¿Cómo serán las fábricas dentro de una década? La transformación progresiva hacia la Smart Factory
Articulo16 de agosto de 2021
Este artículo es el primero de varios a modo de capítulos, donde se visionará cómo serán las fábricas a 10 años vista (centrándonos en las de estampación). Lo haremos pronosticando desde el punto de vista de TECNOLOGÍAS, pues la Industria4.0 o Cuarta Revolución Industrial va principalmente de tecnologías disruptivas; pero también de PERSONAS con talento, y de qué perfiles y habilidades requerirán estas futuras fábricas inteligentes.
Estructuraremos los capítulos tecnológicos bajo las 3 etapas principales de cómo una fábrica evolucionará desde a día de hoy hasta transformarse progresivamente en una fábrica inteligente (smart factory). Y también considerando el vector de Automatización avanzada, así como las infraestructuras IT & Telecom & CiberSeguridad.
La Industria4.0 va de tecnologías disruptivas y personas con habilidades concretas.
Más información: Los 3 estados de transformación progresiva.
No hay un único estado actual común en todas las fábricas. Cada una de ellas ha ido evolucionando estos últimos 20 años, implementando gradualmente nuevas tecnologías de la 3ª revolución industrial.
E incluso, dentro de una misma fábrica, no suele existir una homogeneización tecnológica. Por ejemplo, en el mundo Estampación para la Automoción es muy normal encontrarte con fábricas con Sistemas de Gestión de Almacén (SGA) más o menos fiables (“lo que debería haber en el almacén Vs. lo que realmente hay”) pero es menos frecuente ver implementaciones de Sistemas de Mantenimiento (GMAO) o Sistemas de Monitorización & Control de la producción (MES). Haciendo un símil con la industria automovilística, el parque de coches en España incluye vehículos de hace 15 años hasta los actuales vehículos cargados de sensores y cámaras para aparcamiento en automático, control de velocidad de crucero, luces en automático, etc. Todos conviviendo en la ciudad y carreteras.
Dentro de una misma fábrica no suele existir una homogeneización tecnológica.
Por último, existen otros aspectos que justifican la actual heterogeneidad de las fábricas de estampación. No es lo mismo una planta capacitada para estampación de piezas grandes respecto refuerzos y piezas pequeñas, o líneas de estampación bajo bobina que alimentación en formato, o con procesos de estampación en caliente respecto los convencionales en frío, o estampar aceros respecto aluminio, por ejemplo. Todo ello condiciona muchísimo la tipología de fábrica, tecnologías3.0 que dispone y qué necesitará en un futuro para aumentar la competitividad de fabricación.
Por este motivo es una falacia el vender a modo de “receta única” una hoja de ruta universal para cualquier fábrica de cómo debe pasar de ser una planta productiva convencional a una fábrica Smart. Lamentablemente empiezan a haber “vendedores de elixires de la juventud” pero esto no va de una pastilla mágica que vale para todo y para todos.
Estamos hablando de proyectos “a la carta” porque cada fábrica es un mundo, eso sí, bajo una metodología y un plan maestro como el que el autor plantea en esta serie de artículos: proyectos de digitalización de la fábrica, proyectos de conectividad y proyectos de dotar de inteligencia autónoma; junto a proyectos de automatización / robotización de las operaciones y, por último, dotar a la fábrica de infraestructuras IT-Telecomunicaciones-CiberSeguridad (Tecnologías “Cross”).
No existe una hoja de ruta universal para convertirse en una Smart factory.
Los artículos que se proponen son genéricos pero centrados al sector de la estampación, que lógicamente tiene sus singularidades respecto la inyección de plástico, por ejemplo. Ambos tienen sus propias diferencias pero con aspectos comunes pues son procesos de manufactura cíclicos, lo cual implica que algunas de las tecnologias4.0 que se detallarán sean válidas para ambos sectores y otros. Pero no “reutilizables” en plantas con procesos continuos como cementeras, refinerías, etc.
Capítulo 1: ¿Cómo serán las fábricas del futuro?
En el 2030, ¿cómo serán las fábricas de estampación de componentes metálicos para las carrocerías de vehículo?
Se plantea solamente a 10 años vista porque si tratamos de visualizar más allá… quién sabe si los coches se seguirán carroceando con materiales metálicos dados los nuevos materiales que ya se están desarrollando, o las nuevas maneras de producción (fabricación aditiva / Impresión 3D por ejemplo). O dada la evolución imparable del vehículo eléctrico-conectado-compartido-autónomo, ¿se requerirán elementos estructurales muchísimo más ligeros (como propone la estampación en caliente) y con métodos de conformación y de unión más simples, alejándonos de matrices, estampación y soldadura?
Pensando en que evolucione de una manera incremental y no disruptiva, bajo innovación de procesos y no de producto, todo apunta a que las fábricas de estampación y soldadura que serán competitivas en el 2030 dispondrán de:
- Sistemas de alimentación en automático, desde el proveedor de materia prima (sobre todo bobinas) suministrando en JIT (Just in Time) y entregando el material hasta la cabecera de la prensa.
- Para ello, será indispensable disponer de un sistema de control de la producción integrado al sistema de planificación y su aprovisionamiento de materias primas.
- Una flota de AGV y otros vehículos autónomos que gestionen automáticamente todo el movimiento en interno de la planta (logística inHouse).
- Sistema de cambio automático de las matrices, eliminando actividades manuales que son ineficientes en cuanto a productividad y Eficiencia General de los Equipos (OEE) de las prensas.
- Un sistema inteligente que en función de las características del material en la prensa (información que suministrará el proveedor de materia prima junto al suministro físico), la prensa realice en automático los ajustes necesarios de sus parámetros, para producir correctamente sin defectos. Eliminando así los ajustes de prensa que son realizados a día de hoy de manera manual.
- Una monitorización a tiempo real e inteligente, basada en un sistema “Gemelo Digital”, que controle todas las variables del proceso de estampación (considerando también los consumos energéticos), conforme están en los umbrales correctos.
- Un control total de la calidad del producto acabado, mediante la inspección en línea y a ciclo productivo para el 100% de las piezas y el 100% de su geometría, basado en Visión e Inteligencia Artificial a final de cada línea de estampación.
- Respecto al mantenimiento de este parque de maquinaria tan sofisticada, será necesario de un sistema total de sensorización de matrices y prensas, de manera que sean éstas quienes informen al equipo humano a nivel predictivo.
Capítulo 2: Aprovisionamiento de materias primas
En 2010 nació la generación alpha (α), la segunda completamente digital junto con la Z. Los futuros consumidores no habrán conocido otra forma de comunicarse ni trabajar que no sea esa, ni la aceptarán. Actualmente estamos frente a un cliente cada vez más digitalizado que está causando la revolución en las Cadenas de Suministro, “obligándolas” a digitalizar y conectar todos sus eslabones, ofreciéndole 100% trazabilidad, transparencia y visibilidad, información a tiempo real, etc. La compra online, con plataformas eComerce cada vez más potentes, así como las campañas de Marketing tipo “Black Friday”, condicionan que sean las fábricas y centros logísticos el factor limitante de venta; es decir, los activos que limitan la CAPACIDAD y FLEXIBILIDAD asumible. Y de ahí que todo lo que sea implementar tecnologías de la Industria 4.0 en tales centros para aumentar sus prestaciones, son bienvenidas.
Se puede hablar del concepto Digital B2B2C, en el caso de una pequeña cadena de suministro formada por un proveedor inicial que entrega al nivel1 y este es quien genera la venta directa al consumidor/cliente. Por tanto, en función del tamaño de la cadena, definiríamos B2B2B…B2C, siendo el número de “B´s” los proveedores que forman los eslabones de la cadena.
Hoy en día se habla mucho de evolucionar la SCM a Cadena de Valor, eliminado toda “B” que no aporta nada o muy poco y con ello, reducir la distancia del consumidor (C) con el que le genera el producto/servicio (el valor). Esta tendencia explica por qué el 30% de pymes va a desaparecer, por cuantificar un porcentaje medio, empresas que están en eslabones de poco valor y “alejadas” del consumidor final.
En este capítulo expondremos una serie de oportunidades de mejora que demanda el sector de la estampación automoción, agrupadas en tres grandes bloques que tienen estrecha relación con los proveedores de Materia Prima:
1. Todo lo que tiene que ver con la PLANIFICACIÓN Y CONTROL
- Planificación de todos los recursos: MP, contenedores, plantilla…
- Secuenciación ágil y eficiente de los pedidos. Posibilidad de simular escenarios ante imprevistos.
- Alineación de la planificación de las entregas desde el plan inicial.
- Trazabilidad online y real time. Anticipación gracias a la predicción.
2. Todo lo que tiene que ver con el APROVISIONAMIENTO DE MATERIA PRIMA
- Procedimientos manuales: trámites lentos, papel, errores humanos.
- Mejorar el control de la calidad en la recepción de la MP.
- Trazabilidad de la MP desde su origen (la fábrica del proveedor MP).
- Sincronizar los aprovisionamientos del Proveedor con la producción del estampador.
3. Todo lo que tiene que ver con la CALIDAD
- Gestión calidad en todo proceso completo.
- Seguimiento por lote y por pieza unitaria.
- Trazabilidad desde la MP hasta la pieza estampada PA (producto acabado).
Detallemos un poco más las dos primeras oportunidades de mejora que tienen los estampadores en esta nueva década 2020.
Planificación y control
El inicio de la planificación del estampador es la demanda de los clientes finales (por lo general, OEM´S), que generarán los pedidos a la planta. Estos “disparan” la planificación de todos los recursos del estampador, destacando las materias primas, los operarios, los contenedores y por descontando, la línea de prensas y las matrices.
Hoy en día, la planificación cada vez plantea situaciones más complejas, con múltiples consideraciones como la MP en diferentes formatos, contenedores homologados para las piezas, operarios capacitados y habilitados.
Y se requiere mayor agilidad y flexibilidad en la secuenciación de pedidos, pues son cada vez más frecuentes los cambios de última hora en la demanda. La posibilidad de hacer un seguimiento online de los principales KPI´s de la producción, y retroalimentando en real-time las opciones de planificación.
Aprovisionamiento de materia prima
Las tareas de recepción son mayoritariamente manuales y consumen grandes cantidades de papel, que pueden comportar errores que impactan en todo el flujo “aguas abajo”. Además, implican “tiempos de espera” entre la recepción física de materiales y su registro informático.
Sería interesante disponer de un control online y sin errores de los inventarios de materia prima.
Por otra banda, los clientes de los estampadores cada vez son más exigentes en cuanto a conocer la trazabilidad de la materia prima.
Y, por último, se necesita incrementar la integración online con proveedores, sincronizando el aprovisionamiento y teniendo en cuenta la situación real de producción.
Si analizamos estos 3 grandes bloques desde la perspectiva de las tecnologías 4.0 y tendencias en la SCM, se trata de evolucionar la relación Cliente-Proveedor de aceros hacia el desarrollo de una CADENA DE VALOR ÁGIL, CONECTADA E INTELIGENTE. Estableciendo nuevas relaciones de fidelización del proveedor de Materia Prima con los estampadores, basadas en formato digital.
“No se trata de CÓMO SE FABRICA sino de CÓMO SE SIRVE A LOS CLIENTES”.
Y en este sentido, los podemos agrupar en dos grandes retos tecnológicos:
1) Relacionado con la LOGISTICA INBOUND: el propio suministro físico (por lotes, etc.), la planificación y programación_fina cliente-proveedor, los sistemas de comunicación, Trazabilidad-geolocalización de inicio a fin (incluyendo transporte) Online/Tiempo_real, etc. 2) Relacionado con la FICHA DIGITAL DEL PRODUCTO: la información de los productos suministrados. Todo lo que tiene que ver con el certificado de materiales, su composición y sus propiedades mecánicas de cada bobina o lote de fabricación de formatos. En formato digital en Online/Tiempo_real.
Autor: Toni Laserna García
Experto en Transformación Digital en la Industria.
Correo: tlaserna@logikaservices.com
Sitio Web: https://applitechgnosis.website/
LinkedIn: https://www.linkedin.com/in/tlaserna/
Dinos qué te ha parecido el artículo
Artículos recomendados
Precursores de la ingeniería industrial

Operación de plantas industriales: Una guía de gestión eficiente

Educación Formal para el Mantenimiento

Vibraciones Mecánicas: Herramienta de análisis del comportamiento dinámico de equipos

Publica tu artículo en la revista #1 de Mantenimiento Industrial
Publicar un artículo en la revista es gratis, no tiene costo.
Solo debes asegurarte que no sea un artículo comercial.
¿Qué esperas?
O envía tu artículo directo: articulos@predictiva21.com
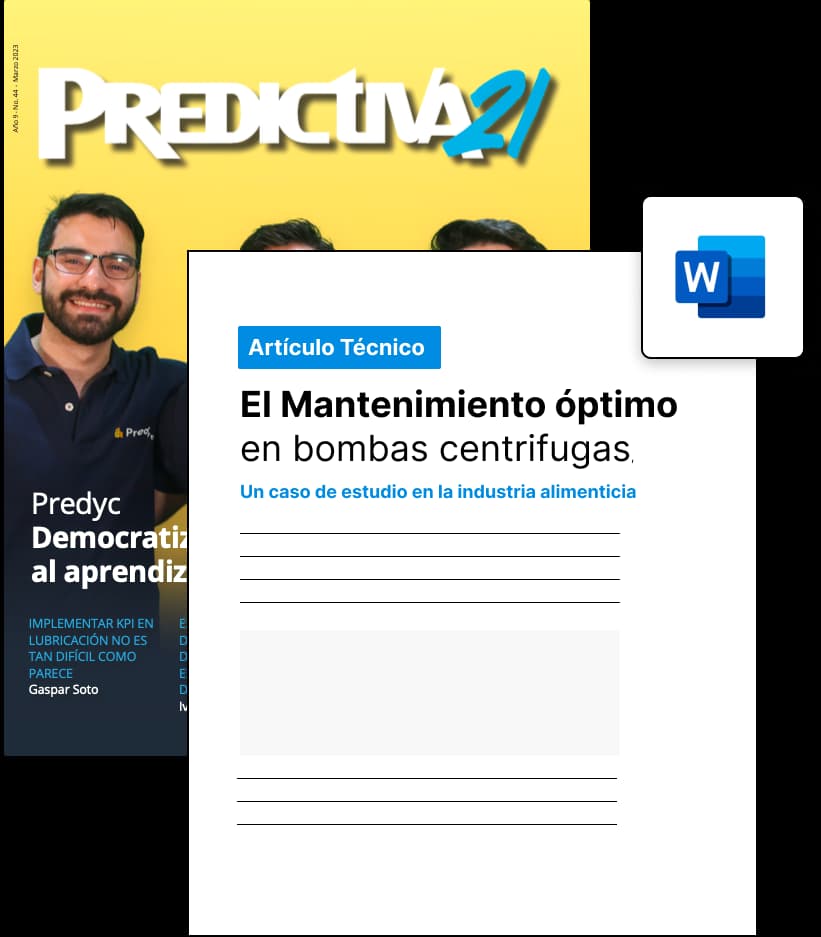
¿Cómo serán las fábricas dentro de una década? La transformación progresiva hacia la Smart Factory
Articulo 16 de agosto de 2021Este artículo es el primero de varios a modo de capítulos, donde se visionará cómo serán las fábricas a 10 años vista (centrándonos en las de estampación). Lo haremos pronosticando desde el punto de vista de TECNOLOGÍAS, pues la Industria4.0 o Cuarta Revolución Industrial va principalmente de tecnologías disruptivas; pero también de PERSONAS con talento, y de qué perfiles y habilidades requerirán estas futuras fábricas inteligentes.
Estructuraremos los capítulos tecnológicos bajo las 3 etapas principales de cómo una fábrica evolucionará desde a día de hoy hasta transformarse progresivamente en una fábrica inteligente (smart factory). Y también considerando el vector de Automatización avanzada, así como las infraestructuras IT & Telecom & CiberSeguridad.
La Industria4.0 va de tecnologías disruptivas y personas con habilidades concretas.
Más información: Los 3 estados de transformación progresiva.
No hay un único estado actual común en todas las fábricas. Cada una de ellas ha ido evolucionando estos últimos 20 años, implementando gradualmente nuevas tecnologías de la 3ª revolución industrial.
E incluso, dentro de una misma fábrica, no suele existir una homogeneización tecnológica. Por ejemplo, en el mundo Estampación para la Automoción es muy normal encontrarte con fábricas con Sistemas de Gestión de Almacén (SGA) más o menos fiables (“lo que debería haber en el almacén Vs. lo que realmente hay”) pero es menos frecuente ver implementaciones de Sistemas de Mantenimiento (GMAO) o Sistemas de Monitorización & Control de la producción (MES). Haciendo un símil con la industria automovilística, el parque de coches en España incluye vehículos de hace 15 años hasta los actuales vehículos cargados de sensores y cámaras para aparcamiento en automático, control de velocidad de crucero, luces en automático, etc. Todos conviviendo en la ciudad y carreteras.
Dentro de una misma fábrica no suele existir una homogeneización tecnológica.
Por último, existen otros aspectos que justifican la actual heterogeneidad de las fábricas de estampación. No es lo mismo una planta capacitada para estampación de piezas grandes respecto refuerzos y piezas pequeñas, o líneas de estampación bajo bobina que alimentación en formato, o con procesos de estampación en caliente respecto los convencionales en frío, o estampar aceros respecto aluminio, por ejemplo. Todo ello condiciona muchísimo la tipología de fábrica, tecnologías3.0 que dispone y qué necesitará en un futuro para aumentar la competitividad de fabricación.
Por este motivo es una falacia el vender a modo de “receta única” una hoja de ruta universal para cualquier fábrica de cómo debe pasar de ser una planta productiva convencional a una fábrica Smart. Lamentablemente empiezan a haber “vendedores de elixires de la juventud” pero esto no va de una pastilla mágica que vale para todo y para todos.
Estamos hablando de proyectos “a la carta” porque cada fábrica es un mundo, eso sí, bajo una metodología y un plan maestro como el que el autor plantea en esta serie de artículos: proyectos de digitalización de la fábrica, proyectos de conectividad y proyectos de dotar de inteligencia autónoma; junto a proyectos de automatización / robotización de las operaciones y, por último, dotar a la fábrica de infraestructuras IT-Telecomunicaciones-CiberSeguridad (Tecnologías “Cross”).
No existe una hoja de ruta universal para convertirse en una Smart factory.
Los artículos que se proponen son genéricos pero centrados al sector de la estampación, que lógicamente tiene sus singularidades respecto la inyección de plástico, por ejemplo. Ambos tienen sus propias diferencias pero con aspectos comunes pues son procesos de manufactura cíclicos, lo cual implica que algunas de las tecnologias4.0 que se detallarán sean válidas para ambos sectores y otros. Pero no “reutilizables” en plantas con procesos continuos como cementeras, refinerías, etc.
Capítulo 1: ¿Cómo serán las fábricas del futuro?
En el 2030, ¿cómo serán las fábricas de estampación de componentes metálicos para las carrocerías de vehículo?
Se plantea solamente a 10 años vista porque si tratamos de visualizar más allá… quién sabe si los coches se seguirán carroceando con materiales metálicos dados los nuevos materiales que ya se están desarrollando, o las nuevas maneras de producción (fabricación aditiva / Impresión 3D por ejemplo). O dada la evolución imparable del vehículo eléctrico-conectado-compartido-autónomo, ¿se requerirán elementos estructurales muchísimo más ligeros (como propone la estampación en caliente) y con métodos de conformación y de unión más simples, alejándonos de matrices, estampación y soldadura?
Pensando en que evolucione de una manera incremental y no disruptiva, bajo innovación de procesos y no de producto, todo apunta a que las fábricas de estampación y soldadura que serán competitivas en el 2030 dispondrán de:
- Sistemas de alimentación en automático, desde el proveedor de materia prima (sobre todo bobinas) suministrando en JIT (Just in Time) y entregando el material hasta la cabecera de la prensa.
- Para ello, será indispensable disponer de un sistema de control de la producción integrado al sistema de planificación y su aprovisionamiento de materias primas.
- Una flota de AGV y otros vehículos autónomos que gestionen automáticamente todo el movimiento en interno de la planta (logística inHouse).
- Sistema de cambio automático de las matrices, eliminando actividades manuales que son ineficientes en cuanto a productividad y Eficiencia General de los Equipos (OEE) de las prensas.
- Un sistema inteligente que en función de las características del material en la prensa (información que suministrará el proveedor de materia prima junto al suministro físico), la prensa realice en automático los ajustes necesarios de sus parámetros, para producir correctamente sin defectos. Eliminando así los ajustes de prensa que son realizados a día de hoy de manera manual.
- Una monitorización a tiempo real e inteligente, basada en un sistema “Gemelo Digital”, que controle todas las variables del proceso de estampación (considerando también los consumos energéticos), conforme están en los umbrales correctos.
- Un control total de la calidad del producto acabado, mediante la inspección en línea y a ciclo productivo para el 100% de las piezas y el 100% de su geometría, basado en Visión e Inteligencia Artificial a final de cada línea de estampación.
- Respecto al mantenimiento de este parque de maquinaria tan sofisticada, será necesario de un sistema total de sensorización de matrices y prensas, de manera que sean éstas quienes informen al equipo humano a nivel predictivo.
Capítulo 2: Aprovisionamiento de materias primas
En 2010 nació la generación alpha (α), la segunda completamente digital junto con la Z. Los futuros consumidores no habrán conocido otra forma de comunicarse ni trabajar que no sea esa, ni la aceptarán. Actualmente estamos frente a un cliente cada vez más digitalizado que está causando la revolución en las Cadenas de Suministro, “obligándolas” a digitalizar y conectar todos sus eslabones, ofreciéndole 100% trazabilidad, transparencia y visibilidad, información a tiempo real, etc. La compra online, con plataformas eComerce cada vez más potentes, así como las campañas de Marketing tipo “Black Friday”, condicionan que sean las fábricas y centros logísticos el factor limitante de venta; es decir, los activos que limitan la CAPACIDAD y FLEXIBILIDAD asumible. Y de ahí que todo lo que sea implementar tecnologías de la Industria 4.0 en tales centros para aumentar sus prestaciones, son bienvenidas.
Se puede hablar del concepto Digital B2B2C, en el caso de una pequeña cadena de suministro formada por un proveedor inicial que entrega al nivel1 y este es quien genera la venta directa al consumidor/cliente. Por tanto, en función del tamaño de la cadena, definiríamos B2B2B…B2C, siendo el número de “B´s” los proveedores que forman los eslabones de la cadena.
Hoy en día se habla mucho de evolucionar la SCM a Cadena de Valor, eliminado toda “B” que no aporta nada o muy poco y con ello, reducir la distancia del consumidor (C) con el que le genera el producto/servicio (el valor). Esta tendencia explica por qué el 30% de pymes va a desaparecer, por cuantificar un porcentaje medio, empresas que están en eslabones de poco valor y “alejadas” del consumidor final.
En este capítulo expondremos una serie de oportunidades de mejora que demanda el sector de la estampación automoción, agrupadas en tres grandes bloques que tienen estrecha relación con los proveedores de Materia Prima:
1. Todo lo que tiene que ver con la PLANIFICACIÓN Y CONTROL
- Planificación de todos los recursos: MP, contenedores, plantilla…
- Secuenciación ágil y eficiente de los pedidos. Posibilidad de simular escenarios ante imprevistos.
- Alineación de la planificación de las entregas desde el plan inicial.
- Trazabilidad online y real time. Anticipación gracias a la predicción.
2. Todo lo que tiene que ver con el APROVISIONAMIENTO DE MATERIA PRIMA
- Procedimientos manuales: trámites lentos, papel, errores humanos.
- Mejorar el control de la calidad en la recepción de la MP.
- Trazabilidad de la MP desde su origen (la fábrica del proveedor MP).
- Sincronizar los aprovisionamientos del Proveedor con la producción del estampador.
3. Todo lo que tiene que ver con la CALIDAD
- Gestión calidad en todo proceso completo.
- Seguimiento por lote y por pieza unitaria.
- Trazabilidad desde la MP hasta la pieza estampada PA (producto acabado).
Detallemos un poco más las dos primeras oportunidades de mejora que tienen los estampadores en esta nueva década 2020.
Planificación y control
El inicio de la planificación del estampador es la demanda de los clientes finales (por lo general, OEM´S), que generarán los pedidos a la planta. Estos “disparan” la planificación de todos los recursos del estampador, destacando las materias primas, los operarios, los contenedores y por descontando, la línea de prensas y las matrices.
Hoy en día, la planificación cada vez plantea situaciones más complejas, con múltiples consideraciones como la MP en diferentes formatos, contenedores homologados para las piezas, operarios capacitados y habilitados.
Y se requiere mayor agilidad y flexibilidad en la secuenciación de pedidos, pues son cada vez más frecuentes los cambios de última hora en la demanda. La posibilidad de hacer un seguimiento online de los principales KPI´s de la producción, y retroalimentando en real-time las opciones de planificación.
Aprovisionamiento de materia prima
Las tareas de recepción son mayoritariamente manuales y consumen grandes cantidades de papel, que pueden comportar errores que impactan en todo el flujo “aguas abajo”. Además, implican “tiempos de espera” entre la recepción física de materiales y su registro informático.
Sería interesante disponer de un control online y sin errores de los inventarios de materia prima.
Por otra banda, los clientes de los estampadores cada vez son más exigentes en cuanto a conocer la trazabilidad de la materia prima.
Y, por último, se necesita incrementar la integración online con proveedores, sincronizando el aprovisionamiento y teniendo en cuenta la situación real de producción.
Si analizamos estos 3 grandes bloques desde la perspectiva de las tecnologías 4.0 y tendencias en la SCM, se trata de evolucionar la relación Cliente-Proveedor de aceros hacia el desarrollo de una CADENA DE VALOR ÁGIL, CONECTADA E INTELIGENTE. Estableciendo nuevas relaciones de fidelización del proveedor de Materia Prima con los estampadores, basadas en formato digital.
“No se trata de CÓMO SE FABRICA sino de CÓMO SE SIRVE A LOS CLIENTES”.
Y en este sentido, los podemos agrupar en dos grandes retos tecnológicos:
1) Relacionado con la LOGISTICA INBOUND: el propio suministro físico (por lotes, etc.), la planificación y programación_fina cliente-proveedor, los sistemas de comunicación, Trazabilidad-geolocalización de inicio a fin (incluyendo transporte) Online/Tiempo_real, etc. 2) Relacionado con la FICHA DIGITAL DEL PRODUCTO: la información de los productos suministrados. Todo lo que tiene que ver con el certificado de materiales, su composición y sus propiedades mecánicas de cada bobina o lote de fabricación de formatos. En formato digital en Online/Tiempo_real.
Autor: Toni Laserna García
Experto en Transformación Digital en la Industria.
Correo: tlaserna@logikaservices.com
Sitio Web: https://applitechgnosis.website/
LinkedIn: https://www.linkedin.com/in/tlaserna/
Dinos qué te ha parecido el artículo
Artículos recomendados
Disminución de los costos por hora en neumáticos de camiones mineros

Plan modular de Alineación Láser y Condition Monitoring

Uso de la psicología del comportamiento en Reportes de Mantenimiento basado en Condición para hacerlos más efectivos

Ciclo Brayton

Publica tu artículo en la revista #1 de Mantenimiento Industrial
Publicar un artículo en la revista es gratis, no tiene costo.
Solo debes asegurarte que no sea un artículo comercial.
¿Qué esperas?
O envía tu artículo directo: articulos@predictiva21.com
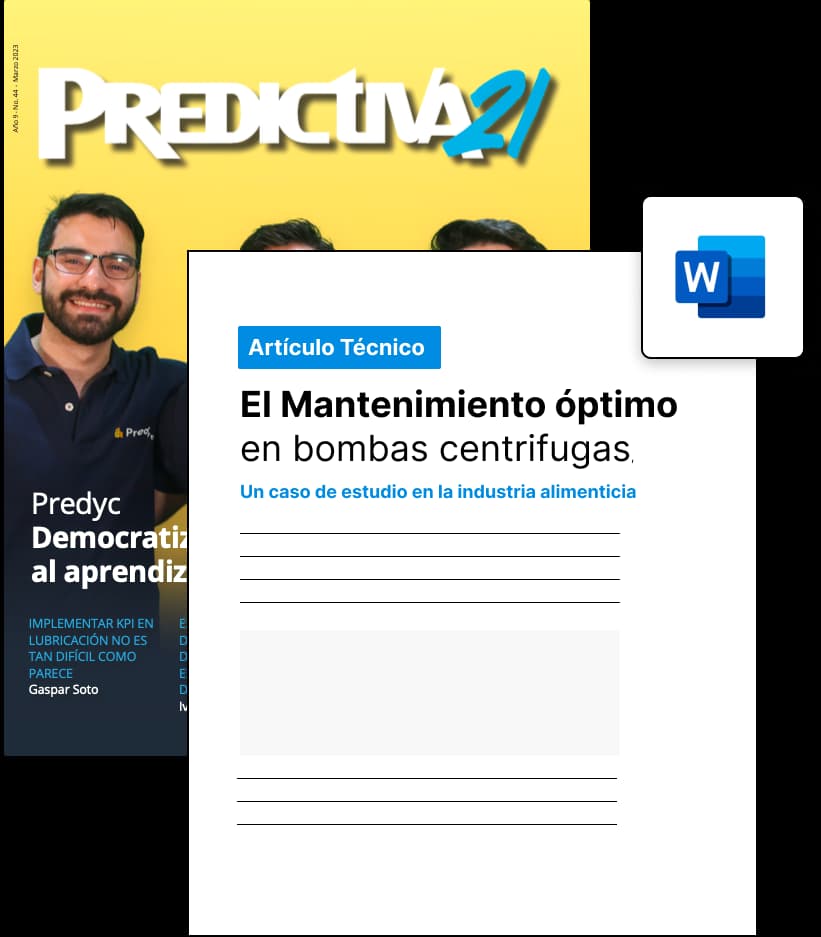