Argenis Mindiola: El Mantenimiento Predictivo es el Arte del Mantenimiento
Entrevista4 de mayo de 2020
Este comprometido ingeniero, con largos años de experiencia en el campo del mantenimiento, habla con sencillez de su gran pasión por el mantenimiento predictivo, y la importancia de legar estos conocimientos a la generación de relevo.
El predictivo es el arte del mantenimiento, es lo más refinado que existe en esa área.
A. Mindiola
Diagnosticar, inspeccionar, predecir y favorecer la productividad parecen ser máximas asociadas al mantenimiento predictivo, una de las ramas más comprometidas dentro de la ingeniería de mantenimiento. Escuchar a un experto como Argenis Mindiola hablar de sus inicios y de la pasión que le imprime a su trabajo, es tan placentero como inspirador. Luego de tres décadas laborando para varias filiales nacionales, Mindiola no contempla el retiro como una opción, sino como la oportunidad de seguir desarrollando su pasión por el mantenimiento, enmarcada en su teoría Running Spare o capacidad rodante, en la cual trabaja desde el año 2004, y que contempla los aspectos teóricos, de diseño y selección de esquemas de compresión que no queman gas dentro del sistema de compresión.
Comenzamos la entrevista con las evocadoras frases de Argenis, quien se remonta en el tiempo para hacer un breve esbozo de lo que ha sido su prolífica vida profesional. Comenzó en la antigua filial nacional petrolera Maraven, balanceando pequeños rotores a escala, ejercicio apasionante y a la vez metódico, que decidiría, a no dudar, el rumbo de su carrera. Corría el año 1981, y el otrora joven ingeniero, que trabajaba de día en el Lago de Maracaibo, permanecía hasta altas horas de la noche, intentando develar los secretos del balanceo a escala. Y un día, la oportunidad apareció, bajo la forma de problema, como suele suceder. “Un amigo y colega me comentó que tenían un problema con cierta maquinaria desde hacía varios meses. Le pedí mirar la cinta de datos, y le dije que tenían un problema de balanceo, lo cual suponía varios meses de diagnóstico errado. Fue toda una sorpresa. Así que me asignaron arreglar el equipo. Era una turbina con un generador eléctrico, y logré que mis superiores confiaran en mí lo suficiente como para asumir este importante reto. Nos comprometimos a fondo con este proyecto, y logramos arreglar el equipo, que además era muy sofisticado y delicado para la época” –relata Mindiola. Obviamente, fue todo un éxito. Para esa época la revista de Maraven registró el hecho, y obtuvo reconocido mérito entre sus colegas, lo cual marcó para nuestro entrevistado el inicio de una brillante y fructífera etapa profesional. Este primer trabajo marcó el inicio de otros proyectos a cargo de Equipos Rotativos, que asumieron trabajos en otras filiales nacionales e interfiliales, con el consecutivo aumento de la confianza y las responsabilidades.
Predictiva21: Luego de esta primera etapa, en la cual usted y su equipo se encargan de resolver el problema de un equipo rotativo de alta factura, ¿qué siguió?
Argenis Mindiola: Lo interesante de este primer trabajo y los que le siguieron fue que logramos sentar bases importantes en el área de equipos rotativos, bases sobre las que después se apoyaron otros colegas y otros proyectos. A mi despedida de la parte de inspección de equipos rotativos, me asignaron como superintendente de taller central de Turbomáquinas de Maraven.
P21: Parte de este hacer ¿Quedó registrado?
AM: Sí, como no. Para esa época escribí un libro, basado en todas estas experiencias y aprendizajes. El libro se llama Análisis de Vibraciones Nivel Avanzado, editado por Maraven, y es ahora un libro de consulta para muchos analistas. Yo soy un fiel convencido de que el conocimiento ha de fluir, expandirse, crecer, y tocar a todos, de eso depende el avance de la civilización.
P21: ¿Cómo fue la reacción de la empresa, luego de estos logros?
AM: Este interés constante en el mantenimiento nos permitió fundar el Departamento de Mantenimiento Predictivo, que para la época era una novedad. Corrían los años ochenta, y la filial petrolera puso a todo a nuestra disposición, en favor del desarrollo del mantenimiento predictivo. Nos concedieron equipos muy de avanzada para ese tiempo: analizadores de espectro, todo tipo de equipos para diagnóstico, alineación láser, teníamos la tecnología de punta, y aprendimos a hacer un diagnóstico más profundo. Colectamos firmas de los equipos, hacíamos análisis de frecuencia y con eso determinábamos qué componente podía fallar. Ese aprendizaje del diagnóstico hizo que nos apodaran los brujos. Pero no era brujería, claro, era diagnóstico.
P21: ¿Qué otros aportes recuerda de esa época?
AM: Existen tres tipos de mantenimiento: correctivo por avería, preventivo y necesario, se maneja en platas nucleares, y luego viene la etapa avanzada, que es el predictivo. No sustituye al preventivo, sino que optimiza. En atención a esto, propusimos hacer, por primera vez, una parada de equipo en sincronía con una parada de planta, de forma conjunta con el mantenimiento de pozos y toda la estructura asociada, es decir, hacer todos los mantenimientos basados en el predictivo. Fue muy novedoso, y al principio lucía muy arriesgado. Pero logramos vender la idea, pudimos hacer una planificación macro que incluyó mantenimiento de pozos, de estaciones de recolección de flujo, mantenimiento de plantas de gas y mantenimiento de líneas, toda sincronizada con una sola parada, basados en el predictivo. Fue un éxito, porque bajamos los tiempos de parada, unos 20 días, reduciéndolos a un tercio, lo cual se tradujo en producción. Ese fue uno de nuestros grandes éxitos.
P21: ¿Cómo prosiguió su desarrollo profesional? ¿Qué rumbo tomó su investigación?
AM: Me gusta mucho la matemática, los cálculos y las ecuaciones. Entonces hice un programa de predicción de parámetros operacionales, bajo el nombre Pronóstico de Comportamiento de equipos basado en modelos estadísticos y ecuaciones matemáticas. Enamorado del predictivo como estaba, decidí diseñar esta herramienta, con la ayuda de un amigo y colega matemático. Para la primera parte de la investigación, tomé un valor de temperatura de un equipo rotativo, y me dediqué a registrar sus cambios, y los tiempos en los cuales ocurrían las variaciones. Luego determiné el patrón matemático que regía ese comportamiento (por ejemplo, el valor de la curva), y así empecé a hacer el modelo. Como paso posterior, extrapolé estos datos de variaciones a un modelo matemático, basándome en método de ajuste de curvas por mínimos cuadrados, y esta fue la base para diseñar todo mi sistema de ecuaciones. Combiné todos los datos de una máquina seleccionada para determinar puntos de inflexión, parámetros de comportamiento y luego ofrecer un diagnóstico presente, y uno predictivo a futuro. Fue una etapa muy prematura de inteligencia artificial, y sin lugar a dudas muy exitoso.
Otros rumbos, la misma pasión
Mindiola relata que luego de esa época pasó a ser Jefe de Talleres de Turbomáquinas, en una etapa de gran importancia, porque marcó el inicio de las reparaciones de turbinas dentro del territorio venezolano. Posteriormente, estudió en California, Estados Unidos, para certificarse como reparador de Turbinas Allison. Luego regresó al país, para dedicarse a la fabricación de los sellos laberinto, los primeros de manufactura nacional. Los sellos laberinto constituían en esa época un aspecto crítico en el mantenimiento de compresores. Al lograr hacerlos en el país significó un gran paso, elaborándose incluso un manual de procedimiento para la fabricación de estos, lo cual allanó el camino para procesos futuros.
Para el año 2004, Argenis Mindiola se sentía tan comprometido con el mantenimiento predictivo como a comienzos de su muy exitosa carrera. Ese año se dedicó a formular la teoría Running Spare o capacidad rodante. En el sistema de compresión, esta teoría contempla los aspectos teóricos, de diseño y selección de esquemas de compresión que no queman gas. Luego de muchos cálculos y pruebas, Mindiola se reunió con los jefes de ingeniería de diseño de varias marcas afamadas como Solar Turbine, Siemmens, Nuovo Pignone, GE y Dresser Rand, ante quienes expuso su teoría. Según esta propuesta, si existe una batería de equipos laborando a un determinado nivel de eficiencia y carga determinada, y uno de ellos falla, los demás equipos deben tener la capacidad de asumir la carga del equipo en cuestión, sin que esto implique afectaciones, como la quema de gas o el cierre de la producción. En los últimos años, Mindiola ha laborado en PDVSA Holanda, a donde fue como gerente técnico y luego pasó a encargarse de otras gerencias. Ahora, próximo a jubilarse, Mindiola espera poder enfocarse en el desarrollo de esta teoría, que ya fue presentada ante ASME, además de trabajar para seguir apoyando la ingeniería y su gran pasión: el mantenimiento predictivo.

Texto y fotos: Alimey Díaz M
Dinos qué te ha parecido el artículo
Artículos recomendados
Armando Negrotti: El Facility Management comienza desde la proyección de la edificación

Jim Fitch: En Noria seguimos comprometidos con la calidad, la confiabilidad y la satisfacción de nuestros clientes

Argenis Mindiola: El Mantenimiento Predictivo es el Arte del Mantenimiento

María Teresa Romero: El Mantenimiento y la Gestión de Activos pueden Proporcionarnos un Mundo Mejor

Publica tu artículo en la revista #1 de Mantenimiento Industrial
Publicar un artículo en la revista es gratis, no tiene costo.
Solo debes asegurarte que no sea un artículo comercial.
¿Qué esperas?
O envía tu artículo directo: articulos@predictiva21.com
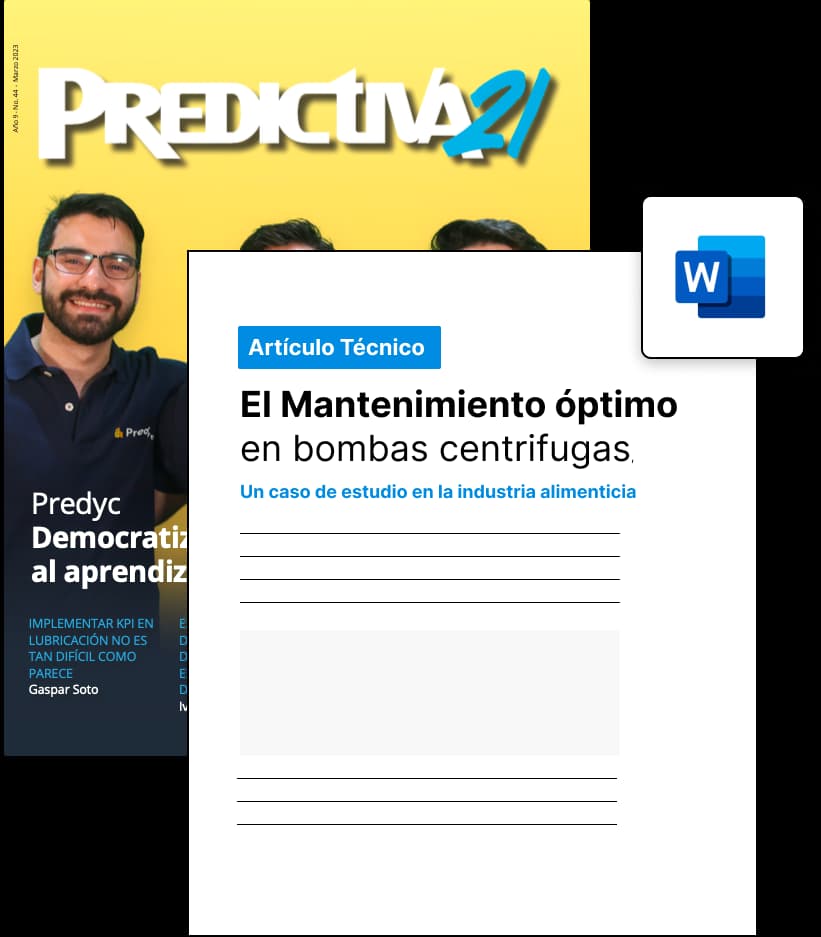
Argenis Mindiola: El Mantenimiento Predictivo es el Arte del Mantenimiento
Entrevista 4 de mayo de 2020Este comprometido ingeniero, con largos años de experiencia en el campo del mantenimiento, habla con sencillez de su gran pasión por el mantenimiento predictivo, y la importancia de legar estos conocimientos a la generación de relevo.
El predictivo es el arte del mantenimiento, es lo más refinado que existe en esa área.
A. Mindiola
Diagnosticar, inspeccionar, predecir y favorecer la productividad parecen ser máximas asociadas al mantenimiento predictivo, una de las ramas más comprometidas dentro de la ingeniería de mantenimiento. Escuchar a un experto como Argenis Mindiola hablar de sus inicios y de la pasión que le imprime a su trabajo, es tan placentero como inspirador. Luego de tres décadas laborando para varias filiales nacionales, Mindiola no contempla el retiro como una opción, sino como la oportunidad de seguir desarrollando su pasión por el mantenimiento, enmarcada en su teoría Running Spare o capacidad rodante, en la cual trabaja desde el año 2004, y que contempla los aspectos teóricos, de diseño y selección de esquemas de compresión que no queman gas dentro del sistema de compresión.
Comenzamos la entrevista con las evocadoras frases de Argenis, quien se remonta en el tiempo para hacer un breve esbozo de lo que ha sido su prolífica vida profesional. Comenzó en la antigua filial nacional petrolera Maraven, balanceando pequeños rotores a escala, ejercicio apasionante y a la vez metódico, que decidiría, a no dudar, el rumbo de su carrera. Corría el año 1981, y el otrora joven ingeniero, que trabajaba de día en el Lago de Maracaibo, permanecía hasta altas horas de la noche, intentando develar los secretos del balanceo a escala. Y un día, la oportunidad apareció, bajo la forma de problema, como suele suceder. “Un amigo y colega me comentó que tenían un problema con cierta maquinaria desde hacía varios meses. Le pedí mirar la cinta de datos, y le dije que tenían un problema de balanceo, lo cual suponía varios meses de diagnóstico errado. Fue toda una sorpresa. Así que me asignaron arreglar el equipo. Era una turbina con un generador eléctrico, y logré que mis superiores confiaran en mí lo suficiente como para asumir este importante reto. Nos comprometimos a fondo con este proyecto, y logramos arreglar el equipo, que además era muy sofisticado y delicado para la época” –relata Mindiola. Obviamente, fue todo un éxito. Para esa época la revista de Maraven registró el hecho, y obtuvo reconocido mérito entre sus colegas, lo cual marcó para nuestro entrevistado el inicio de una brillante y fructífera etapa profesional. Este primer trabajo marcó el inicio de otros proyectos a cargo de Equipos Rotativos, que asumieron trabajos en otras filiales nacionales e interfiliales, con el consecutivo aumento de la confianza y las responsabilidades.
Predictiva21: Luego de esta primera etapa, en la cual usted y su equipo se encargan de resolver el problema de un equipo rotativo de alta factura, ¿qué siguió?
Argenis Mindiola: Lo interesante de este primer trabajo y los que le siguieron fue que logramos sentar bases importantes en el área de equipos rotativos, bases sobre las que después se apoyaron otros colegas y otros proyectos. A mi despedida de la parte de inspección de equipos rotativos, me asignaron como superintendente de taller central de Turbomáquinas de Maraven.
P21: Parte de este hacer ¿Quedó registrado?
AM: Sí, como no. Para esa época escribí un libro, basado en todas estas experiencias y aprendizajes. El libro se llama Análisis de Vibraciones Nivel Avanzado, editado por Maraven, y es ahora un libro de consulta para muchos analistas. Yo soy un fiel convencido de que el conocimiento ha de fluir, expandirse, crecer, y tocar a todos, de eso depende el avance de la civilización.
P21: ¿Cómo fue la reacción de la empresa, luego de estos logros?
AM: Este interés constante en el mantenimiento nos permitió fundar el Departamento de Mantenimiento Predictivo, que para la época era una novedad. Corrían los años ochenta, y la filial petrolera puso a todo a nuestra disposición, en favor del desarrollo del mantenimiento predictivo. Nos concedieron equipos muy de avanzada para ese tiempo: analizadores de espectro, todo tipo de equipos para diagnóstico, alineación láser, teníamos la tecnología de punta, y aprendimos a hacer un diagnóstico más profundo. Colectamos firmas de los equipos, hacíamos análisis de frecuencia y con eso determinábamos qué componente podía fallar. Ese aprendizaje del diagnóstico hizo que nos apodaran los brujos. Pero no era brujería, claro, era diagnóstico.
P21: ¿Qué otros aportes recuerda de esa época?
AM: Existen tres tipos de mantenimiento: correctivo por avería, preventivo y necesario, se maneja en platas nucleares, y luego viene la etapa avanzada, que es el predictivo. No sustituye al preventivo, sino que optimiza. En atención a esto, propusimos hacer, por primera vez, una parada de equipo en sincronía con una parada de planta, de forma conjunta con el mantenimiento de pozos y toda la estructura asociada, es decir, hacer todos los mantenimientos basados en el predictivo. Fue muy novedoso, y al principio lucía muy arriesgado. Pero logramos vender la idea, pudimos hacer una planificación macro que incluyó mantenimiento de pozos, de estaciones de recolección de flujo, mantenimiento de plantas de gas y mantenimiento de líneas, toda sincronizada con una sola parada, basados en el predictivo. Fue un éxito, porque bajamos los tiempos de parada, unos 20 días, reduciéndolos a un tercio, lo cual se tradujo en producción. Ese fue uno de nuestros grandes éxitos.
P21: ¿Cómo prosiguió su desarrollo profesional? ¿Qué rumbo tomó su investigación?
AM: Me gusta mucho la matemática, los cálculos y las ecuaciones. Entonces hice un programa de predicción de parámetros operacionales, bajo el nombre Pronóstico de Comportamiento de equipos basado en modelos estadísticos y ecuaciones matemáticas. Enamorado del predictivo como estaba, decidí diseñar esta herramienta, con la ayuda de un amigo y colega matemático. Para la primera parte de la investigación, tomé un valor de temperatura de un equipo rotativo, y me dediqué a registrar sus cambios, y los tiempos en los cuales ocurrían las variaciones. Luego determiné el patrón matemático que regía ese comportamiento (por ejemplo, el valor de la curva), y así empecé a hacer el modelo. Como paso posterior, extrapolé estos datos de variaciones a un modelo matemático, basándome en método de ajuste de curvas por mínimos cuadrados, y esta fue la base para diseñar todo mi sistema de ecuaciones. Combiné todos los datos de una máquina seleccionada para determinar puntos de inflexión, parámetros de comportamiento y luego ofrecer un diagnóstico presente, y uno predictivo a futuro. Fue una etapa muy prematura de inteligencia artificial, y sin lugar a dudas muy exitoso.
Otros rumbos, la misma pasión
Mindiola relata que luego de esa época pasó a ser Jefe de Talleres de Turbomáquinas, en una etapa de gran importancia, porque marcó el inicio de las reparaciones de turbinas dentro del territorio venezolano. Posteriormente, estudió en California, Estados Unidos, para certificarse como reparador de Turbinas Allison. Luego regresó al país, para dedicarse a la fabricación de los sellos laberinto, los primeros de manufactura nacional. Los sellos laberinto constituían en esa época un aspecto crítico en el mantenimiento de compresores. Al lograr hacerlos en el país significó un gran paso, elaborándose incluso un manual de procedimiento para la fabricación de estos, lo cual allanó el camino para procesos futuros.
Para el año 2004, Argenis Mindiola se sentía tan comprometido con el mantenimiento predictivo como a comienzos de su muy exitosa carrera. Ese año se dedicó a formular la teoría Running Spare o capacidad rodante. En el sistema de compresión, esta teoría contempla los aspectos teóricos, de diseño y selección de esquemas de compresión que no queman gas. Luego de muchos cálculos y pruebas, Mindiola se reunió con los jefes de ingeniería de diseño de varias marcas afamadas como Solar Turbine, Siemmens, Nuovo Pignone, GE y Dresser Rand, ante quienes expuso su teoría. Según esta propuesta, si existe una batería de equipos laborando a un determinado nivel de eficiencia y carga determinada, y uno de ellos falla, los demás equipos deben tener la capacidad de asumir la carga del equipo en cuestión, sin que esto implique afectaciones, como la quema de gas o el cierre de la producción. En los últimos años, Mindiola ha laborado en PDVSA Holanda, a donde fue como gerente técnico y luego pasó a encargarse de otras gerencias. Ahora, próximo a jubilarse, Mindiola espera poder enfocarse en el desarrollo de esta teoría, que ya fue presentada ante ASME, además de trabajar para seguir apoyando la ingeniería y su gran pasión: el mantenimiento predictivo.

Texto y fotos: Alimey Díaz M
Dinos qué te ha parecido el artículo
Artículos recomendados
CIFMers: Lo más Novedoso del Facility Management para Iberoamérica y el Mundo

Entrevista a Johanna Durán

Santiago Sotuyo: The long road to reliability

WIRAM: El lado femenino de la Ingeniería en Mantenimiento

Publica tu artículo en la revista #1 de Mantenimiento Industrial
Publicar un artículo en la revista es gratis, no tiene costo.
Solo debes asegurarte que no sea un artículo comercial.
¿Qué esperas?
O envía tu artículo directo: articulos@predictiva21.com
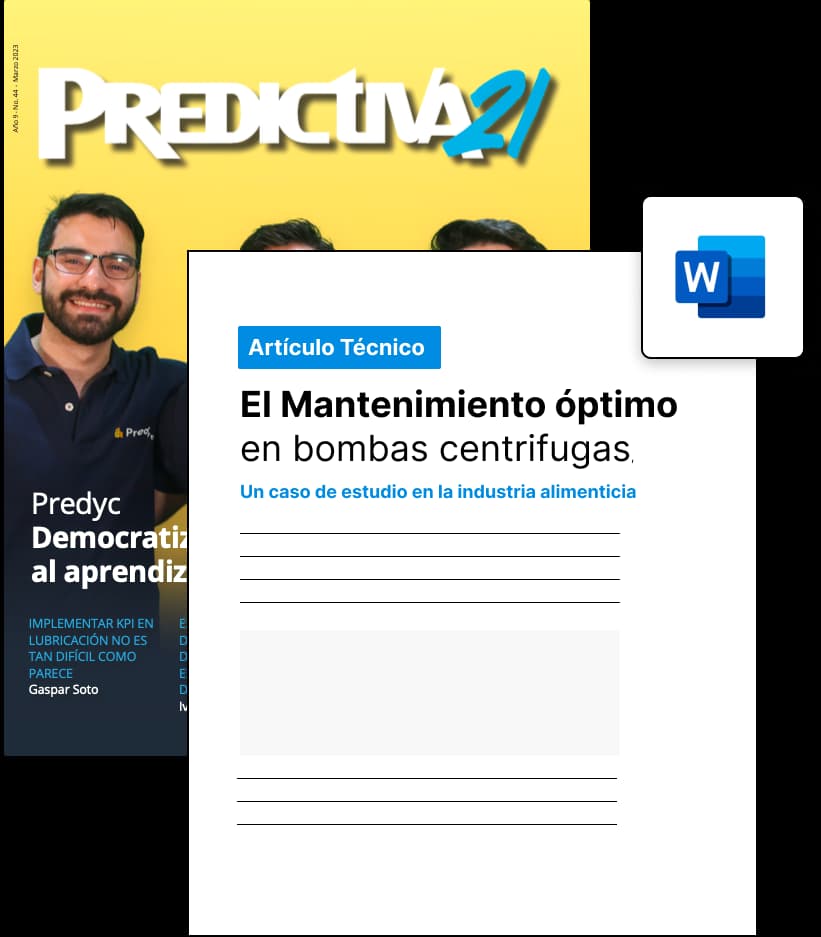