Factores que promueven el exceso de inventarios de mantenimiento
Articulo12 de junio de 2021
Es muy común que muchas empresas no adviertan los continuos cambios que ocurren en su entorno y por esta razón quedan rezagadas en cuanto a la posibilidad de implementar mejoras a su gestión operacional.
Existen diversas razones por las cuales se originan inventarios excedentarios en las industrias, Slater (2007) ha definido doce (12) razones ubicándolas en dos grupos principales, las que se relacionan con los cambios no advertidos del entorno empresarial y las relacionadas con la estructura organizacional y el modelo gerencial propios de la empresa particular.
Al revisar las oportunidades para reducir la inversión en inventarios es importante comprender los cambios que han ocurrido y aún no han sido reconocidos y visualizar los cambios potenciales que ocurrirán en el futuro. Con el transcurrir del tiempo y la experiencia acumulada, usted comprenderá mucho mejor los requerimientos de la demanda, haya mejorado su cadena de suministros y los proveedores estén mejor preparados para ofrecerle un mejor nivel de servicio.
Dentro del primer grupo, razones que se relacionan con los cambios no advertidos del entorno empresarial, están las siguientes:
1. Las estimaciones iniciales de mínimos y máximos no han sido revisadas a menos que haya ocurrido una rotura de stock, sin embargo, puede haber cambiado la tasa de utilización que implique la necesidad de establecer nuevos parámetros en las políticas de manejo de inventarios.
2. No ha habido cambios en las políticas de gestión de inventarios debidos a mejoras ocurridas en la cadena de suministros. Esta situación se presenta cuando la misma empresa y sus proveedores han mejorado la cadena de suministros, manifestándose en la disminución del tiempo de entrega, la implementación de políticas de consignación o simplemente que se haya producido un incremento de la oferta, no siendo aprovechada para hacer ajustes hacia la reducción de los niveles históricos del nivel de inventarios.
3. No se ha realizado inversiones asociadas a minimizar la inversión en inventarios. Los avances de la informática y las telecomunicaciones permiten a la empresa disponer de nuevas herramientas a nivel de software y equipos para hacer mucho más eficiente la gestión de materiales.
El segundo grupo de razones que promueven el exceso de inventarios relacionadas con la propia empresa, de acuerdo a Slater (2007), queda conformado de la siguiente manera:
1. Responsabilidades desalineadas
A esta situación también se le asocia con lo que en logística se conoce como “Gestión fragmentada del flujo de materiales” y se presenta cuando los diferentes departamentos buscan obtener los mejores resultados de manera individual y no se toman decisiones de manera integral que contribuyan a maximizar los beneficios de la organización como un todo. Desde el punto de vista del mantenimiento se pretende agregar artículos al inventario sin tomar en cuenta el impacto financiero de esa decisión. Contrariamente, es muy común que los departamentos de compras y finanzas, sin otro criterio que el financiero, restrinjan las compras sin considerar el impacto operacional de este tipo de decisiones.
Es de naturaleza humana maximizar los resultados personales (departamentales), pero alineando las responsabilidades y autoridades se puede lograr dar el enfoque apropiado a las decisiones sobre inventarios (Mentalidad Logística).
2. El sistema de gestión
Uno de los factores que mayor influencia tiene sobre el nivel de inventarios es el tiempo de entrega o tiempo de reposición, ya que dependiendo de su magnitud será necesario mayor o menor nivel de existencias para satisfacer la demanda durante ese tiempo de entrega. Existe una tendencia generalizada a responsabilizar a la gestión de los proveedores por los retrasos que ocurren en la entrega de los materiales. Lo primero que toda empresa debe tener en cuenta es que su propio sistema de compras es parte muy importante del tiempo total del ciclo de pedido-entrega, por lo que se requiere una revisión detallada de los procesos internos para producir mejoras significativas en la reducción de ese tiempo. Cuando un artículo es utilizado, el sistema de gestión de inventarios debe reconocer rápidamente su movimiento y tomar las acciones correctivas, ya que un sistema de reposición lento incrementará el nivel de existencias.
3. El número de almacenes
La necesidad de disponer de repuestos en diferentes localizaciones implica tener diferentes almacenes y mientras más almacenes existan para almacenar un artículo, mayor será la cantidad almacenada. A menor número de almacenes, menor será el nivel de existencias. Se puede logra ahorros importantes centralizando el almacenamiento.
4. Punto de pedido elevado
Un punto de pedido es el nivel de existencias para el cual se debe hacer un pedido para atender la demanda normal y sus posibles fluctuaciones durante el tiempo de entrega y este debe ser ajustado debido a cambios en la demanda o en la cadena de suministro. Un punto de pedido elevado trae como consecuencia un nivel promedio de existencias también elevado. Es muy común que los niveles máximos y mínimos se fijen de forma empírica y de manera similar para una gama amplia de artículos, sin embargo, no todos presentan el mismo comportamiento y por tanto los parámetros del inventario deberían determinarse individualmente artículo por artículo.
5. Tamaño de pedido elevado
Pedidos grandes también mantiene un elevado nivel promedio de existencias. Existe una tendencia generalizada de pedir en cantidades superiores a las realmente necesarias debido a la preocupación del departamento de mantenimiento con respecto a la eficiencia del departamento de compras y este por su parte quiere evitar las compras repetitivas o muy frecuentes del mismo artículo. Grandes pedidos se justifican solamente cuando los costos logísticos son elevados. El avance tecnológico permite minimizar las cantidades a pedir ya que la gestión de compras se hace a muy bajos costos y con gran rapidez. El análisis de la cantidad económica de pedido se justifica siempre que el artículo tenga una alta demanda.
6. Desconocimiento de la obsolescencia
La existencia de artículos obsoletos es muy común en todos los almacenes, reconocerlos no es una tarea fácil por la resistencia a deshacerse de ellos debido a la “posibilidad” de necesitarlos en algún momento o sencillamente que su desincorporación del inventario resulta ser un procedimiento tan complicado que se prefiere olvidarlos. La mayoría de los sistemas de gestión de inventarios manejan artículos vigentes y los obsoletos generalmente pasan desapercibidos trayendo como consecuencia una valoración irreal del inventario obteniéndose resultados financieros no acordes con la realidad además de tomar decisiones gerenciales erradas.
7. Variedad y complejidad de los artículos
En la mayoría de las empresas existe equipos y maquinarias con diferentes edades tecnológicas y de diferentes orígenes, esto crea la necesidad de mantener en stock una gran variedad de repuestos con características muy diversas en cuanto a precios, oferta, tasa de utilización y criticidad lo que obliga a determinar requisitos particulares para cada artículo, de lo contrario se podría originar un nivel de existencias marcado por las necesidades de los artículos con mayor frecuencia de utilización. Nunca se debe aplicar la misma “receta” y se debe hacer un esfuerzo para minimizar la variedad y complejidad de los materiales a mantener almacenados.
8. Proyectos y situaciones especiales
Este es uno de los factores que más promueve el exceso de inventarios, especialmente cuando se ejecutan proyectos de mantenimiento de gran envergadura, como es el caso de las paradas de planta, en las que está en riesgo gran cantidad de dinero, no solo por el costo del proyecto sino por la paralización de la producción. En estos casos, el compromiso de terminar el proyecto en el tiempo previsto sin ningún tipo de contratiempo hace que exista una tendencia a comprar más de lo necesario para evitar el riesgo de interrumpir las actividades por falta de algún material y con la justificación de que cualquier sobrante podrá ser utilizado en otra oportunidad. Estos eventos no pueden convertirse en una excusa para mantener inventarios en exceso, por lo que se debe determinar la demanda con mucha precisión y comprar justamente lo que se necesita.
9. Requerimientos de operaciones logísticas
Algunos sistemas logísticos, tanto de clientes como de proveedores, tienen procesos de compras que establecen cantidades mínimas “eficientes” para el esfuerzo (manejo, tiempo, transporte, precio) involucrado en la adquisición de productos, es decir, se tiene un nivel mínimo de existencias determinado por la cadena de suministros y no por la demanda real.
Autor: José Contreras Márquez
Venezuela
Instructor de INGEMAN, CONSCIOUS RELIABILITY y ASME para Latinoamérica.
Correo: jocomarquez@yahoo.com y jocomarquez@gmail.com
https://ve.linkedin.com/in/josecontrerasmarquez
Consultor e instructor de temas sobre Gestión del Mantenimiento, especialmente en la búsqueda de maximizar su eficiencia. Con amplia experiencia industrial y académica. Autor de los libros “Sistemas de Medición del Desempeño en Mantenimiento basados en Indicadores de Gestión” y “Gestión y Optimización de Inventarios para Mantenimiento”. Desarrollador de software “OPTIM” para determinar parámetros claves de los inventarios para materiales de alta y baja rotación. También creador de las guías de auditoría para la gestión del trabajo, proyectos e inventarios de mantenimiento. Director de www.mantenimientoeficiente.com.
Dinos qué te ha parecido el artículo
Artículos recomendados
¿En qué consiste el Mantenimiento?

Vibraciones Mecánicas

Las Revoluciones Industriales en el Mundo (II Parte)

Metodología Propuesta para Toma de Decisión de Inspección de Líneas de Flujo de Crudo Basado en Modelos Estadísticos de Criticidad

Publica tu artículo en la revista #1 de Mantenimiento Industrial
Publicar un artículo en la revista es gratis, no tiene costo.
Solo debes asegurarte que no sea un artículo comercial.
¿Qué esperas?
O envía tu artículo directo: articulos@predictiva21.com
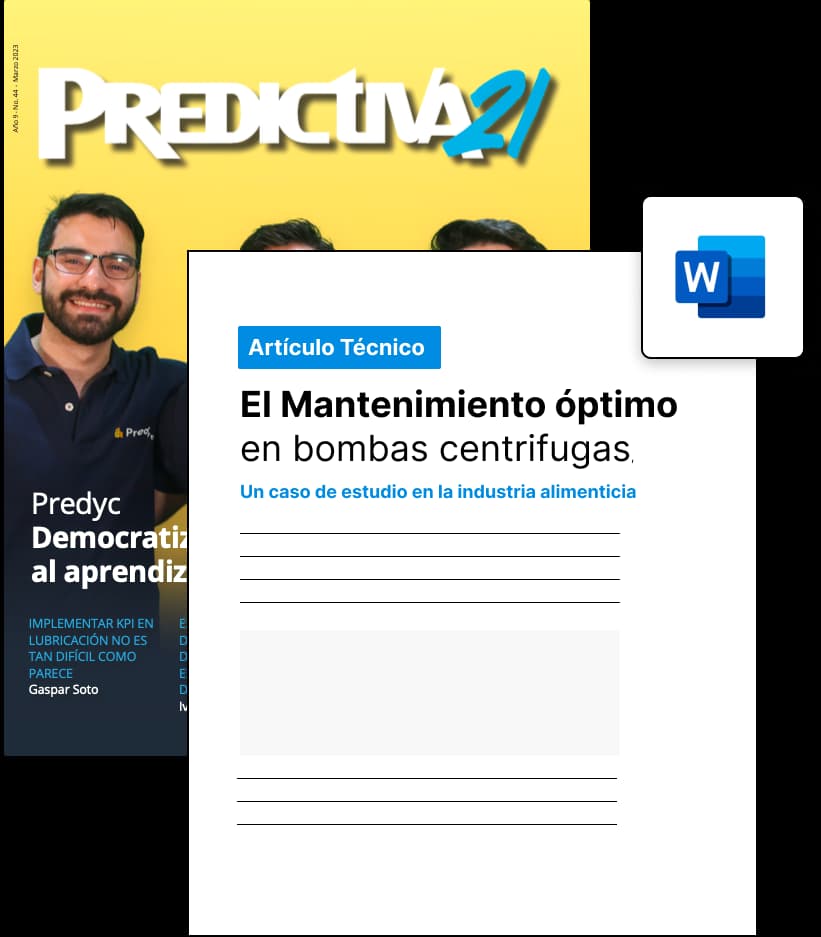
Factores que promueven el exceso de inventarios de mantenimiento
Articulo 12 de junio de 2021Es muy común que muchas empresas no adviertan los continuos cambios que ocurren en su entorno y por esta razón quedan rezagadas en cuanto a la posibilidad de implementar mejoras a su gestión operacional.
Existen diversas razones por las cuales se originan inventarios excedentarios en las industrias, Slater (2007) ha definido doce (12) razones ubicándolas en dos grupos principales, las que se relacionan con los cambios no advertidos del entorno empresarial y las relacionadas con la estructura organizacional y el modelo gerencial propios de la empresa particular.
Al revisar las oportunidades para reducir la inversión en inventarios es importante comprender los cambios que han ocurrido y aún no han sido reconocidos y visualizar los cambios potenciales que ocurrirán en el futuro. Con el transcurrir del tiempo y la experiencia acumulada, usted comprenderá mucho mejor los requerimientos de la demanda, haya mejorado su cadena de suministros y los proveedores estén mejor preparados para ofrecerle un mejor nivel de servicio.
Dentro del primer grupo, razones que se relacionan con los cambios no advertidos del entorno empresarial, están las siguientes:
1. Las estimaciones iniciales de mínimos y máximos no han sido revisadas a menos que haya ocurrido una rotura de stock, sin embargo, puede haber cambiado la tasa de utilización que implique la necesidad de establecer nuevos parámetros en las políticas de manejo de inventarios.
2. No ha habido cambios en las políticas de gestión de inventarios debidos a mejoras ocurridas en la cadena de suministros. Esta situación se presenta cuando la misma empresa y sus proveedores han mejorado la cadena de suministros, manifestándose en la disminución del tiempo de entrega, la implementación de políticas de consignación o simplemente que se haya producido un incremento de la oferta, no siendo aprovechada para hacer ajustes hacia la reducción de los niveles históricos del nivel de inventarios.
3. No se ha realizado inversiones asociadas a minimizar la inversión en inventarios. Los avances de la informática y las telecomunicaciones permiten a la empresa disponer de nuevas herramientas a nivel de software y equipos para hacer mucho más eficiente la gestión de materiales.
El segundo grupo de razones que promueven el exceso de inventarios relacionadas con la propia empresa, de acuerdo a Slater (2007), queda conformado de la siguiente manera:
1. Responsabilidades desalineadas
A esta situación también se le asocia con lo que en logística se conoce como “Gestión fragmentada del flujo de materiales” y se presenta cuando los diferentes departamentos buscan obtener los mejores resultados de manera individual y no se toman decisiones de manera integral que contribuyan a maximizar los beneficios de la organización como un todo. Desde el punto de vista del mantenimiento se pretende agregar artículos al inventario sin tomar en cuenta el impacto financiero de esa decisión. Contrariamente, es muy común que los departamentos de compras y finanzas, sin otro criterio que el financiero, restrinjan las compras sin considerar el impacto operacional de este tipo de decisiones.
Es de naturaleza humana maximizar los resultados personales (departamentales), pero alineando las responsabilidades y autoridades se puede lograr dar el enfoque apropiado a las decisiones sobre inventarios (Mentalidad Logística).
2. El sistema de gestión
Uno de los factores que mayor influencia tiene sobre el nivel de inventarios es el tiempo de entrega o tiempo de reposición, ya que dependiendo de su magnitud será necesario mayor o menor nivel de existencias para satisfacer la demanda durante ese tiempo de entrega. Existe una tendencia generalizada a responsabilizar a la gestión de los proveedores por los retrasos que ocurren en la entrega de los materiales. Lo primero que toda empresa debe tener en cuenta es que su propio sistema de compras es parte muy importante del tiempo total del ciclo de pedido-entrega, por lo que se requiere una revisión detallada de los procesos internos para producir mejoras significativas en la reducción de ese tiempo. Cuando un artículo es utilizado, el sistema de gestión de inventarios debe reconocer rápidamente su movimiento y tomar las acciones correctivas, ya que un sistema de reposición lento incrementará el nivel de existencias.
3. El número de almacenes
La necesidad de disponer de repuestos en diferentes localizaciones implica tener diferentes almacenes y mientras más almacenes existan para almacenar un artículo, mayor será la cantidad almacenada. A menor número de almacenes, menor será el nivel de existencias. Se puede logra ahorros importantes centralizando el almacenamiento.
4. Punto de pedido elevado
Un punto de pedido es el nivel de existencias para el cual se debe hacer un pedido para atender la demanda normal y sus posibles fluctuaciones durante el tiempo de entrega y este debe ser ajustado debido a cambios en la demanda o en la cadena de suministro. Un punto de pedido elevado trae como consecuencia un nivel promedio de existencias también elevado. Es muy común que los niveles máximos y mínimos se fijen de forma empírica y de manera similar para una gama amplia de artículos, sin embargo, no todos presentan el mismo comportamiento y por tanto los parámetros del inventario deberían determinarse individualmente artículo por artículo.
5. Tamaño de pedido elevado
Pedidos grandes también mantiene un elevado nivel promedio de existencias. Existe una tendencia generalizada de pedir en cantidades superiores a las realmente necesarias debido a la preocupación del departamento de mantenimiento con respecto a la eficiencia del departamento de compras y este por su parte quiere evitar las compras repetitivas o muy frecuentes del mismo artículo. Grandes pedidos se justifican solamente cuando los costos logísticos son elevados. El avance tecnológico permite minimizar las cantidades a pedir ya que la gestión de compras se hace a muy bajos costos y con gran rapidez. El análisis de la cantidad económica de pedido se justifica siempre que el artículo tenga una alta demanda.
6. Desconocimiento de la obsolescencia
La existencia de artículos obsoletos es muy común en todos los almacenes, reconocerlos no es una tarea fácil por la resistencia a deshacerse de ellos debido a la “posibilidad” de necesitarlos en algún momento o sencillamente que su desincorporación del inventario resulta ser un procedimiento tan complicado que se prefiere olvidarlos. La mayoría de los sistemas de gestión de inventarios manejan artículos vigentes y los obsoletos generalmente pasan desapercibidos trayendo como consecuencia una valoración irreal del inventario obteniéndose resultados financieros no acordes con la realidad además de tomar decisiones gerenciales erradas.
7. Variedad y complejidad de los artículos
En la mayoría de las empresas existe equipos y maquinarias con diferentes edades tecnológicas y de diferentes orígenes, esto crea la necesidad de mantener en stock una gran variedad de repuestos con características muy diversas en cuanto a precios, oferta, tasa de utilización y criticidad lo que obliga a determinar requisitos particulares para cada artículo, de lo contrario se podría originar un nivel de existencias marcado por las necesidades de los artículos con mayor frecuencia de utilización. Nunca se debe aplicar la misma “receta” y se debe hacer un esfuerzo para minimizar la variedad y complejidad de los materiales a mantener almacenados.
8. Proyectos y situaciones especiales
Este es uno de los factores que más promueve el exceso de inventarios, especialmente cuando se ejecutan proyectos de mantenimiento de gran envergadura, como es el caso de las paradas de planta, en las que está en riesgo gran cantidad de dinero, no solo por el costo del proyecto sino por la paralización de la producción. En estos casos, el compromiso de terminar el proyecto en el tiempo previsto sin ningún tipo de contratiempo hace que exista una tendencia a comprar más de lo necesario para evitar el riesgo de interrumpir las actividades por falta de algún material y con la justificación de que cualquier sobrante podrá ser utilizado en otra oportunidad. Estos eventos no pueden convertirse en una excusa para mantener inventarios en exceso, por lo que se debe determinar la demanda con mucha precisión y comprar justamente lo que se necesita.
9. Requerimientos de operaciones logísticas
Algunos sistemas logísticos, tanto de clientes como de proveedores, tienen procesos de compras que establecen cantidades mínimas “eficientes” para el esfuerzo (manejo, tiempo, transporte, precio) involucrado en la adquisición de productos, es decir, se tiene un nivel mínimo de existencias determinado por la cadena de suministros y no por la demanda real.
Autor: José Contreras Márquez
Venezuela
Instructor de INGEMAN, CONSCIOUS RELIABILITY y ASME para Latinoamérica.
Correo: jocomarquez@yahoo.com y jocomarquez@gmail.com
https://ve.linkedin.com/in/josecontrerasmarquez
Consultor e instructor de temas sobre Gestión del Mantenimiento, especialmente en la búsqueda de maximizar su eficiencia. Con amplia experiencia industrial y académica. Autor de los libros “Sistemas de Medición del Desempeño en Mantenimiento basados en Indicadores de Gestión” y “Gestión y Optimización de Inventarios para Mantenimiento”. Desarrollador de software “OPTIM” para determinar parámetros claves de los inventarios para materiales de alta y baja rotación. También creador de las guías de auditoría para la gestión del trabajo, proyectos e inventarios de mantenimiento. Director de www.mantenimientoeficiente.com.
Dinos qué te ha parecido el artículo
Artículos recomendados
Educación Formal para el Mantenimiento

Confiabilidad y Mantenibilidad en el Ciclo de Vida del Activo

¿Qué tal emprender un negocio de Outsourcing de Mantenimiento?

Curso TPM y lo que aprenderás en uno

Publica tu artículo en la revista #1 de Mantenimiento Industrial
Publicar un artículo en la revista es gratis, no tiene costo.
Solo debes asegurarte que no sea un artículo comercial.
¿Qué esperas?
O envía tu artículo directo: articulos@predictiva21.com
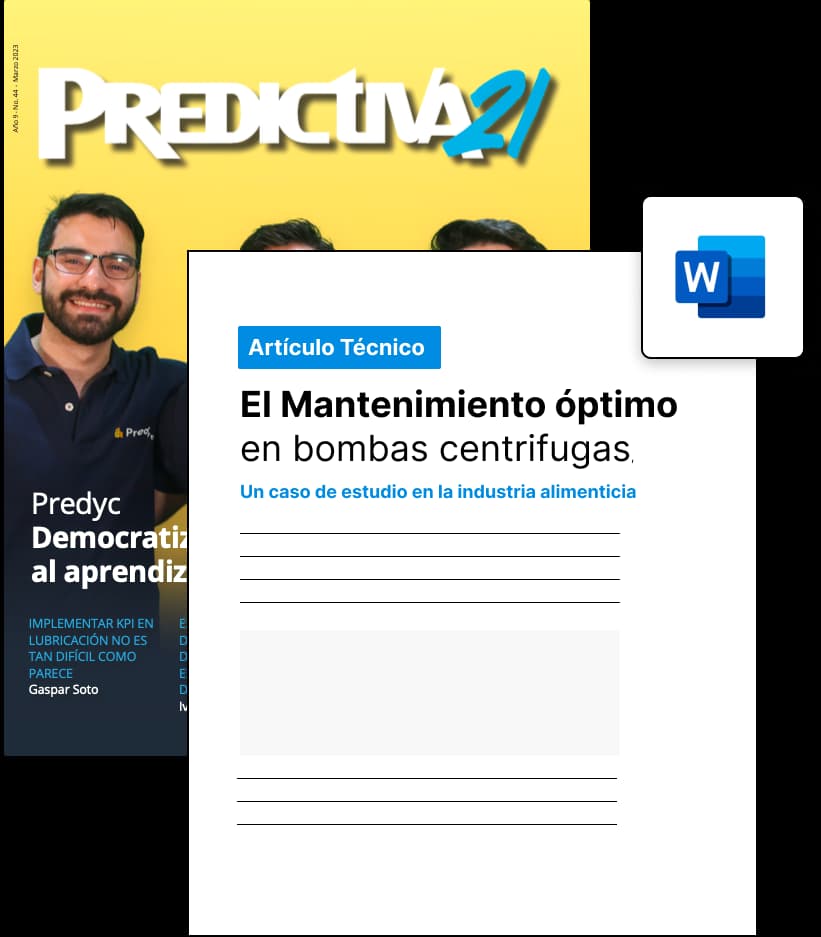