8.5. Mantenimiento Estratégico Visto bajo el Foco de la Necesidad
Libros31 de agosto de 2020
Se ha de analizar la relación entre el acompañamiento de la disponibilidad "versus" la necesidad de utilización de equipos, presentada en la Figura 71, donde fueron obtenidos los respectivos índices de "disponibilidad" y "necesidad de utilización".

En la mayoría de los equipos, el índice de disponibilidad es superior al de la necesidad de utilización de cada uno. En el caso de que los elevados índices de disponibilidad estén siendo obtenidos a expensas de altas inversiones de recursos humanos y en caso la confiabilidad operativa del equipo no sea crítica, deben ser efectuadas nuevas re evaluaciones respecto a los criterios de mantenimiento utilizados.
Se observa que, en este caso, las Bombas de Proceso 1 y 2, presentaron disponibilidad menor que la necesitada, siendo éste el punto prioritario de análisis y acción de reajuste del Sistema de Planificación, que también deberá considerar su importancia operacional en el proceso, los costos de reparación y los tiempos medios entre fallas y reparación.
El análisis indicado para los equipos, también puede ser aplicado a componentes o piezas, siendo esta utilización correcta para evaluar que partes de un equipo, obra o instalación deben merecer mayor atención por parte de los responsables del mantenimiento y en que parte se puede aplicar simplemente el mantenimiento preventivo por condición (reparación de defecto) o correctivo.
Veamos un ejemplo:
¿Si una flota de camiones es utilizada solamente durante el día, cuál sería la necesidad de efectuar un mantenimiento planificado en el sistema de iluminación de los mismos (faros, luces de la cabina etc.)?
Obviamente que estas partes del equipo, podrían ser objeto de un simple mantenimiento correctivo siendo, inclusive, recomendable que el cambio de lámparas quemadas fuese efectuada por el propio operador del equipo.
La evaluación de los criterios de mantenimiento a ser aplicados, depende normalmente del análisis de disponibilidad frente a la necesidad de utilización del equipo, no obstante se deben observar otros aspectos, como: su importancia en la actividad objeto de la empresa, el costo de mantenimiento con relación al inmovilizado (costo acumulado de mantenimiento con relación al costo de adquisición del equipo), el tiempo medio entre fallas, el tiempo medio para reparación, la obsolescencia del equipo, las condiciones de operación a que son sometidos, los aspectos de seguridad y los aspectos de medio ambiente.
Considerando un conjunto de ítems (equipos, obras o instalaciones) fundamentales en una línea de proceso o servicio, donde sus mayores disponibilidades tienen relación homogénea con mayor productividad y consecuente producción de utilidades para la empresa, en la evaluación de los puntos críticos pueden ser encontradas las siguientes condiciones:
Ítems en serie - La disponibilidad final será obtenida por el producto de las disponibilidades de cada ítem.

Ítems en paralelo - La disponibilidad final, será obtenida por la suma de los productos de las disponibilidades de cada ítem por sus capacidades de producción, dividido por el producto de las capacidades de producción de esos ítems.

Ítems redundantes - La disponibilidad final, será obtenida por la diferencia entre la unidad y los productos de la diferencia de la unidad con la disponibilidad de cada ítem.

Obviamente, la disponibilidad final de un sistema mixto de ítems, será el resultado de la conversión a un sistema simple (serie) y posteriormente la búsqueda del elemento que esté contribuyendo para el peor valor - Figura 72
De esta forma, deberán ser analizadas las estructuras del Sistema Productivo, a través de sus sectores serie, paralelo, redundante y mixto, calculando en función de las disponibilidades individuales, su disponibilidad total.
La mejor productividad final del sistema, quedará limitada por su peor máquina, como en el ejemplo presentado: por la máquina 2 y aunque se obtenga el máximo de productividad en el resto de los equipos el resultado continua comprometido por ella.
Esta determinación es de gran importancia, para permitir la adecuada prioridad y definición de estrategias, de manera que se evite el riesgo de obtener "10% más de eficiencia en el equipo equivocado".

Con este análisis, dos caminos deben ser adoptados. Armonizar los resultados de todos los ítems, en relación al que presenta el peor desempeño (solución económica) y, a continuación, tratar de aumentar la disponibilidad de todos de forma uniforme para obtener mayor productividad del conjunto (solución estratégica).
Una vez que el mantenimiento estratégico (o "mantenimiento centrado en el riesgo" o "mantenimiento orientado al negocio") es una ruptura de paradigma, pues pasa a enfocar las acciones en el aspecto "Sistemático" y no más por equipo individual, el primer paso es determinar cual es el equipo que está creando las retenciones en el proceso, o sea, ¿cual es el que se convierte en "cuello de botella" del proceso o servicio?
Determinados los "cuellos de botella", deben ser examinados los reflejos en la disponibilidad final en las siguientes condiciones:
- 1) Aumento de disponibilidad en el ítem que se constituye en el mayor "cuello de botella" del Sistema y/o
- 2) Examen de la posibilidad de transferir, para otro sector productivo, la capacidad operacional reduciendo aquel donde se encuentra el "cuello de botella".
En conclusión, utilizando el árbol de decisiones, se deberán comparar los datos de disponibilidad y capacidad con valores de otros índices y variables como:
- tiempo medio entre falla (TMEF);
- tiempo medio para reparaciones (TMPR);
- costo relativo de reparación;
- antigüedad del equipo;
- responsable por el mantenimiento;
- condición insegura de operación;
- riesgo al medio ambiente;
- rentabilidad operacional, etc...
… para definir el tipo de estrategia de intervención a ser adoptada.
Como alternativa para el establecimiento del tipo de intervención a ser adoptada, pueden ser utilizados símbolos o señales gráficas para indicar la condición favorable, indiferente o desfavorable de satisfacción a las necesidades operativas del ítem, como por ejemplo: "flecha para arriba", flecha para abajo" o "flecha para la derecha"; señales de "+", "-" o "±"; "cara alegre", "cara triste" o "cara indiferente" etc.
La combinación de estas características o símbolos, determinará la mejor estrategia de actuación en cada caso, pudiendo todavía, ser establecidos "valores" para cada una de las variables para indicar su mejor o peor importancia, en lo que se refiere a decisiones a ser tomadas, utilizando para tanto, la experiencia de cada uno de los involucrados en el proceso.
Esta versión del mantenimiento para el próximo siglo, es muy interesante en el aspecto de reducción de costos y, por ser un enfoque nuevo, podrá recibir muchas contribuciones, lo que la caracteriza como "una visión de futuro".
Autor: Lourival Augusto Tavares
Brasil
Consultor en Ingeniería de Mantenimiento
Empresa: Director nacional de ABRAMAN (Asociación Brasileña de Mantenimiento) en dos mandatos.
Correo: l.tavares@mandic.com.br
Ingeniero Electricista, formado por la Escuela Federal de Ingeniería de Rio de Janeiro, en el año de 1967. Past-Presidente del Comité Panamericano de Ingeniería de Mantenimiento. Supervisor de Mantenimiento en FURNAS – Centrales Eléctricas S.A. durante 23 años. Fue el jefe de la Asesoría Técnica de Apoyo en ITAIPU Binacional. Reconocido como “notorio saber” en mantenimiento por la Universidad Federal de Rio de Janeiro y por la Universidad Federal de Paraíba.
Dinos qué te ha parecido el artículo
Artículos recomendados
Confiabilidad y Riesgo: una perspectiva bayesiana

6.1.- Como se Determina el NPSHA

Evaluación de riesgos: Teoría, métodos y aplicaciones

1.1. La evolución organizacional del mantenimiento

Publica tu artículo en la revista #1 de Mantenimiento Industrial
Publicar un artículo en la revista es gratis, no tiene costo.
Solo debes asegurarte que no sea un artículo comercial.
¿Qué esperas?
O envía tu artículo directo: articulos@predictiva21.com
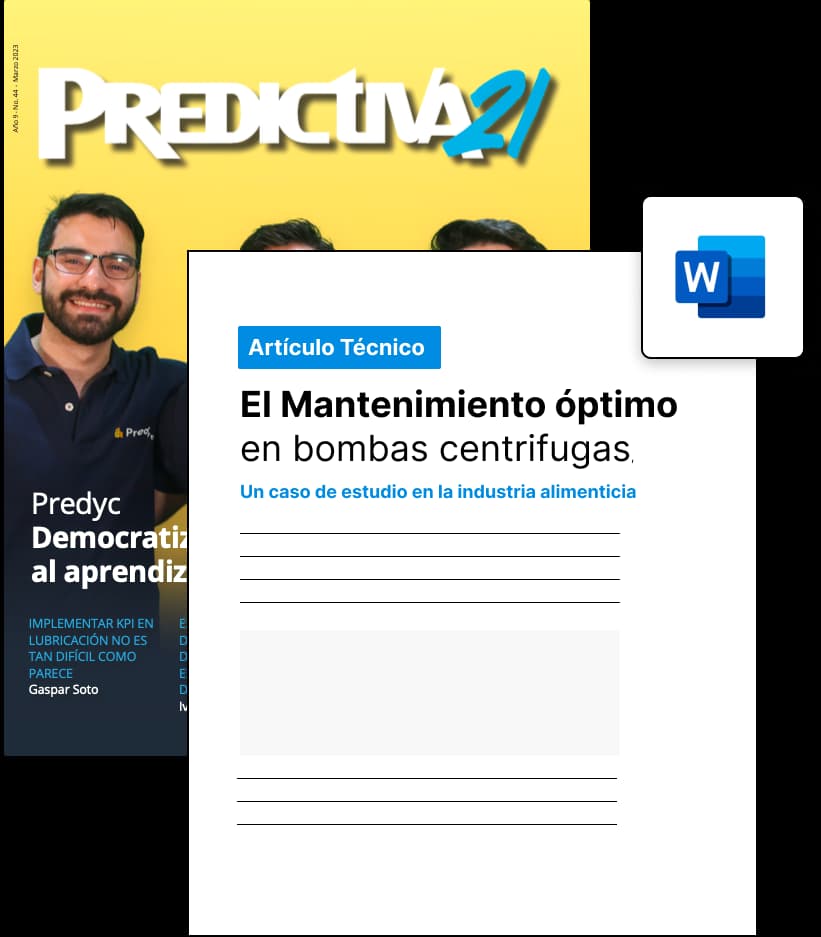
8.5. Mantenimiento Estratégico Visto bajo el Foco de la Necesidad
Libros 31 de agosto de 2020Se ha de analizar la relación entre el acompañamiento de la disponibilidad "versus" la necesidad de utilización de equipos, presentada en la Figura 71, donde fueron obtenidos los respectivos índices de "disponibilidad" y "necesidad de utilización".

En la mayoría de los equipos, el índice de disponibilidad es superior al de la necesidad de utilización de cada uno. En el caso de que los elevados índices de disponibilidad estén siendo obtenidos a expensas de altas inversiones de recursos humanos y en caso la confiabilidad operativa del equipo no sea crítica, deben ser efectuadas nuevas re evaluaciones respecto a los criterios de mantenimiento utilizados.
Se observa que, en este caso, las Bombas de Proceso 1 y 2, presentaron disponibilidad menor que la necesitada, siendo éste el punto prioritario de análisis y acción de reajuste del Sistema de Planificación, que también deberá considerar su importancia operacional en el proceso, los costos de reparación y los tiempos medios entre fallas y reparación.
El análisis indicado para los equipos, también puede ser aplicado a componentes o piezas, siendo esta utilización correcta para evaluar que partes de un equipo, obra o instalación deben merecer mayor atención por parte de los responsables del mantenimiento y en que parte se puede aplicar simplemente el mantenimiento preventivo por condición (reparación de defecto) o correctivo.
Veamos un ejemplo:
¿Si una flota de camiones es utilizada solamente durante el día, cuál sería la necesidad de efectuar un mantenimiento planificado en el sistema de iluminación de los mismos (faros, luces de la cabina etc.)?
Obviamente que estas partes del equipo, podrían ser objeto de un simple mantenimiento correctivo siendo, inclusive, recomendable que el cambio de lámparas quemadas fuese efectuada por el propio operador del equipo.
La evaluación de los criterios de mantenimiento a ser aplicados, depende normalmente del análisis de disponibilidad frente a la necesidad de utilización del equipo, no obstante se deben observar otros aspectos, como: su importancia en la actividad objeto de la empresa, el costo de mantenimiento con relación al inmovilizado (costo acumulado de mantenimiento con relación al costo de adquisición del equipo), el tiempo medio entre fallas, el tiempo medio para reparación, la obsolescencia del equipo, las condiciones de operación a que son sometidos, los aspectos de seguridad y los aspectos de medio ambiente.
Considerando un conjunto de ítems (equipos, obras o instalaciones) fundamentales en una línea de proceso o servicio, donde sus mayores disponibilidades tienen relación homogénea con mayor productividad y consecuente producción de utilidades para la empresa, en la evaluación de los puntos críticos pueden ser encontradas las siguientes condiciones:
Ítems en serie - La disponibilidad final será obtenida por el producto de las disponibilidades de cada ítem.

Ítems en paralelo - La disponibilidad final, será obtenida por la suma de los productos de las disponibilidades de cada ítem por sus capacidades de producción, dividido por el producto de las capacidades de producción de esos ítems.

Ítems redundantes - La disponibilidad final, será obtenida por la diferencia entre la unidad y los productos de la diferencia de la unidad con la disponibilidad de cada ítem.

Obviamente, la disponibilidad final de un sistema mixto de ítems, será el resultado de la conversión a un sistema simple (serie) y posteriormente la búsqueda del elemento que esté contribuyendo para el peor valor - Figura 72
De esta forma, deberán ser analizadas las estructuras del Sistema Productivo, a través de sus sectores serie, paralelo, redundante y mixto, calculando en función de las disponibilidades individuales, su disponibilidad total.
La mejor productividad final del sistema, quedará limitada por su peor máquina, como en el ejemplo presentado: por la máquina 2 y aunque se obtenga el máximo de productividad en el resto de los equipos el resultado continua comprometido por ella.
Esta determinación es de gran importancia, para permitir la adecuada prioridad y definición de estrategias, de manera que se evite el riesgo de obtener "10% más de eficiencia en el equipo equivocado".

Con este análisis, dos caminos deben ser adoptados. Armonizar los resultados de todos los ítems, en relación al que presenta el peor desempeño (solución económica) y, a continuación, tratar de aumentar la disponibilidad de todos de forma uniforme para obtener mayor productividad del conjunto (solución estratégica).
Una vez que el mantenimiento estratégico (o "mantenimiento centrado en el riesgo" o "mantenimiento orientado al negocio") es una ruptura de paradigma, pues pasa a enfocar las acciones en el aspecto "Sistemático" y no más por equipo individual, el primer paso es determinar cual es el equipo que está creando las retenciones en el proceso, o sea, ¿cual es el que se convierte en "cuello de botella" del proceso o servicio?
Determinados los "cuellos de botella", deben ser examinados los reflejos en la disponibilidad final en las siguientes condiciones:
- 1) Aumento de disponibilidad en el ítem que se constituye en el mayor "cuello de botella" del Sistema y/o
- 2) Examen de la posibilidad de transferir, para otro sector productivo, la capacidad operacional reduciendo aquel donde se encuentra el "cuello de botella".
En conclusión, utilizando el árbol de decisiones, se deberán comparar los datos de disponibilidad y capacidad con valores de otros índices y variables como:
- tiempo medio entre falla (TMEF);
- tiempo medio para reparaciones (TMPR);
- costo relativo de reparación;
- antigüedad del equipo;
- responsable por el mantenimiento;
- condición insegura de operación;
- riesgo al medio ambiente;
- rentabilidad operacional, etc...
… para definir el tipo de estrategia de intervención a ser adoptada.
Como alternativa para el establecimiento del tipo de intervención a ser adoptada, pueden ser utilizados símbolos o señales gráficas para indicar la condición favorable, indiferente o desfavorable de satisfacción a las necesidades operativas del ítem, como por ejemplo: "flecha para arriba", flecha para abajo" o "flecha para la derecha"; señales de "+", "-" o "±"; "cara alegre", "cara triste" o "cara indiferente" etc.
La combinación de estas características o símbolos, determinará la mejor estrategia de actuación en cada caso, pudiendo todavía, ser establecidos "valores" para cada una de las variables para indicar su mejor o peor importancia, en lo que se refiere a decisiones a ser tomadas, utilizando para tanto, la experiencia de cada uno de los involucrados en el proceso.
Esta versión del mantenimiento para el próximo siglo, es muy interesante en el aspecto de reducción de costos y, por ser un enfoque nuevo, podrá recibir muchas contribuciones, lo que la caracteriza como "una visión de futuro".
Autor: Lourival Augusto Tavares
Brasil
Consultor en Ingeniería de Mantenimiento
Empresa: Director nacional de ABRAMAN (Asociación Brasileña de Mantenimiento) en dos mandatos.
Correo: l.tavares@mandic.com.br
Ingeniero Electricista, formado por la Escuela Federal de Ingeniería de Rio de Janeiro, en el año de 1967. Past-Presidente del Comité Panamericano de Ingeniería de Mantenimiento. Supervisor de Mantenimiento en FURNAS – Centrales Eléctricas S.A. durante 23 años. Fue el jefe de la Asesoría Técnica de Apoyo en ITAIPU Binacional. Reconocido como “notorio saber” en mantenimiento por la Universidad Federal de Rio de Janeiro y por la Universidad Federal de Paraíba.
Dinos qué te ha parecido el artículo
Artículos recomendados
Teoría de la Confiabilidad del Sistema: modelos, métodos estadísticos y aplicaciones

Índice

Diagnóstico de fallos y control sostenible de aerogeneradores: Estrategias robustas basadas en datos y en modelos

Guía del estudiante sobre estadísticas bayesianas

Publica tu artículo en la revista #1 de Mantenimiento Industrial
Publicar un artículo en la revista es gratis, no tiene costo.
Solo debes asegurarte que no sea un artículo comercial.
¿Qué esperas?
O envía tu artículo directo: articulos@predictiva21.com
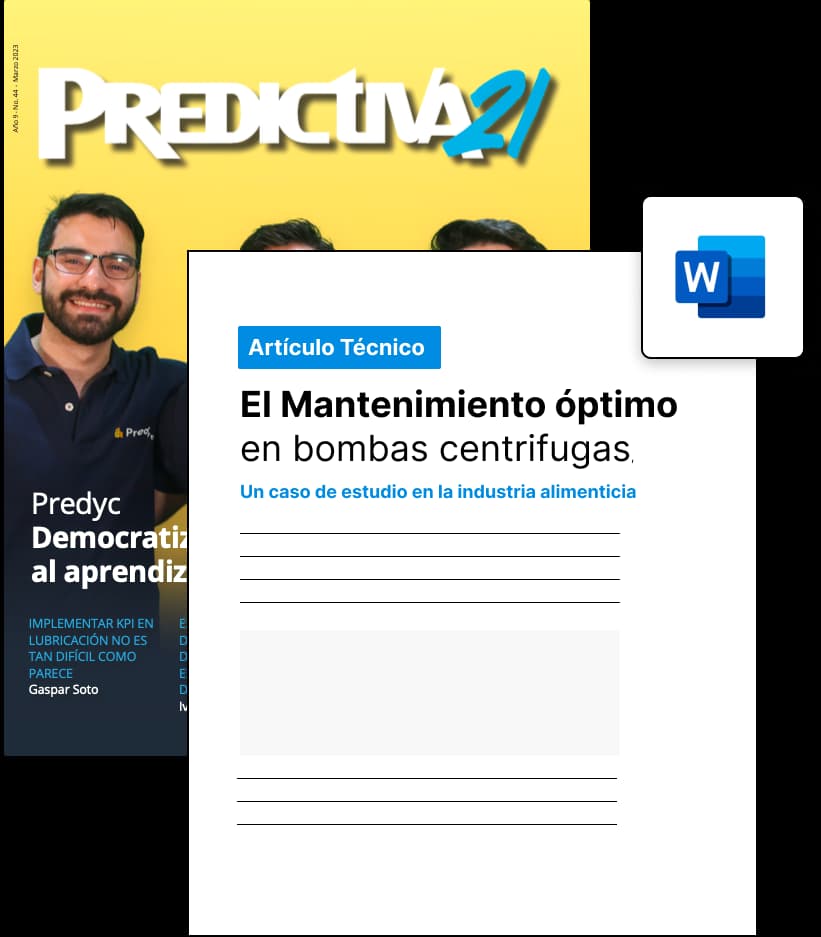