Uso del análisis de vibraciones en el mantenimiento Predictivo de maquinas rotantes
Articulo12 de abril de 2019
Hoy en día en la mayoría de las plantas industriales tienen como objetivo principal elevar el nivel de confiabilidad del área de mantenimiento y por ende el de sus equipos, ya que ello les garantiza mantener un nivel de productividad considerable de sus máquinas rotantes. Por lo tanto, escogen dentro de los distintos tipos de mantenimiento a él predictivo, ya que el mismo les brinda las herramientas necesarias para obtener una gran cantidad de información útil al momento de diagnosticar las máquinas, y determinar las posibles fallas incipientes, que se podrían presentar en las mismas.

Los pasos en que se basa el programa de mantenimiento predictivo siguen una secuencia lógica desde que se detecta un problema, se estudia, se encuentra su causa y finalmente se decide la posibilidad de corregirlo en el momento oportuno con la máxima eficiencia posible.

Los pasos fundamentales son tres:
- Detección: Reconocimiento del problema.
- Análisis: Localización de la causa del problema.
- Corrección: Encontrar el momento y forma de solucionar el problema.
Existen algunos estudios que determinan los valores promedio aproximados de reducción de costos al implementar un programa de mantenimiento predictivo, que serían los siguientes para cada rubro:
- Costos de mantenimiento, reducción de hasta un 50%.
- Reducción de fallas inesperadas, hasta un 55%.
- Reparación del equipo y tiempos del reacondicionamiento, reducción hasta un 60%.
- Reducción del stock de las piezas de repuesto, hasta un 30%.
- Aumento de tiempo medio de funcionamiento de la maquinaria sin paradas, reducción hasta un 30%.
- Reducción de consumo energéticos, hasta un 10%.
Además, en el mantenimiento predictivo existen varias técnicas que nos ayudan a realizar el Análisis Causa-Raíz de algún problema presente en nuestra máquina rotante, con el objetivo de mejorar el desempeño de las máquinas.
Entre las técnicas predictivas más usadas están las siguientes, Análisis de Aceite, Termografía Infrarroja y unas de las más utilizadas como es el Análisis de Vibraciones.

Esta técnica forma parte fundamental en la aplicación de un programa de mantenimiento predictivo ya que nos ayuda a diagnosticar las distintas causa-raíz de cada uno de los problemas presentes y nos brinda una completa información acerca del estado de cada uno de los elementos rotantes, para no tener paradas imprevistas de los equipos.
Concepto de vibración
Se dice que un cuerpo vibra cuando experimenta cambios alternativos, de tal modo que sus puntos oscilen sincrónicamente en torno a sus posiciones de equilibrio, sin que el campo cambie de lugar.
Como otro concepto de vibración, se puede decir que es un intercambio de energía cinética en cuerpos con rigidez y masa finitas, el cual surge de una entrada de energía dependiente del tiempo.
Este intercambio de energía puede ser producido por algunas de las siguientes causas:
- Desequilibrios estáticos o dinámicos.
- Desalienación en máquinas rotatorias.
- Circulación de Fluidos.
- Energía Electromagnética.
- Solturas Mecánicas.
- Resonancias.
- Excentricidades.

Cuando se realizan los análisis de vibraciones la idea básica es buscar la existencia de una fuerza excitatriz, o de excitación, en el sistema estudiado, la cual genera una perturbación en el estado de funcionamiento normal de la máquina, lo que se traduce en una falla presente en la maquina bajo objeto de estudio, por lo se debe diagnosticar acerca del origen de la misma y como contrarrestarla para minimizar la presencia de esa fuerza excitatriz. El diagnostico de las posibles fuentes de perturbación en nuestra maquina rotante, es debido al uso del algoritmo computacional llamado Transformada Rápida de Fourier (FFT).

Sea cualquiera la causa de la vibración, su reducción es necesaria debido a diversas razones entre las cuales tenemos:
- La vibraciones está íntimamente relacionada con la confiabilidad de la maquina rotante.
- Disminuye la vida útil de los rodamientos.
- La excesiva vibración puede limitar la velocidad de procesamiento.
- La vibración es responsable de la pobre calidad de los productos elaborados.
- La vibración de maquinarias puede resultar en radiación de ruido.
- La vibración puede alcanzar a otros instrumentos de precisión de otras fuentes, y causar fallas de funcionamiento.
Hoy en día en toda industria es muy difícil evitar la presencia de las vibraciones, las cuales suelen producirse por la presencia de efectos dinámicos causando el aumentando en la severidad de las amplitudes de vibración. Algunas de las causas que se podrían enunciar serían las siguientes: tolerancias y/o holguras de fabricación, contactos entre partes del rodamiento, fricción entre las piezas de las maquinas giratorios y/o las desalineaciones existentes, entre otros.
Por ende, se lograría diagnosticar las posibles fallas a futuro cumpliendo con el objetivo principal del mantenimiento predictivo, el cual no es más que predecir la ruptura o parada imprevista de las maquinarias.

Por lo cual los beneficios que obtendrá por la implementación de dicha técnica predictiva en el análisis de los equipos rotantes, se verán traducidos en mayor conocimiento del comportamiento vibracional, mejores decisiones, mayor rentabilidad y por sobre todo mejor confiabilidad.
Autor: Lic. Martín Lémoli
Capacitador - Analista de Vibraciones Categoría 3
Correo: mlemoli@hotmail.com
Dinos qué te ha parecido el artículo
Artículos recomendados
Calibración de válvulas en Motores Diésel de velocidad media

¿Qué implica la mejora continua en la gestión de activos?

¿Cómo serán las fábricas dentro de una década? La transformación progresiva hacia la Smart Factory

Curso SAP

Publica tu artículo en la revista #1 de Mantenimiento Industrial
Publicar un artículo en la revista es gratis, no tiene costo.
Solo debes asegurarte que no sea un artículo comercial.
¿Qué esperas?
O envía tu artículo directo: articulos@predictiva21.com
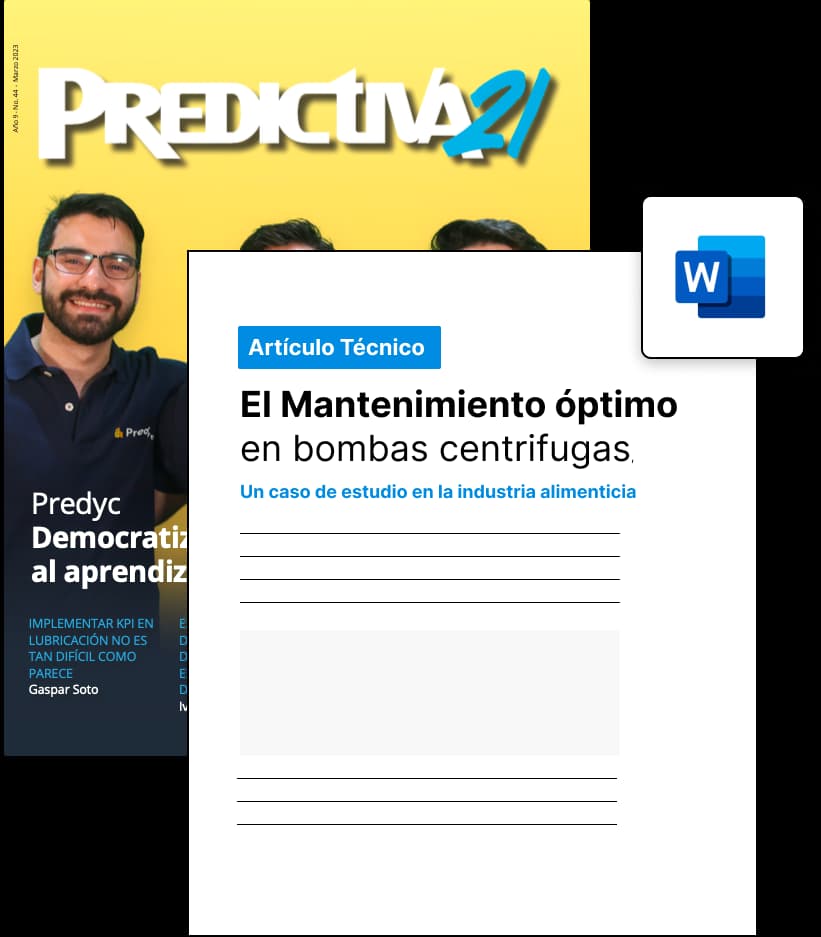
Uso del análisis de vibraciones en el mantenimiento Predictivo de maquinas rotantes
Articulo 12 de abril de 2019Hoy en día en la mayoría de las plantas industriales tienen como objetivo principal elevar el nivel de confiabilidad del área de mantenimiento y por ende el de sus equipos, ya que ello les garantiza mantener un nivel de productividad considerable de sus máquinas rotantes. Por lo tanto, escogen dentro de los distintos tipos de mantenimiento a él predictivo, ya que el mismo les brinda las herramientas necesarias para obtener una gran cantidad de información útil al momento de diagnosticar las máquinas, y determinar las posibles fallas incipientes, que se podrían presentar en las mismas.

Los pasos en que se basa el programa de mantenimiento predictivo siguen una secuencia lógica desde que se detecta un problema, se estudia, se encuentra su causa y finalmente se decide la posibilidad de corregirlo en el momento oportuno con la máxima eficiencia posible.

Los pasos fundamentales son tres:
- Detección: Reconocimiento del problema.
- Análisis: Localización de la causa del problema.
- Corrección: Encontrar el momento y forma de solucionar el problema.
Existen algunos estudios que determinan los valores promedio aproximados de reducción de costos al implementar un programa de mantenimiento predictivo, que serían los siguientes para cada rubro:
- Costos de mantenimiento, reducción de hasta un 50%.
- Reducción de fallas inesperadas, hasta un 55%.
- Reparación del equipo y tiempos del reacondicionamiento, reducción hasta un 60%.
- Reducción del stock de las piezas de repuesto, hasta un 30%.
- Aumento de tiempo medio de funcionamiento de la maquinaria sin paradas, reducción hasta un 30%.
- Reducción de consumo energéticos, hasta un 10%.
Además, en el mantenimiento predictivo existen varias técnicas que nos ayudan a realizar el Análisis Causa-Raíz de algún problema presente en nuestra máquina rotante, con el objetivo de mejorar el desempeño de las máquinas.
Entre las técnicas predictivas más usadas están las siguientes, Análisis de Aceite, Termografía Infrarroja y unas de las más utilizadas como es el Análisis de Vibraciones.

Esta técnica forma parte fundamental en la aplicación de un programa de mantenimiento predictivo ya que nos ayuda a diagnosticar las distintas causa-raíz de cada uno de los problemas presentes y nos brinda una completa información acerca del estado de cada uno de los elementos rotantes, para no tener paradas imprevistas de los equipos.
Concepto de vibración
Se dice que un cuerpo vibra cuando experimenta cambios alternativos, de tal modo que sus puntos oscilen sincrónicamente en torno a sus posiciones de equilibrio, sin que el campo cambie de lugar.
Como otro concepto de vibración, se puede decir que es un intercambio de energía cinética en cuerpos con rigidez y masa finitas, el cual surge de una entrada de energía dependiente del tiempo.
Este intercambio de energía puede ser producido por algunas de las siguientes causas:
- Desequilibrios estáticos o dinámicos.
- Desalienación en máquinas rotatorias.
- Circulación de Fluidos.
- Energía Electromagnética.
- Solturas Mecánicas.
- Resonancias.
- Excentricidades.

Cuando se realizan los análisis de vibraciones la idea básica es buscar la existencia de una fuerza excitatriz, o de excitación, en el sistema estudiado, la cual genera una perturbación en el estado de funcionamiento normal de la máquina, lo que se traduce en una falla presente en la maquina bajo objeto de estudio, por lo se debe diagnosticar acerca del origen de la misma y como contrarrestarla para minimizar la presencia de esa fuerza excitatriz. El diagnostico de las posibles fuentes de perturbación en nuestra maquina rotante, es debido al uso del algoritmo computacional llamado Transformada Rápida de Fourier (FFT).

Sea cualquiera la causa de la vibración, su reducción es necesaria debido a diversas razones entre las cuales tenemos:
- La vibraciones está íntimamente relacionada con la confiabilidad de la maquina rotante.
- Disminuye la vida útil de los rodamientos.
- La excesiva vibración puede limitar la velocidad de procesamiento.
- La vibración es responsable de la pobre calidad de los productos elaborados.
- La vibración de maquinarias puede resultar en radiación de ruido.
- La vibración puede alcanzar a otros instrumentos de precisión de otras fuentes, y causar fallas de funcionamiento.
Hoy en día en toda industria es muy difícil evitar la presencia de las vibraciones, las cuales suelen producirse por la presencia de efectos dinámicos causando el aumentando en la severidad de las amplitudes de vibración. Algunas de las causas que se podrían enunciar serían las siguientes: tolerancias y/o holguras de fabricación, contactos entre partes del rodamiento, fricción entre las piezas de las maquinas giratorios y/o las desalineaciones existentes, entre otros.
Por ende, se lograría diagnosticar las posibles fallas a futuro cumpliendo con el objetivo principal del mantenimiento predictivo, el cual no es más que predecir la ruptura o parada imprevista de las maquinarias.

Por lo cual los beneficios que obtendrá por la implementación de dicha técnica predictiva en el análisis de los equipos rotantes, se verán traducidos en mayor conocimiento del comportamiento vibracional, mejores decisiones, mayor rentabilidad y por sobre todo mejor confiabilidad.
Autor: Lic. Martín Lémoli
Capacitador - Analista de Vibraciones Categoría 3
Correo: mlemoli@hotmail.com
Dinos qué te ha parecido el artículo
Artículos recomendados
¿Cómo serán las fábricas dentro de una década? La transformación progresiva hacia la Smart Factory

Experiencias en el desarrollo de Análisis de Confiabilidad, Disponibilidad y Mantenibilidad (Análisis RAM).

Análisis de causa raíz

Mantenimiento Tercerizado - Beneficios y Consideraciones

Publica tu artículo en la revista #1 de Mantenimiento Industrial
Publicar un artículo en la revista es gratis, no tiene costo.
Solo debes asegurarte que no sea un artículo comercial.
¿Qué esperas?
O envía tu artículo directo: articulos@predictiva21.com
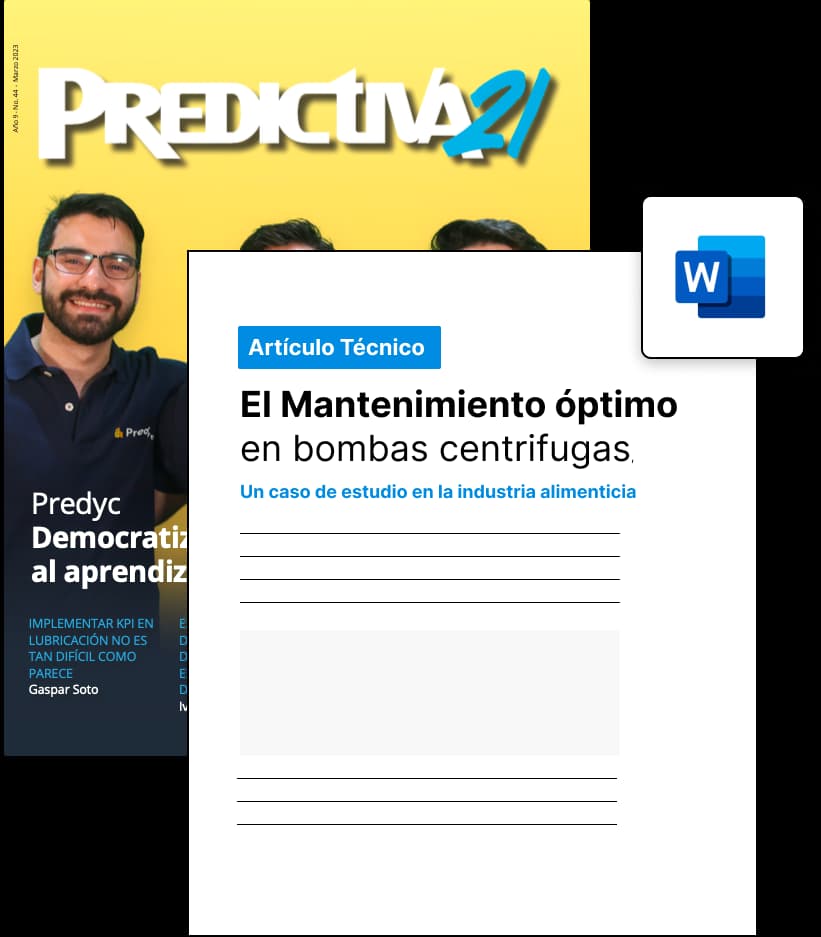