CMMS - GMAO: el futuro para el sector del mantenimiento
Articulo4 de mayo de 2023

La búsqueda de calidad y productividad ha llevado al sector del mantenimiento a convertirse en uno de los más importantes y estratégicos de la industria.
Mantener sus activos en óptimo funcionamiento es un factor crucial para alcanzar altas tasas de fiabilidad y disponibilidad. La operación de mantenimiento de cualquier industria requiere transformar su rutina de mantenimiento correctivo y predictivo, y apostar por tecnología que la lleven hacia la prescripción de fallas.
Las empresas manufactureras mundiales se ven obligadas a mejorar su rendimiento empresarial debido al aumento de la competitividad global (FERNANDEZ et al., 2003) en relación con los cambios del mercado.
Este aumento de la competitividad es una condición de supervivencia para las empresas, que exige, entre otras cosas, la búsqueda del máximo rendimiento financiero de los activos de las instalaciones industriales (BRANCO, 2008).
En este contexto, los sistemas de gestión de mantenimiento como CMMS (Sistema Informatizado de Gestión del Mantenimiento o Software de Mantenimiento) actúa como el puente entre máquinas, sistemas y personas a lo largo de la cadena de producción.
Una de las características principales de la Industria 4.0 es que permite tomar decisiones de forma autónoma a los departamentos de mantenimiento.
Esto aumenta la capacidad de las empresas para anticiparse a fallas, programar el mantenimiento y adaptarse a los cambios imprevistos, esenciales para lograr un mantenimiento de clase mundial.

¿Qué es un CMMS y cómo funciona?
Los sistemas CMMS o GMAO son plataformas que integran en un mismo lugar las diferentes actividades de mantenimiento que requiere una planta industrial.
Con la integración de esta tecnología en la industria, es posible automatizar las operaciones y actividades de mantenimiento, además de armonizar operaciones esenciales como la planificación, control, desempeño operacional y productividad.
Entonces,¿cómo funciona un CMMS en la práctica?

Los sistemas tradicionales tienen dificultades para integrarse en la planificación del mantenimiento de una planta. Fallan, principalmente, en dos cosas: no ofrecen una visión general de la planta y utilizan códigos complicados que requieren ser memorizados.
La intención principal de un CMMS, más allá de las operaciones, es ayudar a los equipos de mantenimiento a gestionar sus flujos de trabajo y minimizar el tiempo de inactividad.
Melo y Silva (2017) dejan claro que el software no sustituye el trabajo humano, pero ayuda a determinar qué tareas están priorizadas correctamente y que todo está en su lugar (inventario, trabajo, etc.). Además, permite que el gestor y su equipo se centren más en el trabajo y menos en la parte burocrática.
El informe de McKinsey, "El estado de la industria 4.0”, señala que, para 2025, algunos procesos relacionados con la Industria 4.0 podrían reducir los costos de mantenimiento de los equipos entre un 10% y un 40%, reducir el consumo de energía entre un 10% y un 20%, y aumentar la eficiencia del trabajo entre un 10% y un 25%.
Así, el CMMS deja de ser únicamente un software, y se convierte en un pilar para la gestión de actividades.
Al fin y al cabo, nadie quiere verse sorprendido por problemas que podrían haberse evitado con una buena gestión, especialmente si el objetivo final es mantener un flujo eficiente en planta.
Las funcionalidades más básicas de cualquier CMMS o GMAO incluye el registro de activos y materiales, la gestión de órdenes de trabajo y el cálculo de KPI (Cabral, 2013; Cohen et al., 2014). El registro de activos contiene los equipos o instalaciones, incluyendo sus características, planes de mantenimiento preventivo, repuestos disponibles y ubicación.
Árbol de activos

Otro punto es que, al utilizarlo, las consultas sobre los principales indicadores de mantenimiento, rutas de planes de mantenimiento, gestión de inventarios, se vuelven más asertivas y eficientes.
Por ejemplo, si su plan de mantenimiento preventivo incluye varias tareas en motores eléctricos, como el cambio de aceite, basta crear una orden de trabajo, agregar los responsables, la periodicidad, describir el procedimiento a realizar, y listo.
Cuando el técnico termina la tarea, usted puede marcarla como "resuelta" y quitar una preocupación de su lista. Las acciones de mantenimiento pueden ser realizadas y seguidas en tiempo real y de forma precisa por los responsables del sector.
Con el uso adecuado de este recurso, obtienen:
- Mayor productividad del equipo de mantenimiento.
- Control asertivo del stock, planificación ideal de la adquisición de insumos y repuestos.
- Reducción del número de mantenimientos de último momento.
- Mayor aprovechamiento de los activos con generación de datos, monitoreo continuo de indicadores y definición de mejores prácticas.
- Datos históricos en un único lugar.
- Reducción del tiempo de inactividad de máquinas y profesionales.
- Aumento de la vida útil de máquinas y equipos.
- Calendario preventivo.
- Control y trazabilidad de las órdenes de trabajo.
Por lo tanto, con la rápida expansión y evolución de la tecnología en las industrias y en todo el mantenimiento, CMMS o GMAO puede ser considerado uno de los caminos para el futuro del mantenimiento.
Los softwares de gestión, creados por quien conoce las reales necesidades de la planta fabril, permiten hacer aún más en menos tiempo, garantizan aciertos, mayores resultados y una gestión dirigida a los datos.
El futuro del mantenimiento debe volcarse a una gestión que considere los datos, principalmente aquellos que indican los aciertos y los posibles errores del proceso, abriendo puertas para correcciones, reducción de costos y garantía de economía de toda la planta.
En suma: crean nuevas posibilidades y aumenta la eficiencia y productividad de los equipos.
Referencias Bibliográficas
BRANCO, F. G. A organização, o planejamento e o controle da manutenção. Rio de Janeiro: Ciência Moderna, 2008.
Cabral, J. P. S. (2013). Gestão da Manutenção de Equipamentos, Instalações e Edifícios (3.a ed.) Lidel - Edições Técnicas. Campbell, J., Jardine, A. K. S., & McGlynn, J. (2010). Excelencia en la gestión de activos: optimización de las decisiones sobre el ciclo de vida de los equipos. En Dekker Mechanical Engineering. https://doi.org/10.1016/S0952-1976(00)00012-9
FERNANDEZ, Oscar et al. A decision support maintenance management system. International Journal of Quality & Reliability Management, 2003
Dinos qué te ha parecido el artículo
Artículos recomendados
Gestión de Activos - ¿De qué estamos hablando en realidad?

Curso SAP

Control de Contaminación de Lubricantes y su Impacto en la Confiabilidad

Refinería Dos Bocas, una obra en medio de la polémica

Publica tu artículo en la revista #1 de Mantenimiento Industrial
Publicar un artículo en la revista es gratis, no tiene costo.
Solo debes asegurarte que no sea un artículo comercial.
¿Qué esperas?
O envía tu artículo directo: articulos@predictiva21.com
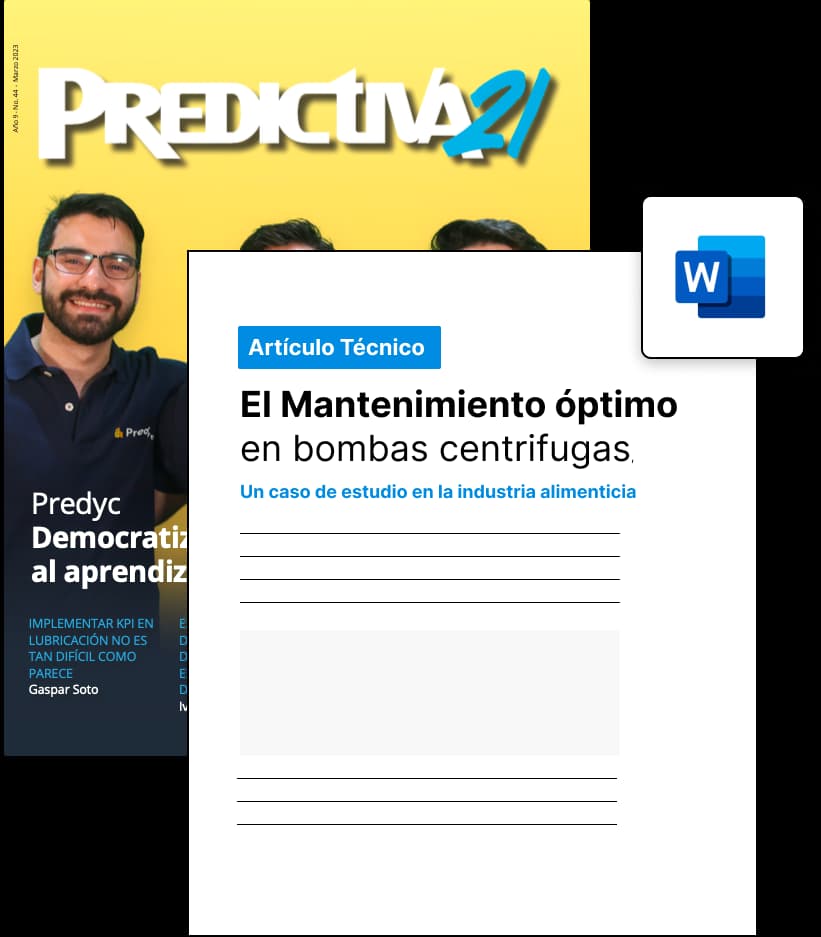
CMMS - GMAO: el futuro para el sector del mantenimiento
Articulo 4 de mayo de 2023
La búsqueda de calidad y productividad ha llevado al sector del mantenimiento a convertirse en uno de los más importantes y estratégicos de la industria.
Mantener sus activos en óptimo funcionamiento es un factor crucial para alcanzar altas tasas de fiabilidad y disponibilidad. La operación de mantenimiento de cualquier industria requiere transformar su rutina de mantenimiento correctivo y predictivo, y apostar por tecnología que la lleven hacia la prescripción de fallas.
Las empresas manufactureras mundiales se ven obligadas a mejorar su rendimiento empresarial debido al aumento de la competitividad global (FERNANDEZ et al., 2003) en relación con los cambios del mercado.
Este aumento de la competitividad es una condición de supervivencia para las empresas, que exige, entre otras cosas, la búsqueda del máximo rendimiento financiero de los activos de las instalaciones industriales (BRANCO, 2008).
En este contexto, los sistemas de gestión de mantenimiento como CMMS (Sistema Informatizado de Gestión del Mantenimiento o Software de Mantenimiento) actúa como el puente entre máquinas, sistemas y personas a lo largo de la cadena de producción.
Una de las características principales de la Industria 4.0 es que permite tomar decisiones de forma autónoma a los departamentos de mantenimiento.
Esto aumenta la capacidad de las empresas para anticiparse a fallas, programar el mantenimiento y adaptarse a los cambios imprevistos, esenciales para lograr un mantenimiento de clase mundial.

¿Qué es un CMMS y cómo funciona?
Los sistemas CMMS o GMAO son plataformas que integran en un mismo lugar las diferentes actividades de mantenimiento que requiere una planta industrial.
Con la integración de esta tecnología en la industria, es posible automatizar las operaciones y actividades de mantenimiento, además de armonizar operaciones esenciales como la planificación, control, desempeño operacional y productividad.
Entonces,¿cómo funciona un CMMS en la práctica?

Los sistemas tradicionales tienen dificultades para integrarse en la planificación del mantenimiento de una planta. Fallan, principalmente, en dos cosas: no ofrecen una visión general de la planta y utilizan códigos complicados que requieren ser memorizados.
La intención principal de un CMMS, más allá de las operaciones, es ayudar a los equipos de mantenimiento a gestionar sus flujos de trabajo y minimizar el tiempo de inactividad.
Melo y Silva (2017) dejan claro que el software no sustituye el trabajo humano, pero ayuda a determinar qué tareas están priorizadas correctamente y que todo está en su lugar (inventario, trabajo, etc.). Además, permite que el gestor y su equipo se centren más en el trabajo y menos en la parte burocrática.
El informe de McKinsey, "El estado de la industria 4.0”, señala que, para 2025, algunos procesos relacionados con la Industria 4.0 podrían reducir los costos de mantenimiento de los equipos entre un 10% y un 40%, reducir el consumo de energía entre un 10% y un 20%, y aumentar la eficiencia del trabajo entre un 10% y un 25%.
Así, el CMMS deja de ser únicamente un software, y se convierte en un pilar para la gestión de actividades.
Al fin y al cabo, nadie quiere verse sorprendido por problemas que podrían haberse evitado con una buena gestión, especialmente si el objetivo final es mantener un flujo eficiente en planta.
Las funcionalidades más básicas de cualquier CMMS o GMAO incluye el registro de activos y materiales, la gestión de órdenes de trabajo y el cálculo de KPI (Cabral, 2013; Cohen et al., 2014). El registro de activos contiene los equipos o instalaciones, incluyendo sus características, planes de mantenimiento preventivo, repuestos disponibles y ubicación.
Árbol de activos

Otro punto es que, al utilizarlo, las consultas sobre los principales indicadores de mantenimiento, rutas de planes de mantenimiento, gestión de inventarios, se vuelven más asertivas y eficientes.
Por ejemplo, si su plan de mantenimiento preventivo incluye varias tareas en motores eléctricos, como el cambio de aceite, basta crear una orden de trabajo, agregar los responsables, la periodicidad, describir el procedimiento a realizar, y listo.
Cuando el técnico termina la tarea, usted puede marcarla como "resuelta" y quitar una preocupación de su lista. Las acciones de mantenimiento pueden ser realizadas y seguidas en tiempo real y de forma precisa por los responsables del sector.
Con el uso adecuado de este recurso, obtienen:
- Mayor productividad del equipo de mantenimiento.
- Control asertivo del stock, planificación ideal de la adquisición de insumos y repuestos.
- Reducción del número de mantenimientos de último momento.
- Mayor aprovechamiento de los activos con generación de datos, monitoreo continuo de indicadores y definición de mejores prácticas.
- Datos históricos en un único lugar.
- Reducción del tiempo de inactividad de máquinas y profesionales.
- Aumento de la vida útil de máquinas y equipos.
- Calendario preventivo.
- Control y trazabilidad de las órdenes de trabajo.
Por lo tanto, con la rápida expansión y evolución de la tecnología en las industrias y en todo el mantenimiento, CMMS o GMAO puede ser considerado uno de los caminos para el futuro del mantenimiento.
Los softwares de gestión, creados por quien conoce las reales necesidades de la planta fabril, permiten hacer aún más en menos tiempo, garantizan aciertos, mayores resultados y una gestión dirigida a los datos.
El futuro del mantenimiento debe volcarse a una gestión que considere los datos, principalmente aquellos que indican los aciertos y los posibles errores del proceso, abriendo puertas para correcciones, reducción de costos y garantía de economía de toda la planta.
En suma: crean nuevas posibilidades y aumenta la eficiencia y productividad de los equipos.
Referencias Bibliográficas
BRANCO, F. G. A organização, o planejamento e o controle da manutenção. Rio de Janeiro: Ciência Moderna, 2008.
Cabral, J. P. S. (2013). Gestão da Manutenção de Equipamentos, Instalações e Edifícios (3.a ed.) Lidel - Edições Técnicas. Campbell, J., Jardine, A. K. S., & McGlynn, J. (2010). Excelencia en la gestión de activos: optimización de las decisiones sobre el ciclo de vida de los equipos. En Dekker Mechanical Engineering. https://doi.org/10.1016/S0952-1976(00)00012-9
FERNANDEZ, Oscar et al. A decision support maintenance management system. International Journal of Quality & Reliability Management, 2003
Dinos qué te ha parecido el artículo
Artículos recomendados
Análisis de Confiabilidad, Disponibilidad y Mantenibilidad de un Sistema de Bombeo

Lubricación de motores estacionarios a gas

Metodología Propuesta para Toma de Decisión de Inspección de Líneas de Flujo de Crudo Basado en Modelos Estadísticos de Criticidad

Vehículos eléctricos: descubre su mantenimiento y cómo funcionan

Publica tu artículo en la revista #1 de Mantenimiento Industrial
Publicar un artículo en la revista es gratis, no tiene costo.
Solo debes asegurarte que no sea un artículo comercial.
¿Qué esperas?
O envía tu artículo directo: articulos@predictiva21.com
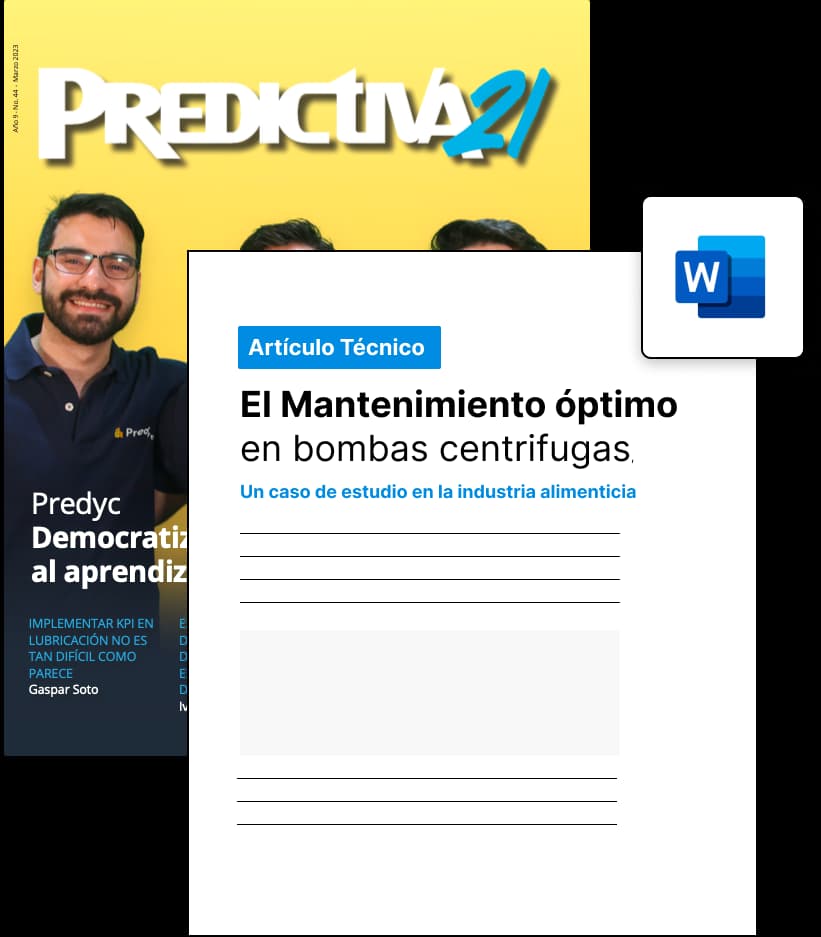