La inspección basada en riesgo y su importancia
Articulo2 de agosto de 2023
Dentro de una empresa o fábrica, es menester realizar tareas o acciones para mitigar los peligros dentro de las instalaciones y proteger no solo los activos y la infraestructura, sino el personal operativo. Para eso, se realizan tareas de inspección, con la intención de verificar el funcionamiento de los sistemas. Por lo tanto, el mantenimiento no es la única acción tomada por el personal de la planta, para resguardar sus activos, existe otra actividad conocida como inspección basada en riesgo. Este proceso es vital para el análisis de causa raíz.
La inspección se define como la acción de comprobar el estado de un objeto o persona velando por su funcionalidad y bienestar. En una planta industrial son tareas planificadas para asegurar un correcto funcionamiento. Por lo tanto, es necesario contar con un personal autorizado para verificar que todos los procesos sigan un reglamento estructurado cumpliendo normas de seguridad e higiene.
No obstante, existe una metodología enfocada en inspeccionar las áreas más susceptibles a desencadenar situaciones que comprometan los sistemas de productividad, la seguridad de los operadores, generar pérdidas de activo o económicas, entre otras, es la inspección de riesgo. No obstante, también se emplea para verificar donde se encuentran los peligros y las medidas para controlar la situación y evitar los peligros para la planta.
Metodología de inspección de riesgo
Para un proceder correcto de la inspección basada en riesgo, los procesos se cimientan en las normas API denominadas así por el “American Petroleum Institute” con la intención de estructurar los requisitos y normas para sostener el estado idóneo de los equipos en la industria del gas y el petróleo. No obstante, se han trasladado estos protocolos a otras industrias las cuáles hagan uso de agentes químicos, tuberías, valvular, entre otros componentes susceptibles a corrosión.
Por lo tanto, permite medir el riesgo asociado de los componentes estáticos dentro de la cadena de producción. Esto, teniendo en cuenta los antecedentes de fallas, formas de deterioro de los componentes, diseño, composición, ambiente, condiciones de operación, mantenimiento, entre otros. Por otra parte, se debe tener en cuenta la calidad inspección, la misma determina las consecuencias y posibilidad de un evento indeseado dentro de la planta.
Por otro lado, la inspección basada en riesgo se ha visto modificada a través del tiempo, permitiendo su evolución para sostener la integridad de activos mecánicos en una planta. Para ampliar el margen de cobertura para medir la disminución de calidad de un equipo con respecto al tiempo se evalúan factores como la integridad mecánica, modelaje probabilístico del deterioro y la valorización del riesgo por corrosión.
Pasos a seguir
La implementación de la inspección basada en riesgo ha ido evolucionando desde su aparición en la década de 1990, en el cual se detallan los peligros implicado en los procesos de producción. Los resultados satisfactorios obtenidos por el sector industrial y la adquisición de nuevas herramientas para la gestión y cálculo de resultados han derivado en la estructuración de una serie de pasos a seguir con la intención de asegurar un procedimiento eficaz. A continuación los procesos estructurados:
- Recolección de datos e información
- Análisis
- Evaluación de consecuencias
- Evaluación de probabilidades
- Evaluación de riesgo
- Clasificación de los riesgos
- Revisión de plan de inspección
- Evaluación de conclusiones
Beneficios de la inspección basada en riesgo
Las actividades enfocadas en sostener la estructura de una organización enfocada en la producción de bienes, tienen como resultado la persistencia en el tiempo de la misma, evitando cualquier suceso perjudicial para la sostenibilidad de las actividades. Por lo tanto, la inspección basada en riesgo es una tarea la cuál conlleva a poseer ventajas para la entidad. A continuación se mencionaran los beneficios de la aplicación:
- Conocer a mejor detalle los sistemas, subsistemas y equipos a disposición por parte de la planta que puedan conllevar a tener riesgos potenciales.
- Resguardar la operatividad de los equipos haciéndolos más confiables en las labores de la planta.
- Mayor seguridad laboral para el personal operativo y de seguridad.
- Reducción de costos en reemplazo de equipos defectuosos o pólizas de seguro.
- Codificación de la información en base de datos, con información sobre los equipos como planos, manuales, informes, procesos y fechas de mantenimiento.
- Aumento de las labores del equipo de trabajo enfocados en el mantenimiento de la planta.
- Optimización de costos al evitar el mantenimiento correctivo de un equipo, para no paralizar las labores de trabajo.
- Detectar métodos para mejorar la calidad de los procesos y los sistemas de gestión de operatividad y mantenimiento.
- Detectar la necesidad de formar a los empleados en nuevas tareas para mejorar la eficiencia dentro de la planta.
Cursos recomendados




%252FImagen%252FRAMPREDYC-1730060420837.webp%3Falt%3Dmedia%26token%3D2634a7f0-988e-4022-b91f-382503e6e9db&w=3840&q=75)



Aplicación de la inspección basada en riesgo
La aplicación de la inspección basa en riesgo, consiste en una serie de pasos anteriormente descritos, por lo tanto, el primero es tener en cuenta los equipos estáticos dentro de la planta, con la intención de obtener una base de datos donde se describa las funciones, componentes y estado de cada uno. No obstante, se puede incluir factores como historial de reparaciones, manuales, planos, fecha de incorporación, entre otros.
Posteriormente, se realiza una evaluación de los equipos para definir las posibles fallas y efectos negativos en los sistemas y subsistemas de la planta. Uno de los factores importantes en esta labor, es identificar el tipo de imperfecto y nivel de gravedad, para medir su consecuencia y nivel de prioridad teniendo en cuenta factores como la economía, seguridad de los empleados, daños a la infraestructura y medio ambiente. De tal manera, se podrá estructurar el nivel de prioridad requerida por máquina en las labores de mantenimiento preventivo.
Por último se planifican los programas de inspección basados en el riesgo, la idea principal es encontrar las posibles fallas que comprometan la estructura de los equipos, dando como resultado la paralización de los subsistemas involucrados. La metodología implementada es realizar actividades de alto rendimiento de los equipos, de esa manera y midiendo el rendimiento comparando los resultados con los descritos por la información anteriormente recolectada se podrá medir el deterioro y situaciones de falla de la máquina.
Relación de la inspección basada en riesgo con el mantenimiento
Cabe destacar, la inspección basa en riesgo se consideraría por su definición y manera de proceder como un pilar fundamental en la estructuración de RCM (“Reliability Centered Maintenance”) o mantenimiento centrado en la confiabilidad, el cual es un procedimiento enfocado en buscar la factibilidad de realizar las labores de mantenimiento preventivo a un equipo teniendo en cuenta las probabilidades de sostener la productividad en un periodo de tiempo determinado.
Para concluir, la inspección basada en riesgo es una actividad procedimental enfocada en buscar los puntos débiles de un equipo, sistema y subsistema con la intención de prever un daño a la infraestructura de la empresa y sus actividades. De tal manera, no se vea comprometido en aspectos de seguridad laboral y económica, evitando un incidente indeseado y permitiendo la entrada de planificación y gestión de mantenimiento preventivo.
Dinos qué te ha parecido el artículo
Artículos recomendados
El internet de las cosas (IoT): pilar de la industria 4.0

Mantenimiento autónomo

9.4 Ventajas del Mantenimiento Predictivo

Excentricidad Dinámica Motores Eléctricos de Inducción

Publica tu artículo en la revista #1 de Mantenimiento Industrial
Publicar un artículo en la revista es gratis, no tiene costo.
Solo debes asegurarte que no sea un artículo comercial.
¿Qué esperas?
O envía tu artículo directo: articulos@predictiva21.com
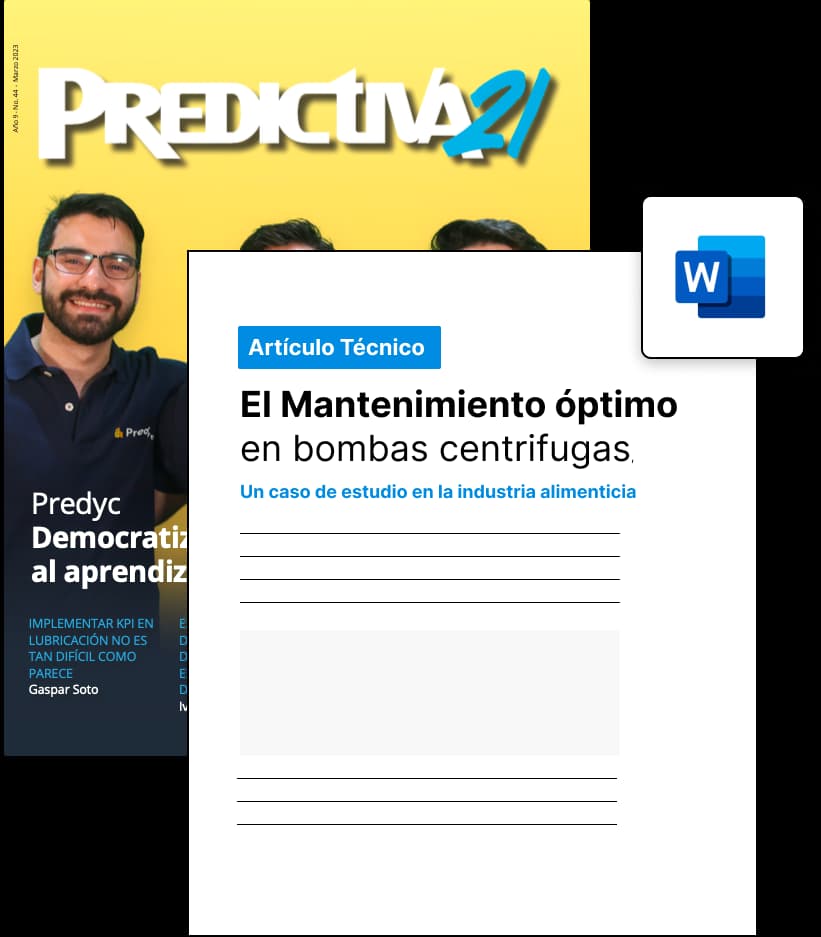
La inspección basada en riesgo y su importancia
Articulo 2 de agosto de 2023Dentro de una empresa o fábrica, es menester realizar tareas o acciones para mitigar los peligros dentro de las instalaciones y proteger no solo los activos y la infraestructura, sino el personal operativo. Para eso, se realizan tareas de inspección, con la intención de verificar el funcionamiento de los sistemas. Por lo tanto, el mantenimiento no es la única acción tomada por el personal de la planta, para resguardar sus activos, existe otra actividad conocida como inspección basada en riesgo. Este proceso es vital para el análisis de causa raíz.
La inspección se define como la acción de comprobar el estado de un objeto o persona velando por su funcionalidad y bienestar. En una planta industrial son tareas planificadas para asegurar un correcto funcionamiento. Por lo tanto, es necesario contar con un personal autorizado para verificar que todos los procesos sigan un reglamento estructurado cumpliendo normas de seguridad e higiene.
No obstante, existe una metodología enfocada en inspeccionar las áreas más susceptibles a desencadenar situaciones que comprometan los sistemas de productividad, la seguridad de los operadores, generar pérdidas de activo o económicas, entre otras, es la inspección de riesgo. No obstante, también se emplea para verificar donde se encuentran los peligros y las medidas para controlar la situación y evitar los peligros para la planta.
Metodología de inspección de riesgo
Para un proceder correcto de la inspección basada en riesgo, los procesos se cimientan en las normas API denominadas así por el “American Petroleum Institute” con la intención de estructurar los requisitos y normas para sostener el estado idóneo de los equipos en la industria del gas y el petróleo. No obstante, se han trasladado estos protocolos a otras industrias las cuáles hagan uso de agentes químicos, tuberías, valvular, entre otros componentes susceptibles a corrosión.
Por lo tanto, permite medir el riesgo asociado de los componentes estáticos dentro de la cadena de producción. Esto, teniendo en cuenta los antecedentes de fallas, formas de deterioro de los componentes, diseño, composición, ambiente, condiciones de operación, mantenimiento, entre otros. Por otra parte, se debe tener en cuenta la calidad inspección, la misma determina las consecuencias y posibilidad de un evento indeseado dentro de la planta.
Por otro lado, la inspección basada en riesgo se ha visto modificada a través del tiempo, permitiendo su evolución para sostener la integridad de activos mecánicos en una planta. Para ampliar el margen de cobertura para medir la disminución de calidad de un equipo con respecto al tiempo se evalúan factores como la integridad mecánica, modelaje probabilístico del deterioro y la valorización del riesgo por corrosión.
Pasos a seguir
La implementación de la inspección basada en riesgo ha ido evolucionando desde su aparición en la década de 1990, en el cual se detallan los peligros implicado en los procesos de producción. Los resultados satisfactorios obtenidos por el sector industrial y la adquisición de nuevas herramientas para la gestión y cálculo de resultados han derivado en la estructuración de una serie de pasos a seguir con la intención de asegurar un procedimiento eficaz. A continuación los procesos estructurados:
- Recolección de datos e información
- Análisis
- Evaluación de consecuencias
- Evaluación de probabilidades
- Evaluación de riesgo
- Clasificación de los riesgos
- Revisión de plan de inspección
- Evaluación de conclusiones
Beneficios de la inspección basada en riesgo
Las actividades enfocadas en sostener la estructura de una organización enfocada en la producción de bienes, tienen como resultado la persistencia en el tiempo de la misma, evitando cualquier suceso perjudicial para la sostenibilidad de las actividades. Por lo tanto, la inspección basada en riesgo es una tarea la cuál conlleva a poseer ventajas para la entidad. A continuación se mencionaran los beneficios de la aplicación:
- Conocer a mejor detalle los sistemas, subsistemas y equipos a disposición por parte de la planta que puedan conllevar a tener riesgos potenciales.
- Resguardar la operatividad de los equipos haciéndolos más confiables en las labores de la planta.
- Mayor seguridad laboral para el personal operativo y de seguridad.
- Reducción de costos en reemplazo de equipos defectuosos o pólizas de seguro.
- Codificación de la información en base de datos, con información sobre los equipos como planos, manuales, informes, procesos y fechas de mantenimiento.
- Aumento de las labores del equipo de trabajo enfocados en el mantenimiento de la planta.
- Optimización de costos al evitar el mantenimiento correctivo de un equipo, para no paralizar las labores de trabajo.
- Detectar métodos para mejorar la calidad de los procesos y los sistemas de gestión de operatividad y mantenimiento.
- Detectar la necesidad de formar a los empleados en nuevas tareas para mejorar la eficiencia dentro de la planta.
Cursos recomendados




%252FImagen%252FRAMPREDYC-1730060420837.webp%3Falt%3Dmedia%26token%3D2634a7f0-988e-4022-b91f-382503e6e9db&w=3840&q=75)



Aplicación de la inspección basada en riesgo
La aplicación de la inspección basa en riesgo, consiste en una serie de pasos anteriormente descritos, por lo tanto, el primero es tener en cuenta los equipos estáticos dentro de la planta, con la intención de obtener una base de datos donde se describa las funciones, componentes y estado de cada uno. No obstante, se puede incluir factores como historial de reparaciones, manuales, planos, fecha de incorporación, entre otros.
Posteriormente, se realiza una evaluación de los equipos para definir las posibles fallas y efectos negativos en los sistemas y subsistemas de la planta. Uno de los factores importantes en esta labor, es identificar el tipo de imperfecto y nivel de gravedad, para medir su consecuencia y nivel de prioridad teniendo en cuenta factores como la economía, seguridad de los empleados, daños a la infraestructura y medio ambiente. De tal manera, se podrá estructurar el nivel de prioridad requerida por máquina en las labores de mantenimiento preventivo.
Por último se planifican los programas de inspección basados en el riesgo, la idea principal es encontrar las posibles fallas que comprometan la estructura de los equipos, dando como resultado la paralización de los subsistemas involucrados. La metodología implementada es realizar actividades de alto rendimiento de los equipos, de esa manera y midiendo el rendimiento comparando los resultados con los descritos por la información anteriormente recolectada se podrá medir el deterioro y situaciones de falla de la máquina.
Relación de la inspección basada en riesgo con el mantenimiento
Cabe destacar, la inspección basa en riesgo se consideraría por su definición y manera de proceder como un pilar fundamental en la estructuración de RCM (“Reliability Centered Maintenance”) o mantenimiento centrado en la confiabilidad, el cual es un procedimiento enfocado en buscar la factibilidad de realizar las labores de mantenimiento preventivo a un equipo teniendo en cuenta las probabilidades de sostener la productividad en un periodo de tiempo determinado.
Para concluir, la inspección basada en riesgo es una actividad procedimental enfocada en buscar los puntos débiles de un equipo, sistema y subsistema con la intención de prever un daño a la infraestructura de la empresa y sus actividades. De tal manera, no se vea comprometido en aspectos de seguridad laboral y económica, evitando un incidente indeseado y permitiendo la entrada de planificación y gestión de mantenimiento preventivo.
Dinos qué te ha parecido el artículo
Artículos recomendados
6 Errores a evitar con el software de gestión de activos (EAM)

Aplicación Práctica del Teorema de Bayes para la Estimación de la Disponibilidad en Activos Industriales

Confiabilidad Organizacional: BEPRO - Método para mejorar los procesos que afectan a la Confiabilidad Operacional

Curso de Mantenimiento de Motores Eléctricos

Publica tu artículo en la revista #1 de Mantenimiento Industrial
Publicar un artículo en la revista es gratis, no tiene costo.
Solo debes asegurarte que no sea un artículo comercial.
¿Qué esperas?
O envía tu artículo directo: articulos@predictiva21.com
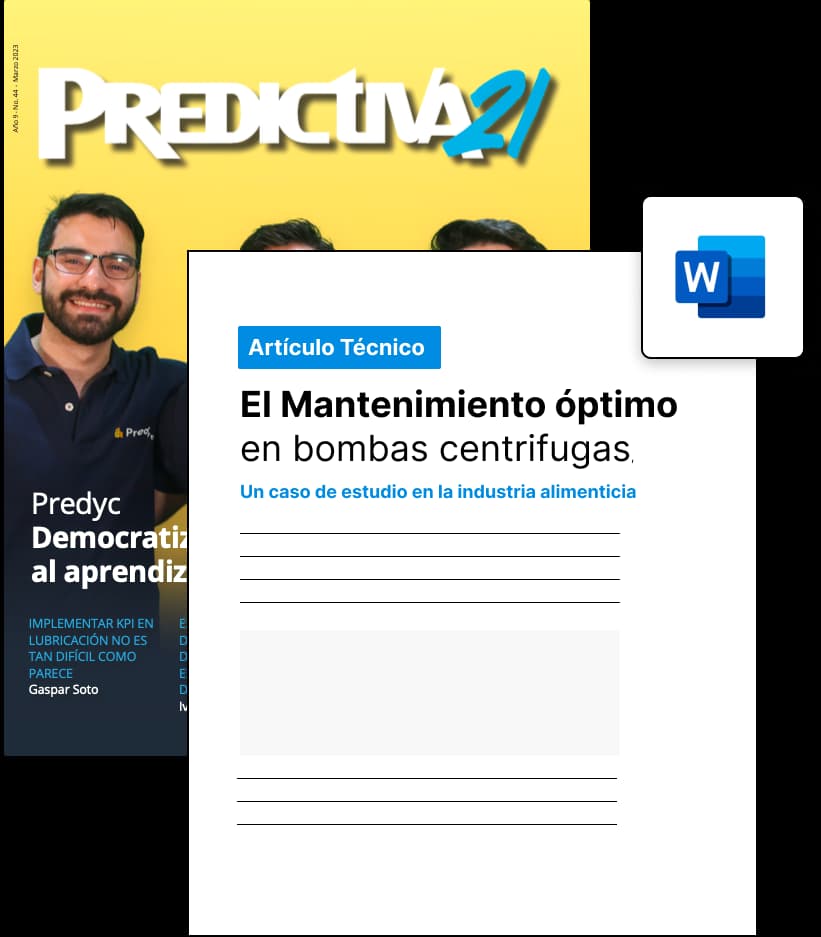