9.3 Tipos de Mantenimiento
Articulo9 de noviembre de 2021
Se puede decir que existen 4 tipos básicos de mantenimiento:
- CORRECTIVO.
- PREVENTIVO.
- FUNCIONAL.
- PREDICTIVO.
Mantenimiento Correctivo
Se reparan todos aquellos defectos que han ocurrido o que se sabe que han ocurrido.
El mantenimiento correctivo es el más fácil de implementar, sin embargo, presenta tres desventajas básicas:
- Permitir un fallo en un componente de una máquina y consecuentemente los costes pueden ser muy altos.
- El fallo puede ocurrir a una hora inconveniente, o si el equipo es móvil, en un lugar inconveniente, de manera que no estará disponible ni el personal ni los repuestos necesarios para su reparación.
- Hay plantas que no pueden ser paradas de un momento a otro, ya sea porque proveen un servicio esencial o porque manejan productos tales como alimentos o materiales fundidos, los cuales se deteriorarán o solidificarán o producirán otros efectos dañinos si la planta se detiene repentinamente.
Mantenimiento Preventivo
Consiste en la realización de rondas de supervisión o de sustitución en periodos fijos de tiempo.
El mantenimiento preventivo realizado a intervalos de tiempos regulares es un avance comparado con el mantenimiento correctivo respecto a la prevención de fallos inesperadas. Sin embargo, no es el método óptimo para obtener una máxima seguridad y confiabilidad de la Planta. Fundamentalmente, porque los fallos no se producen a intervalos regulares de tiempo, sino que se producen a intervalos de tiempo de acuerdo a una distribución. De aquí que el intervalo de tiempo entre intervenciones se elija como un valor de compromiso entre un intervalo corto (sobre mantenimiento) que resulta seguro, pero muy caro, y un
intervalo largo (sub-mantenimiento) que es barato, pero hay riesgo de que ocurran muchas fallos durante dicho intervalo. El intervalo de tiempo entre intervenciones se determina a menudo estadísticamente como el período de tiempo durante el cual el fabricante espera que menos del 2% de máquinas nuevas o totalmente revisados fallen, es decir, una confiabilidad del 98 %. Este intervalo de intervención debe ser revisado continuamente, ya que estudios demuestran que dicho valor cambia a lo largo de la vida de la máquina.
En consecuencia el mantenimiento preventivo presenta tres desventajas básicas.
- Algunas fallos de todas formas ocurrirán entre los intervalos de reparación, y esto puede ser inesperado e inconveniente.
- Durante la detención muchos componentes en buenas condiciones se desmontarán, se inspeccionarán, o se cambiarán innecesariamente, y si se comete algún error en el reensamble, la condición final con que queda la máquina puede ser peor que antes de realizar la intervención.
- Como en una reparación general se requiere examinar gran número de elementos, ello puede tomar un tiempo considerable y puede resultar en una gran pérdida de producción.
Mantenimiento Funcional
Consiste en la búsqueda de fallos no evidentes, fallos que normalmente afectan a los sistemas de protección y consiste en verificar periódicamente que éstos funcionan.
Mantenimiento Predictivo
Consiste en el análisis de parámetros de funcionamiento cuya evolución permite detectar un fallo antes de que este tenga consecuencias más graves.
En general, el Mantenimiento predictivo, consiste en estudiar la evolución temporal de ciertos parámetros y asociarlos a la evolución de fallos, para así determinar en que periodo de tiempo, ese fallo va a tomar una relevancia importante, para así poder planificar todas las intervenciones con tiempo suficiente, para que ese fallo nunca tenga consecuencias graves.
Una de las características más importantes de este tipo de mantenimiento es que no debe alterar el funcionamiento normal de la planta mientras se está aplicando.
La inspección de los parámetros se puede realizar de forma periódica o de forma continua, dependiendo de diversos factores como son: el tipo de planta, los tipos de fallos a diagnosticar y la inversión que se quiera realizar.
La respuesta aparente a estos problemas es realizar un mantenimiento basado en la condición o estado de la máquina. En este tipo de mantenimiento, las revisiones a intervalos fijos de tiempo se sustituyen por mediciones de ciertos síntomas o parámetros a intervalos fijos. Esto se denomina control y seguimiento de la condición, o monitoreo de la condición (condition monitoring). El principio del mantenimiento predictivo es que la intervención de la máquina se realiza únicamente cuando las mediciones indican que es necesario. Esto está, además de acuerdo con el recelo que la mayoría de los ingenieros tiene en intervenir las máquinas que funcionan bien.
Definiremos monitoreo de la condición de la máquina, como el control de su funcionamiento y el análisis de las mediciones obtenidas tendientes a detectar fallos incipientes o deterioro de ella; a diagnosticar estos fallos; y a predecir cuánto tiempo podría funcionar continuamente la máquina en forma segura.
La hipótesis base del mantenimiento predictivo asume que hay características medibles u observables, los cuales definen exactamente la condición de la máquina.
Dinos qué te ha parecido el artículo
Artículos recomendados
6.2 Funciones y sus Estándares de Funcionamiento

Podcast de Gestión de Activos

Termografía I

Las Cláusulas Contractuales para la Adquisición de Activos

Publica tu artículo en la revista #1 de Mantenimiento Industrial
Publicar un artículo en la revista es gratis, no tiene costo.
Solo debes asegurarte que no sea un artículo comercial.
¿Qué esperas?
O envía tu artículo directo: articulos@predictiva21.com
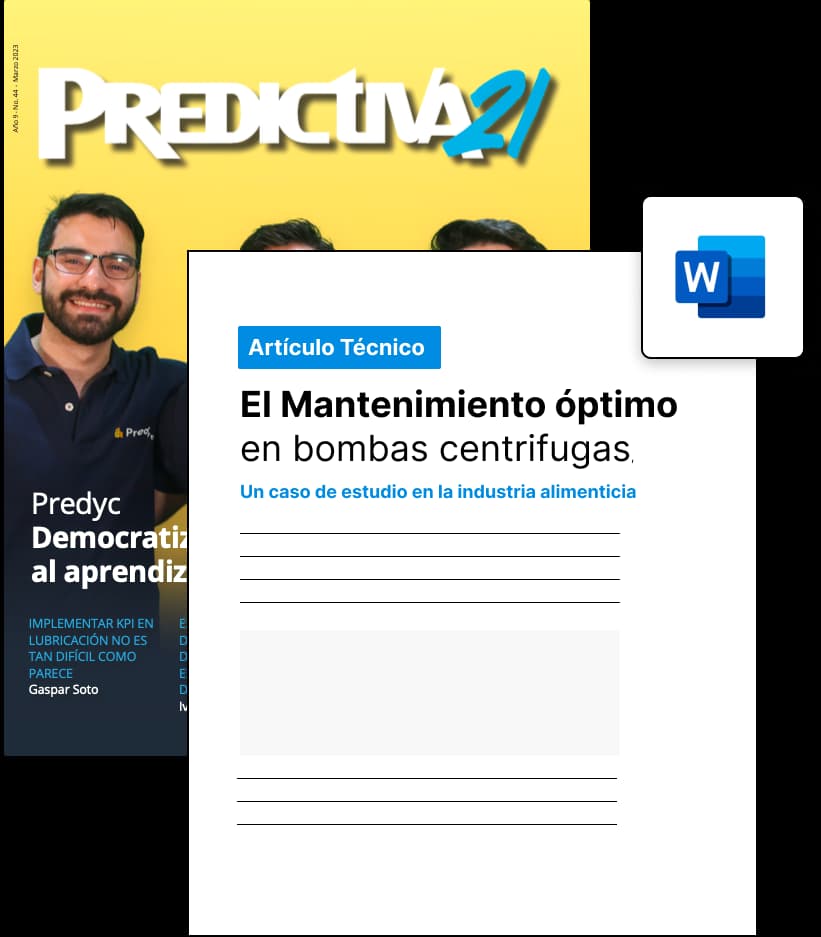
9.3 Tipos de Mantenimiento
Articulo 9 de noviembre de 2021Se puede decir que existen 4 tipos básicos de mantenimiento:
- CORRECTIVO.
- PREVENTIVO.
- FUNCIONAL.
- PREDICTIVO.
Mantenimiento Correctivo
Se reparan todos aquellos defectos que han ocurrido o que se sabe que han ocurrido.
El mantenimiento correctivo es el más fácil de implementar, sin embargo, presenta tres desventajas básicas:
- Permitir un fallo en un componente de una máquina y consecuentemente los costes pueden ser muy altos.
- El fallo puede ocurrir a una hora inconveniente, o si el equipo es móvil, en un lugar inconveniente, de manera que no estará disponible ni el personal ni los repuestos necesarios para su reparación.
- Hay plantas que no pueden ser paradas de un momento a otro, ya sea porque proveen un servicio esencial o porque manejan productos tales como alimentos o materiales fundidos, los cuales se deteriorarán o solidificarán o producirán otros efectos dañinos si la planta se detiene repentinamente.
Mantenimiento Preventivo
Consiste en la realización de rondas de supervisión o de sustitución en periodos fijos de tiempo.
El mantenimiento preventivo realizado a intervalos de tiempos regulares es un avance comparado con el mantenimiento correctivo respecto a la prevención de fallos inesperadas. Sin embargo, no es el método óptimo para obtener una máxima seguridad y confiabilidad de la Planta. Fundamentalmente, porque los fallos no se producen a intervalos regulares de tiempo, sino que se producen a intervalos de tiempo de acuerdo a una distribución. De aquí que el intervalo de tiempo entre intervenciones se elija como un valor de compromiso entre un intervalo corto (sobre mantenimiento) que resulta seguro, pero muy caro, y un
intervalo largo (sub-mantenimiento) que es barato, pero hay riesgo de que ocurran muchas fallos durante dicho intervalo. El intervalo de tiempo entre intervenciones se determina a menudo estadísticamente como el período de tiempo durante el cual el fabricante espera que menos del 2% de máquinas nuevas o totalmente revisados fallen, es decir, una confiabilidad del 98 %. Este intervalo de intervención debe ser revisado continuamente, ya que estudios demuestran que dicho valor cambia a lo largo de la vida de la máquina.
En consecuencia el mantenimiento preventivo presenta tres desventajas básicas.
- Algunas fallos de todas formas ocurrirán entre los intervalos de reparación, y esto puede ser inesperado e inconveniente.
- Durante la detención muchos componentes en buenas condiciones se desmontarán, se inspeccionarán, o se cambiarán innecesariamente, y si se comete algún error en el reensamble, la condición final con que queda la máquina puede ser peor que antes de realizar la intervención.
- Como en una reparación general se requiere examinar gran número de elementos, ello puede tomar un tiempo considerable y puede resultar en una gran pérdida de producción.
Mantenimiento Funcional
Consiste en la búsqueda de fallos no evidentes, fallos que normalmente afectan a los sistemas de protección y consiste en verificar periódicamente que éstos funcionan.
Mantenimiento Predictivo
Consiste en el análisis de parámetros de funcionamiento cuya evolución permite detectar un fallo antes de que este tenga consecuencias más graves.
En general, el Mantenimiento predictivo, consiste en estudiar la evolución temporal de ciertos parámetros y asociarlos a la evolución de fallos, para así determinar en que periodo de tiempo, ese fallo va a tomar una relevancia importante, para así poder planificar todas las intervenciones con tiempo suficiente, para que ese fallo nunca tenga consecuencias graves.
Una de las características más importantes de este tipo de mantenimiento es que no debe alterar el funcionamiento normal de la planta mientras se está aplicando.
La inspección de los parámetros se puede realizar de forma periódica o de forma continua, dependiendo de diversos factores como son: el tipo de planta, los tipos de fallos a diagnosticar y la inversión que se quiera realizar.
La respuesta aparente a estos problemas es realizar un mantenimiento basado en la condición o estado de la máquina. En este tipo de mantenimiento, las revisiones a intervalos fijos de tiempo se sustituyen por mediciones de ciertos síntomas o parámetros a intervalos fijos. Esto se denomina control y seguimiento de la condición, o monitoreo de la condición (condition monitoring). El principio del mantenimiento predictivo es que la intervención de la máquina se realiza únicamente cuando las mediciones indican que es necesario. Esto está, además de acuerdo con el recelo que la mayoría de los ingenieros tiene en intervenir las máquinas que funcionan bien.
Definiremos monitoreo de la condición de la máquina, como el control de su funcionamiento y el análisis de las mediciones obtenidas tendientes a detectar fallos incipientes o deterioro de ella; a diagnosticar estos fallos; y a predecir cuánto tiempo podría funcionar continuamente la máquina en forma segura.
La hipótesis base del mantenimiento predictivo asume que hay características medibles u observables, los cuales definen exactamente la condición de la máquina.
Dinos qué te ha parecido el artículo
Artículos recomendados
Entrevista a Annalisa Ferrari

Mantenimiento preventivo de las fábricas y su impacto en la eficiencia global de equipos

¿Qué es la transformación digital para el Mantenimiento Predictivo?

Análisis de criticidad: ¿Qué es y por qué es importante?

Publica tu artículo en la revista #1 de Mantenimiento Industrial
Publicar un artículo en la revista es gratis, no tiene costo.
Solo debes asegurarte que no sea un artículo comercial.
¿Qué esperas?
O envía tu artículo directo: articulos@predictiva21.com
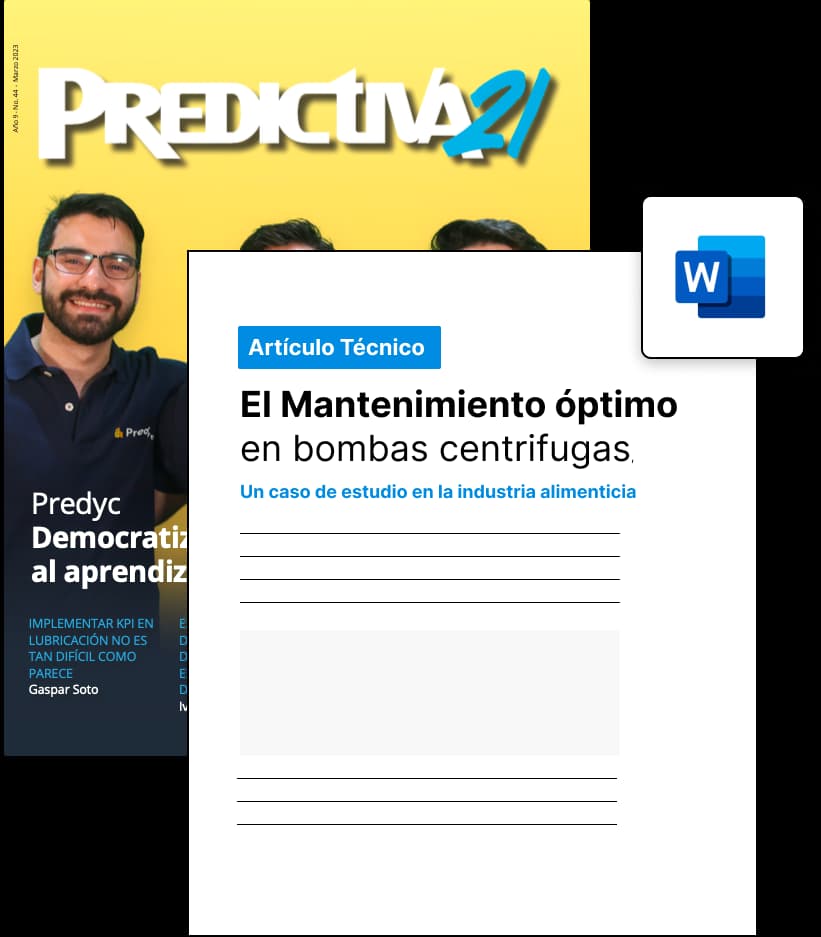