SMED: Estrategia que contribuye al éxito en labores de Mantenimiento
Articulo11 de junio de 2019
SMED es el acrónico de “Single Minutes Exchange of Dies” que traduce: “pequeños minutos en el intercambio de piezas o moldes. También, cambio de piezas en menos de diez minutos”. Esta metodología de trabajo fue desarrollada por el ingeniero industrial Shingeo Shingo en los años 70.
Este ingeniero japonés fue uno de los líderes en las prácticas de manufactura en el sistema de producción de Toyota. Se le acuña el haber creado el Cero Control de Calidad y el Poka Yoke (a prueba de errores). Shingeo refuerzas todos los procesos basándose en las herramientas de Ingeniería Industrial tales como: Ingeniería de Métodos, Medición del trabajo y Estudios del Trabajo, para sacar el máximo provecho y reducir los tiempos fuera de servicio (T.F.S) de las máquinas.
Si bien es cierto que Shingeo se concentró en aplicar estas herramientas al proceso de manufactura de producción en línea, también es muy cierto que podemos aprovecharlo para reforzar el Mantenimiento en una planta con la finalidad de reducir los tiempos de intervención para actividades de ejecución, aumentando de esta manera la disponibilidad y confiabilidad de los activos. SMED es considerado una revolución en la manufactura de los procesos en línea, sin embargo, no todo queda allí, poco a poco sin saberlo los buenos mantenedores han estado en la búsqueda permanente de estrategias que les permitan reducir cada día los tiempos fuera de servicio ya sean para mantenimiento preventivo como para preventivo, que son las dos únicas actividades que restablecen la condición operacional de los activos.
Quizás muchas personas no coincidan conmigo con esta afirmación que hago, debido a que nunca he considerado el mantenimiento predictivo como un mantenimiento en el propio sentido de la palabra. Siempre he considerado la actividad predictiva como una intervención de monitoreo, porque en ningún momento mejora la condición operacional del equipo, tan solo nos dice “en que situación está el equipo”. Como bien lo decimos, son inspecciones que hacemos para tomar decisiones de parar o dejar operando el equipo hasta una próxima parada más conveniente.
Volviendo al tema en cuestión, SMED, podemos fácilmente utilizarlo como una estrategia de trabajo que nos permita contribuir a ser más exitosos en las labores de mantenimiento. Significa analizar todo el flujo de mantenimiento al momento de la presencia de una falla o de una intervención preventiva. Al igual que lo hace sencillamente el SMED durante el proceso de manufactura, en la cual comienzan con hacer un video de todas las actividades separando las operaciones internas como externas, midiendo sus tiempos en cada una de sus fases y analizando sus dificultades y atrasos, podemos igualmente aplicar esta metodología a una intervención cualquiera; y donde también una buena Planificación y Programación son fundamentales, para dar respuestas acertadas y oportuna a las interrogantes que en ellas encontramos: Qué hacer, Cómo Hacerlo, Con qué hacerlos, Con quién hacerlo, Con cuáles herramientas de apoyo, en cuánto tiempo, etc.
Para aclarar con mayor profundidad lo que quiero decir, traigo como ejemplo un caso de estudio, que consistió en el cambio de un sello en un cilindro hidráulico de la tapa de un horno de fundición de chatarra, materia prima para producir briquetas. En su momento uno de estos tres cilindros presentaba fugas, condición que obligó a repararlo inmediatamente. En ese entonces anotamos todo lo que se hacía, hasta la más mínima operación en cuanto a requerimientos de: maniobras, herramientas, materiales y equipos de soporte, seguridad, etc.
Era la primera vez que se ejecutaba el trabajo. Para esa intervención el Tiempo Fuera de Servicio fue de casi tres turnos. Posteriormente, un poco mas de un mes se dañó un cilindro por la misma causa en un horno similar, inmediatamente, ubicamos la información que teníamos del cilindro anterior reparado, la cual aún estaba de manera manual en un cuaderno y se logró reducir el tiempo de intervención a menos de dos turnos de trabajo. Sin saberlo estábamos utilizando de alguna manera algo de SMED porque aun cuando no fue en pocos minutos que se hizo el trabajo y como lo caracteriza esta metodología, lo hicimos muy rápido.
Esta metodología contribuyó para que en el otro horno se construyeran modificaciones que permitían para algunas maniobras, realizarlas en pocos minutos. Para ese entonces me desempeñaba como consultor en esa planta de acería. Que quiero decir con esto. Que sencillamente, si nosotros tenemos procedimientos probados, claros y sencillos que indiquen qué herramientas y equipos requerimos, qué materiales, partes y repuestos son necesarios, con cuáles condiciones de seguridad, el personal y cantidad que se necesita, los soportes escritos, planos, guías, manuales; y muy importante, “modificaciones para mejorar las maniobras a través de SMED”; sin tener duda a equivocarme, estamos en el camino correcto de llevar a buen término una intervención cualquiera por complicada que ésta sea. Y de qué estamos hablando, sencillamente de “SMED”
SMED es una metodología que busca como lo dije anteriormente, que cuando hagamos una maniobra cualquiera para cambiar una pieza, molde, troquel, o simplemente cambiar un componente se haga en pocos minutos. A continuación, les dejo un ejemplo de lo que es el resultado de un trabajo SMED para reducir el tiempo de desmontaje de una brida ciega en una tubería.
Autor: M.Sc Brau Clemenza Consultor
Conferencista y Articulista
www.sistemademantenimento.com
Dinos qué te ha parecido el artículo
Artículos recomendados
La Ingeniería Industrial - ¡Conócela!

La planificación de mantenimiento de trabajo: el primer paso

El Tiempo no Perdona

Evitar los errores humanos en los procesos productivos con el Análisis de Causa Raíz (ACR)

Publica tu artículo en la revista #1 de Mantenimiento Industrial
Publicar un artículo en la revista es gratis, no tiene costo.
Solo debes asegurarte que no sea un artículo comercial.
¿Qué esperas?
O envía tu artículo directo: articulos@predictiva21.com
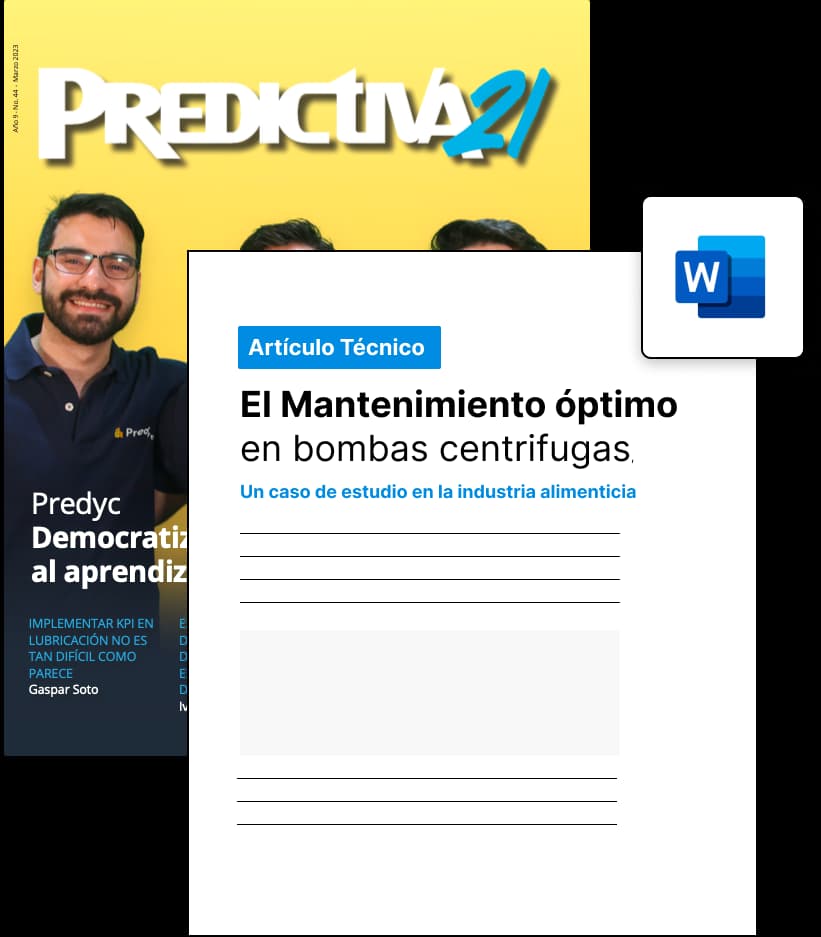
SMED: Estrategia que contribuye al éxito en labores de Mantenimiento
Articulo 11 de junio de 2019SMED es el acrónico de “Single Minutes Exchange of Dies” que traduce: “pequeños minutos en el intercambio de piezas o moldes. También, cambio de piezas en menos de diez minutos”. Esta metodología de trabajo fue desarrollada por el ingeniero industrial Shingeo Shingo en los años 70.
Este ingeniero japonés fue uno de los líderes en las prácticas de manufactura en el sistema de producción de Toyota. Se le acuña el haber creado el Cero Control de Calidad y el Poka Yoke (a prueba de errores). Shingeo refuerzas todos los procesos basándose en las herramientas de Ingeniería Industrial tales como: Ingeniería de Métodos, Medición del trabajo y Estudios del Trabajo, para sacar el máximo provecho y reducir los tiempos fuera de servicio (T.F.S) de las máquinas.
Si bien es cierto que Shingeo se concentró en aplicar estas herramientas al proceso de manufactura de producción en línea, también es muy cierto que podemos aprovecharlo para reforzar el Mantenimiento en una planta con la finalidad de reducir los tiempos de intervención para actividades de ejecución, aumentando de esta manera la disponibilidad y confiabilidad de los activos. SMED es considerado una revolución en la manufactura de los procesos en línea, sin embargo, no todo queda allí, poco a poco sin saberlo los buenos mantenedores han estado en la búsqueda permanente de estrategias que les permitan reducir cada día los tiempos fuera de servicio ya sean para mantenimiento preventivo como para preventivo, que son las dos únicas actividades que restablecen la condición operacional de los activos.
Quizás muchas personas no coincidan conmigo con esta afirmación que hago, debido a que nunca he considerado el mantenimiento predictivo como un mantenimiento en el propio sentido de la palabra. Siempre he considerado la actividad predictiva como una intervención de monitoreo, porque en ningún momento mejora la condición operacional del equipo, tan solo nos dice “en que situación está el equipo”. Como bien lo decimos, son inspecciones que hacemos para tomar decisiones de parar o dejar operando el equipo hasta una próxima parada más conveniente.
Volviendo al tema en cuestión, SMED, podemos fácilmente utilizarlo como una estrategia de trabajo que nos permita contribuir a ser más exitosos en las labores de mantenimiento. Significa analizar todo el flujo de mantenimiento al momento de la presencia de una falla o de una intervención preventiva. Al igual que lo hace sencillamente el SMED durante el proceso de manufactura, en la cual comienzan con hacer un video de todas las actividades separando las operaciones internas como externas, midiendo sus tiempos en cada una de sus fases y analizando sus dificultades y atrasos, podemos igualmente aplicar esta metodología a una intervención cualquiera; y donde también una buena Planificación y Programación son fundamentales, para dar respuestas acertadas y oportuna a las interrogantes que en ellas encontramos: Qué hacer, Cómo Hacerlo, Con qué hacerlos, Con quién hacerlo, Con cuáles herramientas de apoyo, en cuánto tiempo, etc.
Para aclarar con mayor profundidad lo que quiero decir, traigo como ejemplo un caso de estudio, que consistió en el cambio de un sello en un cilindro hidráulico de la tapa de un horno de fundición de chatarra, materia prima para producir briquetas. En su momento uno de estos tres cilindros presentaba fugas, condición que obligó a repararlo inmediatamente. En ese entonces anotamos todo lo que se hacía, hasta la más mínima operación en cuanto a requerimientos de: maniobras, herramientas, materiales y equipos de soporte, seguridad, etc.
Era la primera vez que se ejecutaba el trabajo. Para esa intervención el Tiempo Fuera de Servicio fue de casi tres turnos. Posteriormente, un poco mas de un mes se dañó un cilindro por la misma causa en un horno similar, inmediatamente, ubicamos la información que teníamos del cilindro anterior reparado, la cual aún estaba de manera manual en un cuaderno y se logró reducir el tiempo de intervención a menos de dos turnos de trabajo. Sin saberlo estábamos utilizando de alguna manera algo de SMED porque aun cuando no fue en pocos minutos que se hizo el trabajo y como lo caracteriza esta metodología, lo hicimos muy rápido.
Esta metodología contribuyó para que en el otro horno se construyeran modificaciones que permitían para algunas maniobras, realizarlas en pocos minutos. Para ese entonces me desempeñaba como consultor en esa planta de acería. Que quiero decir con esto. Que sencillamente, si nosotros tenemos procedimientos probados, claros y sencillos que indiquen qué herramientas y equipos requerimos, qué materiales, partes y repuestos son necesarios, con cuáles condiciones de seguridad, el personal y cantidad que se necesita, los soportes escritos, planos, guías, manuales; y muy importante, “modificaciones para mejorar las maniobras a través de SMED”; sin tener duda a equivocarme, estamos en el camino correcto de llevar a buen término una intervención cualquiera por complicada que ésta sea. Y de qué estamos hablando, sencillamente de “SMED”
SMED es una metodología que busca como lo dije anteriormente, que cuando hagamos una maniobra cualquiera para cambiar una pieza, molde, troquel, o simplemente cambiar un componente se haga en pocos minutos. A continuación, les dejo un ejemplo de lo que es el resultado de un trabajo SMED para reducir el tiempo de desmontaje de una brida ciega en una tubería.
Autor: M.Sc Brau Clemenza Consultor
Conferencista y Articulista
www.sistemademantenimento.com
Dinos qué te ha parecido el artículo
Artículos recomendados
Proceso de evaporación de petróleo y sus derivados en tanques de almacenamiento

Mantenimiento Reactivo

Detección temperatura anormal por daños en el asiento de la válvula compresora interna de cuarta etapa, compresor dresser rand

Pilar I - Lubricación de Precisión Techgnosis: Selección del tipo de aceite y cálculo de viscosidad para lubricación de engranajes industriales sometidos a alta carga

Publica tu artículo en la revista #1 de Mantenimiento Industrial
Publicar un artículo en la revista es gratis, no tiene costo.
Solo debes asegurarte que no sea un artículo comercial.
¿Qué esperas?
O envía tu artículo directo: articulos@predictiva21.com
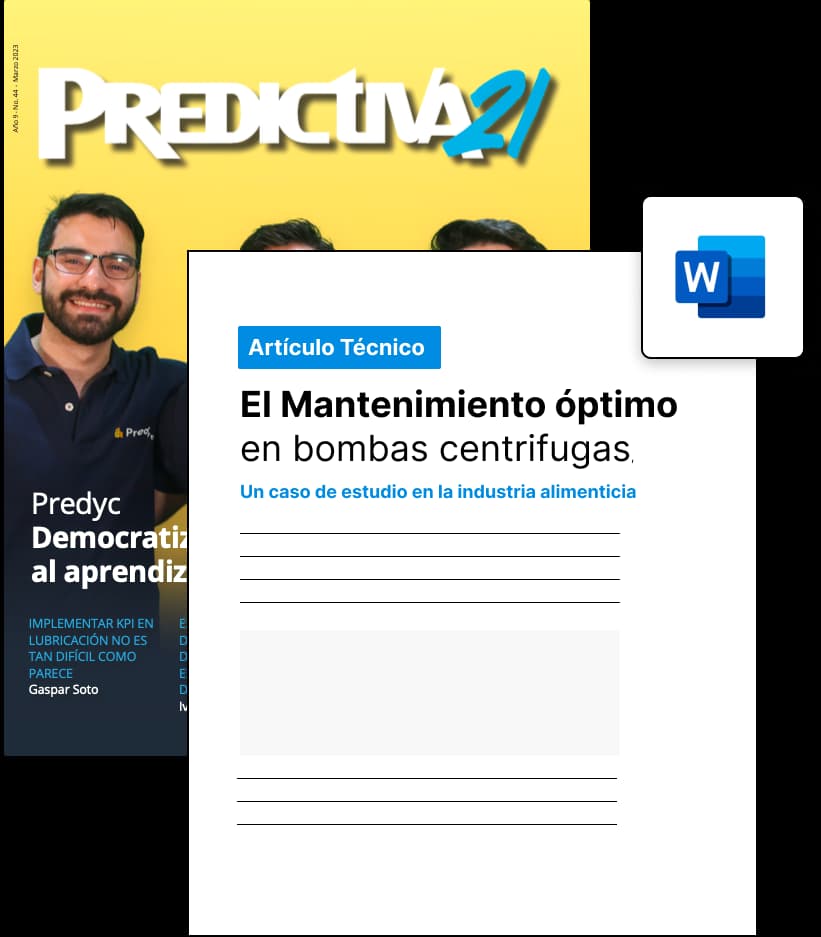