18.- Motores Eléctricos
Articulo7 de septiembre de 2021
En la sección correspondiente a los equipos impulsores se tratan solamente y de manera referencial los motores eléctricos de corriente alterna, ya que estos equipos accionan la mayor parte de las bombas centrífugas existentes en la industria y de hecho el desarrollo de las bombas centrífugas en el siglo pasado, se debe fundamentalmente a la evolución de los motores eléctricos.
El equipo impulsor, es por lo general, el renglón más costoso del conjunto motor-bomba. En muchas oportunidades cuando el fabricante o licitante oferta un conjunto de este tipo trata de disminuir el costo de la oferta, acoplando a la bomba motores que cumplen de forma marginal con las especificaciones del cliente.
Cuando se especifica el equipo o cuando se realizan las aclaratorias técnicas los renglones que usualmente son ampliamente debatidos o problemáticos son el encerramiento del motor, el aislamiento, el material del rotor y los cojinetes.
Lo fundamental de un motor eléctrico de corriente alterna o de un equipo impulsor es que posea la suficiente potencia cubrir los requerimientos de energía para que la bomba trabaje en la faja de procesos especificada y que el torque que desarrolle pueda mover la inercia del fluido durante la etapa de arranque y lo mantenga en movimiento durante el servicio.
Existen a nivel mundial numerosos estándares que regulan la construcción de los motores eléctricos de corriente alterna los principales son el NEMA (National Electric Manufacturers Association) que cubre los motores fabricados principalmente en Estados Unidos de América, en el Canadá y en algunos países asociados. La norma más utilizada es la NEMA MG 1 y las dimensiones de estos motores son en unidades inglesas.
Los motores eléctricos de corriente alterna fabricados en Europa y Asia siguen las regulaciones de las normas IEC/EN International Electrotechnical Commission, que aplican las dimensiones en unidades SI. Destaca en estas normas la IEC 60034 que tienen las prácticas que deben ser seguidas por los fabricantes que participan en la IEC.
Los motores eléctricos básicos están compuestos fundamentalmente por el estator, el rotor, la caja de conexiones, los cojinetes y el ventilador. La figura N 18-1 muestra el diagrama en corte de un motor eléctrico de corriente alterna. Indicando los principales componentes.

Fuente: www.grundfos.com// Grundfos Motor Book
El estator es la parte estacionaria del motor eléctrico, está compuesta por una serie de bobinas las cuales son alimentadas con la corriente alterna. Estas bobinas modifican su polaridad cuando se les aplica la corriente alterna haciendo variar el campo magnético. Generalmente el material de las bobinas es cobre y la estructura que los soporta puede ser de aluminio, hierro u otros materiales similares. El aluminio se utiliza para las estructuras de motores de baja potencia menores a 35 kW (50 HP) debido a que las estructuras de aluminio son propensas a deformarse con la temperatura, mayormente cuando las reparaciones del motor son realizadas de forma inadecuada.
Los rotores son la parte móvil de los motores eléctricos y los diseños más usados de estator son los de jaula de ardilla, que es un tipo de construcción que recuerda un tipo antiguo de jaula usada para mantener las ardillas en cautiverio. El rotor está compuesto por un grupo de láminas radiales perforadas hechas en acero donde es insertado un eje de acero y además contiene barras de inducción paralelas al eje, hechas en aluminio o cobre.
El motor trabaja y genera un torque que mueve la carga cuando el campo magnético, que se produce al introducir la corriente alterna en el estator, produce una corriente en el rotor al cruzarse el campo magnético variable con las barras inductoras. Esta corriente circula por las barras inductoras y crea un campo magnético alrededor de cada barra y como el campo magnético en el rotor esta cambiando constantemente esto genera el movimiento del rotor y por tanto de la carga asociada a este motor eléctrico.
Los cojinetes son los elementos que soportan el eje del motor y lo mantienen concéntrico al estator. En la sección 13.- COJINETES se trató ampliamente sobre el tema. La caja de conexiones es donde son conectados los cables de alimentación eléctrica del motor.
El ventilador está instalado en el lado no conducido del motor y está hecho para inducir una corriente de aire en la superficie externa del estator con la finalidad de remover el calor y mantener este componente dentro de la temperatura de diseño. En motores de mayores potencias, por arriba de 750 kW (1000 HP) el sistema de enfriamiento es más sofisticado que de acuerdo con el diseño incluye intercambiadores de calor con aire o con agua.
Como se indicó el motor eléctrico de corriente alterna más comúnmente usado en la industria es el de rotor de jaula de ardilla los cuales son diseñados para velocidades específicas. Estas velocidades dependen de la frecuencia eléctrica y del número de polos del motor. Las frecuencias eléctricas más comunes son 50 Hz y 60 Hz y los polos van de dos hasta doce polos. La figura 18-2 muestra una tabla con las diferentes velocidades de los motores de acuerdo a la frecuencia y al número de polos del motor.

Fuente: www.grundfos.com// Grundfos Motor Book
Esta velocidad a la cual esta sincronizado el motor tiene un deslizamiento, que en la práctica es una reducción de la velocidad real del motor cuando se encuentra a plena carga y puede llegar hasta el 3% de la velocidad total.
Un aspecto importante y con gran impacto en el desempeño de los motores es el tipo de aislamiento utilizado para las bobinas. Tanto la norma NEMA como la IEC 62114 tratan sobre la clasificación térmica de los motores básicamente tienen tres clasificaciones: La clase E que aplican para una temperatura ambiente de operación máxima de 49 °C (120 °F). La clase B para una temperatura máxima en la bobina de 130 °C (266 °F), clase F para una temperatura máxima en la bobina de 155 °C (311 °F) y la clase H con una temperatura máxima a nivel de bobina de 180 °C (356 °F).
En muchas de las norma y prácticas recomendadas de la Industria Petrolera se recomienda aislamiento tipo F que es para alta temperatura y que por sus características ofrece un rendimiento superior a otros tipos de aislamiento menos costosos, los fabricantes insisten siempre en aplicar los aislamientos tipo B, menos costosos pero que resisten menos temperatura que un aislamiento del tipo F.
El grado de protección es una de las variables importantes de definir en los motores eléctricos de corriente alterna aplicados en la Industria Petrolera. En la industria de motores en europa se sigue la norma IEC 60034-5“Degrees of protection provided by the integraldesign of rotating electrical machines (IP code)-Classification”, allí se establecen los grados de protección para los equipos eléctricos en lo relativo a la entrada de contaminantes sólidos y agua.
Este código está compuesto por dos letras que son IP seguido de dos números el primer número indica el nivel de protección contra el ingreso de objetos sólidos y la segunda letra indica el nivel de protección contra el ingreso de agua.
La primera letra referente al ingreso de sólidos va de 0 (cero) que indica sin protección hasta 6, que indica que el motor es completamente aprueba de contaminantes sólidos. La segunda letra va desde 0 (cero) sin protección hasta 8, donde el motor debe estar protegido para una sumersión total en agua, a las condiciones especificadas por el comprador.
Por ejemplo, si tenemos un motor eléctrico de corriente alterna con protección IP 55 (muy común en aplicaciones en plantas de procesos y unidades de producción para operaciones terrestres de la Industria Petrolera) indica que su protección contra sólidos es 5, lo protege contra sucio y contaminantes y la segunda letra la 5 indica que el motor eléctrico está protegido contra agua proyectada con una manguera en cualquier dirección. Otro nivel de protección muy usado para motores en operaciones costa afuera es la IP 56, donde el segundo número el 6 indica que está protegido contra olas o chorros de agua a alta presión proveniente de cualquier dirección.
La NEMA tiene otras especificaciones para los niveles de protección y los principales son los siguientes:
- Abierto (Open) El aire de enfriamiento circula libremente por los pasajes de ventilación del motor sin ninguna restricción.
- Abierto a Prueba de Sucio (ODP; Open-Dust-Proof) el diseño es abierto al ambiente, pero con canales de ventilación que poseen ángulos y pantallas que limitan la entrada de gotas de humedad y de contaminantes.
- A Prueba de Ambiente Tipo I (WPI, Weather protected Type I) el motor está limitado para la entrada de lluvia, partículas, nieve y otros contaminantes.
- A Prueba de Ambiente Tipo II (WPII, Weather protected Type II) posee las mismas características que el WPI pero con la ventaja que las partículas y elementos que ingresan al motor son descargadas sin que entren en contacto con los elementos eléctricos.
- Totalmente Cerrado (TE, Totally Enclosed) Está completamente cerrado pero diseñado para operar sin la circulación libre de aire de enfriamiento en la parte interna y externa del motor.
- Totalmente Cerrado Enfriado por Ventilador (TEFC, Totally Enclosed Fan Cooled) Estos motores son totalmente cerrados y dispone de un ventilador accionado por el eje del motor que circula aire para enfriamiento.
Muchas empresas petroleras solicitan enceramientos y protección contra el ambiente del tipo TEFC"Total Enclosure Fan Cooler", para los motores eléctricos de corriente alterna, porque este tipo de encerramiento ha demostrado muchas ventajas y sobre todo robustez en los servicios típicos de la Industria Petrolera. La polémica se presenta debido a que los fabricantes recomiendan ampliamente la aplicación de los encerramientos WPI “Weather Proof I” ó WPII que son menos costosos que los TEFC.
El uso de los encerramientos WP se ha extendido en las áreas de producción, donde no se requiere un encerramiento que proteja al motor del ambiente circundante y no existan atmósferas inflamables.
En cuanto a las normas que rigen la fabricación de las principales bombas usada en la Industria Petrolera la ASME B73.1 y la API 610/ISO 13709 se tiene lo siguiente:
La norma ASME B73.1 no contiene ninguna referencia importante del tipo de equipo impulsor a utilizar o regulaciones necesarias para este tipo de equipos.
La norma API 610/ISO 13709 establece en la sección 7“Accessories”sub-sección 7.1“Drivers” una serie de recomendaciones para garantizar que los motores eléctricos tengan suficiente potencia para cubrirán todo los posibles escenarios operacionales de las bombas como son las variaciones del proceso como por ejemplo cambio en las presiones, temperatura o características de los líquidos bombeados, así como ajustarse a cualquier condición de arranque y puesta en marcha de la planta.
Indica que los motores eléctricos deben ser dimensionados de forma que la potencia nominal debe cubrir la condición de operación máxima incluyendo las posibles pérdidas de mecánicas en cojinetes, sellos, cajas de engranajes externas y acoplamientos.
Los motores eléctricos deben tener potencia incluyendo el factor de servicio tal como es indicada en la tabla N° 12 de esa norma, de al menos un 125% de la potencia requerida por la bomba en el punto de garantía, cuando la potencia del motor no excede de 22 kW (30 HP). Cuando la potencia del motor esta entre 22 y 55 kW (30 y 75 HP) la potencia debe ser 115% de la potencia requerida en el punto de garantía. Cuando la potencia excede los 55 kW (75 HP) la potencia debe ser 110% la potencia requerida por la bomba en el punto de garantía.
En cuanto a la vida de los cojinetes es recomendable que los motores eléctricos tengan una vida esperada similar a los calculados para la bomba centrífuga. Como referencia el API 610/ISO 13709 recomienda que la vida esperada del cojinete L10h de al menos 25.000 horas para el manejo de cargas relacionadas con la operación a la condición de diseño o 16.000 horas cuando se opera a la máxima carga tal como lo exige el API para la selección de cojinetes a instalar en las bombas centrífugas.
Dinos qué te ha parecido el artículo
Artículos recomendados
ICA Fluor O&M invierté en +5,000 horas de capacitación para su equipo de Mantenimiento, que incluye profesionales técnicos, supervisores y gerentes con PREDYC

Descubre El ERM: sus elementos y objetivos

1.1 Introducción

Curso de mantención industrial: ¿Qué es? ¡Descúbrelo!

Publica tu artículo en la revista #1 de Mantenimiento Industrial
Publicar un artículo en la revista es gratis, no tiene costo.
Solo debes asegurarte que no sea un artículo comercial.
¿Qué esperas?
O envía tu artículo directo: articulos@predictiva21.com
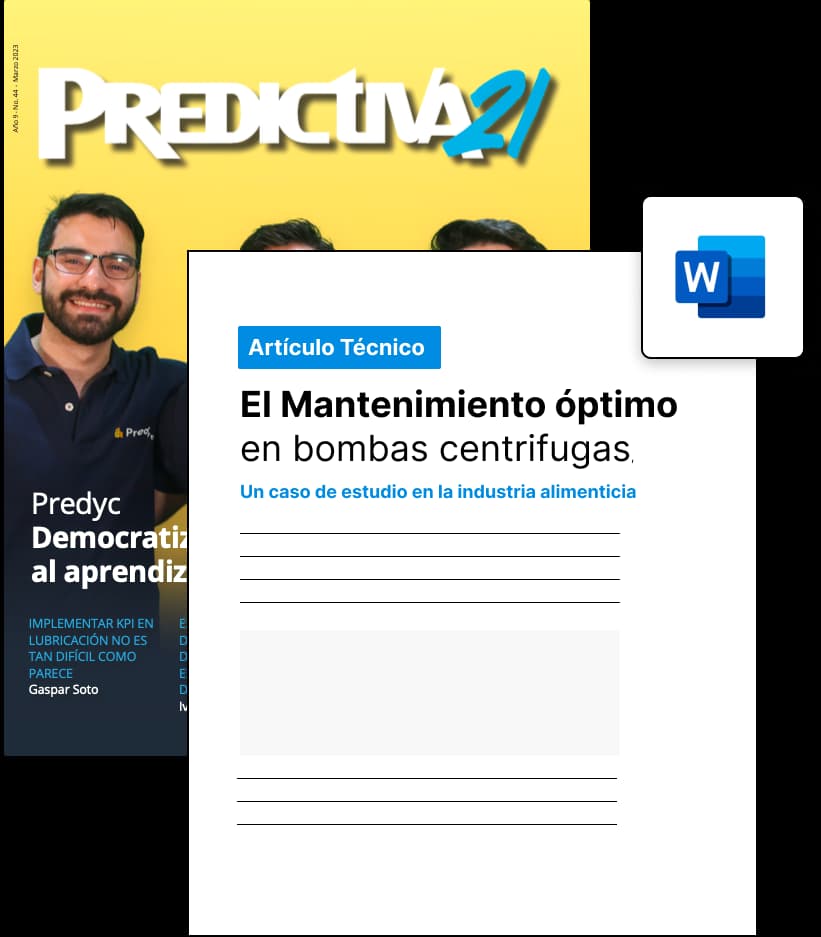
18.- Motores Eléctricos
Articulo 7 de septiembre de 2021En la sección correspondiente a los equipos impulsores se tratan solamente y de manera referencial los motores eléctricos de corriente alterna, ya que estos equipos accionan la mayor parte de las bombas centrífugas existentes en la industria y de hecho el desarrollo de las bombas centrífugas en el siglo pasado, se debe fundamentalmente a la evolución de los motores eléctricos.
El equipo impulsor, es por lo general, el renglón más costoso del conjunto motor-bomba. En muchas oportunidades cuando el fabricante o licitante oferta un conjunto de este tipo trata de disminuir el costo de la oferta, acoplando a la bomba motores que cumplen de forma marginal con las especificaciones del cliente.
Cuando se especifica el equipo o cuando se realizan las aclaratorias técnicas los renglones que usualmente son ampliamente debatidos o problemáticos son el encerramiento del motor, el aislamiento, el material del rotor y los cojinetes.
Lo fundamental de un motor eléctrico de corriente alterna o de un equipo impulsor es que posea la suficiente potencia cubrir los requerimientos de energía para que la bomba trabaje en la faja de procesos especificada y que el torque que desarrolle pueda mover la inercia del fluido durante la etapa de arranque y lo mantenga en movimiento durante el servicio.
Existen a nivel mundial numerosos estándares que regulan la construcción de los motores eléctricos de corriente alterna los principales son el NEMA (National Electric Manufacturers Association) que cubre los motores fabricados principalmente en Estados Unidos de América, en el Canadá y en algunos países asociados. La norma más utilizada es la NEMA MG 1 y las dimensiones de estos motores son en unidades inglesas.
Los motores eléctricos de corriente alterna fabricados en Europa y Asia siguen las regulaciones de las normas IEC/EN International Electrotechnical Commission, que aplican las dimensiones en unidades SI. Destaca en estas normas la IEC 60034 que tienen las prácticas que deben ser seguidas por los fabricantes que participan en la IEC.
Los motores eléctricos básicos están compuestos fundamentalmente por el estator, el rotor, la caja de conexiones, los cojinetes y el ventilador. La figura N 18-1 muestra el diagrama en corte de un motor eléctrico de corriente alterna. Indicando los principales componentes.

Fuente: www.grundfos.com// Grundfos Motor Book
El estator es la parte estacionaria del motor eléctrico, está compuesta por una serie de bobinas las cuales son alimentadas con la corriente alterna. Estas bobinas modifican su polaridad cuando se les aplica la corriente alterna haciendo variar el campo magnético. Generalmente el material de las bobinas es cobre y la estructura que los soporta puede ser de aluminio, hierro u otros materiales similares. El aluminio se utiliza para las estructuras de motores de baja potencia menores a 35 kW (50 HP) debido a que las estructuras de aluminio son propensas a deformarse con la temperatura, mayormente cuando las reparaciones del motor son realizadas de forma inadecuada.
Los rotores son la parte móvil de los motores eléctricos y los diseños más usados de estator son los de jaula de ardilla, que es un tipo de construcción que recuerda un tipo antiguo de jaula usada para mantener las ardillas en cautiverio. El rotor está compuesto por un grupo de láminas radiales perforadas hechas en acero donde es insertado un eje de acero y además contiene barras de inducción paralelas al eje, hechas en aluminio o cobre.
El motor trabaja y genera un torque que mueve la carga cuando el campo magnético, que se produce al introducir la corriente alterna en el estator, produce una corriente en el rotor al cruzarse el campo magnético variable con las barras inductoras. Esta corriente circula por las barras inductoras y crea un campo magnético alrededor de cada barra y como el campo magnético en el rotor esta cambiando constantemente esto genera el movimiento del rotor y por tanto de la carga asociada a este motor eléctrico.
Los cojinetes son los elementos que soportan el eje del motor y lo mantienen concéntrico al estator. En la sección 13.- COJINETES se trató ampliamente sobre el tema. La caja de conexiones es donde son conectados los cables de alimentación eléctrica del motor.
El ventilador está instalado en el lado no conducido del motor y está hecho para inducir una corriente de aire en la superficie externa del estator con la finalidad de remover el calor y mantener este componente dentro de la temperatura de diseño. En motores de mayores potencias, por arriba de 750 kW (1000 HP) el sistema de enfriamiento es más sofisticado que de acuerdo con el diseño incluye intercambiadores de calor con aire o con agua.
Como se indicó el motor eléctrico de corriente alterna más comúnmente usado en la industria es el de rotor de jaula de ardilla los cuales son diseñados para velocidades específicas. Estas velocidades dependen de la frecuencia eléctrica y del número de polos del motor. Las frecuencias eléctricas más comunes son 50 Hz y 60 Hz y los polos van de dos hasta doce polos. La figura 18-2 muestra una tabla con las diferentes velocidades de los motores de acuerdo a la frecuencia y al número de polos del motor.

Fuente: www.grundfos.com// Grundfos Motor Book
Esta velocidad a la cual esta sincronizado el motor tiene un deslizamiento, que en la práctica es una reducción de la velocidad real del motor cuando se encuentra a plena carga y puede llegar hasta el 3% de la velocidad total.
Un aspecto importante y con gran impacto en el desempeño de los motores es el tipo de aislamiento utilizado para las bobinas. Tanto la norma NEMA como la IEC 62114 tratan sobre la clasificación térmica de los motores básicamente tienen tres clasificaciones: La clase E que aplican para una temperatura ambiente de operación máxima de 49 °C (120 °F). La clase B para una temperatura máxima en la bobina de 130 °C (266 °F), clase F para una temperatura máxima en la bobina de 155 °C (311 °F) y la clase H con una temperatura máxima a nivel de bobina de 180 °C (356 °F).
En muchas de las norma y prácticas recomendadas de la Industria Petrolera se recomienda aislamiento tipo F que es para alta temperatura y que por sus características ofrece un rendimiento superior a otros tipos de aislamiento menos costosos, los fabricantes insisten siempre en aplicar los aislamientos tipo B, menos costosos pero que resisten menos temperatura que un aislamiento del tipo F.
El grado de protección es una de las variables importantes de definir en los motores eléctricos de corriente alterna aplicados en la Industria Petrolera. En la industria de motores en europa se sigue la norma IEC 60034-5“Degrees of protection provided by the integraldesign of rotating electrical machines (IP code)-Classification”, allí se establecen los grados de protección para los equipos eléctricos en lo relativo a la entrada de contaminantes sólidos y agua.
Este código está compuesto por dos letras que son IP seguido de dos números el primer número indica el nivel de protección contra el ingreso de objetos sólidos y la segunda letra indica el nivel de protección contra el ingreso de agua.
La primera letra referente al ingreso de sólidos va de 0 (cero) que indica sin protección hasta 6, que indica que el motor es completamente aprueba de contaminantes sólidos. La segunda letra va desde 0 (cero) sin protección hasta 8, donde el motor debe estar protegido para una sumersión total en agua, a las condiciones especificadas por el comprador.
Por ejemplo, si tenemos un motor eléctrico de corriente alterna con protección IP 55 (muy común en aplicaciones en plantas de procesos y unidades de producción para operaciones terrestres de la Industria Petrolera) indica que su protección contra sólidos es 5, lo protege contra sucio y contaminantes y la segunda letra la 5 indica que el motor eléctrico está protegido contra agua proyectada con una manguera en cualquier dirección. Otro nivel de protección muy usado para motores en operaciones costa afuera es la IP 56, donde el segundo número el 6 indica que está protegido contra olas o chorros de agua a alta presión proveniente de cualquier dirección.
La NEMA tiene otras especificaciones para los niveles de protección y los principales son los siguientes:
- Abierto (Open) El aire de enfriamiento circula libremente por los pasajes de ventilación del motor sin ninguna restricción.
- Abierto a Prueba de Sucio (ODP; Open-Dust-Proof) el diseño es abierto al ambiente, pero con canales de ventilación que poseen ángulos y pantallas que limitan la entrada de gotas de humedad y de contaminantes.
- A Prueba de Ambiente Tipo I (WPI, Weather protected Type I) el motor está limitado para la entrada de lluvia, partículas, nieve y otros contaminantes.
- A Prueba de Ambiente Tipo II (WPII, Weather protected Type II) posee las mismas características que el WPI pero con la ventaja que las partículas y elementos que ingresan al motor son descargadas sin que entren en contacto con los elementos eléctricos.
- Totalmente Cerrado (TE, Totally Enclosed) Está completamente cerrado pero diseñado para operar sin la circulación libre de aire de enfriamiento en la parte interna y externa del motor.
- Totalmente Cerrado Enfriado por Ventilador (TEFC, Totally Enclosed Fan Cooled) Estos motores son totalmente cerrados y dispone de un ventilador accionado por el eje del motor que circula aire para enfriamiento.
Muchas empresas petroleras solicitan enceramientos y protección contra el ambiente del tipo TEFC"Total Enclosure Fan Cooler", para los motores eléctricos de corriente alterna, porque este tipo de encerramiento ha demostrado muchas ventajas y sobre todo robustez en los servicios típicos de la Industria Petrolera. La polémica se presenta debido a que los fabricantes recomiendan ampliamente la aplicación de los encerramientos WPI “Weather Proof I” ó WPII que son menos costosos que los TEFC.
El uso de los encerramientos WP se ha extendido en las áreas de producción, donde no se requiere un encerramiento que proteja al motor del ambiente circundante y no existan atmósferas inflamables.
En cuanto a las normas que rigen la fabricación de las principales bombas usada en la Industria Petrolera la ASME B73.1 y la API 610/ISO 13709 se tiene lo siguiente:
La norma ASME B73.1 no contiene ninguna referencia importante del tipo de equipo impulsor a utilizar o regulaciones necesarias para este tipo de equipos.
La norma API 610/ISO 13709 establece en la sección 7“Accessories”sub-sección 7.1“Drivers” una serie de recomendaciones para garantizar que los motores eléctricos tengan suficiente potencia para cubrirán todo los posibles escenarios operacionales de las bombas como son las variaciones del proceso como por ejemplo cambio en las presiones, temperatura o características de los líquidos bombeados, así como ajustarse a cualquier condición de arranque y puesta en marcha de la planta.
Indica que los motores eléctricos deben ser dimensionados de forma que la potencia nominal debe cubrir la condición de operación máxima incluyendo las posibles pérdidas de mecánicas en cojinetes, sellos, cajas de engranajes externas y acoplamientos.
Los motores eléctricos deben tener potencia incluyendo el factor de servicio tal como es indicada en la tabla N° 12 de esa norma, de al menos un 125% de la potencia requerida por la bomba en el punto de garantía, cuando la potencia del motor no excede de 22 kW (30 HP). Cuando la potencia del motor esta entre 22 y 55 kW (30 y 75 HP) la potencia debe ser 115% de la potencia requerida en el punto de garantía. Cuando la potencia excede los 55 kW (75 HP) la potencia debe ser 110% la potencia requerida por la bomba en el punto de garantía.
En cuanto a la vida de los cojinetes es recomendable que los motores eléctricos tengan una vida esperada similar a los calculados para la bomba centrífuga. Como referencia el API 610/ISO 13709 recomienda que la vida esperada del cojinete L10h de al menos 25.000 horas para el manejo de cargas relacionadas con la operación a la condición de diseño o 16.000 horas cuando se opera a la máxima carga tal como lo exige el API para la selección de cojinetes a instalar en las bombas centrífugas.
Dinos qué te ha parecido el artículo
Artículos recomendados
Evaluación Estructural por Elementos Finitos de la Silla de Volcado utilizada en plantas de Laminado en Caliente

Condition Monitoring: Cost have Benefits & Benefits can reduce Cost

Procesos empresariales en mantenimiento de planta

¿Qué es la gestión de riesgos empresariales?

Publica tu artículo en la revista #1 de Mantenimiento Industrial
Publicar un artículo en la revista es gratis, no tiene costo.
Solo debes asegurarte que no sea un artículo comercial.
¿Qué esperas?
O envía tu artículo directo: articulos@predictiva21.com
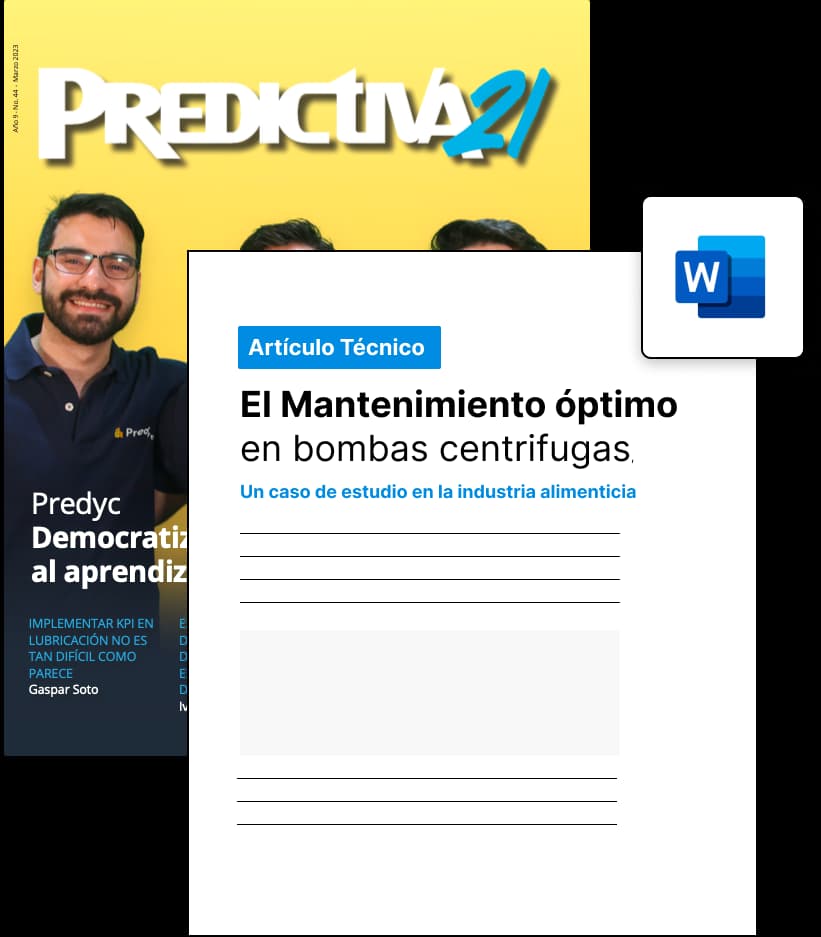