El internista de la 21, Edición 46
Columna14 de diciembre de 2023
Soy Rafael Arguelles F., TSU en Informática, Ingeniero Electricista, MSC en Administración de Negocios, con más de 38 años en el mercado de trabajo técnico, profesional y gerencial. Practicante del Silogismo en mi forma de pensar y actuar, por lo tanto, estoico en mi forma de ser. No les contaré mucho mas de mí, pues no es éste el propósito de esta columna.
En esta oportunidad, estaremos hablando de una “estrategia” y que “contiene” las acciones que deben ejecutarse para garantizar que un activo funcione adecuadamente durante la fase operativa de su ciclo de vida.
Este tema es bastante polémico, especialmente si tomamos en cuenta la diatriba constante e irremediablemente presente, entre quienes piensan una u otra cosa en referencia a la Gestión de Activos y la Gestión del Mantenimiento, sobre todo desde que se publicó un estándar de facto como PAS-55, en forma de estándar oficial, es decir ISO55000. Por supuesto, PAS-55 era un estándar de aplicación solamente local (desde el punto de vista mandatorio), pero era aplicado con mucho éxito en latitudes fuera de su área natural de influencia. Existen colegas, a los cuales respeto en grado sumo como personas y como profesionales, que consideran que la gestión de activos es una cosa, que confiabilidad es otra, que mantenimiento y confiabilidad son procesos antagónicos, etc. Aun se cuentan muchas historias a este respecto, de cómo surgió una y la otra, de cómo el que cuestionó una no cuestionó a la otra, etc. Pero ese no es nuestro tema hoy. Por supuesto, el tema no es cuan antagónico sea, o si uno de ellos incluye al otro. El verdadero tema de importancia es para que existe uno, para que existe el otro y, sobre todo, que espera como salida del proceso quien realmente costea todas estas acciones: EL INVERSOR, dueño de las instalaciones, o cualquier otra figura cuyo nombre no es importante para estos fines, que invierte el capital requerido y que, como un efecto lógico del riesgo que eso implica, espera de regreso una retribución acorde a lo estipulado en los cálculos de retorno de inversión. Por eso, lo que trataremos hoy, no está estrictamente atado a lo que una u otra norma establece (EN16646, ISO55000, etc.).
Referente a esto, les cuento una anécdota, basada por supuesto en experiencias de mis vidas pasadas y cuyo parecido con la realidad de cada quien, es pura coincidencia. Corrían los años 1600, y yo trabajaba para una filial Petroquímica, para quien su producto estrella eran los fertilizantes nitrogenados, y que era propiedad parcial de una multinacional de la misma rama. En una visita para adiestramiento (típico “on the job trainning” de esa empresa) en “RELIABILITY” (en español, cada quien le coloca el nombre que quiere), llamó poderosamente mi atención que ese departamento tenia un nombre muy curioso en aquel entonces para mí: KIR. Por supuesto, tardé un tantito en investigar que significaba dicho nombre, y para mi sorpresa, el mismo era una composición de las iniciales de una frase: “Keep It Running”. Esto se debía, a que existió en un principio una diatriba (una lucha de poder diría yo más bien), por el control de este nuevo juguete cuyo nombre era “RELIABILITY”. ¿Debía estar como una sección en el Departamento de Mantenimiento? O más bien ¿Debía ser una sección en el Departamento de Servicios Técnicos? O quizás, ¿debía funcionar directamente reportando a la Gerencia de Operaciones? Pues bien, el mismísimo CEO de esa empresa (es decir, el máximo representante de los inversores), vino con la perla: “no me importa que nombre tenga, ni en que parte de la empresa esté, a que nivel o a quien reporte, solamente encárguense de que esto sirva para mantener los equipos en funcionamiento (Keep It Running, a.k.a. KIR)”. Aquella fue una lección para mí, que aun agradezco, sobre la importancia de no perder el norte ni la humildad de hacer el trabajo, en equipo, para que los activos se mantengan en servicio, aprovechando al máximo su ciclo de vita útil. Es por esto, que al flujo de trabajo que hoy desglosaré, le colocaré el nombre “The KIR Process Work Flow”. Pero hablemos primero del KIR, recién nacido hace unas 3 o 4 líneas.

Esta entrega la haremos en dos partes: comenzaremos por entregar un poco el significado del proceso, en que consisten las fases, como interactúan para mantener el activo en condiciones de salud optimas, como los costos afectan cada una de las fases, y como el activo se ve afectado por cambios u omisiones en la estrategia. Aquí comenzarán algunas de las más acidas polémicas, pues incluiremos actividades y estrategias en fases que quizás no son las de más típico acomodo. Posteriormente, en nuestra próxima entrega, estableceremos un flujograma para que todo lo ya mencionado, tenga vida propia en el logro del objetivo: Keep It Running. Comencemos entonces, estableciendo nuestra base conceptual de construcción. . En oportunidades, lo más difícil es desaprender lo aprendido, sobre todo si eso aprendido se ha trabajado por cierto tiempo.
Tipos de Mantenimiento: Solo tenemos tres tipos de mantenimiento. Comenzaremos por acá, pues el objetivo de esta columna, como expliqué en la primera edición, es llevar a los más jóvenes profesionales una forma divertida de aprendizajes
Mantenimiento Correctivo: el más “simple” de todos. Pero solo es simple para definirlo, no para ejecutarlo, por eso las comillas. También es el más antiguo de todos, pues al principio de los tiempos, solo se reparaba lo que fallaba, sin intentar evitar dichas fallas. Se trata de las acciones que se ejecutan para llevar un activo que dejó de cumplir su función (parcial o totalmente) por una avería, a una condición estable en la cual puede nuevamente puede cumplir su característica funcional perdida. Antes de continuar, describiendo como se subdivide, preguntémonos:
¿Es malo que tengamos que hacer mantenimiento correctivo? Desde el punto de vista que realmente debemos cuidar, pues la respuesta rotunda es: no necesariamente. De hecho, el RTF (Run To Failure) como estrategia, es ampliamente aceptado e implementado, pues al final del día lo que realmente nos interesa es hacer lo que técnica y sobre todo financieramente, es mejor para la Instalación en la cual este activo se encuentra prestando una función. Es decir, si representa menos pérdida económica dejar que falle, antes que ejecutar otras estrategias de mantenimiento, pues dejarlo fallar es la opción recomendada. Por supuesto, hay estrategias colaterales diversas que deben verse juntas, antes de que esta sea la decisión tomada:
- Repuestos: ¿debo tener un repuesto en mi almacén? Es conveniente entender que tener un repuesto guardado, también tiene un costo)
- Criticidad: Es necesario tener en cuenta la criticidad que induciría una falla en este activo. Por ejemplo, ¿tengo completa redundancia? ¿Si este activo falla de forma inesperada induce una falla catastrófica en otro activo? Un buen ejemplo de este caso, son las bombas de lubricación de ciertos sistemas de compresores o bombas.
- Ambiente/Seguridad: estos dos aspectos, que casi siempre son gerenciados de la mano, por la misma unidad, son frecuentemente olvidados en el análisis.

Ahora, que ya sabemos que no necesariamente el mantenimiento correctivo es malo, hablemos entonces de cuales son necesariamente malos y cuales, incluso, son extremadamente buenos, hablando desde el punto de vista estrictamente financiero (siempre este aspecto debemos tenerlo en cuenta).
Mantenimiento correctivo de emergencia: Es aquel conjunto de acciones que deben ejecutarse de manera inmediata para reponer una función, y que no pueden esperar para ser atendidas. Por supuesto, suponiendo que no tengamos tiempos de espera operacionales, para dar condiciones que se requieren para “entrar” a reparar un equipo. Ejemplos hay de sobra: paradas de equipos rotativos, roturas de tubos (en reformadores, calderas, etc.), fugas de proceso en válvulas o tuberías, etc. Este es, normalmente, el tipo de fallas que queremos evitar a toda costa, pues son las que tienen un mayor costo. Esto último se debe a que el aspecto que más contribuye al alto costo de la falla, es la producción perdida. Es por ello que se implementan otras estrategias, casi siempre predictivas, diseñadas a detectar de forma temprana la falla funcional, de forma que se pueda corregir la misma de forma programada. ¿Qué indicadores nos ayudarían a prevenir este tipo de perdidas funcionales? Lo dejaremos para un poco más tarde.

Mantenimiento Correctivo programado: Cuando una falla funcional parcial es detectada, pero con condiciones operacionales controladas, el equipo en modo “degradado” puede esperar a la preparación requerida para hacer el trabajo, el mantenimiento por su naturaleza es correctivo (pues la intervención está destinada a reponer la función) y también es programado pues no es atendido de emergencia, si no que más bien es un mantenimiento que se realiza aprovechando la “oportunidad” de que otra parte del proceso esta en una falla funcional severa y el proceso está fuera de servicio. Este, es una de las situaciones donde un mantenimiento correctivo no s la mala noticia. Ejemplos, también hay muchísimos, como una bomba que requiere una intervención en un rodamiento, pero aun puede operar en espera de una oportunidad operacional. La oportunidad operacional se presenta ante un blackout eléctrico, y la planta requiere de una parada, y posterior arranque (por supuesto), que permite una ventana de tiempo como para hacer la reparación requerida. Por supuesto, estas intervenciones y situaciones son solamente teóricas, no es que ocurran en la realidad. ¿Cierto? Como les mencioné al principio, cualquier parecido con la realidad es pura coincidencia.

Mantenimiento Correctivo no programado: Es un mantenimiento correctivo que se ejecuta, sin ser programado. Un momento, ¿esto no es un correctivo de emergencia? Pues no, no es lo mismo. Este es otro de los mantenimientos correctivos que traen una consecuencia ¡apetecible! Ocurre principalmente cuando una falla funcional parcial es detectada en un activo y, al intervenir el mismo para corregirla, se evidencia una falla funcional distinta que siendo detectada y sin que la misma introduzca tiempos de parada adicionales, es corregida “aprovechando” la intervención por otra causa. Este tipo de mantenimiento, con frecuencia no es correctamente documentado y mucho menos es correctamente clasificado. Algunos mantenedores tienden a clasificarlo como “preventivo” pues, al detectar el defecto, de forma preventiva fue corregido (esta no es la base conceptual del mantenimiento preventivo, como veremos mas adelante). Otros mantenedores, lo califican como proactivo, pues de forma “proactiva” se corrigió el defecto, lo cual no tiene absolutamente nada que ver con lo que modernamente se ha dado en llamar “Mantenimiento Proactivo” (les confieso que el nombre no me agrada, pues los excesos de esta proactividad suelen traer situaciones un poco difíciles de manejar). El correcto manejo estadístico de estas tres sub clases del mantenimiento correctivo aportan información muy importante que se debe utilizar para mejorar el desempeño y la utilización del activo durante la fase operativa del mismo.
Mantenimiento Preventivo: técnicamente hablando, el mantenimiento preventivo es aquel que se ejecuta antes de que se presente una falla funcional parcial o total, a los fines de impedir la ocurrencia de dicho defecto y que es ejecutado en base a la función tiempo, en una frecuencia determinada, que puede estar dada por un tiempo calendario, o un numero de ciclos cubiertos Por ejemplo, cuando implementamos cambiar un rodamiento cada 5.000 horas, por ejemplo, estamos cambando un elemento cada 5000 horas ya sea que este en falla o no. O, por ejemplo, cuando decidimos cambiar aceite y filtro a un vehículo lo hacemos en base a un recorrido inferencial de tiempo: los km o millas recorridas. El caso del reemplazo del aceite de vehículo es un caso especial, pues dependiendo del tipo de aceite, deberás cambiarlo digamos a los 5.000 km, o a los 10.000 o a los 3.000, pero, independientemente de cuantos km hayas recorrido, en tres meses debes cambiarlo pues se degrada por humedad. Es decir, tiene un doble disparo de mantenimiento preventivo para reemplazar las mismas partes. No siempre involucra el reemplazo programado de piezas, como es costumbre pensar. Esta forma de pensamiento, por cierto, existe debido a que la mayor ocurrencia de fallas funcionales parciales o totales, menores o catastróficas, provienen de desperfectos mecánicos que se “desgastan”, es decir, van perdiendo su capacidad de suplir la función a medida que son usados, como por ejemplo ocurre con los rodamientos. Pero también existen rutinas preventivas, que no involucran el reemplazo de partes pues no hay “piezas que se desgasten”, como por ejemplo ocurre con los elementos de un Sistema de Control, ya sea distribuido o basado en PLC, o instrumentos y componentes en campo o en salas de gabinetes. En los casos en los cuales hablamos de elementos de desgaste, y volvamos al ejemplo del rodamiento, cuando un fabricante te recomienda el reemplazo de un cojinete antifricción (nombre correcto para esta pieza) por horas de operación, lo hace basado en su estadística de falla. Por supuesto, la muestra es tan representativa, que el grado de certeza del tiempo promedio para fallar (MTTF) calculado, es casi siempre muy cercano a la realidad. Sin embargo, es necesario revisar que pasa, cuando ese MTTF no se acerca a la realidad. Si la falla funcional se presenta antes de lo que el MTTF predice, irremediablemente estamos hablando de un MANTENIMIENTO CORRECTIVO DE EMERGENCIA y, dependiendo de la criticidad de este activo, de una pérdida económica muy pero muy importante. ¿Como puede ocurrir esto? Pues algunas causas controlables y otras no controlables, como por ejemplo: mortalidad infantil, mal almacenamiento, errores en el montaje del componente fallado, condiciones operacionales distintas a las establecidas en el diseño, etc. Ahora, si, por el contrario, la falla funcional se presenta después de lo predicho por el MTTF, pues hablamos de una oportunidad perdida. ¿Cuál oportunidad? Pues al reemplazar por recomendación de un fabricante por tiempo, digamos a las 3000 horas de funcionamiento, un componente que aun tiene 1500 horas adicionales. Esto se conoce como un desperdicio. Este tipo de eventos ocurridos en etapas tempranas o tardías en función del MTTF, dieron origen a otra estrategia de mantenimiento: el mantenimiento predictivo.
Mantenimiento Predictivo: Como ya mencionamos, esta estrategia de mantenimiento viene a asistirnos como mantenedores en la reducción significativa de la incertidumbre que rodea a una falla funcional. Actúa, como sabemos todos, por métodos inferenciales. Es decir, inferimos la vida útil remanente de un activo o la existencia de una falla incipiente, en función de la medición de otras variables. Estas variables medidas dependen de la tecnología utilizada en la herramienta predictiva. Existen métodos que predicen la vida útil en función del espectro de temperatura, para por ejemplo detectar puntos calientes en sistemas eléctricos, que equivalen a una conexión eléctrica defectuosa. Es todo lo que podemos inferir con dicha medición, pues existen varias razones por las cuales la conexión eléctrica es defectuosa. Igualmente, podemos utilizar medición de ondas sonoras para detectar defectos, también hacemos cromatografía de gases para condición de aceite, y así sucesivamente. Cuando detectamos una condición no deseada en el comportamiento de un activo, y no conocemos la causa, vamos entonces a realizar pesquisas de falla, o lo que se ha dado en esta modernidad el llamar “Mantenimiento Proactivo” (el nombre de esta estrategia, en sí mismo, debo confesar que me genera incomodidad quizás porque en los años 1600 no tenía un nombre semejante.

Mantenimiento Proactivo (pesquisa de fallas): Como mencioné en varias oportunidades en este mismo artículo, este nombre para esta estrategia no me genera comodidad. Pero lo seguiremos manteniendo. La pesquisa de fallas existe, cuando se trata seriamente, en organizaciones con un grado de madurez importante en la utilización de activos. Trata, sobre todo, esta metodología, de encontrar las causas reales de una perdida funcional y en algunos casos, incluso predecir con determinación de causas cuando un activo pudiera fallar. En este tipo de actividades desarrollamos otras metodologías, como por ejemplo: Los 5 por qué, arboles de falla, what-if, Ishikawa, Pareto, tormenta de ideas (la herramienta, para mi gusto, no es la mejor aplicación para este propósito pues suele tener la tendencia a no aportar evidencias). Es necesario mencionar algunos términos o estrategias que NO SON PARTE DE ESTE SEGMENTO DE MANTENIMIENTO. Por ejemplo, el AMEF (en todas sus variantes o acepciones) no es una estrategia de mantenimiento proactivo. El MANTENIMIENTO CENTRADO EN CONFIABILIDAD (RCM por sus siglas en inglés, como ustedes saben) no es una herramienta de Mantenimiento Proactivo, si no mas bien una estrategia de definición de mantenimiento per sé.

Resumiendo, tenemos el mantenimiento correctivo (reparo cuando falla), el mantenimiento preventivo (reparo o hago servicio en función de una frecuencia, el mantenimiento predictivo (o Mantenimiento Basado en Condición) que utiliza tecnología para aprovechar al máximo cualquier activo y, finalmente, el mantenimiento proactivo que nos lleva a investigar causas raíces para evitar pérdidas funcionales.
Hasta este punto, hemos cubierto distintos aspectos que tienen que ver con el KIR, en las fases 1 y 3, que debemos revisar nuevamente en la próxima entrega, no desde el punto de vista conceptual, si no desde la organización y secuencia lógica en la que deben ocurrir.
En los conceptos han sido enunciados, sin mucha rigurosidad, si no mas bien desde el punto de vista de darle la simplicidad para que sea entendido con claridad. En dichos enunciados, mencionamos con mucha frecuencia una palabra que en particular para mi es clave: “PLANIFICADO”, que es parte fundamental de la fase 2 del KIR. Y es que esta palabra implica, cuando se ejecuta de forma correcta, la diferencia entre poder hacer o no una actividad cualquiera. Lo planificado, aunque suene Cantinflerico debemos decirlo, es algo que existe después de haber pasado por un proceso de planificación. Pero, ¿qué es PLANIFICACIÓN DE MANTENIMIENTO? La planificación del mantenimiento es el proceso de determinar qué trabajo de mantenimiento se debe realizar, que recursos deben estar disponibles para correcta ejecución (herramientas, equipos, insumos, personas y ventana operacional), cual es la prioridad de cada trabajo, que actividades pueden ser concurrentes y cuales deben ser secuenciales. Todas estas fases, si bien son parte de la misma definición, interactúan de manera distinta con cada fase del KIR, pero esto lo trataremos en la segunda entrega. Cerraremos esta entrega, hablando un poco de lo que es backlog. Si a mi me pidieran que, en una sola expresión definiera backlog, inmediatamente respondería: es el mejor indicador de la efectividad del mantenimiento. ¿Por qué? Pues porque mide el retrabajo, los trabajos que se debieron hacer y no se hacen por ventana operacional, los trabajos que estando debidamente planificados (es decir en un plan, preparados y con ventana operacional) no fueron ejecutados. Existen muchas discusiones sobre cómo debe medirse el backlog. De estas formas de medición, yo soy del equipo que el backlog debe llevarse por etapas: las ordenes de trabajo preparadas y en espera de ventana operacional, o sea el backlog de programación. Las ordenes de trabajo que están a la espera de la coordinación de algún recurso, y cuya fecha de solicitud en la orden ya está vencida, es decir el backlog de preparación. La orden de trabajo . . . no hemos hablado al respecto. Y no lo haremos por ahora, pues la orden de trabajo es todo un aspecto de aprendizaje, y que de hecho el flujo relatará desde su nacimiento hasta su cierre, por cuales etapas debe pasar, y en que secuencia debe pasar por dichas etapas.
Dicho esto, espero tengan bastante para interesarse, hablo a los más jóvenes sobre todo, y poder tener un material como para discutir, si así lo desean. Debo cerrar el tema, pues iniciar los tópicos subsiguientes me haría excederme del espacio que dispongo. En la próxima entrega, estaremos hablando de la interrelación de las etapas del KIR, la gestión de mantenimiento, algunas estrategias de mantenimiento (RCM, AMEF, TPM, etc.) y las filosofías o estrategias de optimización con las que pueden convivir (6Ϭ, 5S, etc.).
Referencias Utilizadas:
Paginas Web:
https://instrumentacionhoy.blogspot.com/
https://online.visual-paradigm.com/
Normas/Documentos:
IEC 61511 (Serie)
IEC 61508 (Serie)
Dinos qué te ha parecido el artículo
Artículos recomendados
Mundo ACR Edición 48

Mundo ACR Predictiva21 - Un nuevo Año, una Nueva Etapa

Factores claves para la selección de una bomba centrifuga

El INTERNISTA DE LA 21

Publica tu artículo en la revista #1 de Mantenimiento Industrial
Publicar un artículo en la revista es gratis, no tiene costo.
Solo debes asegurarte que no sea un artículo comercial.
¿Qué esperas?
O envía tu artículo directo: articulos@predictiva21.com
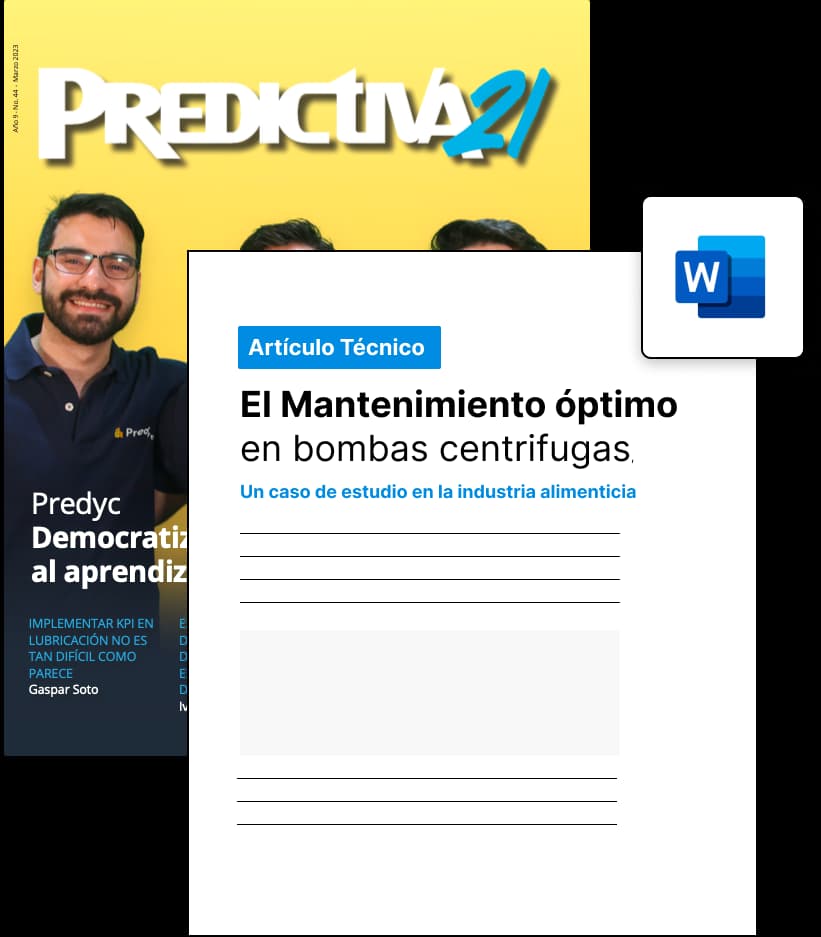
El internista de la 21, Edición 46
Columna 14 de diciembre de 2023Soy Rafael Arguelles F., TSU en Informática, Ingeniero Electricista, MSC en Administración de Negocios, con más de 38 años en el mercado de trabajo técnico, profesional y gerencial. Practicante del Silogismo en mi forma de pensar y actuar, por lo tanto, estoico en mi forma de ser. No les contaré mucho mas de mí, pues no es éste el propósito de esta columna.
En esta oportunidad, estaremos hablando de una “estrategia” y que “contiene” las acciones que deben ejecutarse para garantizar que un activo funcione adecuadamente durante la fase operativa de su ciclo de vida.
Este tema es bastante polémico, especialmente si tomamos en cuenta la diatriba constante e irremediablemente presente, entre quienes piensan una u otra cosa en referencia a la Gestión de Activos y la Gestión del Mantenimiento, sobre todo desde que se publicó un estándar de facto como PAS-55, en forma de estándar oficial, es decir ISO55000. Por supuesto, PAS-55 era un estándar de aplicación solamente local (desde el punto de vista mandatorio), pero era aplicado con mucho éxito en latitudes fuera de su área natural de influencia. Existen colegas, a los cuales respeto en grado sumo como personas y como profesionales, que consideran que la gestión de activos es una cosa, que confiabilidad es otra, que mantenimiento y confiabilidad son procesos antagónicos, etc. Aun se cuentan muchas historias a este respecto, de cómo surgió una y la otra, de cómo el que cuestionó una no cuestionó a la otra, etc. Pero ese no es nuestro tema hoy. Por supuesto, el tema no es cuan antagónico sea, o si uno de ellos incluye al otro. El verdadero tema de importancia es para que existe uno, para que existe el otro y, sobre todo, que espera como salida del proceso quien realmente costea todas estas acciones: EL INVERSOR, dueño de las instalaciones, o cualquier otra figura cuyo nombre no es importante para estos fines, que invierte el capital requerido y que, como un efecto lógico del riesgo que eso implica, espera de regreso una retribución acorde a lo estipulado en los cálculos de retorno de inversión. Por eso, lo que trataremos hoy, no está estrictamente atado a lo que una u otra norma establece (EN16646, ISO55000, etc.).
Referente a esto, les cuento una anécdota, basada por supuesto en experiencias de mis vidas pasadas y cuyo parecido con la realidad de cada quien, es pura coincidencia. Corrían los años 1600, y yo trabajaba para una filial Petroquímica, para quien su producto estrella eran los fertilizantes nitrogenados, y que era propiedad parcial de una multinacional de la misma rama. En una visita para adiestramiento (típico “on the job trainning” de esa empresa) en “RELIABILITY” (en español, cada quien le coloca el nombre que quiere), llamó poderosamente mi atención que ese departamento tenia un nombre muy curioso en aquel entonces para mí: KIR. Por supuesto, tardé un tantito en investigar que significaba dicho nombre, y para mi sorpresa, el mismo era una composición de las iniciales de una frase: “Keep It Running”. Esto se debía, a que existió en un principio una diatriba (una lucha de poder diría yo más bien), por el control de este nuevo juguete cuyo nombre era “RELIABILITY”. ¿Debía estar como una sección en el Departamento de Mantenimiento? O más bien ¿Debía ser una sección en el Departamento de Servicios Técnicos? O quizás, ¿debía funcionar directamente reportando a la Gerencia de Operaciones? Pues bien, el mismísimo CEO de esa empresa (es decir, el máximo representante de los inversores), vino con la perla: “no me importa que nombre tenga, ni en que parte de la empresa esté, a que nivel o a quien reporte, solamente encárguense de que esto sirva para mantener los equipos en funcionamiento (Keep It Running, a.k.a. KIR)”. Aquella fue una lección para mí, que aun agradezco, sobre la importancia de no perder el norte ni la humildad de hacer el trabajo, en equipo, para que los activos se mantengan en servicio, aprovechando al máximo su ciclo de vita útil. Es por esto, que al flujo de trabajo que hoy desglosaré, le colocaré el nombre “The KIR Process Work Flow”. Pero hablemos primero del KIR, recién nacido hace unas 3 o 4 líneas.

Esta entrega la haremos en dos partes: comenzaremos por entregar un poco el significado del proceso, en que consisten las fases, como interactúan para mantener el activo en condiciones de salud optimas, como los costos afectan cada una de las fases, y como el activo se ve afectado por cambios u omisiones en la estrategia. Aquí comenzarán algunas de las más acidas polémicas, pues incluiremos actividades y estrategias en fases que quizás no son las de más típico acomodo. Posteriormente, en nuestra próxima entrega, estableceremos un flujograma para que todo lo ya mencionado, tenga vida propia en el logro del objetivo: Keep It Running. Comencemos entonces, estableciendo nuestra base conceptual de construcción. . En oportunidades, lo más difícil es desaprender lo aprendido, sobre todo si eso aprendido se ha trabajado por cierto tiempo.
Tipos de Mantenimiento: Solo tenemos tres tipos de mantenimiento. Comenzaremos por acá, pues el objetivo de esta columna, como expliqué en la primera edición, es llevar a los más jóvenes profesionales una forma divertida de aprendizajes
Mantenimiento Correctivo: el más “simple” de todos. Pero solo es simple para definirlo, no para ejecutarlo, por eso las comillas. También es el más antiguo de todos, pues al principio de los tiempos, solo se reparaba lo que fallaba, sin intentar evitar dichas fallas. Se trata de las acciones que se ejecutan para llevar un activo que dejó de cumplir su función (parcial o totalmente) por una avería, a una condición estable en la cual puede nuevamente puede cumplir su característica funcional perdida. Antes de continuar, describiendo como se subdivide, preguntémonos:
¿Es malo que tengamos que hacer mantenimiento correctivo? Desde el punto de vista que realmente debemos cuidar, pues la respuesta rotunda es: no necesariamente. De hecho, el RTF (Run To Failure) como estrategia, es ampliamente aceptado e implementado, pues al final del día lo que realmente nos interesa es hacer lo que técnica y sobre todo financieramente, es mejor para la Instalación en la cual este activo se encuentra prestando una función. Es decir, si representa menos pérdida económica dejar que falle, antes que ejecutar otras estrategias de mantenimiento, pues dejarlo fallar es la opción recomendada. Por supuesto, hay estrategias colaterales diversas que deben verse juntas, antes de que esta sea la decisión tomada:
- Repuestos: ¿debo tener un repuesto en mi almacén? Es conveniente entender que tener un repuesto guardado, también tiene un costo)
- Criticidad: Es necesario tener en cuenta la criticidad que induciría una falla en este activo. Por ejemplo, ¿tengo completa redundancia? ¿Si este activo falla de forma inesperada induce una falla catastrófica en otro activo? Un buen ejemplo de este caso, son las bombas de lubricación de ciertos sistemas de compresores o bombas.
- Ambiente/Seguridad: estos dos aspectos, que casi siempre son gerenciados de la mano, por la misma unidad, son frecuentemente olvidados en el análisis.

Ahora, que ya sabemos que no necesariamente el mantenimiento correctivo es malo, hablemos entonces de cuales son necesariamente malos y cuales, incluso, son extremadamente buenos, hablando desde el punto de vista estrictamente financiero (siempre este aspecto debemos tenerlo en cuenta).
Mantenimiento correctivo de emergencia: Es aquel conjunto de acciones que deben ejecutarse de manera inmediata para reponer una función, y que no pueden esperar para ser atendidas. Por supuesto, suponiendo que no tengamos tiempos de espera operacionales, para dar condiciones que se requieren para “entrar” a reparar un equipo. Ejemplos hay de sobra: paradas de equipos rotativos, roturas de tubos (en reformadores, calderas, etc.), fugas de proceso en válvulas o tuberías, etc. Este es, normalmente, el tipo de fallas que queremos evitar a toda costa, pues son las que tienen un mayor costo. Esto último se debe a que el aspecto que más contribuye al alto costo de la falla, es la producción perdida. Es por ello que se implementan otras estrategias, casi siempre predictivas, diseñadas a detectar de forma temprana la falla funcional, de forma que se pueda corregir la misma de forma programada. ¿Qué indicadores nos ayudarían a prevenir este tipo de perdidas funcionales? Lo dejaremos para un poco más tarde.

Mantenimiento Correctivo programado: Cuando una falla funcional parcial es detectada, pero con condiciones operacionales controladas, el equipo en modo “degradado” puede esperar a la preparación requerida para hacer el trabajo, el mantenimiento por su naturaleza es correctivo (pues la intervención está destinada a reponer la función) y también es programado pues no es atendido de emergencia, si no que más bien es un mantenimiento que se realiza aprovechando la “oportunidad” de que otra parte del proceso esta en una falla funcional severa y el proceso está fuera de servicio. Este, es una de las situaciones donde un mantenimiento correctivo no s la mala noticia. Ejemplos, también hay muchísimos, como una bomba que requiere una intervención en un rodamiento, pero aun puede operar en espera de una oportunidad operacional. La oportunidad operacional se presenta ante un blackout eléctrico, y la planta requiere de una parada, y posterior arranque (por supuesto), que permite una ventana de tiempo como para hacer la reparación requerida. Por supuesto, estas intervenciones y situaciones son solamente teóricas, no es que ocurran en la realidad. ¿Cierto? Como les mencioné al principio, cualquier parecido con la realidad es pura coincidencia.

Mantenimiento Correctivo no programado: Es un mantenimiento correctivo que se ejecuta, sin ser programado. Un momento, ¿esto no es un correctivo de emergencia? Pues no, no es lo mismo. Este es otro de los mantenimientos correctivos que traen una consecuencia ¡apetecible! Ocurre principalmente cuando una falla funcional parcial es detectada en un activo y, al intervenir el mismo para corregirla, se evidencia una falla funcional distinta que siendo detectada y sin que la misma introduzca tiempos de parada adicionales, es corregida “aprovechando” la intervención por otra causa. Este tipo de mantenimiento, con frecuencia no es correctamente documentado y mucho menos es correctamente clasificado. Algunos mantenedores tienden a clasificarlo como “preventivo” pues, al detectar el defecto, de forma preventiva fue corregido (esta no es la base conceptual del mantenimiento preventivo, como veremos mas adelante). Otros mantenedores, lo califican como proactivo, pues de forma “proactiva” se corrigió el defecto, lo cual no tiene absolutamente nada que ver con lo que modernamente se ha dado en llamar “Mantenimiento Proactivo” (les confieso que el nombre no me agrada, pues los excesos de esta proactividad suelen traer situaciones un poco difíciles de manejar). El correcto manejo estadístico de estas tres sub clases del mantenimiento correctivo aportan información muy importante que se debe utilizar para mejorar el desempeño y la utilización del activo durante la fase operativa del mismo.
Mantenimiento Preventivo: técnicamente hablando, el mantenimiento preventivo es aquel que se ejecuta antes de que se presente una falla funcional parcial o total, a los fines de impedir la ocurrencia de dicho defecto y que es ejecutado en base a la función tiempo, en una frecuencia determinada, que puede estar dada por un tiempo calendario, o un numero de ciclos cubiertos Por ejemplo, cuando implementamos cambiar un rodamiento cada 5.000 horas, por ejemplo, estamos cambando un elemento cada 5000 horas ya sea que este en falla o no. O, por ejemplo, cuando decidimos cambiar aceite y filtro a un vehículo lo hacemos en base a un recorrido inferencial de tiempo: los km o millas recorridas. El caso del reemplazo del aceite de vehículo es un caso especial, pues dependiendo del tipo de aceite, deberás cambiarlo digamos a los 5.000 km, o a los 10.000 o a los 3.000, pero, independientemente de cuantos km hayas recorrido, en tres meses debes cambiarlo pues se degrada por humedad. Es decir, tiene un doble disparo de mantenimiento preventivo para reemplazar las mismas partes. No siempre involucra el reemplazo programado de piezas, como es costumbre pensar. Esta forma de pensamiento, por cierto, existe debido a que la mayor ocurrencia de fallas funcionales parciales o totales, menores o catastróficas, provienen de desperfectos mecánicos que se “desgastan”, es decir, van perdiendo su capacidad de suplir la función a medida que son usados, como por ejemplo ocurre con los rodamientos. Pero también existen rutinas preventivas, que no involucran el reemplazo de partes pues no hay “piezas que se desgasten”, como por ejemplo ocurre con los elementos de un Sistema de Control, ya sea distribuido o basado en PLC, o instrumentos y componentes en campo o en salas de gabinetes. En los casos en los cuales hablamos de elementos de desgaste, y volvamos al ejemplo del rodamiento, cuando un fabricante te recomienda el reemplazo de un cojinete antifricción (nombre correcto para esta pieza) por horas de operación, lo hace basado en su estadística de falla. Por supuesto, la muestra es tan representativa, que el grado de certeza del tiempo promedio para fallar (MTTF) calculado, es casi siempre muy cercano a la realidad. Sin embargo, es necesario revisar que pasa, cuando ese MTTF no se acerca a la realidad. Si la falla funcional se presenta antes de lo que el MTTF predice, irremediablemente estamos hablando de un MANTENIMIENTO CORRECTIVO DE EMERGENCIA y, dependiendo de la criticidad de este activo, de una pérdida económica muy pero muy importante. ¿Como puede ocurrir esto? Pues algunas causas controlables y otras no controlables, como por ejemplo: mortalidad infantil, mal almacenamiento, errores en el montaje del componente fallado, condiciones operacionales distintas a las establecidas en el diseño, etc. Ahora, si, por el contrario, la falla funcional se presenta después de lo predicho por el MTTF, pues hablamos de una oportunidad perdida. ¿Cuál oportunidad? Pues al reemplazar por recomendación de un fabricante por tiempo, digamos a las 3000 horas de funcionamiento, un componente que aun tiene 1500 horas adicionales. Esto se conoce como un desperdicio. Este tipo de eventos ocurridos en etapas tempranas o tardías en función del MTTF, dieron origen a otra estrategia de mantenimiento: el mantenimiento predictivo.
Mantenimiento Predictivo: Como ya mencionamos, esta estrategia de mantenimiento viene a asistirnos como mantenedores en la reducción significativa de la incertidumbre que rodea a una falla funcional. Actúa, como sabemos todos, por métodos inferenciales. Es decir, inferimos la vida útil remanente de un activo o la existencia de una falla incipiente, en función de la medición de otras variables. Estas variables medidas dependen de la tecnología utilizada en la herramienta predictiva. Existen métodos que predicen la vida útil en función del espectro de temperatura, para por ejemplo detectar puntos calientes en sistemas eléctricos, que equivalen a una conexión eléctrica defectuosa. Es todo lo que podemos inferir con dicha medición, pues existen varias razones por las cuales la conexión eléctrica es defectuosa. Igualmente, podemos utilizar medición de ondas sonoras para detectar defectos, también hacemos cromatografía de gases para condición de aceite, y así sucesivamente. Cuando detectamos una condición no deseada en el comportamiento de un activo, y no conocemos la causa, vamos entonces a realizar pesquisas de falla, o lo que se ha dado en esta modernidad el llamar “Mantenimiento Proactivo” (el nombre de esta estrategia, en sí mismo, debo confesar que me genera incomodidad quizás porque en los años 1600 no tenía un nombre semejante.

Mantenimiento Proactivo (pesquisa de fallas): Como mencioné en varias oportunidades en este mismo artículo, este nombre para esta estrategia no me genera comodidad. Pero lo seguiremos manteniendo. La pesquisa de fallas existe, cuando se trata seriamente, en organizaciones con un grado de madurez importante en la utilización de activos. Trata, sobre todo, esta metodología, de encontrar las causas reales de una perdida funcional y en algunos casos, incluso predecir con determinación de causas cuando un activo pudiera fallar. En este tipo de actividades desarrollamos otras metodologías, como por ejemplo: Los 5 por qué, arboles de falla, what-if, Ishikawa, Pareto, tormenta de ideas (la herramienta, para mi gusto, no es la mejor aplicación para este propósito pues suele tener la tendencia a no aportar evidencias). Es necesario mencionar algunos términos o estrategias que NO SON PARTE DE ESTE SEGMENTO DE MANTENIMIENTO. Por ejemplo, el AMEF (en todas sus variantes o acepciones) no es una estrategia de mantenimiento proactivo. El MANTENIMIENTO CENTRADO EN CONFIABILIDAD (RCM por sus siglas en inglés, como ustedes saben) no es una herramienta de Mantenimiento Proactivo, si no mas bien una estrategia de definición de mantenimiento per sé.

Resumiendo, tenemos el mantenimiento correctivo (reparo cuando falla), el mantenimiento preventivo (reparo o hago servicio en función de una frecuencia, el mantenimiento predictivo (o Mantenimiento Basado en Condición) que utiliza tecnología para aprovechar al máximo cualquier activo y, finalmente, el mantenimiento proactivo que nos lleva a investigar causas raíces para evitar pérdidas funcionales.
Hasta este punto, hemos cubierto distintos aspectos que tienen que ver con el KIR, en las fases 1 y 3, que debemos revisar nuevamente en la próxima entrega, no desde el punto de vista conceptual, si no desde la organización y secuencia lógica en la que deben ocurrir.
En los conceptos han sido enunciados, sin mucha rigurosidad, si no mas bien desde el punto de vista de darle la simplicidad para que sea entendido con claridad. En dichos enunciados, mencionamos con mucha frecuencia una palabra que en particular para mi es clave: “PLANIFICADO”, que es parte fundamental de la fase 2 del KIR. Y es que esta palabra implica, cuando se ejecuta de forma correcta, la diferencia entre poder hacer o no una actividad cualquiera. Lo planificado, aunque suene Cantinflerico debemos decirlo, es algo que existe después de haber pasado por un proceso de planificación. Pero, ¿qué es PLANIFICACIÓN DE MANTENIMIENTO? La planificación del mantenimiento es el proceso de determinar qué trabajo de mantenimiento se debe realizar, que recursos deben estar disponibles para correcta ejecución (herramientas, equipos, insumos, personas y ventana operacional), cual es la prioridad de cada trabajo, que actividades pueden ser concurrentes y cuales deben ser secuenciales. Todas estas fases, si bien son parte de la misma definición, interactúan de manera distinta con cada fase del KIR, pero esto lo trataremos en la segunda entrega. Cerraremos esta entrega, hablando un poco de lo que es backlog. Si a mi me pidieran que, en una sola expresión definiera backlog, inmediatamente respondería: es el mejor indicador de la efectividad del mantenimiento. ¿Por qué? Pues porque mide el retrabajo, los trabajos que se debieron hacer y no se hacen por ventana operacional, los trabajos que estando debidamente planificados (es decir en un plan, preparados y con ventana operacional) no fueron ejecutados. Existen muchas discusiones sobre cómo debe medirse el backlog. De estas formas de medición, yo soy del equipo que el backlog debe llevarse por etapas: las ordenes de trabajo preparadas y en espera de ventana operacional, o sea el backlog de programación. Las ordenes de trabajo que están a la espera de la coordinación de algún recurso, y cuya fecha de solicitud en la orden ya está vencida, es decir el backlog de preparación. La orden de trabajo . . . no hemos hablado al respecto. Y no lo haremos por ahora, pues la orden de trabajo es todo un aspecto de aprendizaje, y que de hecho el flujo relatará desde su nacimiento hasta su cierre, por cuales etapas debe pasar, y en que secuencia debe pasar por dichas etapas.
Dicho esto, espero tengan bastante para interesarse, hablo a los más jóvenes sobre todo, y poder tener un material como para discutir, si así lo desean. Debo cerrar el tema, pues iniciar los tópicos subsiguientes me haría excederme del espacio que dispongo. En la próxima entrega, estaremos hablando de la interrelación de las etapas del KIR, la gestión de mantenimiento, algunas estrategias de mantenimiento (RCM, AMEF, TPM, etc.) y las filosofías o estrategias de optimización con las que pueden convivir (6Ϭ, 5S, etc.).
Referencias Utilizadas:
Paginas Web:
https://instrumentacionhoy.blogspot.com/
https://online.visual-paradigm.com/
Normas/Documentos:
IEC 61511 (Serie)
IEC 61508 (Serie)
Dinos qué te ha parecido el artículo
Artículos recomendados
El internista de la 21, Edición 51
-1736967700910.png%3Falt%3Dmedia%26token%3Da793b062-6090-4b84-b596-192dde707bc4&w=256&q=75)
Factores claves para la selección de una bomba centrifuga

Mundo ACR Edición 48

El internista de la 21 Edición 45

Publica tu artículo en la revista #1 de Mantenimiento Industrial
Publicar un artículo en la revista es gratis, no tiene costo.
Solo debes asegurarte que no sea un artículo comercial.
¿Qué esperas?
O envía tu artículo directo: articulos@predictiva21.com
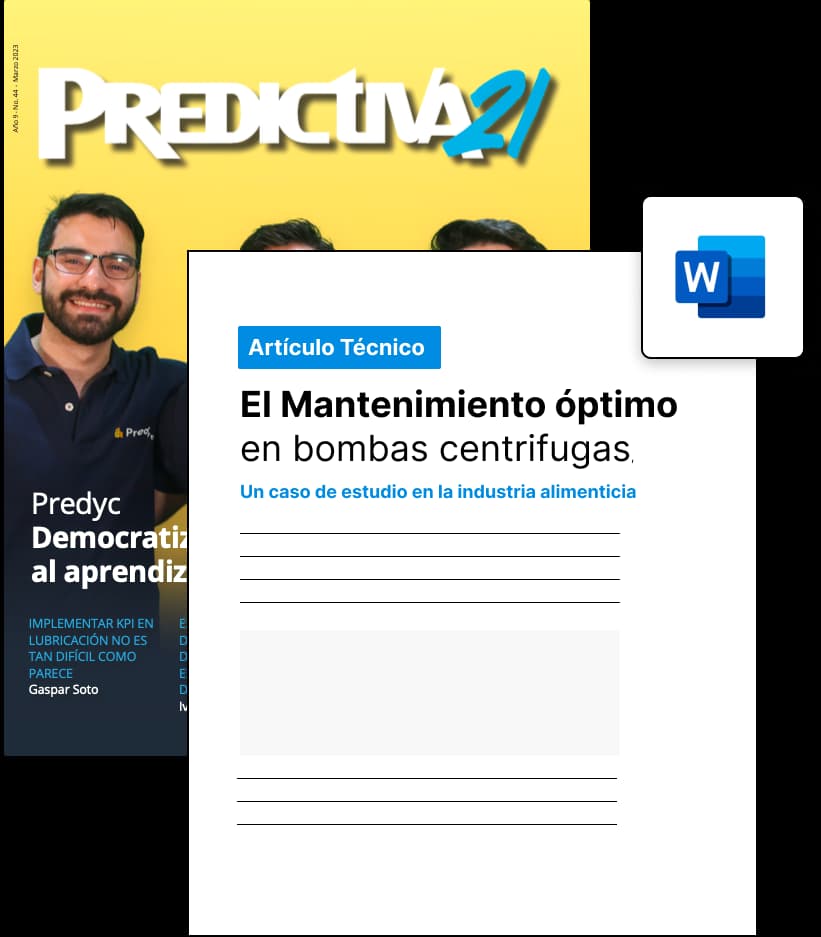