La Otra Visión de la Confiabilidad Operacional
Articulo7 de abril de 2025
¡DESAFÍA LOS DEFECTOS Y OPTIMIZA TUS ACTIVOS! ESTRATEGIAS INNOVADORAS PARA LA ELIMINACIÓN DE DEFECTOS EN PROGRAMAS DE MANTENIMIENTO
En virtud de hacer extensiva La Otra Visión de la Confiabilidad Operacional, desde una perspectiva simplista y de fácil comprensión para el lector, les presento una manera práctica y sencilla de abordar un Proceso de Eliminación de Defectos en Activos de Producción y vincularlo a la Confiabilidad Operacional.
¿Te enfrentas a desafíos constantes debido a defectos en tus activos? ¡No estás solo! En este artículo, te mostraremos cómo superar estos obstáculos y llevar tu operación al siguiente nivel. Con ejemplos inspiradores y consejos prácticos, te invitamos a embarcarte en un viaje hacia la eliminación de defectos y la optimización de tus activos.
La eliminación de defectos en activos dentro de un programa de mantenimiento es fundamental para garantizar la eficiencia operativa y la sostenibilidad empresarial. Sin embargo, este proceso no está exento de desafíos, especialmente cuando se considera la complejidad de las operaciones y la participación de personas en todos los niveles de la organización.
En este artículo, se examinará la naturaleza de los defectos, sus consecuencias y las estrategias necesarias para abordarlos de manera efectiva, cuya finalidad radica en mejorar la rentabilidad de los procesos productivos. Es importante entender que, cada día, se dedican enormes esfuerzos a visualizar, identificar, analizar e implantar mejores prácticas operacionales para la solución de problemas y la toma de decisiones efectivas y acertadas, que involucren un alto impacto en las áreas operativas de una empresa.
De este modo, la actividad empresarial se acompaña esencialmente de la incertidumbre, lo que predetermina la necesidad de elegir entre diferentes alternativas para la eliminación de defectos, teniendo en cuenta las metodologías de confiabilidad operacional.
Palabras clave: Eliminación de defectos, confiabilidad operacional, criticidad, frecuencia de falla, taxonomía, contexto operacional.
Un Proceso de Eliminación de Defectos desde la Perspectiva de ISO 55000
Integra un enfoque sistemático basado en riesgos para la gestión de activos, con el objetivo de optimizar el desempeño y el valor de estos a lo largo de su ciclo de vida y así garantizar la sostenibilidad, considerando como mínimo lo siguiente:
- Gestión integral de activos
- Mejora continua
- Enfoque basado en riesgos
- Énfasis en la sostenibilidad
Participación de las partes interesadas
(Jean Farfán)
Un Proceso de Eliminación de Defectos orientado a la óptica de la Confiabilidad Operacional y la IA, puede resumirse en lo siguiente: prevención proactiva, análisis de causa raíz, mejora continua, uso de datos, participación del personal, big data e internet de las cosas como herramientas integradas en la identificación de problemas y planteamiento de soluciones basadas en datos.
En resumen, la IA no solo ayuda a eliminar defectos, sino que también contribuye a la confiabilidad operacional al prevenir problemas y optimizar procesos. Integrarla a la estrategia de mantenimiento es esencial para garantizar la confiabilidad de los activos a lo largo de su ciclo de vida.
(Jean Farfán)
Activo: Es un artículo, cosa o entidad que tiene un valor potencial o real para una organización. El valor puede ser tangible o intangible, financiero o no financiero.
Fuente: ISO 55000 3.2.1
Instalación: Conjunto de activos destinados a manejar un proceso de acuerdo con la unidad de negocio.
Ciclo de vida del activo: Son todas las etapas definidas por la organización, que enmarcan la gestión de los activos físicos de la compañía desde su diseño conceptual hasta su disposición final.

Calidad de los datos:
La confianza en la confiabilidad y mantenimiento de los datos, así como en su análisis, tiene una estrecha dependencia en la calidad de los datos recolectados. Una información de alta calidad se caracteriza por:
- Tener informes completos de los datos en relación con sus especificaciones.
- Acatar las definiciones de confiabilidad en los parámetros, tipos de datos y formatos.
Precisión en la introducción, transferencia, manejo y almacenamiento de los datos (ya sea en forma manual o a través de mecanismos electrónicos).
Confiabilidad Operacional:
Es la filosofía de trabajo orientada en una serie de procesos de mejora continua, que incorporan de forma sistemática herramientas de diagnóstico, metodologías de análisis y nuevas tecnologías para optimizar la gestión, planeación, ejecución y control de la productividad. Además, lleva implícita la capacidad de una instalación (procesos, tecnología, personas) para cumplir su función o el propósito que se espera de ella, dentro de sus límites de diseño y bajo un contexto operacional específico.
Contexto Operacional:
Es el conjunto de circunstancias que condicionan la operación de un equipo o sistema. Estas están definidas por: localidad, ambiente, fluido de servicio, parámetros de operación, lineamientos ambientales, de seguridad y producción, calidad y disponibilidad de los insumos requeridos, configuración de trabajo, flexibilidad operacional, redundancia, alarmas, monitoreo de primera línea, entre otros.
Falla:
Es la pérdida de capacidad para realizar su función según se requiera.
Falla por Degradación:
Falla que no cesa la(s) función(es) fundamentales, pero afecta una o varias de ellas.
Fuente: ISO 14224 3.11
Falla Incipiente:
Imperfección en el estado o condición de un ítem que puede causar que una falla degradada o crítica ocurra eventualmente si no se realizan acciones correctivas.
Fuente: ISO 14224 3.40
Falla Latente o Falla No Detectada:
Es una falla que aún no se ha hecho evidente. Puede ser revelada mediante el mantenimiento preventivo o al producirse una falla del sistema.
Fuente: ISO 14224 3.44
Falla Oculta:
Falla que no es inmediatamente evidente para el personal de operaciones y/o mantenimiento.
Fuente: ISO 14224 3.35
Mecanismo de Falla:
Proceso físico, químico u otro que conduce a una falla.
Fuente: ISO 14224 3.29
Modo de Falla:
Forma en la que una falla es observada en el elemento que ha fallado.
Fuente: ISO 14224 3.30
Cursos recomendados
%252FImagen%252Frcm-1730083250826.webp%3Falt%3Dmedia%26token%3D3775356a-7b11-4c44-b21f-45b3409fb9ed&w=3840&q=75)



%252FImagen%252FRAMPREDYC-1730060420837.webp%3Falt%3Dmedia%26token%3D2634a7f0-988e-4022-b91f-382503e6e9db&w=3840&q=75)



Taxonomía:
Es una clasificación sistemática de los activos en grupos genéricos, sobre la base de factores comunes a varios de los ítems dentro de un activo, tales como: ubicación, uso, equipos y su subdivisión, componentes y listas de materiales.
Figura N°2. Pirámide de Niveles Taxonómicos
Fuente: Petróleos de Venezuela (2012), Norma MM-01-01-07

Pasos Básicos a Considerar Durante el Levantamiento del Proceso de Eliminación de Defectos
- Utilizar el Contexto Operacional para identificar el proceso y su funcionamiento.
- Evaluar el entorno en el que se encuentra el activo.
- Definir los límites, términos y requerimientos necesarios para llevar a cabo el proceso de eliminación de defectos y fallas en activos, monitorear la corrección de modos de falla y anomalías, con el fin de preservar su continuidad operativa y aumentar la confiabilidad.
Identificar, valorizar, definir, investigar, hacer seguimiento y controlar la eliminación de defectos y causas de falla en:
a) Incidentes en seguridad de procesos
b) Incidentes que afecten a personas, el ambiente o la propiedad
c) Fallas o averías esporádicas sobre activos productivos
d) Fallas o averías recurrentes sobre activos productivos

¿Cómo se integra la gestión del mantenimiento en la industria alineada al proceso de eliminación de defectos?
La gestión del mantenimiento en la industria es una tarea crítica para asegurar el éxito de la producción, la calidad y la mejora continua de los procesos. Ha identificado en los activos los elementos esenciales para mantener una operación eficiente y eficaz.
En este sentido, el proceso de eliminación de defectos forma parte de las herramientas estratégicas utilizadas en las industrias para reducir costos en los activos e incrementar sus niveles de confiabilidad y la rentabilidad del negocio. Este proceso implica una revisión sistemática y continua de los eventos de falla que puedan llegar a materializarse u ocurran durante cada etapa del ciclo de vida de los activos.
La aplicación de técnicas proactivas de confiabilidad desde la fase de diseño busca garantizar que el activo, en toda su vida útil hasta su desincorporación, cuente con herramientas que permitan gestionarlo de manera eficiente. Dentro de estas metodologías podemos mencionar: PMO, MCC, RCM, FMEA, RAM, criticidad y su vinculación con técnicas de investigación de fallas e incidentes, tales como: RCA, TapRooT, entre otras; las cuales buscan identificar, caracterizar, analizar y mitigar a su mínima expresión las causas fundamentales de las fallas o defectos.
El proceso de eliminación de defectos se enfoca en mejorar la confiabilidad y la continuidad operativa de los activos, lo que garantiza una mayor disponibilidad y rendimiento, reduciendo así los costos de operación, mantenimiento y reemplazo de activos.
Esta tarea involucra a múltiples departamentos y áreas de una empresa, como ingeniería, mantenimiento, producción y seguridad, entre otros, para asegurar una visión integral del proceso. La implementación de medidas preventivas, como inspecciones y mantenimiento programado, es una parte fundamental del proceso de eliminación de defectos, ya que permite anticipar posibles fallas y evitar interrupciones en la producción.
¿Cómo alinear el proceso de eliminación de defectos al ciclo PHVA?
El fundamento principal de un adecuado proceso de eliminación de defectos debe estar soportado bajo un esquema integrado del sistema de calidad de la empresa, detallando los documentos principales, así como la descripción de las diferentes técnicas a utilizar. A continuación, se plantea un modelo básico del esquema documental.

En este sentido, las empresas asumen un compromiso inmenso con la mejora continua en la gestión del activo, desde su fase de visualización hasta su desincorporación, lo que se traducirá en una operación más rentable y exitosa, al asegurar la confiabilidad y disponibilidad de estos.
¿Cómo jerarquizar las acciones de eliminación de defectos?
Con el fin de determinar la categoría a la que pertenece la tarea (acción o recomendación), se debe generar una matriz de selección y clasificación de acciones. Como por ejemplo:

El recuadro I corresponde a las tareas que, al implementarlas, eliminarían el defecto y cuyo costo o tiempo de implementación es bajo. Las actividades que queden enmarcadas en esta posición se deben categorizar como acciones.
El recuadro II corresponde a las tareas que, al implementarlas, eliminarían el defecto, pero el costo o tiempo de implementación es elevado. Estas tareas solo se categorizarán como recomendación.
El recuadro III corresponde a las tareas que, al implementarlas, no eliminan el defecto y tienen un costo bajo de implementación. El equipo de investigación debe determinar si se categorizan como recomendaciones.
El recuadro IV corresponde a tareas que, al implementarlas, no eliminan el defecto y tienen un costo alto de implementación. Se categorizan como recomendaciones.
Esta clasificación se debe definir en los documentos del proceso de eliminación de defectos.
¿Cómo verifico la efectividad de las acciones o recomendaciones de la eliminación de defectos?
La verificación de la efectividad de las acciones puede ser reportada trimestralmente por el ente ejecutor a la gerencia de Mantenimiento o al encargado del proceso, los cuales recomiendan los siguientes pasos:
a) Identificar paquetes de solución finalizados: se revisan los paquetes ejecutados y que hayan eliminado el defecto. En caso de desviaciones, se deben solicitar los ajustes al responsable de la acción.
b) Definir período de evaluación: de manera conjunta se define el período de evaluación de la efectividad, tomando como referencia el objetivo del tiempo medio entre fallas del modo de falla a eliminar.
¿Es posible implementar un proceso de eliminación de defectos?
La eliminación de defectos en activos no solo es posible, ¡sino también emocionante! Con la combinación adecuada de estrategias y herramientas, puedes transformar tu operación y alcanzar nuevos niveles de éxito. ¡Así que adelante, desafía los defectos y optimiza tus activos hoy mismo!
En resumen, el concepto universal de eliminación de defectos desde la óptica de la confiabilidad se basa en la prevención proactiva, el análisis de causas raíz, la mejora continua, el uso de datos y la participación del personal para garantizar la confiabilidad y disponibilidad de los activos y procesos en toda la organización.
Bibliografía
- Petróleos de Venezuela, Norma MM-01-01-01: Definiciones de Mantenimiento y Confiabilidad
- ISO 14224:2016
- Petróleos de Venezuela, Norma PDVSA MM-02-01-01: Jerarquización de Activos por Análisis de Criticidad
- La Serie de Normas ISO 55000, Herramienta para la Gestión de Activos – Víctor D. Manríquez, Ingeniero Mecánico, CMRP, MSc Energías Renovables, Ingeniero de Confiabilidad – Stork Perú SAC
- Fundamentos de la Gestión de Activos ISO 55001:2014 (Parte 1)
- Maintenance and Reliability Best Practices, Ramesh Gulati
- Reliability-Centered Maintenance, John Moubray
- Asset Management: A Systematic Approach to Factorial Improvement, David Greenwood
- Comité Técnico ISO/TC 251 sobre Gestión de Activos
Resumen laboral del autor
Ingeniero en Mantenimiento Mecánico con 18 años de experiencia.
Área profesional: Confiabilidad operacional, mantenimiento, sistema integrado de gestión y transporte terrestre, en la industria petrolera (PDVSA). Experiencia con PDVSA INTEVEP para la elaboración, revisión y actualización de normas PDVSA, tales como:
- Modelo de gerencia de mantenimiento
- Definiciones de mantenimiento y confiabilidad
- Niveles de mantenimiento
- Estructura de activos (jerarquización de sistemas y taxonomía de equipos en PDVSA)
- Guía para definir la estructura de activos en PDVSA
- Indicadores de gestión del proceso de mantenimiento
Estudios:
- Especialización en Finanzas
- Diplomado en Gerencia de Mantenimiento Industrial
- Diplomado en Análisis Probabilístico de Riesgos en Proyectos de Exploración y Producción
- Especialización en Ingeniería de Mantenimiento
- Correo electrónico: ljmfl7788@gmail.com
- Contacto móvil: +58 424 9431320
Dinos qué te ha parecido el artículo
Artículos recomendados
¿Cómo lograr una carrera exitosa como ingeniero de confiabilidad?

Confiabilidad Aplicada

Aplicación del estándar API 650 a un activo físico instalado en la industria petroquímica: Caso de estudio basado en el Apéndice “F”

Alexis Lárez: Manager de Mantenimiento AEM 2020 - Rumbo al European Maintenance Manager Award EMMA 2021

Publica tu artículo en la revista #1 de Mantenimiento Industrial
Publicar un artículo en la revista es gratis, no tiene costo.
Solo debes asegurarte que no sea un artículo comercial.
¿Qué esperas?
O envía tu artículo directo: articulos@predictiva21.com
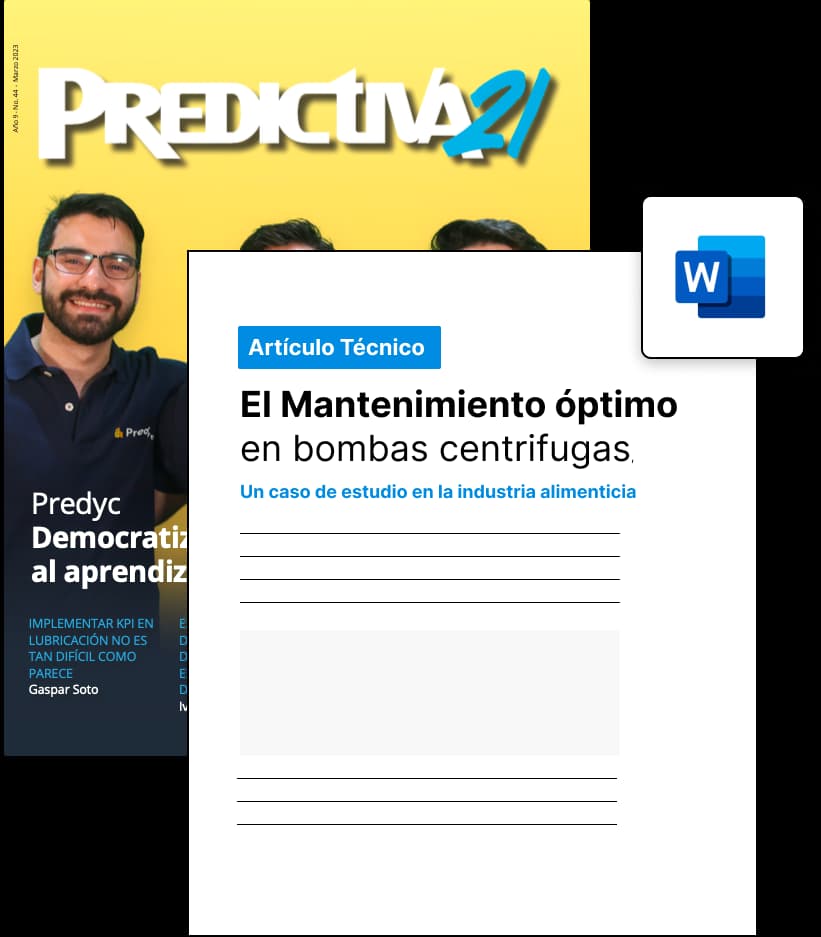
La Otra Visión de la Confiabilidad Operacional
Articulo 7 de abril de 2025¡DESAFÍA LOS DEFECTOS Y OPTIMIZA TUS ACTIVOS! ESTRATEGIAS INNOVADORAS PARA LA ELIMINACIÓN DE DEFECTOS EN PROGRAMAS DE MANTENIMIENTO
En virtud de hacer extensiva La Otra Visión de la Confiabilidad Operacional, desde una perspectiva simplista y de fácil comprensión para el lector, les presento una manera práctica y sencilla de abordar un Proceso de Eliminación de Defectos en Activos de Producción y vincularlo a la Confiabilidad Operacional.
¿Te enfrentas a desafíos constantes debido a defectos en tus activos? ¡No estás solo! En este artículo, te mostraremos cómo superar estos obstáculos y llevar tu operación al siguiente nivel. Con ejemplos inspiradores y consejos prácticos, te invitamos a embarcarte en un viaje hacia la eliminación de defectos y la optimización de tus activos.
La eliminación de defectos en activos dentro de un programa de mantenimiento es fundamental para garantizar la eficiencia operativa y la sostenibilidad empresarial. Sin embargo, este proceso no está exento de desafíos, especialmente cuando se considera la complejidad de las operaciones y la participación de personas en todos los niveles de la organización.
En este artículo, se examinará la naturaleza de los defectos, sus consecuencias y las estrategias necesarias para abordarlos de manera efectiva, cuya finalidad radica en mejorar la rentabilidad de los procesos productivos. Es importante entender que, cada día, se dedican enormes esfuerzos a visualizar, identificar, analizar e implantar mejores prácticas operacionales para la solución de problemas y la toma de decisiones efectivas y acertadas, que involucren un alto impacto en las áreas operativas de una empresa.
De este modo, la actividad empresarial se acompaña esencialmente de la incertidumbre, lo que predetermina la necesidad de elegir entre diferentes alternativas para la eliminación de defectos, teniendo en cuenta las metodologías de confiabilidad operacional.
Palabras clave: Eliminación de defectos, confiabilidad operacional, criticidad, frecuencia de falla, taxonomía, contexto operacional.
Un Proceso de Eliminación de Defectos desde la Perspectiva de ISO 55000
Integra un enfoque sistemático basado en riesgos para la gestión de activos, con el objetivo de optimizar el desempeño y el valor de estos a lo largo de su ciclo de vida y así garantizar la sostenibilidad, considerando como mínimo lo siguiente:
- Gestión integral de activos
- Mejora continua
- Enfoque basado en riesgos
- Énfasis en la sostenibilidad
Participación de las partes interesadas
(Jean Farfán)
Un Proceso de Eliminación de Defectos orientado a la óptica de la Confiabilidad Operacional y la IA, puede resumirse en lo siguiente: prevención proactiva, análisis de causa raíz, mejora continua, uso de datos, participación del personal, big data e internet de las cosas como herramientas integradas en la identificación de problemas y planteamiento de soluciones basadas en datos.
En resumen, la IA no solo ayuda a eliminar defectos, sino que también contribuye a la confiabilidad operacional al prevenir problemas y optimizar procesos. Integrarla a la estrategia de mantenimiento es esencial para garantizar la confiabilidad de los activos a lo largo de su ciclo de vida.
(Jean Farfán)
Activo: Es un artículo, cosa o entidad que tiene un valor potencial o real para una organización. El valor puede ser tangible o intangible, financiero o no financiero.
Fuente: ISO 55000 3.2.1
Instalación: Conjunto de activos destinados a manejar un proceso de acuerdo con la unidad de negocio.
Ciclo de vida del activo: Son todas las etapas definidas por la organización, que enmarcan la gestión de los activos físicos de la compañía desde su diseño conceptual hasta su disposición final.

Calidad de los datos:
La confianza en la confiabilidad y mantenimiento de los datos, así como en su análisis, tiene una estrecha dependencia en la calidad de los datos recolectados. Una información de alta calidad se caracteriza por:
- Tener informes completos de los datos en relación con sus especificaciones.
- Acatar las definiciones de confiabilidad en los parámetros, tipos de datos y formatos.
Precisión en la introducción, transferencia, manejo y almacenamiento de los datos (ya sea en forma manual o a través de mecanismos electrónicos).
Confiabilidad Operacional:
Es la filosofía de trabajo orientada en una serie de procesos de mejora continua, que incorporan de forma sistemática herramientas de diagnóstico, metodologías de análisis y nuevas tecnologías para optimizar la gestión, planeación, ejecución y control de la productividad. Además, lleva implícita la capacidad de una instalación (procesos, tecnología, personas) para cumplir su función o el propósito que se espera de ella, dentro de sus límites de diseño y bajo un contexto operacional específico.
Contexto Operacional:
Es el conjunto de circunstancias que condicionan la operación de un equipo o sistema. Estas están definidas por: localidad, ambiente, fluido de servicio, parámetros de operación, lineamientos ambientales, de seguridad y producción, calidad y disponibilidad de los insumos requeridos, configuración de trabajo, flexibilidad operacional, redundancia, alarmas, monitoreo de primera línea, entre otros.
Falla:
Es la pérdida de capacidad para realizar su función según se requiera.
Falla por Degradación:
Falla que no cesa la(s) función(es) fundamentales, pero afecta una o varias de ellas.
Fuente: ISO 14224 3.11
Falla Incipiente:
Imperfección en el estado o condición de un ítem que puede causar que una falla degradada o crítica ocurra eventualmente si no se realizan acciones correctivas.
Fuente: ISO 14224 3.40
Falla Latente o Falla No Detectada:
Es una falla que aún no se ha hecho evidente. Puede ser revelada mediante el mantenimiento preventivo o al producirse una falla del sistema.
Fuente: ISO 14224 3.44
Falla Oculta:
Falla que no es inmediatamente evidente para el personal de operaciones y/o mantenimiento.
Fuente: ISO 14224 3.35
Mecanismo de Falla:
Proceso físico, químico u otro que conduce a una falla.
Fuente: ISO 14224 3.29
Modo de Falla:
Forma en la que una falla es observada en el elemento que ha fallado.
Fuente: ISO 14224 3.30
Cursos recomendados
%252FImagen%252Frcm-1730083250826.webp%3Falt%3Dmedia%26token%3D3775356a-7b11-4c44-b21f-45b3409fb9ed&w=3840&q=75)



%252FImagen%252FRAMPREDYC-1730060420837.webp%3Falt%3Dmedia%26token%3D2634a7f0-988e-4022-b91f-382503e6e9db&w=3840&q=75)



Taxonomía:
Es una clasificación sistemática de los activos en grupos genéricos, sobre la base de factores comunes a varios de los ítems dentro de un activo, tales como: ubicación, uso, equipos y su subdivisión, componentes y listas de materiales.
Figura N°2. Pirámide de Niveles Taxonómicos
Fuente: Petróleos de Venezuela (2012), Norma MM-01-01-07

Pasos Básicos a Considerar Durante el Levantamiento del Proceso de Eliminación de Defectos
- Utilizar el Contexto Operacional para identificar el proceso y su funcionamiento.
- Evaluar el entorno en el que se encuentra el activo.
- Definir los límites, términos y requerimientos necesarios para llevar a cabo el proceso de eliminación de defectos y fallas en activos, monitorear la corrección de modos de falla y anomalías, con el fin de preservar su continuidad operativa y aumentar la confiabilidad.
Identificar, valorizar, definir, investigar, hacer seguimiento y controlar la eliminación de defectos y causas de falla en:
a) Incidentes en seguridad de procesos
b) Incidentes que afecten a personas, el ambiente o la propiedad
c) Fallas o averías esporádicas sobre activos productivos
d) Fallas o averías recurrentes sobre activos productivos

¿Cómo se integra la gestión del mantenimiento en la industria alineada al proceso de eliminación de defectos?
La gestión del mantenimiento en la industria es una tarea crítica para asegurar el éxito de la producción, la calidad y la mejora continua de los procesos. Ha identificado en los activos los elementos esenciales para mantener una operación eficiente y eficaz.
En este sentido, el proceso de eliminación de defectos forma parte de las herramientas estratégicas utilizadas en las industrias para reducir costos en los activos e incrementar sus niveles de confiabilidad y la rentabilidad del negocio. Este proceso implica una revisión sistemática y continua de los eventos de falla que puedan llegar a materializarse u ocurran durante cada etapa del ciclo de vida de los activos.
La aplicación de técnicas proactivas de confiabilidad desde la fase de diseño busca garantizar que el activo, en toda su vida útil hasta su desincorporación, cuente con herramientas que permitan gestionarlo de manera eficiente. Dentro de estas metodologías podemos mencionar: PMO, MCC, RCM, FMEA, RAM, criticidad y su vinculación con técnicas de investigación de fallas e incidentes, tales como: RCA, TapRooT, entre otras; las cuales buscan identificar, caracterizar, analizar y mitigar a su mínima expresión las causas fundamentales de las fallas o defectos.
El proceso de eliminación de defectos se enfoca en mejorar la confiabilidad y la continuidad operativa de los activos, lo que garantiza una mayor disponibilidad y rendimiento, reduciendo así los costos de operación, mantenimiento y reemplazo de activos.
Esta tarea involucra a múltiples departamentos y áreas de una empresa, como ingeniería, mantenimiento, producción y seguridad, entre otros, para asegurar una visión integral del proceso. La implementación de medidas preventivas, como inspecciones y mantenimiento programado, es una parte fundamental del proceso de eliminación de defectos, ya que permite anticipar posibles fallas y evitar interrupciones en la producción.
¿Cómo alinear el proceso de eliminación de defectos al ciclo PHVA?
El fundamento principal de un adecuado proceso de eliminación de defectos debe estar soportado bajo un esquema integrado del sistema de calidad de la empresa, detallando los documentos principales, así como la descripción de las diferentes técnicas a utilizar. A continuación, se plantea un modelo básico del esquema documental.

En este sentido, las empresas asumen un compromiso inmenso con la mejora continua en la gestión del activo, desde su fase de visualización hasta su desincorporación, lo que se traducirá en una operación más rentable y exitosa, al asegurar la confiabilidad y disponibilidad de estos.
¿Cómo jerarquizar las acciones de eliminación de defectos?
Con el fin de determinar la categoría a la que pertenece la tarea (acción o recomendación), se debe generar una matriz de selección y clasificación de acciones. Como por ejemplo:

El recuadro I corresponde a las tareas que, al implementarlas, eliminarían el defecto y cuyo costo o tiempo de implementación es bajo. Las actividades que queden enmarcadas en esta posición se deben categorizar como acciones.
El recuadro II corresponde a las tareas que, al implementarlas, eliminarían el defecto, pero el costo o tiempo de implementación es elevado. Estas tareas solo se categorizarán como recomendación.
El recuadro III corresponde a las tareas que, al implementarlas, no eliminan el defecto y tienen un costo bajo de implementación. El equipo de investigación debe determinar si se categorizan como recomendaciones.
El recuadro IV corresponde a tareas que, al implementarlas, no eliminan el defecto y tienen un costo alto de implementación. Se categorizan como recomendaciones.
Esta clasificación se debe definir en los documentos del proceso de eliminación de defectos.
¿Cómo verifico la efectividad de las acciones o recomendaciones de la eliminación de defectos?
La verificación de la efectividad de las acciones puede ser reportada trimestralmente por el ente ejecutor a la gerencia de Mantenimiento o al encargado del proceso, los cuales recomiendan los siguientes pasos:
a) Identificar paquetes de solución finalizados: se revisan los paquetes ejecutados y que hayan eliminado el defecto. En caso de desviaciones, se deben solicitar los ajustes al responsable de la acción.
b) Definir período de evaluación: de manera conjunta se define el período de evaluación de la efectividad, tomando como referencia el objetivo del tiempo medio entre fallas del modo de falla a eliminar.
¿Es posible implementar un proceso de eliminación de defectos?
La eliminación de defectos en activos no solo es posible, ¡sino también emocionante! Con la combinación adecuada de estrategias y herramientas, puedes transformar tu operación y alcanzar nuevos niveles de éxito. ¡Así que adelante, desafía los defectos y optimiza tus activos hoy mismo!
En resumen, el concepto universal de eliminación de defectos desde la óptica de la confiabilidad se basa en la prevención proactiva, el análisis de causas raíz, la mejora continua, el uso de datos y la participación del personal para garantizar la confiabilidad y disponibilidad de los activos y procesos en toda la organización.
Bibliografía
- Petróleos de Venezuela, Norma MM-01-01-01: Definiciones de Mantenimiento y Confiabilidad
- ISO 14224:2016
- Petróleos de Venezuela, Norma PDVSA MM-02-01-01: Jerarquización de Activos por Análisis de Criticidad
- La Serie de Normas ISO 55000, Herramienta para la Gestión de Activos – Víctor D. Manríquez, Ingeniero Mecánico, CMRP, MSc Energías Renovables, Ingeniero de Confiabilidad – Stork Perú SAC
- Fundamentos de la Gestión de Activos ISO 55001:2014 (Parte 1)
- Maintenance and Reliability Best Practices, Ramesh Gulati
- Reliability-Centered Maintenance, John Moubray
- Asset Management: A Systematic Approach to Factorial Improvement, David Greenwood
- Comité Técnico ISO/TC 251 sobre Gestión de Activos
Resumen laboral del autor
Ingeniero en Mantenimiento Mecánico con 18 años de experiencia.
Área profesional: Confiabilidad operacional, mantenimiento, sistema integrado de gestión y transporte terrestre, en la industria petrolera (PDVSA). Experiencia con PDVSA INTEVEP para la elaboración, revisión y actualización de normas PDVSA, tales como:
- Modelo de gerencia de mantenimiento
- Definiciones de mantenimiento y confiabilidad
- Niveles de mantenimiento
- Estructura de activos (jerarquización de sistemas y taxonomía de equipos en PDVSA)
- Guía para definir la estructura de activos en PDVSA
- Indicadores de gestión del proceso de mantenimiento
Estudios:
- Especialización en Finanzas
- Diplomado en Gerencia de Mantenimiento Industrial
- Diplomado en Análisis Probabilístico de Riesgos en Proyectos de Exploración y Producción
- Especialización en Ingeniería de Mantenimiento
- Correo electrónico: ljmfl7788@gmail.com
- Contacto móvil: +58 424 9431320
Dinos qué te ha parecido el artículo
Artículos recomendados
¿Cómo lograr una carrera exitosa como ingeniero de confiabilidad?

Confiabilidad Aplicada

Influencia de los parámetros pasivos de vibración en el comportamiento dinámico de equipos

Curso de planificación en mantenimiento

Publica tu artículo en la revista #1 de Mantenimiento Industrial
Publicar un artículo en la revista es gratis, no tiene costo.
Solo debes asegurarte que no sea un artículo comercial.
¿Qué esperas?
O envía tu artículo directo: articulos@predictiva21.com
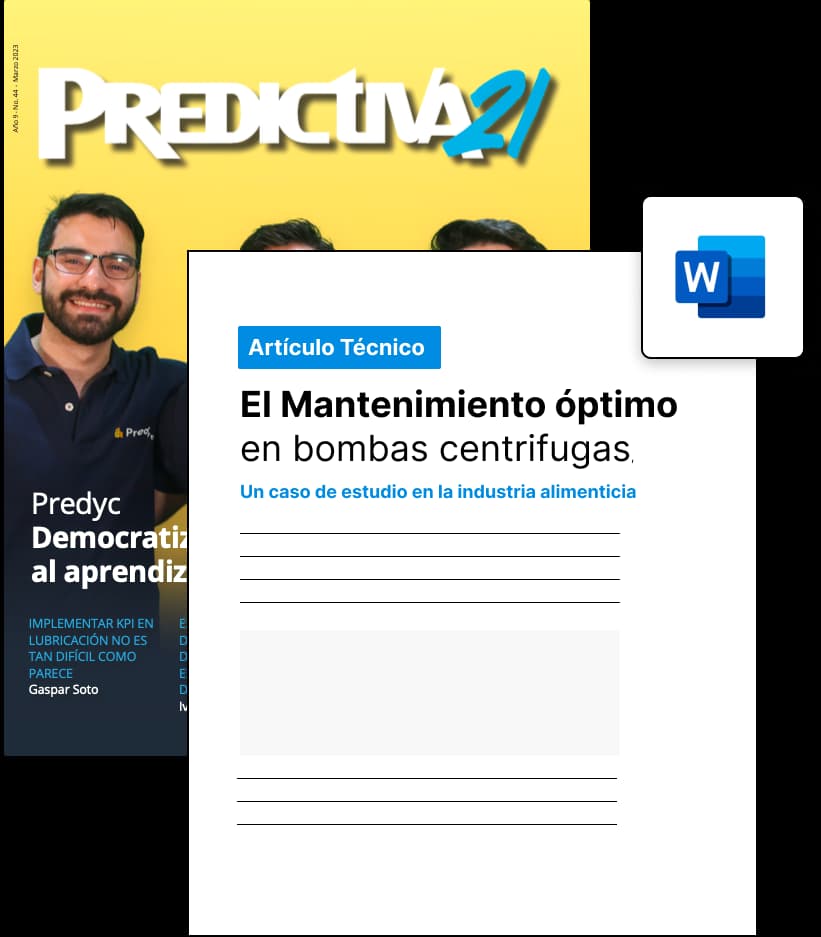