Análisis de modo y efectos de falla (AMEF) en compresores reciprocantes
Articulo8 de abril de 2019
La ruptura de barra (vástago) de pistón y las fallas generadas en crucetas por efectos de no reversión de carga son fallas típicas en compresores reciprocantes utilizados para la compresión de gas. Este tipo de fallas pueden ser minimizadas y su frecuencia de ocurrencia disminuida si se tiene claro los modos, efectos y factores que las generan.
Por experiencias vividas, es común escuchar ante un evento de ruptura de una barra en un compresor reciprocante “¡Se partió una barra del compresor, hubo un no reversall! “. Esto se debe a que el factor de carga en la barra tiene incidencia determinante en ambas fallas, pero de manera muy particular en cada caso. Ello me ha motivado a desarrollar el presente artículo con la finalidad de esclarecer los criterios que definen de manera particular cada una de estas fallas, mediante el análisis de modo y efecto de falla (AMEF).
“Ruptura de Barra de Pistón y Condición de No Reversión de Carga: Dos fallas con modos y efectos distintos pero que tienden a ser
relacionadas entre si."
Para realizar el análisis de las fallas mencionadas en necesario tener claro el concepto de carga total y el comportamiento de esta en el proceso de compresión de Gas. Las acciones de las fuerzas sobre la barra del pistón se dan a compresión y a tensión; a compresión cuando el pistón se desplaza hacia el lado cabezal, en este momento la fuerza ejercida del lado del extremo del cabezal excede la fuerza de lado del extremo del cigüeñal, como se representan en la Figura N° 1.

Fuente: Engine & Compressor Analysis Techniques, Dynalco Controls 2003.
Cuando la barra está sometida a esfuerzos a tensión el pistón se desplaza hacía el lado cigüeñal, las fuerzas ejercidas del lado del extremo del cigüeñal excede la fuerza del lado del extremo del cabezal, como se representa en la Figura N° 2.

Fuente: Engine & Compressor Analysis Techniques, Dynalco Controls 2003.
Es importante describir que la carga sobre la barra, tanto a compresión como a tensión, esta definida como la cantidad total de fuerza que se transfiere a la barra del pistón y es generada por la suma algebraica de dos fuerzas:
Carga estática o Fuerza del Gas: Se refiere a la fuerza resultante sobre los componentes del cilindro debido a la compresión del gas en el interior de este, la cual actúa directamente sobre la cara del pistón.
Carga Inercial: Se refiere a la fuerza desarrollada a partir de la masa de los componentes reciprocantes (Pistón, Tuerca de Pistón, Barra, Tuerca de Barra y Conjunto de la Cruceta).
“La carga inercial actúa en sentido opuesto a la carga de gas”
En la Figura N° 3 se aprecia el comportamiento de la carga total, carga de inercia y carga de gas en el ciclo de compresión de gas (Diagrama P-T).

Fuente: Engine & Compressor Analysis Techniques, Dynalco Controls 2003.
Falla por ruptura de barra o vástago de pistón
Desde el punto de vista de la mecánica de los materiales, la falla por ruptura de barra de pistón se da por el exceso de carga a la cual está sometido el material de este componente, en tal magnitud que sobrepasa el limite elástico del material, llegando al límite plástico y posterior ruptura del mismo. Para el óptimo funcionamiento de este componente, el fabricante suministra los datos de máxima carga a la cual puede ser sometido este, el cual es tomado en consideración por los softwares de selección y diseño de compresores reciprocantes como una de las variables operacionales que determina la aceptación o no de la configuración y características del compresor para el requerimiento operacional exigido.
La sobrecarga en la barra es una condición cuya causa puede darse tanto por factores operacionales como por condiciones inducidas por errores humanos, dichas causas son las siguientes:
- Arrastre de Liquido: Al ser el líquido un fluido incompresible, la presencia de este en el proceso de compresión de gas, es el enemigo número uno que atenta contra la integridad mecánica de estos equipos. La presencia de líquido no sólo atenta contra la integridad de la barra sino que pudiera ocasionar daños irreversibles en el cigüeñal.
- Sobrepresión por falla de válvulas reguladoras de presión: La generación de carga superior al máximo permisible en ocasiones obedecen al incremento de la presión en la línea succión, este hecho puede estar asociado al ineficiente funcionamiento de la válvula de control de presión.
- Error en el montaje de válvulas en los cilindros compresores: este es un factor con baja probabilidad de ocurrencia, sin embargo no esta exento de suceder. La válvula compresora está diseñada para permanecer cerradas, su apertura se da por la fuerza producida por el diferencial de presión entre el interior del cilindro y el laberinto de succión o descarga del gas según sea el caso. El flujo de gas a través de ellas se da en un solo sentido, es decir, trabaja bajo el principio de una válvula check. La colocación errónea de válvulas de succión en la descarga hará que estas funcionen como un “tapón”, lo cual producirá la compresión y re-compresión de este mismo gas, hasta el momento que este efecto genere una fuerza mayor a la máxima capacidad de carga de la barra y esta colapse.

Fuente: Engine & Compressor Analysis Techniques, Dynalco Controls 2003.
Desde el punto de vista de la dinámica de compresión del Gas, los factores antes mencionados, generarán un comportamiento de carga sobre la barra del pistón anormal como el que se muestra en la Figura N° 4. Bajo estas condiciones este componente se hace vulnerable y propenso a su ruptura.
En la Figura N°5 se ilustran fallas de ruptura de barra de pistón generada por arrastre de líquido en el proceso de compresión de gas natural.

Fuente: Propia.
“Los factores que genera una sobre carga sobre la barra son factores capaces de generar fuerzas en magnitud superiores a las que puede soportar este componente”.
Cursos recomendados






%252FImagen%252FRAMPREDYC-1730060420837.webp%3Falt%3Dmedia%26token%3D2634a7f0-988e-4022-b91f-382503e6e9db&w=3840&q=75)

Falla por no reversión de carga
En el ciclo de compresión del gas, debe existir una reversión de esfuerzos producidos sobre la barra, lo cual significa que la carga debe alternar de tensión a compresión y retornar a tensión de nuevo durante los 360 grados de rotación del cigüeñal. La carga se invierte dos (02) veces por ciclo, esto ocurre cuando la carga total cruza el punto cero que delimita la carga a tensión y compresión. El intervalo de reversión abarca hasta el punto donde la carga total cruza nuevamente por el punto cero, como se muestra en la Figura N° 6.

Fuente: Software Windrock MD.
De acuerdo a lo establecido en la norma API 618 de 1995 Reciprocanting Compressor For Petroleum, chemical and Gas Insdustry Services, en la página 6, sección 2.4 Rod And Gas Loading: “… la duración de ésta reversión no debe ser menor de 15 grados de ángulo del cigüeñal y la magnitud del pico de la carga combinada revertida debe ser al menos el 3% de la carga combinada en la dirección opuesta”. Esto significa que si la carga predominante en tiempo sobre la barra es la tensión, al menos durante 15 grados del cigüeñal la barra debe estar a compresión, y el pico de compresión debe ser al menos 3% del pico de la tensión.
Las condiciones de reversión en la carga de la barra son requeridas para garantizar el tiempo, medido en grados, necesarios para asegurar la apropiada lubricación del buje o bocina de la cruceta. El cambio de tensión a compresión causa que el juego entre el buje y el pasador se mueva de un lado otro, lo que permite lubricarlos y enfriarlos. Si la reversión de la carga no ocurriera, la mitad del buje permanecería sin lubricación.
La falla por no reversión es ocasionada por insuficiencia de carga sobre la barra a tensión o a compresión, es decir, por insuficiencia de carga generada en alguno de los dos extremos del cilindro compresor (Lado Cabezal / Lado Cigüeñal), lo cual impide cumplir las condiciones mínimas descritas anteriormente en la norma API 618. A continuación, se describen las condiciones operacionales que propician las fallas por no reversión:
- Falla total de la válvula de descarga del extremo del cabezal.
- Falla total de la válvula de descarga del extremo del cigüeñal.
- Falla total de las válvulas de succión del extremo del cabezal.
- Extremo del cabezal cargado, extremo del cigüeñal descargado.
- Extremo del cigüeñal cargado, extremo del cabezal descargado.
En la Figura N° 7 se ilustra el comportamiento de la carga total sobre la barra en donde es evidentemente que no existen las condiciones mínimas de carga a tensión (3% del punto de máxima carga a compresión) ni los grados mínimos requeridos para el intervalo de reversión (15° grados de reversión), es por ello que se da la falla por no reversión de carga.

Fuente: Engine & Compressor Analysis Techniques, Dynalco Controls 2003.
La falla por no reversión de carga genera daños por temperatura en la bocina, pasador de cruceta y en la biela. En la Figura N° 8 se aprecian los daños ocurridos en estos componentes en un falla por no reversión de carga.

Fuente: Propia
Comentarios finales
- Aun cuando la carga total es un factor determinante que interviene en ambas fallas estudiadas; la ocurrencia de no reversión de carga se da por condiciones totalmente opuestos a la falla de ruptura de barra; por ello es improbable que una condición de no reversión genere una ruptura de barra, así como también una sobrecarga sobre la barra genere una falla por no reversión.
- El exceso de carga sobre la barra además de hacer propicia las condiciones para la ruptura de este componente, también genera fuertes impactos del pasador de la cruceta sobre la bocina durante la inversión de carga, este efecto produce desgaste prematuro de estos dos componentes; sin embargo no se debe relacionar ni confundir con los efectos ocasionados por condiciones de no reversión, los cuales producen daños por temperatura debido a la ineficiente lubricación.
Autor: Odlanier J. Mendoza M
Ingeniero Mecánico
Ingeniero de Integridad Mecánica de Equipos Dinámicos
PDVSA Compresión Gas – Oriente
Maturín; Estado Monagas, Venezuela
Correo: odlaniermendoza@gmail.com / mendozaox@pdvsa.com
Dinos qué te ha parecido el artículo
Artículos recomendados
La Importancia de la Gestión Energética en México

Evitar los errores humanos en los procesos productivos con el Análisis de Causa Raíz (ACR)

Oil Condition Monitoring: Lo que esconde el contaje de partículas en aceites

7.5 Importancia del ACR

Publica tu artículo en la revista #1 de Mantenimiento Industrial
Publicar un artículo en la revista es gratis, no tiene costo.
Solo debes asegurarte que no sea un artículo comercial.
¿Qué esperas?
O envía tu artículo directo: articulos@predictiva21.com
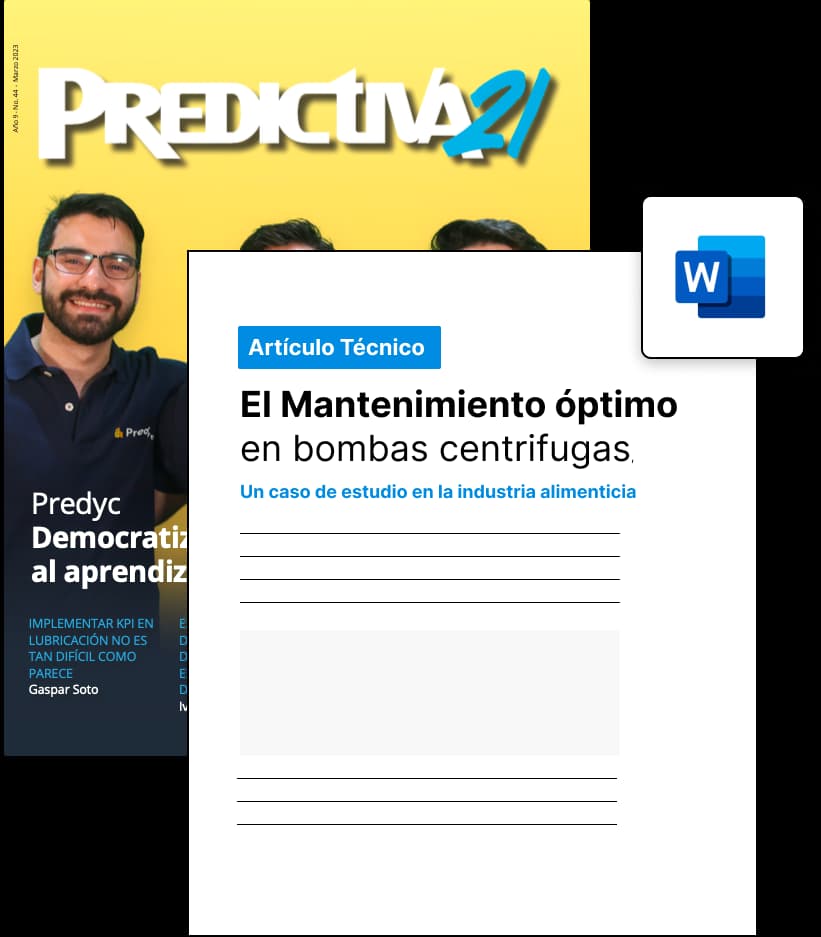
Análisis de modo y efectos de falla (AMEF) en compresores reciprocantes
Articulo 8 de abril de 2019La ruptura de barra (vástago) de pistón y las fallas generadas en crucetas por efectos de no reversión de carga son fallas típicas en compresores reciprocantes utilizados para la compresión de gas. Este tipo de fallas pueden ser minimizadas y su frecuencia de ocurrencia disminuida si se tiene claro los modos, efectos y factores que las generan.
Por experiencias vividas, es común escuchar ante un evento de ruptura de una barra en un compresor reciprocante “¡Se partió una barra del compresor, hubo un no reversall! “. Esto se debe a que el factor de carga en la barra tiene incidencia determinante en ambas fallas, pero de manera muy particular en cada caso. Ello me ha motivado a desarrollar el presente artículo con la finalidad de esclarecer los criterios que definen de manera particular cada una de estas fallas, mediante el análisis de modo y efecto de falla (AMEF).
“Ruptura de Barra de Pistón y Condición de No Reversión de Carga: Dos fallas con modos y efectos distintos pero que tienden a ser
relacionadas entre si."
Para realizar el análisis de las fallas mencionadas en necesario tener claro el concepto de carga total y el comportamiento de esta en el proceso de compresión de Gas. Las acciones de las fuerzas sobre la barra del pistón se dan a compresión y a tensión; a compresión cuando el pistón se desplaza hacia el lado cabezal, en este momento la fuerza ejercida del lado del extremo del cabezal excede la fuerza de lado del extremo del cigüeñal, como se representan en la Figura N° 1.

Fuente: Engine & Compressor Analysis Techniques, Dynalco Controls 2003.
Cuando la barra está sometida a esfuerzos a tensión el pistón se desplaza hacía el lado cigüeñal, las fuerzas ejercidas del lado del extremo del cigüeñal excede la fuerza del lado del extremo del cabezal, como se representa en la Figura N° 2.

Fuente: Engine & Compressor Analysis Techniques, Dynalco Controls 2003.
Es importante describir que la carga sobre la barra, tanto a compresión como a tensión, esta definida como la cantidad total de fuerza que se transfiere a la barra del pistón y es generada por la suma algebraica de dos fuerzas:
Carga estática o Fuerza del Gas: Se refiere a la fuerza resultante sobre los componentes del cilindro debido a la compresión del gas en el interior de este, la cual actúa directamente sobre la cara del pistón.
Carga Inercial: Se refiere a la fuerza desarrollada a partir de la masa de los componentes reciprocantes (Pistón, Tuerca de Pistón, Barra, Tuerca de Barra y Conjunto de la Cruceta).
“La carga inercial actúa en sentido opuesto a la carga de gas”
En la Figura N° 3 se aprecia el comportamiento de la carga total, carga de inercia y carga de gas en el ciclo de compresión de gas (Diagrama P-T).

Fuente: Engine & Compressor Analysis Techniques, Dynalco Controls 2003.
Falla por ruptura de barra o vástago de pistón
Desde el punto de vista de la mecánica de los materiales, la falla por ruptura de barra de pistón se da por el exceso de carga a la cual está sometido el material de este componente, en tal magnitud que sobrepasa el limite elástico del material, llegando al límite plástico y posterior ruptura del mismo. Para el óptimo funcionamiento de este componente, el fabricante suministra los datos de máxima carga a la cual puede ser sometido este, el cual es tomado en consideración por los softwares de selección y diseño de compresores reciprocantes como una de las variables operacionales que determina la aceptación o no de la configuración y características del compresor para el requerimiento operacional exigido.
La sobrecarga en la barra es una condición cuya causa puede darse tanto por factores operacionales como por condiciones inducidas por errores humanos, dichas causas son las siguientes:
- Arrastre de Liquido: Al ser el líquido un fluido incompresible, la presencia de este en el proceso de compresión de gas, es el enemigo número uno que atenta contra la integridad mecánica de estos equipos. La presencia de líquido no sólo atenta contra la integridad de la barra sino que pudiera ocasionar daños irreversibles en el cigüeñal.
- Sobrepresión por falla de válvulas reguladoras de presión: La generación de carga superior al máximo permisible en ocasiones obedecen al incremento de la presión en la línea succión, este hecho puede estar asociado al ineficiente funcionamiento de la válvula de control de presión.
- Error en el montaje de válvulas en los cilindros compresores: este es un factor con baja probabilidad de ocurrencia, sin embargo no esta exento de suceder. La válvula compresora está diseñada para permanecer cerradas, su apertura se da por la fuerza producida por el diferencial de presión entre el interior del cilindro y el laberinto de succión o descarga del gas según sea el caso. El flujo de gas a través de ellas se da en un solo sentido, es decir, trabaja bajo el principio de una válvula check. La colocación errónea de válvulas de succión en la descarga hará que estas funcionen como un “tapón”, lo cual producirá la compresión y re-compresión de este mismo gas, hasta el momento que este efecto genere una fuerza mayor a la máxima capacidad de carga de la barra y esta colapse.

Fuente: Engine & Compressor Analysis Techniques, Dynalco Controls 2003.
Desde el punto de vista de la dinámica de compresión del Gas, los factores antes mencionados, generarán un comportamiento de carga sobre la barra del pistón anormal como el que se muestra en la Figura N° 4. Bajo estas condiciones este componente se hace vulnerable y propenso a su ruptura.
En la Figura N°5 se ilustran fallas de ruptura de barra de pistón generada por arrastre de líquido en el proceso de compresión de gas natural.

Fuente: Propia.
“Los factores que genera una sobre carga sobre la barra son factores capaces de generar fuerzas en magnitud superiores a las que puede soportar este componente”.
Cursos recomendados






%252FImagen%252FRAMPREDYC-1730060420837.webp%3Falt%3Dmedia%26token%3D2634a7f0-988e-4022-b91f-382503e6e9db&w=3840&q=75)

Falla por no reversión de carga
En el ciclo de compresión del gas, debe existir una reversión de esfuerzos producidos sobre la barra, lo cual significa que la carga debe alternar de tensión a compresión y retornar a tensión de nuevo durante los 360 grados de rotación del cigüeñal. La carga se invierte dos (02) veces por ciclo, esto ocurre cuando la carga total cruza el punto cero que delimita la carga a tensión y compresión. El intervalo de reversión abarca hasta el punto donde la carga total cruza nuevamente por el punto cero, como se muestra en la Figura N° 6.

Fuente: Software Windrock MD.
De acuerdo a lo establecido en la norma API 618 de 1995 Reciprocanting Compressor For Petroleum, chemical and Gas Insdustry Services, en la página 6, sección 2.4 Rod And Gas Loading: “… la duración de ésta reversión no debe ser menor de 15 grados de ángulo del cigüeñal y la magnitud del pico de la carga combinada revertida debe ser al menos el 3% de la carga combinada en la dirección opuesta”. Esto significa que si la carga predominante en tiempo sobre la barra es la tensión, al menos durante 15 grados del cigüeñal la barra debe estar a compresión, y el pico de compresión debe ser al menos 3% del pico de la tensión.
Las condiciones de reversión en la carga de la barra son requeridas para garantizar el tiempo, medido en grados, necesarios para asegurar la apropiada lubricación del buje o bocina de la cruceta. El cambio de tensión a compresión causa que el juego entre el buje y el pasador se mueva de un lado otro, lo que permite lubricarlos y enfriarlos. Si la reversión de la carga no ocurriera, la mitad del buje permanecería sin lubricación.
La falla por no reversión es ocasionada por insuficiencia de carga sobre la barra a tensión o a compresión, es decir, por insuficiencia de carga generada en alguno de los dos extremos del cilindro compresor (Lado Cabezal / Lado Cigüeñal), lo cual impide cumplir las condiciones mínimas descritas anteriormente en la norma API 618. A continuación, se describen las condiciones operacionales que propician las fallas por no reversión:
- Falla total de la válvula de descarga del extremo del cabezal.
- Falla total de la válvula de descarga del extremo del cigüeñal.
- Falla total de las válvulas de succión del extremo del cabezal.
- Extremo del cabezal cargado, extremo del cigüeñal descargado.
- Extremo del cigüeñal cargado, extremo del cabezal descargado.
En la Figura N° 7 se ilustra el comportamiento de la carga total sobre la barra en donde es evidentemente que no existen las condiciones mínimas de carga a tensión (3% del punto de máxima carga a compresión) ni los grados mínimos requeridos para el intervalo de reversión (15° grados de reversión), es por ello que se da la falla por no reversión de carga.

Fuente: Engine & Compressor Analysis Techniques, Dynalco Controls 2003.
La falla por no reversión de carga genera daños por temperatura en la bocina, pasador de cruceta y en la biela. En la Figura N° 8 se aprecian los daños ocurridos en estos componentes en un falla por no reversión de carga.

Fuente: Propia
Comentarios finales
- Aun cuando la carga total es un factor determinante que interviene en ambas fallas estudiadas; la ocurrencia de no reversión de carga se da por condiciones totalmente opuestos a la falla de ruptura de barra; por ello es improbable que una condición de no reversión genere una ruptura de barra, así como también una sobrecarga sobre la barra genere una falla por no reversión.
- El exceso de carga sobre la barra además de hacer propicia las condiciones para la ruptura de este componente, también genera fuertes impactos del pasador de la cruceta sobre la bocina durante la inversión de carga, este efecto produce desgaste prematuro de estos dos componentes; sin embargo no se debe relacionar ni confundir con los efectos ocasionados por condiciones de no reversión, los cuales producen daños por temperatura debido a la ineficiente lubricación.
Autor: Odlanier J. Mendoza M
Ingeniero Mecánico
Ingeniero de Integridad Mecánica de Equipos Dinámicos
PDVSA Compresión Gas – Oriente
Maturín; Estado Monagas, Venezuela
Correo: odlaniermendoza@gmail.com / mendozaox@pdvsa.com
Dinos qué te ha parecido el artículo
Artículos recomendados
Aprende qué es la planificación y control de mantenimiento

Curso de Mantenimiento de Motores Eléctricos

La importancia de los 5 por qué en el ACR

¿Qué es la gestión de riesgos empresariales?

Publica tu artículo en la revista #1 de Mantenimiento Industrial
Publicar un artículo en la revista es gratis, no tiene costo.
Solo debes asegurarte que no sea un artículo comercial.
¿Qué esperas?
O envía tu artículo directo: articulos@predictiva21.com
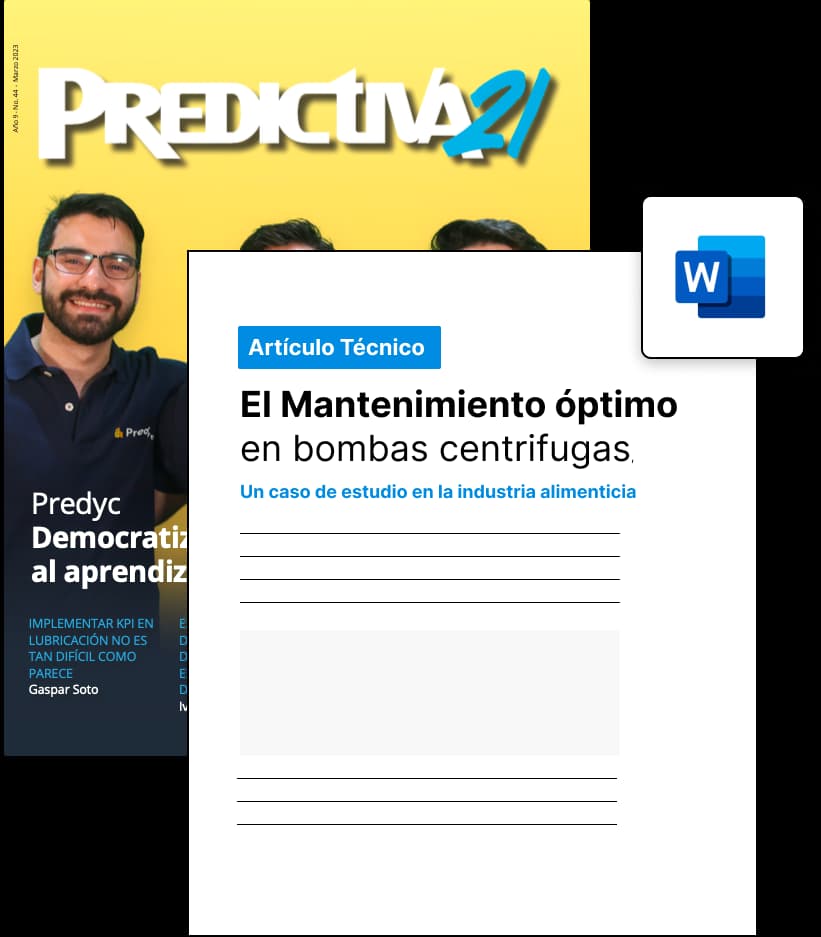