Gestión de Activos Proactiva
Articulo12 de abril de 2019
La Gestión de Activos Proactiva es el objetivo de muchas organizaciones en las que el mantenimiento reactivo puede tener un gran impacto en los costos, la rentabilidad y los riesgos. Un caso de negocio contrastando los dos enfoques, el proactivo y el reactivo, puede revelar la diferencia cuántica entre ambos, al igual que la evaluación comparativa y las auditorías. Se exploran los principios necesarios que la sustentan para apoyar la gestión de activos proactiva durante el ciclo de vida de un activo, y a través de las interacciones del sistema de gestión de mantenimiento. Las áreas a tratar incluirán el comportamiento del sistema de mantenimiento, la toma de decisiones, el uso de los datos, los KPI’s y los roles organizacionales.
Sostener la gestión de activos proactiva requiere de la vigilancia día a día de las fallas, los incidentes y las prácticas de mantenimiento. Para ello se explora cuál información es importante, quién participa, cómo concentrarse en los datos críticos que impulsan la mejora.
Se examinan los procesos necesarios para dirigir el desempeño de la gestión de activos fuera del comportamiento reactivo. Quienes están involucrados y cómo las actividades de mejora compiten por los recursos en un entorno exigente. Todos los procesos requieren de partes interesadas, ¿quiénes son y por qué?
La aplicación de la mejora continua es donde los neumáticos encuentran la carretera. Muchas organizaciones tradicionales no están bien orientadas para esto. A menudo hay obstáculos o atrasos u otras prioridades. Se explora lo que se requiere para la aplicación de los resultados de un sistema de gestión de activos proactiva, y qué medidas se pueden utilizar para asegurarse que los resultados apoyen los objetivos de negocio.
Nos centraremos en gran medida en el papel del Análisis RAMS, RCM, RBD y Apollo RCA a lo largo de este proceso.
Contenido
- Propósito, Objetivos del Programa, Principios que la Sustentan.
- Entradas de Datos e Información.
- Desarrollo del Proceso.
- Resultados Obtenibles y Entregables.
- Papel de la Metodologías de Análisis RAMS, RCM, RBD y Apollo RCA a lo largo de este proceso.
Desarrollaremos estos puntos en forma integral, como elementos de un sistema de gestión de activos proactivo, analizando su funcionamiento global y sus interacciones.
No necesariamente los subtítulos seguirán dicha lista, pero los objetivos, las entradas, el desarrollo, los resultados y las metodologías, serán la columna vertebral del desarrollo.
Propósito, objetivos del programa, principios que la sustentan
La Gestión de Activos Proactiva es el objetivo de muchas organizaciones en las que el mantenimiento reactivo puede tener un gran impacto en los costos, la rentabilidad y los riesgos. Un caso de negocio contrastando los dos enfoques puede revelar la diferencia cuántica entre ambos, al igual que la evaluación comparativa y las auditorías. Este paso explora los principios necesarios que la sustentan para apoyar la gestión de activos proactiva durante el ciclo de vida de un activo, y a través de las interacciones del sistema de gestión de mantenimiento. Las áreas a tratar incluirán el comportamiento del sistema de mantenimiento, la toma de decisiones, el uso de los datos, los KPI’s y los roles organizacionales.
Entradas de datos e información
Sostener la gestión de activos proactiva requiere de la vigilancia día a día de las fallas, los incidentes y las prácticas de mantenimiento. Este paso explora cuál información es importante, quién participa, cómo concentrarse en los datos críticos que impulsan la mejora.
Desarrollo del proceso
Este paso examina los procesos necesarios para dirigir el desempeño de la gestión de activos fuera de comportamiento reactivo. Quienes están involucrados y cómo las actividades de mejora compiten por los recursos en un entorno exigente. Todos los procesos requieren de partes interesadas, ¿quiénes son y por qué?
Resultados obtenibles y entregables
La aplicación de la mejora continua es donde los neumáticos encuentran la carretera. Muchas organizaciones tradicionales no están bien orientadas para esto. A menudo hay obstáculos o atrasos u otras prioridades. Este paso explora lo que se requiere para la aplicación de los resultados de un sistema de gestión de activos proactiva, y qué medidas se pueden utilizar para asegurarse que los resultados apoyen los objetivos de negocio.
Papel de las metodologías de análisis RAMS, RCM, RBD y APOLLO RCA a lo largo de este proceso
A lo largo de los cuatro pasos los participantes comprenderán:
- El papel del análisis RAMS en Nuevos Proyectos.
- Los cuatro pasos para la Solución Efectiva de Problemas y por qué las empresas encuentran tan difícil descubrir las Causas Raíces.
- El poder de tomar decisiones a partir de datos y la forma de hacerlo de manera continua, como parte de la gestión de activos.
- RCM aplicado como parte de la gestión de activos diaria – rápido, fácil y potente.
- Cómo obtener el máximo rendimiento de la implementación y mantener a las principales partes interesadas apoyando el proceso.
- Mantenimiento Centrado en Confiabilidad, RCM, es una metodología disciplinada que crea planes de mantenimiento eficaces que mitigan o minimizan los efectos de los fallos funcionales o fallos potenciales. Este evento de aprendizaje y contactos ofrece una visión general de los distintos enfoques de RCM y analiza casos prácticos para que se pueda aprender lo que funcionó y lo que no funcionó de aquellos que ya han tenido un poco de dolor y un poco de ganancia.
- Apollo Análisis Causa Raíz, Apollo RCA, es una metodología disciplinada para eliminar las fallas recurrentes o crónicas mediante el descubrimiento de las causas raíces reales de esas fallas. Se analizan casos de estudio para brindar una hoja de ruta clara para aplicar estas estrategias para evitar las fallas.
- Al asistir a aprender sobre RCM y Apollo RCA básicos, descubrirá consejos para asegurarse de que usted puede poner en práctica con eficacia y saber qué obstáculos puede esperar y cómo superarlos.
Gestión de activos proactiva
La Gestión de Activos Proactiva es un objetivo de muchas organizaciones. El mantenimiento reactivo tiene un gran impacto en los costos, la rentabilidad y el riesgo de las operaciones con uso de activos intensivos.
Todos los Directores, Gerentes, Ingenieros y Técnicos de las empresas entienden que es mejor actuar en un entorno Proactivo que en uno Reactivo, sin embargo, ¿por qué los sistemas de gestión de activos se vuelven tan frecuentemente reactivos?
Para analizar lo que sucede y como corregirlo vamos a realizar un mapeo típico del proceso de mantenimiento en un ambiente reactivo.

En dicho mapa, visualizamos la demanda de operaciones respecto a obtener un rendimiento de la planta, tenemos un presupuesto de mantenimiento para lograr dicho objetivo con los recursos necesarios, a saber: mano de obra, materiales, repuestos, contratistas, alianzas de suministro y servicios.
Contamos con almacenes y área de compras para asegurar la logística de suministro y servicios. Tenemos una ingeniería de mantenimiento, que planifica y programa la ejecución de las tareas de mantenimiento, generalmente basada en los históricos de trabajos.
Existe un cierto plan de mantenimiento preventivo, con una cobertura de cierto alcance en cuanto al mantenimiento predictivo. Contamos con un aseguramiento de calidad de los trabajos con cierto grado de efectividad.
Pero dada la situación reactiva en que vivimos, con más del 60% de las actividades realizadas en forma correctiva, entonces los planes programados no se cumplen en su totalidad, no alcanzando su real potencial; la iniciación de los trabajos, debido a las urgencias, es verbal, la mayoría de las veces, con la promesa de luego realizar la orden de trabajo, promesa que mayormente no se cumple, resultando en un histórico de trabajos y de fallas incompleto y sin datos vitales respecto a posibles fallas importantes y críticas.
Este círculo vicioso nos mantiene encerrados, no permitiéndonos desarrollar todo el potencial de efectividad que existe. Para salir de la situación reactiva, e iniciar el camino hacia el proactivo, debemos contar con lazos de mejora continua que permitan analizar tanto los resultados del trabajo completado comparando lo planificado y programado versus lo real; así como los efectos de los mismos en las operaciones tanto en sus aspectos económicos como de riesgo.

Debemos analizar los impactos en la línea de resultados de la compañía, tanto en los eventos críticos, como de los repetitivos que por su frecuencia afectan también seriamente al proceso. Estos lazos de mejora continua se desarrollan principalmente mediante una herramienta de excelencia en el análisis y resolución efectiva de problemas que es el Análisis Causa Raíz (RCA por sus siglas en inglés). El RCA es la herramienta básica para iniciar el desarrollo de la Ingeniería de Confiabilidad. Con el RCA podemos definir los problemas ocurridos, analizar las relaciones causa – efecto que los generan, desarrollar soluciones para controlar las causas raíces e implementarlas para asegurar la no repetición del problema.
Una vez identificadas las causas raíces y registrados sus datos de falla en el histórico, podemos entonces alimentar otras herramientas de la Ingeniería de Confiabilidad, como ser, el Análisis de Weibull, el cual nos permitirá conocer los patrones de falla de dichas causas, y de esa manera poder optimizar las estrategias de mantenimiento mediante el Análisis RCM (Mantenimiento Centrado en Confiabilidad). Esto nos permitirá una mejora continua y dinámica de nuestros planes de mantenimiento.
Asimismo, cuando no alcance con mejorar las estrategias de mantenimiento, y rediseños deban ser efectuados, podremos analizar el diseño del sistema y sus equipos, mediante el Análisis RBD (Diagrama de Bloques de Confiabilidad), para así identificar las áreas de oportunidad, como ser, cuellos de botella, redundancias, stocks intermedios, equipos de bajo desempeño, etc. De esta forma realimentaremos a Ingeniería para realizar las mejoras necesarias.

Mediante este proceso de mejora continua, círculo virtuoso de la confiabilidad, es que lograremos superar la situación reactiva con un 60% o más de correctivo, para llegar a la tan deseada situación proactiva con menos del 20% de correctivo, solamente donde el costo de la falla sea claramente más bajo que cualquier alternativa de prevención; y con más predictivo y proactivo liderando nuestros planes de mantenimiento optimizados.
Valor del premio a la confiabilidad
Para entender claramente este proceso debemos entender el valor del impacto que la confiabilidad de los equipos y sistemas tienen en el negocio, y compararlo con el impacto que tiene la situación reactiva.
Existen varios impactos que la mala o pobre confiabilidad tiene sobre el negocio, a saber:
- Altos costos de mantenimiento.
- Baja disponibilidad de planta.
- Alta carga de trabajos reactivos.
- Alto número de incidentes de seguridad y ambientales.
- Alto número de interrupciones del proceso y problemas de calidad.
- Aumento de inversión de capital por cortas vidas útiles de los equipos y sistemas.
Esto genera en el ambiente reactivo los siguientes impactos de alto costo en el negocio:
- Pérdida de ingresos.
- Aumento del desperdicio.
- Baja utilización de mano de obra.
- Altos costos de repuestos.
- Inventarios altos de repuestos.
- Inventarios altos de productos.
Con este escenario es importante estimar al valor del premio por lograr una mejora de confiabilidad que nos marque el costo–beneficio en el camino a la Gestión de Activos Proactiva.
Para ello debemos poder contestar las siguientes preguntas, las que nos ayudarán a armar el caso de negocio de la confiabilidad:
- ¿Qué nivel de mantenimiento planificado tiene su negocio? (Ej.: 85%).
- ¿Qué nivel de disponibilidad de planta promedio tienes su negocio? (Ej.: 88%).
Tomaremos como regla de comparación, una métrica internacionalmente aceptada que dice que:
“El trabajo no planificado cuesta en promedio tres (3) veces más que el mismo trabajo planificado”.
Analizaremos dos escenarios:
- 1) Suponiendo que aplicamos ingeniería de confiabilidad y logramos reducir en 5% el presupuesto de los costos de mantenimiento no planificado, mediante la reducción de las fallas.
- 2) Suponiendo que aplicamos una simple reducción de costos del 5%, rebajando el presupuesto de costos del mantenimiento planificado.
- 3) Finalmente estimaremos el impacto de mayores ingresos por el aumento de disponibilidad de planta del 1%, 5% y 10%.
Tomaremos como base un presupuesto de 100 MUSD para simplificar los números, y dado que supusimos un 85% de mantenimiento planificado, tendremos 85 MUSD en dicho rubro del presupuesto.
Complementariamente tendremos 15 MUSD en el rubro de mantenimiento no planificado.
1) Si logramos con ingeniería de confiabilidad reducir realmente las fallas, de modo que el mantenimiento no planificado reduzca 5% del 15% al 10% (o dicho de otro modo de 15 a 10 MUSD), esto no significa que bajará el presupuesto global en 5 MUSD. Los modos de falla que dejaron de ser atendidos por tareas no programadas, ahora serán atendidos por tareas programadas, lo cual aplicando la regla del 3:1 en cuanto a costos de no programado versus costo de programado, indica que el costo de las nuevas tareas programadas para atender estos modos de falla será de 1,65 MUSD. Por lo tanto el beneficio neto para el negocio será de 3, 35 MUSD.
2) Ahora veamos el caso de la reducción simple de costos a los gastos de tareas programadas, algo que todos hemos sufrido alguna vez. Aquí cuando reducimos el gasto de mantenimiento programado un 5%, esto no significa que los modos de falla que eran atendidos por las tareas suprimidas van a desaparecer por arte de magia. Por el contrario significa que dichos modos de falla pasarán a ser atendidos por actividades no programadas cuando ocurra la falla. Si nuevamente aplicamos la regla del 3:1, del no programado versus programado, aquellos modos de falla que con actividades programadas costaban 5 MUSD, ahora con actividades no programadas costarán 15 MUSD. Resultando que el pretendido ahorro de 5 MUSD se convirtió en una pérdida neta para el negocio de 10 MUSD.
Para evitar que algún escéptico nos señale que todo esto se basa en una regla del 3:1 de la cual no hemos demostrado su validez, hagámoslo pues, demostrémosla.
Cuando desarrollamos un trabajo planeado de, por ejemplo, cambio de rodamientos, efectivamente solo cambiamos el rodamiento. El hecho de ser planeado nos permite tener todo organizado a pie de máquina antes de la intervención y además nos da la oportunidad de elegir el momento de forma de minimizar, y eventualmente reducir a cero, el costo de parada asociado.
En cambio, cuando la reparación es de emergencia, no planeada, entonces el fallo imprevisto del rodamiento, trae consigo eventuales daños del acople, del eje, del alojamiento del rodamiento y del impulsor de la bomba o estator del motor, sumados a los costos de parada imprevistos.
Todos estos costos extras, sumados a la espera logística de obtener recursos humanos y materiales no planeados, y que por lo tanto no estaban necesariamente disponibles para realizar la tarea, con los eventuales costos extras de sobreprecios y tiempo extra, son los que justifican dicha relación promedio de 3:1 entre los costos de reparaciones no planificadas versus los costos de reparaciones planificadas.
3) Para estimar el impacto de mayores ingresos mediante el aumento de la disponibilidad de planta en 1%, 5% y 10 % haremos algunas hipótesis para fijar ideas. Consideramos como caso base lo siguiente: 88% de disponibilidad, por lo tanto 12% de tiempos de paradas de planta, consideremos que se trata de una empresa con uso intensivo de activos, por lo tanto tomaremos un costo de pérdida de producción por parada de 100.000 USD/hr. Para este caso base tendremos 1051,2 horas de parada al año, generando una pérdida total respecto a las 8760 horas anuales de 105.120.000 USD. Ahora si analizaremos los resultados de calcular la mejora de 1%, 5% y 10% de disponibilidad.

Entonces vemos que los beneficios respectivos son de:
- 1%: 8.760.000 USD.
- 5%: 43.800.000 USD.
- 10%:87.600.000 USD.
Este beneficio extra de 87,6 horas de operación para un 1% de aumento de disponibilidad, que vale 8,76 MUSD, es un fuerte estímulo para la mejora de mantenimiento, mostrando el costo beneficio de la misma.
Pero al mismo tiempo, también genera un fuerte estímulo a que operaciones no entregue los equipos para dar servicio, intentando aumentar los intervalos entre paradas, para así ganar este valor en más operaciones.
Esto genera el riesgo de que el equipo falle en operación, en cuyo caso el costo de la falla sería el triple, generando una pérdida de 8,76×3 MUSD por tiempo de parada.
Entonces se hace necesario un acuerdo importante entre operaciones y mantenimiento de alineación de objetivos, para desarrollar una gestión del cambio que nos lleve del reactivo al proactivo, sin estos contratiempos.
Cursos recomendados






%252FImagen%252FRAMPREDYC-1730060420837.webp%3Falt%3Dmedia%26token%3D2634a7f0-988e-4022-b91f-382503e6e9db&w=3840&q=75)

Herramientas de confiabilidad
Las herramientas modernas de la confiabilidad, tales como el análisis RAMS, el RCM, el RBD, Weibull y el RCA entre otros, permiten desarrollar modelos para evaluar resultados mediante la aplicación de la simulación matemática.
Estas herramientas nos permiten:
- a) Evaluar resultados de diferentes escenarios.
- b) Comparar entre escenarios alternativos, como por ejemplo: Correr a la falla (RTF por sus siglas en inglés), Plan de Mantenimiento actual y Plan de Mantenimiento optimizado.
- c) Armar modelos de planta y equipo donde desarrollamos el Análisis RCM. Evaluamos cada modo de falla, optimizándolo en función de la probabilidad de falla y su impacto en el negocio.
- d) Una vez optimizadas las tareas por cada modo de falla, se forman grupos de tareas, agrupadas por equipo, tipo de tarea, frecuencia, especialidad, condición de equipo parado o en operación, etc. Estos grupos de tareas también se optimizan como grupo.
- e) Permite realizar predicciones base cero del presupuesto de mantenimiento.
- f) Evaluar los perfiles de los planes de mantenimiento por mano de obra y repuestos, identificando el presupuesto necesario optimizado en cada rubro.
- g) Conocer cuáles son los modos de falla críticos, antes de mejorar para poder optimizar con eficacia, y luego de la mejora para saber hacia dónde orientar en el futuro la búsqueda de oportunidades.
Entre las herramientas de la confiabilidad se destacan:
A) Análisis Causa Raíz (RCA). Es una metodología de resolución efectiva de problemas que se basa en los siguientes pasos:
- a. Definir el Problema, estableciendo el Qué, Cuándo, Dónde y la Importancia del mismo.
- b. Desarrollar el Gráfico Causa y Efecto, identificando todas las relaciones causales y soportando cada causa con Evidencias.
- c. Generar Soluciones Creativas para las diferentes causas del gráfico causa y efecto, identificando las Mejores Soluciones.
- d. Implementar y Monitorear las Mejores.
- e. Soluciones para asegurar los resultados.
B) Análisis de Mantenimiento Centrado en Confiabilidad (RCM). Es una metodología estructurada para definir estrategias de mantenimiento que se basa en 7 preguntas claves:
- a. ¿Cuáles son las funciones de los activos? FUNCIONES.
- b. ¿Cuáles son las fallas funcionales de los activos? FALLAS FUNCIONALES.
- c. ¿Qué causa cada falla funcional? MODOS DE FALLA.
- d. ¿Qué sucede cuando cada causa ocurre? EFECTOS DE FALLA.
- e. ¿Que nos importa de todo eso que sucede? CONSECUENCIAS.
- f. ¿Qué debe ser hecho para predecir y/o prevenir la falla? TAREAS PROACTIVAS.
- g. Qué hacer si no hay una buena tarea proactiva? TAREAS A FALTA DE.
Permite desarrollar y simular planes efectivos de mantenimiento para lograr:
- Minimizar los riesgos de seguridad y medio ambiente,
- Minimizar los costos de falla,
- Optimizar las capacidades.
Los sistemas modernos, basados en simulación matemática por el método de Montecarlo, con el soporte de programas de computadoras para realizarlos, permiten desarrollar la jerarquía de los activos, importar datos de bibliotecas de activos similares, desarrollar el análisis funcional, identificar las fallas funcionales, e identificar los modos de falla.
Asociado a cada modo de falla, deberemos indicar sus efectos, los datos de falla con parámetros de la curva de Weibull, los recursos necesarios y la duración de las tareas correctivas y de las tareas predictivas y preventivas posibles de realizar.
Finalmente nos permiten evaluar entre las diferentes opciones:
- No hacer nada. (correctivo),
- Seguir con la estrategia actual,
- Preventivo,
- Predictivo,
- Detectivo, o
- Rediseños.
Para la evaluación de estrategias óptimas, luego de definir las tareas, es posible optimizar su frecuencia y calcular el costo de ciclo de vida (LCC por su sigla en inglés) de cada una de las opciones, y así elegir siempre la mejor opción global.
Este análisis de alternativas realizado a nivel de cada modo de falla, nos garantiza que todo el plan será el óptimo y nos brinda además una herramienta de mejora continua, una vez que podemos recalcular el óptimo para modos de falla que hayan sufrido cambios en sus datos de entrada.
El plan de mantenimiento se convierte así en un documento vivo que constantemente se puede adaptar a medida que los datos de rendimiento se generan y se analizan.
Optimizando los planes por costo de ciclo de vida de los activos, obtenemos planes de mantenimiento con presupuestos base cero, y podemos desarrollar entonces las instrucciones de trabajo detalladas, elaborar las predicciones de mano de obra y repuestos necesarios, así como planificar toda la logística de soporte.
C) Análisis de Diagramas de Bloques de Confiabilidad (RBD). Es una herramienta de simulación para evaluar la capacidad y disponibilidad de una planta o sistema durante su ciclo de vida para:
- a. Mitigar los riesgo de seguridad y medio ambiente,
- b. Minimizar los costos de falla,
- c. Optimizar capacidades y disponibilidades. En el RBD se representa al sistema por las series, paralelos, redundancias, by-pases, buflers y fuentes de potencial que reflejan las relaciones de confiabilidad del sistema, o sea se representa cada elemento no por su incidencia en el flujo de masas o energía del proceso, sino por su incidencia en los fallos del sistema.
Este análisis puede ser realizado tanto a alto nivel, tomando cada sistema, subsistema o equipo como un bloque global complejo, y considerando su falla como de tipo exponencial (aleatoria), dada la complejidad de la misma al evaluarla a alto nivel.
O puede ser realizado bajando al nivel de detalle que se desee, hasta alcanzar los modos de falla individuales con toda la variedad de patrones de falla de Weibull para cada uno.
Esto permite que esta herramienta sea utilizada desde etapas tempranas de la gestión de activos, tanto en la pre-factibilidad como en la factibilidad de proyectos de capital.
D) Análisis de Weibull. La función de Weibull permite representar todos los patrones de falla conocidos, mediante la variación de sus parámetros: h (eta) – vida característica; b (beta) – parámetro de forma; g (gama) – parámetro de localización.

Una vez recolectados datos de falla, podemos aplicar el Análisis de Weibull para conocer los parámetros correspondientes a dichos datos de falla y así conocer el patrón de falla asociado a dicho modo de falla del cual surgieron los datos.

Esto nos permite luego optimizar las estrategias de mantenimiento mediante el RCM.
Resumen final
En resumen, este conjunto de herramientas de confiabilidad que nos permitieron generar los lazos de mejora continua y optimización para salir del reactivo e iniciar el camino al proactivo, nos acompañan en todo el desarrollo del proceso, a lo largo de todo el ciclo de vida de los activos.
Pueden ser usadas tanto para optimizar proyectos de capital de plantas nuevas, como para optimizar plantas existentes en operación. Son la columna vertebral de la Gestión de Activos Proactiva.
La Gestión de Activos Proactiva, es el proceso global de gestión a través del cual consistentemente agregamos valor a la compañía mediante el uso y cuidado de los activos en todo el ciclo de vida. [Partimos de los objetivos del negocio, definimos las estrategias de activos, desarrollamos las herramientas de confiabilidad, disponibilidad, mantenibilidad y seguridad (RAMS) y optimizamos las estrategias de mantenimiento y sus recursos.
La importancia de iniciar estas actividades en las etapas tempranas del ciclo de vida de los activos, es que el costo de los cambios crece en progresión geométrica.

Y que en las etapas tempranas del desarrollo de los proyectos de capital se definen más del 80% de los que serán los futuros costos del ciclo de vida. La modificación de algo en estas etapas tempranas, muchas veces solo representa el costo de tinta sobre papel, pero genera un ahorro significativo a futuro.
Decisiones adecuadas tomadas tempranamente en la fase de proyecto, permite optimizaciones inteligentes que ahorran costos y riesgos importantes.

Además nos permite evitar esos ahorros de corto plazo, tempranos y tentadores, que luego dan lugar al dicho de “lo barato sale caro”.
Sembrando Confiabilidad en épocas tempranas, podremos cosechar una Gestión de Activos Proactiva, con costos optimizados y riesgos minimizados a lo largo de todo el Ciclo de Vida de los Activos.
Autor: Ing. Ind. Santiago Sotuyo, CMRP
Gerente Ingeniería – Latino América
ARMS Reliability
San Pedro M-223 S-8, El Pinar Ciudad de la Costa, CP 15008 Canelones, Uruguay
Correo: ssotuyo@armsreliability.com
Dinos qué te ha parecido el artículo
Artículos recomendados
El Plan de Mejora Operativa como Metodología para detectar Áreas de Oportunidad en la Turbo Maquinaria de instalaciones Costa Afuera

Serie: “Confiabilidad en Sistemas de misión Critica: Empezar por el Principio”. Sistemas de Puesta a Tierra (II Parte)

El RCA y la cultura del dato

Gestión del Mantenimiento a Generadores eléctricos aplicando el método de Mantenimiento Basado en la condición

Publica tu artículo en la revista #1 de Mantenimiento Industrial
Publicar un artículo en la revista es gratis, no tiene costo.
Solo debes asegurarte que no sea un artículo comercial.
¿Qué esperas?
O envía tu artículo directo: articulos@predictiva21.com
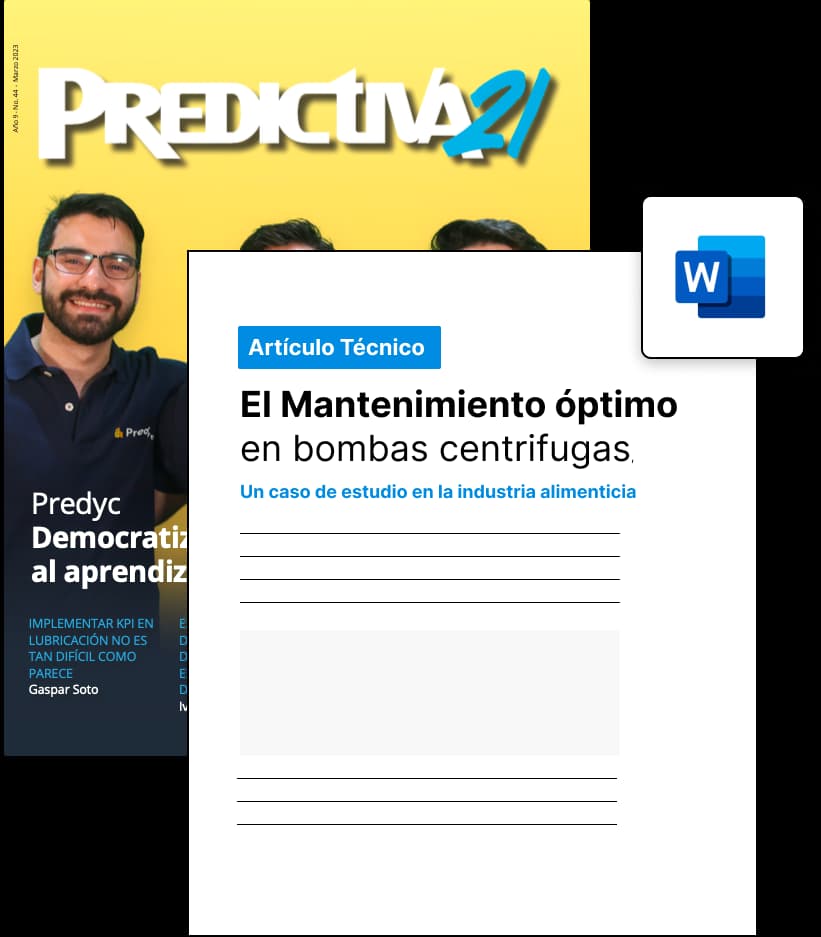
Gestión de Activos Proactiva
Articulo 12 de abril de 2019La Gestión de Activos Proactiva es el objetivo de muchas organizaciones en las que el mantenimiento reactivo puede tener un gran impacto en los costos, la rentabilidad y los riesgos. Un caso de negocio contrastando los dos enfoques, el proactivo y el reactivo, puede revelar la diferencia cuántica entre ambos, al igual que la evaluación comparativa y las auditorías. Se exploran los principios necesarios que la sustentan para apoyar la gestión de activos proactiva durante el ciclo de vida de un activo, y a través de las interacciones del sistema de gestión de mantenimiento. Las áreas a tratar incluirán el comportamiento del sistema de mantenimiento, la toma de decisiones, el uso de los datos, los KPI’s y los roles organizacionales.
Sostener la gestión de activos proactiva requiere de la vigilancia día a día de las fallas, los incidentes y las prácticas de mantenimiento. Para ello se explora cuál información es importante, quién participa, cómo concentrarse en los datos críticos que impulsan la mejora.
Se examinan los procesos necesarios para dirigir el desempeño de la gestión de activos fuera del comportamiento reactivo. Quienes están involucrados y cómo las actividades de mejora compiten por los recursos en un entorno exigente. Todos los procesos requieren de partes interesadas, ¿quiénes son y por qué?
La aplicación de la mejora continua es donde los neumáticos encuentran la carretera. Muchas organizaciones tradicionales no están bien orientadas para esto. A menudo hay obstáculos o atrasos u otras prioridades. Se explora lo que se requiere para la aplicación de los resultados de un sistema de gestión de activos proactiva, y qué medidas se pueden utilizar para asegurarse que los resultados apoyen los objetivos de negocio.
Nos centraremos en gran medida en el papel del Análisis RAMS, RCM, RBD y Apollo RCA a lo largo de este proceso.
Contenido
- Propósito, Objetivos del Programa, Principios que la Sustentan.
- Entradas de Datos e Información.
- Desarrollo del Proceso.
- Resultados Obtenibles y Entregables.
- Papel de la Metodologías de Análisis RAMS, RCM, RBD y Apollo RCA a lo largo de este proceso.
Desarrollaremos estos puntos en forma integral, como elementos de un sistema de gestión de activos proactivo, analizando su funcionamiento global y sus interacciones.
No necesariamente los subtítulos seguirán dicha lista, pero los objetivos, las entradas, el desarrollo, los resultados y las metodologías, serán la columna vertebral del desarrollo.
Propósito, objetivos del programa, principios que la sustentan
La Gestión de Activos Proactiva es el objetivo de muchas organizaciones en las que el mantenimiento reactivo puede tener un gran impacto en los costos, la rentabilidad y los riesgos. Un caso de negocio contrastando los dos enfoques puede revelar la diferencia cuántica entre ambos, al igual que la evaluación comparativa y las auditorías. Este paso explora los principios necesarios que la sustentan para apoyar la gestión de activos proactiva durante el ciclo de vida de un activo, y a través de las interacciones del sistema de gestión de mantenimiento. Las áreas a tratar incluirán el comportamiento del sistema de mantenimiento, la toma de decisiones, el uso de los datos, los KPI’s y los roles organizacionales.
Entradas de datos e información
Sostener la gestión de activos proactiva requiere de la vigilancia día a día de las fallas, los incidentes y las prácticas de mantenimiento. Este paso explora cuál información es importante, quién participa, cómo concentrarse en los datos críticos que impulsan la mejora.
Desarrollo del proceso
Este paso examina los procesos necesarios para dirigir el desempeño de la gestión de activos fuera de comportamiento reactivo. Quienes están involucrados y cómo las actividades de mejora compiten por los recursos en un entorno exigente. Todos los procesos requieren de partes interesadas, ¿quiénes son y por qué?
Resultados obtenibles y entregables
La aplicación de la mejora continua es donde los neumáticos encuentran la carretera. Muchas organizaciones tradicionales no están bien orientadas para esto. A menudo hay obstáculos o atrasos u otras prioridades. Este paso explora lo que se requiere para la aplicación de los resultados de un sistema de gestión de activos proactiva, y qué medidas se pueden utilizar para asegurarse que los resultados apoyen los objetivos de negocio.
Papel de las metodologías de análisis RAMS, RCM, RBD y APOLLO RCA a lo largo de este proceso
A lo largo de los cuatro pasos los participantes comprenderán:
- El papel del análisis RAMS en Nuevos Proyectos.
- Los cuatro pasos para la Solución Efectiva de Problemas y por qué las empresas encuentran tan difícil descubrir las Causas Raíces.
- El poder de tomar decisiones a partir de datos y la forma de hacerlo de manera continua, como parte de la gestión de activos.
- RCM aplicado como parte de la gestión de activos diaria – rápido, fácil y potente.
- Cómo obtener el máximo rendimiento de la implementación y mantener a las principales partes interesadas apoyando el proceso.
- Mantenimiento Centrado en Confiabilidad, RCM, es una metodología disciplinada que crea planes de mantenimiento eficaces que mitigan o minimizan los efectos de los fallos funcionales o fallos potenciales. Este evento de aprendizaje y contactos ofrece una visión general de los distintos enfoques de RCM y analiza casos prácticos para que se pueda aprender lo que funcionó y lo que no funcionó de aquellos que ya han tenido un poco de dolor y un poco de ganancia.
- Apollo Análisis Causa Raíz, Apollo RCA, es una metodología disciplinada para eliminar las fallas recurrentes o crónicas mediante el descubrimiento de las causas raíces reales de esas fallas. Se analizan casos de estudio para brindar una hoja de ruta clara para aplicar estas estrategias para evitar las fallas.
- Al asistir a aprender sobre RCM y Apollo RCA básicos, descubrirá consejos para asegurarse de que usted puede poner en práctica con eficacia y saber qué obstáculos puede esperar y cómo superarlos.
Gestión de activos proactiva
La Gestión de Activos Proactiva es un objetivo de muchas organizaciones. El mantenimiento reactivo tiene un gran impacto en los costos, la rentabilidad y el riesgo de las operaciones con uso de activos intensivos.
Todos los Directores, Gerentes, Ingenieros y Técnicos de las empresas entienden que es mejor actuar en un entorno Proactivo que en uno Reactivo, sin embargo, ¿por qué los sistemas de gestión de activos se vuelven tan frecuentemente reactivos?
Para analizar lo que sucede y como corregirlo vamos a realizar un mapeo típico del proceso de mantenimiento en un ambiente reactivo.

En dicho mapa, visualizamos la demanda de operaciones respecto a obtener un rendimiento de la planta, tenemos un presupuesto de mantenimiento para lograr dicho objetivo con los recursos necesarios, a saber: mano de obra, materiales, repuestos, contratistas, alianzas de suministro y servicios.
Contamos con almacenes y área de compras para asegurar la logística de suministro y servicios. Tenemos una ingeniería de mantenimiento, que planifica y programa la ejecución de las tareas de mantenimiento, generalmente basada en los históricos de trabajos.
Existe un cierto plan de mantenimiento preventivo, con una cobertura de cierto alcance en cuanto al mantenimiento predictivo. Contamos con un aseguramiento de calidad de los trabajos con cierto grado de efectividad.
Pero dada la situación reactiva en que vivimos, con más del 60% de las actividades realizadas en forma correctiva, entonces los planes programados no se cumplen en su totalidad, no alcanzando su real potencial; la iniciación de los trabajos, debido a las urgencias, es verbal, la mayoría de las veces, con la promesa de luego realizar la orden de trabajo, promesa que mayormente no se cumple, resultando en un histórico de trabajos y de fallas incompleto y sin datos vitales respecto a posibles fallas importantes y críticas.
Este círculo vicioso nos mantiene encerrados, no permitiéndonos desarrollar todo el potencial de efectividad que existe. Para salir de la situación reactiva, e iniciar el camino hacia el proactivo, debemos contar con lazos de mejora continua que permitan analizar tanto los resultados del trabajo completado comparando lo planificado y programado versus lo real; así como los efectos de los mismos en las operaciones tanto en sus aspectos económicos como de riesgo.

Debemos analizar los impactos en la línea de resultados de la compañía, tanto en los eventos críticos, como de los repetitivos que por su frecuencia afectan también seriamente al proceso. Estos lazos de mejora continua se desarrollan principalmente mediante una herramienta de excelencia en el análisis y resolución efectiva de problemas que es el Análisis Causa Raíz (RCA por sus siglas en inglés). El RCA es la herramienta básica para iniciar el desarrollo de la Ingeniería de Confiabilidad. Con el RCA podemos definir los problemas ocurridos, analizar las relaciones causa – efecto que los generan, desarrollar soluciones para controlar las causas raíces e implementarlas para asegurar la no repetición del problema.
Una vez identificadas las causas raíces y registrados sus datos de falla en el histórico, podemos entonces alimentar otras herramientas de la Ingeniería de Confiabilidad, como ser, el Análisis de Weibull, el cual nos permitirá conocer los patrones de falla de dichas causas, y de esa manera poder optimizar las estrategias de mantenimiento mediante el Análisis RCM (Mantenimiento Centrado en Confiabilidad). Esto nos permitirá una mejora continua y dinámica de nuestros planes de mantenimiento.
Asimismo, cuando no alcance con mejorar las estrategias de mantenimiento, y rediseños deban ser efectuados, podremos analizar el diseño del sistema y sus equipos, mediante el Análisis RBD (Diagrama de Bloques de Confiabilidad), para así identificar las áreas de oportunidad, como ser, cuellos de botella, redundancias, stocks intermedios, equipos de bajo desempeño, etc. De esta forma realimentaremos a Ingeniería para realizar las mejoras necesarias.

Mediante este proceso de mejora continua, círculo virtuoso de la confiabilidad, es que lograremos superar la situación reactiva con un 60% o más de correctivo, para llegar a la tan deseada situación proactiva con menos del 20% de correctivo, solamente donde el costo de la falla sea claramente más bajo que cualquier alternativa de prevención; y con más predictivo y proactivo liderando nuestros planes de mantenimiento optimizados.
Valor del premio a la confiabilidad
Para entender claramente este proceso debemos entender el valor del impacto que la confiabilidad de los equipos y sistemas tienen en el negocio, y compararlo con el impacto que tiene la situación reactiva.
Existen varios impactos que la mala o pobre confiabilidad tiene sobre el negocio, a saber:
- Altos costos de mantenimiento.
- Baja disponibilidad de planta.
- Alta carga de trabajos reactivos.
- Alto número de incidentes de seguridad y ambientales.
- Alto número de interrupciones del proceso y problemas de calidad.
- Aumento de inversión de capital por cortas vidas útiles de los equipos y sistemas.
Esto genera en el ambiente reactivo los siguientes impactos de alto costo en el negocio:
- Pérdida de ingresos.
- Aumento del desperdicio.
- Baja utilización de mano de obra.
- Altos costos de repuestos.
- Inventarios altos de repuestos.
- Inventarios altos de productos.
Con este escenario es importante estimar al valor del premio por lograr una mejora de confiabilidad que nos marque el costo–beneficio en el camino a la Gestión de Activos Proactiva.
Para ello debemos poder contestar las siguientes preguntas, las que nos ayudarán a armar el caso de negocio de la confiabilidad:
- ¿Qué nivel de mantenimiento planificado tiene su negocio? (Ej.: 85%).
- ¿Qué nivel de disponibilidad de planta promedio tienes su negocio? (Ej.: 88%).
Tomaremos como regla de comparación, una métrica internacionalmente aceptada que dice que:
“El trabajo no planificado cuesta en promedio tres (3) veces más que el mismo trabajo planificado”.
Analizaremos dos escenarios:
- 1) Suponiendo que aplicamos ingeniería de confiabilidad y logramos reducir en 5% el presupuesto de los costos de mantenimiento no planificado, mediante la reducción de las fallas.
- 2) Suponiendo que aplicamos una simple reducción de costos del 5%, rebajando el presupuesto de costos del mantenimiento planificado.
- 3) Finalmente estimaremos el impacto de mayores ingresos por el aumento de disponibilidad de planta del 1%, 5% y 10%.
Tomaremos como base un presupuesto de 100 MUSD para simplificar los números, y dado que supusimos un 85% de mantenimiento planificado, tendremos 85 MUSD en dicho rubro del presupuesto.
Complementariamente tendremos 15 MUSD en el rubro de mantenimiento no planificado.
1) Si logramos con ingeniería de confiabilidad reducir realmente las fallas, de modo que el mantenimiento no planificado reduzca 5% del 15% al 10% (o dicho de otro modo de 15 a 10 MUSD), esto no significa que bajará el presupuesto global en 5 MUSD. Los modos de falla que dejaron de ser atendidos por tareas no programadas, ahora serán atendidos por tareas programadas, lo cual aplicando la regla del 3:1 en cuanto a costos de no programado versus costo de programado, indica que el costo de las nuevas tareas programadas para atender estos modos de falla será de 1,65 MUSD. Por lo tanto el beneficio neto para el negocio será de 3, 35 MUSD.
2) Ahora veamos el caso de la reducción simple de costos a los gastos de tareas programadas, algo que todos hemos sufrido alguna vez. Aquí cuando reducimos el gasto de mantenimiento programado un 5%, esto no significa que los modos de falla que eran atendidos por las tareas suprimidas van a desaparecer por arte de magia. Por el contrario significa que dichos modos de falla pasarán a ser atendidos por actividades no programadas cuando ocurra la falla. Si nuevamente aplicamos la regla del 3:1, del no programado versus programado, aquellos modos de falla que con actividades programadas costaban 5 MUSD, ahora con actividades no programadas costarán 15 MUSD. Resultando que el pretendido ahorro de 5 MUSD se convirtió en una pérdida neta para el negocio de 10 MUSD.
Para evitar que algún escéptico nos señale que todo esto se basa en una regla del 3:1 de la cual no hemos demostrado su validez, hagámoslo pues, demostrémosla.
Cuando desarrollamos un trabajo planeado de, por ejemplo, cambio de rodamientos, efectivamente solo cambiamos el rodamiento. El hecho de ser planeado nos permite tener todo organizado a pie de máquina antes de la intervención y además nos da la oportunidad de elegir el momento de forma de minimizar, y eventualmente reducir a cero, el costo de parada asociado.
En cambio, cuando la reparación es de emergencia, no planeada, entonces el fallo imprevisto del rodamiento, trae consigo eventuales daños del acople, del eje, del alojamiento del rodamiento y del impulsor de la bomba o estator del motor, sumados a los costos de parada imprevistos.
Todos estos costos extras, sumados a la espera logística de obtener recursos humanos y materiales no planeados, y que por lo tanto no estaban necesariamente disponibles para realizar la tarea, con los eventuales costos extras de sobreprecios y tiempo extra, son los que justifican dicha relación promedio de 3:1 entre los costos de reparaciones no planificadas versus los costos de reparaciones planificadas.
3) Para estimar el impacto de mayores ingresos mediante el aumento de la disponibilidad de planta en 1%, 5% y 10 % haremos algunas hipótesis para fijar ideas. Consideramos como caso base lo siguiente: 88% de disponibilidad, por lo tanto 12% de tiempos de paradas de planta, consideremos que se trata de una empresa con uso intensivo de activos, por lo tanto tomaremos un costo de pérdida de producción por parada de 100.000 USD/hr. Para este caso base tendremos 1051,2 horas de parada al año, generando una pérdida total respecto a las 8760 horas anuales de 105.120.000 USD. Ahora si analizaremos los resultados de calcular la mejora de 1%, 5% y 10% de disponibilidad.

Entonces vemos que los beneficios respectivos son de:
- 1%: 8.760.000 USD.
- 5%: 43.800.000 USD.
- 10%:87.600.000 USD.
Este beneficio extra de 87,6 horas de operación para un 1% de aumento de disponibilidad, que vale 8,76 MUSD, es un fuerte estímulo para la mejora de mantenimiento, mostrando el costo beneficio de la misma.
Pero al mismo tiempo, también genera un fuerte estímulo a que operaciones no entregue los equipos para dar servicio, intentando aumentar los intervalos entre paradas, para así ganar este valor en más operaciones.
Esto genera el riesgo de que el equipo falle en operación, en cuyo caso el costo de la falla sería el triple, generando una pérdida de 8,76×3 MUSD por tiempo de parada.
Entonces se hace necesario un acuerdo importante entre operaciones y mantenimiento de alineación de objetivos, para desarrollar una gestión del cambio que nos lleve del reactivo al proactivo, sin estos contratiempos.
Cursos recomendados






%252FImagen%252FRAMPREDYC-1730060420837.webp%3Falt%3Dmedia%26token%3D2634a7f0-988e-4022-b91f-382503e6e9db&w=3840&q=75)

Herramientas de confiabilidad
Las herramientas modernas de la confiabilidad, tales como el análisis RAMS, el RCM, el RBD, Weibull y el RCA entre otros, permiten desarrollar modelos para evaluar resultados mediante la aplicación de la simulación matemática.
Estas herramientas nos permiten:
- a) Evaluar resultados de diferentes escenarios.
- b) Comparar entre escenarios alternativos, como por ejemplo: Correr a la falla (RTF por sus siglas en inglés), Plan de Mantenimiento actual y Plan de Mantenimiento optimizado.
- c) Armar modelos de planta y equipo donde desarrollamos el Análisis RCM. Evaluamos cada modo de falla, optimizándolo en función de la probabilidad de falla y su impacto en el negocio.
- d) Una vez optimizadas las tareas por cada modo de falla, se forman grupos de tareas, agrupadas por equipo, tipo de tarea, frecuencia, especialidad, condición de equipo parado o en operación, etc. Estos grupos de tareas también se optimizan como grupo.
- e) Permite realizar predicciones base cero del presupuesto de mantenimiento.
- f) Evaluar los perfiles de los planes de mantenimiento por mano de obra y repuestos, identificando el presupuesto necesario optimizado en cada rubro.
- g) Conocer cuáles son los modos de falla críticos, antes de mejorar para poder optimizar con eficacia, y luego de la mejora para saber hacia dónde orientar en el futuro la búsqueda de oportunidades.
Entre las herramientas de la confiabilidad se destacan:
A) Análisis Causa Raíz (RCA). Es una metodología de resolución efectiva de problemas que se basa en los siguientes pasos:
- a. Definir el Problema, estableciendo el Qué, Cuándo, Dónde y la Importancia del mismo.
- b. Desarrollar el Gráfico Causa y Efecto, identificando todas las relaciones causales y soportando cada causa con Evidencias.
- c. Generar Soluciones Creativas para las diferentes causas del gráfico causa y efecto, identificando las Mejores Soluciones.
- d. Implementar y Monitorear las Mejores.
- e. Soluciones para asegurar los resultados.
B) Análisis de Mantenimiento Centrado en Confiabilidad (RCM). Es una metodología estructurada para definir estrategias de mantenimiento que se basa en 7 preguntas claves:
- a. ¿Cuáles son las funciones de los activos? FUNCIONES.
- b. ¿Cuáles son las fallas funcionales de los activos? FALLAS FUNCIONALES.
- c. ¿Qué causa cada falla funcional? MODOS DE FALLA.
- d. ¿Qué sucede cuando cada causa ocurre? EFECTOS DE FALLA.
- e. ¿Que nos importa de todo eso que sucede? CONSECUENCIAS.
- f. ¿Qué debe ser hecho para predecir y/o prevenir la falla? TAREAS PROACTIVAS.
- g. Qué hacer si no hay una buena tarea proactiva? TAREAS A FALTA DE.
Permite desarrollar y simular planes efectivos de mantenimiento para lograr:
- Minimizar los riesgos de seguridad y medio ambiente,
- Minimizar los costos de falla,
- Optimizar las capacidades.
Los sistemas modernos, basados en simulación matemática por el método de Montecarlo, con el soporte de programas de computadoras para realizarlos, permiten desarrollar la jerarquía de los activos, importar datos de bibliotecas de activos similares, desarrollar el análisis funcional, identificar las fallas funcionales, e identificar los modos de falla.
Asociado a cada modo de falla, deberemos indicar sus efectos, los datos de falla con parámetros de la curva de Weibull, los recursos necesarios y la duración de las tareas correctivas y de las tareas predictivas y preventivas posibles de realizar.
Finalmente nos permiten evaluar entre las diferentes opciones:
- No hacer nada. (correctivo),
- Seguir con la estrategia actual,
- Preventivo,
- Predictivo,
- Detectivo, o
- Rediseños.
Para la evaluación de estrategias óptimas, luego de definir las tareas, es posible optimizar su frecuencia y calcular el costo de ciclo de vida (LCC por su sigla en inglés) de cada una de las opciones, y así elegir siempre la mejor opción global.
Este análisis de alternativas realizado a nivel de cada modo de falla, nos garantiza que todo el plan será el óptimo y nos brinda además una herramienta de mejora continua, una vez que podemos recalcular el óptimo para modos de falla que hayan sufrido cambios en sus datos de entrada.
El plan de mantenimiento se convierte así en un documento vivo que constantemente se puede adaptar a medida que los datos de rendimiento se generan y se analizan.
Optimizando los planes por costo de ciclo de vida de los activos, obtenemos planes de mantenimiento con presupuestos base cero, y podemos desarrollar entonces las instrucciones de trabajo detalladas, elaborar las predicciones de mano de obra y repuestos necesarios, así como planificar toda la logística de soporte.
C) Análisis de Diagramas de Bloques de Confiabilidad (RBD). Es una herramienta de simulación para evaluar la capacidad y disponibilidad de una planta o sistema durante su ciclo de vida para:
- a. Mitigar los riesgo de seguridad y medio ambiente,
- b. Minimizar los costos de falla,
- c. Optimizar capacidades y disponibilidades. En el RBD se representa al sistema por las series, paralelos, redundancias, by-pases, buflers y fuentes de potencial que reflejan las relaciones de confiabilidad del sistema, o sea se representa cada elemento no por su incidencia en el flujo de masas o energía del proceso, sino por su incidencia en los fallos del sistema.
Este análisis puede ser realizado tanto a alto nivel, tomando cada sistema, subsistema o equipo como un bloque global complejo, y considerando su falla como de tipo exponencial (aleatoria), dada la complejidad de la misma al evaluarla a alto nivel.
O puede ser realizado bajando al nivel de detalle que se desee, hasta alcanzar los modos de falla individuales con toda la variedad de patrones de falla de Weibull para cada uno.
Esto permite que esta herramienta sea utilizada desde etapas tempranas de la gestión de activos, tanto en la pre-factibilidad como en la factibilidad de proyectos de capital.
D) Análisis de Weibull. La función de Weibull permite representar todos los patrones de falla conocidos, mediante la variación de sus parámetros: h (eta) – vida característica; b (beta) – parámetro de forma; g (gama) – parámetro de localización.

Una vez recolectados datos de falla, podemos aplicar el Análisis de Weibull para conocer los parámetros correspondientes a dichos datos de falla y así conocer el patrón de falla asociado a dicho modo de falla del cual surgieron los datos.

Esto nos permite luego optimizar las estrategias de mantenimiento mediante el RCM.
Resumen final
En resumen, este conjunto de herramientas de confiabilidad que nos permitieron generar los lazos de mejora continua y optimización para salir del reactivo e iniciar el camino al proactivo, nos acompañan en todo el desarrollo del proceso, a lo largo de todo el ciclo de vida de los activos.
Pueden ser usadas tanto para optimizar proyectos de capital de plantas nuevas, como para optimizar plantas existentes en operación. Son la columna vertebral de la Gestión de Activos Proactiva.
La Gestión de Activos Proactiva, es el proceso global de gestión a través del cual consistentemente agregamos valor a la compañía mediante el uso y cuidado de los activos en todo el ciclo de vida. [Partimos de los objetivos del negocio, definimos las estrategias de activos, desarrollamos las herramientas de confiabilidad, disponibilidad, mantenibilidad y seguridad (RAMS) y optimizamos las estrategias de mantenimiento y sus recursos.
La importancia de iniciar estas actividades en las etapas tempranas del ciclo de vida de los activos, es que el costo de los cambios crece en progresión geométrica.

Y que en las etapas tempranas del desarrollo de los proyectos de capital se definen más del 80% de los que serán los futuros costos del ciclo de vida. La modificación de algo en estas etapas tempranas, muchas veces solo representa el costo de tinta sobre papel, pero genera un ahorro significativo a futuro.
Decisiones adecuadas tomadas tempranamente en la fase de proyecto, permite optimizaciones inteligentes que ahorran costos y riesgos importantes.

Además nos permite evitar esos ahorros de corto plazo, tempranos y tentadores, que luego dan lugar al dicho de “lo barato sale caro”.
Sembrando Confiabilidad en épocas tempranas, podremos cosechar una Gestión de Activos Proactiva, con costos optimizados y riesgos minimizados a lo largo de todo el Ciclo de Vida de los Activos.
Autor: Ing. Ind. Santiago Sotuyo, CMRP
Gerente Ingeniería – Latino América
ARMS Reliability
San Pedro M-223 S-8, El Pinar Ciudad de la Costa, CP 15008 Canelones, Uruguay
Correo: ssotuyo@armsreliability.com
Dinos qué te ha parecido el artículo
Artículos recomendados
Big data en la industria 4.0

5.3 Definición del Contexto Operacional

Ciclo Brayton

El Sistema WMS: descubre su aporte a las empresas

Publica tu artículo en la revista #1 de Mantenimiento Industrial
Publicar un artículo en la revista es gratis, no tiene costo.
Solo debes asegurarte que no sea un artículo comercial.
¿Qué esperas?
O envía tu artículo directo: articulos@predictiva21.com
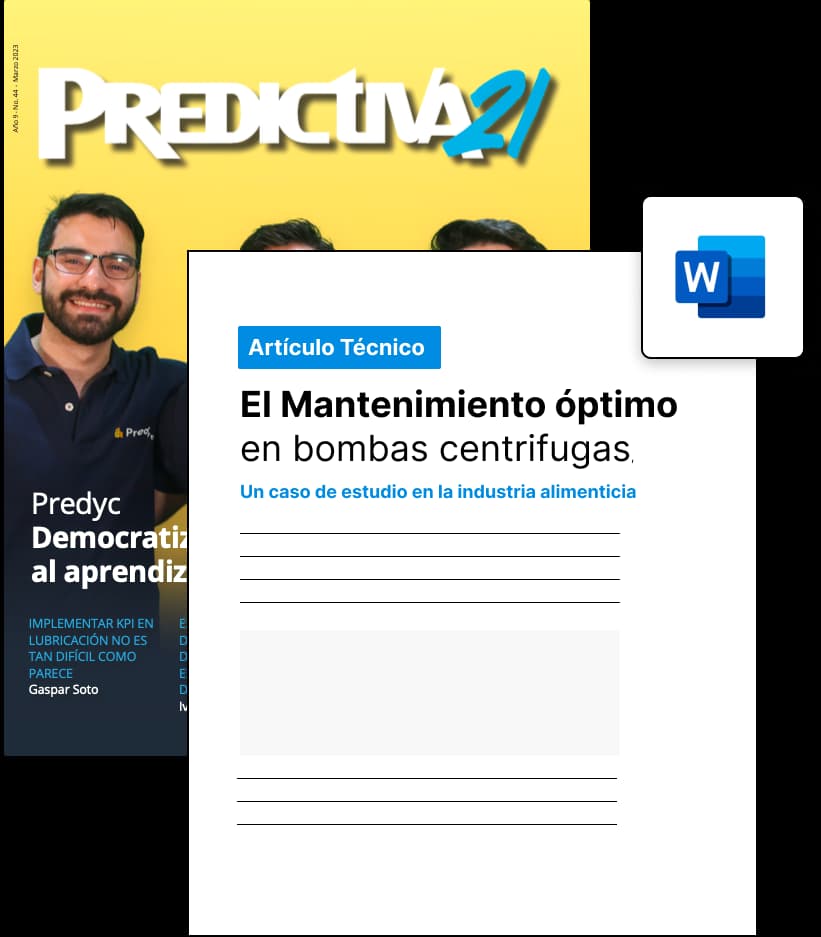