Compensación de Potencia Reactiva alineada a un modelo de gestión de mantenimiento en plantas industriales
Articulo23 de enero de 2021
Actualmente, el desarrollo de instalaciones eléctricas implica problemas de rentabilidad en sus procesos, donde la toma de decisiones están orientadas a la eficiencia energética sin considerar posibles impactos sobre determinados riesgos, puede presentar altos costos no rentables para una planta. Este trabajo muestra un estudio de caso de problemas de compensación de potencia reactiva, mostrando diferentes indicadores técnicos de mantenimiento y gestión económica relacionados con el factor de potencia, considerando impactos de confiabilidad, mantenimiento, costos de consumo de energía y penalizaciones, mostrando una nueva forma de abordar problemas de eficiencia energética alineados con mantenimiento y gestión de activos.
Palabras claves: Gerencia de Eficiencia Energética, Factor de Potencia, Gerencia del Mantenimiento, Tasa de Falla.
I. Introducción
Las transformaciones que se van dando en las redes eléctricas ha iniciado la necesidad de utilizar estrategias de gestión que permitan una mejor optimización de los activos críticos a nivel de generación, distribución, transmisión y subtransmisión teniendo como resultados una mejor rentabilidad, control de riesgos, confiabilidad operativa, ahorro y eficiencia energética [1,2].
La eficiencia energética eléctrica ha sido una estrategia que han implementado algunas organizaciones, donde una de las situaciones que se ha presentado en la gestión de la eficiencia energética, es que muchas veces no logra consolidarse debido a que ha sido enfocada mayormente en la eficacia (acciones a corto plazo) y no en la eficiencia (acciones a mediano y largo plazo), teniendo un énfasis en los costos de facturación no considerando los impactos que pueden presentarse en el mantenimiento, confiabilidad y rentabilidad de la planta [3,4], como se muestra en la Fig. 1.

Fuente: El autor.
Por otra parte la carencia de un modelo de gestión de mantenimiento que contemple aspectos de ahorro y eficiencia energética en la industria es una situación muy común de observar, impactando muchas veces en situaciones no deseables.
II. Gestión del mantenimiento en sistemas eléctricos
Un modelo de gestión de mantenimiento consolidado en los sistemas eléctricos, involucra el uso de herramientas y metodologías de optimización que permitan agregar valor. En el modelo mostrado en la Fig. 2, se presenta un modelo generalizado de 8 etapas [5,6], en donde las primeras 3 etapas condicionan a la gestión de eficacia (estrategias a corto plazo), las 2 siguientes etapas a la eficiencia del mismo (a mediano y largo plazo), las 2 posteriores a la evaluación de activos y el último a la mejora continua. La fase 1 muestra los objetivos planteados para mejoras en una planta, dentro de esta etapa se pueden encontrar indicadores técnicos, de operación y financieros mediante una matriz de información llamada cuadro de mando integral. La fase 2 hace relación a establecer una criticidad en sistemas/equipos/componentes críticos (como pueden ser transformadores, protecciones que su disparo involucren una pérdida financiera, etc.), en donde la pérdida de la función impacta en una planta financieramente. La fase 3 hace relación en el análisis de problemas recurrentes significativos en una planta, en donde muchas veces debido al desconocimiento de cómo afrontarlos se decide adaptarse al problema (como puede ser operar una planta a un 70% o de lo contrario se disparan las protecciones o considerar los pagos por penalizaciones por bajo factor de potencia y distorsión armónica). Las fases 4 y 5 hacen referencia a optimizar planes de mantenimiento para evitar la pérdida de la función de activos críticos que pudieran impactar en la planta (que se debe hacer para que cualquier activo crítico continúe con su función en el contexto operacional). En la fase 6, se aplican distribuciones de probabilidades consideradas con el funcionamiento de los activos basados en indicadores básicos de mantenimiento y confiabilidad. La fase 7 se refiere a la evaluación de activos mediante la proyección de todos los costos a lo largo del ciclo de vida, considerando los impactos en el área de confiabilidad y mantenibilidad en los activos. La fase 8 se refiere al uso e implementación de nuevas herramientas que realicen mejoras en una planta. El modelo anterior mostrado para que sea rentable a una organización deberá estar alineado a la gestión de activos como se muestra en la Fig. 1.
![Figura 2. Modelo de Gestión de Mantenimiento alineado a una gestión de activos [5,6].](/_next/image?url=https%3A%2F%2Ffirebasestorage.googleapis.com%2Fv0%2Fb%2Fpredyc2023.appspot.com%2Fo%2FArticulosP21%252Fcompensacion-potencia-reactiva%252Fimage-20-1024x561.png%3Falt%3Dmedia%26token%3D8baeff24-96e0-46b9-91f6-25d4cc68a670&w=1920&q=75)
Fuente: El autor.
III. Gestión de activos en sistemas eléctricos
La gestión de activos puede definirse como el conjunto de actividades y prácticas, sistemáticas y coordinadas, que una organización utiliza para conseguir que sus activos entreguen resultados y objetivos de manera consistente y sostenible, gestionando el riesgo y fomentando la cultura corporativa [7]. Esta definición de la gestión de activos representa significativamente un mayor alcance que el de la gestión del mantenimiento y operación técnica de los activos físicos.
Actualmente los sistemas eléctricos han comenzado a enfrentar problemáticas debido a una vulnerabilidad con sus activos [8], existiendo el riesgo de sufrir pérdidas económicas como se muestra en la Fig. 3. En consecuencia por lo anterior expuesto, han empezado a surgir algunos estándares como son la serie de guías ISO 55000/01/02, que mencionan algunas recomendaciones para gestionar los activos a lo largo del ciclo de vida de los equipos [9,10,11], donde una de las sugerencias es poder integrar el uso de indicadores técnicos con los indicadores financieros.

Fuente: El autor.
IV. Metodología técnica convencional para soluciones de compensación de potencia reactiva
Una estrategia de ahorro y eficiencia energética eléctrica en una planta es mejorar la compensación de potencia reactiva [12, 13,14], en donde los efectos no deseados por no compensar la potencia reactiva es el incremento de la potencia aparente entregada por transformadores e incrementos de corrientes en alimentadores ocasionando una degradación de la vida útil operativa de los componentes del sistema eléctrico y costos de penalizaciones significativas en las facturaciones. Una manera de abordar este problema de compensación de potencia reactiva, es mediante la medición de indicadores técnicos eléctricos como son: potencia activa, potencia reactiva, potencia aparente, factor de potencia (FP), corriente de la demanda máxima, pérdidas de energía y caída de tensión.
A. Cálculo del factor de potencia (FP)
El factor de potencia se puede calcular de diversas maneras, pero esta definido por:

donde P y S son la potencia activa y aparente trifásica de un centro de carga, dadas generalmente en kW y kVA. Una manera convencional de calcular el FP es utilizando (1) cada 5, 10 o 15 minutos durante un periodo de facturación, o mediante la energía consumida en el periodo de facturación, es decir:

Considerando una demanda de energía constante, se tiene que el factor de potencia se ve reducido conforme la potencia aparente se incremente, esto debido al incremento de potencia reactiva kVAr demandada por la carga. De esta manera el reducir el consumo de la potencia reactiva entregada por el transformador principal, mejorará considerablemente el factor de potencia.
B. Compensación de potencia reactiva mediante un banco de capacitores
Para mejorar el FP, se pueden utilizar bancos de capacitores, ya sean fijos, conexión/desconexión automática o mediante un compensador estativo de VAr (CEVs), según sean los requerimientos de potencia reactiva de la planta. El más convencional es mediante el uso de bancos de capacitores fijos, donde el cálculo de bancos de capacitores (Q en kVAr) para corregir el FP se puede calcular de la siguiente manera:

Donde:

El subíndice 1 indica el FP del sistema actual y el subdíndice 2 indica el FP del sistema deseado.
V. Indicadores de gestión de mantenimiento y económicos
El tema de indicadores de gestión en el mantenimiento es diverso, sin embargo para el presente trabajo se muestran algunos indicadores de fácil aplicación que pueden relacionarse con indicadores económicos y que posteriormente muestren la rentabilidad adecuada mediante una proyección anual de costos. Desarrollar una gestión de mantenimiento en una planta consiste en reducir la probabilidad de presencia de fallas (confiabilidad), recuperar de forma rápida y eficiente la operabilidad de los sistemas (mantenibilidad) una vez que se ha presentado la interrupción de la función, minimizar el impacto por las consecuencias de los eventos de fallas (costos por indisponibilidad). Por lo anterior mencionado, una gestión eficiente del mantenimiento busca: mejorar la continuidad operacional (disponibilidad), maximizar la rentabilidad a través de los activos (ganancias económicas) y minimizar los riesgos sobre la seguridad, ambiente y las operaciones a niveles tolerables (consecuencias de los eventos de fallas) a lo largo del ciclo de vida útil [15, 16, 17,18].
a) Indicadores técnicos de mantenimiento básicos
El tiempo promedio de operación (TPO) es un indicador que nos muestra la confiabilidad operativa mediante un promedio de tiempos de operación de un componente, máquina o sistema.

Donde TOF es el tiempo operativo hasta el fallo o hasta la sustitución programada y es el número total de fallos o sustituciones programadas en el periodo evaluado. Mediante este indicador se obtiene inversamente proporcional la frecuencia de fallos dada por la ecuación (7).

Este indicador es aplicado para el presente estudio solo al transformador y banco de capacitores.
El tiempo promedio de reparación TPPR nos muestra la mantenibilidad de un componente, máquina o sistema.

Donde el TR es el tiempo de reparación.
El tiempo promedio fuera de servicio (TPFS) es un indicador que muestra los impactos por los tiempos de reparación y tiempos fuera de control.

Donde el TFS es el tiempo fuera de servicio.
Para cadaTFSi se consideran los tiempos fuera de control (logística, imprevistos, etc.) y los tiempos promedios de reparación, como se muestra en (10):

Otro indicador utilizado es la disponibilidad operacional (Ao), el cual puede ser de varios tipos, para este estudio será considerada la disponibilidad operacional genérica (Ao) del sistema para un periodo determinado.

b) Indicador de costos por indisponibilidad en fiabilidad (CIF)
Es un indicador económico de costos que vincula los indicadores técnicos ff (falla/año) y TPFS (hr/falla) mostrando los impactos de la confiabilidad y mantenibilidad en un valor monetario anualizado [19]. Considera las penalizaciones CP (costos directos, calidad, seguridad, etc).

c) Indicador de riesgo total anualizado (RTA)
Es un indicador económico que proyecta los costos anuales y sirve para realizar una comparación de componentes/equipos/sistemas y está dado por:

Donde CI son los costos de inversión, CO son los costos de operación, en ellos van incluidos los costos por energía, insumos y materia prima, CMM son los costos de mantenimiento mayor, CMP son los costos de mantenimiento preventivo y el CIF son los costos por infiabilidad.
d) Indicador financiero EBITDA (Earning Before Interest Taxes Depreciation Amortization)
Es un indicador financiero que muestra la rentabilidad antes de intereses, impuestos y depreciaciones [19,20]. Una manera de calcularlo es como se muestra en (14).

Donde PV es el producto vendido, calculado como:

Donde IP es el ingreso potencial ($) y Ao es la disponibilidad operacional (%).
CMT son los costos de mantenimiento anuales, donde son considerados los mantenimientos preventivos, mantenimientos mayores y correctivos no programados (CIF).

CO son los costos de operación. Para el presente estudio solo son considerados los gastos de consumo de energía involucrando los costos de las penalizaciones y bonificaciones por FP.
GA son los gastos administrativos, GV son los gastos por ventas y DA es la depreciación/amortización.
Cursos recomendados






%252FImagen%252FRAMPREDYC-1730060420837.webp%3Falt%3Dmedia%26token%3D2634a7f0-988e-4022-b91f-382503e6e9db&w=3840&q=75)

VI. Caso de estudio. Compensación de potencia reactiva optimizada
El estudio presentado corresponde a un sistema eléctrico de una industria, en donde existe un transformador de 500 kVA, operando a un FP de 0.7, que alimenta una carga de 360 kW. La carga es alimentada mediante un alimentador conformado por 2 conductores por fase calibre 600 KCM con una longitud de 100 m, operando 20 horas diarias [11]. La Fig. 4 muestra el diagrama del sistema actual y del sistema propuesto con su banco de capacitores para tener un factor de potencia de 0.95 y evitar alguna penalización.

Fuente: El autor.
Para esta planta de la Fig 4, se tiene una tarifa de Gran Demanda Media Tensión Ordinaria (GDMTO), presentando los siguientes valores en la facturación mensual mostrados en la Tabla I, en dicha tabla se muestra una penalización por bajo factor de potencia.

Si ahora se calcula el banco de capacitors para un FP de 0.95 aplicando (3) se tiene:

Mediante esta solución técnica se observa en la Fig. 4 que al transformador se le libera carga, así mismo a los alimentadores se les reduce la corriente por fase IL y por ende a las corrientes de los conductores Iconductor, esto es debido a la inserción del banco de capacitores de 250 kVAr. El conductor de 600 KCM tiene una resistencia de 0.0753 Ω/km, entonces la resistencia para una distancia de 100 m es de:

Donde las pérdidas considerando la corriente en el conductor para el sistema actual es:

Y para el sistema propuesto:

Donde los siguientes valores en la facturación, como se muestran en la Tabla II, en esta tabla se observa ahora una bonificación por factor de potencia.

De esta manera se tiene una reducción del consumo de energía mensual por pérdidas en los cables de:

Lo que representa un ahorro de $16,046.64 considerando el costo por kWh de $2.85.
Para el retorno de la inversión, se considera un costo del banco de capacitores de $250,000.00, entonces el retorno simple de inversión está dado por:

Donde el retorno de la inversión es aproximadamente en dos meses:

Se menciona que esta propuesta de solución técnica no considera los impactos por confiabilidad y mantenimiento. Aplicando el modelo de gestión de mantenimiento, se puede observar que los impactos técnicos con los gerenciales tienen una relación como se muestran en la Tabla III.

Por lo anterior, utilizando el modelo mostrado en la Fig. 1, se abordan solo las tres fases, que corresponde a un problema recurrente significativo, como lo es el bajo FP.
Analizando la fase 1, se muestra una parte de un cuadro de mando integral, donde se encuentran indicadores técnicos y económicos, como se muestra en la Tabla IV.

La Tabla III muestra el impacto crítico de los transformadores y alimentadores del sistema, que es considerado en la fase 2 del modelo de gestión de mantenimiento.
El evento no deseado de un bajo FP es un problema recurrente que impacta en los objetivos gerenciales, lo que corresponde a la fase 3, en donde se ha analizado la solución técnica (banco de capacitores de 250 kVAr) sin embargo ahora considerando los impactos por confiabilidad, mantenibilidad y rentabilidad se aplican las ecuaciones mostradas anteriormente considerando los siguientes datos adicionales recabados en planta.
Para el transformador se muestran los datos en la Tabla V, en donde el costo por penalización corresponde a lo que se pierde en producción por paro total. El costo de inversión (CI) es de $750,000.00.

Los datos de los bancos de capacitores propuestos son dos, en donde se observa en la Tabla VI las características técnicas de cada uno de ellos. Se menciona que los costos de penalización se calculan en función de la facturación cuando existe la penalización por bajo FP, considerando en falla el banco de capacitores ya sea el de Tipo 1 o Tipo 2. La diferencia de los tipos de bancos de capacitores es de acuerdo a las características técnicas de mantenimiento, confiabilidad y de costos de inversión mostrados en la Tabla VI.

Con los datos anteriores se calculan los indicadores económicos como se muestra en la Tabla VII.
Analizando los CIF para cada escenario, en la condición inicial solo es considerado el transformador, en las posteriores condiciones se considera el transformador y banco de capacitores.
En el estudio del indicador RTA para cada escenario son considerados los costos de inversión de cada componente del sistema siendo $750,000.00 para el transformador, $250,000.00 para el banco de capacitores tipo 1 y $ 150,000.00 para el banco de capacitores tipo 2. Los costos de operación involucran la facturación de energía anual con penalización y bonificación por FP. Para los costos de mantenimiento preventivo (CMP) y mayor (CMM) se tiene un valor anualizado de $20,000.00 para la condición inicial y para las otras condiciones un valor de $5,000.00. El análisis del CTPF considera las características técnicas de mantenimiento y confiabilidad, en donde para la condición inicial solo se toma en cuenta el transformador y en las condiciones posteriores se considera el transformador y el banco de capacitores, haciendo énfasis en que un banco de capacitores tiene una confiabilidad y mantenibilidad apropiada y el otro no, así de esta manera se obtiene una proyección anual de costos.
Para la interpretación del indicador EBITDA que es un indicador financiero de rentabilidad, se hace énfasis en las variables PV, CMT y CO, en donde en el indicador PV se observa el impacto que produce la disponibilidad Ao que a la vez vincula con los indicadores TPO y los TPFS. En la variable CMT se observa cómo influye el indicador CIF que vincula la ff, TPFS y CP. Por último en los CO se observa cómo influye la compensación reactiva en la facturación del consumo de energía eléctrica, existiendo penalizaciones o bonificaciones. El IP y los costos de GA, GV y DA se consideran costos fijos.
En la Tabla VII se puede observar el escenario con mayor rentabilidad, que es el sistema con el banco de capacitores Tipo 1, ya que observando los costos proyectados anualmente se observa que aunque el CIF muestre un panorama mejor para la condición inicial, el RTA es el menor y el EBITDA referido a la rentabilidad es el mayor valor, esto es debido a a la consideración de los costos de operación que involucran la penalización o bonificación por FP.

VII. Conclusiones
Tener una solución técnica para problemas de compensación de potencia reactiva requiere considerar factores adicionales como son los indicadores de mantenimiento, confiabilidad y financieros, así de esta manera se permite tener criterios justificados que mejoren la rentabilidad en una planta de una manera más óptima. Mediante un modelo de gestión de mantenimiento alineado a la gestión de activos, se permite analizar problemas recurrentes mediante las tres primeras fases y poder mitigarlos de una manera optimizada, alineando la eficiencia energética eléctrica a la gestión de mantenimiento y estas dos a la gestión de activos.
VIII. Referencias
- W. Shu, X. Liu, Y. Liu “Assestment of harmonic resonance potential for shun capacitor applications”, Electric Power Systems Research 57 (2001) 97–104, September 2004.
- J. Meyer, R Stiegler. P. Schegner, I. Röder, A. Belger “Harmonic resonances in residential low-voltage networks caused by consumer electronic”,IET Journal, CIRED, Open Access Proc. J., 2017, Vol. 2017, Iss. 1, pp. 672–676
- A .F. Zooba, “Maintaining a Good Power Factor and Saving Money for Industrial Loads “, IEEE Transactions on industrial electronics, Vol. 53, No. 2, April 2006.
- M. Ahrens, Z. Konstantinovic, “Harmonic filters and power factor compensation for cement Plants”, Conference Record Cement Industry Technical Conference, Kansas, USA, 2005.
- M.Sanz, Use, Operation and Maintenance of Renewable Energy Systems, Experiences and Future Approaches, Edit. Springer, Spain, 2014, Chapter 1, Pag. 22.
- A.Crespo, V.Gozalez, J.F.Gomez, Advanced Maintenance Modelling for Asset Management Techniques and Methods for Complex Industrial Systems, Edit. Springer, Spain, 2018, Chapter 1, Pag.6.
- Z.Ma, L.Zhou, W.Sheng, “analysis of The New Asset Management Standard ISO 55000 AND PAS 55”, China International Conference on Electricity Distribution (CICED 2014), Shenzhen, 23-26 Sep. 2014.
- J.Elias, A.Romero, “Consideraciones para la Gestión de Líneas de Alta Tensión, según ISO 55000”, IEEE Biennial Congress of Argentina (ARGENCON), Mayo 2014.
- Consultora WoodHouse Partnership Ltd England, 2017, seminario de gestión de activos en la generación de energía eléctrica en México, 2017.
- S. K. Ray Mohapatra, Subrata Mukhopadhyay “Risk and Asset Management of Transmission System in a Reformed Power Sector”, Power India Conference, 2006 IEEE
- M.Shahid, M. Mahamood, N. Das “Integrated Asset Magnagement Framework for Australian Wind Farm”, Australasian Universities Power Engineering Conference– AUPEC2016.
- Acha E. Madrigal M. Power System Harmonics, Computer Modelling and Analysis, Edit. John Wiley & Sons, , UK. 2001, Pag. 65-70.
- J.C. Das, Power System Harmonics and Passive Filter Designs, Edit. John Wiley & Sons, Canada. 2005.
- Consultora IMELHIA, Caso práctico de compensación de potencia reactiva, Quintana Roo, México 2002.
- IEEE Recommended Practice for the Maintenance of Industrial and Commercial Power Systems, IEEE Std 3007.2 – 2010.
- R. Arno, N. Dowling, R.J. Schuerger, “Equipment failure characteristic and RCM for optimizing maintenance cost “, IEEE Transactions on Industry Application, Vol. 52, Issue 2, March 2016.
- IEEE Recommended Practice for Evaluating the Reliability of Existing Industrial and Commercial Power Systems, IEEE Std 3006.2™-2016.
- IEEE Recommended Practice for Collecting Data for Use in Reliability, Availability, and Maintainability Assessments of Industrial and Commercial Power Systems. IEEE Std XXX, año
- Parra C., Ingeniería de Mantenimiento y Fiabilidad aplicada en la Gestión de Activos, 2da edición edit. Ingeman, España, 2015.
- K. Kushuwan, K. Waiyamai, “ EBITDA Time Series Forecasting Case study: Provincial Waterworks Authority”, International Conference on Digital Arts, Media and Technology with ECTI Northern Section Conference on Electrical, Electronics, Computer and Telecommunications Engineering, Thailand 2019.
Autores:
R. Cetina
Instituto Tecnológico de Morelia
Morelia Michoacán, México
Correo: rubencetinaabreu@hotmail.com
Descripción: R. J. Cetina es Ingeniero Electricista egresado de la Universidad Autónoma del Carmen, Campeche, México en 2008. Obtuvo el grado de Maestro en Ingeniería Industrial, Mantenimiento y Confiabilidad en el Centro de Estudios Superiores de la Isla (CESIC), Carmen, Campeche, México, el de Maestro en Energías Renovables en el Centro de Investigaciones de Materiales Avanzados (CIMAV), en Chihuahua, México en 2014 y el grado de Doctor en Ciencias de la Ingeniería Eléctrica en el Instituto Tecnológico de Morelia (ITM) en 2020. Sus áreas de interés son calidad de la energía, ingeniería de mantenimiento y confiabilidad de sistemas eléctricos de potencia y de fuentes renovables de energía.
V. Torres
UN AM
Cd-Mx, México
Correo: v.torres.1982@ieee.org
Descripción: V. Torres-García nació en Morelia, Michoacán, se gradúo de la carrera de ingeniería eléctrica del Instituto Tecnológico de Morelia en el 2008, recibió el grado de maestro y doctor en ciencias de la ingeniería eléctrica en la misma institución en 2009 y 2014 respectivamente. Actualmente se desempeña como profesor de carrera en la facultad de ingeniería de la Universidad Nacional Autónoma de México, sus áreas de interés son sistemas eléctricos de potencia y distribución, transitorios electromagnéticos y protecciones eléctricas.
M. Madrigal
Instituto Tecnológico de Morelia
Morelia Michoacán, México
Correo: manuelmadrigal@ieee.org
Descripción: M. Madrigal es Ingeniero Electricista egresado del Instituto Tecnológico de Morelia en 1993. Obtuvo el grado de Maestro en Ciencias en Ingeniería Eléctrica en 1996 en la Universidad Autónoma de Nuevo León, México y el grado de Doctor en 2001 en la Universidad de Glasgow, Escocia. Es profesor investigador del posgrado en eléctrica del Instituto Tecnológico de Morelia desde 1996. Sus áreas de interés son calidad de la energía, análisis armónico, integración de fuentes renovables de energía a las redes eléctricas y administración de la energía.
Dinos qué te ha parecido el artículo
Artículos recomendados
Auditoría de Gestión de Activos Industriales a través de técnicas Predictivas y Confiabilidad

Los Lubricantes de grado alimenticio y su importancia para la Industria

Conceptos básicos de confiabilidad

Cálculo de cantidad de grasa para la re-lubricación periódica de rodamientos

Publica tu artículo en la revista #1 de Mantenimiento Industrial
Publicar un artículo en la revista es gratis, no tiene costo.
Solo debes asegurarte que no sea un artículo comercial.
¿Qué esperas?
O envía tu artículo directo: articulos@predictiva21.com
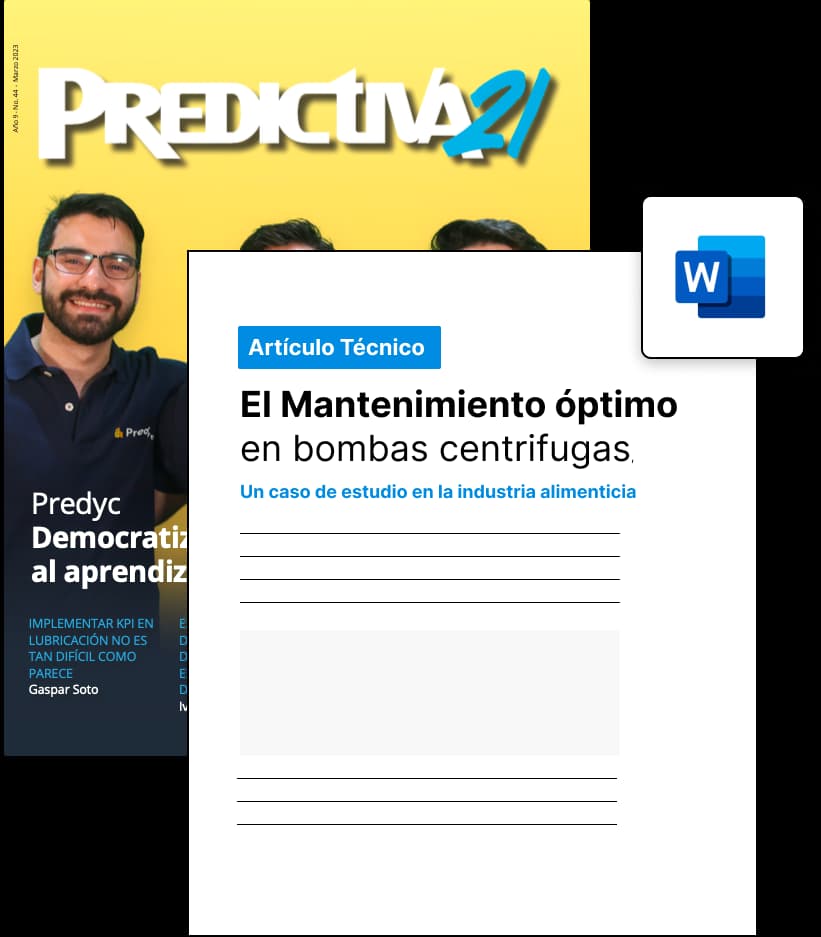
Compensación de Potencia Reactiva alineada a un modelo de gestión de mantenimiento en plantas industriales
Articulo 23 de enero de 2021Actualmente, el desarrollo de instalaciones eléctricas implica problemas de rentabilidad en sus procesos, donde la toma de decisiones están orientadas a la eficiencia energética sin considerar posibles impactos sobre determinados riesgos, puede presentar altos costos no rentables para una planta. Este trabajo muestra un estudio de caso de problemas de compensación de potencia reactiva, mostrando diferentes indicadores técnicos de mantenimiento y gestión económica relacionados con el factor de potencia, considerando impactos de confiabilidad, mantenimiento, costos de consumo de energía y penalizaciones, mostrando una nueva forma de abordar problemas de eficiencia energética alineados con mantenimiento y gestión de activos.
Palabras claves: Gerencia de Eficiencia Energética, Factor de Potencia, Gerencia del Mantenimiento, Tasa de Falla.
I. Introducción
Las transformaciones que se van dando en las redes eléctricas ha iniciado la necesidad de utilizar estrategias de gestión que permitan una mejor optimización de los activos críticos a nivel de generación, distribución, transmisión y subtransmisión teniendo como resultados una mejor rentabilidad, control de riesgos, confiabilidad operativa, ahorro y eficiencia energética [1,2].
La eficiencia energética eléctrica ha sido una estrategia que han implementado algunas organizaciones, donde una de las situaciones que se ha presentado en la gestión de la eficiencia energética, es que muchas veces no logra consolidarse debido a que ha sido enfocada mayormente en la eficacia (acciones a corto plazo) y no en la eficiencia (acciones a mediano y largo plazo), teniendo un énfasis en los costos de facturación no considerando los impactos que pueden presentarse en el mantenimiento, confiabilidad y rentabilidad de la planta [3,4], como se muestra en la Fig. 1.

Fuente: El autor.
Por otra parte la carencia de un modelo de gestión de mantenimiento que contemple aspectos de ahorro y eficiencia energética en la industria es una situación muy común de observar, impactando muchas veces en situaciones no deseables.
II. Gestión del mantenimiento en sistemas eléctricos
Un modelo de gestión de mantenimiento consolidado en los sistemas eléctricos, involucra el uso de herramientas y metodologías de optimización que permitan agregar valor. En el modelo mostrado en la Fig. 2, se presenta un modelo generalizado de 8 etapas [5,6], en donde las primeras 3 etapas condicionan a la gestión de eficacia (estrategias a corto plazo), las 2 siguientes etapas a la eficiencia del mismo (a mediano y largo plazo), las 2 posteriores a la evaluación de activos y el último a la mejora continua. La fase 1 muestra los objetivos planteados para mejoras en una planta, dentro de esta etapa se pueden encontrar indicadores técnicos, de operación y financieros mediante una matriz de información llamada cuadro de mando integral. La fase 2 hace relación a establecer una criticidad en sistemas/equipos/componentes críticos (como pueden ser transformadores, protecciones que su disparo involucren una pérdida financiera, etc.), en donde la pérdida de la función impacta en una planta financieramente. La fase 3 hace relación en el análisis de problemas recurrentes significativos en una planta, en donde muchas veces debido al desconocimiento de cómo afrontarlos se decide adaptarse al problema (como puede ser operar una planta a un 70% o de lo contrario se disparan las protecciones o considerar los pagos por penalizaciones por bajo factor de potencia y distorsión armónica). Las fases 4 y 5 hacen referencia a optimizar planes de mantenimiento para evitar la pérdida de la función de activos críticos que pudieran impactar en la planta (que se debe hacer para que cualquier activo crítico continúe con su función en el contexto operacional). En la fase 6, se aplican distribuciones de probabilidades consideradas con el funcionamiento de los activos basados en indicadores básicos de mantenimiento y confiabilidad. La fase 7 se refiere a la evaluación de activos mediante la proyección de todos los costos a lo largo del ciclo de vida, considerando los impactos en el área de confiabilidad y mantenibilidad en los activos. La fase 8 se refiere al uso e implementación de nuevas herramientas que realicen mejoras en una planta. El modelo anterior mostrado para que sea rentable a una organización deberá estar alineado a la gestión de activos como se muestra en la Fig. 1.
![Figura 2. Modelo de Gestión de Mantenimiento alineado a una gestión de activos [5,6].](/_next/image?url=https%3A%2F%2Ffirebasestorage.googleapis.com%2Fv0%2Fb%2Fpredyc2023.appspot.com%2Fo%2FArticulosP21%252Fcompensacion-potencia-reactiva%252Fimage-20-1024x561.png%3Falt%3Dmedia%26token%3D8baeff24-96e0-46b9-91f6-25d4cc68a670&w=1920&q=75)
Fuente: El autor.
III. Gestión de activos en sistemas eléctricos
La gestión de activos puede definirse como el conjunto de actividades y prácticas, sistemáticas y coordinadas, que una organización utiliza para conseguir que sus activos entreguen resultados y objetivos de manera consistente y sostenible, gestionando el riesgo y fomentando la cultura corporativa [7]. Esta definición de la gestión de activos representa significativamente un mayor alcance que el de la gestión del mantenimiento y operación técnica de los activos físicos.
Actualmente los sistemas eléctricos han comenzado a enfrentar problemáticas debido a una vulnerabilidad con sus activos [8], existiendo el riesgo de sufrir pérdidas económicas como se muestra en la Fig. 3. En consecuencia por lo anterior expuesto, han empezado a surgir algunos estándares como son la serie de guías ISO 55000/01/02, que mencionan algunas recomendaciones para gestionar los activos a lo largo del ciclo de vida de los equipos [9,10,11], donde una de las sugerencias es poder integrar el uso de indicadores técnicos con los indicadores financieros.

Fuente: El autor.
IV. Metodología técnica convencional para soluciones de compensación de potencia reactiva
Una estrategia de ahorro y eficiencia energética eléctrica en una planta es mejorar la compensación de potencia reactiva [12, 13,14], en donde los efectos no deseados por no compensar la potencia reactiva es el incremento de la potencia aparente entregada por transformadores e incrementos de corrientes en alimentadores ocasionando una degradación de la vida útil operativa de los componentes del sistema eléctrico y costos de penalizaciones significativas en las facturaciones. Una manera de abordar este problema de compensación de potencia reactiva, es mediante la medición de indicadores técnicos eléctricos como son: potencia activa, potencia reactiva, potencia aparente, factor de potencia (FP), corriente de la demanda máxima, pérdidas de energía y caída de tensión.
A. Cálculo del factor de potencia (FP)
El factor de potencia se puede calcular de diversas maneras, pero esta definido por:

donde P y S son la potencia activa y aparente trifásica de un centro de carga, dadas generalmente en kW y kVA. Una manera convencional de calcular el FP es utilizando (1) cada 5, 10 o 15 minutos durante un periodo de facturación, o mediante la energía consumida en el periodo de facturación, es decir:

Considerando una demanda de energía constante, se tiene que el factor de potencia se ve reducido conforme la potencia aparente se incremente, esto debido al incremento de potencia reactiva kVAr demandada por la carga. De esta manera el reducir el consumo de la potencia reactiva entregada por el transformador principal, mejorará considerablemente el factor de potencia.
B. Compensación de potencia reactiva mediante un banco de capacitores
Para mejorar el FP, se pueden utilizar bancos de capacitores, ya sean fijos, conexión/desconexión automática o mediante un compensador estativo de VAr (CEVs), según sean los requerimientos de potencia reactiva de la planta. El más convencional es mediante el uso de bancos de capacitores fijos, donde el cálculo de bancos de capacitores (Q en kVAr) para corregir el FP se puede calcular de la siguiente manera:

Donde:

El subíndice 1 indica el FP del sistema actual y el subdíndice 2 indica el FP del sistema deseado.
V. Indicadores de gestión de mantenimiento y económicos
El tema de indicadores de gestión en el mantenimiento es diverso, sin embargo para el presente trabajo se muestran algunos indicadores de fácil aplicación que pueden relacionarse con indicadores económicos y que posteriormente muestren la rentabilidad adecuada mediante una proyección anual de costos. Desarrollar una gestión de mantenimiento en una planta consiste en reducir la probabilidad de presencia de fallas (confiabilidad), recuperar de forma rápida y eficiente la operabilidad de los sistemas (mantenibilidad) una vez que se ha presentado la interrupción de la función, minimizar el impacto por las consecuencias de los eventos de fallas (costos por indisponibilidad). Por lo anterior mencionado, una gestión eficiente del mantenimiento busca: mejorar la continuidad operacional (disponibilidad), maximizar la rentabilidad a través de los activos (ganancias económicas) y minimizar los riesgos sobre la seguridad, ambiente y las operaciones a niveles tolerables (consecuencias de los eventos de fallas) a lo largo del ciclo de vida útil [15, 16, 17,18].
a) Indicadores técnicos de mantenimiento básicos
El tiempo promedio de operación (TPO) es un indicador que nos muestra la confiabilidad operativa mediante un promedio de tiempos de operación de un componente, máquina o sistema.

Donde TOF es el tiempo operativo hasta el fallo o hasta la sustitución programada y es el número total de fallos o sustituciones programadas en el periodo evaluado. Mediante este indicador se obtiene inversamente proporcional la frecuencia de fallos dada por la ecuación (7).

Este indicador es aplicado para el presente estudio solo al transformador y banco de capacitores.
El tiempo promedio de reparación TPPR nos muestra la mantenibilidad de un componente, máquina o sistema.

Donde el TR es el tiempo de reparación.
El tiempo promedio fuera de servicio (TPFS) es un indicador que muestra los impactos por los tiempos de reparación y tiempos fuera de control.

Donde el TFS es el tiempo fuera de servicio.
Para cadaTFSi se consideran los tiempos fuera de control (logística, imprevistos, etc.) y los tiempos promedios de reparación, como se muestra en (10):

Otro indicador utilizado es la disponibilidad operacional (Ao), el cual puede ser de varios tipos, para este estudio será considerada la disponibilidad operacional genérica (Ao) del sistema para un periodo determinado.

b) Indicador de costos por indisponibilidad en fiabilidad (CIF)
Es un indicador económico de costos que vincula los indicadores técnicos ff (falla/año) y TPFS (hr/falla) mostrando los impactos de la confiabilidad y mantenibilidad en un valor monetario anualizado [19]. Considera las penalizaciones CP (costos directos, calidad, seguridad, etc).

c) Indicador de riesgo total anualizado (RTA)
Es un indicador económico que proyecta los costos anuales y sirve para realizar una comparación de componentes/equipos/sistemas y está dado por:

Donde CI son los costos de inversión, CO son los costos de operación, en ellos van incluidos los costos por energía, insumos y materia prima, CMM son los costos de mantenimiento mayor, CMP son los costos de mantenimiento preventivo y el CIF son los costos por infiabilidad.
d) Indicador financiero EBITDA (Earning Before Interest Taxes Depreciation Amortization)
Es un indicador financiero que muestra la rentabilidad antes de intereses, impuestos y depreciaciones [19,20]. Una manera de calcularlo es como se muestra en (14).

Donde PV es el producto vendido, calculado como:

Donde IP es el ingreso potencial ($) y Ao es la disponibilidad operacional (%).
CMT son los costos de mantenimiento anuales, donde son considerados los mantenimientos preventivos, mantenimientos mayores y correctivos no programados (CIF).

CO son los costos de operación. Para el presente estudio solo son considerados los gastos de consumo de energía involucrando los costos de las penalizaciones y bonificaciones por FP.
GA son los gastos administrativos, GV son los gastos por ventas y DA es la depreciación/amortización.
Cursos recomendados






%252FImagen%252FRAMPREDYC-1730060420837.webp%3Falt%3Dmedia%26token%3D2634a7f0-988e-4022-b91f-382503e6e9db&w=3840&q=75)

VI. Caso de estudio. Compensación de potencia reactiva optimizada
El estudio presentado corresponde a un sistema eléctrico de una industria, en donde existe un transformador de 500 kVA, operando a un FP de 0.7, que alimenta una carga de 360 kW. La carga es alimentada mediante un alimentador conformado por 2 conductores por fase calibre 600 KCM con una longitud de 100 m, operando 20 horas diarias [11]. La Fig. 4 muestra el diagrama del sistema actual y del sistema propuesto con su banco de capacitores para tener un factor de potencia de 0.95 y evitar alguna penalización.

Fuente: El autor.
Para esta planta de la Fig 4, se tiene una tarifa de Gran Demanda Media Tensión Ordinaria (GDMTO), presentando los siguientes valores en la facturación mensual mostrados en la Tabla I, en dicha tabla se muestra una penalización por bajo factor de potencia.

Si ahora se calcula el banco de capacitors para un FP de 0.95 aplicando (3) se tiene:

Mediante esta solución técnica se observa en la Fig. 4 que al transformador se le libera carga, así mismo a los alimentadores se les reduce la corriente por fase IL y por ende a las corrientes de los conductores Iconductor, esto es debido a la inserción del banco de capacitores de 250 kVAr. El conductor de 600 KCM tiene una resistencia de 0.0753 Ω/km, entonces la resistencia para una distancia de 100 m es de:

Donde las pérdidas considerando la corriente en el conductor para el sistema actual es:

Y para el sistema propuesto:

Donde los siguientes valores en la facturación, como se muestran en la Tabla II, en esta tabla se observa ahora una bonificación por factor de potencia.

De esta manera se tiene una reducción del consumo de energía mensual por pérdidas en los cables de:

Lo que representa un ahorro de $16,046.64 considerando el costo por kWh de $2.85.
Para el retorno de la inversión, se considera un costo del banco de capacitores de $250,000.00, entonces el retorno simple de inversión está dado por:

Donde el retorno de la inversión es aproximadamente en dos meses:

Se menciona que esta propuesta de solución técnica no considera los impactos por confiabilidad y mantenimiento. Aplicando el modelo de gestión de mantenimiento, se puede observar que los impactos técnicos con los gerenciales tienen una relación como se muestran en la Tabla III.

Por lo anterior, utilizando el modelo mostrado en la Fig. 1, se abordan solo las tres fases, que corresponde a un problema recurrente significativo, como lo es el bajo FP.
Analizando la fase 1, se muestra una parte de un cuadro de mando integral, donde se encuentran indicadores técnicos y económicos, como se muestra en la Tabla IV.

La Tabla III muestra el impacto crítico de los transformadores y alimentadores del sistema, que es considerado en la fase 2 del modelo de gestión de mantenimiento.
El evento no deseado de un bajo FP es un problema recurrente que impacta en los objetivos gerenciales, lo que corresponde a la fase 3, en donde se ha analizado la solución técnica (banco de capacitores de 250 kVAr) sin embargo ahora considerando los impactos por confiabilidad, mantenibilidad y rentabilidad se aplican las ecuaciones mostradas anteriormente considerando los siguientes datos adicionales recabados en planta.
Para el transformador se muestran los datos en la Tabla V, en donde el costo por penalización corresponde a lo que se pierde en producción por paro total. El costo de inversión (CI) es de $750,000.00.

Los datos de los bancos de capacitores propuestos son dos, en donde se observa en la Tabla VI las características técnicas de cada uno de ellos. Se menciona que los costos de penalización se calculan en función de la facturación cuando existe la penalización por bajo FP, considerando en falla el banco de capacitores ya sea el de Tipo 1 o Tipo 2. La diferencia de los tipos de bancos de capacitores es de acuerdo a las características técnicas de mantenimiento, confiabilidad y de costos de inversión mostrados en la Tabla VI.

Con los datos anteriores se calculan los indicadores económicos como se muestra en la Tabla VII.
Analizando los CIF para cada escenario, en la condición inicial solo es considerado el transformador, en las posteriores condiciones se considera el transformador y banco de capacitores.
En el estudio del indicador RTA para cada escenario son considerados los costos de inversión de cada componente del sistema siendo $750,000.00 para el transformador, $250,000.00 para el banco de capacitores tipo 1 y $ 150,000.00 para el banco de capacitores tipo 2. Los costos de operación involucran la facturación de energía anual con penalización y bonificación por FP. Para los costos de mantenimiento preventivo (CMP) y mayor (CMM) se tiene un valor anualizado de $20,000.00 para la condición inicial y para las otras condiciones un valor de $5,000.00. El análisis del CTPF considera las características técnicas de mantenimiento y confiabilidad, en donde para la condición inicial solo se toma en cuenta el transformador y en las condiciones posteriores se considera el transformador y el banco de capacitores, haciendo énfasis en que un banco de capacitores tiene una confiabilidad y mantenibilidad apropiada y el otro no, así de esta manera se obtiene una proyección anual de costos.
Para la interpretación del indicador EBITDA que es un indicador financiero de rentabilidad, se hace énfasis en las variables PV, CMT y CO, en donde en el indicador PV se observa el impacto que produce la disponibilidad Ao que a la vez vincula con los indicadores TPO y los TPFS. En la variable CMT se observa cómo influye el indicador CIF que vincula la ff, TPFS y CP. Por último en los CO se observa cómo influye la compensación reactiva en la facturación del consumo de energía eléctrica, existiendo penalizaciones o bonificaciones. El IP y los costos de GA, GV y DA se consideran costos fijos.
En la Tabla VII se puede observar el escenario con mayor rentabilidad, que es el sistema con el banco de capacitores Tipo 1, ya que observando los costos proyectados anualmente se observa que aunque el CIF muestre un panorama mejor para la condición inicial, el RTA es el menor y el EBITDA referido a la rentabilidad es el mayor valor, esto es debido a a la consideración de los costos de operación que involucran la penalización o bonificación por FP.

VII. Conclusiones
Tener una solución técnica para problemas de compensación de potencia reactiva requiere considerar factores adicionales como son los indicadores de mantenimiento, confiabilidad y financieros, así de esta manera se permite tener criterios justificados que mejoren la rentabilidad en una planta de una manera más óptima. Mediante un modelo de gestión de mantenimiento alineado a la gestión de activos, se permite analizar problemas recurrentes mediante las tres primeras fases y poder mitigarlos de una manera optimizada, alineando la eficiencia energética eléctrica a la gestión de mantenimiento y estas dos a la gestión de activos.
VIII. Referencias
- W. Shu, X. Liu, Y. Liu “Assestment of harmonic resonance potential for shun capacitor applications”, Electric Power Systems Research 57 (2001) 97–104, September 2004.
- J. Meyer, R Stiegler. P. Schegner, I. Röder, A. Belger “Harmonic resonances in residential low-voltage networks caused by consumer electronic”,IET Journal, CIRED, Open Access Proc. J., 2017, Vol. 2017, Iss. 1, pp. 672–676
- A .F. Zooba, “Maintaining a Good Power Factor and Saving Money for Industrial Loads “, IEEE Transactions on industrial electronics, Vol. 53, No. 2, April 2006.
- M. Ahrens, Z. Konstantinovic, “Harmonic filters and power factor compensation for cement Plants”, Conference Record Cement Industry Technical Conference, Kansas, USA, 2005.
- M.Sanz, Use, Operation and Maintenance of Renewable Energy Systems, Experiences and Future Approaches, Edit. Springer, Spain, 2014, Chapter 1, Pag. 22.
- A.Crespo, V.Gozalez, J.F.Gomez, Advanced Maintenance Modelling for Asset Management Techniques and Methods for Complex Industrial Systems, Edit. Springer, Spain, 2018, Chapter 1, Pag.6.
- Z.Ma, L.Zhou, W.Sheng, “analysis of The New Asset Management Standard ISO 55000 AND PAS 55”, China International Conference on Electricity Distribution (CICED 2014), Shenzhen, 23-26 Sep. 2014.
- J.Elias, A.Romero, “Consideraciones para la Gestión de Líneas de Alta Tensión, según ISO 55000”, IEEE Biennial Congress of Argentina (ARGENCON), Mayo 2014.
- Consultora WoodHouse Partnership Ltd England, 2017, seminario de gestión de activos en la generación de energía eléctrica en México, 2017.
- S. K. Ray Mohapatra, Subrata Mukhopadhyay “Risk and Asset Management of Transmission System in a Reformed Power Sector”, Power India Conference, 2006 IEEE
- M.Shahid, M. Mahamood, N. Das “Integrated Asset Magnagement Framework for Australian Wind Farm”, Australasian Universities Power Engineering Conference– AUPEC2016.
- Acha E. Madrigal M. Power System Harmonics, Computer Modelling and Analysis, Edit. John Wiley & Sons, , UK. 2001, Pag. 65-70.
- J.C. Das, Power System Harmonics and Passive Filter Designs, Edit. John Wiley & Sons, Canada. 2005.
- Consultora IMELHIA, Caso práctico de compensación de potencia reactiva, Quintana Roo, México 2002.
- IEEE Recommended Practice for the Maintenance of Industrial and Commercial Power Systems, IEEE Std 3007.2 – 2010.
- R. Arno, N. Dowling, R.J. Schuerger, “Equipment failure characteristic and RCM for optimizing maintenance cost “, IEEE Transactions on Industry Application, Vol. 52, Issue 2, March 2016.
- IEEE Recommended Practice for Evaluating the Reliability of Existing Industrial and Commercial Power Systems, IEEE Std 3006.2™-2016.
- IEEE Recommended Practice for Collecting Data for Use in Reliability, Availability, and Maintainability Assessments of Industrial and Commercial Power Systems. IEEE Std XXX, año
- Parra C., Ingeniería de Mantenimiento y Fiabilidad aplicada en la Gestión de Activos, 2da edición edit. Ingeman, España, 2015.
- K. Kushuwan, K. Waiyamai, “ EBITDA Time Series Forecasting Case study: Provincial Waterworks Authority”, International Conference on Digital Arts, Media and Technology with ECTI Northern Section Conference on Electrical, Electronics, Computer and Telecommunications Engineering, Thailand 2019.
Autores:
R. Cetina
Instituto Tecnológico de Morelia
Morelia Michoacán, México
Correo: rubencetinaabreu@hotmail.com
Descripción: R. J. Cetina es Ingeniero Electricista egresado de la Universidad Autónoma del Carmen, Campeche, México en 2008. Obtuvo el grado de Maestro en Ingeniería Industrial, Mantenimiento y Confiabilidad en el Centro de Estudios Superiores de la Isla (CESIC), Carmen, Campeche, México, el de Maestro en Energías Renovables en el Centro de Investigaciones de Materiales Avanzados (CIMAV), en Chihuahua, México en 2014 y el grado de Doctor en Ciencias de la Ingeniería Eléctrica en el Instituto Tecnológico de Morelia (ITM) en 2020. Sus áreas de interés son calidad de la energía, ingeniería de mantenimiento y confiabilidad de sistemas eléctricos de potencia y de fuentes renovables de energía.
V. Torres
UN AM
Cd-Mx, México
Correo: v.torres.1982@ieee.org
Descripción: V. Torres-García nació en Morelia, Michoacán, se gradúo de la carrera de ingeniería eléctrica del Instituto Tecnológico de Morelia en el 2008, recibió el grado de maestro y doctor en ciencias de la ingeniería eléctrica en la misma institución en 2009 y 2014 respectivamente. Actualmente se desempeña como profesor de carrera en la facultad de ingeniería de la Universidad Nacional Autónoma de México, sus áreas de interés son sistemas eléctricos de potencia y distribución, transitorios electromagnéticos y protecciones eléctricas.
M. Madrigal
Instituto Tecnológico de Morelia
Morelia Michoacán, México
Correo: manuelmadrigal@ieee.org
Descripción: M. Madrigal es Ingeniero Electricista egresado del Instituto Tecnológico de Morelia en 1993. Obtuvo el grado de Maestro en Ciencias en Ingeniería Eléctrica en 1996 en la Universidad Autónoma de Nuevo León, México y el grado de Doctor en 2001 en la Universidad de Glasgow, Escocia. Es profesor investigador del posgrado en eléctrica del Instituto Tecnológico de Morelia desde 1996. Sus áreas de interés son calidad de la energía, análisis armónico, integración de fuentes renovables de energía a las redes eléctricas y administración de la energía.
Dinos qué te ha parecido el artículo
Artículos recomendados
Contribución del Análisis de Lubricante en tiempos de contingencia

Fricción en rodamientos

Mantenimiento programado

Entrevista a Brau Clemenza

Publica tu artículo en la revista #1 de Mantenimiento Industrial
Publicar un artículo en la revista es gratis, no tiene costo.
Solo debes asegurarte que no sea un artículo comercial.
¿Qué esperas?
O envía tu artículo directo: articulos@predictiva21.com
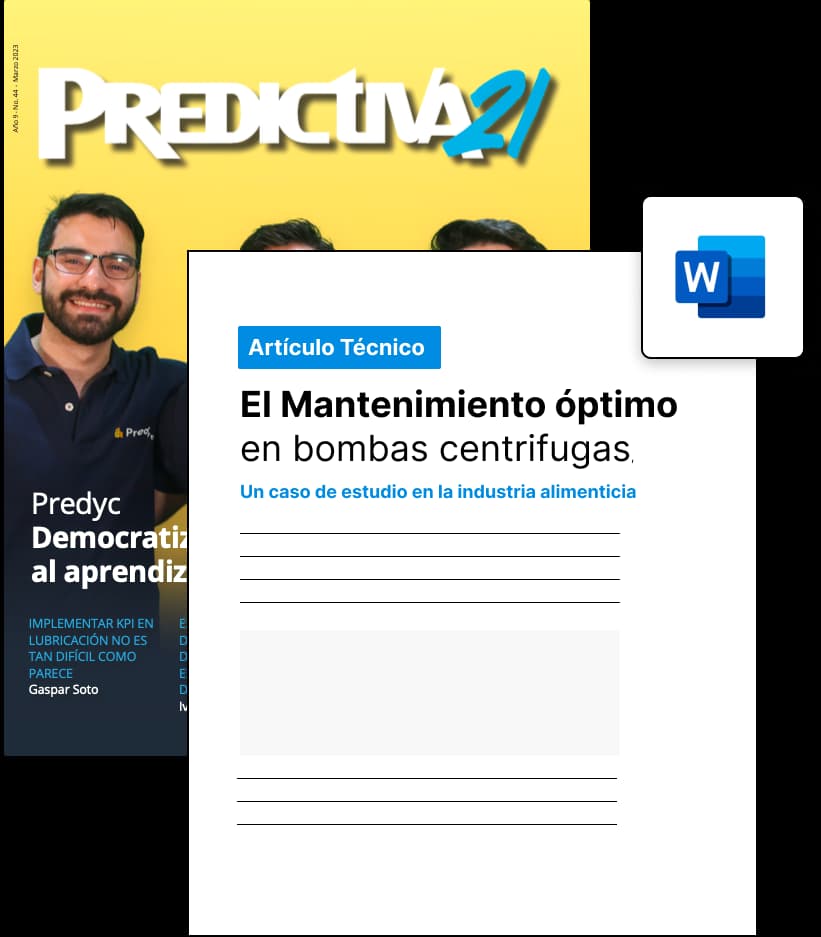