HABLEMOS DE RAM, parte 2. Análisis de caso de éxito: Repotenciación de Vehículos Panhard de la Infantería de Marina Argentina
Articulo15 de febrero de 2024
En el artículo “Hablemos de RAM” publicado en la Edición 46 de Predictiva 21 se planteó el empleo del RAM y la Soportabilidad desde la etapa de diseño de los sistemas, pero también durante la etapa de operación. Esto último surge cuando los activos necesitan recuperar su confiabilidad, cuando aparecen obsolescencias que dificultan y/o encarecen el mantenimiento por la desaparición de repuestos o cuando se necesita mejorar su performance en base a las necesidades de la organización.
Este tipo de trabajos, que pueden ser un overhaul o un upgrade, también son una oportunidad para eliminar problemas congénitos de diseño, eliminar obsolescencias futuras mejorando la mantenibilidad y de ser posible, incrementar la operabilidad, siempre teniendo en cuenta la soportabilidad que debe brindar el sistema.
Todo esto requiere diseño y planificación de detalle y en ese sentido, es saludable crear un proyecto de con enfoque predictivo. El PMBOK7 indica que este enfoque es útil cuando los requisitos del proyecto y del producto pueden definirse, recopilarse y analizarse al comienzo del proyecto y cada fase del proyecto se realiza solo una vez y se centra en un tipo particular de trabajo.
En la figura 1 se puede ver cómo el proyecto predictivo se lleva a cabo en forma paralela a la etapa de operación del ciclo de vida y cómo se rediseña y reconstruye el RAM y la soportabilidad para lograr, en definitiva, la disponibilidad deseada.

Recordemos también que las cuatro fases previstas en la “Guía del Departamento de Defensa de Estados Unidos para alcanzar el RAM” - DoD Guide for achieving Reliability, Availability, And Maintainability [1] son:
- Comprender y documentar las necesidades y limitaciones de los usuarios;
- Diseño y rediseño para el RAM;
- Producir sistemas confiables y mantenibles;
- Supervisar el rendimiento sobre el terreno.
El caso a plantear es la repotenciación de los vehículos de combate Panhard de la Infantería de Marina (IM) de la Armada Argentina. (Ver fotografías)
Estos activos son de origen francés y han prestado y prestan servicio en varios países.
Entre 1982 y 1983 fueron incorporados a la Infantería de Marina Argentina en las versiones ERC 90 Lynx 6x6 y VCR TT / PC / AA / AT 4x4, siendo utilizados profusamente en actividades de adiestramiento y en operaciones reales, como UNFICYP en Chipre y MINUSTAH en Haití.


Si bien son muy buenos vehículos con notables prestaciones operativas, presentaban problemas congénitos de confiabilidad y mantenibilidad, con repuestos de muy elevado costo y plazos de provisión muy largos. Además, por utilizar motores que requerían nafta de elevado octanaje y tener un alto consumo, su costo operativo era muy oneroso. Esto motivó que su empleo se fuese restringiendo en la medida que el presupuesto de defensa se achicaba, hasta quedar prácticamente fuera de uso en su mayoría.
En el año 2004, 12 vehículos fueron destacados Haití, integrando una Compañía de Infantería de Marina Mecanizada que integraba el Batallón Conjunto Argentino que ejecutaría, como parte de MINUSTAH, una operación de Peace Enforcement.
Si bien hubo una preparación previa al despliegue, los problemas congénitos continuaban y a estos se sumaron una gran cantidad de averías en los neumáticos producto del mal estado de los caminos y el terreno en el cual se operaba. En 2005, siendo Jefe de Mantenimiento de la IM, recibí la orden de analizar la viabilidad de repotenciar estos vehículos y de ser viable, confeccionar un proyecto a ese efecto. Cabe señalarse que ya teníamos experiencia en este tipo de tareas, en virtud que estábamos ejecutando la remotorización los Vehículos Anfibios a Rueda LARC5 y estábamos iniciando la repotenciación de los Vehículos Anfibios a Oruga LVTP7.
Cabe señalarse que las 4 fases fueron supervisadas y aprobadas por la Dirección Técnica de la Armada Argentina y que por requerimiento del Ministerio de Defensa, el proyecto fue homologado por la Universidad Tecnológica Nacional – Facultad Regional Buenos Aires.
Entendiendo las necesidades
Si bien la Guía RAM del DoD apareció ese año, en los trabajos ya iniciados estábamos aplicando los lineamientos de los libros Ingeniería Logística e Ingeniería de Sistemas, ambos escritos por Benjamín Blanchard y editados en 1995 por ISDEFE, Ingeniería de Sistemas para la Defensa de España, empresa adscripta al Ministerio de Defensa de España.
El primer paso fue, naturalmente, analizar la situación de los equipos y la “necesidad” de los mismos, o sea, entender qué necesitaban los usuarios y para qué. A tal efecto, el sistema se estudió en base a los componentes que intervienen en el equilibrio del sistema para alcanzar la disponibilidad. (Figura 1)

De análisis de los atributos intrínsecos del vehículo surgieron las siguientes consideraciones:
Confiabilidad:
Los principales problemas se encontraban en los siguientes sistemas:
- Tenía un motor naftero PRV, con una potencia máxima de 132,5 CV @ 5500 RPM y un par máximo 202 Nm @ 3500 RPM, desprogramado, con alto índice de fallas en el sistema de encendido, poco confiable, con un costo de repuestos muy alto, plazos de provisión inciertos y componentes con que no se proveían más. Las fallas más comunes eran en electrónica del motor, y si bien algunos componentes se reparaban en la IM había otros para los que no había solución.
- Sistemas periféricos desprogramados, repuestos importados de muy alto costo, con necesidad de reemplazo frecuente de partes. Por ejemplo los acumuladores de presión del sistema de frenos no funcionaban; los tanques de combustible estaban muy deteriorados y su interior se disolvía obturando sistemáticamente el sistema de combustible del motor y había un engranaje de la caja de velocidades, conocido como “cubo de garra” que sistemáticamente se rompía.
- Mantenibilidad
- El vehículo no era complicado de mantener o reparar, teniendo las herramientas, manuales, los repuestos necesarios y el personal capacitado.
- El sistema de ruedas, que tenía un runflat interno, no era reparable en el teatro de operaciones.
- Operabilidad.
- El vehículo no era complicado de operar, excepto por la caja de velocidades, que por la disposición de las marchas en la palanca era necesario contar un buen nivel de adiestramiento de los conductores y si no lo estaban, rompían la caja.
- Soportabilidad.
- La IM posee vehículos taller (VCR AT) con las herramientas y manuales propios de los mismos y una dotación de repuestos que incluía, por ejemplo, un mecanismo de ruedas completo.
- La obtención de repuestos era muy complicada y había algunos que estaban desprogramados.
- Para reparar o cambiar un neumático se requería una máquina extremadamente grande y muy complicada de operar (ver Foto). Además, los neumáticos no se podían adquirir en el país. Esto motivó que las ruedas averiadas en Haití debieran ser transportadas a la Base Naval Puerto Belgrano para poder ser reparadas.
- Se contaba con un buen taller de mantenimiento de tercer nivel.
- Ámbito de operación y requerimientos operativos.
Si bien estos vehículos estaban operando en Haití, los requisitos operativos no variaron en virtud que estaba preparado de origen para ser utilizado en zonas tropicales. Se incrementó la exigencia en cuanto a horas de uso por año.
Cómo lo diseñamos y planificamos
El segundo paso fue diseñar la repotenciación solucionando los problemas de confiabilidad y mantenibilidad, sabiendo que iba a ser muy difícil mejorar la operabilidad y que se debía asegurar la soportabilidad, tal como se indica en la Figura 1.
Para ello se utilizó el esquema de diseño basado en Ingeniería de Sistemas indicado en la Figura 2.

Necesidad:
La necesidad fue analizada y definida en la primera etapa.
- Viabilidad.
La experiencia obtenida con la remotorización / repotenciación llevada a cabo en los otros vehículos indicaba que teníamos la capacidad para llevar a cabo el trabajo en el país.
Hubo varios ofrecimientos de distintas empresas, que serán analizadas al momento de tratar las Alternativas surgidas.
- Requerimientos Operativos.
Como se indicó anteriormente, no había variación en los mismos.
No se iban a hacer modificaciones ni reparaciones en los sistemas de armas y comunicaciones, debido a que esas tareas se llevarían a cabo en los talleres especializados de la Armada Argentina.
- Concepto del Mantenimiento.
- Nivel de efectividad: Se fijó una Disponibilidad superior al 90 %, básicamente por requerimientos del Memorando de Entendimiento con Naciones Unidas.
- Niveles y Responsabilidades sobre el mantenimiento:
- La única modificación al sistema doctrinario original fue que el 4° nivel se llevaría a cabo en la industria privada.
- Políticas de reparación:
- En operaciones se operaría por cambio de subsistemas / componentes. Por ejemplo, un motor completo.
- Los nuevos sistemas a instalar debían ser de origen nacional o de comercialización normal en el país.
- Se debía crear y asegurar un sistema de provisión de repuestos nacionales en base a cooperación público – privado.
- Se debía buscar la uniformidad / compatibilidad logística con otros vehículos de la IM. (El motor, embrague, bombas de embrague y bomba de freno, son los mismos que posee el Agrale Marrua, que estaba entrando en uso en la IM en ese momento).
- Especificación de los trabajos.
Con todas estas premisas la IM desarrolló una alternativa de repotenciación, confeccionando al efecto la ingeniería básica del proyecto, incluyendo el estudio de aplicación del motor; el concepto para las modificaciones a la caja de velocidades para adaptarla al nuevo motor; el diseño del tanque de combustible y el diseño preliminar del sistema de ruedas.
A efectos de asegurar el RAM y la soportabilidad, las especificaciones indicaban que la empresa que ejecutase el trabajo debía cumplir lo siguiente:
- Trabajos a desarrollar:
- Estaban divididos por procesos para asegurar el recorrido de todos los sistemas.
- La IM entregaba la Ingeniería básica y parte de la de detalle.
- La empresa antes de iniciar los trabajos, presentaba la Ingeniería de detalle para su aprobación. Luego iniciaba la ingeniería de producción y los trabajos.
- Había trabajos mandatorios: reemplazo del motor por un MWM 4.07 TCA, diesel, 132,5 hp @ 3500 RPM / 300 Nm @ 2400 RPM, modificación de la caja de velocidades, indicándose el tipo de construcción y terminación requerido para el par cónico de entrada a la caja, colocación de un nuevo tanque de acero inoxidable con trampa y el reemplazo de las ruedas por otras de tipo desarmables.
- El cambio de las otras partes quedaba a criterio de la empresa.
- Performance a alcanzar.
- La variación aceptada, en menos, respecto a la original no debía superar el 5%.
- Características de los proveedores oferentes:
- Se fijó que los oferentes debía acreditar tener la capacidad Técnica para ejecutar la obra, la cual incluía contar con el personal, la Infraestructura, las herramientas y máquinas herramientas y la experiencia en tareas similares. De tercerizar algún trabajo, por ejemplo la construcción de los pares cónicos o las ruedas desarmables, tenían que contar con un pre-contrato con los ejecutores que debían acreditar contar con la capacidad para ejecutar ese trabajo. Por ejemplo, dado el tamaño de los engranajes del par cónico y la fuerza a transmitir, debían ser pares cónicos espiroidales tallados con sistema Oerlikon o similar con flanco de diente lapidado con calidad 7 según Norma DIN 3965.
- Se requería flexibilidad para aceptar modificaciones menores durante la ejecución de los prototipos.
- Gestión de calidad.
- Control de obra por “calidad total”, con seguimiento documentado pieza por pieza.
- Trazabilidad total de las partes fabricadas.
- Inspectores permanentes de IM en planta para control y asesoramiento técnico.
- Gestión de repuestos.
- Se debían nacionalizar los repuestos, ya sea por fabricación o por existir en el mercado local.
- Los componentes a diseñar y construir debían ser, en lo posible, “reparables”.
- Debían entregar un manual de partes con las piezas a proveer con su número correspondiente.
- Plan de pruebas de recepción.
- Se fijó un protocolo de pruebas, que incluía pruebas por sistemas previo al montaje, pruebas de taller, pruebas en pista y pruebas de campo.
- Transferencia de tecnología:
- Debía haber una transferencia total de tecnología de fabricación de piezas no comerciales, entregando planos, ensayos por simulación y memoria constructiva, los cuales debían ser aprobados antes de ser construidos. Si los fabricaba un subcontratista, debía entregar la misma documentación. Si eran componentes comerciales indicar la denominación, marca y número de parte.
- Debían entregar los manuales de uso y servicio de los nuevos componentes / sistemas.
- Debían entregar los planes de mantenimiento de los nuevos componentes / sistemas. Para los componentes críticos, como el acople elástico motor – traversa de auxiliares, se llevó a cabo análisis RCM para determinar su mantenimiento.
- Los inspectores debían verificar la fabricación / reparación, incluyendo visitas a subcontratistas.
- Garantías técnicas y financieras:
- Se requeriría una garantía técnica por la totalidad del vehículo de un año.
- Se solicitarían las garantías financieras fijadas por la normativa vigente
Respecto al aseguramiento de la Soportabilidad.
- Personal:
- Se preveía una capacitación para mecánicos y electricistas de 3º nivel a través de pasantías semestrales rotativas en planta.
- Se previeron cursos complementarios de actualización de operación y mantenimiento de 1º y 2º nivel a los usuarios, impartidos por los inspectores de IM en planta.
- Herramientas y equipos de mantenimiento:
Al recuperarse los vehículos taller se debía:
- Reponer / recuperar de herramientas y equipos de mantenimiento originales del vehículo.
- Proveer herramientas y equipos para mantenimiento de sistemas nuevos.
- Información Técnica:
Transferencia total de tecnología según lo explicado previamente.
- Repuestos:
Respecto al stock:
- Se previeron insumos y repuestos para mantenimiento preventivo y correctivo menor para un ciclo anual en el taller de 2° nivel.
- El contratista debía asegurar la provisión de repuestos para correctivo mayor en plazo perentorio.
- Se previó incluir los subsistemas / componentes y repuestos para operaciones al recuperar los vehículos taller.
- Conveniencia económica.
Luego del despliegue de los vehículos a Haití, incluso antes de iniciar la etapa de diseño, se presentaron varias empresas ofreciendo repotenciar estos vehículos. Hubo propuestas rechazados por tener un diseño no conveniente, otras por ser incompletas y otras por no solucionar los problemas de mantenibilidad y soportabilidad, ya que se seguía dependiendo de repuestos importados y de máquinas para desarmar las ruedas.
A los fines de la Evaluación del Proyecto, las alternativas retenidas fueron las siguientes:
- Ejecutarla en el taller de 3° nivel de la IM, importando todos los repuestos. Se consideró no apta ni factible por no dar solución a la obsolescencia del motor, los problemas congénitos y los repuestos desprogramados.
- Repotenciar en el país en la Industria Privada, fabricando todas las partes posibles en Argentina, con diseño según nuestras necesidades. Se retuvo como apta, factible y aceptable en cuanto al costo.
- Repotenciar en Francia, según diseño de fábrica. Considerada no apta por:
- Solo ofrecían la remotorización, con costo adicional para recuperar el resto de sistemas.
- El diseño era según las necesidades Ejército Francés, con pérdida de capacidades para la Infantería de Marina.
- No daba solución a la dependencia tecnológica y logística de fábrica.
- La obtención de repuestos quedaba sujeta a vaivenes políticos y paridad de la moneda.
- Había un costo adicional de acarreo, inspección y cursos en Francia.
- Adquirir vehículos nuevos,considerada no apta ni aceptable por el costo total de ciclo de vida y las consideraciones indicadas en la alternativa 3.
Si bien la única alternativa apta, factible y aceptable era la repotenciar en el país, a requerimiento del Ministerio de Defensa se llevó a cabo un análisis del TOTEX, OPEX y CAPEX de las alternativas 1, 2 y 4, para una vida útil de 15 años, aceptando para la alternativa 1 la pérdida de confiabilidad y los riesgos en operaciones y comparando económicamente las alternativas por Costo – Eficiencia a través del Valor Actualizado de Costos (VAC) y Costo Medio a Largo Plazo (CMLP). El resultado fue el siguiente:
ALTERNATIVAS | TOTEX ($) | CAPEX ($) | OPEX ($) | |
VAC15 Años | CMLP1 hs | |||
1. REPARAR EN ARMADA ARGENTINA. (no apta ni factible) | 1,36 | 1,41 | 0,61 | 12,60 |
2. REPOTENCIAR EN INDUSTRIA PRIVADA ARGENTINA. | 1 | 1 | 1 | 1 |
4. ADQUIRIR NUEVOS. (no apta ni aceptable) | 3,64 | 3,51 | 3,40 | 4,34 |
Quedo como alternativa seleccionada la de repotenciar en el país, con un CAPEX aproximado al 29 % del valor de reposición de un vehículo nuevo y un OPEX del orden del 23% del de dicho vehículo.
Cómo lo ejecutamos
Inicialmente se hicieron dos prototipos, un VCR y un ERC. Durante su ejecución se comprobó la ingeniería de detalle, surgiendo algunas modificaciones y se terminó de desarrollar la ingeniería de producción.
Las tareas desarrolladas fueron las siguientes:
SISTEMA | DETALLE |
Motor | Cambio del motor original por uno de última generación MWM 4.07 TCA. |
Adaptación de periféricos. | |
Adecuación sistema de escape. | |
Transmisión | Modificación de la caja de velocidades para adecuar la relación torque – velocidad de giro al nuevo motor. |
Adaptación de un nuevo sistema de embrague. | |
Recorrido de la cadena cinemática | |
Enfriamiento | Reemplazo del radiador por uno de mayor capacidad. |
Colocación del radiador de post enfriado. | |
Adecuación del sistema de ventiladores. | |
Hidráulico, frenos y dirección | Adecuación de los sistemas al régimen de giro del nuevo motor. Reemplazo de acumuladores hidráulicos por nuevos, de tipo industrial, con adaptación de la base de ajuste. |
Recorrido del sistema de frenos | |
Combustible | Reemplazo del tanque por uno nuevo de acero inoxidable, igual capacidad y sin bombas sumergidas. |
Eléctrico | Adecuación de los sistemas al nuevo motor. |
Reemplazo del sistema electrónico de control por uno eléctrico mas simple. | |
Adaptación del talero de instrumentos al nuevo motor. | |
Compresor | Adaptación del sistema de compresor al nuevo motor. |
L.C.I. | Colocación de un nuevo sistema sobre la base de Halón ecológico. |
Mecanismo ruedas | Recorrido general del sistema |
Ruedas | Reemplazo de los neumáticos importados por otros sin cámara marca FATE. |
Reemplazo de llantas originales de 16’’ por nuevo diseño de 20’’, de tipo partida, de fabricación nacional. | |
Reemplazo de runflat original por nuevo diseño de fabricación nacional |
Modificación de sistemas - Recorrido de sistemas
Cómo supervisamos el rendimiento sobre el terreno
Una vez llevadas a cabo las pruebas de campo se corrigieron los detalles que surgieron, se actualizó el proyecto y se dio inicio a las series.
Dada la necesidad operacional en Haití, los vehículos repotenciados fueron enviados de inmediato a ese lugar. Para supervisar el rendimiento, se envió personal del proyecto en los distintos contingentes.
La única falla que surgió fue la avería de un eje conector volante –embrague– caja. La empresa lo repuso, se analizó la rotura y surgió que existía un punto débil en el diseño. Se rediseñó la pieza, se construyeron nuevos ejes, se enviaron a Haití para ser cambiados y se aplicó en nuevo modelo en las series sucesivas.
Tal como se había determinado en el análisis RCM, el acople elástico del motor a la traversa, se confirmó como “crítico”. Se detectó además que la tasa de fallas aumentaba cuando los operadores eran nuevos, debido a aceleraciones bruscas o errores al efectuar los cambios de marcha que generaban mayor torsión en el motor y consecuentemente, mayor desalineación. Dado que amén de corregir las desalineaciones, esta pieza funciona como fusible y por estar su resistencia cerca del límite de los componentes que debe proteger, no existía la posibilidad de ser reforzado



[1] Department of Defense. (2005). Guide for achieving Reliability, Availability, and Maintainability
Autor: Armando Vittorangeli. Infante de Marina Retirado. Lic. en Sistemas Navales. A requerimiento, docente y consultor.
Dinos qué te ha parecido el artículo
Artículos recomendados
Factor kappa en los rodamientos

6.1 Las Siete Preguntas Básicas del M.C.C

Evaluación Estructural por Elementos Finitos de la Silla de Volcado utilizada en plantas de Laminado en Caliente

8.9 Medidas de Contención de Fuentes de Contaminación

Publica tu artículo en la revista #1 de Mantenimiento Industrial
Publicar un artículo en la revista es gratis, no tiene costo.
Solo debes asegurarte que no sea un artículo comercial.
¿Qué esperas?
O envía tu artículo directo: articulos@predictiva21.com
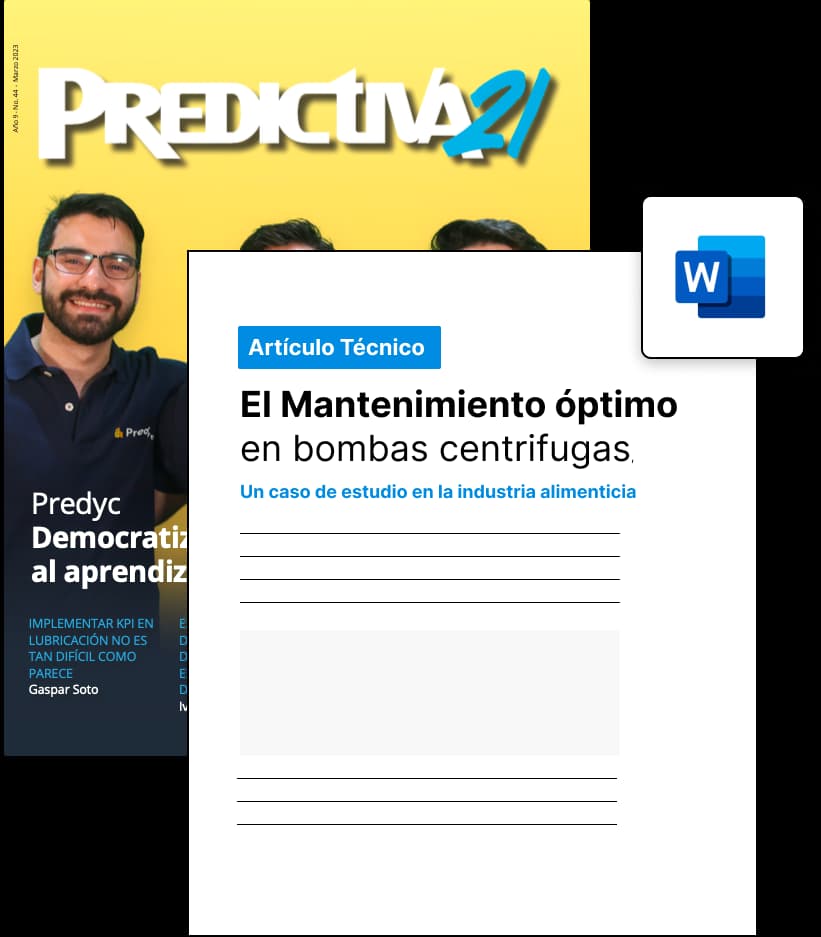
HABLEMOS DE RAM, parte 2. Análisis de caso de éxito: Repotenciación de Vehículos Panhard de la Infantería de Marina Argentina
Articulo 15 de febrero de 2024En el artículo “Hablemos de RAM” publicado en la Edición 46 de Predictiva 21 se planteó el empleo del RAM y la Soportabilidad desde la etapa de diseño de los sistemas, pero también durante la etapa de operación. Esto último surge cuando los activos necesitan recuperar su confiabilidad, cuando aparecen obsolescencias que dificultan y/o encarecen el mantenimiento por la desaparición de repuestos o cuando se necesita mejorar su performance en base a las necesidades de la organización.
Este tipo de trabajos, que pueden ser un overhaul o un upgrade, también son una oportunidad para eliminar problemas congénitos de diseño, eliminar obsolescencias futuras mejorando la mantenibilidad y de ser posible, incrementar la operabilidad, siempre teniendo en cuenta la soportabilidad que debe brindar el sistema.
Todo esto requiere diseño y planificación de detalle y en ese sentido, es saludable crear un proyecto de con enfoque predictivo. El PMBOK7 indica que este enfoque es útil cuando los requisitos del proyecto y del producto pueden definirse, recopilarse y analizarse al comienzo del proyecto y cada fase del proyecto se realiza solo una vez y se centra en un tipo particular de trabajo.
En la figura 1 se puede ver cómo el proyecto predictivo se lleva a cabo en forma paralela a la etapa de operación del ciclo de vida y cómo se rediseña y reconstruye el RAM y la soportabilidad para lograr, en definitiva, la disponibilidad deseada.

Recordemos también que las cuatro fases previstas en la “Guía del Departamento de Defensa de Estados Unidos para alcanzar el RAM” - DoD Guide for achieving Reliability, Availability, And Maintainability [1] son:
- Comprender y documentar las necesidades y limitaciones de los usuarios;
- Diseño y rediseño para el RAM;
- Producir sistemas confiables y mantenibles;
- Supervisar el rendimiento sobre el terreno.
El caso a plantear es la repotenciación de los vehículos de combate Panhard de la Infantería de Marina (IM) de la Armada Argentina. (Ver fotografías)
Estos activos son de origen francés y han prestado y prestan servicio en varios países.
Entre 1982 y 1983 fueron incorporados a la Infantería de Marina Argentina en las versiones ERC 90 Lynx 6x6 y VCR TT / PC / AA / AT 4x4, siendo utilizados profusamente en actividades de adiestramiento y en operaciones reales, como UNFICYP en Chipre y MINUSTAH en Haití.


Si bien son muy buenos vehículos con notables prestaciones operativas, presentaban problemas congénitos de confiabilidad y mantenibilidad, con repuestos de muy elevado costo y plazos de provisión muy largos. Además, por utilizar motores que requerían nafta de elevado octanaje y tener un alto consumo, su costo operativo era muy oneroso. Esto motivó que su empleo se fuese restringiendo en la medida que el presupuesto de defensa se achicaba, hasta quedar prácticamente fuera de uso en su mayoría.
En el año 2004, 12 vehículos fueron destacados Haití, integrando una Compañía de Infantería de Marina Mecanizada que integraba el Batallón Conjunto Argentino que ejecutaría, como parte de MINUSTAH, una operación de Peace Enforcement.
Si bien hubo una preparación previa al despliegue, los problemas congénitos continuaban y a estos se sumaron una gran cantidad de averías en los neumáticos producto del mal estado de los caminos y el terreno en el cual se operaba. En 2005, siendo Jefe de Mantenimiento de la IM, recibí la orden de analizar la viabilidad de repotenciar estos vehículos y de ser viable, confeccionar un proyecto a ese efecto. Cabe señalarse que ya teníamos experiencia en este tipo de tareas, en virtud que estábamos ejecutando la remotorización los Vehículos Anfibios a Rueda LARC5 y estábamos iniciando la repotenciación de los Vehículos Anfibios a Oruga LVTP7.
Cabe señalarse que las 4 fases fueron supervisadas y aprobadas por la Dirección Técnica de la Armada Argentina y que por requerimiento del Ministerio de Defensa, el proyecto fue homologado por la Universidad Tecnológica Nacional – Facultad Regional Buenos Aires.
Entendiendo las necesidades
Si bien la Guía RAM del DoD apareció ese año, en los trabajos ya iniciados estábamos aplicando los lineamientos de los libros Ingeniería Logística e Ingeniería de Sistemas, ambos escritos por Benjamín Blanchard y editados en 1995 por ISDEFE, Ingeniería de Sistemas para la Defensa de España, empresa adscripta al Ministerio de Defensa de España.
El primer paso fue, naturalmente, analizar la situación de los equipos y la “necesidad” de los mismos, o sea, entender qué necesitaban los usuarios y para qué. A tal efecto, el sistema se estudió en base a los componentes que intervienen en el equilibrio del sistema para alcanzar la disponibilidad. (Figura 1)

De análisis de los atributos intrínsecos del vehículo surgieron las siguientes consideraciones:
Confiabilidad:
Los principales problemas se encontraban en los siguientes sistemas:
- Tenía un motor naftero PRV, con una potencia máxima de 132,5 CV @ 5500 RPM y un par máximo 202 Nm @ 3500 RPM, desprogramado, con alto índice de fallas en el sistema de encendido, poco confiable, con un costo de repuestos muy alto, plazos de provisión inciertos y componentes con que no se proveían más. Las fallas más comunes eran en electrónica del motor, y si bien algunos componentes se reparaban en la IM había otros para los que no había solución.
- Sistemas periféricos desprogramados, repuestos importados de muy alto costo, con necesidad de reemplazo frecuente de partes. Por ejemplo los acumuladores de presión del sistema de frenos no funcionaban; los tanques de combustible estaban muy deteriorados y su interior se disolvía obturando sistemáticamente el sistema de combustible del motor y había un engranaje de la caja de velocidades, conocido como “cubo de garra” que sistemáticamente se rompía.
- Mantenibilidad
- El vehículo no era complicado de mantener o reparar, teniendo las herramientas, manuales, los repuestos necesarios y el personal capacitado.
- El sistema de ruedas, que tenía un runflat interno, no era reparable en el teatro de operaciones.
- Operabilidad.
- El vehículo no era complicado de operar, excepto por la caja de velocidades, que por la disposición de las marchas en la palanca era necesario contar un buen nivel de adiestramiento de los conductores y si no lo estaban, rompían la caja.
- Soportabilidad.
- La IM posee vehículos taller (VCR AT) con las herramientas y manuales propios de los mismos y una dotación de repuestos que incluía, por ejemplo, un mecanismo de ruedas completo.
- La obtención de repuestos era muy complicada y había algunos que estaban desprogramados.
- Para reparar o cambiar un neumático se requería una máquina extremadamente grande y muy complicada de operar (ver Foto). Además, los neumáticos no se podían adquirir en el país. Esto motivó que las ruedas averiadas en Haití debieran ser transportadas a la Base Naval Puerto Belgrano para poder ser reparadas.
- Se contaba con un buen taller de mantenimiento de tercer nivel.
- Ámbito de operación y requerimientos operativos.
Si bien estos vehículos estaban operando en Haití, los requisitos operativos no variaron en virtud que estaba preparado de origen para ser utilizado en zonas tropicales. Se incrementó la exigencia en cuanto a horas de uso por año.
Cómo lo diseñamos y planificamos
El segundo paso fue diseñar la repotenciación solucionando los problemas de confiabilidad y mantenibilidad, sabiendo que iba a ser muy difícil mejorar la operabilidad y que se debía asegurar la soportabilidad, tal como se indica en la Figura 1.
Para ello se utilizó el esquema de diseño basado en Ingeniería de Sistemas indicado en la Figura 2.

Necesidad:
La necesidad fue analizada y definida en la primera etapa.
- Viabilidad.
La experiencia obtenida con la remotorización / repotenciación llevada a cabo en los otros vehículos indicaba que teníamos la capacidad para llevar a cabo el trabajo en el país.
Hubo varios ofrecimientos de distintas empresas, que serán analizadas al momento de tratar las Alternativas surgidas.
- Requerimientos Operativos.
Como se indicó anteriormente, no había variación en los mismos.
No se iban a hacer modificaciones ni reparaciones en los sistemas de armas y comunicaciones, debido a que esas tareas se llevarían a cabo en los talleres especializados de la Armada Argentina.
- Concepto del Mantenimiento.
- Nivel de efectividad: Se fijó una Disponibilidad superior al 90 %, básicamente por requerimientos del Memorando de Entendimiento con Naciones Unidas.
- Niveles y Responsabilidades sobre el mantenimiento:
- La única modificación al sistema doctrinario original fue que el 4° nivel se llevaría a cabo en la industria privada.
- Políticas de reparación:
- En operaciones se operaría por cambio de subsistemas / componentes. Por ejemplo, un motor completo.
- Los nuevos sistemas a instalar debían ser de origen nacional o de comercialización normal en el país.
- Se debía crear y asegurar un sistema de provisión de repuestos nacionales en base a cooperación público – privado.
- Se debía buscar la uniformidad / compatibilidad logística con otros vehículos de la IM. (El motor, embrague, bombas de embrague y bomba de freno, son los mismos que posee el Agrale Marrua, que estaba entrando en uso en la IM en ese momento).
- Especificación de los trabajos.
Con todas estas premisas la IM desarrolló una alternativa de repotenciación, confeccionando al efecto la ingeniería básica del proyecto, incluyendo el estudio de aplicación del motor; el concepto para las modificaciones a la caja de velocidades para adaptarla al nuevo motor; el diseño del tanque de combustible y el diseño preliminar del sistema de ruedas.
A efectos de asegurar el RAM y la soportabilidad, las especificaciones indicaban que la empresa que ejecutase el trabajo debía cumplir lo siguiente:
- Trabajos a desarrollar:
- Estaban divididos por procesos para asegurar el recorrido de todos los sistemas.
- La IM entregaba la Ingeniería básica y parte de la de detalle.
- La empresa antes de iniciar los trabajos, presentaba la Ingeniería de detalle para su aprobación. Luego iniciaba la ingeniería de producción y los trabajos.
- Había trabajos mandatorios: reemplazo del motor por un MWM 4.07 TCA, diesel, 132,5 hp @ 3500 RPM / 300 Nm @ 2400 RPM, modificación de la caja de velocidades, indicándose el tipo de construcción y terminación requerido para el par cónico de entrada a la caja, colocación de un nuevo tanque de acero inoxidable con trampa y el reemplazo de las ruedas por otras de tipo desarmables.
- El cambio de las otras partes quedaba a criterio de la empresa.
- Performance a alcanzar.
- La variación aceptada, en menos, respecto a la original no debía superar el 5%.
- Características de los proveedores oferentes:
- Se fijó que los oferentes debía acreditar tener la capacidad Técnica para ejecutar la obra, la cual incluía contar con el personal, la Infraestructura, las herramientas y máquinas herramientas y la experiencia en tareas similares. De tercerizar algún trabajo, por ejemplo la construcción de los pares cónicos o las ruedas desarmables, tenían que contar con un pre-contrato con los ejecutores que debían acreditar contar con la capacidad para ejecutar ese trabajo. Por ejemplo, dado el tamaño de los engranajes del par cónico y la fuerza a transmitir, debían ser pares cónicos espiroidales tallados con sistema Oerlikon o similar con flanco de diente lapidado con calidad 7 según Norma DIN 3965.
- Se requería flexibilidad para aceptar modificaciones menores durante la ejecución de los prototipos.
- Gestión de calidad.
- Control de obra por “calidad total”, con seguimiento documentado pieza por pieza.
- Trazabilidad total de las partes fabricadas.
- Inspectores permanentes de IM en planta para control y asesoramiento técnico.
- Gestión de repuestos.
- Se debían nacionalizar los repuestos, ya sea por fabricación o por existir en el mercado local.
- Los componentes a diseñar y construir debían ser, en lo posible, “reparables”.
- Debían entregar un manual de partes con las piezas a proveer con su número correspondiente.
- Plan de pruebas de recepción.
- Se fijó un protocolo de pruebas, que incluía pruebas por sistemas previo al montaje, pruebas de taller, pruebas en pista y pruebas de campo.
- Transferencia de tecnología:
- Debía haber una transferencia total de tecnología de fabricación de piezas no comerciales, entregando planos, ensayos por simulación y memoria constructiva, los cuales debían ser aprobados antes de ser construidos. Si los fabricaba un subcontratista, debía entregar la misma documentación. Si eran componentes comerciales indicar la denominación, marca y número de parte.
- Debían entregar los manuales de uso y servicio de los nuevos componentes / sistemas.
- Debían entregar los planes de mantenimiento de los nuevos componentes / sistemas. Para los componentes críticos, como el acople elástico motor – traversa de auxiliares, se llevó a cabo análisis RCM para determinar su mantenimiento.
- Los inspectores debían verificar la fabricación / reparación, incluyendo visitas a subcontratistas.
- Garantías técnicas y financieras:
- Se requeriría una garantía técnica por la totalidad del vehículo de un año.
- Se solicitarían las garantías financieras fijadas por la normativa vigente
Respecto al aseguramiento de la Soportabilidad.
- Personal:
- Se preveía una capacitación para mecánicos y electricistas de 3º nivel a través de pasantías semestrales rotativas en planta.
- Se previeron cursos complementarios de actualización de operación y mantenimiento de 1º y 2º nivel a los usuarios, impartidos por los inspectores de IM en planta.
- Herramientas y equipos de mantenimiento:
Al recuperarse los vehículos taller se debía:
- Reponer / recuperar de herramientas y equipos de mantenimiento originales del vehículo.
- Proveer herramientas y equipos para mantenimiento de sistemas nuevos.
- Información Técnica:
Transferencia total de tecnología según lo explicado previamente.
- Repuestos:
Respecto al stock:
- Se previeron insumos y repuestos para mantenimiento preventivo y correctivo menor para un ciclo anual en el taller de 2° nivel.
- El contratista debía asegurar la provisión de repuestos para correctivo mayor en plazo perentorio.
- Se previó incluir los subsistemas / componentes y repuestos para operaciones al recuperar los vehículos taller.
- Conveniencia económica.
Luego del despliegue de los vehículos a Haití, incluso antes de iniciar la etapa de diseño, se presentaron varias empresas ofreciendo repotenciar estos vehículos. Hubo propuestas rechazados por tener un diseño no conveniente, otras por ser incompletas y otras por no solucionar los problemas de mantenibilidad y soportabilidad, ya que se seguía dependiendo de repuestos importados y de máquinas para desarmar las ruedas.
A los fines de la Evaluación del Proyecto, las alternativas retenidas fueron las siguientes:
- Ejecutarla en el taller de 3° nivel de la IM, importando todos los repuestos. Se consideró no apta ni factible por no dar solución a la obsolescencia del motor, los problemas congénitos y los repuestos desprogramados.
- Repotenciar en el país en la Industria Privada, fabricando todas las partes posibles en Argentina, con diseño según nuestras necesidades. Se retuvo como apta, factible y aceptable en cuanto al costo.
- Repotenciar en Francia, según diseño de fábrica. Considerada no apta por:
- Solo ofrecían la remotorización, con costo adicional para recuperar el resto de sistemas.
- El diseño era según las necesidades Ejército Francés, con pérdida de capacidades para la Infantería de Marina.
- No daba solución a la dependencia tecnológica y logística de fábrica.
- La obtención de repuestos quedaba sujeta a vaivenes políticos y paridad de la moneda.
- Había un costo adicional de acarreo, inspección y cursos en Francia.
- Adquirir vehículos nuevos,considerada no apta ni aceptable por el costo total de ciclo de vida y las consideraciones indicadas en la alternativa 3.
Si bien la única alternativa apta, factible y aceptable era la repotenciar en el país, a requerimiento del Ministerio de Defensa se llevó a cabo un análisis del TOTEX, OPEX y CAPEX de las alternativas 1, 2 y 4, para una vida útil de 15 años, aceptando para la alternativa 1 la pérdida de confiabilidad y los riesgos en operaciones y comparando económicamente las alternativas por Costo – Eficiencia a través del Valor Actualizado de Costos (VAC) y Costo Medio a Largo Plazo (CMLP). El resultado fue el siguiente:
ALTERNATIVAS | TOTEX ($) | CAPEX ($) | OPEX ($) | |
VAC15 Años | CMLP1 hs | |||
1. REPARAR EN ARMADA ARGENTINA. (no apta ni factible) | 1,36 | 1,41 | 0,61 | 12,60 |
2. REPOTENCIAR EN INDUSTRIA PRIVADA ARGENTINA. | 1 | 1 | 1 | 1 |
4. ADQUIRIR NUEVOS. (no apta ni aceptable) | 3,64 | 3,51 | 3,40 | 4,34 |
Quedo como alternativa seleccionada la de repotenciar en el país, con un CAPEX aproximado al 29 % del valor de reposición de un vehículo nuevo y un OPEX del orden del 23% del de dicho vehículo.
Cómo lo ejecutamos
Inicialmente se hicieron dos prototipos, un VCR y un ERC. Durante su ejecución se comprobó la ingeniería de detalle, surgiendo algunas modificaciones y se terminó de desarrollar la ingeniería de producción.
Las tareas desarrolladas fueron las siguientes:
SISTEMA | DETALLE |
Motor | Cambio del motor original por uno de última generación MWM 4.07 TCA. |
Adaptación de periféricos. | |
Adecuación sistema de escape. | |
Transmisión | Modificación de la caja de velocidades para adecuar la relación torque – velocidad de giro al nuevo motor. |
Adaptación de un nuevo sistema de embrague. | |
Recorrido de la cadena cinemática | |
Enfriamiento | Reemplazo del radiador por uno de mayor capacidad. |
Colocación del radiador de post enfriado. | |
Adecuación del sistema de ventiladores. | |
Hidráulico, frenos y dirección | Adecuación de los sistemas al régimen de giro del nuevo motor. Reemplazo de acumuladores hidráulicos por nuevos, de tipo industrial, con adaptación de la base de ajuste. |
Recorrido del sistema de frenos | |
Combustible | Reemplazo del tanque por uno nuevo de acero inoxidable, igual capacidad y sin bombas sumergidas. |
Eléctrico | Adecuación de los sistemas al nuevo motor. |
Reemplazo del sistema electrónico de control por uno eléctrico mas simple. | |
Adaptación del talero de instrumentos al nuevo motor. | |
Compresor | Adaptación del sistema de compresor al nuevo motor. |
L.C.I. | Colocación de un nuevo sistema sobre la base de Halón ecológico. |
Mecanismo ruedas | Recorrido general del sistema |
Ruedas | Reemplazo de los neumáticos importados por otros sin cámara marca FATE. |
Reemplazo de llantas originales de 16’’ por nuevo diseño de 20’’, de tipo partida, de fabricación nacional. | |
Reemplazo de runflat original por nuevo diseño de fabricación nacional |
Modificación de sistemas - Recorrido de sistemas
Cómo supervisamos el rendimiento sobre el terreno
Una vez llevadas a cabo las pruebas de campo se corrigieron los detalles que surgieron, se actualizó el proyecto y se dio inicio a las series.
Dada la necesidad operacional en Haití, los vehículos repotenciados fueron enviados de inmediato a ese lugar. Para supervisar el rendimiento, se envió personal del proyecto en los distintos contingentes.
La única falla que surgió fue la avería de un eje conector volante –embrague– caja. La empresa lo repuso, se analizó la rotura y surgió que existía un punto débil en el diseño. Se rediseñó la pieza, se construyeron nuevos ejes, se enviaron a Haití para ser cambiados y se aplicó en nuevo modelo en las series sucesivas.
Tal como se había determinado en el análisis RCM, el acople elástico del motor a la traversa, se confirmó como “crítico”. Se detectó además que la tasa de fallas aumentaba cuando los operadores eran nuevos, debido a aceleraciones bruscas o errores al efectuar los cambios de marcha que generaban mayor torsión en el motor y consecuentemente, mayor desalineación. Dado que amén de corregir las desalineaciones, esta pieza funciona como fusible y por estar su resistencia cerca del límite de los componentes que debe proteger, no existía la posibilidad de ser reforzado



[1] Department of Defense. (2005). Guide for achieving Reliability, Availability, and Maintainability
Autor: Armando Vittorangeli. Infante de Marina Retirado. Lic. en Sistemas Navales. A requerimiento, docente y consultor.
Dinos qué te ha parecido el artículo
Artículos recomendados
Importancia de medir el Desempeño del Sistema de Gestión de Activos, según La ISO 55001 - 2014

La Confiabilidad en Letras

3.1 Equipos naturales de trabajo

7.5 Importancia del ACR

Publica tu artículo en la revista #1 de Mantenimiento Industrial
Publicar un artículo en la revista es gratis, no tiene costo.
Solo debes asegurarte que no sea un artículo comercial.
¿Qué esperas?
O envía tu artículo directo: articulos@predictiva21.com
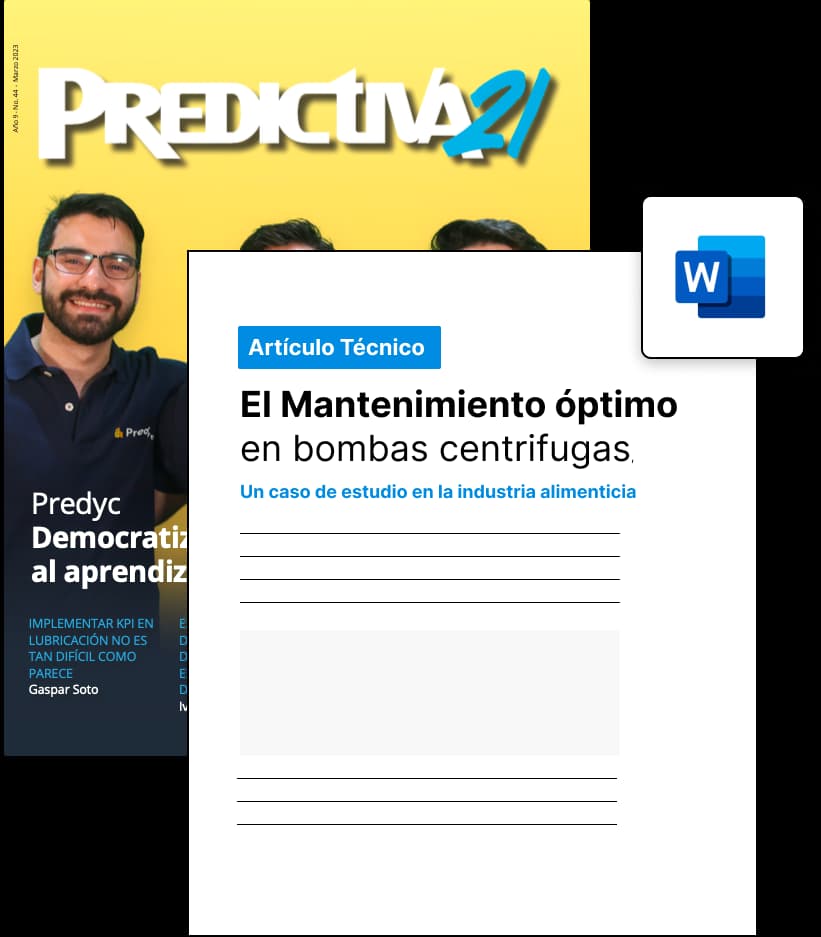