantenimiento con establecimiento de estándares de ejecución, desarrollados a partir de recomendaciones de fabricantes, experiencia del personal interno y bibliografía de empresas similares. Dentro de esos estándares, se destacan las órdenes de pedidos y mantenimiento, las instrucciones de mantenimiento o lista de verificación ("checklist"), las hojas de registro de datos u hoja de variación de especificaciones y el programa maestro de mantenimiento.
Aparentemente la reparación o sustitución de componentes averiados puede parecer más rápida, en un análisis global, se verifica que esta es una concepción falsa, pues generalmente una avería perturba la homogeneidad de los equipos, cuyos resultados acarrean otras necesidades de intervención, y en el computo total, la suma de tiempos de indisponibilidad es mayor a aquel que sería necesario para un examen completo del equipo en la época de la primera intervención.
Además de las referencias presentadas, otros ejemplos de la ventaja de implantación o perfeccionamiento de la filosofía del Mantenimiento Planificado con relación a la del Mantenimiento por Rotura, en el aspecto de disponibilidad, se destacan:
- 1) El aumento de la productividad cerca de 12% de una empresa minera canadiense(14);
- 2) La reducción de costos del mantenimiento en 45% y el aumento de la productividad de 5 a 10% de una empresa portuaria americana(15);
- 3) El aumento de la productividad en 2% de una empresa de energía eléctrica americana(16);
- 4) El aumento de la productividad en 35% de una fábrica de papel inglesa(1).
- 5) La victoria, en una gran competencia, de una empresa japonesa en un país de América del Sur que presentó un índice de rechazo de 0,0001% (uno en un millón) contra 0,5% (cinco en mil) de la competidora nacional(17).
En algunos casos la exigencia de confiabilidad y disponibilidad es de tal orden que se prescinde del estudio de viabilidad económica, de la prevención con relación a la rotura, como en el caso de algunos componentes de una aeronave o del generador de emergencia de un hospital, o de los ascensores de edificios, cuya falla coloca en riesgo vidas humanas o el medio ambiente.
En estos casos son justificadas altas inversiones en planificación y control del mantenimiento para que la confiabilidad alcance valores cercanos a 100%. Se incluyen en esos grupos los equipos cuya parada imprevista, genera grandes pérdidas de materia prima o de la calidad del producto o servicio.
Cursos recomendados




%252FImagen%252FRAMPREDYC-1730060420837.webp%3Falt%3Dmedia%26token%3D2634a7f0-988e-4022-b91f-382503e6e9db&w=3840&q=75)



Referencias
- (1) Introduction to Maintenance Planning in Manufacturing Establishments. United Nations Industrial Development Organization. United Nations - New York - 1975
- (3) Manuale della Manutenzione degli Impianti Industriali. Asturio Baldin, Luciano Furlenetto, Antonio Roversi e Francesco Turco. Franco Angeli Editore. Milano - Italy - 1975
- (11) Mantenimiento Clase Mundial. Fernando Harmsen – Graña & Montero. Trabalho apresentado na Mesa Redonda de Mantenimiento. XXIII Convenção da UPADI – Acapulco – México – 1994
- (12) Como fazer a Manutenção Planejada Compensar. Trabalho divulgado pela Alumax (empresa metalúrgica – E.U.A.) – 1984
- (13) Análise dos Critérios de Manutenção Preventiva de Usinas Geradoras. GCOI – Grupo Coordenador Para Operação Interligada – ELETROBRÁS. GTMU – Grupo de Trabalho de Manutenção de Usinas – 1976
- (14) Programação de Manutenção Preventiva Através de Computador. Falkonbridge Nickel Mines Limited. O.A. MacCann. Artigo apresentado na Ontario Hidro’s (Conf.Man.Mec) – 1974
- (15) Prevenctive & Computerized Maintenance Company – P&CM. 575 Lexington Ave. – New York – NY – 1002. 1975
- (16) Computerized P.M. and System Decreases Dispatcher Duties and Increases Hard Care Savings. George Mack – Western Eletric. Maintenance Engineering. June/1975 – pp 28 a 30
- (17) 3º Seminário Brasileiro sobre Garantia da Qualidade na Manutenção. CETTA – Centro de Treinamento Técnico e Assessoria Ltda. Salvador – Bahia – 1992
Autor: Lourival Augusto Tavares
Brasil
Consultor en Ingeniería de Mantenimiento
Empresa: Director nacional de ABRAMAN (Asociación Brasileña de Mantenimiento) en dos mandatos.
Correo: l.tavares@mandic.com.br
Ingeniero Electricista, formado por la Escuela Federal de Ingeniería de Rio de Janeiro, en el año de 1967. Past-Presidente del Comité Panamericano de Ingeniería de Mantenimiento. Supervisor de Mantenimiento en FURNAS – Centrales Eléctricas S.A. durante 23 años. Fue el jefe de la Asesoría Técnica de Apoyo en ITAIPU Binacional. Reconocido como “notorio saber” en mantenimiento por la Universidad Federal de Rio de Janeiro y por la Universidad Federal de Paraíba.
Dinos qué te ha parecido el artículo
Artículos recomendados
Hornos de Fuego Directo

Garantías extendidas, servicio de mantenimiento y contratos de arrendamiento: modelado y análisis para la toma de decisiones

Tecnología de Confiabilidad: principios y práctica de prevención de fallas en sistemas electrónicos

HALT y HASS de próxima generación: Diseño robusto de electrónica y sistemas

Publica tu artículo en la revista #1 de Mantenimiento Industrial
Publicar un artículo en la revista es gratis, no tiene costo.
Solo debes asegurarte que no sea un artículo comercial.
¿Qué esperas?
O envía tu artículo directo: articulos@predictiva21.com
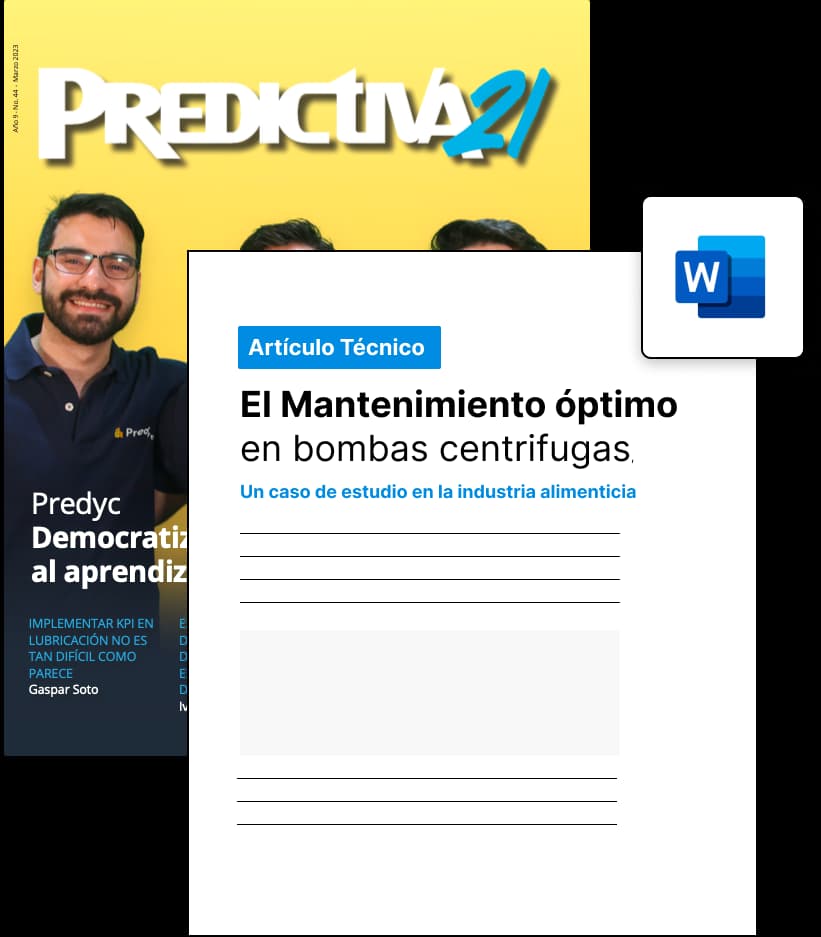
1.2. Costos y productividad
Libros 30 de agosto de 2020En el aspecto de costos, el mantenimiento correctivo a lo largo del tiempo, se presenta con la configuración de una curva ascendente, debido a la reducción de la vida útil de los equipos y la consecuente depreciación del activo, pérdida de producción o calidad de los servicios, aumento de adquisición de repuestos, aumento del "stock" de materia prima improductiva, pago de horas extras del personal de ejecución del mantenimiento, ociosidad de mano de obra operativa, pérdida de mercado y aumento de riesgos de accidentes - Figura 8.

La implantación de la planificación y control, buscando la prevención o predicción de la falla, presenta una configuración de costos invertida, con tasa negativa anual del orden de 20% y tendencia a valores estables, que pueden representar en el computo total, un ahorro de 300 a 500%(9 y 10), siendo más de la mitad de este ahorro debido a la facturación cesante, considerando el Costo Total de una parada de equipo, como la suma del Costo del Mantenimiento, que incluye los costos de mano de obra, repuestos, materiales, combustibles y lubricantes, y el Costo de Indisponibilidad que incluye el costo de Pérdida de Producción (horas no trabajadas), debido a: mala calidad del trabajo; falta de equipos; costo por emergencias; costos extras para reorganizar la producción; costo por repuestos de emergencia; penalidades comerciales e imagen de la empresa. Experiencias de evaluación del Costo de Indisponibilidad muestran que este representa más de la mitad del Costo Total de la parada.(11)
Un ejemplo evidente de los resultados obtenidos con la ejecución de la adecuada Planeación y Control de la función Mantenimiento fue divulgado por una empresa metalúrgica de los Estados Unidos de Norteamérica(12), que presentó los siguientes resultados:
- 1) Conservar el mantenimiento no planificado por debajo del 10%, de los cuales 8,3% es mantenimiento correctivo (la meta de la empresa era de 85% de mantenimiento planificado);
- 2) 0,5% de las horas de trabajo de mantenimiento fueron empleadas en arreglo de daños accidentales, 4,2% en fallas, 2,5% en lubricación, 25,6% en inspecciones, 4,1% en llamadas de emergencia, 6,1% en desmontajes, 40,2% en servicio de rutina programada, 0,2% en servicio de rutina no programada, 7,8% en fabricación y modificaciones y 8,8% en otras actividades como reuniones y capacitación;
- 3) Los costos de mantenimiento eran cerca de 40% por debajo de otras fábricas del mismo tamaño en el sector y se debe básicamente al uso eficiente de mano de obra y el mínimo de horas extras, que da, en promedio, menos de 0,5% por operario/año;
- 4) Los problemas de los equipos son detectados de manera precoz;
- 5) La inversión en mantenimiento incluye personas altamente calificadas, soporte sofisticado de computadora para mantenimiento planificado y una política de mantenimiento de la fábrica y equipos en "estado de nuevo";
- 6) El departamento de mantenimiento tiene total responsabilidad por el mantenimiento de los equipos e instalaciones de la fábrica. Cerca de 2.000 ítems por un valor superior a US$ 200 millones forman la mayor parte de esa responsabilidad.
La inversión inicial en mantenimiento planeado es mayor que el de mantenimiento no planeado y no elimina totalmente las fallas aleatorias, cuyo alto valor inicial es justificado por la inexperiencia del personal de mantenimiento que, al actuar en el equipo, altera su equilibrio operativo. Con el pasar del tiempo y al ganar experiencia, el mantenimiento aleatorio tiende a valores reducidos y estables. La suma general de los gastos del mantenimiento planeado y aleatorio, identificado como mantenimiento preventivo, a partir de un determinado tiempo, pasa a ser inferior al de mantenimiento por rotura(3).
Consecuentemente los beneficios de la prevención solamente ocurrirán a partir del momento en que las áreas comprendidas entre las curvas de mantenimiento por rotura y con prevención, antes y después de ese punto sean iguales. Si la vida útil de los equipos de la instalación es menor que el tiempo de obtención del beneficio, el mantenimiento preventivo pasa a ser económicamente inadecuado. La preparación previa del grupo de ejecución del mantenimiento preventivo reduce los costos iniciales del mantenimiento aleatorio restante, sin embargo, el aumento de la inversión para la formación de ese grupo poco altera el resultado económico del periodo de generación de ingresos o beneficios.
En el aspecto de disponibilidad y confiabilidad, la planeación y control disminuye las interrupciones imprevistas de producción(13) y mejora la distribución de la ocupación de la mano de obra, reduciendo las colas de espera de los equipos que aguardan mantenimiento. La planificación adecuada conduce a métodos de mantenimiento con establecimiento de estándares de ejecución, desarrollados a partir de recomendaciones de fabricantes, experiencia del personal interno y bibliografía de empresas similares. Dentro de esos estándares, se destacan las órdenes de pedidos y mantenimiento, las instrucciones de mantenimiento o lista de verificación ("checklist"), las hojas de registro de datos u hoja de variación de especificaciones y el programa maestro de mantenimiento.
Aparentemente la reparación o sustitución de componentes averiados puede parecer más rápida, en un análisis global, se verifica que esta es una concepción falsa, pues generalmente una avería perturba la homogeneidad de los equipos, cuyos resultados acarrean otras necesidades de intervención, y en el computo total, la suma de tiempos de indisponibilidad es mayor a aquel que sería necesario para un examen completo del equipo en la época de la primera intervención.
Además de las referencias presentadas, otros ejemplos de la ventaja de implantación o perfeccionamiento de la filosofía del Mantenimiento Planificado con relación a la del Mantenimiento por Rotura, en el aspecto de disponibilidad, se destacan:
- 1) El aumento de la productividad cerca de 12% de una empresa minera canadiense(14);
- 2) La reducción de costos del mantenimiento en 45% y el aumento de la productividad de 5 a 10% de una empresa portuaria americana(15);
- 3) El aumento de la productividad en 2% de una empresa de energía eléctrica americana(16);
- 4) El aumento de la productividad en 35% de una fábrica de papel inglesa(1).
- 5) La victoria, en una gran competencia, de una empresa japonesa en un país de América del Sur que presentó un índice de rechazo de 0,0001% (uno en un millón) contra 0,5% (cinco en mil) de la competidora nacional(17).
En algunos casos la exigencia de confiabilidad y disponibilidad es de tal orden que se prescinde del estudio de viabilidad económica, de la prevención con relación a la rotura, como en el caso de algunos componentes de una aeronave o del generador de emergencia de un hospital, o de los ascensores de edificios, cuya falla coloca en riesgo vidas humanas o el medio ambiente.
En estos casos son justificadas altas inversiones en planificación y control del mantenimiento para que la confiabilidad alcance valores cercanos a 100%. Se incluyen en esos grupos los equipos cuya parada imprevista, genera grandes pérdidas de materia prima o de la calidad del producto o servicio.
Cursos recomendados




%252FImagen%252FRAMPREDYC-1730060420837.webp%3Falt%3Dmedia%26token%3D2634a7f0-988e-4022-b91f-382503e6e9db&w=3840&q=75)



Referencias
- (1) Introduction to Maintenance Planning in Manufacturing Establishments. United Nations Industrial Development Organization. United Nations - New York - 1975
- (3) Manuale della Manutenzione degli Impianti Industriali. Asturio Baldin, Luciano Furlenetto, Antonio Roversi e Francesco Turco. Franco Angeli Editore. Milano - Italy - 1975
- (11) Mantenimiento Clase Mundial. Fernando Harmsen – Graña & Montero. Trabalho apresentado na Mesa Redonda de Mantenimiento. XXIII Convenção da UPADI – Acapulco – México – 1994
- (12) Como fazer a Manutenção Planejada Compensar. Trabalho divulgado pela Alumax (empresa metalúrgica – E.U.A.) – 1984
- (13) Análise dos Critérios de Manutenção Preventiva de Usinas Geradoras. GCOI – Grupo Coordenador Para Operação Interligada – ELETROBRÁS. GTMU – Grupo de Trabalho de Manutenção de Usinas – 1976
- (14) Programação de Manutenção Preventiva Através de Computador. Falkonbridge Nickel Mines Limited. O.A. MacCann. Artigo apresentado na Ontario Hidro’s (Conf.Man.Mec) – 1974
- (15) Prevenctive & Computerized Maintenance Company – P&CM. 575 Lexington Ave. – New York – NY – 1002. 1975
- (16) Computerized P.M. and System Decreases Dispatcher Duties and Increases Hard Care Savings. George Mack – Western Eletric. Maintenance Engineering. June/1975 – pp 28 a 30
- (17) 3º Seminário Brasileiro sobre Garantia da Qualidade na Manutenção. CETTA – Centro de Treinamento Técnico e Assessoria Ltda. Salvador – Bahia – 1992
Autor: Lourival Augusto Tavares
Brasil
Consultor en Ingeniería de Mantenimiento
Empresa: Director nacional de ABRAMAN (Asociación Brasileña de Mantenimiento) en dos mandatos.
Correo: l.tavares@mandic.com.br
Ingeniero Electricista, formado por la Escuela Federal de Ingeniería de Rio de Janeiro, en el año de 1967. Past-Presidente del Comité Panamericano de Ingeniería de Mantenimiento. Supervisor de Mantenimiento en FURNAS – Centrales Eléctricas S.A. durante 23 años. Fue el jefe de la Asesoría Técnica de Apoyo en ITAIPU Binacional. Reconocido como “notorio saber” en mantenimiento por la Universidad Federal de Rio de Janeiro y por la Universidad Federal de Paraíba.
Dinos qué te ha parecido el artículo
Artículos recomendados
Hornos de Fuego Directo

Guía del estudiante sobre estadísticas bayesianas

Diseño de ingeniería mecánica de Shigley

9.- Leyes de Afinidad

Publica tu artículo en la revista #1 de Mantenimiento Industrial
Publicar un artículo en la revista es gratis, no tiene costo.
Solo debes asegurarte que no sea un artículo comercial.
¿Qué esperas?
O envía tu artículo directo: articulos@predictiva21.com
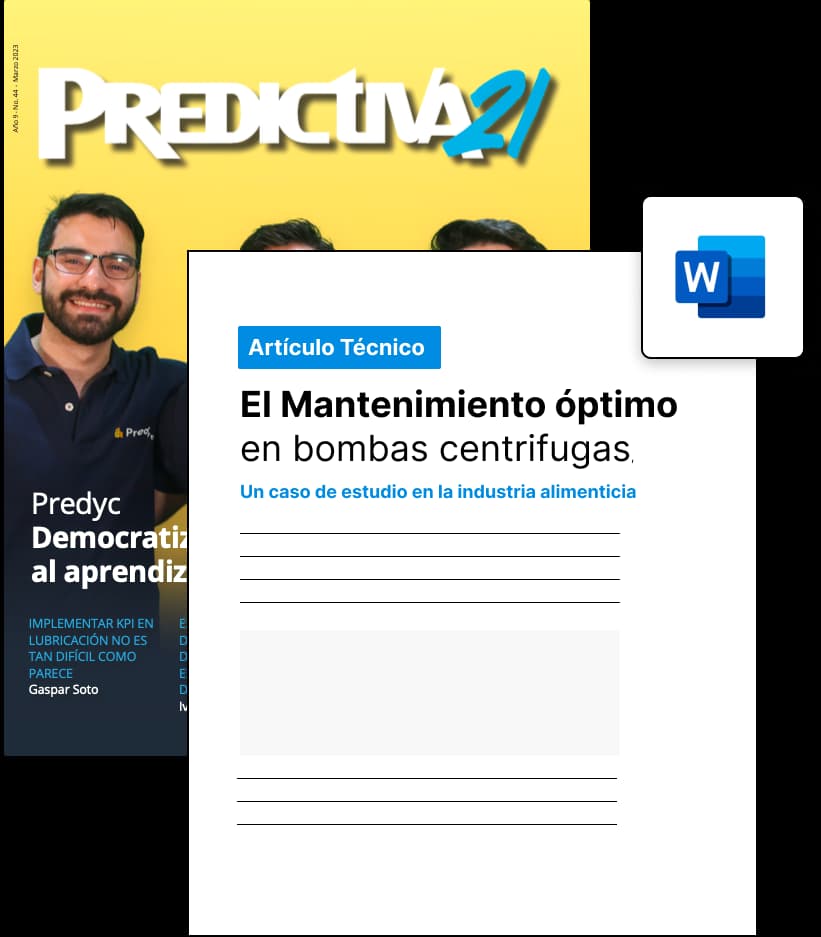