Descubre El Análisis RAM
Articulo2 de agosto de 2023
Autor: Predictiva 21La revista digital de Mantenimiento, Confiabilidad y Gestión de Activos.
Para los trabajadores en mantenimiento, el análisis RAM forma parte esencial de su rutina. En el análisis RAM existe indicadores como lo son: %252FImagen%252Frcm-1730083250826.webp%3Falt%3Dmedia%26token%3D3775356a-7b11-4c44-b21f-45b3409fb9ed&w=3840&q=75)
Andrés GonzálezMantenimiento Centrado en Confiabilidad (RCM)
Carlos VillegasAplicación de la ISO 14224 en la Gestión de Mantenimiento y Confiabilidad%252FImagen%252FRAMPREDYC-1730060420837.webp%3Falt%3Dmedia%26token%3D2634a7f0-988e-4022-b91f-382503e6e9db&w=3840&q=75)
Enrique GonzálezAnálisis de Confiabilidad, Disponibilidad y Mantenibilidad (RAM)
Jose Contreras MarquezGestión y optimización de inventarios para mantenimiento
- La confiabilidad,
- Disponibilidad, y
- Mantenibilidad.
¿Qué es el análisis RAM?
Básicamente, los principales objetivos del análisis RAM consisten en reducir los costes de mantenimiento y funcionamiento. Además, mejorar la productividad y, en consecuencia, aumentar la rentabilidad de la organización. El análisis RAM evalúa el rendimiento del sistema midiendo el número de averías de la máquina, el tiempo entre estas averías, el tiempo para repararlas y otras métricas. Sabiendo que este análisis utiliza cálculos y números para evaluar los equipos, podemos concluir que los resultados medidos por los tres conceptos RAM, en función de sus fórmulas y requisitos, deben expresarse siempre en términos cuantificables. Por ejemplo, el cálculo de la fiabilidad, que corresponde a un porcentaje que indica el correcto funcionamiento del equipo durante un tiempo determinado, medido en horas. Antes de continuar, es necesario recordar que el análisis RAM es una evaluación rigurosa que no debe permitir ninguna desinformación. Es decir, los registros deben ser siempre impecables e imposibles de generar interpretaciones erróneas, ya que esto afecta a toda la cadena de producción.Confiabilidad
La primera letra del análisis RAM (Reliability) representa la probabilidad de que la máquina realice su función. Esta es especificada por el proyecto y en las condiciones de funcionamiento durante un periodo de tiempo determinado. Y esta probabilidad, que tiene en cuenta los fallos que ya se han producido, indica al responsable de mantenimiento hasta qué punto puede confiar en ese equipo.Herramientas para medir la confiabilidad
- AMFE: el Análisis de Modos y Efectos de Fallos identifica los daños en los equipos antes de que se produzcan realmente, así como sus causas y consecuencias. También. clasifica los fallos calculando el RPN (Número de Prioridad de Riesgo). Así, responde las preguntas claves para un plan de mantenimiento: ¿cuál es el fallo? ¿Cómo se ha producido? ¿Cuántas veces? ¿Cuál ha sido su impacto? ¿Cuál es su gravedad? ¿Cuál es el nivel de riesgo?
- Árbol de fallas (FT): una forma organizada y lógica de relacionar los fallos y sus causas. Al reconstruir inversamente el proceso que condujo al problema, el árbol de fallos permite al gestor descubrir las "raíces" de la avería. También, es bastante útil para mostrar la capacidad de un sistema para resistir fallos únicos o múltiples.
Reliability = R(t) = e-λt
Donde:- e: número de Euler ≈ 2,7182
- t: tiempo medido en segundos, horas o días. Cabe destacar que se debe usar la misma unidad de tiempo que en el indicador MTBF.
- λ: tasa de fallos, donde λ(t) = 1/MTBF .
Cursos recomendados
%252FImagen%252Frcm-1730083250826.webp%3Falt%3Dmedia%26token%3D3775356a-7b11-4c44-b21f-45b3409fb9ed&w=3840&q=75)

En línea en vivo4 de octubre


En línea en vivo25 de octubre
%252FImagen%252FRAMPREDYC-1730060420837.webp%3Falt%3Dmedia%26token%3D2634a7f0-988e-4022-b91f-382503e6e9db&w=3840&q=75)

En línea en vivo1 de noviembre


En línea en vivo11 de noviembre
Disponibilidad
La disponibilidad se refiere a eventos del pasado y al tiempo que el equipo ha estado disponible para realizar sus funciones especificadas. Es decir, es la capacidad de un equipo para desempeñar la función que se le ha asignado durante un periodo de tiempo determinado. Al calcular la disponibilidad, comparamos el número de horas que la máquina ha estado disponible con el número de horas de trabajo previstas. Este cálculo se basa en dos indicadores importantes:- MTBF (tiempo medio entre fallos), usado para medir la fiabilidad de una máquina.
- MTTR (Mean Time To Repair), que analiza el tiempo medio que tarda el equipo en reparar la máquina.
Availability = MTBF/(MTBF + MTTR)
Mantenibilidad
La mantenibilidad se refiere a la facilidad con la que podemos reparar la máquina y devolverla a su funcionamiento normal después de un fallo. En el análisis RAM, la mantenibilidad se centra en eliminar obstáculos y dificultades en el trabajo de los técnicos y mantener el buen funcionamiento de la máquina. Porque, lógicamente, entre más difícil sea reparar el equipo, menor será la mantenibilidad. El desenlace, será mayores costes de mantenimiento y mayores impactos en la productividad de la empresa. Una gran diferencia respecto a los otros componentes del análisis RAM (confiabilidad y disponibilidad), la mantenibilidad no es del todo cuantificable. Por tal motivo, requiere una evaluación más humana que tenga en cuenta, además de los costes, algunos aspectos críticos para el trabajo del equipo de mantenimiento.¿Cuándo debo realizar un análisis RAM?
El análisis RAM puede aplicarse en varias fases del ciclo de vida.- Pre-FEED: el análisis RAM puede utilizarse para comparar varias opciones de diseño que se están considerando mediante la cuantificación del rendimiento de producción de cada opción. Se sabe que la realización de un análisis RAM en esta fase, mientras aún se está ultimando el diseño, reduce el impacto en el coste y el calendario del proyecto en comparación con si se realiza en una fase posterior.
- FEED: en la fase FEED se identifican los equipos críticos que podrían causar pérdidas de producción significativas. Normalmente se realiza un análisis RAM de estos equipos críticos para optimizar la configuración de los equipos e identificar las necesidades de piezas de repuesto adicionales o redundancias de equipos para optimizar la disponibilidad del sistema.
- Ingeniería de detalle: en la fase de ingeniería de detalle es probable que el diseño se congele con cambios mínimos. Un estudio RAM en este punto permitiría al cliente identificar los objetivos de rendimiento que debe cumplir el equipo, que pueden utilizarse como parte de la especificación de diseño del equipo durante la adquisición.
- Funcionamiento del proceso: mientras el proceso está en funcionamiento, la realización de un estudio RAM utilizando los datos de la instalación tal y como se construyó puede aportar la ventaja de identificar los equipos poco fiables que están provocando pérdidas de producción.
- DTI.
- Lista de equipos.
- Configuración de los equipos.
- Descripción de los modos de funcionamiento.
- Filosofía de mantenimiento.
Dinos qué te ha parecido el artículo
Artículos recomendados
Capacitación en mantenimiento industrial

Autor: Predictiva 21La revista digital de Mantenimiento, Confiabilidad y Gestión de Activos.
Lanzamiento del nuevo libro "Cases on Optimizing the Asset Management Process"

Autor: Predictiva 21La revista digital de Mantenimiento, Confiabilidad y Gestión de Activos.
Holgura rotativa y sus etapas analizadas con la forma de onda de aceleración

Autor: Predictiva 21La revista digital de Mantenimiento, Confiabilidad y Gestión de Activos.
Análisis de Lubricantes y sus competencias Técnicas

Autor: Predictiva 21La revista digital de Mantenimiento, Confiabilidad y Gestión de Activos.
Publica tu artículo en la revista #1 de Mantenimiento Industrial
Publicar un artículo en la revista es gratis, no tiene costo.
Solo debes asegurarte que no sea un artículo comercial.
¿Qué esperas?
O envía tu artículo directo: articulos@predictiva21.com
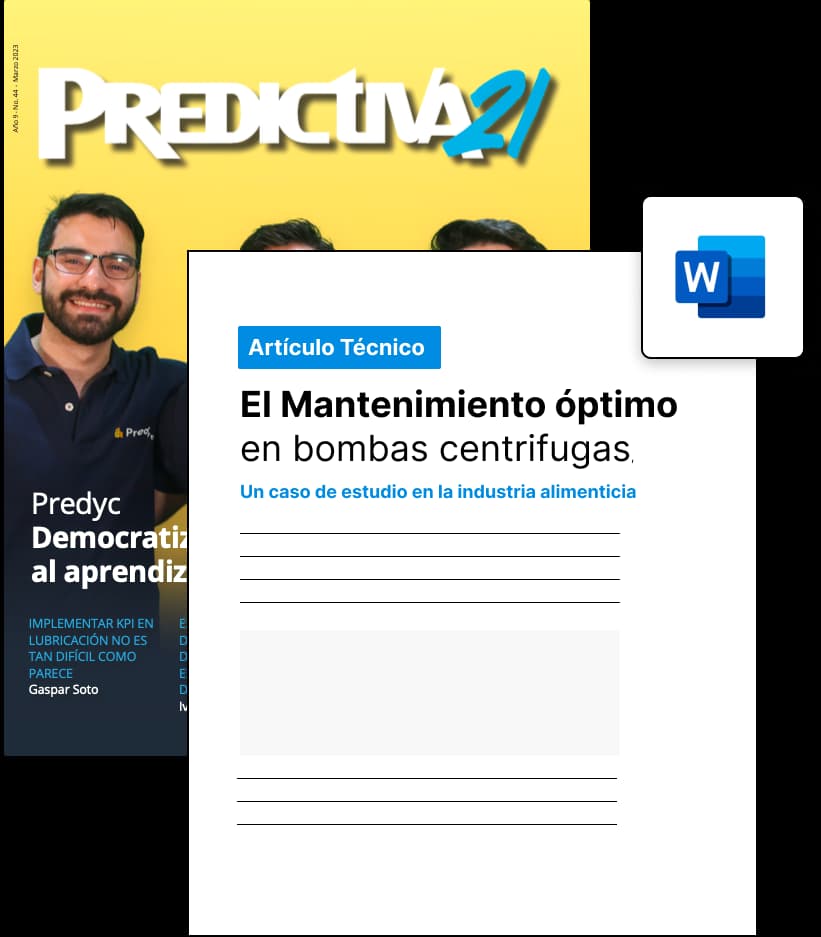
Descubre El Análisis RAM
Articulo 2 de agosto de 2023Para los trabajadores en mantenimiento, el análisis RAM forma parte esencial de su rutina. En el análisis RAM existe indicadores como lo son: %252FImagen%252Frcm-1730083250826.webp%3Falt%3Dmedia%26token%3D3775356a-7b11-4c44-b21f-45b3409fb9ed&w=3840&q=75)
Andrés GonzálezMantenimiento Centrado en Confiabilidad (RCM)
Carlos VillegasAplicación de la ISO 14224 en la Gestión de Mantenimiento y Confiabilidad%252FImagen%252FRAMPREDYC-1730060420837.webp%3Falt%3Dmedia%26token%3D2634a7f0-988e-4022-b91f-382503e6e9db&w=3840&q=75)
Enrique GonzálezAnálisis de Confiabilidad, Disponibilidad y Mantenibilidad (RAM)
Jose Contreras MarquezGestión y optimización de inventarios para mantenimiento
- La confiabilidad,
- Disponibilidad, y
- Mantenibilidad.
¿Qué es el análisis RAM?
Básicamente, los principales objetivos del análisis RAM consisten en reducir los costes de mantenimiento y funcionamiento. Además, mejorar la productividad y, en consecuencia, aumentar la rentabilidad de la organización. El análisis RAM evalúa el rendimiento del sistema midiendo el número de averías de la máquina, el tiempo entre estas averías, el tiempo para repararlas y otras métricas. Sabiendo que este análisis utiliza cálculos y números para evaluar los equipos, podemos concluir que los resultados medidos por los tres conceptos RAM, en función de sus fórmulas y requisitos, deben expresarse siempre en términos cuantificables. Por ejemplo, el cálculo de la fiabilidad, que corresponde a un porcentaje que indica el correcto funcionamiento del equipo durante un tiempo determinado, medido en horas. Antes de continuar, es necesario recordar que el análisis RAM es una evaluación rigurosa que no debe permitir ninguna desinformación. Es decir, los registros deben ser siempre impecables e imposibles de generar interpretaciones erróneas, ya que esto afecta a toda la cadena de producción.Confiabilidad
La primera letra del análisis RAM (Reliability) representa la probabilidad de que la máquina realice su función. Esta es especificada por el proyecto y en las condiciones de funcionamiento durante un periodo de tiempo determinado. Y esta probabilidad, que tiene en cuenta los fallos que ya se han producido, indica al responsable de mantenimiento hasta qué punto puede confiar en ese equipo.Herramientas para medir la confiabilidad
- AMFE: el Análisis de Modos y Efectos de Fallos identifica los daños en los equipos antes de que se produzcan realmente, así como sus causas y consecuencias. También. clasifica los fallos calculando el RPN (Número de Prioridad de Riesgo). Así, responde las preguntas claves para un plan de mantenimiento: ¿cuál es el fallo? ¿Cómo se ha producido? ¿Cuántas veces? ¿Cuál ha sido su impacto? ¿Cuál es su gravedad? ¿Cuál es el nivel de riesgo?
- Árbol de fallas (FT): una forma organizada y lógica de relacionar los fallos y sus causas. Al reconstruir inversamente el proceso que condujo al problema, el árbol de fallos permite al gestor descubrir las "raíces" de la avería. También, es bastante útil para mostrar la capacidad de un sistema para resistir fallos únicos o múltiples.
Reliability = R(t) = e-λt
Donde:- e: número de Euler ≈ 2,7182
- t: tiempo medido en segundos, horas o días. Cabe destacar que se debe usar la misma unidad de tiempo que en el indicador MTBF.
- λ: tasa de fallos, donde λ(t) = 1/MTBF .
Cursos recomendados
%252FImagen%252Frcm-1730083250826.webp%3Falt%3Dmedia%26token%3D3775356a-7b11-4c44-b21f-45b3409fb9ed&w=3840&q=75)

En línea en vivo4 de octubre


En línea en vivo25 de octubre
%252FImagen%252FRAMPREDYC-1730060420837.webp%3Falt%3Dmedia%26token%3D2634a7f0-988e-4022-b91f-382503e6e9db&w=3840&q=75)

En línea en vivo1 de noviembre


En línea en vivo11 de noviembre
Disponibilidad
La disponibilidad se refiere a eventos del pasado y al tiempo que el equipo ha estado disponible para realizar sus funciones especificadas. Es decir, es la capacidad de un equipo para desempeñar la función que se le ha asignado durante un periodo de tiempo determinado. Al calcular la disponibilidad, comparamos el número de horas que la máquina ha estado disponible con el número de horas de trabajo previstas. Este cálculo se basa en dos indicadores importantes:- MTBF (tiempo medio entre fallos), usado para medir la fiabilidad de una máquina.
- MTTR (Mean Time To Repair), que analiza el tiempo medio que tarda el equipo en reparar la máquina.
Availability = MTBF/(MTBF + MTTR)
Mantenibilidad
La mantenibilidad se refiere a la facilidad con la que podemos reparar la máquina y devolverla a su funcionamiento normal después de un fallo. En el análisis RAM, la mantenibilidad se centra en eliminar obstáculos y dificultades en el trabajo de los técnicos y mantener el buen funcionamiento de la máquina. Porque, lógicamente, entre más difícil sea reparar el equipo, menor será la mantenibilidad. El desenlace, será mayores costes de mantenimiento y mayores impactos en la productividad de la empresa. Una gran diferencia respecto a los otros componentes del análisis RAM (confiabilidad y disponibilidad), la mantenibilidad no es del todo cuantificable. Por tal motivo, requiere una evaluación más humana que tenga en cuenta, además de los costes, algunos aspectos críticos para el trabajo del equipo de mantenimiento.¿Cuándo debo realizar un análisis RAM?
El análisis RAM puede aplicarse en varias fases del ciclo de vida.- Pre-FEED: el análisis RAM puede utilizarse para comparar varias opciones de diseño que se están considerando mediante la cuantificación del rendimiento de producción de cada opción. Se sabe que la realización de un análisis RAM en esta fase, mientras aún se está ultimando el diseño, reduce el impacto en el coste y el calendario del proyecto en comparación con si se realiza en una fase posterior.
- FEED: en la fase FEED se identifican los equipos críticos que podrían causar pérdidas de producción significativas. Normalmente se realiza un análisis RAM de estos equipos críticos para optimizar la configuración de los equipos e identificar las necesidades de piezas de repuesto adicionales o redundancias de equipos para optimizar la disponibilidad del sistema.
- Ingeniería de detalle: en la fase de ingeniería de detalle es probable que el diseño se congele con cambios mínimos. Un estudio RAM en este punto permitiría al cliente identificar los objetivos de rendimiento que debe cumplir el equipo, que pueden utilizarse como parte de la especificación de diseño del equipo durante la adquisición.
- Funcionamiento del proceso: mientras el proceso está en funcionamiento, la realización de un estudio RAM utilizando los datos de la instalación tal y como se construyó puede aportar la ventaja de identificar los equipos poco fiables que están provocando pérdidas de producción.
- DTI.
- Lista de equipos.
- Configuración de los equipos.
- Descripción de los modos de funcionamiento.
- Filosofía de mantenimiento.
Dinos qué te ha parecido el artículo
Artículos recomendados
Proceso de evaporación de petróleo y sus derivados en tanques de almacenamiento

Autor: Predictiva 21La revista digital de Mantenimiento, Confiabilidad y Gestión de Activos.
Evaluación de la confiabilidad de los sistemas de energía eléctrica utilizando métodos de Monte Carlo (Física de sólidos y líquidos)

Autor: Predictiva 21La revista digital de Mantenimiento, Confiabilidad y Gestión de Activos.
Análisis Weibull: Ejemplos Básicos de como usarlo para los Análisis de Confiabilidad

Autor: Arquimedes Ferrera MartínezSenior Reliability Engineer
Entrevista a Gerardo Trujillo: Avanzando hacia el Futuro

Autor: Predictiva 21La revista digital de Mantenimiento, Confiabilidad y Gestión de Activos.
Publica tu artículo en la revista #1 de Mantenimiento Industrial
Publicar un artículo en la revista es gratis, no tiene costo.
Solo debes asegurarte que no sea un artículo comercial.
¿Qué esperas?
O envía tu artículo directo: articulos@predictiva21.com
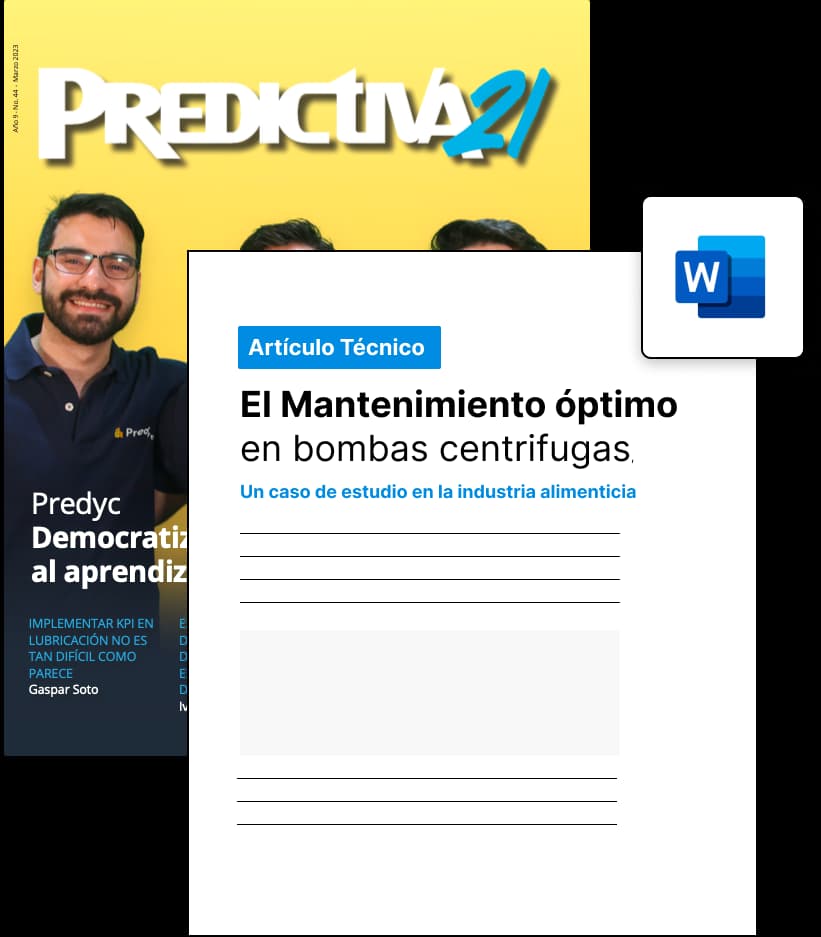