Análisis RAM como Herramienta para la Gestión de Activos Físicos: Caso de Aplicación Industrial
Articulo10 de junio de 2019
La dinámica empresarial actual, exige que los procesos en la industria sean optimizados desde el punto de vista técnico y económico. Es por esta razón, que surge la necesidad de la adopción de un sistema de gestión de activos tal como lo establece la norma ISO 55000, de manera que las organizaciones logren sus objetivos de manera efectiva, eficiente y sostenible en el tiempo.
En este sentido el marco de Normas ISO 55000/01/02-2014 establece que la organización debe desarrollar un Plan Estratégico de Gestión de Activos (PEGA o SAMP por sus siglas inglés) a partir de los objetivos organizacionales, con el propósito de documentar el rol del sistema de gestión de activos para alcanzar los objetivos de la gestión de activos.
Para el desarrollo del Plan Estratégico de Gestión de Activos (PEGA), es necesario obtener toda la información referente a la clase de activo; tal como la criticidad, el valor de los activos y la interdependencia con otros activos de la organización para la entrega de valor.
De allí que la gestión de activos este estrechamente relacionada con la Ingeniería de Confiabilidad, y se apoye en metodologías como Análisis RAM, dado que esta pretende pronosticar el comportamiento de un activo o conjunto de activos durante un periodo de tiempo determinado, siendo esta una información de gran valía para la definición de los objetivos de la gestión de activos y posterior desarrollo de los planes.
El Análisis RAM, permite conocer con cierto grado de certeza el factor de servicio de la instalación y los activos que tienen mayor aporte a la indisponibilidad a través del uso de la probabilidad y estadística y de diagramas de bloques de confiabilidad, pudiendo ser aplicado a cualquier tipo de industria.
Para el caso del presente trabajo se presenta la aplicación de la metodología Análisis RAM en una instalación industrial compleja, cuyos resultados sirven como información base para la elaboración de los planes de gestión de activos de la organización, permitiendo identificar los "cuellos de botella" en el sistema productivo y sirviendo de apoyo a la toma de decisión para la efectiva distribución de los recursos de operación y mantenimiento.
Metodología análisis RAM
El análisis RAM es una metodología que diagnostica el estado actual de un sistema productivo, y pronostica su comportamiento en un periodo determinado de tiempo (Díaz, 2014). Además permite definir cuantitativamente:
- La Disponibilidad y confiabilidad del sistema.
- Las pérdidas de producción por indisponibilidad del proceso productivo.
- El impacto en la disponibilidad del sistema debido a:La política de aprovisionamiento de partes y repuestos.
- La política de mantenimiento.
- La logística e Impacto por redundancia.
La aplicación de un análisis RAM permite determinar los activos que tienen mayor influencia en los indicadores de disponibilidad y confiabilidad en un sistema productivo. La figura 1, sintetiza gráficamente las etapas de implementación de un Análisis RAM:

Análisis de los datos de falla y reparación
El análisis RAM, se inicia con el análisis de los datos de tiempo de falla y reparación de cada uno de los activos que forman parte del sistema o proceso estudiado para la estimación probabilística de la tasa de falla y reparación.
Un resumen de las fuentes de información que se emplean en los estudios RAM se muestra en la figura 2, y el detalle del uso de las mismas se sugiere revisar el artículo de Díaz (2014).

En los estudios RAM y específicamente en el caso de aplicación de este artículo, la obtención de los datos de fallas y reparación en una organización es un verdadero desafío, debido a la falta de cultura del dato, evidenciándose en la inconsistencia en el registro de los mismos.
Por tal razón, y afín de garantizar que los datos representen la realidad operacional de la instalación, se acude al uso de la opinión de un grupo de expertos de la organización, conformado principalmente por personal del área operacional y mantenimiento, siguiendo los siguientes pasos:
- Definición del Grupo de Especialistas que participarán en las reuniones de trabajo.
- Ponderación de la opinión de los expertos.
- Agrupación por familias de equipos en base a la información suministrada por los expertos, considerando: las características de operación, mantenimiento y el contexto operacional de los equipos.
- Elicitación de los valores de las variables Tiempos Entre Fallas (TEF) y Tiempos para Reparar (TPR) para los escenarios: optimista, pesimista y más probable (mínimo, máximo y más probable).
A partir de estos datos recopilados, se hace uso de herramientas estadísticas conocidas como Distribuciones de Probabilidad, con el n de modelar el comportamiento de los Tiempos de Falla y Tiempos de reparación desde el punto de vista matemático.
Es importante destacar, que para el caso de los equipos donde no se tenga información de los expertos por diferentes razones, se recurre al uso de bases de datos genéricas disponibles OREDA, IEEE, CCPS, entre otras.
En la tabla 1 se presentan las Distribuciones utilizadas para la modelación probabilística de los Tiempos de Fallas y Tiempos de Reparación de los equipos de la instalación:

Modelación del Sistema Productivo
La modelación del proceso productivo inicia con la construcción de los Diagramas de Bloques de Confiabilidad (DBC) de la instalación analizada (ver figura 3). Para ello es necesario definir los límites de cada uno de los sistemas, subsistemas, equipos y componentes que intervienen en el sistema productivo y que tienen impacto en la disponibilidad del mismo causando pérdidas en producción.

Para el caso de la industria petrolera y gasífera, la norma ISO 14224, define los límites de batería y estructura sistemáticamente cada uno de los equipos principales utilizados en esa rama de la industria. Para el caso de otras industrias, se puede tomar como base los criterios del estándar citado anteriormente y adaptarlo a la realidad operacional del sistema productivo analizado.
Para la elaboración de los DBC de la aplicación, se revisaron exhaustivamente toda la información técnica inherente al proceso (Diagrama de tubería e instrumentación, diagrama de flujo de proceso, entre otros).
En total se modelaron aproximadamente 1100 equipos de la instalación, distribuidos en 3 unidades y 2 sub-unidades con su porcentaje de afectación al negocio en caso de falla (ver figura 4).

Del DBC de la figura 4, se evidencia que:
- Unidad 1: La instalación dejará de cumplir su función por completo.
- Unidad 2: La instalación operará a un 80% de su capacidad con un 20% de impacto en caso de una falla funcional.
- Unidad 3: La Sub-Unidad A y B son necesarias para operar al 100%.En caso de una falla funcional de la Sub-Unidad A la unidad 3 operará a un 50%.
- En caso de una falla funcional de la Sub-Unidad B la unidad 3 operará a un 70%.
- La disponibilidad total de la instalación, será el producto de las tres unidades.
Es importante destacar, que los arreglos y escenarios de falla y reparación de cada uno de las unidades de la instalación son desarrollados en los diagramas de bloques de confiabilidad respectivos, considerando su filosofía, contexto operacional e interdependencia de los activos.
El modelo desarrollado debe ser validado por expertos en el área de producción y por personal que interviene diariamente en la operación y mantenimiento del sistema productivo. Por tal razón, en sistemas complejos es muy común el uso de funciones lógicas con el fin de modelar y simular el comportamiento real de la instalación.
Simulación del modelo
Una vez modelado el sistema productivo, se procede a realizar la simulación. Para esto es necesario definir el periodo de tiempo en el cual se desea simular el comportamiento del sistema, puesto que las condiciones de operación y mantenimiento dependen de las distribuciones de probabilidad de cada bloque y esta a su vez de la variable tiempo.
En este sentido, y para disminuir la incertidumbre en este tipo de estudios, es necesario hacer uso de del Método de Montecarlo, para obtener los distintos resultados posibles del modelo RAM. Es por esta razón, que para el modelaje de sistemas complejos se recurre al uso de programas computacionales (tales como: MAROS, RAPTOR, RAMP, TITAN entre otros), debido a que es necesario repetir varias veces una simulación del sistema con el mismo valor de tiempo analizado, para obtener los distintos escenarios de comportamiento posible y dar confianza estadística a los valores calculados.
Para el caso de la aplicación práctica, se realizó un pronóstico de la disponibilidad para los próximos 10 años de operación, realizando 3.000 iteraciones lo que permite mitigar el nivel de incertidumbre en el cálculo.
Por otra parte, a fin de estimar un valor de disponibilidad que se acerque más a la realidad, en el modelo RAM se consideraron paros no programados (debido a fallas, modelados a través de distribuciones de probabilidad) y paros programados (planes de mantenimiento típicos para cada tipo de activo y un paro general de planta para el año 2020 y el año 2024 de 40 días de duración.
Los resultados de disponibilidad de la instalación se presentan de manera acumulada y de manera anualizada para cada uno de los años pronosticados. Asimismo, se presentan los percentiles 5 (P5), 50 (P50) y 95 (P95) junto con la Desviación Estándar que son usados como parámetros para describir la distribución normal, siguiendo el Teorema del Límite Central.
De estos percentiles, se puede afirmar que existe un 90% de certeza que la disponibilidad se encontrará entre los valores del percentil 5 y 95, mientras que el valor que tiene mayor probabilidad de ocurrencia es el percentil 50, este valor también es conocido como media debido a la utilización de la distribución normal para modelar los resultados del modelo RAM.
Cursos recomendados


%252FImagen%252Frcm-1730083250826.webp%3Falt%3Dmedia%26token%3D3775356a-7b11-4c44-b21f-45b3409fb9ed&w=3840&q=75)

%252FImagen%252FRAMPREDYC-1730060420837.webp%3Falt%3Dmedia%26token%3D2634a7f0-988e-4022-b91f-382503e6e9db&w=3840&q=75)



Disponibilidad Acumulada
En la Tabla 2 se muestran los valores de Disponibilidad para el caso de aplicación práctica, y en la figura 5 se ilustra el perfil estocástico de estos valores a fin de mostrar gráficamente el cambio de la disponibilidad en función del tiempo.


Del perfil anterior, se puede evidenciar que la Disponibilidad Acumulada de la Instalación, tiene una tendencia hacía la baja. Es decir, bajo la política actual de mantenimiento y operaciones de la instalación, la rentabilidad y la productividad de la misma ira disminuyendo en función del tiempo.
Disponibilidad Anualizada
De igual forma, en la tabla 3 se presentan los valores de Disponibilidad Anualizados, a fin de mostrar el valor real del desempeño de la instalación año a año. Asimismo, en la figura 6 se grafican los cambios de la disponibilidad en función del tiempo.


De la tabla y la figura anterior, se evidencia que los valores de Disponibilidad anualizada entre las paradas programadas del año 2020 y 2024 tienden a la baja, pasando de un promedio de 78,44% en el año 2016 hasta 56,50% del año 2020; y de 83,33% de promedio del año 2021 a 49,84% del año 2024.
Esto concuerda con los resultados de la disponibilidad acumulada, donde los valores de disponibilidad tienden a disminuir en función del tiempo, siendo dominante la tendencia bajista. Otra forma de representar los resultados de disponibilidad anualizada de la instalación, es a través de un gráfico de superposición. Este permite verificar los valores de disponibilidad más probables año a año, y en que rango se encuentra la mayor agrupación de estos. El mismo se presenta en la figura 7.

Jerarquización de criticidad de los activos
Una de las ventajas de realizar un Análisis RAM a sistemas e instalaciones complejas, es que del mismo se puede obtener una lista jerarquizada de los activos que tienen mayor aporte a la indisponibilidad del sistema y su afectación al sistema de producción.
Para el caso particular del ejemplo de la instalación analizada, los resultados de la simulación evidencian una tendencia bajista de los valores de la disponibilidad en función del tiempo. De ahí que a partir de estos resultados, se hace necesario identificar oportunidades que apunten a disminuir el riesgo y aumentar la disponibilidad de la instalación, por lo que se procede a analizar los activos físicos que influyen en la indisponibilidad.
Por tal razón, se verifica en primer lugar cuantos activos tienen un aporte a la indisponibilidad del universo total de equipos de la instalación, y posteriormente se elabora una lista jerarquizada para conocer los activos críticos del sistema y dirigir en ellos las acciones, estrategias y recursos con el objetivo de obtener un mayor rendimiento del sistema productivo (Díaz, 2014). Del gráfico de la figura 8, se tiene que sólo el 28% de los equipos del universo total de instalación, tienen un aporte a la indisponibilidad en caso de fallas. Es decir sólo 308 de los 1100 equipos totales tienen un impacto real en el negocio.

De igual manera, la jerarquización de los activos, se presentan en la siguiente tabla:

Resultados del análisis RAM y su relación con la gestión de activos
Los resultados de la simulación del modelo RAM permiten a la organización:
- Identificar los equipos críticos y los “cuellos de botella” de la instalación.
- Evaluar los perfiles de demanda del producto.
- Verificar del cumplimiento de la función de los activos y volumen de producción.
Con esta información, la organización podrá generar objetivos de la gestión de activos como elementos fundamentales del Plan Estratégico de Gestión de Activos (PEGA), tal como lo establece la norma (ISO 55001:2014) en el requerimiento 6.2.1. Objetivos de la gestión de activos. “La organización debe establecer objetivos de gestión de activos en las funciones y niveles pertinentes, documentarse y actualizarse como parte del PEGA”.
Algunos objetivos de Gestión Activos que se derivan luego de la aplicación del Análisis RAM en la instalación analizada podrían ser:
- Aumentar la capacidad de producción de la instalación de 15 mil barriles de producto diarios a 17,6 mil barriles diarios durante el 2017.
- Incrementar la disponibilidad de la instalación en un 5% al pasar de 75,21% a 80,21% en el 2017.
- Recopilar los tiempos de falla y de reparación de los activos.
Lárez (2016) señala, que estos objetivos reflejan los resultados que la gestión de activos debe producir a la organización. Por lo tanto, necesitan ser apoyados con acciones de muy alto nivel, que algunas organizaciones suelen llamar acciones estratégicas (El-Akruti, Dwight, & Zhang, 2013). Estas acciones estratégicas deben estar acompañadas con los recursos adecuados, plazos de tiempos de- nidos, metas a lograr y el seguimiento respectivo (Henderson, 2014). Las iniciativas de alto nivel, sin embargo, podrían ser implementadas como proyectos en niveles inferiores de servicio con sus respectivos objetivos al detalle, de tal manera que puedan alinearse con planes de inferior nivel (Deix, 2012). Por lo tanto, siguiendo las ideas de Lárez (2016), es útil compartir algunos objetivos de nivel inferior que se alinean con los objetivos estratégicos de nidos anteriormente:
- Colocar en servicio el segundo Compresor de Baja Presión, y adoptar nuevamente la filosofía de operación 1 de 2.
- Colocar en servicio de un Compresor de Alta Presión del Sistema de Inyección de Gas, durante el primer trimestre del año 2017.
- Para incrementar en un 5% la disponibilidad de la instalación:Instalar una Bomba de Despacho de Producto adicional, para obtener mayor flexibilidad operacional para mediados del 2017.
- Implementar herramientas de confiabilidad tales como Mantenimiento Centrado en Confiabilidad (MCC) y Análisis Causa Raíz (ACR) a los equipos más críticos de la lista jerarquizada.
- Implementar un sistema de gestión de mantenimiento asistido por computadora para los activos de la organización durante el año 2017.
Conclusiones
- La gestión de activos físicos está estrechamente relacionada con el RAM, puesto que esta metodología pretende pronosticar el comportamiento de un conjunto de activos durante un periodo de tiempo determinado, siendo esta una información de gran valía para la definición de los objetivos de la gestión de activos y posterior desarrollo del PEGA.
- El Análisis RAM, permite conocer con cierto grado de certeza el factor de servicio de la instalación y los activos que tienen mayor aporte a la indisponibilidad a través del uso de la probabilidad y estadística y de diagramas de bloques de confiabilidad.
- Los arreglos y escenarios de falla y reparación del Modelo RAM de una instalación son desarrollados en diagramas de bloques de confiabilidad, considerando la filosofía, contexto operacional, interdependencia de los activos y aspectos del proceso.
- Para mitigar la incertidumbre en este tipo de estudios, se hace uso del Método de Montecarlo, para obtener los distintos resultados posibles del modelo RAM.
- La jerarquización de activos, permite la identificación de los equipos y sistemas críticos de un sistema productivo. Con esto, la asignación de recursos y esfuerzos corporativos será asertiva, y disminuirá la ocurrencia de eventos no deseados que inciden en la productividad de la organización.
- Con la finalidad de definir estrategias que aseguren el cumplimiento de la función de los activos y que estos sean sostenibles en el tiempo, los objetivos de la gestión de activos deben contener un análisis a la indisponibilidad operacional del sistema productivo a través de otras metodologías de Ingeniería de Confiabilidad.
Referencias
- Calixto, Eduardo. Gas and Oil Reliability Engineering. Modeling and Analysis. (2013). Editorial: Gulf Professional Publishing.
- Deix, S. A., Karoline and Weninger-Vycudil, Alfred. Procedures for Cross Asset Management Optimisation (2012). Procedia - Social and Behavioral Sciences, 48, 2022-2028.
- Díaz, Osberto. Modelación de Sistemas Productivos Complejos a Través del Análisis RAM. (2014). Artículo Presentado en el Congreso Latinoamericano de Gerencia de Activos 2014.
- El-Akruti, K., Dwight, R., & Zhang, T. The strategic role of Engineering Asset Management (2013). International Journal of Production Economics, 146(1), 227-239.
- Henderson, K. P., Georg; Kraska, Olaf. Integrated Asset Management – An Investment in Sustainability (2014). Proc. Engineering, 83, 448-454.
Dinos qué te ha parecido el artículo
Artículos recomendados
El mantenimiento preventivo como cultura de trabajo

Python, una Herramienta de Ingeniería y Confiabilidad

Comunicación y Confiabilidad Humana

La Gestión del Conocimiento como parte de la Gestión de Activos

Publica tu artículo en la revista #1 de Mantenimiento Industrial
Publicar un artículo en la revista es gratis, no tiene costo.
Solo debes asegurarte que no sea un artículo comercial.
¿Qué esperas?
O envía tu artículo directo: articulos@predictiva21.com
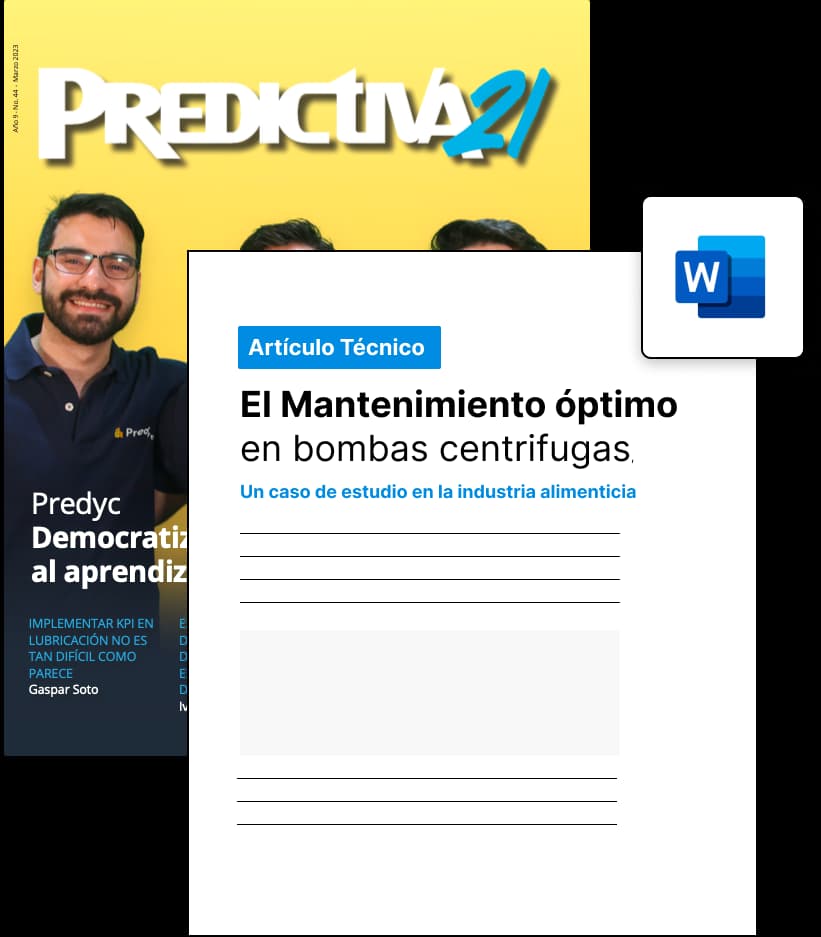
Análisis RAM como Herramienta para la Gestión de Activos Físicos: Caso de Aplicación Industrial
Articulo 10 de junio de 2019La dinámica empresarial actual, exige que los procesos en la industria sean optimizados desde el punto de vista técnico y económico. Es por esta razón, que surge la necesidad de la adopción de un sistema de gestión de activos tal como lo establece la norma ISO 55000, de manera que las organizaciones logren sus objetivos de manera efectiva, eficiente y sostenible en el tiempo.
En este sentido el marco de Normas ISO 55000/01/02-2014 establece que la organización debe desarrollar un Plan Estratégico de Gestión de Activos (PEGA o SAMP por sus siglas inglés) a partir de los objetivos organizacionales, con el propósito de documentar el rol del sistema de gestión de activos para alcanzar los objetivos de la gestión de activos.
Para el desarrollo del Plan Estratégico de Gestión de Activos (PEGA), es necesario obtener toda la información referente a la clase de activo; tal como la criticidad, el valor de los activos y la interdependencia con otros activos de la organización para la entrega de valor.
De allí que la gestión de activos este estrechamente relacionada con la Ingeniería de Confiabilidad, y se apoye en metodologías como Análisis RAM, dado que esta pretende pronosticar el comportamiento de un activo o conjunto de activos durante un periodo de tiempo determinado, siendo esta una información de gran valía para la definición de los objetivos de la gestión de activos y posterior desarrollo de los planes.
El Análisis RAM, permite conocer con cierto grado de certeza el factor de servicio de la instalación y los activos que tienen mayor aporte a la indisponibilidad a través del uso de la probabilidad y estadística y de diagramas de bloques de confiabilidad, pudiendo ser aplicado a cualquier tipo de industria.
Para el caso del presente trabajo se presenta la aplicación de la metodología Análisis RAM en una instalación industrial compleja, cuyos resultados sirven como información base para la elaboración de los planes de gestión de activos de la organización, permitiendo identificar los "cuellos de botella" en el sistema productivo y sirviendo de apoyo a la toma de decisión para la efectiva distribución de los recursos de operación y mantenimiento.
Metodología análisis RAM
El análisis RAM es una metodología que diagnostica el estado actual de un sistema productivo, y pronostica su comportamiento en un periodo determinado de tiempo (Díaz, 2014). Además permite definir cuantitativamente:
- La Disponibilidad y confiabilidad del sistema.
- Las pérdidas de producción por indisponibilidad del proceso productivo.
- El impacto en la disponibilidad del sistema debido a:La política de aprovisionamiento de partes y repuestos.
- La política de mantenimiento.
- La logística e Impacto por redundancia.
La aplicación de un análisis RAM permite determinar los activos que tienen mayor influencia en los indicadores de disponibilidad y confiabilidad en un sistema productivo. La figura 1, sintetiza gráficamente las etapas de implementación de un Análisis RAM:

Análisis de los datos de falla y reparación
El análisis RAM, se inicia con el análisis de los datos de tiempo de falla y reparación de cada uno de los activos que forman parte del sistema o proceso estudiado para la estimación probabilística de la tasa de falla y reparación.
Un resumen de las fuentes de información que se emplean en los estudios RAM se muestra en la figura 2, y el detalle del uso de las mismas se sugiere revisar el artículo de Díaz (2014).

En los estudios RAM y específicamente en el caso de aplicación de este artículo, la obtención de los datos de fallas y reparación en una organización es un verdadero desafío, debido a la falta de cultura del dato, evidenciándose en la inconsistencia en el registro de los mismos.
Por tal razón, y afín de garantizar que los datos representen la realidad operacional de la instalación, se acude al uso de la opinión de un grupo de expertos de la organización, conformado principalmente por personal del área operacional y mantenimiento, siguiendo los siguientes pasos:
- Definición del Grupo de Especialistas que participarán en las reuniones de trabajo.
- Ponderación de la opinión de los expertos.
- Agrupación por familias de equipos en base a la información suministrada por los expertos, considerando: las características de operación, mantenimiento y el contexto operacional de los equipos.
- Elicitación de los valores de las variables Tiempos Entre Fallas (TEF) y Tiempos para Reparar (TPR) para los escenarios: optimista, pesimista y más probable (mínimo, máximo y más probable).
A partir de estos datos recopilados, se hace uso de herramientas estadísticas conocidas como Distribuciones de Probabilidad, con el n de modelar el comportamiento de los Tiempos de Falla y Tiempos de reparación desde el punto de vista matemático.
Es importante destacar, que para el caso de los equipos donde no se tenga información de los expertos por diferentes razones, se recurre al uso de bases de datos genéricas disponibles OREDA, IEEE, CCPS, entre otras.
En la tabla 1 se presentan las Distribuciones utilizadas para la modelación probabilística de los Tiempos de Fallas y Tiempos de Reparación de los equipos de la instalación:

Modelación del Sistema Productivo
La modelación del proceso productivo inicia con la construcción de los Diagramas de Bloques de Confiabilidad (DBC) de la instalación analizada (ver figura 3). Para ello es necesario definir los límites de cada uno de los sistemas, subsistemas, equipos y componentes que intervienen en el sistema productivo y que tienen impacto en la disponibilidad del mismo causando pérdidas en producción.

Para el caso de la industria petrolera y gasífera, la norma ISO 14224, define los límites de batería y estructura sistemáticamente cada uno de los equipos principales utilizados en esa rama de la industria. Para el caso de otras industrias, se puede tomar como base los criterios del estándar citado anteriormente y adaptarlo a la realidad operacional del sistema productivo analizado.
Para la elaboración de los DBC de la aplicación, se revisaron exhaustivamente toda la información técnica inherente al proceso (Diagrama de tubería e instrumentación, diagrama de flujo de proceso, entre otros).
En total se modelaron aproximadamente 1100 equipos de la instalación, distribuidos en 3 unidades y 2 sub-unidades con su porcentaje de afectación al negocio en caso de falla (ver figura 4).

Del DBC de la figura 4, se evidencia que:
- Unidad 1: La instalación dejará de cumplir su función por completo.
- Unidad 2: La instalación operará a un 80% de su capacidad con un 20% de impacto en caso de una falla funcional.
- Unidad 3: La Sub-Unidad A y B son necesarias para operar al 100%.En caso de una falla funcional de la Sub-Unidad A la unidad 3 operará a un 50%.
- En caso de una falla funcional de la Sub-Unidad B la unidad 3 operará a un 70%.
- La disponibilidad total de la instalación, será el producto de las tres unidades.
Es importante destacar, que los arreglos y escenarios de falla y reparación de cada uno de las unidades de la instalación son desarrollados en los diagramas de bloques de confiabilidad respectivos, considerando su filosofía, contexto operacional e interdependencia de los activos.
El modelo desarrollado debe ser validado por expertos en el área de producción y por personal que interviene diariamente en la operación y mantenimiento del sistema productivo. Por tal razón, en sistemas complejos es muy común el uso de funciones lógicas con el fin de modelar y simular el comportamiento real de la instalación.
Simulación del modelo
Una vez modelado el sistema productivo, se procede a realizar la simulación. Para esto es necesario definir el periodo de tiempo en el cual se desea simular el comportamiento del sistema, puesto que las condiciones de operación y mantenimiento dependen de las distribuciones de probabilidad de cada bloque y esta a su vez de la variable tiempo.
En este sentido, y para disminuir la incertidumbre en este tipo de estudios, es necesario hacer uso de del Método de Montecarlo, para obtener los distintos resultados posibles del modelo RAM. Es por esta razón, que para el modelaje de sistemas complejos se recurre al uso de programas computacionales (tales como: MAROS, RAPTOR, RAMP, TITAN entre otros), debido a que es necesario repetir varias veces una simulación del sistema con el mismo valor de tiempo analizado, para obtener los distintos escenarios de comportamiento posible y dar confianza estadística a los valores calculados.
Para el caso de la aplicación práctica, se realizó un pronóstico de la disponibilidad para los próximos 10 años de operación, realizando 3.000 iteraciones lo que permite mitigar el nivel de incertidumbre en el cálculo.
Por otra parte, a fin de estimar un valor de disponibilidad que se acerque más a la realidad, en el modelo RAM se consideraron paros no programados (debido a fallas, modelados a través de distribuciones de probabilidad) y paros programados (planes de mantenimiento típicos para cada tipo de activo y un paro general de planta para el año 2020 y el año 2024 de 40 días de duración.
Los resultados de disponibilidad de la instalación se presentan de manera acumulada y de manera anualizada para cada uno de los años pronosticados. Asimismo, se presentan los percentiles 5 (P5), 50 (P50) y 95 (P95) junto con la Desviación Estándar que son usados como parámetros para describir la distribución normal, siguiendo el Teorema del Límite Central.
De estos percentiles, se puede afirmar que existe un 90% de certeza que la disponibilidad se encontrará entre los valores del percentil 5 y 95, mientras que el valor que tiene mayor probabilidad de ocurrencia es el percentil 50, este valor también es conocido como media debido a la utilización de la distribución normal para modelar los resultados del modelo RAM.
Cursos recomendados


%252FImagen%252Frcm-1730083250826.webp%3Falt%3Dmedia%26token%3D3775356a-7b11-4c44-b21f-45b3409fb9ed&w=3840&q=75)

%252FImagen%252FRAMPREDYC-1730060420837.webp%3Falt%3Dmedia%26token%3D2634a7f0-988e-4022-b91f-382503e6e9db&w=3840&q=75)



Disponibilidad Acumulada
En la Tabla 2 se muestran los valores de Disponibilidad para el caso de aplicación práctica, y en la figura 5 se ilustra el perfil estocástico de estos valores a fin de mostrar gráficamente el cambio de la disponibilidad en función del tiempo.


Del perfil anterior, se puede evidenciar que la Disponibilidad Acumulada de la Instalación, tiene una tendencia hacía la baja. Es decir, bajo la política actual de mantenimiento y operaciones de la instalación, la rentabilidad y la productividad de la misma ira disminuyendo en función del tiempo.
Disponibilidad Anualizada
De igual forma, en la tabla 3 se presentan los valores de Disponibilidad Anualizados, a fin de mostrar el valor real del desempeño de la instalación año a año. Asimismo, en la figura 6 se grafican los cambios de la disponibilidad en función del tiempo.


De la tabla y la figura anterior, se evidencia que los valores de Disponibilidad anualizada entre las paradas programadas del año 2020 y 2024 tienden a la baja, pasando de un promedio de 78,44% en el año 2016 hasta 56,50% del año 2020; y de 83,33% de promedio del año 2021 a 49,84% del año 2024.
Esto concuerda con los resultados de la disponibilidad acumulada, donde los valores de disponibilidad tienden a disminuir en función del tiempo, siendo dominante la tendencia bajista. Otra forma de representar los resultados de disponibilidad anualizada de la instalación, es a través de un gráfico de superposición. Este permite verificar los valores de disponibilidad más probables año a año, y en que rango se encuentra la mayor agrupación de estos. El mismo se presenta en la figura 7.

Jerarquización de criticidad de los activos
Una de las ventajas de realizar un Análisis RAM a sistemas e instalaciones complejas, es que del mismo se puede obtener una lista jerarquizada de los activos que tienen mayor aporte a la indisponibilidad del sistema y su afectación al sistema de producción.
Para el caso particular del ejemplo de la instalación analizada, los resultados de la simulación evidencian una tendencia bajista de los valores de la disponibilidad en función del tiempo. De ahí que a partir de estos resultados, se hace necesario identificar oportunidades que apunten a disminuir el riesgo y aumentar la disponibilidad de la instalación, por lo que se procede a analizar los activos físicos que influyen en la indisponibilidad.
Por tal razón, se verifica en primer lugar cuantos activos tienen un aporte a la indisponibilidad del universo total de equipos de la instalación, y posteriormente se elabora una lista jerarquizada para conocer los activos críticos del sistema y dirigir en ellos las acciones, estrategias y recursos con el objetivo de obtener un mayor rendimiento del sistema productivo (Díaz, 2014). Del gráfico de la figura 8, se tiene que sólo el 28% de los equipos del universo total de instalación, tienen un aporte a la indisponibilidad en caso de fallas. Es decir sólo 308 de los 1100 equipos totales tienen un impacto real en el negocio.

De igual manera, la jerarquización de los activos, se presentan en la siguiente tabla:

Resultados del análisis RAM y su relación con la gestión de activos
Los resultados de la simulación del modelo RAM permiten a la organización:
- Identificar los equipos críticos y los “cuellos de botella” de la instalación.
- Evaluar los perfiles de demanda del producto.
- Verificar del cumplimiento de la función de los activos y volumen de producción.
Con esta información, la organización podrá generar objetivos de la gestión de activos como elementos fundamentales del Plan Estratégico de Gestión de Activos (PEGA), tal como lo establece la norma (ISO 55001:2014) en el requerimiento 6.2.1. Objetivos de la gestión de activos. “La organización debe establecer objetivos de gestión de activos en las funciones y niveles pertinentes, documentarse y actualizarse como parte del PEGA”.
Algunos objetivos de Gestión Activos que se derivan luego de la aplicación del Análisis RAM en la instalación analizada podrían ser:
- Aumentar la capacidad de producción de la instalación de 15 mil barriles de producto diarios a 17,6 mil barriles diarios durante el 2017.
- Incrementar la disponibilidad de la instalación en un 5% al pasar de 75,21% a 80,21% en el 2017.
- Recopilar los tiempos de falla y de reparación de los activos.
Lárez (2016) señala, que estos objetivos reflejan los resultados que la gestión de activos debe producir a la organización. Por lo tanto, necesitan ser apoyados con acciones de muy alto nivel, que algunas organizaciones suelen llamar acciones estratégicas (El-Akruti, Dwight, & Zhang, 2013). Estas acciones estratégicas deben estar acompañadas con los recursos adecuados, plazos de tiempos de- nidos, metas a lograr y el seguimiento respectivo (Henderson, 2014). Las iniciativas de alto nivel, sin embargo, podrían ser implementadas como proyectos en niveles inferiores de servicio con sus respectivos objetivos al detalle, de tal manera que puedan alinearse con planes de inferior nivel (Deix, 2012). Por lo tanto, siguiendo las ideas de Lárez (2016), es útil compartir algunos objetivos de nivel inferior que se alinean con los objetivos estratégicos de nidos anteriormente:
- Colocar en servicio el segundo Compresor de Baja Presión, y adoptar nuevamente la filosofía de operación 1 de 2.
- Colocar en servicio de un Compresor de Alta Presión del Sistema de Inyección de Gas, durante el primer trimestre del año 2017.
- Para incrementar en un 5% la disponibilidad de la instalación:Instalar una Bomba de Despacho de Producto adicional, para obtener mayor flexibilidad operacional para mediados del 2017.
- Implementar herramientas de confiabilidad tales como Mantenimiento Centrado en Confiabilidad (MCC) y Análisis Causa Raíz (ACR) a los equipos más críticos de la lista jerarquizada.
- Implementar un sistema de gestión de mantenimiento asistido por computadora para los activos de la organización durante el año 2017.
Conclusiones
- La gestión de activos físicos está estrechamente relacionada con el RAM, puesto que esta metodología pretende pronosticar el comportamiento de un conjunto de activos durante un periodo de tiempo determinado, siendo esta una información de gran valía para la definición de los objetivos de la gestión de activos y posterior desarrollo del PEGA.
- El Análisis RAM, permite conocer con cierto grado de certeza el factor de servicio de la instalación y los activos que tienen mayor aporte a la indisponibilidad a través del uso de la probabilidad y estadística y de diagramas de bloques de confiabilidad.
- Los arreglos y escenarios de falla y reparación del Modelo RAM de una instalación son desarrollados en diagramas de bloques de confiabilidad, considerando la filosofía, contexto operacional, interdependencia de los activos y aspectos del proceso.
- Para mitigar la incertidumbre en este tipo de estudios, se hace uso del Método de Montecarlo, para obtener los distintos resultados posibles del modelo RAM.
- La jerarquización de activos, permite la identificación de los equipos y sistemas críticos de un sistema productivo. Con esto, la asignación de recursos y esfuerzos corporativos será asertiva, y disminuirá la ocurrencia de eventos no deseados que inciden en la productividad de la organización.
- Con la finalidad de definir estrategias que aseguren el cumplimiento de la función de los activos y que estos sean sostenibles en el tiempo, los objetivos de la gestión de activos deben contener un análisis a la indisponibilidad operacional del sistema productivo a través de otras metodologías de Ingeniería de Confiabilidad.
Referencias
- Calixto, Eduardo. Gas and Oil Reliability Engineering. Modeling and Analysis. (2013). Editorial: Gulf Professional Publishing.
- Deix, S. A., Karoline and Weninger-Vycudil, Alfred. Procedures for Cross Asset Management Optimisation (2012). Procedia - Social and Behavioral Sciences, 48, 2022-2028.
- Díaz, Osberto. Modelación de Sistemas Productivos Complejos a Través del Análisis RAM. (2014). Artículo Presentado en el Congreso Latinoamericano de Gerencia de Activos 2014.
- El-Akruti, K., Dwight, R., & Zhang, T. The strategic role of Engineering Asset Management (2013). International Journal of Production Economics, 146(1), 227-239.
- Henderson, K. P., Georg; Kraska, Olaf. Integrated Asset Management – An Investment in Sustainability (2014). Proc. Engineering, 83, 448-454.
Dinos qué te ha parecido el artículo
Artículos recomendados
Precursores de la ingeniería industrial

¿Cómo implementar de manera estratégica energías renovables en la Industria?

Bombas Centrífugas

Confiabilidad en la formación del recurso humano

Publica tu artículo en la revista #1 de Mantenimiento Industrial
Publicar un artículo en la revista es gratis, no tiene costo.
Solo debes asegurarte que no sea un artículo comercial.
¿Qué esperas?
O envía tu artículo directo: articulos@predictiva21.com
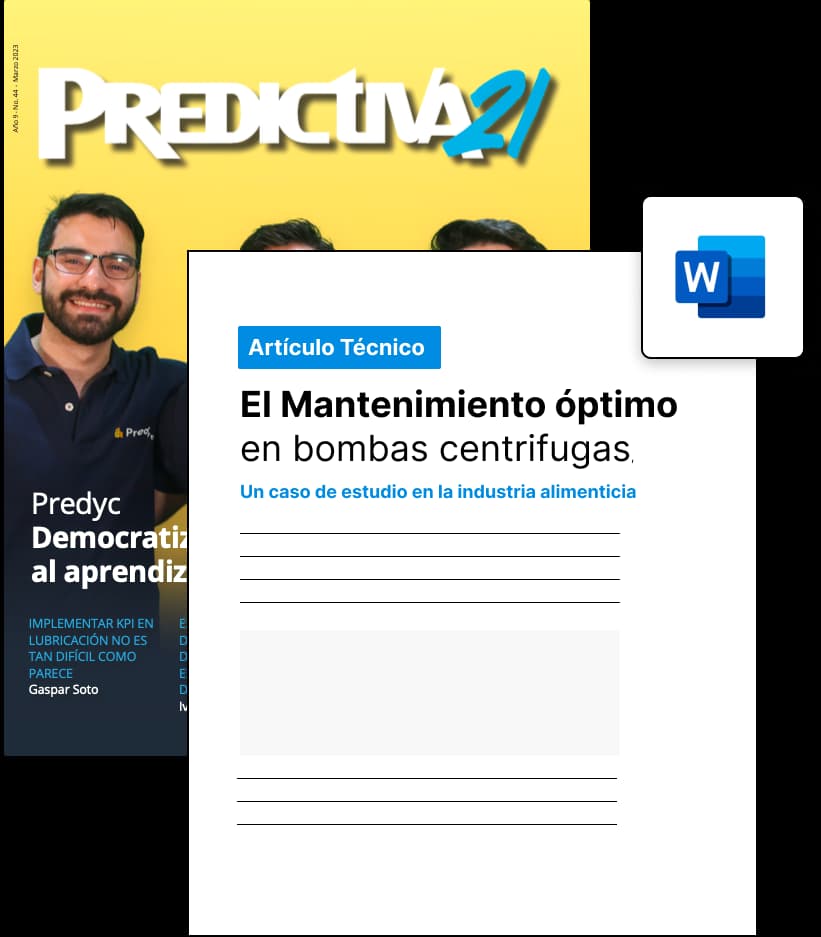