Diagramas de Pareto y de Dispersión, herramientas claves de evaluación seguimiento y control del mantenimiento
Articulo19 de junio de 2019
Estas técnicas se aplicaron en la industria siderúrgica. La herramienta utilizada fue a través de una planilla electrónica Excel 2010, a continuación se presentan los detalles de su implementación.
Generalmente en las industrias intensivas en activos físicos se realiza un control estadístico de las fallas ocurridas en un período de análisis, el cual normalmente tiene una frecuencia mensual y es parte del informe de gestión de la unidad de mantenimiento.
Salvo algunas excepciones de sectores industriales específicos, la gran mayoría tiene únicamente como indicador de fallas las horas de detención producto de fallas en los equipos a cargo. Este indicador generalmente es llamado “atraso” y se asigna a la unidad responsable de la detención.
La suma de los atrasos totales es contabilizada mensualmente y se compara con una meta pre-establecida la cual se basa en un histórico o bien en un deseable establecido por la unidad. Este indicador tiene la ventaja de ser simple y fácil de registrar e indica si se cumplió o no la meta. La desventaja fundamental es que no aporta información relevante para establecer correctamente las acciones a seguir con el objetivo de disminuir el número de fallas y el tiempo de detenciones y con ello lograr aumentar la disponibilidad operacional.
En el presente artículo se muestran y comparan dos herramientas de análisis estadístico que a partir de los datos básicos que son registrados en la industria, pueden entregar valiosa información para establecer correctas estrategias de mantenimiento y planes de acción enfocados, aumentando de esta forma la confiabilidad y disponibilidad al menor costo posible.
Desarrollo
1. Diagrama de Pareto: La ley natural de distribución de fenómenos encontrada por Vilfredo Pareto establece que el grupo minoritario del veinte por ciento posee el ochenta por ciento del fenómeno. Estas cifras son arbitrarias, y en muchos casos no son exactas y pueden variar. Por lo tanto deben ser adaptables a cada caso en particular.
En el caso de los eventos de fallas en activos físicos, el principio se lee de la siguiente forma: “Existe el veinte por ciento de los equipos que provoca el ochenta por ciento del tiempo total de detenciones producto de eventos de falla”.
Una vez encontrado los equipos que pertenecen a dicho grupo, es posible aplicar alguna metodología que permita disminuir el número y tiempos de detenciones en estos equipos. En este caso es posible aplicar RCA (Root Cause Analysis) para aquellas fallas que son repetitivas en el tiempo y que no se ha encontrado la mejor solución, lo que puede derivar en alguna modificación genética del equipo, cambio en el tipo y frecuencia del mantenimiento preventivo o bien en la aplicación de un mantenimiento predictivo dependiendo del tipo de equipo analizado, todo esto para evitar el evento falla no deseado. También es posible aplicar la metodología RCM (Reliability Centered Maintenance) el cual nos permitirá establecer la mejor estrategia de mantenimiento en base a los modos de fallas presentados o que tengan mayor probabilidad de ocurrencia con una alta consecuencia.
A continuación se muestra un ejemplo y caso estudio de la aplicación del diagrama de Pareto para un conjunto de equipos perteneciente a un laminador de barras de una empresa siderúrgica utilizando la planilla electrónica Excel 2010 para un periodo de datos de tres meses de fallas mecánicas y eléctricas en los distintos equipos. Los datos de nombres de equipos, números de eventos de falla y tiempos por equipos fueron modificados por reserva de la empresa.
Todos los equipos en análisis tienen una configuración en serie y no poseen equipos redundantes, por lo tanto se considera que el tiempo de detención de uno afecta a la detención de la línea de producción completa.
La imagen 01. “Tabla análisis Pareto de tiempos de falla de equipos” muestra en las dos primeras columnas los datos extraídos de la base de datos de la compañía correspondiente al n° de fallas y la suma de los tiempos de falla para cada equipo en el lapso de tres meses, ordenado de mayor a menor según el tiempo de falla total. La tercera columna corresponde al % de tiempo de falla calculado para cada equipo respecto al total de tiempo de falla. La última columna corresponde a la suma acumulada del % de tiempo de falla total.


Fuente: Siderúrgica CAP Acero
En este ejemplo se puede observar que la suma de los tiempos de falla total hasta el equipo 10 se obtiene un 79% del tiempo total de detenciones. Esto implica que 10 sobre 29 equipos, o en términos porcentuales, un 34% de los equipos generan el 79% de los tiempos de detenciones. En forma gráfica podemos observar el principio de Pareto aplicado a los tiempos de detenciones.

Fuente: Siderúrgica CAP Acero
Debido a los recursos de tiempo, HH, costos, especialistas etc., los cuales siempre son escasos, se debe priorizar en los equipos más críticos dentro de la selección del principio de Pareto. En este caso es recomendable analizar la guillotina de corte comercial y el laminador 18H/V que producen el 36% de las detenciones totales. El análisis debe contemplar los modos de fallos presentados y su frecuencia. Si es un modo de fallo preponderante, entonces la investigación se orienta a realizar la metodología RCA (análisis de causa raíz) y luego realizar los cambios pertinentes para disminuir o eliminar la probabilidad de ocurrencia de dicho modo de falla. Estos cambios pueden ser tal como variación en el diseño, mejora en el material, cambio en la estrategia de mantenimiento, restitución a condición estándar operativa, etc. Por el contrario, si se presentan múltiples modos de fallo con igual o similares frecuencias entonces sería aconsejable aplicar un RCM (Mantenimiento centrado en la confiabilidad) el cual permitiría verificar las respectivas probabilidades y consecuencias de cada modo de fallo y de esta forma realizar una mejora según la importancia de cada una.
Para el control, seguimiento y evaluación de las acciones correctivas es necesario realizar mensual o trimestralmente el análisis de Pareto para verificar si disminuyeron los tiempos de detención y si entraron nuevos equipos al veinte por ciento que generan el ochenta por ciento del tiempo de detención.
2. Diagrama de Dispersión: El diagrama de Pareto antes mostrado, indica tiempos totales de detenciones pero no precisa información sobre la frecuencia de estas. A modo de ejemplo podemos tener un equipo que sólo detuvo una vez y su detención llevó un considerable tiempo de reparación y por otro lado podemos tener otro equipo que tuvo múltiples detenciones y en cada detención ocupó un bajo tiempo de reparación. Los dos equipos tienen similar tiempo total de detención pero estas ocurrieron de distintas maneras. Por esta razón el diagrama de dispersión toma importancia debido a que puede diferenciar estos dos tipos de fenómenos.
El diagrama de dispersión que se analizará es el diagrama Jack Knife. A partir de la imagen 03 “Tabla análisis dispersión de tiempos y frecuencias de falla de equipos” y considerando los datos de números de fallas y tiempo de falla total por equipo, se tienen las siguientes relaciones que se graficarán en Excel 2010.

Fuente: Siderúrgica CAP Acero
Siendo: El eje de las ordenadas corresponderá al MTTR y el eje de las abscisas al número de fallas.

Cada cuadrante tiene la siguiente denominación:
Cuadrante Crónico-Agudo: Es aquel en donde se agrupan los equipos que poseen alto número de fallas y un elevado MTTR. (Baja confiabilidad y mantenibilidad).
Cuadrante Crónico: Es aquel en donde se agrupan los equipos que poseen un alto número de detenciones y un bajo MTTR. (Baja confiabilidad).
Cuadrante Agudo: Es aquel en donde se agrupan los equipos que poseen un bajo número de fallas y un elevado MTTR. (Baja mantenibilidad).
Cuadrante Leve: Es aquel en donde se agrupan los equipos que poseen un bajo número de fallas y un bajo MTTR.
El diagrama de dispersión Jack Knife se grafica en escala logarítmica para mejor visualización de los resultados.
Además se grafican las curvas de iso-no disponibilidad. En este ejemplo se trazaron cuatro curvas correspondiente a la no disponibilidad de 100, 200, 500 y 1000 minutos. Para esto se ocupa una tabla estándar según las curvas que se deseen graficar:

Fuente: Siderúrgica CAP Acero
Ocupando el gráfico de dispersión de Excel, se relaciona el MTTR (tiempo medio para reparar) con el número de fallas para cada equipo el cual se muestra en la imagen 05 “Gráfico análisis dispersión de tiempos y frecuencia de falla de equipos”.

Fuente: Siderúrgica CAP Acero
Se puede apreciar que el equipo 1 está sobre la curva de no disponibilidad de 1000 minutos. Esto significa que en los tres meses de análisis, dicho equipo estuvo más de 1000 minutos en estado de falla.
El equipo 2 está entre la iso-no disponibilidad de 500 y 1000 minutos y los equipos 3 al 9 están entre la iso-no disponibilidad de 200 y 500 minutos.
Según la clasificación por cuadrante, se obtuvo lo siguiente:
- Cuadrante Crónico-Agudo: Equipos 1, 2, 5 y 6.
- Cuadrante Crónico: Equipos 3, 8, 10,16, 18 y 19.
- Cuadrante Agudo: Equipos 4, 7, 9 y 14.
- Cuadrante Leve: Todo el resto de equipos.
Acá se puede apreciar claramente una diferencia entre los equipos 6, 7 y 8, los cuales tienen similares tiempos de fallas (en torno a los 260 min), pero de comportamiento diferente. El equipo 6 está en el cuadrante crónico-agudo, el equipo 7 en el cuadrante agudo y el equipo 8 en el cuadrante crónico.

Fuente: Siderúrgica CAP Acero
Esto significa que la naturaleza de las fallas en estos equipos es diferente y por ende deben tener una estrategia de acción diferente. En particular el transportador hidráulico barras, el cual está en el cuadrante agudo, posee bajo número de fallas y un alto tiempo de reparación. Esto implica que la reparación es más complicada y la gestión debería orientarse en eliminar o disminuir la probabilidad de ocurrencia de ese modo de falla a partir de un RCA (análisis de causa raíz).
Al contrario del equipo estación atadora, el cual está en el cuadrante crónico, posee un alto número de fallas y bajo MTTR. Esto significa que las reparaciones son rápidas pero el equipo falla reiteradamente y el equipo puede ser catalogado de baja confiabilidad. En este caso, la estrategia de acción es revisar los modos de fallas presentados. Si son múltiples los modos de fallas presentados se sugiere aplicar la metodología RCM y si solo es un modo de falla preponderante entonces se puede aplicar la metodología RCA.
De todas formas, considerando las limitaciones de recursos disponibles, se sugiere comenzar el análisis y orientar el presupuesto hacia los equipos que están en el cuadrante crónico-agudo. Luego se deberá ir controlando mensual o trimestralmente la evolución de estos equipos en el diagrama Jack Knife. De esta forma se verificará si las acciones realizadas ayudan a disminuir los tiempos y número de fallas.
Cursos recomendados






%252FImagen%252FRAMPREDYC-1730060420837.webp%3Falt%3Dmedia%26token%3D2634a7f0-988e-4022-b91f-382503e6e9db&w=3840&q=75)

Conclusión
Según los datos que se recopilan en la industria, se verifica que para el análisis de tiempos de fallas o “atrasos”, es aconsejable utilizar el diagrama de dispersión Jack Knife, debido a que entrega valiosa información del fenómeno falla, clasificando estas según el comportamiento en base a la duración y frecuencia de los eventos.
La clasificación resultante permite establecer planes de acción y metodologías a aplicar según el comportamiento del fenómeno y de esta forma asignar correctamente los recursos existentes. Por otro lado permite definir prioridades en la delimitación de la estrategia a implementar, enfocando tiempo y presupuesto en los equipos del cuadrante crónico-agudo que superen determinada iso-no disponibilidad.
Aunque el diagrama Jack Knife contiene los resultados del diagrama de Pareto, de igual forma es aconsejable aplicar primeramente el principio de Pareto para obtener de forma rápida la condición de los equipos y ver la existencia de equipos que se alejan demasiado del comportamiento de la mayoría.
Referencias
- Diagramas de Pareto: https://es.wikipedia.org/wiki/Diagrama_de_Pareto Bibliografía
- Moubray, John; “Reliability Centred Maintenance (RCM)”. Industrial Press Inc. New York, 2nd ed. 1997.
- Keith Mobley, R; “Maintenance Engineering Handbook”. McGraw-Hill, 7a ed. 2008.
Autor: MSc. Ing José Luis Muñoz Pincheira
Jefe de Ing. de Mantenimiento Cap Acero
Talcahuano, Chile
Correo: joseluismunoz@gmail.com
Dinos qué te ha parecido el artículo
Artículos recomendados
Hablemos de Confiabilidad, Disponibilidad, Mantenibilidad, Seguridad y Riesgo de Activos

Experiencias en el desarrollo de Análisis de Confiabilidad, Disponibilidad y Mantenibilidad (Análisis RAM).

Metodología Propuesta para Toma de Decisión de Inspección de Líneas de Flujo de Crudo Basado en Modelos Estadísticos de Criticidad

ICA Fluor O&M invierté en +5,000 horas de capacitación para su equipo de Mantenimiento, que incluye profesionales técnicos, supervisores y gerentes con PREDYC

Publica tu artículo en la revista #1 de Mantenimiento Industrial
Publicar un artículo en la revista es gratis, no tiene costo.
Solo debes asegurarte que no sea un artículo comercial.
¿Qué esperas?
O envía tu artículo directo: articulos@predictiva21.com
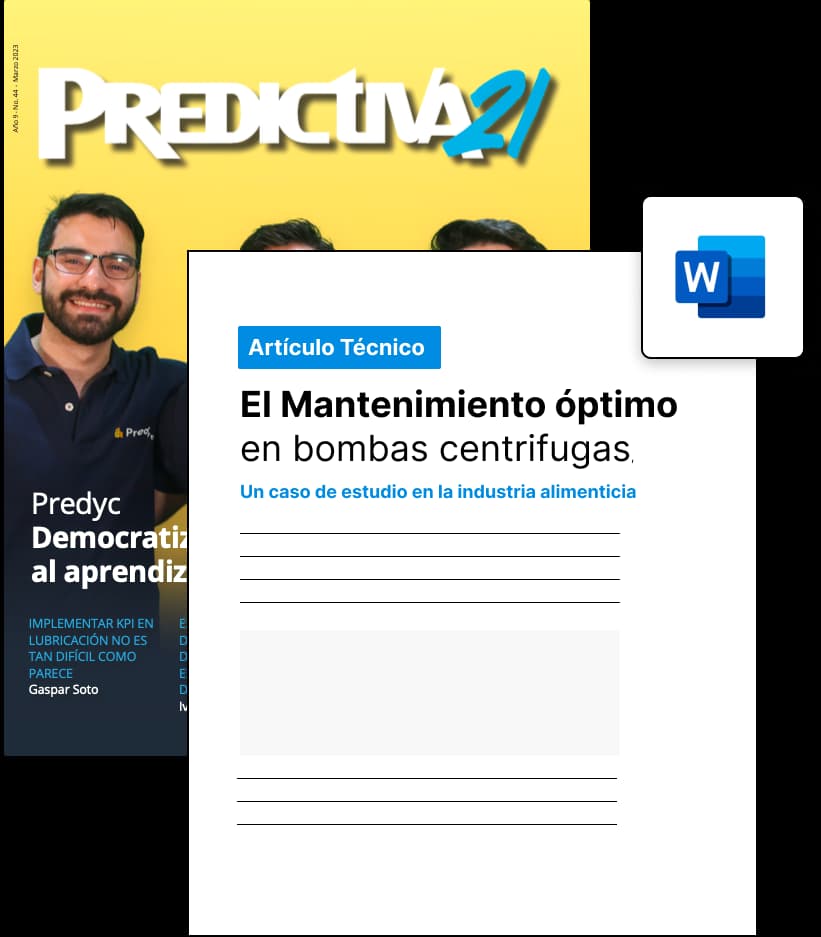
Diagramas de Pareto y de Dispersión, herramientas claves de evaluación seguimiento y control del mantenimiento
Articulo 19 de junio de 2019Estas técnicas se aplicaron en la industria siderúrgica. La herramienta utilizada fue a través de una planilla electrónica Excel 2010, a continuación se presentan los detalles de su implementación.
Generalmente en las industrias intensivas en activos físicos se realiza un control estadístico de las fallas ocurridas en un período de análisis, el cual normalmente tiene una frecuencia mensual y es parte del informe de gestión de la unidad de mantenimiento.
Salvo algunas excepciones de sectores industriales específicos, la gran mayoría tiene únicamente como indicador de fallas las horas de detención producto de fallas en los equipos a cargo. Este indicador generalmente es llamado “atraso” y se asigna a la unidad responsable de la detención.
La suma de los atrasos totales es contabilizada mensualmente y se compara con una meta pre-establecida la cual se basa en un histórico o bien en un deseable establecido por la unidad. Este indicador tiene la ventaja de ser simple y fácil de registrar e indica si se cumplió o no la meta. La desventaja fundamental es que no aporta información relevante para establecer correctamente las acciones a seguir con el objetivo de disminuir el número de fallas y el tiempo de detenciones y con ello lograr aumentar la disponibilidad operacional.
En el presente artículo se muestran y comparan dos herramientas de análisis estadístico que a partir de los datos básicos que son registrados en la industria, pueden entregar valiosa información para establecer correctas estrategias de mantenimiento y planes de acción enfocados, aumentando de esta forma la confiabilidad y disponibilidad al menor costo posible.
Desarrollo
1. Diagrama de Pareto: La ley natural de distribución de fenómenos encontrada por Vilfredo Pareto establece que el grupo minoritario del veinte por ciento posee el ochenta por ciento del fenómeno. Estas cifras son arbitrarias, y en muchos casos no son exactas y pueden variar. Por lo tanto deben ser adaptables a cada caso en particular.
En el caso de los eventos de fallas en activos físicos, el principio se lee de la siguiente forma: “Existe el veinte por ciento de los equipos que provoca el ochenta por ciento del tiempo total de detenciones producto de eventos de falla”.
Una vez encontrado los equipos que pertenecen a dicho grupo, es posible aplicar alguna metodología que permita disminuir el número y tiempos de detenciones en estos equipos. En este caso es posible aplicar RCA (Root Cause Analysis) para aquellas fallas que son repetitivas en el tiempo y que no se ha encontrado la mejor solución, lo que puede derivar en alguna modificación genética del equipo, cambio en el tipo y frecuencia del mantenimiento preventivo o bien en la aplicación de un mantenimiento predictivo dependiendo del tipo de equipo analizado, todo esto para evitar el evento falla no deseado. También es posible aplicar la metodología RCM (Reliability Centered Maintenance) el cual nos permitirá establecer la mejor estrategia de mantenimiento en base a los modos de fallas presentados o que tengan mayor probabilidad de ocurrencia con una alta consecuencia.
A continuación se muestra un ejemplo y caso estudio de la aplicación del diagrama de Pareto para un conjunto de equipos perteneciente a un laminador de barras de una empresa siderúrgica utilizando la planilla electrónica Excel 2010 para un periodo de datos de tres meses de fallas mecánicas y eléctricas en los distintos equipos. Los datos de nombres de equipos, números de eventos de falla y tiempos por equipos fueron modificados por reserva de la empresa.
Todos los equipos en análisis tienen una configuración en serie y no poseen equipos redundantes, por lo tanto se considera que el tiempo de detención de uno afecta a la detención de la línea de producción completa.
La imagen 01. “Tabla análisis Pareto de tiempos de falla de equipos” muestra en las dos primeras columnas los datos extraídos de la base de datos de la compañía correspondiente al n° de fallas y la suma de los tiempos de falla para cada equipo en el lapso de tres meses, ordenado de mayor a menor según el tiempo de falla total. La tercera columna corresponde al % de tiempo de falla calculado para cada equipo respecto al total de tiempo de falla. La última columna corresponde a la suma acumulada del % de tiempo de falla total.


Fuente: Siderúrgica CAP Acero
En este ejemplo se puede observar que la suma de los tiempos de falla total hasta el equipo 10 se obtiene un 79% del tiempo total de detenciones. Esto implica que 10 sobre 29 equipos, o en términos porcentuales, un 34% de los equipos generan el 79% de los tiempos de detenciones. En forma gráfica podemos observar el principio de Pareto aplicado a los tiempos de detenciones.

Fuente: Siderúrgica CAP Acero
Debido a los recursos de tiempo, HH, costos, especialistas etc., los cuales siempre son escasos, se debe priorizar en los equipos más críticos dentro de la selección del principio de Pareto. En este caso es recomendable analizar la guillotina de corte comercial y el laminador 18H/V que producen el 36% de las detenciones totales. El análisis debe contemplar los modos de fallos presentados y su frecuencia. Si es un modo de fallo preponderante, entonces la investigación se orienta a realizar la metodología RCA (análisis de causa raíz) y luego realizar los cambios pertinentes para disminuir o eliminar la probabilidad de ocurrencia de dicho modo de falla. Estos cambios pueden ser tal como variación en el diseño, mejora en el material, cambio en la estrategia de mantenimiento, restitución a condición estándar operativa, etc. Por el contrario, si se presentan múltiples modos de fallo con igual o similares frecuencias entonces sería aconsejable aplicar un RCM (Mantenimiento centrado en la confiabilidad) el cual permitiría verificar las respectivas probabilidades y consecuencias de cada modo de fallo y de esta forma realizar una mejora según la importancia de cada una.
Para el control, seguimiento y evaluación de las acciones correctivas es necesario realizar mensual o trimestralmente el análisis de Pareto para verificar si disminuyeron los tiempos de detención y si entraron nuevos equipos al veinte por ciento que generan el ochenta por ciento del tiempo de detención.
2. Diagrama de Dispersión: El diagrama de Pareto antes mostrado, indica tiempos totales de detenciones pero no precisa información sobre la frecuencia de estas. A modo de ejemplo podemos tener un equipo que sólo detuvo una vez y su detención llevó un considerable tiempo de reparación y por otro lado podemos tener otro equipo que tuvo múltiples detenciones y en cada detención ocupó un bajo tiempo de reparación. Los dos equipos tienen similar tiempo total de detención pero estas ocurrieron de distintas maneras. Por esta razón el diagrama de dispersión toma importancia debido a que puede diferenciar estos dos tipos de fenómenos.
El diagrama de dispersión que se analizará es el diagrama Jack Knife. A partir de la imagen 03 “Tabla análisis dispersión de tiempos y frecuencias de falla de equipos” y considerando los datos de números de fallas y tiempo de falla total por equipo, se tienen las siguientes relaciones que se graficarán en Excel 2010.

Fuente: Siderúrgica CAP Acero
Siendo: El eje de las ordenadas corresponderá al MTTR y el eje de las abscisas al número de fallas.

Cada cuadrante tiene la siguiente denominación:
Cuadrante Crónico-Agudo: Es aquel en donde se agrupan los equipos que poseen alto número de fallas y un elevado MTTR. (Baja confiabilidad y mantenibilidad).
Cuadrante Crónico: Es aquel en donde se agrupan los equipos que poseen un alto número de detenciones y un bajo MTTR. (Baja confiabilidad).
Cuadrante Agudo: Es aquel en donde se agrupan los equipos que poseen un bajo número de fallas y un elevado MTTR. (Baja mantenibilidad).
Cuadrante Leve: Es aquel en donde se agrupan los equipos que poseen un bajo número de fallas y un bajo MTTR.
El diagrama de dispersión Jack Knife se grafica en escala logarítmica para mejor visualización de los resultados.
Además se grafican las curvas de iso-no disponibilidad. En este ejemplo se trazaron cuatro curvas correspondiente a la no disponibilidad de 100, 200, 500 y 1000 minutos. Para esto se ocupa una tabla estándar según las curvas que se deseen graficar:

Fuente: Siderúrgica CAP Acero
Ocupando el gráfico de dispersión de Excel, se relaciona el MTTR (tiempo medio para reparar) con el número de fallas para cada equipo el cual se muestra en la imagen 05 “Gráfico análisis dispersión de tiempos y frecuencia de falla de equipos”.

Fuente: Siderúrgica CAP Acero
Se puede apreciar que el equipo 1 está sobre la curva de no disponibilidad de 1000 minutos. Esto significa que en los tres meses de análisis, dicho equipo estuvo más de 1000 minutos en estado de falla.
El equipo 2 está entre la iso-no disponibilidad de 500 y 1000 minutos y los equipos 3 al 9 están entre la iso-no disponibilidad de 200 y 500 minutos.
Según la clasificación por cuadrante, se obtuvo lo siguiente:
- Cuadrante Crónico-Agudo: Equipos 1, 2, 5 y 6.
- Cuadrante Crónico: Equipos 3, 8, 10,16, 18 y 19.
- Cuadrante Agudo: Equipos 4, 7, 9 y 14.
- Cuadrante Leve: Todo el resto de equipos.
Acá se puede apreciar claramente una diferencia entre los equipos 6, 7 y 8, los cuales tienen similares tiempos de fallas (en torno a los 260 min), pero de comportamiento diferente. El equipo 6 está en el cuadrante crónico-agudo, el equipo 7 en el cuadrante agudo y el equipo 8 en el cuadrante crónico.

Fuente: Siderúrgica CAP Acero
Esto significa que la naturaleza de las fallas en estos equipos es diferente y por ende deben tener una estrategia de acción diferente. En particular el transportador hidráulico barras, el cual está en el cuadrante agudo, posee bajo número de fallas y un alto tiempo de reparación. Esto implica que la reparación es más complicada y la gestión debería orientarse en eliminar o disminuir la probabilidad de ocurrencia de ese modo de falla a partir de un RCA (análisis de causa raíz).
Al contrario del equipo estación atadora, el cual está en el cuadrante crónico, posee un alto número de fallas y bajo MTTR. Esto significa que las reparaciones son rápidas pero el equipo falla reiteradamente y el equipo puede ser catalogado de baja confiabilidad. En este caso, la estrategia de acción es revisar los modos de fallas presentados. Si son múltiples los modos de fallas presentados se sugiere aplicar la metodología RCM y si solo es un modo de falla preponderante entonces se puede aplicar la metodología RCA.
De todas formas, considerando las limitaciones de recursos disponibles, se sugiere comenzar el análisis y orientar el presupuesto hacia los equipos que están en el cuadrante crónico-agudo. Luego se deberá ir controlando mensual o trimestralmente la evolución de estos equipos en el diagrama Jack Knife. De esta forma se verificará si las acciones realizadas ayudan a disminuir los tiempos y número de fallas.
Cursos recomendados






%252FImagen%252FRAMPREDYC-1730060420837.webp%3Falt%3Dmedia%26token%3D2634a7f0-988e-4022-b91f-382503e6e9db&w=3840&q=75)

Conclusión
Según los datos que se recopilan en la industria, se verifica que para el análisis de tiempos de fallas o “atrasos”, es aconsejable utilizar el diagrama de dispersión Jack Knife, debido a que entrega valiosa información del fenómeno falla, clasificando estas según el comportamiento en base a la duración y frecuencia de los eventos.
La clasificación resultante permite establecer planes de acción y metodologías a aplicar según el comportamiento del fenómeno y de esta forma asignar correctamente los recursos existentes. Por otro lado permite definir prioridades en la delimitación de la estrategia a implementar, enfocando tiempo y presupuesto en los equipos del cuadrante crónico-agudo que superen determinada iso-no disponibilidad.
Aunque el diagrama Jack Knife contiene los resultados del diagrama de Pareto, de igual forma es aconsejable aplicar primeramente el principio de Pareto para obtener de forma rápida la condición de los equipos y ver la existencia de equipos que se alejan demasiado del comportamiento de la mayoría.
Referencias
- Diagramas de Pareto: https://es.wikipedia.org/wiki/Diagrama_de_Pareto Bibliografía
- Moubray, John; “Reliability Centred Maintenance (RCM)”. Industrial Press Inc. New York, 2nd ed. 1997.
- Keith Mobley, R; “Maintenance Engineering Handbook”. McGraw-Hill, 7a ed. 2008.
Autor: MSc. Ing José Luis Muñoz Pincheira
Jefe de Ing. de Mantenimiento Cap Acero
Talcahuano, Chile
Correo: joseluismunoz@gmail.com
Dinos qué te ha parecido el artículo
Artículos recomendados
Redes de conocimiento AMGA

La Actitud y Aptitud del Mantenimiento

Big Data en Mantenimiento de Planta

¿Qué nos perdemos si ignoramos la estrategia predictiva?

Publica tu artículo en la revista #1 de Mantenimiento Industrial
Publicar un artículo en la revista es gratis, no tiene costo.
Solo debes asegurarte que no sea un artículo comercial.
¿Qué esperas?
O envía tu artículo directo: articulos@predictiva21.com
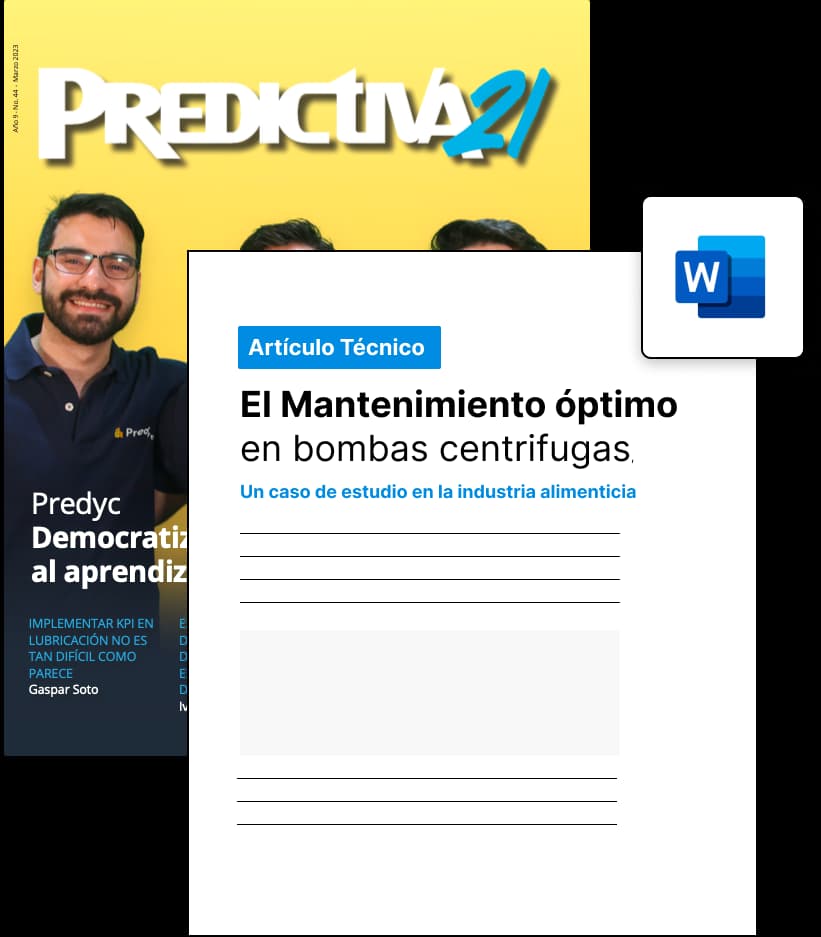