Eliminando los Silos entre Mantenimiento y Compras
Articulo27 de febrero de 2025
Abstract
Uno de los temas que normalmente sale a la luz en las interacciones con la gente de mantenimiento es el problema que tienen con el Área de Compras y Contrataciones para obtener lo que necesitan. Muchas veces, no es porque no lo compren, sino porque “compran tarde” o “compran mal”.
Luego de mi retiro de la Infantería de Marina Argentina, donde adquirí aptitudes en logística y mantenimiento, comencé a trabajar en el ámbito de la Gestión de Activos. Desde esa posición, pensé cómo podía, en base a mi experiencia, hacer un aporte para tratar de “alinear horizontalmente” las funciones operativas y financieras durante la etapa de operación de los activos, particularmente en la eterna “controversia” entre el responsable de Mantenimiento y el responsable de Compras, que tanto perjuicio causa a las organizaciones, muchas veces sin que ellos se den cuenta.
A medida que el análisis iba madurando, inicialmente parecía que podía tener una solución ligada a la conducción de la organización y a acciones técnicas, pero descubrí dos cosas: la primera es que iba a ser muy difícil resolverlo únicamente con la imposición de una directiva de la Alta Dirección; y la segunda, que más allá de que esta se emitiese, había cuestiones técnicas que una orden no podía solucionar. En definitiva, era necesario acabar con los silos.
Desarrollo
En primer lugar, deseo agradecer al Lic. Guillermo Míguez por su inestimable ayuda en el desarrollo del presente ensayo, aportando su visión y experiencia desde el Área de Compras, y a The Woodhouse Partnership Ltd, en la figura del Ingeniero José Durán, por haberme invitado a participar en el Seminario Digital de Mantenimiento y Gestión de Activos 2020, así como al Ingeniero Genaro Pérez Illanes, quien, en la sesión “Gestión del cambio cultural y la productividad de la empresa”, aportó claridad al análisis que estaba realizando y que ahora queda plasmado en este ensayo.
Uno de los temas que normalmente sale a la luz en las interacciones con la gente de mantenimiento es el problema que tienen con el Área de Compras y Contrataciones para obtener lo que necesitan. Muchas veces, no es porque no lo compren, sino porque “compran tarde” o “compran mal”.
Por mi parte, proviniendo del sector de Defensa, más precisamente de la Armada Argentina, me he sentido plenamente identificado con esta problemática. En los muchos años en los que serví en funciones de logística y mantenimiento, además de contar con escasos recursos, a veces extremadamente limitados, me resultaba difícil evitar que los organismos de contrataciones “compraran tarde” o “compraran mal”. Se me enseñó que, en el Estado, la regla de compra es “siempre lo más barato”, pero en el último cuarto de mi carrera, después de obtener un par de posgrados y diplomaturas relacionadas con la logística y el mantenimiento, y tras arduos “intercambios académicos” con abogados y contadores, descubrí que si bien esa afirmación era correcta, también era incompleta. En realidad, la regla completa era: “dentro de lo especificado, siempre lo más barato”. Solo entonces pude comenzar a obtener lo que la Unidad realmente necesitaba para cumplir su función.
Ya fuera del servicio y adentrándome en el ámbito de la Gestión de Activos, pensé cómo podía, desde mi experiencia, hacer un aporte para tratar de “alinear horizontalmente” las funciones operativas y financieras durante la etapa de operación de los activos, particularmente con la eterna “controversia” entre el responsable de Mantenimiento y el responsable de Compras, que tanto perjuicio causa a las organizaciones, muchas veces sin que ellos se den cuenta.
A medida que el análisis iba madurando, inicialmente parecía que podía tener una solución ligada a la conducción de la organización y a acciones técnicas, pero descubrí dos cosas: la primera es que iba a ser muy difícil resolverlo únicamente con la imposición de una directiva de la Alta Dirección; y la segunda, que más allá de que esta se emitiese, había cuestiones técnicas que una orden no podía solucionar.
El Contexto
Para entender el contexto, es necesario comprender las motivaciones y realidades de cada una de las partes involucradas.
El primer problema son los objetivos. Ambas áreas, Mantenimiento y Compras, son habilitadores del área operativa, que es la encargada de cumplir la función que da vida a la organización. Para lograrlo, Mantenimiento debe asegurar que los activos utilizados en operaciones estén disponibles cuando se necesiten, y Compras debe garantizar que los insumos requeridos por operaciones estén disponibles en el momento adecuado. Es decir, el objetivo de Mantenimiento es permitir que operaciones sea eficaz en su cometido, mientras que el de Compras es proveer insumos buscando que la empresa gaste menos dinero, es decir, que sea eficiente. Aquí surge el primer problema: ambas áreas tienen objetivos que, en la relación horizontal y puramente pragmática, parecen opuestos entre sí.
El segundo problema es cómo se miden los objetivos de ambas áreas por parte de la Alta Dirección. Mantenimiento es evaluado por la disponibilidad de los equipos, indicador que representa la primera variable que afecta el OEE (Overall Equipment Effectiveness). Para mejorar la disponibilidad, se pueden llevar a cabo muchas acciones, cuyos resultados en algunos casos no se evidencian de inmediato, sino después de varios años. Como todas estas acciones tienen un costo asociado, los beneficios económicos —es decir, la eficiencia— solo se podrán apreciar tras determinado tiempo.
Paralelamente, Compras es evaluado por la eficiencia en la ejecución del gasto, siendo el indicador más común la relación entre “ventas totales sobre gastos totales” en un año. Si para evaluar la eficiencia de las acciones de Mantenimiento se necesita más de un año, evaluar el gasto asociado mediante comparaciones interanuales no solo tiene poca utilidad, sino que además no refleja la realidad, generando otra controversia.
Por último, ambas áreas hablan idiomas diferentes. Inexorablemente, el área de Mantenimiento intentará explicar sus necesidades a Compras utilizando su propio lenguaje técnico. Probablemente detallará cómo se puede alargar el MTTF (Mean Time to Failure) del equipo “XXX”, mejorando su confiabilidad y disponibilidad. Compras, por su parte, escuchará la explicación, pero no se sentirá particularmente movilizado, porque en toda la argumentación el término “costos” o cualquier referencia a la moneda solo aparecerá asociada a un incremento del gasto.
Resumiendo: Mantenimiento habla un idioma técnico, necesita invertir en insumos y repuestos para sostener el sistema funcionando y es medido por la disponibilidad que logra de los activos. Compras habla un idioma contable, necesita regular el gasto para sostener el negocio y es evaluado por cuánto menos gastó respecto al ejercicio anterior, manteniendo la eficacia de la empresa. Como resultado, ambas funciones terminan convirtiéndose en “silos”.
El contexto está planteado y la solución, que en un principio parecía simple, no lo es.
EL PROBLEMA ADAPTATIVO
Lo que inicialmente planteé acerca de una solución proveniente de la Alta Dirección, basada en el liderazgo y la conducción de la organización, o sea, una “directiva” que dé solución al problema, resultó no ser tan simple ni directa. Recién este año, nunca es tarde para aprender, caí en la cuenta de que, si bien estaba orientado en cuanto al origen de los problemas, el camino para solucionarlos era otro.
En el Seminario Digital de Mantenimiento y Gestión de Activos, dictado recientemente por The Woodhouse Partnership Ltd, en la sesión “Gestión del cambio cultural y la productividad de la empresa”, el ingeniero Genaro Pérez Illanes planteó un par de cuestiones que ordenaron mi pensamiento. La primera fue que los “puntos de unión entre áreas son puntos de conflicto”. Creo que huelgan comentarios al respecto: el conflicto entre Mantenimiento y Compras es algo muy común porque sus motivaciones son opuestas. Respecto a la segunda, presentó las brechas más comunes que se encuentran en las organizaciones y de ellas rescaté dos: por un lado, la “falta de visión integrada de cómo opera la organización” y, por otro, la “falta de visión de largo plazo”. Luego mostró varias causas frecuentes de estos gaps y de ellas tomé las siguientes:
1- Estructura funcional versus procesos
Lo planteado anteriormente nos permite ver que existe, indubitablemente, una estructura funcional, donde entre las áreas que dan soporte a la actividad principal no existe una relación de procesos. Dicho esto, podríamos pensar en una alineación horizontal pobre, y es cierto, existe un sistema de “silos”, pero también la alineación vertical no es buena, porque la eficacia de cada silo para alcanzar los objetivos organizacionales no necesariamente redunda en la eficiencia de la organización.
2- Coexistencia de diferentes negocios
Es el “comportamiento de silos”. Cada área resuelve sus problemas, en este caso apoyar a operaciones en su labor productiva, pero también cada uno “atiende su juego” sin importar demasiado las necesidades de las áreas paralelas, en tanto y en cuanto, de haber problemas, los proyectiles impacten fuera de su propio silo. ¿Es un comportamiento egoísta? No sabría si tildarlo de tal, pero lo que sí puedo afirmar es que existe falta de orientación y liderazgo de la Alta Dirección para hacer que las áreas abandonen ese comportamiento y trabajen en pos de la maximización del valor a través de sus activos.

3- Medición del desempeño por áreas y anualmente
Este es un mal generalizado y lo analizaré por partes.
Medición del desempeño por áreas
Respecto a la medición del desempeño por áreas y con relación al tema de este ensayo, la Disponibilidad, o indisponibilidad, y el Costo por Indisponibilidad son indicadores que impactan de lleno en el área de Mantenimiento y ambos tienen un factor común: el “Tiempo Total de Reparación”, definido en el punto 3.61 (figura 5) de la norma ISO/TR 12489:2013.

En la figura se puede apreciar que en el parámetro b, “Preparation and/or delay” (Preparación y/o Demoras), definido en la norma como el “tiempo transcurrido antes de comenzar la reparación”, se contemplan las cuestiones administrativas, logísticas y técnicas que están “fuera de control” de Mantenimiento y que producen demoras. Son ejemplos de esto: “el jefe que autoriza el gasto no está” o “para comprar el repuesto hay que licitar”; “el repuesto no está en depósito” o “el repuesto que está en depósito no es el correcto”; y “el responsable de seguridad no está disponible para autorizar el inicio de la tarea”.
La desagregación del “factor tiempo” en estos KPI permite a la Alta Dirección conocer dónde tiene las brechas en el funcionamiento del sistema y corregirlas, midiendo diferencialmente y con un solo indicador el funcionamiento de las distintas áreas y, además, la alineación horizontal de la organización.
Sé positivamente que esto es muy difícil y he visto que en algunas empresas, para dar solución a esta desalineación que produce tantos dolores de cabeza, los jefes de mantenimiento montan un “pañol paralelo” donde guardan repuestos que consideran críticos, los cuales se han dado por utilizados en el sistema. ¿Pero esta práctica es útil? Si dijese que no, estaría mintiendo, porque yo también lo hice, pero soy consciente de que no le hace bien al sistema, porque en primer lugar “evade” el problema y, en segundo, porque se trabaja bajo premisas falsas y, por consiguiente, las mediciones también son falsas.
Medición anual
Vimos que los objetivos de Mantenimiento y Compras pueden parecer contrapuestos. El primero necesita “gastar” para lograr la disponibilidad requerida, por la cual lo van a evaluar, y el segundo necesita “NO gastar” para poder ahorrar y presentar las mejoras interanuales, por las cuales lo van a medir. Esto, que puede parecer ridículo, es una de las causas que lleva al comportamiento de silos, como ya mencioné anteriormente.
En Gestión de Activos se plantea analizar el costo sobre todo el ciclo de vida de los activos de la organización. Calcularlo cuando se está dentro de lo que se suele llamar proyecto, en las etapas de diseño y construcción, es simple: se mide el CAPEX presupuestado más el OPEX calculado en base a lo planificado, el tiempo que demandará el inicio de producción y se comparan opciones. No se deben perder de vista algunos aspectos, como incluir en el CAPEX los repuestos críticos de baja o nula rotación que se deberían mantener en stock por su criticidad y dificultad de obtención y, en el OPEX, la calidad y rapidez del servicio posventa de los distintos fabricantes y su impacto en el downtime productivo.
Visualizar el OPEX una vez que el sistema está operando es más difícil. En primer lugar, porque, como decimos en la Infantería de Marina, todo plan cambia a partir de que suena el primer disparo; segundo, porque rara vez se analizan con el detalle adecuado los desvíos del OPEX real respecto al planificado y se tiende a justificar los desvíos negativos con causas externas; y tercero, porque los KPIs son usualmente anuales y, más aún, los financieros, ya que estos últimos responden a normas contables que regulan los cierres de balance y cuando se trata de comparaciones interanuales el detalle que implica la rutina del mantenimiento no se aprecia.
Dicho esto, parecería que el CEO no puede evaluar si los niveles intermedios de la organización están siendo realmente eficientes en el gasto. Por ejemplo, el CEO, al chequear los indicadores de su organización, ve que el OEE es muy bueno y que el nivel de gastos interanual se mantiene, lo que le hace suponer que es eficaz, pero nada le indica que es eficiente. ¿Por qué? Porque tanto Mantenimiento como Compras son eficaces, pero su trabajo en silos puede hacer que sean ineficientes si están gastando más de lo necesario.
Para fomentar la cooperación entre Compras y Mantenimiento-Operaciones, es conveniente definir algunos indicadores específicos para medir y propender a la alineación de los objetivos de esos sectores.
Indudablemente, estas causas frecuentes son las mayores generadoras de la falta de alineación horizontal. Tal como plantea el ingeniero Pérez Illanes, son problemas adaptativos, no técnicos y, más allá de contar con indicadores que ayuden a exponer las ineficiencias, la solución también requiere trabajar sobre las competencias de las personas, en este caso las de nivel intermedio, haciéndoles conocer el impacto de su tarea en los objetivos de la organización. La capacitación en Gestión de Activos es una solución, pero no es suficiente; se debe trabajar en lo actitudinal para desarmar los silos e ingresar en un sistema colaborativo.
Para lograr esto, la Alta Dirección debe ejercer su liderazgo e involucrarse en la obtención de explicaciones a las variaciones que hacen a la mejora continua y no un mero análisis forense de las causas, porque sin esto, será muy difícil que la adaptación tenga el final esperado.
EL PROBLEMA TÉCNICO.
Si bien he planteado precedentemente que el problema de desalineación es adaptativo, considero que existen también problemas de índole técnica cuya solución está en ese ámbito. Por otra parte, cabe también la posibilidad de que la Alta Dirección no intervenga para resolver el problema adaptativo y el único camino que quede, para dar alguna solución parcial a esta desalineación, es aplicar un recurso técnico.
El enfoque del presente ensayo va exclusivamente sobre la provisión de insumos y repuestos para mantenimiento. No entraré en el área de la contratación de servicios porque es algo más complejo donde, normalmente, la influencia de Compras no es tan significativa y, más allá de que algunas cuestiones tratadas aquí pueden ser de utilidad para esas situaciones, sugiero prestar mucha atención a lo señalado en el punto 8.3 de la ISO 55.001.
Desde este punto de vista, se pueden identificar dos situaciones genéricas posibles: 1. Que cuando vaya al depósito a buscar el repuesto no esté y 2. Que el repuesto que compraron sea de mala calidad o no sea lo que se pidió.
El repuesto no está.
También en este caso hay dos causas genéricas posibles: 1. Mantenimiento no lo pidió y 2. Compras no lo adquirió. El primero es simple, solo se puede hacer un “mea culpa” y corregir el error. El segundo es más complejo y las respuestas de Compras pueden ser “como ese repuesto nunca lo piden, decidí no reponerlo” o “no tengo dinero para comprarlo”, o aún peor, “ese repuesto es muy caro como para tenerlo en el depósito”. Pero si aparece una falla en un “equipo crítico”, el repuesto para repararlo no está en depósito y se genera una parada de planta con un costo por indisponibilidad muy elevado, “comienza el baile” para todos, ¿o solo para mantenimiento?
Analicémoslo con más profundidad. La “criticidad” de un repuesto no solo responde a la criticidad del equipo al cual pertenece y otros factores, como el cambio de la situación de proveedores, antigüedad del equipamiento a mantener, reformas a los mismos, identificación de repuestos sustitutos, etc., también juegan los factores “precio del repuesto” y “tiempo de obtención”. Veamos cómo se relacionan entre sí.
Si el repuesto es caro y su rotación es muy baja, genera costos por capital inmovilizado, gastos por mantenerlo en stock e incrementa el valor de los impuestos a pagar, pero si no está en estantería al ser requerido, genera Costos por Indisponibilidad (CIF) directamente proporcionales al tiempo en que el sistema está fuera de servicio. Además, hay otras cuestiones que contribuyen a aumentar el CIF, por ejemplo, si es un repuesto de alto costo, la empresa seguramente tiene un procedimiento de compra más lento que el de Compras no estará dispuesto a vulnerar, dilatándose el trámite de adquisición y, si además se lo debe transportar en forma urgente desde el lugar de entrega hasta donde es requerido, será necesario utilizar medios que usualmente son más caros, cosa que también va a generar controversia. Se sabe que la urgencia siempre genera costos más elevados.
Otra cuestión que la organización no puede manejar, aun en repuestos de bajo costo, es el plazo de provisión. Hay veces que los fabricantes de equipos, por diferentes cuestiones y más aún cuando estos ya tienen varios años de uso, no disponen del repuesto y deben fabricarlo o requerirlo a sus propios proveedores. Este tiempo también va a estar penalizando los Costos por Indisponibilidad si el repuesto no está en estantería.
En definitiva, a la sumatoria de todos los tiempos que involucran las acciones requeridas para obtener el repuesto la llamaré “Tiempo de Obtención” y abarca el período desde que se detecta la inexistencia de la pieza en el depósito hasta que, una vez provista, se la retira del mismo para ejecutar la reparación. Algunos de estos lapsos están bajo control de Mantenimiento y otros no. Ejemplo de esos tiempos son los siguientes:
• Especificación del repuesto;
• Presupuestación inicial;
• Decisión de compra;
• Conformación de los pliegos;
• Licitación;
• Autorización del gasto;
• Adjudicación;
• Entrega por parte del proveedor;
• Acarreo del repuesto hasta el depósito;
Todos estos son factores de la ecuación que el Jefe de Mantenimiento debe conocer para poder calcular el “Tiempo Total Medio de Reparación” de una falla de no contarse con el repuesto, porque es algo que no solo depende de su área, también juegan cuestiones administrativas y logísticas que no están bajo su control. Estos datos le van a posibilitar calcular el Costo por Indisponibilidad probable para esa falla de no tener el repuesto en estantería, el cual cuantificará la consecuencia del Riesgo de esa carencia y también le permitirá llevar el problema a un idioma que el de Compras entiende: costos y beneficios. En definitiva, cuánto cuesta tener el repuesto y cuánto costaría si no se lo tiene y surge la falla. Este ejercicio debería realizarse con todos los equipos críticos y, mediante RCM, determinar el stock de repuestos críticos que debería tener en estantería, incluyendo el nivel de seguridad, que va a depender fundamentalmente del Tiempo de Obtención del repuesto.
Esta planificación y cálculo no es otra cosa que una evaluación y cuantificación de riesgos, por esta razón es la Alta Dirección quien debe revisar el plan, considerar las probabilidades de ocurrencia, las consecuencias, los costos involucrados y aprobar las acciones a seguir, asignando responsabilidades y recursos para su logro.
Asimismo, se podría analizar la posibilidad de hacer un “Master Contract” de revisión anual con un proveedor, incluso puede ser pre-aprobado por la Dirección, que prevea todos los detalles en caso de una urgencia, incluso el transporte por avión del repuesto y/o el viaje del técnico del fabricante para su configuración.
También puede ocurrir que la Alta Dirección decida no involucrarse en este tema, entonces con estos datos, el Jefe de Mantenimiento se tendría que reunir con el de Compras para explicarle la necesidad del stock en un idioma que ambos entienden y hacer una “Transferencia del riesgo”, o sea, hacer que comparta las consecuencias de no tener un repuesto. Dicho en buen romance, poner el balón en el campo de juego del financista mediante una comunicación formal en la que se detalle la situación, el requerimiento y los riesgos cuantificados. Si luego no compra lo necesario, deberá “pagar” su parte del costo de las consecuencias del evento si este se presenta y entonces, el baile no será solo para Mantenimiento.
El repuesto que compraron “no sirve”.
La segunda posibilidad es que el repuesto que compraron no sea lo que se pidió o sea de mala calidad. En este caso, la calidad es sinónimo de vida útil del mismo, de acuerdo al uso que se le está dando y en las condiciones en las cuales trabaja, lo cual no necesaria-mente significa que debe estar entre las más costosas de plaza.
El punto de partida del análisis es la comprensión del Ciclo Logístico, que es el proceso mediante el cual se producen acciones para la ejecución de las funciones logísticas, para cumplir eficientemente el abastecimiento de insumos / repuestos en la cantidad, calidad y lugar requeridos y en el momento oportuno. El Ciclo tiene tres fases: Determinación, Ob-tención y Distribución.
La “Determinación de los requerimientos” es el punto de partida del ciclo, nace de una necesidad que debería ser satisfecha al finalizar el mismo y esta fase debe ser llevada a cabo por el “Requirente”, el que necesita el efecto, en este caso Mantenimiento. De la exactitud de esta etapa depende la satisfacción o no de la necesidad y por eso demanda un análisis detallado de la situación y un conocimiento profundo de lo que se va a pedir. Culmina con la cualificación y cuantificación de los efectos, esto significa que el ítem debe ser referido con una “Especificación” precisa, una “Cantidad”, un “Momento de provisión” y un “Lugar de entrega”.
La “Obtención de los requerimientos” es la fase en la que las “necesidades” requeridas se transforman en “efectos”. La compra de ítems no requeridos, equivocados o de una cali-dad inferior a la necesaria implica gastar recursos sin producir el fin deseado y podría deri-var en la salida de servicio de equipos, de ahí la importancia de una adecuada Determina-ción, formalizada a Compras mediante un requerimiento completo y detallado. Por otra par-te, si bien es una etapa netamente “comercial”, resorte directo de la oficina de Compras, es necesario que se cuente con asesoramiento del elemento técnico.
La “Distribución de los efectos” es la fase que cumple con la satisfacción de la necesidad. La eficiencia y regularidad de la distribución son determinantes al definir los niveles de operación y seguridad del stock y tiene un papel muy importante el transporte.
Definido esto, se puede apreciar donde juega cada uno de los actores que se están analizando.

Mantenimiento, como responsable de la “Determinación”, es quien debería confeccionar las especificaciones técnicas de los insumos y repuestos para que Compras los adquiera. Por lo menos eso dice la teoría y la lógica.
Supongamos que hay cambiar un rodamiento de diferencial de un camión. Mantenimiento lo puede pedir de las siguientes formas:
1. Rodamiento según muestra y mandar a Compras el rodamiento en una bolsa de nylon.
2. Rodamiento de rodillos cónicos 91384.
3. Rodamiento de rodillos cónicos para diferencial de camión “Mionca” modelo “LR4000”, numero de parte 177755567.
4. Rodamiento de rodillos cónicos de una hilera en pulgadas, marca BAC, Designación H 913842/810/QCL7C.
5. Rodamiento de rodillos cónicos de una hilera en pulgadas, marca BAC, Designación H 913842/810/QCL7C o equivalentes, de marcas FGH, NMN, Ruedabien o Goodrod.
6. Rodamiento de rodillos cónicos de una hilera en pulgadas, marca BAC, Designación H 913842/810/QCL7C o equivalentes, que cumpla con los siguientes parámetros: medidas ajustadas según norma hhh, capacidad de carga dinámica según norma nnn superior a rrr kN; capacidad de carga estática según norma fff superior a ccc kN, ….
A medida que se especifica mejor, se van acotando las probabilidades de que Compras adquiera un rodamiento que no sirva, pero también se van limitando las posibilidades de comprar lo que se necesita, con la calidad adecuada, al menor costo. Veamos que podría resultar de cada una de las especificaciones planteadas.
• Especificación 1: las probabilidades de recibir un rodamiento barato y/o incorrecto son muy altas.
• Especificación 2: es probable recibir un rodamiento barato y/o que no cumpla con los requerimientos para la función.
• Especificación 3: se restringe a Compras a un repuesto automotriz. Puede adquirir un original o un “alternativo”, que seguramente será más económico pero no necesaria-mente asegurará la calidad que se requiere.
• Especificación 4: se ata a Compras a un rodamiento en particular, de una marca precisa con características perfectamente definidas, pero muy probablemente se genere una controversia por no darle la posibilidad de analizar diferentes alternativas. También pueden ocasionarse demoras para conseguir “ese” rodamiento por haber faltante en plaza.
• Especificación 5: se ata a Compras a un rodamiento de características perfectamente definidas, con diferentes alternativas en cuanto a marcas y solo entre ellas, la más bara-ta.
• Especificación 6: se ata a Compras a un rodamiento de características perfectamente definidas, con parámetros normados que se tienen que cumplir y paralelamente le da la posibilidad de comprar, dentro de todas las marcas que cumplan esos parámetros, la más barata y esto se define como “la más conveniente”. Si se trabaja dentro de una Or-ganización Estatal, este tipo de especificación no es objetada por ninguna de las nor-mas vigentes, por lo menos en Argentina y de hecho, es la única que respeta los princi-pios que rigen el Sistema de Adquisiciones del Estado.
De este ejemplo se puede concluir que:
1. La Determinación de los Requerimientos debe ser hecha meticulosamente, so pena de recibir algo que no sirve al propósito para el que se erogaron los recursos. Una especifi-cación pobre o mal hecha incrementa sensiblemente las probabilidades de recibir un producto que no va a servir.
2. Esta fase se debe plasmar en especificaciones técnicas precisas, que indiquen clara-mente “qué” es lo que se pide, “cuantos” se necesitan, “cuándo” se lo requerirá y “don-de” deberá ser entregado.
3. Las especificaciones técnicas confeccionadas sobre parámetros regidos por normas, aseguran que el producto solicitado se ajuste a las necesidades y tenga la calidad re-querida para las solicitaciones a las que será sometido, dando a Compras la posibilidad de poder “hacer su trabajo” y elegir, dentro de lo especificado, lo más barato.
Ahora bien, ¿esto garantiza que Compras adquiera exactamente lo especificado?
Si su Organización tiene procedimientos donde indica que Mantenimiento específica y participa en el análisis de las ofertas y en la recepción de los efectos y que Compras, por su parte, lleva adelante todo el proceso administrativo de adquisición, la respuesta es sí.
Si no existe este procedimiento, la sugerencia es hacer un “Acuerdo de Servicio” entre Mantenimiento y Compras, donde se incluya que el primero especifica los efectos, asesora técnicamente al momento de evaluar las ofertas, para asegurar que lo que se ofrece es lo que se pide y en la recepción de los mismos, para verificar que lo entregado cumpla con lo especificado, dejando al segundo el resto del trámite. De esta forma, se asegurará que lo que se adquiere sea lo que Mantenimiento necesita.
Cursos recomendados




%252FImagen%252FRAMPREDYC-1730060420837.webp%3Falt%3Dmedia%26token%3D2634a7f0-988e-4022-b91f-382503e6e9db&w=3840&q=75)



Conclusiones
Se vio a lo largo del ensayo que la desalineación horizontal entre Mantenimiento y Com-pras tiene dos aristas, una Actitudinal y otra Técnica.
Para solucionar la primera se deben trabajar las competencias de los responsables de ambas áreas y los indicadores técnicos y financieros, comparándolos durante más de un período fiscal a efectos de poder visualizar la ejecución del gasto en el ciclo de vida del activo, pero eso no es suficiente, se debe eliminar el “comportamiento de silos” en las dife-rentes funciones.
Se podría capacitar a toda la organización en Gestión de Activos, pero no es una solución completa y duradera, se debe trabajar en lo actitudinal para buscar desarmar los silos e ingresar en un sistema colaborativo, donde los resultados se consigan y se evalúen en conjunto y en el mediano plazo, dando tiempo a que los cambios que se produzcan den los beneficios esperados. Para lograr esto, la Alta Dirección debe ejercer adecuadamente su liderazgo e involucrarse en la obtención de explicaciones a las variaciones que hacen a la mejora continua y no un mero análisis forense de las causas, porque sin esto, será muy difícil que la adaptación tenga el final esperado.
Para remediar la segunda hace falta plantear claramente la relación costo – riesgo – bene-ficio de tener o no un repuesto y paralelamente, que cada área asuma la parte que le co-rresponde del Ciclo Logístico, a efectos de lograr que se compre lo que se necesita al pre-cio más conveniente para la Organización.
Pero hay un factor común en ambas aristas y es el liderazgo de la Alta Dirección, requerido para señalar el camino hacia la Gestión de los Activos Físicos, ya que sin él será muy difícil que la gestión de la Organización pase de ser eficaz a ser eficiente y así maximizar el valor que obtiene de sus activos.
Bibliografía:
- ISO 55.000: 2015.
- ISO/TR 12489: 2013.
- Seminario Digital de Mantenimiento y Gestión de Activos. The Woodhouse Partnership Ltd. “Gestión del cambio cultural y la productividad de la empresa”. Ing. Genaro Pérez Illanes.
Referencias:
www.twpl.com
Dinos qué te ha parecido el artículo
Artículos recomendados
Comprendiendo las economías de escala

Modelo del lote económico EOQ para la gestión de stocks

Re-evolución de la naturaleza holística del aire

El BIM como soporte a la Gestión de Activos ISO 55000

Publica tu artículo en la revista #1 de Mantenimiento Industrial
Publicar un artículo en la revista es gratis, no tiene costo.
Solo debes asegurarte que no sea un artículo comercial.
¿Qué esperas?
O envía tu artículo directo: articulos@predictiva21.com
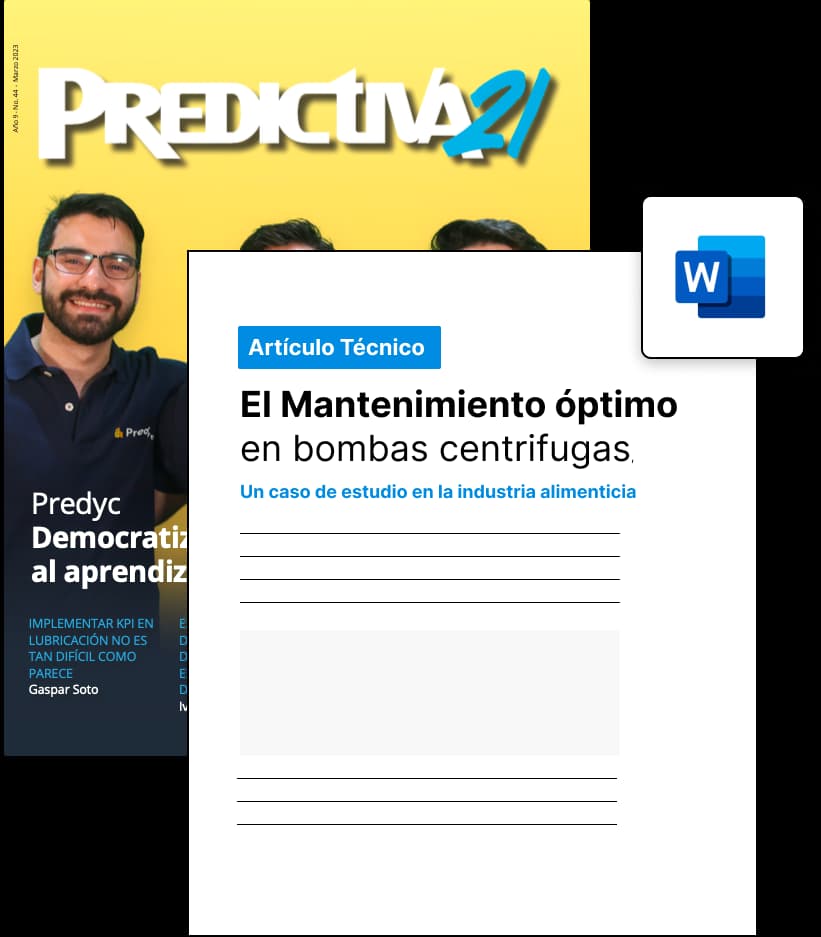
Eliminando los Silos entre Mantenimiento y Compras
Articulo 27 de febrero de 2025Abstract
Uno de los temas que normalmente sale a la luz en las interacciones con la gente de mantenimiento es el problema que tienen con el Área de Compras y Contrataciones para obtener lo que necesitan. Muchas veces, no es porque no lo compren, sino porque “compran tarde” o “compran mal”.
Luego de mi retiro de la Infantería de Marina Argentina, donde adquirí aptitudes en logística y mantenimiento, comencé a trabajar en el ámbito de la Gestión de Activos. Desde esa posición, pensé cómo podía, en base a mi experiencia, hacer un aporte para tratar de “alinear horizontalmente” las funciones operativas y financieras durante la etapa de operación de los activos, particularmente en la eterna “controversia” entre el responsable de Mantenimiento y el responsable de Compras, que tanto perjuicio causa a las organizaciones, muchas veces sin que ellos se den cuenta.
A medida que el análisis iba madurando, inicialmente parecía que podía tener una solución ligada a la conducción de la organización y a acciones técnicas, pero descubrí dos cosas: la primera es que iba a ser muy difícil resolverlo únicamente con la imposición de una directiva de la Alta Dirección; y la segunda, que más allá de que esta se emitiese, había cuestiones técnicas que una orden no podía solucionar. En definitiva, era necesario acabar con los silos.
Desarrollo
En primer lugar, deseo agradecer al Lic. Guillermo Míguez por su inestimable ayuda en el desarrollo del presente ensayo, aportando su visión y experiencia desde el Área de Compras, y a The Woodhouse Partnership Ltd, en la figura del Ingeniero José Durán, por haberme invitado a participar en el Seminario Digital de Mantenimiento y Gestión de Activos 2020, así como al Ingeniero Genaro Pérez Illanes, quien, en la sesión “Gestión del cambio cultural y la productividad de la empresa”, aportó claridad al análisis que estaba realizando y que ahora queda plasmado en este ensayo.
Uno de los temas que normalmente sale a la luz en las interacciones con la gente de mantenimiento es el problema que tienen con el Área de Compras y Contrataciones para obtener lo que necesitan. Muchas veces, no es porque no lo compren, sino porque “compran tarde” o “compran mal”.
Por mi parte, proviniendo del sector de Defensa, más precisamente de la Armada Argentina, me he sentido plenamente identificado con esta problemática. En los muchos años en los que serví en funciones de logística y mantenimiento, además de contar con escasos recursos, a veces extremadamente limitados, me resultaba difícil evitar que los organismos de contrataciones “compraran tarde” o “compraran mal”. Se me enseñó que, en el Estado, la regla de compra es “siempre lo más barato”, pero en el último cuarto de mi carrera, después de obtener un par de posgrados y diplomaturas relacionadas con la logística y el mantenimiento, y tras arduos “intercambios académicos” con abogados y contadores, descubrí que si bien esa afirmación era correcta, también era incompleta. En realidad, la regla completa era: “dentro de lo especificado, siempre lo más barato”. Solo entonces pude comenzar a obtener lo que la Unidad realmente necesitaba para cumplir su función.
Ya fuera del servicio y adentrándome en el ámbito de la Gestión de Activos, pensé cómo podía, desde mi experiencia, hacer un aporte para tratar de “alinear horizontalmente” las funciones operativas y financieras durante la etapa de operación de los activos, particularmente con la eterna “controversia” entre el responsable de Mantenimiento y el responsable de Compras, que tanto perjuicio causa a las organizaciones, muchas veces sin que ellos se den cuenta.
A medida que el análisis iba madurando, inicialmente parecía que podía tener una solución ligada a la conducción de la organización y a acciones técnicas, pero descubrí dos cosas: la primera es que iba a ser muy difícil resolverlo únicamente con la imposición de una directiva de la Alta Dirección; y la segunda, que más allá de que esta se emitiese, había cuestiones técnicas que una orden no podía solucionar.
El Contexto
Para entender el contexto, es necesario comprender las motivaciones y realidades de cada una de las partes involucradas.
El primer problema son los objetivos. Ambas áreas, Mantenimiento y Compras, son habilitadores del área operativa, que es la encargada de cumplir la función que da vida a la organización. Para lograrlo, Mantenimiento debe asegurar que los activos utilizados en operaciones estén disponibles cuando se necesiten, y Compras debe garantizar que los insumos requeridos por operaciones estén disponibles en el momento adecuado. Es decir, el objetivo de Mantenimiento es permitir que operaciones sea eficaz en su cometido, mientras que el de Compras es proveer insumos buscando que la empresa gaste menos dinero, es decir, que sea eficiente. Aquí surge el primer problema: ambas áreas tienen objetivos que, en la relación horizontal y puramente pragmática, parecen opuestos entre sí.
El segundo problema es cómo se miden los objetivos de ambas áreas por parte de la Alta Dirección. Mantenimiento es evaluado por la disponibilidad de los equipos, indicador que representa la primera variable que afecta el OEE (Overall Equipment Effectiveness). Para mejorar la disponibilidad, se pueden llevar a cabo muchas acciones, cuyos resultados en algunos casos no se evidencian de inmediato, sino después de varios años. Como todas estas acciones tienen un costo asociado, los beneficios económicos —es decir, la eficiencia— solo se podrán apreciar tras determinado tiempo.
Paralelamente, Compras es evaluado por la eficiencia en la ejecución del gasto, siendo el indicador más común la relación entre “ventas totales sobre gastos totales” en un año. Si para evaluar la eficiencia de las acciones de Mantenimiento se necesita más de un año, evaluar el gasto asociado mediante comparaciones interanuales no solo tiene poca utilidad, sino que además no refleja la realidad, generando otra controversia.
Por último, ambas áreas hablan idiomas diferentes. Inexorablemente, el área de Mantenimiento intentará explicar sus necesidades a Compras utilizando su propio lenguaje técnico. Probablemente detallará cómo se puede alargar el MTTF (Mean Time to Failure) del equipo “XXX”, mejorando su confiabilidad y disponibilidad. Compras, por su parte, escuchará la explicación, pero no se sentirá particularmente movilizado, porque en toda la argumentación el término “costos” o cualquier referencia a la moneda solo aparecerá asociada a un incremento del gasto.
Resumiendo: Mantenimiento habla un idioma técnico, necesita invertir en insumos y repuestos para sostener el sistema funcionando y es medido por la disponibilidad que logra de los activos. Compras habla un idioma contable, necesita regular el gasto para sostener el negocio y es evaluado por cuánto menos gastó respecto al ejercicio anterior, manteniendo la eficacia de la empresa. Como resultado, ambas funciones terminan convirtiéndose en “silos”.
El contexto está planteado y la solución, que en un principio parecía simple, no lo es.
EL PROBLEMA ADAPTATIVO
Lo que inicialmente planteé acerca de una solución proveniente de la Alta Dirección, basada en el liderazgo y la conducción de la organización, o sea, una “directiva” que dé solución al problema, resultó no ser tan simple ni directa. Recién este año, nunca es tarde para aprender, caí en la cuenta de que, si bien estaba orientado en cuanto al origen de los problemas, el camino para solucionarlos era otro.
En el Seminario Digital de Mantenimiento y Gestión de Activos, dictado recientemente por The Woodhouse Partnership Ltd, en la sesión “Gestión del cambio cultural y la productividad de la empresa”, el ingeniero Genaro Pérez Illanes planteó un par de cuestiones que ordenaron mi pensamiento. La primera fue que los “puntos de unión entre áreas son puntos de conflicto”. Creo que huelgan comentarios al respecto: el conflicto entre Mantenimiento y Compras es algo muy común porque sus motivaciones son opuestas. Respecto a la segunda, presentó las brechas más comunes que se encuentran en las organizaciones y de ellas rescaté dos: por un lado, la “falta de visión integrada de cómo opera la organización” y, por otro, la “falta de visión de largo plazo”. Luego mostró varias causas frecuentes de estos gaps y de ellas tomé las siguientes:
1- Estructura funcional versus procesos
Lo planteado anteriormente nos permite ver que existe, indubitablemente, una estructura funcional, donde entre las áreas que dan soporte a la actividad principal no existe una relación de procesos. Dicho esto, podríamos pensar en una alineación horizontal pobre, y es cierto, existe un sistema de “silos”, pero también la alineación vertical no es buena, porque la eficacia de cada silo para alcanzar los objetivos organizacionales no necesariamente redunda en la eficiencia de la organización.
2- Coexistencia de diferentes negocios
Es el “comportamiento de silos”. Cada área resuelve sus problemas, en este caso apoyar a operaciones en su labor productiva, pero también cada uno “atiende su juego” sin importar demasiado las necesidades de las áreas paralelas, en tanto y en cuanto, de haber problemas, los proyectiles impacten fuera de su propio silo. ¿Es un comportamiento egoísta? No sabría si tildarlo de tal, pero lo que sí puedo afirmar es que existe falta de orientación y liderazgo de la Alta Dirección para hacer que las áreas abandonen ese comportamiento y trabajen en pos de la maximización del valor a través de sus activos.

3- Medición del desempeño por áreas y anualmente
Este es un mal generalizado y lo analizaré por partes.
Medición del desempeño por áreas
Respecto a la medición del desempeño por áreas y con relación al tema de este ensayo, la Disponibilidad, o indisponibilidad, y el Costo por Indisponibilidad son indicadores que impactan de lleno en el área de Mantenimiento y ambos tienen un factor común: el “Tiempo Total de Reparación”, definido en el punto 3.61 (figura 5) de la norma ISO/TR 12489:2013.

En la figura se puede apreciar que en el parámetro b, “Preparation and/or delay” (Preparación y/o Demoras), definido en la norma como el “tiempo transcurrido antes de comenzar la reparación”, se contemplan las cuestiones administrativas, logísticas y técnicas que están “fuera de control” de Mantenimiento y que producen demoras. Son ejemplos de esto: “el jefe que autoriza el gasto no está” o “para comprar el repuesto hay que licitar”; “el repuesto no está en depósito” o “el repuesto que está en depósito no es el correcto”; y “el responsable de seguridad no está disponible para autorizar el inicio de la tarea”.
La desagregación del “factor tiempo” en estos KPI permite a la Alta Dirección conocer dónde tiene las brechas en el funcionamiento del sistema y corregirlas, midiendo diferencialmente y con un solo indicador el funcionamiento de las distintas áreas y, además, la alineación horizontal de la organización.
Sé positivamente que esto es muy difícil y he visto que en algunas empresas, para dar solución a esta desalineación que produce tantos dolores de cabeza, los jefes de mantenimiento montan un “pañol paralelo” donde guardan repuestos que consideran críticos, los cuales se han dado por utilizados en el sistema. ¿Pero esta práctica es útil? Si dijese que no, estaría mintiendo, porque yo también lo hice, pero soy consciente de que no le hace bien al sistema, porque en primer lugar “evade” el problema y, en segundo, porque se trabaja bajo premisas falsas y, por consiguiente, las mediciones también son falsas.
Medición anual
Vimos que los objetivos de Mantenimiento y Compras pueden parecer contrapuestos. El primero necesita “gastar” para lograr la disponibilidad requerida, por la cual lo van a evaluar, y el segundo necesita “NO gastar” para poder ahorrar y presentar las mejoras interanuales, por las cuales lo van a medir. Esto, que puede parecer ridículo, es una de las causas que lleva al comportamiento de silos, como ya mencioné anteriormente.
En Gestión de Activos se plantea analizar el costo sobre todo el ciclo de vida de los activos de la organización. Calcularlo cuando se está dentro de lo que se suele llamar proyecto, en las etapas de diseño y construcción, es simple: se mide el CAPEX presupuestado más el OPEX calculado en base a lo planificado, el tiempo que demandará el inicio de producción y se comparan opciones. No se deben perder de vista algunos aspectos, como incluir en el CAPEX los repuestos críticos de baja o nula rotación que se deberían mantener en stock por su criticidad y dificultad de obtención y, en el OPEX, la calidad y rapidez del servicio posventa de los distintos fabricantes y su impacto en el downtime productivo.
Visualizar el OPEX una vez que el sistema está operando es más difícil. En primer lugar, porque, como decimos en la Infantería de Marina, todo plan cambia a partir de que suena el primer disparo; segundo, porque rara vez se analizan con el detalle adecuado los desvíos del OPEX real respecto al planificado y se tiende a justificar los desvíos negativos con causas externas; y tercero, porque los KPIs son usualmente anuales y, más aún, los financieros, ya que estos últimos responden a normas contables que regulan los cierres de balance y cuando se trata de comparaciones interanuales el detalle que implica la rutina del mantenimiento no se aprecia.
Dicho esto, parecería que el CEO no puede evaluar si los niveles intermedios de la organización están siendo realmente eficientes en el gasto. Por ejemplo, el CEO, al chequear los indicadores de su organización, ve que el OEE es muy bueno y que el nivel de gastos interanual se mantiene, lo que le hace suponer que es eficaz, pero nada le indica que es eficiente. ¿Por qué? Porque tanto Mantenimiento como Compras son eficaces, pero su trabajo en silos puede hacer que sean ineficientes si están gastando más de lo necesario.
Para fomentar la cooperación entre Compras y Mantenimiento-Operaciones, es conveniente definir algunos indicadores específicos para medir y propender a la alineación de los objetivos de esos sectores.
Indudablemente, estas causas frecuentes son las mayores generadoras de la falta de alineación horizontal. Tal como plantea el ingeniero Pérez Illanes, son problemas adaptativos, no técnicos y, más allá de contar con indicadores que ayuden a exponer las ineficiencias, la solución también requiere trabajar sobre las competencias de las personas, en este caso las de nivel intermedio, haciéndoles conocer el impacto de su tarea en los objetivos de la organización. La capacitación en Gestión de Activos es una solución, pero no es suficiente; se debe trabajar en lo actitudinal para desarmar los silos e ingresar en un sistema colaborativo.
Para lograr esto, la Alta Dirección debe ejercer su liderazgo e involucrarse en la obtención de explicaciones a las variaciones que hacen a la mejora continua y no un mero análisis forense de las causas, porque sin esto, será muy difícil que la adaptación tenga el final esperado.
EL PROBLEMA TÉCNICO.
Si bien he planteado precedentemente que el problema de desalineación es adaptativo, considero que existen también problemas de índole técnica cuya solución está en ese ámbito. Por otra parte, cabe también la posibilidad de que la Alta Dirección no intervenga para resolver el problema adaptativo y el único camino que quede, para dar alguna solución parcial a esta desalineación, es aplicar un recurso técnico.
El enfoque del presente ensayo va exclusivamente sobre la provisión de insumos y repuestos para mantenimiento. No entraré en el área de la contratación de servicios porque es algo más complejo donde, normalmente, la influencia de Compras no es tan significativa y, más allá de que algunas cuestiones tratadas aquí pueden ser de utilidad para esas situaciones, sugiero prestar mucha atención a lo señalado en el punto 8.3 de la ISO 55.001.
Desde este punto de vista, se pueden identificar dos situaciones genéricas posibles: 1. Que cuando vaya al depósito a buscar el repuesto no esté y 2. Que el repuesto que compraron sea de mala calidad o no sea lo que se pidió.
El repuesto no está.
También en este caso hay dos causas genéricas posibles: 1. Mantenimiento no lo pidió y 2. Compras no lo adquirió. El primero es simple, solo se puede hacer un “mea culpa” y corregir el error. El segundo es más complejo y las respuestas de Compras pueden ser “como ese repuesto nunca lo piden, decidí no reponerlo” o “no tengo dinero para comprarlo”, o aún peor, “ese repuesto es muy caro como para tenerlo en el depósito”. Pero si aparece una falla en un “equipo crítico”, el repuesto para repararlo no está en depósito y se genera una parada de planta con un costo por indisponibilidad muy elevado, “comienza el baile” para todos, ¿o solo para mantenimiento?
Analicémoslo con más profundidad. La “criticidad” de un repuesto no solo responde a la criticidad del equipo al cual pertenece y otros factores, como el cambio de la situación de proveedores, antigüedad del equipamiento a mantener, reformas a los mismos, identificación de repuestos sustitutos, etc., también juegan los factores “precio del repuesto” y “tiempo de obtención”. Veamos cómo se relacionan entre sí.
Si el repuesto es caro y su rotación es muy baja, genera costos por capital inmovilizado, gastos por mantenerlo en stock e incrementa el valor de los impuestos a pagar, pero si no está en estantería al ser requerido, genera Costos por Indisponibilidad (CIF) directamente proporcionales al tiempo en que el sistema está fuera de servicio. Además, hay otras cuestiones que contribuyen a aumentar el CIF, por ejemplo, si es un repuesto de alto costo, la empresa seguramente tiene un procedimiento de compra más lento que el de Compras no estará dispuesto a vulnerar, dilatándose el trámite de adquisición y, si además se lo debe transportar en forma urgente desde el lugar de entrega hasta donde es requerido, será necesario utilizar medios que usualmente son más caros, cosa que también va a generar controversia. Se sabe que la urgencia siempre genera costos más elevados.
Otra cuestión que la organización no puede manejar, aun en repuestos de bajo costo, es el plazo de provisión. Hay veces que los fabricantes de equipos, por diferentes cuestiones y más aún cuando estos ya tienen varios años de uso, no disponen del repuesto y deben fabricarlo o requerirlo a sus propios proveedores. Este tiempo también va a estar penalizando los Costos por Indisponibilidad si el repuesto no está en estantería.
En definitiva, a la sumatoria de todos los tiempos que involucran las acciones requeridas para obtener el repuesto la llamaré “Tiempo de Obtención” y abarca el período desde que se detecta la inexistencia de la pieza en el depósito hasta que, una vez provista, se la retira del mismo para ejecutar la reparación. Algunos de estos lapsos están bajo control de Mantenimiento y otros no. Ejemplo de esos tiempos son los siguientes:
• Especificación del repuesto;
• Presupuestación inicial;
• Decisión de compra;
• Conformación de los pliegos;
• Licitación;
• Autorización del gasto;
• Adjudicación;
• Entrega por parte del proveedor;
• Acarreo del repuesto hasta el depósito;
Todos estos son factores de la ecuación que el Jefe de Mantenimiento debe conocer para poder calcular el “Tiempo Total Medio de Reparación” de una falla de no contarse con el repuesto, porque es algo que no solo depende de su área, también juegan cuestiones administrativas y logísticas que no están bajo su control. Estos datos le van a posibilitar calcular el Costo por Indisponibilidad probable para esa falla de no tener el repuesto en estantería, el cual cuantificará la consecuencia del Riesgo de esa carencia y también le permitirá llevar el problema a un idioma que el de Compras entiende: costos y beneficios. En definitiva, cuánto cuesta tener el repuesto y cuánto costaría si no se lo tiene y surge la falla. Este ejercicio debería realizarse con todos los equipos críticos y, mediante RCM, determinar el stock de repuestos críticos que debería tener en estantería, incluyendo el nivel de seguridad, que va a depender fundamentalmente del Tiempo de Obtención del repuesto.
Esta planificación y cálculo no es otra cosa que una evaluación y cuantificación de riesgos, por esta razón es la Alta Dirección quien debe revisar el plan, considerar las probabilidades de ocurrencia, las consecuencias, los costos involucrados y aprobar las acciones a seguir, asignando responsabilidades y recursos para su logro.
Asimismo, se podría analizar la posibilidad de hacer un “Master Contract” de revisión anual con un proveedor, incluso puede ser pre-aprobado por la Dirección, que prevea todos los detalles en caso de una urgencia, incluso el transporte por avión del repuesto y/o el viaje del técnico del fabricante para su configuración.
También puede ocurrir que la Alta Dirección decida no involucrarse en este tema, entonces con estos datos, el Jefe de Mantenimiento se tendría que reunir con el de Compras para explicarle la necesidad del stock en un idioma que ambos entienden y hacer una “Transferencia del riesgo”, o sea, hacer que comparta las consecuencias de no tener un repuesto. Dicho en buen romance, poner el balón en el campo de juego del financista mediante una comunicación formal en la que se detalle la situación, el requerimiento y los riesgos cuantificados. Si luego no compra lo necesario, deberá “pagar” su parte del costo de las consecuencias del evento si este se presenta y entonces, el baile no será solo para Mantenimiento.
El repuesto que compraron “no sirve”.
La segunda posibilidad es que el repuesto que compraron no sea lo que se pidió o sea de mala calidad. En este caso, la calidad es sinónimo de vida útil del mismo, de acuerdo al uso que se le está dando y en las condiciones en las cuales trabaja, lo cual no necesaria-mente significa que debe estar entre las más costosas de plaza.
El punto de partida del análisis es la comprensión del Ciclo Logístico, que es el proceso mediante el cual se producen acciones para la ejecución de las funciones logísticas, para cumplir eficientemente el abastecimiento de insumos / repuestos en la cantidad, calidad y lugar requeridos y en el momento oportuno. El Ciclo tiene tres fases: Determinación, Ob-tención y Distribución.
La “Determinación de los requerimientos” es el punto de partida del ciclo, nace de una necesidad que debería ser satisfecha al finalizar el mismo y esta fase debe ser llevada a cabo por el “Requirente”, el que necesita el efecto, en este caso Mantenimiento. De la exactitud de esta etapa depende la satisfacción o no de la necesidad y por eso demanda un análisis detallado de la situación y un conocimiento profundo de lo que se va a pedir. Culmina con la cualificación y cuantificación de los efectos, esto significa que el ítem debe ser referido con una “Especificación” precisa, una “Cantidad”, un “Momento de provisión” y un “Lugar de entrega”.
La “Obtención de los requerimientos” es la fase en la que las “necesidades” requeridas se transforman en “efectos”. La compra de ítems no requeridos, equivocados o de una cali-dad inferior a la necesaria implica gastar recursos sin producir el fin deseado y podría deri-var en la salida de servicio de equipos, de ahí la importancia de una adecuada Determina-ción, formalizada a Compras mediante un requerimiento completo y detallado. Por otra par-te, si bien es una etapa netamente “comercial”, resorte directo de la oficina de Compras, es necesario que se cuente con asesoramiento del elemento técnico.
La “Distribución de los efectos” es la fase que cumple con la satisfacción de la necesidad. La eficiencia y regularidad de la distribución son determinantes al definir los niveles de operación y seguridad del stock y tiene un papel muy importante el transporte.
Definido esto, se puede apreciar donde juega cada uno de los actores que se están analizando.

Mantenimiento, como responsable de la “Determinación”, es quien debería confeccionar las especificaciones técnicas de los insumos y repuestos para que Compras los adquiera. Por lo menos eso dice la teoría y la lógica.
Supongamos que hay cambiar un rodamiento de diferencial de un camión. Mantenimiento lo puede pedir de las siguientes formas:
1. Rodamiento según muestra y mandar a Compras el rodamiento en una bolsa de nylon.
2. Rodamiento de rodillos cónicos 91384.
3. Rodamiento de rodillos cónicos para diferencial de camión “Mionca” modelo “LR4000”, numero de parte 177755567.
4. Rodamiento de rodillos cónicos de una hilera en pulgadas, marca BAC, Designación H 913842/810/QCL7C.
5. Rodamiento de rodillos cónicos de una hilera en pulgadas, marca BAC, Designación H 913842/810/QCL7C o equivalentes, de marcas FGH, NMN, Ruedabien o Goodrod.
6. Rodamiento de rodillos cónicos de una hilera en pulgadas, marca BAC, Designación H 913842/810/QCL7C o equivalentes, que cumpla con los siguientes parámetros: medidas ajustadas según norma hhh, capacidad de carga dinámica según norma nnn superior a rrr kN; capacidad de carga estática según norma fff superior a ccc kN, ….
A medida que se especifica mejor, se van acotando las probabilidades de que Compras adquiera un rodamiento que no sirva, pero también se van limitando las posibilidades de comprar lo que se necesita, con la calidad adecuada, al menor costo. Veamos que podría resultar de cada una de las especificaciones planteadas.
• Especificación 1: las probabilidades de recibir un rodamiento barato y/o incorrecto son muy altas.
• Especificación 2: es probable recibir un rodamiento barato y/o que no cumpla con los requerimientos para la función.
• Especificación 3: se restringe a Compras a un repuesto automotriz. Puede adquirir un original o un “alternativo”, que seguramente será más económico pero no necesaria-mente asegurará la calidad que se requiere.
• Especificación 4: se ata a Compras a un rodamiento en particular, de una marca precisa con características perfectamente definidas, pero muy probablemente se genere una controversia por no darle la posibilidad de analizar diferentes alternativas. También pueden ocasionarse demoras para conseguir “ese” rodamiento por haber faltante en plaza.
• Especificación 5: se ata a Compras a un rodamiento de características perfectamente definidas, con diferentes alternativas en cuanto a marcas y solo entre ellas, la más bara-ta.
• Especificación 6: se ata a Compras a un rodamiento de características perfectamente definidas, con parámetros normados que se tienen que cumplir y paralelamente le da la posibilidad de comprar, dentro de todas las marcas que cumplan esos parámetros, la más barata y esto se define como “la más conveniente”. Si se trabaja dentro de una Or-ganización Estatal, este tipo de especificación no es objetada por ninguna de las nor-mas vigentes, por lo menos en Argentina y de hecho, es la única que respeta los princi-pios que rigen el Sistema de Adquisiciones del Estado.
De este ejemplo se puede concluir que:
1. La Determinación de los Requerimientos debe ser hecha meticulosamente, so pena de recibir algo que no sirve al propósito para el que se erogaron los recursos. Una especifi-cación pobre o mal hecha incrementa sensiblemente las probabilidades de recibir un producto que no va a servir.
2. Esta fase se debe plasmar en especificaciones técnicas precisas, que indiquen clara-mente “qué” es lo que se pide, “cuantos” se necesitan, “cuándo” se lo requerirá y “don-de” deberá ser entregado.
3. Las especificaciones técnicas confeccionadas sobre parámetros regidos por normas, aseguran que el producto solicitado se ajuste a las necesidades y tenga la calidad re-querida para las solicitaciones a las que será sometido, dando a Compras la posibilidad de poder “hacer su trabajo” y elegir, dentro de lo especificado, lo más barato.
Ahora bien, ¿esto garantiza que Compras adquiera exactamente lo especificado?
Si su Organización tiene procedimientos donde indica que Mantenimiento específica y participa en el análisis de las ofertas y en la recepción de los efectos y que Compras, por su parte, lleva adelante todo el proceso administrativo de adquisición, la respuesta es sí.
Si no existe este procedimiento, la sugerencia es hacer un “Acuerdo de Servicio” entre Mantenimiento y Compras, donde se incluya que el primero especifica los efectos, asesora técnicamente al momento de evaluar las ofertas, para asegurar que lo que se ofrece es lo que se pide y en la recepción de los mismos, para verificar que lo entregado cumpla con lo especificado, dejando al segundo el resto del trámite. De esta forma, se asegurará que lo que se adquiere sea lo que Mantenimiento necesita.
Cursos recomendados




%252FImagen%252FRAMPREDYC-1730060420837.webp%3Falt%3Dmedia%26token%3D2634a7f0-988e-4022-b91f-382503e6e9db&w=3840&q=75)



Conclusiones
Se vio a lo largo del ensayo que la desalineación horizontal entre Mantenimiento y Com-pras tiene dos aristas, una Actitudinal y otra Técnica.
Para solucionar la primera se deben trabajar las competencias de los responsables de ambas áreas y los indicadores técnicos y financieros, comparándolos durante más de un período fiscal a efectos de poder visualizar la ejecución del gasto en el ciclo de vida del activo, pero eso no es suficiente, se debe eliminar el “comportamiento de silos” en las dife-rentes funciones.
Se podría capacitar a toda la organización en Gestión de Activos, pero no es una solución completa y duradera, se debe trabajar en lo actitudinal para buscar desarmar los silos e ingresar en un sistema colaborativo, donde los resultados se consigan y se evalúen en conjunto y en el mediano plazo, dando tiempo a que los cambios que se produzcan den los beneficios esperados. Para lograr esto, la Alta Dirección debe ejercer adecuadamente su liderazgo e involucrarse en la obtención de explicaciones a las variaciones que hacen a la mejora continua y no un mero análisis forense de las causas, porque sin esto, será muy difícil que la adaptación tenga el final esperado.
Para remediar la segunda hace falta plantear claramente la relación costo – riesgo – bene-ficio de tener o no un repuesto y paralelamente, que cada área asuma la parte que le co-rresponde del Ciclo Logístico, a efectos de lograr que se compre lo que se necesita al pre-cio más conveniente para la Organización.
Pero hay un factor común en ambas aristas y es el liderazgo de la Alta Dirección, requerido para señalar el camino hacia la Gestión de los Activos Físicos, ya que sin él será muy difícil que la gestión de la Organización pase de ser eficaz a ser eficiente y así maximizar el valor que obtiene de sus activos.
Bibliografía:
- ISO 55.000: 2015.
- ISO/TR 12489: 2013.
- Seminario Digital de Mantenimiento y Gestión de Activos. The Woodhouse Partnership Ltd. “Gestión del cambio cultural y la productividad de la empresa”. Ing. Genaro Pérez Illanes.
Referencias:
www.twpl.com
Dinos qué te ha parecido el artículo
Artículos recomendados
Comprendiendo las economías de escala

Modelo del lote económico EOQ para la gestión de stocks

Aumento de la carga dinámica en rodamientos por causa del desbalance

Desafíos que enfrentan los Gerentes de Mantenimiento

Publica tu artículo en la revista #1 de Mantenimiento Industrial
Publicar un artículo en la revista es gratis, no tiene costo.
Solo debes asegurarte que no sea un artículo comercial.
¿Qué esperas?
O envía tu artículo directo: articulos@predictiva21.com
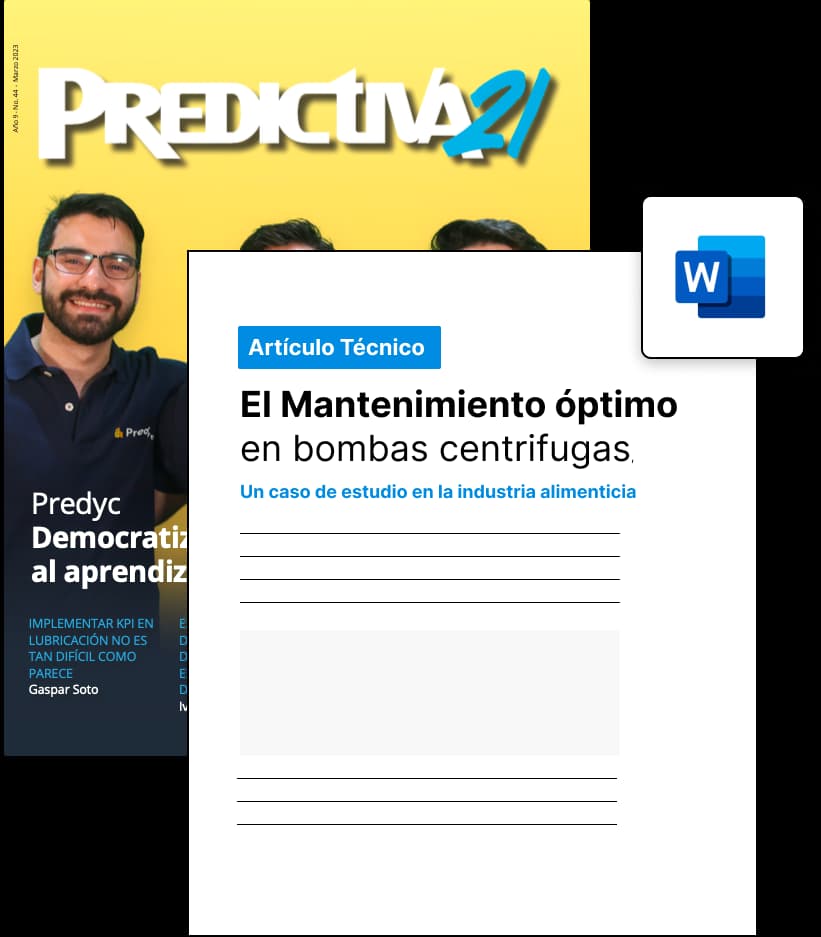