Aplicación de la Metodología de Análisis Causa Raíz. Caso: Fallas Recurrentes del Sistema de Distribución Eléctrica en 34,5kv de un Campo Petrolero
Articulo29 de abril de 2020
En el presente trabajo se abordará la aplicación de una de las “buenas prácticas” en el ámbito de la confiabilidad operacional, como lo es la aplicación de la metodología de análisis causa raíz como estrategia de gestión. Se explicarán las fases del sistema “per sec”, así como el alcance y sus funciones, de igual manera se mostrará un caso práctico dentro de la industria del petróleo y gas, desde la aplicación de la técnica de valoración de problemas, se definirán los criterios para la designación de los miembros del equipo natural de trabajo, se desarrollará la aplicación de la metodología de análisis causa raíz (ACR), donde se mostrarán las causas raíces físicas, humanas y organizacionales o latentes; así mismo se describirá el plan de acción tendiente a mitigar o erradicar las dichas causas y se presentarán los resultados de la aplicación de dichas iniciativas. El artículo muestra la aplicación de un esquema de valoración del Riesgo mediante el método cuantitativo el cual involucra la definición de expresiones matemáticas que utilizan hechos y/o los datos numéricos asociados con el problema para su determinación, y refiere el método semicuantitativo aplicable para casos en donde no se dispongan de registros. Se muestra la importancia de la implementación de técnicas para la toma de “decisiones bajo certidumbre” donde se conoce con certeza la consecuencia de cada una de las alternativas que implica la selección de la decisión; de igual manera se demuestra la conformación del ENT como un esfuerzo multidisciplinario para abordar análisis de problemas, apuntando al logro de un objetivo común; se aprecia que el ACR permite generar beneficios tempranos, de corto y largo plazo, y en muchos casos (sino en todos) visualizar, mitigar y/o solucionar los problemas que repercuten en la rentabilidad del negocio de un sistema productivo.
Introducción
La utilización de metodologías para el análisis sistemático de los problemas o fallas en un sistema productivo está relacionada principalmente al compromiso de la línea gerencial de dicho negocio, es claro que sin este esfuerzo se hace cuesta arriba la aplicación de cualquier sistema de gestión, debido a que de este nivel se desprenden los recursos necesarios para llevar a término satisfactorio, producir los resultados, y obtener los beneficios futuros. En la industria petrolera los eventos de fallas y/o problemas de los sistemas productivos suelen ser impactantes y costosos; los eventos aislados, esporádicos y de frecuencias muy bajas, de un impacto significativamente mayor a los eventos recurrentes o repetitivos, estos eventos (esporádicos) normalmente son investigados por su propia razón de ser, debido a que suelen estar sujetos al ámbito de la seguridad industrial y/o medioambientales; por el contrario los eventos recurrentes habitualmente no son analizados debido principalmente a que su impacto es relativamente menor en comparación. El problema radica en que los eventos recurrentes debido a su alta frecuencia producen a lo largo de la vida útil de un sistema productivo un impacto igual o mayor, ocasionando deterioro de las unidades productivas y afectando el comportamiento de las personas hacia dichos eventos.
Contenido
En adelante se abordará la metodología de análisis causa raíz enmarcada en el ámbito de la solución de problemas como estrategia de gestión. Así mismo se explicará el caso de estudio dentro de la industria petrolera desde su fase inicial hasta la verificación de los resultados.
Sistema de gestión de problemas y fallas
El sistema de gestión de problemas y fallas implementado se encuentra enmarcado dentro de los principios del proceso administrativo el cual involucra: planificación, organización, dirección y control (Stoner et al. 1996). Ver la figura 1.

Este sistema de gestión está soportado sobre la base de la optimización de los recursos, direccionándolos hacia los problemas que destruyen mayor valor. El sistema se encuentra estructurado en cuatro bloques funcionales como se indica en la figura 1.
El bloque número 1 es el de mayor peso del sistema debido a que está atado al compromiso de la línea gerencial donde se autorizarán los recursos necesarios para la puesta en funcionamiento del sistema, dentro de sus responsabilidades se encuentran:
- El seguimiento de metas y resultados.
- Suministrar los recursos necesarios.
- Comunicar a todo el personal las prioridades.
- Designar los facilitadores.
- Designar los equipos naturales de trabajo (ENT).
- Garantizar la capacitación continua en la materia.
- Autorizar la ejecución del plan de acción.
El bloque número 2 tiene la función de valorar y jerarquizar los problemas aplicando las estrategias previamente definidas, a fin de establecer un orden de ejecución y optimizar los recursos disponibles.
El bloque número 3 tiene la función de ejecutar propiamente el análisis de la falla y/o problema para determinar la causas raíces física, humanas y organizacionales o latentes, así mismo tiene la responsabilidad de elaborar el plan de acción tendiente a mitigar o erradicar las causas del problema; el bloque número 4 tiene la función de justificar a través de la utilización de análisis técnicos y económicos las acciones propuestas en el plan de acción, a fin de gestionar su autorización (R2M, 2007).
Valoración de los problemas
El sistema productivo objeto de análisis en este trabajo, al igual que cualquier otro sistema productivo posee una variedad de problemas e inconvenientes propios, por ende, es necesario comparar dichos problemas entre sí para ofrecer a la línea gerencial herramientas para la toma de decisiones efectivas.
En este sentido se utilizó la definición de Riesgo (R) como el producto entre la Frecuencia de ocurrencia (F) y la Consecuencia (C), a fin de valorar cada una de las fallas o problemas:
R = F x C (1)
En la ecuación (1) se tiene que: la Frecuencia (F) está definida como la cantidad de eventos por año para cada uno de los problemas o fallas, y la Consecuencia (C) se cuantifica como la sumatoria de los impactos generados por la ocurrencia de un evento utilizando como unidad el dólar (US$) y está a su vez se puede desglosar en tantos elementos como puedan ser descritos para cada problema y/o falla, como se describe en la siguiente ecuación:
R= F x (Cp + Cm + Csi + Cma + Cop + Cotros) (2)
De la ecuación (2) se detallan a continuación los diferentes factoresque aportan a la consecuencia, a saber:
Producción (Cp), se refiere a la producción perdida o diferida, también se denomina costos de penalización, por ejemplo: Supongamos la falla de la alimentación eléctrica de la planta 1, con 100 barriles de producción diferida (Pdiferida) a un precio del barril de 97 US$ por barril (PrecioBarril), se calcularía como sigue:
Cp = (Pdiferida) x (CostoBarril)
Cp = (100 bls) x (97 US$/bls) = 9700 US$
Mantenimiento (Cm), se refiere a la sumatoria de los costos de mantenimiento, en este se incluyen: materiales, partes, repuestos, equipos, mano de obra y/o servicios; por ejemplo: fusibles de 2 Amperios (50 US$), alquiler de equipo de elevación de personas (1000 US$/día), cuadrilla de mantenimiento (60 US$/hora):

Seguridad Industrial (Csi), se refiere a los costos de: materiales consumibles de seguridad, sistemas de señalización, equipos de protección personal, mano de obra y/o servicios, por ejemplo: 50 metros de cinta de demarcación (10US$/m), sin costos de equipos y servicio.

Medio ambiente (Cma), se refiere a los costos de: equipos de control contra derrame, productos químicos, disposición final, entre otros, aplicando la siguiente ecuación:

Operativos (Cop), se refiere a los costos derivados de las acciones operacionales que involucra la ocurrencia de este evento, en este elemento se incluye: mano de obra y/o servicios requeridos para mitigar la ocurrencia;

Otros (Cotros), se refiere los costos de: reconocimiento e indemnización de afectaciones a propietarios, gastos de tipo legal, administrativo y/o financiero, afectación de la imagen de la empresa, entre otros.

Suponiendo una frecuencia de un evento al año (F=1) y aplicando la ecuación (2) se tiene un Riesgo de 11590 US$/Año por la falla de la alimentación eléctrica de la Planta 1 como se muestra a continuación:
R = 1 evento/Año x (9700 US$ + 1390 US$ + 500 US$ + 0 + 0) = 11590 US$⁄Año
Los métodos para la determinación de estos factores pueden ser de tipo semicuantitativos cuando se dispone de registros suficientes para calcular ambos factores (F y C) que corresponde al caso de estudio (arriba ejemplificado).
El método semicuantitativo es usado cuando no se dispone de registros que permitan calcular la frecuencia y la consecuencia, en este caso se dispone de criterios para la determinación de la frecuencia (ver tabla I) y la consecuencia (ver tabla II) mediante de matrices de evaluación riesgo las cuales varían en cada compañía, en dichas tablas se muestra los criterios de la empresa Repsol (2010).

La valoración de cada criterio se establece mediante el ENT utilizando un facilitador con experiencia en valoraciones de Riesgo y se restringe a los criterios de dicha matriz, en este caso se utiliza la comparación entre categorías para definir cada selección, la jerarquía entre problemas vendrá dada por la comparación del valor de Riesgo, y en caso de paridad la decisión entre uno u otro obedecerá a la dirección de la empresa.
El tipo de equipo juega un papel fundamental en la determinación de la valoración, los tipos de equipos estáticos (recipientes, tuberías, válvulas, etc.) se caracterizan por ser de baja frecuencia de ocurrencia y de altos impactos (se utiliza la valoración del riesgo indicada en la API-580/581 referida a Inspección Basada en Riesgo), los tipos de equipos dinámicos y rotativos suelen tener alta frecuencia y bajos impactos, los equipos eléctricos y de instrumentación suelen tener valores medios de frecuencia e impactos moderados. Sin embargo, una matriz de evaluación del riesgo debe incluir por igual a todos los equipos de un sistema productivo, en razón de que pertenecen a un mismo negocio en términos de Riesgo financiero.

La tabla III, muestra una lista problemas con Valoración del Riesgo (R) mediante el método cuantitativo, ordenada en función del valor del riesgo, es decir, el “Problema 1” es de mayor impacto que el “Problema 2” y así sucesivamente hasta el “Problema n”.

Aplicación del sistema de valoración
La aplicación del sistema de valoración debe ejecutarse por un equipo multidisciplinario de profesionales dentro del departamento responsable del sistema productivo. En la tabla IV se muestra el resultado de la valoración del riesgo aplicado (bloque 2 de la figura 1), donde fueron calculados los Riesgos de siete (7) problemas al sistema productivo en estudio, en esta se evidencia que el problema de mayor impacto en sistema productivo es la “Falla del sistema de distribución eléctrica de 34.5KV” con un impacto estimado anual de US$ 357.906,96. Queda en evidencia que a pesar de que el ítem 1 posee una consecuencia (C) menor a los ítems 2, 3, 5 y 6, su impacto (R) es relativamente mayor debido a que su frecuencia de ocurrencia estimada es superior a todas las evaluadas. Es decir, el ítem 1 destruye más valor en el sistema productivo.

Una vez obtenidos estos resultados el Comité de Gerencia autorizó la ejecución del análisis causa raíz con mayor Riesgo (Ítem 1), esto a razón de gestionar adecuadamente los recursos de la organización. En este caso particular y de acuerdo al contexto de la empresa es contraproducente la ejecución de más de un análisis por vez debido a limitaciones de recurso humano (bloque 1 de la figura 1).
Cursos recomendados




%252FImagen%252FRAMPREDYC-1730060420837.webp%3Falt%3Dmedia%26token%3D2634a7f0-988e-4022-b91f-382503e6e9db&w=3840&q=75)



Aplicación de la metodología acr para el caso de estudio
El ACR es una metodología sistemática yorganizada la cual está dirigida a la solución de problemas de diversa índole,está diseñada para ayudar a determinar la secuencia de causas y efectos queconllevan a la ocurrencia de un evento no deseado, el proceso se detiene cuandose consiguen las causas raíces del evento, o sea, las causas que al serresueltas evitan su recurrencia (Andersen y Fagerhaug, 2006).
En el siguiente apartado se describe la aplicación “per sec” de la metodología de análisis causa raíz, que va desde el planteamiento del problema hasta la determinación de las causas raíces.
Conformación del ENT
El ENT se define como “el conjunto de personas de diferentes funciones de la organización, que trabajan juntas por un periodo de tiempo determinado en un clima de potenciación de energía, para analizar problemas comunes de los distintos departamentos, apuntando al logro de un objetivo común” (Huerta, 2004). El Comité de Gerencia designó al equipo natural de trabajo (ENT) para llevar adelante el análisis de la siguiente manera:
- Facilitador de la metodología y líder de equipo.
- Supervisor de operaciones.
- Supervisor de mantenimiento.
- Técnico de mantenimiento eléctrico.
- Técnico de operaciones de producción.
- Planificador de mantenimiento.
Contexto operacional y planteamiento del problema
El sistema productivo de referencia tiene unnivel de producción superior a los 10.000 barriles por día de crudo extraídosde tres yacimientos petrolíferos, producen en un sistema mixto de flujo naturaly levantamiento artificial. Está provisto de un sistema de distribucióneléctrica propio, tipo aéreo y que se surte de la red eléctrica nacional.
La topografía del campo petrolero esaccidentada, involucra a un numero de comunidades dentro de su área de influencia,la vegetación es de tipo de bosque seco tropical y húmedo tropical, latemperatura promedio anual de 26,4 °C y precipitaciones de 1.935 mm (promedioanual).
El enunciado del problema se definió como“Fallas recurrentes del sistema de distribución eléctrica 34.5 KV del campopetrolero”, registrándose interrupción del servicio eléctrico en forma parcialy/o total, incurriendo en la parada no programada de los pozos, estaciones yplanta No. 1.
Desarrollo del ACR
Se inició la aplicación de la metodología de análisiscausa raíz (ACR) determinando los modos de falla, aplicando el principio decausa-efecto, y la validación de las hipótesis utilizando las diferentestécnicas disponibles (experiencia del personal, comprobación de registros,entrevistas, entre otras), así mismo se utilizó el “Método Delphi” en unaversión modificada para determinar las ponderaciones de rama debido a que losregistros disponibles eran insuficientes. El Método Delphi es un proceso paraobtener consenso dentro de un grupo de expertos; es un proceso reiterativo, sufuncionamiento se basa en la interpretación de cada opinión (Krajewski yRitzman, 2000).
En la figura 2, se observa el desarrollo de una sección del árbol lógico de falla (el árbol consta de 12 ramificaciones no mostradas en la gráfica por razones visuales).

Fuente: Registro del caso de estudio.
De la figura anterior el modo de falla de mayor impacto (70%) referido al disparo de las “PROTECCIONES ELECTRICAS”, así mismo se muestra la determinación de la causa raíz física indicada en color amarillo (MALEZA-ARBOLES EN POSTES Y LINEAS), la causa raíz humana en color verde (FRECUENCIA DE MANTENIMIENTO INADECUADA) y la causa raíz latente u organizacional en color rojo (FALTA DE UN PLAN DE MANTENIMIENTO).
Resultados del ACR, resumen de causas raíces
A continuación, se muestra la tabla V las causas raíces físicas y latentes (organizacionales) encontradas por el ENT:

Fuente: Registro del caso de estudio.
El plan de acción
Posterior a la determinación de las causas seprocedió a elaborar el plan de acción tendiente a la mitigación del problema,requisito para lograr la aprobación de las acciones.
Justificación de acciones
Las medidas autorizadas por la gerencia de línea posterior a la aplicación de análisis de costos-beneficio (ACB) según el paso identificado en el bloque 3 de la figura 1, son como sigue:
- Incorporar a la estructura las vacantes existentes (Supervisor de Mantenimiento Eléctrico y Técnico de Mantenimiento Eléctrico)
- Contratar un servicio de desmalezamiento, pica y poda de la franja de seguridad del tendido eléctrico
- Procurar las partes y repuestos necesarios para ejecutar los reemplazos por deterioro e incorporar al inventario
- Procurar un equipo de elevación de personal para trabajos eléctricos en líneas aéreas, así como las herramientas manuales necesarias para trabajos eléctricos en alta tensión
- Ejecutar un plan acelerado de mejoras y adecuaciones desde el punto de vista de maniobrabilidad y disponibilidad
- Contratar un servicio de reparación de transformadores eléctricos de diversas capacidades en el nivel de voltaje de 34.5KV.
Dentro del plan de acción existieron un grupode medidas no autorizadas por la gerencia de línea, por diversos motivos(presupuesto, nivel técnico, etc.), y otras que por su naturaleza correspondela aprobación a las gerencias de soporte.
El control y seguimiento
El Comité de Gerencia, autorizó los recursosfinancieros y humanos a fin de ejecutar lo propuesto en el plan de accióndentro de su ámbito de control (bloque 1, figura 1), implementó un sistema deseguimiento semanal de actividades críticas que produjo la puesta en prácticadichas iniciativas.
Resultados
Posterior a la aplicación de dichas medidas durante los años 2.011 y 2.012, se obtuvo como resultado una reducción de 60% de la producción diferida 7.780 barriles por año lo que equivale a US$ 780.000,00 (2012), con una tendencia favorable y a la baja. A la vez se registró una reducción de 57% de la producción diferida por cortes eléctricos programados de 988 barriles por año en 2.010 a 424 barriles por año en 2.012 lo que equivale a US$ 56.400,00 evidenciando un incremento de la calidad de los trabajos eléctricos programados. Ver figura 3.

Fuente: Registro del caso de estudio.

Fuente: Registro del caso de estudio.
Conclusiones
El sistema de gestión implementado en elsistema productivo es eficiente y optimiza la asignación de recursos, con laaplicación de la valorización del Riesgo como medida de jerarquización de losproblemas. Esta valoración contempla el cálculo del Riesgo mediante métodossemicuantitativos usados cuando no se disponen de registros, para este caso seemplean índices globales potenciales estimados a través de las estadísticasprocedente de las experiencias de compañías del sector y utiliza conclusionescomparativas entre criterios para determinar la selección según Storch y García(2008) y cuantitativos los cuales involucran la elaboración de expresionesmatemáticas basadas en datos numéricos asociados con el problema segúnAnderson, et al. (2004). Lo que hace viable su replicación en diversos sistemasproductivos.
El éxito en la implementación del sistema degestión de problemas y fallas viene de la mano del apoyo de la línea gerencial(dirección), debido a que involucra la aprobación de los recursos y permeasobre la estructura organizacional las prioridades de la organización. Por estola importancia de la implementación de técnicas para la “toma de decisionesbajo certidumbre” donde se conoce con certeza la consecuencia de ellas segúnRender, et al. (2006) es determinante para la asignación y programación de losrecursos.
La implementación de un sistema por sí mismoinvolucra un esfuerzo multidisciplinario, la utilización de Equipos Naturalesde Trabajo (ENT) adecuadamente dimensionados y a razón de que el personal demantenimiento no puede contestar a todas las preguntas por sí mismos, ya quemuchas de las respuestas sólo pueden proporcionarlas el personal deoperaciones, entre otros, según Moubray, J. (2004) posibilita a que laorganización obtenga los beneficios de la contribución de valor que estepresupone y la obtención de resultados.
La metodología ACR es una de las técnicas quegeneran beneficios tempranos, de corto y largo plazo; y permite en muchos casosvisualizar los problemas que repercuten en la rentabilidad del negocio(Amendola, 2006), su implementación puede solucionar inclusive problemas que aúnno se han analizado, ya que las soluciones de nivel organizacional son comunesa diversos problemas, por ejemplo: la revisión de los planes de mantenimientorepercutirá no solo en el caso de estudio sino también en aquellos equipos ysistemas que tengan debilidad en este particular.
La modalidad de pesos ponderados dentro de lametodología ACR ofreció al Comité de Gerencia en términos numéricosherramientas para la toma de decisiones ya que permitió observar ladistribución de los impactos de acuerdo a las causas encontradas, aspecto clavepara el análisis de costo-beneficio, puesto que cada causa apunta directamentea una porción numérica del Riesgo total.
Las medidas autorizadas por el Comité deGerencia apuntaron a solucionar y/o mitigar parte del problema, observándosebeneficios superiores a los esperados en la disminución de la frecuencia deocurrencia. Mediante la técnica de análisis costo-beneficio (ACB) implementadase comparó los beneficios esperados contra los costos de implementar dicha acción,en tanto que los beneficios fueron superiores a los costos, esto aportó unjuicio positivo que sugirió su aceptación (Cohen y Franco, 2000) y permitiócomparar las acciones según este criterio.
Otro de los aspectos fundamentales en laconcreción de las acciones que mitigaron el problema fue la aplicación de lasmedidas de control y seguimiento adecuadas (alcance, tiempo y costos) lo cualpermitió comparar lo que estaba ocurriendo en la realidad, con los objetivosprevistos y se tomaron las decisiones para reencausar y corregir cambios odesviaciones que se hayan producido (Publicaciones Vértice S.L., 2008)resultando en la aplicación de las medidas previstas en el plan de acción.
Autor: Héctor Díaz
Ingeniero Electrónico, Mención Control
Correo: hdiaze@repsol.com / hectorjdiaz@gmail.com
Dinos qué te ha parecido el artículo
Artículos recomendados
AMEF: descubre el análisis de modos de fallos

ISO 55000 - Lo que necesita saber

¿Qué es el Micro dieseling?

El mantenimiento industrial

Publica tu artículo en la revista #1 de Mantenimiento Industrial
Publicar un artículo en la revista es gratis, no tiene costo.
Solo debes asegurarte que no sea un artículo comercial.
¿Qué esperas?
O envía tu artículo directo: articulos@predictiva21.com
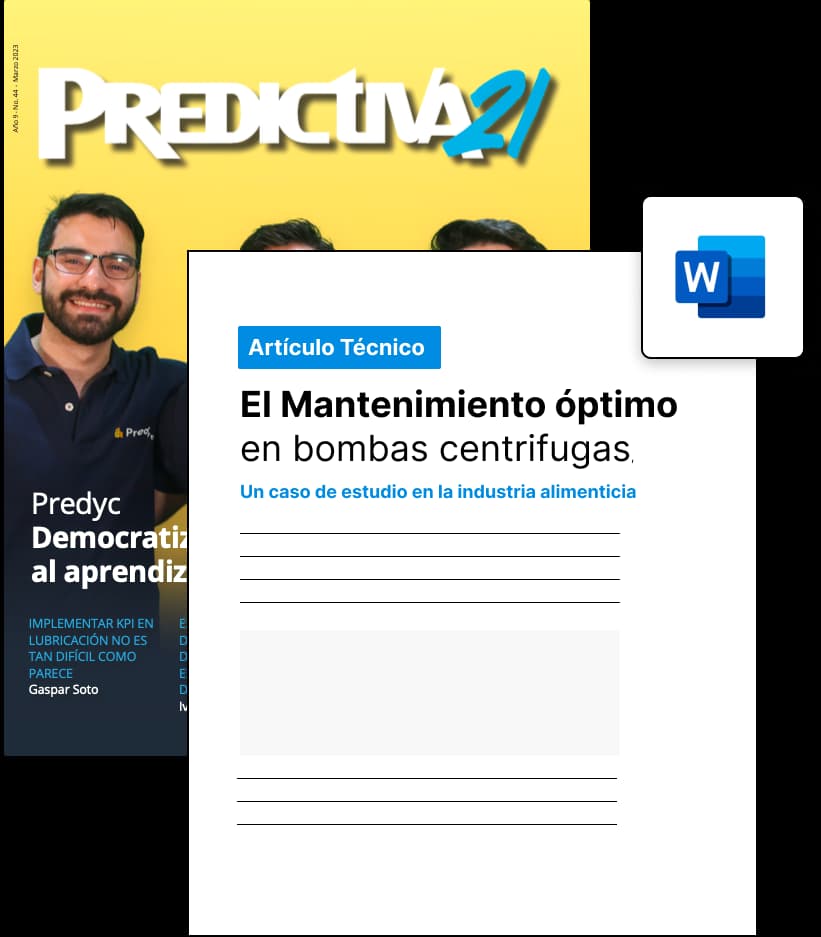
Aplicación de la Metodología de Análisis Causa Raíz. Caso: Fallas Recurrentes del Sistema de Distribución Eléctrica en 34,5kv de un Campo Petrolero
Articulo 29 de abril de 2020En el presente trabajo se abordará la aplicación de una de las “buenas prácticas” en el ámbito de la confiabilidad operacional, como lo es la aplicación de la metodología de análisis causa raíz como estrategia de gestión. Se explicarán las fases del sistema “per sec”, así como el alcance y sus funciones, de igual manera se mostrará un caso práctico dentro de la industria del petróleo y gas, desde la aplicación de la técnica de valoración de problemas, se definirán los criterios para la designación de los miembros del equipo natural de trabajo, se desarrollará la aplicación de la metodología de análisis causa raíz (ACR), donde se mostrarán las causas raíces físicas, humanas y organizacionales o latentes; así mismo se describirá el plan de acción tendiente a mitigar o erradicar las dichas causas y se presentarán los resultados de la aplicación de dichas iniciativas. El artículo muestra la aplicación de un esquema de valoración del Riesgo mediante el método cuantitativo el cual involucra la definición de expresiones matemáticas que utilizan hechos y/o los datos numéricos asociados con el problema para su determinación, y refiere el método semicuantitativo aplicable para casos en donde no se dispongan de registros. Se muestra la importancia de la implementación de técnicas para la toma de “decisiones bajo certidumbre” donde se conoce con certeza la consecuencia de cada una de las alternativas que implica la selección de la decisión; de igual manera se demuestra la conformación del ENT como un esfuerzo multidisciplinario para abordar análisis de problemas, apuntando al logro de un objetivo común; se aprecia que el ACR permite generar beneficios tempranos, de corto y largo plazo, y en muchos casos (sino en todos) visualizar, mitigar y/o solucionar los problemas que repercuten en la rentabilidad del negocio de un sistema productivo.
Introducción
La utilización de metodologías para el análisis sistemático de los problemas o fallas en un sistema productivo está relacionada principalmente al compromiso de la línea gerencial de dicho negocio, es claro que sin este esfuerzo se hace cuesta arriba la aplicación de cualquier sistema de gestión, debido a que de este nivel se desprenden los recursos necesarios para llevar a término satisfactorio, producir los resultados, y obtener los beneficios futuros. En la industria petrolera los eventos de fallas y/o problemas de los sistemas productivos suelen ser impactantes y costosos; los eventos aislados, esporádicos y de frecuencias muy bajas, de un impacto significativamente mayor a los eventos recurrentes o repetitivos, estos eventos (esporádicos) normalmente son investigados por su propia razón de ser, debido a que suelen estar sujetos al ámbito de la seguridad industrial y/o medioambientales; por el contrario los eventos recurrentes habitualmente no son analizados debido principalmente a que su impacto es relativamente menor en comparación. El problema radica en que los eventos recurrentes debido a su alta frecuencia producen a lo largo de la vida útil de un sistema productivo un impacto igual o mayor, ocasionando deterioro de las unidades productivas y afectando el comportamiento de las personas hacia dichos eventos.
Contenido
En adelante se abordará la metodología de análisis causa raíz enmarcada en el ámbito de la solución de problemas como estrategia de gestión. Así mismo se explicará el caso de estudio dentro de la industria petrolera desde su fase inicial hasta la verificación de los resultados.
Sistema de gestión de problemas y fallas
El sistema de gestión de problemas y fallas implementado se encuentra enmarcado dentro de los principios del proceso administrativo el cual involucra: planificación, organización, dirección y control (Stoner et al. 1996). Ver la figura 1.

Este sistema de gestión está soportado sobre la base de la optimización de los recursos, direccionándolos hacia los problemas que destruyen mayor valor. El sistema se encuentra estructurado en cuatro bloques funcionales como se indica en la figura 1.
El bloque número 1 es el de mayor peso del sistema debido a que está atado al compromiso de la línea gerencial donde se autorizarán los recursos necesarios para la puesta en funcionamiento del sistema, dentro de sus responsabilidades se encuentran:
- El seguimiento de metas y resultados.
- Suministrar los recursos necesarios.
- Comunicar a todo el personal las prioridades.
- Designar los facilitadores.
- Designar los equipos naturales de trabajo (ENT).
- Garantizar la capacitación continua en la materia.
- Autorizar la ejecución del plan de acción.
El bloque número 2 tiene la función de valorar y jerarquizar los problemas aplicando las estrategias previamente definidas, a fin de establecer un orden de ejecución y optimizar los recursos disponibles.
El bloque número 3 tiene la función de ejecutar propiamente el análisis de la falla y/o problema para determinar la causas raíces física, humanas y organizacionales o latentes, así mismo tiene la responsabilidad de elaborar el plan de acción tendiente a mitigar o erradicar las causas del problema; el bloque número 4 tiene la función de justificar a través de la utilización de análisis técnicos y económicos las acciones propuestas en el plan de acción, a fin de gestionar su autorización (R2M, 2007).
Valoración de los problemas
El sistema productivo objeto de análisis en este trabajo, al igual que cualquier otro sistema productivo posee una variedad de problemas e inconvenientes propios, por ende, es necesario comparar dichos problemas entre sí para ofrecer a la línea gerencial herramientas para la toma de decisiones efectivas.
En este sentido se utilizó la definición de Riesgo (R) como el producto entre la Frecuencia de ocurrencia (F) y la Consecuencia (C), a fin de valorar cada una de las fallas o problemas:
R = F x C (1)
En la ecuación (1) se tiene que: la Frecuencia (F) está definida como la cantidad de eventos por año para cada uno de los problemas o fallas, y la Consecuencia (C) se cuantifica como la sumatoria de los impactos generados por la ocurrencia de un evento utilizando como unidad el dólar (US$) y está a su vez se puede desglosar en tantos elementos como puedan ser descritos para cada problema y/o falla, como se describe en la siguiente ecuación:
R= F x (Cp + Cm + Csi + Cma + Cop + Cotros) (2)
De la ecuación (2) se detallan a continuación los diferentes factoresque aportan a la consecuencia, a saber:
Producción (Cp), se refiere a la producción perdida o diferida, también se denomina costos de penalización, por ejemplo: Supongamos la falla de la alimentación eléctrica de la planta 1, con 100 barriles de producción diferida (Pdiferida) a un precio del barril de 97 US$ por barril (PrecioBarril), se calcularía como sigue:
Cp = (Pdiferida) x (CostoBarril)
Cp = (100 bls) x (97 US$/bls) = 9700 US$
Mantenimiento (Cm), se refiere a la sumatoria de los costos de mantenimiento, en este se incluyen: materiales, partes, repuestos, equipos, mano de obra y/o servicios; por ejemplo: fusibles de 2 Amperios (50 US$), alquiler de equipo de elevación de personas (1000 US$/día), cuadrilla de mantenimiento (60 US$/hora):

Seguridad Industrial (Csi), se refiere a los costos de: materiales consumibles de seguridad, sistemas de señalización, equipos de protección personal, mano de obra y/o servicios, por ejemplo: 50 metros de cinta de demarcación (10US$/m), sin costos de equipos y servicio.

Medio ambiente (Cma), se refiere a los costos de: equipos de control contra derrame, productos químicos, disposición final, entre otros, aplicando la siguiente ecuación:

Operativos (Cop), se refiere a los costos derivados de las acciones operacionales que involucra la ocurrencia de este evento, en este elemento se incluye: mano de obra y/o servicios requeridos para mitigar la ocurrencia;

Otros (Cotros), se refiere los costos de: reconocimiento e indemnización de afectaciones a propietarios, gastos de tipo legal, administrativo y/o financiero, afectación de la imagen de la empresa, entre otros.

Suponiendo una frecuencia de un evento al año (F=1) y aplicando la ecuación (2) se tiene un Riesgo de 11590 US$/Año por la falla de la alimentación eléctrica de la Planta 1 como se muestra a continuación:
R = 1 evento/Año x (9700 US$ + 1390 US$ + 500 US$ + 0 + 0) = 11590 US$⁄Año
Los métodos para la determinación de estos factores pueden ser de tipo semicuantitativos cuando se dispone de registros suficientes para calcular ambos factores (F y C) que corresponde al caso de estudio (arriba ejemplificado).
El método semicuantitativo es usado cuando no se dispone de registros que permitan calcular la frecuencia y la consecuencia, en este caso se dispone de criterios para la determinación de la frecuencia (ver tabla I) y la consecuencia (ver tabla II) mediante de matrices de evaluación riesgo las cuales varían en cada compañía, en dichas tablas se muestra los criterios de la empresa Repsol (2010).

La valoración de cada criterio se establece mediante el ENT utilizando un facilitador con experiencia en valoraciones de Riesgo y se restringe a los criterios de dicha matriz, en este caso se utiliza la comparación entre categorías para definir cada selección, la jerarquía entre problemas vendrá dada por la comparación del valor de Riesgo, y en caso de paridad la decisión entre uno u otro obedecerá a la dirección de la empresa.
El tipo de equipo juega un papel fundamental en la determinación de la valoración, los tipos de equipos estáticos (recipientes, tuberías, válvulas, etc.) se caracterizan por ser de baja frecuencia de ocurrencia y de altos impactos (se utiliza la valoración del riesgo indicada en la API-580/581 referida a Inspección Basada en Riesgo), los tipos de equipos dinámicos y rotativos suelen tener alta frecuencia y bajos impactos, los equipos eléctricos y de instrumentación suelen tener valores medios de frecuencia e impactos moderados. Sin embargo, una matriz de evaluación del riesgo debe incluir por igual a todos los equipos de un sistema productivo, en razón de que pertenecen a un mismo negocio en términos de Riesgo financiero.

La tabla III, muestra una lista problemas con Valoración del Riesgo (R) mediante el método cuantitativo, ordenada en función del valor del riesgo, es decir, el “Problema 1” es de mayor impacto que el “Problema 2” y así sucesivamente hasta el “Problema n”.

Aplicación del sistema de valoración
La aplicación del sistema de valoración debe ejecutarse por un equipo multidisciplinario de profesionales dentro del departamento responsable del sistema productivo. En la tabla IV se muestra el resultado de la valoración del riesgo aplicado (bloque 2 de la figura 1), donde fueron calculados los Riesgos de siete (7) problemas al sistema productivo en estudio, en esta se evidencia que el problema de mayor impacto en sistema productivo es la “Falla del sistema de distribución eléctrica de 34.5KV” con un impacto estimado anual de US$ 357.906,96. Queda en evidencia que a pesar de que el ítem 1 posee una consecuencia (C) menor a los ítems 2, 3, 5 y 6, su impacto (R) es relativamente mayor debido a que su frecuencia de ocurrencia estimada es superior a todas las evaluadas. Es decir, el ítem 1 destruye más valor en el sistema productivo.

Una vez obtenidos estos resultados el Comité de Gerencia autorizó la ejecución del análisis causa raíz con mayor Riesgo (Ítem 1), esto a razón de gestionar adecuadamente los recursos de la organización. En este caso particular y de acuerdo al contexto de la empresa es contraproducente la ejecución de más de un análisis por vez debido a limitaciones de recurso humano (bloque 1 de la figura 1).
Cursos recomendados




%252FImagen%252FRAMPREDYC-1730060420837.webp%3Falt%3Dmedia%26token%3D2634a7f0-988e-4022-b91f-382503e6e9db&w=3840&q=75)



Aplicación de la metodología acr para el caso de estudio
El ACR es una metodología sistemática yorganizada la cual está dirigida a la solución de problemas de diversa índole,está diseñada para ayudar a determinar la secuencia de causas y efectos queconllevan a la ocurrencia de un evento no deseado, el proceso se detiene cuandose consiguen las causas raíces del evento, o sea, las causas que al serresueltas evitan su recurrencia (Andersen y Fagerhaug, 2006).
En el siguiente apartado se describe la aplicación “per sec” de la metodología de análisis causa raíz, que va desde el planteamiento del problema hasta la determinación de las causas raíces.
Conformación del ENT
El ENT se define como “el conjunto de personas de diferentes funciones de la organización, que trabajan juntas por un periodo de tiempo determinado en un clima de potenciación de energía, para analizar problemas comunes de los distintos departamentos, apuntando al logro de un objetivo común” (Huerta, 2004). El Comité de Gerencia designó al equipo natural de trabajo (ENT) para llevar adelante el análisis de la siguiente manera:
- Facilitador de la metodología y líder de equipo.
- Supervisor de operaciones.
- Supervisor de mantenimiento.
- Técnico de mantenimiento eléctrico.
- Técnico de operaciones de producción.
- Planificador de mantenimiento.
Contexto operacional y planteamiento del problema
El sistema productivo de referencia tiene unnivel de producción superior a los 10.000 barriles por día de crudo extraídosde tres yacimientos petrolíferos, producen en un sistema mixto de flujo naturaly levantamiento artificial. Está provisto de un sistema de distribucióneléctrica propio, tipo aéreo y que se surte de la red eléctrica nacional.
La topografía del campo petrolero esaccidentada, involucra a un numero de comunidades dentro de su área de influencia,la vegetación es de tipo de bosque seco tropical y húmedo tropical, latemperatura promedio anual de 26,4 °C y precipitaciones de 1.935 mm (promedioanual).
El enunciado del problema se definió como“Fallas recurrentes del sistema de distribución eléctrica 34.5 KV del campopetrolero”, registrándose interrupción del servicio eléctrico en forma parcialy/o total, incurriendo en la parada no programada de los pozos, estaciones yplanta No. 1.
Desarrollo del ACR
Se inició la aplicación de la metodología de análisiscausa raíz (ACR) determinando los modos de falla, aplicando el principio decausa-efecto, y la validación de las hipótesis utilizando las diferentestécnicas disponibles (experiencia del personal, comprobación de registros,entrevistas, entre otras), así mismo se utilizó el “Método Delphi” en unaversión modificada para determinar las ponderaciones de rama debido a que losregistros disponibles eran insuficientes. El Método Delphi es un proceso paraobtener consenso dentro de un grupo de expertos; es un proceso reiterativo, sufuncionamiento se basa en la interpretación de cada opinión (Krajewski yRitzman, 2000).
En la figura 2, se observa el desarrollo de una sección del árbol lógico de falla (el árbol consta de 12 ramificaciones no mostradas en la gráfica por razones visuales).

Fuente: Registro del caso de estudio.
De la figura anterior el modo de falla de mayor impacto (70%) referido al disparo de las “PROTECCIONES ELECTRICAS”, así mismo se muestra la determinación de la causa raíz física indicada en color amarillo (MALEZA-ARBOLES EN POSTES Y LINEAS), la causa raíz humana en color verde (FRECUENCIA DE MANTENIMIENTO INADECUADA) y la causa raíz latente u organizacional en color rojo (FALTA DE UN PLAN DE MANTENIMIENTO).
Resultados del ACR, resumen de causas raíces
A continuación, se muestra la tabla V las causas raíces físicas y latentes (organizacionales) encontradas por el ENT:

Fuente: Registro del caso de estudio.
El plan de acción
Posterior a la determinación de las causas seprocedió a elaborar el plan de acción tendiente a la mitigación del problema,requisito para lograr la aprobación de las acciones.
Justificación de acciones
Las medidas autorizadas por la gerencia de línea posterior a la aplicación de análisis de costos-beneficio (ACB) según el paso identificado en el bloque 3 de la figura 1, son como sigue:
- Incorporar a la estructura las vacantes existentes (Supervisor de Mantenimiento Eléctrico y Técnico de Mantenimiento Eléctrico)
- Contratar un servicio de desmalezamiento, pica y poda de la franja de seguridad del tendido eléctrico
- Procurar las partes y repuestos necesarios para ejecutar los reemplazos por deterioro e incorporar al inventario
- Procurar un equipo de elevación de personal para trabajos eléctricos en líneas aéreas, así como las herramientas manuales necesarias para trabajos eléctricos en alta tensión
- Ejecutar un plan acelerado de mejoras y adecuaciones desde el punto de vista de maniobrabilidad y disponibilidad
- Contratar un servicio de reparación de transformadores eléctricos de diversas capacidades en el nivel de voltaje de 34.5KV.
Dentro del plan de acción existieron un grupode medidas no autorizadas por la gerencia de línea, por diversos motivos(presupuesto, nivel técnico, etc.), y otras que por su naturaleza correspondela aprobación a las gerencias de soporte.
El control y seguimiento
El Comité de Gerencia, autorizó los recursosfinancieros y humanos a fin de ejecutar lo propuesto en el plan de accióndentro de su ámbito de control (bloque 1, figura 1), implementó un sistema deseguimiento semanal de actividades críticas que produjo la puesta en prácticadichas iniciativas.
Resultados
Posterior a la aplicación de dichas medidas durante los años 2.011 y 2.012, se obtuvo como resultado una reducción de 60% de la producción diferida 7.780 barriles por año lo que equivale a US$ 780.000,00 (2012), con una tendencia favorable y a la baja. A la vez se registró una reducción de 57% de la producción diferida por cortes eléctricos programados de 988 barriles por año en 2.010 a 424 barriles por año en 2.012 lo que equivale a US$ 56.400,00 evidenciando un incremento de la calidad de los trabajos eléctricos programados. Ver figura 3.

Fuente: Registro del caso de estudio.

Fuente: Registro del caso de estudio.
Conclusiones
El sistema de gestión implementado en elsistema productivo es eficiente y optimiza la asignación de recursos, con laaplicación de la valorización del Riesgo como medida de jerarquización de losproblemas. Esta valoración contempla el cálculo del Riesgo mediante métodossemicuantitativos usados cuando no se disponen de registros, para este caso seemplean índices globales potenciales estimados a través de las estadísticasprocedente de las experiencias de compañías del sector y utiliza conclusionescomparativas entre criterios para determinar la selección según Storch y García(2008) y cuantitativos los cuales involucran la elaboración de expresionesmatemáticas basadas en datos numéricos asociados con el problema segúnAnderson, et al. (2004). Lo que hace viable su replicación en diversos sistemasproductivos.
El éxito en la implementación del sistema degestión de problemas y fallas viene de la mano del apoyo de la línea gerencial(dirección), debido a que involucra la aprobación de los recursos y permeasobre la estructura organizacional las prioridades de la organización. Por estola importancia de la implementación de técnicas para la “toma de decisionesbajo certidumbre” donde se conoce con certeza la consecuencia de ellas segúnRender, et al. (2006) es determinante para la asignación y programación de losrecursos.
La implementación de un sistema por sí mismoinvolucra un esfuerzo multidisciplinario, la utilización de Equipos Naturalesde Trabajo (ENT) adecuadamente dimensionados y a razón de que el personal demantenimiento no puede contestar a todas las preguntas por sí mismos, ya quemuchas de las respuestas sólo pueden proporcionarlas el personal deoperaciones, entre otros, según Moubray, J. (2004) posibilita a que laorganización obtenga los beneficios de la contribución de valor que estepresupone y la obtención de resultados.
La metodología ACR es una de las técnicas quegeneran beneficios tempranos, de corto y largo plazo; y permite en muchos casosvisualizar los problemas que repercuten en la rentabilidad del negocio(Amendola, 2006), su implementación puede solucionar inclusive problemas que aúnno se han analizado, ya que las soluciones de nivel organizacional son comunesa diversos problemas, por ejemplo: la revisión de los planes de mantenimientorepercutirá no solo en el caso de estudio sino también en aquellos equipos ysistemas que tengan debilidad en este particular.
La modalidad de pesos ponderados dentro de lametodología ACR ofreció al Comité de Gerencia en términos numéricosherramientas para la toma de decisiones ya que permitió observar ladistribución de los impactos de acuerdo a las causas encontradas, aspecto clavepara el análisis de costo-beneficio, puesto que cada causa apunta directamentea una porción numérica del Riesgo total.
Las medidas autorizadas por el Comité deGerencia apuntaron a solucionar y/o mitigar parte del problema, observándosebeneficios superiores a los esperados en la disminución de la frecuencia deocurrencia. Mediante la técnica de análisis costo-beneficio (ACB) implementadase comparó los beneficios esperados contra los costos de implementar dicha acción,en tanto que los beneficios fueron superiores a los costos, esto aportó unjuicio positivo que sugirió su aceptación (Cohen y Franco, 2000) y permitiócomparar las acciones según este criterio.
Otro de los aspectos fundamentales en laconcreción de las acciones que mitigaron el problema fue la aplicación de lasmedidas de control y seguimiento adecuadas (alcance, tiempo y costos) lo cualpermitió comparar lo que estaba ocurriendo en la realidad, con los objetivosprevistos y se tomaron las decisiones para reencausar y corregir cambios odesviaciones que se hayan producido (Publicaciones Vértice S.L., 2008)resultando en la aplicación de las medidas previstas en el plan de acción.
Autor: Héctor Díaz
Ingeniero Electrónico, Mención Control
Correo: hdiaze@repsol.com / hectorjdiaz@gmail.com
Dinos qué te ha parecido el artículo
Artículos recomendados
¿Quién debe planificar los trabajos de Mantenimiento?

Entrevista Luis Felipe Sexto

Curso TPM y lo que aprenderás en uno

La Permeabilidad del Mantenimiento

Publica tu artículo en la revista #1 de Mantenimiento Industrial
Publicar un artículo en la revista es gratis, no tiene costo.
Solo debes asegurarte que no sea un artículo comercial.
¿Qué esperas?
O envía tu artículo directo: articulos@predictiva21.com
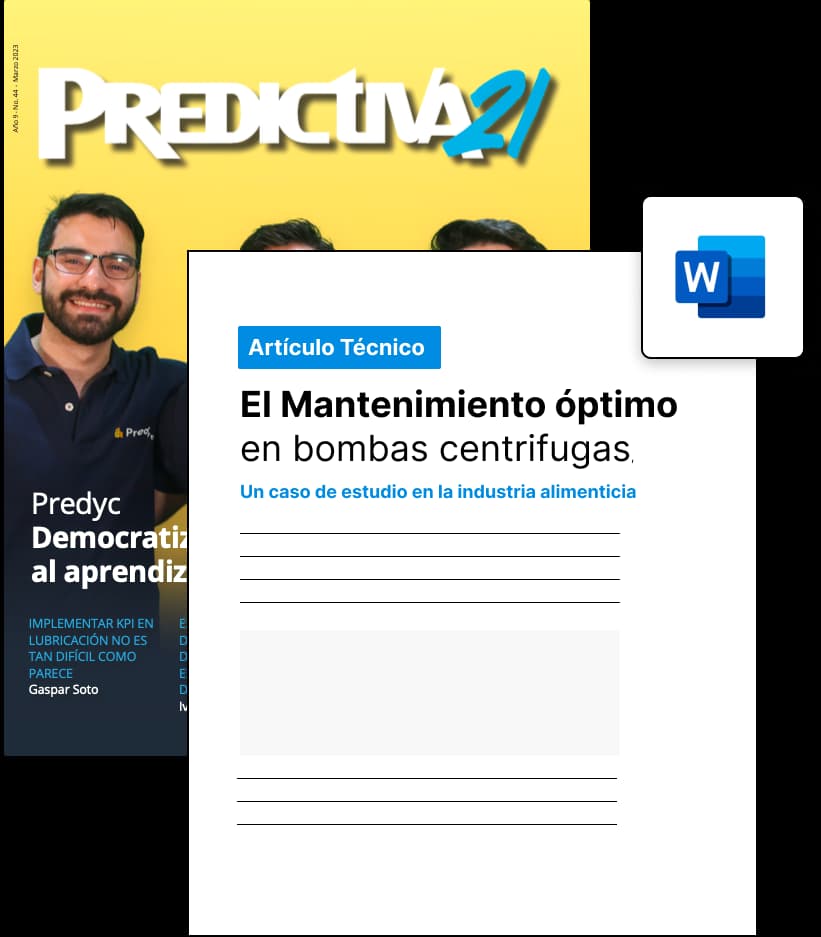