Análisis de Grasa y Ultrasonido para Rodamientos
Articulo20 de enero de 2025
A principios del 2010 tuve mi primer encuentro con una de las tecnologías del mantenimiento predictivo que, desde que la aprendí a utilizar, vi el potencial que tiene, y sobre todo, cuando se utiliza en combinación con otras herramientas del PdM.El ultrasonido propagado en aire para la inspección de rodamientos es, probablemente, una de las herramientas más sencillas y versátiles de utilizar, cuyos resultados pueden observarse casi inmediatamente.
Dependiendo de la fuente y el autor, el ultrasonido suele estar al inicio de la curva P-F, por delante de otras herramientas. Si bien esto es discutible y habrá casos en los que sí y otros en los que no, en lo que estamos de acuerdo es en que no podemos negar su valor y el beneficio que tiene en la determinación de la condición del rodamiento. En el peor de los escenarios, y si no se aplica ningún remedio, el ultrasonido inaudible tenderá a volverse audible, y el rodamiento estará muy cerca de un fallo funcional.

De manera muy simplista, la teoría que rige esta herramienta dice que el ultrasonido (dB) es el resultado de la fricción entre el elemento rodante, la pista interna, la jaula, el lubricante y otros elementos como la contaminación externa y el desgaste generado internamente. Para mantener el ultrasonido en un rango de normalidad, el lubricante —grasa, en el análisis del presente estudio— se añade para minimizar la fricción entre los componentes del rodamiento. De esta manera, se reduce el contacto, el desgaste y se extiende la vida en servicio del rodamiento para intentar alcanzar la vida esperada.
Alrededor de este concepto, y con el pujante ingreso de la Industria 4.0 al sector del PdM, se han diseñado sensores que añaden grasa de manera automática, en un volumen preciso para no sobrecargar de grasa el poco espacio que existe en el rodamiento, siempre que se detecten valores anómalos de ultrasonido.
Hasta aquí todo parece andar sobre ruedas, de manera tal que el engrase de rodamientos representa un antes y un después tras esta tecnología.Pero, ¿qué pasa con la grasa que está en servicio? Si hiciésemos un interrogatorio a dicha grasa, ¿qué nos diría? ¿Qué valor nos aportaría?
Grasa, ¿qué puede decirnos?
El primer informe de análisis de grasa en servicio en un rodamiento de motor eléctrico que tuve en mis manos databa de 1994. Año del mundial de fútbol, mientras yo veía el partido inaugural que enfrentaba al todopoderoso conjunto alemán contra 11 guerreros bolivianos, alguien bajo el sol del pleno verano estaba tomando una muestra de grasa de un rodamiento que había fallado, con la intención de saber si esa muestra podía dar alguna pista del fallo. Para ese tiempo, el análisis de aceite ya llevaba unas cuantas décadas reportando beneficios, pero la grasa… ¡a quién se le ocurriría analizar grasa!
Ahora sabemos que el análisis de grasa puede aportar mucho al mantenimiento y a la fiabilidad. Al menos algunos lo tenemos claro y sabemos cómo extraer el máximo provecho de esto.Una muestra de grasa obtenida adecuadamente evidencia la condición del rodamiento, puede desvelar si existe contaminación, de qué tipo, cuánta contaminación, si existe paso de corriente, si hubo mezcla de grasas, si esa mezcla es incompatible, y un largo etcétera. Esto es mucho pedir, al menos a un fluido no newtoniano.
[TIP] En la industria de procesado de grano para obtención de harinas, los rodamientos sufren un modo de fallo único, que no se observa en otras industrias. Se debe precisamente a la propiedad de los fluidos no newtonianos sometidos a altas cargas y presiones. ¿Te interesa saber más?
Volviendo a la grasa, su análisis es tan importante que, en la industria de aerogeneración, por citar un ejemplo, un análisis apropiado puede advertir de un fallo funcional del rodamiento principal, evitando así incurrir en un alto costo prevenible de mantenimiento.
Ultrasonido & Análisis de grasa, ¿qué aportan en conjunto?
Como hemos visto, de manera aislada ambas herramientas son increíbles, y si se utilizan adecuadamente, aportan muchos beneficios.
Pero, ¿podrían utilizarse en conjunto?
Llevaba años haciéndome esta pregunta. Había sido capaz de analizar unos 30 rodamientos, obteniendo muestras de grasas y ultrasonido, pero puntualmente, sin lograr la trazabilidad adecuada. Se necesita al menos dos puntos para trazar una recta, y con solo un punto no tenía más que suposiciones y no resultados coherentes.
Fue en una planta petroquímica donde pude calmar esa sed de conocimiento y durante dos años recolecté muestras tanto de grasa como de ultrasonido en un grupo de alrededor de 60 activos de diferentes características y condiciones. Los resultados y conclusiones presentadas en este artículo no pueden ser generalizados, ya que dependen mucho de factores como el tipo de rodamiento, la velocidad, las condiciones de operación, el ambiente operativo, los tipos de grasa utilizados en planta y el factor humano, además de la variabilidad del reengrase manual —no podemos sensorizar el 100% de los activos— al menos de momento.
Si bien la medida obtenida por el ultrasonido es única y se expresa en dB, el resultado del análisis de grasa está dividido en las siguientes variables:
- Desgastes ≤ 7 μ
- Desgastes ≥ 5 μ
- Desgaste de jaula (teniendo en cuenta que no había jaulas de poliamida)
- Consistencia de la grasa
- Incompatibilidad entre espesantes
- Diferentes viscosidades de aceite
De estas seis variables, los resultados mostrados en este breve artículo se centran únicamente en las dos primeras: desgastes del rodamiento. Por otro lado, se muestran únicamente resultados del rodamiento del lado del acoplamiento.
Al cabo de los dos años se obtuvieron alrededor de 500 muestras de cada tecnología. Utilizando un sistema de colores, de manera aislada, los resultados son los siguientes:

A grandes rasgos, la mayoría de los rodamientos tiene un comportamiento similar en función de los desgastes y el nivel de decibelios, y es posible sacar bastantes conclusiones de un análisis de este tipo.Tomaremos como ejemplo el rodamiento del lado de acoplamiento correspondiente a la unidad JBX – 102A.Este rodamiento tuvo que ser reemplazado al mes siguiente del último análisis, debido a que se podía oír la fricción producida internamente, y un posterior análisis evidenció un daño irreparable en la pista interna.
Es importante mencionar los siguientes puntos:
- El engrase se realiza dentro del concepto de mantenimiento preventivo, con una frecuencia definida.
- Los rodamientos se cambian en función del mantenimiento correctivo; es decir, operan hasta el fallo.
- La frecuencia de reengrase es bimensual, marcada con un recuadro en la figura 2.
- En los meses en los que no se realiza el reengrase, solo se recolecta información.
- El volumen de grasa añadido no supera el volumen calculado.


Cursos recomendados


%252FImagen%252FRAMPREDYC-1730060420837.webp%3Falt%3Dmedia%26token%3D2634a7f0-988e-4022-b91f-382503e6e9db&w=3840&q=75)





Resultados iniciales
Siguiendo la línea de tiempo, podemos ver algunos resultados remarcables:
- La línea base de ultrasonido para este rodamiento se sitúa en 38 dB, y la tecnología alerta que se ha rebasado este límite al cabo del tercer mes (Jun-18). ¡Punto a favor para el ultrasonido! El análisis de grasa no muestra que los desgastes se encuentren dentro de valores anómalos.
- Avanzamos en el tiempo y, tras el reengrase habitual, el ultrasonido regresa a valores normales. Cuando todo parece estar bien, los desgastes medidos por partículas inferiores a 7 μm superan el límite establecido (Sep-18). ¡Punto para el análisis de grasa! El análisis por ultrasonido se encuentra dentro de valores normales.
- Tras el reengrase de Nov-18, el ultrasonido está dentro de niveles normales, pero ambos tipos de desgastes han superado sus límites admisibles.
- A partir de este punto, entramos en una zona de no retorno con unas tendencias crecientes para las tres variables. A esto se debe sumar que, por fallo humano, no se realizó el reengrase de Feb-19 y, para cuadrar cuentas con el sistema de gestión de mantenimiento, se reengrasó dos meses seguidos: Mar-19 y Abr-19.
- Pasado este punto, los dB no se incrementan de manera exagerada como sí lo hacen los desgastes, hasta acabar en un fallo funcional del rodamiento.
Conclusiones: quizá sirvan de algo
Volviendo a la curva P-F, ¿quién se adelanta al fallo funcional del rodamiento en este caso? Difícil decir quién. Lo cierto es que podemos aprender cosas interesantes de esta situación:
- El ultrasonido, al menos en esta situación, es un gran indicador del resultado cualitativo de la condición del rodamiento. Sí, nos da un valor en dB y este resultado es cuantificable, pero no nos dice cómo es el desgaste.
- El análisis de grasa, al menos en esta situación, es un gran indicador del resultado cuantitativo de la condición del rodamiento. Sí, nos dice cuánto se desgasta, pero no cómo es la fricción entre los elementos del rodamiento.
- El desgaste de los componentes del rodamiento es resultado de la fricción, y esta a su vez genera más desgaste.
- El valor agregado cuando se trabaja con ambas tecnologías radica precisamente en determinar cómo es la fricción y cómo son los desgastes.
- Desafortunadamente, la grasa no fluye con facilidad y tiende a retener las partículas de desgaste generadas por fricción.
- Muchas configuraciones de rodamientos no tienen un punto de purga para eliminar la grasa y partículas incluidas de manera adecuada, por lo que los desgastes, en muchos casos, forman parte del sistema.
- Pasar de un mantenimiento preventivo, donde se engrasa en función de frecuencia, a uno predictivo, donde se engrasa en función de condición, requiere un sistema de seguimiento casi perfecto; la fricción y los desgastes no conocen límites.
- Los límites hay que respetarlos. Ya sean 80 km/h, 38 dB o 50 ppm de hierro, han sido puestos por alguna razón.
- Las acciones correctivas de mantenimiento deben ser apropiadas a los resultados obtenidos. Quizá no sea necesario reemplazar el rodamiento a los 44 dB/40 ppm Fe, pero será imprescindible definir qué se debe hacer; caso contrario, el fallo funcional decidirá por nosotros.

Dinos qué te ha parecido el artículo
Artículos recomendados
Aceite, lubricación y más: La trayectoria de Jorge Alarcón en Confiabilidad

Lubricación de Precisión - Selección y Cálculo de Viscosidad para Aceites de Transmisiones Industriales con Fórmula de Crook & Archard y con la Ecuación Ubbelohde-Walter

Auditoría de Lubricación

La Permeabilidad del Mantenimiento

Publica tu artículo en la revista #1 de Mantenimiento Industrial
Publicar un artículo en la revista es gratis, no tiene costo.
Solo debes asegurarte que no sea un artículo comercial.
¿Qué esperas?
O envía tu artículo directo: articulos@predictiva21.com
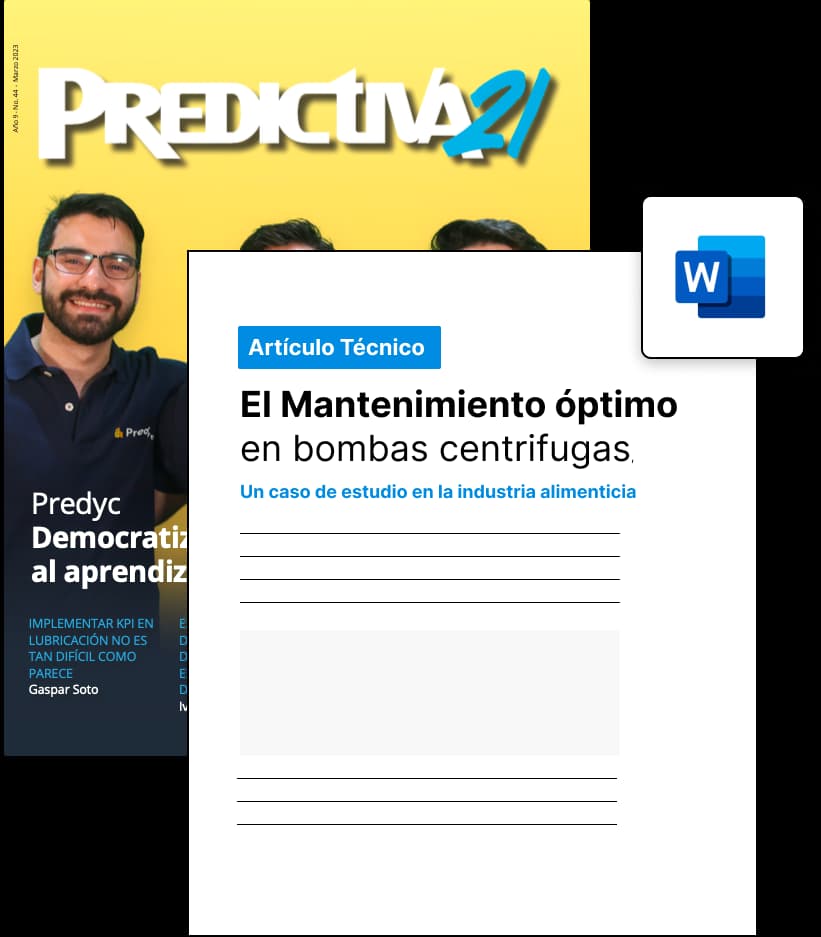
Análisis de Grasa y Ultrasonido para Rodamientos
Articulo 20 de enero de 2025A principios del 2010 tuve mi primer encuentro con una de las tecnologías del mantenimiento predictivo que, desde que la aprendí a utilizar, vi el potencial que tiene, y sobre todo, cuando se utiliza en combinación con otras herramientas del PdM.El ultrasonido propagado en aire para la inspección de rodamientos es, probablemente, una de las herramientas más sencillas y versátiles de utilizar, cuyos resultados pueden observarse casi inmediatamente.
Dependiendo de la fuente y el autor, el ultrasonido suele estar al inicio de la curva P-F, por delante de otras herramientas. Si bien esto es discutible y habrá casos en los que sí y otros en los que no, en lo que estamos de acuerdo es en que no podemos negar su valor y el beneficio que tiene en la determinación de la condición del rodamiento. En el peor de los escenarios, y si no se aplica ningún remedio, el ultrasonido inaudible tenderá a volverse audible, y el rodamiento estará muy cerca de un fallo funcional.

De manera muy simplista, la teoría que rige esta herramienta dice que el ultrasonido (dB) es el resultado de la fricción entre el elemento rodante, la pista interna, la jaula, el lubricante y otros elementos como la contaminación externa y el desgaste generado internamente. Para mantener el ultrasonido en un rango de normalidad, el lubricante —grasa, en el análisis del presente estudio— se añade para minimizar la fricción entre los componentes del rodamiento. De esta manera, se reduce el contacto, el desgaste y se extiende la vida en servicio del rodamiento para intentar alcanzar la vida esperada.
Alrededor de este concepto, y con el pujante ingreso de la Industria 4.0 al sector del PdM, se han diseñado sensores que añaden grasa de manera automática, en un volumen preciso para no sobrecargar de grasa el poco espacio que existe en el rodamiento, siempre que se detecten valores anómalos de ultrasonido.
Hasta aquí todo parece andar sobre ruedas, de manera tal que el engrase de rodamientos representa un antes y un después tras esta tecnología.Pero, ¿qué pasa con la grasa que está en servicio? Si hiciésemos un interrogatorio a dicha grasa, ¿qué nos diría? ¿Qué valor nos aportaría?
Grasa, ¿qué puede decirnos?
El primer informe de análisis de grasa en servicio en un rodamiento de motor eléctrico que tuve en mis manos databa de 1994. Año del mundial de fútbol, mientras yo veía el partido inaugural que enfrentaba al todopoderoso conjunto alemán contra 11 guerreros bolivianos, alguien bajo el sol del pleno verano estaba tomando una muestra de grasa de un rodamiento que había fallado, con la intención de saber si esa muestra podía dar alguna pista del fallo. Para ese tiempo, el análisis de aceite ya llevaba unas cuantas décadas reportando beneficios, pero la grasa… ¡a quién se le ocurriría analizar grasa!
Ahora sabemos que el análisis de grasa puede aportar mucho al mantenimiento y a la fiabilidad. Al menos algunos lo tenemos claro y sabemos cómo extraer el máximo provecho de esto.Una muestra de grasa obtenida adecuadamente evidencia la condición del rodamiento, puede desvelar si existe contaminación, de qué tipo, cuánta contaminación, si existe paso de corriente, si hubo mezcla de grasas, si esa mezcla es incompatible, y un largo etcétera. Esto es mucho pedir, al menos a un fluido no newtoniano.
[TIP] En la industria de procesado de grano para obtención de harinas, los rodamientos sufren un modo de fallo único, que no se observa en otras industrias. Se debe precisamente a la propiedad de los fluidos no newtonianos sometidos a altas cargas y presiones. ¿Te interesa saber más?
Volviendo a la grasa, su análisis es tan importante que, en la industria de aerogeneración, por citar un ejemplo, un análisis apropiado puede advertir de un fallo funcional del rodamiento principal, evitando así incurrir en un alto costo prevenible de mantenimiento.
Ultrasonido & Análisis de grasa, ¿qué aportan en conjunto?
Como hemos visto, de manera aislada ambas herramientas son increíbles, y si se utilizan adecuadamente, aportan muchos beneficios.
Pero, ¿podrían utilizarse en conjunto?
Llevaba años haciéndome esta pregunta. Había sido capaz de analizar unos 30 rodamientos, obteniendo muestras de grasas y ultrasonido, pero puntualmente, sin lograr la trazabilidad adecuada. Se necesita al menos dos puntos para trazar una recta, y con solo un punto no tenía más que suposiciones y no resultados coherentes.
Fue en una planta petroquímica donde pude calmar esa sed de conocimiento y durante dos años recolecté muestras tanto de grasa como de ultrasonido en un grupo de alrededor de 60 activos de diferentes características y condiciones. Los resultados y conclusiones presentadas en este artículo no pueden ser generalizados, ya que dependen mucho de factores como el tipo de rodamiento, la velocidad, las condiciones de operación, el ambiente operativo, los tipos de grasa utilizados en planta y el factor humano, además de la variabilidad del reengrase manual —no podemos sensorizar el 100% de los activos— al menos de momento.
Si bien la medida obtenida por el ultrasonido es única y se expresa en dB, el resultado del análisis de grasa está dividido en las siguientes variables:
- Desgastes ≤ 7 μ
- Desgastes ≥ 5 μ
- Desgaste de jaula (teniendo en cuenta que no había jaulas de poliamida)
- Consistencia de la grasa
- Incompatibilidad entre espesantes
- Diferentes viscosidades de aceite
De estas seis variables, los resultados mostrados en este breve artículo se centran únicamente en las dos primeras: desgastes del rodamiento. Por otro lado, se muestran únicamente resultados del rodamiento del lado del acoplamiento.
Al cabo de los dos años se obtuvieron alrededor de 500 muestras de cada tecnología. Utilizando un sistema de colores, de manera aislada, los resultados son los siguientes:

A grandes rasgos, la mayoría de los rodamientos tiene un comportamiento similar en función de los desgastes y el nivel de decibelios, y es posible sacar bastantes conclusiones de un análisis de este tipo.Tomaremos como ejemplo el rodamiento del lado de acoplamiento correspondiente a la unidad JBX – 102A.Este rodamiento tuvo que ser reemplazado al mes siguiente del último análisis, debido a que se podía oír la fricción producida internamente, y un posterior análisis evidenció un daño irreparable en la pista interna.
Es importante mencionar los siguientes puntos:
- El engrase se realiza dentro del concepto de mantenimiento preventivo, con una frecuencia definida.
- Los rodamientos se cambian en función del mantenimiento correctivo; es decir, operan hasta el fallo.
- La frecuencia de reengrase es bimensual, marcada con un recuadro en la figura 2.
- En los meses en los que no se realiza el reengrase, solo se recolecta información.
- El volumen de grasa añadido no supera el volumen calculado.


Cursos recomendados


%252FImagen%252FRAMPREDYC-1730060420837.webp%3Falt%3Dmedia%26token%3D2634a7f0-988e-4022-b91f-382503e6e9db&w=3840&q=75)





Resultados iniciales
Siguiendo la línea de tiempo, podemos ver algunos resultados remarcables:
- La línea base de ultrasonido para este rodamiento se sitúa en 38 dB, y la tecnología alerta que se ha rebasado este límite al cabo del tercer mes (Jun-18). ¡Punto a favor para el ultrasonido! El análisis de grasa no muestra que los desgastes se encuentren dentro de valores anómalos.
- Avanzamos en el tiempo y, tras el reengrase habitual, el ultrasonido regresa a valores normales. Cuando todo parece estar bien, los desgastes medidos por partículas inferiores a 7 μm superan el límite establecido (Sep-18). ¡Punto para el análisis de grasa! El análisis por ultrasonido se encuentra dentro de valores normales.
- Tras el reengrase de Nov-18, el ultrasonido está dentro de niveles normales, pero ambos tipos de desgastes han superado sus límites admisibles.
- A partir de este punto, entramos en una zona de no retorno con unas tendencias crecientes para las tres variables. A esto se debe sumar que, por fallo humano, no se realizó el reengrase de Feb-19 y, para cuadrar cuentas con el sistema de gestión de mantenimiento, se reengrasó dos meses seguidos: Mar-19 y Abr-19.
- Pasado este punto, los dB no se incrementan de manera exagerada como sí lo hacen los desgastes, hasta acabar en un fallo funcional del rodamiento.
Conclusiones: quizá sirvan de algo
Volviendo a la curva P-F, ¿quién se adelanta al fallo funcional del rodamiento en este caso? Difícil decir quién. Lo cierto es que podemos aprender cosas interesantes de esta situación:
- El ultrasonido, al menos en esta situación, es un gran indicador del resultado cualitativo de la condición del rodamiento. Sí, nos da un valor en dB y este resultado es cuantificable, pero no nos dice cómo es el desgaste.
- El análisis de grasa, al menos en esta situación, es un gran indicador del resultado cuantitativo de la condición del rodamiento. Sí, nos dice cuánto se desgasta, pero no cómo es la fricción entre los elementos del rodamiento.
- El desgaste de los componentes del rodamiento es resultado de la fricción, y esta a su vez genera más desgaste.
- El valor agregado cuando se trabaja con ambas tecnologías radica precisamente en determinar cómo es la fricción y cómo son los desgastes.
- Desafortunadamente, la grasa no fluye con facilidad y tiende a retener las partículas de desgaste generadas por fricción.
- Muchas configuraciones de rodamientos no tienen un punto de purga para eliminar la grasa y partículas incluidas de manera adecuada, por lo que los desgastes, en muchos casos, forman parte del sistema.
- Pasar de un mantenimiento preventivo, donde se engrasa en función de frecuencia, a uno predictivo, donde se engrasa en función de condición, requiere un sistema de seguimiento casi perfecto; la fricción y los desgastes no conocen límites.
- Los límites hay que respetarlos. Ya sean 80 km/h, 38 dB o 50 ppm de hierro, han sido puestos por alguna razón.
- Las acciones correctivas de mantenimiento deben ser apropiadas a los resultados obtenidos. Quizá no sea necesario reemplazar el rodamiento a los 44 dB/40 ppm Fe, pero será imprescindible definir qué se debe hacer; caso contrario, el fallo funcional decidirá por nosotros.

Dinos qué te ha parecido el artículo
Artículos recomendados
Aceite, lubricación y más: La trayectoria de Jorge Alarcón en Confiabilidad

Lubricación de Precisión - Selección y Cálculo de Viscosidad para Aceites de Transmisiones Industriales con Fórmula de Crook & Archard y con la Ecuación Ubbelohde-Walter

Auditoría de Lubricación

Gestión de la comunicación en proyectos del sector de servicios petroleros

Publica tu artículo en la revista #1 de Mantenimiento Industrial
Publicar un artículo en la revista es gratis, no tiene costo.
Solo debes asegurarte que no sea un artículo comercial.
¿Qué esperas?
O envía tu artículo directo: articulos@predictiva21.com
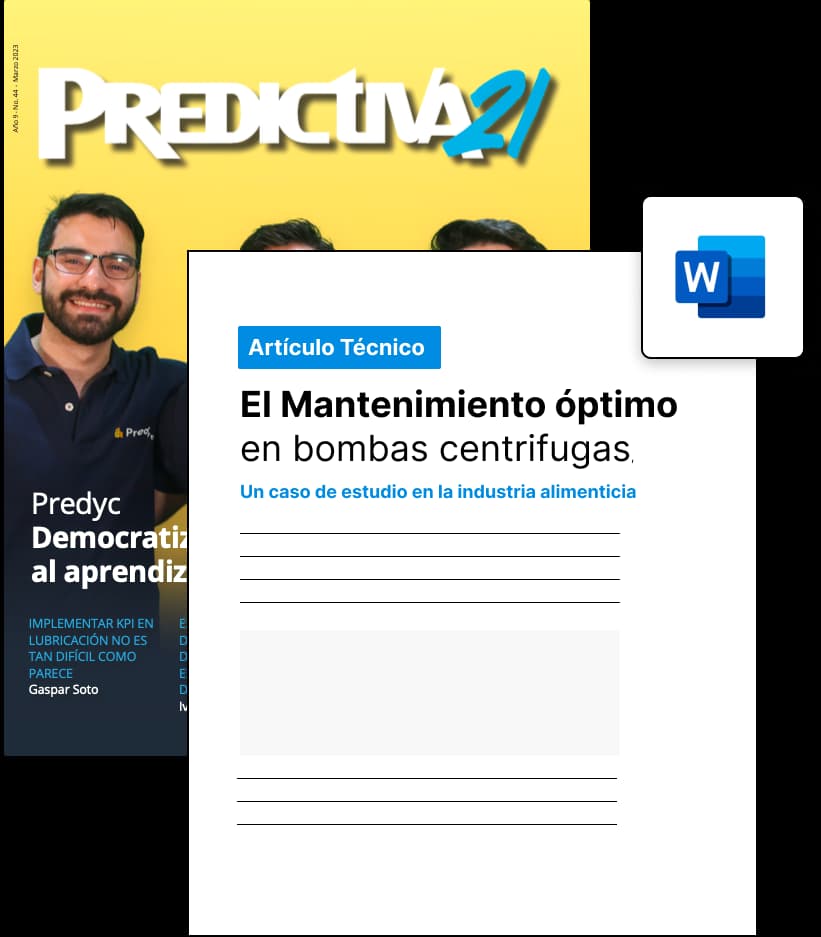