Policy and Procedures
Articulo4 de septiembre de 2019
Plant Hexcellence™ - Policy and Procedures
This article is the 4th in a series of articles. The series documents the continuing journey and quest for a guide to Manufacturing Excellence. The frame we are using to guide or lead us through this journey is the proprietary model called Plant Hexcellence™. As we were discussing in the last issue, the Processes Cell is used to visually map out the flow through a procedure or methodology. We also discussed the interconnection between the Processes cell and the Policy and Procedures cell.
Turning to the the P&P cell, lets first discuss what is a policy, then about procedures and processes and their connectivity in support of the policy.
Certain processes are important enough that the strict adherence to the process is required. Traditionally, policies are created and set in place to deal with regulatory compliance, but they can easily be expanded to encompass any process that is deemed critical or and has multiple variables that need to be managed.

Definition
A Policy is a written and published set of rules, principles or guidelines to create governance. Policies are designed to create a documented standardized behavior or action in specific circumstances. Policies are then supported by Procedures.
Procedures are the specific methods employed to express policies into action in day-to-day operations of the organization. Together, policies and procedures ensure that a point of view/ guideline held by the governing body of an organization is translated into documented steps that result in an outcome compatible with that view.
Lets discuss a real world example that is very relevant and I have seen usually to be absent or lacking within organizations. It will reinforce the connectivity of the Policy-Procedure-Process chain.
Root Cause Failure Analysis (RCA/RCFA)
I have seen in most companies or organization that there is some form of RCFA executed. It is usually around safety / environmental incident investigations, but can be very spotty outside of those disciplines. In addition, more often than not, Safety and Environmental entities are acting independently with little or no shared method or tools for conducting the investigation. RCFA can be a very powerful method and tool for identifying and the elimination of failure while understanding the real causal factors around the incident. The issue is that it is done very haphazardly and adhoc in timing and methodology. This is especially true in organizations that have multiple sites and have grown through acquisition versus organic growth.
In earlier articles, we discussed the balance required in a business to be healthy. There must occur a balance in Safety, Environmental and Profit. A single RCA/RCFA policy should be written that encompasses all of these elements.
- The policy should declare that an RCA/RCFA shall be executed in specific circumstances. (Note: Shall is a word with legal obligation, non optional in execution).
- Trigger points should be defined.
- – A Safety incident or near miss.
- – An Environmental incident or near miss.
- – Loss of Profit incident.
- a) Loss of revenue greater than X dollars as result of the failure (be sure to include potential fines or contract loss as part of the potential total value).
- b) Production down time greater than X as result of the failure (use of this metric is when the cost of down time is unknown or is in a process with accumulation of WIP (Work in Progress) and therefore there is minimal or no loss in end product revenue).
- c) Cost of repair greater than X dollars as result of the failure (this must include all manpower and rework).
- There should be two levels for each trigger point so that a less stringent method of RCFA can be used without effecting operations greatly i.e. 5-Why.
- Once the trigger has been activated, then a cross functional team “must” meet within a specific time frame of the incident (ideally 24 hours or less).
- The RCFA team will have a standard listing of roles that must be in attendance.
- – Individual names will be listed as to who is qualified to fill that role in that circumstance in writing.
- The method of RCFA is listed in the policy.
- All personnel that are listed will have had training in the methodology.
- A time frame is designated for initial results.
- A time frame is designated for final results.
- A set procedure and process should be declared on how to document and implement change as result of the findings.
A documented work ow process map should be made to create a visual representation of the method of 1. When to execute an RCFA? 2. Method and flow to actually execute the RCFA? 3. Methods to implement actions as result of the RCFA.
Now the organization has a policy and standard method for understanding:
- What is an RCFA?
- Why to execute?
- When to execute?
- Who will execute?
- How to execute?
- Result expectations from the execution.
Looking at the example above, It becomes very evident about the inter-connectivity between the Policy-Procedure-Processes chain and how that connectivity can help an organization achieve it’s goals.
Stay tuned for the next article in the series where we will discuss the Performance (measurement) of a organization.
Author: Scott Kelley, CMRP
Managing Director
c: 713.962.1978
Mail: scottkelley@geometricreliability.com
Dinos qué te ha parecido el artículo
Artículos recomendados
Desafíos que enfrentan los Gerentes de Mantenimiento

Ultrasonido

Propuesta de adopción de modelos de optimización de alcance, duración y costo en paradas de planta

Lo que dejó el 2023 en Predictiva21. Tú eres parte de esto.

Publica tu artículo en la revista #1 de Mantenimiento Industrial
Publicar un artículo en la revista es gratis, no tiene costo.
Solo debes asegurarte que no sea un artículo comercial.
¿Qué esperas?
O envía tu artículo directo: articulos@predictiva21.com
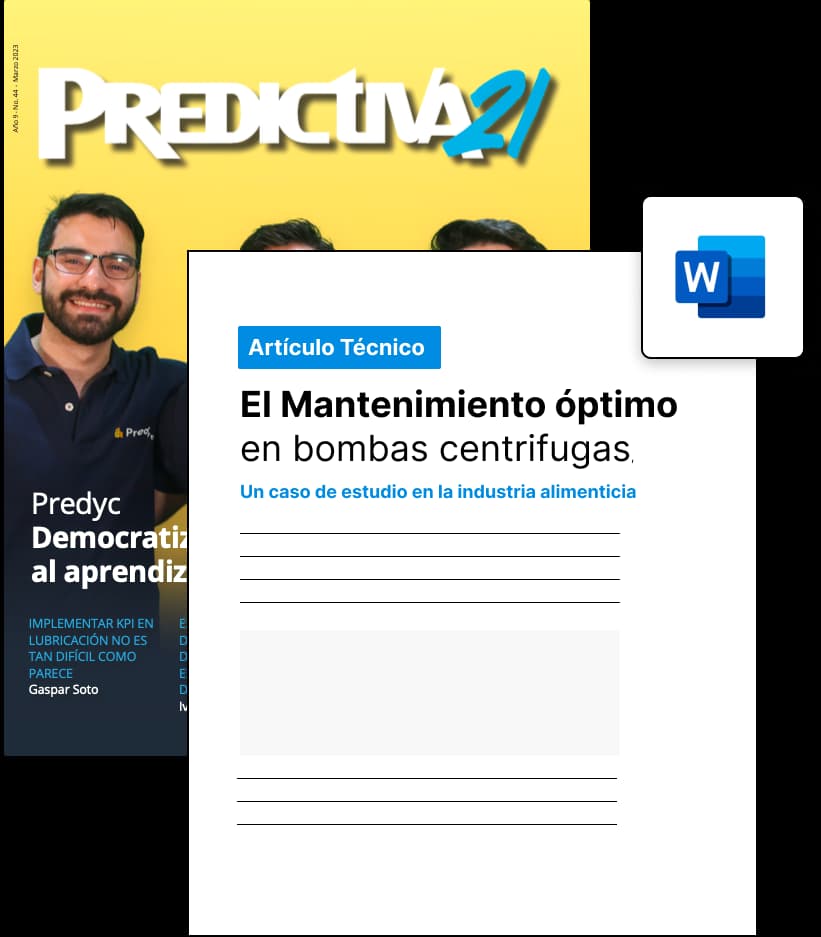
Policy and Procedures
Articulo 4 de septiembre de 2019Plant Hexcellence™ - Policy and Procedures
This article is the 4th in a series of articles. The series documents the continuing journey and quest for a guide to Manufacturing Excellence. The frame we are using to guide or lead us through this journey is the proprietary model called Plant Hexcellence™. As we were discussing in the last issue, the Processes Cell is used to visually map out the flow through a procedure or methodology. We also discussed the interconnection between the Processes cell and the Policy and Procedures cell.
Turning to the the P&P cell, lets first discuss what is a policy, then about procedures and processes and their connectivity in support of the policy.
Certain processes are important enough that the strict adherence to the process is required. Traditionally, policies are created and set in place to deal with regulatory compliance, but they can easily be expanded to encompass any process that is deemed critical or and has multiple variables that need to be managed.

Definition
A Policy is a written and published set of rules, principles or guidelines to create governance. Policies are designed to create a documented standardized behavior or action in specific circumstances. Policies are then supported by Procedures.
Procedures are the specific methods employed to express policies into action in day-to-day operations of the organization. Together, policies and procedures ensure that a point of view/ guideline held by the governing body of an organization is translated into documented steps that result in an outcome compatible with that view.
Lets discuss a real world example that is very relevant and I have seen usually to be absent or lacking within organizations. It will reinforce the connectivity of the Policy-Procedure-Process chain.
Root Cause Failure Analysis (RCA/RCFA)
I have seen in most companies or organization that there is some form of RCFA executed. It is usually around safety / environmental incident investigations, but can be very spotty outside of those disciplines. In addition, more often than not, Safety and Environmental entities are acting independently with little or no shared method or tools for conducting the investigation. RCFA can be a very powerful method and tool for identifying and the elimination of failure while understanding the real causal factors around the incident. The issue is that it is done very haphazardly and adhoc in timing and methodology. This is especially true in organizations that have multiple sites and have grown through acquisition versus organic growth.
In earlier articles, we discussed the balance required in a business to be healthy. There must occur a balance in Safety, Environmental and Profit. A single RCA/RCFA policy should be written that encompasses all of these elements.
- The policy should declare that an RCA/RCFA shall be executed in specific circumstances. (Note: Shall is a word with legal obligation, non optional in execution).
- Trigger points should be defined.
- – A Safety incident or near miss.
- – An Environmental incident or near miss.
- – Loss of Profit incident.
- a) Loss of revenue greater than X dollars as result of the failure (be sure to include potential fines or contract loss as part of the potential total value).
- b) Production down time greater than X as result of the failure (use of this metric is when the cost of down time is unknown or is in a process with accumulation of WIP (Work in Progress) and therefore there is minimal or no loss in end product revenue).
- c) Cost of repair greater than X dollars as result of the failure (this must include all manpower and rework).
- There should be two levels for each trigger point so that a less stringent method of RCFA can be used without effecting operations greatly i.e. 5-Why.
- Once the trigger has been activated, then a cross functional team “must” meet within a specific time frame of the incident (ideally 24 hours or less).
- The RCFA team will have a standard listing of roles that must be in attendance.
- – Individual names will be listed as to who is qualified to fill that role in that circumstance in writing.
- The method of RCFA is listed in the policy.
- All personnel that are listed will have had training in the methodology.
- A time frame is designated for initial results.
- A time frame is designated for final results.
- A set procedure and process should be declared on how to document and implement change as result of the findings.
A documented work ow process map should be made to create a visual representation of the method of 1. When to execute an RCFA? 2. Method and flow to actually execute the RCFA? 3. Methods to implement actions as result of the RCFA.
Now the organization has a policy and standard method for understanding:
- What is an RCFA?
- Why to execute?
- When to execute?
- Who will execute?
- How to execute?
- Result expectations from the execution.
Looking at the example above, It becomes very evident about the inter-connectivity between the Policy-Procedure-Processes chain and how that connectivity can help an organization achieve it’s goals.
Stay tuned for the next article in the series where we will discuss the Performance (measurement) of a organization.
Author: Scott Kelley, CMRP
Managing Director
c: 713.962.1978
Mail: scottkelley@geometricreliability.com
Dinos qué te ha parecido el artículo
Artículos recomendados
Understanding and implementing Maintenance Excellence

Uso y abuso del concepto “Creación de valor desde la gestión de mantenimiento”

Gestión de mantenimiento de averías

Educación Formal para el Mantenimiento

Publica tu artículo en la revista #1 de Mantenimiento Industrial
Publicar un artículo en la revista es gratis, no tiene costo.
Solo debes asegurarte que no sea un artículo comercial.
¿Qué esperas?
O envía tu artículo directo: articulos@predictiva21.com
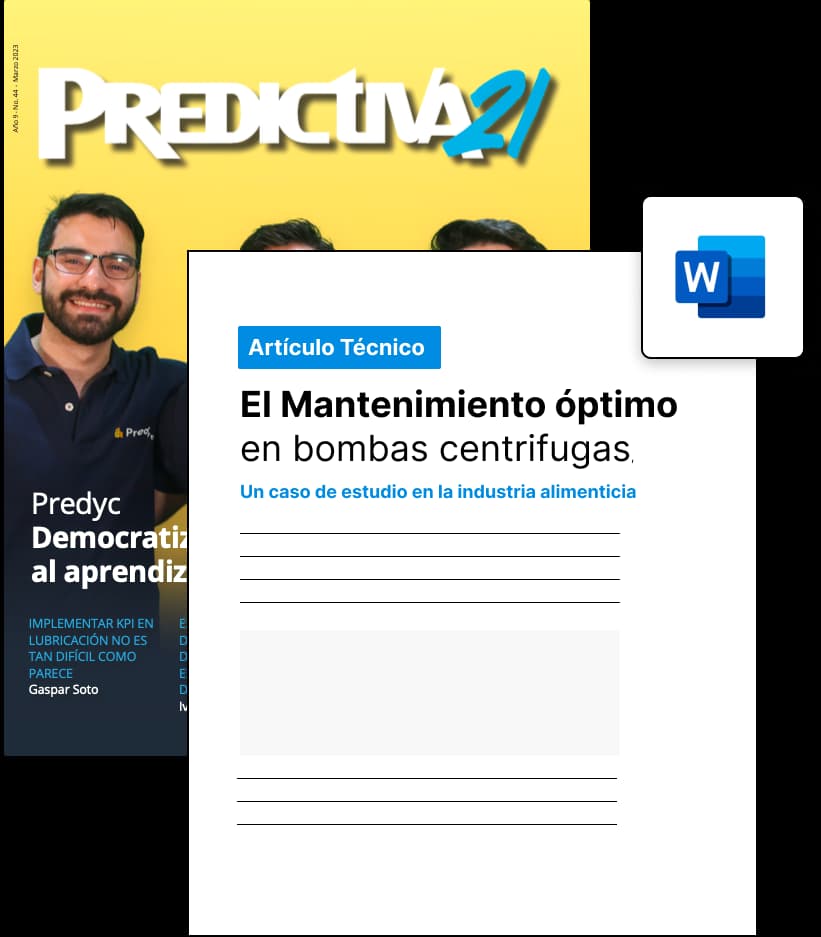