ESTUDIO DE LA VELOCIDAD DE CORROSIÓN EN EL PAR DE ACEROS ASTM-A36 Y AISI/SAE 304 EN UN SISTEMA AGUA-COQUE DE PETRÓLEO
Articulo29 de marzo de 2024
Palabras claves: Dupla metálica, gravimetría, vida útil.
RESUMEN
En la sinergia producida por la acción de los porcentajes de azufre, sodio, y demás elementos que componen
químicamente al coque de petróleo venezolano, en compañía de una proporción significativa de agua en dicha mezcla, genera un ambiente con índices corrosivos importantes para cualquier equipo metálico que tenga interacción con este, tanto en la industria petrolera como en cualquiera otra que use este combustible como producto o insumo en sus operaciones. En este trabajo se realizaron ensayos de laboratorio para determinar la velocidad de corrosión en un sistema conformado por el par metálico de acero estructural ASTM-A36 y el acero inoxidable AISI/SAE 304. El estudio se realizó mediante gravimetría, que es la metodología empleada frecuente para establecer valores de pérdida de masa en el tiempo, usando las normativas internacionales correspondientes, y así poder determinar el tiempo de vida útil de cualquier estructura de almacenamiento, expuestos a la corrosión generada por este ambiente
Keywords: Dupla metallic, gravimetry, service life.
ABSTRACT
A corrosive environment which can damage steel occurs as a result of the synergy produced by the action of the percentages of sulfur, sodium, and other elements present in the chemistry of Venezuelan petroleum coke when it is mixed with a significant proportion of water. This mixture which is very common in the petroleumcoke and oil industry, as well as in any other that uses this product as input fuel for their operations, accounts for a high percentage of material damage specially when there are couples of different materials joint together. In this work, laboratory tests were conducted to determine the corrosion rate in a system consisting of a metal couple made of ASTM-A36 structural steel and AISI / SAE 304 stainless steel, commonly found in the production of petroleum coke industry. The study was performed by gravity, which is the common methodology to establish mass loss values after a time exposure to an environment according to internationals standards, the service life of any structure exposed storage corrosion generated by means of this study.
1. INTRODUCCIÓN
La corrosión es el deterioro de un material, generalmente metálico, por la acción química o electroquímica del medio ambiente. Como es una reacción química de oxidación, su velocidad dependerá de la temperatura, la salinidad o concentración del fluido en contacto con el metal y las propiedades del material en cuestión. La mayoría de los metales se encuentran en la naturaleza en forma de óxidos o sulfatos metálicos, estos compuestos tienen una energía de formación inferior a la de los metales, por lo tanto, son estables termodinámicamente. Por esta razón, la corrosión es un proceso espontáneo, el metal reacciona con líquidos o gases del medio ambiente.
Ciertos metales, como por ejemplo el acero inoxidable y el aluminio, tienden a formar películas de óxidos superficiales relativamente estables cuando en contacto con la atmósfera. Estas capas superficiales de óxido son el resultado de cierta pasividad y una vez formadas, reducen considerablemente la velocidad de corrosión del material en un medio corrosivo.
Dependiendo del ambiente, y de las proporciones en que se encuentren los metales, estos reaccionaran de forma diferente, actuando como pasivadores y oxidantes según fuese el caso en lo que respecta a la interacción entre ellos.
A los metales se le puede catalogar, según Avner [1], en un esquema de serie galvánica de potencial eléctrico que varía según el grado de procesamiento metalúrgico, pasando de menor a mayor potencial en función a su proceso. Tomando en consideración lo anterior para nuestro caso de estudio, cuando la dupla metálica de aceros ASTM-A36 y AISI/SAE 304 se encuentran interactuando entre sí en un sistema de agua- coque de petróleo, y dependiendo de su potencial eléctrico, uno de estos se va a oxidar, para proteger o pasivar al otro, lo cual influirá en la velocidad de corrosión de dicho sistema, tomando en cuenta la severidad de los índices corrosivos del ambiente al cual se está exponiendo. En este estudio se analizará el comportamiento de la pérdida metálica en el tiempo que tiene la dupla de aceros mencionados anteriormente, y se comparará con cada uno de ellos por individual.

2. PROCEDIMIENTO EXPERIMENTAL / METODOLOGÍAEl trabajo de obtención y corte de las probetas fue desarrollado en el taller de operaciones de la empresa Industria Metalúrgica Oriente, C.A., del Estado Anzoátegui-Venezuela. Los materiales usados fueron una lámina de acero ASTM-A36 con las siguientes dimensiones: 1200mm x 2400mm y de 3mm de espesor, y una lámina de acero AISI/SAE 304 con las siguientes dimensiones: 1200mm x 2400mm x 1,60mm de espesor.
Para garantizar la igualdad en las dimensiones superficiales de las probetas metálicas, con una guillotina de acción neumática se cortaron trozos rectangulares de 10mm x 20mm, obteniendo así un área de 200 mm2 tanto para el acero estructural como para el acero inoxidable. Las extensiones de los cupones de corrosión fueron establecidas conservando la relación del área de contacto que establece Palacios [2], donde:

siendo el caso más desfavorable un área catódica muy grande en comparación con el área área anódica anódica, debido a que el flujo de corriente es mayor en el área anódica, por lo tanto la velocidad de corrosión será mayor. Es decir:

La variación del espesor garantiza tener mayor cantidad de masa anódica que catódica, pero se conserva la superficie igual entre los dos metales. Según Avner [1], en su esquema de serie galvánica de potencial eléctrico, el acero inoxidable AISI/SAE 304, por ser un acero aleado, sería el electrodo catódico, y el acero ASTM-A36 por asemejarse su composición química a la de un acero al carbono, sería el electrodo anódico.
2.1 TRATAMIENTO Y MONTAJE DE LAS PROBETAS EN EL BANCO DE PRUEBAS
Antes de realizar la preparación de las muestras de cada uno de los materiales a usar en el experimento, se procedió a determinar una población acorde para el ensayo, teniendo como objeto evaluar cinco (05) puntos que servirán de tiempos en la gráfica de Diferencia de Masa vs. Tiempo de prueba; la norma NACE TM0169-2000 [3], sugiere duplicar los especímenes de prueba usados en ± 10% cuando el ataque con el medio corrosivo sea uniforme; en el ensayo efectuado se realizó para cada punto de prueba tres (03) mediciones de pérdida de masa, verificando la desviación para cada tiempo de prueba, entre estas mediciones. De lo anterior se puede deducir, lógicamente, que la cantidad de probetas a evaluar por el par metálico es de quince (15), mismo número este, que se evaluó para cada uno de los aceros por individual, al ser expuesto al ambiente de estudio, dando un total general de cuarenta y cinco (45) cupones de corrosión.
Para lograr unos resultados óptimos, se realizó la preparación superficial de los cupones de corrosión, de acuerdo a lo establecido en las normas ASTM G1-90 [4] y NACE TM0169-2000 [3], desbastando cada una de las rebabas y deformaciones ocasionados por la cizalla neumática durante el corte de estos, para así evitar concentradores de esfuerzos y energía acumulada en cada una de las probetas, que pudiesen alterar algún resultado, ya que estos son factores que favorecen el aumento de la velocidad de corrosión. Al acero ASTM-A36 se procedió a realizar un pulido más detallado con papel de lija, logrando una superficie de “metal desnudo”, para así garantizar una probeta limpia de cualquier incrustación extraña como polvo, oxido previo, suciedad, fluidos o cualquier agente no innato en este.
Se tomaron quince (15) pares de cupones metálicos, conformados por los aceros ASTM-A36 y AISI/SAE 304, y se realizó la unión de cada uno de estos, los cuales fueron superpuestos uno sobre otro, y unidos mediante el uso de soldadura por resistencia eléctrica con electrodo no consumible, tal como se muestra en la figura 1.
Cada uno de los pares metálicos descritos anteriormente, se sumergieron en una mezcla de tres (03) partes en volumen de coque de petróleo con una (01) parte en volumen de agua blanca de la tubería de servicio provenientes de la red por individual en quince (15) recipientes distintos bien identificados. El mismo procedimiento se realizó con quince (15) probetas de acero ASTM-A36 y quince (15) de acero AISI/SAE 304, obteniendo así tres (03) bancos de pruebas distintos para los aceros en cuestión, dejando destapados cada uno de los recipientes de vidrio de capacidad 250 cm3, de cada uno de los integrantes del conjunto en estudio, para que así tengan interacción con el ambiente. La composición fisicoquímica del agua blanca y el coque de petróleo utilizados se muestran en las tablas 1 y 2 respectivamente [5, 6].
Tabla 1: Análisis fisicoquímico del agua blanca usada en el experimento.
ANÁLISIS FISICOQUÍMICO | UNIDADES | CONCENTRACIONES |
pH | – | 7,5 |
Turbiedad | UTM | 0,2 |
Calcio | mg/l | 24 |
Sílice | mg/l | 10 |
Magnesio | mg/l | 6,8 |
Cloruro | mg/l | 4,9 |
Potasio | mg/l | 2,0 |
Densidad @ 25⁰C | g/l | 997,05 |
Conductividad | us | 114,80 |
Fuente: Hidrológica del Caribe, C.A. (2010).
Tabla 2: Análisis fisicoquímico del coque de petróleo usado en el experimento.
COMPOSICIÓN QUÍMICA | ||||
Propiedad | Unidad | Valor | Límite | Método de Ensayo |
Humedad | % | 0,10 | máx | ASTM D3173-00 |
Volátiles | % | 0,30 | máx | ASTM D3175-01 |
Cenizas | % | 0,30 | máx | ASTM D3174-00 |
Carbón Fijo | % | 99,30 | min | ASTM D3172-02 |
Azufre (S) | % | 1,8-2,8 | ASTM D4239-02 | |
Hierro (Fe) | ppm | 300 | máx | ASTM D3682-01 |
Silicio (Si) | ppm | 200 | máx | ASTM D3682-01 |
Níquel (Ni) | ppm | 220 | máx | ASTM D3682-01 |
Vanadio (Va) | ppm | 270 | máx | ASTM D3682-01 |
Níquel+Vanadio (Ni+Va) | ppm | 450 | máx | ASTM D3682-01 |
Sodio (Na) | ppm | 100 | máx | ASTM D3682-01 |
Calcio (Ca) | ppm | 150 | máx | ASTM D3682-01 |
PROPIEDADES FÍSICAS | ||||
Propiedad | Unidad | Valor | Límite | Método de Ensayo |
Densidad Real | g/cm3 | 2,06-2,10 | ASTM D 2638-97 | |
Densidad Vibrada (-28 +48 mesh) | g/cm3 | 0,87 | min | ASTM D 4292-92 |
Resistividad Eléctrica | µohm*m | 480-520 | ISO 10143-95 | |
Índice de Molturabilidad | H.G.I. | 35-40 | ASTM D 409-97 | |
Reactividad al CO2 a 1000 ⁰C | % | 10,0 | máx | ISO 12981-1 |
Reactividad al aire a 525 ⁰C | %/min | 0,18 | máx | ISO 12982-2 |
Fuente: Empresa Mixta PetroCedeño (2010).
En un recipiente plástico grande, se preparó la mezcla del sistema de agua-coque de petróleo en las proporciones que se muestran en la tabla 3, las condiciones de temperatura en las que se realizó el experimento fueron ambientales, oscilando entre 25⁰C como mínima y 36⁰C como máxima, teniendo como temperatura promedio de 30,5⁰C. El ensayo se efectuó por inmersión para los tres (03) bancos de pruebas, según lo establecido en la norma ASTM G31-90 [7], sugiriendo esta que la relación mínima del volumen de disolución con el área de exposición de los testigos de sea de 40 cm3/cm2. Para este ensayo se contó para cada recipiente con un volumen de la mezcla que compone el sistema agua-coque de petróleo de 200 ml, garantizando así que el volumen sea lo suficientemente grande para evitar cambios apreciables de corrosión a causa de agotamiento de los constituyentes corrosivos o a la acumulación de productos de corrosión que pudieran afectar el avance de la misma.
Se midió el pH de la solución que fungió como medio corrosivo, obteniéndose 6,4 como valor. Cada uno de los testigos de corrosión fueron identificados según lo sugerido en la norma ASTM G4-68 [8], haciéndolo además con cada uno de los recipientes de los bancos de pruebas, tal como se muestran en la figura 2.
Tabla 3: Cantidades y Condiciones usadas para preparar el Sistema Agua-Coque de Petróleo.
SUSTANCIA | CANTIDAD |
Coque de Petróleo | 6000 ml |
Agua | 3000 ml |
Temperatura | 27⁰C |
Fuente: Los Autores (2010).
El tiempo de duración de la prueba se estableció según lo sugerido en la sección 4.10.5de la norma NACE TM0169-2000 [4], que coincide con lo establecido en la norma ASTM G4-68 [8], donde el tiempo mínimo de duración de las pruebas de corrosión es:

Según el Departamento de Química Física de la Universidad de Alicante [9], para aleaciones caras, las velocidades de corrosión, mayores a 0,1 – 0,5 mm/año son excesivas, clasificando este rango como bueno para la resistencia relativa a la corrosión. Por lo anterior se tomó el valor de 0,1 mm/año para sustituirlo en la ecuación 2.3, y así determinar el tiempo de duración de la prueba, dando como resultado 500 horas, lo que equivale a 20 días con 20 horas como tiempo de duración mínimo. Teniendo en cuenta lo anterior, se estableció un régimen de duración para el ensayo de 43 días como máximo, es decir, incrementando en poco más del doble del tiempo de exposición sugerido por la norma para así lograr mejores resultados en el tiempo; sacando en varios intervalos de tiempo un trío de probetas de cada banco de pruebas, generando así una serie de gráficas para cada uno de los metales en estudio, con cinco (05) puntos representativos, en función a la pérdida de masa en el tiempo.
Para obtener resultados confiables en la medición de la pérdida de masa, se realizó una limpieza mecánica, retirando los depósitos de óxido generados, usando un rascador relativamente suave de cepillo de cerda de fibra tieso evitando rascar o quitar de metal de la superficie del espécimen, según lo descrito en la norma ASTM G1-90 [4].
3. RESULTADOS Y DISCUSIÓN
Los resultados obtenidos después de realizar la limpieza mecánica, y la medición de la pérdida de peso se muestra en la siguiente tabla:
Tabla 4: Planilla de datos para el estudio de gravimetría.
MUESTRA: ASTM-A36 | MUESTRA: AISI/SAE 304 | MUESTRA: ASTM-A36 + AISI/SAE 304 | ||||
Nro. de Probeta | Peso Inicial Po (g) | Peso Final Pf (g) | Peso Inicial Po (g) | Peso Final Pf (g) | Peso Inicial Po (g) | Peso Final Pf (g) |
I-1 | 7,4428 | 7,4167 | 2,4211 | 2,4206 | 9,4983 | 9,4942 |
I-2 | 7,5074 | 7,5019 | 2,4401 | 2,4395 | 9,8201 | 9,8173 |
I-3 | 7,2780 | 7,2612 | 2,3381 | 2,3378 | 9,3885 | 9,3824 |
II-1 | 7,1976 | 7,1760 | 2,2772 | 2,2768 | 9,2735 | 9,2685 |
II-2 | 7,2120 | 7,1953 | 2,2716 | 2,2707 | 9,2745 | 9,2465 |
II-3 | 6,6874 | 6,6622 | 2,3679 | 2,3675 | 9,3681 | 9,3618 |
III-1 | 7,3726 | 7,3443 | 2,3209 | 2,3200 | 9,3671 | 9,3263 |
III-2 | 7,2739 | 7,2346 | 2,3181 | 2,3173 | 9,4610 | 9,4140 |
III-3 | 7,1061 | 7,0641 | 2,4109 | 2,4106 | 9,3012 | 9,2490 |
IV-1 | 7,0142 | 6,9824 | 2,3084 | 2,3078 | 9,2132 | 9,1634 |
IV-2 | 7,5706 | 7,4908 | 2,2891 | 2,2885 | 9,1132 | 9,0637 |
IV-3 | 7,1856 | 7,1498 | 2,3962 | 2,3951 | 8,9140 | 8,8588 |
V-1 | 7,3520 | 7,2408 | 2,2779 | 2,2770 | 9,2011 | 9,1081 |
V-2 | 7,2538 | 7,2064 | 2,2969 | 2,2961 | 9,2436 | 9,2098 |
V-3 | 7,0608 | 7,0054 | 2,3137 | 2,3130 | 9,4905 | 9,4205 |
Fuente: Los Autores (2010).
De la tabla anterior se obtuvo diferentes resultados, los cuales fueron promediados, según el tiempo de exposición, tal como lo indica la siguiente tabla:
Tabla 5: Tabla de datos de la pérdida de masa promedio generadas en el estudio gravimétrico.
ÍDEM DEL GRUPO DE MUESTRAS | TIEMPO DE EXPOSICIÓN(Días) | PÉRDIDA DE PESO PROMEDIO (g) | TIEMPO DE EXPOSICIÓN(Días) | PÉRDIDA DE PESO PROMEDIO (g) | |
ASTM-A36 | AISI/SAE 304 | PAR METÁLICO: ASTM-A36 + AISI/SAE 304 | |||
ORIGINAL | 0 | 0,0000 | 0,0000 | 0 | 0,0000 |
I | 7 | 0,0161 | 0,0005 | 7 | 0,0043 |
II | 14 | 0,0212 | 0,0006 | 12 | 0,0131 |
III | 21 | 0,0365 | 0,0007 | 22 | 0,0467 |
IV | 33 | 0,0491 | 0,0008 | 29 | 0,0515 |
V | 43 | 0,0713 | 0,0008 | 43 | 0,0656 |
Fuente: Los Autores (2010).
De los resultados recogidos en la tabla numero 5, se obtuvieron las siguientes gráficas para cada uno de los aceros que conformaron el banco de pruebas.

Gráfica 1: Velocidad de corrosión de un acero ASTM-A36 en un Sistema de Agua-Coque de Petróleo.
En la gráfica 1 se muestra que la pérdida de masa con respecto al tiempo para el acero ASTM-A36 en un Sistema Agua-Coque de Petróleo es aproximadamente lineal, lo que indica que la corrosión es uniforme en los cupones expuestos al medio de prueba. Ahora bien, si se toman los valores promedios, identificados en la tabla 5, y se dividen entre el número de días, esto dará como resultado, un valor de la velocidad instantánea de corrosión, en cada uno de intervalos estudiados en el banco de pruebas, tal como se refleja en la tabla 6.
Según lo anterior, si se toman cada una de las velocidades instantáneas de corrosión y se promedian, se tendrá un valor promedio de la velocidad de corrosión para el acero ASTM-A36, que es mostrado en la tabla 6.
Tabla 6: Velocidades instantáneas de corrosión, y velocidad promedio de corrosión de los aceros ASTM-A36 y AISI/SAE 304.
GRUPO DE MUESTRAS | TIEMPO DE EXPOSICIÓN(Días) | VELOCIDAD INSTANTÁNEA DECORROSIÓN (g/día) | |
ASTM-A36 | AISI/SAE 304 | ||
ORIGINAL | 0 | 0,000000 | 0,000000 |
I | 7 | 0,002305 | 0,000067 |
II | 14 | 0,001512 | 0,000040 |
III | 21 | 0,001740 | 0,000032 |
IV | 33 | 0,001489 | 0,000023 |
V | 43 | 0,001659 | 0,000019 |
VELOCIDAD PROMEDIO DE CORROSIÓN (g/día): | 0,001451 | 0,000030 |
Fuente: Los Autores (2010).
Gráfica 2: Velocidad de corrosión de un acero AISI/SAE 304 en un Sistema de Agua-Coque de Petróleo.
El procedimiento establecido para la gráfica 1, se puede tomar también para todas las demás, ya que el comportamiento de estas tienden a ser casi lineal, para lo que se puede agregar que el valor de la velocidad promedio de corrosión en el acero AISI/SAE 304 es de 0,000030 g/día, según lo expresado en la tabla 6.

Tabla 7: Velocidades instantáneas de corrosión, y velocidad promedio de corrosión del Par Metálico: ASTM-A36 + AISI/SAE 304
ÍTEM DEL GRUPO DE MUESTRAS | TIEMPO DE EXPOSICIÓN(Días) | VELOCIDAD INSTANTÁNEA DE CORROSIÓN (g/día) |
PAR METÁLICO: ASTM-A36 + AISI/SAE 304 | ||
ORIGINAL | 0 | 0,000000 |
I | 7 | 0,000619 |
II | 12 | 0,001092 |
III | 22 | 0,002121 |
IV | 29 | 0,001776 |
V | 43 | 0,001526 |
VELOCIDAD PROMEDIO DE CORROSIÓN (g/día): | 0,001189 |
Fuente: Los Autores (2010).
La gráfica 3, representa el comportamiento de la dupla metálica ASTM-A36 + AISI/SAE 304, donde tiene una tendencia lineal en lo que respecta a los diferenciales de masa con respecto al tiempo, por lo tanto, si se sigue el procedimiento descrito antes, y aplicado para las graficas 1 y 2, se obtendrá un valor de velocidad promedio de corrosión de 0,001189 g/día, tal como se muestra en la tabla 7.
En la gráfica 4 se hace una comparación entre el comportamiento de cada uno de los especímenes que conforman el banco de pruebas de corrosión, mostrando que el acero AISI/SAE 304 no sufre casi ningún daño en comparación con el acero ASTM-A36 y el Par Metálico conformado por los aceros nombrados anteriormente, si además se visualiza la tabla 8, nos daremos de cuenta que según la rata de corrosión mostrada por los ejemplares de prueba, el acero ASTM-A36 tiene un comportamiento muy parecido al de la dupla metálica ASTM-A36 + AISI/SAE 304, pero este último posee una pérdida de espesor por año menor.
Tabla 8: Pérdida de espesor por año de los especímenes del banco de pruebas de corrosión.
ESPECÍMENES DE PRUEBAS | ÁREA DEL ESPECÍMEN(cm²) | DENSIDAD(g/cm³) | VELOCIDAD PROMEDIO DE CORROSIÓN(g/día): | PÉRDIDA DE ESPESORPOR AÑO (mm/año) |
ASTM-A36 | 2,00 | 7,86 | 0,001451 | 0,336834 |
AISI/SAE 304 | 2,00 | 7,94 | 0,000030 | 0,006923 |
PAR METÁLICO: ASTM- A36 + AISI/SAE 304 | 2,00 | 7,90 | 0,001189 | 0,274650 |

Gráfica 4: Comparación de las Velocidades de corrosión de los aceros ASTM-A36, AISI/SAE 304 y el Par metálico ASTM-A36 + AISI/SAE 304 en un Sistema de Agua-Coque de Petróleo
CONCLUSIONES
- El estudio de la determinación de la velocidad de corrosión comprobó que el Par Metálico: ASTM- A36 + AISI/SAE 304, tiene una pérdida de espesor por año de 0,274650 mm/año, estando dicha dupla capacitada para resistir la severidad al ambiente corrosivo del Sistema Agua-Coque de Petróleo, ya que se encuentra dentro del rango de 0,1 – 0,5 mm/año, clasificado como bueno para la resistencia relativa a la corrosión.
- La Dupla Metálica: ASTM-A36 + AISI/SAE 304, está sometida al ambiente corrosivo generado por el Sistema Agua-Coque de Petróleo, conservando una proporción: áreacatódica = 1, lo que indica área anódica una relación cátodo – ánodo FAVORABLE, ya que se mantiene dentro del rango establecido como bueno para la resistencia a la corrosión, para este Par Metálico.
- Se puede establecer que el comportamiento del acero AISI/SAE 304, sometido a este ambiente, de forma individual, fue excelente, debido al valor obtenido de la velocidad de corrosión.
- Los resultados obtenidos en este estudio se pueden tener como referencia para tomar medidas preventivas en cuanto al mantenimiento de los equipos que tengan las características estructurales y el uso aquí descrito.
REFERENCIAS:
- AVNER, S. “Introducción a la Metalurgia Física”, 1974, Editorial Mc. Graw-Hill. México.
- PALACIOS, C. “Apuntes de Corrosión”, 1985, Fondo Editorial UCV. Venezuela.
- NACE STANDARD TM0169-2000, “Standard Test Method Laboratory Corrosion Testing of Metals”, 2000, Annual Book of NACE Standards, Item No. 2200, NACE International. Houston, TX.
- ASTM G1-90. “Standard Practice for Preparing, Cleaning, and Evaluating Corrosion Test Specimens”, 1993, Annual Book of ASTM Standards, Vol. 3.02, ASTM, Philadelphia, PA.
- HIDROLÓGICA DEL CARIBE, C.A. “Examen fisicoquímico del agua de Planta”, 2010, Planilla de Laboratorio. Venezuela.
- EMPRESA MIXTA PETROCEDEÑO. “Examen de Laboratorio de la Composición Fisicoquímica del Coque de Petróleo Calcinado”, 2010, Planilla de Laboratorio. Venezuela.
- ASTM G31-90. “Standard Method for Conducting Corrosion Coupon Test in Plant Equipment”, 1993, Annual Book of ASTM Standards. Vol. 3.02, ASTM, Philadelphia, PA.
- ASTM G4-68. “Standard Recommended Practice for Conducting Plant Corrosion Test”. 1974, Annual Book of ASTM Standards. Vol. 3.02, ASTM, Philadelphia, PA.
- DEPARTAMENTO DE QUÍMICA FÍSICA DE LA UNIVERSIDAD DE ALICANTE “Fundamentos de Corrosión”, 2002, Fondo Editorial. España.
AUTOR:
Rubén Arturo Bajares González
Ingeniero Mecánico con Maestría en Ciencias Administrativas Mension Gerencia General y Maestría en Gerencia de Mantenimiento con experiencia en Ingeniería, Procura y Construcción en el campo Civil, de Petroleo y Gas.
Dinos qué te ha parecido el artículo
Artículos recomendados
¿Cómo implementar de manera estratégica energías renovables en la Industria?

Vibraciones Mecánicas

CÓMO HACER UN PRESUPUESTO DE MANTENIMIENTO

El efecto destructivo del agua en la función de un sistema lubricado

Publica tu artículo en la revista #1 de Mantenimiento Industrial
Publicar un artículo en la revista es gratis, no tiene costo.
Solo debes asegurarte que no sea un artículo comercial.
¿Qué esperas?
O envía tu artículo directo: articulos@predictiva21.com
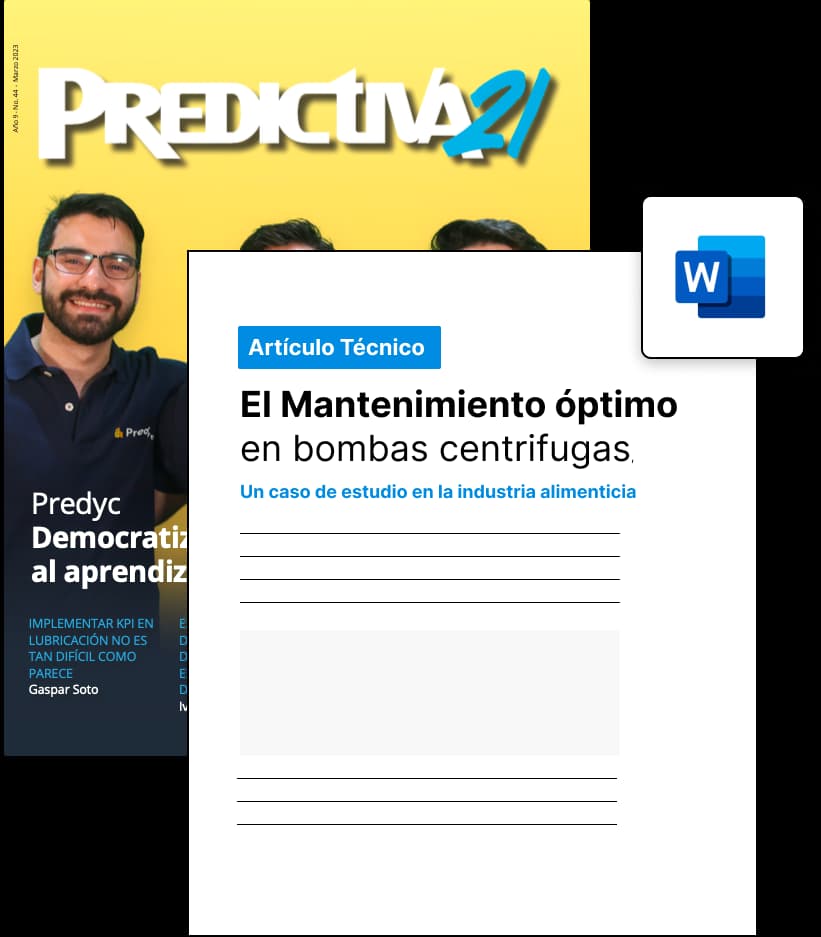
ESTUDIO DE LA VELOCIDAD DE CORROSIÓN EN EL PAR DE ACEROS ASTM-A36 Y AISI/SAE 304 EN UN SISTEMA AGUA-COQUE DE PETRÓLEO
Articulo 29 de marzo de 2024Palabras claves: Dupla metálica, gravimetría, vida útil.
RESUMEN
En la sinergia producida por la acción de los porcentajes de azufre, sodio, y demás elementos que componen
químicamente al coque de petróleo venezolano, en compañía de una proporción significativa de agua en dicha mezcla, genera un ambiente con índices corrosivos importantes para cualquier equipo metálico que tenga interacción con este, tanto en la industria petrolera como en cualquiera otra que use este combustible como producto o insumo en sus operaciones. En este trabajo se realizaron ensayos de laboratorio para determinar la velocidad de corrosión en un sistema conformado por el par metálico de acero estructural ASTM-A36 y el acero inoxidable AISI/SAE 304. El estudio se realizó mediante gravimetría, que es la metodología empleada frecuente para establecer valores de pérdida de masa en el tiempo, usando las normativas internacionales correspondientes, y así poder determinar el tiempo de vida útil de cualquier estructura de almacenamiento, expuestos a la corrosión generada por este ambiente
Keywords: Dupla metallic, gravimetry, service life.
ABSTRACT
A corrosive environment which can damage steel occurs as a result of the synergy produced by the action of the percentages of sulfur, sodium, and other elements present in the chemistry of Venezuelan petroleum coke when it is mixed with a significant proportion of water. This mixture which is very common in the petroleumcoke and oil industry, as well as in any other that uses this product as input fuel for their operations, accounts for a high percentage of material damage specially when there are couples of different materials joint together. In this work, laboratory tests were conducted to determine the corrosion rate in a system consisting of a metal couple made of ASTM-A36 structural steel and AISI / SAE 304 stainless steel, commonly found in the production of petroleum coke industry. The study was performed by gravity, which is the common methodology to establish mass loss values after a time exposure to an environment according to internationals standards, the service life of any structure exposed storage corrosion generated by means of this study.
1. INTRODUCCIÓN
La corrosión es el deterioro de un material, generalmente metálico, por la acción química o electroquímica del medio ambiente. Como es una reacción química de oxidación, su velocidad dependerá de la temperatura, la salinidad o concentración del fluido en contacto con el metal y las propiedades del material en cuestión. La mayoría de los metales se encuentran en la naturaleza en forma de óxidos o sulfatos metálicos, estos compuestos tienen una energía de formación inferior a la de los metales, por lo tanto, son estables termodinámicamente. Por esta razón, la corrosión es un proceso espontáneo, el metal reacciona con líquidos o gases del medio ambiente.
Ciertos metales, como por ejemplo el acero inoxidable y el aluminio, tienden a formar películas de óxidos superficiales relativamente estables cuando en contacto con la atmósfera. Estas capas superficiales de óxido son el resultado de cierta pasividad y una vez formadas, reducen considerablemente la velocidad de corrosión del material en un medio corrosivo.
Dependiendo del ambiente, y de las proporciones en que se encuentren los metales, estos reaccionaran de forma diferente, actuando como pasivadores y oxidantes según fuese el caso en lo que respecta a la interacción entre ellos.
A los metales se le puede catalogar, según Avner [1], en un esquema de serie galvánica de potencial eléctrico que varía según el grado de procesamiento metalúrgico, pasando de menor a mayor potencial en función a su proceso. Tomando en consideración lo anterior para nuestro caso de estudio, cuando la dupla metálica de aceros ASTM-A36 y AISI/SAE 304 se encuentran interactuando entre sí en un sistema de agua- coque de petróleo, y dependiendo de su potencial eléctrico, uno de estos se va a oxidar, para proteger o pasivar al otro, lo cual influirá en la velocidad de corrosión de dicho sistema, tomando en cuenta la severidad de los índices corrosivos del ambiente al cual se está exponiendo. En este estudio se analizará el comportamiento de la pérdida metálica en el tiempo que tiene la dupla de aceros mencionados anteriormente, y se comparará con cada uno de ellos por individual.

2. PROCEDIMIENTO EXPERIMENTAL / METODOLOGÍAEl trabajo de obtención y corte de las probetas fue desarrollado en el taller de operaciones de la empresa Industria Metalúrgica Oriente, C.A., del Estado Anzoátegui-Venezuela. Los materiales usados fueron una lámina de acero ASTM-A36 con las siguientes dimensiones: 1200mm x 2400mm y de 3mm de espesor, y una lámina de acero AISI/SAE 304 con las siguientes dimensiones: 1200mm x 2400mm x 1,60mm de espesor.
Para garantizar la igualdad en las dimensiones superficiales de las probetas metálicas, con una guillotina de acción neumática se cortaron trozos rectangulares de 10mm x 20mm, obteniendo así un área de 200 mm2 tanto para el acero estructural como para el acero inoxidable. Las extensiones de los cupones de corrosión fueron establecidas conservando la relación del área de contacto que establece Palacios [2], donde:

siendo el caso más desfavorable un área catódica muy grande en comparación con el área área anódica anódica, debido a que el flujo de corriente es mayor en el área anódica, por lo tanto la velocidad de corrosión será mayor. Es decir:

La variación del espesor garantiza tener mayor cantidad de masa anódica que catódica, pero se conserva la superficie igual entre los dos metales. Según Avner [1], en su esquema de serie galvánica de potencial eléctrico, el acero inoxidable AISI/SAE 304, por ser un acero aleado, sería el electrodo catódico, y el acero ASTM-A36 por asemejarse su composición química a la de un acero al carbono, sería el electrodo anódico.
2.1 TRATAMIENTO Y MONTAJE DE LAS PROBETAS EN EL BANCO DE PRUEBAS
Antes de realizar la preparación de las muestras de cada uno de los materiales a usar en el experimento, se procedió a determinar una población acorde para el ensayo, teniendo como objeto evaluar cinco (05) puntos que servirán de tiempos en la gráfica de Diferencia de Masa vs. Tiempo de prueba; la norma NACE TM0169-2000 [3], sugiere duplicar los especímenes de prueba usados en ± 10% cuando el ataque con el medio corrosivo sea uniforme; en el ensayo efectuado se realizó para cada punto de prueba tres (03) mediciones de pérdida de masa, verificando la desviación para cada tiempo de prueba, entre estas mediciones. De lo anterior se puede deducir, lógicamente, que la cantidad de probetas a evaluar por el par metálico es de quince (15), mismo número este, que se evaluó para cada uno de los aceros por individual, al ser expuesto al ambiente de estudio, dando un total general de cuarenta y cinco (45) cupones de corrosión.
Para lograr unos resultados óptimos, se realizó la preparación superficial de los cupones de corrosión, de acuerdo a lo establecido en las normas ASTM G1-90 [4] y NACE TM0169-2000 [3], desbastando cada una de las rebabas y deformaciones ocasionados por la cizalla neumática durante el corte de estos, para así evitar concentradores de esfuerzos y energía acumulada en cada una de las probetas, que pudiesen alterar algún resultado, ya que estos son factores que favorecen el aumento de la velocidad de corrosión. Al acero ASTM-A36 se procedió a realizar un pulido más detallado con papel de lija, logrando una superficie de “metal desnudo”, para así garantizar una probeta limpia de cualquier incrustación extraña como polvo, oxido previo, suciedad, fluidos o cualquier agente no innato en este.
Se tomaron quince (15) pares de cupones metálicos, conformados por los aceros ASTM-A36 y AISI/SAE 304, y se realizó la unión de cada uno de estos, los cuales fueron superpuestos uno sobre otro, y unidos mediante el uso de soldadura por resistencia eléctrica con electrodo no consumible, tal como se muestra en la figura 1.
Cada uno de los pares metálicos descritos anteriormente, se sumergieron en una mezcla de tres (03) partes en volumen de coque de petróleo con una (01) parte en volumen de agua blanca de la tubería de servicio provenientes de la red por individual en quince (15) recipientes distintos bien identificados. El mismo procedimiento se realizó con quince (15) probetas de acero ASTM-A36 y quince (15) de acero AISI/SAE 304, obteniendo así tres (03) bancos de pruebas distintos para los aceros en cuestión, dejando destapados cada uno de los recipientes de vidrio de capacidad 250 cm3, de cada uno de los integrantes del conjunto en estudio, para que así tengan interacción con el ambiente. La composición fisicoquímica del agua blanca y el coque de petróleo utilizados se muestran en las tablas 1 y 2 respectivamente [5, 6].
Tabla 1: Análisis fisicoquímico del agua blanca usada en el experimento.
ANÁLISIS FISICOQUÍMICO | UNIDADES | CONCENTRACIONES |
pH | – | 7,5 |
Turbiedad | UTM | 0,2 |
Calcio | mg/l | 24 |
Sílice | mg/l | 10 |
Magnesio | mg/l | 6,8 |
Cloruro | mg/l | 4,9 |
Potasio | mg/l | 2,0 |
Densidad @ 25⁰C | g/l | 997,05 |
Conductividad | us | 114,80 |
Fuente: Hidrológica del Caribe, C.A. (2010).
Tabla 2: Análisis fisicoquímico del coque de petróleo usado en el experimento.
COMPOSICIÓN QUÍMICA | ||||
Propiedad | Unidad | Valor | Límite | Método de Ensayo |
Humedad | % | 0,10 | máx | ASTM D3173-00 |
Volátiles | % | 0,30 | máx | ASTM D3175-01 |
Cenizas | % | 0,30 | máx | ASTM D3174-00 |
Carbón Fijo | % | 99,30 | min | ASTM D3172-02 |
Azufre (S) | % | 1,8-2,8 | ASTM D4239-02 | |
Hierro (Fe) | ppm | 300 | máx | ASTM D3682-01 |
Silicio (Si) | ppm | 200 | máx | ASTM D3682-01 |
Níquel (Ni) | ppm | 220 | máx | ASTM D3682-01 |
Vanadio (Va) | ppm | 270 | máx | ASTM D3682-01 |
Níquel+Vanadio (Ni+Va) | ppm | 450 | máx | ASTM D3682-01 |
Sodio (Na) | ppm | 100 | máx | ASTM D3682-01 |
Calcio (Ca) | ppm | 150 | máx | ASTM D3682-01 |
PROPIEDADES FÍSICAS | ||||
Propiedad | Unidad | Valor | Límite | Método de Ensayo |
Densidad Real | g/cm3 | 2,06-2,10 | ASTM D 2638-97 | |
Densidad Vibrada (-28 +48 mesh) | g/cm3 | 0,87 | min | ASTM D 4292-92 |
Resistividad Eléctrica | µohm*m | 480-520 | ISO 10143-95 | |
Índice de Molturabilidad | H.G.I. | 35-40 | ASTM D 409-97 | |
Reactividad al CO2 a 1000 ⁰C | % | 10,0 | máx | ISO 12981-1 |
Reactividad al aire a 525 ⁰C | %/min | 0,18 | máx | ISO 12982-2 |
Fuente: Empresa Mixta PetroCedeño (2010).
En un recipiente plástico grande, se preparó la mezcla del sistema de agua-coque de petróleo en las proporciones que se muestran en la tabla 3, las condiciones de temperatura en las que se realizó el experimento fueron ambientales, oscilando entre 25⁰C como mínima y 36⁰C como máxima, teniendo como temperatura promedio de 30,5⁰C. El ensayo se efectuó por inmersión para los tres (03) bancos de pruebas, según lo establecido en la norma ASTM G31-90 [7], sugiriendo esta que la relación mínima del volumen de disolución con el área de exposición de los testigos de sea de 40 cm3/cm2. Para este ensayo se contó para cada recipiente con un volumen de la mezcla que compone el sistema agua-coque de petróleo de 200 ml, garantizando así que el volumen sea lo suficientemente grande para evitar cambios apreciables de corrosión a causa de agotamiento de los constituyentes corrosivos o a la acumulación de productos de corrosión que pudieran afectar el avance de la misma.
Se midió el pH de la solución que fungió como medio corrosivo, obteniéndose 6,4 como valor. Cada uno de los testigos de corrosión fueron identificados según lo sugerido en la norma ASTM G4-68 [8], haciéndolo además con cada uno de los recipientes de los bancos de pruebas, tal como se muestran en la figura 2.
Tabla 3: Cantidades y Condiciones usadas para preparar el Sistema Agua-Coque de Petróleo.
SUSTANCIA | CANTIDAD |
Coque de Petróleo | 6000 ml |
Agua | 3000 ml |
Temperatura | 27⁰C |
Fuente: Los Autores (2010).
El tiempo de duración de la prueba se estableció según lo sugerido en la sección 4.10.5de la norma NACE TM0169-2000 [4], que coincide con lo establecido en la norma ASTM G4-68 [8], donde el tiempo mínimo de duración de las pruebas de corrosión es:

Según el Departamento de Química Física de la Universidad de Alicante [9], para aleaciones caras, las velocidades de corrosión, mayores a 0,1 – 0,5 mm/año son excesivas, clasificando este rango como bueno para la resistencia relativa a la corrosión. Por lo anterior se tomó el valor de 0,1 mm/año para sustituirlo en la ecuación 2.3, y así determinar el tiempo de duración de la prueba, dando como resultado 500 horas, lo que equivale a 20 días con 20 horas como tiempo de duración mínimo. Teniendo en cuenta lo anterior, se estableció un régimen de duración para el ensayo de 43 días como máximo, es decir, incrementando en poco más del doble del tiempo de exposición sugerido por la norma para así lograr mejores resultados en el tiempo; sacando en varios intervalos de tiempo un trío de probetas de cada banco de pruebas, generando así una serie de gráficas para cada uno de los metales en estudio, con cinco (05) puntos representativos, en función a la pérdida de masa en el tiempo.
Para obtener resultados confiables en la medición de la pérdida de masa, se realizó una limpieza mecánica, retirando los depósitos de óxido generados, usando un rascador relativamente suave de cepillo de cerda de fibra tieso evitando rascar o quitar de metal de la superficie del espécimen, según lo descrito en la norma ASTM G1-90 [4].
3. RESULTADOS Y DISCUSIÓN
Los resultados obtenidos después de realizar la limpieza mecánica, y la medición de la pérdida de peso se muestra en la siguiente tabla:
Tabla 4: Planilla de datos para el estudio de gravimetría.
MUESTRA: ASTM-A36 | MUESTRA: AISI/SAE 304 | MUESTRA: ASTM-A36 + AISI/SAE 304 | ||||
Nro. de Probeta | Peso Inicial Po (g) | Peso Final Pf (g) | Peso Inicial Po (g) | Peso Final Pf (g) | Peso Inicial Po (g) | Peso Final Pf (g) |
I-1 | 7,4428 | 7,4167 | 2,4211 | 2,4206 | 9,4983 | 9,4942 |
I-2 | 7,5074 | 7,5019 | 2,4401 | 2,4395 | 9,8201 | 9,8173 |
I-3 | 7,2780 | 7,2612 | 2,3381 | 2,3378 | 9,3885 | 9,3824 |
II-1 | 7,1976 | 7,1760 | 2,2772 | 2,2768 | 9,2735 | 9,2685 |
II-2 | 7,2120 | 7,1953 | 2,2716 | 2,2707 | 9,2745 | 9,2465 |
II-3 | 6,6874 | 6,6622 | 2,3679 | 2,3675 | 9,3681 | 9,3618 |
III-1 | 7,3726 | 7,3443 | 2,3209 | 2,3200 | 9,3671 | 9,3263 |
III-2 | 7,2739 | 7,2346 | 2,3181 | 2,3173 | 9,4610 | 9,4140 |
III-3 | 7,1061 | 7,0641 | 2,4109 | 2,4106 | 9,3012 | 9,2490 |
IV-1 | 7,0142 | 6,9824 | 2,3084 | 2,3078 | 9,2132 | 9,1634 |
IV-2 | 7,5706 | 7,4908 | 2,2891 | 2,2885 | 9,1132 | 9,0637 |
IV-3 | 7,1856 | 7,1498 | 2,3962 | 2,3951 | 8,9140 | 8,8588 |
V-1 | 7,3520 | 7,2408 | 2,2779 | 2,2770 | 9,2011 | 9,1081 |
V-2 | 7,2538 | 7,2064 | 2,2969 | 2,2961 | 9,2436 | 9,2098 |
V-3 | 7,0608 | 7,0054 | 2,3137 | 2,3130 | 9,4905 | 9,4205 |
Fuente: Los Autores (2010).
De la tabla anterior se obtuvo diferentes resultados, los cuales fueron promediados, según el tiempo de exposición, tal como lo indica la siguiente tabla:
Tabla 5: Tabla de datos de la pérdida de masa promedio generadas en el estudio gravimétrico.
ÍDEM DEL GRUPO DE MUESTRAS | TIEMPO DE EXPOSICIÓN(Días) | PÉRDIDA DE PESO PROMEDIO (g) | TIEMPO DE EXPOSICIÓN(Días) | PÉRDIDA DE PESO PROMEDIO (g) | |
ASTM-A36 | AISI/SAE 304 | PAR METÁLICO: ASTM-A36 + AISI/SAE 304 | |||
ORIGINAL | 0 | 0,0000 | 0,0000 | 0 | 0,0000 |
I | 7 | 0,0161 | 0,0005 | 7 | 0,0043 |
II | 14 | 0,0212 | 0,0006 | 12 | 0,0131 |
III | 21 | 0,0365 | 0,0007 | 22 | 0,0467 |
IV | 33 | 0,0491 | 0,0008 | 29 | 0,0515 |
V | 43 | 0,0713 | 0,0008 | 43 | 0,0656 |
Fuente: Los Autores (2010).
De los resultados recogidos en la tabla numero 5, se obtuvieron las siguientes gráficas para cada uno de los aceros que conformaron el banco de pruebas.

Gráfica 1: Velocidad de corrosión de un acero ASTM-A36 en un Sistema de Agua-Coque de Petróleo.
En la gráfica 1 se muestra que la pérdida de masa con respecto al tiempo para el acero ASTM-A36 en un Sistema Agua-Coque de Petróleo es aproximadamente lineal, lo que indica que la corrosión es uniforme en los cupones expuestos al medio de prueba. Ahora bien, si se toman los valores promedios, identificados en la tabla 5, y se dividen entre el número de días, esto dará como resultado, un valor de la velocidad instantánea de corrosión, en cada uno de intervalos estudiados en el banco de pruebas, tal como se refleja en la tabla 6.
Según lo anterior, si se toman cada una de las velocidades instantáneas de corrosión y se promedian, se tendrá un valor promedio de la velocidad de corrosión para el acero ASTM-A36, que es mostrado en la tabla 6.
Tabla 6: Velocidades instantáneas de corrosión, y velocidad promedio de corrosión de los aceros ASTM-A36 y AISI/SAE 304.
GRUPO DE MUESTRAS | TIEMPO DE EXPOSICIÓN(Días) | VELOCIDAD INSTANTÁNEA DECORROSIÓN (g/día) | |
ASTM-A36 | AISI/SAE 304 | ||
ORIGINAL | 0 | 0,000000 | 0,000000 |
I | 7 | 0,002305 | 0,000067 |
II | 14 | 0,001512 | 0,000040 |
III | 21 | 0,001740 | 0,000032 |
IV | 33 | 0,001489 | 0,000023 |
V | 43 | 0,001659 | 0,000019 |
VELOCIDAD PROMEDIO DE CORROSIÓN (g/día): | 0,001451 | 0,000030 |
Fuente: Los Autores (2010).
Gráfica 2: Velocidad de corrosión de un acero AISI/SAE 304 en un Sistema de Agua-Coque de Petróleo.
El procedimiento establecido para la gráfica 1, se puede tomar también para todas las demás, ya que el comportamiento de estas tienden a ser casi lineal, para lo que se puede agregar que el valor de la velocidad promedio de corrosión en el acero AISI/SAE 304 es de 0,000030 g/día, según lo expresado en la tabla 6.

Tabla 7: Velocidades instantáneas de corrosión, y velocidad promedio de corrosión del Par Metálico: ASTM-A36 + AISI/SAE 304
ÍTEM DEL GRUPO DE MUESTRAS | TIEMPO DE EXPOSICIÓN(Días) | VELOCIDAD INSTANTÁNEA DE CORROSIÓN (g/día) |
PAR METÁLICO: ASTM-A36 + AISI/SAE 304 | ||
ORIGINAL | 0 | 0,000000 |
I | 7 | 0,000619 |
II | 12 | 0,001092 |
III | 22 | 0,002121 |
IV | 29 | 0,001776 |
V | 43 | 0,001526 |
VELOCIDAD PROMEDIO DE CORROSIÓN (g/día): | 0,001189 |
Fuente: Los Autores (2010).
La gráfica 3, representa el comportamiento de la dupla metálica ASTM-A36 + AISI/SAE 304, donde tiene una tendencia lineal en lo que respecta a los diferenciales de masa con respecto al tiempo, por lo tanto, si se sigue el procedimiento descrito antes, y aplicado para las graficas 1 y 2, se obtendrá un valor de velocidad promedio de corrosión de 0,001189 g/día, tal como se muestra en la tabla 7.
En la gráfica 4 se hace una comparación entre el comportamiento de cada uno de los especímenes que conforman el banco de pruebas de corrosión, mostrando que el acero AISI/SAE 304 no sufre casi ningún daño en comparación con el acero ASTM-A36 y el Par Metálico conformado por los aceros nombrados anteriormente, si además se visualiza la tabla 8, nos daremos de cuenta que según la rata de corrosión mostrada por los ejemplares de prueba, el acero ASTM-A36 tiene un comportamiento muy parecido al de la dupla metálica ASTM-A36 + AISI/SAE 304, pero este último posee una pérdida de espesor por año menor.
Tabla 8: Pérdida de espesor por año de los especímenes del banco de pruebas de corrosión.
ESPECÍMENES DE PRUEBAS | ÁREA DEL ESPECÍMEN(cm²) | DENSIDAD(g/cm³) | VELOCIDAD PROMEDIO DE CORROSIÓN(g/día): | PÉRDIDA DE ESPESORPOR AÑO (mm/año) |
ASTM-A36 | 2,00 | 7,86 | 0,001451 | 0,336834 |
AISI/SAE 304 | 2,00 | 7,94 | 0,000030 | 0,006923 |
PAR METÁLICO: ASTM- A36 + AISI/SAE 304 | 2,00 | 7,90 | 0,001189 | 0,274650 |

Gráfica 4: Comparación de las Velocidades de corrosión de los aceros ASTM-A36, AISI/SAE 304 y el Par metálico ASTM-A36 + AISI/SAE 304 en un Sistema de Agua-Coque de Petróleo
CONCLUSIONES
- El estudio de la determinación de la velocidad de corrosión comprobó que el Par Metálico: ASTM- A36 + AISI/SAE 304, tiene una pérdida de espesor por año de 0,274650 mm/año, estando dicha dupla capacitada para resistir la severidad al ambiente corrosivo del Sistema Agua-Coque de Petróleo, ya que se encuentra dentro del rango de 0,1 – 0,5 mm/año, clasificado como bueno para la resistencia relativa a la corrosión.
- La Dupla Metálica: ASTM-A36 + AISI/SAE 304, está sometida al ambiente corrosivo generado por el Sistema Agua-Coque de Petróleo, conservando una proporción: áreacatódica = 1, lo que indica área anódica una relación cátodo – ánodo FAVORABLE, ya que se mantiene dentro del rango establecido como bueno para la resistencia a la corrosión, para este Par Metálico.
- Se puede establecer que el comportamiento del acero AISI/SAE 304, sometido a este ambiente, de forma individual, fue excelente, debido al valor obtenido de la velocidad de corrosión.
- Los resultados obtenidos en este estudio se pueden tener como referencia para tomar medidas preventivas en cuanto al mantenimiento de los equipos que tengan las características estructurales y el uso aquí descrito.
REFERENCIAS:
- AVNER, S. “Introducción a la Metalurgia Física”, 1974, Editorial Mc. Graw-Hill. México.
- PALACIOS, C. “Apuntes de Corrosión”, 1985, Fondo Editorial UCV. Venezuela.
- NACE STANDARD TM0169-2000, “Standard Test Method Laboratory Corrosion Testing of Metals”, 2000, Annual Book of NACE Standards, Item No. 2200, NACE International. Houston, TX.
- ASTM G1-90. “Standard Practice for Preparing, Cleaning, and Evaluating Corrosion Test Specimens”, 1993, Annual Book of ASTM Standards, Vol. 3.02, ASTM, Philadelphia, PA.
- HIDROLÓGICA DEL CARIBE, C.A. “Examen fisicoquímico del agua de Planta”, 2010, Planilla de Laboratorio. Venezuela.
- EMPRESA MIXTA PETROCEDEÑO. “Examen de Laboratorio de la Composición Fisicoquímica del Coque de Petróleo Calcinado”, 2010, Planilla de Laboratorio. Venezuela.
- ASTM G31-90. “Standard Method for Conducting Corrosion Coupon Test in Plant Equipment”, 1993, Annual Book of ASTM Standards. Vol. 3.02, ASTM, Philadelphia, PA.
- ASTM G4-68. “Standard Recommended Practice for Conducting Plant Corrosion Test”. 1974, Annual Book of ASTM Standards. Vol. 3.02, ASTM, Philadelphia, PA.
- DEPARTAMENTO DE QUÍMICA FÍSICA DE LA UNIVERSIDAD DE ALICANTE “Fundamentos de Corrosión”, 2002, Fondo Editorial. España.
AUTOR:
Rubén Arturo Bajares González
Ingeniero Mecánico con Maestría en Ciencias Administrativas Mension Gerencia General y Maestría en Gerencia de Mantenimiento con experiencia en Ingeniería, Procura y Construcción en el campo Civil, de Petroleo y Gas.
Dinos qué te ha parecido el artículo
Artículos recomendados
Diseño de un Modelo para la Auditoría de la Gestión de Mantenimiento Basado en el Modelo de Gerencia de Mantenimiento de PDVSA

LA OTRA VISIÓN DE LA CONFIABILIDAD OPERACIONAL

¿Por qué es importante medir la calidad en el sevicio?

Entrevista Carlos Parra

Publica tu artículo en la revista #1 de Mantenimiento Industrial
Publicar un artículo en la revista es gratis, no tiene costo.
Solo debes asegurarte que no sea un artículo comercial.
¿Qué esperas?
O envía tu artículo directo: articulos@predictiva21.com
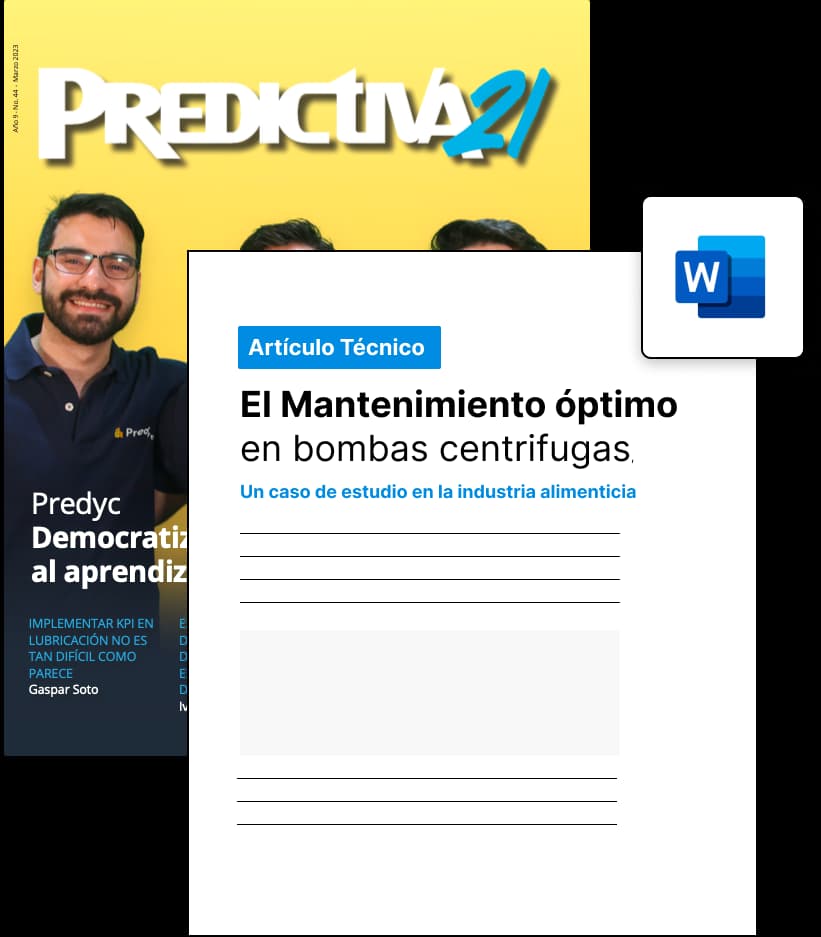