La otra visión de la Confiabilidad Operacional
Articulo2 de octubre de 2019
En virtud de hacer extensiva La Otra Visión de la Confiabilidad Operacional desde una perspectiva simplista y de fácil comprensión al lector, le presento una manera práctica y sencilla la metodología de Confiabilidad Operacional «Criticidad» aplicada en la industria Petrolera Nacional en Venezuela.
En base a las experiencias vividas en los Campos Petroleros de Venezuela y en la cotidianidad en las áreas operacionales, me permito compartir en estas cortas líneas para describir La otra visión de ver el Mundo de la Confiabilidad Operacional y su aplicación tradicional, cuya finalidad radica en mejorar la rentabilidad de los procesos productivos y entendiendo que cada día, se dedican enormes esfuerzos destinados a visualizar, identificar, analizar e implantar mejores prácticas operacionales para la solución de problemas y toma de decisiones efectivas y acertadas, que involucren un alto impacto en las áreas operativas de una empresa.
En líneas generales, el objetivo fundamental de las empresas, está en fortalecer sus metas del negocio y obtener niveles máximos de eficiencia, eficacia y confiabilidad operacional, que satisfagan y orienten los niveles de productividad de un negocio. Lo que traerán consigo una serie de desafíos los cuales deben ser afrontados en corto, mediano y largo plazo, según sea el caso.
De este modo, la actividad empresarial se acompaña esencialmente de la incertidumbre que predetermina la necesidad de elegir una de las diferentes alternativas para la ejecución de un diagnóstico certero. Considerando una gama de metodologías de Confiabilidad Operacional, en la cual logre determinar la condición actual de un sistema, muy distinta a la manera tradicional que se conoce de realizar un diagnóstico.
La finalidad de todo estudio es ir de lo simple a lo complejo, para ello se presenta una serie de definiciones básicas a conocer cuando se dispongan a realizar un Análisis De Criticidad.
¿Por qué es Importante la Aplicación de la Metodología de Criticidad para Realizar Diagnósticos?
Sencillo, nos permite establecer prioridades de instalaciones, sistemas y equipos, cuyo fin es facilitar la toma de decisiones efectivas, direccionando el esfuerzo y los recursos en áreas donde sea necesario mejorar basada en la realidad actual y garantizar los niveles de confiabilidad operacional de los activos.
Palabras Clave: Confiabilidad operacional, criticidad, frecuencia de falla, índice de probabilidad de falla, taxonomía, contexto operacional.
Abreviaturas. AC: Análisis de criticidad. ENT: Equipo natural de trabajo. IPF: Índice de probabilidad de falla. MBND: Miles de barriles día de petróleo. MMPCND: Millones de pies cúbicos normal día de gas. MBA: Miles de barriles de agua. %AyS: Porcentaje de Agua y Sólidos. SPC: Sistema de protección catódica. TPFS: Tiempo promedio fuera de servicio.
Un Análisis de Criticidad (AC): Es una metodología que establece la jerarquía de activos, considerando variables de frecuencia (FF) e índice de probabilidad de falla (IPF) y sus consecuencias, con la finalidad de direccionar esfuerzo y recursos en áreas a mejorar que impacten la confiabilidad operacional. (Jean Farfán)
Activo: Es un elemento tangible o intangible capitalizable de naturaleza permanente, que cumple una función en un proceso productivo y está sujeto a acciones de mantenimiento [1].
Análisis Funcional del Activo: Es la identificación de la relación o interconexión entre los diferentes procesos, sistemas y subsistemas de una instalación [1].
Criticidad: Es un método de fácil manejo y compresión, cuya virtud es proveer donde mejorar el activo y jerarquizarlos. Es representado a través de una Matriz 5×5, que denota el valor cuantitativo a mejorar, al combinar la frecuencia de ocurrencia o índice de probabilidad de fallas con las consecuencias que tienen. [1].
La fórmula utilizada es:

Fuente: Petróleos de Venezuela Norma MM-01-01-02 (2011)
Consecuencias: Resultado de un evento. Pueden existir una o más consecuencias de un evento, las cuales sean expresadas cualitativa o cuantitativamente [1].
Consecuencias = ((Nivel de producción. x tiempo promedio fuera de servicio (TPFS) x Impacto de producción.) / 24 horas + Costo de reparación + Impacto en Seguridad. + Impacto Ambiental).
Ciclo de vida de un Activo: Es todo lo que ocurre con el activo desde la idea con la cual se lo crea o incorpora a un proyecto, hasta su disposición final. Este ciclo de vida tiene asociado el “Costo de Ciclo de Vida”, el cual es la sumatoria de todos los costos asignables al activo (directos e indirectos, variables y fijos). [2] .
Etapas del Ciclo de Vida de un Activo

Fuente: https://cmc-latam. com/gestion-activos-ciclo-vida (2019)
Confiabilidad Operacional: Es la filosofía de trabajo orientada en una serie de procesos de mejora continua, que incorporan en forma sistemática, herramientas de diagnóstico, metodologías de análisis y nuevas tecnologías, para optimizar la gestión, planeación, ejecución y control de la productividad; además lleva implícita la capacidad de una instalación (procesos, tecnología, gente), para cumplir su función o el propósito que se espera de ella, dentro de sus límites de diseño y bajo un específico contexto operacional. [1].
Contexto Operacional: Es el conjunto de circunstancias que condicionan la operación de un equipo o sistema, están definidas como: localidad, ambiente, fluido de servicio, parámetros de operación, lineamientos ambientales, de seguridad y producción, calidad y disponibilidad de los insumos requeridos, configuración de trabajo, flexibilidad operacional, redundancia, alarmas, monitoreo de primera línea y otros. [1].
Costo – Beneficio: Es una herramienta financiera que mide la relación entre los costos y beneficios asociados a un proyecto de inversión con el fin de evaluar su rentabilidad, entendiéndose por proyecto de inversión no solo como la creación de un nuevo negocio, sino también, como inversiones que se pueden hacer en un negocio en marcha tales como el desarrollo de nuevo producto o la adquisición de nueva maquinaria. [3].
Custodio de Instalación: Es el ente encargado de velar por el funcionamiento de los activos dentro de los parámetros operacionales establecidos, con el fin de lograr el producto bajo las especificaciones requeridas. [1].
Datos del Equipo: Son los parámetros técnicos, operativos y ambientales que caracterizan el diseño y la utilización de una unidad de equipo. [1].
Equipo: Es un elemento de producción dentro de un arreglo lógico funcional que cumple con los siguientes criterios:
- Está sujeto a planes de mantenimiento.
- No es componente, parte o pieza (ejemplos: sello mecánico, manómetros, haz de tubo, tarjeta electrónica, entre otros).
- El valor de reemplazo es mayor que el costo de mantenimiento.
- Es trazable en el tiempo.
- Está sujeto a un control de gastos ocasionados por la aplicación de mantenimiento correctivo, preventivo, proyectos de mantenimiento y paradas de planta. [1].
Equipo Natural de Trabajo (ENT): Es un equipo multidisciplinario constituido por especialistas o actores de diferentes disciplinas que tienen como objetivo guiar la implementación de estrategias de mantenimiento y confiabilidad, la sincronización de actividades, el establecimiento de planes integrales de acción y la optimización de los costos de producción y mantenimiento en la organización. Entre los actores o especialistas que pueden conformar el ENT se encuentran: custodios de instalaciones, planificador, programador, ejecutor, ente técnico, entre otros. [1].
Estructura Taxonómica: Es una representación por niveles de los activos de una organización en un arreglo lógico y funcional en el SGCM, a través del cual se realizan todos los documentos técnicos y operativos que permiten controlar y asegurar el registro de todas las operaciones de mantenimiento. [4].

Fuente: Petróleos de Venezuela Norma MM-01-01-07 (2012)
Falla: Es la pérdida de capacidad para realizar su función según se requiera. [5].
Función: Es la capacidad de un elemento o activo de brindar un determinado servicio según las condiciones de trabajo, respetando su diseño. [1].
Índice de Probabilidad de Falla (IPF): Es un Índice que se calcula en función de las actividades de inspección y mantenimiento que se llevan a cabo en cada uno de los sistemas, considerando factores que están referidos a condiciones operacionales, corrosión, integridad mecánica, desempeño, control y protección, entre otras. [6].
Instalación: Es el tercer nivel de la estructura taxonómica que hace referencia al macroproceso productivo, localización o disposición geográfica. [1].
Modo de Falla: Es cualquier evento que genera una falla funcional- [7].
Mantenimiento: Es una combinación de todas las acciones técnicas y administrativas, que pretenden retener o restaurar un activo en un estado en el que pueda ejecutar una(s) función(es) requerida(s). [1].
Metodología de los Puntos: La estructura de criticidad que provee la llamada “metodología de los puntos” tiene su origen en el movimiento de mejora de la confiabilidad de los procesos productivos que se inició en la industria petrolera del Mar del Norte en la década del 90 [manual de criticidad de PDVSA – CIED] y hoy es ampliamente utilizada en la industria petrolera; por supuesto, con múltiples adecuaciones y modificaciones. La base fundamental de este enfoque es el establecimiento de un sistema de puntos para valorar la criticidad; y de una matriz cuyos rangos de frecuencia y consecuencia se expresan en “puntos”.
Se recomienda la participación de “equipos naturales de trabajo” en la valoración de la criticidad para minimizar el sesgo y la subjetividad. [16].

Fuente: R2M. S.A Reliability and Risk Management , Análisis De Criticidad Integral De Activos (2007)
Planta / Unidad: Es el cuarto nivel de la estructura taxonómica que hace referencia a un proceso productivo que integra la instalación. [1].
Sección / Sistema: Es el quinto nivel de la estructura taxonómica que hace referencia a las subdivisiones que componen una planta o unidad. [1].
Sub-Sección/Sub-Sistema o Lazo: Es el nivel 5.1 de la estructura taxonómica, definido en la Norma Técnica PDVSA MM–01–01–07, que se establece para ser utilizado según la complejidad de la organización y el contexto operacional que requiera un nivel de detalle adicional a los cinco niveles previos. Ejemplo: sub–sistema de ventilación, sub–sistema de bombeo, sub–sistema de alimentación, lazo de control, entre otros. [1].
Tiempo promedio entre fallas (TPEF): Es el tiempo promedio entre una falla y otra, éste incluye el tiempo fuera de servicio. [1].
Técnicas de análisis de riesgo: Existen diferentes técnicas para dimensionar el riesgo, tales como: Cualitativas, Semi- Cuantitativas y Cuantitativas.
Premisas básicas a considerar en un Estudio de Criticidad
- Utilizar el Contexto Operacional para identificar el proceso y su funcionamiento.
- Evaluar el entorno en donde se encuentra el activo.
- Contar con la Estructura Taxonómica de los Activos en un Sistema de Gestión y Control.
- Planos, otros.
Métodos para el Cálculo de Criticidad
Para el cálculo de criticidad son utilizados comúnmente las siguientes:
- Método de los Puntos.
- Método de Tony Cilliberti.
- NORSOK Z-008.
- Estándar Military.
¿Cómo se realiza un Análisis De Criticidad?
- Definiendo un alcance y propósito
- Estableciendo criterios de importancia tales como:
- Nivel de Producción.
- Impacto al Ambiente.
- Costos de Reparación.
- Imagen.
- Tiempos Fuera de Servicio.
- Impacto en Producción.

Fuente: Elaborada por el autor (2019)
¿Cuáles son los pasos sugeridos en un Análisis de Criticidad?

Fuente: Elaborada por el autor (2019)
¿Cuándo hacer un Análisis de Criticidad?
- Fijar prioridades en sistemas complejos.
- Administrar recursos escasos.
- Necesidad de crear valor.
- Cambios en instalaciones, sistemas y equipos.
- Buscar determinar el impacto en el negocio.
¿En dónde se aplica un Análisis de Criticidad?
En cualquier conjunto de: Procesos, plantas, sistemas, equipos y/o componentes, que requieran ser jerarquizados en función de su impacto al negocio.
Cursos recomendados






%252FImagen%252FRAMPREDYC-1730060420837.webp%3Falt%3Dmedia%26token%3D2634a7f0-988e-4022-b91f-382503e6e9db&w=3840&q=75)

¿Quiénes participan en los AC?
Entre los actores o especialistas que pueden conformar el Equipo Natural de Trabajo (ENT), se encuentran: custodios de instalaciones, planificador, programador, ejecutor, ente técnico, proyectos, finanzas, mantenedores, ingenieros de proceso, confiabilidad, entre otros.
¿Qué resultados se obtienen de un Análisis de Criticidad?
Una representación de la frecuencia de falla ó IPF x consecuencias (Matriz de 5X5), en donde se resalta con colores el nivel de criticidad para cada proceso, plantas, sistemas, equipos y/o componentes, a fin de poder atacarlos en base a la jerarquización resultante del estudio.
“La criticidad es un indicador del nivel de riesgo”.

Fuente: Elaborada por el autor (2019)
¿Cuáles son los beneficios de un Análisis de Criticidad?
- Proveer soluciones durante el ciclo de vida útil de los activos.
- Mejorar los niveles de confiabilidad.
- Reducir la tasa de falla de los activos.
- Incrementar la eficiencia en los procesos productivos.
¿Qué hacer después de obtener los resultados de la Criticidad?
Seguimiento y control de planes de acción: Después de emitir el plan de acción asociado a la matriz de criticidad, se debe crear y establecer el seguimiento y control por parte del ingeniero de confiabilidad operacional, a fin de garantizar la ejecución de las acciones y el cumplimiento de las recomendaciones consecuentes del estudio.
Los objetivos del seguimiento y control a considerar en la criticidad:
- Asegurar la continuidad en el tiempo de aplicación de planes de acción resultantes de la implementación de la metodología de análisis de criticidad.
- Monitorear los cambios o mejoras (Reingeniería, Rediseños, otros) que pueden derivarse de la aplicación de las acciones generadas como resultados del análisis AC, para determinar si se requiere un nuevo estudio.
- Mantener actualizado el Sistema de Gestión y Control de Recomendaciones, en base a las acciones ejecutadas y del avance de las tareas que se encuentran en progreso.
Valor Agregado
En palabras simples “hacer algo más para ver resultados exitosos” en la aplicación de los estudios de criticidad.

Fuente: Elaborada por el autor (2019)
Caso 1 Método de los puntos y frecuencia de falla (FF)
Se explicará el método de los puntos y la frecuencia de falla (FF), para determinar la criticidad en un conjunto de instalaciones petroleras que procesan fluido multifásico (crudo, gas y agua) en Venezuela, dichos sistemas de manera general se pueden mencionar como el conjunto de activos que realizan las funciones básicas para operar y mantener con los mayores estándares de eficiencia de empresas de primer nivel.
Dichos equipos son: (Pozos, múltiples de recolección, oleoductos, gasoductos, acueductos, separadores, depuradores, enfriadores, despojadores de líquidos, fosas API, torre de absorción, intercambiador de calor, rehervidor bombas, unidades de medición fiscal, filtros, deshidratadores, tanques de estabilización, almacenamiento, compresores, motores, turbinas, generadores eléctricos, mechurrios, que realizan el proceso macro de extraer, manejar, disponer, almacenar y transportar el fluido (petróleo, gas y agua) extraído de los yacimientos para su uso en el mercado interno como su venta en el exterior.
El campo petrolero estudiado inició su producción en el año 1930.
Plan de producción del año en estudio es de 187 mil barriles normales día de petróleo (MBND) con una gravedad 23 °API. Con 31 Yacimientos Activos, los métodos de Producción son: BES / BM /BCP /GL/FN y actualmente están 7 Campos activos.
El Rango de producción / Pozo está en el rango de: 50 – 2300 BPD, los compromisos de producción del año son: Producción del año: 187 MBD, Inyección de gas: 450 MMPCG e Inyección de Agua: 410 MBA.
Una vez conocido el entorno del sistema a estudiar, definido el objetivo, alcance y conformación del ENT, se procede a describir de manera clara y sencilla el contexto operacional del activo sujeto al estudio de la siguiente manera:

Fuente: Elaborada por el autor (2019)
Es importante resaltar que los estudios de criticidad (AC) tienen su particularidad en cuanto a la definición de variables, premisas y consideraciones según sea el Contexto Operacional del sistema a evaluar.
Para el caso planteado el ENT estableció las siguientes premisas del estudio
- Frecuencia de Falla (FF).
- Tiempo promedio fuera de servicio z Nivel de producción.
- Impacto en producción.
- Costo de reparación.
- Impacto en la seguridad personal.
- Impacto Ambiental.
Más adelante se detalla el alcance de cada una de las variables consideradas para este estudio.
-Frecuencia de Falla (FF): Es la cantidad de eventos (Fallos) suscitados en el activo con afectación al sistema productivo.
Nota: Los valores de FF y TPFS fueron tomados de los indicadores de desempeño correspondientes al año de estudio, y para aquellas instalaciones que no se les llevan el registro histórico, la data fue generada del ENT y revisión del libro de operadores y mantenedores.
-Tiempo promedio fuera de servicio (TPFS): Se consideró el tiempo para reparar una falla recurrente y se mide la efectividad en restituir el activo a condiciones de operabilidad una vez que la unidad queda fuera de servicio (F/S). -Nivel de producción: Está relacionada a la capacidad de producción diaria del activo sujeto al estudio, a condiciones de operación existentes.
-Impacto en producción: Es el porcentaje de producción que se ve afectada cuando ocurren fallas en el activo sujeto al estudio.
-Costo de reparación: Son los costos incurridos (labor, materiales y transporte) para reparar las fallas del activo sujeto al estudio y así restituir su función. Los costos se calculan a una paridad cambiaria fijada por el Banco Central de Venezuela (BCV). Este costo lo suministra el equipo de Ingeniería de Costos.
-Impacto en la seguridad personal: representa la posibilidad de que sucedan eventos no deseados que ocasionen lesiones, heridas o fatalidades del personal descritas en las leyes y normas nacionales e internacionales vigentes.
-Impacto Ambiental: representa la posibilidad de que sucedan eventos no deseados que ocasione la violación de cualquier regulación ambiental.

Fuente: Elaborada por el autor (2019)
Una vez definidos todos los elementos (FF y Consecuencias) procedemos al cálculo de la criticidad, utilizando la plantilla diseñada para el sistema en estudio, aplicando la siguiente fórmula:

Fuente: Petróleos de Venezuela Norma MM-01-01-02 (2011)
Ya realizados los pasos previos descritos en el flujo grama mostrado en la figura N°5, el estudio se presenta preliminarmente ante el ENT para revisar y validar los resultados de la criticidad.
A continuación, se muestran los resultados por proceso (Crudo, Gas y Agua) de la aplicación de criticidad utilizando la frecuencia de falla (FF), representados en una matriz 5 x 5.

Fuente: Elaborada por el autor (2019)

Fuente: Elaborada por el autor (2019)

Fuente: Elaborada por el autor (2019)
Ya finalizado este paso (Matriz 5×5), el ENT genera un listado de alertas y acciones con la finalidad de facilitar la toma de decisiones efectivas, direccionar el esfuerzo y los recursos en áreas a mejorar en el corto, mediano y largo plazo.
Análisis de resultados
A continuación se muestra el detalle más relevante que generó la condición de criticidad de las instalaciones estudiadas (Ver figura 15).

Fuente: Elaborada por el autor (2019)
Conclusiones
En base a la volumetría de instalaciones estudiadas (14), se tiene que 4 activos están en alta criticidad, 4 en media y 6 en baja criticidad.
- En alta criticidad dos (2) plantas de manejo de agua, una (1) crudo y una /1) de gas.
- Media criticidad tres (3) plantas de gas y una (1) de crudo.
- En baja criticidad tres (3) plantas de gas, dos (2) de crudo y una (1) de agua.
- Con la determinación de la criticidad, se están generando las alertas a los niveles de autoridad correspondientes para la toma de decisiones oportunas que puedan afectar los objetivos de producción, el presupuesto, la seguridad, salud, ambiente y a la comunidad, ya que permitirá mejorar los procesos.
Plan de Acción

Fuente: Elaborada por el autor (2019)
Referencias
- [1] Petróleos de Venezuela (2010) Norma MM-01-01-01 Definiciones de Mantenimiento y Confiabilidad).
- [2] Gestión de Activos y Ciclo de Vida Por: Equipo de Investigación y Desarrollo de Ellmann, Sueiro y Asociados https://cmc-latam.com/gestion-activos-ciclo.
- [3] Costo-beneficio Por Arturo R. 18 Abr 2012 https://www.crecenegocios.com/ el-analisis-costo-beneficio/
- [4] Petróleos de Venezuela (2011) Norma PDVSA MM-01-01-07 Taxonomía de Activos para Sistema de Control y Gestión de Mantenimiento).
- [5] Estándar internacional ISO 14224:2016.
- [6] Petróleos de Venezuela (2011) Norma PDVSA MM-02-01-01 Jerarquización de Activos por Análisis de Criticidad).
- [7] SAE JA-1011 año 2011.
- [8] Petróleos de Venezuela 2013 Análisis de Mejorabilidad Instalaciones de Manejo de Crudo, Gas y Agua Distrito Furrial- IM-IT-ICO-FU-001-13.
- [9] Petróleos de Venezuela 2012 Jerarquización Por Condición Referencial De Riesgo De Las Líneas De Transferencia Del Campo Furrial IM-IT-ICO-DF-007-12.
- [10] El Análisis de Criticidad, una Metodología para mejorar la Confiabilidad Operacional. https://reliabilityweb.com/sp/articles/entry/el-analisis-de-criticidad-una metodología-para-mejorar-la-confiabilidad-ope/
- [11] Análisis de criticidad de plataformas Activo Integral Cantarell PEMEX Exploración y Producción Desarrollo e Implementación de un Modelo de Variables de Estado de Equipos y Estructuras Jorge Enrique Martínez Frías a, Andrés Eduardo Rivas b, Richard J. Matthews c Departamento de Integridad Mecánica y Confiabilidad PIMS Of London LTD. (https://docplayer.es/14054076- Analisis-de-criticidad-de-plataformas.html)
- [12] Análisis de criticidad parte 1 y 2. http://a3consultraining.com/analisis-de-criticidad-de-activos-parte-1/.
- [13] PROTECCIÓN CONTRA LA CORROSIÓN EN TUBERÍAS por Ing. José Gregorio Rendón https://ICONSA WebsiteArticulos TecnicosArticulosSt17v2…. 2/13/2006.
- [14] Análisis de criticidad personalizados Revista de Ingeniería Mecánica, vol. 12, núm. 3, septiembre-diciembre, 2009, pp. 1-12 Instituto Superior Politécnico José Antonio Echeverría Cuba.
- [15] Análisis De Criticidad Integral De Activos (2007) R2M. S.A Reliability and Risk Managemen por: Edwin Gutiérrez, Miguel Aguero, Ivaneska Calixto.
Autor: Jean Farfán
Correo: ljmfl7788@gmail.com
Dinos qué te ha parecido el artículo
Artículos recomendados
Engrasando tu carrera en mantenimiento predictivo

Aplicación Práctica del Teorema de Bayes para la Estimación de la Disponibilidad en Activos Industriales

La Evolución Industrial “Camino a la Industria 5.0”

Entrevista a Fracttal

Publica tu artículo en la revista #1 de Mantenimiento Industrial
Publicar un artículo en la revista es gratis, no tiene costo.
Solo debes asegurarte que no sea un artículo comercial.
¿Qué esperas?
O envía tu artículo directo: articulos@predictiva21.com
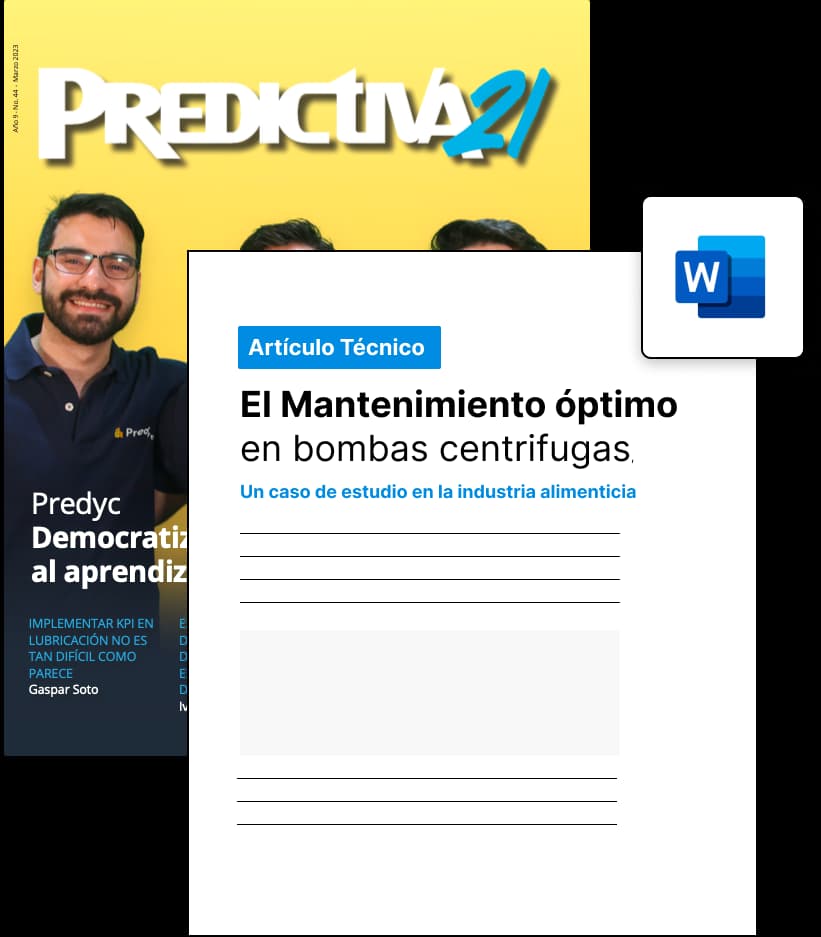
La otra visión de la Confiabilidad Operacional
Articulo 2 de octubre de 2019En virtud de hacer extensiva La Otra Visión de la Confiabilidad Operacional desde una perspectiva simplista y de fácil comprensión al lector, le presento una manera práctica y sencilla la metodología de Confiabilidad Operacional «Criticidad» aplicada en la industria Petrolera Nacional en Venezuela.
En base a las experiencias vividas en los Campos Petroleros de Venezuela y en la cotidianidad en las áreas operacionales, me permito compartir en estas cortas líneas para describir La otra visión de ver el Mundo de la Confiabilidad Operacional y su aplicación tradicional, cuya finalidad radica en mejorar la rentabilidad de los procesos productivos y entendiendo que cada día, se dedican enormes esfuerzos destinados a visualizar, identificar, analizar e implantar mejores prácticas operacionales para la solución de problemas y toma de decisiones efectivas y acertadas, que involucren un alto impacto en las áreas operativas de una empresa.
En líneas generales, el objetivo fundamental de las empresas, está en fortalecer sus metas del negocio y obtener niveles máximos de eficiencia, eficacia y confiabilidad operacional, que satisfagan y orienten los niveles de productividad de un negocio. Lo que traerán consigo una serie de desafíos los cuales deben ser afrontados en corto, mediano y largo plazo, según sea el caso.
De este modo, la actividad empresarial se acompaña esencialmente de la incertidumbre que predetermina la necesidad de elegir una de las diferentes alternativas para la ejecución de un diagnóstico certero. Considerando una gama de metodologías de Confiabilidad Operacional, en la cual logre determinar la condición actual de un sistema, muy distinta a la manera tradicional que se conoce de realizar un diagnóstico.
La finalidad de todo estudio es ir de lo simple a lo complejo, para ello se presenta una serie de definiciones básicas a conocer cuando se dispongan a realizar un Análisis De Criticidad.
¿Por qué es Importante la Aplicación de la Metodología de Criticidad para Realizar Diagnósticos?
Sencillo, nos permite establecer prioridades de instalaciones, sistemas y equipos, cuyo fin es facilitar la toma de decisiones efectivas, direccionando el esfuerzo y los recursos en áreas donde sea necesario mejorar basada en la realidad actual y garantizar los niveles de confiabilidad operacional de los activos.
Palabras Clave: Confiabilidad operacional, criticidad, frecuencia de falla, índice de probabilidad de falla, taxonomía, contexto operacional.
Abreviaturas. AC: Análisis de criticidad. ENT: Equipo natural de trabajo. IPF: Índice de probabilidad de falla. MBND: Miles de barriles día de petróleo. MMPCND: Millones de pies cúbicos normal día de gas. MBA: Miles de barriles de agua. %AyS: Porcentaje de Agua y Sólidos. SPC: Sistema de protección catódica. TPFS: Tiempo promedio fuera de servicio.
Un Análisis de Criticidad (AC): Es una metodología que establece la jerarquía de activos, considerando variables de frecuencia (FF) e índice de probabilidad de falla (IPF) y sus consecuencias, con la finalidad de direccionar esfuerzo y recursos en áreas a mejorar que impacten la confiabilidad operacional. (Jean Farfán)
Activo: Es un elemento tangible o intangible capitalizable de naturaleza permanente, que cumple una función en un proceso productivo y está sujeto a acciones de mantenimiento [1].
Análisis Funcional del Activo: Es la identificación de la relación o interconexión entre los diferentes procesos, sistemas y subsistemas de una instalación [1].
Criticidad: Es un método de fácil manejo y compresión, cuya virtud es proveer donde mejorar el activo y jerarquizarlos. Es representado a través de una Matriz 5×5, que denota el valor cuantitativo a mejorar, al combinar la frecuencia de ocurrencia o índice de probabilidad de fallas con las consecuencias que tienen. [1].
La fórmula utilizada es:

Fuente: Petróleos de Venezuela Norma MM-01-01-02 (2011)
Consecuencias: Resultado de un evento. Pueden existir una o más consecuencias de un evento, las cuales sean expresadas cualitativa o cuantitativamente [1].
Consecuencias = ((Nivel de producción. x tiempo promedio fuera de servicio (TPFS) x Impacto de producción.) / 24 horas + Costo de reparación + Impacto en Seguridad. + Impacto Ambiental).
Ciclo de vida de un Activo: Es todo lo que ocurre con el activo desde la idea con la cual se lo crea o incorpora a un proyecto, hasta su disposición final. Este ciclo de vida tiene asociado el “Costo de Ciclo de Vida”, el cual es la sumatoria de todos los costos asignables al activo (directos e indirectos, variables y fijos). [2] .
Etapas del Ciclo de Vida de un Activo

Fuente: https://cmc-latam. com/gestion-activos-ciclo-vida (2019)
Confiabilidad Operacional: Es la filosofía de trabajo orientada en una serie de procesos de mejora continua, que incorporan en forma sistemática, herramientas de diagnóstico, metodologías de análisis y nuevas tecnologías, para optimizar la gestión, planeación, ejecución y control de la productividad; además lleva implícita la capacidad de una instalación (procesos, tecnología, gente), para cumplir su función o el propósito que se espera de ella, dentro de sus límites de diseño y bajo un específico contexto operacional. [1].
Contexto Operacional: Es el conjunto de circunstancias que condicionan la operación de un equipo o sistema, están definidas como: localidad, ambiente, fluido de servicio, parámetros de operación, lineamientos ambientales, de seguridad y producción, calidad y disponibilidad de los insumos requeridos, configuración de trabajo, flexibilidad operacional, redundancia, alarmas, monitoreo de primera línea y otros. [1].
Costo – Beneficio: Es una herramienta financiera que mide la relación entre los costos y beneficios asociados a un proyecto de inversión con el fin de evaluar su rentabilidad, entendiéndose por proyecto de inversión no solo como la creación de un nuevo negocio, sino también, como inversiones que se pueden hacer en un negocio en marcha tales como el desarrollo de nuevo producto o la adquisición de nueva maquinaria. [3].
Custodio de Instalación: Es el ente encargado de velar por el funcionamiento de los activos dentro de los parámetros operacionales establecidos, con el fin de lograr el producto bajo las especificaciones requeridas. [1].
Datos del Equipo: Son los parámetros técnicos, operativos y ambientales que caracterizan el diseño y la utilización de una unidad de equipo. [1].
Equipo: Es un elemento de producción dentro de un arreglo lógico funcional que cumple con los siguientes criterios:
- Está sujeto a planes de mantenimiento.
- No es componente, parte o pieza (ejemplos: sello mecánico, manómetros, haz de tubo, tarjeta electrónica, entre otros).
- El valor de reemplazo es mayor que el costo de mantenimiento.
- Es trazable en el tiempo.
- Está sujeto a un control de gastos ocasionados por la aplicación de mantenimiento correctivo, preventivo, proyectos de mantenimiento y paradas de planta. [1].
Equipo Natural de Trabajo (ENT): Es un equipo multidisciplinario constituido por especialistas o actores de diferentes disciplinas que tienen como objetivo guiar la implementación de estrategias de mantenimiento y confiabilidad, la sincronización de actividades, el establecimiento de planes integrales de acción y la optimización de los costos de producción y mantenimiento en la organización. Entre los actores o especialistas que pueden conformar el ENT se encuentran: custodios de instalaciones, planificador, programador, ejecutor, ente técnico, entre otros. [1].
Estructura Taxonómica: Es una representación por niveles de los activos de una organización en un arreglo lógico y funcional en el SGCM, a través del cual se realizan todos los documentos técnicos y operativos que permiten controlar y asegurar el registro de todas las operaciones de mantenimiento. [4].

Fuente: Petróleos de Venezuela Norma MM-01-01-07 (2012)
Falla: Es la pérdida de capacidad para realizar su función según se requiera. [5].
Función: Es la capacidad de un elemento o activo de brindar un determinado servicio según las condiciones de trabajo, respetando su diseño. [1].
Índice de Probabilidad de Falla (IPF): Es un Índice que se calcula en función de las actividades de inspección y mantenimiento que se llevan a cabo en cada uno de los sistemas, considerando factores que están referidos a condiciones operacionales, corrosión, integridad mecánica, desempeño, control y protección, entre otras. [6].
Instalación: Es el tercer nivel de la estructura taxonómica que hace referencia al macroproceso productivo, localización o disposición geográfica. [1].
Modo de Falla: Es cualquier evento que genera una falla funcional- [7].
Mantenimiento: Es una combinación de todas las acciones técnicas y administrativas, que pretenden retener o restaurar un activo en un estado en el que pueda ejecutar una(s) función(es) requerida(s). [1].
Metodología de los Puntos: La estructura de criticidad que provee la llamada “metodología de los puntos” tiene su origen en el movimiento de mejora de la confiabilidad de los procesos productivos que se inició en la industria petrolera del Mar del Norte en la década del 90 [manual de criticidad de PDVSA – CIED] y hoy es ampliamente utilizada en la industria petrolera; por supuesto, con múltiples adecuaciones y modificaciones. La base fundamental de este enfoque es el establecimiento de un sistema de puntos para valorar la criticidad; y de una matriz cuyos rangos de frecuencia y consecuencia se expresan en “puntos”.
Se recomienda la participación de “equipos naturales de trabajo” en la valoración de la criticidad para minimizar el sesgo y la subjetividad. [16].

Fuente: R2M. S.A Reliability and Risk Management , Análisis De Criticidad Integral De Activos (2007)
Planta / Unidad: Es el cuarto nivel de la estructura taxonómica que hace referencia a un proceso productivo que integra la instalación. [1].
Sección / Sistema: Es el quinto nivel de la estructura taxonómica que hace referencia a las subdivisiones que componen una planta o unidad. [1].
Sub-Sección/Sub-Sistema o Lazo: Es el nivel 5.1 de la estructura taxonómica, definido en la Norma Técnica PDVSA MM–01–01–07, que se establece para ser utilizado según la complejidad de la organización y el contexto operacional que requiera un nivel de detalle adicional a los cinco niveles previos. Ejemplo: sub–sistema de ventilación, sub–sistema de bombeo, sub–sistema de alimentación, lazo de control, entre otros. [1].
Tiempo promedio entre fallas (TPEF): Es el tiempo promedio entre una falla y otra, éste incluye el tiempo fuera de servicio. [1].
Técnicas de análisis de riesgo: Existen diferentes técnicas para dimensionar el riesgo, tales como: Cualitativas, Semi- Cuantitativas y Cuantitativas.
Premisas básicas a considerar en un Estudio de Criticidad
- Utilizar el Contexto Operacional para identificar el proceso y su funcionamiento.
- Evaluar el entorno en donde se encuentra el activo.
- Contar con la Estructura Taxonómica de los Activos en un Sistema de Gestión y Control.
- Planos, otros.
Métodos para el Cálculo de Criticidad
Para el cálculo de criticidad son utilizados comúnmente las siguientes:
- Método de los Puntos.
- Método de Tony Cilliberti.
- NORSOK Z-008.
- Estándar Military.
¿Cómo se realiza un Análisis De Criticidad?
- Definiendo un alcance y propósito
- Estableciendo criterios de importancia tales como:
- Nivel de Producción.
- Impacto al Ambiente.
- Costos de Reparación.
- Imagen.
- Tiempos Fuera de Servicio.
- Impacto en Producción.

Fuente: Elaborada por el autor (2019)
¿Cuáles son los pasos sugeridos en un Análisis de Criticidad?

Fuente: Elaborada por el autor (2019)
¿Cuándo hacer un Análisis de Criticidad?
- Fijar prioridades en sistemas complejos.
- Administrar recursos escasos.
- Necesidad de crear valor.
- Cambios en instalaciones, sistemas y equipos.
- Buscar determinar el impacto en el negocio.
¿En dónde se aplica un Análisis de Criticidad?
En cualquier conjunto de: Procesos, plantas, sistemas, equipos y/o componentes, que requieran ser jerarquizados en función de su impacto al negocio.
Cursos recomendados






%252FImagen%252FRAMPREDYC-1730060420837.webp%3Falt%3Dmedia%26token%3D2634a7f0-988e-4022-b91f-382503e6e9db&w=3840&q=75)

¿Quiénes participan en los AC?
Entre los actores o especialistas que pueden conformar el Equipo Natural de Trabajo (ENT), se encuentran: custodios de instalaciones, planificador, programador, ejecutor, ente técnico, proyectos, finanzas, mantenedores, ingenieros de proceso, confiabilidad, entre otros.
¿Qué resultados se obtienen de un Análisis de Criticidad?
Una representación de la frecuencia de falla ó IPF x consecuencias (Matriz de 5X5), en donde se resalta con colores el nivel de criticidad para cada proceso, plantas, sistemas, equipos y/o componentes, a fin de poder atacarlos en base a la jerarquización resultante del estudio.
“La criticidad es un indicador del nivel de riesgo”.

Fuente: Elaborada por el autor (2019)
¿Cuáles son los beneficios de un Análisis de Criticidad?
- Proveer soluciones durante el ciclo de vida útil de los activos.
- Mejorar los niveles de confiabilidad.
- Reducir la tasa de falla de los activos.
- Incrementar la eficiencia en los procesos productivos.
¿Qué hacer después de obtener los resultados de la Criticidad?
Seguimiento y control de planes de acción: Después de emitir el plan de acción asociado a la matriz de criticidad, se debe crear y establecer el seguimiento y control por parte del ingeniero de confiabilidad operacional, a fin de garantizar la ejecución de las acciones y el cumplimiento de las recomendaciones consecuentes del estudio.
Los objetivos del seguimiento y control a considerar en la criticidad:
- Asegurar la continuidad en el tiempo de aplicación de planes de acción resultantes de la implementación de la metodología de análisis de criticidad.
- Monitorear los cambios o mejoras (Reingeniería, Rediseños, otros) que pueden derivarse de la aplicación de las acciones generadas como resultados del análisis AC, para determinar si se requiere un nuevo estudio.
- Mantener actualizado el Sistema de Gestión y Control de Recomendaciones, en base a las acciones ejecutadas y del avance de las tareas que se encuentran en progreso.
Valor Agregado
En palabras simples “hacer algo más para ver resultados exitosos” en la aplicación de los estudios de criticidad.

Fuente: Elaborada por el autor (2019)
Caso 1 Método de los puntos y frecuencia de falla (FF)
Se explicará el método de los puntos y la frecuencia de falla (FF), para determinar la criticidad en un conjunto de instalaciones petroleras que procesan fluido multifásico (crudo, gas y agua) en Venezuela, dichos sistemas de manera general se pueden mencionar como el conjunto de activos que realizan las funciones básicas para operar y mantener con los mayores estándares de eficiencia de empresas de primer nivel.
Dichos equipos son: (Pozos, múltiples de recolección, oleoductos, gasoductos, acueductos, separadores, depuradores, enfriadores, despojadores de líquidos, fosas API, torre de absorción, intercambiador de calor, rehervidor bombas, unidades de medición fiscal, filtros, deshidratadores, tanques de estabilización, almacenamiento, compresores, motores, turbinas, generadores eléctricos, mechurrios, que realizan el proceso macro de extraer, manejar, disponer, almacenar y transportar el fluido (petróleo, gas y agua) extraído de los yacimientos para su uso en el mercado interno como su venta en el exterior.
El campo petrolero estudiado inició su producción en el año 1930.
Plan de producción del año en estudio es de 187 mil barriles normales día de petróleo (MBND) con una gravedad 23 °API. Con 31 Yacimientos Activos, los métodos de Producción son: BES / BM /BCP /GL/FN y actualmente están 7 Campos activos.
El Rango de producción / Pozo está en el rango de: 50 – 2300 BPD, los compromisos de producción del año son: Producción del año: 187 MBD, Inyección de gas: 450 MMPCG e Inyección de Agua: 410 MBA.
Una vez conocido el entorno del sistema a estudiar, definido el objetivo, alcance y conformación del ENT, se procede a describir de manera clara y sencilla el contexto operacional del activo sujeto al estudio de la siguiente manera:

Fuente: Elaborada por el autor (2019)
Es importante resaltar que los estudios de criticidad (AC) tienen su particularidad en cuanto a la definición de variables, premisas y consideraciones según sea el Contexto Operacional del sistema a evaluar.
Para el caso planteado el ENT estableció las siguientes premisas del estudio
- Frecuencia de Falla (FF).
- Tiempo promedio fuera de servicio z Nivel de producción.
- Impacto en producción.
- Costo de reparación.
- Impacto en la seguridad personal.
- Impacto Ambiental.
Más adelante se detalla el alcance de cada una de las variables consideradas para este estudio.
-Frecuencia de Falla (FF): Es la cantidad de eventos (Fallos) suscitados en el activo con afectación al sistema productivo.
Nota: Los valores de FF y TPFS fueron tomados de los indicadores de desempeño correspondientes al año de estudio, y para aquellas instalaciones que no se les llevan el registro histórico, la data fue generada del ENT y revisión del libro de operadores y mantenedores.
-Tiempo promedio fuera de servicio (TPFS): Se consideró el tiempo para reparar una falla recurrente y se mide la efectividad en restituir el activo a condiciones de operabilidad una vez que la unidad queda fuera de servicio (F/S). -Nivel de producción: Está relacionada a la capacidad de producción diaria del activo sujeto al estudio, a condiciones de operación existentes.
-Impacto en producción: Es el porcentaje de producción que se ve afectada cuando ocurren fallas en el activo sujeto al estudio.
-Costo de reparación: Son los costos incurridos (labor, materiales y transporte) para reparar las fallas del activo sujeto al estudio y así restituir su función. Los costos se calculan a una paridad cambiaria fijada por el Banco Central de Venezuela (BCV). Este costo lo suministra el equipo de Ingeniería de Costos.
-Impacto en la seguridad personal: representa la posibilidad de que sucedan eventos no deseados que ocasionen lesiones, heridas o fatalidades del personal descritas en las leyes y normas nacionales e internacionales vigentes.
-Impacto Ambiental: representa la posibilidad de que sucedan eventos no deseados que ocasione la violación de cualquier regulación ambiental.

Fuente: Elaborada por el autor (2019)
Una vez definidos todos los elementos (FF y Consecuencias) procedemos al cálculo de la criticidad, utilizando la plantilla diseñada para el sistema en estudio, aplicando la siguiente fórmula:

Fuente: Petróleos de Venezuela Norma MM-01-01-02 (2011)
Ya realizados los pasos previos descritos en el flujo grama mostrado en la figura N°5, el estudio se presenta preliminarmente ante el ENT para revisar y validar los resultados de la criticidad.
A continuación, se muestran los resultados por proceso (Crudo, Gas y Agua) de la aplicación de criticidad utilizando la frecuencia de falla (FF), representados en una matriz 5 x 5.

Fuente: Elaborada por el autor (2019)

Fuente: Elaborada por el autor (2019)

Fuente: Elaborada por el autor (2019)
Ya finalizado este paso (Matriz 5×5), el ENT genera un listado de alertas y acciones con la finalidad de facilitar la toma de decisiones efectivas, direccionar el esfuerzo y los recursos en áreas a mejorar en el corto, mediano y largo plazo.
Análisis de resultados
A continuación se muestra el detalle más relevante que generó la condición de criticidad de las instalaciones estudiadas (Ver figura 15).

Fuente: Elaborada por el autor (2019)
Conclusiones
En base a la volumetría de instalaciones estudiadas (14), se tiene que 4 activos están en alta criticidad, 4 en media y 6 en baja criticidad.
- En alta criticidad dos (2) plantas de manejo de agua, una (1) crudo y una /1) de gas.
- Media criticidad tres (3) plantas de gas y una (1) de crudo.
- En baja criticidad tres (3) plantas de gas, dos (2) de crudo y una (1) de agua.
- Con la determinación de la criticidad, se están generando las alertas a los niveles de autoridad correspondientes para la toma de decisiones oportunas que puedan afectar los objetivos de producción, el presupuesto, la seguridad, salud, ambiente y a la comunidad, ya que permitirá mejorar los procesos.
Plan de Acción

Fuente: Elaborada por el autor (2019)
Referencias
- [1] Petróleos de Venezuela (2010) Norma MM-01-01-01 Definiciones de Mantenimiento y Confiabilidad).
- [2] Gestión de Activos y Ciclo de Vida Por: Equipo de Investigación y Desarrollo de Ellmann, Sueiro y Asociados https://cmc-latam.com/gestion-activos-ciclo.
- [3] Costo-beneficio Por Arturo R. 18 Abr 2012 https://www.crecenegocios.com/ el-analisis-costo-beneficio/
- [4] Petróleos de Venezuela (2011) Norma PDVSA MM-01-01-07 Taxonomía de Activos para Sistema de Control y Gestión de Mantenimiento).
- [5] Estándar internacional ISO 14224:2016.
- [6] Petróleos de Venezuela (2011) Norma PDVSA MM-02-01-01 Jerarquización de Activos por Análisis de Criticidad).
- [7] SAE JA-1011 año 2011.
- [8] Petróleos de Venezuela 2013 Análisis de Mejorabilidad Instalaciones de Manejo de Crudo, Gas y Agua Distrito Furrial- IM-IT-ICO-FU-001-13.
- [9] Petróleos de Venezuela 2012 Jerarquización Por Condición Referencial De Riesgo De Las Líneas De Transferencia Del Campo Furrial IM-IT-ICO-DF-007-12.
- [10] El Análisis de Criticidad, una Metodología para mejorar la Confiabilidad Operacional. https://reliabilityweb.com/sp/articles/entry/el-analisis-de-criticidad-una metodología-para-mejorar-la-confiabilidad-ope/
- [11] Análisis de criticidad de plataformas Activo Integral Cantarell PEMEX Exploración y Producción Desarrollo e Implementación de un Modelo de Variables de Estado de Equipos y Estructuras Jorge Enrique Martínez Frías a, Andrés Eduardo Rivas b, Richard J. Matthews c Departamento de Integridad Mecánica y Confiabilidad PIMS Of London LTD. (https://docplayer.es/14054076- Analisis-de-criticidad-de-plataformas.html)
- [12] Análisis de criticidad parte 1 y 2. http://a3consultraining.com/analisis-de-criticidad-de-activos-parte-1/.
- [13] PROTECCIÓN CONTRA LA CORROSIÓN EN TUBERÍAS por Ing. José Gregorio Rendón https://ICONSA WebsiteArticulos TecnicosArticulosSt17v2…. 2/13/2006.
- [14] Análisis de criticidad personalizados Revista de Ingeniería Mecánica, vol. 12, núm. 3, septiembre-diciembre, 2009, pp. 1-12 Instituto Superior Politécnico José Antonio Echeverría Cuba.
- [15] Análisis De Criticidad Integral De Activos (2007) R2M. S.A Reliability and Risk Managemen por: Edwin Gutiérrez, Miguel Aguero, Ivaneska Calixto.
Autor: Jean Farfán
Correo: ljmfl7788@gmail.com
Dinos qué te ha parecido el artículo
Artículos recomendados
Sensores en el análisis de aceite

Detección de Fugas Internas en Válvulas Mediante la Técnica de Ultrasonido

7.7 Niveles del ACR

Aumento de la carga dinámica en rodamientos por causa del desbalance

Publica tu artículo en la revista #1 de Mantenimiento Industrial
Publicar un artículo en la revista es gratis, no tiene costo.
Solo debes asegurarte que no sea un artículo comercial.
¿Qué esperas?
O envía tu artículo directo: articulos@predictiva21.com
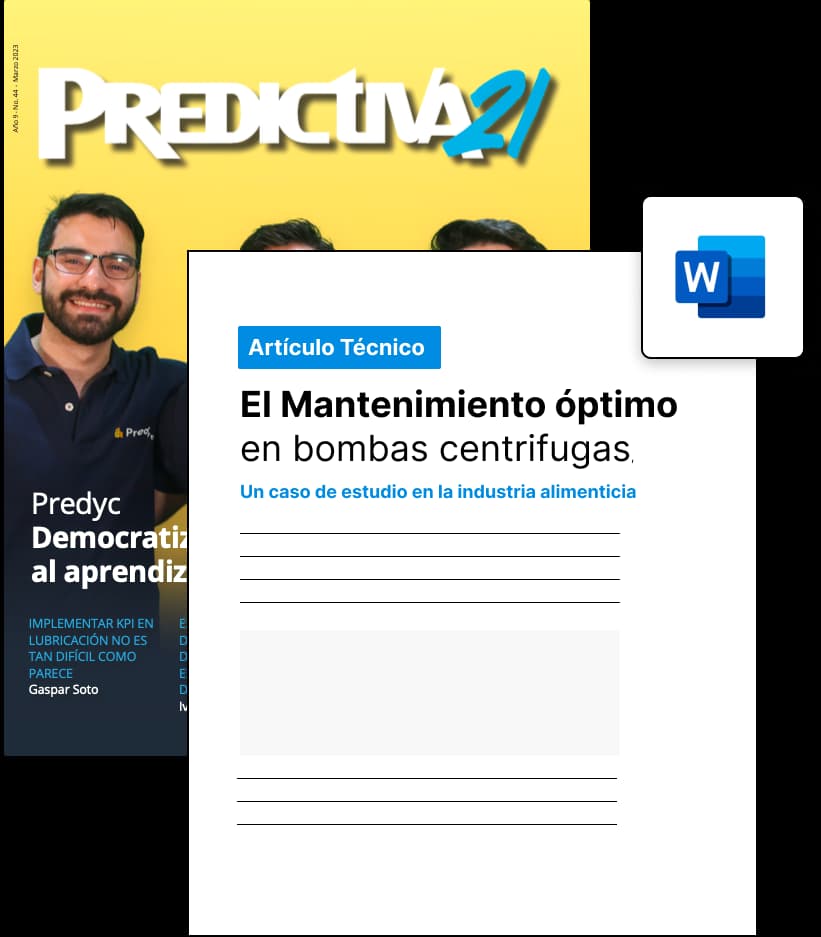