Calculando la frecuencia óptima de inspección - Considerando costos, riesgo y desempeño Caso de estudio basado en métodos y normas vigentes
Articulo30 de septiembre de 2019
Resumen
Las buenas prácticas descritas en las normas ISO 55000 “Gestión de Activos” y UNE – EN 16646 “Mantenimiento en la Gestión de los Activos Físicos”, establecen que toda organización debe aprovechar el valor potencial de sus activos durante el tiempo de vida. Esto incluye en primer lugar la determinación para incorporar nuevos activos para luego operarlos, mantenerlos, mejorarlos y desincorporarlos en el momento oportuno.
Los requisitos de las actividades de mantenimiento no permanecen estables, sino que cambian cuando cambian los entornos de negocio y tecnológicos. Por lo tanto, la función de mantenimiento debería evaluar continuamente sus objetivos y sus modos de funcionamiento y modificarlos cuando sea necesario. Esto implica la actualización de los planes de mantenimiento, desarrollo y reestructuración de recursos y evaluación de procesos y redefinición de los existentes. Por esta razón, el objetivo del departamento de mantenimiento de una organización es prevenir o mitigar el deterioro del desempeño de los activos en servicio y gestionar el riesgo de una falla cuando se pierde la función deseada del activo. Es una muy buena práctica de gestión de activos tener una lista de estrategias de mantenimiento para asegurar un nivel aceptable y predecible del desempeño a través de la vida útil del activo. Esto incluye inspecciones, monitoreo o pruebas en línea y política de mantenimiento preventivo (basado en el tiempo, basado en la condición, y basado en el uso). Normalmente, los fabricantes o proveedores de equipos entregan una lista de tareas de mantenimiento e inspección y la frecuencia de aplicación la cual no corresponde con el contexto operacional actual, la vida/edad del activo y las consecuencias de la falla del activo en el negocio. En este trabajo se mostrará un modelo matemático a través de una hoja de cálculo para determinar la frecuencia óptima de inspección considerando los costos, riesgo y desempeño.
Palabras Claves: Functional Failure, Deterioro, Activo Físico, Reliability, Disponibilidad, Ingeniería de Confiabilidad, Mantenibilidad, Life Cycle Costing, Inspección, Función.
1.- Introducción
Las empresas desarrollan planes de mantenimiento para garantizar el continuo servicio de sus sistemas, equipos y máquinas de tal manera de incrementar la confiabilidad y disponibilidad. En las últimas décadas, el mantenimiento ha sido protagonista del éxito, en la medida que las empresas se hacen más sólidas y confiables, al comprender que un mantenimiento mal planificado es responsable y limita los volúmenes de producción, afecta la calidad, deteriora el servicio al cliente, condiciona accidentes y daño al medio ambiente y origina costos indirectos que superan largamente el costo tradicional del mantenimiento planificado.
La idea general del mantenimiento está cambiando cada día, estos cambios se deben al aumento de mecanización, es decir, mayor complejidad de la maquinaria, las nuevas técnicas de mantenimiento y nuevos enfoques en las empresas y organizaciones. El mantenimiento también está reaccionando ante nuevas expectativas; esto incluye una mayor importancia a los aspectos de seguridad y ambiente, un conocimiento en la conexión existente entre el mantenimiento y la calidad del servicio o producto y un aumento de la presión ejercida para seguir una alta disponibilidad de los equipos y maquinaria.
Estos cambios ponen a prueba las actitudes y conocimientos del personal; dicho personal de mantenimiento que va del mecánico al gerente, deben adoptar nuevas formas de pensar y actuar, buscando un nuevo camino para evitar ineficiencias en el mantenimiento, tratando de encontrar un marco de trabajo estratégico que sintetice los nuevos avances, de forma que puedan evaluarlos racionalmente y aplicar aquellos que sean de mayor validez para ellos y su corporación.
Debido a la necesidad de incrementar la confiabilidad y disponibilidad de los activos fiscos se hace perentorio la elaboración o diseño de planes de mantenimiento haciendo uso de las metodologías desde la etapa temprana del ciclo de vida del activo tales como (RCM, FMECA, FMEA, RBI), para de esta manera adecuar el plan de cuidado del activo al contexto actual. Por otro lado es sumamente importante definir el intervalo óptimo de la frecuencia de inspección de los activos basados en el deterioro de los equipos para el monitoreo de la condición y por ende se requiere conocer la frecuencia optima de inspección la cual debe ser oportuna para evitar la falla funcional del equipo. (Fuenmayor, 2017)
2.- Modelo de Decisión Costo – Riesgo
Para determinar la frecuencia óptima de inspección se requiere de la construcción de dos curvas. Una que representa el costo asociado a las diferentes políticas de inspección modelado a diferente frecuencia y otra que indica los costos de riesgo asociado a una falla o perdida de la función primaria o secundaria del activo físico (Riesgo = Probabilidad de Falla x Consecuencia). Estas dos curvas se combinan en un modelo de decisión conocido como Modelo “Costo/Riesgo” (Woodhouse, 1993).
En años recientes grandes corporaciones industriales, especialmente del sector de hidrocarburos y de la industria de proceso, han volcado su atención hacia el modelo de decisión “Costo-Riesgo”, debido a que el mismo permite comparar el costo asociado a una acción de mantenimiento contra el nivel de reducción de riesgo o mejora en el desempeño debido a dicha acción; en otras palabras, el modelo permite saber “cuanto se obtiene por lo que se gasta”.
El análisis “Costo – Riesgo” resulta particularmente útil para decidir en escenarios en intereses en conflicto, como el escenario “Operación – Mantenimiento”, por una parte el departamento de operaciones requiere que el equipo o proceso opere por un tiempo prolongado para alcanzar las metas de producción y, simultáneamente, por otro lado, el departamento de mantenimiento requiere que el proceso o el activo físico se detenga con cierta frecuencia para poder intervenirlo y poder ganar confiabilidad en ellos. El modelo Costo – Riesgo es el indicado para resolver el conflicto previamente mencionado, dado que permite determinar el nivel óptimo de riesgo y la cantidad adecuada de inspección para obtener el máximo beneficio o mínimo impacto en el negocio.
En el modelo Costo – Riesgo pueden destacarse tres curvas que varían en el tiempo:
• La curva del nivel de riesgo (Riesgo = Probabilidad x Consecuencia). Entre las variables a considerar para el cálculo de riesgo se encuentran el incremento de la rata de falla conllevando a la reducción de la confiabilidad o incremento de la probabilidad de falla, incremento de los costos operacionales, perdida de desempeño entre otras variables. Esta curva es ascendente en el tiempo.
• La curva del costo de inspección (Costos Directos + Costos Indirectos), en la cual se simulan los costos de diferentes frecuencias para la acción de inspección. Esta curva es descendiente en el tiempo.
• La curva de impacto total al negocio, que resulta de la suma punto a punto de la curva de riesgo y la curva de los costos de inspección. El “mínimo o punto de inflexión” de esta curva representa el “mínimo impacto posible en el negocio” y está ubicado sobre el valor que puede traducirse como el periodo o frecuencia óptima para la realización de la acción de mantenimiento. Llevar a cabo la inspección a la izquierda de este punto nos llevaría a incurrir en un costo muy alto. Llevar a cabo la inspección a la derecha de este punto seria asumir mucho riesgo, por esta razón la recomendación es realizar la inspección en el punto óptimo de la curva de impacto total al negocio.

Fuente: Asset management an anatomy. IAM. 2015
La dificultad para el uso del modelo, se centra en la estimación o modelaje de la curva del riesgo, ya que la misma requiere la estimación de la probabilidad de falla (y su variación con el tiempo) y las consecuencias (Woodhouse, 1993).
El riesgo, base fundamental del modelo de decisión descrito anteriormente, es un término de naturaleza probabilística, que se define como la “probabilidad de tener una pérdida” y comúnmente se expresa en unidades monetarias. Matemáticamente, el riesgo se calcula con la siguiente ecuación:
Riesgo (t) = Probabilidad de falla x Consecuencias de la Falla
El análisis de la ecuación del riesgo, permite entender el poder de este indicador para el diagnóstico y la toma de decisiones, debido a que el mismo combina probabilidades o frecuencias de fallas con consecuencias, permitiendo la comparación de unidades como los equipos dinámicos, que normalmente presentan altas frecuencias de fallas con bajas consecuencias, con equipos estáticos, que normalmente presentan patrones de baja frecuencia de fallas y alta consecuencia.
El riesgo se comporta como una balanza, que permite pesar la influencia de ambas magnitudes (Probabilidad de falla y Consecuencia de la falla) en una decisión particular. El mantenimiento moderno, sustentado en la Ingeniería de la Confiabilidad, requiere de un cuidadoso proceso de diagnóstico de equipos y sistemas. El diagnóstico, basado en el “riesgo”, puede entenderse entonces como un proceso que busca caracterizar el estado actual y predecir el comportamiento futuro de equipos y sistemas.
Para el logro de un diagnóstico integrado el riesgo debe calcularse usando toda la información disponible; es decir, debe incluir el análisis del historial de fallas, los datos de condición y datos técnicos. De esta forma, se podrán identificar las acciones correctivas y preventivas que puedan efectivamente optimizar costos y minimizar su impacto en el negocio medular. (Woodhouse, 1993)
Entendiendo entonces que el “riesgo” es el indicador para un diagnóstico integrado, se analizará a continuación, con el máximo detalle posible el proceso para estimarlo. La siguiente Figura 2 muestra gráficamente la descomposición del indicador riesgo.

Fuente: Curso sobre frecuencia optima de inspección y mantenimiento. TWPL. 1999
3.- Propósito de la Inspección
El propósito de la inspección podría ser detectar a tiempo algún evento no deseado que pueda afectar la seguridad del hombre o impactar al ambiente así como mejorar la rentabilidad del negocio, ya que se puede anticipar la falla funcional. Cuando las fallas funcionales de los activos físicos no impactan considerablemente a las organizaciones desde el punto de vista económico quizás no sería necesario invertir dinero y tiempo en una ruta de inspección ya que la inspección genera un costo (Directo + Indirecto) lo cual no es rentable para el negocio. Los propósitos principales de una inspección son:
- Detectar o monitorear el riesgo de una falla de tal manera de evitar una catástrofe o evento con consecuencias graves a través del monitoreo de la condición del activo.
- Detectar la falla de una función que ya ha ocurrido y no es evidente al personal de operaciones.
4.- Tareas Basadas en Condición
Cualquier tarea basada en condición que se seleccione (predictiva, basada en condición o tarea de monitoreo de condición) debe satisfacer los siguientes criterios adicionales:
- a) Debe existir una falla potencial claramente definida.
- b) Debe existir un intervalo P-F identificable (o período para el desarrollo de falla).
- c) El intervalo de la tarea debe ser menor que el intervalo P-F probable más corto.
- d) Debe ser físicamente posible realizar la tarea en intervalos menores que el intervalo P-F.
- e) El tiempo más corto entre la detección de una falla potencial y la ocurrencia de una falla funcional (el intervalo P-F menos el intervalo de la tarea) debe ser suficientemente largo para predeterminar la acción a ser tomada a fin de evitar, eliminar o minimizar las consecuencias del modo de falla.
La mayoría de los modos de falla no ocurren instantáneamente del todo. En tales casos, es muy posible detectar que los elementos concernientes se encuentran en etapas finales de deterioro antes de alcanzar su estado de falla. Esta evidencia de falla inminente se conoce como “falla potencial”, la cual se define como “una condición identificable que indica que una falla funcional está a punto de ocurrir o está en un proceso de ocurrencia”. Si esta condición puede ser detectada, podría ser posible tomar acción para prevenir que el elemento falle completamente y/o evitar las consecuencias del modo de falla. (SAE JA1012, 2002
La Figura 3 ilustra lo que ocurre en las fases finales del proceso de falla. Esta se llama curva P-F, porque muestra como comienza una falla, deteriora hasta el punto en el cual puede ser detectada (“P”) y entonces, si no es detectada y corregida, continúa deteriorándose usualmente a una velocidad acelerada hasta que alcanza el punto de falla funcional (“F”).
Si se detecta una falla funcional entre el punto P y el punto F de la Figura 3, este es el punto en el cual podría ser posible tomar acción para prevenir la falla funcional y/o evitar sus consecuencias (si es posible o no tomar una acción significante dependerá de cuán rápido ocurre la falla funcional). Las tareas diseñadas para detectar las fallas potenciales se conocen como tareas basadas en condición.
Las tareas basadas en condición se llaman así porque los elementos se inspeccionan y se dejan en servicio bajo la condición de que continúen obteniéndose los estándares de operación especificados en otras palabras, bajo la condición que el modo de falla en consideración improbablemente ocurra antes de la próxima revisión. Esto también se conoce como mantenimiento predictivo (porque nosotros estamos tratando de predecir si y posiblemente cuando el elemento va a fallar en base a su comportamiento actual) o mantenimiento basado en condición (porque la necesidad de una acción correctiva o para evitar consecuencias está basada en una evaluación de la condición del elemento). (SAE JA1012, 2002)

Fuente: Norma de mantenimiento centrado en confiabilidad. SAE JA1012. 2002
En adición a la falla potencial, también es necesario considerar la cantidad de tiempo (o el número de ciclos de esfuerzo) que transcurre entre el punto en el cual ocurre la falla potencial en otras palabras, el punto en el cual se hace identificable y el punto en el que se deteriora hacia una falla funcional. Como se muestra en la Figura 4, este intervalo se conoce como el intervalo P-F, así mismo se muestra el desarrollo progresivo del deterioro a la falla.

Fuente: Norma de mantenimiento centrado en confiabilidad. SAE JA1012. 2002

Fuente: Norma de mantenimiento centrado en confiabilidad. SAE JA1012. 2002
El intervalo P-F determina que tan frecuente se deben hacer las tareas basadas en condición. Para detectar la falla potencial antes que se convierta en una falla funcional, el intervalo entre revisiones debe ser menor que el intervalo P-F. También es esencial que la condición de la falla potencial sea lo suficientemente clara para tener la certeza de que la persona que está entrenada para realizar la revisión, detectará la falla potencial siempre y cuando ocurra (o al menos, que la probabilidad de que la falla potencial no sea detectada sea suficientemente baja para reducir la probabilidad de un modo de falla no anticipado a un nivel que sea tolerable para el dueño o usuario del activo). (SAE JA1012, 2002)
El intervalo P-F también se conoce como período de advertencia, el tiempo que conduce hacia una falla funcional o el período de desarrollo de la falla. Este se puede medir en cualesquiera unidades que provean una indicación de la exposición al esfuerzo (tiempo de operación, unidades de producción, ciclos parada-arranque, etc.). Para diferentes modos de falla, estos varían de fracciones de segundo a varias décadas.
Nótese que si se realiza una tarea basada en condición a intervalos que son más largos que el intervalo P-F, existe una posibilidad de que la falla potencial sea abandonada del todo. Por otro lado, si se realiza la tarea a fracciones muy pequeñas del intervalo P-F, los recursos serán gastados en el proceso de revisión.
En la práctica, los intervalos de las tareas siempre se deben seleccionar para ser más cortos que el más corto intervalo P-F probable. En la mayoría de los casos, es suficiente seleccionar un intervalo de tarea igual a la mitad del intervalo P-F. Sin embargo, algunas veces es apropiado seleccionar intervalos de tarea que sean alguna otra fracción del intervalo P-F. Esto se puede regir por el intervalo P-F neto requerido (como se discute más adelante), o puede ser porque el usuario del activo tiene datos históricos relevantes que dictaminan que una fracción diferente es apropiada. (SAE JA1012, 2002)
Cursos recomendados




%252FImagen%252FRAMPREDYC-1730060420837.webp%3Falt%3Dmedia%26token%3D2634a7f0-988e-4022-b91f-382503e6e9db&w=3840&q=75)



5.- El Intervalo Neto P – F
El intervalo P-F rige la duración del período disponible para tomar cualquier acción necesaria con la finalidad de reducir o eliminar las consecuencias del modo de falla. Para que una tarea basada en condición sea técnicamente factible, el intervalo neto P-F debe ser mayor que el periodo requerido para evitar o reducir las consecuencias del modo de falla. Si el intervalo neto P-F es demasiado corto para tomar una acción sensata, entonces la tarea basada en condición no es técnicamente factible. En la práctica, el período requerido varía ampliamente. En algunos casos, puede ser una cuestión de horas (decir hasta el final de un ciclo de operación o el fin de un cambio) o incluso minutos (parar una máquina o para evacuar un edificio). En otros casos, pueden ser semanas o incluso meses (decir hasta un mantenimiento mayor). En general, se desean intervalos P-F mayores por dos razones:
- a) Es posible hacer cualquier cosa necesaria para evitar las consecuencias del modo de falla (incluyendo la planeación de la acción correctiva) de una manera más considerada y por demás controlada.
- b) Se requieren menos inspecciones basadas en condición.
Por esta razón se invierte mucha energía para encontrar las condiciones de la falla potencial y las técnicas basadas en condición que suministran posibles intervalos P-F mayores. Sin embargo; en algunos casos, es posible utilizar intervalos P-F muy cortos.
6.- Categorías de Técnicas Basadas en Condición
Las cuatro categorías mayores de técnicas basadas en condición son las siguientes:
a) Las técnicas basadas en las variaciones de la calidad del producto. En muchos casos, la emergencia de un defecto en un artículo producido por una máquina está directamente relacionada a un modo de falla de la misma. Muchos otros defectos surgen gradualmente, y así proveen evidencia oportuna de fallas potenciales.
b) Técnicas de monitoreo de efectos primarios. Los efectos primarios (velocidad, caudal de flujo, presión, temperatura, potencia, corriente, etc.) son otras fuentes de información acerca de las condiciones del equipo. Los efectos pueden ser monitoreados por una persona a través de la lectura de un indicador, por un computador como parte de un sistema de control de procesos, o por un registrador de mapas.
c) Técnicas basadas en los sentidos humanos (observar, escuchar, sentir, y oler).
d) Técnicas de monitoreo de condición. Estas son técnicas para detectar fallas potenciales que involucran el uso de equipo especializado (el cual algunas veces, se incorpora al equipo que se está monitoreando). Estas técnicas son conocidas como monitoreo de condición para distinguirlas de otros tipos de mantenimiento basados en condición.
Muchos modos de falla son precedidos por más de una – frecuentemente varias – fallas potenciales diferentes, así podría ser apropiada más de una categoría de tareas basadas en condición. Cada una de ellas tendrá un intervalo P-F diferente, y cada una requerirá diferentes tipos y niveles de habilidades. Esto significa que ninguna categoría de tareas por sí sola será siempre la más costo efectiva. Entonces, para evitar inclinaciones innecesarias en la selección de la tarea, es esencial:
a) Considerar todos los fenómenos detectables que probablemente precedan cada modo de falla, junto al rango total de tareas basadas en condición que puedan utilizarse para detectar esas advertencias.
b) Aplicar el criterio de selección de tareas del MCC rigurosamente para determinar cuales tareas (si existen) probablemente sean la manera más costo-efectiva de anticipar el modo de falla en consideración.
Nótese que cualquier dispositivo incorporado para determinar si un modo de falla está en proceso de ocurrir, debe satisfacer el mismo criterio para la factibilidad técnica y vale la pena hacerlo de cualquier mantenimiento basado en condición, con modos de falla adicionales, y se deben analizar conforme a ello. (SAE JA1012, 2002)
7.- Modelo para el Cálculo de la Frecuencia Óptima de Inspección
En la siguiente Figura 5 se muestran los cuatros parámetros más importantes en el cálculo de la frecuencia óptima de inspección tales como: Punto de inicio del deterioro, rata de deterioro, punto de falla y precisión en la medición.
Cabe destacar, que el modelo considera el deterioro del activo permitiendo determinar la fecha para la próxima inspección. Este modelo tiene como limitación el cálculo del riesgo en cuanto a la determinación de las variables asociadas a las consecuencias de la pérdida de la función primaria o secundaria. Debe establecerse un programa de inspección en la organización de tal manera de poder construir la curva de tendencia del monitoreo de la condición o deterioro desde el inicio de operación del activo o luego de una reparación mayor, es decir manejo del dato.
Es de resaltar la importancia de la aplicación del estándar API 580/581 debido al manejo de los diferentes mecanismos de deterioro y la estimación de las consecuencias, esto permitirá conocer la fecha para la próxima inspección para equipos de contención de energía. En este modelo se utilizó para pronosticar el deterioro la distribución probabilística Lognormal ya que es la distribución que muestra la cola más larga (ver Figura 7) para pronosticar el deterioro en comparación con las distribuciones (Weibull y Gamma), permitiendo una fecha para la próxima inspección más corta y de esta manera disminuir la probabilidad de alcanzar anticipadamente una falla funcional o pérdida de la función contención en equipos estáticos.

Fuente: Curso sobre frecuencia óptima de inspección y mantenimiento. TWPL. 1999
Generalmente no se conoce la rata en la cual el deterioro ocurrirá. En la siguiente Figura 6 se muestra la distribución de probabilidad de la variación del tiempo para la falla que podría ser esperado como resultado de la variación de la rata de deterioro.

Fuente: Curso sobre frecuencia optima de inspección y mantenimiento. TWPL. 1999
En muchos casos, aunque el propósito de la inspección puede ser prevenir las consecuencias catastróficas de algún modo de falla (por ejemplo ruptura de un recipiente), puede haber otro nivel de falla antes del modo de falla crítico, es decir, pueden haber múltiples niveles de falla, como se muestra en la Figura 7.

Fuente: Curso sobre frecuencia óptima de inspección y mantenimiento. TWPL. 1999
8.- Caso de Estudio. Tanque de Ácido Sulfúrico al 98%
En este caso de estudio se mostrará el análisis realizado con una hoja de cálculo, considerando todas las variables descritas en las primeras páginas de este documento. Adicionalmente, para validar los resultados arrojados por la hoja de cálculo se utilizaron los valores numéricos arrojados por un programa computacional de amplia trayectoria mundial en gestión de activos, lo que demuestra la certeza en los datos. Los datos son alterados por confidencialidad.
Se dispone de un tanque de ácido sulfúrico al 98% instalado en una planta petroquímica de operación continua por 20 años, en los cuales se ha cumplido con las recomendaciones del licenciante y el departamento técnico en cuanto las acciones de mantenimiento en cada parada de planta. El Ingeniero de Confiabilidad asignado a la planta, luego de diseñar el plan de mantenimiento basado en la confiabilidad utilizando la metodología RCM, se dispone a optimizar la frecuencia de inspección de acuerdo al monitoreo de la condición tal como lo muestran los informes del departamento de inspección de equipos estáticos. De no llevar a cabo la acción de inspección se afectaría la confiabilidad del proceso productivo y las consecuencias serían graves debido a la pérdida de la función contención en cuanto a la afectación al hombre y al ambiente al igual que los costos operacionales se incrementarían, y disminuiría el desempeño del activo con el tiempo. En la siguiente Tabla 1 se muestran los datos de entrada al modelo matemático.

Fuente: Propia

Fuente: Propia

Fuente: Propia

Fuente: Propia

Fuente: Propia
A continuación se muestra la tabla de los resultados indicando la frecuencia óptima para la próxima inspección. Estos resultados son obtenidos a través de la aplicación de un modelo matemático que modela el deterioro a diferentes frecuencias considerando costos, riesgos y desempeño.

Fuente: Propia
De acuerdo a este modelo la próxima inspección debe ser realizada en 7 años. No obstante, es recomendable el monitoreo cada cierto tiempo de las variables de deterioro para pronosticar el momento oportuno para la intervención del equipo. Para la resolución de este cálculo se modeló el costo de realizar la tarea de inspección a varias frecuencias y de la misma manera se calculó el riesgo de no hacer la tarea de inspección. Cabe destacar que los resultados obtenidos por la hoja de cálculo fueron validados y son muy cercanos a los arrojados por un programa computacional comercial de amplia trayectoria mundial con aplicación en varios sectores industriales. La poca diferencia se debe a la exactitud o precisión utilizada en el modelo del programa comercial, la cual por razones de confidencialidad no es posible conocerla. La matemática utilizada en la hoja de cálculo dispone de los parámetros y ajustes necesarios, los cuales están definidos en las normas y bibliografías consultadas.

Fuente: AMT – Inspection. 2017
9.- Conclusiones
En resumen, no basta con diseñar un plan de mantenimiento (PERFECTO) considerando todos los modos de fallas que han ocurrido o los que pueden ocurrir, a través de las diferentes herramientas o metodologías que sirven de soporte para responder la pregunta qué HACER, sino que también se debe definir CUÁNDO hacer la acción de mantenimiento y/o inspección para soportar la toma de decisiones en la gestión de activos. (Fuenmayor, 2017). El estudio de la frecuencia óptima de inspección debe ser calibrado o revisado si el contexto operacional donde está instalado el activo cambia con el tiempo, al igual que el incremento del deterioro ya que esto puede afectar la confiabilidad, el desempeño entre otras variables, debido a la afectación del comportamiento del activo para cumplir con su(s) función(es). Tal como se mostró en las primeras páginas de este documento, la confiabilidad del activo se ve afectada a medida que el equipo envejece, ya que su rata de falla se incrementa, por lo que se recomienda adecuar los planes de inspección a la edad y condición del equipo, considerando los costos en el ciclo de vida para seleccionar las tareas que sean no solo técnicamente factibles sino económicamente rentables y presupuestariamente viables. (Fuenmayor, 2017)
Por otra parte, el cálculo de la frecuencia óptima de inspección o intervalo para la próxima inspección es un parámetro sumamente importante para el monitoreo del deterioro del activo, ya que se puede anticipar la falla, es decir, una vez conocido el punto de la falla potencial se puede establecer el tiempo máximo permitido antes de llegar a la falla funcional. En el caso de equipo de contención de energía como lo son los equipos estáticos es muy esencial definir el momento oportuno para la inspección debido a las consecuencias cuando se pierde la función primaria del equipo.
10.- Referencias
- [1] Edgar Fuenmayor. ‘Calculando la Frecuencia Óptima de Mantenimiento o Reemplazo Preventivo’. Revista Predictiva 21 Nº 23. 2017. https://www.predictiva21.com
- [2] John D. Campbell and James V. Reyes – Picknell: ‘Uptime’, Strategies for Excellence in Maintenance Management, Canada, CRC Press. 2016.
- [3] UNE – EN 16646 Mantenimiento en la Gestión de los Activos Físicos. 2015.
- [4] Asset Management – An Anatomy, Version 3, United Kingdom, IAM. 2015.
- [5] John Woodhouse.: ‘Asset Management Decision-Making: The SALVO Process’, Strategic Assets: Life Cycle Value Optimization, United Kingdom, TWPL. 2014.
- [6] ISO – 55000 Asset Management — Overview, Principles and Terminology, 2014.
- [7] Andrew K.S. Jardine and Albert H. C. Tsang, Maintenance, Replacement, and Reliability (Theory and Applications), Second Edition, CRC Press. 2014.
- [8] Ramesh Gulati, ‘Maintenance and Reliability’ Best Practices, Second Edition, Industrial Press, Inc. 2013.
- [9] John D. Campbell, Andrew K.S. Jardine and Joel McGlynn; “Asset Management Excellence: Optimizing Equipment Life-Cycle Decisions”, CRC Press. 2011.
- [10] Edgar Fuenmayor, José Durán y Luís Sojo: ‘Decisión de Reemplazo o Reparación de un Equipo’, 2011. http:/www.gestionpas55.com
- [11] Macro Project EU 1488, 2008, http:/www.macroproject.org
- [12] Medardo Yáñez, Hernando Gómez de la Vega, Genebelin Valbuena.: ‘Ingeniería de Confiabilidad y Análisis Probabilístico de Riesgo’, Venezuela, R2M. 2004.
- [13] SAE JA1012, Una guía para la Norma de Mantenimiento Centrado en Confiabilidad (MCC). 2002.
- [14] John Moubray.: ‘Reliability Centered Maintenance’, RCM II, Second Edition, Industrial Press, Inc. 1997.
- [15] John Woodhouse.: ‘Managing Industrial Risk’, Getting value for money in your business, London, Chapman & Hall. 1993.
- [16] Colin Labouchere, C.M.: ‘Use of a Small Computer to Assist in Making Maintenance Decisions’, Proceedings of UK Maintenance Congress, London 1982.
Autor: Edgar Fuenmayor
Ing. MSc. CMRP
Correo: edgarfuenmayor1@gmail.com
Dinos qué te ha parecido el artículo
Artículos recomendados
Universidad de los Andes: Dr. Giacomo Barbieri

Ciclo Brayton

¿Son las personas de la organización “activos humanos”?

20.2.- Bomba Vertical en Línea

Publica tu artículo en la revista #1 de Mantenimiento Industrial
Publicar un artículo en la revista es gratis, no tiene costo.
Solo debes asegurarte que no sea un artículo comercial.
¿Qué esperas?
O envía tu artículo directo: articulos@predictiva21.com
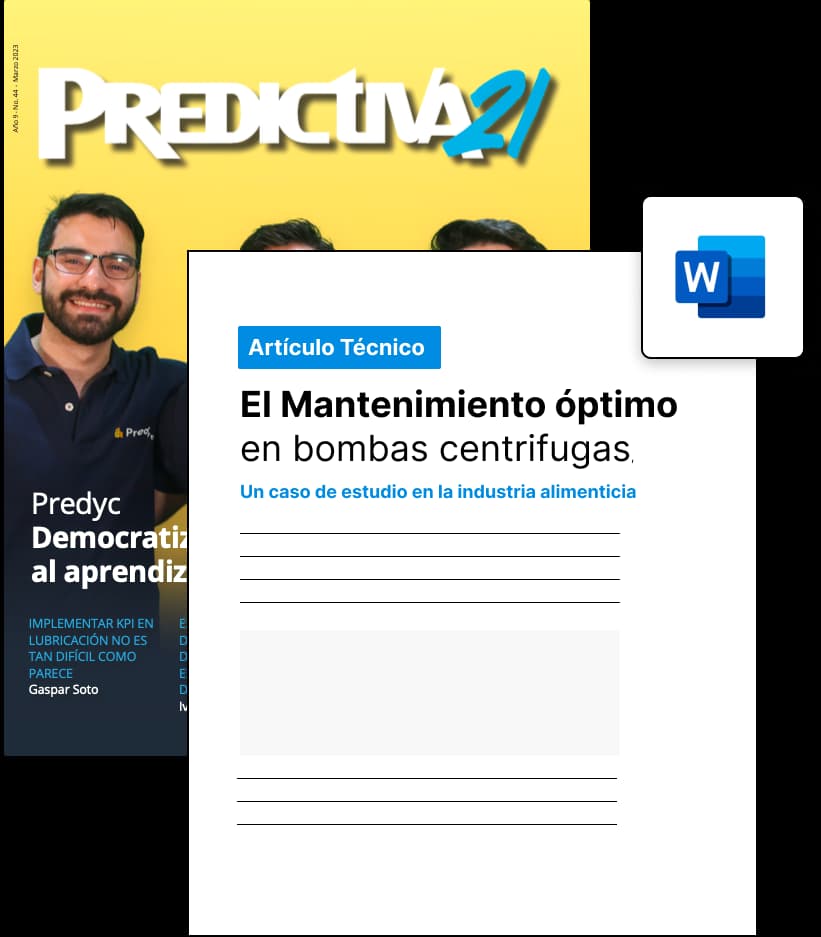
Calculando la frecuencia óptima de inspección - Considerando costos, riesgo y desempeño Caso de estudio basado en métodos y normas vigentes
Articulo 30 de septiembre de 2019Resumen
Las buenas prácticas descritas en las normas ISO 55000 “Gestión de Activos” y UNE – EN 16646 “Mantenimiento en la Gestión de los Activos Físicos”, establecen que toda organización debe aprovechar el valor potencial de sus activos durante el tiempo de vida. Esto incluye en primer lugar la determinación para incorporar nuevos activos para luego operarlos, mantenerlos, mejorarlos y desincorporarlos en el momento oportuno.
Los requisitos de las actividades de mantenimiento no permanecen estables, sino que cambian cuando cambian los entornos de negocio y tecnológicos. Por lo tanto, la función de mantenimiento debería evaluar continuamente sus objetivos y sus modos de funcionamiento y modificarlos cuando sea necesario. Esto implica la actualización de los planes de mantenimiento, desarrollo y reestructuración de recursos y evaluación de procesos y redefinición de los existentes. Por esta razón, el objetivo del departamento de mantenimiento de una organización es prevenir o mitigar el deterioro del desempeño de los activos en servicio y gestionar el riesgo de una falla cuando se pierde la función deseada del activo. Es una muy buena práctica de gestión de activos tener una lista de estrategias de mantenimiento para asegurar un nivel aceptable y predecible del desempeño a través de la vida útil del activo. Esto incluye inspecciones, monitoreo o pruebas en línea y política de mantenimiento preventivo (basado en el tiempo, basado en la condición, y basado en el uso). Normalmente, los fabricantes o proveedores de equipos entregan una lista de tareas de mantenimiento e inspección y la frecuencia de aplicación la cual no corresponde con el contexto operacional actual, la vida/edad del activo y las consecuencias de la falla del activo en el negocio. En este trabajo se mostrará un modelo matemático a través de una hoja de cálculo para determinar la frecuencia óptima de inspección considerando los costos, riesgo y desempeño.
Palabras Claves: Functional Failure, Deterioro, Activo Físico, Reliability, Disponibilidad, Ingeniería de Confiabilidad, Mantenibilidad, Life Cycle Costing, Inspección, Función.
1.- Introducción
Las empresas desarrollan planes de mantenimiento para garantizar el continuo servicio de sus sistemas, equipos y máquinas de tal manera de incrementar la confiabilidad y disponibilidad. En las últimas décadas, el mantenimiento ha sido protagonista del éxito, en la medida que las empresas se hacen más sólidas y confiables, al comprender que un mantenimiento mal planificado es responsable y limita los volúmenes de producción, afecta la calidad, deteriora el servicio al cliente, condiciona accidentes y daño al medio ambiente y origina costos indirectos que superan largamente el costo tradicional del mantenimiento planificado.
La idea general del mantenimiento está cambiando cada día, estos cambios se deben al aumento de mecanización, es decir, mayor complejidad de la maquinaria, las nuevas técnicas de mantenimiento y nuevos enfoques en las empresas y organizaciones. El mantenimiento también está reaccionando ante nuevas expectativas; esto incluye una mayor importancia a los aspectos de seguridad y ambiente, un conocimiento en la conexión existente entre el mantenimiento y la calidad del servicio o producto y un aumento de la presión ejercida para seguir una alta disponibilidad de los equipos y maquinaria.
Estos cambios ponen a prueba las actitudes y conocimientos del personal; dicho personal de mantenimiento que va del mecánico al gerente, deben adoptar nuevas formas de pensar y actuar, buscando un nuevo camino para evitar ineficiencias en el mantenimiento, tratando de encontrar un marco de trabajo estratégico que sintetice los nuevos avances, de forma que puedan evaluarlos racionalmente y aplicar aquellos que sean de mayor validez para ellos y su corporación.
Debido a la necesidad de incrementar la confiabilidad y disponibilidad de los activos fiscos se hace perentorio la elaboración o diseño de planes de mantenimiento haciendo uso de las metodologías desde la etapa temprana del ciclo de vida del activo tales como (RCM, FMECA, FMEA, RBI), para de esta manera adecuar el plan de cuidado del activo al contexto actual. Por otro lado es sumamente importante definir el intervalo óptimo de la frecuencia de inspección de los activos basados en el deterioro de los equipos para el monitoreo de la condición y por ende se requiere conocer la frecuencia optima de inspección la cual debe ser oportuna para evitar la falla funcional del equipo. (Fuenmayor, 2017)
2.- Modelo de Decisión Costo – Riesgo
Para determinar la frecuencia óptima de inspección se requiere de la construcción de dos curvas. Una que representa el costo asociado a las diferentes políticas de inspección modelado a diferente frecuencia y otra que indica los costos de riesgo asociado a una falla o perdida de la función primaria o secundaria del activo físico (Riesgo = Probabilidad de Falla x Consecuencia). Estas dos curvas se combinan en un modelo de decisión conocido como Modelo “Costo/Riesgo” (Woodhouse, 1993).
En años recientes grandes corporaciones industriales, especialmente del sector de hidrocarburos y de la industria de proceso, han volcado su atención hacia el modelo de decisión “Costo-Riesgo”, debido a que el mismo permite comparar el costo asociado a una acción de mantenimiento contra el nivel de reducción de riesgo o mejora en el desempeño debido a dicha acción; en otras palabras, el modelo permite saber “cuanto se obtiene por lo que se gasta”.
El análisis “Costo – Riesgo” resulta particularmente útil para decidir en escenarios en intereses en conflicto, como el escenario “Operación – Mantenimiento”, por una parte el departamento de operaciones requiere que el equipo o proceso opere por un tiempo prolongado para alcanzar las metas de producción y, simultáneamente, por otro lado, el departamento de mantenimiento requiere que el proceso o el activo físico se detenga con cierta frecuencia para poder intervenirlo y poder ganar confiabilidad en ellos. El modelo Costo – Riesgo es el indicado para resolver el conflicto previamente mencionado, dado que permite determinar el nivel óptimo de riesgo y la cantidad adecuada de inspección para obtener el máximo beneficio o mínimo impacto en el negocio.
En el modelo Costo – Riesgo pueden destacarse tres curvas que varían en el tiempo:
• La curva del nivel de riesgo (Riesgo = Probabilidad x Consecuencia). Entre las variables a considerar para el cálculo de riesgo se encuentran el incremento de la rata de falla conllevando a la reducción de la confiabilidad o incremento de la probabilidad de falla, incremento de los costos operacionales, perdida de desempeño entre otras variables. Esta curva es ascendente en el tiempo.
• La curva del costo de inspección (Costos Directos + Costos Indirectos), en la cual se simulan los costos de diferentes frecuencias para la acción de inspección. Esta curva es descendiente en el tiempo.
• La curva de impacto total al negocio, que resulta de la suma punto a punto de la curva de riesgo y la curva de los costos de inspección. El “mínimo o punto de inflexión” de esta curva representa el “mínimo impacto posible en el negocio” y está ubicado sobre el valor que puede traducirse como el periodo o frecuencia óptima para la realización de la acción de mantenimiento. Llevar a cabo la inspección a la izquierda de este punto nos llevaría a incurrir en un costo muy alto. Llevar a cabo la inspección a la derecha de este punto seria asumir mucho riesgo, por esta razón la recomendación es realizar la inspección en el punto óptimo de la curva de impacto total al negocio.

Fuente: Asset management an anatomy. IAM. 2015
La dificultad para el uso del modelo, se centra en la estimación o modelaje de la curva del riesgo, ya que la misma requiere la estimación de la probabilidad de falla (y su variación con el tiempo) y las consecuencias (Woodhouse, 1993).
El riesgo, base fundamental del modelo de decisión descrito anteriormente, es un término de naturaleza probabilística, que se define como la “probabilidad de tener una pérdida” y comúnmente se expresa en unidades monetarias. Matemáticamente, el riesgo se calcula con la siguiente ecuación:
Riesgo (t) = Probabilidad de falla x Consecuencias de la Falla
El análisis de la ecuación del riesgo, permite entender el poder de este indicador para el diagnóstico y la toma de decisiones, debido a que el mismo combina probabilidades o frecuencias de fallas con consecuencias, permitiendo la comparación de unidades como los equipos dinámicos, que normalmente presentan altas frecuencias de fallas con bajas consecuencias, con equipos estáticos, que normalmente presentan patrones de baja frecuencia de fallas y alta consecuencia.
El riesgo se comporta como una balanza, que permite pesar la influencia de ambas magnitudes (Probabilidad de falla y Consecuencia de la falla) en una decisión particular. El mantenimiento moderno, sustentado en la Ingeniería de la Confiabilidad, requiere de un cuidadoso proceso de diagnóstico de equipos y sistemas. El diagnóstico, basado en el “riesgo”, puede entenderse entonces como un proceso que busca caracterizar el estado actual y predecir el comportamiento futuro de equipos y sistemas.
Para el logro de un diagnóstico integrado el riesgo debe calcularse usando toda la información disponible; es decir, debe incluir el análisis del historial de fallas, los datos de condición y datos técnicos. De esta forma, se podrán identificar las acciones correctivas y preventivas que puedan efectivamente optimizar costos y minimizar su impacto en el negocio medular. (Woodhouse, 1993)
Entendiendo entonces que el “riesgo” es el indicador para un diagnóstico integrado, se analizará a continuación, con el máximo detalle posible el proceso para estimarlo. La siguiente Figura 2 muestra gráficamente la descomposición del indicador riesgo.

Fuente: Curso sobre frecuencia optima de inspección y mantenimiento. TWPL. 1999
3.- Propósito de la Inspección
El propósito de la inspección podría ser detectar a tiempo algún evento no deseado que pueda afectar la seguridad del hombre o impactar al ambiente así como mejorar la rentabilidad del negocio, ya que se puede anticipar la falla funcional. Cuando las fallas funcionales de los activos físicos no impactan considerablemente a las organizaciones desde el punto de vista económico quizás no sería necesario invertir dinero y tiempo en una ruta de inspección ya que la inspección genera un costo (Directo + Indirecto) lo cual no es rentable para el negocio. Los propósitos principales de una inspección son:
- Detectar o monitorear el riesgo de una falla de tal manera de evitar una catástrofe o evento con consecuencias graves a través del monitoreo de la condición del activo.
- Detectar la falla de una función que ya ha ocurrido y no es evidente al personal de operaciones.
4.- Tareas Basadas en Condición
Cualquier tarea basada en condición que se seleccione (predictiva, basada en condición o tarea de monitoreo de condición) debe satisfacer los siguientes criterios adicionales:
- a) Debe existir una falla potencial claramente definida.
- b) Debe existir un intervalo P-F identificable (o período para el desarrollo de falla).
- c) El intervalo de la tarea debe ser menor que el intervalo P-F probable más corto.
- d) Debe ser físicamente posible realizar la tarea en intervalos menores que el intervalo P-F.
- e) El tiempo más corto entre la detección de una falla potencial y la ocurrencia de una falla funcional (el intervalo P-F menos el intervalo de la tarea) debe ser suficientemente largo para predeterminar la acción a ser tomada a fin de evitar, eliminar o minimizar las consecuencias del modo de falla.
La mayoría de los modos de falla no ocurren instantáneamente del todo. En tales casos, es muy posible detectar que los elementos concernientes se encuentran en etapas finales de deterioro antes de alcanzar su estado de falla. Esta evidencia de falla inminente se conoce como “falla potencial”, la cual se define como “una condición identificable que indica que una falla funcional está a punto de ocurrir o está en un proceso de ocurrencia”. Si esta condición puede ser detectada, podría ser posible tomar acción para prevenir que el elemento falle completamente y/o evitar las consecuencias del modo de falla. (SAE JA1012, 2002
La Figura 3 ilustra lo que ocurre en las fases finales del proceso de falla. Esta se llama curva P-F, porque muestra como comienza una falla, deteriora hasta el punto en el cual puede ser detectada (“P”) y entonces, si no es detectada y corregida, continúa deteriorándose usualmente a una velocidad acelerada hasta que alcanza el punto de falla funcional (“F”).
Si se detecta una falla funcional entre el punto P y el punto F de la Figura 3, este es el punto en el cual podría ser posible tomar acción para prevenir la falla funcional y/o evitar sus consecuencias (si es posible o no tomar una acción significante dependerá de cuán rápido ocurre la falla funcional). Las tareas diseñadas para detectar las fallas potenciales se conocen como tareas basadas en condición.
Las tareas basadas en condición se llaman así porque los elementos se inspeccionan y se dejan en servicio bajo la condición de que continúen obteniéndose los estándares de operación especificados en otras palabras, bajo la condición que el modo de falla en consideración improbablemente ocurra antes de la próxima revisión. Esto también se conoce como mantenimiento predictivo (porque nosotros estamos tratando de predecir si y posiblemente cuando el elemento va a fallar en base a su comportamiento actual) o mantenimiento basado en condición (porque la necesidad de una acción correctiva o para evitar consecuencias está basada en una evaluación de la condición del elemento). (SAE JA1012, 2002)

Fuente: Norma de mantenimiento centrado en confiabilidad. SAE JA1012. 2002
En adición a la falla potencial, también es necesario considerar la cantidad de tiempo (o el número de ciclos de esfuerzo) que transcurre entre el punto en el cual ocurre la falla potencial en otras palabras, el punto en el cual se hace identificable y el punto en el que se deteriora hacia una falla funcional. Como se muestra en la Figura 4, este intervalo se conoce como el intervalo P-F, así mismo se muestra el desarrollo progresivo del deterioro a la falla.

Fuente: Norma de mantenimiento centrado en confiabilidad. SAE JA1012. 2002

Fuente: Norma de mantenimiento centrado en confiabilidad. SAE JA1012. 2002
El intervalo P-F determina que tan frecuente se deben hacer las tareas basadas en condición. Para detectar la falla potencial antes que se convierta en una falla funcional, el intervalo entre revisiones debe ser menor que el intervalo P-F. También es esencial que la condición de la falla potencial sea lo suficientemente clara para tener la certeza de que la persona que está entrenada para realizar la revisión, detectará la falla potencial siempre y cuando ocurra (o al menos, que la probabilidad de que la falla potencial no sea detectada sea suficientemente baja para reducir la probabilidad de un modo de falla no anticipado a un nivel que sea tolerable para el dueño o usuario del activo). (SAE JA1012, 2002)
El intervalo P-F también se conoce como período de advertencia, el tiempo que conduce hacia una falla funcional o el período de desarrollo de la falla. Este se puede medir en cualesquiera unidades que provean una indicación de la exposición al esfuerzo (tiempo de operación, unidades de producción, ciclos parada-arranque, etc.). Para diferentes modos de falla, estos varían de fracciones de segundo a varias décadas.
Nótese que si se realiza una tarea basada en condición a intervalos que son más largos que el intervalo P-F, existe una posibilidad de que la falla potencial sea abandonada del todo. Por otro lado, si se realiza la tarea a fracciones muy pequeñas del intervalo P-F, los recursos serán gastados en el proceso de revisión.
En la práctica, los intervalos de las tareas siempre se deben seleccionar para ser más cortos que el más corto intervalo P-F probable. En la mayoría de los casos, es suficiente seleccionar un intervalo de tarea igual a la mitad del intervalo P-F. Sin embargo, algunas veces es apropiado seleccionar intervalos de tarea que sean alguna otra fracción del intervalo P-F. Esto se puede regir por el intervalo P-F neto requerido (como se discute más adelante), o puede ser porque el usuario del activo tiene datos históricos relevantes que dictaminan que una fracción diferente es apropiada. (SAE JA1012, 2002)
Cursos recomendados




%252FImagen%252FRAMPREDYC-1730060420837.webp%3Falt%3Dmedia%26token%3D2634a7f0-988e-4022-b91f-382503e6e9db&w=3840&q=75)



5.- El Intervalo Neto P – F
El intervalo P-F rige la duración del período disponible para tomar cualquier acción necesaria con la finalidad de reducir o eliminar las consecuencias del modo de falla. Para que una tarea basada en condición sea técnicamente factible, el intervalo neto P-F debe ser mayor que el periodo requerido para evitar o reducir las consecuencias del modo de falla. Si el intervalo neto P-F es demasiado corto para tomar una acción sensata, entonces la tarea basada en condición no es técnicamente factible. En la práctica, el período requerido varía ampliamente. En algunos casos, puede ser una cuestión de horas (decir hasta el final de un ciclo de operación o el fin de un cambio) o incluso minutos (parar una máquina o para evacuar un edificio). En otros casos, pueden ser semanas o incluso meses (decir hasta un mantenimiento mayor). En general, se desean intervalos P-F mayores por dos razones:
- a) Es posible hacer cualquier cosa necesaria para evitar las consecuencias del modo de falla (incluyendo la planeación de la acción correctiva) de una manera más considerada y por demás controlada.
- b) Se requieren menos inspecciones basadas en condición.
Por esta razón se invierte mucha energía para encontrar las condiciones de la falla potencial y las técnicas basadas en condición que suministran posibles intervalos P-F mayores. Sin embargo; en algunos casos, es posible utilizar intervalos P-F muy cortos.
6.- Categorías de Técnicas Basadas en Condición
Las cuatro categorías mayores de técnicas basadas en condición son las siguientes:
a) Las técnicas basadas en las variaciones de la calidad del producto. En muchos casos, la emergencia de un defecto en un artículo producido por una máquina está directamente relacionada a un modo de falla de la misma. Muchos otros defectos surgen gradualmente, y así proveen evidencia oportuna de fallas potenciales.
b) Técnicas de monitoreo de efectos primarios. Los efectos primarios (velocidad, caudal de flujo, presión, temperatura, potencia, corriente, etc.) son otras fuentes de información acerca de las condiciones del equipo. Los efectos pueden ser monitoreados por una persona a través de la lectura de un indicador, por un computador como parte de un sistema de control de procesos, o por un registrador de mapas.
c) Técnicas basadas en los sentidos humanos (observar, escuchar, sentir, y oler).
d) Técnicas de monitoreo de condición. Estas son técnicas para detectar fallas potenciales que involucran el uso de equipo especializado (el cual algunas veces, se incorpora al equipo que se está monitoreando). Estas técnicas son conocidas como monitoreo de condición para distinguirlas de otros tipos de mantenimiento basados en condición.
Muchos modos de falla son precedidos por más de una – frecuentemente varias – fallas potenciales diferentes, así podría ser apropiada más de una categoría de tareas basadas en condición. Cada una de ellas tendrá un intervalo P-F diferente, y cada una requerirá diferentes tipos y niveles de habilidades. Esto significa que ninguna categoría de tareas por sí sola será siempre la más costo efectiva. Entonces, para evitar inclinaciones innecesarias en la selección de la tarea, es esencial:
a) Considerar todos los fenómenos detectables que probablemente precedan cada modo de falla, junto al rango total de tareas basadas en condición que puedan utilizarse para detectar esas advertencias.
b) Aplicar el criterio de selección de tareas del MCC rigurosamente para determinar cuales tareas (si existen) probablemente sean la manera más costo-efectiva de anticipar el modo de falla en consideración.
Nótese que cualquier dispositivo incorporado para determinar si un modo de falla está en proceso de ocurrir, debe satisfacer el mismo criterio para la factibilidad técnica y vale la pena hacerlo de cualquier mantenimiento basado en condición, con modos de falla adicionales, y se deben analizar conforme a ello. (SAE JA1012, 2002)
7.- Modelo para el Cálculo de la Frecuencia Óptima de Inspección
En la siguiente Figura 5 se muestran los cuatros parámetros más importantes en el cálculo de la frecuencia óptima de inspección tales como: Punto de inicio del deterioro, rata de deterioro, punto de falla y precisión en la medición.
Cabe destacar, que el modelo considera el deterioro del activo permitiendo determinar la fecha para la próxima inspección. Este modelo tiene como limitación el cálculo del riesgo en cuanto a la determinación de las variables asociadas a las consecuencias de la pérdida de la función primaria o secundaria. Debe establecerse un programa de inspección en la organización de tal manera de poder construir la curva de tendencia del monitoreo de la condición o deterioro desde el inicio de operación del activo o luego de una reparación mayor, es decir manejo del dato.
Es de resaltar la importancia de la aplicación del estándar API 580/581 debido al manejo de los diferentes mecanismos de deterioro y la estimación de las consecuencias, esto permitirá conocer la fecha para la próxima inspección para equipos de contención de energía. En este modelo se utilizó para pronosticar el deterioro la distribución probabilística Lognormal ya que es la distribución que muestra la cola más larga (ver Figura 7) para pronosticar el deterioro en comparación con las distribuciones (Weibull y Gamma), permitiendo una fecha para la próxima inspección más corta y de esta manera disminuir la probabilidad de alcanzar anticipadamente una falla funcional o pérdida de la función contención en equipos estáticos.

Fuente: Curso sobre frecuencia óptima de inspección y mantenimiento. TWPL. 1999
Generalmente no se conoce la rata en la cual el deterioro ocurrirá. En la siguiente Figura 6 se muestra la distribución de probabilidad de la variación del tiempo para la falla que podría ser esperado como resultado de la variación de la rata de deterioro.

Fuente: Curso sobre frecuencia optima de inspección y mantenimiento. TWPL. 1999
En muchos casos, aunque el propósito de la inspección puede ser prevenir las consecuencias catastróficas de algún modo de falla (por ejemplo ruptura de un recipiente), puede haber otro nivel de falla antes del modo de falla crítico, es decir, pueden haber múltiples niveles de falla, como se muestra en la Figura 7.

Fuente: Curso sobre frecuencia óptima de inspección y mantenimiento. TWPL. 1999
8.- Caso de Estudio. Tanque de Ácido Sulfúrico al 98%
En este caso de estudio se mostrará el análisis realizado con una hoja de cálculo, considerando todas las variables descritas en las primeras páginas de este documento. Adicionalmente, para validar los resultados arrojados por la hoja de cálculo se utilizaron los valores numéricos arrojados por un programa computacional de amplia trayectoria mundial en gestión de activos, lo que demuestra la certeza en los datos. Los datos son alterados por confidencialidad.
Se dispone de un tanque de ácido sulfúrico al 98% instalado en una planta petroquímica de operación continua por 20 años, en los cuales se ha cumplido con las recomendaciones del licenciante y el departamento técnico en cuanto las acciones de mantenimiento en cada parada de planta. El Ingeniero de Confiabilidad asignado a la planta, luego de diseñar el plan de mantenimiento basado en la confiabilidad utilizando la metodología RCM, se dispone a optimizar la frecuencia de inspección de acuerdo al monitoreo de la condición tal como lo muestran los informes del departamento de inspección de equipos estáticos. De no llevar a cabo la acción de inspección se afectaría la confiabilidad del proceso productivo y las consecuencias serían graves debido a la pérdida de la función contención en cuanto a la afectación al hombre y al ambiente al igual que los costos operacionales se incrementarían, y disminuiría el desempeño del activo con el tiempo. En la siguiente Tabla 1 se muestran los datos de entrada al modelo matemático.

Fuente: Propia

Fuente: Propia

Fuente: Propia

Fuente: Propia

Fuente: Propia
A continuación se muestra la tabla de los resultados indicando la frecuencia óptima para la próxima inspección. Estos resultados son obtenidos a través de la aplicación de un modelo matemático que modela el deterioro a diferentes frecuencias considerando costos, riesgos y desempeño.

Fuente: Propia
De acuerdo a este modelo la próxima inspección debe ser realizada en 7 años. No obstante, es recomendable el monitoreo cada cierto tiempo de las variables de deterioro para pronosticar el momento oportuno para la intervención del equipo. Para la resolución de este cálculo se modeló el costo de realizar la tarea de inspección a varias frecuencias y de la misma manera se calculó el riesgo de no hacer la tarea de inspección. Cabe destacar que los resultados obtenidos por la hoja de cálculo fueron validados y son muy cercanos a los arrojados por un programa computacional comercial de amplia trayectoria mundial con aplicación en varios sectores industriales. La poca diferencia se debe a la exactitud o precisión utilizada en el modelo del programa comercial, la cual por razones de confidencialidad no es posible conocerla. La matemática utilizada en la hoja de cálculo dispone de los parámetros y ajustes necesarios, los cuales están definidos en las normas y bibliografías consultadas.

Fuente: AMT – Inspection. 2017
9.- Conclusiones
En resumen, no basta con diseñar un plan de mantenimiento (PERFECTO) considerando todos los modos de fallas que han ocurrido o los que pueden ocurrir, a través de las diferentes herramientas o metodologías que sirven de soporte para responder la pregunta qué HACER, sino que también se debe definir CUÁNDO hacer la acción de mantenimiento y/o inspección para soportar la toma de decisiones en la gestión de activos. (Fuenmayor, 2017). El estudio de la frecuencia óptima de inspección debe ser calibrado o revisado si el contexto operacional donde está instalado el activo cambia con el tiempo, al igual que el incremento del deterioro ya que esto puede afectar la confiabilidad, el desempeño entre otras variables, debido a la afectación del comportamiento del activo para cumplir con su(s) función(es). Tal como se mostró en las primeras páginas de este documento, la confiabilidad del activo se ve afectada a medida que el equipo envejece, ya que su rata de falla se incrementa, por lo que se recomienda adecuar los planes de inspección a la edad y condición del equipo, considerando los costos en el ciclo de vida para seleccionar las tareas que sean no solo técnicamente factibles sino económicamente rentables y presupuestariamente viables. (Fuenmayor, 2017)
Por otra parte, el cálculo de la frecuencia óptima de inspección o intervalo para la próxima inspección es un parámetro sumamente importante para el monitoreo del deterioro del activo, ya que se puede anticipar la falla, es decir, una vez conocido el punto de la falla potencial se puede establecer el tiempo máximo permitido antes de llegar a la falla funcional. En el caso de equipo de contención de energía como lo son los equipos estáticos es muy esencial definir el momento oportuno para la inspección debido a las consecuencias cuando se pierde la función primaria del equipo.
10.- Referencias
- [1] Edgar Fuenmayor. ‘Calculando la Frecuencia Óptima de Mantenimiento o Reemplazo Preventivo’. Revista Predictiva 21 Nº 23. 2017. https://www.predictiva21.com
- [2] John D. Campbell and James V. Reyes – Picknell: ‘Uptime’, Strategies for Excellence in Maintenance Management, Canada, CRC Press. 2016.
- [3] UNE – EN 16646 Mantenimiento en la Gestión de los Activos Físicos. 2015.
- [4] Asset Management – An Anatomy, Version 3, United Kingdom, IAM. 2015.
- [5] John Woodhouse.: ‘Asset Management Decision-Making: The SALVO Process’, Strategic Assets: Life Cycle Value Optimization, United Kingdom, TWPL. 2014.
- [6] ISO – 55000 Asset Management — Overview, Principles and Terminology, 2014.
- [7] Andrew K.S. Jardine and Albert H. C. Tsang, Maintenance, Replacement, and Reliability (Theory and Applications), Second Edition, CRC Press. 2014.
- [8] Ramesh Gulati, ‘Maintenance and Reliability’ Best Practices, Second Edition, Industrial Press, Inc. 2013.
- [9] John D. Campbell, Andrew K.S. Jardine and Joel McGlynn; “Asset Management Excellence: Optimizing Equipment Life-Cycle Decisions”, CRC Press. 2011.
- [10] Edgar Fuenmayor, José Durán y Luís Sojo: ‘Decisión de Reemplazo o Reparación de un Equipo’, 2011. http:/www.gestionpas55.com
- [11] Macro Project EU 1488, 2008, http:/www.macroproject.org
- [12] Medardo Yáñez, Hernando Gómez de la Vega, Genebelin Valbuena.: ‘Ingeniería de Confiabilidad y Análisis Probabilístico de Riesgo’, Venezuela, R2M. 2004.
- [13] SAE JA1012, Una guía para la Norma de Mantenimiento Centrado en Confiabilidad (MCC). 2002.
- [14] John Moubray.: ‘Reliability Centered Maintenance’, RCM II, Second Edition, Industrial Press, Inc. 1997.
- [15] John Woodhouse.: ‘Managing Industrial Risk’, Getting value for money in your business, London, Chapman & Hall. 1993.
- [16] Colin Labouchere, C.M.: ‘Use of a Small Computer to Assist in Making Maintenance Decisions’, Proceedings of UK Maintenance Congress, London 1982.
Autor: Edgar Fuenmayor
Ing. MSc. CMRP
Correo: edgarfuenmayor1@gmail.com
Dinos qué te ha parecido el artículo
Artículos recomendados
Mantenimiento autónomo

Funciones de un planificador de mantenimiento

Cursos SAP PM

Modelo de Confiabilidad con Metodología RAM para un sistema de bombeo de agua de inyección

Publica tu artículo en la revista #1 de Mantenimiento Industrial
Publicar un artículo en la revista es gratis, no tiene costo.
Solo debes asegurarte que no sea un artículo comercial.
¿Qué esperas?
O envía tu artículo directo: articulos@predictiva21.com
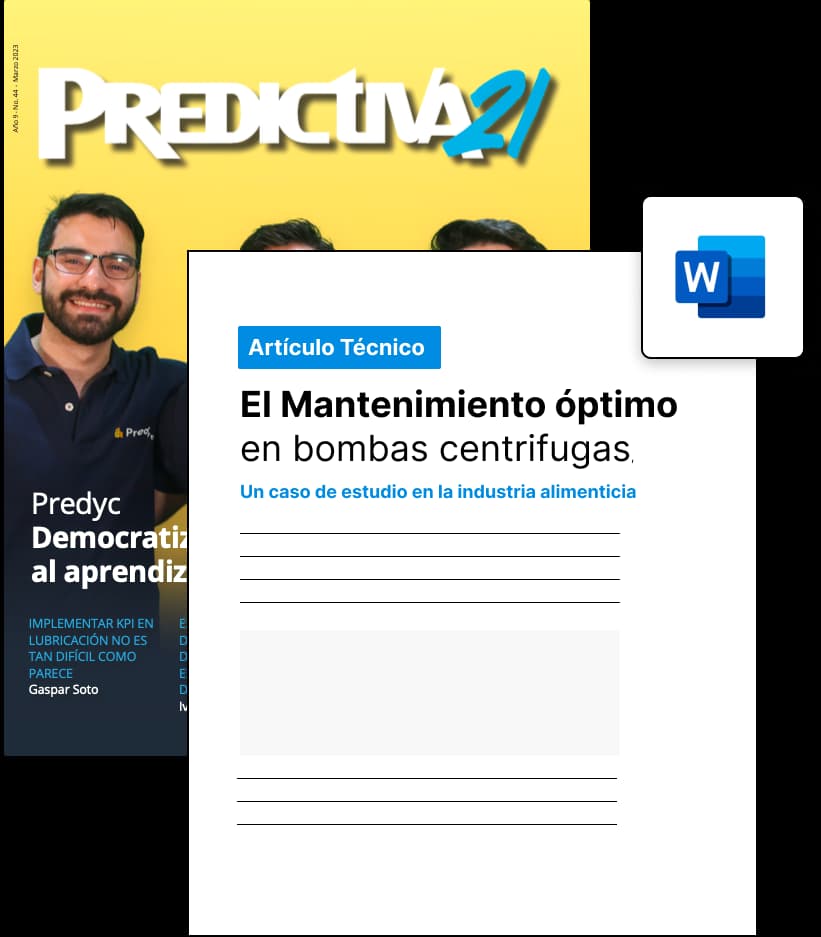