Understanding the Consequences that Resonance has on Reliability
Articulo11 de noviembre de 2019
Equipment is being built lighter and cheaper. This means that resonance has become more of a reliability problem with equipment. Most engineers, CM analysts, mechanics and managers are not aware of how resonance may be affecting their equipment. Resonance frequencies will excite any vibration occurring at or near the same frequency. This can include misalignment, unbalance, bearing faults or other defect frequencies. This will cause your equipment to fail more quickly as well as other unwanted effects.
You should to be aware of and document the resonance frequencies affecting your equipment. Many methods can be used to determine the resonance frequencies in your equipment and a good vibration analyzer will have the resources to help you do so. Methods such as an impact test (bump test), negative averaging, startup, coast down, etc. can be used to identify resonance frequencies. Additionally, the vibration analyst should look for signs of resonance-related issues when doing routine equipment analysis. For example, always look at the amplitude ratios between horizontal and vertical vibration measurements. Ratios of 3 to 1 or higher (horizontal versus vertical) are an indication of resonance issues in the equipment being monitored.
What should you do once a resonance problem is known and the unwanted reliability consequences understood? It is important to keep equipment operational speeds away from these critical frequencies by at least 20-30 percent. Actions can be taken to shift these critical frequencies and minimize and/or eliminate their negative effect on your equipment reliability. The primary methods are: Add Mass: Adding mass will lower the resonant frequency.
Add Stiffness: Adding stiffness raises the resonant frequency.
Damping: Dampens the vibration to keep it from becoming a destructive force.
Make sure you understand the consequences that resonance has on your equipment. Not understanding and addressing equipment resonance will lead to unwanted and costly reliability issues.
Tomado de: www.ludeca.com
Dinos qué te ha parecido el artículo
Artículos recomendados
19.- Vibración Mecánica en Bombas Centrífugas

Certificación SMRP: descubre este importante certificado

Certificación ISO 55000

La importancia de los 5 por qué en el ACR

Publica tu artículo en la revista #1 de Mantenimiento Industrial
Publicar un artículo en la revista es gratis, no tiene costo.
Solo debes asegurarte que no sea un artículo comercial.
¿Qué esperas?
O envía tu artículo directo: articulos@predictiva21.com
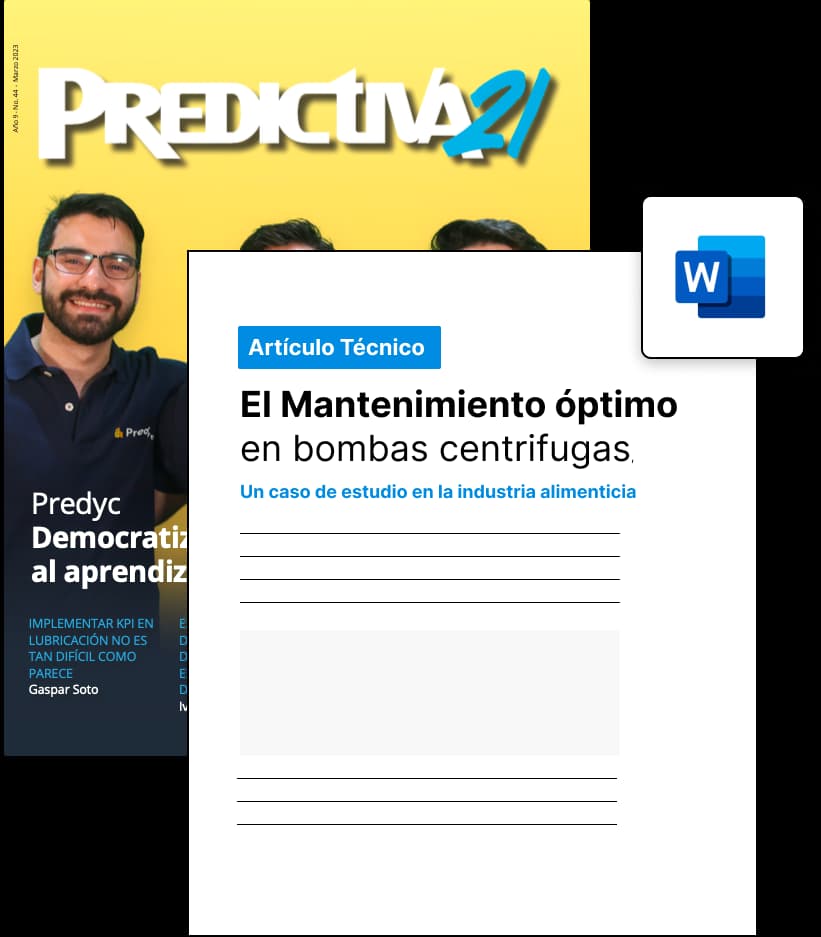
Understanding the Consequences that Resonance has on Reliability
Articulo 11 de noviembre de 2019Equipment is being built lighter and cheaper. This means that resonance has become more of a reliability problem with equipment. Most engineers, CM analysts, mechanics and managers are not aware of how resonance may be affecting their equipment. Resonance frequencies will excite any vibration occurring at or near the same frequency. This can include misalignment, unbalance, bearing faults or other defect frequencies. This will cause your equipment to fail more quickly as well as other unwanted effects.
You should to be aware of and document the resonance frequencies affecting your equipment. Many methods can be used to determine the resonance frequencies in your equipment and a good vibration analyzer will have the resources to help you do so. Methods such as an impact test (bump test), negative averaging, startup, coast down, etc. can be used to identify resonance frequencies. Additionally, the vibration analyst should look for signs of resonance-related issues when doing routine equipment analysis. For example, always look at the amplitude ratios between horizontal and vertical vibration measurements. Ratios of 3 to 1 or higher (horizontal versus vertical) are an indication of resonance issues in the equipment being monitored.
What should you do once a resonance problem is known and the unwanted reliability consequences understood? It is important to keep equipment operational speeds away from these critical frequencies by at least 20-30 percent. Actions can be taken to shift these critical frequencies and minimize and/or eliminate their negative effect on your equipment reliability. The primary methods are: Add Mass: Adding mass will lower the resonant frequency.
Add Stiffness: Adding stiffness raises the resonant frequency.
Damping: Dampens the vibration to keep it from becoming a destructive force.
Make sure you understand the consequences that resonance has on your equipment. Not understanding and addressing equipment resonance will lead to unwanted and costly reliability issues.
Tomado de: www.ludeca.com
Dinos qué te ha parecido el artículo
Artículos recomendados
Transformando el Monitoreo de Turbomáquinas, nuevas perspectivas desde la Gestión de Activos

¿Qué es el RCM? Descubre este poderoso proceso

Las Cláusulas Contractuales para la Adquisición de Activos

El análisis de causa raíz en los problemas simples, complicados y complejos.

Publica tu artículo en la revista #1 de Mantenimiento Industrial
Publicar un artículo en la revista es gratis, no tiene costo.
Solo debes asegurarte que no sea un artículo comercial.
¿Qué esperas?
O envía tu artículo directo: articulos@predictiva21.com
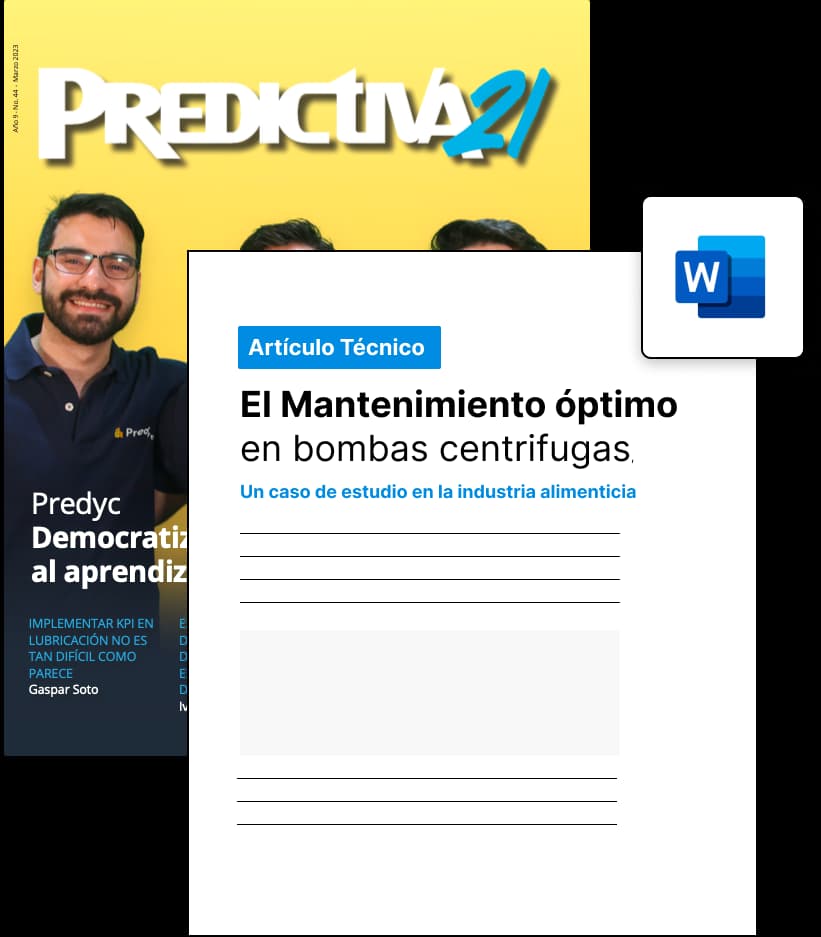