Mantenimiento, un listado de tareas o un proceso integral
Articulo31 de marzo de 2024
Hablemos de mantenimiento, mantenimiento típicamente lo consideramos como un listado de tareas, una lista de actividades que se tiene que hacer semanalmente o cuando hacemos un mantenimiento mayor.
Típicamente cuando hacemos un mantenimiento mayor es cuando dedicamos más tiempo a la planeación y programación del mantenimiento, se garantiza que se tengan las refacciones, al personal y todos los recursos necesarios para poder ejecutarlo de manera exitosa.
Pero en realidad mantenimiento no es solamente un listado de tareas o un listado de actividades, muchos grupos de Mantenimiento consideran que esto “es hacer Mantenimiento”, hacerlo de esta manera genera muchos desperdicios y hace que tengamos equipos de trabajo muy poco eficientes, donde no se logran realizar las actividades, las tareas se hacen de manera parcial y al final tenemos un impacto en la confiabilidad y eficiencia de la operación.
Pero no solo es el listado de tareas o actividades de Mantenimiento que generamos en nuestro día a día, aunado a eso es la falta de condiciones básicas de las maquinas, problemas de estandarización y falta de refacciones, problemas en los arranques de nuevos proyectos, la suma de todas las variables afecta de manera directa la eficiencia de las Operaciones, es por eso por lo que Mantenimiento es un proceso Integral.
Mantenimiento es un proceso Integral:
Mantenimiento parte desde la etapa de:
- Proyectos
- Instalación del activo
- Arranque
- Operación
- Ajustes
- Inspección y Cuidado diario de los activos
- Mantenimiento programado
En realidad, Mantenimiento está presente desde la correcta selección de un equipo hasta las intervenciones planeadas para mantener los equipos en las condiciones óptimas, garantizando la eficiencia de la Operación.
El Mantenimiento es un proceso Integral y una responsabilidad compartida.

1. Proyectos – Involucración Temprana
Cuando hablamos de mantenimiento como un proceso integral, tenemos que dar varios pasos hacia atrás, es decir el mantenimiento parte desde la definición del equipo que vamos a comprar para nuestra unidad de negocio, parte desde trabajar con el grupo de ingeniería y entender cual es la necesidad real que se tiene en la operación para hacer una buena adquisición del equipo, esto se llama involucración temprana.

Involucración temprana, es involucrar a los grupos de Mantenimiento y Operación desde la definición del equipo, en esta etapa la participación de ambos grupos es fundamental para garantizar que estamos cubriendo los aspectos que van a sumar para tener un arranque vertical y una operación confiables.
Algunos de los puntos importantes para considerar desde etapa de definición del proyecto:

En la etapa de la Ejecución del Proyecto se deben de desarrollar los PM, creación de los BOM e al ingreso al CMMS. Por la parte operativa los estándares y normas que nos van a ayudar a mantener el equipo en condiciones básicas.
Es decir, qué desde antes de ser instalado, estamos haciendo todo un proceso de participación integral con el área de proyectos, de esa manera garantizamos sumar los elementos para tener arranques verticales. “Esto es hacer Mantenimiento desde los Proyectos”.
¿Qué es un arranque vertical?
Garantizar que el equipo va a arrancar con los criterios de éxito definidos. Cuando hablamos de criterios de éxito, nos referimos, por ejemplo: Eficiencia y Desempeño, esto quiere decir que va a llegar a las eficiencias y el desempeño proyectado en un tiempo definido.
2. Operación – Cuidados Básicos del Equipo (MA)
Cuando hablamos de mantener el Equipo en Condiciones Básicas, nos referimos a una actividad que debe realizar el equipo de operaciones, esto es cómo el carro, el mantener el equipo limpio, con gasolina, con las presiones adecuadas en las llantas, la inspección de los niveles de aceite, agua, anticongelante, … estás son actividades del usuario, es decir de Operaciones, pero más aún, Mantenimiento Integral implica:

¿Qué es eliminar el deterioro forzado?
Regresemos al ejemplo del carro, podemos transitar por calles que son pavimentadas a cierta velocidad y no tenemos impacto en las suspensión, pero si de repente decidimos que un carro transite a alta velocidad por calles que tienen empedrados o algunos baches, definitivamente el carro sufrirá un desgaste acelerado en la suspensión; justo ahí enfocamos la parte del porqué mantenimiento implica una operación y ajustes correctos de la maquinaria, esto evita que el equipo tenga un deterioro acelerado. ¿Cómo lo vemos reflejado en nuestras operaciones? Cuando forzamos la operación de los equipos sometiéndolos a condiciones fuera de diseño, presiones, temperaturas, velocidades, … esto puede provocar golpes de ariete, piezas dañadas, fugas por altas presiones, ….

¿Cuáles son las condiciones básicas?
Cuando los equipos están teniendo un deterioro forzado vemos condiciones tales como: fugas de aceite, fugas de producto, reparaciones temporales que en muchos casos se reparan con cinchos, trapos, alambres, …. esto es tener un equipo fuera de condiciones básicas, debemos de tener equipos libres de este tipo de defectos, tener una mentalidad de “Cero Defectos”.
Las condiciones básicas de un equipo son: lubricado, limpio y ajustado, por supuesto sin defectos.
¿Por qué es tan importante mantener las condiciones básicas?
Del 65% al 85% de las fallas que tienen nuestros equipos es por falta de condiciones básicas, ahora pensemos la enorme carga de trabajo que tendrá un grupo de Mantenimiento cuando tenemos equipos sin condiciones básicas, es por ello que muchas empresas viven en emergencias todos los días, apagando fuegos y solo haciendo reparaciones temporales, el problema es que es un círculo vicioso y provoca desgaste en toda la organización y cómo consecuencia problemas de eficiencia operativa.
El rol del equipo de Operación: Operar los equipos en las condiciones y especificaciones establecidas, ajustar los equipos de acuerdo con los parámetros establecidos e inspeccionar y cuidar diariamente el equipo, esto se ve reflejado en la disponibilidad de los activos y por consiguiente en la eficiencia de la Operación. “Esto es hacer Mantenimiento desde Operaciones”.
La primera parte de la operación y ajustes de los equipos es sumamente importante, pero se ve afectada por la falta de inspección y cuidado de los equipos, esto se ve reflejado en fallas en los equipos, desgaste en los componentes provocando sobre ajustes, por mencionar algunos, por eso de vital importancia la transición del equipo de operación de:

El inspeccionar y cuidar el equipo en el día a día es una actividad vital y que sumamente importante en las tareas de Mantenimiento, pasamos de tener un grupo de Mantenimiento que trata de mantener las maquinas a un grupo de Mantenimiento y Operación manteniendo y cuidando diariamente y de manera programada las maquinas.

Ejemplo de estándares de Limpieza, Inspección y Lubricación.
- Mantenimiento – Condiciones Óptimas de los Activos
Mantenimiento es vital para los equipos, si regresamos el ejemplo del carro, la buena selección de un carro dependiendo de la necesidad que deseamos cubrir, aunado a una buena operación, inspección y cuidado diario por parte del usuario son fundamentales para mantener la unidad con las condiciones iniciales y con las condiciones básicas del mismo, pero mantener su continuidad es un tema de Mantenimiento Planeado, es decir que debemos de aplicar el Mantenimiento en la unidad para mantener las Condiciones Óptimas, esto nos permitirá tener el mayor ciclo de vida de los componentes y de la unidad, no tendremos averías imprevistas que detonen en emergencias y por consecuencia en costos no presupuestados, los objetivos de un equipo de Mantenimiento son:
- Mantener el equipo y proceso en condiciones óptimas.
- Lograr la eficacia y la eficiencia en costo de mantenimiento.
- Eficiencia del grupo de Mantenimiento.
Una parte vital de Mantenimiento es la definición de las Estrategias de Mantenimiento:

Es importante resaltar que las emergencias “NO” son una estrategia de Mantenimiento, muchas empresas lo consideran cómo parte de su día a día, pero es incorrecto, las emergencias provocan histéresis y stress en la cadena de suministro.
Las emergencias se suscitan o se detona cuando alguno de los puntos que hemos revisado no funciona, por ejemplo:
- Cuando el equipo no se instala correctamente, podemos tener problema de vibración, problemas de aflojamiento de máquina, … estas pueden detonar una avería y llevarnos a una emergencia.
- Cuando el equipo no se opera o ajusta de manera correcta tenemos un desgaste acelerado lo que puede detonar en una avería y puede provocar emergencias.
- Cuando no se inspecciona diariamente las maquinas podemos tener faltante de lubricante provocando una avería, podemos tener fugas… esto puede detonar en fallas del equipo o averías y provocar emergencias.
- Cuando no se realizó una inspección de Mantenimiento (PM) o una mala ejecución de Mantenimiento, puede detonar una avería y llevarnos a una emergencia.
Contar con un programa de Mantenimiento basado en una buena definición de la estrategia de Mantenimiento es fundamental para garantizar la confiabilidad de la operación, pero:
¿cómo se define la estrategia? En el año 1978 Stanley Nowlan y Howard F. Heap emitieron un informe que revolucionó el mundo del mantenimiento, lo titularon “RELIABILITY CENTERED MAINTENANCE” (MANTENIMIENTO CENTRADO EN LA CONFIABILIDAD), sigue siendo uno de los documentos más importantes en la historia del manejo de los activos físicos.

Este informe nos muestra que 89% de las posibles fallas no están asociadas a la edad, es decir a tiempo, que solo el 11% si lo está, por lo tanto, en nuestra operación debemos de definir nuestra estrategia considerando las PM´s (Mantenimiento Preventivo) de acuerdo a:
- Actividades de Mantenimiento Basadas en Tiempo
- Actividades de Mantenimiento Basadas en Condición
Actividades de Mantenimiento Basadas en Tiempo
Son actividades tales como: reemplazo de componentes de acuerdo a un tiempo establecido, número de vueltas, horas, …. Por ejemplo, en el carro: el cambio de aceite cada 10,000 km.
Actividades de Mantenimiento Basadas en Condición
Son actividades que están basadas en inspecciones que buscan identificar cuando una condición está cambiando y para ello se usan técnicas predictivas, tales como: Análisis de aceite, líquidos penetrantes, termografías, … aún, inspecciones visuales que buscan el cambio de la condición, este tipo de actividades se pueden usar desde la rutinas por el operador o PM por el grupo de Mantenimiento, por ejemplo en el carro: la inspección de los niveles de aceite, el desgaste de los limpiaparabrisas, ….
El tener un plan de Mantenimiento con las estrategias debidamente definidas y herramientas de análisis cuando se presenten averías, nos da cómo resultados un sistema sólido, ahora viene el proceso de ejecución en el día a día, para ello debemos de considerar las actividades claves de Mantenimiento en la gestión diaria de las Ordenes de Trabajo:
- Identificación
- Priorización
- Planeación
- Programación
- Ejecución
- Cierre
- Análisis
En resumen: la suma de cada uno de estos bloques nos da un Mantenimiento Integral, que el objetivo que busca es tener una operación eficiente, grupos de trabajo altamente productivos y el mejor costo de Manufactura.
Autor: Javier Carreño Medina
Fundador & CEO de Effizienter Wandel
Dinos qué te ha parecido el artículo
Artículos recomendados
Cálculo de cantidad de grasa para llenado inicial de rodamientos

Descubre la utilidad de la KPI

Curso TPM y lo que aprenderás en uno

Ingeniería de mantenimiento: pilar de las industrias

Publica tu artículo en la revista #1 de Mantenimiento Industrial
Publicar un artículo en la revista es gratis, no tiene costo.
Solo debes asegurarte que no sea un artículo comercial.
¿Qué esperas?
O envía tu artículo directo: articulos@predictiva21.com
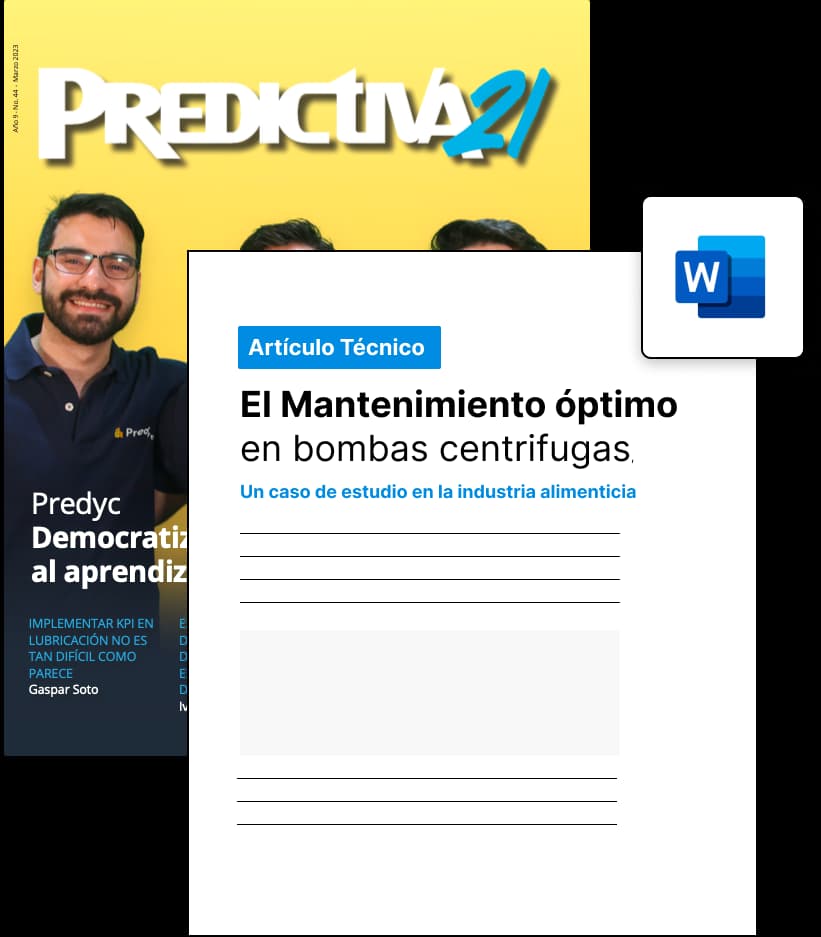
Mantenimiento, un listado de tareas o un proceso integral
Articulo 31 de marzo de 2024Hablemos de mantenimiento, mantenimiento típicamente lo consideramos como un listado de tareas, una lista de actividades que se tiene que hacer semanalmente o cuando hacemos un mantenimiento mayor.
Típicamente cuando hacemos un mantenimiento mayor es cuando dedicamos más tiempo a la planeación y programación del mantenimiento, se garantiza que se tengan las refacciones, al personal y todos los recursos necesarios para poder ejecutarlo de manera exitosa.
Pero en realidad mantenimiento no es solamente un listado de tareas o un listado de actividades, muchos grupos de Mantenimiento consideran que esto “es hacer Mantenimiento”, hacerlo de esta manera genera muchos desperdicios y hace que tengamos equipos de trabajo muy poco eficientes, donde no se logran realizar las actividades, las tareas se hacen de manera parcial y al final tenemos un impacto en la confiabilidad y eficiencia de la operación.
Pero no solo es el listado de tareas o actividades de Mantenimiento que generamos en nuestro día a día, aunado a eso es la falta de condiciones básicas de las maquinas, problemas de estandarización y falta de refacciones, problemas en los arranques de nuevos proyectos, la suma de todas las variables afecta de manera directa la eficiencia de las Operaciones, es por eso por lo que Mantenimiento es un proceso Integral.
Mantenimiento es un proceso Integral:
Mantenimiento parte desde la etapa de:
- Proyectos
- Instalación del activo
- Arranque
- Operación
- Ajustes
- Inspección y Cuidado diario de los activos
- Mantenimiento programado
En realidad, Mantenimiento está presente desde la correcta selección de un equipo hasta las intervenciones planeadas para mantener los equipos en las condiciones óptimas, garantizando la eficiencia de la Operación.
El Mantenimiento es un proceso Integral y una responsabilidad compartida.

1. Proyectos – Involucración Temprana
Cuando hablamos de mantenimiento como un proceso integral, tenemos que dar varios pasos hacia atrás, es decir el mantenimiento parte desde la definición del equipo que vamos a comprar para nuestra unidad de negocio, parte desde trabajar con el grupo de ingeniería y entender cual es la necesidad real que se tiene en la operación para hacer una buena adquisición del equipo, esto se llama involucración temprana.

Involucración temprana, es involucrar a los grupos de Mantenimiento y Operación desde la definición del equipo, en esta etapa la participación de ambos grupos es fundamental para garantizar que estamos cubriendo los aspectos que van a sumar para tener un arranque vertical y una operación confiables.
Algunos de los puntos importantes para considerar desde etapa de definición del proyecto:

En la etapa de la Ejecución del Proyecto se deben de desarrollar los PM, creación de los BOM e al ingreso al CMMS. Por la parte operativa los estándares y normas que nos van a ayudar a mantener el equipo en condiciones básicas.
Es decir, qué desde antes de ser instalado, estamos haciendo todo un proceso de participación integral con el área de proyectos, de esa manera garantizamos sumar los elementos para tener arranques verticales. “Esto es hacer Mantenimiento desde los Proyectos”.
¿Qué es un arranque vertical?
Garantizar que el equipo va a arrancar con los criterios de éxito definidos. Cuando hablamos de criterios de éxito, nos referimos, por ejemplo: Eficiencia y Desempeño, esto quiere decir que va a llegar a las eficiencias y el desempeño proyectado en un tiempo definido.
2. Operación – Cuidados Básicos del Equipo (MA)
Cuando hablamos de mantener el Equipo en Condiciones Básicas, nos referimos a una actividad que debe realizar el equipo de operaciones, esto es cómo el carro, el mantener el equipo limpio, con gasolina, con las presiones adecuadas en las llantas, la inspección de los niveles de aceite, agua, anticongelante, … estás son actividades del usuario, es decir de Operaciones, pero más aún, Mantenimiento Integral implica:

¿Qué es eliminar el deterioro forzado?
Regresemos al ejemplo del carro, podemos transitar por calles que son pavimentadas a cierta velocidad y no tenemos impacto en las suspensión, pero si de repente decidimos que un carro transite a alta velocidad por calles que tienen empedrados o algunos baches, definitivamente el carro sufrirá un desgaste acelerado en la suspensión; justo ahí enfocamos la parte del porqué mantenimiento implica una operación y ajustes correctos de la maquinaria, esto evita que el equipo tenga un deterioro acelerado. ¿Cómo lo vemos reflejado en nuestras operaciones? Cuando forzamos la operación de los equipos sometiéndolos a condiciones fuera de diseño, presiones, temperaturas, velocidades, … esto puede provocar golpes de ariete, piezas dañadas, fugas por altas presiones, ….

¿Cuáles son las condiciones básicas?
Cuando los equipos están teniendo un deterioro forzado vemos condiciones tales como: fugas de aceite, fugas de producto, reparaciones temporales que en muchos casos se reparan con cinchos, trapos, alambres, …. esto es tener un equipo fuera de condiciones básicas, debemos de tener equipos libres de este tipo de defectos, tener una mentalidad de “Cero Defectos”.
Las condiciones básicas de un equipo son: lubricado, limpio y ajustado, por supuesto sin defectos.
¿Por qué es tan importante mantener las condiciones básicas?
Del 65% al 85% de las fallas que tienen nuestros equipos es por falta de condiciones básicas, ahora pensemos la enorme carga de trabajo que tendrá un grupo de Mantenimiento cuando tenemos equipos sin condiciones básicas, es por ello que muchas empresas viven en emergencias todos los días, apagando fuegos y solo haciendo reparaciones temporales, el problema es que es un círculo vicioso y provoca desgaste en toda la organización y cómo consecuencia problemas de eficiencia operativa.
El rol del equipo de Operación: Operar los equipos en las condiciones y especificaciones establecidas, ajustar los equipos de acuerdo con los parámetros establecidos e inspeccionar y cuidar diariamente el equipo, esto se ve reflejado en la disponibilidad de los activos y por consiguiente en la eficiencia de la Operación. “Esto es hacer Mantenimiento desde Operaciones”.
La primera parte de la operación y ajustes de los equipos es sumamente importante, pero se ve afectada por la falta de inspección y cuidado de los equipos, esto se ve reflejado en fallas en los equipos, desgaste en los componentes provocando sobre ajustes, por mencionar algunos, por eso de vital importancia la transición del equipo de operación de:

El inspeccionar y cuidar el equipo en el día a día es una actividad vital y que sumamente importante en las tareas de Mantenimiento, pasamos de tener un grupo de Mantenimiento que trata de mantener las maquinas a un grupo de Mantenimiento y Operación manteniendo y cuidando diariamente y de manera programada las maquinas.

Ejemplo de estándares de Limpieza, Inspección y Lubricación.
- Mantenimiento – Condiciones Óptimas de los Activos
Mantenimiento es vital para los equipos, si regresamos el ejemplo del carro, la buena selección de un carro dependiendo de la necesidad que deseamos cubrir, aunado a una buena operación, inspección y cuidado diario por parte del usuario son fundamentales para mantener la unidad con las condiciones iniciales y con las condiciones básicas del mismo, pero mantener su continuidad es un tema de Mantenimiento Planeado, es decir que debemos de aplicar el Mantenimiento en la unidad para mantener las Condiciones Óptimas, esto nos permitirá tener el mayor ciclo de vida de los componentes y de la unidad, no tendremos averías imprevistas que detonen en emergencias y por consecuencia en costos no presupuestados, los objetivos de un equipo de Mantenimiento son:
- Mantener el equipo y proceso en condiciones óptimas.
- Lograr la eficacia y la eficiencia en costo de mantenimiento.
- Eficiencia del grupo de Mantenimiento.
Una parte vital de Mantenimiento es la definición de las Estrategias de Mantenimiento:

Es importante resaltar que las emergencias “NO” son una estrategia de Mantenimiento, muchas empresas lo consideran cómo parte de su día a día, pero es incorrecto, las emergencias provocan histéresis y stress en la cadena de suministro.
Las emergencias se suscitan o se detona cuando alguno de los puntos que hemos revisado no funciona, por ejemplo:
- Cuando el equipo no se instala correctamente, podemos tener problema de vibración, problemas de aflojamiento de máquina, … estas pueden detonar una avería y llevarnos a una emergencia.
- Cuando el equipo no se opera o ajusta de manera correcta tenemos un desgaste acelerado lo que puede detonar en una avería y puede provocar emergencias.
- Cuando no se inspecciona diariamente las maquinas podemos tener faltante de lubricante provocando una avería, podemos tener fugas… esto puede detonar en fallas del equipo o averías y provocar emergencias.
- Cuando no se realizó una inspección de Mantenimiento (PM) o una mala ejecución de Mantenimiento, puede detonar una avería y llevarnos a una emergencia.
Contar con un programa de Mantenimiento basado en una buena definición de la estrategia de Mantenimiento es fundamental para garantizar la confiabilidad de la operación, pero:
¿cómo se define la estrategia? En el año 1978 Stanley Nowlan y Howard F. Heap emitieron un informe que revolucionó el mundo del mantenimiento, lo titularon “RELIABILITY CENTERED MAINTENANCE” (MANTENIMIENTO CENTRADO EN LA CONFIABILIDAD), sigue siendo uno de los documentos más importantes en la historia del manejo de los activos físicos.

Este informe nos muestra que 89% de las posibles fallas no están asociadas a la edad, es decir a tiempo, que solo el 11% si lo está, por lo tanto, en nuestra operación debemos de definir nuestra estrategia considerando las PM´s (Mantenimiento Preventivo) de acuerdo a:
- Actividades de Mantenimiento Basadas en Tiempo
- Actividades de Mantenimiento Basadas en Condición
Actividades de Mantenimiento Basadas en Tiempo
Son actividades tales como: reemplazo de componentes de acuerdo a un tiempo establecido, número de vueltas, horas, …. Por ejemplo, en el carro: el cambio de aceite cada 10,000 km.
Actividades de Mantenimiento Basadas en Condición
Son actividades que están basadas en inspecciones que buscan identificar cuando una condición está cambiando y para ello se usan técnicas predictivas, tales como: Análisis de aceite, líquidos penetrantes, termografías, … aún, inspecciones visuales que buscan el cambio de la condición, este tipo de actividades se pueden usar desde la rutinas por el operador o PM por el grupo de Mantenimiento, por ejemplo en el carro: la inspección de los niveles de aceite, el desgaste de los limpiaparabrisas, ….
El tener un plan de Mantenimiento con las estrategias debidamente definidas y herramientas de análisis cuando se presenten averías, nos da cómo resultados un sistema sólido, ahora viene el proceso de ejecución en el día a día, para ello debemos de considerar las actividades claves de Mantenimiento en la gestión diaria de las Ordenes de Trabajo:
- Identificación
- Priorización
- Planeación
- Programación
- Ejecución
- Cierre
- Análisis
En resumen: la suma de cada uno de estos bloques nos da un Mantenimiento Integral, que el objetivo que busca es tener una operación eficiente, grupos de trabajo altamente productivos y el mejor costo de Manufactura.
Autor: Javier Carreño Medina
Fundador & CEO de Effizienter Wandel
Dinos qué te ha parecido el artículo
Artículos recomendados
Entrevista con Blas Galván

Mobius Institute lanza RELIABILITY CONNECT® y RELIABILITY CONNECT® en Español.

Planificación de mantenimiento mecánico

TENDENCIAS EN TEMAS DE DIVERSIDAD E INCLUSIÓN EN LOS PROCESOS DE ATRACCIÓN DE TALENTO: ¿CÓMO PROMOVER LA ÉTICA, LA DIVERSIDAD Y LA INCLUSIÓN?

Publica tu artículo en la revista #1 de Mantenimiento Industrial
Publicar un artículo en la revista es gratis, no tiene costo.
Solo debes asegurarte que no sea un artículo comercial.
¿Qué esperas?
O envía tu artículo directo: articulos@predictiva21.com
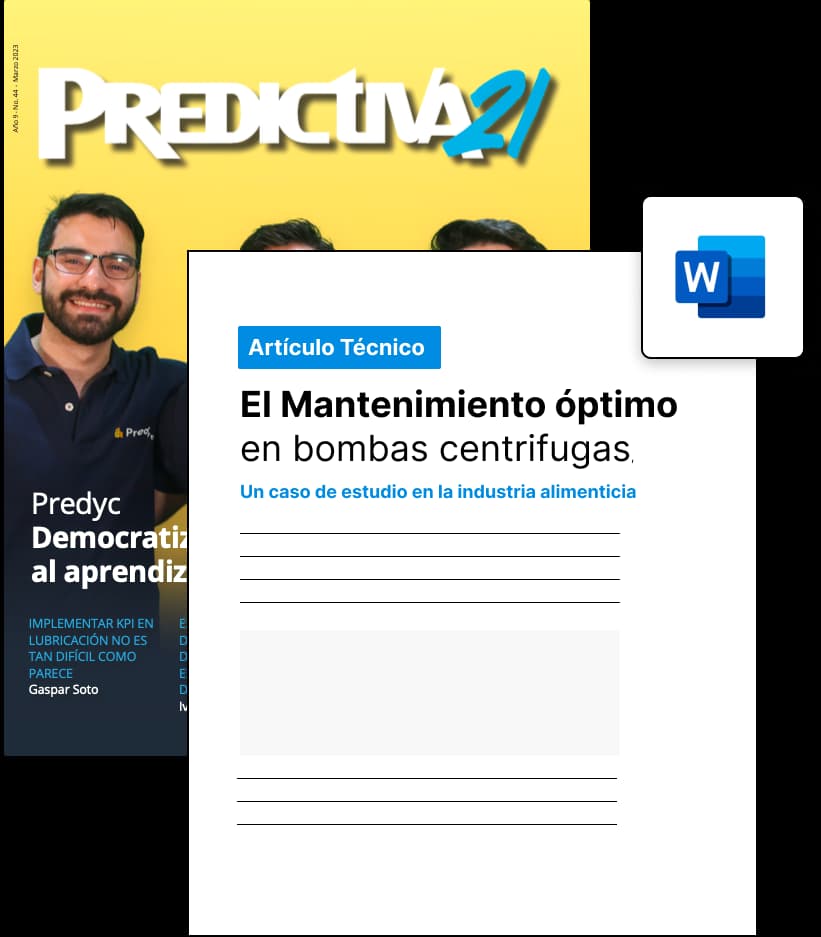