15.3.- Sellos Mecánicos
Articulo6 de septiembre de 2021
Los sellos mecánicos en la actualidad, a nivel mundial, equipan al 95% de las bombas centrífugas instaladas.
Los sellos mecánicos sellan mediante la interacción de las caras sellantes, las cuales se mantienen unidas debido al esfuerzo ejercido por resortes o fuelles en la parte posterior de una de estas caras. En la parte interna de las dos caras se forma una película lubricante que reduce la temperatura y forma una barrera que evita la fuga de producto a la atmósfera.
De acuerdo con estadísticas obtenidas en las refinerías, las fallas de sellos mecánicos representan el 75% del total de fallas mecánicas de las bombas centrífugas. De allí la importancia de seleccionar el diseño o arreglo de sello mecánico adecuado al servicio o a la aplicación propuesta. Adicionalmente a esto el costo de un sello mecánico, representa un porcentaje importante en los costos de los accesorios de las bombas y pueden tener incidencia determinante en los costos de operación y mantenimiento. La figura N° 15-5 muestra la fotografía de un sello mecánico simple con un resorte como elemento de arrastre y cara rotativa de carbono.

Fuente: www.daemar.com
Los sellos mecánicos tienen una amplia gama de complejidad y de precios, se puede ir desde un sello muy simple de fuelle de goma para aplicaciones en bombas centrífugas para agua de servicios domésticos o sistemas de circulación de agua de los vehículos automotores, pasando por sellos que tienen como elemento de arrastre un resorte metálico usados como elemento sellante en servicios industriales ligeros, llegando hasta los sellos de fuelle con sellos secundarios de grafito para altas temperaturas.
En los primeros desarrollos de sellos mecánicos uno de los principales problemas observados, y por tanto una variable que originaba una gran cantidad de fallas, es el control de la fuerza que ejercía el elemento de arrastre o resorte contra las caras de los sellos. La presión dentro de la caja de sellado es alta por lo que se hace necesario un resorte o fuelle que provea una fuerza positiva que mantenga las caras de los sellos cerradas, pero que al mismo tiempo esta fuerza no sea tan alta como para romper la película de lubricación entre las caras.
Como el ajuste de la fuerza ejercida entre las caras se hacía de forma manual los errores eran muy frecuentes, entonces surgieron los sellos balanceados. En los sellos mecánicos balanceados con la forma tanto de las caras rotativas como las caras fijas se buscaba balancear las superficies expuestas a la presión de la caja de sellos, con la finalidad de equilibrar la presión sobre la película lubricante del sello mecánico y evitar de esta forma el sobrecalentamiento de las caras de los sellos, debido a fuerzas excesivas.
El paso siguiente fue la creación de los sellos tipo cartuchos, en este tipo de sellos se mantiene el balance de las fuerzas en las caras por el diseño de las áreas expuestas y adicionalmente el conjunto del sello está montado en una camisa y una brida que ya tiene ajustado la distancia necesaria para que el resorte o fuelle de la bomba aplique la fuerza precisa para mantener las caras de los sellos cerrada, sin romper la película de lubricación. La distancia es ajusta en fábrica y se mantiene el sello descargado hasta instalarlo, en ese momento se retiran unos seguros que liberan el resorte o fuelle proporcionando la carga a las caras de los sellos.
Por ejemplo, la presión en la cara de los sellos varia cuando se ajusta el juego axial en bombas con impulsores abiertos que requieren ajuste axial para mantener la Eficiencia. En este tipo de bomba es necesaria la utilización de sellos de cartucho para evitar cambiar la fuerza ejercida sobre las caras de los sellos
El sello mecánico tiene una serie de ventajas sobre las empaquetaduras que incluye entre otras cosas:
- Producen menos pérdidas de energía que las empaquetaduras, en estudios realizados por usuarios y fabricantes se determinó que un sello mecánico consume aproximadamente la sexta parte de la energía consumida por las empaquetaduras en un servicio similar.
- Reducen el desgaste de las camisas y del eje de la bomba.
- Pueden aplicarse a bombas de alta presión.
- Limitan la fuga de producto hacia la atmosfera.
- Tienen un mayor número de opciones de arreglos para el sellado de los ejes.
Las principales desventajas de los sellos son:
- Son complejos.
- Los costos de adquisición son relativamente altos.
- La imposibilidad de ajustarlos para controlar las fugas si fallan.
La Figura N° 15-6 muestra el diagrama de un sello mecánico balanceado de tipo cartucho.

Fuente: www.direcindustry.com/prod/general-seal-comp…..
Las normas editadas en los países desarrollados recomiendan el uso de sellos mecánicos en todas las bombas que manejan líquidos que puedan ser contaminantes, debido a las estrictas regulaciones ambientales existentes en estos países. Esta tendencia es observada en el API 610/ISO 13709 queexige que todas las bombas fabricadas siguiendo este estándar deben ser equipadas con sellos mecánicos balanceados, el ASME B73.1 es más flexible yacepta en las bombas fabricadas siguiendo este estándar tanto empaquetaduras como sellos mecánicos.
15.3.1.- Partes de los Sellos Mecánicos
Los sellos mecánicos tienen diferentes configuraciones y sus componentes varían de acuerdo con las condiciones de operación y del tipo de bomba centrífuga en la cual son instalados, sin embargo, tienen una serie de componentes básicos que los caracterizan. En la figura 15-7 se muestran estos componentes básicos, en el corte de un sello mecánico del tipo de fuelle metálico instalado en la caja de sellos de una bomba centrífuga.

Fuente: http://www.flowserve.com/files/Files/ProductLiterature/Seals/lit_FSD101Prod_Services3.pdf
Estos componentes de los sellos mecánicos son la cara rotativa, cara estacionaria, sellos secundarios, elementos de arrastre, elementos de fijación y buje de restricción, son comentado y descritos a continuación.
15.3.1.1.- Cara Rotativa
La cara rotativa está unida al eje por lo que gira con El durante el funcionamiento de la bomba, de allí que se denomine cara rotativa. Por lo general es fabricada en Carbón, denominándose cara blanda, aunque de acuerdo con la aplicación pudiese tener caras de otros materiales, como Cerámica, Carburo de Tungsteno, Carburo de Silicio, etc.
Cuando es fabricada de Carbón (esta cara realmente es un compuesto de carbón) está constituida por aproximadamente un 80% de Grafito o Coque y de 15 a 20% de Resina u otro elemento aglomerante y aditivos. Los sellos mecánicos son elementos de alta precisión que requieren acabados de espejo para poder cumplir su función.
Tanto la cara rotativa como la estacionaria son pulidas hasta lograr acabados superficiales que se miden en bandas de luz de helio. Como referencia los sellos son lapeados para lograr un acabado de tres bandas de luz aproximadamente 0,86μm (0,000034 pulgadas). Cuando la planitud llega a cinco (5) bandas de luz o mayor es posible observar fuga de producto por las caras de los sellos, de allí la importancia de lograr un buen acabado de las caras de los sellos. En la figura 15-8 se presenta la cara de un sello mostrando la medición de la plenitud de la cara mediante las bandas de luz de helio.
15.3.1.2.- Cara Estacionaria
La cara estacionaria se fija a la brida del sello y es la denominada cara dura siendo construida de Carburo de Tungsteno, Carburo de Silicio, Cerámica, fundición, etc. En la actualidad en la Industria Petrolera se usan como caras duras fundamentalmente Carburo de Tungsteno y Carburo de Silicio, los cuales son materiales compuestos, fabricados por sinterizado. Cuando son usados con caras rotativas de Carbón tienen un buen rendimiento con altos valores de la relación Presión-Velocidad.

Fuente: Diamond Advances Seal Face Performance Written by Charles F. West, Advanced Diamond Technologies, Inc._ Pumps and Systems, May 2009
15.3.1.3.- Sello Secundario
El sello secundario complementa el sellado realizado por las caras del sello. Sella estáticamente el fluido en la caja de sellos, conteniendo el fluido dentro de la caja sobre todo cuando el equipo no está en funcionamiento. Los sellos secundarios son construidos de distintos materiales y se aplican en diferentes configuraciones, pero modernamente se usan anillos en «O» (O Rings) fabricados con elastómeros como son los Fluorelastómeros (FKM) y Nitrilo, para temperaturas hasta 175 °C (350 °F).
Para servicios de mayor temperatura y para servicios con condiciones particulares, con es el caso de productos químicos que pudiesen alterar los elastómeros tradicionales se utilizan materiales como Teflón (PTFE) y los Perfluorelastómeros (FFKM) que pueden trabajar a temperaturas hasta 290 °C (550 °F). Para muy altas temperaturas de operación el material de los sellos secundarios es Grafito, que para esta aplicación tiene una presentación en cintas que son conformadas para formar el anillo que será utilizado como sello secundario las temperaturas máximas a las que pueden trabajar estos sellos secundarios son 480 °C (900 °F).
En los primeros diseños estos sellos secundarios eran empaquetaduras que sellaban mediante la acción de una fuerza positiva dada por el resorte, lo que hacía el sistema frágil y dependiente del desgate de la empaquetadura que estaba en interacción dinámica con la camisa del eje, el cual también se desgastaba. Con la introducción de los anillos en “O” se eliminó este problema, ya que estos anillos en “O” son elementos estáticos y principalmente resultan dañados por efectos de la temperatura, por ataque químico y más raramente debido a fuerzas excesivas.
15.3.1.4.- Elemento de Arrastre o Conducción
Está constituido por uno o varios fuelles o resortes, este elemento suministra la energía para mantener unidas las caras sellantes. Para aplicaciones comunes se usan sellos monoresortes y multiresortes, los fuelles son usados para servicios de alta presión o temperatura. En los diseños iniciales se usaban los resortes únicos para cerrar las caras de los sellos, pero tenían la desventaja de que para bombas con dos cajas de sellos o caja de empaquetaduras como las del tipo BB (Entre cojinetes o “Between Bearings”) se deben usar dos tipos de resortes diferentes uno que gire a la derecha y otro que gire a la izquierda, lo cual generaba frecuentes errores y aumento de las necesidades de repuestos.
Para resolver este problema surgieron los sellos multiresortes que son una serie de resortes relativamente pequeños alrededor de la cara rotativa, lo que permitía, al no estar girando con el centro de rotación del eje que fueran intercambiables los sellos del lado derecho con los del lado izquierdo.
Para atender servicios de altas temperaturas fueron creados los fuelles metálicos, con materiales de alta aleación. Los sellos mecánicos de fuelle metálicos tienen el elemento de arrastre formado por un fuelle fabricado de láminas metálicas de alta aleación con alta resistencia a presiones y temperaturas.
15.3.1.5.- Elementos de Fijación
Dentro de esta categoría se pueden agrupar los tornillos que fijan la parte rodante del sello al eje de la bomba, la camisa que sostiene el cuerpo del sello mecánico y la brida que forma parte de los sellos de cartucho. La brida aparte de ser un elemento importante en la fijación y en el correcto ajuste de la carga sobre la cara de los sellos, contiene las conexiones para entrada y salida de los líquidos para lubricación de las caras de los sellos, para limpieza y para refrigeración.
15.3.1.6.- Buje de Restricción
Para controlar la fuga en caso de la falla catastrófica del sello mecánico se coloca en la brida del sello mecánico un anillo para restringir el espacio entre la brida y el eje de la bomba, limitando de esta forma el flujo que pudiese salir a la atmósfera. Este buje puede ser construido de diferentes materiales relativamente suaves para evitar daños en el eje, tales como Bronce, Aluminio, Teflón, pero principalmente de un compuesto de Carbón. La holgura de rodaje para que el dispositivo sea más efectivo debe ser de 0,002 mm/mm (0,002 pulgadas/pulgadas) del diámetro del eje.
15.3.2.- Arreglos de Sellos Mecánicos
Los sellos mecánicos pueden ser aplicados en arreglos simples, es decir un solo sello en cada caja de sellos o en arreglod dobles con dos sellos mecánicos instalados por caja de sellos. Los sellos dobles pueden ser colocados en la cajera en alineación Cara a Cara o “back to back” y en arreglo en línea o como su termino en ingles en “tandem”.
15.3.2.1.- Sello Mecánico Simple
El sistema de sellado con un sello mecánico simple es el que contiene un solo sello mecánico por bomba. Este arreglo tiene como ventaja sobre otros sistemas la sencillez y un costo relativo menor por lo que es aplicado en sistemas de bombeo de bajo costo, tanto para aplicaciones domésticas como para aplicaciones industriales y de plantas de procesos.
Entre las desventajas observables en los sellos simples están:
- En caso de falla el fluido contenido en la bomba se derrama a la atmosfera.
- Muchos de ellos de bajo costo no son balanceados lo que genera altas caras en las caras de sellado.
La figura 15-9 muestra el diagrama de un sello mecánico simple, indicando las partes principales.

Fuente: http://www.depac.at/EN/pag
15.3.2.2.- Sello Mecánico Doble
Los sistemas de sellos dobles son ampliamente usados en bombas de ingeniería, en equipos donde no es tolerada la emisión del fluido de procesos a la atmosfera, o cunado el fluido de procesos no posee las propiedades adecuadas para lubricar la cara de los sellos. Los sellos mecánicos dobles pueden ser instalados en arreglo espalda con espalda (back to back) o en línea (tándem).
En el sello espalda con espalda (back to back) para la lubricación de los sellos se introduce una presión en el espacio entre los dos sellos que es superior a la presión de descarga de la bomba. El sello primario es el que realmente hace el sellado del fluido de procesos en la carcasa de la bomba, cuando el sello primario falla el fluido de procesos ingresa en el cuerpo de la bomba debido a que su presión es superior a la presión desarrollada por la bomba evitando que el salga a la atmosfera.
Existen varias configuraciones o planes de lubricación de las caras de los sellos para suministrar la presión al fluido de sellado puede ser mediante un circuito cerrado equipado con bombas para la circulación y presurización del fluido. Esta solución resulta en mayores costos de operación, costos de inversión inicial y en la mayor fragilidad del sistema desde el punto de vista de confiabilidad al incorporar equipos adicionales en el sistema. La figura 15-10 muestra el arreglo de un sello doble.

Fuente:http://www.flowserve.com/files/Files/ProductLiterature/Seals/l.
Existen sistemas de lubricación para sellos dobles más compactos y económicos que utilizan recipientes cerrados de acero inoxidable que se encuentran presurizados, en oportunidades estos sistemas tienen intercambiadores de calor para retirar calor del líquido contenido en el recipiente.
El recipiente del sistema de sellado está presurizado, el fluido de barrera se hace circulando debido al diferencial de temperatura entre la caja de sellado y el recipiente (efecto sifón) y a la acción de los anillos de bombeo. Cuando el sello primario falla, el líquido de barrera contenido en el recipiente entra al proceso debido a que está a mayor presión que la presión de descarga de la bomba. La migración del líquido de barrera hacia la bomba resulta en una caída de nivel del líquido en el recipiente, hasta que se acciona la alarma por bajo nivel, seguido del accionamiento del interruptor por muy bajo nivel de líquido en el interior del recipiente.
15.3.2.3.- Sello Mecánico en Línea
En este arreglo se utilizan dos sellos mecánicos instalados en línea (tándem). Uno de ellos está en contacto con el fluido de procesos. Entre los dos sellos se coloca un fluido de barrera no presurizado que es sellado a la atmosfera con el segundo sello.
Los sellos en línea son ampliamente utilizados para sellar bombas que manejan fluidos con alta presión de vapor (HVP) con tendencia a cambiar de estado o cristalizarse en contacto con la atmosfera. La figura 15-11 muestra un sistema de sellos en línea o “tandem”.

Fuente:http://www.flowserve.com/files/Files/ProductLiterature/Seals/l..
Estos sistemas usan un circuito cerrado con un recipiente que no está presurizado y que está conectado al venteo general de la planta. Este circuito está diseñado con la finalidad de que en servicios donde se tienen fluidos de procesos con baja presión de vapor (HVP), los vapores generados en el proceso venteen fuera del área de las bombas. Al igual que el sistema de sellos doble el recipiente tiene indicadores de nivel (visor), interruptores tanto por alto, como por bajo nivel de líquido en el recipiente.
Cuando ocurre la falla del sello primario el fluido de procesos pasa a la cámara auxiliar de sellado, siendo contenido por el sello secundario y obligado a dirigirse hacia el recipiente auxiliar saturándolo y produciendo la alarma por alto nivel e interrupción del funcionamiento de la bomba por muy alto nivel de líquido en el recipiente.
Cursos recomendados




%252FImagen%252FRAMPREDYC-1730060420837.webp%3Falt%3Dmedia%26token%3D2634a7f0-988e-4022-b91f-382503e6e9db&w=3840&q=75)



15.3.3.- Elementos Resaltantes del API 682
La norma API 682/ISO 21049 “Pumps-Shaft Sealing Systems for Centrifugal and Rotary Pumps” es la norma que regula tanto el uso como los diseños de los sellos mecánicos instalados en las bombas centrifugas y rotativas. En las ediciones iniciales del API 610/ISO 13709 se hacía una descripción detallada de las características de los sellos y poseía una nomenclatura propia para designarlos que era ampliamente utilizada por los fabricantes y usuarios tanto de las bombas centrífugas como de los sellos mecánicos. Con el surgimiento del API 682/ISO 21049, a mediados de los años 90 del siglo XX, el foco se desplazó progresivamente a esa norma hasta reemplazar los conceptos del API 610 por completo.
La norma API 682/ISO 21049 surgió como una necesidad de ampliar la visión sobre los sellos mecánicos debido a que a nivel de industria la mayoría de las fallas asociadas a las bombas centrífugas son causadas por malfuncionamiento de los sellos mecánicos. El fin de la norma no es entrar en detalles del diseño de los componentes de los sellos mecánicos, sin embargo, en el interior de la norma se observa que se tratan detalles constructivos con cierta profundidad con un gran número de requerimientos, en prácticamente todos los componentes de los sellos mecánicos.
El principal objetivo perseguido por la norma es lograr la operación del sello mecánico en servicio continuo por 25.000 horas sin necesidad de reemplazo, para ello establece una serie de requisitos constructivos, dimensionales y de pruebas de los diferentes sistemas de sellado.
A continuación, se ofrecerá una breve descripción de los principales elementos contenidos en esta norma, sin abordar los detalles constructivos en cuanto a dimensiones y acabados tanto de los sellos como de los accesorios.
15.3.3.1.- Categoría de los Sellos
Las categorías de los sellos establecen las ventanas o bandas de operación de los sellos, esto se incluye en la norma con la finalidad de separar los diferentes tipos de servicios no puede ser igual un arreglo de sellos mecánicos estructurado para una bomba de procesos químicos en el rango de operación de la norma ASME B73.1 que un arreglo de sellos para una bomba API 610 a ser aplicada en un servicio de alta presión y temperatura en una refinería.
Las categorías están descritas en la sección 4 “Sealing systems” Sub-sección 4.1.2 “Seal categories” del API 682/ISO 21049. Allí son presentadas y descritas tres categorías, las categorías 1, 2 y 3.
La categoría 1: es aplicada para bombas usadas en servicios petroquímicos amparados por la norma ASME B73.1 y B73.2 e ISO 3069“frame”C. El rango de operación establecido es para temperaturas que van de -40 a 260 °C (-40 a 500 °F) y presiones de 22 bar (315 psi), con un nivel de ensayos categoría 1 y con requerimientos mínimos a nivel de contrato. En esta categoría entran las bombas centrífugas generales de procesos.
La categoría 2: Esta categoría está pensada para bombas construidas siguiendo el API 610/ISO 13709 las cuales son aplicadas en servicios de refinerías en trabajos no tan severos y para atender un rango de temperaturas que van de -40 a 400 °C (-40 a 750 °F) y presiones de 42 bar (615 psi), con un nivel de ensayos categoría 2 y requerimientos mínimos a nivel de contrato. En esta categoría entran las bombas para servicios intermedios.
La categoría 3: Esta categoría está pensada para bombas construidas siguiendo el API 610/ISO 13709 aplicadas en bombas para refinerías en servicios severos y para atender un rango de temperaturas que van de -40 a 400 °C (-40 a 750 °F) y presiones de 42 bar (615 psi), con un nivel de ensayos completo para los cartuchos de los sellos y requerimientos de contrato riguroso. Esta categoría es para las bombas de servicio pesado.
15.3.3.2.- Tipos de Sellos
Los tipos de sellos definidos en el API 682 son los tipos A, tipo B y tipo C. El tipo de sello establece cual debe ser el diseño del sello incluyendo los materiales con los cuales deben ser fabricados.
El sello tipo A, es un sello de arrastre de montaje interno de resortes múltiples, con el elemento flexible normalmente montado sobre el eje, que posee anillos en “O” o “O rings” como sellos secundarios, con caras de “Silicon Carbide” e contra Carbón. Los materiales de construcción son acero inoxidable 316 en los componentes, aleación C-276 para los resortes y fluoroelatómeros como material para los anillos en “O”. La figura 15-12 muestra el diagrama de un sello tipo A, tal como es indicado en el API 682.

Fuente: API 682/ISO 21049 “Pumps—Shaft Sealing Systems for Centrifugal and Rotary Pumps”
El sello tipo B, es un sello de fuelle dinámico (fuelle montado en la parte rotativa de la bomba), los materiales de las caras de los sellos son la cara rotativa de “Silicon Carbide” y la cara fija de Carbón, al igual que el tipo A los componentes son fabricados en acero inoxidable 316, el fuelle es fabricado en aleación C-276 y el material de los anillos en “O” es de fluoroelastómero. La figura 15-13 muestra el diagrama de un sello tipo B.

Fuente: API 682/ISO 21049 “Pumps—Shaft Sealing Systems for Centrifugal and Rotary Pumps”
El sello tipo C, es un sello de fuelle estático (el fuelle está montado en la parte estacionaria del sello), los materiales de construcción son acero inoxidable 316 en los componentes, aleación C-718 como material para el fuelle, el sello secundario es un diafragma fabricado en Grafito. La figura 15-14 muestra el diagrama de un sello tipo C.
15.3.3.3.- Arreglo de Sellos
Existe también dentro de la norma el concepto de los arreglos del sello que indica el número de sellos en el cartucho de sellado y la presión en la cavidad entre los dos sellos. En el arreglo 1 se instala un sello por cada cartucho de sellado. En el arreglo 2 la configuración del cartucho contiene dos sellos mecánicos, con la indicación que la presión en el espacio entre los dos sellos es menor a la presión existente en la cámara del sello.

Fuente: API 682/ISO 21049 “Pumps-Shaft Sealing Systems for Centrifugal and Rotary Pumps”
En el arreglo 3 el cartucho de sellos contiene también dos sellos, pero utiliza una fuente externa para el suministro del líquido de barrera que provee una presión en el espacio entre sello mayor a la presión de la cámara de sello. Otro aspecto cubierto en esta norma es la orientación que tienen los sellos en los arreglos 2 y 3.
15.3.3.4.- Otros Aspectos Relevantes
Un aspecto para destacar en la norma es el énfasis en la estandarización de las pruebas y ensayos a los sellos con la finalidad de poder lograr la meta de duración establecida para los sellos. Para facilitar el proceso de selección de los sellos mecánicos la norma contiene en el anexo A (Recommended seal selection procedure) una guía de selección para que los usuarios seleccionen adecuadamente los sellos para las aplicaciones específicas.
El API 610 hasta la octava edición tenía un código de cinco letras para clasificar los sellos mecánicos, este código resultaba muy práctico porque ayudada a identificar las características del sello con una palabra codificada. Cuando surgió la norma API 682/ISO 21049 este código desapareció quedando un vacío en esta área en la última edición de la norma la tercera de septiembre del 2004, en el anexo D (Mechanical seal codes) se introduce un código de cuatro componentes para compensar la pérdida del código del API 610. Las letras tienen el siguiente significado:
- Primera letra: Establece la categoría del sello, tiene como prefijo la letra C y puede ser C1, C2 o C3 de acuerdo con la categoría del sello.
- Segunda letra: Tiene como prefijo la letra A y define el arreglo de sellos que pueden ser también A1, A2 o A3.
- Tercera letra: arreglo de sello puede tener las letras A, B o C, de acuerdo con el tipo de sello.
- Cuarta letra: es el tipo de lubricación del sello que está indicado en el anexo G. Cuando se utiliza la letra X indica que se debe explicar el tipo de arreglo a usar.
Por ejemplo, un sello clasificado C2A1A11, indica que el sello es categoría 2, sello para bomba API 610 de trabajo ligero, arreglo 1 sello simple, el prefijo a indica el tipo de sello que es A para servicios de bombas general de procesos, y el último prefijo el 11 indica un plan de sellado 11.
Los planes de sellado están en el anexo G, y cubren un amplio espectro de posibilidad y servicios. Los materiales de construcción para los sellos y sus componentes están explicados en el anexo B, “Typical materials standards for seal chamber and mechanical seal components”, comprende las caras rotativas, caras fijas, tornillos de fijación, bridas, fuelles, camisas, anillos en “O”, además este anexo contiene tutoriales que orientan en la selección de los materiales para los diferentes componentes.
15.3.4.- Planes de Lubricación de los Sellos Mecánicos
Como se refirió anteriormente el principio de funcionamiento del sello mecánico se basa en la formación de una película de fluido en las caras sellantes, por esta razón es importante indicar como serán lubricada las caras de los sellos, lo cual se denomina “Plan de Lubricación”. Para el desempeño adecuado del sello es necesario seleccionar el plan de lubricación de las caras del sello más adecuada y que mantenga una buena relación costo beneficio.
Por lo general y por razones prácticas el fluido lubricante de las caras de los sellos mecánicos es el fluido manejado por la bomba. Ahora si este fluido tiene alto grado de contaminación, bajas propiedades lubricantes, se cristalizan en contacto con la atmosfera, tienen baja presión de vapor (HVP), lo más probable es que se recurra a fuentes de lubricación extremas.
En el anexo G del API–682/ISO 21049, titulado “(normative) Standard flush plans and auxiliary hardware” se indican los planes de lubricación a usar en cada aplicación. El ASME B73.1 básicamente utiliza los mismos planes de lubricación del API 682 con la misma designación, pero anteponiéndole un 73 al número del plan, por ejemplo, el plan 11 del API 682 es el plan 7311 en el ASME B73.1.
Existe una variedad importante de planes que contemplan refrigeración del fluido bombeado, eliminación de partículas abrasivas o el uso de fuentes externas de lubricación para los sellos a continuación se hará referencia a los más importantes.
Los planes de lubricación de las caras de los sellos son el plan 01 y el plan 02, los cuales son aplicados en equipos de bajo costo y baja energía (bajo caudal y baja presión) debido a su simplicidad. El plan 01 consiste perforar un agujero para conectar la descarga con la caja de sellos por la parte interna de la carcasa, lo que permite la circulación del fluido desde la descarga a la succión para lubricar las caras de los sellos mecánicos.
La principal precaución que tomar en este plan de lubricación es garantizar que la circulación sea suficiente para retirar el calor generado en el sello. En el plan de lubricación 02 no se tiene prevista la circulación de fluidos, se usa para bombas de baja energía o con chaquetas de enfriamiento sobre la caja de sellos. Lafigura 15-15 muestra el esquema de un plan de lubricación 02.
En el ámbito industrial el plan de lubricación para las caras de los sellos más usado y uno de los mas simples es el plan 11, de hecho, es el plan base del API 682. En este plan de lubricación se toma fluido de la descarga de la bomba mediante el uso de una línea, y se llevan a la caja de sellos para la lubricación de las caras sellantes. El caudal hacia la cara del sello es controlado, mediante una placa orificio, con la finalidad de evitar el exceso de velocidad del fluido que esta entrando a la cámara del sello y que podría erocionar las caras de los sellos.

Fuente: www.polyflon.com
Este plan de lubricación tiene la ventaja de mantener un flujo positivo en el interior de la caja de sellos. Es aplicable a fluidos a temperatura moderada y que no tengan contaminantes, abrasivos o tendencia cristalizarse, debido a que el orifico de la placa tiende a obstruirse. La figura N° 15-16 muestra el diagrama de un arreglo de lubricación para sellos mecánicos basado en el plan 11.

Fuente: Flowserve_Mechanical seal piping plans_Flowserve Solutions Divition
El plan 11 de lubricación para sellos mecánicos del API 610/ISO 13709, soluciona una serie de problemas de sellado que se presentan en el ámbito de las aplicaciones industriales. Sin embargo, existen otras variantes del plan 11 que agrega valor en otras situaciones, por ejemplo, el plan 12, es el mismo plan 11 pero al cual se le agrega un colador en Y a la línea de alimentación del sello mecánico, inmediatamente antes de la placa orificio, con la finalidad de manejar líquidos con algo de contaminación. Si a este mismo plan 12 se adiciona un intercambiador de calor, para bajar la temperatura del líquido que se usará como lubricante de las caras tenemos un plan 22.
Un plan de lubricación para los sellos usado con bastante frecuencia en la Industria Petrolera es el plan 31. Este plan de lubricación es un plan 11 donde se le retira el orificio de restricción y se agrega un ciclón para remover las partículas suspendidas en el fluido, las partículas removidas con el ciclón son enviadas a la succión de la bomba. Esta solución se aplica con la finalidad de retirar los sólidos suspendidos en el fluido de procesos antes de que entren en la cámara de sellado. El principal problema de este plan de lubricación es el ciclón que se satura si el volumen de sólidos es muy alto o es ineficaz si la Gravedad Específica de los sólidos no es al menos dos veces la Gravedad Específica del fluido de procesos.
El API 682 establece en la sección 8.5.1 “Cyclon separador” que las dos condiciones básicas para que los ciclones de separación trabajen eficientemente a pesar de existir otras variables como son el tamaño de las partículas, es que la presión diferencial sea de al menos 1,7 bar (25 psi) y que los sólidos que se quieran remover tengan al menos el doble de la densidad del fluido. La figura N° 15-17 muestra el esquema de una bomba con un plan de lubricación 31.

Fuente: Flowserve_Mechanical seal piping plans_Flowserve Solutions Divition
Otro plan de lubricación importante es el plan 32 que consiste en la inyección de un líquido limpio en la cámara de sellado desde una fuente externa. Se usa cuando el fluido de procesos está sucio o contaminado, posee partículas en suspensión, en el caso de fluidos de procesos a altas temperaturas, para aumentar la presión en la caja de sellado y evitar la vaporización, cuando los fluidos tienen alta presión de vapor (HVP) o se trabaja a altas temperaturas. También se usan cuando los fluidos se polimerizan, se degeneran por oxidación o tienen malas propiedades para la lubricación.
Los principales cuidados y problemas observados en este plan es que el fluido de la fuente externa debe ser compatible con el fluido bombeado, la fuente de suministros del fluido externo debe ser confiable y con la suficiente robustez para mantener el caudal necesario para la lubricación del sello.
La presión de suministro y el caudal del fluido suministrado son medidos mediante un rotámetro y un manómetro instalado en el sistema. Los fluidos externos usado en la Industria Petrolera son mezclas de Glicol y agua o aceites lubricantes ligeros. La figura N° 15-18 presenta el diagrama de un sello mecánico lubricado con un plan 32 indicando los principales componentes de este arreglo.

Fuente: Flowserve_Mechanical seal piping plans_Flowserve Solutions Divition
Con el auge de la preservación del ambiente se han ampliado los planes de lubricación ecológicos donde el fluido no debe tener contacto con la atmosfera o donde no son toleradas las emisiones por ser los productos tóxicos o contaminantes uno de estos planes de lubricación es el plan 52 que consiste en un sistema de sello doble, donde en la cámara entre los dos sellos se tiene un fluido de barrera despresurizado que circula, ayudado por un anillo de bombeo, a un recipiente instrumentado con indicadores de nivel, interruptores de nivel alto y bajo y un interruptor de presión.
El plan 52 es ampliamente usado porque no necesita el mantenimiento de una presión en el sistema, allí al fallar el primer sello el fluido de barrera se contamina con el fluido de procesos, lo que hace que suba el nivel del recipiente accionado el interruptor de nivel alto o el de presión. Los recipientes están normalizados en el API 682 deben tener una capacidad mínima de 12 litros (3 galones), y tienen que ser fabricados en acero 316L, deben contar visores de nivel, conexiones para entrada y salida del fluido de barrera, serpentín para enfriamiento con las conexiones para la entrada y la salida del fluido refrigerante, conexiones de drenaje y venteo, así como para la instalación de interruptores de nivel, interruptores de presión e indicadores de presión. La figura 15-19 muestra un sistema con un plan de lubricación 52 y la instrumentación correspondiente.

Fuente: Flowserve_Mechanical seal piping plans_Flowserve Solutions Divition
Cuando se tienen las mismas restricciones ambientales, los fluidos de procesos son inapropiados para lubricar las caras de los sellos y no se cuenta con una fuente externa confiable y a la presión requerida de fluido para la lubricación de las caras de los sellos una alternativa es el plan de lubricación 54 que es un sistema de circulación que suministra un fluido de barrera externo mediante un sistema de bombeo autónomo a un sistema de sellos dobles.
La desventaja de este sistema es el costo del sistema que es relativamente alto a parte de los costos de mantenimiento, también se corre el peligro que ante la falla del sello o los sellos se contamine todo el fluido de barrera contenido en el sistema, además es necesario mantener siempre el sistema energizado. La figura 15-20 muestra el diagrama de un sistema de lubricación para la cara de sellos del tipo plan 54, donde es posible ver la fuente externa de presión y las líneas de circulación.

Fuente: www.polyflon.com
Entre los planes de lubricación más actuales está el plan 72, que es aplicado fundamentalmente cuando se usan en sistemas de sellado no presurizados con sellos dobles en “tandem” que tienen como fluido de barrera gas, el gas es típicamente nitrógeno.
El plan 72 se aplica para sellar fluidos con alta presión de vapor (HVP), para hidrocarburos livianos, fluidos tóxicos o contaminantes. Los cuidados que se deben tener es poseer una fuente de gas confiable, mantener la presión del fluido de barrera al menos 1,75 bar (25 psi) por arriba de la presión de la cámara de sellado. La figura 15-21 muestra el diagrama de un sistema de lubricación para sellos mecánicos plan 72, donde se indican los componentes básicos del sistema.
Lo fundamental para seleccionar el plan de lubricación adecuado a cada servicio es ajustarse a las necesidades reales del proceso, no complicarlo con accesorios excesivos o innecesarios, atender a la disponibilidad de los recursos existentes en la planta y a la filosofía de operación establecida.

Fuente: Flowserve_Mechanical seal piping plans_Flowserve Solutions Divition
Dinos qué te ha parecido el artículo
Artículos recomendados
19.- Vibración Mecánica en Bombas Centrífugas

Enfoque basado en procesos

La Gestión del Conocimiento como parte de la Gestión de Activos

Planificación de un paro de Mantenimiento

Publica tu artículo en la revista #1 de Mantenimiento Industrial
Publicar un artículo en la revista es gratis, no tiene costo.
Solo debes asegurarte que no sea un artículo comercial.
¿Qué esperas?
O envía tu artículo directo: articulos@predictiva21.com
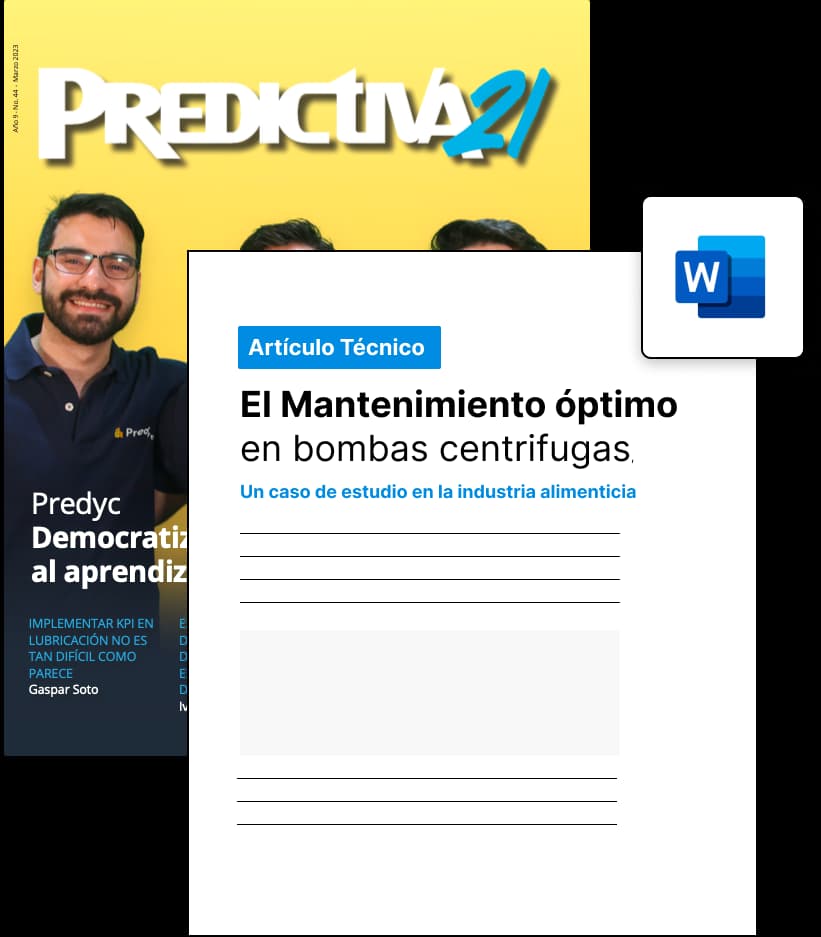
15.3.- Sellos Mecánicos
Articulo 6 de septiembre de 2021Los sellos mecánicos en la actualidad, a nivel mundial, equipan al 95% de las bombas centrífugas instaladas.
Los sellos mecánicos sellan mediante la interacción de las caras sellantes, las cuales se mantienen unidas debido al esfuerzo ejercido por resortes o fuelles en la parte posterior de una de estas caras. En la parte interna de las dos caras se forma una película lubricante que reduce la temperatura y forma una barrera que evita la fuga de producto a la atmósfera.
De acuerdo con estadísticas obtenidas en las refinerías, las fallas de sellos mecánicos representan el 75% del total de fallas mecánicas de las bombas centrífugas. De allí la importancia de seleccionar el diseño o arreglo de sello mecánico adecuado al servicio o a la aplicación propuesta. Adicionalmente a esto el costo de un sello mecánico, representa un porcentaje importante en los costos de los accesorios de las bombas y pueden tener incidencia determinante en los costos de operación y mantenimiento. La figura N° 15-5 muestra la fotografía de un sello mecánico simple con un resorte como elemento de arrastre y cara rotativa de carbono.

Fuente: www.daemar.com
Los sellos mecánicos tienen una amplia gama de complejidad y de precios, se puede ir desde un sello muy simple de fuelle de goma para aplicaciones en bombas centrífugas para agua de servicios domésticos o sistemas de circulación de agua de los vehículos automotores, pasando por sellos que tienen como elemento de arrastre un resorte metálico usados como elemento sellante en servicios industriales ligeros, llegando hasta los sellos de fuelle con sellos secundarios de grafito para altas temperaturas.
En los primeros desarrollos de sellos mecánicos uno de los principales problemas observados, y por tanto una variable que originaba una gran cantidad de fallas, es el control de la fuerza que ejercía el elemento de arrastre o resorte contra las caras de los sellos. La presión dentro de la caja de sellado es alta por lo que se hace necesario un resorte o fuelle que provea una fuerza positiva que mantenga las caras de los sellos cerradas, pero que al mismo tiempo esta fuerza no sea tan alta como para romper la película de lubricación entre las caras.
Como el ajuste de la fuerza ejercida entre las caras se hacía de forma manual los errores eran muy frecuentes, entonces surgieron los sellos balanceados. En los sellos mecánicos balanceados con la forma tanto de las caras rotativas como las caras fijas se buscaba balancear las superficies expuestas a la presión de la caja de sellos, con la finalidad de equilibrar la presión sobre la película lubricante del sello mecánico y evitar de esta forma el sobrecalentamiento de las caras de los sellos, debido a fuerzas excesivas.
El paso siguiente fue la creación de los sellos tipo cartuchos, en este tipo de sellos se mantiene el balance de las fuerzas en las caras por el diseño de las áreas expuestas y adicionalmente el conjunto del sello está montado en una camisa y una brida que ya tiene ajustado la distancia necesaria para que el resorte o fuelle de la bomba aplique la fuerza precisa para mantener las caras de los sellos cerrada, sin romper la película de lubricación. La distancia es ajusta en fábrica y se mantiene el sello descargado hasta instalarlo, en ese momento se retiran unos seguros que liberan el resorte o fuelle proporcionando la carga a las caras de los sellos.
Por ejemplo, la presión en la cara de los sellos varia cuando se ajusta el juego axial en bombas con impulsores abiertos que requieren ajuste axial para mantener la Eficiencia. En este tipo de bomba es necesaria la utilización de sellos de cartucho para evitar cambiar la fuerza ejercida sobre las caras de los sellos
El sello mecánico tiene una serie de ventajas sobre las empaquetaduras que incluye entre otras cosas:
- Producen menos pérdidas de energía que las empaquetaduras, en estudios realizados por usuarios y fabricantes se determinó que un sello mecánico consume aproximadamente la sexta parte de la energía consumida por las empaquetaduras en un servicio similar.
- Reducen el desgaste de las camisas y del eje de la bomba.
- Pueden aplicarse a bombas de alta presión.
- Limitan la fuga de producto hacia la atmosfera.
- Tienen un mayor número de opciones de arreglos para el sellado de los ejes.
Las principales desventajas de los sellos son:
- Son complejos.
- Los costos de adquisición son relativamente altos.
- La imposibilidad de ajustarlos para controlar las fugas si fallan.
La Figura N° 15-6 muestra el diagrama de un sello mecánico balanceado de tipo cartucho.

Fuente: www.direcindustry.com/prod/general-seal-comp…..
Las normas editadas en los países desarrollados recomiendan el uso de sellos mecánicos en todas las bombas que manejan líquidos que puedan ser contaminantes, debido a las estrictas regulaciones ambientales existentes en estos países. Esta tendencia es observada en el API 610/ISO 13709 queexige que todas las bombas fabricadas siguiendo este estándar deben ser equipadas con sellos mecánicos balanceados, el ASME B73.1 es más flexible yacepta en las bombas fabricadas siguiendo este estándar tanto empaquetaduras como sellos mecánicos.
15.3.1.- Partes de los Sellos Mecánicos
Los sellos mecánicos tienen diferentes configuraciones y sus componentes varían de acuerdo con las condiciones de operación y del tipo de bomba centrífuga en la cual son instalados, sin embargo, tienen una serie de componentes básicos que los caracterizan. En la figura 15-7 se muestran estos componentes básicos, en el corte de un sello mecánico del tipo de fuelle metálico instalado en la caja de sellos de una bomba centrífuga.

Fuente: http://www.flowserve.com/files/Files/ProductLiterature/Seals/lit_FSD101Prod_Services3.pdf
Estos componentes de los sellos mecánicos son la cara rotativa, cara estacionaria, sellos secundarios, elementos de arrastre, elementos de fijación y buje de restricción, son comentado y descritos a continuación.
15.3.1.1.- Cara Rotativa
La cara rotativa está unida al eje por lo que gira con El durante el funcionamiento de la bomba, de allí que se denomine cara rotativa. Por lo general es fabricada en Carbón, denominándose cara blanda, aunque de acuerdo con la aplicación pudiese tener caras de otros materiales, como Cerámica, Carburo de Tungsteno, Carburo de Silicio, etc.
Cuando es fabricada de Carbón (esta cara realmente es un compuesto de carbón) está constituida por aproximadamente un 80% de Grafito o Coque y de 15 a 20% de Resina u otro elemento aglomerante y aditivos. Los sellos mecánicos son elementos de alta precisión que requieren acabados de espejo para poder cumplir su función.
Tanto la cara rotativa como la estacionaria son pulidas hasta lograr acabados superficiales que se miden en bandas de luz de helio. Como referencia los sellos son lapeados para lograr un acabado de tres bandas de luz aproximadamente 0,86μm (0,000034 pulgadas). Cuando la planitud llega a cinco (5) bandas de luz o mayor es posible observar fuga de producto por las caras de los sellos, de allí la importancia de lograr un buen acabado de las caras de los sellos. En la figura 15-8 se presenta la cara de un sello mostrando la medición de la plenitud de la cara mediante las bandas de luz de helio.
15.3.1.2.- Cara Estacionaria
La cara estacionaria se fija a la brida del sello y es la denominada cara dura siendo construida de Carburo de Tungsteno, Carburo de Silicio, Cerámica, fundición, etc. En la actualidad en la Industria Petrolera se usan como caras duras fundamentalmente Carburo de Tungsteno y Carburo de Silicio, los cuales son materiales compuestos, fabricados por sinterizado. Cuando son usados con caras rotativas de Carbón tienen un buen rendimiento con altos valores de la relación Presión-Velocidad.

Fuente: Diamond Advances Seal Face Performance Written by Charles F. West, Advanced Diamond Technologies, Inc._ Pumps and Systems, May 2009
15.3.1.3.- Sello Secundario
El sello secundario complementa el sellado realizado por las caras del sello. Sella estáticamente el fluido en la caja de sellos, conteniendo el fluido dentro de la caja sobre todo cuando el equipo no está en funcionamiento. Los sellos secundarios son construidos de distintos materiales y se aplican en diferentes configuraciones, pero modernamente se usan anillos en «O» (O Rings) fabricados con elastómeros como son los Fluorelastómeros (FKM) y Nitrilo, para temperaturas hasta 175 °C (350 °F).
Para servicios de mayor temperatura y para servicios con condiciones particulares, con es el caso de productos químicos que pudiesen alterar los elastómeros tradicionales se utilizan materiales como Teflón (PTFE) y los Perfluorelastómeros (FFKM) que pueden trabajar a temperaturas hasta 290 °C (550 °F). Para muy altas temperaturas de operación el material de los sellos secundarios es Grafito, que para esta aplicación tiene una presentación en cintas que son conformadas para formar el anillo que será utilizado como sello secundario las temperaturas máximas a las que pueden trabajar estos sellos secundarios son 480 °C (900 °F).
En los primeros diseños estos sellos secundarios eran empaquetaduras que sellaban mediante la acción de una fuerza positiva dada por el resorte, lo que hacía el sistema frágil y dependiente del desgate de la empaquetadura que estaba en interacción dinámica con la camisa del eje, el cual también se desgastaba. Con la introducción de los anillos en “O” se eliminó este problema, ya que estos anillos en “O” son elementos estáticos y principalmente resultan dañados por efectos de la temperatura, por ataque químico y más raramente debido a fuerzas excesivas.
15.3.1.4.- Elemento de Arrastre o Conducción
Está constituido por uno o varios fuelles o resortes, este elemento suministra la energía para mantener unidas las caras sellantes. Para aplicaciones comunes se usan sellos monoresortes y multiresortes, los fuelles son usados para servicios de alta presión o temperatura. En los diseños iniciales se usaban los resortes únicos para cerrar las caras de los sellos, pero tenían la desventaja de que para bombas con dos cajas de sellos o caja de empaquetaduras como las del tipo BB (Entre cojinetes o “Between Bearings”) se deben usar dos tipos de resortes diferentes uno que gire a la derecha y otro que gire a la izquierda, lo cual generaba frecuentes errores y aumento de las necesidades de repuestos.
Para resolver este problema surgieron los sellos multiresortes que son una serie de resortes relativamente pequeños alrededor de la cara rotativa, lo que permitía, al no estar girando con el centro de rotación del eje que fueran intercambiables los sellos del lado derecho con los del lado izquierdo.
Para atender servicios de altas temperaturas fueron creados los fuelles metálicos, con materiales de alta aleación. Los sellos mecánicos de fuelle metálicos tienen el elemento de arrastre formado por un fuelle fabricado de láminas metálicas de alta aleación con alta resistencia a presiones y temperaturas.
15.3.1.5.- Elementos de Fijación
Dentro de esta categoría se pueden agrupar los tornillos que fijan la parte rodante del sello al eje de la bomba, la camisa que sostiene el cuerpo del sello mecánico y la brida que forma parte de los sellos de cartucho. La brida aparte de ser un elemento importante en la fijación y en el correcto ajuste de la carga sobre la cara de los sellos, contiene las conexiones para entrada y salida de los líquidos para lubricación de las caras de los sellos, para limpieza y para refrigeración.
15.3.1.6.- Buje de Restricción
Para controlar la fuga en caso de la falla catastrófica del sello mecánico se coloca en la brida del sello mecánico un anillo para restringir el espacio entre la brida y el eje de la bomba, limitando de esta forma el flujo que pudiese salir a la atmósfera. Este buje puede ser construido de diferentes materiales relativamente suaves para evitar daños en el eje, tales como Bronce, Aluminio, Teflón, pero principalmente de un compuesto de Carbón. La holgura de rodaje para que el dispositivo sea más efectivo debe ser de 0,002 mm/mm (0,002 pulgadas/pulgadas) del diámetro del eje.
15.3.2.- Arreglos de Sellos Mecánicos
Los sellos mecánicos pueden ser aplicados en arreglos simples, es decir un solo sello en cada caja de sellos o en arreglod dobles con dos sellos mecánicos instalados por caja de sellos. Los sellos dobles pueden ser colocados en la cajera en alineación Cara a Cara o “back to back” y en arreglo en línea o como su termino en ingles en “tandem”.
15.3.2.1.- Sello Mecánico Simple
El sistema de sellado con un sello mecánico simple es el que contiene un solo sello mecánico por bomba. Este arreglo tiene como ventaja sobre otros sistemas la sencillez y un costo relativo menor por lo que es aplicado en sistemas de bombeo de bajo costo, tanto para aplicaciones domésticas como para aplicaciones industriales y de plantas de procesos.
Entre las desventajas observables en los sellos simples están:
- En caso de falla el fluido contenido en la bomba se derrama a la atmosfera.
- Muchos de ellos de bajo costo no son balanceados lo que genera altas caras en las caras de sellado.
La figura 15-9 muestra el diagrama de un sello mecánico simple, indicando las partes principales.

Fuente: http://www.depac.at/EN/pag
15.3.2.2.- Sello Mecánico Doble
Los sistemas de sellos dobles son ampliamente usados en bombas de ingeniería, en equipos donde no es tolerada la emisión del fluido de procesos a la atmosfera, o cunado el fluido de procesos no posee las propiedades adecuadas para lubricar la cara de los sellos. Los sellos mecánicos dobles pueden ser instalados en arreglo espalda con espalda (back to back) o en línea (tándem).
En el sello espalda con espalda (back to back) para la lubricación de los sellos se introduce una presión en el espacio entre los dos sellos que es superior a la presión de descarga de la bomba. El sello primario es el que realmente hace el sellado del fluido de procesos en la carcasa de la bomba, cuando el sello primario falla el fluido de procesos ingresa en el cuerpo de la bomba debido a que su presión es superior a la presión desarrollada por la bomba evitando que el salga a la atmosfera.
Existen varias configuraciones o planes de lubricación de las caras de los sellos para suministrar la presión al fluido de sellado puede ser mediante un circuito cerrado equipado con bombas para la circulación y presurización del fluido. Esta solución resulta en mayores costos de operación, costos de inversión inicial y en la mayor fragilidad del sistema desde el punto de vista de confiabilidad al incorporar equipos adicionales en el sistema. La figura 15-10 muestra el arreglo de un sello doble.

Fuente:http://www.flowserve.com/files/Files/ProductLiterature/Seals/l.
Existen sistemas de lubricación para sellos dobles más compactos y económicos que utilizan recipientes cerrados de acero inoxidable que se encuentran presurizados, en oportunidades estos sistemas tienen intercambiadores de calor para retirar calor del líquido contenido en el recipiente.
El recipiente del sistema de sellado está presurizado, el fluido de barrera se hace circulando debido al diferencial de temperatura entre la caja de sellado y el recipiente (efecto sifón) y a la acción de los anillos de bombeo. Cuando el sello primario falla, el líquido de barrera contenido en el recipiente entra al proceso debido a que está a mayor presión que la presión de descarga de la bomba. La migración del líquido de barrera hacia la bomba resulta en una caída de nivel del líquido en el recipiente, hasta que se acciona la alarma por bajo nivel, seguido del accionamiento del interruptor por muy bajo nivel de líquido en el interior del recipiente.
15.3.2.3.- Sello Mecánico en Línea
En este arreglo se utilizan dos sellos mecánicos instalados en línea (tándem). Uno de ellos está en contacto con el fluido de procesos. Entre los dos sellos se coloca un fluido de barrera no presurizado que es sellado a la atmosfera con el segundo sello.
Los sellos en línea son ampliamente utilizados para sellar bombas que manejan fluidos con alta presión de vapor (HVP) con tendencia a cambiar de estado o cristalizarse en contacto con la atmosfera. La figura 15-11 muestra un sistema de sellos en línea o “tandem”.

Fuente:http://www.flowserve.com/files/Files/ProductLiterature/Seals/l..
Estos sistemas usan un circuito cerrado con un recipiente que no está presurizado y que está conectado al venteo general de la planta. Este circuito está diseñado con la finalidad de que en servicios donde se tienen fluidos de procesos con baja presión de vapor (HVP), los vapores generados en el proceso venteen fuera del área de las bombas. Al igual que el sistema de sellos doble el recipiente tiene indicadores de nivel (visor), interruptores tanto por alto, como por bajo nivel de líquido en el recipiente.
Cuando ocurre la falla del sello primario el fluido de procesos pasa a la cámara auxiliar de sellado, siendo contenido por el sello secundario y obligado a dirigirse hacia el recipiente auxiliar saturándolo y produciendo la alarma por alto nivel e interrupción del funcionamiento de la bomba por muy alto nivel de líquido en el recipiente.
Cursos recomendados




%252FImagen%252FRAMPREDYC-1730060420837.webp%3Falt%3Dmedia%26token%3D2634a7f0-988e-4022-b91f-382503e6e9db&w=3840&q=75)



15.3.3.- Elementos Resaltantes del API 682
La norma API 682/ISO 21049 “Pumps-Shaft Sealing Systems for Centrifugal and Rotary Pumps” es la norma que regula tanto el uso como los diseños de los sellos mecánicos instalados en las bombas centrifugas y rotativas. En las ediciones iniciales del API 610/ISO 13709 se hacía una descripción detallada de las características de los sellos y poseía una nomenclatura propia para designarlos que era ampliamente utilizada por los fabricantes y usuarios tanto de las bombas centrífugas como de los sellos mecánicos. Con el surgimiento del API 682/ISO 21049, a mediados de los años 90 del siglo XX, el foco se desplazó progresivamente a esa norma hasta reemplazar los conceptos del API 610 por completo.
La norma API 682/ISO 21049 surgió como una necesidad de ampliar la visión sobre los sellos mecánicos debido a que a nivel de industria la mayoría de las fallas asociadas a las bombas centrífugas son causadas por malfuncionamiento de los sellos mecánicos. El fin de la norma no es entrar en detalles del diseño de los componentes de los sellos mecánicos, sin embargo, en el interior de la norma se observa que se tratan detalles constructivos con cierta profundidad con un gran número de requerimientos, en prácticamente todos los componentes de los sellos mecánicos.
El principal objetivo perseguido por la norma es lograr la operación del sello mecánico en servicio continuo por 25.000 horas sin necesidad de reemplazo, para ello establece una serie de requisitos constructivos, dimensionales y de pruebas de los diferentes sistemas de sellado.
A continuación, se ofrecerá una breve descripción de los principales elementos contenidos en esta norma, sin abordar los detalles constructivos en cuanto a dimensiones y acabados tanto de los sellos como de los accesorios.
15.3.3.1.- Categoría de los Sellos
Las categorías de los sellos establecen las ventanas o bandas de operación de los sellos, esto se incluye en la norma con la finalidad de separar los diferentes tipos de servicios no puede ser igual un arreglo de sellos mecánicos estructurado para una bomba de procesos químicos en el rango de operación de la norma ASME B73.1 que un arreglo de sellos para una bomba API 610 a ser aplicada en un servicio de alta presión y temperatura en una refinería.
Las categorías están descritas en la sección 4 “Sealing systems” Sub-sección 4.1.2 “Seal categories” del API 682/ISO 21049. Allí son presentadas y descritas tres categorías, las categorías 1, 2 y 3.
La categoría 1: es aplicada para bombas usadas en servicios petroquímicos amparados por la norma ASME B73.1 y B73.2 e ISO 3069“frame”C. El rango de operación establecido es para temperaturas que van de -40 a 260 °C (-40 a 500 °F) y presiones de 22 bar (315 psi), con un nivel de ensayos categoría 1 y con requerimientos mínimos a nivel de contrato. En esta categoría entran las bombas centrífugas generales de procesos.
La categoría 2: Esta categoría está pensada para bombas construidas siguiendo el API 610/ISO 13709 las cuales son aplicadas en servicios de refinerías en trabajos no tan severos y para atender un rango de temperaturas que van de -40 a 400 °C (-40 a 750 °F) y presiones de 42 bar (615 psi), con un nivel de ensayos categoría 2 y requerimientos mínimos a nivel de contrato. En esta categoría entran las bombas para servicios intermedios.
La categoría 3: Esta categoría está pensada para bombas construidas siguiendo el API 610/ISO 13709 aplicadas en bombas para refinerías en servicios severos y para atender un rango de temperaturas que van de -40 a 400 °C (-40 a 750 °F) y presiones de 42 bar (615 psi), con un nivel de ensayos completo para los cartuchos de los sellos y requerimientos de contrato riguroso. Esta categoría es para las bombas de servicio pesado.
15.3.3.2.- Tipos de Sellos
Los tipos de sellos definidos en el API 682 son los tipos A, tipo B y tipo C. El tipo de sello establece cual debe ser el diseño del sello incluyendo los materiales con los cuales deben ser fabricados.
El sello tipo A, es un sello de arrastre de montaje interno de resortes múltiples, con el elemento flexible normalmente montado sobre el eje, que posee anillos en “O” o “O rings” como sellos secundarios, con caras de “Silicon Carbide” e contra Carbón. Los materiales de construcción son acero inoxidable 316 en los componentes, aleación C-276 para los resortes y fluoroelatómeros como material para los anillos en “O”. La figura 15-12 muestra el diagrama de un sello tipo A, tal como es indicado en el API 682.

Fuente: API 682/ISO 21049 “Pumps—Shaft Sealing Systems for Centrifugal and Rotary Pumps”
El sello tipo B, es un sello de fuelle dinámico (fuelle montado en la parte rotativa de la bomba), los materiales de las caras de los sellos son la cara rotativa de “Silicon Carbide” y la cara fija de Carbón, al igual que el tipo A los componentes son fabricados en acero inoxidable 316, el fuelle es fabricado en aleación C-276 y el material de los anillos en “O” es de fluoroelastómero. La figura 15-13 muestra el diagrama de un sello tipo B.

Fuente: API 682/ISO 21049 “Pumps—Shaft Sealing Systems for Centrifugal and Rotary Pumps”
El sello tipo C, es un sello de fuelle estático (el fuelle está montado en la parte estacionaria del sello), los materiales de construcción son acero inoxidable 316 en los componentes, aleación C-718 como material para el fuelle, el sello secundario es un diafragma fabricado en Grafito. La figura 15-14 muestra el diagrama de un sello tipo C.
15.3.3.3.- Arreglo de Sellos
Existe también dentro de la norma el concepto de los arreglos del sello que indica el número de sellos en el cartucho de sellado y la presión en la cavidad entre los dos sellos. En el arreglo 1 se instala un sello por cada cartucho de sellado. En el arreglo 2 la configuración del cartucho contiene dos sellos mecánicos, con la indicación que la presión en el espacio entre los dos sellos es menor a la presión existente en la cámara del sello.

Fuente: API 682/ISO 21049 “Pumps-Shaft Sealing Systems for Centrifugal and Rotary Pumps”
En el arreglo 3 el cartucho de sellos contiene también dos sellos, pero utiliza una fuente externa para el suministro del líquido de barrera que provee una presión en el espacio entre sello mayor a la presión de la cámara de sello. Otro aspecto cubierto en esta norma es la orientación que tienen los sellos en los arreglos 2 y 3.
15.3.3.4.- Otros Aspectos Relevantes
Un aspecto para destacar en la norma es el énfasis en la estandarización de las pruebas y ensayos a los sellos con la finalidad de poder lograr la meta de duración establecida para los sellos. Para facilitar el proceso de selección de los sellos mecánicos la norma contiene en el anexo A (Recommended seal selection procedure) una guía de selección para que los usuarios seleccionen adecuadamente los sellos para las aplicaciones específicas.
El API 610 hasta la octava edición tenía un código de cinco letras para clasificar los sellos mecánicos, este código resultaba muy práctico porque ayudada a identificar las características del sello con una palabra codificada. Cuando surgió la norma API 682/ISO 21049 este código desapareció quedando un vacío en esta área en la última edición de la norma la tercera de septiembre del 2004, en el anexo D (Mechanical seal codes) se introduce un código de cuatro componentes para compensar la pérdida del código del API 610. Las letras tienen el siguiente significado:
- Primera letra: Establece la categoría del sello, tiene como prefijo la letra C y puede ser C1, C2 o C3 de acuerdo con la categoría del sello.
- Segunda letra: Tiene como prefijo la letra A y define el arreglo de sellos que pueden ser también A1, A2 o A3.
- Tercera letra: arreglo de sello puede tener las letras A, B o C, de acuerdo con el tipo de sello.
- Cuarta letra: es el tipo de lubricación del sello que está indicado en el anexo G. Cuando se utiliza la letra X indica que se debe explicar el tipo de arreglo a usar.
Por ejemplo, un sello clasificado C2A1A11, indica que el sello es categoría 2, sello para bomba API 610 de trabajo ligero, arreglo 1 sello simple, el prefijo a indica el tipo de sello que es A para servicios de bombas general de procesos, y el último prefijo el 11 indica un plan de sellado 11.
Los planes de sellado están en el anexo G, y cubren un amplio espectro de posibilidad y servicios. Los materiales de construcción para los sellos y sus componentes están explicados en el anexo B, “Typical materials standards for seal chamber and mechanical seal components”, comprende las caras rotativas, caras fijas, tornillos de fijación, bridas, fuelles, camisas, anillos en “O”, además este anexo contiene tutoriales que orientan en la selección de los materiales para los diferentes componentes.
15.3.4.- Planes de Lubricación de los Sellos Mecánicos
Como se refirió anteriormente el principio de funcionamiento del sello mecánico se basa en la formación de una película de fluido en las caras sellantes, por esta razón es importante indicar como serán lubricada las caras de los sellos, lo cual se denomina “Plan de Lubricación”. Para el desempeño adecuado del sello es necesario seleccionar el plan de lubricación de las caras del sello más adecuada y que mantenga una buena relación costo beneficio.
Por lo general y por razones prácticas el fluido lubricante de las caras de los sellos mecánicos es el fluido manejado por la bomba. Ahora si este fluido tiene alto grado de contaminación, bajas propiedades lubricantes, se cristalizan en contacto con la atmosfera, tienen baja presión de vapor (HVP), lo más probable es que se recurra a fuentes de lubricación extremas.
En el anexo G del API–682/ISO 21049, titulado “(normative) Standard flush plans and auxiliary hardware” se indican los planes de lubricación a usar en cada aplicación. El ASME B73.1 básicamente utiliza los mismos planes de lubricación del API 682 con la misma designación, pero anteponiéndole un 73 al número del plan, por ejemplo, el plan 11 del API 682 es el plan 7311 en el ASME B73.1.
Existe una variedad importante de planes que contemplan refrigeración del fluido bombeado, eliminación de partículas abrasivas o el uso de fuentes externas de lubricación para los sellos a continuación se hará referencia a los más importantes.
Los planes de lubricación de las caras de los sellos son el plan 01 y el plan 02, los cuales son aplicados en equipos de bajo costo y baja energía (bajo caudal y baja presión) debido a su simplicidad. El plan 01 consiste perforar un agujero para conectar la descarga con la caja de sellos por la parte interna de la carcasa, lo que permite la circulación del fluido desde la descarga a la succión para lubricar las caras de los sellos mecánicos.
La principal precaución que tomar en este plan de lubricación es garantizar que la circulación sea suficiente para retirar el calor generado en el sello. En el plan de lubricación 02 no se tiene prevista la circulación de fluidos, se usa para bombas de baja energía o con chaquetas de enfriamiento sobre la caja de sellos. Lafigura 15-15 muestra el esquema de un plan de lubricación 02.
En el ámbito industrial el plan de lubricación para las caras de los sellos más usado y uno de los mas simples es el plan 11, de hecho, es el plan base del API 682. En este plan de lubricación se toma fluido de la descarga de la bomba mediante el uso de una línea, y se llevan a la caja de sellos para la lubricación de las caras sellantes. El caudal hacia la cara del sello es controlado, mediante una placa orificio, con la finalidad de evitar el exceso de velocidad del fluido que esta entrando a la cámara del sello y que podría erocionar las caras de los sellos.

Fuente: www.polyflon.com
Este plan de lubricación tiene la ventaja de mantener un flujo positivo en el interior de la caja de sellos. Es aplicable a fluidos a temperatura moderada y que no tengan contaminantes, abrasivos o tendencia cristalizarse, debido a que el orifico de la placa tiende a obstruirse. La figura N° 15-16 muestra el diagrama de un arreglo de lubricación para sellos mecánicos basado en el plan 11.

Fuente: Flowserve_Mechanical seal piping plans_Flowserve Solutions Divition
El plan 11 de lubricación para sellos mecánicos del API 610/ISO 13709, soluciona una serie de problemas de sellado que se presentan en el ámbito de las aplicaciones industriales. Sin embargo, existen otras variantes del plan 11 que agrega valor en otras situaciones, por ejemplo, el plan 12, es el mismo plan 11 pero al cual se le agrega un colador en Y a la línea de alimentación del sello mecánico, inmediatamente antes de la placa orificio, con la finalidad de manejar líquidos con algo de contaminación. Si a este mismo plan 12 se adiciona un intercambiador de calor, para bajar la temperatura del líquido que se usará como lubricante de las caras tenemos un plan 22.
Un plan de lubricación para los sellos usado con bastante frecuencia en la Industria Petrolera es el plan 31. Este plan de lubricación es un plan 11 donde se le retira el orificio de restricción y se agrega un ciclón para remover las partículas suspendidas en el fluido, las partículas removidas con el ciclón son enviadas a la succión de la bomba. Esta solución se aplica con la finalidad de retirar los sólidos suspendidos en el fluido de procesos antes de que entren en la cámara de sellado. El principal problema de este plan de lubricación es el ciclón que se satura si el volumen de sólidos es muy alto o es ineficaz si la Gravedad Específica de los sólidos no es al menos dos veces la Gravedad Específica del fluido de procesos.
El API 682 establece en la sección 8.5.1 “Cyclon separador” que las dos condiciones básicas para que los ciclones de separación trabajen eficientemente a pesar de existir otras variables como son el tamaño de las partículas, es que la presión diferencial sea de al menos 1,7 bar (25 psi) y que los sólidos que se quieran remover tengan al menos el doble de la densidad del fluido. La figura N° 15-17 muestra el esquema de una bomba con un plan de lubricación 31.

Fuente: Flowserve_Mechanical seal piping plans_Flowserve Solutions Divition
Otro plan de lubricación importante es el plan 32 que consiste en la inyección de un líquido limpio en la cámara de sellado desde una fuente externa. Se usa cuando el fluido de procesos está sucio o contaminado, posee partículas en suspensión, en el caso de fluidos de procesos a altas temperaturas, para aumentar la presión en la caja de sellado y evitar la vaporización, cuando los fluidos tienen alta presión de vapor (HVP) o se trabaja a altas temperaturas. También se usan cuando los fluidos se polimerizan, se degeneran por oxidación o tienen malas propiedades para la lubricación.
Los principales cuidados y problemas observados en este plan es que el fluido de la fuente externa debe ser compatible con el fluido bombeado, la fuente de suministros del fluido externo debe ser confiable y con la suficiente robustez para mantener el caudal necesario para la lubricación del sello.
La presión de suministro y el caudal del fluido suministrado son medidos mediante un rotámetro y un manómetro instalado en el sistema. Los fluidos externos usado en la Industria Petrolera son mezclas de Glicol y agua o aceites lubricantes ligeros. La figura N° 15-18 presenta el diagrama de un sello mecánico lubricado con un plan 32 indicando los principales componentes de este arreglo.

Fuente: Flowserve_Mechanical seal piping plans_Flowserve Solutions Divition
Con el auge de la preservación del ambiente se han ampliado los planes de lubricación ecológicos donde el fluido no debe tener contacto con la atmosfera o donde no son toleradas las emisiones por ser los productos tóxicos o contaminantes uno de estos planes de lubricación es el plan 52 que consiste en un sistema de sello doble, donde en la cámara entre los dos sellos se tiene un fluido de barrera despresurizado que circula, ayudado por un anillo de bombeo, a un recipiente instrumentado con indicadores de nivel, interruptores de nivel alto y bajo y un interruptor de presión.
El plan 52 es ampliamente usado porque no necesita el mantenimiento de una presión en el sistema, allí al fallar el primer sello el fluido de barrera se contamina con el fluido de procesos, lo que hace que suba el nivel del recipiente accionado el interruptor de nivel alto o el de presión. Los recipientes están normalizados en el API 682 deben tener una capacidad mínima de 12 litros (3 galones), y tienen que ser fabricados en acero 316L, deben contar visores de nivel, conexiones para entrada y salida del fluido de barrera, serpentín para enfriamiento con las conexiones para la entrada y la salida del fluido refrigerante, conexiones de drenaje y venteo, así como para la instalación de interruptores de nivel, interruptores de presión e indicadores de presión. La figura 15-19 muestra un sistema con un plan de lubricación 52 y la instrumentación correspondiente.

Fuente: Flowserve_Mechanical seal piping plans_Flowserve Solutions Divition
Cuando se tienen las mismas restricciones ambientales, los fluidos de procesos son inapropiados para lubricar las caras de los sellos y no se cuenta con una fuente externa confiable y a la presión requerida de fluido para la lubricación de las caras de los sellos una alternativa es el plan de lubricación 54 que es un sistema de circulación que suministra un fluido de barrera externo mediante un sistema de bombeo autónomo a un sistema de sellos dobles.
La desventaja de este sistema es el costo del sistema que es relativamente alto a parte de los costos de mantenimiento, también se corre el peligro que ante la falla del sello o los sellos se contamine todo el fluido de barrera contenido en el sistema, además es necesario mantener siempre el sistema energizado. La figura 15-20 muestra el diagrama de un sistema de lubricación para la cara de sellos del tipo plan 54, donde es posible ver la fuente externa de presión y las líneas de circulación.

Fuente: www.polyflon.com
Entre los planes de lubricación más actuales está el plan 72, que es aplicado fundamentalmente cuando se usan en sistemas de sellado no presurizados con sellos dobles en “tandem” que tienen como fluido de barrera gas, el gas es típicamente nitrógeno.
El plan 72 se aplica para sellar fluidos con alta presión de vapor (HVP), para hidrocarburos livianos, fluidos tóxicos o contaminantes. Los cuidados que se deben tener es poseer una fuente de gas confiable, mantener la presión del fluido de barrera al menos 1,75 bar (25 psi) por arriba de la presión de la cámara de sellado. La figura 15-21 muestra el diagrama de un sistema de lubricación para sellos mecánicos plan 72, donde se indican los componentes básicos del sistema.
Lo fundamental para seleccionar el plan de lubricación adecuado a cada servicio es ajustarse a las necesidades reales del proceso, no complicarlo con accesorios excesivos o innecesarios, atender a la disponibilidad de los recursos existentes en la planta y a la filosofía de operación establecida.

Fuente: Flowserve_Mechanical seal piping plans_Flowserve Solutions Divition
Dinos qué te ha parecido el artículo
Artículos recomendados
Enfriadores de sellos

Curso de Mantenimiento de Motores Eléctricos

Introducción a la gestión de inventarios

7.5 Importancia del ACR

Publica tu artículo en la revista #1 de Mantenimiento Industrial
Publicar un artículo en la revista es gratis, no tiene costo.
Solo debes asegurarte que no sea un artículo comercial.
¿Qué esperas?
O envía tu artículo directo: articulos@predictiva21.com
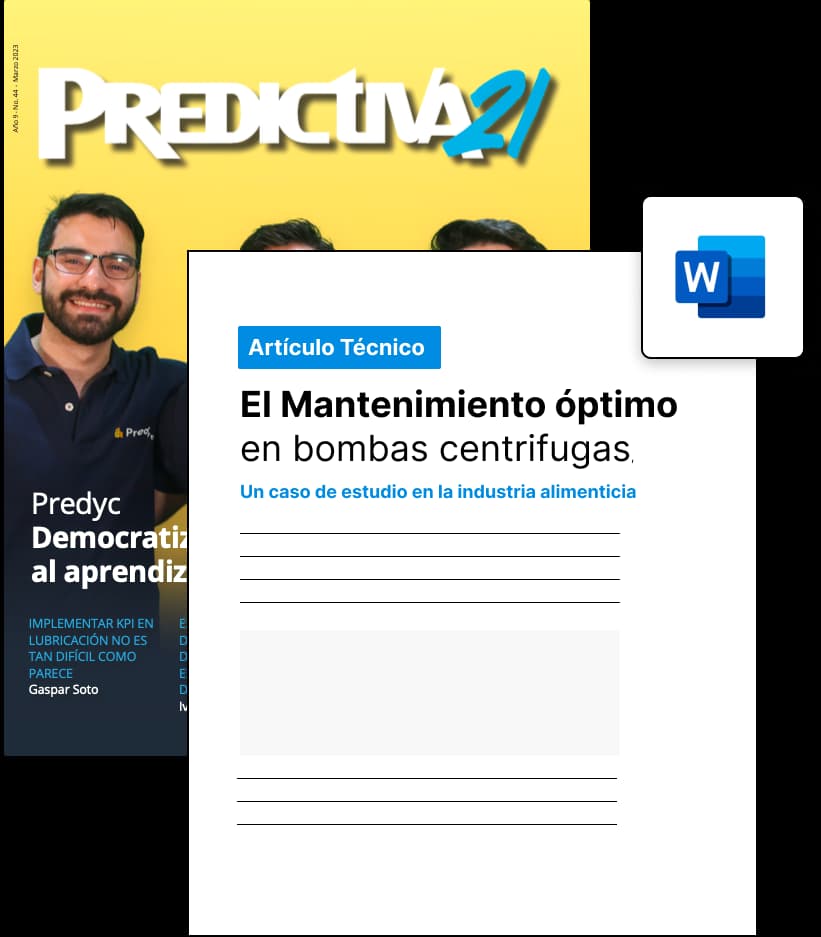