Investigación de Fallas, Reparación y Remedio Operativo Mínimo. Bomba de Alto Rendimiento
Articulo25 de abril de 2021
1.- Introducción y antecedentes
Esta bomba de alto rendimiento sufrió una falla catastrófica durante el arranque inmediatamente después de un mantenimiento mayor. El haz hidrodinámico, el rotor y el cojinete DE se dañaron.
El operador solicitó reparar la bomba y permitir el funcionamiento de la bomba de alto rendimiento por un período de 4 a 6 meses, período que sería seguido por la actualización de cojinetes y acoplamientos.
Además, el operador solicitó una investigación de fallas y una justificación para el remedio prescrito.
La bomba de alto rendimiento es del tipo de alimentación de caldera de caja doble, 9 etapas, 750 gpm de agua, bomba centrífuga Ps 1800, Pd 5250 psi. El haz hidrodinámico es de tipo voluta. La velocidad nominal se incrementó de 6000 a 6600 RPM para mejorar el rendimiento hidráulico. Sin embargo, esto creó una especie de problema rotordinámico.

2.- Objetivo
El objetivo de este informe es brindar pautas para reparar el eje fallado, encontrar la causa raíz de la falla y diseñar un remedio operativo mínimo que permita operar la bomba de alto rendimiento a niveles vibratorios aceptables de 0.4 in / seg.
3.- Juego de sellos internos. La causa raíz más probable del fallo
La holgura recomendada para el sello central, el pistón de balance, el ojo y el cubo del impulsor se muestran en la Tabla 1 a continuación.

La Tabla 1 muestra la comparación entre las holguras internas (haz hidrodinámico) pertenecientes a tres fuentes diferentes, a saber:
- Bomba de alto rendimiento, diseño y medidas actuales el 10/02/17 en el Taller de la empresa O&G en Puerto La Cruz, VE.
- Holgura mínima según API 610.
- Típico de una bomba similar con problemas de vibración.
La Tabla 1 constituye la herramienta de diagnóstico clave de este informe en la medida en que se realiza esta investigación. La causa más probable de la falla son las holguras reducidos en los sellos internos. Las holguras libres ampliados recomendados se muestran en la Tabla 1.
4.- Efecto dinámico de los sellos internos
Las Tablas 2 y 3 presentan un estudio comparativo de coeficientes dinámicos entre cojinetes existentes y sellos internos existentes como un intento de validar el análisis de respuesta sincrónica preliminar mostrado en las Figuras 3, 4 y 5.


Los sellos internos existentes se analizan con una holgura de diseño 1x y una holgura de diseño 2x como lo sugiere API 610. Las Tablas 2 y 3 comparan el efecto del sello con el efecto del cojinete en el comportamiento del rotor.
Una conclusión de las Tablas 2 y 3 es que el análisis de respuesta forzada necesita incorporar cuidadosamente el efecto de los sellos internos para ser confiable. Vea cómo los valores de los cojinetes (filas 5 y 84) tienen el mismo orden de magnitud que los sellos (fila “tot”).
Otra conclusión es que un fuerte efecto desestabilizador tanto de los cojinetes como de los sellos está actuando sobre estos componentes y este efecto aumenta con cojinetes y sellos apretados.
Es evidente en este análisis que el efecto de los sellos sobre la respuesta forzada es predominante sobre el de los cojinetes existentes. Entonces, los sellos apretados están impulsando la respuesta del rotor.
Los sellos internos apretados empujan la primera velocidad crítica muy por encima del rango de operación (efecto lomakin) como se ve claramente en la Figura 4.
5.- Retrofit acoplamiento momento reducido en eje más corto
Se ha encontrado in situ que el eje es excesivamente largo en el lado opuesto al acople. Un acoplamiento de momento reducido junto con el acortamiento del eje sería beneficioso para mantener la respuesta sincrónica del rotor lejos de las resonancias. Ver Figura 1.

Fuente: Luis Infante
La Figura 1 muestra cómo el centro de gravedad del acoplamiento de momento reducido y los discos flexibles se acercan al rodamiento. El acoplamiento de retroadaptación es más ligero y, por lo tanto aumenta el promotor de velocidad crítica.
Consulte los detalles en un informe de análisis rotordinámico separado.
6.- Cojinete basculante de seis almohadillas para mejorar estabilidad y soporte
El cojinete de almohadilla basculante de seis almohadillas es una buena opción para la estabilidad y el soporte de este eje delgado de alta velocidad. La Figura 2 muestra especificaciones detalladas y análisis de distribución de las almohadillas que muestran cómo el aumento de las holguras libres descargan las almohadillas superiores y también por qué la disposición de 6 almohadillas ofrece el mejor soporte.

Fuente: Luis Infante Excepto imagen inferior derecha
Consulte el análisis de estabilidad y rodamiento rotordinámico en un informe separado.
Cursos recomendados




%252FImagen%252FRAMPREDYC-1730060420837.webp%3Falt%3Dmedia%26token%3D2634a7f0-988e-4022-b91f-382503e6e9db&w=3840&q=75)



7.- Lecturas de vibración vs respuesta sincrónica simulada
Los altos niveles de vibración (20 mil de, 5 mil LA) en la Figura 3 llevaron a simular el comportamiento rotordinámico de la bomba con un peso desequilibrado de prueba ubicado en el acoplamiento, tomando en cuenta que el operador informó que el acople no ajustaba bien. El modelo matemático elastomásico se muestra en la Figura 4.

Fuente: Luis Infante

Fuente: Luis Infante y Rodolfo Alvarado
El efecto Lomakin proporcionado por los sellos internos ubica la primera velocidad crítica en la vecindad de 10,000 rpm muy por encima de 6,600 rpm, velocidad de operación cuando esta bomba se retroadapta con el cojinete y el acoplamiento prescritos en este informe. Consulte la Figura 5. Por lo tanto, es probable que esta bomba no resuene a pesar del trazo de vibración pronunciado obtenido (consulte la parte inferior de la Figura 5). Desafortunadamente, la respuesta rotordinámica con el rodamiento y el acoplamiento existentes no estaba disponible en el momento de redactar este informe.

Fuente: Luis Infante
La atención debe centrarse entonces en el equilibrio y la estabilidad dinámica del sistema de soporte de la subestructura del rodamiento del rotor y es la razón por la que recomendamos una modificación del rodamiento y el acoplamiento con un plano de equilibrio en el acoplamiento. Recortar el eje en la zona final de la transmisión (hay espacio disponible) también es un enfoque de mitigación previsible.
Un enfoque de calibración para el modelo matemático de masa elástica en la Figura 4 se presenta en el anexo 2 - configuración para prueba funcional.
8.- Destacando mitigación
La Tabla 4 a continuación presenta un compendio de la mitigación mínima necesaria para lograr el objetivo propuesto de tener un desempeño vibratorio aceptable, utilizando el cojinete y el acoplamiento existentes, dando así alivio mientras se lleva a cabo el Remedio prescrito (reacondicionamiento del cojinete y del acoplamiento).

9.- Especificaciones técnicas de reparación de la bomba
La Tabla 5 mas abajo presenta algunas especificaciones técnicas clave para el trabajo de reparación a realizar en el taller de máquinas.

Estas especificaciones técnicas han sido revisadas y comparadas con trabajos similares realizados por el mismo OEM en bombas de alimentación de calderas similares a nuestra bomba de alto rendimiento.
O&G Co debe discutir estas recomendaciones con el OEM y consultar al autor en caso de discrepancias.
10.- Conclusiones y recomendaciones
En este informe se proporcionan abundantes conclusiones y recomendaciones en los capítulos individuales y las figuras y tablas respectivas. Vea el capítulo 7.
La causa más probable de la falla son las holguras reducidas de los sellos internos del haz hidrodinámico.
11.- Recomendaciones adicionales de reparación. Bomba centrífuga 9 etapas - procedimiento de taller
- Verifique los centros del eje. Ajuste si es necesario.
- Mida el runout a lo largo de todo el rotor.
- Enderece el eje si el runout es superior a 2 milésimas de pulgada TIR.
- Limpiar con lija 400 la zona de los anillos de sello de desgaste giratorios. En estacionaria, elimine las rebabas con limas.
- Rectifique el manguito giratorio central del eje y la zona del pistón de balance con el metal base (elimine el metalizado y logre una superficie de metal base homogénea) y pula.
- Equilibre dinámicamente MAX 4 W / N.
- Fabrique el buje central y el buje de equilibrio del pistón con un material con una dureza 50 Brinell menor que la dureza del eje (eje pulido). El espacio libre del sello central debe estar entre 13 y 14 milésimas de pulgada de diámetro. El espacio libre en la balanza del pistón debe estar entre 12 y 14 milésimas de pulgada de diámetro.
- Desbalance residual máximo permitido 4 W / N = 4 x 400/6600 => .24 oz-in o 0.12 oz-in por plano. Dos planos de equilibrio.
NOTA: El presente método se ha desarrollado en base a las siguientes premisas:
- No hay repuestos (partes).
- Es urgente volver a poner la bomba en funcionamiento.
12.- Preparando la prueba de impacto sobre el eje
- Rotor colgado muy horizontalmente con dos cuerdas por el medio de los muñones. Cuerdas del mayor largo posible. Longitud mínima de la cuerda = tramo en puente / 3. Registre la longitud de la cuerda.
- Colocar un pequeño acelerómetro en un extremo del rotor, en posición horizontal.
- Registrar la longitud total del rotor, la distancia entre ejes, el peso y el centro de gravedad CG del rotor completo. El CG se determinará colgando el rotor con una cuerda, hasta que quede horizontal. Luego mida la distancia desde un extremo hasta la cuerda.
- Asegúrese de que estén instalados el collar, los manguitos de los sellos, el cubo del acople. Tome las medidas necesarias para unir / incorporar la mitad del peso del espaciador al cubo. Si es demasiado difícil, no importa, no lo haga (coloque el cubo solo).
- Golpear con un martillo de latón en el otro extremo del rotor, golpeando exactamente en horizontal. Grabe un espectro con un promedio de 5 o 6 muestras. Repite dos veces. Obtenga la Tabla de picos del analizador. Luego golpee con un martillo de plástico duro y registre un espectro. Repite dos veces.
- Repita el paso 5 golpeando en otro lugar y colocando también el acelerómetro en otro lugar.
- Asegúrate de identificar todos los espectros con la configuración utilizada.
- Proporcione el grado de acero para el eje.
Autor: Luis Infante
Director De Ingeniería
Ingeniero Mecánico / Especialista en Equipos Rotativos con más de 35 años de experiencia en Confiabilidad de Turbomaquinaria en la Industria Petrolera y Petroquímica.
Correo: infanteluis7@gmail.com
LinkedIn: https://www.linkedin.com/in/luisinfanteherrera/
Autor: Rodolfo Alvarado
Ingeniero Mecánico Principal y Gerente de Proyectos
Ingeniero Mecánico Especialista en Proyectos Multidisciplinarios de Ingeniería con más de 20 años de experiencia en Gerencia de Proyectos en la Industria Petrolera y Minera.
LinkedIn: https://www.linkedin.com/in/rodolfo-alvarado-santa-gadea-1a449439/
Dinos qué te ha parecido el artículo
Artículos recomendados
Buenas Prácticas de Mantenimiento Aeronáutico en el Mantenimiento Industrial

Mantenimiento y gestión de activos físicos

Barreras y factores de éxito para implementar la Gestión de Activos

HABLEMOS DE RAM, parte 2. Análisis de caso de éxito: Repotenciación de Vehículos Panhard de la Infantería de Marina Argentina

Publica tu artículo en la revista #1 de Mantenimiento Industrial
Publicar un artículo en la revista es gratis, no tiene costo.
Solo debes asegurarte que no sea un artículo comercial.
¿Qué esperas?
O envía tu artículo directo: articulos@predictiva21.com
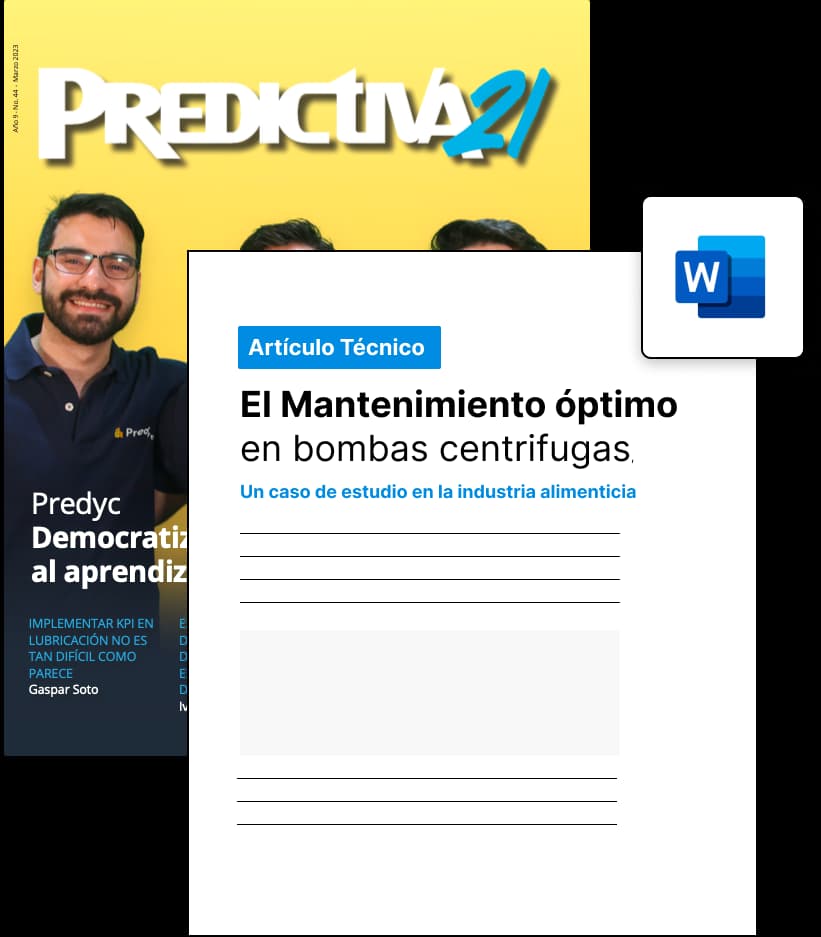
Investigación de Fallas, Reparación y Remedio Operativo Mínimo. Bomba de Alto Rendimiento
Articulo 25 de abril de 20211.- Introducción y antecedentes
Esta bomba de alto rendimiento sufrió una falla catastrófica durante el arranque inmediatamente después de un mantenimiento mayor. El haz hidrodinámico, el rotor y el cojinete DE se dañaron.
El operador solicitó reparar la bomba y permitir el funcionamiento de la bomba de alto rendimiento por un período de 4 a 6 meses, período que sería seguido por la actualización de cojinetes y acoplamientos.
Además, el operador solicitó una investigación de fallas y una justificación para el remedio prescrito.
La bomba de alto rendimiento es del tipo de alimentación de caldera de caja doble, 9 etapas, 750 gpm de agua, bomba centrífuga Ps 1800, Pd 5250 psi. El haz hidrodinámico es de tipo voluta. La velocidad nominal se incrementó de 6000 a 6600 RPM para mejorar el rendimiento hidráulico. Sin embargo, esto creó una especie de problema rotordinámico.

2.- Objetivo
El objetivo de este informe es brindar pautas para reparar el eje fallado, encontrar la causa raíz de la falla y diseñar un remedio operativo mínimo que permita operar la bomba de alto rendimiento a niveles vibratorios aceptables de 0.4 in / seg.
3.- Juego de sellos internos. La causa raíz más probable del fallo
La holgura recomendada para el sello central, el pistón de balance, el ojo y el cubo del impulsor se muestran en la Tabla 1 a continuación.

La Tabla 1 muestra la comparación entre las holguras internas (haz hidrodinámico) pertenecientes a tres fuentes diferentes, a saber:
- Bomba de alto rendimiento, diseño y medidas actuales el 10/02/17 en el Taller de la empresa O&G en Puerto La Cruz, VE.
- Holgura mínima según API 610.
- Típico de una bomba similar con problemas de vibración.
La Tabla 1 constituye la herramienta de diagnóstico clave de este informe en la medida en que se realiza esta investigación. La causa más probable de la falla son las holguras reducidos en los sellos internos. Las holguras libres ampliados recomendados se muestran en la Tabla 1.
4.- Efecto dinámico de los sellos internos
Las Tablas 2 y 3 presentan un estudio comparativo de coeficientes dinámicos entre cojinetes existentes y sellos internos existentes como un intento de validar el análisis de respuesta sincrónica preliminar mostrado en las Figuras 3, 4 y 5.


Los sellos internos existentes se analizan con una holgura de diseño 1x y una holgura de diseño 2x como lo sugiere API 610. Las Tablas 2 y 3 comparan el efecto del sello con el efecto del cojinete en el comportamiento del rotor.
Una conclusión de las Tablas 2 y 3 es que el análisis de respuesta forzada necesita incorporar cuidadosamente el efecto de los sellos internos para ser confiable. Vea cómo los valores de los cojinetes (filas 5 y 84) tienen el mismo orden de magnitud que los sellos (fila “tot”).
Otra conclusión es que un fuerte efecto desestabilizador tanto de los cojinetes como de los sellos está actuando sobre estos componentes y este efecto aumenta con cojinetes y sellos apretados.
Es evidente en este análisis que el efecto de los sellos sobre la respuesta forzada es predominante sobre el de los cojinetes existentes. Entonces, los sellos apretados están impulsando la respuesta del rotor.
Los sellos internos apretados empujan la primera velocidad crítica muy por encima del rango de operación (efecto lomakin) como se ve claramente en la Figura 4.
5.- Retrofit acoplamiento momento reducido en eje más corto
Se ha encontrado in situ que el eje es excesivamente largo en el lado opuesto al acople. Un acoplamiento de momento reducido junto con el acortamiento del eje sería beneficioso para mantener la respuesta sincrónica del rotor lejos de las resonancias. Ver Figura 1.

Fuente: Luis Infante
La Figura 1 muestra cómo el centro de gravedad del acoplamiento de momento reducido y los discos flexibles se acercan al rodamiento. El acoplamiento de retroadaptación es más ligero y, por lo tanto aumenta el promotor de velocidad crítica.
Consulte los detalles en un informe de análisis rotordinámico separado.
6.- Cojinete basculante de seis almohadillas para mejorar estabilidad y soporte
El cojinete de almohadilla basculante de seis almohadillas es una buena opción para la estabilidad y el soporte de este eje delgado de alta velocidad. La Figura 2 muestra especificaciones detalladas y análisis de distribución de las almohadillas que muestran cómo el aumento de las holguras libres descargan las almohadillas superiores y también por qué la disposición de 6 almohadillas ofrece el mejor soporte.

Fuente: Luis Infante Excepto imagen inferior derecha
Consulte el análisis de estabilidad y rodamiento rotordinámico en un informe separado.
Cursos recomendados




%252FImagen%252FRAMPREDYC-1730060420837.webp%3Falt%3Dmedia%26token%3D2634a7f0-988e-4022-b91f-382503e6e9db&w=3840&q=75)



7.- Lecturas de vibración vs respuesta sincrónica simulada
Los altos niveles de vibración (20 mil de, 5 mil LA) en la Figura 3 llevaron a simular el comportamiento rotordinámico de la bomba con un peso desequilibrado de prueba ubicado en el acoplamiento, tomando en cuenta que el operador informó que el acople no ajustaba bien. El modelo matemático elastomásico se muestra en la Figura 4.

Fuente: Luis Infante

Fuente: Luis Infante y Rodolfo Alvarado
El efecto Lomakin proporcionado por los sellos internos ubica la primera velocidad crítica en la vecindad de 10,000 rpm muy por encima de 6,600 rpm, velocidad de operación cuando esta bomba se retroadapta con el cojinete y el acoplamiento prescritos en este informe. Consulte la Figura 5. Por lo tanto, es probable que esta bomba no resuene a pesar del trazo de vibración pronunciado obtenido (consulte la parte inferior de la Figura 5). Desafortunadamente, la respuesta rotordinámica con el rodamiento y el acoplamiento existentes no estaba disponible en el momento de redactar este informe.

Fuente: Luis Infante
La atención debe centrarse entonces en el equilibrio y la estabilidad dinámica del sistema de soporte de la subestructura del rodamiento del rotor y es la razón por la que recomendamos una modificación del rodamiento y el acoplamiento con un plano de equilibrio en el acoplamiento. Recortar el eje en la zona final de la transmisión (hay espacio disponible) también es un enfoque de mitigación previsible.
Un enfoque de calibración para el modelo matemático de masa elástica en la Figura 4 se presenta en el anexo 2 - configuración para prueba funcional.
8.- Destacando mitigación
La Tabla 4 a continuación presenta un compendio de la mitigación mínima necesaria para lograr el objetivo propuesto de tener un desempeño vibratorio aceptable, utilizando el cojinete y el acoplamiento existentes, dando así alivio mientras se lleva a cabo el Remedio prescrito (reacondicionamiento del cojinete y del acoplamiento).

9.- Especificaciones técnicas de reparación de la bomba
La Tabla 5 mas abajo presenta algunas especificaciones técnicas clave para el trabajo de reparación a realizar en el taller de máquinas.

Estas especificaciones técnicas han sido revisadas y comparadas con trabajos similares realizados por el mismo OEM en bombas de alimentación de calderas similares a nuestra bomba de alto rendimiento.
O&G Co debe discutir estas recomendaciones con el OEM y consultar al autor en caso de discrepancias.
10.- Conclusiones y recomendaciones
En este informe se proporcionan abundantes conclusiones y recomendaciones en los capítulos individuales y las figuras y tablas respectivas. Vea el capítulo 7.
La causa más probable de la falla son las holguras reducidas de los sellos internos del haz hidrodinámico.
11.- Recomendaciones adicionales de reparación. Bomba centrífuga 9 etapas - procedimiento de taller
- Verifique los centros del eje. Ajuste si es necesario.
- Mida el runout a lo largo de todo el rotor.
- Enderece el eje si el runout es superior a 2 milésimas de pulgada TIR.
- Limpiar con lija 400 la zona de los anillos de sello de desgaste giratorios. En estacionaria, elimine las rebabas con limas.
- Rectifique el manguito giratorio central del eje y la zona del pistón de balance con el metal base (elimine el metalizado y logre una superficie de metal base homogénea) y pula.
- Equilibre dinámicamente MAX 4 W / N.
- Fabrique el buje central y el buje de equilibrio del pistón con un material con una dureza 50 Brinell menor que la dureza del eje (eje pulido). El espacio libre del sello central debe estar entre 13 y 14 milésimas de pulgada de diámetro. El espacio libre en la balanza del pistón debe estar entre 12 y 14 milésimas de pulgada de diámetro.
- Desbalance residual máximo permitido 4 W / N = 4 x 400/6600 => .24 oz-in o 0.12 oz-in por plano. Dos planos de equilibrio.
NOTA: El presente método se ha desarrollado en base a las siguientes premisas:
- No hay repuestos (partes).
- Es urgente volver a poner la bomba en funcionamiento.
12.- Preparando la prueba de impacto sobre el eje
- Rotor colgado muy horizontalmente con dos cuerdas por el medio de los muñones. Cuerdas del mayor largo posible. Longitud mínima de la cuerda = tramo en puente / 3. Registre la longitud de la cuerda.
- Colocar un pequeño acelerómetro en un extremo del rotor, en posición horizontal.
- Registrar la longitud total del rotor, la distancia entre ejes, el peso y el centro de gravedad CG del rotor completo. El CG se determinará colgando el rotor con una cuerda, hasta que quede horizontal. Luego mida la distancia desde un extremo hasta la cuerda.
- Asegúrese de que estén instalados el collar, los manguitos de los sellos, el cubo del acople. Tome las medidas necesarias para unir / incorporar la mitad del peso del espaciador al cubo. Si es demasiado difícil, no importa, no lo haga (coloque el cubo solo).
- Golpear con un martillo de latón en el otro extremo del rotor, golpeando exactamente en horizontal. Grabe un espectro con un promedio de 5 o 6 muestras. Repite dos veces. Obtenga la Tabla de picos del analizador. Luego golpee con un martillo de plástico duro y registre un espectro. Repite dos veces.
- Repita el paso 5 golpeando en otro lugar y colocando también el acelerómetro en otro lugar.
- Asegúrate de identificar todos los espectros con la configuración utilizada.
- Proporcione el grado de acero para el eje.
Autor: Luis Infante
Director De Ingeniería
Ingeniero Mecánico / Especialista en Equipos Rotativos con más de 35 años de experiencia en Confiabilidad de Turbomaquinaria en la Industria Petrolera y Petroquímica.
Correo: infanteluis7@gmail.com
LinkedIn: https://www.linkedin.com/in/luisinfanteherrera/
Autor: Rodolfo Alvarado
Ingeniero Mecánico Principal y Gerente de Proyectos
Ingeniero Mecánico Especialista en Proyectos Multidisciplinarios de Ingeniería con más de 20 años de experiencia en Gerencia de Proyectos en la Industria Petrolera y Minera.
LinkedIn: https://www.linkedin.com/in/rodolfo-alvarado-santa-gadea-1a449439/
Dinos qué te ha parecido el artículo
Artículos recomendados
Generalización, Beneficios e Impacto de la Tecnología SGestMan©

Uso y aplicación de la Prueba de Gota

Planificación de Mantenimiento en PM-SAP

Cursos de mantenimiento preventivo: ¿Por qué deberías tomarlos?

Publica tu artículo en la revista #1 de Mantenimiento Industrial
Publicar un artículo en la revista es gratis, no tiene costo.
Solo debes asegurarte que no sea un artículo comercial.
¿Qué esperas?
O envía tu artículo directo: articulos@predictiva21.com
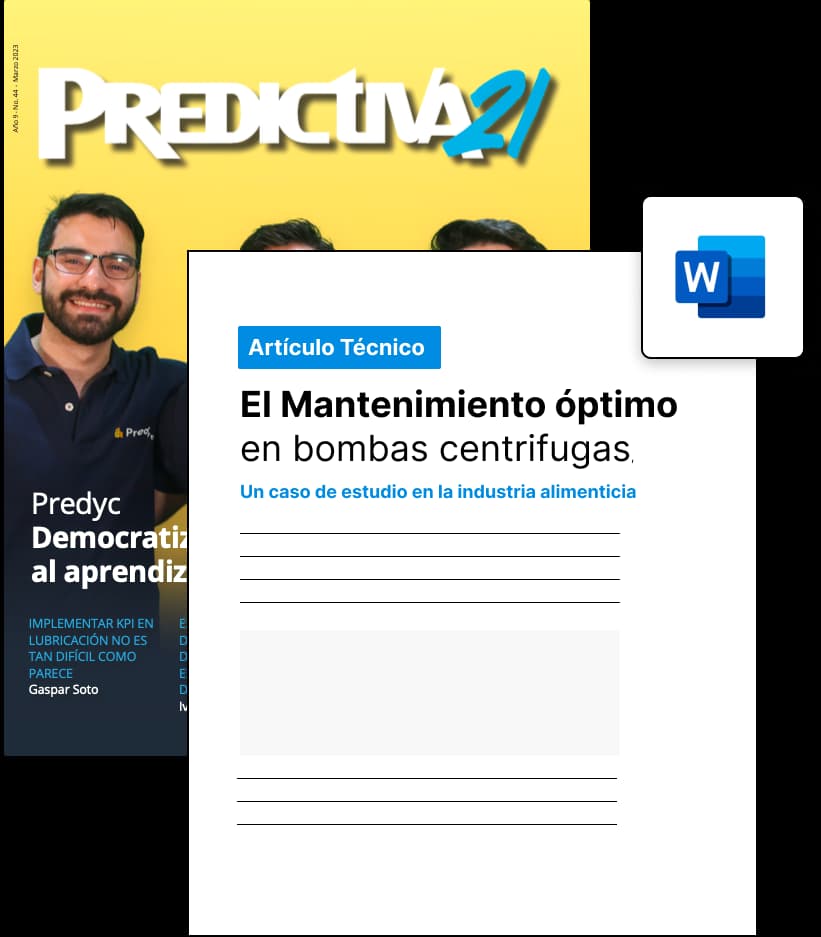