Optimización de Inventarios de Partes y Repuestos para el Mantenimiento (II Parte)
Articulo27 de abril de 2020
Repuestos Centrado en Confiabilidad (RCC)
Repuestos Centrado en Confiabilidad (RCC - Reliability-Centered Spares/RCS) es "un método para determinar el nivel de inventarios de repuestos en base a la vida a través de los costos y los requisitos de los equipos y la operación de mantenimiento que los soportes de inventario".
El RCC se puede aplicar en cualquier momento del ciclo de vida de un activo (es decir, antes de comprar las piezas de repuesto o cuando el activo ha estado en servicio durante algún tiempo). Se puede aplicar de forma selectiva al inventario usando el principio de Pareto (Análisis ABC), tomando en cuenta que un pequeño número de repuestos suelen ser los responsables de una gran proporción del valor de inventario y/o podrían inducir a grandes pérdidas de producción en el caso de falta de existencias.
Mayormente, el RCC se le aplica a los repuestos de bajo índice de rotación que derivan luego de realizar un Análisis ABC (ver Figura 4).

Este método se basa directamente en la metodología del Mantenimiento Centrado en Confiabilidad (MCC), fundamentándose en responder de forma lógica, cuatro preguntas que permiten establecer la política de stock adecuada para cada repuesto. Estas preguntas básicas son:
1. ¿Cuáles son los requerimientos de mantenimiento del equipo?
Los requerimientos se obtienen mediante la generación de los planes de mantenimiento, aplicando la metodología de MCC. Las restantes tres preguntas aseguran que el inventario de repuestos cumpla con los requerimientos de operación y mantenimiento.
2. ¿Qué pasa si no está disponible un repuesto?
El RCC se basa en la decisión de qué ocurre si no se dispone del repuesto y no necesariamente en las recomendaciones del fabricante, o en el juicio subjetivo de los grupos de ingeniería encargados de velar por el mantenimiento de los equipos. Este paso en el proceso hace posible decidir si el faltante es importante, y por lo tanto qué recursos son necesarios para reducir el riesgo cuando ocurra el faltante.
Al igual que el MCC, el RCC reconoce cinco categorías de consecuencias que son:
- Consecuencias de las fallas ocultas (Riesgo)
La falta de repuesto no es detectable por los operarios bajo circunstancias normales de operación. Para que una falla oculta tenga consecuencias graves, debe producirse una falla múltiple que requiera la activación del sistema o equipo que presente la falla oculta. También puede ser detectada por inspección periódica.
- Consecuencias para la Seguridad
La falta de repuesto tiene consecuencias para la seguridad si puede comprometer la integridad de los equipos o causar la lesión o muerte de alguna persona.
- Consecuencias para el Medio Ambiente
La falta de repuesto tiene consecuencias para el medio ambiente si conduce a la infracción de cualquier normativa o reglamento relacionado con el medio ambiente.
- Consecuencias Operacionales
La falta de repuesto trae consecuencias operacionales si tiene un efecto adverso directo sobre la capacidad operacional.
- Consecuencias No Operacionales
Son consecuencias no operacionales la falta de repuesto que no ejercen ningún efecto sobre el riesgo, la capacidad operacional, la seguridad o el medio ambiente. La única consecuencia derivada de estas fallas es el costo directo de la reparación.
¿Se puede anticipar el requerimiento del repuesto?
Algunos requerimientos de repuestos pueden ser anticipados como:
- Las partes o repuestos necesarios para mantenimientos preventivos o reemplazos rutinarios, que ocurren en intervalos regulares, sin tener en cuenta la condición del equipo.
- Las partes o repuestos sujetos a un monitoreo continuo de condición o mantenimiento predictivo, que pueden ser reemplazados al evidenciarse una falla potencial.
- Sin embargo, algunos requerimientos de repuestos son inherentemente no planificados por ser fallas aleatorias, sin signos obvios de desgaste o condición defectuosa.
¿Qué cantidad de repuesto es requerido en inventario?
El RCC reconoce que el 100% de disponibilidad es un ideal imposible de obtener. En los casos en que no es posible anticipar el requerimiento del repuesto, y por tanto minimizar los repuestos en inventario, la metodología RCC pregunta cuantas partes deben mantenerse en inventario para soportar el mantenimiento y la producción. Para ellos se debe establecer los requerimientos de desempeño los cuales dependen de las consecuencias que son:

Mediante el diagrama de decisión de RCC (ver Figura 5) se puede establecer la política de stock requerida para cada repuesto tomando en cuenta las distintas preguntas discutidas anteriormente.

Cursos recomendados




%252FImagen%252FRAMPREDYC-1730060420837.webp%3Falt%3Dmedia%26token%3D2634a7f0-988e-4022-b91f-382503e6e9db&w=3840&q=75)



Número optimo de repuestos (optimización costo-riesgo)
Este análisis permite determinar a través de la aplicación metodológica del OCR (Optimización Costo-Riesgo), la cantidad óptima de repuestos con bajo índice de rotación cuyas consecuencias son operacionales y deben ser almacenados en inventario local. Con ello se logra contar de forma óptima y mínimo riesgo, con los repuestos necesarios para el mantenimiento y las operaciones; apuntando al incremento de la disponibilidad y confiabilidad operacional de las instalaciones de la empresa y a la vez de optimizar costos de mantenimiento.
La optimización consiste en minimizar el costo total de operación de los equipos, el cual está integrado por los siguientes componentes:
- El costo de adquirir y almacenar los repuestos. El mismo incrementa en proporción directa con el inventario.
- El costo de indisponibilidad de la planta que utiliza los repuestos en el caso que existiera insuficiencias para cubrir las fallas o los mantenimientos programados. El mismo reduce con el aumento del inventario.
La Figura 6 muestra en forma gráfica los costos de inventario, costos de indisponibilidad y costos totales. Puede observarse en la curva de costo total un mínimo que corresponde al valor óptimo según costo riesgo.

Variables requeridas para aplicar el OCR
Capacidad Instalada:
- Número de Unidades Instaladas: consiste en la cantidad de unidades instaladas que utilizan el repuesto en estudio.
- Número de Unidades Requeridas para la operación normal: consiste en la cantidad de unidades que se requieren para operar de forma normal.
- Horas de Operación del Activo por Año: consiste en el número de horas de operación por año del repuesto en estudio.
Costos de Compra y de Pertenencia:
- Costos de Reabastecimiento: consiste en el costo correspondiente al reabastecimiento de la existencia cuando se produce la falla, normalmente estos costos son más elevados que los que costaría una compra ordinaria.
- Pérdida de Producción: estos costos corresponden a la pérdida en la recepción de ingresos generadas de la paralización del equipo por la indisponibilidad del repuesto.
- Costos de Aceleración de la compra: consiste en los costos de la compra de emergencia del repuesto.
Los costos descritos anteriormente se pueden subdividir en:
- Costo de Compra: consiste en el costo del repuesto.
- Costo Capital: consiste en el costo capital determinado por la corporación.
- Almacenaje y Mantenimiento: consiste en el costo de almacenar el repuesto y el costo de cualquier actividad de mantenimiento requerida por el fabricante para la conservación del repuesto.
- Vida Útil del repuesto en almacén o vida de obsolescencia: consiste en si el repuesto tiene un tiempo finito de uso, típicamente ocasionado por alguna de las siguientes razones:
- Vida limitada de almacenamiento, y luego no podría ser utilizado para cumplir con sus funciones.
- Posibilidad de obsolescencia.
- Puede que sea requerido para soportar una operación que se debe a una operación cerrada en un futuro previamente estimado.
Consecuencias de la Indisponibilidad:
Describe las consecuencias de la indisponibilidad del repuesto, las cuales pueden ser seleccionadas de una lista de opciones, siendo estas las siguientes:
- Parada de Planta.
- Perdida mayor de la variable de salida.
- Perdida pequeña de variable de salida.
- Perdidas de menor impacto.
- Fuera de Categoría.
- Impacto de no tener disponible el repuesto: consiste en los costos de penalización en los que se tiene que incurrir por la indisponibilidad del repuesto cuando este es requerido.
- Reincidencia en la indisponibilidad del repuesto: consiste en colocar los costos de penalización que tiene que sufragar por la reincidencia en la indisponibilidad del repuesto cuando éste es requerido.
Tiempo de Reabastecimiento:
- Unidades de Tiempo para el Reabastecimiento: consiste en seleccionar entre una lista de opciones, la unidad de tiempo que será utilizada para efectuar los cálculos.
- Tiempo de Reemplazo: consiste en la duración en tiempo desde la solicitud del repuesto hasta que el suplidor realiza el suministro.
- Tiempo de Penalización cuando ocurre una emergencia: consiste en el tiempo que tarda subsanar la emergencia cuando el repuesto no está disponible, normalmente representado por un incremento en los costos, ya sea del precio de compra del repuesto o de cualquier otro costo.
- Probabilidad de reparar el repuesto dañado: consiste en la posibilidad de que el repuesto dañado pueda ser reparado.
- Tiempo de reparación del repuesto dañado: consiste en el tiempo que tarda la reparación del repuesto dañado.
En la Figura 7 se puede observar un ejemplo de Número Optimo de Repuesto, tomando en cuenta el análisis de un sello tipo laberinto, parte de una válvula de un proceso medular de una planta petroquímica.

Referencias
- Cálculo de repuestos críticos - John Woodhouse
- Procedimiento para Mantener Máximos y Mínimos de Bienes en Almacenes de la Gerencia de Obras y Conservación. - Grupo Aeroportuario de la Ciudad de México, S.A. de C.V. - Octubre 2002.
- Una Aproximación a los Modelos de Inventarios - Teoría de Inventarios - www.investigacion-operaciones.com/modelo inventarios.htm - Agosto 2013.
- Modelo de Planificación y Control de Inventarios para Mantenimiento - Ing. Alfredo J. Leal M. - Universidad del Zulia - Febrero de 2004.
- Reliability-centred Spares (RCS) - Mutual Consultants LTD -http://www.mutualconsultants.co.uk/rcs.html - Enero 2014.
Autor: Custodio José De Piño Brito
Ingeniero de Sistemas. U.B.A., 1991-1996, Maracay, Venezuela.
T.S.U. en Informática. IUTIRLA, 1990 -1993, Maturín, Venezuela.
Mantenimiento Mecánico. INAPET (CIED), 1977-1979 Anaco, Venezuela.
Dinos qué te ha parecido el artículo
Artículos recomendados
Entrevista Angeles Ysidro

Lubricantes sintéticos: usos y características

Tecnologías de la industria 4.0 que están ayudando a modernizar la gestión de activos y del mantenimiento

¿Quién debe planificar los trabajos de Mantenimiento?

Publica tu artículo en la revista #1 de Mantenimiento Industrial
Publicar un artículo en la revista es gratis, no tiene costo.
Solo debes asegurarte que no sea un artículo comercial.
¿Qué esperas?
O envía tu artículo directo: articulos@predictiva21.com
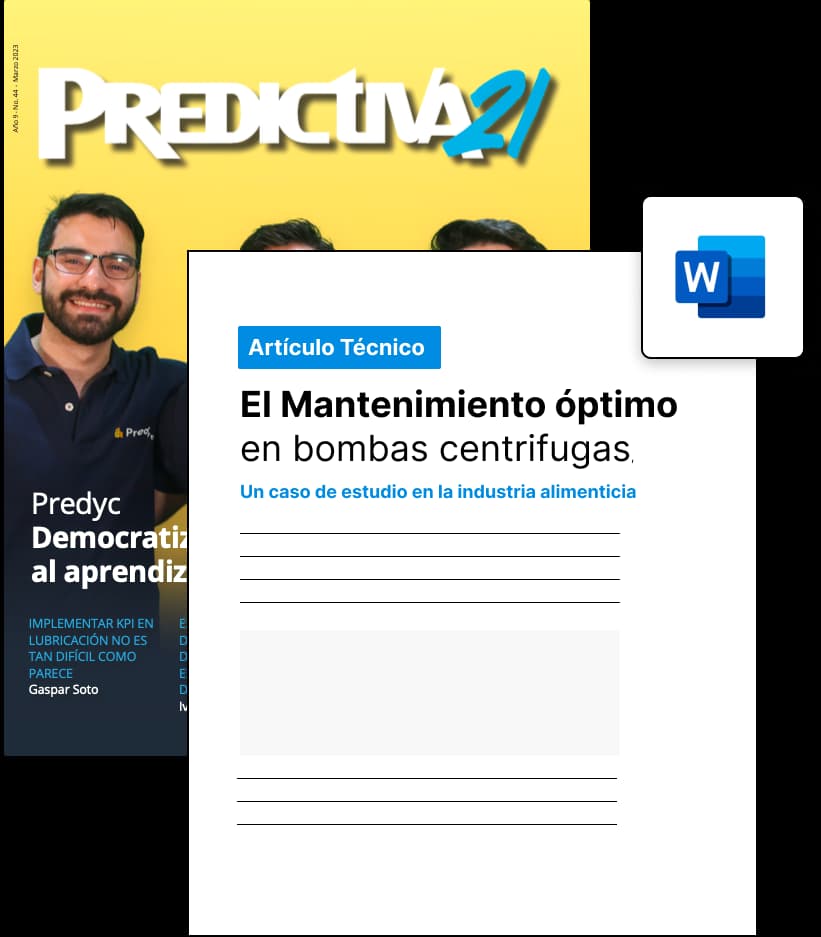
Optimización de Inventarios de Partes y Repuestos para el Mantenimiento (II Parte)
Articulo 27 de abril de 2020Repuestos Centrado en Confiabilidad (RCC)
Repuestos Centrado en Confiabilidad (RCC - Reliability-Centered Spares/RCS) es "un método para determinar el nivel de inventarios de repuestos en base a la vida a través de los costos y los requisitos de los equipos y la operación de mantenimiento que los soportes de inventario".
El RCC se puede aplicar en cualquier momento del ciclo de vida de un activo (es decir, antes de comprar las piezas de repuesto o cuando el activo ha estado en servicio durante algún tiempo). Se puede aplicar de forma selectiva al inventario usando el principio de Pareto (Análisis ABC), tomando en cuenta que un pequeño número de repuestos suelen ser los responsables de una gran proporción del valor de inventario y/o podrían inducir a grandes pérdidas de producción en el caso de falta de existencias.
Mayormente, el RCC se le aplica a los repuestos de bajo índice de rotación que derivan luego de realizar un Análisis ABC (ver Figura 4).

Este método se basa directamente en la metodología del Mantenimiento Centrado en Confiabilidad (MCC), fundamentándose en responder de forma lógica, cuatro preguntas que permiten establecer la política de stock adecuada para cada repuesto. Estas preguntas básicas son:
1. ¿Cuáles son los requerimientos de mantenimiento del equipo?
Los requerimientos se obtienen mediante la generación de los planes de mantenimiento, aplicando la metodología de MCC. Las restantes tres preguntas aseguran que el inventario de repuestos cumpla con los requerimientos de operación y mantenimiento.
2. ¿Qué pasa si no está disponible un repuesto?
El RCC se basa en la decisión de qué ocurre si no se dispone del repuesto y no necesariamente en las recomendaciones del fabricante, o en el juicio subjetivo de los grupos de ingeniería encargados de velar por el mantenimiento de los equipos. Este paso en el proceso hace posible decidir si el faltante es importante, y por lo tanto qué recursos son necesarios para reducir el riesgo cuando ocurra el faltante.
Al igual que el MCC, el RCC reconoce cinco categorías de consecuencias que son:
- Consecuencias de las fallas ocultas (Riesgo)
La falta de repuesto no es detectable por los operarios bajo circunstancias normales de operación. Para que una falla oculta tenga consecuencias graves, debe producirse una falla múltiple que requiera la activación del sistema o equipo que presente la falla oculta. También puede ser detectada por inspección periódica.
- Consecuencias para la Seguridad
La falta de repuesto tiene consecuencias para la seguridad si puede comprometer la integridad de los equipos o causar la lesión o muerte de alguna persona.
- Consecuencias para el Medio Ambiente
La falta de repuesto tiene consecuencias para el medio ambiente si conduce a la infracción de cualquier normativa o reglamento relacionado con el medio ambiente.
- Consecuencias Operacionales
La falta de repuesto trae consecuencias operacionales si tiene un efecto adverso directo sobre la capacidad operacional.
- Consecuencias No Operacionales
Son consecuencias no operacionales la falta de repuesto que no ejercen ningún efecto sobre el riesgo, la capacidad operacional, la seguridad o el medio ambiente. La única consecuencia derivada de estas fallas es el costo directo de la reparación.
¿Se puede anticipar el requerimiento del repuesto?
Algunos requerimientos de repuestos pueden ser anticipados como:
- Las partes o repuestos necesarios para mantenimientos preventivos o reemplazos rutinarios, que ocurren en intervalos regulares, sin tener en cuenta la condición del equipo.
- Las partes o repuestos sujetos a un monitoreo continuo de condición o mantenimiento predictivo, que pueden ser reemplazados al evidenciarse una falla potencial.
- Sin embargo, algunos requerimientos de repuestos son inherentemente no planificados por ser fallas aleatorias, sin signos obvios de desgaste o condición defectuosa.
¿Qué cantidad de repuesto es requerido en inventario?
El RCC reconoce que el 100% de disponibilidad es un ideal imposible de obtener. En los casos en que no es posible anticipar el requerimiento del repuesto, y por tanto minimizar los repuestos en inventario, la metodología RCC pregunta cuantas partes deben mantenerse en inventario para soportar el mantenimiento y la producción. Para ellos se debe establecer los requerimientos de desempeño los cuales dependen de las consecuencias que son:

Mediante el diagrama de decisión de RCC (ver Figura 5) se puede establecer la política de stock requerida para cada repuesto tomando en cuenta las distintas preguntas discutidas anteriormente.

Cursos recomendados




%252FImagen%252FRAMPREDYC-1730060420837.webp%3Falt%3Dmedia%26token%3D2634a7f0-988e-4022-b91f-382503e6e9db&w=3840&q=75)



Número optimo de repuestos (optimización costo-riesgo)
Este análisis permite determinar a través de la aplicación metodológica del OCR (Optimización Costo-Riesgo), la cantidad óptima de repuestos con bajo índice de rotación cuyas consecuencias son operacionales y deben ser almacenados en inventario local. Con ello se logra contar de forma óptima y mínimo riesgo, con los repuestos necesarios para el mantenimiento y las operaciones; apuntando al incremento de la disponibilidad y confiabilidad operacional de las instalaciones de la empresa y a la vez de optimizar costos de mantenimiento.
La optimización consiste en minimizar el costo total de operación de los equipos, el cual está integrado por los siguientes componentes:
- El costo de adquirir y almacenar los repuestos. El mismo incrementa en proporción directa con el inventario.
- El costo de indisponibilidad de la planta que utiliza los repuestos en el caso que existiera insuficiencias para cubrir las fallas o los mantenimientos programados. El mismo reduce con el aumento del inventario.
La Figura 6 muestra en forma gráfica los costos de inventario, costos de indisponibilidad y costos totales. Puede observarse en la curva de costo total un mínimo que corresponde al valor óptimo según costo riesgo.

Variables requeridas para aplicar el OCR
Capacidad Instalada:
- Número de Unidades Instaladas: consiste en la cantidad de unidades instaladas que utilizan el repuesto en estudio.
- Número de Unidades Requeridas para la operación normal: consiste en la cantidad de unidades que se requieren para operar de forma normal.
- Horas de Operación del Activo por Año: consiste en el número de horas de operación por año del repuesto en estudio.
Costos de Compra y de Pertenencia:
- Costos de Reabastecimiento: consiste en el costo correspondiente al reabastecimiento de la existencia cuando se produce la falla, normalmente estos costos son más elevados que los que costaría una compra ordinaria.
- Pérdida de Producción: estos costos corresponden a la pérdida en la recepción de ingresos generadas de la paralización del equipo por la indisponibilidad del repuesto.
- Costos de Aceleración de la compra: consiste en los costos de la compra de emergencia del repuesto.
Los costos descritos anteriormente se pueden subdividir en:
- Costo de Compra: consiste en el costo del repuesto.
- Costo Capital: consiste en el costo capital determinado por la corporación.
- Almacenaje y Mantenimiento: consiste en el costo de almacenar el repuesto y el costo de cualquier actividad de mantenimiento requerida por el fabricante para la conservación del repuesto.
- Vida Útil del repuesto en almacén o vida de obsolescencia: consiste en si el repuesto tiene un tiempo finito de uso, típicamente ocasionado por alguna de las siguientes razones:
- Vida limitada de almacenamiento, y luego no podría ser utilizado para cumplir con sus funciones.
- Posibilidad de obsolescencia.
- Puede que sea requerido para soportar una operación que se debe a una operación cerrada en un futuro previamente estimado.
Consecuencias de la Indisponibilidad:
Describe las consecuencias de la indisponibilidad del repuesto, las cuales pueden ser seleccionadas de una lista de opciones, siendo estas las siguientes:
- Parada de Planta.
- Perdida mayor de la variable de salida.
- Perdida pequeña de variable de salida.
- Perdidas de menor impacto.
- Fuera de Categoría.
- Impacto de no tener disponible el repuesto: consiste en los costos de penalización en los que se tiene que incurrir por la indisponibilidad del repuesto cuando este es requerido.
- Reincidencia en la indisponibilidad del repuesto: consiste en colocar los costos de penalización que tiene que sufragar por la reincidencia en la indisponibilidad del repuesto cuando éste es requerido.
Tiempo de Reabastecimiento:
- Unidades de Tiempo para el Reabastecimiento: consiste en seleccionar entre una lista de opciones, la unidad de tiempo que será utilizada para efectuar los cálculos.
- Tiempo de Reemplazo: consiste en la duración en tiempo desde la solicitud del repuesto hasta que el suplidor realiza el suministro.
- Tiempo de Penalización cuando ocurre una emergencia: consiste en el tiempo que tarda subsanar la emergencia cuando el repuesto no está disponible, normalmente representado por un incremento en los costos, ya sea del precio de compra del repuesto o de cualquier otro costo.
- Probabilidad de reparar el repuesto dañado: consiste en la posibilidad de que el repuesto dañado pueda ser reparado.
- Tiempo de reparación del repuesto dañado: consiste en el tiempo que tarda la reparación del repuesto dañado.
En la Figura 7 se puede observar un ejemplo de Número Optimo de Repuesto, tomando en cuenta el análisis de un sello tipo laberinto, parte de una válvula de un proceso medular de una planta petroquímica.

Referencias
- Cálculo de repuestos críticos - John Woodhouse
- Procedimiento para Mantener Máximos y Mínimos de Bienes en Almacenes de la Gerencia de Obras y Conservación. - Grupo Aeroportuario de la Ciudad de México, S.A. de C.V. - Octubre 2002.
- Una Aproximación a los Modelos de Inventarios - Teoría de Inventarios - www.investigacion-operaciones.com/modelo inventarios.htm - Agosto 2013.
- Modelo de Planificación y Control de Inventarios para Mantenimiento - Ing. Alfredo J. Leal M. - Universidad del Zulia - Febrero de 2004.
- Reliability-centred Spares (RCS) - Mutual Consultants LTD -http://www.mutualconsultants.co.uk/rcs.html - Enero 2014.
Autor: Custodio José De Piño Brito
Ingeniero de Sistemas. U.B.A., 1991-1996, Maracay, Venezuela.
T.S.U. en Informática. IUTIRLA, 1990 -1993, Maturín, Venezuela.
Mantenimiento Mecánico. INAPET (CIED), 1977-1979 Anaco, Venezuela.
Dinos qué te ha parecido el artículo
Artículos recomendados
Gestión Tribológica de Activos® - Su ejecución y medición a través del Indice Techgnosis (ITG®)

Mantenimiento Centrado en Fiabilidad: Análisis de mejoras en el mantenimiento y explotación de un sistema industrial

El internet de las cosas (IoT): pilar de la industria 4.0

Selección de Potencia del Motor Eléctrico en Compresores Reciprocantes de Múltiples Etapas

Publica tu artículo en la revista #1 de Mantenimiento Industrial
Publicar un artículo en la revista es gratis, no tiene costo.
Solo debes asegurarte que no sea un artículo comercial.
¿Qué esperas?
O envía tu artículo directo: articulos@predictiva21.com
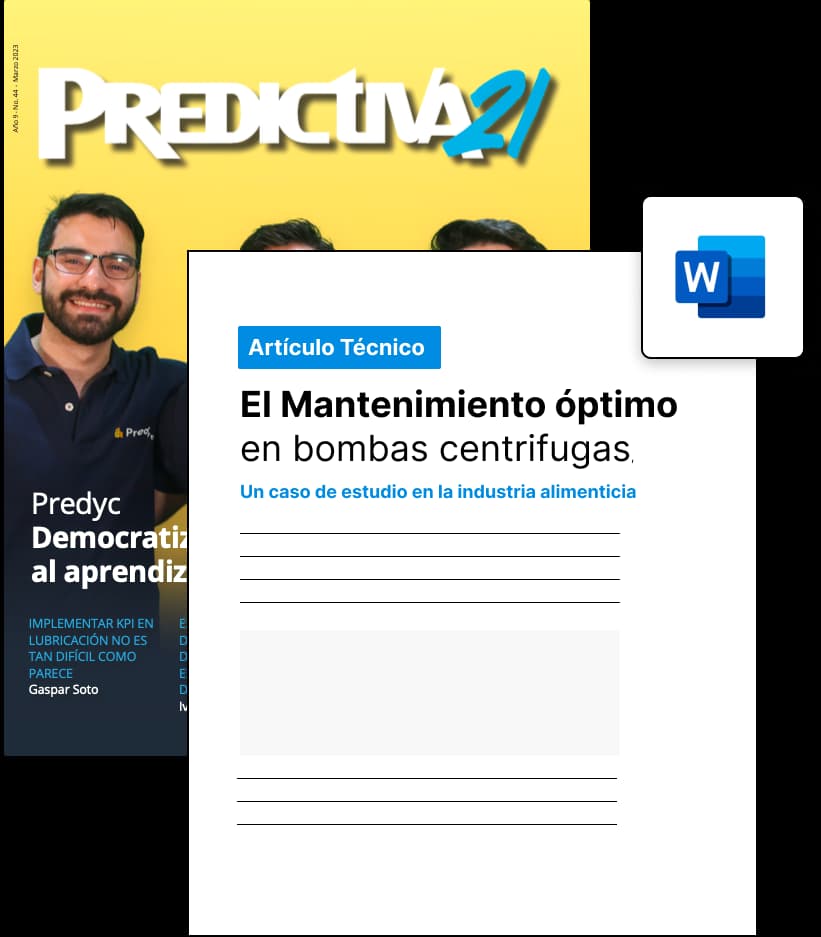