Programación del Mantenimiento - Inventario, OT, Datos y Registro
Libros31 de agosto de 2020
Programa Maestro de Mantenimiento Preventivo
Se llama Programa Maestro de Mantenimiento Preventivo, al proceso de correlación de los códigos de los equipos con la periodicidad, cronogramas de ejecución de las actividades programadas, instrucciones de mantenimiento, datos de medición, centros de costos, códigos de material y cualquier otro dato, juzgado por el usuario como necesario para actuar preventivamente en los equipos.
El montaje tradicional del Programa Maestro de Mantenimiento Preventivo, en el sistema de control manual ocurre a través de mapas, donde son registrados: en la primera columna, el código de localización (código de equipo), es correlacionado en las columnas siguientes, con el: nombre del equipo, los códigos de instrucción de mantenimiento y la página de registro de datos, el órgano responsable por el mantenimiento y la periodicidad. Este conjunto es seguido por 52 columnas, una para cada semana del año, donde son pintadas las mitades de las casillas (o puestos alfileres marcadores), de las semanas previstas para la realización de los servicios programados, de acuerdo con la periodicidad establecida para cada equipo. La otra mitad de estos cuadros se completa con otro color, cuando el servicio es ejecutado (en la semana prevista, anterior o posterior), o usando el mismo color de la programación en el caso de reprogramaciones, o aun, usando un tercer color en el caso de la cancelación del servicio previsto. Dicho mapa puede ser montado para una programación anual o de más años, cuando posee varios conjuntos de 52 columnas, uno para cada año. La figura 24 ilustra un modelo de mapa de programación anual.

Eventualmente, el conjunto de las seis primeras columnas, puede ser reducido o ampliado, en función de la supresión de uno o más correlaciones, o de la interacción con otra información juzgada necesaria por los usuarios, como: los códigos de los centros de costo, las estimativas de gasto en mano de obra etc.
Este mapa presenta, como gran desventaja, la posibilidad de error debido a su gran extensión, pues puede ocurrir que el usuario durante la búsqueda de los equipos a ser mantenidos en una determinada semana, se equivoque en la correlación de ésta con los respectivos equipos por cambio de línea, especialmente en el caso de aquellas que están colocadas al final del mapa.
Es común la elaboración de más de un mapa de programa maestro, siendo uno para Mantenimiento Preventivo Sistemático (para periodos iguales o superiores al trimestre con desmontaje total o parcial del equipo), otro para mantenimientos de rutina (para lapsos de tiempo inferiores al trimestre y generalmente sin desconexión del equipo, donde en lugar de codificar la instrucción de mantenimiento se realiza una descripción resumida de la actividad a ser ejecutada) y un tercer mapa para lubricación, cuyas columnas indican la parte del equipo a ser lubricado, tipo de lubricante, código, cantidad de lubricante a ser adicionado, número de puntos a ser lubricados, tipo de servicio a ejecutar entre las opciones de adicionar, analizar y cambiar y por último, la periodicidad, que es seguida por las columnas para las semanas o meses, siendo en este caso registrado en la casilla el día de la semana y el mes, en que el servicio deberá ser ejecutado.
Normalmente al final de cada semana, los encargados de los sectores de mantenimiento, o el responsable por el control de programación, controlan en el mapa los servicios previstos para la semana siguiente y los registran en formularios de programación semanal, uno para cada sector, los cuales son discutidos en la reunión de evaluación de esas actividades, especialmente en lo que se refiere al relacionamiento interno entre diferentes sectores.
Una forma de transformar el mapa de programación, en más compacto y consecuentemente de simple manejo y con menor posibilidad de error en la búsqueda de los equipos programados, es la sustitución de las 52 columnas por una sola, donde se escribe el número de la semana o semanas, en el caso de periodos inferiores a un año, manteniendo la información del mapa indicado anteriormente.
Normalmente son necesarias otras columnas, además de aquella adicional a la de programación, para permitir registros de reprogramación (semana y motivo), una vez que los mantenimientos realizados de acuerdo con la programación son identificados sobreponiendo un «X» sobre el número de la semana prevista.
La utilización de este proceso de programación, trae como desventaja el perjuicio en la visualización de las actividades ejecutadas, reprogramadas, pendientes y canceladas, sin embargo, además de la ventaja de eliminar los errores de selección arriba identificados, facilita el manejo cuando los formularios pueden ser encuadernados armando el libro base de programación, que puede ser hecho en varias reproducciones para su distribución a los encargados.
El «NSFI – Norwegian Ship Research Institute» (Instituto de Investigación de la Marina Noruega), desarrolló un sistema de programación manual que denominó «TSAR – Time Scheduling and Recording», que tiene como base un panel plástico con varias ventanillas donde son colocadas tiras de cartones coloridos en forma de «T», una para cada equipo, donde se registran los datos necesarios al mantenimiento programado de esos equipos.
En caso de que el panel plástico sea montado para la programación del mantenimiento, usando como unidad de periodicidad la semana, es recomendable que tenga, además de las 52 columnas, dos o tres más para los principales tipos de prorrogas de tal actividad, como ejemplo: liberación del equipo para la operación, servicio a ser ejecutado durante una gran reparación, aguardando pieza de repuesto, etc.
La gran variedad de colores de las tiras «T», permite que el órgano de planeación y control de mantenimiento, caracterice a los sectores responsables por el mantenimiento, o las unidades de mantenimiento o las clases de los equipos o aun otra característica juzgada de mayor importancia, para su identificación inmediata.
El uso de este panel, facilita la reprogramación de mantenimiento en el mismo año, siendo suficiente cambiar la posición de la tira de una columna por otra. También es más práctico que los otros métodos manuales, ya que dispensa algunas otras referencias, pues algunos datos necesarios para mantenimiento pueden ser escritos en el anverso y reverso de la tira. Sin embargo, esta tarjeta no permite el uso del Registro de Medición o de Variación de las especificaciones de origen, especialmente en caso que se desee implementar el control Predictivo del Mantenimiento a mediano o a largo plazo.
En el sistema de control informatizado, no existe necesidad de elaborar mapas, cartones o tiras. Toda la información es archivada en la computadora, la cual, semanalmente (o diariamente) emite la relación de los servicios a ser ejecutados bajo dos formas: listados para seguimiento de las actividades programadas por el supervisor y solicitudes de trabajo parcialmente compiladas para el uso del ejecutante. Se hace necesario solo un sistema de retorno de informaciones de los mantenimientos ejecutados integral o parcialmente, o reprogramados, lo que puede ser echo a través de la compilación de algunos registros de la propia Orden de Trabajo.
El establecimiento de criterios de programación, tomando la semana como unidad de periodicidad, puede traer la siguiente dificultad en el cálculo automático por el sistema, para la periodicidad mensual y bimensual:
- Una vez que el número de días del mes (30, 31 y 29 en los años bisiestos) no es múltiplo del número de días de la semana (7), se tendría siempre 13 intervenciones mensuales por año, debido a la consideración de que un mes tiene 4 semanas y eventualmente casi 7 bimestres (8 semanas en cada uno).
Para resolver este problema pueden ser utilizadas una de las siguientes alternativas:
- 1) Eliminar 4 semanas del año, unidas o separadamente (en el caso de eliminar semanas intercaladas, se sugiere suprimir los múltiplos de 13). En este caso, el año pasaría a tener, para efecto de programación 48 semanas y así, la periodicidad sería calculada considerando: la mensual como múltiplo de 4, la bimestral como múltiplo de 8, la trimestral como múltiplo de 12, la semestral como múltiplo de 24 y la anual como múltiplo de 48.
- 2) Trabajar con el calendario «juliano» y en este caso la programación sería hecha por el número de la semana del mes (ejemplo: 3ª semana de mayo).
Es evidente, que existe la alternativa de que el usuario, marque manualmente todas las semanas que desee y que las intervenciones sean efectuadas, en función del período previsto la para ejecución del trabajo. Sin embargo, en virtud de que ese trabajo sea efectuado solamente una vez, para algunas empresas puede ser compensador utilizar esta opción.
Naturalmente, de acuerdo con criterios de cada empresa, nuevas correlaciones de equipos (o componentes), pueden ser agregadas o suprimidas del Programa Maestro, recordando que, con excepción de los datos de catastro, hasta la composición de la programación, la computadora desconoce las correlaciones indicadas, y esas correlaciones inducirán las responsabilidades burocráticas de búsqueda, tras la implantación del Sistema.
Análogamente al catastro, la programación de mantenimiento desarrollada por computadora personal, puede ser subdivida en módulos con las siguientes finalidades: actualización de las tablas de programación; de las instrucciones de mantenimiento; del programa maestro de mantenimiento preventivo; emisión de listados de programación; emisión de órdenes de trabajo de actividades programadas y emisión de órdenes de trabajo de actividades no programadas.
Para evitar que el usuario tenga necesidad de recurrir al listado de las tablas, o tenga que memorizar todos los códigos para efectuar una actualización de programación, el sistema puede, abrir las tablas correspondientes, a medida que el usuario vaya introduciendo los datos de programación, enseguida, el mismo usuario, a través de barrer con el «Mouse» selecciona el elemento de la tabla que desea incluir o alterar.
En la Figura 25, se presenta un modelo de pantalla con los datos existentes en una programación seleccionada.

El sistema debe permitir la emisión de listados ordenados: por el nombre del equipo o componente, por el código, por las semanas, o cualquier otra ordenación deseada por los usuarios.
Dentro del orden posible de las listas de programación, se resaltan:
- por orden alfabético de equipos o de componentes;
- por orden de semana;
- para una semana específica – emitida para el Supervisor de Mantenimiento, para el seguimiento de las actividades programadas para una semana elegida.
De los ejemplos aquí ilustrados, se nota que podrían ser emitidas listas ordenadas por cualquiera de las columnas que componen el programa maestro de mantenimiento preventivo, siendo una de las más interesantes la del Código de Material, pues permite visualizar la intercambiabilidad de los componentes o piezas que reciben el mismo código.
Inventario y Catastro
para implantar un sistema de control del mantenimiento, es recomendable iniciar el proyecto de recopilación de datos, con la identificación de los elementos que componen la instalación industrial o de servicios, su localizacion y utilidade. Este conjunto de informaciones, llamado Inventario, correlaciona cada equipo con su respectiva área de aplicación, función, centro de costos y posición física o geográfica en el área de producción y ofrece ayudas al personal de la gerencia, para el dimensionamiento de los equipos de operación y mantenimiento, cualificación necesaria al personal, definición de instrumentos, herramientas y máquinas, además de la proyección del plan general de construcción y distribución de los talleres de apoyo.
Una vez identificados los equipos que componen la instalación, los registros se complementan, en la medida de lo posible, en base a un estándar, con la demás informaciones las cuales deben ser suficientemente amplias para absolver consultas de especificación, fabricación, adquisición, traslado, instalación, operación y mantenimiento. A este conjunto de información la llamamos Catastro, que es definido como:
«Registro del mayor número de datos posibles de los equipos, a través de formularios o pantallas estandarizadas, que archivados(as) de forma conveniente, posibiliten el acceso rápido a cualquier información necesaria, para: mantener, comparar y analizar condiciones operativas, sin que sea necesario recurrir a fuentes diversas de consulta».

Por lo tanto, el catastro deberá reunir para cada tipo de equipo: los datos de construcción (manuales, catálogos y diseños), de compra (adquisición, solicitudes, presupuesto, fechas y costos), de origen (fabricante, proveedor, tipo y modelo), de transporte y almacenamiento (dimensiones, peso y recomendaciones), de operación (características normales y límites operativos) y de mantenimiento (lubricantes, repuestos generales y específicos, curvas características, recomendaciones de los fabricantes, límites, holguras y ajustes).
Actualmente la concepción de la recopilación de datos de catastro, está presentando mejoras con la evolución de los criterios de planeación y control de mantenimiento. Los primeros formularios desarrollados para esa finalidad, tenían la configuración de una tarjeta impresa con información genérica y aplicada a cualquier tipo de equipo, donde los datos generales y específicos aparecían mezclados y algunos indefinidos.
En la secuencia evolutiva, el reverso de la tarjeta pasó a ser utilizada para el registro del historial, a través de dos columnas, una para la fecha y otra para la descripción de la ocurrencia.
A partir de esa concepción, surgió la tarjeta de Catastro e Historial, con el cuidado de indicar en la primera columna la descripción de la ocurrencia y en las siguientes, las fechas en que la misma sucedía. Ese esmero trajo como ventajas adicionales, el evitar la repetición de la misma ocurrencia varias veces, facilitando la visualización de aquellas que presentaban mayor incidencia, además de realizar algunos aciertos en la disposición de datos, lo que también, permitía facilitar la búsqueda en cuatro formas: Número del archivo, Código de Catastro, Número Individual del Equipo y Código de Equipo.
Con la utilización de la computadora en el proceso de control del mantenimiento, surgió la idea de asociar el catastro de equipos, a sus respectivos repuestos de uso específico y de uso común. Y el órgano de mantenimiento pasó a utilizar, para el Código de Catastro, la misma estructura de codificación del órgano de administración de material. Como consecuencia de esa fusión, el Código de Catastro pasó a representar una «familia» de equipos del mismo fabricante, tipo y/o modelo y surgió la propuesta de separar los datos comunes de los datos específicos de los equipos durante el catastro.
Por lo tanto, al «Código de Catastro» (o «Código de Familia») pasaron a ser asociadas las características administrativas y técnicas de la familia de equipos. Considerándose que en una instalación industrial que tuviese «x» bombas iguales, sería suficiente la compilación de apenas un grupo de registros.
En los registros de datos específicos, el código de catastro fue asociado al número de identificación que individualizaba cada equipo de la instalación. Ese número de identificación podía ser el número de serie suministrado por el fabricante, o el número que recibe del órgano de control de bienes patrimoniales de la empresa, o en el caso de ausencia de ambos, un número secuencial dado por el propio sistema, que es impreso o troquelado en el equipo. Tal número de identificación caracteriza un conjunto de datos individuales a cada equipo y así, para el ejemplo considerado, sería necesario compilar «x» formularios de datos específicos, uno para cada bomba de la instalación.
Tanto en los datos generales (o comunes) como en los datos específicos, existen registros de naturaleza administrativa (fechas, costo, números de documentos, localización etc.) y de naturaleza técnica, entre las cuales se destaca su función en el proceso o servicio.
La correlación entre el código de catastro, el número de identificación y el código de posición operativa («tag» o código de equipo), permite la obtención de información para una «familia » de equipos (código de catastro) o para un equipo específico (número de identificación), o para los equipos que operan en una determinada localización de la instalación (código de equipo), lo que representa una inmensa ventaja para el análisis y decisión de los gerentes de mantenimiento.
Se ha de ilustrar esta ventaja con el siguiente ejemplo: suponiendo que en una planta existan tres compresores de iguales características, todos importantes para el proceso productivo y, por esta razón se tiene en el almacén, uno de reserva para una rápida sustitución. Si uno de los compresores queda inoperante, es sustituido inmediatamente por el de reserva, mientras el primero va para reparación.
Los cuatro compresores (tres en operación y uno de reserva), por tener las mismas características de fabricación, recibieron el mismo Código de Catastro, «A», mientras cada uno tiene su Número de Identificación «1», «2», «3», «4», y un Código de Posición Operativa, «a», «b», «c», «d». Si el compresor que dejó de funcionar fue el número «2» y fue sustituido por el número «4», se tendrá la situación indicada en la Figura 17.

Existiendo la necesidad de un análisis de ocurrencia con este tipo de equipo, los gerentes de mantenimiento pueden solicitar el registro de las incidencias por el código de catastro, que incluirá los cuatro compresores (A), y mostrará el tiempo que operaron, el tiempo que uno de ellos estuvo en reparación y la sustitución en el almacén; o por el código de equipo (por ejemplo – b), que mostrará el comportamiento de los compresores que actuaron en aquella posición operativa de la instalación (en este caso los compresores 2 y 4); o por el número de identificación que mostrará el comportamiento de uno de los compresores elegido.
Con el recurso de la utilización de una red de computadoras personales, el catastro puede ser efectuado aportando la información directamente al sistema informatizado, sin que sea necesario el desarrollo de formularios para esa finalidad. Con esta modalidad, es necesario analizar la composición de las «pantallas», que auxiliarán a los usuarios en la alimentación de datos, para formación de los archivos relativos a los equipos instalados y, con el auxilio de las tablas (tanto para los datos administrativos como técnicos), el sistema ayuda al usuario en la compilación de cada campo.
Las técnicas modernas de composición de banco de datos, permiten que el usuario visualice los nombres de los equipos, evitando de esta manera, la necesidad del conocimiento de esos códigos, que quedaran limitados al trabajo de procesamiento por la computadora, aumentando así, su desempeño y reduciendo tiempos de búsqueda – Figura 18.

En las Figuras 19 y 20 se muestran modelos de pantallas con Catastro General y Catastro Específico.


Los archivos de catastro general y de catastro específico, pueden ser independientes (en este caso, correlacionados por el código de catastro) o comunes (en este caso, con el recurso de «duplicación de datos») o sea, la compilación de datos iguales de un nuevo equipo, es hecha sobre los datos de otro existente con las mismas características de construcción – Figura 21.

En esta condición, todos los datos serán almacenados en un único archivo. Nótese que esa opción genera archivos con datos repetidos lo que, actualmente, con la alta capacidad de los discos rígidos y la alta velocidad de procesamiento de las computadoras, dejó de ser un inconveniente.
Es común en los sistemas modernos, que el usuario, pueda registrar componentes de equipos y crear un árbol jerárquico de esos componentes con relación al equipo, al sistema operacional y a la propia planta. De esta forma, además de la posibilidad de consulta por «familia» o por individuo, podrán también ser hechas para todos los equipos de una planta o de un sistema operacional. Obviamente también podrán ser hechos filtros para consultas de datos de un determinado componente de un equipo, o de componentes de igual naturaleza de varios equipos.
La compilación de datos de catastro debe ser de simple operación, donde el sistema sea capaz de abrir automáticamente la tabla correspondiente de cada dato a ser registrado, en el caso de «inclusión» o «modificación» y sobre la información a ser tratada en el caso de «consulta», recordando que, normalmente el usuario no tiene conocimientos de informática y de esta forma no tendrá acceso al programa para adaptarlo a sus necesidades.
La separación de los registros en dos grupos de datos de catastro (común y específico) trae como ventaja adicional la posibilidad de establecer la correspondencia entre las «familias» y los repuestos a ésta aplicados – Figura 22.

Además de las críticas, por el sistema, respecto del tamaño de los campos, en el aspecto de su composición, incluyendo el tipo de carácter a ser usado (numéricos y/o alfabéticos, mayúsculas y/o minúsculas, símbolos gráficos y matemáticos) y fechas (número de días en el mes, los años bisiestos y cronología), debe ser previsto el uso de las teclas de función para la búsqueda de tablas, que auxiliarán al usuario en la composición de los códigos.
La emisión de los listados de catastro podrá ser efectuada para uno, algunos o todos los equipos, de acuerdo a la necesidad del usuario (filtro). Análogamente, deberá ser prevista la emisión de estas listas bajo varios requerimientos, de acuerdo con la definición hecha durante la fase de Proyecto del Sistema.
Tanto en el Catastro por el Sistema Manual, como en los Sistemas Automatizados o por Computadora, podría ser necesario definir los criterios de arreglo de la información archivada, de las listas emitidas por la impresora y/o a través de la pantalla.
Entre las varias opciones de agrupación de la información objetiva facilita el análisis, cono el los ejemplos:
- Agrupación por línea de producción;
- Agrupación por tipo de equipo;
- Agrupación por área geográfica;
- Agrupación por unidad de producción;
- Agrupación por importancia operacional;
- Agrupación por unidad móvil.
Es frecuente que se realice, en una misma empresa, la consulta de datos de catastro bajo diferentes formas de agrupación; cuando esto sucede en el catastro por el sistema manual, el proceso de archivo se torna más complejo, existiendo la necesidad de composición de nuevas tablas auxiliares de periodicidad, y en algunos casos, duplicidad de registros. En el catastro a través de sistemas automatizados, estas inconveniencias son eliminadas, puesto que, a través de programas adecuados, la computadora presentará la información bajo diferentes formas de agrupación, en función de la necesidad y deseo del usuario.
No habiendo una definición previa por parte de los usuarios, respecto a la forma de archivo y emisión de informes de catastro, los proyectistas deberán elegir los criterios a ser adoptados la agrupación de la información, tomando como base el proceso adoptado, el detalle de los formularios, la importancia operacional de los equipos, los órganos y niveles de gestión a ser atendidos y la movilidad de los equipos.
Instrucciones de Mantenimiento y Recomendaciones de Seguridad
Para normalizar los servicios de las actividades programadas del mantenimiento, es recomendable el desarrollo de Instrucciones de Mantenimiento, orientando objetivamente la ejecución del mantenimiento en esas actividades para evitar que alguna tarea sea omitida por desconocimiento u olvido – Figura 23
Estas instrucciones, deben ser desarrolladas, aprovechando el conocimiento del personal técnico de ejecución , con más experiencia y las recomendaciones de los fabricantes y montadores, indicaciones de los catálogos, manuales, diseños y referencias de profesionales con experiencia de otras empresas similares, relativas a cada equipo.
Cada línea de instrucción es conocida como «tarea». Por lo tanto, una instrucción de mantenimiento es un conjunto de tareas una vez compuestas, es recomendable que se estime su valor en horas-hombre para su ejecución, el cual es conocido como «tiempo patrón».

El «tiempo patrón» debe ser ajustado a la realidad, en la medida en que sean obtenidos los datos reales de cada actividad. Una forma simple de efectuar este ajuste es utilizar el valor medio entre el existente en el archivo y el obtenido en la realidad.
Como una refinación para evitar ajustes indebidos del «tiempo patrón», el sistema puede contener un «desvío patrón» definido por el usuario, o sea, un porcentaje sobre el valor del «tiempo patrón» que cuando sea superado (más o menos) excluye el ajuste del tiempo existente. El uso del «desvío patrón» impide el reajuste de tiempos estándares en caso de anomalía en la ejecución del mantenimiento, como por ejemplo: la fractura de un tornillo al retirar su tuerca.
Las instrucciones pueden ser de carácter genérico o específico, en función al nivel de detalle deseado. Una instrucción de mantenimiento de carácter genérico, no detalla los puntos de ejecución de cada etapa de la tarea que describe y, puede ser utilizada para la ejecución de la misma actividad en cualquier equipo de iguales características operativas; mientras que la Instrucción de Mantenimiento de carácter específico, indica en forma detallada las tareas a ser ejecutadas, normalmente sólo útil al equipo para la cual fue elaborada.
Ya se encuentran en desarrollo, las bibliotecas de tareas de mantenimiento (para la composición de las Instrucciones de Mantenimiento) que serán asociadas al componente del equipo. La utilización de estas bibliotecas, facilitará a las empresas, la implantación de sus actividades programadas de mantenimiento.
Como variante de las instrucciones de mantenimiento, existen los archivos de Recomendaciones de Seguridad, normalmente asociados a la naturaleza del equipo y que tienen por finalidad, evitar actos inseguros durante la ejecución del mantenimiento o el mantenimiento en condiciones inseguras.
Cursos recomendados
-1730145694747.webp%3Falt%3Dmedia%26token%3D719f647e-063f-47e9-a9f4-c3b59cb3a8ab&w=3840&q=75)



%252FImagen%252Frcm-1730083250826.webp%3Falt%3Dmedia%26token%3D3775356a-7b11-4c44-b21f-45b3409fb9ed&w=3840&q=75)

%252FImagen%252FRAMPREDYC-1730060420837.webp%3Falt%3Dmedia%26token%3D2634a7f0-988e-4022-b91f-382503e6e9db&w=3840&q=75)

Recolección de Datos – Recomendaciones
Antes de definir cual información debe ser reunida, se ha de abordar algunas recomendaciones, obtenidas a través de la experiencia práctica, que se consideran fundamentales para que se pueda confiar en los datos obtenidos:
• Aclaración al personal de ejecución, respecto a la finalidad de la recolección de los datos.
Al presentar esta recomendación se sugiere que el proyecto y desarrollo de los mecanismos de recolección de datos, sea hecho con la participación directa del personal de ejecución en todos los niveles, tanto en el aspecto de exposición, como de captación de ideas sobre el proceso a ser utilizado y los resultados pretendidos. Existe mayor probabilidad de éxito, cuando los que vayan a suministrar la información, hayan participado en el proyecto de desarrollo o adaptación del sistema a sus necesidades.
• Simplicidad de diligenciamiento de los documentos o «pantallas» en la recolección de datos.
En el caso de registro en formularios, tratar cuando sea posible, que la información se encuentre previamente impresa, de manera que el registro sea efectuado marcando con una «X» la opción elegida. En caso del registro a través del teclado de la computadora o terminal, la propia computadora deberá auxiliar a el usuario a través de «pantallas» de consulta y utilización del cursor a través del «ratón».
• Nítida definición de lo que deberá ser analizado antes de implementar el proceso.
Esta recomendación, tiene por objeto evitar que sea realizada la recolección de datos innecesarios, sobrecargando el trabajo y sin obtener un fin definido o con detalles innecesarios. Se debe recordar que todos los datos que se reúnan y procesen, posteriormente deben ser analizados obteniendo mejorías en las condiciones de trabajo del personal y de los equipos además de la reducción de costos.
• Reducir al mínimo posible, la cantidad de modelos de formularios a ser diligenciados.
Buscar estandarizar la información en todos los sectores del mantenimiento para evitar que cada uno cree sus propios formularios, lo que encarecería el procesamiento de datos, tanto en el sistema de control manual como el automatizado
• Evitar que la recolección de datos implique la interrupción en la ejecución de los servicios, o trabajo adicional excesivo para el personal de ejecución del mantenimiento.
Es recomendable que el encargado del servicio sea el que haga los registros de historial, sin embargo, los otros registros deben ser hechos por cada responsable del suministro de los datos o sea, los ejecutantes del mantenimiento hacen los registros de sus tiempos ocupados, los bodegueros hacen los registros del material aplicado en cada Orden de Trabajo, los operadores hacen el registro de indisponibilidad y pérdida de producción y el área de recursos humanos hace los registros de disponibilidad de personal y respectivos costos, recordando que todos deben estar conscientes de la importancia de tales datos.
• Capacitar de manera adecuada a los responsables por la recolección de datos.
En caso de utilización de formularios, que serán posteriormente digitados, orientar a los responsables por los registros, en lo referente a la utilización de letras de imprenta: cortar la letra «Z» y el número «0», para evitar que se confundan con el número «2» y la letra «O». También, en lo referente al llenado de la información en los lugares correctos, para facilitar el trabajo de los digitadores y reducir los errores de transcripción de los datos. En el caso de transferencia directa de la información a través de la terminal o en computadora personal, se debe orientar en cuanto a la dimensión de los campos y limitaciones relativos al uso de caracteres.
• No procesar informes por computadora inmediatamente después que se implante un sistema automatizado.
En el caso del cambio de sistema de control manual para automatizado, analizar atentamente los primeros formularios completados, antes de enviarlos a digitación, solicitar emisión de las listas de verificación de los datos, hasta tener seguridad de que los mismos, están siendo correctamente compilados y digitados.
• Estructurar convenientemente la recolección de la información, con el fin de poder analizar los datos reunidos y los informes emitidos.
Ya que cualquier cambio crea reacciones, es fundamental que para el éxito del sistema, los datos después de procesados, traigan beneficios a los responsables de el envío de la información y no exista trabajo adicional de análisis, especialmente en el caso que sean similares a aquellos, que ya se realizaban antes de la implantación del nuevo sistema.
Se debe tener especial atención, para evitar la proliferación de formularios y su multiplicidad con la misma función. Otras recomendaciones dictadas por la experiencia son: la reducción de la responsabilidad burocrática de los ejecutantes del mantenimiento, la estandarización de informaciones, la recolección de datos administrativos en su origen y la interrelación del Banco de Datos, para evitar choques entre diferentes fuentes de información.
Orden de Trabajo
La fuente de datos relativos a las actividades desarrolladas por el personal de ejecución de mantenimiento, debe incluir el tipo de actividad, su prioridad, falla o el defecto encontrado y cómo fue reparado, duración, los recursos humanos y materiales utilizados, y otros datos que permitan evaluar la eficiencia de la actuación del mantenimiento y sus implicaciones con costos y programación.
Las Ordenes de Trabajo (OT) son específicas para cada empresa, en función de la actividad, organización, cantidad y tipos de mano de obra y equipos que posee etc., sin embargo, existe una serie de datos comunes en cualquier ramo industrial o de servicios, que deben estar presentes en este instrumento de información, como: el número consecutivo, el tipo de la actividad de mantenimiento, la prioridad, los registros de historial, si los instrumentos de supervisión actuaron correctamente o no, si la intervención perjudicó la producción, el período de indisponibilidad del equipo y la duración real del mantenimiento.
En los antiguos modelos de OT usadas en el sistema manual, eran presentados en la parte superior: los datos de identificación del equipo y del problema, en la parte media: los datos de planificación, y en la parte inferior: los de ejecución del mantenimiento, subdivididos en dos partes: datos para “Gestión del Equipo” (sumario del servicio ejecutado y comentarios sobre el problema) y para “Gestión de Mano de Obra” (horas-hombre consideradas y utilizadas) – Figura 26.

Los modelos de Orden de Trabajo que siguieron tenían, con relación al anterior, la novedad de la inclusión de las columnas codificadas de “Problema Encontrado”, precursor del actual “Código de Ocurrencias”. En la parte inferior de ese cuadro existían enumeradas, un conjunto de posibles ocurrencias en los equipos relacionados en la referida columna, para que el ejecutante pusiera los números que correspondían a las ocurrencias, en el cuadro correspondiente a la intersección de la línea de la “localización” con la columna del grado de “severidad”, cuyos significados eran presentados al lado de los tipos de ocurrencias.
El modelo siguiente, en la evolución de las OT, fue utilizado durante la fase de transición del sistema de control manual para el automatizado y, por esta razón, apenas la última sección corresponde a la identificación del equipo, la duración del mantenimiento, pérdida de producción, utilización de mano de obra y costos, eran procesadas, no dando el mismo tratamiento a los datos del historial de ocurrencias, que eran transcritos en líneas continuas en la primera y la tercera sección. El formulario era proyectado para producir una tarjeta agujereada (o equivalente), pues poseía 80 caracteres para procesamiento, siendo los cuatro primeros reservados para la identificación del documento.
La orden de trabajo siguiente en el proceso evolutivo fue desarrollada para el sistema de control automatizado, con la producción de una tarjeta agujereada. Presentaba como novedad con relación a la anterior, el registro del “Código de Servicio” con 4 caracteres, siendo el primero destinado a la Ocurrencia (O), que indicaba el origen de la necesidad de la intervención en el equipo, el segundo para la Acción (A), que indicaba lo que había sido realizado por el equipo de mantenimiento y los dos últimos para el Complemento (CPL) de esa acción. La mejor terminología para este código sería: “Código de Ocurrencia”, que serviría para indicar intervenciones debido a Fallas o Defectos, pudiendo también utilizarse el término “Código de Defecto” con el mismo objetivo.
La evolución del modelo de orden de trabajo, utilizada en el sistema automatizado de control del mantenimiento, generaba dos tarjetas perforadas y presentaba, con relación a la anterior, las siguientes particularidades:
- Un campo asociado al número consecutivo para correlacionar a dos o más órdenes de trabajo, cuando la ejecución de las actividades excedía el período mínimo de procesamiento de los informes de gestión, que es definido como “horizonte”;
- El código de mantenimiento compuesto por el código del equipo asociado al componente, actividad y sector;
- La semana y el motivo de la reprogramación, para permitir la replanificación manual, en caso de algún impedimento;
- La indicación de la actuación de supervisión automática;
- El código de ocurrencia compuesto por cuatro “células”, o sea: la Causa: que indicaba la razón de la ocurrencia (falla o defecto) en el equipo; el Efecto: que indicaba como la falla o el defecto eran constatados; la Acción: que indicaba el verbo asociado al servicio ejecutado y el Complemento: que completaba el mensaje de la acción;
- La “espera” que indicaba la cantidad de horas-hombre que quedó inactiva, durante el desarrollo de la actividad de mantenimiento, debido normalmente, a una falla de la planeación. Ese campo estaba asociado al código del motivo que llevaba a esos horas-hombre a la interrupción de sus servicios.
En el inicio de la década de 1 970, surgió el proyecto BOZZ-ALLEN & HAMILTON que presentó como singularidad, la omisión de la recolección de información de la mano de obra en el cuerpo de la orden de trabajo; siendo estas informaciones recogidas, a través de un documento complementario llamado Tarjeta de Tiempo, con forma y tamaño similar a la tarjeta horaria, pero con características diferentes, ya que servía para que cada ejecutante indicase, en cada servicio que recibía, el día, la hora y el minuto en que iniciaba y terminaba, identificando el número de la Orden de Trabajo – Figura 27.
La parte posterior de esta tarjeta contiene los códigos de servicio, espera y ausencia para indicarlos, en la columna respectiva la actividad ejercida, durante cada período de su jornada. A cualquier momento, siempre que se complete una tarjeta, el ejecutante debe sustituirla por una nueva para asegurar la continuidad de los registros.
Como recomendación, para evitar celos de fiscalización individual a los ejecutantes del mantenimiento y, en consecuencia, el sabotaje de los registros, la Tarjeta de Tiempo, debe ser impersonal e individual para cada ejecutante de mantenimiento, o sea, identificar apenas el cargo y no el nombre de la persona.
Como variante de la Tarjeta de Tiempo, puede ser utilizada la Tarjeta de Material, cuya responsabilidad de compilación es del encargado del depósito, que relaciona el material suministrado al respectivo consecutivo de la Orden de Trabajo en la tarjeta – Figura 28


Para implementar tanto la Tarjeta de Tiempo, como la Tarjeta de Material, debe realizarse un trabajo de orientación y búsqueda junto a los ejecutantes, en lo referente a la compilación, para evitar que los datos dejen de ser registrados o lo sean de manera equivocada, involuntariamente o a propósito.
Una innovación importante en el sistema de recolección de datos en el control automatizado de mantenimiento fue la emisión, a través de la propia computadora, de las órdenes de trabajo parcialmente llenadas, a partir de datos provenientes del Plan Maestro de Mantenimiento Preventivo, enfatizando en la reducción de las actividades burocráticas de los ejecutantes de mantenimiento – Figura 29.

Con la implantación de la orden de trabajo para mantenimientos preventivos, emitida a través de la computadora, surgió también la idea de utilizar la máquina para reprogramar actividades que no fuesen ejecutadas dentro de un plazo aceptable y así, permitir este trabajo de reprogramación automatizada, fue fortalecido el concepto de Clase.
Durante el desarrollo del proyecto, se determina para cada actividad el plazo de espera por la computadora, para el retorno de las órdenes de trabajo, plazo que si era excedido, acarreará el cobro del motivo de la no ejecución, siendo esta información transferida para el archivo en el banco de datos para su posterior inscripción en el informe de gestión de no conformidades.
Para dar conocimiento al ejecutante sobre estas limitaciones de plazo, la computadora informa a través de los campos de Próxima Reprogramación y Semana Límite de Reprogramación en la emisión de cada orden de trabajo.
Para reducir aún más las responsabilidades burocráticas de los ejecutantes del mantenimiento y asegurar que los servicios programados, sean realizados de acuerdo con un estándar preestablecido, la orden de trabajo emitida por la computadora, puede contener también, las Instrucciones de Mantenimiento ya impresas.
Sin embargo, es necesario que estas instrucciones sean redactadas de forma concisa, para evitar la proliferación de estos documentos. Como sugerencia, es recomendable que sea limitado a 30 el número de líneas para cada actividad programada en cada componente.
En los Sistemas donde se utiliza para la emisión de la orden de trabajo para actividades programadas a la computadora, es necesario desarrollar otro modelo de orden de trabajo, para permitir la anotación de datos de actividades no programadas.
Para estandarizar los registros de “Descripción” y “Servicio Ejecutado”, además de reducir el número de registros del banco de datos del historial y consecuentemente, el tiempo de búsqueda, hecho importante en el caso de la utilización de computadoras personales de menor performance en el proceso, es recomendable la utilización del “Código de Ocurrencias” citado anteriormente, que traerá como ventaja adicional, la posibilidad de búsqueda en el historial de una ocurrencia específica o de cualquiera de los elementos que compongan este código – Figura 30.

Puede observarse también, en este modelo de OT, la inclusión de campos para la anotación, por parte del usuario de los servicios de mantenimiento (llamado “cliente”), de la evaluación del trabajo ejecutado a través de las opciones: “plenamente ejecutado”, “provisionalmente ejecutado”, “reservicio” y “no atendido”, como un factor de medición de la calidad de los servicios del mantenimiento. Este tipo de registro, que posibilitará la evaluación de la gestión de mantenimiento respecto a las necesidades de producción, puede ser incluido también en las órdenes de trabajo de actividades programadas.
En los modelos de las órdenes de trabajo de actividades programadas y no programadas ilustrados, se puede observar la existencia de un código QR o de barras que puede ser emitido por la computadora, para facilitar la lectura en sistemas integrados (por ejemplo: para que el encargado del depósito asocie el material a emplear al número de la OT).
Para evitar, la utilización de uno de los modelos presentados en las Figuras 29 y 30, en el registro de actividades que no exigen detalle, o para el registro de mantenimientos en equipos que no afectan al proceso productivo (Clase C), o aun, para hacer referencia a actividades diferentes del mantenimiento, que ocupan mano de obra del personal de mantenimiento, puede ser utilizado un formulario común, la Orden de Trabajo de Ruta, u Orden de Trabajo Colectivo u Orden de Trabajo para Actividades Diversas, como el modelo ilustrado en la Figura 31, donde en cada línea es hecho el registro de cada servicio, teniendo para cada uno, apenas el registro del inicio y final de la actividad, para el cálculo por computadora, de la duración de la actividad.

Una vez que este formulario tiene un “horizonte” mensual, para permitir que sus datos sean procesados y formen parte de los informes de gestión de costos y mano de obra; puede recibir un número de identificación consecutivo mensual, que servirá como referencia para su registro, en las Tarjetas de Tiempo de los ejecutantes, para el cálculo de los horas-hombre empleados en este tipo de actividades.
En caso que los usuarios deseen separar la ocupación de mano de obra en mantenimiento (para los equipos Clase C) de los demás (Servicios de Apoyo), pueden ser utilizadas dos Ordenes de Trabajo de Actividades Diversas con números diferentes, una para cada fin. Esta observación también es válida, en el caso de los usuarios que deseen conocer la ocupación de mano de obra en un determinado tipo de Servicio de Apoyo como “tránsito”, o “capacitación interna”.
Mano de obra disponible
Se entiende, como mano de obra disponible de un órgano de ejecución del mantenimiento, el resultado de las horas-hombre efectivas, o sea, el producto del número de empleados de ese órgano por el número de horas trabajadas (normales y extras), menos el número de horas-hombre no presentes por motivo de vacaciones, enfermedad, servicio en otras unidades de la empresa, capacitación externa, accidente o cualquier otro motivo autorizado o no, que haya provocado la ausencia del personal.
Para la recolección de datos de disponibilidad de personal, para la ejecución del mantenimiento propio y de refuerzo en otras áreas de la empresa o de contratistas, es necesario el desarrollo de un formulario, que debe ser completado por el órgano administrativo de cada unidad de producción, a partir de los registros de las tarjetas horarias u otro sistema de control de horario adoptado en la empresa. En el caso de que este órgano, disponga de un sistema específico, para el registro de estos datos y que el sistema esté correlacionado con el de mantenimiento, estos pueden ser transferidos directamente de un sistema para otro.
Datos de operación
Para permitir el procesamiento de información relativa a los informes de gestión de equipos y costos (facturación cesante), debe ser previsto el registro de los datos provenientes de operación, que deberán constar básicamente de: horas de funcionamiento de los equipos por período de control (horizonte), pérdida o reducción de la producción debido al mantenimiento, además de la referencia a cada intervención, normalmente hecha a través de la indicación del número de la orden de trabajo – Figura 32.

Estos registros, deben ser hechos por los propios operadores y, como en el caso anterior, habiendo integración, esta información puede ser obtenida directamente de los bancos de datos de operación.
Registro de Medición
Para el registro de los valores de las mediciones efectuadas, durante el mantenimiento de los equipos prioritarios (Clase A) y algunos secundarios (Clase B), para los cuales se juzgue conveniente acompañar las variables, para la implantación del Control Predictivo del Mantenimiento, se deben estandarizar mecanismos de registro específico, cuyos valores resultantes de medición, serán procesados para la obtener las curvas de dejeneración – Figura 33.
Debe aclararse que, generalmente los resultados prácticos del seguimiento de la variación de las variables de un equipo, con el objetivo de implantar el Análisis de Síntomas, no son inmediatos, pudiendo en algunos casos, presentar resultados tras varios años de seguimiento, siendo inclusive, recomendable que inicialmente sea realizada una evaluación, respecto a la validez del resultado en equipos que no comprometan el proceso productivo (Clase B).
Durante el desarrollo de este tema, es recomendable que los registros indicados, sean compilados por órganos distintos, de manera que se distribuya las tareas y se cierre el ciclo de información, lo que permitirá detectar fallas intencionales o involuntarias de compilación.

También es muy importante, la necesidad de establecer plazos límites («horizonte») para que sean procesados, evitando que algunos informes de gestión carezcan de información o con errores por no computar todos los datos.
Autor: Lourival Augusto Tavares
Brasil
Consultor en Ingeniería de Mantenimiento
Empresa: Director nacional de ABRAMAN (Asociación Brasileña de Mantenimiento) en dos mandatos.
Correo: l.tavares@mandic.com.br
Ingeniero Electricista, formado por la Escuela Federal de Ingeniería de Rio de Janeiro, en el año de 1967. Past-Presidente del Comité Panamericano de Ingeniería de Mantenimiento. Supervisor de Mantenimiento en FURNAS – Centrales Eléctricas S.A. durante 23 años. Fue el jefe de la Asesoría Técnica de Apoyo en ITAIPU Binacional. Reconocido como “notorio saber” en mantenimiento por la Universidad Federal de Rio de Janeiro y por la Universidad Federal de Paraíba.
Dinos qué te ha parecido el artículo
Artículos recomendados
12.- Cojinetes

2.2.- Eje

Simulación con Arena

2.3.- Carcasa

Publica tu artículo en la revista #1 de Mantenimiento Industrial
Publicar un artículo en la revista es gratis, no tiene costo.
Solo debes asegurarte que no sea un artículo comercial.
¿Qué esperas?
O envía tu artículo directo: articulos@predictiva21.com
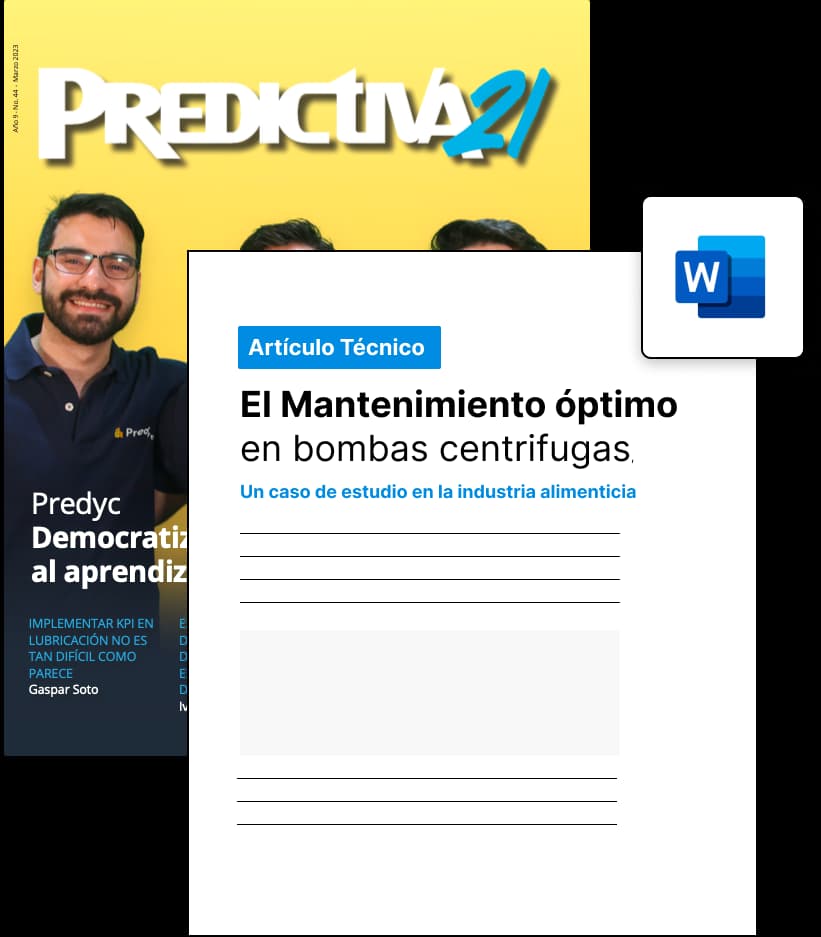
Programación del Mantenimiento - Inventario, OT, Datos y Registro
Libros 31 de agosto de 2020Programa Maestro de Mantenimiento Preventivo
Se llama Programa Maestro de Mantenimiento Preventivo, al proceso de correlación de los códigos de los equipos con la periodicidad, cronogramas de ejecución de las actividades programadas, instrucciones de mantenimiento, datos de medición, centros de costos, códigos de material y cualquier otro dato, juzgado por el usuario como necesario para actuar preventivamente en los equipos.
El montaje tradicional del Programa Maestro de Mantenimiento Preventivo, en el sistema de control manual ocurre a través de mapas, donde son registrados: en la primera columna, el código de localización (código de equipo), es correlacionado en las columnas siguientes, con el: nombre del equipo, los códigos de instrucción de mantenimiento y la página de registro de datos, el órgano responsable por el mantenimiento y la periodicidad. Este conjunto es seguido por 52 columnas, una para cada semana del año, donde son pintadas las mitades de las casillas (o puestos alfileres marcadores), de las semanas previstas para la realización de los servicios programados, de acuerdo con la periodicidad establecida para cada equipo. La otra mitad de estos cuadros se completa con otro color, cuando el servicio es ejecutado (en la semana prevista, anterior o posterior), o usando el mismo color de la programación en el caso de reprogramaciones, o aun, usando un tercer color en el caso de la cancelación del servicio previsto. Dicho mapa puede ser montado para una programación anual o de más años, cuando posee varios conjuntos de 52 columnas, uno para cada año. La figura 24 ilustra un modelo de mapa de programación anual.

Eventualmente, el conjunto de las seis primeras columnas, puede ser reducido o ampliado, en función de la supresión de uno o más correlaciones, o de la interacción con otra información juzgada necesaria por los usuarios, como: los códigos de los centros de costo, las estimativas de gasto en mano de obra etc.
Este mapa presenta, como gran desventaja, la posibilidad de error debido a su gran extensión, pues puede ocurrir que el usuario durante la búsqueda de los equipos a ser mantenidos en una determinada semana, se equivoque en la correlación de ésta con los respectivos equipos por cambio de línea, especialmente en el caso de aquellas que están colocadas al final del mapa.
Es común la elaboración de más de un mapa de programa maestro, siendo uno para Mantenimiento Preventivo Sistemático (para periodos iguales o superiores al trimestre con desmontaje total o parcial del equipo), otro para mantenimientos de rutina (para lapsos de tiempo inferiores al trimestre y generalmente sin desconexión del equipo, donde en lugar de codificar la instrucción de mantenimiento se realiza una descripción resumida de la actividad a ser ejecutada) y un tercer mapa para lubricación, cuyas columnas indican la parte del equipo a ser lubricado, tipo de lubricante, código, cantidad de lubricante a ser adicionado, número de puntos a ser lubricados, tipo de servicio a ejecutar entre las opciones de adicionar, analizar y cambiar y por último, la periodicidad, que es seguida por las columnas para las semanas o meses, siendo en este caso registrado en la casilla el día de la semana y el mes, en que el servicio deberá ser ejecutado.
Normalmente al final de cada semana, los encargados de los sectores de mantenimiento, o el responsable por el control de programación, controlan en el mapa los servicios previstos para la semana siguiente y los registran en formularios de programación semanal, uno para cada sector, los cuales son discutidos en la reunión de evaluación de esas actividades, especialmente en lo que se refiere al relacionamiento interno entre diferentes sectores.
Una forma de transformar el mapa de programación, en más compacto y consecuentemente de simple manejo y con menor posibilidad de error en la búsqueda de los equipos programados, es la sustitución de las 52 columnas por una sola, donde se escribe el número de la semana o semanas, en el caso de periodos inferiores a un año, manteniendo la información del mapa indicado anteriormente.
Normalmente son necesarias otras columnas, además de aquella adicional a la de programación, para permitir registros de reprogramación (semana y motivo), una vez que los mantenimientos realizados de acuerdo con la programación son identificados sobreponiendo un «X» sobre el número de la semana prevista.
La utilización de este proceso de programación, trae como desventaja el perjuicio en la visualización de las actividades ejecutadas, reprogramadas, pendientes y canceladas, sin embargo, además de la ventaja de eliminar los errores de selección arriba identificados, facilita el manejo cuando los formularios pueden ser encuadernados armando el libro base de programación, que puede ser hecho en varias reproducciones para su distribución a los encargados.
El «NSFI – Norwegian Ship Research Institute» (Instituto de Investigación de la Marina Noruega), desarrolló un sistema de programación manual que denominó «TSAR – Time Scheduling and Recording», que tiene como base un panel plástico con varias ventanillas donde son colocadas tiras de cartones coloridos en forma de «T», una para cada equipo, donde se registran los datos necesarios al mantenimiento programado de esos equipos.
En caso de que el panel plástico sea montado para la programación del mantenimiento, usando como unidad de periodicidad la semana, es recomendable que tenga, además de las 52 columnas, dos o tres más para los principales tipos de prorrogas de tal actividad, como ejemplo: liberación del equipo para la operación, servicio a ser ejecutado durante una gran reparación, aguardando pieza de repuesto, etc.
La gran variedad de colores de las tiras «T», permite que el órgano de planeación y control de mantenimiento, caracterice a los sectores responsables por el mantenimiento, o las unidades de mantenimiento o las clases de los equipos o aun otra característica juzgada de mayor importancia, para su identificación inmediata.
El uso de este panel, facilita la reprogramación de mantenimiento en el mismo año, siendo suficiente cambiar la posición de la tira de una columna por otra. También es más práctico que los otros métodos manuales, ya que dispensa algunas otras referencias, pues algunos datos necesarios para mantenimiento pueden ser escritos en el anverso y reverso de la tira. Sin embargo, esta tarjeta no permite el uso del Registro de Medición o de Variación de las especificaciones de origen, especialmente en caso que se desee implementar el control Predictivo del Mantenimiento a mediano o a largo plazo.
En el sistema de control informatizado, no existe necesidad de elaborar mapas, cartones o tiras. Toda la información es archivada en la computadora, la cual, semanalmente (o diariamente) emite la relación de los servicios a ser ejecutados bajo dos formas: listados para seguimiento de las actividades programadas por el supervisor y solicitudes de trabajo parcialmente compiladas para el uso del ejecutante. Se hace necesario solo un sistema de retorno de informaciones de los mantenimientos ejecutados integral o parcialmente, o reprogramados, lo que puede ser echo a través de la compilación de algunos registros de la propia Orden de Trabajo.
El establecimiento de criterios de programación, tomando la semana como unidad de periodicidad, puede traer la siguiente dificultad en el cálculo automático por el sistema, para la periodicidad mensual y bimensual:
- Una vez que el número de días del mes (30, 31 y 29 en los años bisiestos) no es múltiplo del número de días de la semana (7), se tendría siempre 13 intervenciones mensuales por año, debido a la consideración de que un mes tiene 4 semanas y eventualmente casi 7 bimestres (8 semanas en cada uno).
Para resolver este problema pueden ser utilizadas una de las siguientes alternativas:
- 1) Eliminar 4 semanas del año, unidas o separadamente (en el caso de eliminar semanas intercaladas, se sugiere suprimir los múltiplos de 13). En este caso, el año pasaría a tener, para efecto de programación 48 semanas y así, la periodicidad sería calculada considerando: la mensual como múltiplo de 4, la bimestral como múltiplo de 8, la trimestral como múltiplo de 12, la semestral como múltiplo de 24 y la anual como múltiplo de 48.
- 2) Trabajar con el calendario «juliano» y en este caso la programación sería hecha por el número de la semana del mes (ejemplo: 3ª semana de mayo).
Es evidente, que existe la alternativa de que el usuario, marque manualmente todas las semanas que desee y que las intervenciones sean efectuadas, en función del período previsto la para ejecución del trabajo. Sin embargo, en virtud de que ese trabajo sea efectuado solamente una vez, para algunas empresas puede ser compensador utilizar esta opción.
Naturalmente, de acuerdo con criterios de cada empresa, nuevas correlaciones de equipos (o componentes), pueden ser agregadas o suprimidas del Programa Maestro, recordando que, con excepción de los datos de catastro, hasta la composición de la programación, la computadora desconoce las correlaciones indicadas, y esas correlaciones inducirán las responsabilidades burocráticas de búsqueda, tras la implantación del Sistema.
Análogamente al catastro, la programación de mantenimiento desarrollada por computadora personal, puede ser subdivida en módulos con las siguientes finalidades: actualización de las tablas de programación; de las instrucciones de mantenimiento; del programa maestro de mantenimiento preventivo; emisión de listados de programación; emisión de órdenes de trabajo de actividades programadas y emisión de órdenes de trabajo de actividades no programadas.
Para evitar que el usuario tenga necesidad de recurrir al listado de las tablas, o tenga que memorizar todos los códigos para efectuar una actualización de programación, el sistema puede, abrir las tablas correspondientes, a medida que el usuario vaya introduciendo los datos de programación, enseguida, el mismo usuario, a través de barrer con el «Mouse» selecciona el elemento de la tabla que desea incluir o alterar.
En la Figura 25, se presenta un modelo de pantalla con los datos existentes en una programación seleccionada.

El sistema debe permitir la emisión de listados ordenados: por el nombre del equipo o componente, por el código, por las semanas, o cualquier otra ordenación deseada por los usuarios.
Dentro del orden posible de las listas de programación, se resaltan:
- por orden alfabético de equipos o de componentes;
- por orden de semana;
- para una semana específica – emitida para el Supervisor de Mantenimiento, para el seguimiento de las actividades programadas para una semana elegida.
De los ejemplos aquí ilustrados, se nota que podrían ser emitidas listas ordenadas por cualquiera de las columnas que componen el programa maestro de mantenimiento preventivo, siendo una de las más interesantes la del Código de Material, pues permite visualizar la intercambiabilidad de los componentes o piezas que reciben el mismo código.
Inventario y Catastro
para implantar un sistema de control del mantenimiento, es recomendable iniciar el proyecto de recopilación de datos, con la identificación de los elementos que componen la instalación industrial o de servicios, su localizacion y utilidade. Este conjunto de informaciones, llamado Inventario, correlaciona cada equipo con su respectiva área de aplicación, función, centro de costos y posición física o geográfica en el área de producción y ofrece ayudas al personal de la gerencia, para el dimensionamiento de los equipos de operación y mantenimiento, cualificación necesaria al personal, definición de instrumentos, herramientas y máquinas, además de la proyección del plan general de construcción y distribución de los talleres de apoyo.
Una vez identificados los equipos que componen la instalación, los registros se complementan, en la medida de lo posible, en base a un estándar, con la demás informaciones las cuales deben ser suficientemente amplias para absolver consultas de especificación, fabricación, adquisición, traslado, instalación, operación y mantenimiento. A este conjunto de información la llamamos Catastro, que es definido como:
«Registro del mayor número de datos posibles de los equipos, a través de formularios o pantallas estandarizadas, que archivados(as) de forma conveniente, posibiliten el acceso rápido a cualquier información necesaria, para: mantener, comparar y analizar condiciones operativas, sin que sea necesario recurrir a fuentes diversas de consulta».

Por lo tanto, el catastro deberá reunir para cada tipo de equipo: los datos de construcción (manuales, catálogos y diseños), de compra (adquisición, solicitudes, presupuesto, fechas y costos), de origen (fabricante, proveedor, tipo y modelo), de transporte y almacenamiento (dimensiones, peso y recomendaciones), de operación (características normales y límites operativos) y de mantenimiento (lubricantes, repuestos generales y específicos, curvas características, recomendaciones de los fabricantes, límites, holguras y ajustes).
Actualmente la concepción de la recopilación de datos de catastro, está presentando mejoras con la evolución de los criterios de planeación y control de mantenimiento. Los primeros formularios desarrollados para esa finalidad, tenían la configuración de una tarjeta impresa con información genérica y aplicada a cualquier tipo de equipo, donde los datos generales y específicos aparecían mezclados y algunos indefinidos.
En la secuencia evolutiva, el reverso de la tarjeta pasó a ser utilizada para el registro del historial, a través de dos columnas, una para la fecha y otra para la descripción de la ocurrencia.
A partir de esa concepción, surgió la tarjeta de Catastro e Historial, con el cuidado de indicar en la primera columna la descripción de la ocurrencia y en las siguientes, las fechas en que la misma sucedía. Ese esmero trajo como ventajas adicionales, el evitar la repetición de la misma ocurrencia varias veces, facilitando la visualización de aquellas que presentaban mayor incidencia, además de realizar algunos aciertos en la disposición de datos, lo que también, permitía facilitar la búsqueda en cuatro formas: Número del archivo, Código de Catastro, Número Individual del Equipo y Código de Equipo.
Con la utilización de la computadora en el proceso de control del mantenimiento, surgió la idea de asociar el catastro de equipos, a sus respectivos repuestos de uso específico y de uso común. Y el órgano de mantenimiento pasó a utilizar, para el Código de Catastro, la misma estructura de codificación del órgano de administración de material. Como consecuencia de esa fusión, el Código de Catastro pasó a representar una «familia» de equipos del mismo fabricante, tipo y/o modelo y surgió la propuesta de separar los datos comunes de los datos específicos de los equipos durante el catastro.
Por lo tanto, al «Código de Catastro» (o «Código de Familia») pasaron a ser asociadas las características administrativas y técnicas de la familia de equipos. Considerándose que en una instalación industrial que tuviese «x» bombas iguales, sería suficiente la compilación de apenas un grupo de registros.
En los registros de datos específicos, el código de catastro fue asociado al número de identificación que individualizaba cada equipo de la instalación. Ese número de identificación podía ser el número de serie suministrado por el fabricante, o el número que recibe del órgano de control de bienes patrimoniales de la empresa, o en el caso de ausencia de ambos, un número secuencial dado por el propio sistema, que es impreso o troquelado en el equipo. Tal número de identificación caracteriza un conjunto de datos individuales a cada equipo y así, para el ejemplo considerado, sería necesario compilar «x» formularios de datos específicos, uno para cada bomba de la instalación.
Tanto en los datos generales (o comunes) como en los datos específicos, existen registros de naturaleza administrativa (fechas, costo, números de documentos, localización etc.) y de naturaleza técnica, entre las cuales se destaca su función en el proceso o servicio.
La correlación entre el código de catastro, el número de identificación y el código de posición operativa («tag» o código de equipo), permite la obtención de información para una «familia » de equipos (código de catastro) o para un equipo específico (número de identificación), o para los equipos que operan en una determinada localización de la instalación (código de equipo), lo que representa una inmensa ventaja para el análisis y decisión de los gerentes de mantenimiento.
Se ha de ilustrar esta ventaja con el siguiente ejemplo: suponiendo que en una planta existan tres compresores de iguales características, todos importantes para el proceso productivo y, por esta razón se tiene en el almacén, uno de reserva para una rápida sustitución. Si uno de los compresores queda inoperante, es sustituido inmediatamente por el de reserva, mientras el primero va para reparación.
Los cuatro compresores (tres en operación y uno de reserva), por tener las mismas características de fabricación, recibieron el mismo Código de Catastro, «A», mientras cada uno tiene su Número de Identificación «1», «2», «3», «4», y un Código de Posición Operativa, «a», «b», «c», «d». Si el compresor que dejó de funcionar fue el número «2» y fue sustituido por el número «4», se tendrá la situación indicada en la Figura 17.

Existiendo la necesidad de un análisis de ocurrencia con este tipo de equipo, los gerentes de mantenimiento pueden solicitar el registro de las incidencias por el código de catastro, que incluirá los cuatro compresores (A), y mostrará el tiempo que operaron, el tiempo que uno de ellos estuvo en reparación y la sustitución en el almacén; o por el código de equipo (por ejemplo – b), que mostrará el comportamiento de los compresores que actuaron en aquella posición operativa de la instalación (en este caso los compresores 2 y 4); o por el número de identificación que mostrará el comportamiento de uno de los compresores elegido.
Con el recurso de la utilización de una red de computadoras personales, el catastro puede ser efectuado aportando la información directamente al sistema informatizado, sin que sea necesario el desarrollo de formularios para esa finalidad. Con esta modalidad, es necesario analizar la composición de las «pantallas», que auxiliarán a los usuarios en la alimentación de datos, para formación de los archivos relativos a los equipos instalados y, con el auxilio de las tablas (tanto para los datos administrativos como técnicos), el sistema ayuda al usuario en la compilación de cada campo.
Las técnicas modernas de composición de banco de datos, permiten que el usuario visualice los nombres de los equipos, evitando de esta manera, la necesidad del conocimiento de esos códigos, que quedaran limitados al trabajo de procesamiento por la computadora, aumentando así, su desempeño y reduciendo tiempos de búsqueda – Figura 18.

En las Figuras 19 y 20 se muestran modelos de pantallas con Catastro General y Catastro Específico.


Los archivos de catastro general y de catastro específico, pueden ser independientes (en este caso, correlacionados por el código de catastro) o comunes (en este caso, con el recurso de «duplicación de datos») o sea, la compilación de datos iguales de un nuevo equipo, es hecha sobre los datos de otro existente con las mismas características de construcción – Figura 21.

En esta condición, todos los datos serán almacenados en un único archivo. Nótese que esa opción genera archivos con datos repetidos lo que, actualmente, con la alta capacidad de los discos rígidos y la alta velocidad de procesamiento de las computadoras, dejó de ser un inconveniente.
Es común en los sistemas modernos, que el usuario, pueda registrar componentes de equipos y crear un árbol jerárquico de esos componentes con relación al equipo, al sistema operacional y a la propia planta. De esta forma, además de la posibilidad de consulta por «familia» o por individuo, podrán también ser hechas para todos los equipos de una planta o de un sistema operacional. Obviamente también podrán ser hechos filtros para consultas de datos de un determinado componente de un equipo, o de componentes de igual naturaleza de varios equipos.
La compilación de datos de catastro debe ser de simple operación, donde el sistema sea capaz de abrir automáticamente la tabla correspondiente de cada dato a ser registrado, en el caso de «inclusión» o «modificación» y sobre la información a ser tratada en el caso de «consulta», recordando que, normalmente el usuario no tiene conocimientos de informática y de esta forma no tendrá acceso al programa para adaptarlo a sus necesidades.
La separación de los registros en dos grupos de datos de catastro (común y específico) trae como ventaja adicional la posibilidad de establecer la correspondencia entre las «familias» y los repuestos a ésta aplicados – Figura 22.

Además de las críticas, por el sistema, respecto del tamaño de los campos, en el aspecto de su composición, incluyendo el tipo de carácter a ser usado (numéricos y/o alfabéticos, mayúsculas y/o minúsculas, símbolos gráficos y matemáticos) y fechas (número de días en el mes, los años bisiestos y cronología), debe ser previsto el uso de las teclas de función para la búsqueda de tablas, que auxiliarán al usuario en la composición de los códigos.
La emisión de los listados de catastro podrá ser efectuada para uno, algunos o todos los equipos, de acuerdo a la necesidad del usuario (filtro). Análogamente, deberá ser prevista la emisión de estas listas bajo varios requerimientos, de acuerdo con la definición hecha durante la fase de Proyecto del Sistema.
Tanto en el Catastro por el Sistema Manual, como en los Sistemas Automatizados o por Computadora, podría ser necesario definir los criterios de arreglo de la información archivada, de las listas emitidas por la impresora y/o a través de la pantalla.
Entre las varias opciones de agrupación de la información objetiva facilita el análisis, cono el los ejemplos:
- Agrupación por línea de producción;
- Agrupación por tipo de equipo;
- Agrupación por área geográfica;
- Agrupación por unidad de producción;
- Agrupación por importancia operacional;
- Agrupación por unidad móvil.
Es frecuente que se realice, en una misma empresa, la consulta de datos de catastro bajo diferentes formas de agrupación; cuando esto sucede en el catastro por el sistema manual, el proceso de archivo se torna más complejo, existiendo la necesidad de composición de nuevas tablas auxiliares de periodicidad, y en algunos casos, duplicidad de registros. En el catastro a través de sistemas automatizados, estas inconveniencias son eliminadas, puesto que, a través de programas adecuados, la computadora presentará la información bajo diferentes formas de agrupación, en función de la necesidad y deseo del usuario.
No habiendo una definición previa por parte de los usuarios, respecto a la forma de archivo y emisión de informes de catastro, los proyectistas deberán elegir los criterios a ser adoptados la agrupación de la información, tomando como base el proceso adoptado, el detalle de los formularios, la importancia operacional de los equipos, los órganos y niveles de gestión a ser atendidos y la movilidad de los equipos.
Instrucciones de Mantenimiento y Recomendaciones de Seguridad
Para normalizar los servicios de las actividades programadas del mantenimiento, es recomendable el desarrollo de Instrucciones de Mantenimiento, orientando objetivamente la ejecución del mantenimiento en esas actividades para evitar que alguna tarea sea omitida por desconocimiento u olvido – Figura 23
Estas instrucciones, deben ser desarrolladas, aprovechando el conocimiento del personal técnico de ejecución , con más experiencia y las recomendaciones de los fabricantes y montadores, indicaciones de los catálogos, manuales, diseños y referencias de profesionales con experiencia de otras empresas similares, relativas a cada equipo.
Cada línea de instrucción es conocida como «tarea». Por lo tanto, una instrucción de mantenimiento es un conjunto de tareas una vez compuestas, es recomendable que se estime su valor en horas-hombre para su ejecución, el cual es conocido como «tiempo patrón».

El «tiempo patrón» debe ser ajustado a la realidad, en la medida en que sean obtenidos los datos reales de cada actividad. Una forma simple de efectuar este ajuste es utilizar el valor medio entre el existente en el archivo y el obtenido en la realidad.
Como una refinación para evitar ajustes indebidos del «tiempo patrón», el sistema puede contener un «desvío patrón» definido por el usuario, o sea, un porcentaje sobre el valor del «tiempo patrón» que cuando sea superado (más o menos) excluye el ajuste del tiempo existente. El uso del «desvío patrón» impide el reajuste de tiempos estándares en caso de anomalía en la ejecución del mantenimiento, como por ejemplo: la fractura de un tornillo al retirar su tuerca.
Las instrucciones pueden ser de carácter genérico o específico, en función al nivel de detalle deseado. Una instrucción de mantenimiento de carácter genérico, no detalla los puntos de ejecución de cada etapa de la tarea que describe y, puede ser utilizada para la ejecución de la misma actividad en cualquier equipo de iguales características operativas; mientras que la Instrucción de Mantenimiento de carácter específico, indica en forma detallada las tareas a ser ejecutadas, normalmente sólo útil al equipo para la cual fue elaborada.
Ya se encuentran en desarrollo, las bibliotecas de tareas de mantenimiento (para la composición de las Instrucciones de Mantenimiento) que serán asociadas al componente del equipo. La utilización de estas bibliotecas, facilitará a las empresas, la implantación de sus actividades programadas de mantenimiento.
Como variante de las instrucciones de mantenimiento, existen los archivos de Recomendaciones de Seguridad, normalmente asociados a la naturaleza del equipo y que tienen por finalidad, evitar actos inseguros durante la ejecución del mantenimiento o el mantenimiento en condiciones inseguras.
Cursos recomendados
-1730145694747.webp%3Falt%3Dmedia%26token%3D719f647e-063f-47e9-a9f4-c3b59cb3a8ab&w=3840&q=75)



%252FImagen%252Frcm-1730083250826.webp%3Falt%3Dmedia%26token%3D3775356a-7b11-4c44-b21f-45b3409fb9ed&w=3840&q=75)

%252FImagen%252FRAMPREDYC-1730060420837.webp%3Falt%3Dmedia%26token%3D2634a7f0-988e-4022-b91f-382503e6e9db&w=3840&q=75)

Recolección de Datos – Recomendaciones
Antes de definir cual información debe ser reunida, se ha de abordar algunas recomendaciones, obtenidas a través de la experiencia práctica, que se consideran fundamentales para que se pueda confiar en los datos obtenidos:
• Aclaración al personal de ejecución, respecto a la finalidad de la recolección de los datos.
Al presentar esta recomendación se sugiere que el proyecto y desarrollo de los mecanismos de recolección de datos, sea hecho con la participación directa del personal de ejecución en todos los niveles, tanto en el aspecto de exposición, como de captación de ideas sobre el proceso a ser utilizado y los resultados pretendidos. Existe mayor probabilidad de éxito, cuando los que vayan a suministrar la información, hayan participado en el proyecto de desarrollo o adaptación del sistema a sus necesidades.
• Simplicidad de diligenciamiento de los documentos o «pantallas» en la recolección de datos.
En el caso de registro en formularios, tratar cuando sea posible, que la información se encuentre previamente impresa, de manera que el registro sea efectuado marcando con una «X» la opción elegida. En caso del registro a través del teclado de la computadora o terminal, la propia computadora deberá auxiliar a el usuario a través de «pantallas» de consulta y utilización del cursor a través del «ratón».
• Nítida definición de lo que deberá ser analizado antes de implementar el proceso.
Esta recomendación, tiene por objeto evitar que sea realizada la recolección de datos innecesarios, sobrecargando el trabajo y sin obtener un fin definido o con detalles innecesarios. Se debe recordar que todos los datos que se reúnan y procesen, posteriormente deben ser analizados obteniendo mejorías en las condiciones de trabajo del personal y de los equipos además de la reducción de costos.
• Reducir al mínimo posible, la cantidad de modelos de formularios a ser diligenciados.
Buscar estandarizar la información en todos los sectores del mantenimiento para evitar que cada uno cree sus propios formularios, lo que encarecería el procesamiento de datos, tanto en el sistema de control manual como el automatizado
• Evitar que la recolección de datos implique la interrupción en la ejecución de los servicios, o trabajo adicional excesivo para el personal de ejecución del mantenimiento.
Es recomendable que el encargado del servicio sea el que haga los registros de historial, sin embargo, los otros registros deben ser hechos por cada responsable del suministro de los datos o sea, los ejecutantes del mantenimiento hacen los registros de sus tiempos ocupados, los bodegueros hacen los registros del material aplicado en cada Orden de Trabajo, los operadores hacen el registro de indisponibilidad y pérdida de producción y el área de recursos humanos hace los registros de disponibilidad de personal y respectivos costos, recordando que todos deben estar conscientes de la importancia de tales datos.
• Capacitar de manera adecuada a los responsables por la recolección de datos.
En caso de utilización de formularios, que serán posteriormente digitados, orientar a los responsables por los registros, en lo referente a la utilización de letras de imprenta: cortar la letra «Z» y el número «0», para evitar que se confundan con el número «2» y la letra «O». También, en lo referente al llenado de la información en los lugares correctos, para facilitar el trabajo de los digitadores y reducir los errores de transcripción de los datos. En el caso de transferencia directa de la información a través de la terminal o en computadora personal, se debe orientar en cuanto a la dimensión de los campos y limitaciones relativos al uso de caracteres.
• No procesar informes por computadora inmediatamente después que se implante un sistema automatizado.
En el caso del cambio de sistema de control manual para automatizado, analizar atentamente los primeros formularios completados, antes de enviarlos a digitación, solicitar emisión de las listas de verificación de los datos, hasta tener seguridad de que los mismos, están siendo correctamente compilados y digitados.
• Estructurar convenientemente la recolección de la información, con el fin de poder analizar los datos reunidos y los informes emitidos.
Ya que cualquier cambio crea reacciones, es fundamental que para el éxito del sistema, los datos después de procesados, traigan beneficios a los responsables de el envío de la información y no exista trabajo adicional de análisis, especialmente en el caso que sean similares a aquellos, que ya se realizaban antes de la implantación del nuevo sistema.
Se debe tener especial atención, para evitar la proliferación de formularios y su multiplicidad con la misma función. Otras recomendaciones dictadas por la experiencia son: la reducción de la responsabilidad burocrática de los ejecutantes del mantenimiento, la estandarización de informaciones, la recolección de datos administrativos en su origen y la interrelación del Banco de Datos, para evitar choques entre diferentes fuentes de información.
Orden de Trabajo
La fuente de datos relativos a las actividades desarrolladas por el personal de ejecución de mantenimiento, debe incluir el tipo de actividad, su prioridad, falla o el defecto encontrado y cómo fue reparado, duración, los recursos humanos y materiales utilizados, y otros datos que permitan evaluar la eficiencia de la actuación del mantenimiento y sus implicaciones con costos y programación.
Las Ordenes de Trabajo (OT) son específicas para cada empresa, en función de la actividad, organización, cantidad y tipos de mano de obra y equipos que posee etc., sin embargo, existe una serie de datos comunes en cualquier ramo industrial o de servicios, que deben estar presentes en este instrumento de información, como: el número consecutivo, el tipo de la actividad de mantenimiento, la prioridad, los registros de historial, si los instrumentos de supervisión actuaron correctamente o no, si la intervención perjudicó la producción, el período de indisponibilidad del equipo y la duración real del mantenimiento.
En los antiguos modelos de OT usadas en el sistema manual, eran presentados en la parte superior: los datos de identificación del equipo y del problema, en la parte media: los datos de planificación, y en la parte inferior: los de ejecución del mantenimiento, subdivididos en dos partes: datos para “Gestión del Equipo” (sumario del servicio ejecutado y comentarios sobre el problema) y para “Gestión de Mano de Obra” (horas-hombre consideradas y utilizadas) – Figura 26.

Los modelos de Orden de Trabajo que siguieron tenían, con relación al anterior, la novedad de la inclusión de las columnas codificadas de “Problema Encontrado”, precursor del actual “Código de Ocurrencias”. En la parte inferior de ese cuadro existían enumeradas, un conjunto de posibles ocurrencias en los equipos relacionados en la referida columna, para que el ejecutante pusiera los números que correspondían a las ocurrencias, en el cuadro correspondiente a la intersección de la línea de la “localización” con la columna del grado de “severidad”, cuyos significados eran presentados al lado de los tipos de ocurrencias.
El modelo siguiente, en la evolución de las OT, fue utilizado durante la fase de transición del sistema de control manual para el automatizado y, por esta razón, apenas la última sección corresponde a la identificación del equipo, la duración del mantenimiento, pérdida de producción, utilización de mano de obra y costos, eran procesadas, no dando el mismo tratamiento a los datos del historial de ocurrencias, que eran transcritos en líneas continuas en la primera y la tercera sección. El formulario era proyectado para producir una tarjeta agujereada (o equivalente), pues poseía 80 caracteres para procesamiento, siendo los cuatro primeros reservados para la identificación del documento.
La orden de trabajo siguiente en el proceso evolutivo fue desarrollada para el sistema de control automatizado, con la producción de una tarjeta agujereada. Presentaba como novedad con relación a la anterior, el registro del “Código de Servicio” con 4 caracteres, siendo el primero destinado a la Ocurrencia (O), que indicaba el origen de la necesidad de la intervención en el equipo, el segundo para la Acción (A), que indicaba lo que había sido realizado por el equipo de mantenimiento y los dos últimos para el Complemento (CPL) de esa acción. La mejor terminología para este código sería: “Código de Ocurrencia”, que serviría para indicar intervenciones debido a Fallas o Defectos, pudiendo también utilizarse el término “Código de Defecto” con el mismo objetivo.
La evolución del modelo de orden de trabajo, utilizada en el sistema automatizado de control del mantenimiento, generaba dos tarjetas perforadas y presentaba, con relación a la anterior, las siguientes particularidades:
- Un campo asociado al número consecutivo para correlacionar a dos o más órdenes de trabajo, cuando la ejecución de las actividades excedía el período mínimo de procesamiento de los informes de gestión, que es definido como “horizonte”;
- El código de mantenimiento compuesto por el código del equipo asociado al componente, actividad y sector;
- La semana y el motivo de la reprogramación, para permitir la replanificación manual, en caso de algún impedimento;
- La indicación de la actuación de supervisión automática;
- El código de ocurrencia compuesto por cuatro “células”, o sea: la Causa: que indicaba la razón de la ocurrencia (falla o defecto) en el equipo; el Efecto: que indicaba como la falla o el defecto eran constatados; la Acción: que indicaba el verbo asociado al servicio ejecutado y el Complemento: que completaba el mensaje de la acción;
- La “espera” que indicaba la cantidad de horas-hombre que quedó inactiva, durante el desarrollo de la actividad de mantenimiento, debido normalmente, a una falla de la planeación. Ese campo estaba asociado al código del motivo que llevaba a esos horas-hombre a la interrupción de sus servicios.
En el inicio de la década de 1 970, surgió el proyecto BOZZ-ALLEN & HAMILTON que presentó como singularidad, la omisión de la recolección de información de la mano de obra en el cuerpo de la orden de trabajo; siendo estas informaciones recogidas, a través de un documento complementario llamado Tarjeta de Tiempo, con forma y tamaño similar a la tarjeta horaria, pero con características diferentes, ya que servía para que cada ejecutante indicase, en cada servicio que recibía, el día, la hora y el minuto en que iniciaba y terminaba, identificando el número de la Orden de Trabajo – Figura 27.
La parte posterior de esta tarjeta contiene los códigos de servicio, espera y ausencia para indicarlos, en la columna respectiva la actividad ejercida, durante cada período de su jornada. A cualquier momento, siempre que se complete una tarjeta, el ejecutante debe sustituirla por una nueva para asegurar la continuidad de los registros.
Como recomendación, para evitar celos de fiscalización individual a los ejecutantes del mantenimiento y, en consecuencia, el sabotaje de los registros, la Tarjeta de Tiempo, debe ser impersonal e individual para cada ejecutante de mantenimiento, o sea, identificar apenas el cargo y no el nombre de la persona.
Como variante de la Tarjeta de Tiempo, puede ser utilizada la Tarjeta de Material, cuya responsabilidad de compilación es del encargado del depósito, que relaciona el material suministrado al respectivo consecutivo de la Orden de Trabajo en la tarjeta – Figura 28


Para implementar tanto la Tarjeta de Tiempo, como la Tarjeta de Material, debe realizarse un trabajo de orientación y búsqueda junto a los ejecutantes, en lo referente a la compilación, para evitar que los datos dejen de ser registrados o lo sean de manera equivocada, involuntariamente o a propósito.
Una innovación importante en el sistema de recolección de datos en el control automatizado de mantenimiento fue la emisión, a través de la propia computadora, de las órdenes de trabajo parcialmente llenadas, a partir de datos provenientes del Plan Maestro de Mantenimiento Preventivo, enfatizando en la reducción de las actividades burocráticas de los ejecutantes de mantenimiento – Figura 29.

Con la implantación de la orden de trabajo para mantenimientos preventivos, emitida a través de la computadora, surgió también la idea de utilizar la máquina para reprogramar actividades que no fuesen ejecutadas dentro de un plazo aceptable y así, permitir este trabajo de reprogramación automatizada, fue fortalecido el concepto de Clase.
Durante el desarrollo del proyecto, se determina para cada actividad el plazo de espera por la computadora, para el retorno de las órdenes de trabajo, plazo que si era excedido, acarreará el cobro del motivo de la no ejecución, siendo esta información transferida para el archivo en el banco de datos para su posterior inscripción en el informe de gestión de no conformidades.
Para dar conocimiento al ejecutante sobre estas limitaciones de plazo, la computadora informa a través de los campos de Próxima Reprogramación y Semana Límite de Reprogramación en la emisión de cada orden de trabajo.
Para reducir aún más las responsabilidades burocráticas de los ejecutantes del mantenimiento y asegurar que los servicios programados, sean realizados de acuerdo con un estándar preestablecido, la orden de trabajo emitida por la computadora, puede contener también, las Instrucciones de Mantenimiento ya impresas.
Sin embargo, es necesario que estas instrucciones sean redactadas de forma concisa, para evitar la proliferación de estos documentos. Como sugerencia, es recomendable que sea limitado a 30 el número de líneas para cada actividad programada en cada componente.
En los Sistemas donde se utiliza para la emisión de la orden de trabajo para actividades programadas a la computadora, es necesario desarrollar otro modelo de orden de trabajo, para permitir la anotación de datos de actividades no programadas.
Para estandarizar los registros de “Descripción” y “Servicio Ejecutado”, además de reducir el número de registros del banco de datos del historial y consecuentemente, el tiempo de búsqueda, hecho importante en el caso de la utilización de computadoras personales de menor performance en el proceso, es recomendable la utilización del “Código de Ocurrencias” citado anteriormente, que traerá como ventaja adicional, la posibilidad de búsqueda en el historial de una ocurrencia específica o de cualquiera de los elementos que compongan este código – Figura 30.

Puede observarse también, en este modelo de OT, la inclusión de campos para la anotación, por parte del usuario de los servicios de mantenimiento (llamado “cliente”), de la evaluación del trabajo ejecutado a través de las opciones: “plenamente ejecutado”, “provisionalmente ejecutado”, “reservicio” y “no atendido”, como un factor de medición de la calidad de los servicios del mantenimiento. Este tipo de registro, que posibilitará la evaluación de la gestión de mantenimiento respecto a las necesidades de producción, puede ser incluido también en las órdenes de trabajo de actividades programadas.
En los modelos de las órdenes de trabajo de actividades programadas y no programadas ilustrados, se puede observar la existencia de un código QR o de barras que puede ser emitido por la computadora, para facilitar la lectura en sistemas integrados (por ejemplo: para que el encargado del depósito asocie el material a emplear al número de la OT).
Para evitar, la utilización de uno de los modelos presentados en las Figuras 29 y 30, en el registro de actividades que no exigen detalle, o para el registro de mantenimientos en equipos que no afectan al proceso productivo (Clase C), o aun, para hacer referencia a actividades diferentes del mantenimiento, que ocupan mano de obra del personal de mantenimiento, puede ser utilizado un formulario común, la Orden de Trabajo de Ruta, u Orden de Trabajo Colectivo u Orden de Trabajo para Actividades Diversas, como el modelo ilustrado en la Figura 31, donde en cada línea es hecho el registro de cada servicio, teniendo para cada uno, apenas el registro del inicio y final de la actividad, para el cálculo por computadora, de la duración de la actividad.

Una vez que este formulario tiene un “horizonte” mensual, para permitir que sus datos sean procesados y formen parte de los informes de gestión de costos y mano de obra; puede recibir un número de identificación consecutivo mensual, que servirá como referencia para su registro, en las Tarjetas de Tiempo de los ejecutantes, para el cálculo de los horas-hombre empleados en este tipo de actividades.
En caso que los usuarios deseen separar la ocupación de mano de obra en mantenimiento (para los equipos Clase C) de los demás (Servicios de Apoyo), pueden ser utilizadas dos Ordenes de Trabajo de Actividades Diversas con números diferentes, una para cada fin. Esta observación también es válida, en el caso de los usuarios que deseen conocer la ocupación de mano de obra en un determinado tipo de Servicio de Apoyo como “tránsito”, o “capacitación interna”.
Mano de obra disponible
Se entiende, como mano de obra disponible de un órgano de ejecución del mantenimiento, el resultado de las horas-hombre efectivas, o sea, el producto del número de empleados de ese órgano por el número de horas trabajadas (normales y extras), menos el número de horas-hombre no presentes por motivo de vacaciones, enfermedad, servicio en otras unidades de la empresa, capacitación externa, accidente o cualquier otro motivo autorizado o no, que haya provocado la ausencia del personal.
Para la recolección de datos de disponibilidad de personal, para la ejecución del mantenimiento propio y de refuerzo en otras áreas de la empresa o de contratistas, es necesario el desarrollo de un formulario, que debe ser completado por el órgano administrativo de cada unidad de producción, a partir de los registros de las tarjetas horarias u otro sistema de control de horario adoptado en la empresa. En el caso de que este órgano, disponga de un sistema específico, para el registro de estos datos y que el sistema esté correlacionado con el de mantenimiento, estos pueden ser transferidos directamente de un sistema para otro.
Datos de operación
Para permitir el procesamiento de información relativa a los informes de gestión de equipos y costos (facturación cesante), debe ser previsto el registro de los datos provenientes de operación, que deberán constar básicamente de: horas de funcionamiento de los equipos por período de control (horizonte), pérdida o reducción de la producción debido al mantenimiento, además de la referencia a cada intervención, normalmente hecha a través de la indicación del número de la orden de trabajo – Figura 32.

Estos registros, deben ser hechos por los propios operadores y, como en el caso anterior, habiendo integración, esta información puede ser obtenida directamente de los bancos de datos de operación.
Registro de Medición
Para el registro de los valores de las mediciones efectuadas, durante el mantenimiento de los equipos prioritarios (Clase A) y algunos secundarios (Clase B), para los cuales se juzgue conveniente acompañar las variables, para la implantación del Control Predictivo del Mantenimiento, se deben estandarizar mecanismos de registro específico, cuyos valores resultantes de medición, serán procesados para la obtener las curvas de dejeneración – Figura 33.
Debe aclararse que, generalmente los resultados prácticos del seguimiento de la variación de las variables de un equipo, con el objetivo de implantar el Análisis de Síntomas, no son inmediatos, pudiendo en algunos casos, presentar resultados tras varios años de seguimiento, siendo inclusive, recomendable que inicialmente sea realizada una evaluación, respecto a la validez del resultado en equipos que no comprometan el proceso productivo (Clase B).
Durante el desarrollo de este tema, es recomendable que los registros indicados, sean compilados por órganos distintos, de manera que se distribuya las tareas y se cierre el ciclo de información, lo que permitirá detectar fallas intencionales o involuntarias de compilación.

También es muy importante, la necesidad de establecer plazos límites («horizonte») para que sean procesados, evitando que algunos informes de gestión carezcan de información o con errores por no computar todos los datos.
Autor: Lourival Augusto Tavares
Brasil
Consultor en Ingeniería de Mantenimiento
Empresa: Director nacional de ABRAMAN (Asociación Brasileña de Mantenimiento) en dos mandatos.
Correo: l.tavares@mandic.com.br
Ingeniero Electricista, formado por la Escuela Federal de Ingeniería de Rio de Janeiro, en el año de 1967. Past-Presidente del Comité Panamericano de Ingeniería de Mantenimiento. Supervisor de Mantenimiento en FURNAS – Centrales Eléctricas S.A. durante 23 años. Fue el jefe de la Asesoría Técnica de Apoyo en ITAIPU Binacional. Reconocido como “notorio saber” en mantenimiento por la Universidad Federal de Rio de Janeiro y por la Universidad Federal de Paraíba.
Dinos qué te ha parecido el artículo
Artículos recomendados
¿Qué tan confiable es su producto?: 50 formas de mejorar la confiabilidad del producto

Gestión de garantía y fabricación de productos

Árboles de fallos (Sistemas de control, robótica y fabricación)

Confiabilidad de los Sistemas y Prevención de Fallas

Publica tu artículo en la revista #1 de Mantenimiento Industrial
Publicar un artículo en la revista es gratis, no tiene costo.
Solo debes asegurarte que no sea un artículo comercial.
¿Qué esperas?
O envía tu artículo directo: articulos@predictiva21.com
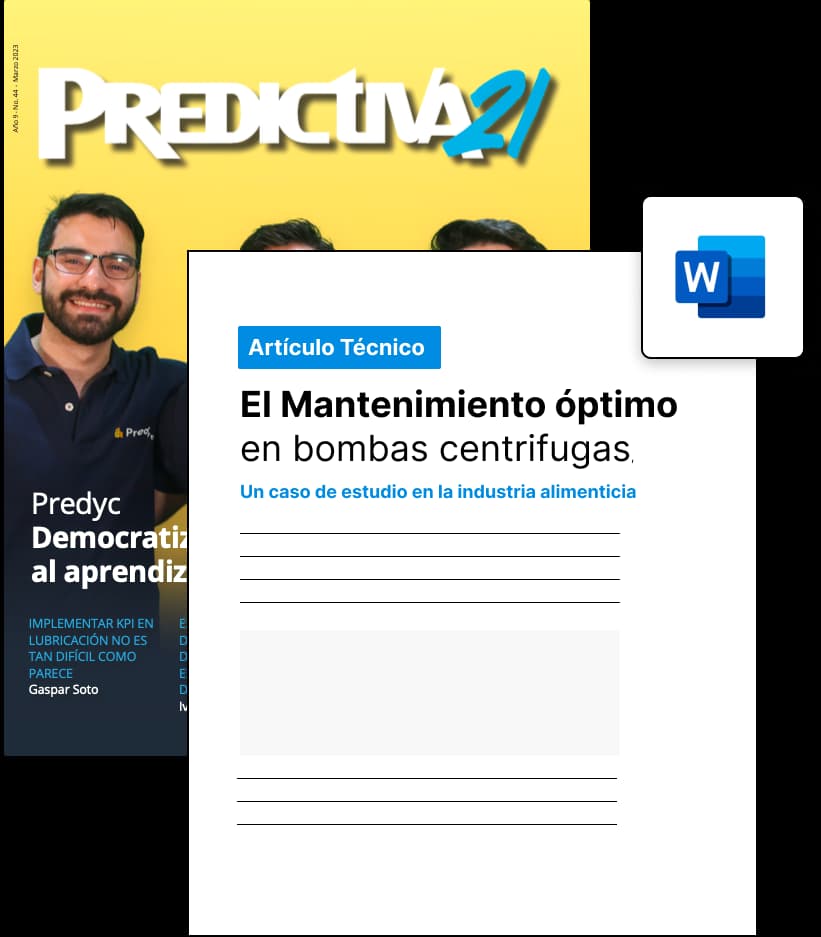