Implementación exitosa de Mantenimiento Lean en la Industria Manufacturera
Articulo29 de marzo de 2024

Introducción
Cada día el Mantenimiento Lean se ha convertido en una herramienta fundamental para mejorar tanto la eficiencia como la productividad en la industria manufacturera. Esta metodología, originada en el Sistema de Producción de Toyota, se enfoca en eliminar el desperdicio y optimizar los procesos de mantenimiento. En este artículo, abordaremos tanto los beneficios como las mejores prácticas para implementar con éxito el Mantenimiento Lean en la industria manufacturera de tal forma que se logren obtener los máximos beneficios en su organización.
¿Qué es Lean?
Cuando hablamos de Lean nos referimos a algo esbelto, liviano, sin grasa. Ahí radica la importancia de tener muy clara la forma de gestionar las empresas de tal manera que ellas sean capaces de poder reaccionar ante cualquier evento sin que afecte su permanencia en el mercado y poder ser sostenibles en el tiempo.
Hablar de Lean es basarnos en las prácticas del “Toyota Production System” con el fin de pensar en el cliente para poderle crear el máximo valor por medio de diferentes vías tales como la reducción de los desperdicios, tiempo, energía y esfuerzo.
De acuerdo con lo anterior podemos identificar los cinco (5) Principios Lean los cuales son:

Principios Lean
¿Qué es Mantenimiento Lean?
El Mantenimiento Lean es una filosofía que busca eliminar las actividades innecesarias y el desperdicio en los procesos de mantenimiento. Se basa en los principios del Lean Manufacturing, que se centra en la reducción de los tiempos de espera, los movimientos innecesarios y la sobreproducción. Al aplicar estos principios al mantenimiento, las empresas pueden mejorar la eficiencia, reducir los costos y aumentar la satisfacción del cliente.
Fundamentos de Mantenimiento Lean
- Definición y Principios Básicos:
El Mantenimiento Lean se define como “un sistema que consiste en realizar operaciones de mantenimiento proactivas que estén alineadas con las buenas prácticas de la metodología TPM (Mantenimiento Productivo Total). Estas prácticas tienen como objetivo optimizar los procesos productivos para eliminar mermas relacionadas con el mal estado o funcionamiento de la maquinaria, dispositivos o equipos de fabricación”.
El objetivo del Mantenimiento Lean es eliminar todo tipo de desperdicio que haga ineficiente la operación las cuales no agregan valor.
Basados en los Principios Lean identificaremos los cinco principios del Mantenimiento Lean los cuales son:
- Generar valor al cliente: en el caso de la industria manufacturera generalmente el cliente es el área de producción. Es muy importante tener en cuenta que el cliente es quien define si agrega o no agrega valor el servicio recibido y se deben identificar las actividades, la planeación y personal de mantenimiento requerido para atender sus compromisos frente a su cliente.
- Comprender el funcionamiento del proceso y métodos que añaden valor a mantenimiento: las áreas de mantenimiento deben conocer muy bien el proceso sobre el cuál ellos interactúan y los métodos de la forma como intervienen los equipos en el momento requerido. No tener en cuenta los anteriores puntos solo conducen a un mantenimiento desenfocado que en vez de solucionar lo que generan son más problemas a la organización. Es importante la elaboración del “Maintenance Value Stream Map” donde se identifican los desperdicios que se generan y mediante indicadores se determina la efectividad de la gestión de mantenimiento hacia manufactura. (OEE, MTBF, MTTR, entre otros).
- Facilitar el flujo de trabajo aplicando metodologías apropiadas: las áreas de mantenimiento son críticas en los procesos de manufactura, pero en muchas ocasiones dichas áreas no cuentan con metodologías que les permita ser ágiles e innovadoras en sus procesos, retardando la entrega efectiva de sus entregables y ocasionando una restricción que desencadena en sobrecostos, desperdicios e incumplimientos al cliente final.
- Mantenimiento pull para garantizar el just in time (cumplimiento de los tiempos de entrega por reparación): lamentablemente es normal escuchar que si mantenimiento dice que entrega la máquina reparada en dos (2) horas entonces significa que en realidad la entregará en cuatro (4) horas. El cumplimiento de los tiempos de entrega por reparación debe ser lo más ajustado posible porque de esto depende muchas decisiones que debe tomar manufactura tales como programación de entregas, despachos, programación de personal, etc.
- Objetivo: la perfección a través de la mejora continua. La mejora continua es el resultado de todas aquellas acciones que las áreas de mantenimiento realizan día a día convirtiéndola en un estilo de vida. Esta mejora continua debe ser soportada mediante la estandarización de sus procesos por medio de pequeños pasos sostenibles en el tiempo y el desarrollo del equipo, empleados y empleadores con respecto a las prácticas Lean en el mantenimiento.
Ejemplos de aplicaciones exitosas:
- Toyota: La empresa automotriz Toyota es conocida por su implementación exitosa de Lean Maintenance. Han aplicado principios como el mantenimiento preventivo y predictivo para minimizar el tiempo de inactividad de las máquinas y optimizar la eficiencia de la producción.
- General Electric: GE ha utilizado Lean Maintenance para mejorar la confiabilidad de sus equipos y reducir los costos de mantenimiento. Han implementado técnicas como el análisis de causa raíz y la planificación de mantenimiento basada en datos para maximizar la disponibilidad de la maquinaria.
- Boeing: En la industria aeroespacial, Boeing ha aplicado Lean Maintenance para optimizar la gestión de activos y aumentar la seguridad en sus operaciones. Han adoptado enfoques como el mantenimiento centrado en la confiabilidad para garantizar un alto rendimiento de sus aviones.
- Nissan: Al igual que Toyota, Nissan ha utilizado Lean Maintenance para mejorar la eficiencia de sus procesos de fabricación. Han implementado prácticas como el mantenimiento autónomo, donde los operadores son responsables del cuidado básico de los equipos, lo que ha llevado a una reducción significativa de los tiempos de inactividad no planificado.
- Caterpillar: La empresa de maquinaria pesada Caterpillar ha aplicado Lean Maintenance para optimizar la gestión de su flota de equipos. Han utilizado herramientas como el análisis de riesgos y la programación de mantenimiento basada en la vida útil de los componentes para maximizar la disponibilidad y prolongar la vida útil de sus máquinas
Beneficios del Mantenimiento Lean
Los beneficios del Mantenimiento Lean cada vez se hacen más relevantes dentro de las organizaciones y está en manos de cada una de ellas sacar el máximo provecho. Dentro de estos beneficios tenemos:
- Reducción de costos operativos y de mantenimiento
Cuando en las empresas se reducen o se disminuyen los tiempos perdidos por paros de mantenimiento permite un beneficio de tipo económico en el ahorro de dinero en reparaciones con altos costos y pérdidas de producción. De igual forma se optimiza el costo de la mano de obra y toda aquella cantidad de repuestos requeridos para la maquinaria.
- Mejora de la eficiencia
Este es uno de los beneficios más relevantes que se identifican con el Mantenimiento Lean al mejorarse la eficiencia de los procesos sobre los cuales estamos interviniendo.
El objetivo es anticiparnos identificar las posibles fallas que se puedan presentar en determinado momento y de esta forma evitamos que las fallas en caso de darse sean costosas y de alto impacto.
- Incremento de la disponibilidad de los equipos
Cuando optimizamos los procesos y las actividades de mantenimiento de inmediato se ve favorecida la disponibilidad de la maquinaria para que sea utilizada en el momento que se requiera y de esta forma podamos responder de forma efectiva a los clientes convirtiéndose en un factor diferenciador.
- Productos con mejor calidad
Cuando la maquinaria y equipos se encuentran en óptimas condiciones esto garantizará en gran proporción que la calidad del producto cada vez sea mejor y se evite rechazos por parte del cliente por problemas de calidad y su satisfacción cada vez sea mayor.
- Fortalecimiento de la cultura de la mejora continua
En muchas ocasiones se trabaja la cultura de la mejora continua solo a nivel de las áreas productivas dejando por fuera al área de mantenimiento mientras que al implementar Mantenimiento Lean el personal de mantenimiento se une con los demás equipos de otras áreas buscando siempre mejores maneras de hacer las cosas permitiendo una mejora constante de hacer las cosas innovando de forma permanente.
- Optimización del tiempo de ciclo
Al fortalecerse cada vez más las labores de mantenimiento conlleva por sí a que los tiempos de ciclo se reduzcan porque los tiempos perdidos cada vez serán menores y de esa forma la respuesta de las empresas hacia los clientes será mucho más rápida logrando cumplir los tiempos de entrega.
- Reducción de la accidentalidad
Mediante el Mantenimiento Lean los equipos serán más confiables por lo que cada vez se requiere intervenir menos a los equipos de forma no planeada y esto permitirá que los accidentes se reduzcan y el clima laboral se mejore arrojando una mejora en la productividad y moral de sus trabajadores.
- Reducción del impacto al medio ambiente
Al tener equipos y maquinaria operando eficientemente el impacto es directo a la reducción del consumo de energía, agua y materiales. De igual forma los equipos van a durar más tiempo por lo que se aplaza la compra de los mismos lo cual redunda en la disminución de residuos y disminución de la huella ambiental contribuyendo a la sostenibilidad.
- Mejora de la planificación y programación del mantenimiento
Con el fortalecimiento de las herramientas y técnicas de mantenimiento se optimiza la programación y asignación de recursos pasando de forma reactiva a una forma planificada conllevando a la mejora de la eficiencia global de toda la operación.
- Reducción de inventarios de repuestos
A medida que los tiempos de paro por falla de maquinaria se reduzcan de igual forma se reducen los costos correspondientes a altos niveles de inventario de repuestos, costos de almacenamiento y reposición permitiendo que el capital que antes se tenía en estos altos niveles de inventario ya se redireccionen a otras áreas de las empresas donde se requieran recursos.
- Mejora en la gestión del conocimiento
Al implementar mantenimiento lean se van a estandarizar las actividades, se elaboran lecciones de un punto, se elaboran los manuales, se elaboran los procedimientos operativos estándar, etc., lo cual permitirá que el conocimiento no se pierda en la organización logrando el desarrollo de nuevas generaciones de personal operativo fortalecido.
Pasos para la implementación del Mantenimiento Lean
- Evaluación inicial
El objetivo de esta evaluación inicial es conocer de forma detallada cómo es la operación actual del departamento de mantenimiento. Dentro de esta evaluación se debe identificar todos los desperdicios actuales y las oportunidades de mejora que puedan presentarse. Es muy importante la participación de todo el personal mas no realizar dicha evaluación solo con los cargos directivos.
- Definición de objetivos
Tanto los objetivos como las metas que se definan deben ser claros y medibles y siempre estar alineados con los objetivos estratégicos de la empresa. Para su definición se recomienda utilizar la Técnica SMART. (específicos, medibles, alcanzables, retadores y en un tiempo definido). ¿Qué quiere lograr con el Mantenimiento Lean?
- Evaluación de equipos críticos
Mediante una matriz de priorización determinar cuáles son los equipos críticos para la producción y en caso de fallar cuál sería su impacto.
- Elaboración del plan de implementación
En la elaboración del plan de implementación debe definir el alcance del proyecto, los recursos necesarios y el cronograma a seguir.
- Formación y capacitación
Se debe establecer el cronograma de capacitación a todo el personal fundamentado en los Principios Lean, tipos de pérdidas y desperdicios y las herramientas específicas de Mantenimiento Lean.
- Identificación de valor
En esta parte es muy importante identificar todas aquellas actividades que agregan valor y todas aquellas actividades que no agregan valor. Tener en cuenta que quien define el valor es el cliente.
- Reducción o eliminación de desperdicios
Una vez identificadas las actividades que no agregan valor en las labores de mantenimiento se procede con los planes de acción para eliminar las actividades y procesos que no son necesarios y que no agregan valor al cliente final.
- Implementar el ciclo PHVA
La importancia de implementar el ciclo de mejora PHVA (planear, hacer, verificar, actuar) es garantizar la mejora continua del Mantenimiento Lean, permitiendo la optimización permanente de los procesos del área de mantenimiento.
- Definir los Indicadores Clave de Desempeño (KPI´s)
Al definir los KPI´s para el área de mantenimiento podemos establecer la línea base y la línea meta a lograr y realizar su seguimiento y actuar en el momento requerido.
- Implementar gerenciamiento diario
El objetivo del gerenciamiento diario es que el personal de mantenimiento se reúna para conocer de forma directa cómo ha estado el desempeño de la maquinaria en el turno comparado con el rendimiento esperado y en caso de tener que tomar correctivos estos se realizan de forma inmediata.
- Desarrollar la cultura de la mejora continua
Permitir que el personal de mantenimiento sea actualizado capacitándolo permanentemente y ellos puedan identificar y proponer soluciones que conlleven a la mejora continua de los procesos de su área.
- Integración con otras áreas funcionales
Una vez maduradas las anteriores etapas, se debe fortalecer la integración del personal de mantenimiento con las demás áreas de la empresa lo cual permitirá fortalecer y optimizar la cadena de valor.
Conclusiones y recomendaciones
Implementar Lean en Mantenimiento puede llevar a una operación más eficiente, rentable y segura, lo que a su vez puede mejorar la satisfacción de los clientes internos y externos. De igual forma dicha implementación genera un valioso aporte a la mejora continua de la organización.
Se recomienda que la implementación de Mantenimiento Lean sea ejecutada por un equipo de trabajo sólido con el apoyo incondicional de la Gerencia porque dar pasos en falso puede desencadenar en la pérdida de confianza de los empelados frente a dichas metodologías o filosofías y generar una resistencia al cambio para futuras mejoras.
Cibergrafía:
- Qué es Lean Maintenance – Rafael Vega
- Propuesta de Implementación de metodología lean para el mantenimiento del equipo crítico en el área acería de empresa del rubro siderúrgico – Robles Gutiérrez Alonso
- Gerenciamiento Diario
- Lean Management: ¿cómo aplicarlo al mantenimiento?
- Metodología LEAN en el Mantenimiento
Autor: Carlos H Betancourth C
Ingeniero Industrial especialista en Gerencia de Producción. Consultor de Mejora Continua – Director de Costos y Productividad – Instructor y Speaker Internacional
Dinos qué te ha parecido el artículo
Artículos recomendados
Probar, Detectar y Aislar – Aplicado al Mantenimiento. (Aplicación del Método recomendado por la OMS para la pandemia de COVID-19 “Probar, Detectar y Aislar” al mantenimiento).

Carrera técnica en mantenimiento industrial

Selección de Potencia del Motor Eléctrico en Compresores Reciprocantes de Múltiples Etapas

Investigación de la aplicación de notación BPMN en Paradas de Planta de Industria Petroquímica de la Zona Libre de Manaus

Publica tu artículo en la revista #1 de Mantenimiento Industrial
Publicar un artículo en la revista es gratis, no tiene costo.
Solo debes asegurarte que no sea un artículo comercial.
¿Qué esperas?
O envía tu artículo directo: articulos@predictiva21.com
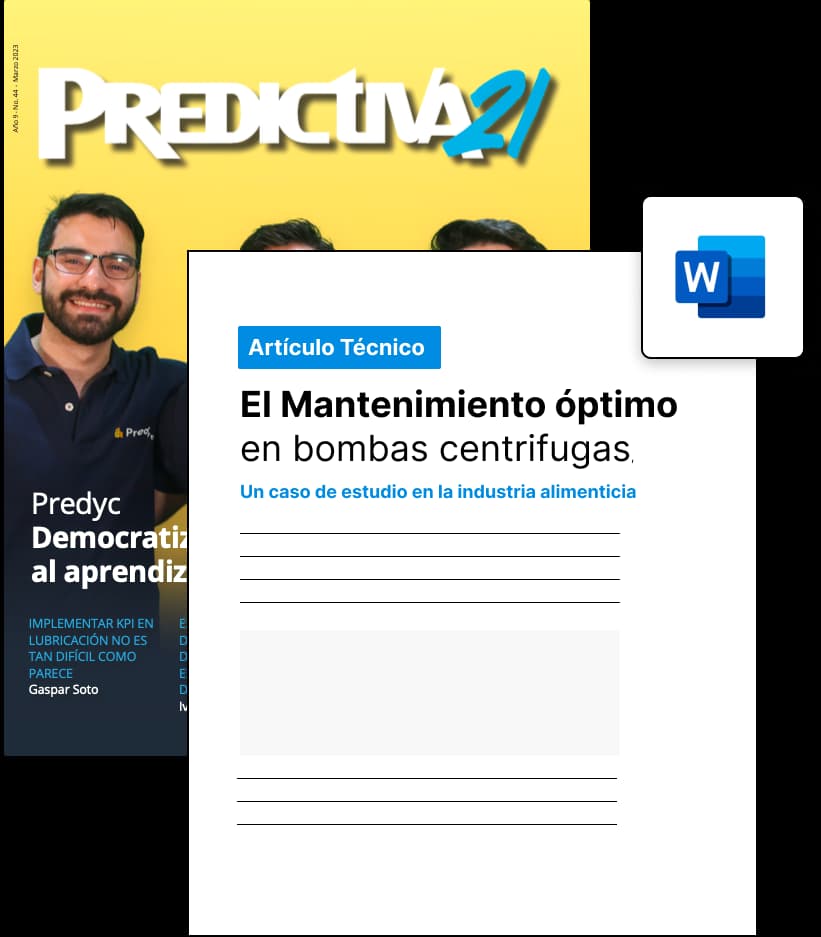
Implementación exitosa de Mantenimiento Lean en la Industria Manufacturera
Articulo 29 de marzo de 2024
Introducción
Cada día el Mantenimiento Lean se ha convertido en una herramienta fundamental para mejorar tanto la eficiencia como la productividad en la industria manufacturera. Esta metodología, originada en el Sistema de Producción de Toyota, se enfoca en eliminar el desperdicio y optimizar los procesos de mantenimiento. En este artículo, abordaremos tanto los beneficios como las mejores prácticas para implementar con éxito el Mantenimiento Lean en la industria manufacturera de tal forma que se logren obtener los máximos beneficios en su organización.
¿Qué es Lean?
Cuando hablamos de Lean nos referimos a algo esbelto, liviano, sin grasa. Ahí radica la importancia de tener muy clara la forma de gestionar las empresas de tal manera que ellas sean capaces de poder reaccionar ante cualquier evento sin que afecte su permanencia en el mercado y poder ser sostenibles en el tiempo.
Hablar de Lean es basarnos en las prácticas del “Toyota Production System” con el fin de pensar en el cliente para poderle crear el máximo valor por medio de diferentes vías tales como la reducción de los desperdicios, tiempo, energía y esfuerzo.
De acuerdo con lo anterior podemos identificar los cinco (5) Principios Lean los cuales son:

Principios Lean
¿Qué es Mantenimiento Lean?
El Mantenimiento Lean es una filosofía que busca eliminar las actividades innecesarias y el desperdicio en los procesos de mantenimiento. Se basa en los principios del Lean Manufacturing, que se centra en la reducción de los tiempos de espera, los movimientos innecesarios y la sobreproducción. Al aplicar estos principios al mantenimiento, las empresas pueden mejorar la eficiencia, reducir los costos y aumentar la satisfacción del cliente.
Fundamentos de Mantenimiento Lean
- Definición y Principios Básicos:
El Mantenimiento Lean se define como “un sistema que consiste en realizar operaciones de mantenimiento proactivas que estén alineadas con las buenas prácticas de la metodología TPM (Mantenimiento Productivo Total). Estas prácticas tienen como objetivo optimizar los procesos productivos para eliminar mermas relacionadas con el mal estado o funcionamiento de la maquinaria, dispositivos o equipos de fabricación”.
El objetivo del Mantenimiento Lean es eliminar todo tipo de desperdicio que haga ineficiente la operación las cuales no agregan valor.
Basados en los Principios Lean identificaremos los cinco principios del Mantenimiento Lean los cuales son:
- Generar valor al cliente: en el caso de la industria manufacturera generalmente el cliente es el área de producción. Es muy importante tener en cuenta que el cliente es quien define si agrega o no agrega valor el servicio recibido y se deben identificar las actividades, la planeación y personal de mantenimiento requerido para atender sus compromisos frente a su cliente.
- Comprender el funcionamiento del proceso y métodos que añaden valor a mantenimiento: las áreas de mantenimiento deben conocer muy bien el proceso sobre el cuál ellos interactúan y los métodos de la forma como intervienen los equipos en el momento requerido. No tener en cuenta los anteriores puntos solo conducen a un mantenimiento desenfocado que en vez de solucionar lo que generan son más problemas a la organización. Es importante la elaboración del “Maintenance Value Stream Map” donde se identifican los desperdicios que se generan y mediante indicadores se determina la efectividad de la gestión de mantenimiento hacia manufactura. (OEE, MTBF, MTTR, entre otros).
- Facilitar el flujo de trabajo aplicando metodologías apropiadas: las áreas de mantenimiento son críticas en los procesos de manufactura, pero en muchas ocasiones dichas áreas no cuentan con metodologías que les permita ser ágiles e innovadoras en sus procesos, retardando la entrega efectiva de sus entregables y ocasionando una restricción que desencadena en sobrecostos, desperdicios e incumplimientos al cliente final.
- Mantenimiento pull para garantizar el just in time (cumplimiento de los tiempos de entrega por reparación): lamentablemente es normal escuchar que si mantenimiento dice que entrega la máquina reparada en dos (2) horas entonces significa que en realidad la entregará en cuatro (4) horas. El cumplimiento de los tiempos de entrega por reparación debe ser lo más ajustado posible porque de esto depende muchas decisiones que debe tomar manufactura tales como programación de entregas, despachos, programación de personal, etc.
- Objetivo: la perfección a través de la mejora continua. La mejora continua es el resultado de todas aquellas acciones que las áreas de mantenimiento realizan día a día convirtiéndola en un estilo de vida. Esta mejora continua debe ser soportada mediante la estandarización de sus procesos por medio de pequeños pasos sostenibles en el tiempo y el desarrollo del equipo, empleados y empleadores con respecto a las prácticas Lean en el mantenimiento.
Ejemplos de aplicaciones exitosas:
- Toyota: La empresa automotriz Toyota es conocida por su implementación exitosa de Lean Maintenance. Han aplicado principios como el mantenimiento preventivo y predictivo para minimizar el tiempo de inactividad de las máquinas y optimizar la eficiencia de la producción.
- General Electric: GE ha utilizado Lean Maintenance para mejorar la confiabilidad de sus equipos y reducir los costos de mantenimiento. Han implementado técnicas como el análisis de causa raíz y la planificación de mantenimiento basada en datos para maximizar la disponibilidad de la maquinaria.
- Boeing: En la industria aeroespacial, Boeing ha aplicado Lean Maintenance para optimizar la gestión de activos y aumentar la seguridad en sus operaciones. Han adoptado enfoques como el mantenimiento centrado en la confiabilidad para garantizar un alto rendimiento de sus aviones.
- Nissan: Al igual que Toyota, Nissan ha utilizado Lean Maintenance para mejorar la eficiencia de sus procesos de fabricación. Han implementado prácticas como el mantenimiento autónomo, donde los operadores son responsables del cuidado básico de los equipos, lo que ha llevado a una reducción significativa de los tiempos de inactividad no planificado.
- Caterpillar: La empresa de maquinaria pesada Caterpillar ha aplicado Lean Maintenance para optimizar la gestión de su flota de equipos. Han utilizado herramientas como el análisis de riesgos y la programación de mantenimiento basada en la vida útil de los componentes para maximizar la disponibilidad y prolongar la vida útil de sus máquinas
Beneficios del Mantenimiento Lean
Los beneficios del Mantenimiento Lean cada vez se hacen más relevantes dentro de las organizaciones y está en manos de cada una de ellas sacar el máximo provecho. Dentro de estos beneficios tenemos:
- Reducción de costos operativos y de mantenimiento
Cuando en las empresas se reducen o se disminuyen los tiempos perdidos por paros de mantenimiento permite un beneficio de tipo económico en el ahorro de dinero en reparaciones con altos costos y pérdidas de producción. De igual forma se optimiza el costo de la mano de obra y toda aquella cantidad de repuestos requeridos para la maquinaria.
- Mejora de la eficiencia
Este es uno de los beneficios más relevantes que se identifican con el Mantenimiento Lean al mejorarse la eficiencia de los procesos sobre los cuales estamos interviniendo.
El objetivo es anticiparnos identificar las posibles fallas que se puedan presentar en determinado momento y de esta forma evitamos que las fallas en caso de darse sean costosas y de alto impacto.
- Incremento de la disponibilidad de los equipos
Cuando optimizamos los procesos y las actividades de mantenimiento de inmediato se ve favorecida la disponibilidad de la maquinaria para que sea utilizada en el momento que se requiera y de esta forma podamos responder de forma efectiva a los clientes convirtiéndose en un factor diferenciador.
- Productos con mejor calidad
Cuando la maquinaria y equipos se encuentran en óptimas condiciones esto garantizará en gran proporción que la calidad del producto cada vez sea mejor y se evite rechazos por parte del cliente por problemas de calidad y su satisfacción cada vez sea mayor.
- Fortalecimiento de la cultura de la mejora continua
En muchas ocasiones se trabaja la cultura de la mejora continua solo a nivel de las áreas productivas dejando por fuera al área de mantenimiento mientras que al implementar Mantenimiento Lean el personal de mantenimiento se une con los demás equipos de otras áreas buscando siempre mejores maneras de hacer las cosas permitiendo una mejora constante de hacer las cosas innovando de forma permanente.
- Optimización del tiempo de ciclo
Al fortalecerse cada vez más las labores de mantenimiento conlleva por sí a que los tiempos de ciclo se reduzcan porque los tiempos perdidos cada vez serán menores y de esa forma la respuesta de las empresas hacia los clientes será mucho más rápida logrando cumplir los tiempos de entrega.
- Reducción de la accidentalidad
Mediante el Mantenimiento Lean los equipos serán más confiables por lo que cada vez se requiere intervenir menos a los equipos de forma no planeada y esto permitirá que los accidentes se reduzcan y el clima laboral se mejore arrojando una mejora en la productividad y moral de sus trabajadores.
- Reducción del impacto al medio ambiente
Al tener equipos y maquinaria operando eficientemente el impacto es directo a la reducción del consumo de energía, agua y materiales. De igual forma los equipos van a durar más tiempo por lo que se aplaza la compra de los mismos lo cual redunda en la disminución de residuos y disminución de la huella ambiental contribuyendo a la sostenibilidad.
- Mejora de la planificación y programación del mantenimiento
Con el fortalecimiento de las herramientas y técnicas de mantenimiento se optimiza la programación y asignación de recursos pasando de forma reactiva a una forma planificada conllevando a la mejora de la eficiencia global de toda la operación.
- Reducción de inventarios de repuestos
A medida que los tiempos de paro por falla de maquinaria se reduzcan de igual forma se reducen los costos correspondientes a altos niveles de inventario de repuestos, costos de almacenamiento y reposición permitiendo que el capital que antes se tenía en estos altos niveles de inventario ya se redireccionen a otras áreas de las empresas donde se requieran recursos.
- Mejora en la gestión del conocimiento
Al implementar mantenimiento lean se van a estandarizar las actividades, se elaboran lecciones de un punto, se elaboran los manuales, se elaboran los procedimientos operativos estándar, etc., lo cual permitirá que el conocimiento no se pierda en la organización logrando el desarrollo de nuevas generaciones de personal operativo fortalecido.
Pasos para la implementación del Mantenimiento Lean
- Evaluación inicial
El objetivo de esta evaluación inicial es conocer de forma detallada cómo es la operación actual del departamento de mantenimiento. Dentro de esta evaluación se debe identificar todos los desperdicios actuales y las oportunidades de mejora que puedan presentarse. Es muy importante la participación de todo el personal mas no realizar dicha evaluación solo con los cargos directivos.
- Definición de objetivos
Tanto los objetivos como las metas que se definan deben ser claros y medibles y siempre estar alineados con los objetivos estratégicos de la empresa. Para su definición se recomienda utilizar la Técnica SMART. (específicos, medibles, alcanzables, retadores y en un tiempo definido). ¿Qué quiere lograr con el Mantenimiento Lean?
- Evaluación de equipos críticos
Mediante una matriz de priorización determinar cuáles son los equipos críticos para la producción y en caso de fallar cuál sería su impacto.
- Elaboración del plan de implementación
En la elaboración del plan de implementación debe definir el alcance del proyecto, los recursos necesarios y el cronograma a seguir.
- Formación y capacitación
Se debe establecer el cronograma de capacitación a todo el personal fundamentado en los Principios Lean, tipos de pérdidas y desperdicios y las herramientas específicas de Mantenimiento Lean.
- Identificación de valor
En esta parte es muy importante identificar todas aquellas actividades que agregan valor y todas aquellas actividades que no agregan valor. Tener en cuenta que quien define el valor es el cliente.
- Reducción o eliminación de desperdicios
Una vez identificadas las actividades que no agregan valor en las labores de mantenimiento se procede con los planes de acción para eliminar las actividades y procesos que no son necesarios y que no agregan valor al cliente final.
- Implementar el ciclo PHVA
La importancia de implementar el ciclo de mejora PHVA (planear, hacer, verificar, actuar) es garantizar la mejora continua del Mantenimiento Lean, permitiendo la optimización permanente de los procesos del área de mantenimiento.
- Definir los Indicadores Clave de Desempeño (KPI´s)
Al definir los KPI´s para el área de mantenimiento podemos establecer la línea base y la línea meta a lograr y realizar su seguimiento y actuar en el momento requerido.
- Implementar gerenciamiento diario
El objetivo del gerenciamiento diario es que el personal de mantenimiento se reúna para conocer de forma directa cómo ha estado el desempeño de la maquinaria en el turno comparado con el rendimiento esperado y en caso de tener que tomar correctivos estos se realizan de forma inmediata.
- Desarrollar la cultura de la mejora continua
Permitir que el personal de mantenimiento sea actualizado capacitándolo permanentemente y ellos puedan identificar y proponer soluciones que conlleven a la mejora continua de los procesos de su área.
- Integración con otras áreas funcionales
Una vez maduradas las anteriores etapas, se debe fortalecer la integración del personal de mantenimiento con las demás áreas de la empresa lo cual permitirá fortalecer y optimizar la cadena de valor.
Conclusiones y recomendaciones
Implementar Lean en Mantenimiento puede llevar a una operación más eficiente, rentable y segura, lo que a su vez puede mejorar la satisfacción de los clientes internos y externos. De igual forma dicha implementación genera un valioso aporte a la mejora continua de la organización.
Se recomienda que la implementación de Mantenimiento Lean sea ejecutada por un equipo de trabajo sólido con el apoyo incondicional de la Gerencia porque dar pasos en falso puede desencadenar en la pérdida de confianza de los empelados frente a dichas metodologías o filosofías y generar una resistencia al cambio para futuras mejoras.
Cibergrafía:
- Qué es Lean Maintenance – Rafael Vega
- Propuesta de Implementación de metodología lean para el mantenimiento del equipo crítico en el área acería de empresa del rubro siderúrgico – Robles Gutiérrez Alonso
- Gerenciamiento Diario
- Lean Management: ¿cómo aplicarlo al mantenimiento?
- Metodología LEAN en el Mantenimiento
Autor: Carlos H Betancourth C
Ingeniero Industrial especialista en Gerencia de Producción. Consultor de Mejora Continua – Director de Costos y Productividad – Instructor y Speaker Internacional
Dinos qué te ha parecido el artículo
Artículos recomendados
17.1.- Control por Regulación de Flujo

Desafíos que enfrentan los Gerentes de Mantenimiento

Aprende a calcular la rotación de inventario de refacciones críticas de tu almacén de mantenimiento en tu empresa

Boroscopio

Publica tu artículo en la revista #1 de Mantenimiento Industrial
Publicar un artículo en la revista es gratis, no tiene costo.
Solo debes asegurarte que no sea un artículo comercial.
¿Qué esperas?
O envía tu artículo directo: articulos@predictiva21.com
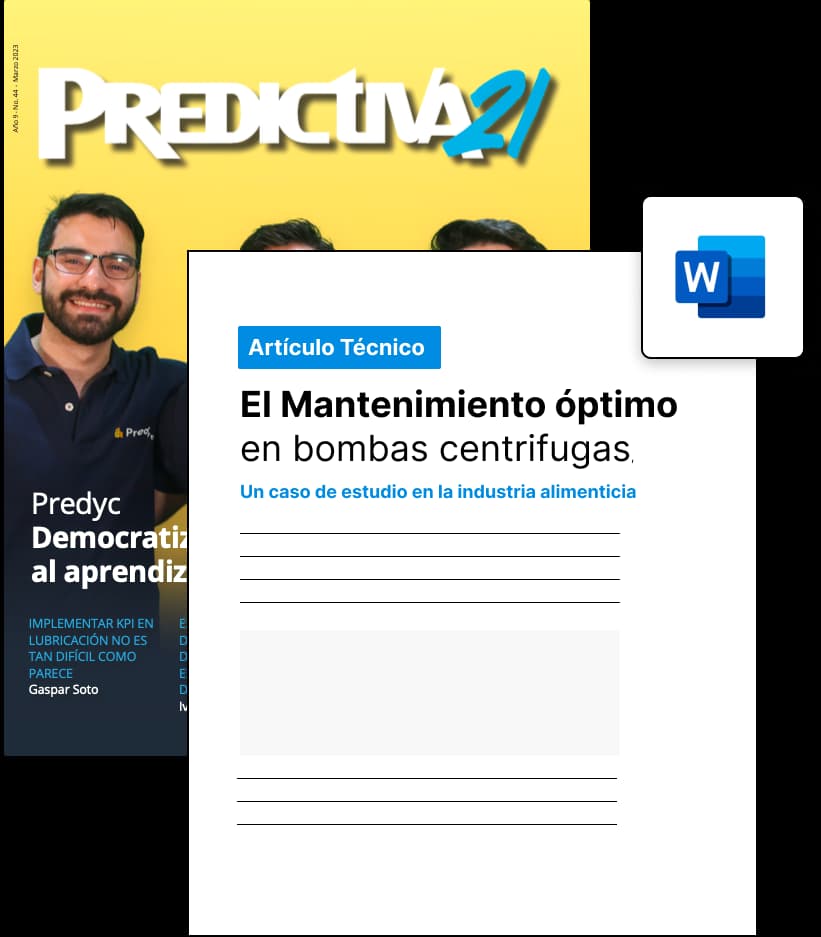