Aprovisionamiento para Garantizar la Confiabilidad de la Producción
Articulo27 de enero de 2020
El presente resumen tiene como finalidad mostrar una visión de cómo debe ser la gestión de aprovisionamiento de repuestos para poder garantizar confiabilidad operativa de una empresa de producción masiva, mostrando conceptos básicos logísticos, operativos, y de mantenimiento, engranándolos para mostrar una visualización global del tema. Además de mostrar un ejemplo de una empresa que presentaba problemas de confiabilidad operativa y de gestión de mantenimiento, también se esquematiza las alternativas de solución que aplicaron para poder superar la problemática que enfrentaban.
Marco Conceptual
El Ph.D y profesor Porter (1985), diseñador de la cadena de valor empresaria, o cadena de valor, explica que “es un modelo teórico que permite describir el desarrollo de las actividades de una organización empresarial generando valor al cliente final”. Donde las actividades primarias se refieren a la creación física del producto, diseño, fabricación, venta y el servicio posventa, y pueden también a su vez, diferenciarse en sub-actividades, directas, indirectas y de control de calidad. El modelo de la cadena de valor distingue cinco actividades primarias:
- Logística interna bilateral: comprende operaciones de recepción, gestionar los pedidos, seguimientos de los pedidos y distribución de los componentes. Es decir: recepción, almacenamiento, control de existencias y distribución interna de materias primas y materiales auxiliares hasta que se incorporan al proceso productivo.
- Operaciones (producción): procesamiento de las materias primas para transformarlas en el producto final. Es en esta etapa donde se procura minimizar los costos.
- Logística externa lateral: almacenamiento y recepción de los productos y distribución del producto al consumidor.
- Marketing y Ventas: actividades con las cuales se da a conocer el producto.
- Servicio: de posventa o mantenimiento, agrupa las actividades destinadas a mantener y realzar el valor del producto, mediante la aplicación de garantías, servicios técnicos y soporte de fábrica al producto.
Siendo la logística según el autor Ballou (2004), “la parte del proceso de la cadena de suministros que planea, lleva a cabo y controla el flujo y almacenamiento eficientes y efectivos de bienes y servicios, así como de la información relacionada, desde el punto de origen hasta el punto de consumo, con el fin de satisfacer los requerimientos de los clientes”.
Y la administración de la cadena de suministros mucho más amplia, incluyendo las funciones de marketing, y producción de una empresa, y las interacciones que se llevan a cabo entre empresas independientes legalmente dentro del canal de flujo de un producto. Es más, en la actualidad se ha añadido eslabones a esta cadena como parte integral de la administración de los suministros como es el desarrollo de productos, y los procesos de apoyo dentro de la cadena de valor al área productiva.
Uno de los elementos fundamentales dentro de la cadena de valor y la cadena de suministros de cualquier empresa es el proceso sustantivo de producción. Conociéndose como producción todo proceso a través del cual un objeto, ya sea natural o con algún grado de elaboración, se transforma en un producto útil para el consumo o para iniciar otro proceso productivo. La producción se realiza por la actividad humana de trabajo y con la ayuda de determinados instrumentos que tienen una mayor o menor perfección desde el punto de vista técnico.
Y la productividad, según la Real Academia de la Lengua Española, es “la capacidad o el nivel de producción por unidad de superficies de tierras cultivadas, de trabajo o de equipos industriales. De acuerdo a la perspectiva con la que se analice este término puede hacer referencia a diversas cosas, aquí presentamos algunas posibles definiciones”.
En tal sentido, para poder garantizar la productividad de un área de producción de una empresa es necesario gestionar los recursos de manera eficiente, para las unidades productivas muchas veces se requiere realizar reparaciones, ajustes, limpiezas y actividades de manutención a máquinas que ahí operan, y de esta manera evitar que se generen paradas no programadas causadas por agentes tanto internos como externos al proceso, trayendo como consecuencia una reducción de la cantidad de producto programado en un período determinado.
De ahí surge la necesidad del mantenimiento operacional, como proceso de apoyo fundamental de las industrias de manufactura y producción masiva, siendo definido éste por la European Federetion of Nacional Mantenance Societies como “todas las acciones que tienen como objeto mantener un artículo o restaurarlo a un estado en el cual pueda llevar a cabo alguna función requerida. Estas acciones incluyen la combinación de las acciones técnicas y administrativas correspondientes”.
En tal sentido para poder llevar los indicadores para el seguimiento y control de la ejecución de los mantenimientos se han formulado los conceptos como son la confiabilidad, mantenibilidad, disponibilidad, entre otros. Para de esta manera poder mejorar las acciones técnicas y administrativas para el control de las tres aristas conocidas del mantenimiento de los equipos, conocidas como el mantenimiento correctivo, preventivo y predictivo respectivamente.
Según Díaz (1992) define confiabilidad como “el conjunto de disciplinas de la mantenibilidad, la disponibilidad, seguridad y la confiabilidad propiamente dicha. Teniendo como objeto estudiar el comportamiento de los equipos en el tiempo”.
Siendo la confiabilidad de que un sistema o equipo cumpla una misión específica bajo condiciones de uso determinadas en un período determinado.
Por su parte la mantenibilidad es la probabilidad de que un dispositivo sea devuelto a un estado en el que se pueda cumplir su misión en un tiempo dado, luego de la aparición de una falla y cuando el mantenimiento es realizado en las condiciones y con los medios y procedimientos pre establecidos.
Para lograr la correcta ejecución de los mantenimientos es necesario garantizar la disponibilidad de insumos y repuestos, partiendo no simplemente de un proceso de compras, sino de un proceso de aprovisionamiento que no es más que el conjunto de actividades que desarrollan las empresas para asegurar la disponibilidad de los bienes y servicios externos que le son necesarios para la realización de sus operaciones, garantizando su adquisición, transporte desde el proveedor hasta el almacén del comprador, control de calidad y cantidad, recepción hasta el ingreso al inventario del almacén.
Marco Modelo
Organización Modelo Necesaria
Dentro de la cadena de valor organizativa se puede definir los procesos mínimos necesarios para garantizar la correcta operatividad de la empresa, sin implicar cambios radicales dentro de la estructura operativa. Un ejemplo de cadena de valor básica se puede visualizar en la figura 1.

Fuente: El Autor
La estructura organizativa depende del tamaño y las labores que lleve a cabo cada organización, pero los procesos deben de ser básicamente los definidos dentro de la cadena de valor previamente mostrada, adaptada a cada empresa en específico, siendo designados como procesos medulares o sustantivos todos aquellos que agreguen valor directo al producto, y procesos de apoyos a todos aquellos que ayudan a que los procesos medulares se lleven a cabo de manera eficaz y eficiente.
Funcionamiento Modelo
Ahora bien, es importante saber, luego de haber conocido los conceptos básicos de la temática a tratar, la importancia de la cadena de suministros dentro de cualquier organización, ya que ésta corta sagitalmente la organización en todos los procesos medulares, y alimentado a su vez a parte de los procesos de apoyo de la empresa. Una de las áreas a las que se le suele brindar mayor atención es la producción, ya que está es el brazo operativo de la empresa, que apalanca a la organización para logra cubrir la demanda del segmento de mercado a la cual satisface. Pero surge la pregunta, ¿Cómo se logra mantener la producción dentro de la programación, sin interrupciones inesperadas?
La respuesta a esta pregunta se puede dividir de la siguiente forma:
- Realizar una correcta gestión de aprovisionamiento de materia prima, para garantizar que no faltará material para poder ejecutar la transformación dentro del proceso productivo.
- Diseñar una programación de mantenimiento preventivo, partiendo de la información que manejamos como empresa, a partir de ahí podemos crear las rutinas:
- Plan de mantenimiento basado en las instrucciones del fabricante: comúnmente empleado cundo se adquiere un equipo nuevo, o se instala una nueva planta, y no se posee registro alguno del desempeño de la máquina, ni de la vida útil de sus componentes, y menos aún de cuáles serían las causas de fallas recurrentes. Por tanto, se crea un plan de mantenimiento basado en las instrucciones del fabricante, que normalmente vienen incluidas en el manual de operación y mantenimiento.
- Unas de las situaciones que hay que evaluar es que cada fabricante intenta llegar al objetivo de calidad exigido por el mercado al mínimo costo posible. Además de que a veces no les conviene solventar fallas en los equipos, así que las rutinas de mantenimiento planteadas por ellos deben de ser evaluadas y mejoradas.
- Plan de mantenimiento basado en protocolos genéricos: El siguiente paso podría ser agrupar los sistemas presentes en la planta, los equipos y elementos de máquina, que compongan cada sistema, y se realizan rutinas estandarizadas, clasificadas por tipo y capacidades, elaborando protocolos que sean comunes, y luego de eso se hace más fácil la correcta ejecución de los mantenimientos, distribuyéndolos en el tiempo según las necesidades de cada proceso productivo, respetando las horas de funcionamiento para evitar fallas en los equipos, y reducir su disponibilidad.
- Es necesario agrupar los sistemas de la manera más sencilla posible, ejemplo: sistema de aire comprimido, sistema de acondicionamiento de aire, sistema de aguas blancas, etc. Y conocer los componentes de cada sistema, e intentar y describir los protocolos lo más detallado posible, por cada uno de los equipos en sus rutinas diarias, mensuales, trimestrales, semestrales y anuales, según sea el caso del requerimiento.
- Plan de mantenimiento basado en la confiabilidad: como siguiente nivel al plan de mantenimiento basado en protocolos genéricos, es necesario llevar un registro estadístico de las fallas más frecuentes, que generan demoras en los procesos productivos, y obligan a bajar la velocidad de producción o la potencia de la máquina en falla, o avería, que causa la parada total de la unidad, y a veces de una línea de producción completa; se procede a realizar un levantamiento completo y agrupación de los tipos de sistemas, equipos y elementos que lo conforman, y se crean rutinas de mantenimiento genéricas, tomando en consideración las mejoras a las rutinas plateadas por el fabricante, en función de los conocimientos adquiridos por la práctica, el seguimiento y control de los mantenimientos ejecutados, el historial de averías, y los mantenimientos correctivos realizados en las líneas de producción, y sus respectivos equipos auxiliares o de apoyo. La confiabilidad de un elemento puede ser caracterizada a través de distintos modelos de probabilidades. Se realizan los diagramas de distribuciones de fallas comunes y se analizan para extraer sus causas y posibles soluciones, y de esta manera generar un aprendizaje para gestionar los recursos de mantenimiento. Convirtiendo el conocimiento ganado de ellas en acciones proactivas de mantenimiento, de manera tal de poder comprender el problema que se tiene con un equipo o sistema determinado, que finalmente se podría convertir en cuello de botella dentro del proceso, que reduciría la cantidad de producción, impactando negativamente en la confiabilidad de las operaciones. El objetivo es entender el problema, pronosticar fallas y analizar riesgos para tomar mejores decisiones de mantenimiento. Estas decisiones impactan el momento elegido para reemplazo, reparación u Overhaull de Maquinaria, como así también optimizar cualquier otra tarea de gestión del mantenimiento principalmente las inspecciones y gestión de repuestos.
- Plan de mantenimiento basado en las instrucciones del fabricante: comúnmente empleado cundo se adquiere un equipo nuevo, o se instala una nueva planta, y no se posee registro alguno del desempeño de la máquina, ni de la vida útil de sus componentes, y menos aún de cuáles serían las causas de fallas recurrentes. Por tanto, se crea un plan de mantenimiento basado en las instrucciones del fabricante, que normalmente vienen incluidas en el manual de operación y mantenimiento.
- Gestionar de manera efectiva y eficiente la cadena de suministros y aprovisionamiento de repuestos para la ejecución del plan de mantenimiento preventivo, y predictivo (en caso de tenerlo), además de un stock mínimo para caso de contingencias o de cualquier correctivo que se generen, que puedan retrasar el proceso.
- Para ello hay que realizar una planificación detallada de las necesidades de repuestos y consumibles para cada mantenimiento, y basándose en el estudio sistemático de las paradas correctivas y su frecuencia, y la cantidad de consumibles agotados por período, se debe de estimar un stock mínimo y los puntos de pedido.
- Si se calcula mal el punto de pedido y se queda por debajo de la demanda programada y prevista de un repuesto, produciendo bien sea exceso de horas de operación sin mantenimiento, acarreando consigo un mayor desgaste de los elementos de los equipos, reduciendo así su confiabilidad, o peor aún paradas de las unidades, sin tener piezas de recambio, que trae consigo paradas prolongadas de sistemas y hasta líneas productivas, reduciendo o paralizando por completo la producción, corriendo el riesgo de perder un mercado en específico por desabastecimiento de producto.
- Si se calcula por exceso, la empresa incurriría en unos costes innecesarios por inmovilización de existencias, y costos de almacenamiento de productos, por baja rotación del inventario.
- Para ello hay que realizar una planificación detallada de las necesidades de repuestos y consumibles para cada mantenimiento, y basándose en el estudio sistemático de las paradas correctivas y su frecuencia, y la cantidad de consumibles agotados por período, se debe de estimar un stock mínimo y los puntos de pedido.
Organización Caso de Estudio
Se plantea como caso de estudio una empresa de consumo masivo, fabricante de productos alimenticios, que llamaremos a partir de ahora “Alfa”, ubicada en la República Bolivariana de Venezuela, ésta empresa tenía problemas con paradas prolongadas en sus líneas de producción, no podían crecer dentro de un mercado muy competitivo, y constantemente tenían que realizar jornadas de sobre tiempo para poder sacar la producción requerida por mercadeo, y muchas veces no lograban llegar la meta. Mostrando serios problemas operativos. Algunas de las causas estudiadas para poder evaluar la situación de la empresa Alfa se muestran en el diagrama de Ishikawa de la figura 2.7

Fuente: El Autor
Cursos recomendados






%252FImagen%252FRAMPREDYC-1730060420837.webp%3Falt%3Dmedia%26token%3D2634a7f0-988e-4022-b91f-382503e6e9db&w=3840&q=75)

Marco Explicativo
Ahora bien, al estudiar la problemática de la empresa Alfa se pudo visualizar las causas mostradas en la figura 2, y aplicando el método de Pareto se determinó que las causas que influían en mayor medida en la baja confiabilidad productiva de la empresa eran las que se desarrollan a continuación:
Planificación del Mantenimiento: La organización Alfa, llevaba un sistema de planificación de mantenimiento basado en las instrucciones de fabricante; no habían tomado la previsión de diseñar indicadores y toma de datos estadísticos de las paradas y sus posibles causas. Trayendo como consecuencia paradas correctivas recurrentes que no eran consideradas para un replanteamiento de la planificación.
Además, se pudo ver que no se poseían pautas detalladas para la ejecución del mantenimiento, y mucho menos vinculación con los repuestos y consumibles asociados a cada mantenimiento, así que les era difícil prever la cantidad y tipos de repuestos necesarios para la ejecución de cada mantenimiento, y mucho menos del plan completo.
Al no levantar estadísticas también se tiene como consecuencia el no saber exactamente cuál es la causa de la recurrencia de cada falla, que generan las paradas, porque podrían ser también repuestos de mala calidad.
- En tal sentido se planteó el crear en principio planes de mantenimiento basados en procedimientos estándares, donde dentro de estos procedimientos se debía detallar los pasos a seguir para la ejecución de cada uno de los mantenimientos, además de vincular las actividades a los repuestos y consumibles que se emplearía en la ejecución. Esto por dos motivos importantes, el primero, poder tener los repuestos a la mano antes de la ejecución del mantenimiento, y evitar intervenir la máquina sin tener todas las piezas de recambio que deben de ser sustituidas; y segundo para poder proyectar el consumo de repuestos para la ejecución del plan anual, y el respectivo cálculo de punto y tiempo de pedido. Además, estas estadísticas también formarán la base para poder desarrollar posteriormente un mantenimiento centrado en la confiabilidad, con el cálculo de indicadores de disponibilidad, mantenibilidad y confiabilidad, y estadísticas para reducción de paradas no programadas y reducir exponencialmente los mantenimientos correctivos en la Planta.
Gestión del Inventario: El inventario de repuestos en la empresa Alfa era muy deficiente, era muy común que, al momento de ejecutar un mantenimiento, fuera planificado o no, no se contara con los repuestos y consumibles necesarios para su ejecución. Prolongando de esta manera en casos de fallas catastróficas y de averías, la ejecución del mantenimiento y la puesta en marcha del proceso productivo.
Los constantes quiebres de inventarios ocasionaban paradas de líneas de producción, o en mejor de los casos, reducción de velocidad de las líneas de producción, formando de esta forma cuellos de botella.
La mayor parte de los repuestos que consume la empresa Alfa son importados, y en un país con control cambiario, es necesario tomar en consideración el tiempo de adquisición de las divisas, además de las características del aprovisionamiento. En ésta organización el departamento de compras muchas veces cambiaba los términos de las contrataciones (según Incoterms), CIF, otros FOB, y en otros casos DDP. Además de los tiempos rectores de nacionalización y liberación de las cargas en la aduana.
Las constantes paradas de las líneas de producción generaban además problemas con los inventarios de materia prima, puesto que, al ser productos perecederos, en ocasiones existía merma del producto por vencimiento dentro de los almacenes de materia prima.
- Para éste problema se planteó como alternativa de solución llevar estadísticas de los repuestos y consumibles empleados realmente en cada mantenimiento, y los faltantes para la correcta ejecución, con esto se podrá realizar el cálculo más real del punto mínimo de pedido dentro del stock y el límite superior por insumo. Además, realizar un estudio del tiempo promedio en el cual la administración de la empresa Alfa se tarda en la adquisición de divisas, revisar con cada proveedor las características de las condiciones de contratación internacional, que para ésta empresa en específico la recomendación fue hacerla DDP. También se le recomendó hacer un plan de desarrollo de proveedores nacionales, para poder mejorar los tiempos de entrega de éstos proveedores, y poder garantizar la entrega a tiempo y con la calidad requerida de los consumibles y repuesto de fabricación nacional. Al garantizar la confiabilidad del mantenimiento y de la producción, se dará base para poder garantizar también la confiabilidad de las operaciones, y se reducirán las mermas por vencimiento de la materia prima, y se podrá cumplir con las metas de ventas fijadas por mercadeo, permitiendo ser a la empresa más competitiva.
Planeación Agregada de la Producción: La empresa Alfa se veía muy afectada por las constantes paradas del proceso productivo, generando fuertes retrasos en la producción de los lotes, la gerencia de producción frecuentemente tomaba la decisión de generar sobre tiempo para poder cumplir con la meta, además de generar gran cantidad de mermas por desperdicios en las constantes paradas y arranques de las máquinas, y merma de materia prima por vencimiento, por la baja rotación del inventario por las largas paradas de las líneas de producción.
- Una vez solucionado el problema de mantenimiento se podrá revisar la disponibilidad de las líneas de producción, y su eficiencia, y esta manera se podrá parametrizar de una mejor manera la planeación agregada de la producción. De esta forma se verán reducidas las jornadas de sobre tiempo, y las mermas de producto a causa de vencimiento de materia prima y por las paradas y arranque constantes de las líneas de producción.
Acuerdo de Paradas Planificadas: A causa de las continuas paradas de las líneas de producción, y la gran cantidad de cuellos de botella dentro del proceso productivo, generado por máquinas trabajando a menos de su capacidad por deterioro de sus sistemas, la gerencia de producción se negaba a entregar las unidades a la gerencia de mantenimiento para ejecutar el plan de manutención preventiva. Aludiendo que “las máquinas era más el tiempo que están averiadas que las que están produciendo, y los números no están cuadrando”, así que normalmente no existía un acuerdo entre producción y mantenimiento para poder intervenir las máquinas dentro del plan de mantenimiento preventivo. Como se puede visualizar en el cuadro 1, se realizó un estudio sistemático de las paradas y sus causas, para la mejora de las líneas de producción y del proceso en sí.

- Basándose en la restructuración del plan de mantenimiento, y del proceso de aprovisionamiento a tiempo de repuestos, se debe de hacer un compromiso real entre las dos gerencias, producción y mantenimiento, para la correcta ejecución del plan, las planeaciones agregadas de producción y mantenimiento deben de concatenar, para poder cumplir con las metas de producción, con eficacia y eficiencia, con unidades con altos niveles de disponibilidad y confiabilidad. Generándose una gran reducción en las micro paradas de planta, como se puede visualizar en la figura 3; demás de un incremento en la disponibilidad de las unidades productivas, y a su vez una mejora sustancial en la planeación agregada de la producción, reduciendo las jornadas extraordinarias de trabajo, y un incremento en la productividad y eficiencia del área de producción.

- Se plateó realizar reuniones de coordinación mensual entre las gerencias, para poder coordinar y ajustar las fechas de la planificación anual, distribuyéndolas en los días del mes que permitieran producir lo requerido por línea, y no generara gran desfase en la planificación del mantenimiento.
Finalmente, la empresa Alfa al aplicar los correctivos planteados, lograron incrementar sus niveles de producción en un 23% en el ejercicio del primer año, reduciendo además en 15% las mermas por desperdicio, 38% las mermas por vencimiento de la materia prima, la gestión de mantenimiento permitió tener una disponibilidad de 82%, aumentando así la confiabilidad de las líneas de producción, reduciendo las jornadas de sobretiempo de forma exponencial.
Referencias
- -Ballou, R (2004). Logística. Administración de la cadena de suministros. Prentice Hall, México.
- -Porter, M (1985). Competitive Advantage: Creating and Sustaining Superior Performance.
- -Díaz, A. (1992). Confiabilidad en mantenimiento. Ediciones IESA, Caracas, Venezuela.
- -http://www.aec.es/web/guest/centro-conocimiento/mantenimiento.
Autor: Carlos Alberto Díaz Palacios
Ingeniero en Mantenimiento Mecánico
Dinos qué te ha parecido el artículo
Artículos recomendados
Ciclo Brayton

La Codificación de Activos

Plan de monitoreo de condición: descubre su importancia

Entrevista a Annalisa Ferrari

Publica tu artículo en la revista #1 de Mantenimiento Industrial
Publicar un artículo en la revista es gratis, no tiene costo.
Solo debes asegurarte que no sea un artículo comercial.
¿Qué esperas?
O envía tu artículo directo: articulos@predictiva21.com
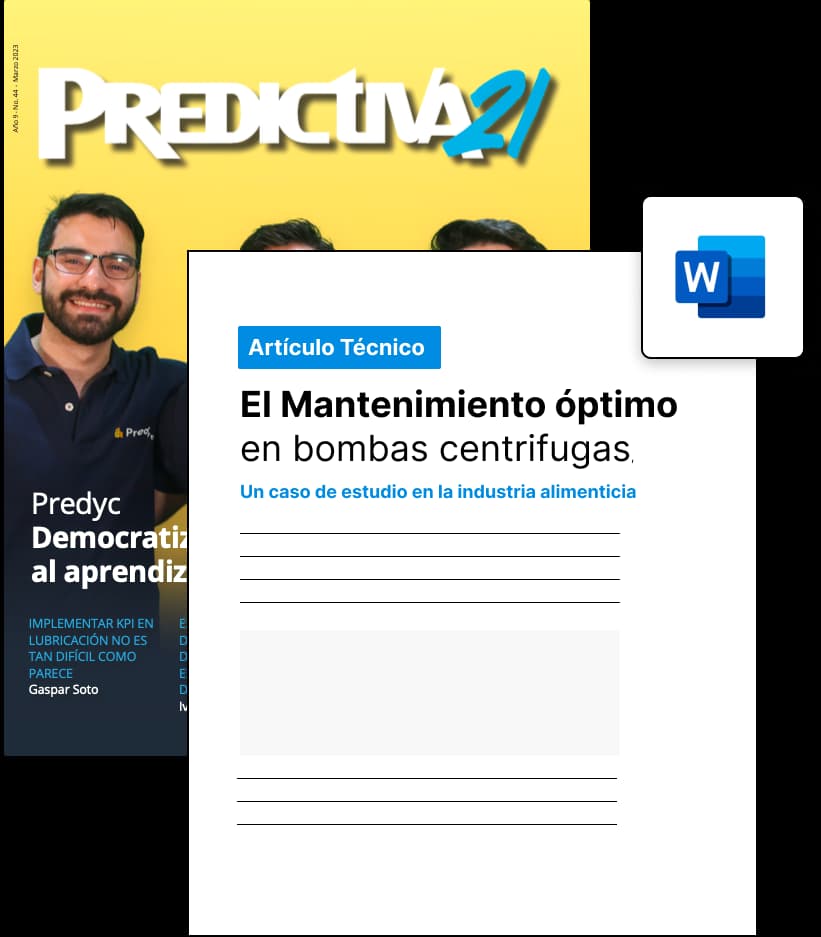
Aprovisionamiento para Garantizar la Confiabilidad de la Producción
Articulo 27 de enero de 2020El presente resumen tiene como finalidad mostrar una visión de cómo debe ser la gestión de aprovisionamiento de repuestos para poder garantizar confiabilidad operativa de una empresa de producción masiva, mostrando conceptos básicos logísticos, operativos, y de mantenimiento, engranándolos para mostrar una visualización global del tema. Además de mostrar un ejemplo de una empresa que presentaba problemas de confiabilidad operativa y de gestión de mantenimiento, también se esquematiza las alternativas de solución que aplicaron para poder superar la problemática que enfrentaban.
Marco Conceptual
El Ph.D y profesor Porter (1985), diseñador de la cadena de valor empresaria, o cadena de valor, explica que “es un modelo teórico que permite describir el desarrollo de las actividades de una organización empresarial generando valor al cliente final”. Donde las actividades primarias se refieren a la creación física del producto, diseño, fabricación, venta y el servicio posventa, y pueden también a su vez, diferenciarse en sub-actividades, directas, indirectas y de control de calidad. El modelo de la cadena de valor distingue cinco actividades primarias:
- Logística interna bilateral: comprende operaciones de recepción, gestionar los pedidos, seguimientos de los pedidos y distribución de los componentes. Es decir: recepción, almacenamiento, control de existencias y distribución interna de materias primas y materiales auxiliares hasta que se incorporan al proceso productivo.
- Operaciones (producción): procesamiento de las materias primas para transformarlas en el producto final. Es en esta etapa donde se procura minimizar los costos.
- Logística externa lateral: almacenamiento y recepción de los productos y distribución del producto al consumidor.
- Marketing y Ventas: actividades con las cuales se da a conocer el producto.
- Servicio: de posventa o mantenimiento, agrupa las actividades destinadas a mantener y realzar el valor del producto, mediante la aplicación de garantías, servicios técnicos y soporte de fábrica al producto.
Siendo la logística según el autor Ballou (2004), “la parte del proceso de la cadena de suministros que planea, lleva a cabo y controla el flujo y almacenamiento eficientes y efectivos de bienes y servicios, así como de la información relacionada, desde el punto de origen hasta el punto de consumo, con el fin de satisfacer los requerimientos de los clientes”.
Y la administración de la cadena de suministros mucho más amplia, incluyendo las funciones de marketing, y producción de una empresa, y las interacciones que se llevan a cabo entre empresas independientes legalmente dentro del canal de flujo de un producto. Es más, en la actualidad se ha añadido eslabones a esta cadena como parte integral de la administración de los suministros como es el desarrollo de productos, y los procesos de apoyo dentro de la cadena de valor al área productiva.
Uno de los elementos fundamentales dentro de la cadena de valor y la cadena de suministros de cualquier empresa es el proceso sustantivo de producción. Conociéndose como producción todo proceso a través del cual un objeto, ya sea natural o con algún grado de elaboración, se transforma en un producto útil para el consumo o para iniciar otro proceso productivo. La producción se realiza por la actividad humana de trabajo y con la ayuda de determinados instrumentos que tienen una mayor o menor perfección desde el punto de vista técnico.
Y la productividad, según la Real Academia de la Lengua Española, es “la capacidad o el nivel de producción por unidad de superficies de tierras cultivadas, de trabajo o de equipos industriales. De acuerdo a la perspectiva con la que se analice este término puede hacer referencia a diversas cosas, aquí presentamos algunas posibles definiciones”.
En tal sentido, para poder garantizar la productividad de un área de producción de una empresa es necesario gestionar los recursos de manera eficiente, para las unidades productivas muchas veces se requiere realizar reparaciones, ajustes, limpiezas y actividades de manutención a máquinas que ahí operan, y de esta manera evitar que se generen paradas no programadas causadas por agentes tanto internos como externos al proceso, trayendo como consecuencia una reducción de la cantidad de producto programado en un período determinado.
De ahí surge la necesidad del mantenimiento operacional, como proceso de apoyo fundamental de las industrias de manufactura y producción masiva, siendo definido éste por la European Federetion of Nacional Mantenance Societies como “todas las acciones que tienen como objeto mantener un artículo o restaurarlo a un estado en el cual pueda llevar a cabo alguna función requerida. Estas acciones incluyen la combinación de las acciones técnicas y administrativas correspondientes”.
En tal sentido para poder llevar los indicadores para el seguimiento y control de la ejecución de los mantenimientos se han formulado los conceptos como son la confiabilidad, mantenibilidad, disponibilidad, entre otros. Para de esta manera poder mejorar las acciones técnicas y administrativas para el control de las tres aristas conocidas del mantenimiento de los equipos, conocidas como el mantenimiento correctivo, preventivo y predictivo respectivamente.
Según Díaz (1992) define confiabilidad como “el conjunto de disciplinas de la mantenibilidad, la disponibilidad, seguridad y la confiabilidad propiamente dicha. Teniendo como objeto estudiar el comportamiento de los equipos en el tiempo”.
Siendo la confiabilidad de que un sistema o equipo cumpla una misión específica bajo condiciones de uso determinadas en un período determinado.
Por su parte la mantenibilidad es la probabilidad de que un dispositivo sea devuelto a un estado en el que se pueda cumplir su misión en un tiempo dado, luego de la aparición de una falla y cuando el mantenimiento es realizado en las condiciones y con los medios y procedimientos pre establecidos.
Para lograr la correcta ejecución de los mantenimientos es necesario garantizar la disponibilidad de insumos y repuestos, partiendo no simplemente de un proceso de compras, sino de un proceso de aprovisionamiento que no es más que el conjunto de actividades que desarrollan las empresas para asegurar la disponibilidad de los bienes y servicios externos que le son necesarios para la realización de sus operaciones, garantizando su adquisición, transporte desde el proveedor hasta el almacén del comprador, control de calidad y cantidad, recepción hasta el ingreso al inventario del almacén.
Marco Modelo
Organización Modelo Necesaria
Dentro de la cadena de valor organizativa se puede definir los procesos mínimos necesarios para garantizar la correcta operatividad de la empresa, sin implicar cambios radicales dentro de la estructura operativa. Un ejemplo de cadena de valor básica se puede visualizar en la figura 1.

Fuente: El Autor
La estructura organizativa depende del tamaño y las labores que lleve a cabo cada organización, pero los procesos deben de ser básicamente los definidos dentro de la cadena de valor previamente mostrada, adaptada a cada empresa en específico, siendo designados como procesos medulares o sustantivos todos aquellos que agreguen valor directo al producto, y procesos de apoyos a todos aquellos que ayudan a que los procesos medulares se lleven a cabo de manera eficaz y eficiente.
Funcionamiento Modelo
Ahora bien, es importante saber, luego de haber conocido los conceptos básicos de la temática a tratar, la importancia de la cadena de suministros dentro de cualquier organización, ya que ésta corta sagitalmente la organización en todos los procesos medulares, y alimentado a su vez a parte de los procesos de apoyo de la empresa. Una de las áreas a las que se le suele brindar mayor atención es la producción, ya que está es el brazo operativo de la empresa, que apalanca a la organización para logra cubrir la demanda del segmento de mercado a la cual satisface. Pero surge la pregunta, ¿Cómo se logra mantener la producción dentro de la programación, sin interrupciones inesperadas?
La respuesta a esta pregunta se puede dividir de la siguiente forma:
- Realizar una correcta gestión de aprovisionamiento de materia prima, para garantizar que no faltará material para poder ejecutar la transformación dentro del proceso productivo.
- Diseñar una programación de mantenimiento preventivo, partiendo de la información que manejamos como empresa, a partir de ahí podemos crear las rutinas:
- Plan de mantenimiento basado en las instrucciones del fabricante: comúnmente empleado cundo se adquiere un equipo nuevo, o se instala una nueva planta, y no se posee registro alguno del desempeño de la máquina, ni de la vida útil de sus componentes, y menos aún de cuáles serían las causas de fallas recurrentes. Por tanto, se crea un plan de mantenimiento basado en las instrucciones del fabricante, que normalmente vienen incluidas en el manual de operación y mantenimiento.
- Unas de las situaciones que hay que evaluar es que cada fabricante intenta llegar al objetivo de calidad exigido por el mercado al mínimo costo posible. Además de que a veces no les conviene solventar fallas en los equipos, así que las rutinas de mantenimiento planteadas por ellos deben de ser evaluadas y mejoradas.
- Plan de mantenimiento basado en protocolos genéricos: El siguiente paso podría ser agrupar los sistemas presentes en la planta, los equipos y elementos de máquina, que compongan cada sistema, y se realizan rutinas estandarizadas, clasificadas por tipo y capacidades, elaborando protocolos que sean comunes, y luego de eso se hace más fácil la correcta ejecución de los mantenimientos, distribuyéndolos en el tiempo según las necesidades de cada proceso productivo, respetando las horas de funcionamiento para evitar fallas en los equipos, y reducir su disponibilidad.
- Es necesario agrupar los sistemas de la manera más sencilla posible, ejemplo: sistema de aire comprimido, sistema de acondicionamiento de aire, sistema de aguas blancas, etc. Y conocer los componentes de cada sistema, e intentar y describir los protocolos lo más detallado posible, por cada uno de los equipos en sus rutinas diarias, mensuales, trimestrales, semestrales y anuales, según sea el caso del requerimiento.
- Plan de mantenimiento basado en la confiabilidad: como siguiente nivel al plan de mantenimiento basado en protocolos genéricos, es necesario llevar un registro estadístico de las fallas más frecuentes, que generan demoras en los procesos productivos, y obligan a bajar la velocidad de producción o la potencia de la máquina en falla, o avería, que causa la parada total de la unidad, y a veces de una línea de producción completa; se procede a realizar un levantamiento completo y agrupación de los tipos de sistemas, equipos y elementos que lo conforman, y se crean rutinas de mantenimiento genéricas, tomando en consideración las mejoras a las rutinas plateadas por el fabricante, en función de los conocimientos adquiridos por la práctica, el seguimiento y control de los mantenimientos ejecutados, el historial de averías, y los mantenimientos correctivos realizados en las líneas de producción, y sus respectivos equipos auxiliares o de apoyo. La confiabilidad de un elemento puede ser caracterizada a través de distintos modelos de probabilidades. Se realizan los diagramas de distribuciones de fallas comunes y se analizan para extraer sus causas y posibles soluciones, y de esta manera generar un aprendizaje para gestionar los recursos de mantenimiento. Convirtiendo el conocimiento ganado de ellas en acciones proactivas de mantenimiento, de manera tal de poder comprender el problema que se tiene con un equipo o sistema determinado, que finalmente se podría convertir en cuello de botella dentro del proceso, que reduciría la cantidad de producción, impactando negativamente en la confiabilidad de las operaciones. El objetivo es entender el problema, pronosticar fallas y analizar riesgos para tomar mejores decisiones de mantenimiento. Estas decisiones impactan el momento elegido para reemplazo, reparación u Overhaull de Maquinaria, como así también optimizar cualquier otra tarea de gestión del mantenimiento principalmente las inspecciones y gestión de repuestos.
- Plan de mantenimiento basado en las instrucciones del fabricante: comúnmente empleado cundo se adquiere un equipo nuevo, o se instala una nueva planta, y no se posee registro alguno del desempeño de la máquina, ni de la vida útil de sus componentes, y menos aún de cuáles serían las causas de fallas recurrentes. Por tanto, se crea un plan de mantenimiento basado en las instrucciones del fabricante, que normalmente vienen incluidas en el manual de operación y mantenimiento.
- Gestionar de manera efectiva y eficiente la cadena de suministros y aprovisionamiento de repuestos para la ejecución del plan de mantenimiento preventivo, y predictivo (en caso de tenerlo), además de un stock mínimo para caso de contingencias o de cualquier correctivo que se generen, que puedan retrasar el proceso.
- Para ello hay que realizar una planificación detallada de las necesidades de repuestos y consumibles para cada mantenimiento, y basándose en el estudio sistemático de las paradas correctivas y su frecuencia, y la cantidad de consumibles agotados por período, se debe de estimar un stock mínimo y los puntos de pedido.
- Si se calcula mal el punto de pedido y se queda por debajo de la demanda programada y prevista de un repuesto, produciendo bien sea exceso de horas de operación sin mantenimiento, acarreando consigo un mayor desgaste de los elementos de los equipos, reduciendo así su confiabilidad, o peor aún paradas de las unidades, sin tener piezas de recambio, que trae consigo paradas prolongadas de sistemas y hasta líneas productivas, reduciendo o paralizando por completo la producción, corriendo el riesgo de perder un mercado en específico por desabastecimiento de producto.
- Si se calcula por exceso, la empresa incurriría en unos costes innecesarios por inmovilización de existencias, y costos de almacenamiento de productos, por baja rotación del inventario.
- Para ello hay que realizar una planificación detallada de las necesidades de repuestos y consumibles para cada mantenimiento, y basándose en el estudio sistemático de las paradas correctivas y su frecuencia, y la cantidad de consumibles agotados por período, se debe de estimar un stock mínimo y los puntos de pedido.
Organización Caso de Estudio
Se plantea como caso de estudio una empresa de consumo masivo, fabricante de productos alimenticios, que llamaremos a partir de ahora “Alfa”, ubicada en la República Bolivariana de Venezuela, ésta empresa tenía problemas con paradas prolongadas en sus líneas de producción, no podían crecer dentro de un mercado muy competitivo, y constantemente tenían que realizar jornadas de sobre tiempo para poder sacar la producción requerida por mercadeo, y muchas veces no lograban llegar la meta. Mostrando serios problemas operativos. Algunas de las causas estudiadas para poder evaluar la situación de la empresa Alfa se muestran en el diagrama de Ishikawa de la figura 2.7

Fuente: El Autor
Cursos recomendados






%252FImagen%252FRAMPREDYC-1730060420837.webp%3Falt%3Dmedia%26token%3D2634a7f0-988e-4022-b91f-382503e6e9db&w=3840&q=75)

Marco Explicativo
Ahora bien, al estudiar la problemática de la empresa Alfa se pudo visualizar las causas mostradas en la figura 2, y aplicando el método de Pareto se determinó que las causas que influían en mayor medida en la baja confiabilidad productiva de la empresa eran las que se desarrollan a continuación:
Planificación del Mantenimiento: La organización Alfa, llevaba un sistema de planificación de mantenimiento basado en las instrucciones de fabricante; no habían tomado la previsión de diseñar indicadores y toma de datos estadísticos de las paradas y sus posibles causas. Trayendo como consecuencia paradas correctivas recurrentes que no eran consideradas para un replanteamiento de la planificación.
Además, se pudo ver que no se poseían pautas detalladas para la ejecución del mantenimiento, y mucho menos vinculación con los repuestos y consumibles asociados a cada mantenimiento, así que les era difícil prever la cantidad y tipos de repuestos necesarios para la ejecución de cada mantenimiento, y mucho menos del plan completo.
Al no levantar estadísticas también se tiene como consecuencia el no saber exactamente cuál es la causa de la recurrencia de cada falla, que generan las paradas, porque podrían ser también repuestos de mala calidad.
- En tal sentido se planteó el crear en principio planes de mantenimiento basados en procedimientos estándares, donde dentro de estos procedimientos se debía detallar los pasos a seguir para la ejecución de cada uno de los mantenimientos, además de vincular las actividades a los repuestos y consumibles que se emplearía en la ejecución. Esto por dos motivos importantes, el primero, poder tener los repuestos a la mano antes de la ejecución del mantenimiento, y evitar intervenir la máquina sin tener todas las piezas de recambio que deben de ser sustituidas; y segundo para poder proyectar el consumo de repuestos para la ejecución del plan anual, y el respectivo cálculo de punto y tiempo de pedido. Además, estas estadísticas también formarán la base para poder desarrollar posteriormente un mantenimiento centrado en la confiabilidad, con el cálculo de indicadores de disponibilidad, mantenibilidad y confiabilidad, y estadísticas para reducción de paradas no programadas y reducir exponencialmente los mantenimientos correctivos en la Planta.
Gestión del Inventario: El inventario de repuestos en la empresa Alfa era muy deficiente, era muy común que, al momento de ejecutar un mantenimiento, fuera planificado o no, no se contara con los repuestos y consumibles necesarios para su ejecución. Prolongando de esta manera en casos de fallas catastróficas y de averías, la ejecución del mantenimiento y la puesta en marcha del proceso productivo.
Los constantes quiebres de inventarios ocasionaban paradas de líneas de producción, o en mejor de los casos, reducción de velocidad de las líneas de producción, formando de esta forma cuellos de botella.
La mayor parte de los repuestos que consume la empresa Alfa son importados, y en un país con control cambiario, es necesario tomar en consideración el tiempo de adquisición de las divisas, además de las características del aprovisionamiento. En ésta organización el departamento de compras muchas veces cambiaba los términos de las contrataciones (según Incoterms), CIF, otros FOB, y en otros casos DDP. Además de los tiempos rectores de nacionalización y liberación de las cargas en la aduana.
Las constantes paradas de las líneas de producción generaban además problemas con los inventarios de materia prima, puesto que, al ser productos perecederos, en ocasiones existía merma del producto por vencimiento dentro de los almacenes de materia prima.
- Para éste problema se planteó como alternativa de solución llevar estadísticas de los repuestos y consumibles empleados realmente en cada mantenimiento, y los faltantes para la correcta ejecución, con esto se podrá realizar el cálculo más real del punto mínimo de pedido dentro del stock y el límite superior por insumo. Además, realizar un estudio del tiempo promedio en el cual la administración de la empresa Alfa se tarda en la adquisición de divisas, revisar con cada proveedor las características de las condiciones de contratación internacional, que para ésta empresa en específico la recomendación fue hacerla DDP. También se le recomendó hacer un plan de desarrollo de proveedores nacionales, para poder mejorar los tiempos de entrega de éstos proveedores, y poder garantizar la entrega a tiempo y con la calidad requerida de los consumibles y repuesto de fabricación nacional. Al garantizar la confiabilidad del mantenimiento y de la producción, se dará base para poder garantizar también la confiabilidad de las operaciones, y se reducirán las mermas por vencimiento de la materia prima, y se podrá cumplir con las metas de ventas fijadas por mercadeo, permitiendo ser a la empresa más competitiva.
Planeación Agregada de la Producción: La empresa Alfa se veía muy afectada por las constantes paradas del proceso productivo, generando fuertes retrasos en la producción de los lotes, la gerencia de producción frecuentemente tomaba la decisión de generar sobre tiempo para poder cumplir con la meta, además de generar gran cantidad de mermas por desperdicios en las constantes paradas y arranques de las máquinas, y merma de materia prima por vencimiento, por la baja rotación del inventario por las largas paradas de las líneas de producción.
- Una vez solucionado el problema de mantenimiento se podrá revisar la disponibilidad de las líneas de producción, y su eficiencia, y esta manera se podrá parametrizar de una mejor manera la planeación agregada de la producción. De esta forma se verán reducidas las jornadas de sobre tiempo, y las mermas de producto a causa de vencimiento de materia prima y por las paradas y arranque constantes de las líneas de producción.
Acuerdo de Paradas Planificadas: A causa de las continuas paradas de las líneas de producción, y la gran cantidad de cuellos de botella dentro del proceso productivo, generado por máquinas trabajando a menos de su capacidad por deterioro de sus sistemas, la gerencia de producción se negaba a entregar las unidades a la gerencia de mantenimiento para ejecutar el plan de manutención preventiva. Aludiendo que “las máquinas era más el tiempo que están averiadas que las que están produciendo, y los números no están cuadrando”, así que normalmente no existía un acuerdo entre producción y mantenimiento para poder intervenir las máquinas dentro del plan de mantenimiento preventivo. Como se puede visualizar en el cuadro 1, se realizó un estudio sistemático de las paradas y sus causas, para la mejora de las líneas de producción y del proceso en sí.

- Basándose en la restructuración del plan de mantenimiento, y del proceso de aprovisionamiento a tiempo de repuestos, se debe de hacer un compromiso real entre las dos gerencias, producción y mantenimiento, para la correcta ejecución del plan, las planeaciones agregadas de producción y mantenimiento deben de concatenar, para poder cumplir con las metas de producción, con eficacia y eficiencia, con unidades con altos niveles de disponibilidad y confiabilidad. Generándose una gran reducción en las micro paradas de planta, como se puede visualizar en la figura 3; demás de un incremento en la disponibilidad de las unidades productivas, y a su vez una mejora sustancial en la planeación agregada de la producción, reduciendo las jornadas extraordinarias de trabajo, y un incremento en la productividad y eficiencia del área de producción.

- Se plateó realizar reuniones de coordinación mensual entre las gerencias, para poder coordinar y ajustar las fechas de la planificación anual, distribuyéndolas en los días del mes que permitieran producir lo requerido por línea, y no generara gran desfase en la planificación del mantenimiento.
Finalmente, la empresa Alfa al aplicar los correctivos planteados, lograron incrementar sus niveles de producción en un 23% en el ejercicio del primer año, reduciendo además en 15% las mermas por desperdicio, 38% las mermas por vencimiento de la materia prima, la gestión de mantenimiento permitió tener una disponibilidad de 82%, aumentando así la confiabilidad de las líneas de producción, reduciendo las jornadas de sobretiempo de forma exponencial.
Referencias
- -Ballou, R (2004). Logística. Administración de la cadena de suministros. Prentice Hall, México.
- -Porter, M (1985). Competitive Advantage: Creating and Sustaining Superior Performance.
- -Díaz, A. (1992). Confiabilidad en mantenimiento. Ediciones IESA, Caracas, Venezuela.
- -http://www.aec.es/web/guest/centro-conocimiento/mantenimiento.
Autor: Carlos Alberto Díaz Palacios
Ingeniero en Mantenimiento Mecánico
Dinos qué te ha parecido el artículo
Artículos recomendados
How Inflation And Lack Of Foreign Currency Affect The Maintenance Of A Country

El RCA y la cultura del dato

La renovación de las infraestructuras: una necesidad económica

HxGN EAM: Un Enfoque Estratégico para la Gestión Eficiente de Activos

Publica tu artículo en la revista #1 de Mantenimiento Industrial
Publicar un artículo en la revista es gratis, no tiene costo.
Solo debes asegurarte que no sea un artículo comercial.
¿Qué esperas?
O envía tu artículo directo: articulos@predictiva21.com
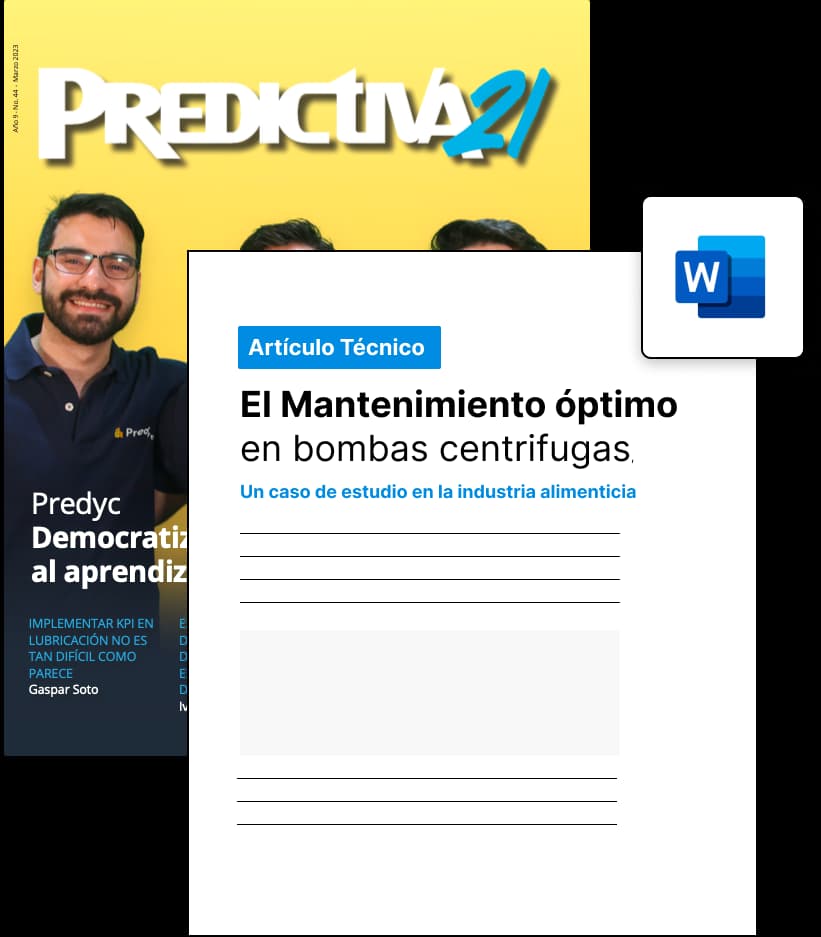