¿Qué es el RCM? Descubre este poderoso proceso
Articulo9 de agosto de 2023
Autor: Predictiva 21La revista digital de Mantenimiento, Confiabilidad y Gestión de Activos.
Historia del RCM
El RCM es un proceso desarrollado en la década de 1960 y 1970. El RCM nació con la finalidad de ayudar a las personas a determinar las políticas para mejorar las funciones de los activos físicos y manejar las consecuencias de sus fallas. Por esto, de la mayoría de los procesos, el RCM es el más efectivo. Entonces, a mediados de 1970, el gobierno de E.E.U.U necesitaba saber más acerca de la filosofía actual en el área de mantenimiento de aeronaves, que estaba surgiendo en esa época. En consecuencia, solicitaron un reporte sobre éste a la industria aérea. El reporte fue creado por Stanley Nowlan y Howard Heap, de United Airlines. Ellos lo titularon como “Reliability Centered Maintenance” (o mantenimiento centrado en la confiabilidad, de acuerdo a sus siglas en inglés). Este reporte fue publicado en 1978. Actualmente, se sigue considerando como uno de los documentos más importantes en la historia del manejo de los activos físicos. El reporte de Nowlan y Heap ha sido usado, desde entonces, como base para varios modelos de RCM de tipo militar e incluso para las actividades no relacionadas con la aviación. Así, en la década de los ochenta, la técnica RCM comenzó a usarse en la industria en general.Definición formal de RCM
John Moubray, define al RCM como “un proceso utilizado para determinar que se debe hacer, para asegurar que cualquier activo continúe haciendo lo que sus usuarios quieren que haga, en su contexto operacional”. Entonces, podemos describir el RCM como una metodología empleada para elaborar planes de mantenimiento que incluyan todo tipo de estrategias (mantenimiento preventivo, predictivo, búsqueda de fallas, etc.), basadas en la confiabilidad de los equipos.Las 7 preguntas claves para la técnica RCM
De acuerdo con la norma SAE - JA1011/J1012, todo proceso RCM debe responder en secuencia a las siguientes siete preguntas.- ¿Cuál es la función?, Lo que el usuario desea que el activo haga.
- ¿Cuál es la falla funcional?, Razones por las que deja de hacer lo que el usuario desea que haga.
- ¿Cuál es el modo de falla?, Que pudo causar la falla funcional.
- ¿Cuál es el efecto de la falla?, Que ocurre cuando la falla se produce.
- ¿Cuál es la consecuencia de la falla?, Razones por las que importa que falle.
- ¿Qué se puede hacer para evitar o minimizar la consecuencia de la falla?
- ¿Qué se hace si no se encuentra ninguna tarea para evitar o minimizar la consecuencia de la falla?
6 pasos para realizar un programa de mantenimiento centrado en la confiabilidad
Existe una gran variedad y métodos diversos en las aplicaciones del RCM. Entonces, la mayoría de los programas aplican los siguientes seis pasos como punto de partida para implementar un plan RCM.Paso 1: Seleccionar un análisis RCM de activos.
Primero, se debe elegir un activo sobre el que realizar el análisis RCM. Algunos factores a tener en cuenta son:- el grado de criticidad del activo para las operaciones,
- sus costes de reparación en el pasado,
- los costes de mantenimiento preventivo anteriores.
Cursos recomendados


En línea en vivo5 de julio


En línea en vivo5 de julio


En línea en vivo9 de agosto
%252FImagen%252FRAMPREDYC-1730060420837.webp%3Falt%3Dmedia%26token%3D2634a7f0-988e-4022-b91f-382503e6e9db&w=3840&q=75)

En línea en vivo1 de noviembre
Paso 2: Describir las funciones del sistema para el activo seleccionado.
Es importante conocer las funciones del sistema, incluidas sus entradas y salidas, por pequeñas que sean. Por ejemplo, las entradas de una cinta transportadora son las mercancías y la energía mecánica que impulsa la cinta.Paso 3: Definir los modos de fallo.
Comprender las diferentes formas en que puede fallar el sistema. Por ejemplo, la cinta transportadora puede transportar la mercancía con la suficiente rapidez o no transportarla por completo de un extremo a otro.Paso 4: Evaluar las consecuencias del fallo.
El fallo de un activo puede dar lugar a problemas de seguridad y a un mal rendimiento de la empresa. También, puede afectar a otros equipos. Los operarios de la planta, los expertos en equipos y los técnicos de mantenimiento deben trabajar juntos para identificar las causas fundamentales de los fallos de cada activo. Este proceso ayuda a determinar cómo priorizar las tareas.Paso 5: Determinar una estrategia de mantenimiento para cada modo de fallo.
Aquí, se selecciona una estrategia de mantenimiento para cada modo de fallo crítico. Debe ser factible tanto económica como técnicamente. Puedes utilizar el mantenimiento basado en la condición o CBM, el mantenimiento preventivo o el mantenimiento predictivo. En caso de no poder aplicar una estrategia determinada para un modo de fallo concreto, se considera la posibilidad de rediseñar el sistema para modificar o eliminar el modo de fallo.Paso 6: Aplicar la estrategia y realizar revisiones periódicas al programa RCM.
Para que un programa de RCM sea eficiente, es necesario poner en práctica las recomendaciones de mantenimiento identificadas en el paso 5. Luego, tras la aplicación, las revisiones periódicas ayudan a mejorar los sistemas y el rendimiento.Herramientas para aplicar un programa RCM
Las herramientas fundamentales para el desarrollo del proceso de análisis del RCM, son:- La Hoja de análisis y registro: también es conocida como FMECA. Está constituida para la una secciona de análisis de las funciones, fallas y efectos y otra sección, de registro de consecuencias y decisiones.
- El Diagrame de Decisiones: proporciona la base para decidir “si merece la pena realizar” una acción de manteniendo o una acción “a falta de”, en función de las consecuencias y de acuerdo a la naturaleza de la falla. Es decir, si puede ser prevenida o no.
¿Cómo seleccionar el tipo de mantenimiento adecuado?
En el RCM, la selección de políticas de mantenimiento está gobernada por la categoría de consecuencias a la que pertenece la falla.- Para fallas con consecuencias ocultas, la tarea optima es aquella que consigue la disponibilidad requerida del dispositivo de protección.
- Para fallas con consecuencias de seguridad o medio ambiente, la tarea optima es aquella que consigue reducir la probabilidad de la falla hasta un nivel tolerable.
- Para fallas con consecuencias económicas (operacionales y no operacionales), la tarea optima es aquella que minimiza los costos totales para la organización.
Dinos qué te ha parecido el artículo
Artículos recomendados
Análisis de Criticidad Integral de Activos

Autor: Predictiva 21La revista digital de Mantenimiento, Confiabilidad y Gestión de Activos.
Como un CMMS ayuda a impulsar la Excelencia Operativa

Autor: Predictiva 21La revista digital de Mantenimiento, Confiabilidad y Gestión de Activos.
Processes

Autor: Predictiva 21La revista digital de Mantenimiento, Confiabilidad y Gestión de Activos.
Certificación ISO 55000

Autor: Predictiva 21La revista digital de Mantenimiento, Confiabilidad y Gestión de Activos.
Publica tu artículo en la revista #1 de Mantenimiento Industrial
Publicar un artículo en la revista es gratis, no tiene costo.
Solo debes asegurarte que no sea un artículo comercial.
¿Qué esperas?
O envía tu artículo directo: articulos@predictiva21.com
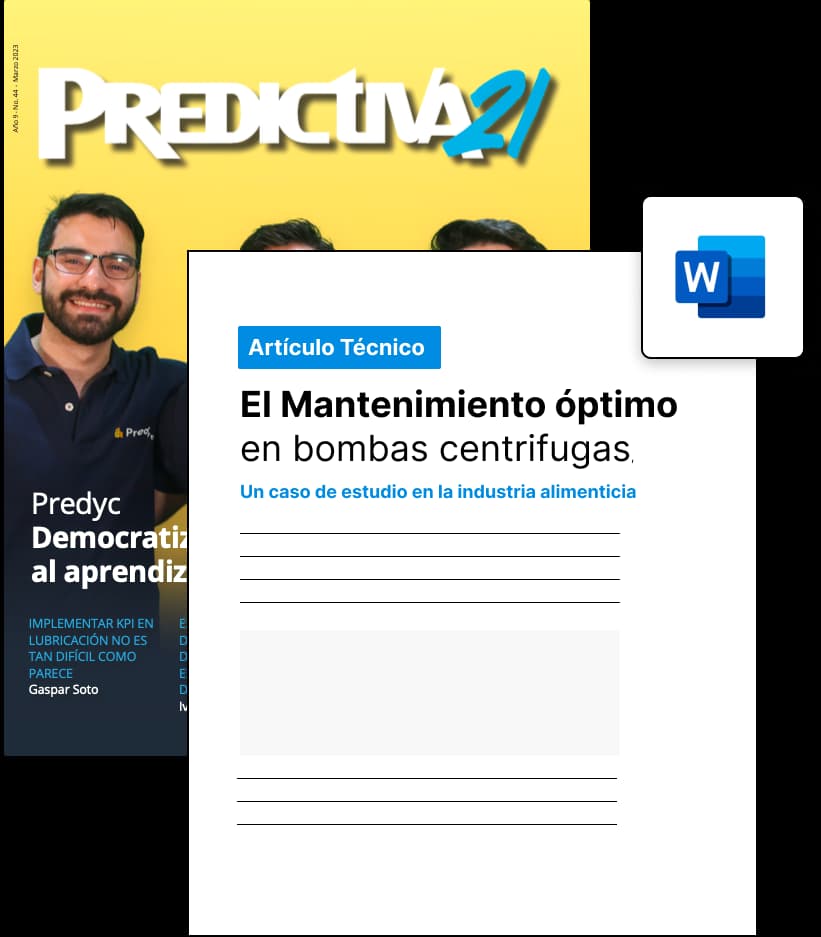
¿Qué es el RCM? Descubre este poderoso proceso
Articulo 9 de agosto de 2023Historia del RCM
El RCM es un proceso desarrollado en la década de 1960 y 1970. El RCM nació con la finalidad de ayudar a las personas a determinar las políticas para mejorar las funciones de los activos físicos y manejar las consecuencias de sus fallas. Por esto, de la mayoría de los procesos, el RCM es el más efectivo. Entonces, a mediados de 1970, el gobierno de E.E.U.U necesitaba saber más acerca de la filosofía actual en el área de mantenimiento de aeronaves, que estaba surgiendo en esa época. En consecuencia, solicitaron un reporte sobre éste a la industria aérea. El reporte fue creado por Stanley Nowlan y Howard Heap, de United Airlines. Ellos lo titularon como “Reliability Centered Maintenance” (o mantenimiento centrado en la confiabilidad, de acuerdo a sus siglas en inglés). Este reporte fue publicado en 1978. Actualmente, se sigue considerando como uno de los documentos más importantes en la historia del manejo de los activos físicos. El reporte de Nowlan y Heap ha sido usado, desde entonces, como base para varios modelos de RCM de tipo militar e incluso para las actividades no relacionadas con la aviación. Así, en la década de los ochenta, la técnica RCM comenzó a usarse en la industria en general.Definición formal de RCM
John Moubray, define al RCM como “un proceso utilizado para determinar que se debe hacer, para asegurar que cualquier activo continúe haciendo lo que sus usuarios quieren que haga, en su contexto operacional”. Entonces, podemos describir el RCM como una metodología empleada para elaborar planes de mantenimiento que incluyan todo tipo de estrategias (mantenimiento preventivo, predictivo, búsqueda de fallas, etc.), basadas en la confiabilidad de los equipos.Las 7 preguntas claves para la técnica RCM
De acuerdo con la norma SAE - JA1011/J1012, todo proceso RCM debe responder en secuencia a las siguientes siete preguntas.- ¿Cuál es la función?, Lo que el usuario desea que el activo haga.
- ¿Cuál es la falla funcional?, Razones por las que deja de hacer lo que el usuario desea que haga.
- ¿Cuál es el modo de falla?, Que pudo causar la falla funcional.
- ¿Cuál es el efecto de la falla?, Que ocurre cuando la falla se produce.
- ¿Cuál es la consecuencia de la falla?, Razones por las que importa que falle.
- ¿Qué se puede hacer para evitar o minimizar la consecuencia de la falla?
- ¿Qué se hace si no se encuentra ninguna tarea para evitar o minimizar la consecuencia de la falla?
6 pasos para realizar un programa de mantenimiento centrado en la confiabilidad
Existe una gran variedad y métodos diversos en las aplicaciones del RCM. Entonces, la mayoría de los programas aplican los siguientes seis pasos como punto de partida para implementar un plan RCM.Paso 1: Seleccionar un análisis RCM de activos.
Primero, se debe elegir un activo sobre el que realizar el análisis RCM. Algunos factores a tener en cuenta son:- el grado de criticidad del activo para las operaciones,
- sus costes de reparación en el pasado,
- los costes de mantenimiento preventivo anteriores.
Cursos recomendados


En línea en vivo5 de julio


En línea en vivo5 de julio


En línea en vivo9 de agosto
%252FImagen%252FRAMPREDYC-1730060420837.webp%3Falt%3Dmedia%26token%3D2634a7f0-988e-4022-b91f-382503e6e9db&w=3840&q=75)

En línea en vivo1 de noviembre
Paso 2: Describir las funciones del sistema para el activo seleccionado.
Es importante conocer las funciones del sistema, incluidas sus entradas y salidas, por pequeñas que sean. Por ejemplo, las entradas de una cinta transportadora son las mercancías y la energía mecánica que impulsa la cinta.Paso 3: Definir los modos de fallo.
Comprender las diferentes formas en que puede fallar el sistema. Por ejemplo, la cinta transportadora puede transportar la mercancía con la suficiente rapidez o no transportarla por completo de un extremo a otro.Paso 4: Evaluar las consecuencias del fallo.
El fallo de un activo puede dar lugar a problemas de seguridad y a un mal rendimiento de la empresa. También, puede afectar a otros equipos. Los operarios de la planta, los expertos en equipos y los técnicos de mantenimiento deben trabajar juntos para identificar las causas fundamentales de los fallos de cada activo. Este proceso ayuda a determinar cómo priorizar las tareas.Paso 5: Determinar una estrategia de mantenimiento para cada modo de fallo.
Aquí, se selecciona una estrategia de mantenimiento para cada modo de fallo crítico. Debe ser factible tanto económica como técnicamente. Puedes utilizar el mantenimiento basado en la condición o CBM, el mantenimiento preventivo o el mantenimiento predictivo. En caso de no poder aplicar una estrategia determinada para un modo de fallo concreto, se considera la posibilidad de rediseñar el sistema para modificar o eliminar el modo de fallo.Paso 6: Aplicar la estrategia y realizar revisiones periódicas al programa RCM.
Para que un programa de RCM sea eficiente, es necesario poner en práctica las recomendaciones de mantenimiento identificadas en el paso 5. Luego, tras la aplicación, las revisiones periódicas ayudan a mejorar los sistemas y el rendimiento.Herramientas para aplicar un programa RCM
Las herramientas fundamentales para el desarrollo del proceso de análisis del RCM, son:- La Hoja de análisis y registro: también es conocida como FMECA. Está constituida para la una secciona de análisis de las funciones, fallas y efectos y otra sección, de registro de consecuencias y decisiones.
- El Diagrame de Decisiones: proporciona la base para decidir “si merece la pena realizar” una acción de manteniendo o una acción “a falta de”, en función de las consecuencias y de acuerdo a la naturaleza de la falla. Es decir, si puede ser prevenida o no.
¿Cómo seleccionar el tipo de mantenimiento adecuado?
En el RCM, la selección de políticas de mantenimiento está gobernada por la categoría de consecuencias a la que pertenece la falla.- Para fallas con consecuencias ocultas, la tarea optima es aquella que consigue la disponibilidad requerida del dispositivo de protección.
- Para fallas con consecuencias de seguridad o medio ambiente, la tarea optima es aquella que consigue reducir la probabilidad de la falla hasta un nivel tolerable.
- Para fallas con consecuencias económicas (operacionales y no operacionales), la tarea optima es aquella que minimiza los costos totales para la organización.
Dinos qué te ha parecido el artículo
Artículos recomendados
Efecto del desalineamiento y desbalance de maquinaria en la eficiencia energética

Autor: Predictiva 21La revista digital de Mantenimiento, Confiabilidad y Gestión de Activos.
Auditoría de mantenimiento: mejora la gestión del mantenimiento

Autor: Predictiva 21La revista digital de Mantenimiento, Confiabilidad y Gestión de Activos.
El papel de un Consultor o un consultor de papel

Autor: Predictiva 21La revista digital de Mantenimiento, Confiabilidad y Gestión de Activos.
Metodología para estudiar la factibilidad de cogeneración eléctrica en turbinas a gas

Autor: Predictiva 21La revista digital de Mantenimiento, Confiabilidad y Gestión de Activos.
Publica tu artículo en la revista #1 de Mantenimiento Industrial
Publicar un artículo en la revista es gratis, no tiene costo.
Solo debes asegurarte que no sea un artículo comercial.
¿Qué esperas?
O envía tu artículo directo: articulos@predictiva21.com
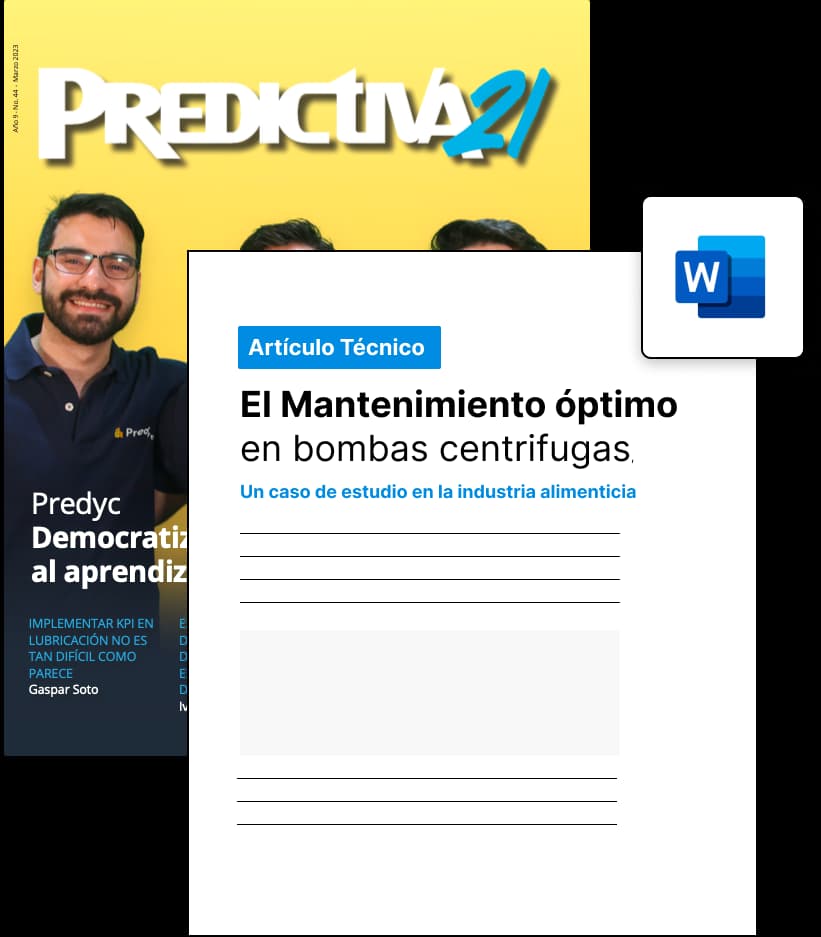