La fiabilidad 4.0 como parte del proceso de gestión de activos: Caso de estudio de una plataforma de petróleo
Articulo21 de junio de 2020
Resumen
Muchos activos físicos en el mundo no alcanzan un alto rendimiento no por la mala gestión de mantenimiento, o falta de cultura de fiabilidad, sino por el bajo desempeño en fiabilidad de equipos críticos.
Para resolver esta cuestión, proponemos la revolución de la fiabilidad 4.0 integrada al proceso de gestión de activos, que considera el monitoreo del desempeño del activo físico automático basado en los datos de fallas insertados en el sistema de reporte de fallas y acciones correctivas (FRACAS).
1. Introducción
Muchos activos físicos en el mundo no alcanzan un alto rendimiento no por la mala gestión de mantenimiento, o falta de cultura de fiabilidad, sino por el bajo desempeño en fiabilidad de equipos críticos.
Durante décadas, la gestión de activos físicos y la implementación de ingeniería de fiabilidad aplicada al monitoreo del desempeño de activos físicos se han hecho por separado.
Aunque algunas soluciones para la gestión de activos físicos presentan herramientas de ingeniería de fiabilidad como el crecimiento de la fiabilidad (CROW AMSSA) y el análisis de vida útil, el mismo concepto prevalece.
El concepto de evaluación de desempeño de fiabilidad basado en crecimiento de fiabilidad y análisis de vida útil todavía se basa en la recopilación de datos y aplicación de métodos estadísticos complejos.
Debido a que este hecho es una gran dificultad para técnicos de mantenimiento, operadores e incluso para ingenieros, el rendimiento de equipos ha sido evaluado de forma simple por indicadores como MTTF o tasas de fallo constante, que conduce a decisiones erróneas en relación con la decisión de alcanzar el rendimiento y la definición de tiempos de inspección.
Para resolver esta cuestión, proponemos la revolución de la fiabilidad 4.0 integrada al proceso de gestión de activos, que considera el monitoreo del desempeño del activo físico automático basado en los datos de fallas insertados en el sistema de reporte de fallas y acciones correctivas (DE LOS MÁS DÉBILES).
2. Gestión de Activos Físicos
Antes de presentar el concepto y los beneficios de la revolución de la fiabilidad 4.0, es necesario entender el sistema y proceso de gestión de activos físicos en el cual el monitoreo del desempeño.
El sistema de gestión de activos es un conjunto de actividades administrativas cuyo objetivo es apoyar la gestión del activo físico.
Basado en la norma ISO 55001, el sistema de gestión de activos debe ser iniciado por la comprensión del plan estratégico de negocio de la organización, que considera los requisitos legales, las demandas de clientes y stakeholders y así, tal plan de negocio puede traducirse en un plan estratégico de gestión de activos (SAMP).
A partir de la definición del plan estratégico de gestión de activos, algunos elementos son fundamentales para la completa implantación del sistema de gestión de activos como:
- Contexto de la organización
- Liderazgo
- La planificación
- Soporte
- Operación
- Análisis de la performance
- Mejora continua
El Contexto Organizacional tiene como objetivo la configuración del plan estratégico de gestión de activos basado en el plan de negocio de la organización, que considera las demandas externas, capacidad interna, así como las exigencias de stakeholders. El producto final será el plan estratégico de gestión de activos.
Liderazgo tiene como objetivo asegurar el compromiso de líderes en todos los niveles organizativos, definición de la política del sistema de gestión de activos, implantación del plan estratégico de gestión de activos, así como la definición de las responsabilidades en todos los niveles del sistema de gestión de activos.
La planificación tiene como objetivo definir los riesgos en la implantación de la gestión de activos, así como los riesgos operativos, que puedan impedir el logro de los objetivos estratégicos definidos del plan estratégico de gestión de activos.
El Soporte tiene como objetivo definir los recursos necesarios para la implantación del sistema de gestión de activos, así como, asegurar que los involucrados tengan conciencia de su papel en la gestión de activos. Además, es necesario establecer el proceso de comunicación y los procedimientos de gestión de la información dentro del sistema de gestión de activos.
La Operación tiene como objetivo planificar y controlar todos los aspectos operativos para garantizar el logro de los indicadores de rendimiento de los activos físicos, así como la efectividad de todas las actividades relacionadas con el sistema de gestión de activos.
El Análisis de desempeño tiene como objetivo evaluar el desempeño de los activos físicos, así como el resultado de auditorías del sistema de gestión de activos por los líderes.
La mejora continua tiene como objetivo la implantación de las acciones necesarias para el tratamiento de las irregularidades relativas a las auditorías del sistema de gestión de activos, así como las acciones de mejora para alcanzar el rendimiento deseado de los activos físicos y los objetivos estratégicos de la gestión de activos.
La figura 1 siguiente muestra el ciclo de gestión de activos basado en al gestión de activos.

Fuente: ISO 55000:2014.
Aunque el sistema de gestión de activos tiene su importancia para garantizar las actividades relativas a la gestión del activo físico de forma eficiente, la implantación de la norma ISO 55001 no garantiza por sí sola el alto rendimiento de los activos físicos.
3. Proceso de gestión de activos físicos
Además de la implantación del sistema de gestión de activos, es necesario definir el proceso de gestión de activos de forma que la gestión de activos forme parte de la rutina operativa de la organización. Por lo tanto, todas las etapas del proceso de gestión de activos físicos deben tener en cuenta a todos los involucrados en la consecución y garantía del alto rendimiento de los activos físicos.
Para que el proceso de gestión de activos físicos sea efectivo, se necesita un sistema centralizado de información que permita a todos los participantes en diferentes niveles organizativos acceder a toda la información y permita a los líderes tomar decisiones rápidas basadas en datos reales y fiables.
Además, es necesario equilibrar las acciones de mitigación de riesgos operativos con los límites de presupuesto y enfocarse en acciones que traigan el mejor costo/beneficio para la organización. Así, el proceso de gestión de activos físicos tiene los siguientes pasos:
- Monitoreo del desempeño & pronóstico de salud del activo (PHM)
- Gestión de mantenimiento preventivo, inspección y órdenes de servicio
- Informe de fallos y acciones correctivas
- Sistema de Información Geográfica (GIS)
- Gestión de fallos
- Gestión del riesgo operativo y coste/beneficio de las acciones de mitigación
- Gestión de la integridad de los activos centrada en los elementos críticos de seguridad
- Gestión de la rutina basada en las actividades de los equipos
- Aprendizaje de la organización
- Revisión de desempeño y mejora continua
La figura 2, a continuación, muestra la gestión del proceso de activos aplicada a través de una solución SaaS.

Fuente: Integrity PRO SaaS software.
Como el enfoque del texto es la fiabilidad 4.0, a partir de ahora nos centraremos en el monitoreo del desempeño del activo físico.
El monitoreo de desempeño se da de forma reactiva y preventiva. El modelo reactivo se produce cuando la verificación de rendimiento considera los fallos y eventos ocurridos en un período de tiempo.
La fiabilidad 4.0 es un tipo de monitoreo de desempeño reactivo, que comienza en el nivel de sistema con la medición de la eficiencia de producción y disponibilidad operativa, pasando a nivel de equipos y componentes para medir la disponibilidad operativa y la fiabilidad de los equipos.
Aunque este es el foco del texto, reconocemos la importancia de la medición de la performance basado en una metodologia preventiva, que tiene como centro la medición de la degradación de equipos y componentes a través del mantenimiento predictivo, o como hemos propuesto en nuestro proceso de gestión de activo físico, vía pronóstico de salud del equipo (PHM).
De hecho, incluso la fiabilidad 4.0 es un monitoreo de desempeño reactivo, es posible al instante verificar el cumplimiento de requisitos de garantía de fiabilidad entre otras ventajas.
4. Revolución de la Fiabilidad 4.0
El programa de Ingeniería de fiabilidad debe ser implantado desde la fase conceptual del activo físico para definir los requisitos de fiabilidad de los sistemas y equipos y la selección de proveedores, que puedan entregar equipos de alta performance en fiabilidad.
Desafortunadamente, esto no ocurre en muchos casos dando lugar a un bajo rendimiento en la fiabilidad de los equipos críticos, que afecta el rendimiento de los sistemas (activos físicos).
Durante la fase de operación, la evaluación del rendimiento del equipo es esencial para la correcta toma de decisiones en relación con el mejor intervalo de tiempo para inspección y mantenimiento preventivo, así como la verificación y validación del cumplimiento de los requisitos de fiabilidad.
En muchas organizaciones, el concepto de fiabilidad y la verificación y validación de la fiabilidad se aplican erróneamente. Esto a menudo lleva a muchos líderes a tomar decisiones equivocadas. Estos hechos ocurren por las siguientes causas:
- Comprensión incorrecta del concepto de fiabilidad.
- Incorrecta definición de indicadores de rendimiento como MTTF y constante tasa de fallas.
- Falta de un sistema de fallas y acciones correctivas consistentes (FRACAS).
- Falta de implantación de un programa de fiabilidad y mantenimiento desde la fase de diseño y diseño.
- Falta de inversión en formación en Ingeniería de fiabilidad.
- Pesada rutina de mantenimiento y operación causando falta de tiempo para actividades de ingeniería de fiabilidad.
La supervisión de la gestión de activos a través del rendimiento de la fiabilidad de los equipos debe integrarse al sistema FRACAS y predecir automáticamente el rendimiento de fiabilidad. De esta manera, el primer paso es la definición de los parámetros de la función Weibul y luego la definición de los siguientes índices de performance tales como:
- Fiabilidad en un tiempo de operación específico.
- Disponibilidad operativa de los equipos.
- Siguiente tiempo de fallo (basado en el modelo CROW AMSAA).
- Tendencia y proyección del MTBF (basado en el modelo CROW AMSAA).
- Tendencia y proyección de la función de intensidad de fallos (basado en el modelo CROW AMSAA).
- Tiempo esperado de reparación (MTTR).
5. Estudio de caso de la implantación de la Fiabilidad 4.0 en una plataforma de petróleo
El estudio de caso presentado fue aplicado en la implantación del sistema integrado de gestión de activos en una plataforma de petróleo en una empresa en África. Al igual que la gestión de activos físicos, la supervisión de la gestión de activos a través del rendimiento de la fiabilidad de los equipos debe integrarse al sistema FRACAS y predecir automáticamente el rendimiento de fiabilidad. Por lo tanto, una vez que los datos han sido introducidos en el sistema de fallos por los técnicos de mantenimiento y los operadores, el primer paso de la fiabilidad 4.0 es la definición automática de los parámetros de la función Weibull, basados en pruebas estadísticas predefinidas, y posteriormente, la definición de los índices de fiabilidad y crecimiento de la fiabilidad según se ha definido anteriormente. Las figuras 3.1,3.2,3.3 y 3.4 abajo muestran a una bomba de una plataforma: (b=5,17 e h=9472,58 (horas)).
Uno de los puntos más importantes en la gestión de activos y la implantación de Confiabilidad 4.0 es la integración de estos sistemas con la rutina operativa. De esta forma, es muy importante que sea posible el rápido acceso de equipos críticos y predicado de la performance de confiabilidad de tales equipos. Así, la figura 3.1 muestra la visualización de los equipos críticos disponibles para todo el equipo de mantenimiento y la producción para comprobar el rendimiento de la fiabilidad 4.0. Como se muestra en la figura 3.1, depende de la importancia de la maquinaria de los diferentes colores se señalan. El color rojo muestra equipos críticos con bajo rendimiento en confiabilidad, el color naranja muestra equipos con nivel de degradación moderado con posible fallo y el color verde muestra quioscos que apeasr de un inicial.

Fuente: El autor.
Al seleccionar uno de los equipos mostrados en el mapa electrónico es posible verificar informaciones relacionadas con los equipos como su Descripción, tag, Sistema, subsistema, estado y estado de salud. El estado se puede definir como LTU «Largo Term unavailable», que significa, un período de más de una semana no disponible. o SPF «Single Point of Failure», que significa, equipos que en caso de fallo causan indisponibilidad del sistema. En la esquina derecha se define el estado de salud, «Equipment Health», que indica el nivel de degradación en diferentes colores como muestra la figura 3.2.

Fuente: El autor.
Al seleccionar uno de los equipos en el mapa de equipo crítico es posible la comprobación automática de la fiabilidad y el crecimiento de cada equipo. La figura 3.3 muestra la predicación de los parámetros de PDF Weibull 2P, fiabilidad, disponibilidad operativa, MTTR, MTTF (basado en crecimiento de fiabilidad), tasa de fallo (basado en crecimiento de fiabilidad).

Fuente: Integrity PRO software.
Por lo general, para llevar a cabo LDA, es necesario tener datos históricos al menos en el nivel del equipo. Muchas empresas, incluidos los proveedores de equipos en la industria del petróleo y el gas, y también en otras industrias, no tienen una base de datos organizada con datos históricos de sus equipos. Por lo tanto, el primer paso, antes de la LDA, es recoger los datos de fallo disponibles. La situación ideal es contar con una base de datos muy estructurada, como el informe de fallos y las medidas correctoras (FRACAS). El primer paso antes de iniciar la metodología LDA es entender el concepto de la función de densidad de probabilidad (PDF). Los PDF describen gráficamente la posibilidad de que ocurran eventos a lo largo del tiempo; en el caso del análisis de datos de vida del equipo, esto significa que el tiempo de falla o reparación se produce con el tiempo. Los pasos de la metodología LDA son:
- Primer paso: Para definir la muestra de datos (agrupados o no agrupados).
- Segundo paso: Para definir el tipo de datos (Censurado o completo).
- Tercer Paso: Para realizar la bondad del análisis de ajuste (Parcela, Regresión, MLE, otros).
- Cuarto Paso: Definir el parámetro PDF.
- Quinto paso: Para predecir la fiabilidad, probabilidad de fallo y la función de tasa de fallo.
Basado en la Fiabilidad 4.0, todos estos pasos se realizan automáticamente en base a la configuración adecuada para el tipo de activo físico. Por lo tanto, la fiabilidad 4.0 permite a todos los empleados entender los resultados de fiabilidad basados en la predicción auomática sin la necesidad de tener un profundo conocimiento de estadísticas y la fiabilidade, y sin la necesidad de utilizar otro software para predicción de fiabilidad.

Fuente: Integrity PRO software.
Además del predicado de la fiabilidad, el predicado del crecimiento de la confiabilidad también se calcula así como los gráficos de fiabilidad, probabilidad de fallas, tasa de fallo, tendencia de MTTF, tendencia de tasa de falla y número esperado de fallas como muestran las figuras 3.3 y 3.4. La metodología de Análisis de Crecimiento de Confiabilidad se aplica a la evaluación de equipos durante la operación y se basa únicamente en el Modelo Crow AMSSA. Este modelo fue introducido por el Dr. Larry H. Crow en 1974, es un modelo estadístico que utiliza el parámetro de distribución Weibull para describir la relación entre el tiempo acumulado entre el fallo y el tiempo de prueba. Este enfoque se aplica en el análisis de crecimiento de la fiabilidad para mostrar el efecto de las acciones correctoras sobre la fiabilidad cuando se está desarrollando un producto o incluso en sistemas reparables durante la fase de funcionamiento. De este modo, siempre que se introducen mejoras durante las pruebas (test-fix-test), el modelo Crow AMSAA se utiliza para predecir el crecimiento de la fiabilidad y el número acumulativo esperado de fallos. El comportamiento de crecimiento defiabilidad puede aumentar/disminuir o permanecer constante con el tiempo. De hecho, depende de los valores β que es un parámetro de forma de la función de falla de intensidad en el modelo Crow AMSAA. Por lo tanto, en este modelo cuando β > 1, la fiabilidad disminuye con el tiempo porque la intensidad de fallo está aumentando, o en otras palabras, las acciones del producto correctivo no están mejorando el producto. Cuando β < 1, la intensidad del fallo está disminuyendo con el tiempo, o en otras palabras, las acciones correctivas del producto están mejorando la fiabilidad del producto.Cuando β = 1, el producto se comporta como si no se hubiera tomado ninguna acción correctiva y la intensidad de la falla es constante en el tiempo. Es importante tener en cuenta que la β del modelo Crow-AMSAA describe un comportamiento de falla de intensidad y no tiene relación con el parámetro de la forma de distribución de Weibull.
El origen de los datos de fallos y reparación se produce por el sistema FRACAS. De esta manera, a través de una ficha electrónica de falahs que puede ser accedida a través del teléfono móvil o vía computada, las fallas pueden ser insertadas en el sistema y a partir de más de tres datos cuantitativos la fiabilidad y el crecimiento de la fiabilidad se calculan automáticamente. El Sistema FRACAS Electrónico está basado en FMEA, que definen los modos de falla las causas y consecuencias así como los modos de detección de fallas. Tales informaciones son estandarizadas e insertadas en el FRACAS.
De esta manera, los medios de operación y los operadores pueden abrir una ficha de fallo de forma simple y rápida. La figura 3.5 muestra la primera ficha electrónica del FRACAS. Después de completar esta ficha, los supervisores revisarán los datos y aprobarán análisis. Luego se dará el análisis de la causa raíz y la definición de las acciones mitigadoras para la apertura de la orden del servicio. Todo este proceso es parte del proceso de gestión de activos (Integrity Pro Saas). En el monento no vamos a detallar el sitema FRACAS, pues el objetivo de este paper es demostrar la fiabilidad 4.0, pero es importante demostrar también el origen de los datos para los cálculos de confiabilidad que se da por el sistema FRACAS.

Fuente: Integrity PRO software.

Fuente: Integrity PRO software.
Con el objetivo de verificar y validar los resultados de fiabilidad 4.0 presentados en el software Integrity pro, el renombrado software Weibull ++ de Reliasoft fue aplicado utilizando los mismos intervalos de fallo y métodos estadísticos.
La figura 4 muestra el resultado de la estimación de los parámetros de distribución Weibull 2p calculados por el software Weibul que fueron: b=5,47 e h=9423 (horas), bien próximos a los valores calculados por la solución fiabilidad 4.0 en el software Integrity pro.

Fuente: Weibull ++ software.
Finalmente, una de las grandes ventajas de la fiabilidad 4.0 es la posibilidad de generar automáticamente una base de datos de fiabilidad como muestra la figura 5. De esta manera, la plataforma de petróleo pasará a tener su propia base de datos de fiabilidad en tiempo real. Dicha base de datos puede utilizarse como base para estudios de fiabilidad, seguridad y análisis de riesgos en la fase de proyecto y operativa. Esto elimina el uso de bases de datos genéricas como OREDA y AICHE.

Fuente: Integrity PRO software.
6. Conclusión
El objetivo del estudio fue demostrar la revolución de la fiabilidad 4.0 a través de un estudio de caso práctico aplicado a la industria del petróleo.
Mediante la verificación y validación realizada por el software Weibull ++ fue posible verificar la consistencia de los resultados producidos automáticamente por la fiabilidad 4.0. De esta forma, los principales beneficios de la fiabilidad 4.0 son:
- Integración de herramientas de ingeniería de fiabilidad como FRACAS, análisis de vida útil y análisis de crecimiento de fiabilidad en el proceso de gestión de activos.
- Predicción de fiabilidad y crecimiento de fiabilidad basada en datos reales con resultados fiables.
- Posibilidad de verificación de la performance de fiabilidad por cualquiera de los integrantes del proceso de gestión de activos físicos en línea de forma automática, que permite una rápida toma de decisiones.
- Eliminación de la necesidad de cálculos complejos y uso de software auxiliar para la predicción de la fiabilidad y el crecimiento de la fiabilidad.
- Reducción drástica del tiempo de cálculo de performance de fiabilidad.
- Reducción de la inversión en software y entrenamientos en análisis de vida útil.
Una de las limitaciones de las predicciones de desempeño en fiabilidad es la necesidad de datos de fallas para posteriormente predecir la fiabilidad o la tendencia de la disminución del intervalo entre fallas.
Sin embargo, como se ha dicho anteriormente, el pronóstico de salud de los activos físicos es parte del proceso propuesto de gestión de activos físicos y permite verificar la degradación de los activos físicos cuando éstos operan por encima de los límites operativos. Ese tema será discutido en un próximo artículo.
7. Referencias
- [1] «Gas and Oil Reliability Engineering: Modelling and Simulation. Second edition, Elsevier ISBN: 9780123919144, 26 May2016).
- [2] RAMS and LCC engineering applied to railway industry: Analysis, Modelling and Optimization. 18-04-2018.Amazon. ISBN-13: 978-1986524704.
Autor: Eduadardo Calixto
Eduardo Calixto Consulting, Alemanha
Correo: ec@eduardocalixto.com
Dinos qué te ha parecido el artículo
Artículos recomendados
Entrevista con Blas Galván

Aplicación de la Metodología de Análisis Causa Raíz. Caso: Fallas Recurrentes del Sistema de Distribución Eléctrica en 34,5kv de un Campo Petrolero

Cosentino digitaliza su mantenimiento predictivo: claves y aprendizajes

Entrevista Eduardo Calixto, Fundador y CEO de ECC

Publica tu artículo en la revista #1 de Mantenimiento Industrial
Publicar un artículo en la revista es gratis, no tiene costo.
Solo debes asegurarte que no sea un artículo comercial.
¿Qué esperas?
O envía tu artículo directo: articulos@predictiva21.com
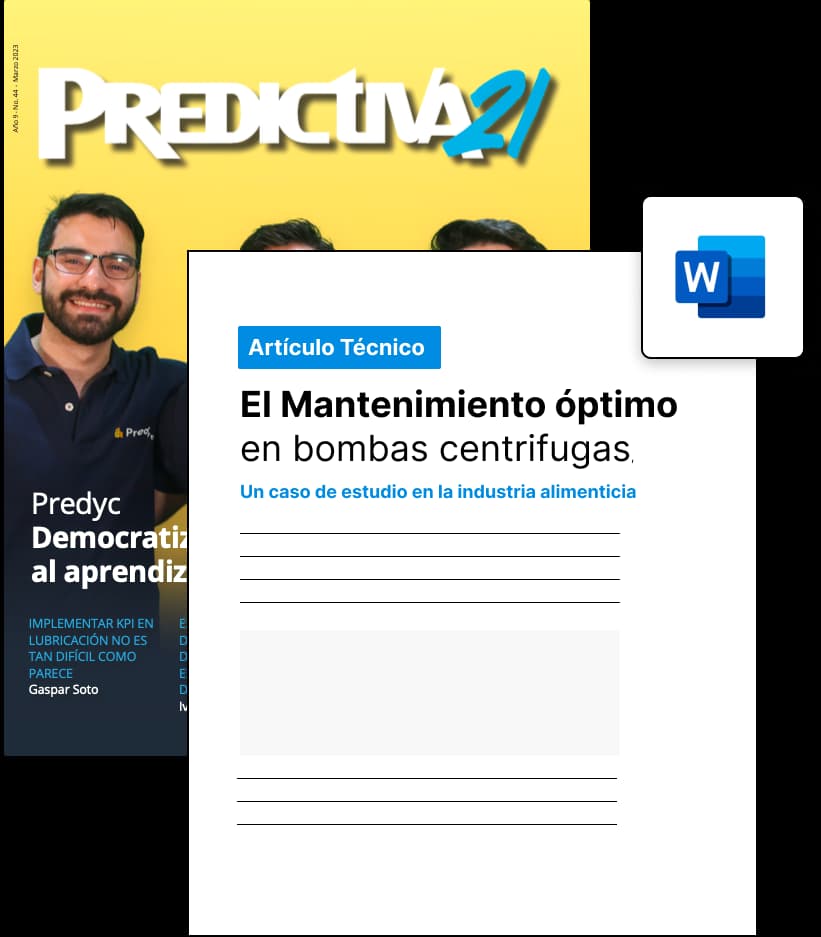
La fiabilidad 4.0 como parte del proceso de gestión de activos: Caso de estudio de una plataforma de petróleo
Articulo 21 de junio de 2020Resumen
Muchos activos físicos en el mundo no alcanzan un alto rendimiento no por la mala gestión de mantenimiento, o falta de cultura de fiabilidad, sino por el bajo desempeño en fiabilidad de equipos críticos.
Para resolver esta cuestión, proponemos la revolución de la fiabilidad 4.0 integrada al proceso de gestión de activos, que considera el monitoreo del desempeño del activo físico automático basado en los datos de fallas insertados en el sistema de reporte de fallas y acciones correctivas (FRACAS).
1. Introducción
Muchos activos físicos en el mundo no alcanzan un alto rendimiento no por la mala gestión de mantenimiento, o falta de cultura de fiabilidad, sino por el bajo desempeño en fiabilidad de equipos críticos.
Durante décadas, la gestión de activos físicos y la implementación de ingeniería de fiabilidad aplicada al monitoreo del desempeño de activos físicos se han hecho por separado.
Aunque algunas soluciones para la gestión de activos físicos presentan herramientas de ingeniería de fiabilidad como el crecimiento de la fiabilidad (CROW AMSSA) y el análisis de vida útil, el mismo concepto prevalece.
El concepto de evaluación de desempeño de fiabilidad basado en crecimiento de fiabilidad y análisis de vida útil todavía se basa en la recopilación de datos y aplicación de métodos estadísticos complejos.
Debido a que este hecho es una gran dificultad para técnicos de mantenimiento, operadores e incluso para ingenieros, el rendimiento de equipos ha sido evaluado de forma simple por indicadores como MTTF o tasas de fallo constante, que conduce a decisiones erróneas en relación con la decisión de alcanzar el rendimiento y la definición de tiempos de inspección.
Para resolver esta cuestión, proponemos la revolución de la fiabilidad 4.0 integrada al proceso de gestión de activos, que considera el monitoreo del desempeño del activo físico automático basado en los datos de fallas insertados en el sistema de reporte de fallas y acciones correctivas (DE LOS MÁS DÉBILES).
2. Gestión de Activos Físicos
Antes de presentar el concepto y los beneficios de la revolución de la fiabilidad 4.0, es necesario entender el sistema y proceso de gestión de activos físicos en el cual el monitoreo del desempeño.
El sistema de gestión de activos es un conjunto de actividades administrativas cuyo objetivo es apoyar la gestión del activo físico.
Basado en la norma ISO 55001, el sistema de gestión de activos debe ser iniciado por la comprensión del plan estratégico de negocio de la organización, que considera los requisitos legales, las demandas de clientes y stakeholders y así, tal plan de negocio puede traducirse en un plan estratégico de gestión de activos (SAMP).
A partir de la definición del plan estratégico de gestión de activos, algunos elementos son fundamentales para la completa implantación del sistema de gestión de activos como:
- Contexto de la organización
- Liderazgo
- La planificación
- Soporte
- Operación
- Análisis de la performance
- Mejora continua
El Contexto Organizacional tiene como objetivo la configuración del plan estratégico de gestión de activos basado en el plan de negocio de la organización, que considera las demandas externas, capacidad interna, así como las exigencias de stakeholders. El producto final será el plan estratégico de gestión de activos.
Liderazgo tiene como objetivo asegurar el compromiso de líderes en todos los niveles organizativos, definición de la política del sistema de gestión de activos, implantación del plan estratégico de gestión de activos, así como la definición de las responsabilidades en todos los niveles del sistema de gestión de activos.
La planificación tiene como objetivo definir los riesgos en la implantación de la gestión de activos, así como los riesgos operativos, que puedan impedir el logro de los objetivos estratégicos definidos del plan estratégico de gestión de activos.
El Soporte tiene como objetivo definir los recursos necesarios para la implantación del sistema de gestión de activos, así como, asegurar que los involucrados tengan conciencia de su papel en la gestión de activos. Además, es necesario establecer el proceso de comunicación y los procedimientos de gestión de la información dentro del sistema de gestión de activos.
La Operación tiene como objetivo planificar y controlar todos los aspectos operativos para garantizar el logro de los indicadores de rendimiento de los activos físicos, así como la efectividad de todas las actividades relacionadas con el sistema de gestión de activos.
El Análisis de desempeño tiene como objetivo evaluar el desempeño de los activos físicos, así como el resultado de auditorías del sistema de gestión de activos por los líderes.
La mejora continua tiene como objetivo la implantación de las acciones necesarias para el tratamiento de las irregularidades relativas a las auditorías del sistema de gestión de activos, así como las acciones de mejora para alcanzar el rendimiento deseado de los activos físicos y los objetivos estratégicos de la gestión de activos.
La figura 1 siguiente muestra el ciclo de gestión de activos basado en al gestión de activos.

Fuente: ISO 55000:2014.
Aunque el sistema de gestión de activos tiene su importancia para garantizar las actividades relativas a la gestión del activo físico de forma eficiente, la implantación de la norma ISO 55001 no garantiza por sí sola el alto rendimiento de los activos físicos.
3. Proceso de gestión de activos físicos
Además de la implantación del sistema de gestión de activos, es necesario definir el proceso de gestión de activos de forma que la gestión de activos forme parte de la rutina operativa de la organización. Por lo tanto, todas las etapas del proceso de gestión de activos físicos deben tener en cuenta a todos los involucrados en la consecución y garantía del alto rendimiento de los activos físicos.
Para que el proceso de gestión de activos físicos sea efectivo, se necesita un sistema centralizado de información que permita a todos los participantes en diferentes niveles organizativos acceder a toda la información y permita a los líderes tomar decisiones rápidas basadas en datos reales y fiables.
Además, es necesario equilibrar las acciones de mitigación de riesgos operativos con los límites de presupuesto y enfocarse en acciones que traigan el mejor costo/beneficio para la organización. Así, el proceso de gestión de activos físicos tiene los siguientes pasos:
- Monitoreo del desempeño & pronóstico de salud del activo (PHM)
- Gestión de mantenimiento preventivo, inspección y órdenes de servicio
- Informe de fallos y acciones correctivas
- Sistema de Información Geográfica (GIS)
- Gestión de fallos
- Gestión del riesgo operativo y coste/beneficio de las acciones de mitigación
- Gestión de la integridad de los activos centrada en los elementos críticos de seguridad
- Gestión de la rutina basada en las actividades de los equipos
- Aprendizaje de la organización
- Revisión de desempeño y mejora continua
La figura 2, a continuación, muestra la gestión del proceso de activos aplicada a través de una solución SaaS.

Fuente: Integrity PRO SaaS software.
Como el enfoque del texto es la fiabilidad 4.0, a partir de ahora nos centraremos en el monitoreo del desempeño del activo físico.
El monitoreo de desempeño se da de forma reactiva y preventiva. El modelo reactivo se produce cuando la verificación de rendimiento considera los fallos y eventos ocurridos en un período de tiempo.
La fiabilidad 4.0 es un tipo de monitoreo de desempeño reactivo, que comienza en el nivel de sistema con la medición de la eficiencia de producción y disponibilidad operativa, pasando a nivel de equipos y componentes para medir la disponibilidad operativa y la fiabilidad de los equipos.
Aunque este es el foco del texto, reconocemos la importancia de la medición de la performance basado en una metodologia preventiva, que tiene como centro la medición de la degradación de equipos y componentes a través del mantenimiento predictivo, o como hemos propuesto en nuestro proceso de gestión de activo físico, vía pronóstico de salud del equipo (PHM).
De hecho, incluso la fiabilidad 4.0 es un monitoreo de desempeño reactivo, es posible al instante verificar el cumplimiento de requisitos de garantía de fiabilidad entre otras ventajas.
4. Revolución de la Fiabilidad 4.0
El programa de Ingeniería de fiabilidad debe ser implantado desde la fase conceptual del activo físico para definir los requisitos de fiabilidad de los sistemas y equipos y la selección de proveedores, que puedan entregar equipos de alta performance en fiabilidad.
Desafortunadamente, esto no ocurre en muchos casos dando lugar a un bajo rendimiento en la fiabilidad de los equipos críticos, que afecta el rendimiento de los sistemas (activos físicos).
Durante la fase de operación, la evaluación del rendimiento del equipo es esencial para la correcta toma de decisiones en relación con el mejor intervalo de tiempo para inspección y mantenimiento preventivo, así como la verificación y validación del cumplimiento de los requisitos de fiabilidad.
En muchas organizaciones, el concepto de fiabilidad y la verificación y validación de la fiabilidad se aplican erróneamente. Esto a menudo lleva a muchos líderes a tomar decisiones equivocadas. Estos hechos ocurren por las siguientes causas:
- Comprensión incorrecta del concepto de fiabilidad.
- Incorrecta definición de indicadores de rendimiento como MTTF y constante tasa de fallas.
- Falta de un sistema de fallas y acciones correctivas consistentes (FRACAS).
- Falta de implantación de un programa de fiabilidad y mantenimiento desde la fase de diseño y diseño.
- Falta de inversión en formación en Ingeniería de fiabilidad.
- Pesada rutina de mantenimiento y operación causando falta de tiempo para actividades de ingeniería de fiabilidad.
La supervisión de la gestión de activos a través del rendimiento de la fiabilidad de los equipos debe integrarse al sistema FRACAS y predecir automáticamente el rendimiento de fiabilidad. De esta manera, el primer paso es la definición de los parámetros de la función Weibul y luego la definición de los siguientes índices de performance tales como:
- Fiabilidad en un tiempo de operación específico.
- Disponibilidad operativa de los equipos.
- Siguiente tiempo de fallo (basado en el modelo CROW AMSAA).
- Tendencia y proyección del MTBF (basado en el modelo CROW AMSAA).
- Tendencia y proyección de la función de intensidad de fallos (basado en el modelo CROW AMSAA).
- Tiempo esperado de reparación (MTTR).
5. Estudio de caso de la implantación de la Fiabilidad 4.0 en una plataforma de petróleo
El estudio de caso presentado fue aplicado en la implantación del sistema integrado de gestión de activos en una plataforma de petróleo en una empresa en África. Al igual que la gestión de activos físicos, la supervisión de la gestión de activos a través del rendimiento de la fiabilidad de los equipos debe integrarse al sistema FRACAS y predecir automáticamente el rendimiento de fiabilidad. Por lo tanto, una vez que los datos han sido introducidos en el sistema de fallos por los técnicos de mantenimiento y los operadores, el primer paso de la fiabilidad 4.0 es la definición automática de los parámetros de la función Weibull, basados en pruebas estadísticas predefinidas, y posteriormente, la definición de los índices de fiabilidad y crecimiento de la fiabilidad según se ha definido anteriormente. Las figuras 3.1,3.2,3.3 y 3.4 abajo muestran a una bomba de una plataforma: (b=5,17 e h=9472,58 (horas)).
Uno de los puntos más importantes en la gestión de activos y la implantación de Confiabilidad 4.0 es la integración de estos sistemas con la rutina operativa. De esta forma, es muy importante que sea posible el rápido acceso de equipos críticos y predicado de la performance de confiabilidad de tales equipos. Así, la figura 3.1 muestra la visualización de los equipos críticos disponibles para todo el equipo de mantenimiento y la producción para comprobar el rendimiento de la fiabilidad 4.0. Como se muestra en la figura 3.1, depende de la importancia de la maquinaria de los diferentes colores se señalan. El color rojo muestra equipos críticos con bajo rendimiento en confiabilidad, el color naranja muestra equipos con nivel de degradación moderado con posible fallo y el color verde muestra quioscos que apeasr de un inicial.

Fuente: El autor.
Al seleccionar uno de los equipos mostrados en el mapa electrónico es posible verificar informaciones relacionadas con los equipos como su Descripción, tag, Sistema, subsistema, estado y estado de salud. El estado se puede definir como LTU «Largo Term unavailable», que significa, un período de más de una semana no disponible. o SPF «Single Point of Failure», que significa, equipos que en caso de fallo causan indisponibilidad del sistema. En la esquina derecha se define el estado de salud, «Equipment Health», que indica el nivel de degradación en diferentes colores como muestra la figura 3.2.

Fuente: El autor.
Al seleccionar uno de los equipos en el mapa de equipo crítico es posible la comprobación automática de la fiabilidad y el crecimiento de cada equipo. La figura 3.3 muestra la predicación de los parámetros de PDF Weibull 2P, fiabilidad, disponibilidad operativa, MTTR, MTTF (basado en crecimiento de fiabilidad), tasa de fallo (basado en crecimiento de fiabilidad).

Fuente: Integrity PRO software.
Por lo general, para llevar a cabo LDA, es necesario tener datos históricos al menos en el nivel del equipo. Muchas empresas, incluidos los proveedores de equipos en la industria del petróleo y el gas, y también en otras industrias, no tienen una base de datos organizada con datos históricos de sus equipos. Por lo tanto, el primer paso, antes de la LDA, es recoger los datos de fallo disponibles. La situación ideal es contar con una base de datos muy estructurada, como el informe de fallos y las medidas correctoras (FRACAS). El primer paso antes de iniciar la metodología LDA es entender el concepto de la función de densidad de probabilidad (PDF). Los PDF describen gráficamente la posibilidad de que ocurran eventos a lo largo del tiempo; en el caso del análisis de datos de vida del equipo, esto significa que el tiempo de falla o reparación se produce con el tiempo. Los pasos de la metodología LDA son:
- Primer paso: Para definir la muestra de datos (agrupados o no agrupados).
- Segundo paso: Para definir el tipo de datos (Censurado o completo).
- Tercer Paso: Para realizar la bondad del análisis de ajuste (Parcela, Regresión, MLE, otros).
- Cuarto Paso: Definir el parámetro PDF.
- Quinto paso: Para predecir la fiabilidad, probabilidad de fallo y la función de tasa de fallo.
Basado en la Fiabilidad 4.0, todos estos pasos se realizan automáticamente en base a la configuración adecuada para el tipo de activo físico. Por lo tanto, la fiabilidad 4.0 permite a todos los empleados entender los resultados de fiabilidad basados en la predicción auomática sin la necesidad de tener un profundo conocimiento de estadísticas y la fiabilidade, y sin la necesidad de utilizar otro software para predicción de fiabilidad.

Fuente: Integrity PRO software.
Además del predicado de la fiabilidad, el predicado del crecimiento de la confiabilidad también se calcula así como los gráficos de fiabilidad, probabilidad de fallas, tasa de fallo, tendencia de MTTF, tendencia de tasa de falla y número esperado de fallas como muestran las figuras 3.3 y 3.4. La metodología de Análisis de Crecimiento de Confiabilidad se aplica a la evaluación de equipos durante la operación y se basa únicamente en el Modelo Crow AMSSA. Este modelo fue introducido por el Dr. Larry H. Crow en 1974, es un modelo estadístico que utiliza el parámetro de distribución Weibull para describir la relación entre el tiempo acumulado entre el fallo y el tiempo de prueba. Este enfoque se aplica en el análisis de crecimiento de la fiabilidad para mostrar el efecto de las acciones correctoras sobre la fiabilidad cuando se está desarrollando un producto o incluso en sistemas reparables durante la fase de funcionamiento. De este modo, siempre que se introducen mejoras durante las pruebas (test-fix-test), el modelo Crow AMSAA se utiliza para predecir el crecimiento de la fiabilidad y el número acumulativo esperado de fallos. El comportamiento de crecimiento defiabilidad puede aumentar/disminuir o permanecer constante con el tiempo. De hecho, depende de los valores β que es un parámetro de forma de la función de falla de intensidad en el modelo Crow AMSAA. Por lo tanto, en este modelo cuando β > 1, la fiabilidad disminuye con el tiempo porque la intensidad de fallo está aumentando, o en otras palabras, las acciones del producto correctivo no están mejorando el producto. Cuando β < 1, la intensidad del fallo está disminuyendo con el tiempo, o en otras palabras, las acciones correctivas del producto están mejorando la fiabilidad del producto.Cuando β = 1, el producto se comporta como si no se hubiera tomado ninguna acción correctiva y la intensidad de la falla es constante en el tiempo. Es importante tener en cuenta que la β del modelo Crow-AMSAA describe un comportamiento de falla de intensidad y no tiene relación con el parámetro de la forma de distribución de Weibull.
El origen de los datos de fallos y reparación se produce por el sistema FRACAS. De esta manera, a través de una ficha electrónica de falahs que puede ser accedida a través del teléfono móvil o vía computada, las fallas pueden ser insertadas en el sistema y a partir de más de tres datos cuantitativos la fiabilidad y el crecimiento de la fiabilidad se calculan automáticamente. El Sistema FRACAS Electrónico está basado en FMEA, que definen los modos de falla las causas y consecuencias así como los modos de detección de fallas. Tales informaciones son estandarizadas e insertadas en el FRACAS.
De esta manera, los medios de operación y los operadores pueden abrir una ficha de fallo de forma simple y rápida. La figura 3.5 muestra la primera ficha electrónica del FRACAS. Después de completar esta ficha, los supervisores revisarán los datos y aprobarán análisis. Luego se dará el análisis de la causa raíz y la definición de las acciones mitigadoras para la apertura de la orden del servicio. Todo este proceso es parte del proceso de gestión de activos (Integrity Pro Saas). En el monento no vamos a detallar el sitema FRACAS, pues el objetivo de este paper es demostrar la fiabilidad 4.0, pero es importante demostrar también el origen de los datos para los cálculos de confiabilidad que se da por el sistema FRACAS.

Fuente: Integrity PRO software.

Fuente: Integrity PRO software.
Con el objetivo de verificar y validar los resultados de fiabilidad 4.0 presentados en el software Integrity pro, el renombrado software Weibull ++ de Reliasoft fue aplicado utilizando los mismos intervalos de fallo y métodos estadísticos.
La figura 4 muestra el resultado de la estimación de los parámetros de distribución Weibull 2p calculados por el software Weibul que fueron: b=5,47 e h=9423 (horas), bien próximos a los valores calculados por la solución fiabilidad 4.0 en el software Integrity pro.

Fuente: Weibull ++ software.
Finalmente, una de las grandes ventajas de la fiabilidad 4.0 es la posibilidad de generar automáticamente una base de datos de fiabilidad como muestra la figura 5. De esta manera, la plataforma de petróleo pasará a tener su propia base de datos de fiabilidad en tiempo real. Dicha base de datos puede utilizarse como base para estudios de fiabilidad, seguridad y análisis de riesgos en la fase de proyecto y operativa. Esto elimina el uso de bases de datos genéricas como OREDA y AICHE.

Fuente: Integrity PRO software.
6. Conclusión
El objetivo del estudio fue demostrar la revolución de la fiabilidad 4.0 a través de un estudio de caso práctico aplicado a la industria del petróleo.
Mediante la verificación y validación realizada por el software Weibull ++ fue posible verificar la consistencia de los resultados producidos automáticamente por la fiabilidad 4.0. De esta forma, los principales beneficios de la fiabilidad 4.0 son:
- Integración de herramientas de ingeniería de fiabilidad como FRACAS, análisis de vida útil y análisis de crecimiento de fiabilidad en el proceso de gestión de activos.
- Predicción de fiabilidad y crecimiento de fiabilidad basada en datos reales con resultados fiables.
- Posibilidad de verificación de la performance de fiabilidad por cualquiera de los integrantes del proceso de gestión de activos físicos en línea de forma automática, que permite una rápida toma de decisiones.
- Eliminación de la necesidad de cálculos complejos y uso de software auxiliar para la predicción de la fiabilidad y el crecimiento de la fiabilidad.
- Reducción drástica del tiempo de cálculo de performance de fiabilidad.
- Reducción de la inversión en software y entrenamientos en análisis de vida útil.
Una de las limitaciones de las predicciones de desempeño en fiabilidad es la necesidad de datos de fallas para posteriormente predecir la fiabilidad o la tendencia de la disminución del intervalo entre fallas.
Sin embargo, como se ha dicho anteriormente, el pronóstico de salud de los activos físicos es parte del proceso propuesto de gestión de activos físicos y permite verificar la degradación de los activos físicos cuando éstos operan por encima de los límites operativos. Ese tema será discutido en un próximo artículo.
7. Referencias
- [1] «Gas and Oil Reliability Engineering: Modelling and Simulation. Second edition, Elsevier ISBN: 9780123919144, 26 May2016).
- [2] RAMS and LCC engineering applied to railway industry: Analysis, Modelling and Optimization. 18-04-2018.Amazon. ISBN-13: 978-1986524704.
Autor: Eduadardo Calixto
Eduardo Calixto Consulting, Alemanha
Correo: ec@eduardocalixto.com
Dinos qué te ha parecido el artículo
Artículos recomendados
Mantenimiento y gestión de activos físicos

Importancia del clima organizacional y los elementos que lo configuran

Qué son los cursos de mantenimiento online

Tasa Interna de Retorno: medida fundamental en empresas

Publica tu artículo en la revista #1 de Mantenimiento Industrial
Publicar un artículo en la revista es gratis, no tiene costo.
Solo debes asegurarte que no sea un artículo comercial.
¿Qué esperas?
O envía tu artículo directo: articulos@predictiva21.com
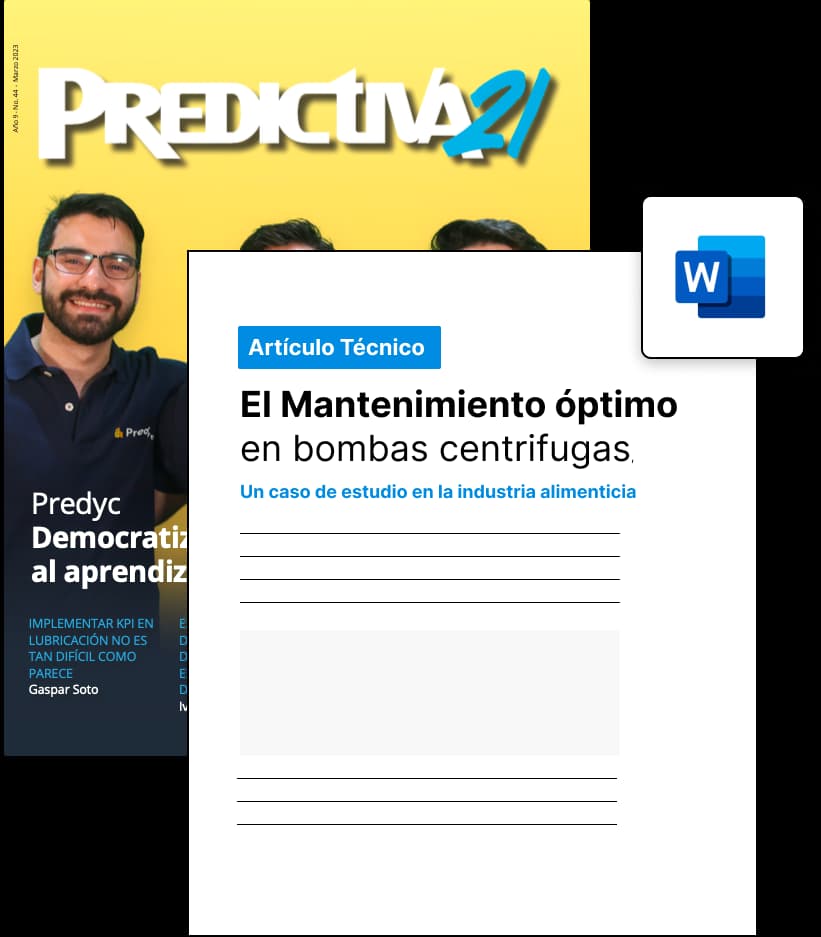