8.14 Supervisión Autónoma
Articulo8 de noviembre de 2021
Durante este paso se espera que los operadores lleven a cabo una supervisión autónoma y sigan los estándares que ellos mismos pusieron. También se espera que se haya logrado el cero accidentes, cero defectos y cero fallas. En otras palabras al alcanzar este paso TPM ya ha sido implementado totalmente en la compañía.
Los operadores mantienen las condiciones básicas del equipo y restauran sus partes deterioradas. Por otro lado el personal de mantenimiento provee de un plan de mantenimiento altamente sofisticado al aplicar mantenimiento preventivo a las máquinas críticas.
Para llegar a este punto se requiere al menos de cinco años, si se toman con cuidado el paso seis para obtener cero defecto probablemente haya que añadirle otros dos años como mínimo. Para lograr TPM se necesita coger un camino largo.
Una vez alcanzado este nivel es necesario mantenerse en él, para ello los operarios deben trabajar en conjunto con los de mantenimiento para seguir los pasos anteriores del programa de desarrollo de TPM.
Los operadores inspeccionan el deterioro del equipo y lo restauran a fin de mantener las condiciones del mismo, mientras tanto mantenimiento utiliza sus habilidades para alcanzar mejores niveles técnicos.
Un problema frecuente al implementar TPM ocurre cuando las personas son reemplazadas, gradualmente los nuevos empiezan a creer que cero defectos, cero fallas y cero accidentes es algo común y empiezan a dejar el plan del TPM, esto mata al sistema de TPM, lo que lleva otra vez al inicio de la campaña.
TPM debe ser enseñado a los miembros nuevos, deben ser entrenados en los conceptos fundamentales de TQM, como limpieza e inspección, mantener las condiciones básicas del equipo, etc.
Una vez que se logran los objetivos del TPM, ¿qué es lo que se debe hacer después? La respuesta está basada en las siguientes dos dimensiones:
Renovaciones poco frecuentes del equipo
Se da típicamente en industrias de proceso como la del petróleo, químico, cemento, etc.
Cada uno de estos procesos produce únicamente un solo tipo de producto. Técnicamente están altamente desarrollados y sus productos tienen una larga vida y pocas esperanzas de cambiar.
En general cuando se construye una planta queda operando así hasta que los costes de mantenimiento son tan altos que es mejor cerrarla, nunca se cambia el equipo (que es altamente caro y especializado), solamente se hacen pequeñas modificaciones o reparaciones nunca por entero porque saldría más caro que poner otra planta en otro lugar.
En estos casos el mantenimiento sale caro porque existen pocas personas trabajando en la planta, TPM puede hacer poco aquí prácticamente se limita a reducir costes de mantenimiento.
Renovaciones frecuentes del equipo
Se encuentra típicamente en industrias de ensamblaje como la automotriz, electrónica, etc. El cambio tan variante en el gusto de los consumidores hace que los productos tengan un ciclo de vida muy corto. Se necesitan cambios muy rápidos y drásticos, aunado a innovaciones para ayudar a la tecnología, aunque la automatización progresa bastante rápido todavía persiste el trabajo manual en el piso.
¿Qué se debe hacer después de TPM?
Todavía no existe una segunda generación de TPM, las compañías que alcanzan la etapa final implantan una automatización de la planta. La nueva generación de TPM no debe enfocarse únicamente al equipo, debe enfocarse también a la información.
Dinos qué te ha parecido el artículo
Artículos recomendados
Aplicación de un Análisis RAM en un Sistema de Bombeo de Agua Cruda - Caso Estudio

Ingeniería de confiabilidad: sus campos de trabajo

Hablemos de RAM

María Anna Amerio, Presidente de FUNINDES USB

Publica tu artículo en la revista #1 de Mantenimiento Industrial
Publicar un artículo en la revista es gratis, no tiene costo.
Solo debes asegurarte que no sea un artículo comercial.
¿Qué esperas?
O envía tu artículo directo: articulos@predictiva21.com
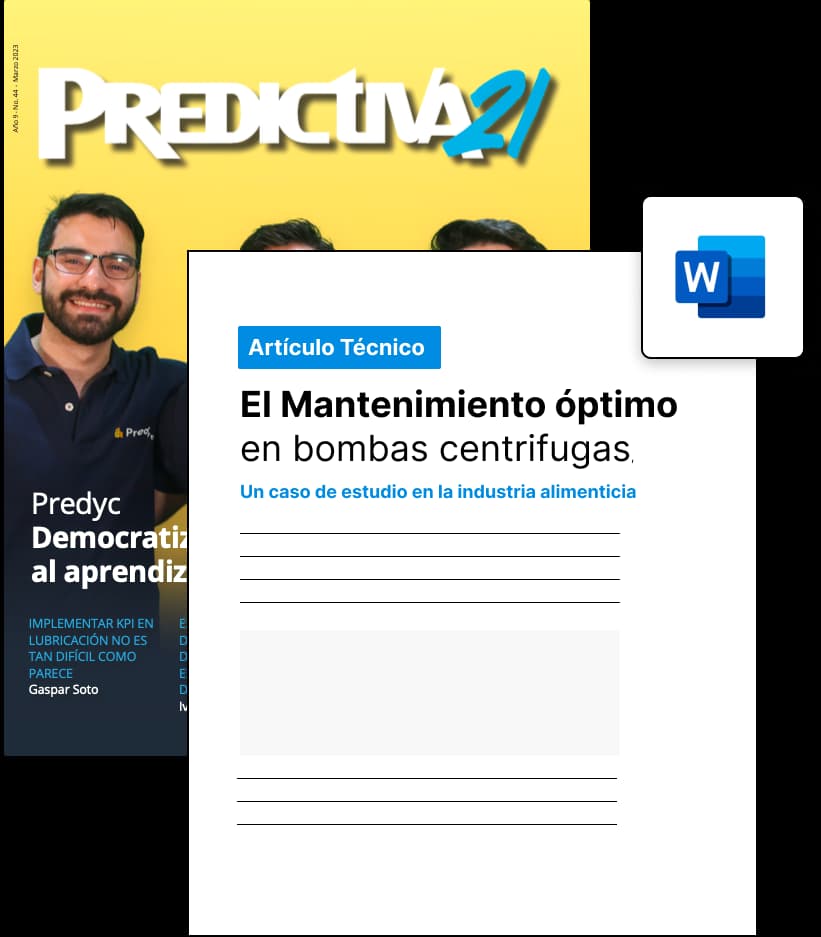
8.14 Supervisión Autónoma
Articulo 8 de noviembre de 2021Durante este paso se espera que los operadores lleven a cabo una supervisión autónoma y sigan los estándares que ellos mismos pusieron. También se espera que se haya logrado el cero accidentes, cero defectos y cero fallas. En otras palabras al alcanzar este paso TPM ya ha sido implementado totalmente en la compañía.
Los operadores mantienen las condiciones básicas del equipo y restauran sus partes deterioradas. Por otro lado el personal de mantenimiento provee de un plan de mantenimiento altamente sofisticado al aplicar mantenimiento preventivo a las máquinas críticas.
Para llegar a este punto se requiere al menos de cinco años, si se toman con cuidado el paso seis para obtener cero defecto probablemente haya que añadirle otros dos años como mínimo. Para lograr TPM se necesita coger un camino largo.
Una vez alcanzado este nivel es necesario mantenerse en él, para ello los operarios deben trabajar en conjunto con los de mantenimiento para seguir los pasos anteriores del programa de desarrollo de TPM.
Los operadores inspeccionan el deterioro del equipo y lo restauran a fin de mantener las condiciones del mismo, mientras tanto mantenimiento utiliza sus habilidades para alcanzar mejores niveles técnicos.
Un problema frecuente al implementar TPM ocurre cuando las personas son reemplazadas, gradualmente los nuevos empiezan a creer que cero defectos, cero fallas y cero accidentes es algo común y empiezan a dejar el plan del TPM, esto mata al sistema de TPM, lo que lleva otra vez al inicio de la campaña.
TPM debe ser enseñado a los miembros nuevos, deben ser entrenados en los conceptos fundamentales de TQM, como limpieza e inspección, mantener las condiciones básicas del equipo, etc.
Una vez que se logran los objetivos del TPM, ¿qué es lo que se debe hacer después? La respuesta está basada en las siguientes dos dimensiones:
Renovaciones poco frecuentes del equipo
Se da típicamente en industrias de proceso como la del petróleo, químico, cemento, etc.
Cada uno de estos procesos produce únicamente un solo tipo de producto. Técnicamente están altamente desarrollados y sus productos tienen una larga vida y pocas esperanzas de cambiar.
En general cuando se construye una planta queda operando así hasta que los costes de mantenimiento son tan altos que es mejor cerrarla, nunca se cambia el equipo (que es altamente caro y especializado), solamente se hacen pequeñas modificaciones o reparaciones nunca por entero porque saldría más caro que poner otra planta en otro lugar.
En estos casos el mantenimiento sale caro porque existen pocas personas trabajando en la planta, TPM puede hacer poco aquí prácticamente se limita a reducir costes de mantenimiento.
Renovaciones frecuentes del equipo
Se encuentra típicamente en industrias de ensamblaje como la automotriz, electrónica, etc. El cambio tan variante en el gusto de los consumidores hace que los productos tengan un ciclo de vida muy corto. Se necesitan cambios muy rápidos y drásticos, aunado a innovaciones para ayudar a la tecnología, aunque la automatización progresa bastante rápido todavía persiste el trabajo manual en el piso.
¿Qué se debe hacer después de TPM?
Todavía no existe una segunda generación de TPM, las compañías que alcanzan la etapa final implantan una automatización de la planta. La nueva generación de TPM no debe enfocarse únicamente al equipo, debe enfocarse también a la información.
Dinos qué te ha parecido el artículo
Artículos recomendados
Perfilaje Gamma de Columnas de Fraccionamiento: Herramienta Preventiva de Excelencia

Stress, Distress, Burn Out y los Errores Humanos

Experiencias en el desarrollo de Análisis de Confiabilidad, Disponibilidad y Mantenibilidad (Análisis RAM).

Gestión Tribológica de Activos®: Su ejecución y medición a través del Índice Techgnosis (ITG®)

Publica tu artículo en la revista #1 de Mantenimiento Industrial
Publicar un artículo en la revista es gratis, no tiene costo.
Solo debes asegurarte que no sea un artículo comercial.
¿Qué esperas?
O envía tu artículo directo: articulos@predictiva21.com
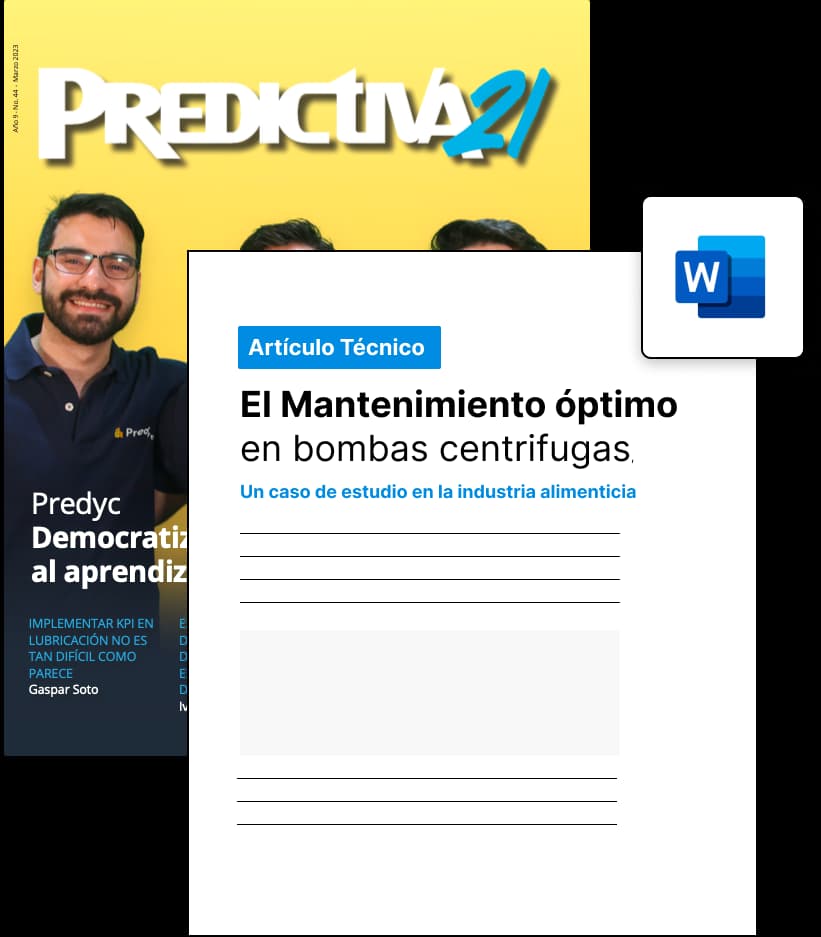