Probar, Detectar y Aislar – Aplicado al Mantenimiento. (Aplicación del Método recomendado por la OMS para la pandemia de COVID-19 “Probar, Detectar y Aislar” al mantenimiento).
Articulo12 de agosto de 2020
Siempre he creído que los métodos que funcionan en una disciplina pueden ser llevados transversalmente a otras. Conceptos lógicos como el que publicamos en nuestro artículo anterior “Redefiniendo la regla de Pareto” y que proviene de las estrategias para la atención de los contagiados por el virus del COVID-19, pueden aportar resultados sorprendentes cuando los adaptamos a nuestro contexto.
Esta semana estudiaba las estrategias que se han seguido en diversos países para conseguir de manera óptima controlar los contagios y lograr “aplanar la curva”. La Organización Mundial de la Salud (OMS) ha recomendado hacer pruebas (muchas pruebas), para detectar aquellos contagiados y entonces aislarlos para detener la cadena de transmisión. Al leer el artículo, rápidamente vino a mi mente la conexión con nuestra industria y las estrategias de monitorización de la condición de la salud de las máquinas.
Probar: En muchas ocasiones en el diseño de las estrategias de mantenimiento basado en condición (MBC) hemos caído en el error de hacer pocas pruebas (modelo centinela) y eso nos lleva a detectar muchos menos casos que los que realmente existen. Usando las estimaciones de este modelo en el caso del COVID-19, podríamos estimar que por cada caso que detectamos con esta estrategia pudieran existir entre 8 y 12 casos no detectados.
En el caso del MBC, además de seleccionar las máquinas críticas y sus modos de fallo críticos, es necesario establecer una frecuencia de monitorización con base en el desarrollo del modo de fallo. Es común encontrar en la industria un intento por estandarizar las frecuencias de muestra en máquinas con diferentes contextos operacionales y diferentes tiempos de desarrollo de la falla. Todas tienen la misma frecuencia de muestreo y contrapone lo establecido en el estándar internacional ISO 17359:18.
Identificar: Este es el objetivo de la estrategia: identificar una variación en algún parámetro que saque de estabilidad a la máquina y que pueda ocasionar una falla funcional. Buscamos un positivo en su fase más temprana para poder tratar el caso con la acción adecuada que permita ampliar la vida del componente. Exactamente lo que se pretende con la estrategia de identificar las personas infectadas con el virus. Deseamos que su detección nos permita evitar llegar a ese 5% de los casos que requieren de hospitalización y terapias de ventilación. En ocasiones detectamos la falla más cercana a la falla funcional y entonces lo que nos queda por hacer es un tratamiento de emergencia o incluso la programación de una intervención de reemplazo del componente para evitar la pérdida de la función. Si nuestra muestra llega tarde debido a que hemos seleccionado una frecuencia mayor al tiempo de desarrollo de la falla, estaremos asumiendo la pérdida de la función del componente sin un aviso previo. Esta es la razón principal por la que las estrategias de MBC no logran detectar muchas de las fallas de la máquina. No deseo hacer la analogía con la salud en este caso.
Aislar: En el caso de la contingencia aislar al paciente permite controlar la cadena de transmisión del virus. En el caso de nuestra máquina, lo que deseamos es el aislamiento de la causa de la condición anormal. Identificarla plenamente y establecer una acción que contribuya a evitar que se vuelva a presentar. Proactivamente, remover el defecto para que no se vuelva a presentar. El éxito del MBC depende de la efectividad de estas acciones y ello depende de la capacidad y conocimiento del especialista que está efectuando el diagnóstico y el pronóstico. Con base en esta información y la detección de la “enfermedad” (modo de falla), se recomienda el tratamiento adecuado. Que esa persona no contagie a otros sería en este caso que ese defecto no vuelva a ocasionar un problema.
Les deseo éxito en sus estrategias de cuidado de la salud de ustedes y sus personas cercanas, así como en sus estrategias de MBC.
Autor: Gerardo Trujillo C.
Dinos qué te ha parecido el artículo
Artículos recomendados
El Know How y la Gestión del Activo Humano

Serie: “Confiabilidad en Sistemas de Misión Crítica: Empezar por el Principio”. Sistemas de Alimentación Eléctrica Crítica (III Parte)

Termografía I

Funciones de un planificador de mantenimiento

Publica tu artículo en la revista #1 de Mantenimiento Industrial
Publicar un artículo en la revista es gratis, no tiene costo.
Solo debes asegurarte que no sea un artículo comercial.
¿Qué esperas?
O envía tu artículo directo: articulos@predictiva21.com
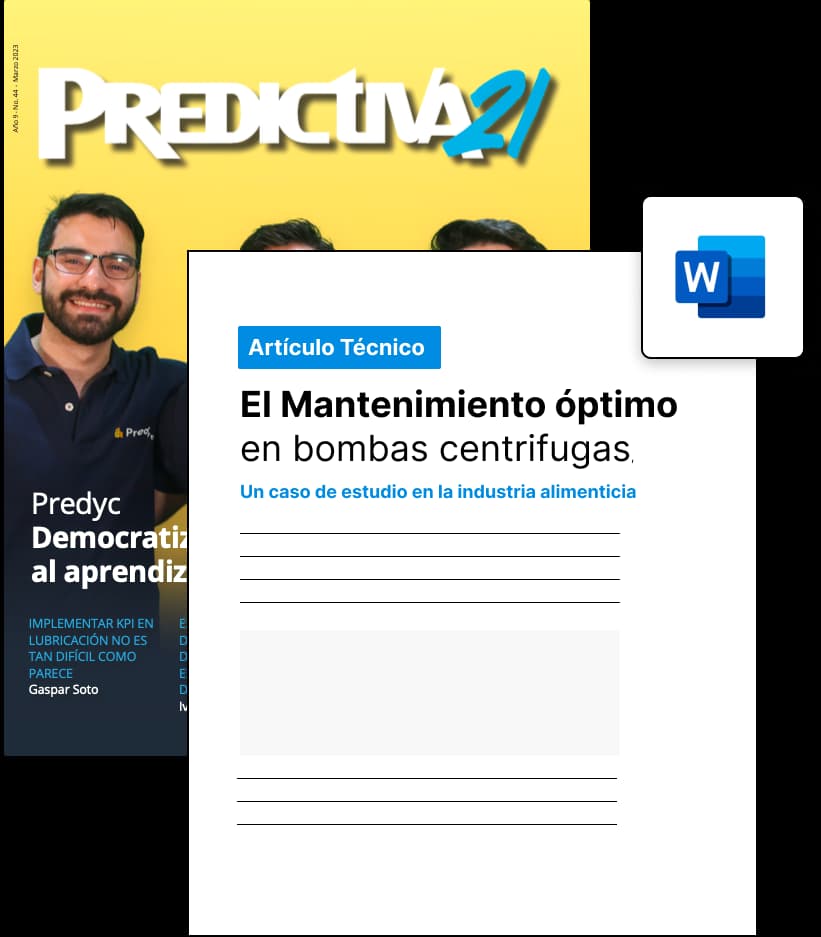
Probar, Detectar y Aislar – Aplicado al Mantenimiento. (Aplicación del Método recomendado por la OMS para la pandemia de COVID-19 “Probar, Detectar y Aislar” al mantenimiento).
Articulo 12 de agosto de 2020Siempre he creído que los métodos que funcionan en una disciplina pueden ser llevados transversalmente a otras. Conceptos lógicos como el que publicamos en nuestro artículo anterior “Redefiniendo la regla de Pareto” y que proviene de las estrategias para la atención de los contagiados por el virus del COVID-19, pueden aportar resultados sorprendentes cuando los adaptamos a nuestro contexto.
Esta semana estudiaba las estrategias que se han seguido en diversos países para conseguir de manera óptima controlar los contagios y lograr “aplanar la curva”. La Organización Mundial de la Salud (OMS) ha recomendado hacer pruebas (muchas pruebas), para detectar aquellos contagiados y entonces aislarlos para detener la cadena de transmisión. Al leer el artículo, rápidamente vino a mi mente la conexión con nuestra industria y las estrategias de monitorización de la condición de la salud de las máquinas.
Probar: En muchas ocasiones en el diseño de las estrategias de mantenimiento basado en condición (MBC) hemos caído en el error de hacer pocas pruebas (modelo centinela) y eso nos lleva a detectar muchos menos casos que los que realmente existen. Usando las estimaciones de este modelo en el caso del COVID-19, podríamos estimar que por cada caso que detectamos con esta estrategia pudieran existir entre 8 y 12 casos no detectados.
En el caso del MBC, además de seleccionar las máquinas críticas y sus modos de fallo críticos, es necesario establecer una frecuencia de monitorización con base en el desarrollo del modo de fallo. Es común encontrar en la industria un intento por estandarizar las frecuencias de muestra en máquinas con diferentes contextos operacionales y diferentes tiempos de desarrollo de la falla. Todas tienen la misma frecuencia de muestreo y contrapone lo establecido en el estándar internacional ISO 17359:18.
Identificar: Este es el objetivo de la estrategia: identificar una variación en algún parámetro que saque de estabilidad a la máquina y que pueda ocasionar una falla funcional. Buscamos un positivo en su fase más temprana para poder tratar el caso con la acción adecuada que permita ampliar la vida del componente. Exactamente lo que se pretende con la estrategia de identificar las personas infectadas con el virus. Deseamos que su detección nos permita evitar llegar a ese 5% de los casos que requieren de hospitalización y terapias de ventilación. En ocasiones detectamos la falla más cercana a la falla funcional y entonces lo que nos queda por hacer es un tratamiento de emergencia o incluso la programación de una intervención de reemplazo del componente para evitar la pérdida de la función. Si nuestra muestra llega tarde debido a que hemos seleccionado una frecuencia mayor al tiempo de desarrollo de la falla, estaremos asumiendo la pérdida de la función del componente sin un aviso previo. Esta es la razón principal por la que las estrategias de MBC no logran detectar muchas de las fallas de la máquina. No deseo hacer la analogía con la salud en este caso.
Aislar: En el caso de la contingencia aislar al paciente permite controlar la cadena de transmisión del virus. En el caso de nuestra máquina, lo que deseamos es el aislamiento de la causa de la condición anormal. Identificarla plenamente y establecer una acción que contribuya a evitar que se vuelva a presentar. Proactivamente, remover el defecto para que no se vuelva a presentar. El éxito del MBC depende de la efectividad de estas acciones y ello depende de la capacidad y conocimiento del especialista que está efectuando el diagnóstico y el pronóstico. Con base en esta información y la detección de la “enfermedad” (modo de falla), se recomienda el tratamiento adecuado. Que esa persona no contagie a otros sería en este caso que ese defecto no vuelva a ocasionar un problema.
Les deseo éxito en sus estrategias de cuidado de la salud de ustedes y sus personas cercanas, así como en sus estrategias de MBC.
Autor: Gerardo Trujillo C.
Dinos qué te ha parecido el artículo
Artículos recomendados
¿Cómo implementar de manera estratégica energías renovables en la Industria?

ISO 55000 series: A Tool for Assets Management

CÓMO HACER UN PRESUPUESTO DE MANTENIMIENTO

Estudio de Causa de Fallo realizado al Turborreactor Viper MK540 de la AeronaveAermachi, perteneciente a la Armada Argentina

Publica tu artículo en la revista #1 de Mantenimiento Industrial
Publicar un artículo en la revista es gratis, no tiene costo.
Solo debes asegurarte que no sea un artículo comercial.
¿Qué esperas?
O envía tu artículo directo: articulos@predictiva21.com
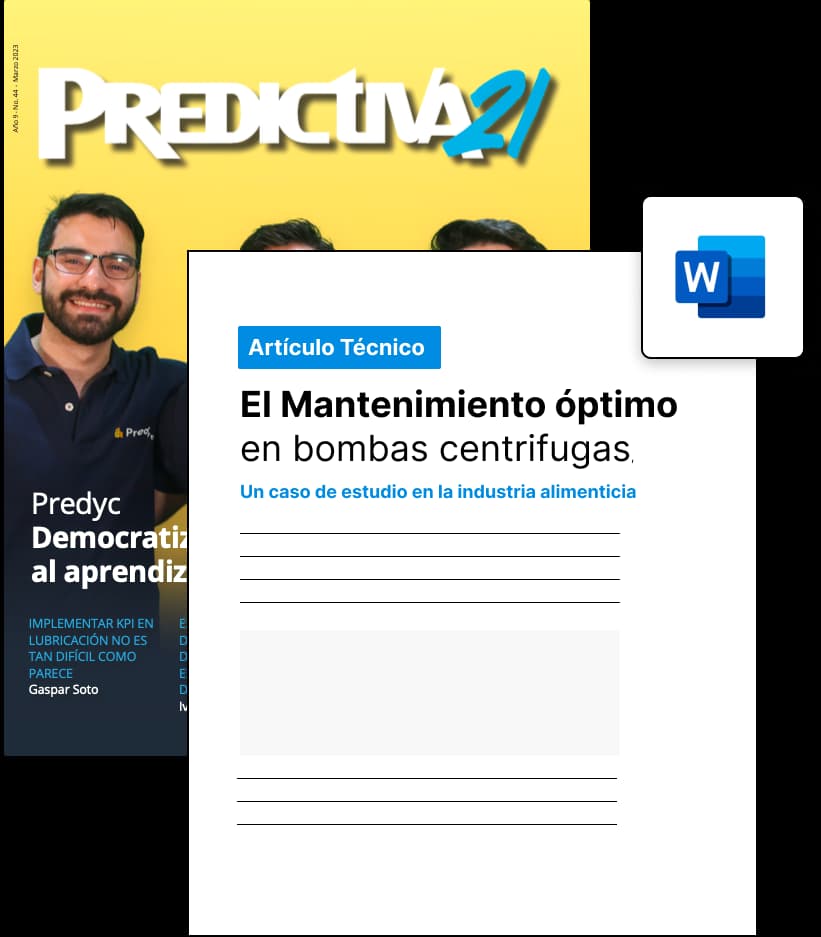